AUTOPSTENHOJ Masterlift 2.35 Combi User manual

Manual no.: 9000195GB
Date: 10.07.2019
ALWAYS KEEP
operating instructions
ready to hand on the
unit
Read the operating
instructions before
working with the
unit
Masterlift
2.35 Combi / "Check-in"
Installation instructions
(TRANSLATED VERSION)

© AUTOPSTENHOJ GmbH
Sandkampstr. 90
D – 48432 Rheine
Tel.: + 49 5971/860202
E-mail: info@autopstenhoj.com
Internet.: www.autopstenhoj.com
Index: g
Before
taking into operation
check system compo-
nents, control, emer-
gency stop and safety
equipment for conditi-
on, damage and
correct function!
2 / 45 9000195GB
Masterlift 2.35 Combi / "Check-in"

3 / 45
Masterlift 2.35 Combi / "Check-in"
9000195GB
Table of contents
1 General............................................................................................................................................... 5
1.1 Information for the installation instruction............................................................................................ 5
1.2 Explanation of symbols ....................................................................................................................... 5
1.3 Liability and warranty .......................................................................................................................... 6
1.4 Copyright protection ............................................................................................................................ 6
2. Safety ................................................................................................................................................. 7
2.1 General ............................................................................................................................................... 7
2.2 Work safety ......................................................................................................................................... 7
2.3 Personal safety equipment.................................................................................................................. 7
2.4 Behavior in case of danger or accidents............................................................................................. 8
2.4.1 Preventative Measures ....................................................................................................................... 8
2.4.2 If the worst comes to the worst: Do the right things! ........................................................................... 8
3 Technical data ................................................................................................................................... 9
3.1 General function of Masterlift Combi................................................................................................... 9
3.2 General function of Masterlift Combi "Check-in" ............................................................................... 10
3.3 Connected loads ............................................................................................................................... 11
3.3.1 PLC control unit................................................................................................................................. 11
3.3.2 Motor ................................................................................................................................................. 11
3.3.3 Operating values............................................................................................................................... 11
3.3.4 Hydraulic system............................................................................................................................... 12
3.4 Weights ............................................................................................................................................. 12
3.5 Name plate........................................................................................................................................ 12
3.6 Requirements of the place of Installation.......................................................................................... 13
4 Installation of the lifting unit .......................................................................................................... 14
4.1 Overview of components Masterlift Combi........................................................................................ 14
4.2 Overview of components Masterlift Combi "Check-in"...................................................................... 15
4.3 Placing, aligning and concreting the steel cassette .......................................................................... 16
4.4 Installation of the hydraulic components........................................................................................... 17
4.4.1 Installation of hydraulic cylinders Masterlift Combi .......................................................................... 17
4.4.2 Installation of hydraulic cylinders Masterlift Combi "Check-in........................................................... 18
4.4.3 Installation of preassembled cylinders .............................................................................................. 19
4.4.4 Installation of the hydraulic pump unit............................................................................................... 20
4.5 Installation of the control unit components........................................................................................ 21
4.5.1 Introduction ....................................................................................................................................... 21
4.5.2 Insulation test and continuity of the protective conductor ................................................................. 21
4.5.3 Cable connections............................................................................................................................. 22
4.5.4 Control box and terminal box ............................................................................................................ 22
4.5.4.1 Connection of the control unit ........................................................................................................... 23
4.5.4.2 Connection of the terminal box ......................................................................................................... 24
4.5.4.3 Terminal block on the hydraulic pump unit........................................................................................ 24
4.5.5 Installation of the sensor ladder rack - Combi................................................................................... 25
4.5.6 Installation of the sensor ladder rack - Combi "Check-in" ................................................................. 28
4.6 Connection of the synchronization bars............................................................................................ 31
4.7 Connection of pneumatic emergency lowering ................................................................................. 31
4.8 Aligning the hydraulic cylinders......................................................................................................... 32
4.9 Installation of recessed version......................................................................................................... 32
4.10 Installationrecessedversion(withushoordevice) ....................................................................... 33
4.10.1 Installation and adjustment of the cover plates................................................................................. 34

