Apollo POWER VS Series User manual

Apollo Sprayers
POWER VS
SERIES
Turbine Instruction Manual

Page 2
TABLE OF CONTENTS
1
Safety.........................................................................................................................................................
3
2True HVLP™SprayFinishingSystems
....................................................................................................
5
2.1 How Your HVLP Turbine System
W
orks
..................................................................................................
5
2.2 How Your SprayGun
Works ....................................................................................................................
5
2.3 PreparingTo Use Your HVLP Turbine
....................................................................................................
6
2.4 FamiliarizeYourself
W
ith Your True HVLP™Turbine Spray
Gun ..........................................................
6
2.5 Get To Know Your Turbine
.....................................................................................................................
6
3ApolloHVLP
Turbines ..............................................................................................................................
7
3.1 ApolloTurbine Models Power-3 VS,Power-4 VS,and
Power-5 VS …...................................................
8
4Know Your
Coatings .................................................................................................................................
9
4.1 Coating
Properties ...................................................................................................................
................
9
4.2 Your Choice of Coatings and
Viscosity ....................................................................................................
9
4.3
Technique ..............................................................................................................................................
11
5Using Pressure Pots
W
ith Turbine
Systems ….......................................................................................
12
5.1 TestingAir Pressure In Pressure
Pot …………………………………………………………………………..1
3
5.2 CleaningPressure Pot .
..........................................................................................................................
13
6 Record Of Turbine ..
................................................................................................................................
14
7 Record Of Turbine
Maintenance .............................................................................................................
14
8TurbineMaintenanceAnd
Cleaning .......................................................................................................
15
8.1 Pre-Filter
Maintenance ..........................................................................................................
.................
15
8.2 Filter
Maintenance ..................................................................................................................................
16
8.3 Annual Maintenance
..............................................................................................................................
17
9Running MultipleSprayGuns
W
ith A
Turbine ........................................................................................
17
10 Model 4500 ……………………………………………………………………………………………………..18
11 Model 4550 …..………………………………………………………...………………………………………19
12 GenuineApollo Accessories ..
................................................................................................................ 21
13
Warranty .................................................................................................................................................
24

Page 3
1 Safety
Read all instructionsand safetyprecautionsbefore operating the unit.
Indicates a hazardous situation, which, if not avoided, will result in death or serious injury.
Indicates a hazardous situation, which, if not avoided, could result in death or serious injury.
Indicates a hazardous situation, which, if not avoided, could result in minor or moderate injury.
NOTICE
Indicates a situation that could result in damage to the equipment or other property.
Risk of fire or explosion! Solvent and paint fumes can explode or ignite, causing
severe injury and property damage.
Paints and solvents containing HALOGENATED HYDROCARBONS can react
explosively with aluminum. Always check the product’s label before using these
materials in the unit.
Hazardous vapors: Paint, solvents, insecticides and other materials may be
harmful if inhaled, causing severe nausea, fainting or poisoning.
Make sure the room is well ventilated. Avoid all ignition sources, such as static electricity, sparks,
open flames, hot objects, sparks from connecting and disconnecting power
cords, and working light switches.
Follow the material and solvent manufacturers’ safety precautions and warnings.
Do not use liquids with flash points less than 100° F (38° C).
Static electricity can be produced by HVLP spraying. Make sure any electrically
conductive object being sprayed is grounded to prevent static sparking. The
sprayer is grounded to prevent static sparking. The sprayer is grounded through
the electrical cord.
Use a respirator or mask whenever there is a chance that vapors may be inhaled.
Read all instructions with the mask to ensure that the mask will provide the
necessary protection against the inhalation of harmful vapors.
Do not carry the turbine while spraying.
Keep the turbine at the maximum distance from the spraying area.

Page 4
NOTICE
•Tipping the spray gun causes the spray gun to clog. Dried spray material also clogs the pressure delivery
tube and fittings. The spray gun does not function when clogging occurs.
•When not in use, be sure to disconnect the hose and place the spray gun into the Handi-Hold™ Docking
Station on the turbine to avoid tipping.
Improper installation of the ground plug can result in the risk of electrical shock. If repair or
replacement of the plug or cord is necessary, do not connect the ground wire to either flat blade
terminal. The wire with green insulation (with or without a yellow stripe) is the
grounding wire.
1. For any question regarding proper installation of the ground plug, consult a qualified (licensed
or certified)electrician.
2. Do not modify the plug provided. If the plug does not fit the outlet, have the proper outlet
installed by a qualifiedelectrician.
3. This product is for use on a nominal 110-volt circuit and has a grounding plug that looks like
the plug in Figure 2. Make sure that the product is connected to an outlet having the same
configurationas the plug. Do not use adapters with this product.
4. If an extension cord is required, use only a three-wire extension cord that has the same
configuration as the unit cord, including the (round) ground terminal. Make sure that the
extensioncord is plugged into a properlygroundedreceptacle.
5.
W
hen using an extension cord, be sure it is in good condition and heavy enough to meet the
specifications in the chart below. If an extension cord is needed the following wire sizes must
be used.
25’ cord
(7.62m)…………………………............................
10, 12, or 14 Gauge
50’ cord
(15.24m)………………………………...................
10 or 12 Gauge
100’ cord (30.48m)…………
……………………………......
10 Gauge
Groundinginstructionsfor all countries using a 2-prongedplug configuration.
Figure 2
This product must be properly grounded. In the event of an electrical short circuit, grounding reduces
the risk of electrical shock by providing an alternate path for the electrical current.
This product is equipped with a cord that has a ground wire and an appropriate ground plug. Plug the unit into an outlet that
is properlyinstalled and grounded in accordancewith local codes and ordinances.
Safety Note: Users in countries in continental Europe and Australia and anywhere that offers a two-pronged plug must
be aware that this
configuration
does not provide grounding.

