Asco 7000 Series User manual

7000 Series Medium Voltage Transfer Switch User Manual
Version
V1.0
Revision Date
May 12, 2016
BOM Code
31013291
Emerson Network Power provides customers with technical support. Users may contact the nearest
Emerson Network Power sales office or service center.
Copyright © 2016 by Emerson Network Power Co., Ltd.
All rights reserved. The contents in this document are subject to change without notice.
Emerson Network Power Co., Ltd.
Block B2, Nanshan I Park, No.1001 Xueyuan Road, Nanshan District, Shenzhen, 518055, P.R. China
E-mail: custo[email protected]m


Contents
Chapter 1 Overview..................................................................................................................................................... 1
1.1 Model Description.......................................................................................................................................... 1
1.2 Appearance................................................................................................................................................... 2
1.3 Product Composition...................................................................................................................................... 2
1.4 Climate classes.............................................................................................................................................. 3
Chapter 2 Installation And Operation............................................................................................................................ 4
2.1 Installation..................................................................................................................................................... 5
2.1.1 Supporting Structure ........................................................................................................................... 5
2.1.2 Mounting............................................................................................................................................. 5
2.1.3 Testing Power Conductors .................................................................................................................. 5
2.1.4 Line Connections ................................................................................................................................ 5
2.1.5 Engine-Generator Control Connections................................................................................................ 5
2.1.6 Auxiliary Circuits ................................................................................................................................. 6
2.2 Operation ...................................................................................................................................................... 6
2.2.1 Configuration of Shipped ATS.............................................................................................................. 6
2.2.2 Energizing the Normal Source, Setting Automatic Operation Mode....................................................... 6
2.2.3 Controller Settings for MV ATSs.......................................................................................................... 7
2.2.4 ATS Electrical Operation ..................................................................................................................... 8
2.2.5 ACTS Electrical Operation................................................................................................................... 9
2.2.6 ADTS Electrical Operation..................................................................................................................10
Chapter 3 Troubleshooting..........................................................................................................................................11
3.1 Troubleshooting for MV ATS .........................................................................................................................11
3.2 Troubleshooting for MV ACTS.......................................................................................................................12
3.3 Troubleshooting for MV ADTS.......................................................................................................................13


Chapter 1 Overview 1
ASCO 7000 Series Medium Voltage Transfer Switch User Manual
Chapter 1 Overview
TheASCO 7000 Series medium voltage transfer switch meets GB3906 and IEC62271-200 standards.
This chapter will introduce the model description, appearance, product composition, and application environment, as
well as the mechanical and electrical parameters of this transfer switch.
1.1 Model Description
Taking E7ADTC03125085XL as an example, the model description is shown in Table 1-1.
Table 1-1 Model Description and Order Information
E
7
A
D
T
C
0
3
1250
8
5
X
L
①
②
③
④
⑤
⑥
⑦
⑧
⑨
⑩
⑪
⑫
⑬
Description
①
Short-circuit breakring Current(1)
A
25kA
E
31.5kA
B
40kA
②
7000 Series Medium Voltage
Automatic Transfer Switch
7
7000 Series Medium Voltage Automatic Transfer Switch
③
Operation Type
A
Automatic
④
Transition Type
Blank
Open
C
Closed
D
Delayed
⑤
Construction
T
Transfer
⑥
Device Type
C
GB/IEC MV Dual CB Transfer Switch
⑦
Neutral Code
0
None
⑧
Poles
3
3
⑨
Rated Current Code(2)
0630
630A
1250
1250A
2000
2000A
2500
2500A
⑩
Rated Voltage Code(3)
3
3.3kV
4
6kV
6
6.6kV
8
10kV
v
11kV
2
22Kv
O
Other
⑪
Controller
5
GROUP 5
⑫
Accessory
0
None
X
Per Accessory Number
Z
Per Specification
⑬
Enclosures
L
IP4X
(1) 24kV class systems are only available in 25kAIC and 31.5kAIC configurations.
(2) 24kV class systems are only available in 1250Aand 2000Aconfigurations.
(3) When the nominal system voltage is 3.3kV, 6kV or 6.6kV, the rated voltage of the switchgear is 7.2kV;
When the nominal system voltage is 10kV or 11kV, the rated voltage of the switchgear is 12kV;
When the nominal system voltage is 20kV or 22kV, the rated voltage of the switchgear is 24kV.

