BAILI ERTONG SMC Series User manual

SM-22
(Read this operation manual carefully before using the product)
SMC Series Valve Electric Actuator
Operation Manual
TIANJIN BAILI ERTONG MACHINERY CO., LTD.
ཙҼ䙊7(7

Content
Part I SMC Series Basic Type Operation Manual ...............................................1
Part II SMC series integral type operation manual..............................................13
Part III SMC explosion-proof type operation manual .........................................14
Part IV SMC-04SMC-2 low-temperature operation manual...........................16
ཙҼ䙊7(7

1
Part I SMC Series Basic Type Operation Manual
1. Summary
SMC series multi-turn electric valve actuator (hereafter referred to as electric actuator) is used to operate
gate valve, globe valve, diaphragm valve and other multi-turn valves which drive valve’s disc to make linear
movement. Some of SMC series different seating numbers products could be combined with BA bevel gear
reducer or spur gear reducer, as a SMC/BA combined multi-turn electric actuator. SMC series could be
combined with HBC worm reducer or planetary reducer to form a combined quarter-turn electric actuator
which is used to operate ball valve, butterfly valve, cock valve and other quarter-turn valves.
SMC series could be electrically remotely controlled (in the control room) and could also controlled by
control buttons on site so as to be operated locally. SMC series’ manual operation mechanism realize local
manual operation against valve.
While the controlling part and modulating part of SMC/BA, SMC/HBC, SMC/JA and other combined
electric actuator are on SMC, this Operation Manual also can be used for those products above mentioned.
Fig1 to Fig9 are SMC, SMC/BA, SMC/HBC and SMC/JA basic type’s outline diagram. For the outline
dimensions and connection dimensions of the above products, please refer to the product catalog. For the
output torque, rotation speed, rotation number, motor power and other parameters, please refer to the
nameplate on the electric actuator.
2. Major technical parameter
The product complies with GB/T 24923ljBasic Type Electric Valve Actuator Technical ParameterNJ.
2.1Power supply:380V,50Hz (special orders, including 220V,415V,440V,460V,480V,660V,690V,50Hz,60Hz,
are available.) ;three-phase sine AC (for some models, single-phase 220V motor is available according to
user’s requirement.)
2.2 Enclosure protection grade:IP65IP67 (Please notify us if IP68 is required.)
2.3 Ambient temperature: -20ć70 (as user required)ć
2.4 Relative humidity: 90ˁ(at 25 )ć
2.5 Altitude: 1000m
2.6 Short-time duty: 10minǃ15minǃ30min rated time (according to motor loading)
2.7 Without strong vibration
2.8 Without strong corrosive medium and explosive mixture gas
3. Main content of the product nameplate
Some main technical features of the product are noted on the electric actuator’s nameplate. Users should
pay attention to it.
a. Model: the product’s model.
b. Nominal torque: the maximum controllable torque value (N.m) which is set before products leaves the
factory.
c. Output speed: turning numbers of the output shaft in a unit time (r/min).
d. Maximum turning numbers: the total turning numbers when the indication mechanism’s pointer starts
from 0 and ends at 100%.
e. Serial number: total serial number or serial number of this year.
f. Contract number: the product’s contract number in this year, which is helpful to search all the information
of this product and provide after-sales service.
4. Main structure
Electric actuator consists of the following components:
4.1 Special-used motor: it applies to valve’s loading performance and service condition. Type: YLT
4.2 Reducer mechanism: Used to transfer and increase the power of motor. There are 3-5 kinds of ration of
ཙҼ䙊7(7
s outlin
utli
e refer to thefer to
nd other parameother param
ters
Electric Valve Actuator TElectric Valve Actuato
ding 220V,415V,440V,460ng 220V,415V,440V
models,odels,
single-phase 220single-phase 2
67 (Please notify us if IP6Please notify us if IP
(as user required)s user required)
25 ))
ć
ǃ
15min15
ǃ
30min rated tirate
ation
ion
orrosive medium and exp
osive medium and e
product nameproduct
ures of theof

2
worm and worm gear and various motor gears and worm shaft gears combination, so that can get wider output
speed range.
ཙҼ䙊7

3
4.3 Driving tubular shaft: it is the electric actuator’s power take-off component, including three types which
are 2-PC, 1-PC and jaw type. For its structure, refer to Fig.10 to Fig.12.
2-PC driving tubular shaft has a inside valve stem nut and electric actuator bears valve’s axial force.
Generally, valve stem’s inner thread is processed by user. 1-PC driving tubular shaft is applied to non-rising
stem valve; or it could be connected with input shaft of HBC, BA, JA and other reducers. Its inner hole could
be single key, double key and spline. Jaw type driving tubular shaft could be meshed with valve stem’s jaw.
The type of the driving tubular shaft is chosen by user.
1.Driving shaft 2. Worm steel 3.Valve stem nut 4. Lock master
5.Bearings 6.Bearing 7.Valvestem
SMC/BA combined multi-turn electric actuator’s driving tubular shaft has three types.
For SMC/HBC, SMC/JA quarter-turn electric actuator’s driving shaft structure, refer to Fig.13. It has a
spline joint head inside it, which makes the connection between valve and electric actuator easily.
The hole which is used to connect spline and valve is generally processed by user.
4.4 Manual-electric switching mechanism
It is used to switch the electric actuator from electric operation mode to manual operation mode and vice
versa. It called “half-electrical mode, and electric operation mode is on the priority”. Push the switch handle
䙊7(7
actuato
uato
ng tubular shaftubular
JA and other reducers
and other redu
shaft could be meshed w
ft could be meshed

4
according to the arrow position before start to operate manually, and then try to turn the handwheel until the
switch handle gets 100% right place. Manual- electric mode switch is done at that time. Turn the handwheel to
begin manual operation. When electric operation is required, OPEN or CLOSE button can be pushed to make
the electric actuator in electric mode. For the deposition of manual-electric switch, refer to Fig.14.
Note: forbid to turn the switch handle forcefully to its electric mode position, which could
make the inner actuator damaged.
4.5 Manual operation mechanism: after finish switching the electric actuator into manual operation mode
and then begin to operate it manually. Manual operation mode of SMC-04 and SMC-03 is connected with
low-speed shaft. When in manual operation, turn the driving tubular shaft directly. Manual operation
mechanism is connected with high-speed shaft; while using it, manual operating by the handwheel through
worm gear shaft of reduction unit.
4.6 Torque control mechanism: it is used to control the electric actuator’s output torque. It is formed by two
parts which are worm gear, torque swing unit and torque switch unit.
Torque switch (hereafter referred as T.SW): when “Position Control” is selected, T.SW starts its protect
function. When “torque positioning” is closed, T.SW starts it control function.
4.7 Stroke control mechanism: it is used to control the valve’s end position and feedback valve’s contact
signal. It is composed of counter, middle transmission assembly, finger shape contact sheet seat and rotating
contact switch. The stroke control movement of SMC-04~2 starts from low-speed shaft(driving tubular
shaft). The limit control movement of SMC-3~5 starts from high-speed shaft(worm gear shaft).
Limit control mechanism of SMC series is also called “gear limit switch” (herein after referred as G·L·SW).
ཙҼ䙊7(
ng the electric actuator ing the electric actuato
ration mode of SMC-04ation mode of SMC-
turn the driving tubularrn the driving tubu
aft; while using it, manuawhile using it, man
used to control the electrico control the elec
swing unit and torque swig unit and torque sw
erred as T.SW): when “Ps T.SW): when
tioning” is closed, T.SWoning” is closed, T.S

