Assa Abloy InControl 3270 User manual

InControl 3270 and ToConnect 3270
Incedo™ Open Quick Start Brochure 1.0 1
For more information, see:
Incedo™ Open InControl 3270 / ToConnect 3270 Installation Guide
Incedo™ Open User Guide
Controller Unit Specications
Power supply 17-30 V DC. A UPS solution is recommended
Internal current consumption At 27.8 V: 96 mA Max 120 mA
PoE PoE+ 30 W IEEE 802.3af/at
Power Out 12-14 V DC, max 1.6 A (independent of
power option)
Operating environment +5 ° C to +40 ° C, RH 5 % to 95 %
IP class 44
Dimensions (housing) 182.3 x 182.3 x 45.5 (W x H x D mm)
Maximum number of Door
controllers per Controller
16
Controller Unit Overview
Hardware components such as electric strikes and readers are
connected to Controllers and Door controllers on terminal
blocks. Settings for either controller unit can be made on the
Mode selection DIP (J), and relay jumper pins (E). The RS-485
bus is terminated on the terminal block T3 (G).
Controllers are equipped with an additional PCB (M), but the I/O
connectivity is the same for both controller units.
A) RJ-45 Ethernet connector PoE+
B) RJ-45 Ethernet connector (no PoE)
C) Tamper switch
D) Terminal block T1: Analogue inputs and relay outputs
E) Relay jumper pins
F) Terminal block T2: DC IN, Hi-O, DC OUT
G) Terminal block T3: RS-485
H) RS-485 termination
I) Add-on card connector
J) Mode selection DIP
K) Label with QR code and MAC Address for Door controller
L) Controllers only: Additional PCB with QR code and MAC
address label for Controller
The MAC address is used to map controller units in the Incedo™
Open web application. The (InControl 3270) Controller has two
separate MAC addresses, since it can act both as a Controller and
a Door Controller.
LED Indicators
Controller and Door controller LED reference:
LED Col Name On Blinking
D1 Red Input IN1 Input is active (triggered) Sabotage (wire cut)
D2 Red Input IN2 Input is active (triggered) Sabotage (wire cut)
D3 Red Input IN3 Input is active (triggered) Sabotage (wire cut)
D4 Yellow Relay RE1 Relay is active n/a
D5 Yellow Relay RE2 Relay is active n/a
D6 Red Not used n/a n/a
D7 Yellow DC out over-
load
12 V DC output and/or
onboard relays draw current
beyond capacity
n/a
D8 Red Hi-O encrypted Hi-O bus is locked (en-
crypted)
n/a
D9 Green Hi-O unlocked Hi-O bus is unlocked n/a
D10 Green RS-485 RX Data is being received over
the RS-485 bus
n/a
D11 Red RS-485 TX Data is being transmitted
over the RS-485 bus
n/a
D12 Yellow Voltage
detected
Voltage between 12-28 V de-
tected on the DC IN terminal
or the PoE+ port
n/a
D13 Red Not used n/a n/a
D14 Green Network status Door controller is communi-
cating with the Controller.
IP address received
D15 Blue Service status Door controller is not running
the rmware
Door controller is running
the rmware
D16 Blue Controller
status
n/a Slow blinking: Controller
is working, connected
to cloud. Fast blinking:
Controller is not connected
to cloud.
D17 Green Number of
connected
devices
n/a Blinking to indicate number
of connected devices (Door
controller or WellCom
units). One blink per con-
nected device, then a pause
for 3-4 seconds (repeated).
D18 Red Number of
disconnected
devices
n/a Blinking to indicate number
of disconnected devices
(Door controller or Well-
Com units). One blink per
disconnected device, then
a pause for 3-4 seconds
(repeated).
RE1 RE2
RS-485
DC OUTHi-ODC IN
D10
D1
D2
D3
D4
D5
D6
D7
D8
D9
D11D13
D12
D15
D14
D16
D17
D18
Warning!
