BIFFI ICON3000 Series User manual

Copyright © Biffi. The information in this document is subject to change without notice. Updated data sheets can be obtained from our website www.biffi.it or from your nearest Biffi Center:
Biffi Italia s.r.l. - Strada Biffi 165, 29017 Fiorenzuola d'Arda (PC) – Italy PH: +39 0523 944 411 – [email protected]
Bif ICON3000
PROFIBUS DPV1 Module
Installation, Operation and Maintenance Manual
MAN 618-42 Rev. 7
November 2021

2
Installation, Operation and Maintenance Manual
MAN 618-42 Rev. 7
Table of Contents
Notes
November 2021
Revision Details
Rev. Date Description Prepared Approved
7 November 2021 General update (Migration to new template)
6 August 2017 Added Note for Base card FW 7.00 F.P. C.D.
5 October 2015 Added EDD, DTM and Redundancy application note references F.P. C.D.
4 October 2009 Updated PROFIBUS certication valid for life C.D. A.A.
3 May 2009 Added explanations to diagnostics data structure and other minor changes C.D. A.A.
2 May 2005 Added CERTIFICATION document C.D. A.A.
1 November 2004 Reviewed Usr_Prm string and Slot/Index assignment C.D. A.A.
0 October 2004 Instruction for rev. 4.0 PROFIBUS DPV1 Interface C.D. A.A.

i
Installation, Operation and Maintenance Manual
MAN 618-42 Rev. 7
Table of Contents
November 2021
Table of Contents
Table of Contents
Section 1: Introduction
Introduction ........................................................................................................... 1
Section 2: Operation and Storage
Operation and Storage............................................................................................ 2
Section 3: Communication Features
Communication Features........................................................................................ 3
Section 4: ICON2000v4_DPV1 Module
4.1 On Board Indication ...................................................................................... 4
Section 5: PROFIBUS DP Description
PROFIBUS DP Description........................................................................................ 5
Section 6: RS485 Transmission Mode
RS485 Transmission Mode ...................................................................................... 6
Section 7: Slave Redundancy
Slave Redundancy ................................................................................................... 8
Section 8: ICON2000v4_DPV1 Power-Up
ICON2000v4_DPV1 Power Up............................................................................... 11
Section 9: Data Exchanged During Parameterization
Data Exchanged During Parameterization............................................................. 12

ii
Table of Contents
November 2021
Installation, Operation and Maintenance Manual
MAN 618-42 Rev. 7
Table of Contents
Section 10: Data Exchange Mode
10.1 Cyclic Communications DPV0 ..................................................................... 15
10.1.1 Output Data..................................................................................... 15
10.1.2 Input Data ........................................................................................ 16
10.1.3 Diagnosis Message ........................................................................... 18
10.2 Acyclic Communication DPV1..................................................................... 23
10.2.1 Nameplate ....................................................................................... 23
10.2.2 General Data .................................................................................... 24
10.2.3 Maintenance Information ................................................................. 24
10.2.4 Alarm and Warning Log .................................................................... 26
10.2.5 Maintenance Commands.................................................................. 27
Section 11: Data at Local Operator Interface
11.1 Bus Control ................................................................................................. 28
11.2 Node Report ............................................................................................... 29
11.3 Bus Signal Failure Indication ........................................................................ 30
Appendix A: GSD File
GSD File ................................................................................................................ 31
Appendix B: PROFIBUS Certicate
PROFIBUS Certicate............................................................................................. 34
Appendix C: Note for Base Card FW 7.00
Note for Base Card FW 7.00................................................................................... 35

Installation, Operation and Maintenance Manual
MAN 618-42 Rev. 7 November 2021
Introduction 1
Section 1: Introduction
Section 1: Introduction
The ICON2000v4_DPV1 is an electronic module that allows connecting the Bif electrical actuator
ICON3000 to a PROFIBUS DP network. The module has its microprocessor and a program stored
internally controls it, it works as a pure bus interface and does not affect the actuator control
integrity. It is installed inside the actuator housing and takes the electrical power from the actuator
power supply module. The RS485 interface is located on the module board. The PROFIBUS network is
fully isolated from the actuator electronics.
The ICON2000v4_DPV1 is designed to support PROFIBUS redundant communication by installing
two electronic modules on the same Bif electrical actuator ICON3000.

November 2021
Installation, Operation and Maintenance Manual
MAN 618-42 Rev. 7
Operation and Storage
2
Section 2: Operation and Storage
Section 2: Operation and Storage
The module is designed to work and to be stored in the same environment of the actuator.