4 / 45 9000195GB
Masterlift 2.35 Combi / "Check-in"
5 Installation of superstructure ........................................................................................................ 35
5.1 Installation of the repair platform for ML Combi ................................................................................ 35
5.2 Installation of the repair platform for ML Combi "Check-in"............................................................... 36
5.3 Installation of the wheel free superstructures.................................................................................... 37
5.3.1 Repair platform superstructure type "Pv" .......................................................................................... 37
5.3.2 Swivel arm superstructure type "S"................................................................................................... 37
6 Adjustment of the lift ...................................................................................................................... 39
6.1 Adjusting the main cylinder ............................................................................................................... 39
6.2 Adjusting the safety zone.................................................................................................................. 40
6.3 Adjusting the limit switch ................................................................................................................... 40
6.4 Testing of adjustments ...................................................................................................................... 40
7 Installation of the cassette cover .................................................................................................. 41
8 Training of personnel in the operation of the lift ......................................................................... 41
9 Malfunction monitoring .................................................................................................................. 41
9.1 Malfunction indication PLC control unit............................................................................................. 41
9.2 Malfunction analysis.......................................................................................................................... 43
10 Overview: Wiring diagrams............................................................................................................ 44
11 Overview: Hydraulic circuit diagrams........................................................................................... 44
12 Overview: Other circuit diagrams.................................................................................................. 44

5 / 45
Masterlift 2.35 Combi / "Check-in"
9000195GB
1 General
1.1 Information for the installation instruction
This installation instruction describes the installation of the lifting unit and the superstructure. Compliance with
the notes on safety and procedural instructions is a prerequisite for the safe and proper installation of the lift.
Furthermore they are to be kept for the applicable local accident prevention guidelines and the general safety
regulations regarding the lift’s range of applications.
The graphic illustrations in this manual can, if necessary, differ slightly from the actual execution of the lift.
The operating manual for the lift as well as the installation and operating manuals of the supporting compo-
nents apply besides these installation instructions. Please observe the notes contained therein - especially the
safety notes.
1.2 Explanation of symbols
Important safety and machine-technical notes in these installation instructions are marked with symbols. The
notes must be respected to in order to avoid accidents, personal injuries and damage to property.
WARNING!
This symbolizes dangers that can lead to adverse effects on health, injuries, permanent physical dama-
ge or to death.
Adhere at all costs to the notes specied regarding work safety, and be particularly careful in these
cases.
WARNING! Danger of electric current!
This symbol draws attention to dangerous situations involving electrical currents. There is a danger of
serious injury or death if the safety notes are not complied with. The work may only be carried out by
qualied electricians.
ATTENTION!
This symbolizes notes, which if not complied with, can lead to damages, malfunctions and/or break-
down of the machine.
NOTE!
This symbol highlights tips and information that are to be observed for efcient and disruption-free assembly of
the machine.

6 / 45 9000195GB
Masterlift 2.35 Combi / "Check-in"
1.3 Liability and warranty
All information and notes in these installation instructions are provided under due consideration of valid regula-
tions, the latest technical status of development as well as our years of expertise and experience.
The translation of these installation instructions has also been made to the best of our knowledge. We do not
accept any liability for errors in translation. The version of the installation instructions marked with “Original
version” shall be binding.
For optional design versions, the use of additional ordering options or the implementation of the latest technical
modicationstheactualscopeofdeliverymaydifferfromthedescriptionsandillustrationsinthismanual.Ifyou
have any questions please contact the manufacturer.
We reserve the right for technical changes to the product within the framework of improving the usability and
further development.
1.4 Copyright protection
Theseinstallationinstructionsistobetreatedascondential.Itissolelyintendedforthepersonsengagedin
the installation of the machine. Relinquishment of the installation instructions to third parties without the written
permission of the manufacturer is forbidden. If necessary please contact the manufacturer.
NOTE!
The contextual details, texts, drawings, pictures and special illustrations contained within are protected by copy-
right and subject to further commercial property rights. All misuses are punishable.
Reproduction in any kind or form – also in part – as well as the utilization and/or the communication of contents
are forbidden without the written permission of the manufacturer. Any violations require compensation. Further
claims remain reserved.

