Betts EV1XAETM-AAVB Manual

Form Title:
Document #:
INSTALLATION AND MAINTENANCE MANUAL
MM-EV005
(Form: DEF-006A-4)
Revision:
0
Document Title:
Date:
1” Cable Operated Water Drain Valve
May 5, 2022
Page:
1 of 11
Betts Industries Inc. ▪814·723·1250 ▪1800 Pennsylvania Ave. West ▪Warren, PA 16365 ▪www.BettsInd.com
Print Date: 6/20/2022 This form is considered uncontrolled 24 hrs. after print date.
PART NUMBERS (Including, but not inclusive)
EV1XAETM-AAVB
EV1ETM-AAVB
EV1XAETM-AAFS
EV1ETM-AAFS
Table of Contents:
1.0 General
2.0 Parts List
3.0 Description and Intended Use
4.0 Installation
5.0 Inspection and Testing
6.0 Disassembly and Rebuild Instructions
7.0 Trouble Shooting Guide

Form Title:
Document #:
INSTALLATION AND MAINTENANCE MANUAL
MM-EV005
(Form: DEF-006A-4)
Revision:
0
Document Title:
Date:
1” Cable Operated Water Drain Valve
May 5, 2022
Page:
2 of 11
Betts Industries Inc. ▪814·723·1250 ▪1800 Pennsylvania Ave. West ▪Warren, PA 16365 ▪www.BettsInd.com
Print Date: 6/20/2022 This form is considered uncontrolled 24 hrs. after print date.
1.0 General Maintenance Manual Guidelines
1.1 It is strongly recommended that this entire manual be read prior to any operation, disassembly, or
assembly of this equipment.
1.2 Betts Industries, Inc. provides this manual as a guideline for reference only and assumes no
responsibility for personal injury or property damage that may occur in conjunction with this manual.
Betts Industries, Inc. cannot be held responsible for incorrect installation, operation or maintenance
ofthis equipment. Useonlygenuine Bettsreplacementparts. Substitutepartswill voidallwarranties
and could impair the proper function making this equipment unsafe.
1.3 Betts Industries, Inc. recommends all equipment be placed on a regular maintenance schedule that
includes the routine replacement of seals and gaskets and visual inspection for leaks and corrosion.
The end user must make their own determination and set their own schedule based upon use and
environment. In some cases, regulationsmay dictate the minimum testing frequency of items. Make
sure operators are aware of all applicable codes.
1.4 Only trained and qualified personnel should perform maintenance on this equipment.
1.5 As with any maintenance work, proper safety gear must be utilized and approved procedures must
be followed at all times. Examples of safety gear may include but are not limited to gloves, safety
goggles, face shields, protective suits and respirators. It is the responsibility of the person/company
working on this equipment to identify the hazardous products that the equipment has been exposed
to and designate specific and appropriate protective gear and safety procedures.
1.6 Safety alert symbols are used to alert operator to potential personal injury hazards. These symbols
are per ANSI Z535.5 and are listed below. Operator MUST obey all instructions that follow a safety
symbol. Alerts will be used to indicate known safety concerns.
A list of hazards may include but are not limited to fall hazards, pressure hazards, loaded springs,
corrosive material, flammable product, pinch points. Additional concerns are possible and should
be identified and avoided by the operator.
1.7 Product Warranty shall be void if equipment is subject to misapplication, misuse, neglect, alteration,
or damage.
1.8 Specific design details described in this document are for reference only and are subject to change
without notice. See Betts Industries, Inc. web page for the most recent revision to this document.
www.bettsind.com
1.9 WARNING: This product can expose you to chemicals including Chromium (hexavalent
compounds), which is known to the State of California to cause cancer and birth defects or other
reproductive harm. For more information go to: www.P65Warnings.ca.gov
1.10 For additional questions or more detailed technical assistance, contact the Betts Industries, Inc.
Customer Service, Sales or Engineering Department at (814) 723-1250.
Indicates an imminently hazardous situation which, if not
avoided, will result in death or serious injury.
Indicates a potentially hazardous situation which, if not
avoided, could result in death or serious injury.
Indicates a potentially hazardous situation which, if not
avoided, may result in minor or moderate injury. It may also be
used to alert against unsafe practices.

Form Title:
Document #:
INSTALLATION AND MAINTENANCE MANUAL
MM-EV005
(Form: DEF-006A-4)
Revision:
0
Document Title:
Date:
1” Cable Operated Water Drain Valve
May 5, 2022
Page:
3 of 11
Betts Industries Inc. ▪814·723·1250 ▪1800 Pennsylvania Ave. West ▪Warren, PA 16365 ▪www.BettsInd.com
Print Date: 6/20/2022 This form is considered uncontrolled 24 hrs. after print date.
2.0 Parts List
Rebuild Kit P/N EV76247VB –includes items 5,10,12,14,15
WARNING: Use only genuine Betts Industries Inc. replacement parts. Use of substitute parts can impair the proper
functioning of the Water Drain Valve.
9
8
5
1
11
12
13
14
15
6
4
3
2
10 10
7
8
No.
Description
Req.
Material
Part No.