5
For its structure, refer to Fig.16. It can provide two kinds of contact types which are 4R-2C and 4R-4C. 4R-2C
type has 8 self-cleaning, large capacity, swiveling contact switches. 4R-4C has 16 this kind of switches.
According to control modes, it shall be chose by user when places orders.
Each row of the swiveling contact on the G·L·SW’s position could be arranged freely. That is to say, the
rotor of the same row can be arranged as “OFF” type or “OFF””ON” type. (“OFF”“ON”type is often applied.)
Two middle rows of swiveling contact switches on the G·L·SW can be used as two certain position’s signal
output of the valve. Also, it can be set up to achieve synchronous action with other rows.
Ҽ䙊

6
4.8 Position indicator mechanism: it is used to show valve’s position. It is also called MDPI. Two functions:
pointer-dial scale type, indicating valve position on site; potentiometer makes feedback of valve position to
show in the control room. The above functions could be totally
or partly provided to user.
G·L·SW’s contact signal is different and MDPI’s valve
position feedback signal is continuous.
Fig.19 shows MDPI position indicator mechanism. Numerous
pairs of small modulus gears can be seen from Fig.19. This
mechanism can fulfill valves with any nominal diameters to
show a dial scale which is from 0% to 100%.
ȒAbout the electric actuator’s controller
In the general control theory, controller is a separate part from
the electric control part. The controller is always set in the
control room. If required by user, another order shall be placed
for the controller.
For the Integral electric actuator, there is no use of a separate
controller. The electric components of the control system are
totally set in the electric actuator’s controller case.
Any kind of control type shall chosen by user. Our company
provides separate controller and its instruction manual.
5. Mounting and dismantling(against the valve)
5.1 Beforehand, process the valve stem nut’s inner thread or spline jointed head’s inner hole/ key, so that will
fit with the valve(1-PC and jaw type driving tubular shaft do not need to do so.)
5.2 Mounting and dismantling methods for the electric actuator with 2-PC driving tubular shaft are as
following:
Put the processed valve stem nut in the tubular shaft and fix it by using locknut. Lift up the electric actuator
Fi
g
.19
ow valve’s position. It is aw valve’s position. It i
n on site; potentiometer mon site; potentiomete
ons could be totallyd be totally
fferent and MDPI’s vant and MDPI’s
uous.
on indicator mechanism. Nindicator mechanis
gears can be seen from Fars can be seen fro
l valves with any nomi
valves with any no
is from 0% to 100%
om 0% to 100%
tuator’s contruator’s
y, coo
ntrn

7
to align the stem with the internal thread of the stem nut.(Revolve direction is left for standard stem thread.)
Turn manually the actuator for valve open and lower it down gradually until touch the valve connection
surface. When the holes of flange aligned, tighten the electric actuator with the valve by bolts.
In order to assure the bolts tightened reliably, damage a part of the meshed thread of the upper part of the
sleeve and the locknut with a tool to prevent the locknut from quitting freely.
To remove the electric actuator from the valve, the method is to hang up the electric actuator properly, then
loose the bolts which connected the valve with the electric actuator, turn the actuator manually in the direction
of the valve close, then the actuator may be lifted up. (Note: Should hang the electric actuator in any
time until it separates from the stem. Should ensure to keep the hanging balance and reliable.
Especially for greater torque and size products which should be paid more attention to.)
5.3 The mounting procedure for 1-pc and the electric actuator of jaw driving sleeve is: Hang up of the valve
stem nut aligned, and then tighten the electric actuator with the valve reliably. When dismantling, first reliable
hang the electric actuator, then loose the tightened bolts, simply take off the bolts from the flange of valve.
5.4 The mounting and dismantling procedure of SMC/HBC, SMC/JA partial turn product is as following.
Mount the spline connection onto the valve stem and turn the driving shaft of the electric actuator second
grade decelerator mechanism manually to the same position as that of the valve (It is ideal that the valve in
any of the extreme position in this case). Lift up the electric actuator, make the driving shaft with the spline
connection and tighten the valve and the electric actuator by bolts reliably.
Firstly, hang the electric actuator reliably when disassemble, then loose the tighten bolts and take them off
from the valve.
(Note: Either multi-turn of partial turn electric actuator, only allow lift the electric actuator
itself by swinging ring and must not lift them with the valve).
5.5 Before mounting the actuator, it is necessary to clean the valve stem and coat it with grease. For
multi-turn valve with exposed stem, it is necessary to ensure that the protrusion of the stem must be less than
the height of the stem cover.
5.6 Pay attention to the electric valve place in the pipe line when mounting the actuator to ensure the
reasonable space for maintenance or inspection for the electric actuator.
5.7 As to the position of the mounted electric actuator no principle requirements are prescribed in normal
case. However it is recommended to make the motor shaft in horizontal position and the G.L.SW cover of box
in horizontal or vertical position facing upward, downward. This is advantageous to lubrication, maintenance
and observation on valve position.
6. Lubrication
6.1 The actuator was filled with special grease in our workshop. The product shall be inspected for
lubrication at least once a year. If no abnormal phenomenon was discovered, the lubricant may be further
used.
6.2 In normal case, the grease in the bearing of motor need not to be changed or added.
6.3 If changing grease after maintenance, should pay attention to its antioxidation, water resistance,
heat-resistance, corrosion resistance and mechanical stability etc... And also should pay attention to the
anticompression to ensure actuator lubrication and high transmission efficiency.
6.4 Special grease is preferred.
6.5 When grease is applied, care should be taken not to bring in foreign matters. After grease is filled, the oil
plug should be would with PTFE sealing tape and then tightened.
6.6 When lubricant (thin oil)is adopted in the electric actuator for special use, the electric actuator is not
filled with oil before dispatch. It is necessary to fill it with oil before putting it into operation.
7. Electric control principle diagram and electric wiring.
Because the electric control principle of SMC series electric actuators are in wide range, the electric control
ཙҼ䙊7(7
haft of
ft of
f the valve (Ite valv
tor, make the driving
make the dri
ts reliably.eliab
ble, then loose the tightenthen loose the tig
ctrtr
ic actuator, only alloic actuator, only
em with the valve).with the valve)
ecessary toary to
clean the valclean the v
necessary to ensussary to ensu
re that thre that
valve place in the pipeve place in the p
nce or inspection for the elce or inspection for th
the mounted electric actue mounted electric
mmended to make the mo
mended to make the
al position facing upwa
position facing upw
position.osition
it
i