Installation, Operation and Maintenance Manual
MAN 618-42 Rev. 7 November 2021
Communication Features 3
Section 3: Communication Features
Section 3: Communication Features
Communication protocol : PROFIBUS DP according to EN 50170
Network topology : Line (bus) structure. With repeaters tree structures
can also be realized
Transmission medium : Twisted, screened copper cable according to EN 50170
Data rate : 9.6 19.2 45.45 93.75 187.5 500 1500 Kbit/second
Cable length without repeater : 1200 1200 1200 1200 1000 400 200 m
Station type : DPV0 and DPV1 slave
Device number : 32 devices per segment without repeater (max 126, with repeaters)
Bus access : Token-passing between masters and polling for slaves
Electrical power : Actuator powered (as option: auxiliary external voltage supply)
Bus termination : Congurable on board via local operator interface of actuator
Temperature : -40 °C, +85 °C
Fieldbus redundancy : Two independent communication interfaces
EMC protections : EN 50081-2 and EN 50082-2
Types of operation : Cyclic data exchange, Sync mode, Freeze mode, Fail-safe mode
Baud rate : Automatic recognition
Addressing : Congurable via local operator interface

November 2021
Installation, Operation and Maintenance Manual
MAN 618-42 Rev. 7
ICON2000v4_DPV1 Module4
Section 4: ICON2000v4_DPV1 Module
LED DL1
LED DL2
LED DL3
Jumper J2
LED DL6
LED DL5
LED DL4
4.1 On Board Indication
Five LEDs are mounted on the ICON2000v4_DPV1 to give the following indications for Field service.
LEDs indications are active only when jumper JP2 is closed.
DL1 (Red) Data Area Empty: ON when Data Area on interface card is not yet loaded.
BLINK when Data Area is being read from base card.
OFF when Data Area is completely loaded.
DL2 (Red) Base comm: ON when the communication between the base card
and the interface is not working properly.
OFF when the communication between the base card
and the interface is correct.
DL3 (Orange) Slave State: ON when the interface acts as an Primary Slave (i.e. it is the
interface with a valid communication with the Master).
BLINK when the interface acts as a Backup Slave and it is ready
(only for redundant conguration).
OFF when the interface is not communicating with any Master.
DL4 (Green) Termination: ON when the on bard PROFIBUS termination has been inserted.
OFF when the on bard PROFIBUS termination has not been inserted.
DL5 (Green) PROFIBUS: ON when PROFIBUS communication has been established and the
interface has entered in DATA_EX state.
DL6 (Green) Power: ON when the interface is correctly powered.
More indications are given on local operator interface as described in Section 11.2, Node Report.
Section 4: ICON2000v4_DPV1 Module
The module consists in a single PCB that is installed inside the actuator housing. It is connected to the
ICON3000 base card via strip connector. The internal wiring connects the PROFIBUS data lines to the
actuator terminal board.
Figure 1

Installation, Operation and Maintenance Manual
MAN 618-42 Rev. 7 November 2021
PROFIBUS DP Description 5
Section 5: PROFIBUS DP Description
Section 5: PROFIBUS DP Description
PROFIBUS is a vendor-independent, open eld bus standard used in a wide range of application
in process automation. Vendor independence and openness are ensured by the international
standards EN 50170 and EN 50254. The DP communication prole is designed for data exchange at
the eld level. The central controllers (as PLC) communicate via serial connection with eld devices
(as sensors and actuators). Data exchange is mainly cyclic. The central controller (called Master)
cyclically reads the input information from the eld devices (called Slaves) and cyclically writes the
output information to the slaves. In addition, PROFIBUS DP provides communication services for
parameterization, alarm handling and monitoring of intelligent eld devices. The maximum number
of Master and Slave devices in a bus segment is 32 without repeaters. With repeaters, the number can
be extended to 126. The maximum cable length depends on the speed of transmission. Higher is the
speed, shorter is the length. For instance, with baud rate 93.75 kb/s, the max cable length is 1,200 m
without repeaters.
Mono-master or multi-master system conguration can be provided. Bus access is controlled by token
passing procedure between masters and master-slave procedure (polling) between master and slaves.
Types of devices:
DP Master Class 1 (DPM 1): This is the central controller that cyclically exchange information
with the eld devices. Typical devices are PLC or PC.
DP Master Class 2 (DPM 2): These devices are necessary for commissioning, maintenance
and diagnostics.
Slave: Field device such transmitters, actuators, drives, etc.
Figure 2 below shows a PROFIBUS DP conguration with two Master devices and different Slave devices.
Figure 2
2000 actuators
Logical token ring between master devices
Master
devices
Slave devices
General Drive Transmitter
PLC PC