7 / 45
Masterlift 2.35 Combi / "Check-in"
9000195GB
2. Safety
This section gives an overview of all important security aspects for the optimal protection of personnel as well
as for the safety and malfunction-free operation of the machine.
Additionally, the individual chapters contain concrete safety notes, marked with safety symbols, for the preven-
tion of immediate dangers. Furthermore, any pictograms, signs and labels on the machine are to be observed
and kept in good, legible condition at all times.
2.1 General
At the time of its deployment and manufacture, the machine is built according to recognized codes of practice
and is deemed operationally safe. However, dangers may arise from this machine if it is not used professionally
by trained personnel, or if it is used improperly or not according to the designated purpose. Each person autho-
rized to work with the machine must have read and understood the assembly manual before beginning work.
Changes of any kind, as well as attachments or alterations to the machine are prohibited
All security, warning and handling notes on the machine are to be constantly kept in good, legible condition.
Damaged signs or labels must be immediately renewed.
Supplied setting values or adjustment ranges are to be complied with unconditionally.
2.2 Work safety
By following the security notes during work on the machine damages to equipment and personnel can be
avoided. Non-compliance with these notes leads to a considerable risk of injury to personnel and creates the
danger of damaging or destroying the machine.
With disregard of the safety regulations all liabilities and damage claims for compensation against the manufac-
turer or its commissaries are excluded.
2.3 Personal safety equipment
In principle, the following is to be worn when working on or with the machine:
Protective work clothing
Tightttingworkclothing(minimaltearstrength,nowidesleeves,no
rings or other jewellery, etc.)
Safety Shoes
Safety Shoes for protection against any heavy, falling parts and slipping
on non-skidproof ground.

8 / 45 9000195GB
Masterlift 2.35 Combi / "Check-in"
2.4 Behavior in case of danger or accidents
2.4.1 Preventative Measures
•Alwaysbepreparedforaccidentsorre!
•Keeprstaidequipment(rstaidkit,blankets,etc.)andreghtingequipmentclosetohand.
•Makepersonnelfamiliarwiththelocationanduseofsafety,accidentreporting,rstaidandrescueequip-
mentandhavethistrainingconrmed.
•Clear access routes for rescue vehicles.
2.4.2 If the worst comes to the worst: Do the right things!
•Operate the EMERGENCY STOP to shut down the machine.
•Inform the responsible person at the place of use.
•Alarmaphysicianandtherebrigade.
•Rescuepersonsfromthedangerzone,startrstaidmeasures.
•Keep access routes for rescue vehicles clear.

9 / 45
Masterlift 2.35 Combi / "Check-in"
9000195GB
3 Technical data
Generally the lifts Masterlift Combi and Masterlift Combi "Check-in" differ in respect of their general function.
3.1 General function of Masterlift Combi
The Masterlift Combi lift is a multi-functional lift both for diagnostics and repair work. The structure basically
represents to "nested" Masterlift lifting units. The outer lifting unit with the 1705 mm piston spacing supports the
platforms, the inner lifting unit carries the freely selectable wheel free device. The following superstructures can
be mounted as wheel free device:
Pv and Pvv
Saa 135
Saav 135 "Van"
Based on its principle of function, the max. stroke is 1900 mm. The stroke can thereby be freely divided bet-
weentheplatformandthewheelfreedevice.Iftheunitismountedushwiththeoortogetherwithushoor
device, the wheel free device can be used as "regular" work area.
Fig. 1: Schematic drawing Masterlift Combi

10 / 45 9000195GB
Masterlift 2.35 Combi / "Check-in"
3.2 General function of Masterlift Combi "Check-in"
The Masterlift Combi "Check in" lift is explicitly designed for the reception area.
Thelifthastwoliftingunits:therstoneforthemainplatformliftandthesecondoneforthewheelfreedevices.
The piston distance for both units is 1335mm.
Due to the principle of this lift, the maximum stroke is 1835 mm. The stroke can be spread on the superstructu-
res, platforms or wheel free device.
Fig. 2: Schematic drawing Masterlift Combi "Check-in"