8
principle diagram which used in practice behind the instruction as an attachment. The terminal contrast table,
electric element data table are on the Basic electric control principle diagram.
Procedure and precaution for wiring:
7.1 Confirm that power supply voltage is identical with motor voltage shown in the name plate.
7.2 For actuators SMC-04, 03, 00, 0, 1, 2, without field push button lamp box, before wiring, remove the
G.L.SW cover (the cover with indicator window), the G.L.SW upper and front terminal plates are visible. The
wire inlet holes are located at the lower, upper or the side of the main housing.
For actuators SMC-04, 03, 00, 0, 1, 2, with field push button lamp box, before wiring, remove the G.L.SW
cover and T.SW cover (the cover at the other side of the main housing). The wire inlet hole is also located in
T.SW housing because generally the wiring terminal board is inside the T.SW housing.
Before wiring remove front square cover for various type SMC-3,4,5 products because G.L.SW and T.SW
located in same housing for above products, wire inlet hole is located down or upper of the main housing.
7.3 Connect the core wire and power cables to corresponding terminals separately according to wire numbers
shown in the electric control principle diagram. The wiring connection should be tightly and reliably(The
wiring between the electric actuator and controller also should conform to the corresponding terminal
number.)
7.4 The external ground bolt of the electric actuator is located on the main housing. The ground connection
of the products must be secure and reliable.
7.5 Inspect the phase sequence of power supply: Turn manually the valve to its middle position. Then press
“open” or “close” push button and ensure that the valve moving direction is identical with the control
operating direction. Otherwise exchange the phase sequence connections on the motor.
7.6 Thermorelay (KH): Function of thermorelay is to protect the motor against damage when trouble occurs
on wiring switch. Value of the thermorelay is set so that the motor can be stopped when trouble occurs. It can
be adjusted as follows: With starting current: Acts about 10 sec later.
With rated current: No action within rated period, (Caution: The wire inlet hole of electric actuator is
a thread hole, normally set a coiled pipe screws into the thread hole to protect the cable and
ensure integral machine sealing performance, the position and dimension of the thread hole can
see the catalogue of our company. If it is not set the wire inlet, after wiring of product also
should provide suitable sealing measure, if it is not, that would affect its outdoor performance.)
8. Adjustment of G.L.SW
Refer to Fjg.16, 4R-2C is shown in the figure. If another set of 4R-2C is added, then a 4R-4Cmechanism is
resulted, so the volume will be increased to the place shown in dotted lines.
In case no special requirements are given and the driving sleeve is in normal rotating direction (right for
valve closed):
ƸThe rotor of row 1 is used to control Valve open position.
ƸThe rotor of row 4 is used to control value close position.
ƸThe rotor of row 2, row 3 are used separately in the processes of open-close and close-open to control
any one position or to provide signal for the end position of valve open or valve close.
ƸThe “Adjusting axle” number (1), (2),(3), and (4) corresponding to the above mentioned rotor are used to
adjust separately the corresponded rotors.
ƸNumber (5) designated “Adjusting screw” is used to control in side gear disengaged or meshing.
8.1 Close position adjusting of valve (adjustment of rotor of “row 4”).
Ensure the phase sequence of power source is identical with the direction “open” and “close” of the valve
before adjusting. If it is not clear whether the phase sequence is right, according to the above 7.5.
Be sure to cut off the power before adjustment.
a. Turn the valve toward close direction manually. Remember the direction of rotation “Adjusting axle” No.
(4), Operate the valve manually to full close position and then stop it. (Carry on the exact adjusting after
ཙҼ䙊7(7
m t
e main housing.ain hous
ally the valve to its middl
the valve to its mid
e moving direction is idmoving direction i
ence connections on the mnce connections on th
to protect the motor agaito protect the motor a
t so thathat
the motor can bethe motor ca
tt
Acts about 10 sec later.about 10 sec later.
ted period,er
(Caution: Th(Caution: T
iled pipe screws intopipe screws
ing performance, therformance, th
e p
company. If it is notompany. If it is n
le sealing meassealing m
ure, if ite,
L.SW
SW
C is shown in the fs shown
be increasere
nts
s

9
initial adjusting of the close position so that the adjusting would be more reliable for some multi-turn valve.
The certain allowance is dependent on the valve operating experiences of customer).
b. Now observe the rotor switch 8A-8B for controlling motor power, the Fig. 17 shows No. (8) switch will
occur two cases:
1. The power switch 8A-8B is in “on” position.
2. The power switch 8A-8B is in “off” position
c. Screw in slightly the “Adjusting screw” No.(5) with a screw driver to certain degree and try to turn the
adjusting shaft No.(4), if it can be moved, this means that the intermittent gear is disengaged and adjustment
can be done.
d. The detail adjusting methods for above two cases are as follows:
First case: 8A-8B is in “ON” position, which means that power is not cut off. It is necessary to turn the
adjusting axle with a screw driver toward the direction in which the adjusting shaft (4) should be turned
during closing of the valve manually. It should be stopped until rotor of row(4) is turned for 90 so that 8A-8B
is in “OFF” position.
Second case: 8A-8B is in “OFF” position, i.e. power is cut off in advance. It is necessary to turn the
adjusting shaft NO (4) with a screw driver toward the direction reverse to the direction that it should be turned
during closing the valve to make the rotor of row (4) turned for 90 to 8A-8B “ON” position and then turn the
adjusting shaft (4) a little make 8A-8B disengaged. (The direction reverse to that of the screw driver during
adjusting).
When the above mentioned adjustment is accomplished, slightly screw out the “Adjusting screw” (5) back
anti-clock wisely until it can not be rotated. Then turn slightly the “Adjusting axle” (4) with a screw driver. If
it can’t be turned, it means that the internal gears have been properly meshed. Now adjustment of the full
close position of the valve is accomplished.
(Caution: Observe the motion of the rotor switch during adjusting to prevent the counter
mechanism from over adjusting or disorder. Screw out the “adjusting screw” NO.5 after
finishing the adjusting.)
e. Energize the actuator and inspect it:
Actuate the valve manually to its middle position. Connect power. Actuate the valve electrically to move the
valve toward close direction. When the electric actuator make the valve to the close position, 8A-8B rotor
switch can cut off power supply to stop the motor, it is ensured that the adjusting is correct.
8.2 Adjustments of valve full open position (“row 1” rotor switch adjusting)
Cut off power supply before adjusting.
a. Make the valve move toward full open direction manually. Remember the rotation direction of “Adjusting
shaft(1). Operate the valve manually to full open position and then stop it. (There should be certain allowance
from full open position to limit position for some multi-turn valves)
b. Watch the rotor switch 4A-4B for controlling the power supply for the motor, i.e the switch.
NO.4 shown in Fig 17 may be in two cases. “ON” or “OFF”.
c. Screw out the “Adjusting screw” No.5 with a screw driver to certain degree and try to turn the “adjusting
shaft” No.1. If it can be moved, this means the intermittent gear is disengaged and adjustment can be done.
d. Procedure of adjusting for the two different cases:
Refer to 8.1 “d”, but in this Procedure “adjusting axle” NO.1 and the adjusted rotor switch 4A-4B should be
used for adjusting.
(Note: Screw out the “adjusting screw” NO.5 after adjustment stroke of the actuator and inspect
it.)
8.3 Accurate adjusting
If the valve switch position is not reached after the initial adjusting, accurate adjusting should be carried
out.
ཙҼ䙊7(7
an
the direcdire
8A-8B “ON” po8B “ON
n reverse to that of the
everse to that of t
slightly screw out the “Aghtly screw out the
lightly the “Adjusting axlightly the “Adjusting
haha
ve been properly meshve been properly m
e rotor switch duringr switch during
or disorder. Screw ouisorder. Screw o
pect it::
o its middle position. Conits middle position.
on. When the electric acn. When the electri
er supply to stop the moto
supply to stop the m
ve full open position
ull open
e adjusting.ti
rd fullfu