November 2021
Installation, Operation and Maintenance Manual
MAN 618-42 Rev. 7
RS485 Transmission Mode6
Section 6: RS485 Transmission Mode
Section 6: RS485 Transmission Mode
The ICON2000v4_DPV1 module uses a half duplex, multidrop, serial communication line RS485. The
module communicates with the Masters via its RS485 interface and the transmission media consists in
a shielded twisted pair cable. Transmission speed from 9.6 kbit/s to 1.5 Mbit/s are available. One unique
transmission speed is allowed for all devices on the bus when the system works.
All devices are connected in a bus structure. Up to 32 station (Master and Slaves) can be connected in
one segment without repeaters. Repeaters can be used to extend the number of device up to 126 and
to enlarge the network area. Table 1 shows the relationship between baud rate and segment length.
Table 1.
The bus must be terminated by an active bus terminator at the beginning and at the end of each
segment. Only two terminations in one bus segment must be provided. To ensure error-free
operation, both bus terminators must be powered. The maximum cable length depends on the
transmission speed. Cable lengths indicated in Table 1 are based on type A cable, as specied by the
EN 50170, having the following characteristics.
• Impedance from 135 to 165 ohm
• Capacity < 30 pF/m
• Loop resistance 110 ohm/km
• Wire gauge 0.64 mm
• Conductor area > 0.34 mm2
The use of cable of previously used type B is not recommended.
The data lines must not be reversed. Use of shielded cable is mandatory for having high system
immunity against electromagnetic disturbs. The shield should be connected to ground on both
sides. The data lines should be kept separate from all other cables. It should be laid in separate,
conductive and earthed cable trunking. It must be ensured that there are no voltage difference
between individual nodes of PROFIBUS DP.
Baud Rate Maximum segment length (no repeater)
9.6 K 1200 m
19.2 K 1200 m
45.45 K 1200 m
93.75 K 1000 m
187.5 K 1000 m
500 K 400 m
1500 K 200 m
DEVICE 1 DEVICE 2
CABLE BUS TERMINATION
shielding
VP (5 V DC)
Data line
Data line
Figure 3

VP
390 ohm
390 ohm
220 ohm
Rx/Tx-P-in
Rx/Tx-N-in
Rx/Tx-P-out
Rx/Tx-N-out
DGND
Installation, Operation and Maintenance Manual
MAN 618-42 Rev. 7 November 2021
RS485 Transmission Mode 7
Section 6: RS485 Transmission Mode
The ICON2000v4_DPV1 module takes its electrical supply from the actuator power supply module.
The RS485 bus transceiver is isolated from the actuator electronics. Also, the voltage supply of
the bus termination is isolated. The ICON2000v4_DPV1 module is equipped with on-board bus
termination that should be used when the actuator is at the beginning or at the end of the bus
segment and if there is no external termination. The bus termination can be switched on the data
lines by means of a link, congurable via local operator interface.
Since the bus termination is a crucial component to ensure error-free operation, it is important that
termination remains powered also when the actuator supply has left. If the internal termination are
used, it is suggested to connect to the actuator also an auxiliary 18/36 V AC/DC generated by safe
source that will supply just the actuator electronics and the PROFIBUS termination.
Figure 4 below shows the wiring in case of not redundant connection. The termination must be linked
to the data lines only if the actuator is at the beginning or at the end of the bus segment.
Figure 4
Data line -
Shield
Data line +
Termination
control
PROFIBUS
RS485
transceiver
ICON2000_DPV1r
module
Terminal
board
bus out bus in
PLC
MAINS MAINS
Term. OFF Term. OFFTerm. ON
MAINS + 18-36 V AC/DC
from UPS
BUS cable
Term. ON
Figure 5 below shows the bus with an actuator at the end of the bus segment. Ensure that the
terminations are supplied. Also, if the mains fails, an auxiliary voltage supply generated by an UPS is
connected to the actuator to supply the electronics and the termination.
Figure 5

November 2021
Installation, Operation and Maintenance Manual
MAN 618-42 Rev. 7
Slave Redundancy8
Section 7: Slave Redundancy
Section 7: Slave Redundancy
The ICON2000v4_DPV1 is designed to allow the actuator to acts as a redundant slave as described
in this section, additional information about Slave Redundancy of ICON2000v4_DPV1 are descripted
on “DTDE443 Redundancy Operation Description”, and “MDE236 Integration of ICON3000 in
Redundant S7-400H System”.
To achieve the Slave Redundancy, two ICON2000v4_DPV1 modules are mounted in the actuator: in
this way the actuator is equipped with a full redundant communication interface as specied by the
PROFIBUS Guideline. The schematic of the Redundant Slave is as follow:
Figure 6
PROFIBUS
PROFIBUS
RS485
Transceiver
PROFIBUS
ASIC
microprocessor
Internal comm.
channel
Internal comm.
channel
Actuator
base card
PROFIBUS
RS485
Transceiver
PROFIBUS
ASIC
Internal comm.
channel
Internal comm.
channel
The two interfaces are indicated as Primary Slave and Backup Slave. The following simple rules dene
the redundancy strategy:
• An internal arbitration denes the role of the interfaces during the start-up.
• The base card tries rst to establish a valid communication with the Primary Slave.
• There is always just one Slave (Primary or Backup) with a valid communication with the
PROFIBUS line. It is indicated Active Slave.
• Both Slaves can answer to PROFIBUS interrogation: only the Active Slave has valid data and
this condition is indicated by a specic bit in the cyclic communication.
• Both Slaves receive the commands from Master but the base card can execute only the
commands from the Active Slave.
• When the Primary Slave stops to work or its interface does not sense any PROFIBUS
communication, the base card enables the Backup Slave that becomes Active.
• After the Primary Slave fails, the PROFIBUS communication continues via the current Active
Slave. A maintenance service is necessary to restore the Primary Slave.
• The PROFIBUS slave addresses are assigned for each interface from the Local Operator
Interface of the actuator and the addressing is depending on the redundant system
structures that has been selected.
microprocessor