2 Chapter 1 Overview
ASCO 7000 Series Medium Voltage Transfer Switch User Manual
1.2 Appearance
The appearance of the transfer switch is shown in Figure 1-1.
Figure 1-1 Appearance
(
Master section shown on right
)
1.3 Product Composition
7000 Series medium voltagetransfer switch includes one normal source incoming switchgear, one emergency source
incoming switchgear and on master outgoing switchgear. Typical 7000 Series MVATS with location of major
components (1250Amps) are shown in Figure 1-2.
Figure 1-2 Typical 7000 Series MV ATS with location of major components (1250A, Load section shown on right
)
Normal Source Circuit
Breaker
Normal Source Circuit
Breaker Control Switch
Emergency Source
Circuit Breaker
Emergency Source
Circuit Breaker Control
Switch
Transfer control
& lights
Controller
Transfer Switch
control
Potential Indicator
Temperature & Humidity
Controller
Source 1 Incoming
Source 2 Incoming
Load Outgoing

Chapter 1 Overview 3
ASCO 7000 Series Medium Voltage Transfer Switch User Manual
1.4 Climate classes
Ambient air temperture: -5°C to +40°C
Site altitude: 1000m and below
Relative humidity: max.95% for 24 hours, max. 90% for one month.
Earthquake intensity is smaller than magnitude 8.
Site without fire, blast danger, serious dirt and severe shocks.
The climate classes are classified according to IEC 60721-3-3 and GB 3906-2006.

4Chapter 2 Installation And Operation
ASCO 7000 Series Medium Voltage Transfer Switch User Manual
Chapter 2 Installation And Operation
DANGER
!
DANGER is used in this manual to warn of a hazard situation which, if not avoided, will result in death or serious
injury.
WARNING
!
WARNING is used in this manual to warn of a hazardous situation which, if not avoided, could result death or serious
injury.
CAUTION
!
CAUTION is used in this manual to warn of a hazardous situation which, if not avoided, could result in minor or
moderate injury.
NOTICE
NOTICE is used in this manual to bring attention to an incorrect application which, if not avoided, could result in
improper operation.
An experienced licensed electrician must install theATS.
Each automatic transfer switch contains a rating label (name plate) to define the rate load (Ampere rating). Refer to
the label on the transfer switch for specific values.
DANGER
!
Do not exceed the values on the rating label.
Exceeding the rating can cause personal injury or serious equipment damage.

Chapter 2 Installation And Operation 5
ASCO 7000 Series Medium Voltage Transfer Switch User Manual
2.1 Installation
The ASCO 7000 Series Medium-Voltage Automatic Transfer Switch (ATS) is factory wired and tested.
Refer to the manual from the manufacturer of the metal-clad switchgear for section handling, installation, power
connections, and testing.
2.1.1 Supporting Structure
The supporting foundation for the enclosure must be level and straight. Refer to the applicable enclosure outline
drawing included with the transfer switch for all mounting details including door opening space.
2.1.2 Mounting
Refer to the outline and mounting diagram and mount the automatic transfer switch according to details and
instructions shown on the diagram.
CAUTION
!
Protect the transfer switch from construction grit and metal chips to prevent malfunction or shortened life of the
transfer switch.
2.1.3 Testing Power Conductors
Do not connect the power conductors to the transfer switch until they are tested. Installing power cables in conduit,
cable troughs, and ceiling-suspended hangers often requires considerable force. The pulling of cables can damage
insulation and stretch or break the conductor’s strands. For this reason, after the cables are pulled into position, and
before they are connected, they should be tested to verify that they are not defective or have been damaged during
installation.
2.1.4 Line Connections
Refer to the wiring diagram provided with the transfer switch. All wiring must be made in accordance with the National
Electrical Code and local codes.
DANGER
!
De-energize all conductors, open all circuit breakers, and rack out all voltage transformers before making any
connections. De-energize any UPS, station battery system, or any similar system providing standby control power.
Be sure that the Normal and Emergency line connections are in proper phase rotation.
Place the engine generator starting control in the OFF position.
Make sure engine generator is not in operation.
2.1.5 Engine-Generator Control Connections
All customer connections, including the engine control contact connections, are located on terminal block TB. This terminal
block is located on the interior left side of the control section. Refer to the wiring diagram provided with the automatic transfer
switch. Connect the engine start wires to the appropriate terminals. See Figure 2-1 and Table 2-1.
Table 2-1 Engine-generator control contacts
When normal source fails
TB terminals
contact closes
TB : 1 and TB : 2
contact opens
TB : 1 and TB : 3
Figure 2-1 Customer terminal block TB in controls section
engine -generator
control
connections