10
Following is the procedure of “close direction” exact adjusting as an example.(including two cases)
a. When the valve close position is not reached (after power-operated), properly actuate the valve manually
to reach the close position from the initially adjusted position. Screw out “Adjusting screw” No.5 to make it
internal gears disengaged. Now the rotor switch 8A-8B is in “OFF” position, carry out adjusting and
inspection according to the second case in 8.1d-e.
b. After the valve is closed, the T.SW acts, but the rotor switch 8A-8B is in “ON” position. If T.SW act is
unwanted, it is possible to actuate the valve manually toward open direction and reaches the reasonable
position under the prerequisite to ensure the valve is closed. Screw out “Adjusting screw” NO.(5) and make
the internal gears disengaged. Up to now, 8A-8B is in “ON” position, so should carry out adjustment and
inspection accord to 8.1d-e, first case.
(Caution: Screw out “adjusting screw” No.(5) after finishing the adjustment.)
The exact adjusting means: When the valve switch does not reach “ON” or “OFF” position, adjust the rotor
switch slightly delay and make it disconnected. If the valve switch slightly over “ON” or “OFF” limit, should
turn the rotor switch a little advance to cut off.
Sometimes only need to turn adjusting axle a little angle, 1~2 gears on the counter unit-digit gear.
8.4 Adjustment the intermediate position of valve (Adjustment of rotor of row 2 and row 3).
The position of rotor switch row 2 and row 3 shall be set as requirements. They can be used as terminal
signal output, and can also be used as intermediate position signal output. Procedure of adjusting of above
mentioned two row rotor switch please refer to the contents of 8.1-8.3 section.
9. Adjustment of position indicating system(MDPI)
Refer to MDPI mechanism is shown in Fig 19 during adjustment.
The gear of potentiometer of the actuator is out of meshing when delivered.
9.1 Adjustment of “0” position for valve close;
After G.L.S.W is adjusted (or when it is being adjusted), drive the valve to its close position electrically.
Loosen the fix screw of the pointer of mechanical indicator and se the pointer in “0” position, and then tighten
the fix screw.
Turn the movable arm of the potentiometer to its initial position and turn it back a little. This location is the
zero position of the potentiometer, loosen the screw on the gear of potentiometer and push the gear into
meshing position, and then tighten the screw again. (In this design, the rotation direction of the movable arm
of potentiometer and that of the pointer of position indicator are the same. Therefore the zero position of the
potentiometer is consistent with that indicated by the pointer of indicator.)
9.2 Adjustment of valve open 100% position.
When driving the valve electrically to full open position, the pointer should be in the point 100%. If any
slight deviation exists, move the pointer to correct position. If much deviation exists, adjust the valve open
position corrected. If the deviation is too much, it is necessary to inspect for mistakes in model selection or in
manufacturing.
9.3 Inspection
The inspection of the position indicator system includes G.L.S.W contact signal.
After the valve is driven to close position and stops automatically, now the pointer of MDPI should be in “0”
position and the valve open indicator lamp is lighted up.
After the valve is driven to open position and stops automatically, now the pointer of MDPI should be in
“100%” position and the valve open indicator lamp is lighted up.
The pointer of the position indicator on the controller should be in corresponding position when it is in
“ON” “OFF” position. If not, it can be adjusted by the potentiometer that located on controller.
10. Adjustment of torque switch mechanism (T.SW)
The adjusting section of the torque switch shown in Fig 15.
The output torque values (MK) in both open and close direction are controlled by T.SW that was set before
ཙҼ䙊7(7
cou
of row 2 anow 2 a
uirements. They c
ments. Th
nal output. Procedure o
output. Procedure
8.1-8.3 section.-8.3 section
)
g adjustment.adjustment.
f meshing when deliveredf meshing when delive
being adjusted), drive thdjusted), drive th
echanical indicator and senical indicator and s
otentiometer to its initial pometer to its init
meter, loosen the screweter, loosen the scr
n tighten the screw again.tighten the screw ag
hat of the pointer of posit
t of the pointer of p
tent with that indicate
with that indicate
pen 100% pospen 100%
ctricallyca

11
dispatch. The set value is slightly greater than or equal to the maximum torque (MV max) needed for opening
and closing the valve. The user need not adjust it.
10.1 In case that “Torque positioning method” is used, if the valve can not be hermetically closed after T.SW
acts, and there is certain distance between the indicator and the limit plate, you may adjust the indicator
toward the limit plate to increase value MK. If adjustment can’t be done any more, inspection must be made
according to point 1,2 in table 1. If everything is normal, this means that the actuator selected is smaller than
that needed. Its output torque does not meet the requirement.
10.2 In case that “Torque positioning” method is used, if the sealing force of the valve can’t be determined
accurately, in order to reduce excessive unit pressure for hermetic closing of the valve, you may firstly set a
smaller value MK1, (MK1<MK) according to the “Torque switch graduations-output torque” curve on the
products ex-factory test report. Find out the position of the indicator from the curve and set the indicator in
this position. If hermetic closing can’t be realized with such set value, increase value MK1 gradually until
hermetic closing is realized.
11. Precautions for operation and maintenance.
11.1 The valve stem cap or the pipe tap on the top of the actuator must be tightened reliably. When the valve
stem cap or the pipe tap is removed for maintenance, it is necessary to cover the top of the actuator to avoid
falling in of foreign matters.
11.2 The glass of position indicating window should never be hit by solid matters.
11.3 Do not carry out outdoor installing or open the cover of the G.L.SW box, the T.SW box and other
electric hermetic position.
11.4 After maintenance and adjusting have been carried out, it is necessary to mount up and tighten the parts
for sealing the electric components and care should be taken to keep the sealing rings not lost to avoid
invading of moisture and rain water which may cause the electric components malfunction or parts damaging.
11.5 When opening the enclosure of electric assembly, it is necessary firstly to cut off the power.
11.6 The power of motor depended on output torque, speed of the actuator. The user should never replace the
motor arbitrarily.
11.7 Should never remove or reduce the limit plate of the torque
11.8 In case of “Torque positioning”, the spring cover of torque should never loose or remove (The spring
cover of torque of SMC-04,03 located on the position of manual/electric changeover axle, the spring cover of
torque SMC-00~4 located on the position of handwheel axle.)
11.9 After the manual/electric change lever is set in “Manual position, do not move it to “electric” position
artificially.
To conduct manual/electric changeover, press the lever down as indicated by the arrow referring to the
nameplate on the lever. If not seated, turn the handwheel appropriately.
11.10 When manual operation is to be conducted, do not turn the handwheel forcibly by way of adding a
sleeve or inserting a rod.
11.11 When the actuator has been removed from the valve to be serviced and then mounted again, it is
necessary to adjust the G.L,SW before putting it into operation.
11.12 In case that the actuator is rarely used, a scheme of periodical starting and inspection of electric valve
should be made if the production process allows to do so.
11.13 Ground bolt and ground cable of the actuator should be connected reliably.
11.14The design service life of actuator is 8000 times.
11.15 According to the regulations on the recycling and treatment of waste electrical and electronic products,
please comply with the relevant national regulations and properly dispose of waste products. Or call our
after-sales service department for recycling. Tel: 022-26740033.
11.16 Service commitment: When the equipment breaks down, please contact the technical responsible
person appointed by our company at first, and we will provide processing opinions and technical support
ཙҼ䙊7(7
igh
cover the ter the
by solid matters.solid matters.
r of the G.L.SW box, the
f the G.L.SW box,
ed out, it is necessary to md out, it is necessary t
uld be taken to keep theld be taken to keep
cause the electric componause the electric com
c assembly, it is necessambly, it is necessa
ryry
output torque, speed of thet torque, speed of th
uce the limit plate of the the limit plate of t
tioning”, the spring coveoning”, the spring c
4,03 located on the positio03 located on the po
ted on the position of hand
d on the position of
l/electric change lever
ric change leve
changeovg

