BIFFI IMVS2000v2 User manual

Installation, Operation and Maintenance Manual
MAN720_IMVS2000v2_IOM Rev. 6
September 2019
Bif IMVS2000v2
Integrated Monitoring Valve System

MAN720_IMVS2000v2_IOM Rev. 6

I
Installation, Operation and Maintenance Manual Table of Contents
September 2019
MAN720_IMVS2000v2_IOM Rev. 6
Table of Contents
Table of Contents
Section 1: Reference Documents
Section 2: General Safety Instructions
2.1 Manufacturer................................................................................................ 2
2.2 Intended Use................................................................................................. 2
2.3 Terms and Conditions ................................................................................... 3
2.4 Manufacturer’s Liability................................................................................. 3
2.5 Applicable Standards and Regulations........................................................... 4
2.6 CSA/CSAus Certifications Details................................................................... 4
Section 3: Storage
Section 4: Device Description
4.1 General Description ...................................................................................... 8
4.1.1 Main Features..................................................................................... 8
4.2 Identification of the Main Parts...................................................................... 9
4.3 Technical Specifications .............................................................................. 12
4.4 Overall Dimensions ..................................................................................... 14
4.5 Options....................................................................................................... 14
Section 5: Working Principle and Detailed Description
5.1 Working Principle........................................................................................ 15
5.1.1 Calibration ....................................................................................... 16
5.1.2 Signature ......................................................................................... 16
5.1.3 Opening and Closing FST (External Source)....................................... 17
5.1.4 PST................................................................................................... 17
5.1.5 SOVs Test ......................................................................................... 18
5.1.6 Closing FST Details ........................................................................... 20
5.1.7 Opening FST Details ......................................................................... 21
5.1.8 PST and SOV TEST Details................................................................. 22
5.2 Detailed Description ................................................................................... 31
5.2.1 Configuration-Managing Interfaces.................................................. 31
5.2.2 Digital Input ..................................................................................... 31
5.2.3 Digital Output .................................................................................. 34
5.2.4 SIS Signals - SOV Outputs ................................................................. 35
5.2.5 Position Sensor................................................................................. 35
5.2.6 Pressure Sensors .............................................................................. 36
5.2.7 Alarms.............................................................................................. 36
5.2.8 Graphs – Sampling Time – Memory.................................................. 37
Section 6: Conguration Parameters
6.1 Normal Mode Menu .................................................................................... 58
6.2 “Act.Mode”and “SOVs Qty”........................................................................ 59

II
Table of Contents Installation, Operation and Maintenance Manual
September 2019 MAN720_IMVS2000v2_IOM Rev. 6 MAN720_IMVS2000v2_IOM Rev. 6
Table of Contents
Section 7: Local Operator Interface
7.1 Normal Mode Menu .................................................................................... 61
7.2 Log in Menu ................................................................................................ 62
7.3 View/Setup Mode Menu.............................................................................. 63
7.3.1 View Graph of the Setup/View Mode Menus..................................... 63
7.3.2 Push-buttons Functionality .............................................................. 68
Section 8: Table of Alarms
Section 9: Wiring Diagrams – Signals Description
9.1 Signals Description...................................................................................... 74
9.1.1 Standard Signals............................................................................... 74
9.1.2 Optional Card Signals ....................................................................... 76
9.2 Wiring Diagrams ......................................................................................... 78
9.2.1 Configuration A – Wiring Diagram.................................................... 78
9.2.2 Configuration B – Wiring Diagram.................................................... 79
9.2.3 Configuration C – Wiring Diagram.................................................... 80
9.2.4 Configuration D – Wiring Diagram ................................................... 81
9.2.5 Configuration E – Wiring Diagram .................................................... 82
9.2.6 Configuration F – Wiring Diagram .................................................... 83
9.2.7 Configuration G – Wiring Diagram.................................................... 84
9.2.8 Configuration H – Wiring Diagram ................................................... 85
9.2.9 Hart Card – Wiring Diagram ............................................................. 86
Section 10: INSTALLATION – START-UP
10.1 Installation in ambient with explosive dusts................................................. 88
10.2 Checks to be performed before installation................................................. 88
10.3 Preliminary operations ................................................................................ 89
10.4 Mechanical Connections ............................................................................. 90
10.4.1 Mounting IMVS2000v2 onto RP/RPS type actuators......................... 90
10.4.2 Mounting IMVS2000v2 onto ALGA/ALGAS type actuators................ 91
10.5 Pressure Connections.................................................................................. 92
10.6 Cables and Electrical Connections............................................................... 92
10.6.1 Cables Connection ........................................................................... 92
10.6.2 Removing the electrical enclosure’s covers....................................... 94
10.6.3 Unused entries ................................................................................. 96
10.6.4 Cables requirements – EMC protection............................................. 96
10.6.5 Wires dimensions............................................................................. 97
10.7 Commissioning Procedure .......................................................................... 97
Section 11: Parts List
11.1 General Assembly ....................................................................................... 98
11.2 Spare Parts................................................................................................ 100
Section 12: Decommissioning
Section 13: Trouble Shooting
Section 14: Ordering Table
Section 15: Document Revision