Ensure that the controller unit is powered off before
connecting or disconnecting any wire or cable.

InControl 3270 and ToConnect 3270
Incedo™ Open Quick Start Brochure 1.0 2
Installing Controller Unit
The supplied housing have room for one add-on card.
It is secured to the wall using four 5mm screws (not included).
Cables can either be run from a hole in the wall or from the
sides. Before mounting, consider placement with respect to
cabling needs and exposure to wear and damage.
1) Secure the back cover to the wall, with the part marked UP
facing upwards.
2) Optional: Install an additional relay board.
3) For the selected components and interfaces, make the
desired cable connections.
4) Connect the power supply, and power up the unit.
If powering from PoE+, connect the network cable.
5) Connect the controller unit to the local network.
A number of LEDs on the controller unit should light up.
6) Ensure that the tamper spring (A) is secured to the tamper
switch (B). It should t tightly around the button.
7) Close the front cover and secure it with the two screws.
Connecting Controller Unit
A) Network router or switch
B) RJ-45 Ethernet connector PoE+
C) RJ-45 Ethernet connector (no PoE)
1) To connect a Controller to the cloud service:
Controller Connect to
RJ-45 PoE* Local network router or switch with Internet access.
2) To connect a Door Controller to the parent Controller:
Door controller Connect to
RJ-45 PoE* • The parent controller’s local network switch.
• Optional: The parent controller’s free RJ-45
connector (no PoE).
* Power over Ethernet (PoE) is optional. It is recommended to
power controller units from DC IN.
Connecting 12 V Electric Strike
Optional dual loop (A), door sensor (B), yback diode (C).
1) Select input and relay.
An additional relay board can also be used.
Function Quantity I/O
Electric strike 1 RE1-2 Relay board: RE3-RE8
Door sensor 0-1 IN1-IN3 Relay board: IN4-IN7
2) Connect the electric strike.
Congure the relay to supply 12 V. Congure the electric
strike for NO (fail-secure) or NC (fail-safe) operation. Mount
a yback diode between the + and C/0 V/GND terminals.
Jumper setting Relay output mode
Powered mode: RE1 or RE2 connector NC or NO
supplied +12 V DC C connected to ground.
Make the connections.
Terminal T1 Electric strike
NO or NC + (NO or NC)
C C/0 V/GND
3) Optional: Connect the door sensor.
Mount the input as dual loop in the web application and
connect dual loop resistors in the switch.
Make the connections.
Terminal T1 Electric strike
IN NC
GND 0 V/C
C– +
Note!
The LEDs on the PCB are turned off when the lid is
closed properly, with the tamper spring in correct
position.
Note!
When running a network cable, the bending radius
must be 3 cm or larger. Category 5e, or higher,
twisted-pair cable is recommended.
Ethernet/PoE
B C
> 3 cm
A
T1
+12 V
GND
NC
C
NO
C– +
IN1 NC NO
RE1 RE2
C NC NO CL- CL+CIN2 IN3GND GND GND
RE2
RE1
R2
R1
IN1 NC NO
RE1 RE2
C NC NO CL- CL+CIN2 IN3GND GND GND
IN1 NC NO
RE1 RE2
C NC NO CL- CL+CIN2 IN3GND GND GND
C
BA
148,1 mm
126,1
144
5 mm

InControl 3270 and ToConnect 3270
Incedo™ Open Quick Start Brochure 1.0 3
Connecting 24 V Electric Strike
1) Follow step 1) from Connecting 12 V Electric Strike.
2) Connect the electric strike.
Congure the relay to passive mode and supply 24 V from
the board. Congure the electric strike for NO (fail-secure)
or NC (fail-safe) mode, and mount a yback diode between
the + and C/0 V/GND terminals.
Jumper setting Relay output mode
Passive mode: RE1 or RE2 connectors NC, NO, and C
directly connected to the relay.
3) Make the connections.
