Balluff SMARTCAMERA IO User manual

english
BVS SC-_1280Z00-07-0_0
SMARTCAMERA IO
User's Guide

www.balluff.com
Original user's manual
All rights reserved. Protected within the legally permissible limits of the United States and internationally. This document may
not be copied or modified without prior written permission from Balluff.
All the trademarks and names appearing here are for identification purposes only. Some of these trademarks may be regi-
stered trademarks of the respective owners.
Balluff is not liable for any technical or printing errors, removal of the text contained herein or unintended damage resulting
from use of the material.

www.balluff.com
3
BVS SC-_1280Z00-07-0_0
SMARTCAMERA IO
english
1 User Instructions 4
1.1 Introduction 4
1.2 Typographical Conventions 4
1.3 Abbreviations 5
1.4 Copyright 6
1.5 Legal Requirements 6
1.6 Updates and Upgrades 6
1.7 Trademarks 6
2 Safety 7
2.1 Intended Use 7
2.2 General Safety Notes 7
2.3 Meaning of Warning Notes 7
2.4 Disposal 7
3 Product Description 8
3.1 Product Variants 8
3.2 Scope of delivery 9
3.3 Assembly 10
3.4 Product specification 11
3.5 Connections and Pin Assignment 12
3.6 Display elements 20
3.7 Cleaning 20
4 First Steps 21
4.1 Step 1: Establishing a network connection with the SMARTCAMERA 21
4.2 Step 2: Switching on the SMARTCAMERA 21
4.3 Step 3: Opening the BVSCockpit web interface 22
5 Commissioning 23
5.1 Network Topologies 23
5.2 System Settings 24
5.3 Selecting the Communication Interface for the Process Data 24
5.4 Network Settings / LAN Interface 25
5.5 Locating the Camera in the Network 25
5.6 Digital I/O Interface 26
6 Communication Functions of the LAN Interface 28
6.1 General Information 28
6.2 Structure of the Messages 28
6.3 The Individual Messages 29
7 Appendix 32
7.1 Type Code 32
7.2 Accessories 32

4
1User Instructions
BVS SC-_1280Z00-07-0_0
SMARTCAMERA IO
english
These operating instructions describe the SMARTCAMERA product from the Balluff Vision
Solution BVS SC product family as well as the data interfaces and the startup for an immediate
operation.
The web-based software interface integrated in the SMARTCAMERA is described in the sepa-
rate software manual (BVS Cockpit manual).
Both manuals are available on the Balluff product website via www.balluff.com or via the help
system of the BVS Cockpit interface.
The SMARTCAMERA was developed to identify objects in automated industrial environments
via optical codings (barcode, 2D codes or plain text) and to recognize and verify characteristics
of objects such as presence, contours, dimensions, colors and positions. THe test results can
be processed in a flexible way and forwarded to the higher-level control system. Some outstan-
ding properties are:
– Complete camera control and evaluation integrated in the device
– Simple camera access from the network
– Simple and user-friendly settings, control of camera without additional software
– Easiest, user-supporting operation
– Support of Industry 4.0 through IO-Link
– Separate data channel for larger data volumes
– Integrated, flexible displays of process statistics
These characteristics make it possible to easily create test and identification tasks in automation,
to flexibly check the status of the test process, to monitor long-term processes in a clearly
arranged way.
Hence, the SMARTCAMERA perfectly supports logistics processes and quality assurance in
different industries.
These operating instructions apply to the following variants of the SMARTCAMERA:
Order code Product name Description
BVS002C BVS SC-M1280Z00-07-000 SMARTCAMERA
Monochrome IO
BVS0028 BVS SC-M1280Z00-07-010 SMARTCAMERA Ident
Monochrome IO
BVS002E BVS SC-C1280Z00-07-000 SMARTCAMERA
Color IO
Balluff GmbH completes the customer offering with a distinct service and accessories palette.
The following conventions are used in this manual:
Enumerations
Enumerations are shown as a list with an en-dash.
– Entry 1
– Entry 2
Actions
Action instructions are indicated by a preceding triangle. The result of an action is indicated by
an arrow.
►Action instruction 1
⇒Action result
►Action instruction 2
1.1 Introduction
1.2 Typographical
Conventions

www.balluff.com
5
1User Instructions
BVS SC-_1280Z00-07-0_0
SMARTCAMERA IO
english
Numbers:
– Decimal numbers are shown without additional indicators (e.g. 123).
– Fixed-point numbers are shown with a period (e.g. 0.123).
– Hexadecimal numbers are shown with the additional indicator hex (e.g. 00hex).
Parameters:
Parameters are shown in italics (e.g. CRC_16).
Directory paths:
Path information for saving data is shown with capital letters
(e.g.
Project:\Data tyPes\User-DefineD).
ASCII code:
Characters transmitted in ASCII code are set in apostrophes (e.g. 'L').
Symbols
Note, tip
This symbol indicates general notes.
BVS Balluff Vision Solution
CMOS Complementary metal-oxide-semiconductor
DCP Discovery and basic Configuration Protocol
DHCP Dynamic Host Configuration Protocol
DID Device ID
I/O port Digital input and output port
EEPROM Electrical Erasable and Programmable ROM
EMC Electromagnetic compatibility
FCC Federal Communications Commission
FE Function ground
GND Ground
I/O port Digital input / output port
ID Identification
IO Input / Output
IP Internet Protocol
LAN Local Area Network
LPS Limited Power Source
MAC Media Access Control
n.c. not connected
PC Personal Computer
RX Receiver
SC SMARTCAMERA
SIO Standard Input/Output
PLC Programmable Logic Controller
TX Transmitter
UINT8 unsigned integer, 1 byte long
UINT16 unsigned integer, 2 bytes long
UINT32 unsigned integer, 4 bytes long
1.3 Abbreviations