11 / 45
Masterlift 2.35 Combi / "Check-in"
9000195GB
3.3 Connected loads
3.3.1 PLC control unit
Supply line via main switch 400V / 3p+N+PE / 50Hz
Voltage power adaptor primary/secondary 230V AC / 24V DC
Control voltage 24V DC
Sensor voltage 24V DC
Voltage of magnetic coil 24V DC
Power input operation / rest max. 74 W / 3,5 W
IP Protection terminal box / control unit IP65 / IP54
Temperature range -10…+60 °C
Sound level of buzzer min. 65 dB
Max. power output motor protection (K1) 4 kW
Max. power output motor lighting (BEL) 500W
Fuse lighting (F2) 3,15A/tr.
3.3.2 Motor
Voltage 230/400V(Δ/Y)
Phases / frequency 3p+PE / 50 Hz
Current consumption 16 A
Power input 3,0 kW
Rated speed 2770 rpm
3.3.3 Operating values
Lifting/lowering speed Approx. 6 cm/s
Permanent sound level ≤70dB(A)
Operating temperature range -10… +60 °C
Operating pressure for emergency lowering
(at port A):
min. 6 bar

12 / 45 9000195GB
Masterlift 2.35 Combi / "Check-in"
3.3.4 Hydraulic system
Max. pressure of hydraulic pump 250 bar
Hydraulicpumpowvolume 10,6 l/min
Max.owvolumeofowcontrolvalve 8,6 ± 0,8 l/min
Capacity [kg] 3500
Operating pressure [bar] 215
Setting of pressure relief valve [bar] 225
Total oil volume in circuit Approx. 10 l
Oil volume in tank Approx. 6,5 l
3.4 Weights
Superstructure: All components fastened on the hydraulic cylinders
Cassette: Steel cassette concreted in the foundation containing the lifting unit
Liftingunit:Hydrauliccylinderswithguides/stufngboxes,synchronizationbar,hydraulicpumpunitincl.hy-
draulic oil, control unit, and sensor ladder rack for the signal tone. The lifting unit is built into the cassette,
except for the control unit.
Component Lift (Type) Weight (kg) approx.
Superstructure see operating
instructions
see operating
instructions
Cassette
Lifting unit
3.5 Name plate
The name plate is located on the control and contains the following information:
•Manufacturer
•Type designation
•Machine serial-no.
•Load bearing capacity
•Year of manufacture
•Setting of excess-pressure valve
•Operating pressure
•Supply voltage
Fig. 3: Name plate

13 / 45
Masterlift 2.35 Combi / "Check-in"
9000195GB
3.6 Requirements of the place of Installation
Liftsinthisseriesconsistofanaboveooraswellasanunderoorcomponent.Theycanbeinstalledasstan-
dard, basement or ceiling installation version.
Hydrauliccylinder,hydraulicpump,motor,valvesandpartsofthecontrolareunderoor-mountedinacovered
foundation frame or in a steel cassette. The foundation depth thereby depends on the design of the lift (“Te-
chnical Data”).
Superstructure,possiblywithintegratedwheelfreedevice,andcontrolboxrepresenttheaboveoormodules.
Theliftmustonlybeinstalledindryindoorworkshopsorinoutdoorareasprotectedagainsttheinuencesof
weather(wind-load,humidityetc.).Theinstallationrequiresaleveloor.Theinstallationlocationmustbefree
of high dust and/or dirt loads. It must be assured that the foundation will remain dry and clean over the entire
utilization time of the lift.
Whenworkingontheooredge(e.g.tilingoftheoor)thejackettubesofthehydrauliccylinderandtheseal
packages must be appropriately protected against dust, sand, mortar, cleansing agents and other foreign mat-
ter.
The manufacturer or his representative will not accept any liability, compensation and/or warranty claims for
damage caused by the entry or introduction of foreign materials into the working range of the lift.
NOTE!
Before starting work inform the person responsible for building work about the necessary precautions in the
vicinity of the lifting platform!
Use of the lift in wet rooms, such as a car wash, is only permitted in combination with special optional equip-
ment, which is available from the manufacturer on request. In this case the control must be installed, well
protected against moisture at a place with unobstructed view to the danger zone.