Terminal Electric strike
NO or NC + (NO or NC)
0 V C/0 V/GND
Terminal T1 Terminal T2
C DC IN 24 V
4) Follow step 3) from Connecting 12 V Electric Strike.
Adding Hi-O Devices
Mode selection DIP (A), +12 V DC (B), from controller unit.
1) Locate terminal block T2.
2) Connect the Hi-O bus device to the controller unit.
Terminal T2 Connect to
Hi-O H H terminal on the Hi-O device or bus.
Hi-O L L terminal on the Hi-O device or bus.
DC OUT 0 V 0 V/ground terminal on the Hi-O device or bus.
DC OUT 12 V Optional. +12 V on the Hi-O device or bus.
3) If externally powered, power up the Hi-O device.
4) Optional: Test the Hi-O device before pairing.
a) Power up the controller unit.
b) Test the device on the bus.
c) Disconnect the unit from the power supply.
5) To pair the Hi-O device with the controller unit, set the
Mode selection DIP switch 1 to ON.
Mode selection DIP Function
DIP1 = ON: Hi-O pairing mode at power-up
6) Optional: Select the desired electric lock failsafe and fail
secure modes at power failures.
Mode selection DIP Function
DIP2 = ON: Motor lock door monitor (Hi-O) is
deactivated.
DIP2= OFF: Default. Motor lock door monitor
(Hi-O) is activated.
DIP3 = ON: Failsafe for electric strikes.
Unpowered strikes are unlocked.
DIP3 = OFF: Fail secure for electric strikes.
Unpowered strikes remain locked.
7) Ensure that the bus is properly terminated.
8) Power up the controller unit.
LED D15 (blue, Service status) is steadily lit during the Hi-O
pairing process. When LED D15 blinks, and LED D7 (yellow,
DC overload) blinks fast, the pairing process is complete.
9) Reset the Mode selection DIP.
Mode selection DIP Function
DIP1 = OFF: Normal operational mode.
The Mode selection DIP must be reset before the controller
unit reboots after 20 seconds. After reboot, LED D8 (red,
Hi-O encrypted) should be on. If LED D9 (green, Hi-O un-
locked) is on, the pairing process failed.
10) Power cycle the controller unit.
Removing Hi-O Devices
1) If externally powered, turn the Hi-O device on.
2) Set the Mode selection DIP switch 1 to ON.
DIP2 and DIP3 are not used while unpairing the Hi-O bus.
3) Press and hold the tamper switch.
4) Power up the controller unit.
When LED D15 blinks, and LED D7 blinks fast, the unpairing
process is complete.
5) When the unpairing process is complete, release the tam-
per switch.
6) Power off the controller unit.
7) Disconnect, add, or remove the Hi-O device from the bus.
The removed device can now be used with other controller
units.
8) To pair the Hi-O bus, follow Adding Hi-O Devices from step 3.
C– +
123456
ON
123456
ON
123456
ON
Note!
During the Hi-O pairing process, exit buttons cannot
be used to open the door.
123456
ON
6 5 4 3 2 1
ON
T2
OV
L
0V
24V
H
DC OUTHi-ODC IN
12V
HL12 V 0 V
A
B
T1
+24 V
GND
NC
C
NO
OV
C– +
L
0V
24V
IN1 NC NO
RE1 RE2
C NC NO CL- CL+CIN2 IN3GND GND GND
RE2
RE1
H
DC OUTHi-ODC IN
12V
T2
Note!
Ensure that the specications are not exceeded.
The maximum load is 1 A at 28 V DC.
123456
ON

InControl 3270 and ToConnect 3270
Incedo™ Open Quick Start Brochure 1.0 4
Connecting Readers Over RS-485
RS-485 termination DIP (A), +12 V DC (B), from controller unit.
1) Locate terminal block T3.
2) Connect the RS-485 bus devices to the controller unit.
Terminal T3 Connect to
A A terminal on the RS-485 device or bus.