6
1User Instructions
BVS SC-_1280Z00-07-0_0
SMARTCAMERA IO
english
Copyright © Balluff GmbH, Neuhausen a.d.F., Germany, 2015. All rights reserved. In particular:
Right to duplication, modification, dissemination and translation into other languages. Please
note that all texts, graphics and images contained in these operating instructions are protected
by copyright and other protection laws. Commercial duplications, reproductions, modifications
and disseminations of any type require the prior written approval of Balluff GmbH.
All information and notes in these operating instructions, particularly the chapter Safety Instruc-
tions, must be observed.
The General Terms and Conditions of Balluff GmbH in their respective current version and the
conditions in these operating instructions exclusively apply to all deliveries of products and to all
other services of Balluff GmbH (henceforth referred to as "GTC"). The provisioning of the soft-
ware is exclusively subject to the respective current GTC, the conditions in these operating
instructions as well as the regulations of the "Balluff Enduser Licensing Agreement". You may use
the software only in compliance with these provisions. If they should not yet be available, Balluff
GmbH will gladly provide the current GTC upon request.
Balluff GmbH is authorized – but not obligated – to make updates or upgrades of the firmware
available via the website of Balluff GmbH or in any other form. In such a case, Balluff GmbH is
authorized – but not obligated – to inform you about the updates or upgrades. The use of such
upgrades or updates assumes that you accepted the validity of the current GTC as well as the
additional conditions in the operating instructions.
The product, trade, company and technology designations used (e.g. Microsoft®, Windows 7®,
Internet Explorer®, Google Chrome®, Mozilla Firefox® and HALCON®) are trademarks of the
respective owners.
1.4 Copyright
1.5 Legal
Requirements
1.6 Updates and
Upgrades
1.7 Trademarks

www.balluff.com
7
2Safety
BVS SC-_1280Z00-07-0_0
SMARTCAMERA IO
english
The SMARTCAMERA BVS SC is a camera with integrated image analysis for contactless acqui-
sition and examination of objects in industrial environments.
The intended use also includes that you have read these operating instructions in their entirety
and follow all the information - particularly the chapter Safety Instructions.
Installation and Startup
Installation and commissioning may only be performed by trained specialist personnel. Any
damage resulting from unauthorized manipulation or improper use voids warranty and liability
claims against the manufacturer.
When connecting the SMARTCAMERA to an external controller, observe proper selection and
polarity of the connection as well as the power supply (see “Assembly” on page 10).
The SMARTCAMERA may only be used with an approved power supply (see “Product
specification” on page 11).
Conformity
This product was developed and manufactured in accordance with the
applicable European directives. CE conformity has been verified.
All approvals and certifications are no longer valid in the following cases:
– Components are used that are not part of the SMARTCAMERA BVS SC.
– Components are used that have not been explicitly approved by Balluff. For a list of the
approved components, see chapter 7.2 “Accessories”.
Operation and testing
The operator is responsible for ensuring that local safety regulations are observed.
In case of defects and non-correctable faults, immediately take the vision system out of service
and secure it against unauthorized use.
NOTICE
The signal word NOTICE warns against possible property damage.
►Always observe the described measures for preventing this danger.
CAUTION
The pictogram used with the signal word CAUTION warns of a possible hazardous
situation affecting the health of persons. Failure to observe these warning notes may
result in injury.
►Always observe the described measures for preventing this danger.
►Observe the national regulations for disposal.
2.1 Intended Use
2.2 General Safety
Notes
2.3 Meaning of
Warning Notes
2.4 Disposal

8
3Product Description
BVS SC-_1280Z00-07-0_0
SMARTCAMERA IO
english
The Balluff SMARTCAMERA BVS SC is a camera for the acquisition and analysis of black-and-
white and color images. Application areas are optical identifications of codes and plain text,
inspections for quality assurance and the measurement of objects. The camera can also be used
in robot environments.
With the Gigabit LAN interface, the host industrial system can affect the processes in the camera
and receive customer-specific processed result data.
The product is suitable for use in harsh industrial environments (IP67 with lens protection, stan-
dard M12 industry plug connections, standardized industry network connections).
Since the complete software is located on the SMARTCAMERA itself,no external software is
required for the configuration and monitor display. Using standardized web browsers such as
Google Chrome, Mozilla Firefox or Internet Explorer, the user can easily connect with the
SMARTCAMERA and work in the Balluff BVS Cockpit interface developed specifically for
camera systems.
SMARTCAMERA BVS SC
Image Acquisition
Image Analysis
Result output via
corresponding interfaces
Figure 1: Function blocks of the SMARTCAMERA Figure 2: SMARTCAMERA with lens
The SMARTCAMERA has been designed in accordance with current, industrial standards:
– Image acquisition: C-mount lenses with corresponding matching filters; 1280x 1024pixel
monochrome or color sensor
– LAN connection via Gigabit Ethernet M12
– Configuration/monitoring via Google Chrome, Mozilla Firefox or Microsoft Internet Explorer
– Digital input/output channels for NPN and PNP connections
– Integrated IO-Link 1.1 Master via M12 plug connector
– The SMARTCAMERA product family is available in different designs.
The distinguishing features are:
– Monochrome/color imaging sensor
– Image processing functionality (identification tools, complete set)
Description Sensor Image pro-
cessing
LAN Fieldbus IO-
Link
Digital
I/Os
BVS002C
BVS SC-M1280Z00-07-000
Mono-
chrome All tools
Yes No No 8
BVS002E
BVS SC-C1280Z00-07-000 Color
BVS0028
BVS SC-M1280Z00-07-010
Mono-
chrome
Identification
tools
3.1 Product
Variants

www.balluff.com
9
3Product Description
BVS SC-_1280Z00-07-0_0
SMARTCAMERA IO
english
Included in the scope of delivery:
– SMARTCAMERA BVS SC
– 2 × cap M12
– Safety instructions
– Quick Start Guide
A lens protection is available for specific environmental conditions which is screwed directly onto
the camera housing, thereby meeting the requirements in accordance with IP67.
B
B
45
43,4
54
B-B
(1 : 1)
Figure 3: BAM PC-VS-023-1 (BAM02NA)
Please note that only C-mount lenses with a maximum diameter of 42 mm and a length of
40 mm can be used here.
The following accessory groups complete the Balluff product range:
– C-mount lenses (BAM LS-VS-004-C2/3-xx14-2)
– Screw-on filter (BAM OF-VS-002-xx-yy)
– Lights (BAE LX)
– Touchpanel PC (BAE-PD-VS-011-01)
– Mounting Accessories
– Connection cable
– Power supply units
Note
Visit www.balluff.com for more information on available software and accessories.
3.2 Scope of
delivery