Page 5
2 TrueHVLP™ Spray Finishing Systems
CONGRATULATIONS!!
You have just purchased the finest HVLP air turbine system available. You are about to enjoy the
great benefitsof
TrueHVLP™.
Our designs are the result of many years of experiencein
manufacturing
HVLP turbine
systems, and HVLP spray guns.
W
e have
painstakingly
worked and consultedwith
professional
sprayfinishers to bring you
this versatile, well-engineeredtool.
Whether you are new to sprayfinishing, you have spray finishedbefore,or are just new to HVLP spraying;there are some
basic sprayfinishing guidelines that will help you to achieve the best results and optimum success from your new equipment.
Reading this informationcarefullyand following these simple steps will ensure that you get the best
performance
and results
from your newTrueHVLP™spraysystem.
Check the contents of your box. The followingare included:
(1) Power Series TurbineUnit
(1) TrueHVLP™SprayGun
(1) Air Hose
(1) InstructionManual
(1)
W
rench
(1) Spray Gun Lube
(1) Cleaning Brush
(1) Electric Cord
(2) Quick Coupler (1x Handi-Hold™) (1x Hose
Coupler)
2.1 How Your HVLP Turbine System Works
Your turbine system has three
components:
the turbine unit (1), spray gun (2) and air hose (3). The turbine unit, when
connectedto the correct electricalpower supply and with the on/off switch in the “on” position, provides a continuous
sourc
e of
clean, warm, dry, High VolumeLow Pressure(HVLP) air. The air hose connectsthe turbine unit to the spraygun. Air flows
throughthe hose to the nozzle of the speciallydesigned
TrueHVLP™
spraygun. Atomizationof the coating is achieved when
the air mixes with the stream of fluid passingthroughthe tip/nozzle.This low-pressureatomizationprinciple
achieves
minimum
misting(overspray)to the sprayenvironment.
2.2 How Your Spray Gun Works
Apollo offers two types of Turbine Spray Guns. The 5000 series and the 7700 series. The 5000 series spray guns are bleeder
style.
W
hen the turbine blower is turned “on”, air will
constantly
flow through the air cap. The 7700 series spray guns are non-
bleeder style.
W
hen the turbine blower is turned“on”, air will onlyflow throughthe air cap when the trigger on the spray gun
is activated or pulled back. Air also flows throughthe air feed tube to pressurizethe cup and deliverfluid to the tip/nozzle.
When the paint flow screw is opened and the trigger pulled back, fluid flows throughthe tip/nozzle mixing with the air flow

Page 6
deliveredfrom the air cap and projects a fine atomizedmist to your work piece. Spraypattern control will vary dependingon
the spray gun model. Consult your individualspraygun manualfor detailed operation and
maintenance
of your spray gun.
2.3 Preparing To Use Your HVLP Turbine System
Connect the air hose to the turbine. Pull back the spring loaded quick disconnectcouplerand insert the male connectoron
the air hose into the turbine connector. Releasethe ring. Your air hose will be locked into place. To releasethe air hose, pull
back on the spring-loaded quick couplerring with your fingers and pull. Connect other end of hose to spraygun using this
same procedure.Plug the power cord into an outlet that is properlyinstalled and groundedin accordancewith local codes
and ordinances.
NOTICE
Do not cover or enclose the turbine. It is important to draw cool/ambient air through the unit for
optimum performance. Avoid placing the turbine in a warm environment or in direct sunlight.
Do not spray in ambient temperatures above 90 degrees. If you want to be able to spray in
hotter temperatures we recommend placing a fan in front of your turbine to help it pull in cool
air.
2.4 Familiarize Yourself With Your True HVLP™ Turbine Spray Gun
Refer to your SprayGun InstructionManual for information,setup,and operation of your modelspray gun.
You are now ready to spray your coating of choice on your work piece. Good qualityresults with your
TrueHVLP™
spray
finishingequipmentare a combinationof carefulpreparationof your project,a proper spraying
environment,
a basic
knowledgeof the coatings you will be using and how these coatings work with your TrueHVLP™spray equipment.
Pressure will remain in the spray cup when unit is off. If you pull the trigger back, a stream of fluid
will flow. To prevent accidents, turn material flow screw clockwise until it is completely closed. The
trigger is now locked in the closed position.
Note: It is not necessaryto empty and clean your spray gun when you pause betweenapplications.Be sure, however, to
clean your spray gun thoroughlyat the end of your work session. Do not leave material in your spray gun overnight.Extra
caution must be taken when sprayingcoatings that have a catalyst or hardener added. These coatings can harden in your
spray gun quickly, makingcleaning difficult or impossible.Read
manufacturer’s
coating instructionsas to how much time you
have before
catalyst/hardener
begins to set up.
2.5 Get To Know Your Turbine
Handi-Hold™
Spray Gun Docking Station
Every Power Series turbine comes equipped with the Handi-Hold™Spray
Gun DockingStation (A), Apollo’s smart innovation.Store, hold or
transport your spray gun in a vertical position with no risk of it falling over.
Readyto spray when you are. Disconnecthose from spraygun and
insert couplerinto the Handi-Hold™ Spray Gun DockingStation (A). As
shown.