1
Retaining Ring
1
Stainless Steel
9Q9720
2
Spring Retainer
1
Aluminum
76165AL
3
Spring
1
Stainless Steel
76166SS
4
O-ring Holder Stem
1
Anodized Aluminum
76164AL
5a
O-Ring Main Seal
1
FKM-B
75096VB
5b
Fluorosilicone
75096FS
6
Push Stem
1
Stainless Steel
76163SS
7
Lever
1
Stainless Steel
29375SL
8
Binding Barrel
1
Stainless Steel
9Q9722
9
10-24 –3/8 Button Cap Screw
1
Stainless Steel
9Q9721
10
Nylon Washer
2
Nylon
9Q9712
11
Roller Chain Connecting Link
1
Steel
9Z9734
12
Boot
1
EPDM
75933EP
13
Retaining Ring
1
Stainless Steel
9Q4999
14
Bushing
1
Oil Embed Bronze
76167BR
15a
O-Ring Push Stem
1
FKM-B
19505VB
15b
Fluorosilicone
19505FS

Form Title:
Document #:
INSTALLATION AND MAINTENANCE MANUAL
MM-EV005
(Form: DEF-006A-4)
Revision:
0
Document Title:
Date:
1” Cable Operated Water Drain Valve
May 5, 2022
Page:
4 of 11
Betts Industries Inc. ▪814·723·1250 ▪1800 Pennsylvania Ave. West ▪Warren, PA 16365 ▪www.BettsInd.com
Print Date: 6/20/2022 This form is considered uncontrolled 24 hrs. after print date.
3.0 Description and Intended Use
The Betts 1” Water Drain Valve meets HM183 requirements for an
internal self-closing stop valve and is ideal for use as a water
drain/sampling valve. The valve is manually operated with use of a pull
cable and offers a 1” NPT male threaded inlet and ¾” NPT female
threaded outlet. Optional features include a conversion to pneumatic
actuation or a 1” NPT female outlet.
The shear section is located above both the pull lever and push stem
connection point which helps to provide a cleaner separation in the
event of an under-carriage impact. The valve meets the shear section
requirements of 49CFR §178.345-8 and is tested per TTMA RP84.
The valve body and O-ring holder stem are constructed of lightweight
anodized aluminum to maximize durability and corrosion resistance.
The valve push stem is 316 stainless steel and is supported by an oil
impregnated bushing with FKM-B (Viton® B) standard seals for
compatibility with a wide range of products and temperatures. The
simplistic design allows for easy tear-down and maintenance.
Valve MAWP: 25 psi [1.7bar]
Minimum Bursting Pressure: 100 psi [6.9bar]
Valve Temperature Range: –45F to +380F [-43C to +193C]
FKM-B (Viton® B) - Seals
Weight: .82 lbs [.38kg]
*Dimension will vary dependent on thread engagement.
4.0 Installation
4.1 Prior to installation, it is recommended to verify proper function of the water drain valve.
Refer to 5.0 for detailed instructions.
4.2 Apply PTFE tape or thread sealant to the male threads of the water drain valve. Ensure
that the sealant is compatible with the product being hauled or stored.
4.3 Thread the valve into the 1” NPT fitting or sump.
4.3.1 The flow rates of the valve will vary depending on the type of fitting used. The
major diameter of the valve is 1.20” in diameter. Any full or half coupling used
must have an inside diameter of a minimum of 1.25”. It is not recommended to
use a full coupling as the flow path of fluid through the valve windows will be
drastically restricted.
4.4 Use an adjustable wrench or 1-5/8” wrench on the valve hex to fully tighten the valve to
the sump or fitting. Overtightening the valve can cause damage to the threads.
4.4.1 Check the threaded mounting joint for leakage. Additional tightening or additional
PTFE tape or thread sealant may be required to ensure a leak tight joint.
1.46
[37.1 mm]
3.0*
[76.2 mm]
8.14
[206.8 mm]

Form Title:
Document #:
INSTALLATION AND MAINTENANCE MANUAL
MM-EV005
(Form: DEF-006A-4)
Revision:
0
Document Title:
Date:
1” Cable Operated Water Drain Valve
May 5, 2022
Page:
5 of 11
Betts Industries Inc. ▪814·723·1250 ▪1800 Pennsylvania Ave. West ▪Warren, PA 16365 ▪www.BettsInd.com
Print Date: 6/20/2022 This form is considered uncontrolled 24 hrs. after print date.
4.5 Apply PTFE tape or thread sealant to the male fitting/connection that will install to the
female outlet threads of the water drain valve. Ensure that the sealant is compatible with
the product being hauled or stored.
4.6 Use a wrench and fully tighten the outlet piping to the valve
4.6.1 Overtightening the fitting/piping can cause damage to the threads.
4.6.2 Additional tightening or additional PTFE tape or thread sealant may be required to
ensure a leak tight joint.
4.7 Ensure outlet piping is supported to reduce the transmission of vibration or load which
may damage the valve.
4.8 Use the lever mounting 7/16” hole to attach cable.
4.8.1 It is important to review the cable system to ensure the valve spring force is
sufficient to close the valve and retract the cable. Reduce cable friction by
minimizing bends and long runs.
4.8.2 Use of a wire thimble will help prevent the cable from being damaged during
actuation
4.8.3 A fusible link is available as an option if additional thermal protection is desired.
The fusible element melts at not more than 250°F and uses a nonslip adjustable
cable attachment. The Fusible Link part number is 76173SLZC.