6Chapter 2 Installation And Operation
ASCO 7000 Series Medium Voltage Transfer Switch User Manual
2.1.6 Auxiliary Circuits
Connect auxiliary circuit wires to appropriate terminals on terminal block TB as shown on the wiring diagram provided
with the automatic transfer switch.
2.2 Operation
2.2.1 Configuration of Shipped ATS
The MVATS is shipped with the circuit breakers and controls in the following state:
SOURCE 1 SECTION, check these items
Normal source circuit breaker (CBN)
In the OPEN position with the closing spring discharged.
Normal source circuit breaker control switch (53CBN)
In the NAT (normal after trip) position (green target displayed on control switch if the power of control circuit
energized)
SOURCE 2 SECTION, check these items
Emergency source circuit breaker (CBE)
In the OPEN position with the closing spring discharged.
Emergency source circuit breaker control
switch (53CBE)
In the NAT (normal after trip) position
(green target displayed on control switch
if the power of control circuit energized)
LOAD SECTION, check this item
Transfer Switch Auto-Man selector switch
(53AM) in the MAN (manual) position.
Figure 2-2 Location of control switches
Figure 2-3 Control switches
2.2.2 Energizing the Normal Source, Setting Automatic Operation Mode
After the MVATS is installed, the Normal source can be energized. Then the controls can be set for automatic
(standby) operation. The Normal and Emergency sources must be available. Follow this procedure:
1. LOAD SECTION –Controls, check these items
The transfer control indicator lights Normal Source Accepted and TS Locked Out should be on.
The controller display should show that the transfer switch is Locked Out.
2. SOURCE 1 SECTION - Circuit Breakers, check these items
Normal source circuit breaker control switch should indicate that the circuit breaker is OPEN (green light).
3. SOURCE 2 SECTION - Circuit Breakers, check these items
Emergency source circuit breaker control switch should indicate that the circuit breaker is OPEN (green
light).
Green
Red
Breaker control
target indicator
Green=tripped
Red=closed
Emergency source
circuit breaker
control switch
Normal source
circuit breaker
control switch
Transfer Switch
Auto-Man selector
switch

Chapter 2 Installation And Operation 7
ASCO 7000 Series Medium Voltage Transfer Switch User Manual
4. Energizing procedure
On Control Section, turn the Transfer Switch Auto-Man selector switch to the AUTO (automatic) position.
On CB Section, turn the Normal source circuit breaker control switch to CLOSE position (red target
window).
On CB Section, turn the Emergency source circuit breaker control switch to the CLOSE position (red
target).
On Control Section, press the transfer controlsAlarm Reset button. Normal source circuit breaker should
close.
The Normal source CB control switch should indicate that the circuit breaker is CLOSED (red light).
TheATS is now in an automatic (standby) operating mode. Proceed to transfer test.
2.2.3 Controller Settings for MV ATSs
Refer to the manual from the manufacturer of the metal-clad switchgear for section handling, installation, power
connections, and testing.
The Group 5 Controller is factory set for medium voltage operation. These are the special settings:
1. Controller Voltage Jumper Blocks
The control voltage is typically stepped down to 120V, so the eight jumper blocks are factory arranged
horizontally for 120 V input.
2. Controller Menu Settings
ATS Information Rating is 1200, 2000, or 3000 A. TheATS information rating setting is 1200A, 2000A, or 3000A.
ATS Information is Circuit Breaker Non Bypass. The ATS information type setting is BRKR NBPS.
3. Lock-Out Relay (optional)
If an optional protective relay (device) is ordered for the normal and/or emergency source circuit breaker, a
Lock-Out Relay (LOR) is provided on the appropriate circuit breaker compartment door. The LOR responds to a
signal from a protective relay and in turn trips the appropriate circuit breaker. The LOR locks out the circuit
breaker until the fault is cleared and the protective relay and LOR has been reset. Ared light and orange window
shows tripped.
Figure 2-4 Lock-Out Relay
What to do if a circuit breaker trips
1. Check the protective relay and determine the cause of the trip. Refer to device’s instructions. After fault is cleared,
reset the protective relay.
2. Reset the Lock-Out Relay by turning it to RESET.
3. Turn the Breaker Control switch to CLOSE.
4. Press the Alarm Reset button. The circuit breaker should close if its connected source is selected by the controller
to serve the load.
Status window
black=ready to respond
orange=trip signal sent to CB
Lock-Out Relay status lights
green=ready to respond
red=trip signal sent to CB