Page 7
Hour Use Meter
All Power Series turbines are fitted with an hour use meter (B). Use this
meter in conjunction with the Record of Turbine Maintenance at the end
of this manual. Using the hour meter will help you maintain your turbine
better and keep your system running in good condition.
Variable Speed Motor Control (VS)
The POWER VS Series turbo spray systems integrate a motor speed
control to enable you to control your atomizing pressure. To change the
pressure, rotate the dial from left to right to increase the pressure and
from right to left to decrease the pressure. The graduation marks behind
the knob do not indicate any particular pressure achieved. Do not use
these marks to replicate pressures as they will not always relate
depending on the temperature and length of use. It is always best to set
the pressure by doing some spray outs with the material you are going to
spray. Adjust the pressure to use the lowest amount of air pressure to
achieve the best atomization with that material. Check your spray pattern
for even droplet sizes around the edges of the spray out. Once your
particles are all the appropriate size you should get good results.
3 Apollo HVLP Turbines
Each
TrueHVLP™
Turbine Unit offers the finisher a maximum operatingpressure. This pressureis determinedby the size
and output of the unit you have selected.The maximum availablepressure will have a direct bearingupon the viscosityof
the fluid that you choose to spray. Atomizing pressure and fluid viscositydirectlyrelate to the
efficiency
of the equipment
operationand the quality of the results that you will achieve.
The available air volume and pressure at the air cap of the spraygun will meet the deliveryof fluid comingout of the nozzle
to create a fine mist called
atomization.
This mist travels directlyto your work piece where it blends together to form a
connectedwet film. Achievinga smooth,level surfacewill depend on the proper relationshipbetween availableatomizing
pressure, the viscosityof the coating being applied and the propertiesof the coating and the size of the needle,nozzle and
air cap used.

Page 8
3.1 Apollo Turbine Models Power-3 VS, Power-4 VS, and Power-5 VS
Model Power-3 VS
Fan Stages: 3
Sealed Pressure: 7.0 psi (0.48 bar)
Filter type: Dual (pre-filter and main filter)
Watts: 1508
Current: 110 vac - 60 hz or 240 vac - 50 hz
Weight: 23 lbs (10.4 kg)
Height: 12" (30.48 cm)
Width: 8.5" (21.6 cm)
Length: 15" (38.1 cm)
All 240-volt units shipped
All 110-volt units are
tested and certified.
Model Powe-4 VS
Fan Stages: 4
Sealed Pressure: 9.0 psi (0.62 bar)
Filter type: Dual (pre-filter and main filter)
Watts: 1568
Current: 110 vac - 60 hz or 240 vac - 50 hz
Weight: 24 lbs (10.8 kg)
Height: 12" (30.48 cm)
Width: 8.5" (21.6 cm)
Length: 15" (38.1 cm)
All 240-volt units shipped
All 110-volt units are
tested and certified.
Model Power-5 VS
Fan Stages: 5
Filter type: Dual (pre-filter and main filter)
Watts: 1858
Current: 110 vac - 60 hz or 240 vac - 50 hz
Weight: 25 lbs/11.3 kg
Height: 12" (30.48 cm)
Width: 8.5" (21.6 cm)
Length: 15" (38.1 cm)
All
EU
units
shipped
All 110-volt units are
tested and certified.
NOTE: All turbine pressures quoted are measured sealed and at the motor outlet. Actual spraying pressures will vary depending on
the model and size of the turbine.