76173SLZC –Fusible Link

Form Title:
Document #:
INSTALLATION AND MAINTENANCE MANUAL
MM-EV005
(Form: DEF-006A-4)
Revision:
0
Document Title:
Date:
1” Cable Operated Water Drain Valve
May 5, 2022
Page:
6 of 11
Betts Industries Inc. ▪814·723·1250 ▪1800 Pennsylvania Ave. West ▪Warren, PA 16365 ▪www.BettsInd.com
Print Date: 6/20/2022 This form is considered uncontrolled 24 hrs. after print date.
5.0 Inspection and Testing
5.1 Bench Test:
•Use Betts Part number: 76248SLBN Inlet Test Fixture 1-11.5NPS
•Use Betts Part number: 76249SSBN Outlet Test Fixture ¾-14NPS
•Use Betts Part number: 76250SSBN Outlet Test Fixture 1-11.5NPS
5.1.2 Use silicone grease to lubricate the O-ring in the test fixture
5.1.3 Thread the fixture all the way down onto the valve
5.1.4 Attach a regulated air supply to the test fixture and set at the desired test pressure
(valve MAWP is 25 psi).
5.1.5 Dunk the valve into a water tank and check for bubbles propagating from the outlet
of the valve indicating a leak of the main seal.
•If the valve leaks, disassemble the test fixture and check the valve O-ring and
valve seat for any debris, dirt or scratches. Repair the valve and retest.
•If leaks are propagatingfrom the threads of the valve, inspect andclean/change
the O-ring seal (-217) in the fixture.
5.1.6 Thread the plug fixture with gasket into the outlet of the valve body sealing on the
face of the valve. Ensure that the face of the valve body is free of any dirt debris
or scratches.
5.1.7 With the regulated air supply still attached, dunk the valve into the water tank and
open the valve. Check for bubbles propagating from either the valve body or the
push stem seal.
•If the push stem leaks, repair the valve and retest.

Form Title:
Document #:
INSTALLATION AND MAINTENANCE MANUAL
MM-EV005
(Form: DEF-006A-4)
Revision:
0
Document Title:
Date:
1” Cable Operated Water Drain Valve
May 5, 2022
Page:
7 of 11
Betts Industries Inc. ▪814·723·1250 ▪1800 Pennsylvania Ave. West ▪Warren, PA 16365 ▪www.BettsInd.com
Print Date: 6/20/2022 This form is considered uncontrolled 24 hrs. after print date.
5.2 Inspection and testing on the cargo tank: Ensure the tank does not contain pressure or
product.
5.2.1 Once the valve has been mounted, pressure can be applied to the tank. The
MAWP of the valve is 25 psi [1.7bar]
•Inspect the valve for leaks and repair if necessary.
6.0 Disassembly and Rebuild Instructions
6.1 Always wear protective gear appropriate to the product being transported. Examples may
include gloves, safety goggles, face shields, protective suits and respirators. It is the
responsibility of the operator to know the product being hauled and the gear required.
6.2 Ensure the tank does not contain pressure or product.
6.3 Remove the cable attachment to the valve lever.
6.4 Unthread the outlet piping or fittings from the valve.
6.5 Unthread the valve from the sump or fitting.
6.6 Using a 1/8” hex key (Allen) wrench, insert into the button cap screw (9). While holding the
1/8” hex key (Allen) wrench, unscrew the binding barrel (8) with a Phillips head screwdriver
6.7 Remove the binding barrel (8), the cap screw (9) and the two nylon washers (10). Inspect
parts for damage and replace if necessary.
6.8 Pull out the Push Stem (6), Lever (7), and Roller Chain Connecting Link (11). Inspect parts
for damage.
Pressure Hazard –Cargo tank or piping may contain
residual pressure and failure to safely relieve could result in
sudden loss of pressure causing death or serious injury.
Flammable Product –Cargo tank or piping may contain
product that could present risk of fire, explosion, asphyxiation
or other hazards resulting in death or serious injury.
Corrosive Material –Cargo tank or piping may contain
corrosive material. Protective clothing including gloves and
face shield shall be worn.
Pressure Hazard –Cargo tank or piping may contain
residual pressure and failure to safely relieve could result in
sudden loss of pressure causing death or serious injury.
Flammable Product –Cargo tank or piping may contain
product that could present risk of fire, explosion, asphyxiation
or other hazards resulting in death or serious injury.
Corrosive Material –Cargo tank or piping may contain
corrosive material. Protective clothing including gloves and
face shield shall be worn.

Form Title:
Document #:
INSTALLATION AND MAINTENANCE MANUAL
MM-EV005
(Form: DEF-006A-4)
Revision:
0
Document Title:
Date:
1” Cable Operated Water Drain Valve
May 5, 2022
Page:
8 of 11
Betts Industries Inc. ▪814·723·1250 ▪1800 Pennsylvania Ave. West ▪Warren, PA 16365 ▪www.BettsInd.com
Print Date: 6/20/2022 This form is considered uncontrolled 24 hrs. after print date.
6.8.1 Make sure Push Stem (6) is smooth with no scratches in the area of the push
stem that rides past the push stem O-ring. If the push stem needs replaced
remove the Roller Chain Connecting Link (11)
•Use a flat head screwdriver to help remove the side plate of the roller chain
connecting link. Be careful not to deform the side plate. If the side plate is
deformed during removal, replace.