8Chapter 2 Installation And Operation
ASCO 7000 Series Medium Voltage Transfer Switch User Manual
2.2.4 ATS Electrical Operation
Figure 2-5 7ATS controls and indicators.
ATS Electrical Operation
This procedure checks the electrical operation of the
automatic transfer switch. See Figure 2-5.
Transfer Test
Both normal and emergency sources must be available
and the emergency source generator (if used) must be
capable of being started in this procedure.
Perform the steps at the right. Observe the status lights.
■ Black square means light is on.
□ White square means light is off.
1
The Transfer Switch Connected
to Normal and Normal Source
Accepted lights should be on.
2
Turn and hold the Transfer
Control switch clockwise to
Transfer Test until the engine
starts and runs (within 15 sec.).
The Emergency Source
Accepted light should come on.
3
The transfer switch will operate
to the Emergency position after
Feature 2B time delay.
The Transfer Switch Connected
to Emergency light should come
on and Load Connected to
Normal light goes off.
4
The transfer switch will operate
back to the Normal position after
Feature 3Atime delay.
For immediate retransfer turn
the Transfer Control counter-
clockwise to Retransfer Delay
Bypass.
The Transfer Switch Connected to Normal light
should come on; the Transfer Switch Connected
to Emergency light should go off.
5
The engine-generator will stop
after the Feature 2E time delay
(unloaded running engine cool-
down). The Emergency Source
Accepted light should go off.

Chapter 2 Installation And Operation 9
ASCO 7000 Series Medium Voltage Transfer Switch User Manual
2.2.5 ACTS Electrical Operation
Figure 2-6 7ACTS controls and indicators.
ACTS Electrical Operation
This procedure checks the electrical operation of the
automatic closed-transition transfer switch. See Figure
2-6.
Transfer Test
Both normal and emergency sources must be available
and the emergency source generator (if used) must be
capable of being started in this procedure.
Perform the steps at the right. Observe the status lights.
■ Black square means light is on.
□ White square means light is off.
** If you do not want closed-transition transfer, press the
Closed Transition Bypass pushbutton while the
controller display shows Waiting for In-Sync. This action
causes open-transition (momentary load interruption)
transfer to the opposite source, if conditions permit. Also
refer to the Group 5 Controller User’s Guide 381333-126.
1
The Transfer Switch Connected
to Normal and Normal Source
Accepted lights should be on.
2
Turn and hold the Transfer
Control switch clockwise to
Transfer Test until the engine
starts and runs (within 15 sec.).
The Emergency Source
Accepted light should come on.
3
The transfer switch will operate
to the Emergency position after
Feature 2B time delay. The
Transfer Switch Connected to
Emergency light should come on
and Load Connected to Normal
light goes off. You might see and
hear the brief overlap transfer.**
4
The transfer switch will operate
back to the Normal position after
Feature 3Atime dely.
For immediate retransfer turn
the Transfer Control counter-
clockwise to Retransfer Delay
Bypass.
The Transfer Switch Connected to Normal light
should come on; the Transfer Switch Connected
to Emergency light should go off.
5
The engine-generator will stop
after the Feature 2E time delay
(unloaded running engine
cool-down). The Emergency
Source Accepted light should go
off.

10 Chapter 2 Installation And Operation
ASCO 7000 Series Medium Voltage Transfer Switch User Manual
2.2.6 ADTS Electrical Operation
Figure 2-7 7ADTS controls and indicators.
ADTS Electrical Operation
This procedure checks the electrical operation of the
automatic delayed-transition transfer switch. See Figure
2-7.
Transfer Test
Both normal and emergency sources must be available
and the emergency source generator (if used) must be
capable of being started in this procedure.
Perform the steps at the right. Observe the status lights.
■ Black square means light is on.
□ White square means light is off.
1
Turn and hold the Transfer
Control switch clockwise to
Transfer Test until the engine
starts and runs (within 15 sec.).
The Emergency Source
Accepted light should come on.
2
CBN opens and the Transfer
Switch Connected to Normal
light should go off and the Load
Disconnect Active light should
come on. Both CBN and CBE
contacts are now open.
3
After the delay transition time
delay, CBE closes. The
Transfer Switch Connected to
Emergency light should come on
and the Load Disconnect Active
light goes off.
4
CBN closes after Feature 3A
time delay. For immediate
retransfer turn the Transfer
Control counter-clockwise to
Retransfer Delay Bypass. The
Transfer Switch Connected to
Normal light should come on;
the Transfer Switch Connected
to Emergency light should go off.
5
The engine-generator will stop
after the Feature 2E time delay
(unloaded running engine
cool-down). The Emergency
Source Accepted light should go
off.