September 2019
MAN720_IMVS2000v2_IOM Rev. 6
Installation, Operation and Maintenance Manual
Reference Documents
Section 1: Reference Documents
[1]: MDE231 IMVS2000v2 - Biffi-Assistant User Manual
[2]: MDE232 HRT_IMVS2000v2 User Manual
[3]: MDE243 IMVS2000v2 MODBUS User Manual
1
Section 1: Reference Documents

September 2019
Installation, Operation and Maintenance Manual
MAN720_IMVS2000v2_IOM Rev. 6 MAN720_IMVS2000v2_IOM Rev. 6
General Safety Instructions
Section 2: General Safety Instructions
2.1 Manufacturer
The manufacturer with respect to Machinery Directive 2006/42/EC is Bif Italia, as specied
on the machinery label.
2.2 Intended Use
The IMVS2000v2 electro-mechanical device covered in this Instruction and Operating
Manual is designed to provide the Partial Stroke Test, i.e., perform the valve/actuator test
and/or movement able to verify and compare (diagnostic capability) signature values with
ongoing test, in particular, the continuously position verication (via encoder) and pressure
verication in actuator cylinder (these two functions are always active). IMVS2000v2 can
be used in a wide range of applications (heavy industrial, chemical, petrochemical plants,
waterworks, water pipelines, waste paper plants and power plants, etc). IMVS2000v2
devices are produced by Bif Italia and identied by a label with a product designation
code. Bif Italia will not be liable for any possible damage or physical injury resulting
from use in other than the designated applications or by lack of care during installation,
operation, adjustment and maintenance of the machine. Such risks lie entirely with
the user. Depending on the specic working conditions, additional precautions may be
requested. Considering that Bif Italia has no direct control over particular applications,
operation or maintenance conditions, it is the operator’s responsibility to comply with all
applicable safety rules. Please inform Bif Italia urgently if you face unsafe situations not
described in this IOM. It is the sole responsibility of the operator to ensure that the local
health and safety regulations are adhered to.
WARNING
It is assumed that the installation, setting, commissioning, maintenance and repair works
are carried out by qualified personnel and checked by responsible Specialists.
WARNING
Any repair work other than the operations outlines in this IOM will be strictly reserved to
qualified BIFFI ITALIA personnel or to personnel directly authorised by the Company itself.
WARNING
The flameproof joints are not intended to be repaired but where necessary the original
manufacturer shall be contacted for guidance and information on the dimensions of the
flameproof joints.
WARNING
The user shall be aware that all external fasteners on which the flameproof enclosure
depends are stainless steel socket head cap screws class A4 -grade 70.
2
Section 2: General Safety Instructions

Installation, Operation and Maintenance Manual
September 2019
MAN720_IMVS2000v2_IOM Rev. 6
General Safety Instructions
IMVS2000v2 devices are designed in accordance with the applicable International Rules
and Specifications, but the following Regulations must be observed in any case:
• the general and safety regulations
• the plant specific regulations and requirements
• the proper use of personal and protective devices (glasses, clothing, gloves, etc)
• the proper use of tools, lifting and transport equipment
WARNING
The electronic parts of the IMVS2000v2 and all the options can be damaged by a discharge
of static electricity. Before you start, touch a grounded metal surface to discharge any
static electricity.
CAUTION
Danger of explosion if battery is incorrectly replaced.
Replace only with the same or equivalent type.
2.3 Terms and Conditions
Biffi Italia guarantees each single product to be free from defects and to conform to current
goods specifications. The warranty period is one year from the date of installation by the
first user, or eighteen months from the date of shipment to the first user, whichever occurs
first. No warranty is given for products which have been subject to improper storage,
improper installation, misuse, or corrosion, or which have been modified or repaired by
unauthorised personnel. Repair work due to improper use will be charged at standard rates.
2.4 Manufacturer’s Liability
Biffi Italia declines all liability in the event of:
• use of the device in contravention of local safety at work legislation
• incorrect installation, disregard or incorrect application of the instructions
provided on the device nameplate and in this manual
• modifications without Biffi’s authorisation
• work done on the unit by unqualified or unsuitable persons
3
Section 2: General Safety Instructions

September 2019
Installation, Operation and Maintenance Manual
MAN720_IMVS2000v2_IOM Rev. 6 MAN720_IMVS2000v2_IOM Rev. 6
General Safety Instructions
2.5 Applicable Standards and Regulations
EN ISO 12100: Safety of machinery
EN 60204/1: Electrical equipment of industrial machines. Part 1- General requirements
2006/42/EC: Machinery directive
2004/108/EC: EMC Directive
2014/34/UE: ATEX Directive
97/23/EC: PED Directive
IEC 61508: Functional safety of E/E/PE safety-related systems (*)
CSA/CSAus certified (see paragraph 2.5.1 for details)
(*) The IEC 61508 standard is applied only to demonstrate that the IMVS2000v2 does not
adversely affect the execution of the safety function (ESD) by the superior SIS and does not
contribute to the PFDav.
2.6 CSA/CSAus Certications Details
Canada
Class I Division 1 Groups B, C, D; T4
Class II, Groups E, F, and G; Class III
Ex db ia IIC T4 Gb
Ex tb IIIC T135 °C Db
Integrated Monitoring Valve System, Model IMVS2000v2,
Ambient temperature range -40 °C to +75 °C, Type 4, 4X, 6, IP66/68
Class I Division 1 Groups C, D; T4
Class II, Groups E, F, and G; Class III
Ex db ia IIB T4 Gb
Ex tb IIIC T135 °C Db
Integrated Monitoring Valve System, Model IMVS2000v2 with optional local indicator,
Ambient temperature range -40 °C to +75 °C, Type 4, 4X, 6, IP66/68
4
Section 2: General Safety Instructions