B B terminal on the RS-485 device or bus.
0V 0 V/GND on the RS-485 device or bus.
12V Optional. +12 V on the RS-485 device or bus.
3) Ensure that the bus is properly terminated.
Any end node (controller unit or bus device) on the bus
must be terminated.
Termination DIP Termination state
RS-485 not terminated on the controller unit.
RS-485 terminated on the controller unit.
12V
T3
TERM
0V AB
1
2
ON
BA0V 12V
A
B
1
2
ON
1
2
ON
This manual suits for next models
1
Other Assa Abloy Controllers manuals
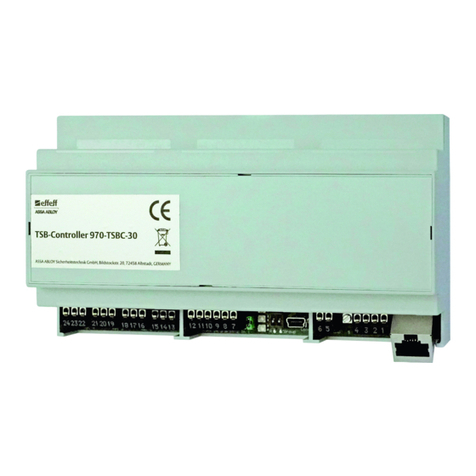
Assa Abloy
Assa Abloy effeff TSB-Controller II User manual