14 / 45 9000195GB
Masterlift 2.35 Combi / "Check-in"
4 Installation of the lifting unit
4.1 Overview of components Masterlift Combi
The main components diagrammed in the following illustrations belong to this series.
Fig. 4: Component overview of lifting unit ML Combi in steel cassette
Cover of the cassette
with sealing
Guide /
Stufngbox
Main cylinder
Cable guide
tube
Hydraulic pump
unit
Hydraulic valve of the
hydraulic cylinder
Flow divider
Synchroniza-
tion bar
Terminal box
Struts
Hydraulic hoses
to the wheel free
cylinder
Hydraulic hose
to the main
cylinder
Sensor ladder
rack
Cassette
Wheel free
cylinder

15 / 45
Masterlift 2.35 Combi / "Check-in"
9000195GB
4.2 Overview of components Masterlift Combi "Check-in"
Fig. 5: Component overview of lifting unit ML Combi "Check-in" in steel cassette
Cover of cassette with
sealing
Hydraulic valve of
the hydraulic cyinder
Flow divider
Guide /
Stufngbox
Hydraulic hoses
to the wheel free
cylinder
Main cylinder
/ wheel free
cylinder
Cable guiding
tube
Synchroniza-
tion bar
Terminal box
Struts
Hydraulic pump
unit
Hydraulic ho-
ses to the main
cylinder
Sensor ladder
rack
Cassette

16 / 45 9000195GB
Masterlift 2.35 Combi / "Check-in"
4.3 Placing, aligning and concreting the steel cassette
Before beginning assembly, check and determine the general layout, the placement of the control box, the steel
cassette and the foundation measurements.
For the construction of the foundation and the arrangement of the steel cassette, depending on the installation
(ontopofoor,ushwiththeoor,etc.)afoundationplan,agreed-uponbythemanufacturerorarchitectisto
be used.
The measurement SFF (Surface of Finished Floor) must be marked by the architect or the responsible con-
struction manager. The steel cassette must be aligned according to the measurement of the foundation plans.
Themeasurementsspeciedinthefoundationplanmustbestrictlycompliedwith.
Place the steel cassette in the foundation with a suitable lifting machine and secure by means of assembly
bars,inordertosafeguardagainstoating.Thereferencealignmentfortheheightmeasurement of +3/-0 mm
to SFF is the tile frame welded on the cassette frame. Likewise verify that the steel cassette is concreted leve-
led. This is measured by means of a spirit level, which is placed crossways on the foundation frame (measure
length and width).
In order to be able to lay any supply and control cables at a later time, conduits must be installed between the
steel cassette and control box. All supply cables provided from the customer are to be pulled to the control box.
SFF-measurement must
be taken by architect
Spirit level
Spacers
Steel cassette Fig. 6: Control of the steel cassette installation
SFF

17 / 45
Masterlift 2.35 Combi / "Check-in"
9000195GB
4.4 Installation of the hydraulic components
Before installation of the lifting unit, both the transport cover and the struts must be removed from the inside of
the steel cassette.
4.4.1 Installation of hydraulic cylinders Masterlift Combi
NOTE!
When mounting older cassettes before setting the cylinder, put the bracket for the sensor ladder rack in the
steel cassette (it does not belong to the delivery of the lifting unit).
With new cassettes this is already welded in.
NOTE!
The sensor ladder rack is mounted in the cassette behind the hydraulic tank.
Transport locks and
bleeding screws
Thread for ring
screws
Transport locks and
bleeding screws
Flat gasket
Sensor ladder rack
Hydraulic connections
Bottom bracket
Fig. 7: Installation of hydraulic cylinders ML Combi
Bracket for pump unit
Wheel free
cylinder
Main cylinder