12
within 24 hours. If necessary, we will send technical personnel to the user site within 72 hours in the city, 3-5
days reaches the user site according to the distance outside the city until the problem is solved.
Complaints Tel: 022-26740033; Hotline: 022-26740033
(Note: The electric actuator should be stored in dry and non-corrosive circumstance.)
12.Trouble-shooting and remedy
Table 1
Trouble Cause Remedy
1. Motor can’t started. 1. No power supply.
2. Too low power voltage.
3. Thermore lay (KH)acts.
4. T.SW acts.
5. Operation torque of valve is too high.
1. Inspect power supply.
2. Inspect voltage.
3. Wait for KH restoring to normal state.
4. Adjust T.SW to increase torque.
5. Forcibly starting.
6. Inspect valve.
2. Motor stops during open or
close operation.
1. T.SW act caused by overload.
2. Thermorelay acts.
3. Poor status of valve, excessive load.
1. In crease set value of torque if maximum
output torque allows.
2. Adjust thermorelay
3.1 Inspect valve and correct it into normal.
3.2 Operate the valve periodically if possible.
3.Motor can’t be stopped by
G.L.SW
1.The motor runs in reverse direction
2.Misadjustment of switch
3.Reset of screw is forgotten after
adjustment
4.Trouble on control power source
5. The gear of limit switch is damaged
1.Reverse the phase sequence
2.Readjust
3.Reset the adjusting screw
4.Inspect and remedy
5.Inspect and replace it with a new one if
necessary.
4. T.SW, G.L.SW acts, but the
motor can’t be stopped.
1.The motor runs in reverse direction
2.Trouble of grounding
1. Reverse the phase-sequence.
2. Inspect and measure resistance.
5. Indicating lamps for full open,
full close can’t be lighted up.
The T.SW acts, but the valve has not been
seated in position
Adjust T.SW
6.Remote position indication not
effective
1. The gear of signal output potentiometer
becomes loose so that the potentiometer
axle couldn’t be turned.
2. Improper power supply
3. The potentiometer is damaged.
1.Tighten the screw
2.Inspect the power supply
3.Replace it with a new one
7.The motor runs but valve is not
actuated
1. The Manual/Electric change over
mechanism is abnormal.
2.Locknut becomes loose
1. Dismantle, inspect and restore it to normal
operation.
2. Tighten and chisel the locknut
8. Manual operation can’t actuate
the valve.
The jaws of clutch and jaws of handwheel
body are out of meshing.
Turn the hand wheel a little to bring the jaws
into meshing.
9. Valve stem vibrates during
starting.
Stem nut becomes loose or improperly
tightened.
Dismantle the stem or pipe tap and tighten the
locknut.
10.Improper insulation Invasion of rain water (improper sealing
of wire in wet)
1. Repair sealing parts.
2. Dry the electric elements and motor.
3. Pay attention to the sealing of wire inlet
11.Oil leakage 1. Sealing is damaged.
2.The ambient temperature is too high.
Internal pressure of main horsing rises up.
1.Inspect and repair
2.Loosen a screw which not affecting
working to vent air out (oil plug is preferred)
ཙҼ䙊7(7
rease
put torque atorque
2. Adjust thermordjust th
3.1 Inspect valve and c
3.1 Inspect valve an
3.2 Operate the valve
3.2 Operate the va
7(
tion
forgotten afterforgotten
rol power sourcepower source
f limit switch is damagedtch is damaged
1.Reverse the phaReverse the
2.Readjustdjus
3.Reset th3.Re
4.InspI
5
7(7
䙊7(
or runs in reverse directionns in reverse direction
uble of groundingf gr
Ҽ䙊
he T.SW acts, but the valve hW acts, but the valv
seated in positionsea
Ҽ
ཙ
notot
1. The gear of signal ouhe gear of sign
becomes loose sobecomes loose
axle couldn’t bxle couldn’t b
2. ImproperIm
3. The pTh
ཙҼ
ཙ
ཙ

13
Part II SMC series integral type operation manual
1. Summary
SMC series Integral type of electric actuator includes Standard Integral type and Explosion-proof Integral
type which are on the basis of SMC Standard type and SMC Standard explosion-proof type, mounting a
integral electric control components. Thus, SMC(Ex.)IN series are born, whose type includes
SMC-04(Ex.)IN~SMC-4(Ex.) IN. Because AC Contactor of single controller and other electric component are
added in the electric actuator; besides, there is local control buttons on the control case through which the
electric actuator can achieve the converting control between local and remote. Other part of the electric
actuator is the same with SMC Standard(explosion-proof)type so that it is convenient for the user to operate or
to debug.
2. Function and features
SMC series Integral type of electric actuator has provided several of electric control means and functions.
Users make his choice according to their needs. Major functions and features:
2.1 Automatic phase-discriminator; phase-loss protection
2.2 DC24V is applied for remote control; with a convenient wiring connection means.
2.3 Dry contact indicates working status of the electric actuator, which is convenient for DCS system to
monitor the electric actuator.
2.4 Set up the electric actuator’s monitor relay, which provides comprehensive signal for DSC system.
2.5 With the functions of stroke limit protection, torque protection, overheated protection,
motor-overcorrect/current-leakage protection, stalled protection and operating direction converting protection,
etc.
2.6 4~20mA valve position signal feedback.
2.7 4~20mA valve position control.
3. Notes:
3.1 Please refer to the attached schematic diagram for product’s functions and control methods
3.2 Connect the wires according to the attached schematic diagram’s terminal No., and should be careful to
seal all the inlet wire parts.
3.3 Debugging for this product is the same as SMC Standard type. Please refer to Part I.
3.4 Should fix the case’s cap reliably after debug the product so as to ensure the product’s outdoor
performance.
3.5 Don’t have the Integral case body hit by any outside force while the product is being mounted or used.
3.6 Please refer to SMC Standard (Explosion-proof type) type operation manual for other notes.
ཙҼ䙊7(7
nnection meanction m
r, which is convenien
which is conve
ides comprehensive signas comprehensive si
ctio
n, torque protectiotorque protec
protection and operatingprotection and opera
hematic diagram for produatic diagram for p
ing to the attached schemsch
product is the same as
roduct is the same as
SM
case’s cap reliably aft
se’s cap reliably a
case bodybo
rd
d