Page 9
4 Know Your Coatings
4.1 Coating Properties
Coatings are a blend of resins and additives to create a product that will provide a protective and beautifying surface to
yo
ur
work piece. Different resins have different properties. It is important to use the correct coating to achieve a desired result.
Manufacturers of coatings can control the resin solids content, production viscosity, sheen, color, flow-out enhancement and
other properties. Some products offer ways to adjust the coating properties such as speeding up or slowing down the drying
time, adding catalysts to strengthen the molecular bond or adding flatting agents to lower the sheen. Manufacturers will
ofte
n
give some guidelines on how to thin their product for spray application. There are many different types of spray equipment in
use. Coatings manufacturers cannot address all of them. It is important for the finisher to understand the spray equipment
and to use common sense to arrive at the correct fluid viscosityto produce the best possible results with the selected coating
and the equipmentbeing used.
4.2 Your Choice of Coatings and Viscosity
Extremely thin, watery or light bodied fluids such as inks, aniline dyes and oil stains can generally be used straight from
t
he
can. RTS or Ready to Spray water-based finishing products are formulated to be used straight from the can without thinning
with a 3 stage or larger turbine. Most other coating products will need to be thinned anywhere from 10% to 50% depending
on the availableair pressureof the turbine model and the properties of the coating selected.(see chart below).
Chart A Turbine Performance
Turbine Size
Sealed Air Pressure
Coating Types
3
STAGE
7.0
PSI
Low-MediumViscosityMaterials
4
STAGE
9.0
PSI
Low-High ViscosityMaterials
5
STAGE
10.0
PSI
Low-High ViscosityMaterials
Using Latex (Emulsion) Paint
Although your turbine spray system is best suited to spray Class A Finish coatings such as lacquers, enamels, urethanes,
varnishes, waterborne and water base etc., you can spray latex (emulsion) house paint if you follow a few simple rules.
First
, it
is generally necessary to thin latex (emulsion) paint. This will vary from as little as 10% to as much as 50% depending on the
model turbine you are using and the quality of the paint used. Second, it is necessary to use a larger nozzle and needle set
in the spray gun (2.0mm or 2.5mm). It is recommended that a latex (emulsion) paint conditioner like Floetrol®, be added to
aid flow-out.These products are sold at local paint stores.
Chart B Nozzle, Needle And Air Caps For 7500 & 7700 Series Spray Guns
Tip/NeedleSize
Application
Air Cap
0.8MM (.029)
Inks, Dyes, Stains,
extremely
thin
viscosity
fluids,
W
ater based finishes
A
1.0MM (.039) All purpose,thin lacquers,thin
enamels,W
ater basedfinishes, Automotive,
Marine, Airplane finishes
B
1.3MM (.051) All purpose,thin lacquers,thin
enamels,W
ater basedfinishes, Automotive,
Marine, Airplanefinishes
B
1.5MM (.059) Catalyzed lacquers, Conversion Varnish, Primers,
W
ater-based finishes,
Automotive,Marine, Airplanefinishes, Varnish, High Viscosity
IndustrialCoatings,Urethanes, Enamel
B or C
1.8MM (.070) Catalyzedlacquers,ConversionVarnish,Primers, Automotive,Marine, Airplane
finishes, Varnish, High ViscosityIndustrialCoatings, Urethanes,Enamel
C
2.0MM (.079) Thinned Latex (Emulsion)Paint, Multispec,HeavyPrimers, Butyrate, Nitrate
Dope, C High ViscosityIndustrialCoatings
C
2.5MM (.098) Thinned Latex (Emulsion)Paint, Multispec,Solvent
adhesives,W
ax based
strippers
D

Page 10
Viscosity
Cup
Comparison
Chart
ZAHN #2 FORD # 4
16
5
17
8
18
10
19
12
20
15
22
17
24
19
27
21
30
23
34
26
37
29
41
31
49
36
58
41
66
45
74
51
82
56
Chart C Viscosity
Coating
Thin/Reduce
Lacquers
25%-50%
SandingSealer 20%-30%
Enamels
20%-40%
Stains
use from can
Acrylic Enamel 50%-60%
CatalyzedPolyurethane 10%-30%
Polyurethane's
Varnishes 20%-30%
WaterborneCoatings 00%-10%
Latex/Emulsion
Paint 10%- 40%
Note: Chart C should be used as a guide to thinningvarious coatings. Actual
reductionwill dependupon model turbine used, flow out properties of the coating
and the final visual results of the sprayed work piece.

Page 11
4.3 Technique
Like any skill, practice makes perfect. Never try to rush the spray finishing process. Learn the characteristics of the coating
you will be spraying. Build up layers of material (3-4 applications or more if necessary). Sand between coats and allow
proper drying time betweenapplications.
Some rules for effectivesprayfinishing:
1. Rememberto always keep the distance between the spray gun and the surface the same when moving across your work,
(or up and down) called a “pass”. Do not rotate or turn your wrist from side to side.
See Chart E Below
2. Move the spray gun across your work from end to end.
3. Be sure to maintain the same speedof
movement.
This ensures an even applicationof coating.
4. At the end of a “pass” always release the trigger. To continue, spray in the opposite direction and overlap your previous
coat by 1/3 to 1/2.
5.
W
hen finished you should have an even wet coat on your work. If you have dry spots you have overlappedtoo wide. If you
have heavyor wet spots, you have overlappedtoo much or sprayed too slowly.
6.
W
hen sprayinga large or
pre-assembled
piece, start at the top and work down.
7. Try to spraythe hard to reach and underneathsurfacesfirst.
Common sense and some forethought will prevent errors. Remember, that a light wet film will generally produce better
results than a heavy wet coat.
W
hen spraying a vertical surface, it is advisable to apply a thin/light “tack” coat first, followed
by a normallight wet coat. This techniquewill help prevent“runs” and “sags”.
Chart E Spray Gun
Technique
When using your SprayGun you control five variables:
1. Fluid flow.
2. Distanceof the spraygun from your work. 4”-8” (10-20cm)is average.Closer if necessary.
3. Pattern direction(vertical fan, horizontalfan and round).
4. Speed of application.
5. Fan pattern size. 7700 series with Fan Pattern Control Ring. 5000 series move the spray gun closer to or further away
from work piece.
NOTE:Items 1, 2, and 4 directly relate to each other.
Cleaning Your
TrueHVLP™
Spray Gun
Refer to your spraygun manualfor cleaning and maintenanceof your spray gun model.