10
3Product Description
BVS SC-_1280Z00-07-0_0
SMARTCAMERA IO
english
The camera features 12threads for installation at the location of use. Four threads each at the
rear, the left and the right. This ensures a secure and reliable mounting. The following drawings
describe the exact position of all mounting holes.
Individual threads are also used for fastening optional accessories (see chapter
7.2 “Accessories”).
61
97,5
70
105,7
44,3
1723,3
30,5
82,5
105,7
54,8
34,3
18
108,5
Figure 4: Mechanical connection (dimensions in mm)
60,9
28,5
69,5
24
97,5
4 x M4
54,8
16
60,9
18,6 24
24
Figure 5: Mechanical connection at rear/bottom (dimensions in mm)
The screw connections at the rear plate have an M4 thread. The maximum thread length is 5
mm. The maximum tightening torque is 2 Nm.
The lateral screw connections have an M5 thread. The maximum thread length is 5 mm. The
maximum tightening torque is 2.6 Nm.
3.3 Assembly

www.balluff.com
11
3Product Description
BVS SC-_1280Z00-07-0_0
SMARTCAMERA IO
english
Image sensor
Model variant Monochrome (CMOS) Color (CMOS)
Resolution 1280 × 1024
Max. frame rate [Hz] 60
Shutter type Global shutter 1)
Sensor size 1/1.8"
Pixel size [µm] 5.3 × 5.3
1) A global shutter sensor is not read line by line ot column by column, but in one access. This rules out
distortions with moving motifs (rolling shutter effect).
Mechanical data
Housing material Painted aluminum die-cast box
Degree of protection IP67 (with connectors and protection tube)
Weight (without lens) Approx. 360 g
Dimensions (L × B × H,
without connector, without
lens)
110 × 62 × 55 mm
Electrical data
Supply voltage 24 V ± 20 % LPS Class 2
Residual ripple ≤ 5%
Rated current consumption
without external load
300 mA
Max. current consumption 4 A
Operating conditions
Ambient temperature 0 °C … +55 °C
Storage temperature –25 °C…+70 °C
EMC EN 61000-4-2/3/4/5/6
EN 61000-6-2
EN 61000-6-3
EN 55011
Vibration/shock for operation
inside
EN 60068 Part 2-6/27
Vibration/shock was verified for the SmartCamera – the C-mount lens used and its adjustment
rings must be secured accordingly for operation.
3.4 Product
specification

12
3Product Description
BVS SC-_1280Z00-07-0_0
SMARTCAMERA IO
english
The product variants differ by the existing interfaces.
I/O variant
1
2
3
4
1
2
3
4
Power
I/O
I/O Light
LAN
Figure 6: Connections and pin assignment of I/O variant
Connection Function
Power Voltage supply of SMARTCAMERA, two freely configurable I/O signals are also
available.
LAN Integrates the SMARTCAMERA in a local network.
I/O To connect sensors/actuator, 6 galvanically isolated I/O signals are available
I/O Light 2 I/O signals and supply voltage output, e.g. for an external lighting
Information
In order to ensure enclosure rating IP67, unused I/O ports must be closed with cover
caps.
Connected accessories may be operated only with NEC Class 2.
5-pin M12 plug, A-coded
Pin Description Function
1 +24 VDC Supply voltage
2 I/O 0 Input/output
3 GND Ground
4 I/O 1 Input/output
5 n.c. Not connected
Information
The digital sensor inputs correspond to the guideline concerning inputs,
EN61131-2,Type3
The maximum load on any output is 100mA. The total current of the module must
not exceed 4 A per pin.
3.5 Connections
and Pin
Assignment
Power

www.balluff.com
13
3Product Description
BVS SC-_1280Z00-07-0_0
SMARTCAMERA IO
english
8-pin M12 socket, X-coded
Pin Description Function
1BI_DA + Bidirectional data, Pair A +
2BI_DA – Bidirectional data, Pair A –
3BI_DB + Bidirectional data, Pair B +
4BI_DB – Bidirectional data, Pair B –
5BI_DD + Bidirectional data, Pair D +
6BI_DD – Bidirectional data, Pair D –
7BI_DC – Bidirectional data, Pair C –
8BI_DC + Bidirectional data, Pair C +
Information
The cable must correspond at least to category 5e in accordance with EIA/TIA-568.
Transfer in accordance with 1000BASE-T/100BASE-TX/10BASE-T is being sup-
ported.
8-pin M12 socket, A-coded
Pin Description Function
1 I/O 0 Input/output
2 Common Out e.g. +24 V (PNP) / GND (NPN)
3 I/O 1 Input/output
4 I/O 2 Input/output
5 I/O 3 Input/output
6 I/O 4 Input/output
7 Common In e.g. GND (PNP) / +24 V (NPN)
8 I/O 5 Input/output
Information
These inputs / outputs are galvanically decoupled from the supply voltage of the
SMARTCAMERA. For this reason, Common In and Common out must always be
connected, even if only one input or output function is required.
Every output may be loaded with a maximum current of 100mA.
For a description of the interconnections, see the section “I/O” on page 17.
5-pin M12 socket, A-coded
Pin Description Function
1 VP (+24 VDC) Supply voltage
2 I/O 6 Input/output
3 GND Ground
4 I/O 7 Input/output
5 n.c. Not connected
Information
The maximum load on the supply voltage output is 1.2 A.
The digital sensor inputs correspond to the guideline concerning inputs,
EN61131-2,Type3
Every output may be loaded with a maximum current of 100mA.
LAN (Gigabit
Ethernet)
I/O
I/O Light