14
Part III SMC explosion-proof type operation manual
1. Summary
This part is the attached instruction for SMC explosion-proof type. When this type is applied, carefully read
Part III besides following the mounting and debugging methods in the Standard type instruction, so as to
ensure the product’s explosion-proof performance.
SMC explosion-proof type electric valve actuator(herein after referred as “electric actuator”) is designed
and manufactured on the basis of GB/T 3836.1ljGeneral Requirement for the Equipment Used in Explosive
Environment, Part INJand GB/T 3836.2ljThe Equipment Protected by Explosion-proof Enclosure “d” Used in
Explosive Environment, Part IINJ. The product’s technical documents, product sample and components are
entirely have been tested, experimented and finally verified by the national verified explosion-proof
organization. SMC series have achieved Conformity Certificate of Explosion-Proof issued by the above
organization.(Pay attention to the nameplate which includes the product’s technical conditions serial No. and
the Certificate of Explosion-proof No.).
SMC explosion-proof type includes three types:
1) Standard explosion-proof type: without local button light box and explosion-proof controller.
2) The type with local buttons light box: explosive-proof local button light box is added on the basis of
the Standard type
3) Integral type: explosive-proof controller is added on the electric actuator, with local buttons light box.
To be clarified, the different size of 4R-4C and 4R-2C is due to the inner different stroke and different
indication mechanism structure (4R-4C has 16 contacts and 4R-2C has 8 contacts.).
2. Instruction for explosion-proof performance:
The type of this product is the entire product explosion-proof type (including explosion-proof motor).
Every explosion-proof case and the major case form the entire explosion-proof case which can bear the inner
explosive gas pressure and prevent inner explosion transmit to the outside of the body case(that is, when
explosion happened in the inner side , that will not ignite outside part). Explosion-proof grade is Ex db IIB T4
Gb.
Ex db IIB T4 Gb---IIB Class T4 temperature electric apparatus. The sign “Ex” shows that the electric
apparatus comply with the Explosion-proof Standard; “db” shows that the explosion-proof type is enclosure
explosion-proof; II class represents that electric apparatus used in explosive gas environment except for gas
made from coal; IIB represents that the gas is ethylene; T4 indicates that the permissible surface temperature
is 135ć˗Gb is apparatus protection degree.
3. Usage and maintenance notice
Besides the No.11, Part I of this Operation Manual “Usage and maintenance notice”, pay attention to the
followings:
3.1 Cut off the power supply when open the electric cover box or case (pay attention to the Warn Notice
“Forbid to open the case with power supply”)
3.2 Protect the nameplate and warn notice plate from being damaged; keep it on hanging on the electric
actuator and keep the words on it be clear and readable.
3.3 Request the manufacturer to renew the components or parts while it is damaged. Don’t start electric
operation before mount the renewed components.
3.4 Fixed screws on the explosion-proof unit reliable. Check out its reliability performance when it is being
used in vibration condition.
3.5 Take care not to lose the sealing ring and renew it after it is damaged.
4. Schematic diagram for electric control and explosion-proof terminal board
If there no special control requirement, the manufacturer will provide three standard schematic
nd explosion-pexplos
l button light box is
utton light bo
the electric actuator, withelectric actuator, w
-2
C is due to the inner dis due to the inner
ts and 4R-2C has 8 contacs and 4R-2C has 8 c
nce:e:
oduct exuct ex
plosion-proof typplosion-proof t
case form thee form the
entire explentire exp
nner explosion tranexplosion tran
smit tsmi
de , that will not ignihat will not igni
te outte o
Class T4 tempass T4 t
erature eleure
he Explosion-proof Stand
e Explosion-proof S
ass represents th
represents th
at electrat elec
esents that the gaents tha
rotection dio
otic
ti

15
diagram(attached in the manual operation) to suit for three types mentioned in the Summary. User can identify
its kinds according to the nameplate.
In the standard schematic diagram, D1, D2, D3 and N are aligned with U,V,W,E on the terminal board(that
is, D1UˈD2VˈD3WˈEN). Other wire No. is totally aligned with the terminal No.. Unconnected
terminals could be seen as spare parts.
If user has special requirements on control parts or has offered the schematic diagram to the manufacturer,
there is attached schematic diagram in the end of this manual operation.
5.The position of the wiring outlet
There are three plugs and user should back out while using it. Use appropriate outlet unit which is aligned
with the outlet hole’s thread (the outlet unit should comply with the explosion-proof standard GB/T 3836.1
and GB/T 3836.2). Pay attention to the enclosure protection to ensure the protection grade. The wire outlet
unit is offered by user. Keep the unused outlet in the state before delivered.
6.Wiring procedure for the apparatus
6.1 Open the “wiring case” and back out plug.
6.2 Choose appropriate cable outlet unit according to the size of cable and wire outlet screw hole.
6.3 Screw in the cable outlet unit and seal it properly so as to keep the product in its origin protection grade.
6.4 Connect the “lug plate” with the wire core of the cable by using electric tool.
6.5 Connect the wire cores which with “lug plate” to the corresponding terminals according to the schematic
diagram. The lug plate should be lifted upwards.
6.6 Check out whether the cable position is right before make sure the wiring is correct.
6.7 Close the “wiring case” and screw it tightly.
7. Others:
As the sealing ring could be damaged after several mounting and dismantling, contact the manufacturer
when it is damaged.
The screws of the contacts U,V,W,E on the terminal board applies M6 and others are M4. User chooses “lug
plate ” according to its size.
ཙҼ䙊7(7
wire
roduct in itduct in
electric tool.ctric tool.
ponding terminals accord
ding terminals acc
make sure the wiring is core sure the wiring is
r several mounting and dseveral mounting an
n the terminalter
board apploard app

16
Part IV SMC-04SMC-2 low-temperature operation manual
1. Summary
This part is the instruction for SMC-04~SMC-2(including the Explosion-proof type, Integral
explosion-proof type and combined quarter-turn type) low temperature type of electric actuator.
When low temperature type is applied, for mounting and debugging, refer to the manual operation of
standard type of electric actuator; besides, read carefully and comply with this part of instruction so as to
ensure the product’s low temperature performance.
SMC-04~SMC-2 low temperature type of electric valve actuator is manufactured on the basis of GB/T
24923 and GB/T 2423.1, and is verified by national verified explosion-proof organization from which the
products achieved Certificate.
2. Classification of low temperature type
According to low temperature range, the kind of product can be classified into two types: Low temperature
I and Low temperature II.
The lowest temperature range for Low temperature I: above -20ć~-40ć
The lowest temperature range for Low temperature II: above-40ć~-55ć
3. Notes:
When this kind of product is used in low temperature, it should be kept powered on. This kind of product
has been coated with low temperature lubrication. If it is need to be changed or to be added, please initiate the
manufacturer to know the type of low temperature lubrication.
When this kind of product is used in a relative high temperature(the highest could be up to 40ć) , it is
better not to have the product being powered on. Because it is in favor of the product performance and usage.
4. Others
When the spare parts of the products are damaged due to several times of mantling and dismantling, user
shall ask the manufacturer for the spare part list so as to change new spare parts which are suitable for low
temperature use.
ཙҼ䙊7(7
ć
55
ćć
ould be kept powered on.
d be kept powered
ed to be changed or to beto be changed or to
cation.ati
high temperature(the highhigh temperature(the
Because it is in favor of thcause it is in favor
are damaged dueamaged due
to severto seve
are part list so asart
to chano c