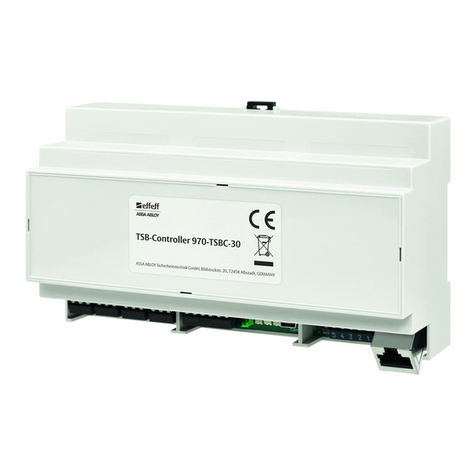
Assa Abloy
Assa Abloy effeff 970-TSBC-30-10 User manual

Assa Abloy
Assa Abloy Incedo EAC-M90 User manual

Assa Abloy
Assa Abloy LCU9016III User manual
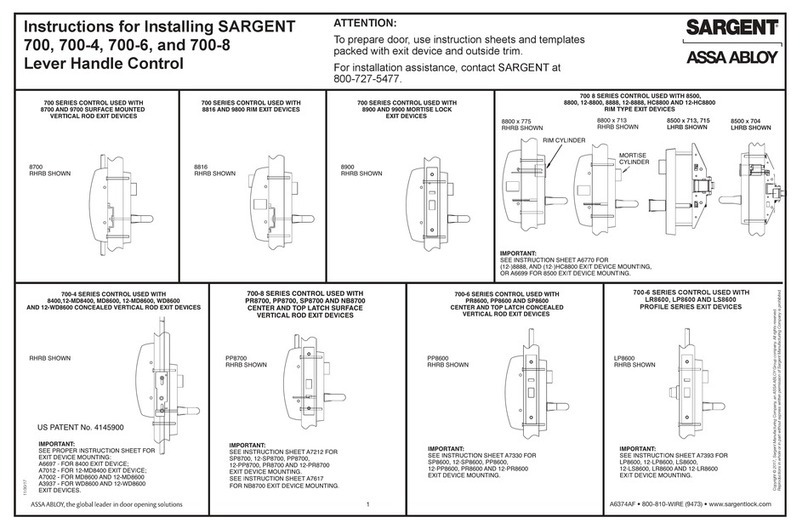
Assa Abloy
Assa Abloy Sargent 700 User manual
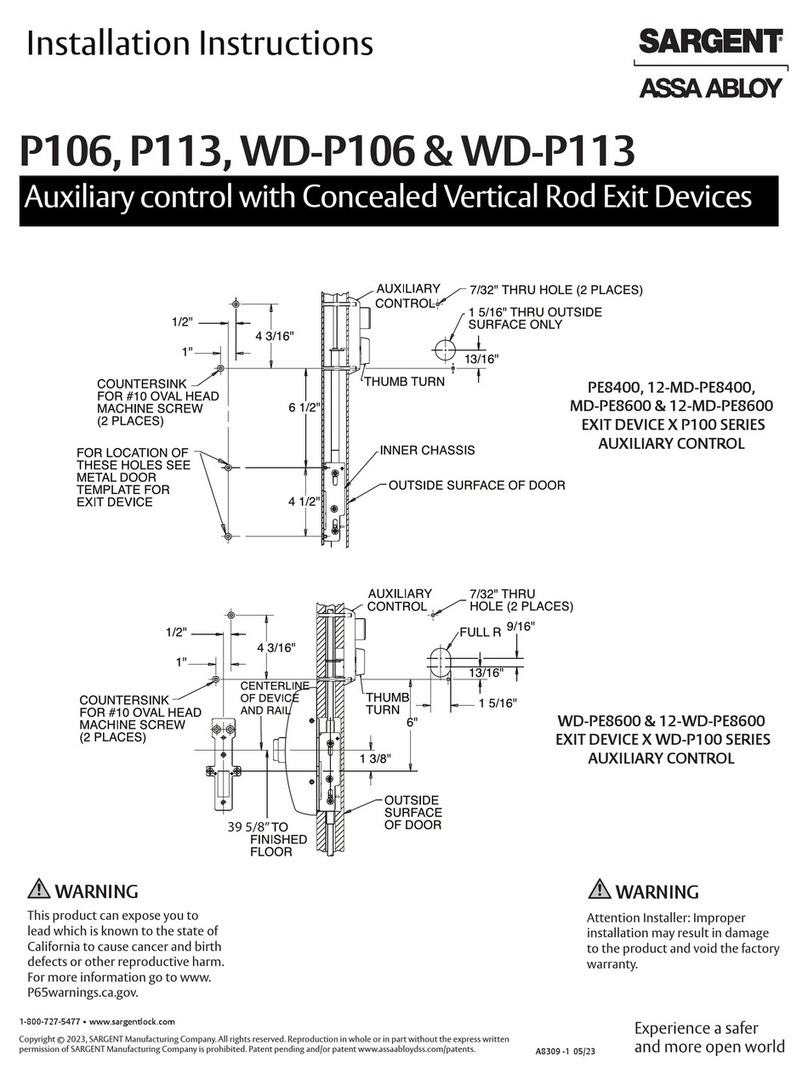