Section618/42Page8
Installation, Operation and Maintenance Manual
MAN 618-42 Rev. 7 November 2021
Slave Redundancy 9
Section 7: Slave Redundancy
Master
#1
Master
#2
Channel 1 Channel 2
In this layout, the two interfaces may have the same address because the two interfaces are on
different channels. A synchronization method must be active between the Master stations to take the
information from the Active Slave.
Master
Figure 7
Figure 8
In this layout, the two interfaces shall have different addresses because the two interfaces are on the
same channel.
The very exible redundancy strategy implemented in the ICON2000v4_DPV1 module allows also
different layout that the Master station can drive. The bus terminations can be switched on each data
lines by means of two links, congurable via local operator interface.

VP
390 ohm
390 ohm
220 ohm
Rx/Tx-P-in
Rx/Tx-N-in
Rx/Tx-P-out
Rx/Tx-N-out
DGND
VP
390 ohm
390 ohm
220 ohm
Rx/Tx-P-in
Rx/Tx-N-in
Rx/Tx-P-out
Rx/Tx-N-out
DGND
November 2021
Installation, Operation and Maintenance Manual
MAN 618-42 Rev. 7
Slave Redundancy10
Section 7: Slave Redundancy
Figure 9
Data line -
Data line -
Data line +
Data line +
bus out
Shield
Shield
Terminal
board
bus in
Termination
control
Termination
control
ICON2000_DPV1r
module #1
ICON2000_DPV1r
module #2
bus out bus in
PROFIBUS
RS485
transceiver
PROFIBUS
RS485
transceiver
Figure 9 below shows the wiring necessary in case of redundant slave. The termination must be linked
to the data lines only if the actuator is at the beginning or at the end of the bus segment.

Installation, Operation and Maintenance Manual
MAN 618-42 Rev. 7 November 2021
ICON2000v4_DPV1 Power-Up 11
Section 8: ICON2000v4_DPV1 Power-Up
Figure 10
Section 8: ICON2000v4_DPV1 Power-Up
On power-up, the module checks the baud rate and then it waits for the “parameterization” telegram
from the Master. The parameterization message contains user information needed for actuator
operation and listed in the Section 9: ‘Data exchanged during parameterization‘.
After that, the module waits for the “conguration” telegram from Master. The conguration
message contains the number of input and output bytes reserved in the memory of the Master
device for each slave. Only the number of bytes determined in the conguration is transmitted
between Master and Slave. This information is called “module”. The ICON2000v4_DPV1 board
implements the following modules:
• Module 1 : 1 byte output; 2 bytes input
• Module 2 : 4 byte output; 8 bytes input
• Module 3 : 1 byte output; 2 bytes input - Consistent
• Module 4 : 4 byte output; 8 bytes input - Consistent
Consistent is an attribute that specify the capability of the module to maintains data consistency
over the entire data length. In this way, the data will not change during the reading by the PROFIBUS
DP-Master. For example, if module 2 is selected, the output telegram consists in 4 bytes and the input
telegram in 8 bytes.
When parameters and conguration are correct, the module enters in “data exchange mode” and
starts with normal operation. The Master cyclically sends commands to the Slave and read its status.
Figure 10 shows the state machine of a DP slave:
Wait
parameterization
Wait
configuration
Data exchange
mode
Set Slave address
Check parameters
Parameterization correct
Check conguration
Conguration not OK
Slave Fault
Configuration correct
Cyclic data exchange
Power on