6.8.2 Replace the Lever (7) if necessary.
6.9 Using a small flat head screwdriver, remove the Retaining Ring (13) by inserting into the
grooved portion of the retaining ring and prying up as you “walk”the screwdriver around
the Retaining Ring (13)
6.10 Pull out the Bushing (14). An O-ring pick can be used to assist removal of the Bushing
(14) if it is stuck. Replace with a new Bushing (14).
6.11 Using an O-ring pick remove the O-ring Push Stem (15). Use care to not scratch the O-
ring groove in the valve body. Inspect the O-ring groove for debris or scratches, and
replace the O-ring. Use a silicone grease or product compatible lubricant to reinstall the
seal.
6.12 Using retaining ring pliers remove the Retaining Ring (1), Spring Retainer (2), Spring (3),
O-ring Holder Stem (4), and O-ring Main Seal (5).
6.12.1 Inspect the O-ring Holder Stem (4) for wear or scratches and replace if
necessary.
6.12.2 Inspect the Spring Retainer (2) for wear or scratches and replace if necessary.
6.12.3 Using an O-ring pick remove the O-Ring Main Seal (5) and replace. Use a
silicone grease or product compatible lubricant to reinstall the seal.
6.13 Remove the EPDM Boot (12) by pulling off the valve and inspect for damage or
degradation and replace if necessary.
6.14 Fully inspect the valve body. Check all sealing points, thread damage, or corrosion and
replace if necessary.
6.15 Rebuilding: With the valve body, install the O-ring Push Stem (15), ensuring that the O-
ring, the Bushing (14), and the Retaining Ring (13).
•Use a silicone grease or product compatible lubricant to reinstall the seal.
•Ensure the O-ring is seated in the smaller counterbore.
•Ensure that the Retaining Ring (13) snaps into the groove. Start with one end
into the groove and “walk”around with your fingers.

Form Title:
Document #:
INSTALLATION AND MAINTENANCE MANUAL
MM-EV005
(Form: DEF-006A-4)
Revision:
0
Document Title:
Date:
1” Cable Operated Water Drain Valve
May 5, 2022
Page:
9 of 11
Betts Industries Inc. ▪814·723·1250 ▪1800 Pennsylvania Ave. West ▪Warren, PA 16365 ▪www.BettsInd.com
Print Date: 6/20/2022 This form is considered uncontrolled 24 hrs. after print date.
6.16 Install the O-ring Holder Main Seal (5) into the O-ring Holder Stem (4). Use a silicone
grease or product compatible lubricant to reinstall the seal.
6.17 Install the O-ring Holder Stem (4), Spring (3), Spring Retainer (2), and the Retaining
Ring (1).
•Set the parts in order into the valve body. With the Retaining ring (1) on top
insert the retaining ring pliers into the Retaining Ring (1). While compressing
the Retaining Ring (1) push down until the spring compresses enough to
expose the retaining ring groove. Release the retaining ring pliers until the
retaining ring compresses or snaps into the groove. Ensure that the retaining
ring (1) is completely seated into the retaining ring groove.
13
14
15
5
1
4
3
2

Form Title:
Document #:
INSTALLATION AND MAINTENANCE MANUAL
MM-EV005
(Form: DEF-006A-4)
Revision:
0
Document Title:
Date:
1” Cable Operated Water Drain Valve
May 5, 2022
Page:
10 of 11
Betts Industries Inc. ▪814·723·1250 ▪1800 Pennsylvania Ave. West ▪Warren, PA 16365 ▪www.BettsInd.com
Print Date: 6/20/2022 This form is considered uncontrolled 24 hrs. after print date.
6.18 Install the Lever (7) and Push Stem (6) utilizing the Roller Chain Connecting Link (11)
•The Side plate of the Roller Chain
Connecting plate can be removed
with a flat head screwdriver and
needle nose pliers.
•Use the flat head screwdriver push
the side plate back. Ensure that
the side plate isn’t damaged when
removed.
6.19 Install the Boot (12) onto the valve.
•To aid assembly, turn the top portion of the boot inside out and push completely
onto the valve body boss. Once installed roll top portion of boot into place.
6.20 Slide the Push Stem (6) and Lever (7) into the valve.
•Ensure that the Push Stem (6) does not damage the Push Stem O-ring (15) by
wiggling the push stem slightly during insertion.
6.21 With the Push Stem (6) and Lever (7) in place, install the Nylon Washers (10) on both
sides of the Lever (7) with the Binding Barrel (8)
6.22 Apply removable thread lock on the Button Cap Screw (9).
6.23 Screw the Button Cap Screw into the Binding Barrel (8) using a Phillips head screwdriver
and a 1/8” hex key (Allen) wrench in the Binding Barrel. Tighten down until the is minimal
slop between the NylonWashers (10) and the Lever (7). Overtightening will cause too much
friction and the valve will not operate properly. Manually actuate the valve to ensure the
spring closes the valve.