14
3Product Description
BVS SC-_1280Z00-07-0_0
SMARTCAMERA IO
english
The power plug connector supplies the SMARTCAMERA with the supply voltage and offers two
I/O-24V switching signals (I/O0 & I/O1) for the connection with sensors, actuators or PLC.
These two inputs and outputs feature a push-pull output stage. This allows using the output
signal for PNP logic as well as NPN logic. The input stage always features PNP logic.
I/O 0 & I/O 1 (power plug connectors)
Operation as input
Voltage Signal 0 0…5 V < 2 mA
Signal 1 11…30 V 2…5 mA
Delay < 150 µs
Operation as output
Voltage Signal 0 0 V (+VD)100 mA max.
Signal 1 24 V (VDC – VD)100 mA max.
Voltage drop VD< 2 V
Delay < 10 µs
See also the guideline on digital inputs, EN 61131-2, Type 3.
Below are examples how inputs and outputs must be connected to obtain input and output
function.
Information
I/Os of the same name are logically connected with each other.
When operating the I/Os as output, then e.g. I/O0 is connected at the power connec-
tion and I/O0 at the IO connection.
If the I/Os are configured as input, their signals are ored. A 1 signal is recognized if a 1
signal is present either at I/O0 of the power connection or I/O0 of the I/O connection.
Input connection
If I/O0 is configured as input, it is sinking and can be connected directly with the PNP output of
a sensor, a PLC. A 1 signal is being detected if the input is connected with the supply voltage. A
0 signal is being detected if the input is set to ground or is not connected.
If an NPN device is to be connected to the input, then an external level converter must be con-
nected upstream.
1
2
3
4
+VDC
I/O 0
GND
24 V
I/O 1 +
−
Figure 7: Input connection
3.5.1 Power

www.balluff.com
15
3Product Description
BVS SC-_1280Z00-07-0_0
SMARTCAMERA IO
english
Output connection
If I/O0 is configured as output, the supply voltage is applied at the output and the actuator, PLC
input is supplied with it if 1 is being output. The output is connected with GND if 0 is being
output. The output current of an I/O may not exceed 100mA.
If the output is being overloaded, e.g. by a short circuit, it is switched off and periodically che-
cked whether the fault occurrence is still present. If the error was removed, the output is again in
normal operating state without a reset.
PNP output connection
PNP logic is predominantly used in Europe. The output is sourcing, so that the load between I/O
and GND must be switched accordingly. The load is connected with supply voltage if 1 is being
output.
1
2
3
4
+VDC
I/O 0
GND
24 V
I/O 1 +
−
+ −
Figure 8: PNP output connection
NPN output connection
NPN logic is predominantly used in Asia. The output is sinking, so that the load between I/O and
supply voltage must be switched accordingly. The load is set to GND if 0 is being output.
To obtain a normal switching behavior, the output can be inverted.
1
2
3
4
+VDC
I/O 0
GND
24 V
I/O 1 +
−
− +
Figure 9: NPN output connection
The LAN interface meets the Ethernet standard in accordance with IEEE 802.3-2008 (up to
1Gigabit). This network connection is used to call up the web interface BVS Cockpit for the
configuration. In addition, a communication channel is available to control the image analysis and
to call up the generated result values.
3.5.2 LAN

16
3Product Description
BVS SC-_1280Z00-07-0_0
SMARTCAMERA IO
english
The I/O light interface provides 24 volt and two I/O signals (I/O6 & I/O7). These I/Os, similar to
the two I/Os at the power plug connectors (see section “Power” on page 14), are equipped
with a push-pull output stage and a PNP input.
I/O 6 & I/O 7 (I/O light plug connectors)
Operation as input
Voltage Signal 0 0…5 V < 2 mA
Signal 1 11…30 V 2…5 mA
Delay 0 →1 < 150 µs
1 →0 < 150 µs
Operation as output
Voltage Signal 0 0 V (+VD)100 mA max.
Signal 1 24 V (VDC – VD)100 mA max.
Voltage drop VD< 2 V
Delay 0 →1 < 10 µs
1 →0 < 10 µs
Supply voltage output
Voltage VP24 V (VDC – VD) 1.3 A max.
Voltage drop VD< 2 V
Among other things, this makes it possible to easily connect lighting equipment to the SMART-
CAMERA. Either the permanent voltage supply or the I/O signals can be used for this purpose.
The following example shows how the ring lighting BAE LX-VS-RR100 can be connected with
trigger and boost.
1
2
3
4
1
2
3
4
+VP
I/O 6
GND
I/O 7
+VDC
Boost
GND
Light
Trigger
Figure 10: I/O light circuit
The ring lighting is equipped with a M12 plug, so that it can be connected directly with the
SMARTCAMERA. A complex wiring is not necessary.
Naturally, other sensors/actuators can also be connected, the corresponding switching examp-
les are located in the description of the power plug connector (see “Power” on page 14).
3.5.3 I/O Light