November 2021
Installation, Operation and Maintenance Manual
MAN 618-42 Rev. 7
Data Exchanged During Parameterization12
Section 9: Data Exchanged During Parameterization
Section 9: Data Exchanged During
Parameterization
The following data are sent to the ICON2000v4_DPV1 interface:
Table 2.
Byte Name Type Range Default EU
0 Reserved DP V1 1 byte ---
1 Reserved DP V1 1 byte ---
2 Reserved DP V1 1 byte ---
3 Storage Format 1 byte 0LSB rst LSB rst
1MSB rst
4 Fail-safe Action 1 byte 0 Off Off
1Close
2Open
3Stayput
4 Go to position
5 Delay before initiating safe operation 1 byte 0-255 4 seconds
6 Safe Position 1 byte 0-100 50 %
7 Timer Open direction – status 1 byte 0 0ff Off
1On
8 Timer Open direction – on time 1 byte 2-200 2 seconds
9 Timer Open direction – off time 1 byte 1-200 2 seconds
10 Timer Open direction – start position 1 byte 0-100 0 %
11 Timer Open direction – stop position 1 byte 0-100 100 %
12 Timer Close direction – status 1 byte 0 Off Off
1On
13 Timer Close direction – on time 1 byte 2-200 2 sec
14 Timer Close direction – off time 1 byte 1-200 2 sec
15 Timer Close direction – start position 1 byte 0-100 100 %
16 Timer Close direction – stop position 1 byte 0-100 0 %
17 Reserved 1 byte ---
18 Dead band 1 byte 1-255 10 tenth of %
19 Motion inhibit 1 byte 1-255 6 seconds
It should be noted that every time the PROFIBUS communication is established, the parameterization
string will be sent to the device, writing the parameters to the set up values. The values in
parameterization string shall be modied at the Master station.
Byte 0-2 Reserved for DPV1
Byte 3 Storage format
It denes the format of the variables that are transmitted on 2 or 4 bytes.
The setting of this parameter affects the format of the following data:
— Output Data (if Module 2 is selected)
Position Request
— Input Data (if Module 2 is selected)
Actuator Position, Output Torque
— General Maintenance Info Slot 2 Index 0
Actuator Position, Output Torque, Opening
Time, Closing Time, Contactor Cycles, Motor
Run Time, Time Without Power, Utilization Rate
— Recent Maintenance Info Slot 2 Index 1
Recent Contactor Cycles, Recent Motor Run
Time, Recent Time Without Power, Recent
Utilization Rate
— Value 0: LSB byte is transmitted rst (default setting)
1: MSB byte is transmitted rst

Installation, Operation and Maintenance Manual
MAN 618-42 Rev. 7 November 2021
Data Exchanged During Parameterization 13
Section 9: Data Exchanged During Parameterization
Byte 4 Fail-safe action
It denes the action of the actuator in case of loss of the bus signal. The action takes
place only if the local selector is on REMOTE position and if the bus is operating.
When the bus signal restores, the actuator also restores at its normal functioning.
— Value 0: Off - disable (default setting)
1: Close
2: Open
3: Stayput
4: Go to position indicated in the parameter ‘Safe position’
Byte 5 Delay before initiating fail-safe operation
It denes the delay before execute the programmed Safe Action.
— Value minimum: 0 second
maximum: 255 seconds
default value: 4 seconds
Byte 6 Safe position
It denes the Safe position when ‘Safe Action: go to position’ is selected.
— Value minimum: 0 %
maximum: 100%
default value: 50%
Byte 7 Timer Open Direction - Status
It enables the Timer function in Open direction.
— Value 0: Off - disable (default setting)
1: On
Byte 8 Timer Open Direction – On time
It denes the On time of the Timer function in opening.
— Value minimum: 2 seconds
maximum: 200 seconds
default value: 2 seconds
Byte 9 Timer Open Direction – Off time
It denes the Off time of the Timer function in opening.
— Value minimum: 1 second
maximum: 200 seconds
default value: 2 seconds
Byte 10 Timer Open Direction – Start position
It denes the start position of the Timer function in opening.
— Value minimum: 0 %
maximum: 100%
default value: 0%
Byte 11 Timer Open Direction – Stop position
It denes the stop position of the Timer function in opening.
— Value minimum: 100 %
maximum: 0%
default value: 100%

November 2021
Installation, Operation and Maintenance Manual
MAN 618-42 Rev. 7
Data Exchanged During Parameterization14
Section 9: Data Exchanged During Parameterization
Byte 12 Timer Close Direction - Status
It enables the Timer function in close direction.
— Value 0: Off - disable (default setting)
1: On
Byte 13 Timer Close Direction – On time
It denes the On time of the Timer function in closing.
— Value minimum: 2 seconds
maximum: 200 seconds
default value: 2 seconds
Byte 14 Timer Close Direction – Off time
It denes the Off time of the Timer function in closing.
— Value minimum: 1 second
maximum: 200 seconds
default value: 2 seconds
Byte 15 Timer Close Direction – Start position
It denes the start position of the Timer function in closing.
— Value minimum: 100 %
maximum: 0%
default value: 100%
Byte 16 Timer Close Direction – Stop position
It denes the stop position of the Timer function in closing.
— Value minimum: 0 %
maximum: 100%
default value: 0%
Byte 17 Reserved
Byte 18 Dead band
It denes in tenth of % the Dead band of the positioning function available on the
modulating actuator. The movement is inhibited until the difference between
current position and requested position (position error) is lower than Dead band.
— Value minimum: 1 0.1%
maximum: 255 22.5%
default value: 10 1.0%
Byte 19 Motion inhibit time
It denes the minimum delay between two cycles of the motor when the actuator
is in modulating service. It allows to adjust the number of start per hour of the
electric motor.
— Value minimum: 1 second
maximum: 255 seconds
default value: 6 seconds