9
10 10
8
6
11
7

Form Title:
Document #:
INSTALLATION AND MAINTENANCE MANUAL
MM-EV005
(Form: DEF-006A-4)
Revision:
0
Document Title:
Date:
1” Cable Operated Water Drain Valve
May 5, 2022
Page:
11 of 11
Betts Industries Inc. ▪814·723·1250 ▪1800 Pennsylvania Ave. West ▪Warren, PA 16365 ▪www.BettsInd.com
Print Date: 6/20/2022 This form is considered uncontrolled 24 hrs. after print date.
7.0 Trouble Shooting Guide
Problem
Potential Cause
Potential Solution
Product is leaking out of the
inlet threads of the valve
Insufficient use of a thread sealant or tape
Use additional thread sealant or tape
Under tightened valve
Use a 1-5/8 wrench and tighten the
valve up to the sump or fitting
Damaged threads
Replace valve body or sump / fitting
Product is leaking past the
Main O-ring Seal (5)
The Main O-ring Seal (5) is incompatible with
product
Investigate chemical compatibility and
resolve
The Main O-ring Seal (5) is worn or damaged
Replace the Main O-ring Seal (5)
The O-ring Holder Stem (4) O-ring groove is
damaged
Replace the O-ring Holder Stem (4)
The Valve Body O-ring seat is damaged
Replace the Valve Body
Dirt or debris is between the Main O-ring seal
and the Valve body or O-ring Holder Stem
Remove dirt and debris from the seat
areas
The Spring Retainer (2) ID is worn or damaged
Replace the Spring Retainer (2)
Product is leaking past the
Push Stem O-ring (15)
The Push Stem O-ring Seal (15) is
incompatible with product
Investigate chemical compatibility and
resolve
The Push Stem O-ring Seal (15) is worn or
damaged
Replace the Push Stem O-ring (15)
The Push Stem (6) is damaged
Replace the Push Stem (6)
Dirt or debris is between the Push Stem O-ring
seal (15) and the Valve body or Push Stem (6)
Remove dirt and debris from the seat
areas
The Bushing (14) is worn
Replace the Bushing (14)
Product is leaking out of the
outlet threads
Insufficient use of a thread sealant or tape
Use additional thread sealant or tape
Under tightened Piping/fitting