Appendix 2 11
ASCO 7000 Series Medium Voltage Transfer Switch User Manual
Chapter 3 Troubleshooting
3.1 Troubleshooting for MV ATS
DANGER
!
Hazardous voltage capable of causing shock, burns, or death is used in the switch. Do not touch the power or load
terminal of the transfer switch!
Problem
Check in Numerical Sequence
1 Operation
2 Gen-Set
3 Voltage on
Display
Gen-Set does not start
when the Transfer
Control switch is turned
and held in Transfer Test
position or when the
normal source fails.
Hold Transfer Test switch 15
seconds or the outage must
be long enough to allow for
Feature 1C time delay plus
engine cranking and starting
time.
Starting control must be in
the automatic position.
Batteries must be charged
and connected. Check
wiring to engine starting
contacts on customer
terminal block TB. Verify on
the controller that small
plug J3 is connected to
receptacle P3.
Transfer switch does not
transfer the load to the
emergency source after
the engine-generator set
starts.
Wait for Feature 2B time
delay to time out (if used).
Generator output circuit
breaker must be closed.
Generator frequency must
be at least 95% of nominal
(57 Hz for a 60 Hz system.)
Emergency
voltage on
controller display
should read at
least 90% of
nominal phase to
phase voltage.
Transfer switch does not
transfer the load to normal
source when normal
returns or when the
Transfer Control switch is
released.
Wait for Feature 3A time
delay to time out (if used).
Normal voltage on
controller display
should read at
least 90% of
nominal phase to
phase voltage.
Engine-generator set does
not stop after load
retransfer to the normal
source.
Wait for Feature 2E time
delay to time out (if used).
Starting control must be in
the automatic position.
Circuit breaker trips (on an
ATS without protective
relay)
Check the controller display for error messages and determine the cause of the
trip. After the fault is cleared, turn the Breaker Control switch to CLOSE. Press
the Alarm Reset button.
The CB should close.
Circuit breaker trips (on an
ATS with a protective
relay)
Check the protective relay and determine the cause of the trip (refer to device’s
instructions). After fault is cleared, reset the protective relay. Then reset the
Lock-Out Relay by turning it to RESET. Next turn the Breaker Control switch
to CLOSE. Press the Alarm Reset button.
The CB should close.
Refer to the Group 5 Controller User’s Guide 381333-126 for ATS status display messages, time delays, pickup &
dropout settings, & adjustments.

12 Appendix 1
ASCO 7000 Series Medium Voltage Transfer Switch User Manual
3.2 Troubleshooting for MV ACTS
DANGER
!
Hazardous voltage capable of causing shock, burns, or death is used in the switch. Do not touch the power or load
terminal of the transfer switch!
Problem
Check in Numerical Sequence
1 Operation
2 Gen-Set
3 Voltage on
Display
Gen-Set does not start
when the Transfer
Control switch is turned
and held in Transfer Test
position or when the
normal source fails.
Hold Transfer Test switch 15
seconds or the outage must be
long enough to allow for
Feature 1C time delay plus
engine cranking and starting
time.
Starting control must be in
the automatic position.
Batteries must be charged
and connected. Check
wiring to engine starting
contacts on customer
terminal block TB. Verify on
the controller that small
plug J3 is connected to
receptacle P3.
Transfer switch does not
transfer the load to the
emergency source after
the engine-generator set
starts.
Wait for Feature 2B time delay
to time out (if used).
Generator output circuit
breaker must be closed.
Generator frequency must
be at least 95% of nominal
(57 Hz for a 60 Hz system.)
Emergency
voltage on
controller display
should read at
least 90% of
nominal phase to
phase voltage.
Transfer switch does not
transfer the load to
normal source when
normal returns or when
the Transfer Control
switch is released.
Wait for Feature 3A time delay
to time out (if used).
Normal voltage on
controller display
should read at
least 90% of
nominal phase to
phase voltage.
Engine-generator set
does not stop after load
retransfer to the normal
source.
Wait for Feature 2E time delay
to time out (if used).
Starting control must be in
the automatic position.
Failure to Synchronize
light comes on.
Conditions of normal or emergency sources not suitable for closed transition
transfer. Recheck voltage and frequency of both sources. Press Alarm Reset.
Extended Parallel Time
light comes on.
CBN and CBE contacts are closed longer than setting in the controller. Open the
disconnected source CB, then call ASI for assistance.
TS Locked Out light
comes on.
Transfer lockout operation has occurred; transfer switch is disabled from automatic
operation. Open the disconnected source circuit breaker, then call ASI.
Circuit breaker trips (on
an ATS without protective
relay)
Check the controller display for error messages and determine the cause of the
trip. After the fault is cleared, turn the Breaker Control switch to CLOSE. Press
the Alarm Reset button.
The CB should close.
Circuit breaker trips (on
an ATS with a protective
relay)
Check the protective relay and determine the cause of the trip (refer to device’s
instructions). After fault is cleared, reset the protective relay. Then reset the
Lock-Out Relay by turning it to RESET. Next turn the Breaker Control switch to
CLOSE. Press the Alarm Reset button.
The CB should close.
Refer to the Group 5 Controller User’s Guide 381333-126 for ATS status display messages, time delays, pickup &
dropout settings, & adjustments.