Installation, Operation and Maintenance Manual
MAN 618-42 Rev. 7 November 2021
Data Exchange Mode 15
Section 10: Data Exchange Mode
Section 10: Data Exchange Mode
The following paragraph describes the input and output messages of ICON2000v4_DPV1 interface
when working in “data exchange mode” for “cyclic data” and “acyclic data”. In all cases, it is called
“input signal” a data owing from actuator to bus, vice-versa it is called “output signal” a data owing
from bus to slave.
10.1 Cyclic Communications DPV0
10.1.1 Output Data
BYTE = 0
Bit 0 = 1 : Close Command
Bit 1 = 1 : Open Command
Bit 2 = 1 : Stop Command
Bit 3 = 1 : ESD Command***
Bit 4 = 1 : Enable Positioner*
Bit 5 : Reserved
Bit 6 : Reserved
Bit 7 : Reserved MODULE 1 / 3
BYTE = 1
Bit 0 = 1 : Reserved
Bit 1 = 1 : Reserved
Bit 2 = 1 : Reserved
Bit 3 = 1 : Reserved
Bit 4 : Reserved
Bit 5 : Reserved
Bit 6 : Reserved
Bit 7 : Reserved
BYTE = 2
POSITION REQUEST**
BYTE = 3
POSITION REQUEST**
MODULE 2 / 4
* In case of module 1: Reserved
** Position request: Integer 16 bits (value 0 = 0%; value 1000 = 100.0%)
*** See Appendix C: Note for Base card FW 7.00