Special warning
To ensure the actuator complete unit’s outer housing properties, during adjustment and maintenance, the
user should operate according to the operation manual and this special warning! If the user does not operate
correctly or does not operate according to the operation manual and special warning and causing the actuator
out of the factory, all the parts related to outer housing protection have been inspected strictly and be ensured
to be well sealed. If the user open the following parts due to the needs of adjustment or maintenance:
control box cover
wiring box cover
wire outlet assembly
after opening, the user must ensure:
during the operation of adjustment maintenance or some needed, at that time the actuator does not have the
precious protection properties, the user should ensure that it is kept from the invasion of rain, snow, hail,
moisture, dust and so on.
after operation, when the cover is put on or the wire outlet is tightened, the user should ensure that the opened
parts inside does not have any disadvantage elements such as water, dust moisture that may led to the
protection properties damaging.
after operation and the cover is put on, the user should ensure that all the fixing screws and the flat spacer and
spring spacer on the box cover should be tightened, with no phenomenon of leakage or loosening. at the
same time, the user should ensure that the rubber sealing ring which function as sealing part at the
contacting part of cover box and housing, does not be damaged and be painted calcium grease, and then
assemble as previous.
after the wire pass through the wire outlet, the user should ensure to tighten the tightening nut, to ensure
sealing. The screw sealing between the tightening nut and housing must have PTFE. At the same time, the
cable and tightening nutinner holes must be painted sealing (such as 609).
if other parts such as position window or local button, is opened due to some causes. And reassembled, the
user should ensure that the sealing is not affected with disadvantage.
Tianjin Baili Ertong Machinery Co., Ltd.
Address: No. 19, Taikang road, Dongditou industrial zone, Xiditou town, Beichen district, Tianjin
Tel: 86 22 26750313, 84911766, 84911866, 26154275
Zip code: 300408
http://www.tet.cn
Email: scb@tet.cn
Our Company reserves the right to amend this operation manual.
ཙҼ䙊7(7
user s
er s
ater, dust moi, dust
at all the fixing screws an
all the fixing screws
th no phenomenon of leakno phenomenon of
sealing ring which funsealing ring which f
not be damaged and be pot be damaged and b
the user should ensure tuser should ensure
e tightening nut and housghtening nut and hou
s must be painted sealingst be painted sea
ndow or local button, is oor local button,
sealing
is not affected wicted
This manual suits for next models
3
Table of contents
Popular Controllers manuals by other brands
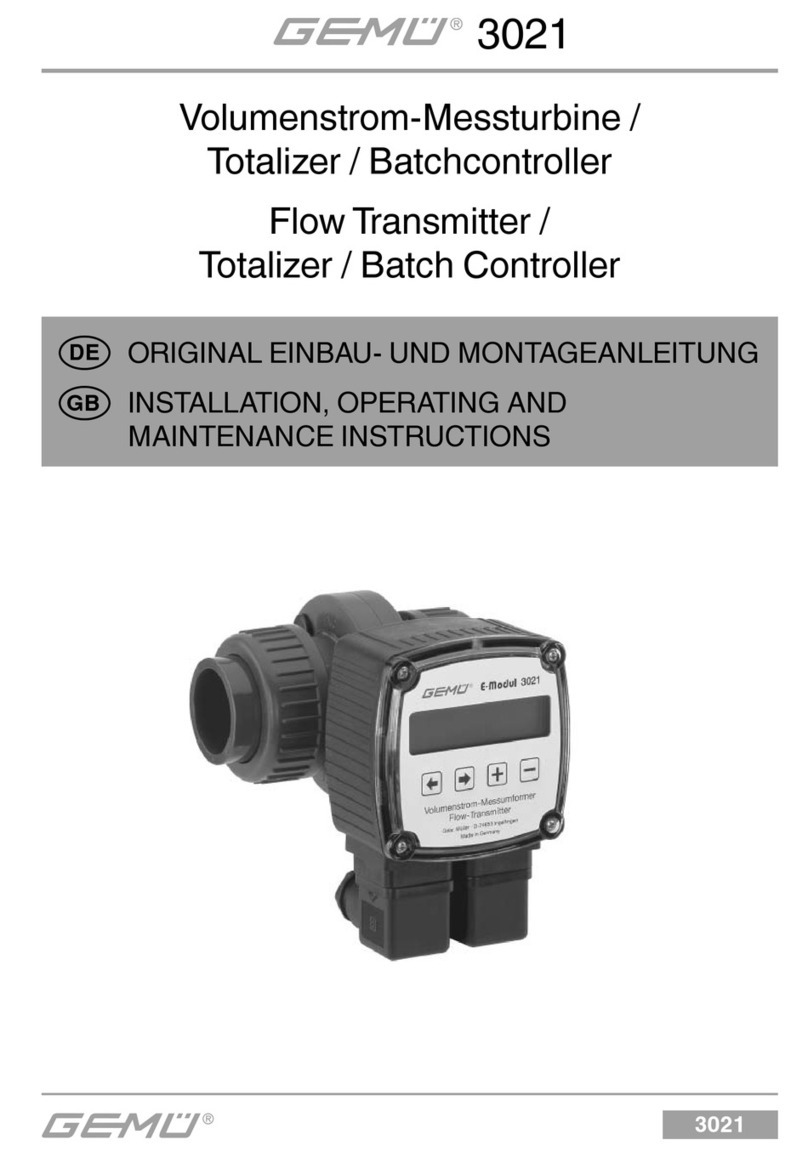
Gemu
Gemu 3021 Installation, operating and maintenance instructions
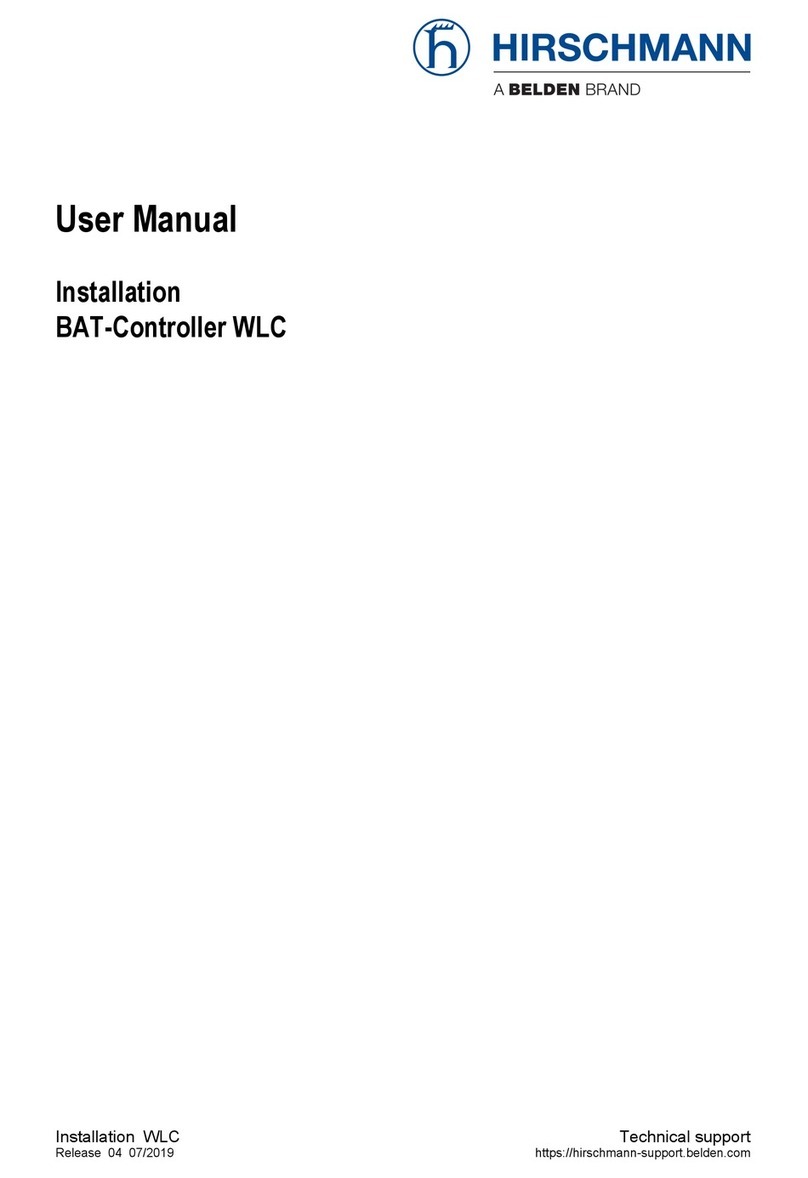
Belden
Belden Hirschmann BAT-Controller WLC Series user manual
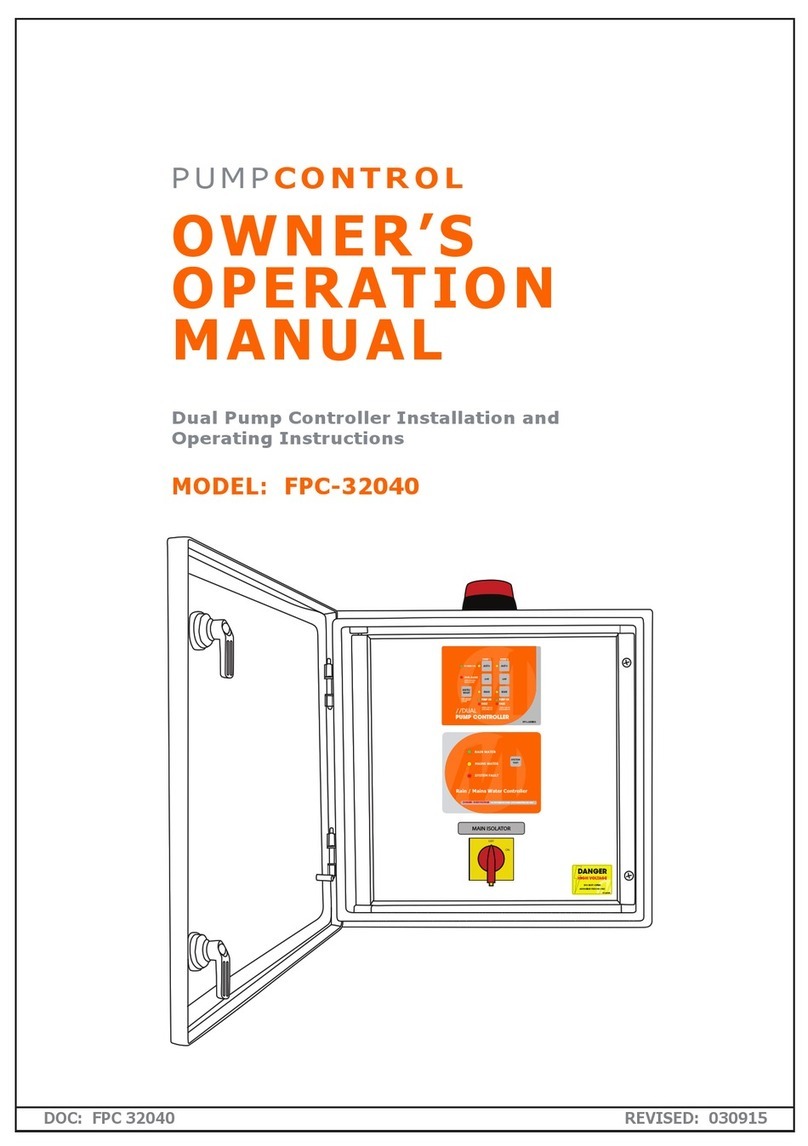
PUMP CONTROL
PUMP CONTROL FPC-32040 Owner's operation manual
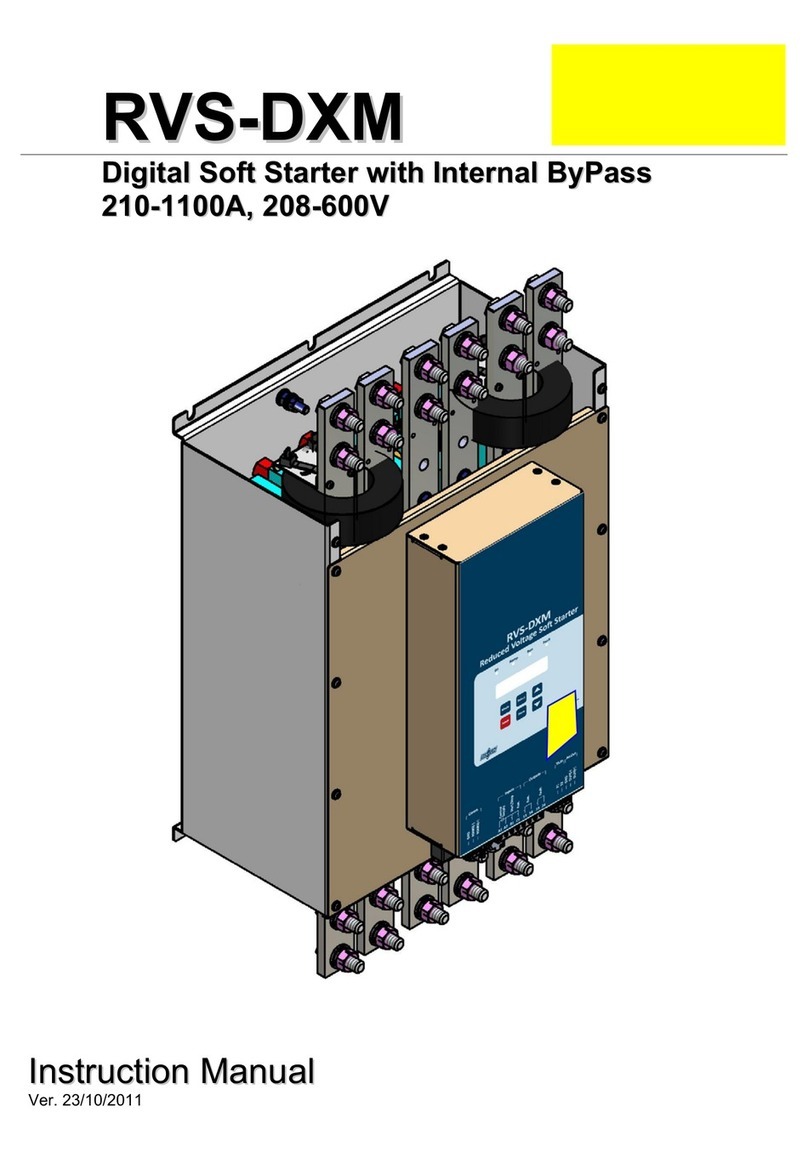
Solcon
Solcon RVS-DXM instruction manual
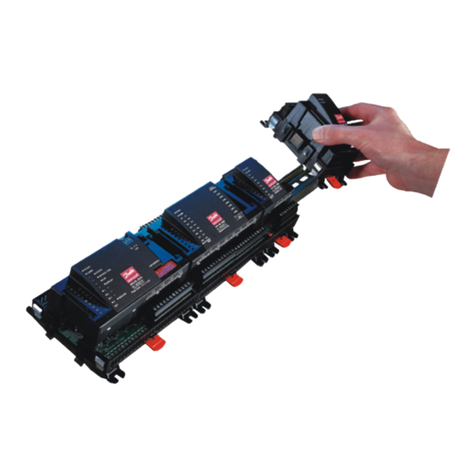
Danfoss
Danfoss ADAP-KOOL AK-PC 781 user guide

Thermaltake
Thermaltake HARDCANO 13 user manual