18 / 45 9000195GB
Masterlift 2.35 Combi / "Check-in"
4.4.2 Installation of hydraulic cylinders Masterlift Combi "Check-in
NOTE!
When mounting older cassettes before setting the cylinder, put the bracket for the sensor ladder rack in the
steel cassette (it does not belong to the delivery of the lifting unit).
With new cassettes this is already welded in.
NOTE!
The sensor ladder rack is mounted in the cassette behind the hydraulic tank.
Fig. 8: Installation of hydraulic cylinders ML Combi "Check-in"
Synchronization
bar
Thread for ring
screws
Bracket for
pump unit
Wheel free
cylinder
Main cylinder
Transport locks
and bleeding
screws
Hydraulic pump
unit
Flat gasket
Hydraulic
connections
Cable guiding
tube
Potential equali-
zation
Sensor ladder
rack
Bottom bracket

19 / 45
Masterlift 2.35 Combi / "Check-in"
9000195GB
4.4.3 Installation of preassembled cylinders
Forliftswithushoordeviceplacethespacer(h=105mm)inthesteelcassettebefore installing the cylinders.
Thespacerisusedforbridgingthespaceneededfortheushoordevice.Lockingisnotnecessary.
Install preassembled cylinders in the steel cassette as follows:
•Placetheatgasketonthefoundationframe.
•Screw two ring screws M 20 into the bearings and mount – for ML Combi the main cylinders – for ML
Combi "Check-in" the pairs of the hydraulic cylinders (main- and wheel free cylinder) - into the cassette
with a suitable lifting device. The positioning of the cylinder goes faster if you screw in threaded bolts M16
as guide bolts into the threads in the foundation frame.
•When setting the cylinder, ensure that the hydraulic hoses are on the opposite side of the pump unit (Also
applieswithType"F..."Theboreinthecarrierangeoftheguideforthecableguidetubemustbeinside
(for ML Combi Check-in, see layout Fig. 8: Assembly of the hydraulic cylinder ML Combi "Check-in") respe-
ctively on the opposite side of the bracket for the pump unit (for ML Combi, see layout Fig. 7)).
•Remove ring screws, then screw in the fastening screws DIN 6912 - M16 x 40 - 8.8 vz, remove the threa-
dedboltsandalsoscrewinthefasteningscrewshere.Tightenscrews.Theboreinthesideoftheangeof
the guide facing the cassette is closed by means of a screw with nut.
•The setting of the wheel free cylinders takes place analogous to the main cylinders (for ML Combi).
•After the setting of the cylinder, remove the transport locking screw on the piston of all cylinders and repla-
ce with the bleeding screw DIN912 - M10x16 – vz (see illustration).
Fig. 9: Sectional view - Hydraulic cylinder with bleeding screw
Bleeding screw
Attention!
Only remove the transport locking plates (wooden plate) from the cylinder Ø123 after the rst time the
lifting unit is raised, otherwise the cylinder will slide into the base guide.

20 / 45 9000195GB
Masterlift 2.35 Combi / "Check-in"
4.4.4 Installation of the hydraulic pump unit
The unit will be delivered preassembled. It will be fastened onto the welded screws inside of the cassette. The
unitmustbeleveledwhenmounting.Thescrewplugintheoilllingboreistobereplacedbythedipstickwith
ventilationlter.Thehydraulichosesofthehydrauliccylindermustbeplacedaccordingtog7.
A) Solenoid valve for hydraulic cylinder in drive-on direction left
B) Solenoid valve for hydraulic cylinder in drive-on direction right
C) Hydraulic connection for hydraulic cylinder in drive-on direction left
D) Hydraulic connection for hydraulic cylinder in drive-on direction right
E) Connection for pressure gauge
F) Oil Tank
G) Pressure control valve
H) Emergency lowering valve
I) Flow divider valve
K) Dipstick
L) Assembly position "Terminal box lighting"
M) Hydraulic connection for wheel free cylinder
N) Flow divider
K E L
AI H
G
D
C
F
Fig. 10: Pump unit type Combi / "Check-in"
B
M
N
Table of contents
Other AUTOPSTENHOJ Lifting System manuals
Popular Lifting System manuals by other brands
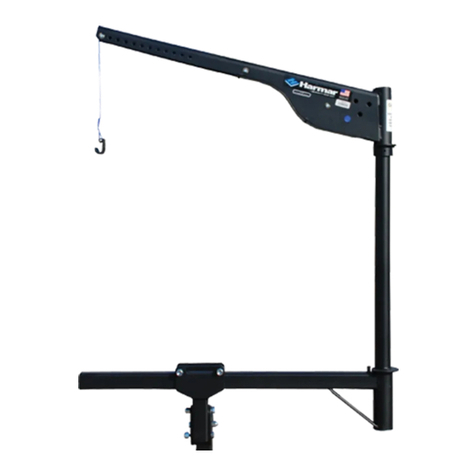
Harmar Mobility
Harmar Mobility AL055 Installation & owner's manual