November 2021
Installation, Operation and Maintenance Manual
MAN 618-42 Rev. 7
Data Exchange Mode16
Section 10: Data Exchange Mode
10.1.2 Input Data
BYTE = 0
Bit 0 = 1 : Close limit
Bit 1 = 1 : Open limit
Bit 2 = 1 : Closing
Bit 3 = 1 : Opening
Bit 4 = 1 : ESD active***
Bit 5 = 1 : Loc. Sel. on Remote
Bit 6 = 1 : Loc. Sel. on Local
Bit 7 = 1 : Loc. Sel. on Off
BYTE = 1
Bit 0 = 1 : Interlock open active
Bit 1 = 1 : Interlock close active
Bit 2 = 1 : Fail-safe action
Bit 3 = 1 : Int. data updated*
Bit 4 = 1 : Warning
Bit 5 = 1 : Channel 1 active
Bit 6 = 1 : Valid data**
Bit 7 = 1 : Alarm MODULE 1 / 3
BYTE = 2
ACTUATOR POSITION §
BYTE = 3
ACTUATOR POSITION §
BYTE = 4
Bit 0 = 1 : Monitor relay
Bit 1 = 1 : Motion inhibited
Bit 2 = 1 : DIN 1
Bit 3 = 1 : DIN 2
Bit 4 = 1 : DIN 3
Bit 5 = 1 : DIN 4
Bit 6 = 1 : DIN 5
Bit 7 = 1 : DIN 6
BYTE = 5
Bit 0 = 1 : Aux_in_open
Bit 1 = 1 : Aux_in_close
Bit 2 = 1 : Aux_in_stop
Bit 3 = 1 : Aux_in_bus-on
Bit 4 = 1 : HW remote mode
Bit 5 = 1 : Positioner mode
Bit 6 : Reserved
Bit 7 : Reserved
BYTE = 6
OUTPUT TORQUE §§
BYTE = 7
OUTPUT TORQUE §§
MODULE 2 / 4
* ‘Internal data updated’ is set to 1 when the Active Slave has updated its internal data area and the acyclic
communications can read updated values.
** ‘Valid data’ is set to 1 when the PROFIBUS interface is the Active Slave and the cyclic communications
contains valid data.
*** See Appendix C: Note for Base card FW 7.00.
§ Position: Integer 16 bits (value 0 = 0%; value 1000 = 100.0%)
§§ Torque: Integer 16 bits (OP: value 0 = 0%; value –100 = 100% - CL: value 0 = 0%; value +100 = 100%)
Other manuals for ICON3000 Series
10
Table of contents
Other BIFFI Control Unit manuals
Popular Control Unit manuals by other brands
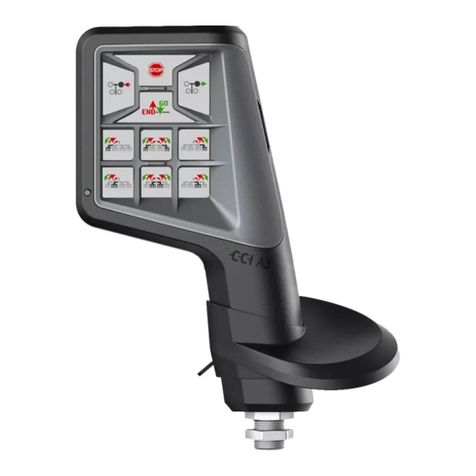
isobus
isobus CCI A3 operating instructions
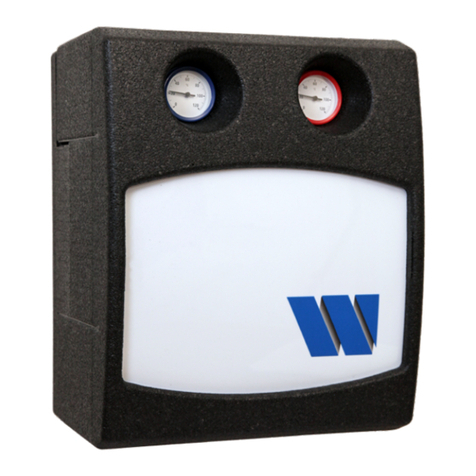
Watts
Watts FlowBox HKF25 Series Installation and operating manual
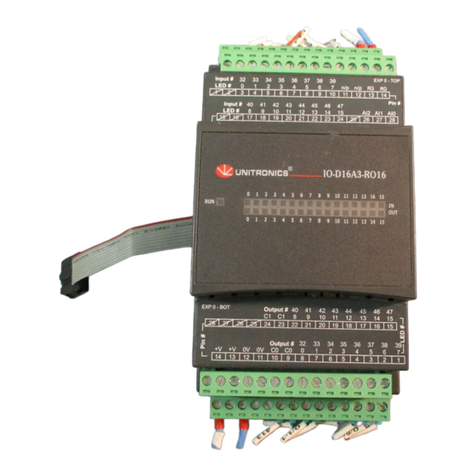
Unitronics
Unitronics IO-D16A3-RO16 installation guide
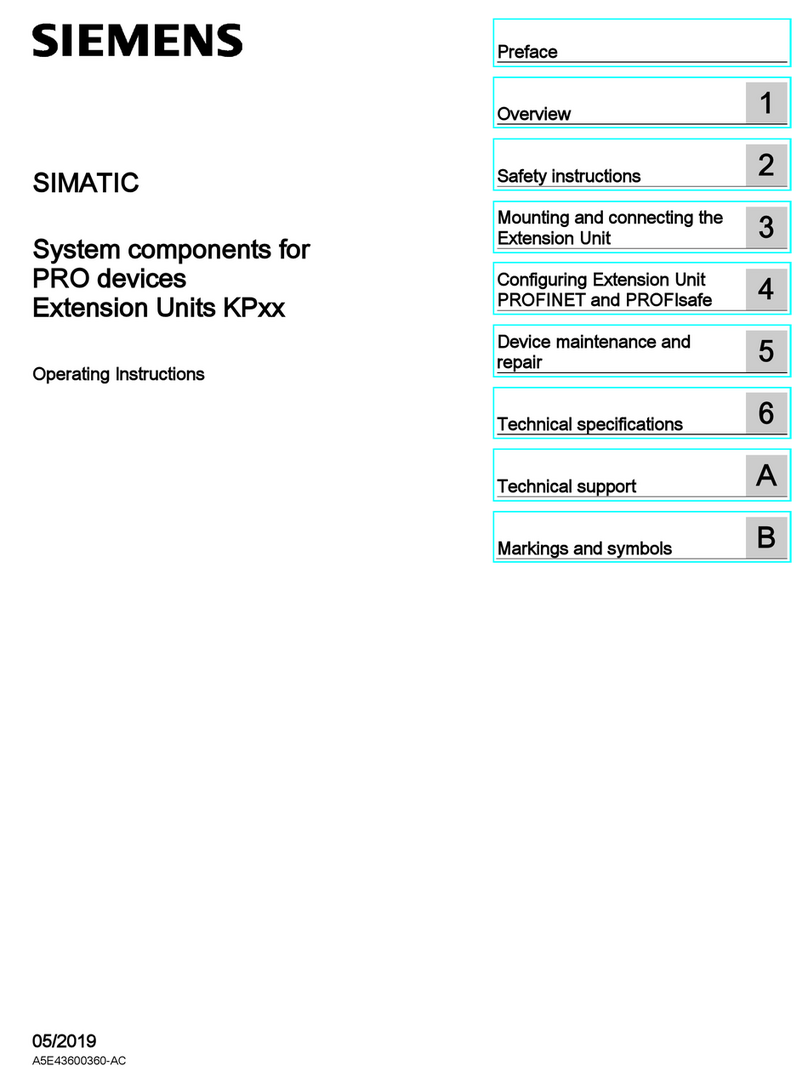
Siemens
Siemens SIMATIC PRO Extension Units KP Series operating instructions
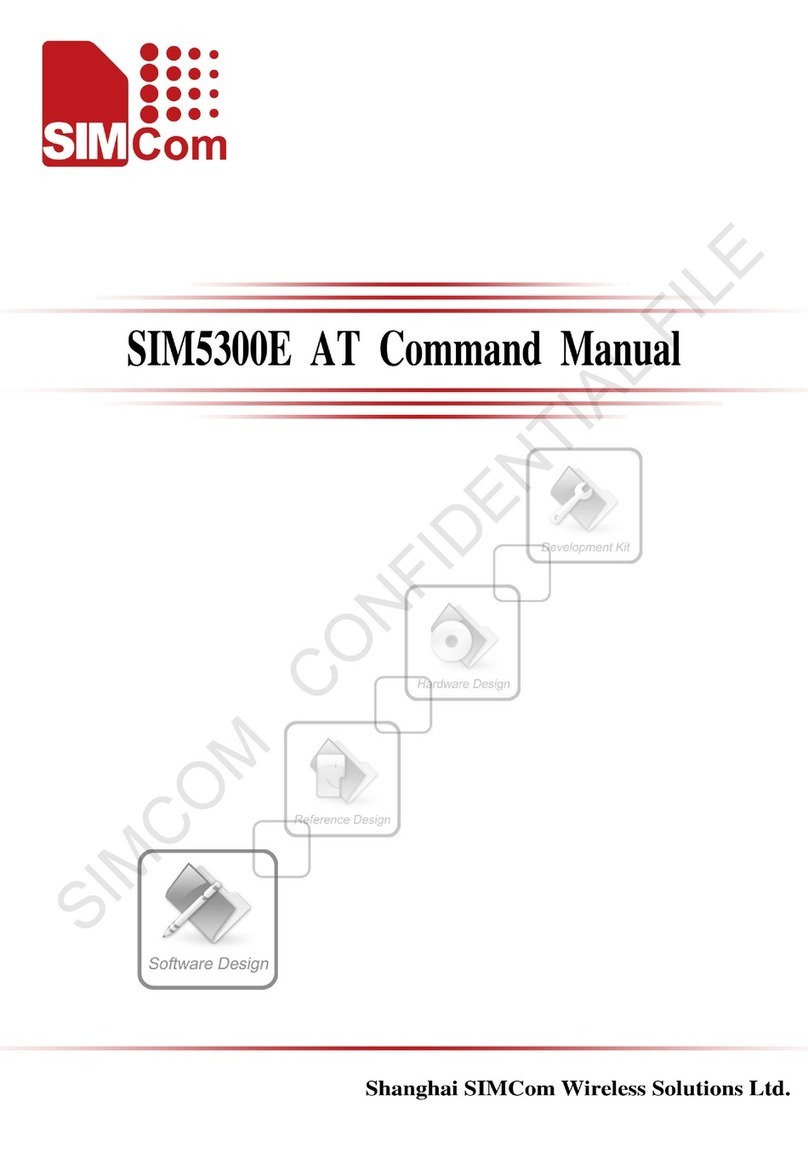
SimCom
SimCom SIM5300E AT Command manual