Use wrench and tighten the piping/
fitting up to the valve
Damaged threads
Replace valve body or pipe/fitting
Valve won’t actuate
Over tightened Binding Barrel (8) and Button
Cap Screw (9)
Loosen the Button Cap screw (9) from
the Binding Barrel (8)
Check cable connection
Adjust cable connection to the valve
and or cable run
Valve won’t return closed
Cable is bound or too much cable friction
Minimize cable runs
Retaining Ring (1) was improperly installed and
has come out of the groove
Replace Retaining ring (1)
Spring (3) broke
Replace Spring (3)
Overtightened biding barrel
Loosen the binding barrel so there is
minimal friction between the Washer10
Spring Retainer (2) has bound the Main O-ring
Holder (4)
Replace the Spring Retainer (2) or
Main O-ring Holder (4)
This manual suits for next models
3
Table of contents
Other Betts Control Unit manuals
Popular Control Unit manuals by other brands
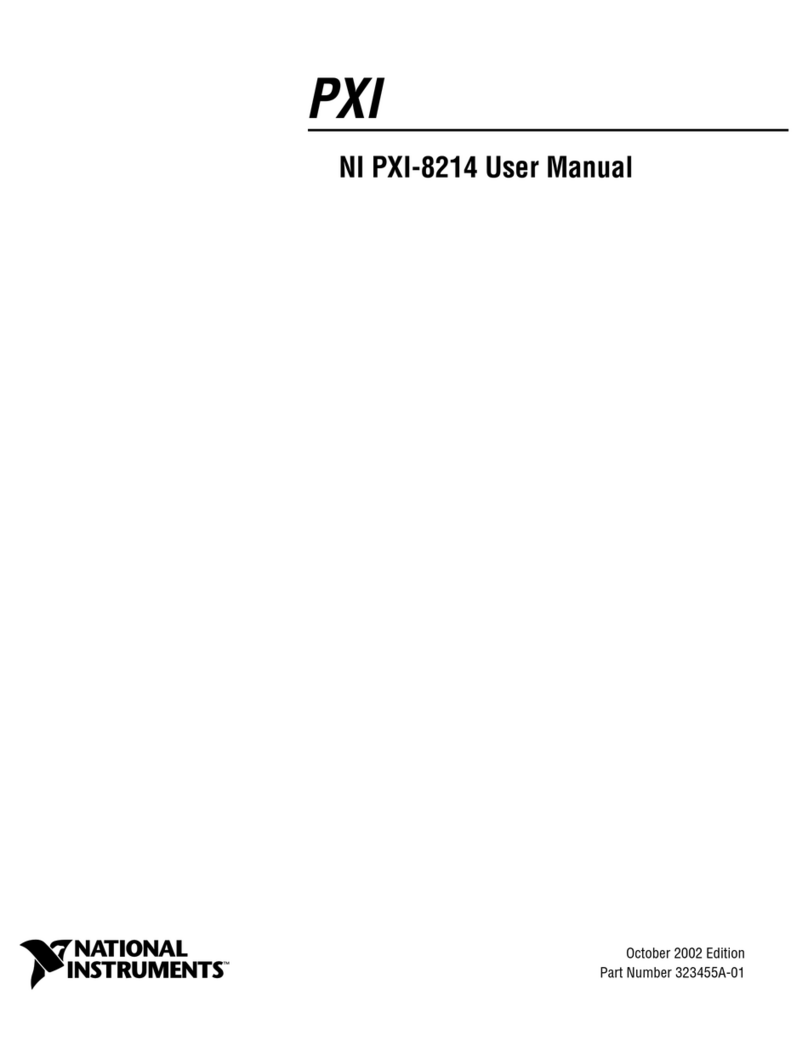
National Instruments