Assa Abloy
Assa Abloy Sargent P106 User manual
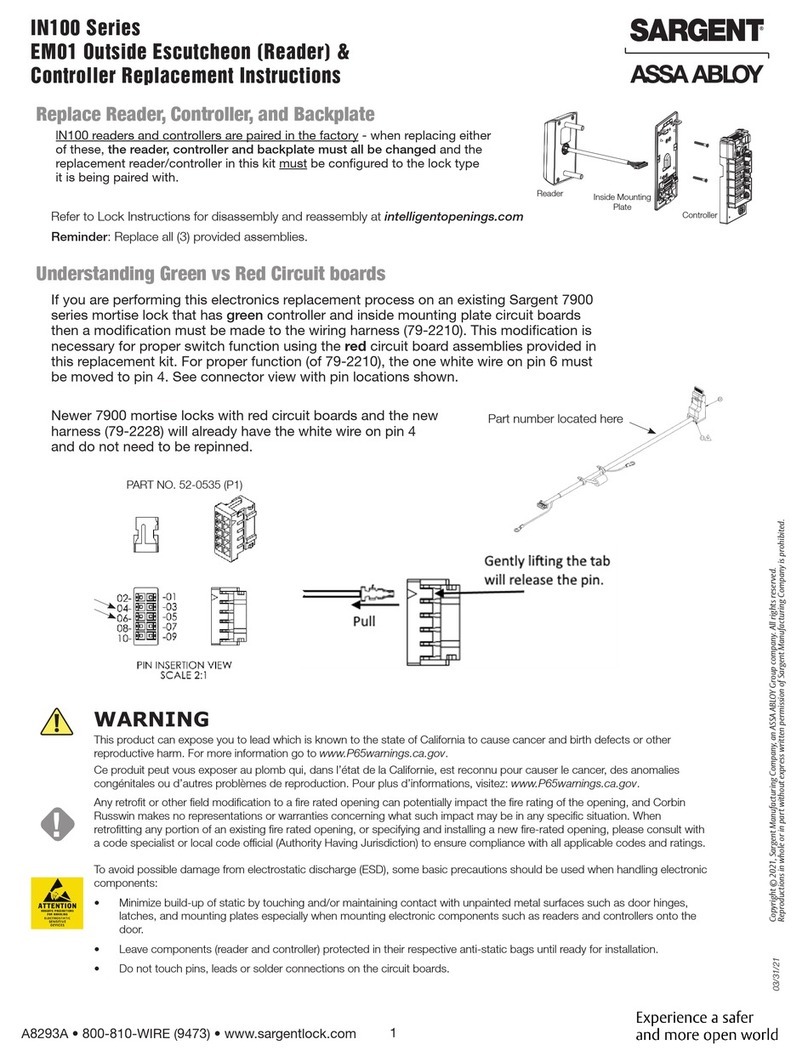
Assa Abloy
Assa Abloy Sargent IN100 Guide
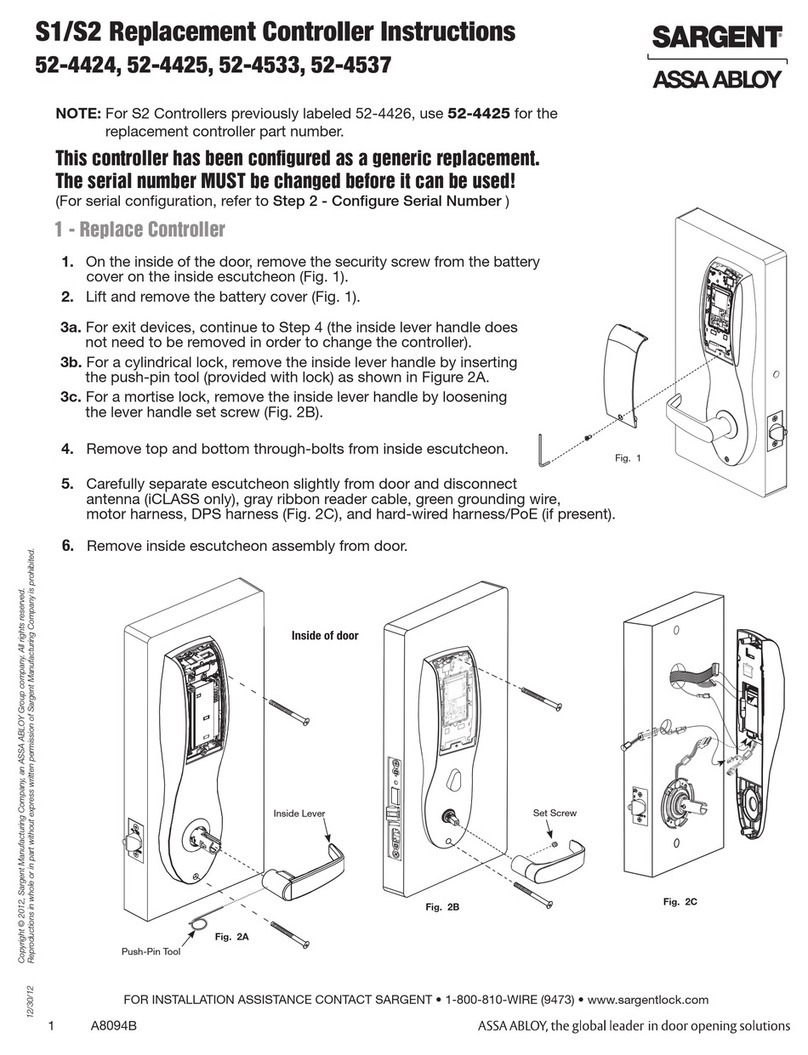
Assa Abloy
Assa Abloy Sargent 52-4424 User manual
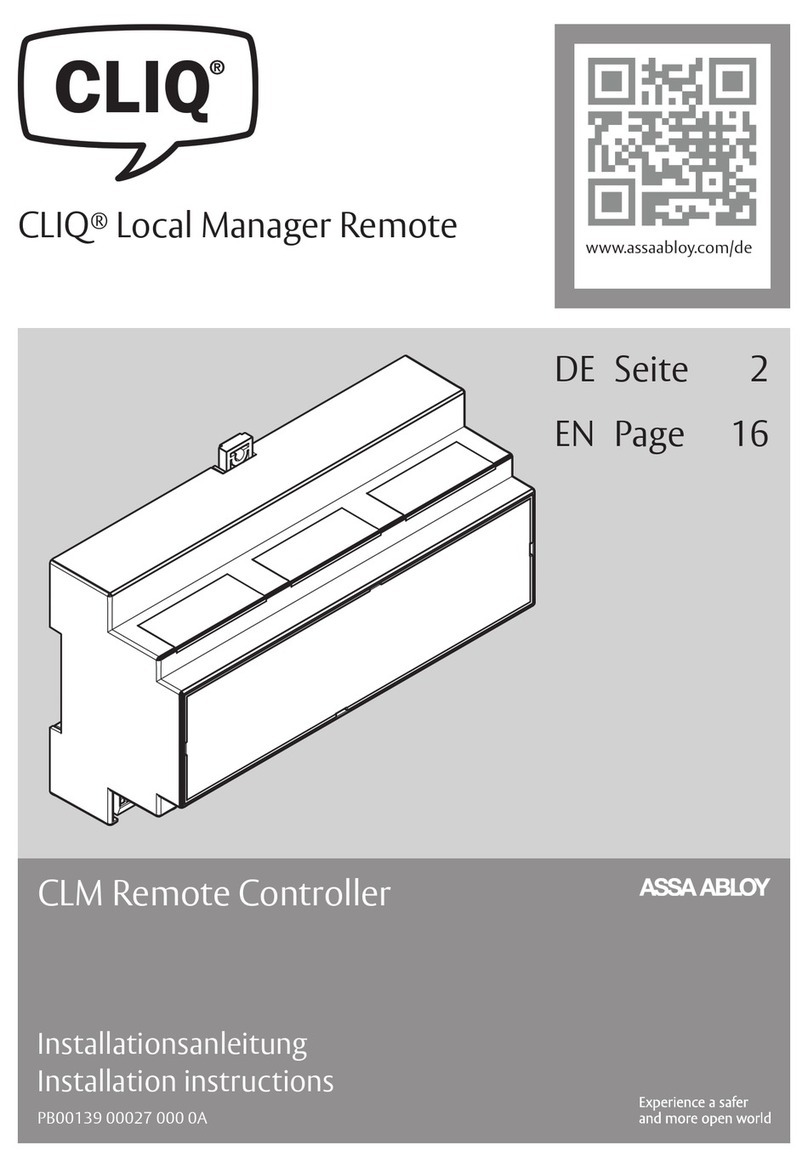
Assa Abloy
Assa Abloy CLIQ CLM User manual