Page 12
5 Using Pressure Pots with Turbine Systems
There are many advantages to using pressure pots with a turbine system. Apollo Sprayers have made this very easy with
our fluid feed systems, 4500 and 4550. Refer to the accessories section of this manual for more information on these and
other products. By removing the paint cup from the spray gun, you immediately reduce the overall weight of the spray gun
by ½. You also get a smaller tool to hold in your hand therebyallowing you to more easily
access the back of cabinets or other tight spaces where a standard cup gun would not fit.
By using a pressure pot you can spray larger quantities of material without stopping to
refill a smaller cup. This can save a lot of time on a long job where you are spraying the
same material all the time.
Using a pressure pot with any size turbine system is very easy. All you need is any size
pressure pot, a fluid hose and a small air compressor.
W
hen using a remote cup or
pressure pot, it is necessary to introduce compressed air in order to pressurize the
remote pot and move the fluid from the pot to the spray gun tip/nozzle. In general, 5PSI
(0.345 Bar) of air pressure is adequate to push most average viscosity fluids to the spray
gun nozzle. Higher pressure would only be necessary for heavier viscosity fluids or if you
are sprayingup a ladder where the fluid has to travel more than 6 feet of elevation.
Connect the black fluid hose to the fluid outlet on the top of the pressurepot. Refer to your
pressure pot instructions for the specific location of the fluid outlet. Seal the threads with Teflon tape and tighten with a
wrench (spanner) to assure no fluid leaks once you pressurize the pot. Next, connect the air line from your compressor to
the air inlet. This should be a male quick connect adjacent to the regulator and gauge. If your quick connect is the same style
as the one on the pot you can pull back the ring on the female end and insert into the male end, releasing the ring to fasten
them together. Connect the other ends of the fluid line and airline to the spray gun and air compressor respectively. Your
turbine air hose will connect as normal directly to your spray gun. Refer to your spray gun instruction manual for more
specific instructions.
Part #A4900- 2.5 gallon (10 liter) deluxe pressurepot. Part #A4600 - 2-quart (2 liter) pressure pot.

Page 13
5.1 Testing Air Pressure In Pressure Pot
It is
necessary
to test the air pressurein the pressure pot to make sure that it is appropriatefor the viscosityof material
being sprayed and the situation in which it is being sprayed. You don’t want the materialcoming out too quicklyso that you
get runs and sags, but you also don’t want it to come out too slowlyso that you are sprayingveryslowly.To test the air
pressure in the pressurepot, follow these simple instructions:
1. DO NOT turn on the turbine at this time.
2. Make sure your air hose and materialhoses are connected
appropriately
to the pressure pot.
3. Turn on your air compressor and wait until you have about 5PSI (0.345 Bar) in the pressure pot. Then, pull the trigger on
the spray gun until a stream of fluid flows from the tip/nozzle. NOTE: This may take a few minutes
depe
nding on the
length of your fluid hose.
4. Adjust the pressure on the pot regulatoruntil the fluid drops off or bends at
approximately
2-1/2 “ (6.35cm).
5. Your pot air pressureshould be correct at this point, however, if the stream bends too short then increasethe air pressure.
If the stream bends too far, then reduce the air pressure. If you need additional help, please feel free to call our
techniciansat 1-888-900-4857.
Depressurize pressure pot using safety valve when equipment will be idle for a while. This
will prevent excess fluid from remaining in fluid hose, and prevent a possible accident if the
trigger is pulled causing material to stream from the spray gun.
Always ensure that the remotepot is tightly sealed, and all gasketsare in good shape, to preventair and fluid leaks. Be sure
to flush and clean the fluid hose at the end of a work session.For smaller jobs, insert a one gallon can inside the 2.5-gallon
(10 liter) pressure pot. This will help to keep the inside of the pot cleaner.
NOTE:It may be necessary to provide extra clearanceby removingthe filter on the bottomof the pickup tube for some paint
cans to fit inside the 2.5-gallon(10 liter) pressurepot.
5.2 Cleaning Pressure Pot
Cleaning your pressure pot is important to many years of long faithful service. If you don’t clean your pressure pot it will
eventuallyget clogged up with dried material from previous jobs. Make sure you not only clean your pressure pot well, but do it
quickly after you are done spraying so as to reduce the amount of time the material has to dry. To clean your pressure pot,
follow these simple instructions:
1. Remove the lid and pour your remaining finish back into your can or if you have reduced it, into a different container for
storage.
2. Pour solvent or water (dependingon the type of finish you have used) into the pressure pot and resealthe lid.
3.
Re-pressurize
the pressurepot with air.
4. Turn on your turbine and pull the trigger on the spraygun fully open until the materialcomes out clean.
5. Removethe lid once again and pour out any unused water or solvent.
6.
W
ipe the inside of the pressurepot, pickup tube and lid with a clean rag.
7. If you use water-basedmaterials, dry the pressurepot.
8. Store in a clean dry place for use next time.