www.balluff.com
17
3Product Description
BVS SC-_1280Z00-07-0_0
SMARTCAMERA IO
english
The IO interface furnishes six galvanically isolated I/O 24-V switching signals for the connection
with sensors, actuator or PLC.
All inputs and all outputs have a Common In or Common Out reference potential. This allows
using the I/Os either for PNP logic or NPN logic. A mixed mode (PNP and NPN at the same time)
is not possible.
These I/O signals can be used to control the camera or transfer individual information to the host
system. As a result, the image acquisition can be triggered via these I/O signals. Outputting a
binary analysis result is also possible. The assignment of the I/O signals is done via the BVS
Cockpit interface (see “Digital I/O Interface” on page 26)
I/O 0 & I/O 5 (I/O plug connectors)
Operation as input
Voltage Signal 0 0…5 V (I/O to VCommon In ) < 2 mA
Signal 1 11…30 V (I/O to VCommon In ) 2…8 mA
Delay 0 →1 < 10 µs
1 →0 < 100 µs
Operation as output
PNP NPN
Voltage Signal 0 High-resistance High-resistance 100 mA max.
Signal 1 24 V (VCommon Out – VD)0 V (VCommon Out + VD)100 mA max.
Voltage drop VD < 2 V
Delay 0 →1 < 10 µs
1 →0 < 50 µs
Supply voltage for I/O 1)
Voltage VCommon Out 24 VDC
( ±20 % LPS Class 2)
0 V
VCommon In 0 V 24 VDC ( ±20 % LPS Class 2)
1) The supply voltage for the I/O of the I/O interface is galvanically isolated from the operational
voltage of the SMARTCAMERA.
Below are examples how inputs and outputs must be connected to obtain input and output
function.
Information
I/Os of the same name are logically connected with each other.
When operating the I/Os as output, then e.g. I/O0 is connected at the I/O connection
and I/O0 at the power connection.
If the I/Os are configured as input, their signals are logically combined with OR. A 1
signal is recognized if a 1 signal is present either at I/O0 of the power connection or
I/O0 of the I/O connection.
3.5.4 I/O

18
3Product Description
BVS SC-_1280Z00-07-0_0
SMARTCAMERA IO
english
PNP mode
PNP logic is predominantly used in Europe. The output is sourcing, the input is sinking.
To operate the I/O port in PNP mode, Common Out must be supplied with +24 V (19.2…30 VDC)
and Common In with 0 V.
If I/O0 is configured as input, it can be connected directly with the PNP output of a sensor, a
PLC or similar. A 1 signal is being detected if the input is connected with Common Out. A 0
signal is being detected if the input is set to Common In or is not connected.
1
2
3
4
5
6
7
8
24 V +
−
I/O 0
Common Out
I/O 1
I/O 2
I/O 3
Common IN
I/O 5
I/O 4
Figure 11: PNP mode, I/O 0 configured as input
If I/O0 is configured as output, the output is connected with Common Out and the actuator,
PLC input or similar is supplied with it if 1 is being output. The output is high-resistance if 0 is
being output.
1
2
3
4
5
6
7
8
24 V +
−
I/O 0
Common Out
I/O 1
I/O 2
I/O 3
Common IN
I/O 5
I/O 4
+ −
Figure 12: PNP mode, I/O 0 configured as output
The output current of an I/O may not exceed 100mA. If the output is being overloaded, e.g. by a
short circuit, it is switched off and periodically checked whether the fault occurrence is still
present. If the error was removed, the output is again in normal operating state without a reset.
It is also possible to use input and output functions at the same time. In the following example,
I/O0 is configured as output and I/O1 as input.
1
2
3
4
5
6
7
8
24 V
+
−
I/O 0
Common Out
I/O 1
I/O 2
I/O 3
Common IN
I/O 5
I/O 4
+ −
Figure 13: PNP mode, I/O0 configured as output and I/O1 as input

www.balluff.com
19
3Product Description
BVS SC-_1280Z00-07-0_0
SMARTCAMERA IO
english
NPN mode
NPN logic is predominantly used in Asia. The output is sinking, the input is sourcing.
To operate the IO port in PNP mode, Common Out must be supplied with 0 V and Common In
with +24 V (19.2…30 VDC).
If I/O0 is configured as input, it can be connected directly with the NPN output of a sensor, a
PLC or similar. A 1 signal is being detected if the input is connected with Common Out. A 0
signal is being detected if the input is set to Common In or is not connected.
1
2
3
4
5
6
7
8
24 V +
−
I/O 0
Common Out
I/O 1
I/O 2
I/O 3
Common IN
I/O 5
I/O 4
Figure 14: NPN mode, I/O 0 configured as input
If I/O0 is configured as output, the output is connected with Common Out and the actuator,
PLC input or similar is supplied with it if 1 is being output. The output is high-resistance if 0 is
being output.
1
2
3
4
5
6
7
8
24 V +
−
I/O 0
Common Out
I/O 1
I/O 2
I/O 3
Common IN
I/O 5
I/O 4
− +
Figure 15: NPN mode, I/O 0 configured as output
The output current of an I/O may not exceed 100mA. If the output is being overloaded, e.g. by a
short circuit, it is switched off and periodically checked whether the fault occurrence is still
present. If the error was removed, the output is again in normal operating state without a reset.
It is also possible to use input and output functions at the same time. In the following example,
I/O0 is configured as output and I/O1 as input.
1
2
3
4
5
6
7
8
24 V
+
−
I/O 0
Common Out
I/O 1
I/O 2
I/O 3
Common IN
I/O 5
I/O 4
− +
Figure 16: NPN mode, I/O0 configured as output and I/O1 as input