Appendix 2 13
ASCO 7000 Series Medium Voltage Transfer Switch User Manual
3.3 Troubleshooting for MV ADTS
DANGER
!
Hazardous voltage capable of causing shock, burns, or death is used in the switch. Do not touch the power or load
terminal of the transfer switch!
Problem
Check in Numerical Sequence
1 Operation
2 Gen-Set
3 Voltage on
Display
Gen-Set does not start
when the Transfer
Control switch is turned
and held in Transfer Test
position or when the
normal source fails.
Hold Transfer Test switch 15
seconds or the outage must
be long enough to allow for
Feature 1C time delay plus
engine cranking and starting
time.
Starting control must be in
the automatic position.
Batteries must be charged
and connected. Check
wiring to engine starting
contacts on customer
terminal block TB. Verify on
the controller that small
plug J3 is connected to
receptacle P3.
Transfer switch does not
transfer the load to the
emergency source after
the engine-generator set
starts.
Wait for Feature 2B time
delay to time out (if used).
Generator output circuit
breaker must be closed.
Generator frequency must
be at least 95% of nominal
(57 Hz for a 60 Hz system.)
Emergency
voltage on
controller display
should read at
least 90% of
nominal phase to
phase voltage.
Transfer switch does not
transfer the load to normal
source when normal
returns or when the
Transfer Control switch is
released.
Wait for Feature 3A time
delay to time out (if used).
Normal voltage on
controller display
should read at
least 90% of
nominal phase to
phase voltage.
Engine-generator set does
not stop after load
retransfer to the normal
source.
Wait for Feature 2E time
delay to time out (if used).
Starting control must be in
the automatic position.
Load Disconnect Active
light comes on.
Wait for load disconnect time
delay to time out.
Explanation: Transfer switch in delayed-transition
transfer mode. Load disconnect time delay is
adjustable from 0 to 5 min. 59 sec.
Load Disconnect Active
light stays on longer than 6
min..
Check load disconnect time
delay setting. Call ASI.
Explanation: Transfer switch contacts are open
longer than 5 min. 59 sec (maximum setting).
Load remains disconnected.
Circuit breaker trips (on an
ATS without protective
relay)
Check the controller display for error messages and determine the cause of the
trip. After the fault is cleared, turn the Breaker Control switch to CLOSE. Press
the Alarm Reset button.
The CB should close.
Circuit breaker trips (on an
ATS with a protective
relay)
Check the protective relay and determine the cause of the trip (refer to device’s
instructions). After fault is cleared, reset the protective relay. Then reset the
Lock-Out Relay by turning it to RESET. Next turn the Breaker Control switch
to CLOSE. Press the Alarm Reset button.
The CB should close.
Refer to the Group 5 Controller User’s Guide 381333-126 for ATS status display messages, time delays, pickup &
dropout settings, & adjustments.
Other manuals for 7000 Series
4
Table of contents
Other Asco Switch manuals
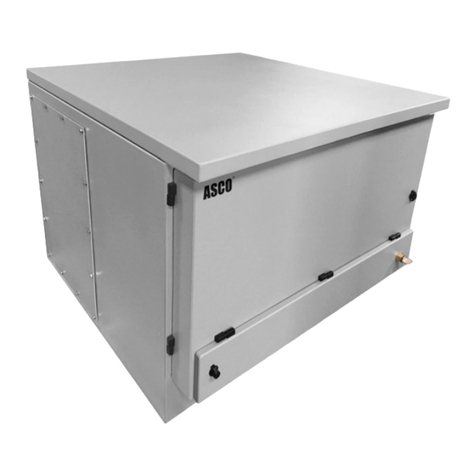
Asco
Asco Series 300 Installation guide