Page 14
6 Record of Turbine Use
Record Of Turbine
Use
Model
Serial
#
Date Purchased
Date
Hours Of Use Total
Hours
Turbine Recommended Maintenance: Clean and/or change pre-filters and/or cartridge filters every 50 hours or when
necessary.See AccessoriesPage for appropriatefilter
replacement
for your model.
7 Record of Turbine Maintenance
Record Of Turbine
Maintenance
Date
Maintenance
Performed

Page 15
8 Turbine Maintenance and Cleaning
Always unplug your turbine from the main electrical supply before doing any maintenance or
repairs.
After Each Use:
Your Apollo turbine system requires very little maintenance. The turbine motor has sealed bearings that are lubricated for
life. The only maintenance that you will need to perform is checking, cleaning and replacing your filters and pre-filters as
required. You should check your filters every 10 hours and replace them as necessary. It is very important that your motor has cool,
clean air to operate efficiently. If you maintain your filters and prefilters well, you will enjoymany years of long servicefrom your
turbine motor.
NOTICE
Always use genuine Apollo filters and pre-filters. Other types of filters and pre-filters may
prevent proper air flow to the motor, resulting in premature motor failure and voiding your
warranty.
8.1 Pre-Filter Maintenance
We recommend that you remove your pre-filters after each use. To remove the pre-filters: push your finger between the filter
(1) and pre-filter (2) until you can curl it up and pull the pre-filter off, rotating your finger around the pre-filter as you pull. Do
not pull hard as you will break the glue line on the pre-filter. Make sure you check both pre-filters as they can get dirty at
different intervals. If they appear to be a little dirty or clogged, you can wash them out using a mild soap and warm water. If
they are not cleanable you need to install new pre-filters.
To reinstall the pre-filters, hold one in both hands and apply the top first, moving your fingers around the
insid
e as you slide it
back over the filter cartridge from top to bottom. NEVER operate your turbine without both filters and pre-filters installed and
clean.

Page 16
8.2 Filter Maintenance
Visually check your filters every 10 hours or when you remove your pre-filters for cleaning. Check for accumulatedmaterial in
the filter element. If you suspect they may be dirty, or if you can see material building up, don’t take a chance, remove the
filter and hold it up to the light.
To remove your filters, remove two dome nuts (1) and pull filter plate (2) off. Filter plate can hang up on the threads so make
sure you pull it off straight. Removefilter (3). If filter is stuck to the side of the case, gentlytap them with your hand.
To check your filters, hold them up to a light, similar to your car air intake filter. If you cannot see light through more than
50% of the filter, replacefilter element.
NOTICE
Filter element may be damaged if more than 50 PSI of air pressure is used to blow out filter
element.
If they appear to be dirty, you can tap them gently on a flat surface to remove any debris. If you have compressed air
available, you can also blow them off with air. If you use compressed air to clean your filters, make sure you blow the air
from the inside out and never use more than 50 PSI or this will damagethe filter element.
To reinstall the filters, reverse the instructions above. Make sure that you line the filter up with the filter plate first, this will
help to keep it straight when replacing the dome nuts.

Page 17
8.3 Annual Maintenance
Check carbonbrushes at least once a year or every150 hours, whichevercomes first. To check your carbon brushes,
consult with an authorized Apollo repair facility.
9 Running Multiple Spray Guns with A Turbine
All current Apollo TurbineModels have one air hose outlet on the side of the unit and are designed to run one spraygun.
Thesemodels are equippedwith an internalair relief valve to
accommodate
a non-bleedstyle spraygun (Apollo Model
7500 or 7700).
It is possibleto run a 4 or 5-stageturbine system with two spray guns at the same time by installingan optional“Y”
Connector,to the turbine outlet port. It is important to note that if the “Y” Connectoris installedand onlyone spray gun is
operated,the 2nd outlet must be cappedor closed so that
performance
to the single spray gun will not be affected.To install
a “Y” connectorfollow these instructions:
1. Unscrewthe femalequick connect from the air outlet located on the side of your turbine.
2. Screw on the “Y” connector.Make sure the “Y” is sideways so you can easily attach your hoses.
3. Screw the female quick connect you removed from your turbine onto the “Y” connector. If you plan on using two spray
guns right away, then make sure you have a 2nd quick connect installedon the other side of the “Y” connector.
4. You are now ready to connect your air hoses and sprayguns.
Remember,we do not
recommend
using the “Y” connector with turbines smaller than 4 or 5-stages. This is due to the power
that each model has. The more stages you have the more power you have.
W
hen you are runningtwo spray guns on
a single
turbine you are splittingthe air power that turbine has.
W
hile you will not divide it equally, you will reduce it considerably,so
make sure you do some test areas before you start on your project.
“Y” Connector with single hose and cap “Y” Connector with two hoses