20
3Product Description
BVS SC-_1280Z00-07-0_0
SMARTCAMERA IO
english
The operating states of the vision system, the IO-Link master and the LAN and fieldbus interface
are displayed using LEDs. The display elements are distributed across the front and the under-
side of the SMARTCAMERA.
Displays on the front Displays at the plug connectors
2
1
4
3
1
2
Power LED
Signal LED
3
4
LAN Act
LAN Link
Figure 17: Display elements on the front and at the plug connectors
Displays on the front
LED Display Function
Power LED Off No supply voltage
Illuminating green Inspection is running or waiting for a trigger
Flashing green Inspection stopped or in configuration mode
Illuminating red Fault
Flashing red Firmware update active
Signal LED Off Signal = 0
Yellow, lit Signal = 1
The signal LED can indicate the status of any I/O signal in the area of the image analysis. The
configuration of this function is done via the BVS Cockpit web interface. (see chapter “Digital I/O
Interface” on page 26)
Displays at the plug connectors
LAN
LED Display Function
LAN Link Off No LAN connection
Green LAN connection established
LAN Act Off No data transfer
Yellow, flashing Data transmission
The outside of the camera can be cleaned with a soft cloth. Persistent dirt can be removed with
a cloth that is first moistened with a soap solution and wrung out. After wiping off the dirt spots,
wipe the camera with a dry cloth.
3.6 Display
elements
3.7 Cleaning
This manual suits for next models
6
Table of contents
Other Balluff Digital Camera manuals