Asco
Asco 940 User manual

Asco
Asco 230 Series User manual
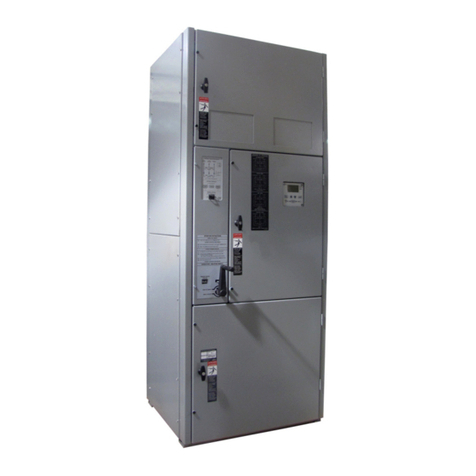
Asco
Asco J 4000 Series User manual
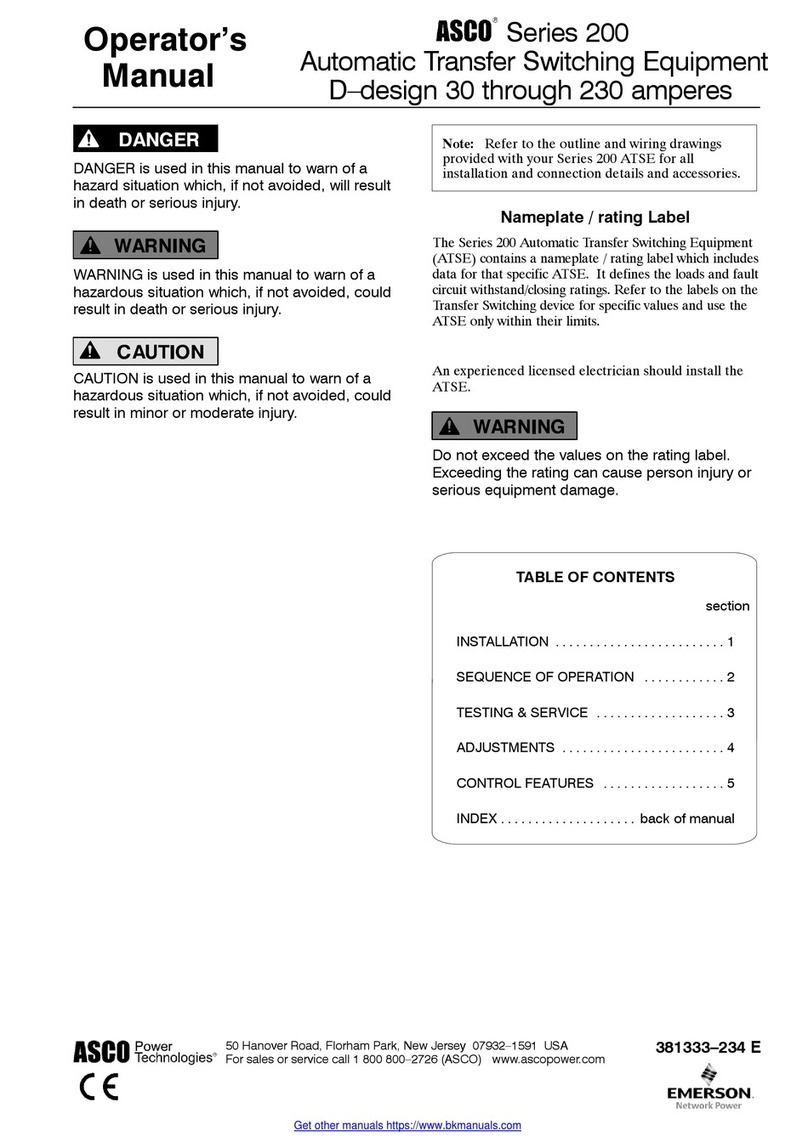
Asco
Asco 200 Series User manual
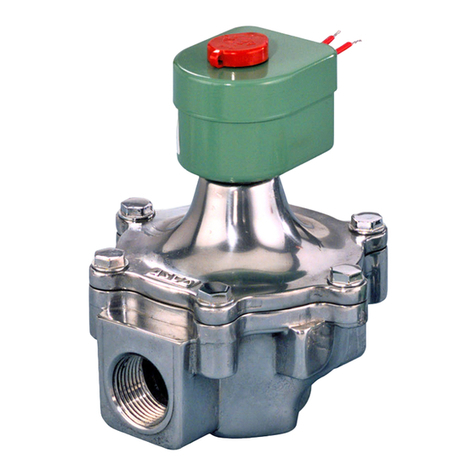
Asco
Asco 8215 Installation and operating instructions