10
Model 4500
15
Page
17

Page 18
Diagram # Part # Description Quantity
1A4501Compressor Deck 1
2A4198110v Mini Compressor Unit 1
3A43201/4" X 20 X 1/2" Hex Bolt Plated .5. 12
4A43001/4" SAE F/W Plated Washer16
5A43081/4" X 20 Hex Nuts Plated 4
6A9016Rubber Foot 4
7A4998Pressure Regulator 1
8A45031/8" Male NPT X 1/4" Male Hose Barb 90°1
9A4033Air Line Hose Clip S.S. 2
10 A21161/4" Air Hose, Per Foot 3
11 A21191/4" X 1/4" Female Swivel Barb1
12 A4026Quick Connect Female With 1/4" Male Thread1
13 A43101/4" X 20 Cap Nut Plated 8
14 A4502Pressure Pot Support Bracket 1
15 A4613Rubber Edge Trim 2
16 A42002 Quart Pressure Pot W/Single Regulator 1

Page 19
11 Model
4550
32
W
I
R
ING
DIAGRAM
MODEL4550
6
This manual suits for next models
5
Table of contents
Other Apollo Paint Sprayer manuals
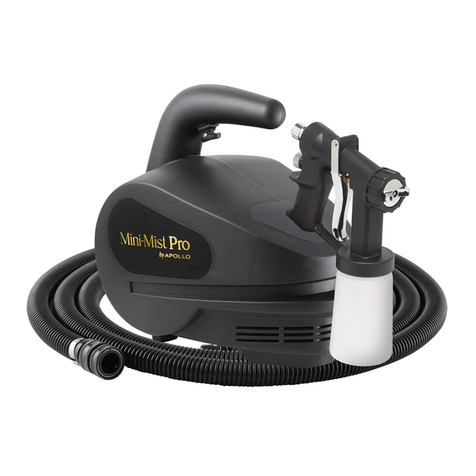
Apollo
Apollo Mini-Mist PRO User manual
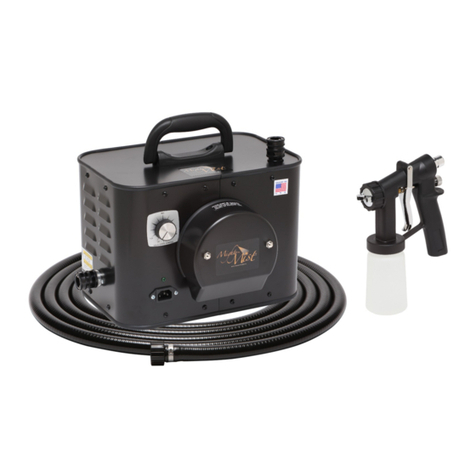
Apollo
Apollo Mighty-Mist T6000 User manual
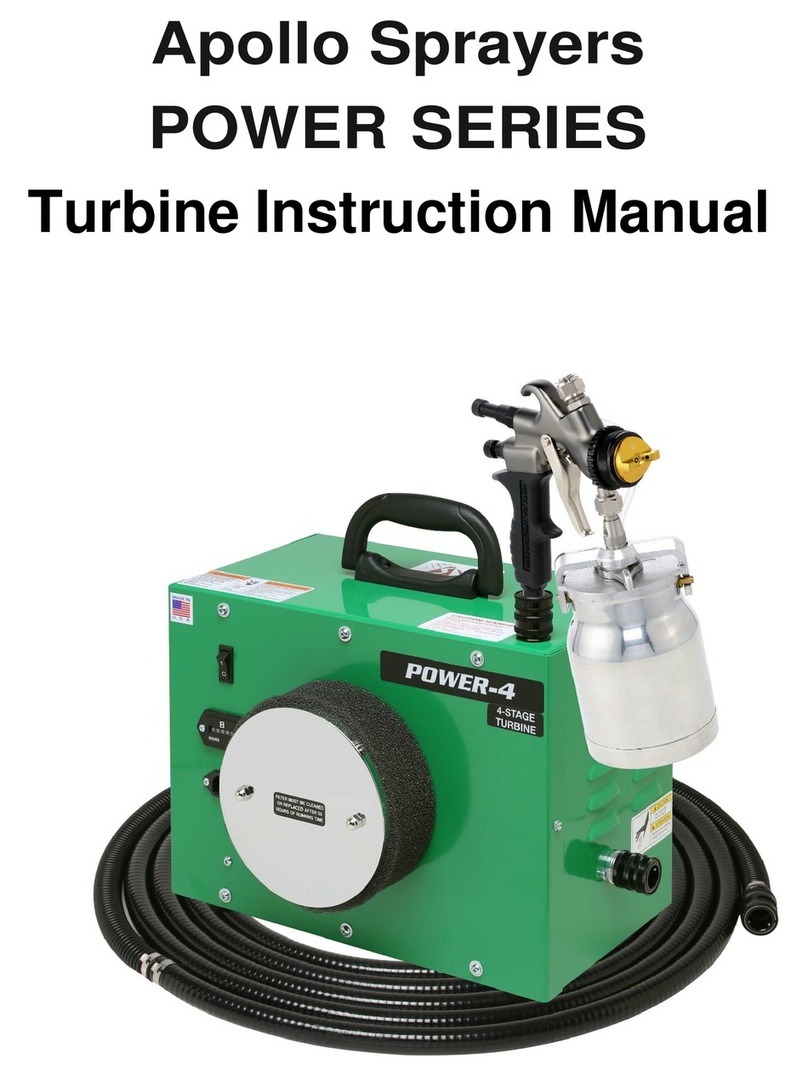
Apollo
Apollo POWER SERIES User manual
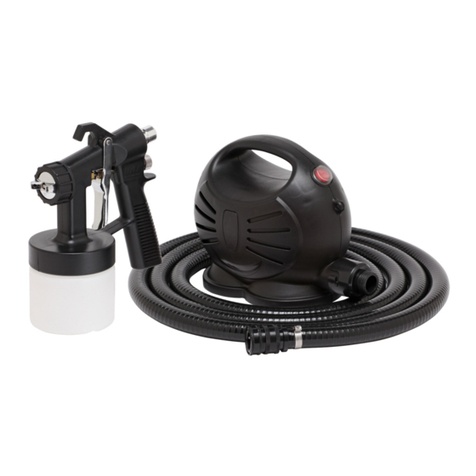
Apollo
Apollo Happy-Mist User manual
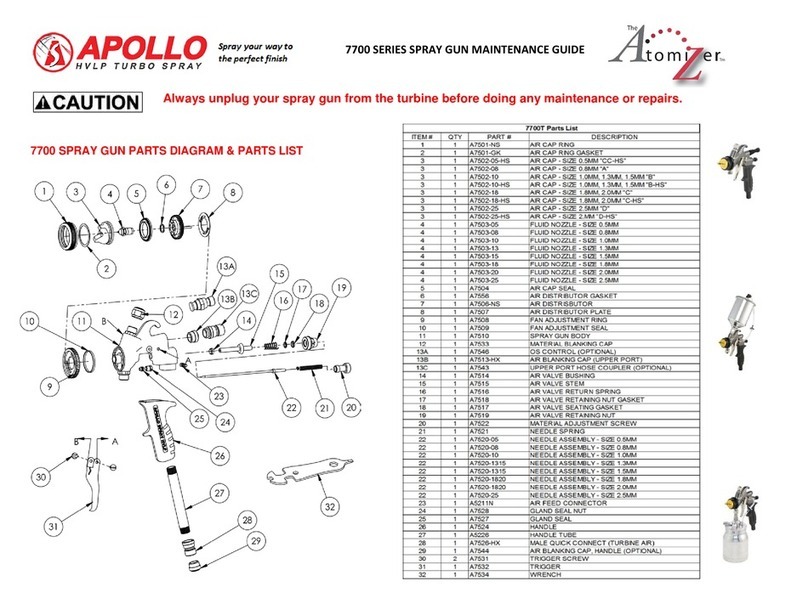
Apollo
Apollo Atomizer 7700 Series Operating manual
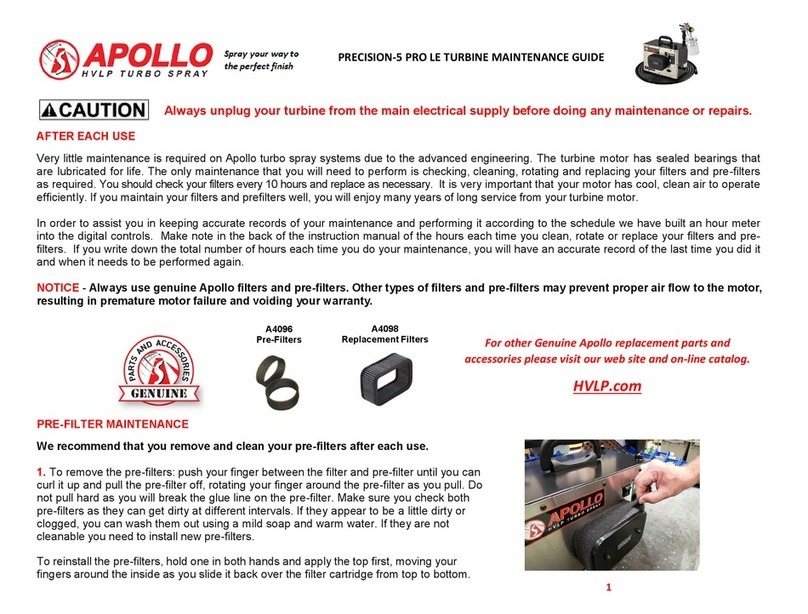
Apollo
Apollo PRECISION-5 PRO PLUS Operating manual

Apollo
Apollo Mini-Mist PRO Deluxe T100 User manual