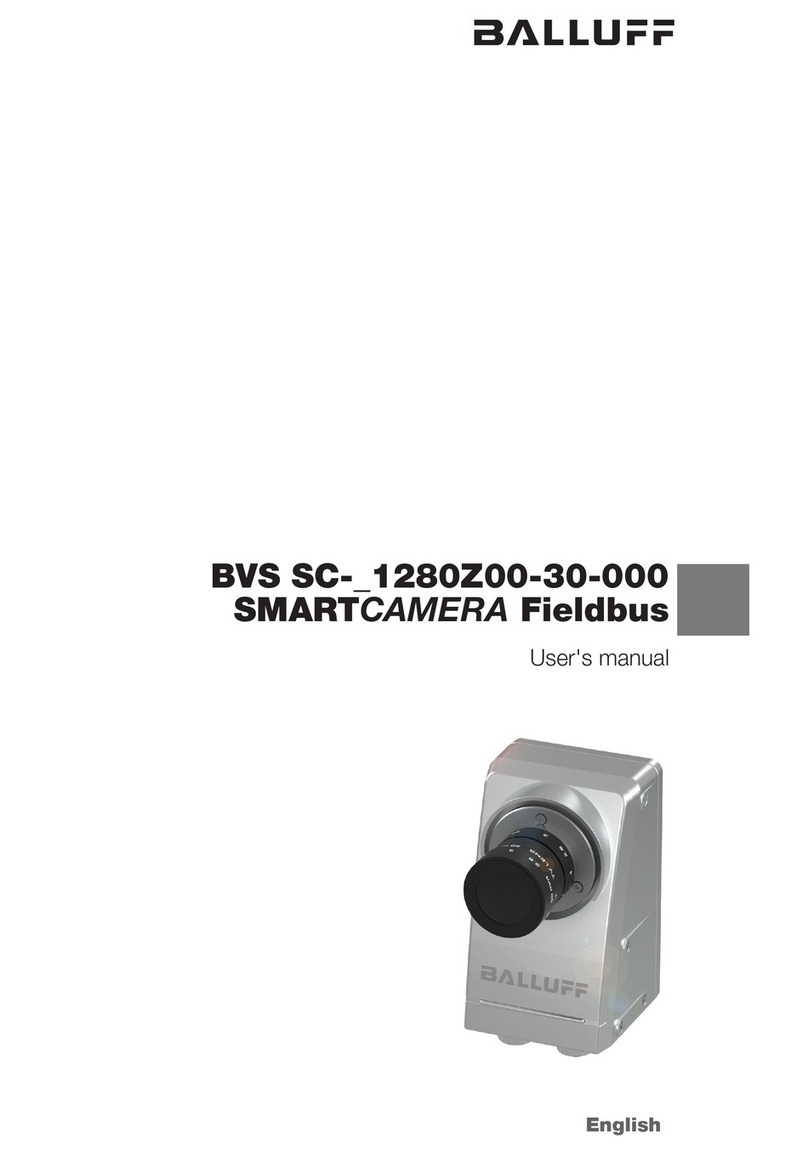
Balluff
Balluff SMARTCAMERA User manual
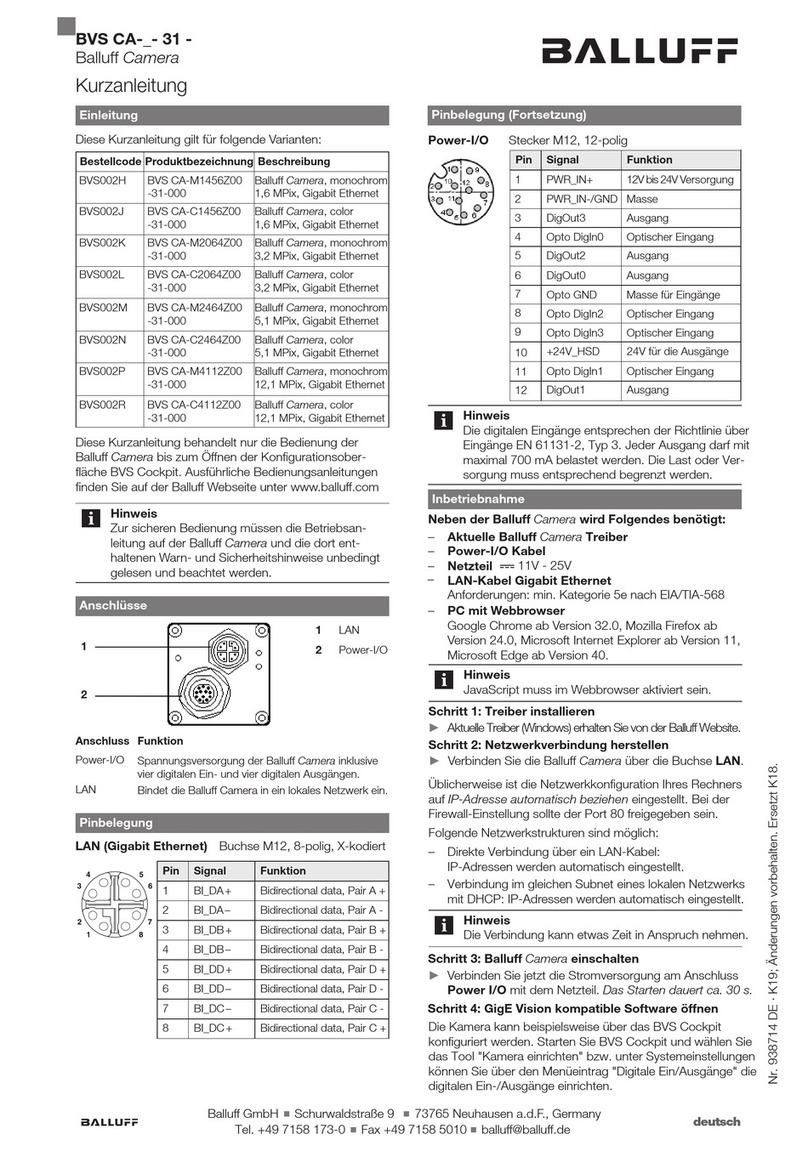
Balluff
Balluff BVS CA 31 Series User manual
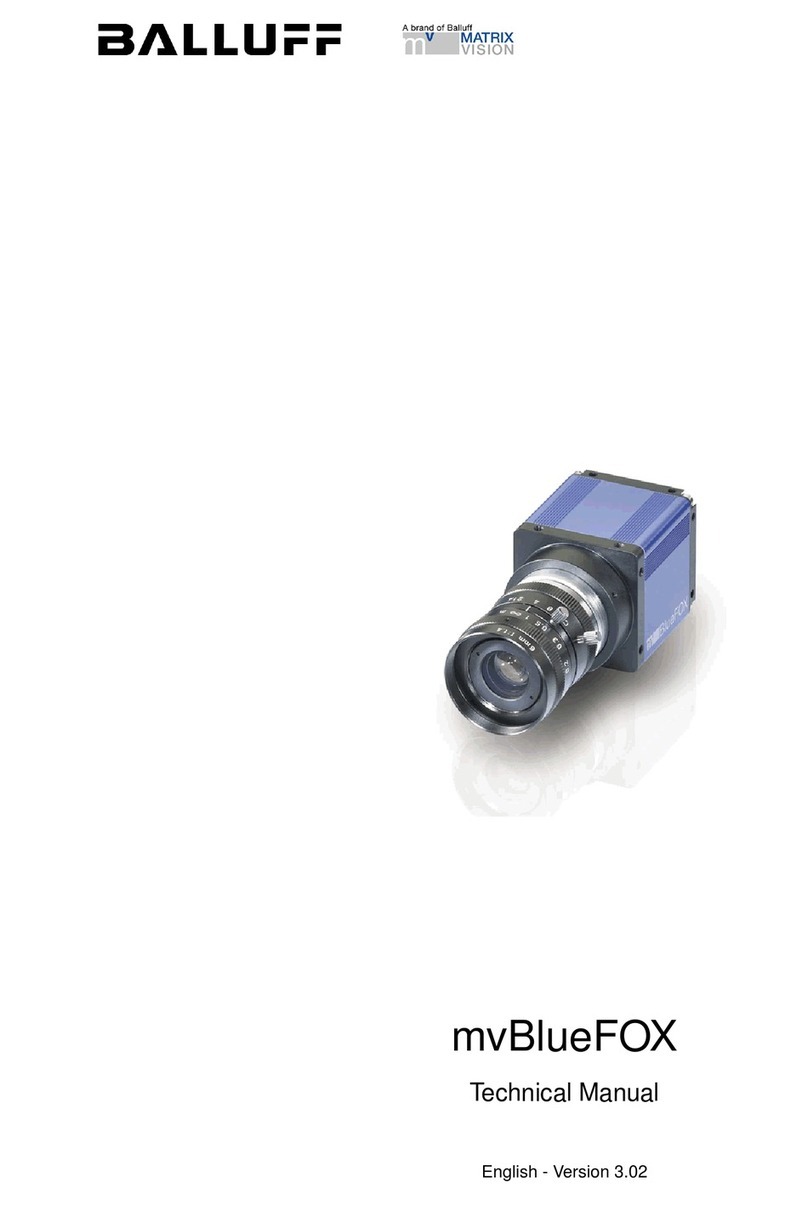
Balluff
Balluff MATRIX VISION mvBlueFOX Series User manual
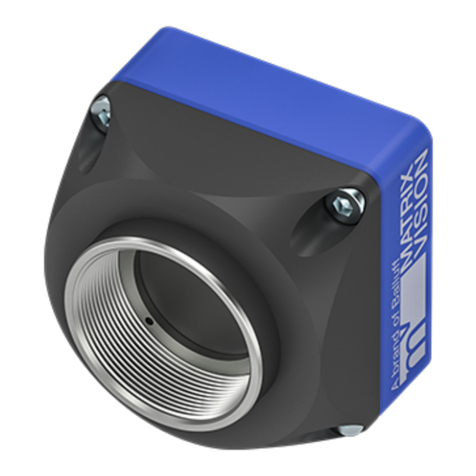
Balluff
Balluff MATRIX VISION mvBlueNAOS User manual
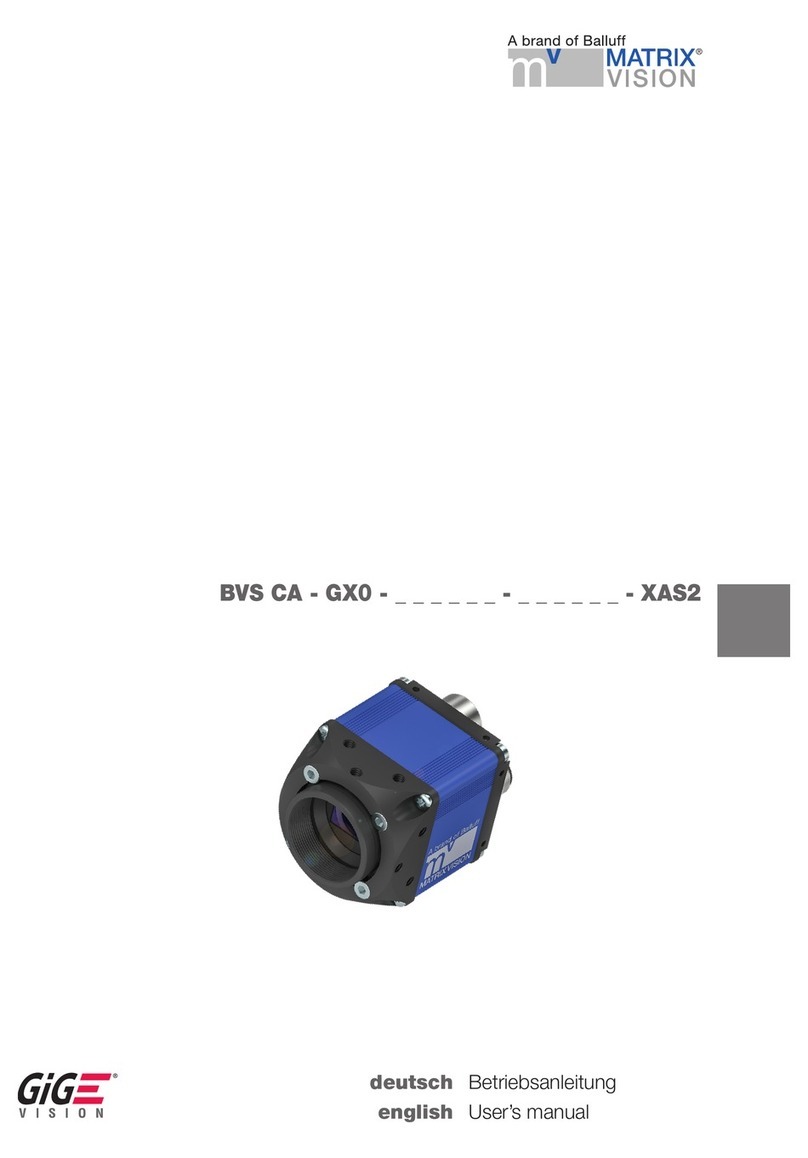
Balluff
Balluff MATRIX VISION GiGE VISION BVS CA-GX0-XAS2... User manual
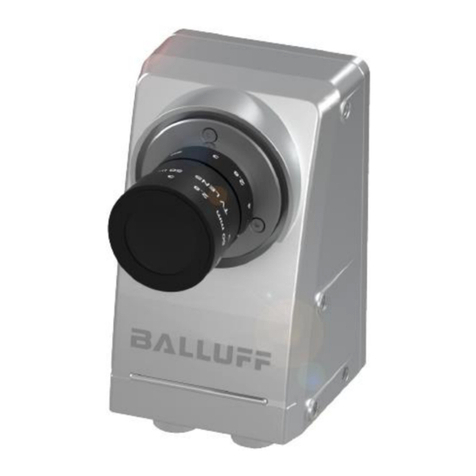
Balluff
Balluff BVS SC 1280Z00-07-000 Series User manual
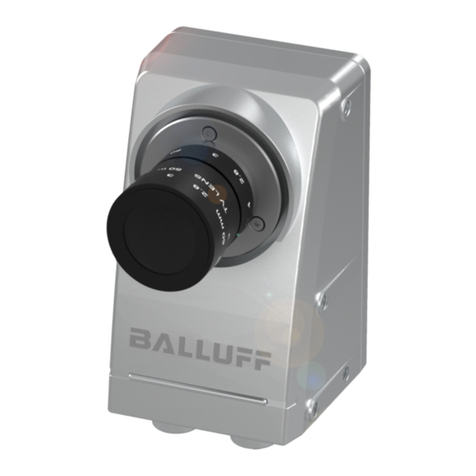
Balluff
Balluff BVS SC Series User manual
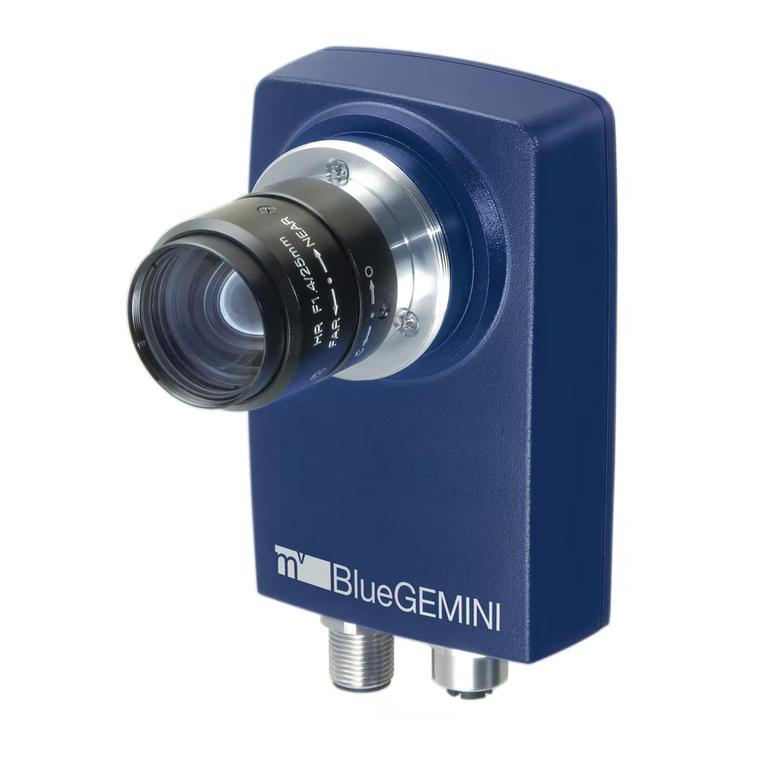
Balluff
Balluff MATRIX VISION mvBlueGEMINI User manual