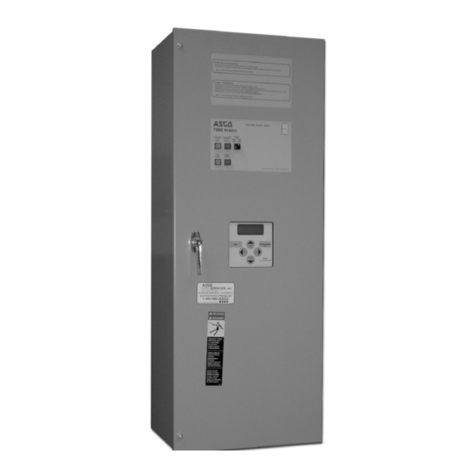
Asco
Asco 7000 Series User manual
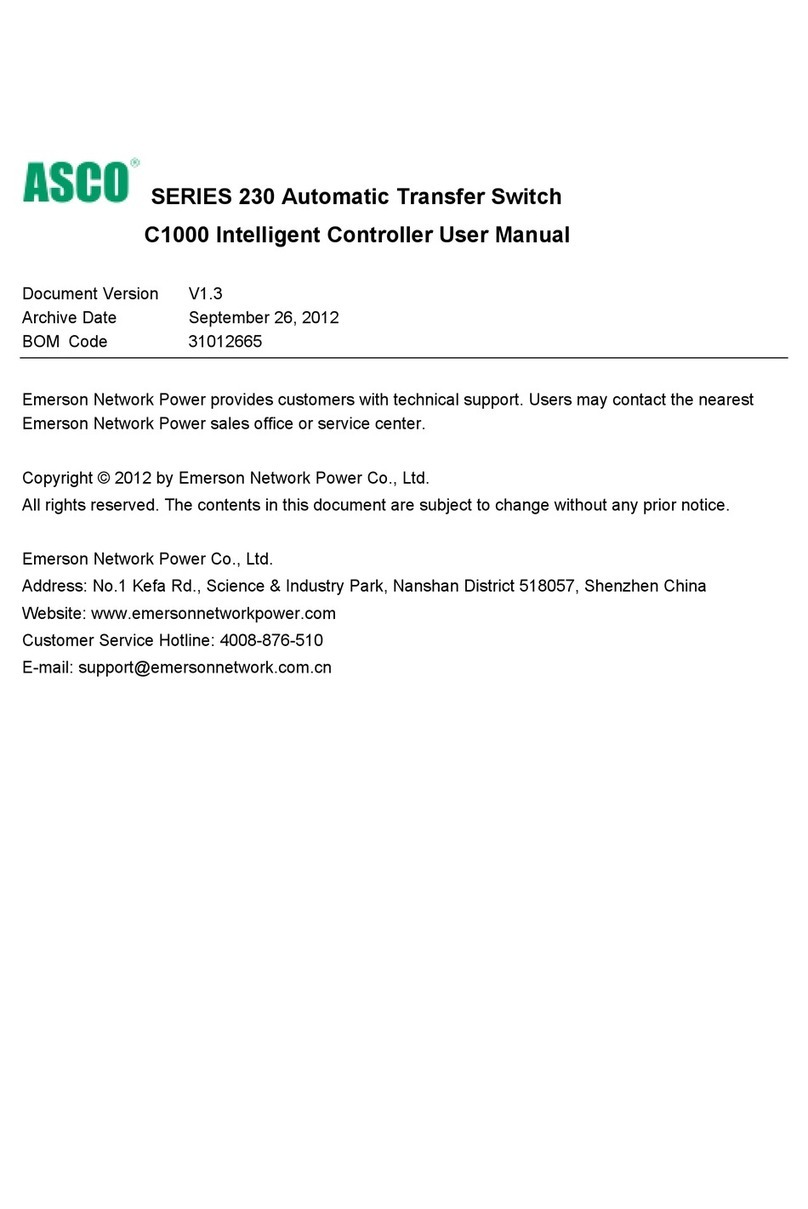
Asco
Asco 230 Series User manual
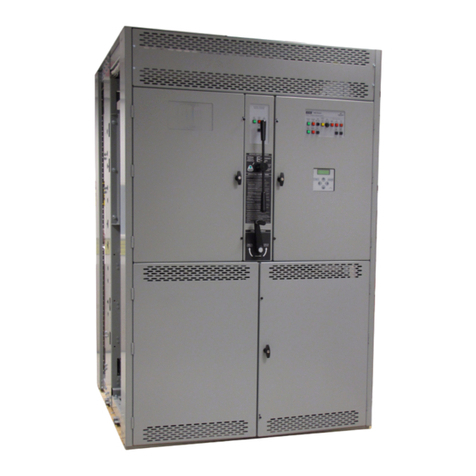
Asco
Asco 7000 Series User manual
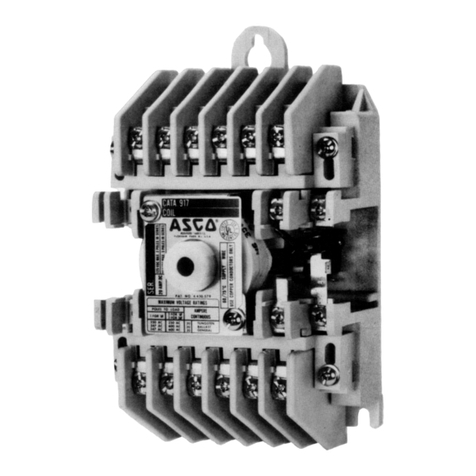
Asco
Asco 917 User manual