Schmalz
Schmalz VACUMASTER COIL operating instructions
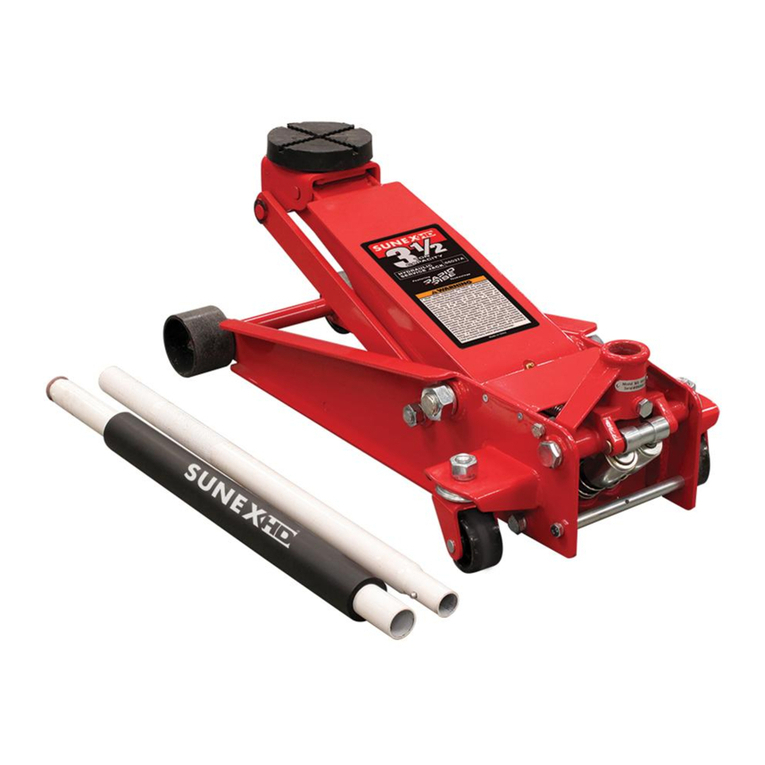
Sunex Tools
Sunex Tools 66037 quick start guide

PLS
PLS Access ACC-1150 instruction manual

Jadeim
Jadeim Handy B.O.B. 1500 AIR LIFT instructions
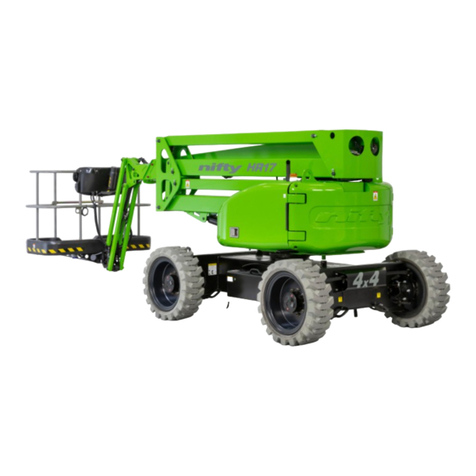
nifty
nifty HR17 SP50 HYBRID SERIES Operating/safety instructions