Contec
Contec CNT24-2GY user guide
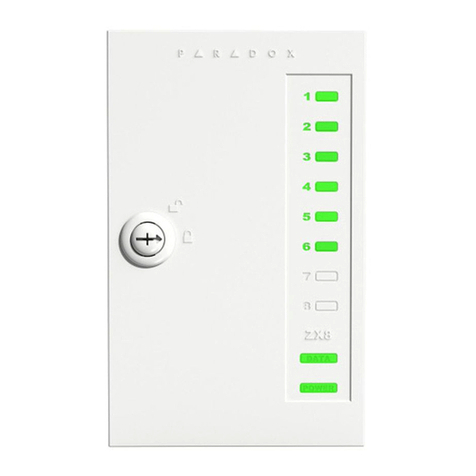
Paradox
Paradox ZX82 installation manual
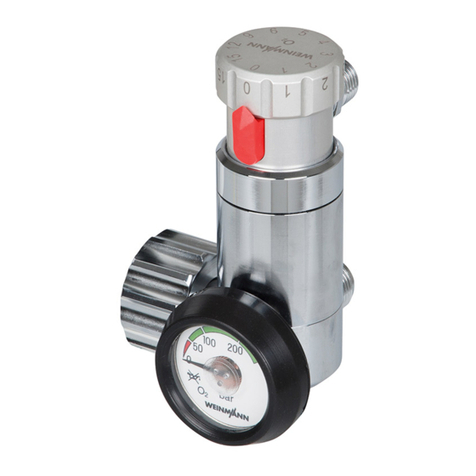
Weinmann
Weinmann OXYWAY Instructions for use

Zurn Wilkins
Zurn Wilkins 375 Installation, Testing, Maintenance Instructions
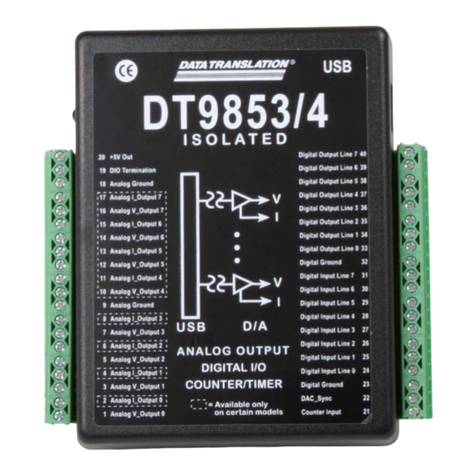
Data Translation
Data Translation DT9850 Series user manual

Motorola
Motorola MVME2300SC Series Installation and use

Wolf
Wolf FWS-2-60 installation instructions