National Instruments PXI-8214 user manual

Miele
Miele A 300/2 operating instructions
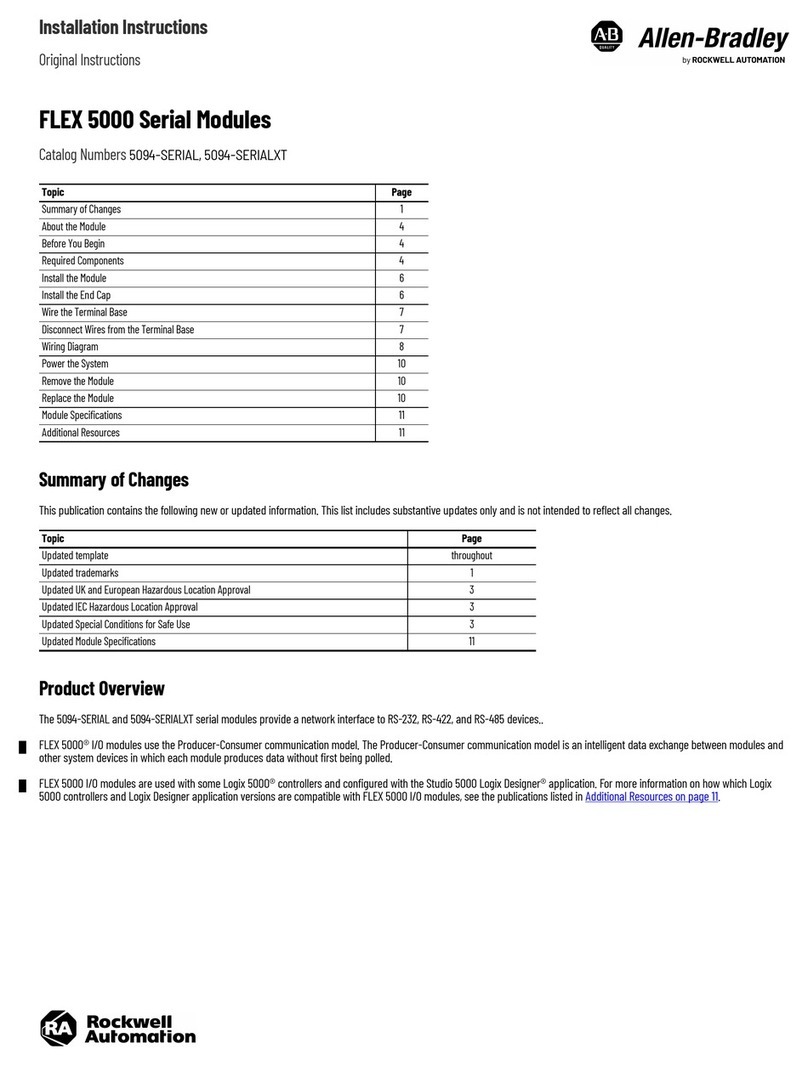
Rockwell Automation
Rockwell Automation Allen-Bradley FLEX 5000 Series installation instructions

HEIDENHAIN
HEIDENHAIN TNC 320 user manual
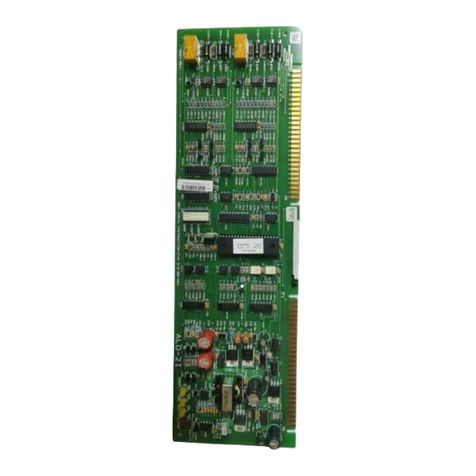
Siemens
Siemens ALD-2I installation instructions
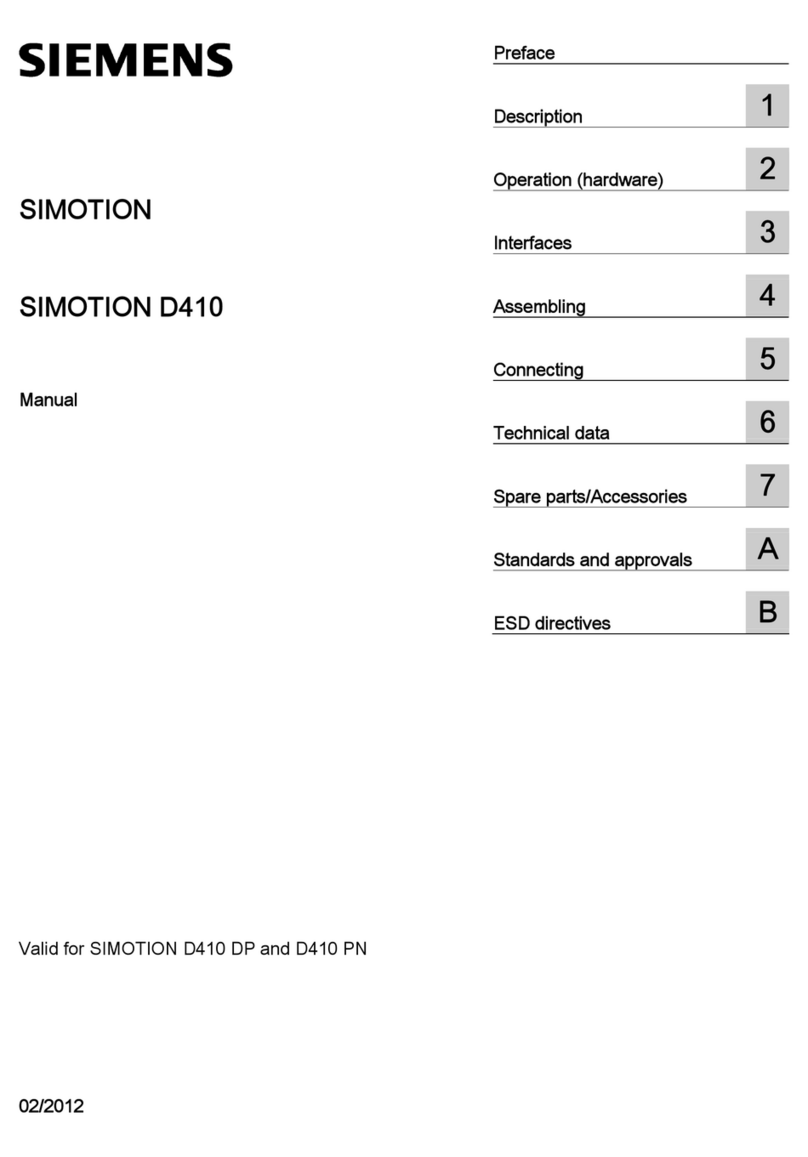
Siemens
Siemens SIMOTION D410 PN manual

iWave
iWave iW-RainboW-G17M Hardware user's guide
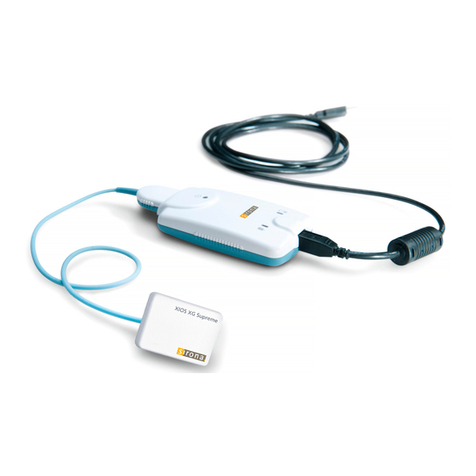
Sirona
Sirona XIOS XG Operating instructions and installation
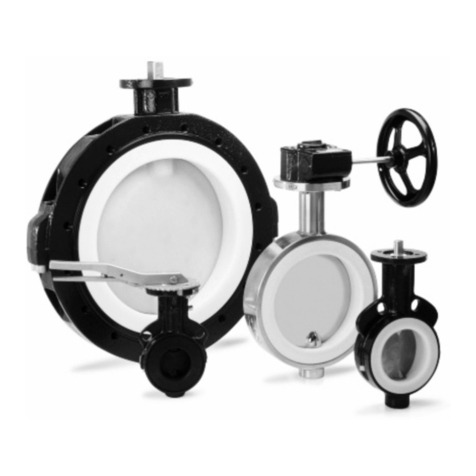
Richter
Richter NKS-C Series Installation and operating manual
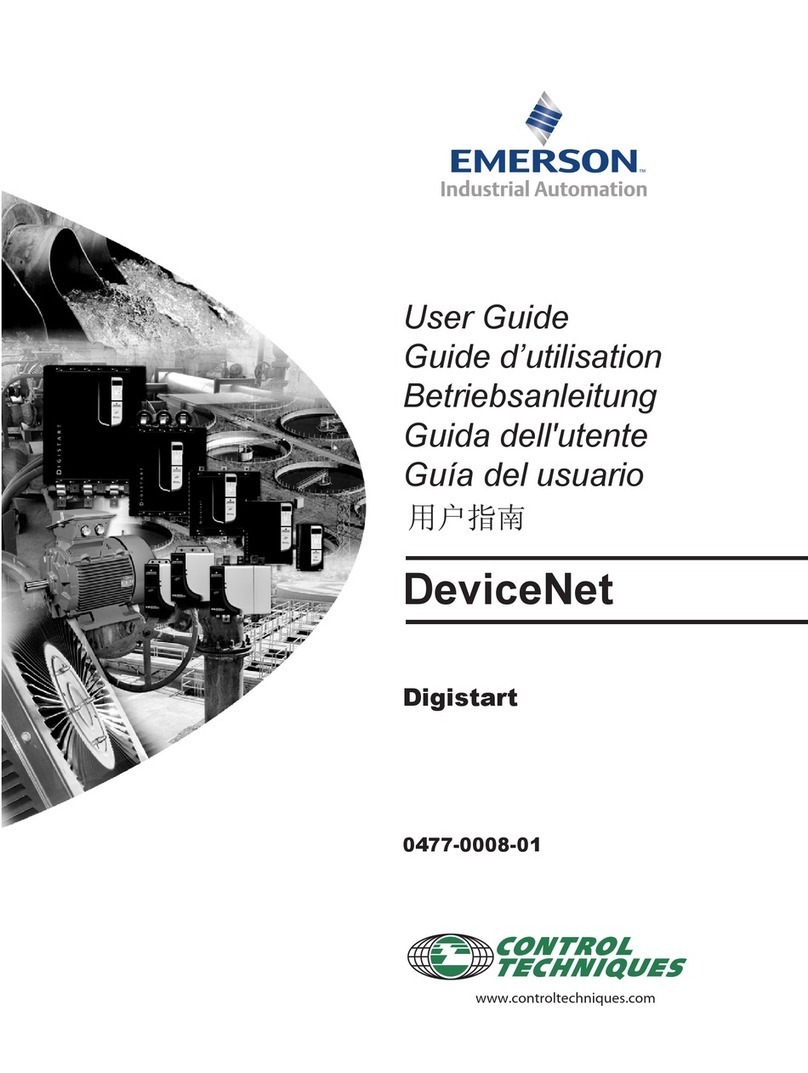
Control Techniques
Control Techniques EMERSON DeviceNet user guide
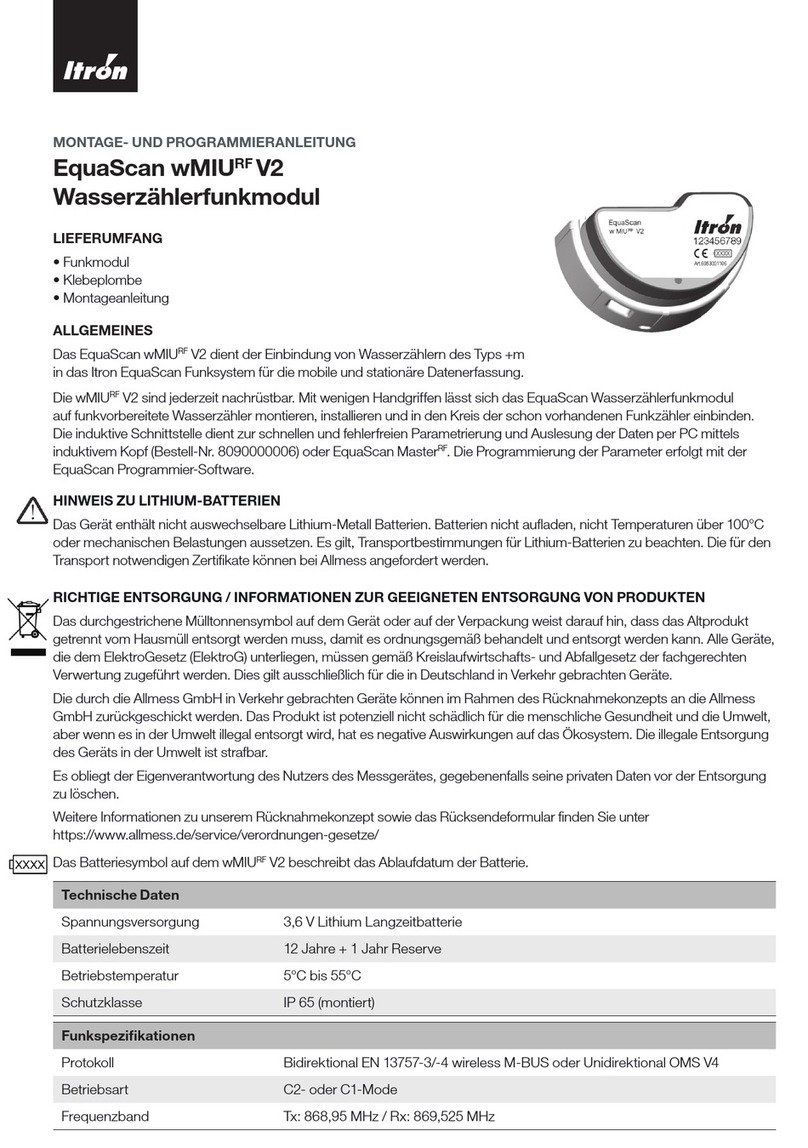
ITRON
ITRON EquaScan wMIURF V2 Assembly instruction
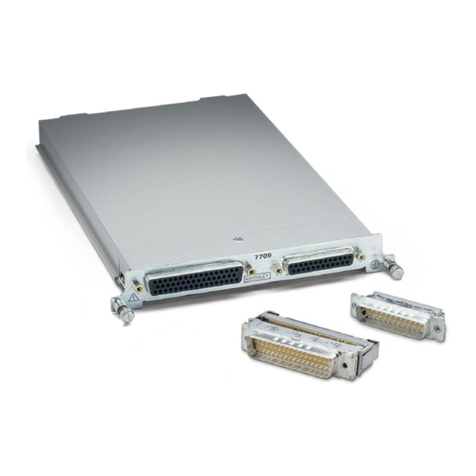
Keithley
Keithley 7709 user guide