Installation, Operation and Maintenance Manual
September 2019
MAN720_IMVS2000v2_IOM Rev. 6
General Safety Instructions
U.S.
Class I Division 1 Groups B, C, D; T4
Class II, Groups E, F, and G; Class III
Class I Zone1 AEx db ia IIC T4 Gb
Zone 21 AEx tb IIIC T135 Db
Integrated Monitoring Valve System, Model IMVS2000v2,
Ambient temperature range -40°C to +75°C, Type 4, 4X, 6, IP66/68
IMVS2000v2 Integrated Monitoring Valve System with optional local indicator
Class I Division 1 Groups C, D; T4
Class II, Groups E, F, and G; Class III
Class I Zone1 AEx db ia IIB T4 Gb
Zone 21 AEx tb IIIC T135 Db
Integrated Monitoring Valve System, Model IMVS2000v2 with optional local indicator,
Ambient temperature range -40 °C to +75 °C, Type 4, 4X, 6, IP66/68
Conditions of Acceptability
1. The flameproof joints are not intended to be repaired but where necessary the
original manufacturer shall be contacted for guidance and information on the
dimensions of the flameproof joints.
2. The user shall be aware that all external fasteners on which the flameproof
enclosure depends are stainless steel socket head cap screws class A4 -grade 70.
3. Equipment is only to be installed by manufacturer trained personnel.
4. The scope of this approval does not include any safety related function,
performance or reliability of the equipment.
5. If at any time there is a conflict between the system safety provisions and any
relevant local (national Or regional) requirements, the local requirements always
take precedence.
Process Pressure Limitation for explosive uids
The IMVS2000v2 has a pressure limitation for explosive fluids of 180 barg. This limitation
is applicable only if the explosive fluid is in direct contact with the pressure sensors of the
IMVS2000v2. If the fluid used for supplying the actuator and consequently in contact with
the pressure sensors of the IMVS2000v2 is not explosive, the pressure limitation is 345 barg.
5
Section 2: General Safety Instructions

September 2019
Installation, Operation and Maintenance Manual
MAN720_IMVS2000v2_IOM Rev. 6 MAN720_IMVS2000v2_IOM Rev. 6
General Safety Instructions
Applicable Requirements
CAN/CSA-C22.2 No. 61010-1-12 Safety Requirements for Electrical Equipment
for Measurement,
Control, and Laboratory Use, Part 1:
General Requirements
UL Std. No. 61010-1 (3rd Edition) Safety Requirements for Electrical Equipment
for Measurement,
Control, and Laboratory Use - Part 1:
General Requirements
CAN/CSA-C22.2 No. 0-10 (R2015) Canadian Electrical Code, Part II - General requirements
CAN/CSA-C22.2 No. 60079-0:15 Electrical apparatus for explosive gas atmospheres-
Part 0: General requirements
CAN/CSA-C22.2 No. 60079-1:16 Explosive Atmospheres – Part 1: Equipment Protection
by Flame-proof Enclosures “d”
CAN/CSA-C22.2 No 60079-11:14 Explosive atmospheres — Part 11: Equipment
protection by intrinsic safety “i”
CAN/CSA-C22.2 No 60079-31:15 Explosive atmospheres — Part 31: Equipment
dust ignition protection by enclosure "t"
CAN/CSA-C22.2 No.30-M1986 (2016) Explosion-Proof Enclosures for Use in Class I
Hazardous Locations
CAN/CSA-C22.2 No 25:1966 (R2014) Enclosures for Use in Class II Groups E, F, and G
Hazardous Locations
CAN/CSA C22.2 No 157 Intrinsically safe and non-incendive equipment or use in
Hazardous Locations
ANSI/ISA 60079-0: Ed 6 Electrical Apparatus for Explosive Gas Atmospheres -
Part 0: Equipment - General Requirements
ANSI/ISA 60079-1: Ed 6 Explosive Atmospheres - Part 1: Equipment Protection
by Flame-proof Enclosures “d”
ANSI/ISA 60079-11: Ed 6.2 Explosive atmospheres - Part 11: Equipment protection
by intrinsic safety “i”
ANSI/ISA 60079-31: Ed 6 Explosive Atmospheres - Part 31: Equipment Dust
Ignition Protection by Enclosure “t”
FM 3600:2011 Electrical Equipment for Use in Hazardous (Classified)
Locations General Requirements
FM 3615:2006 Explosionproof Electrical Equipment,
General Requirements
FM 3610:2015 Intrinsically Safe Apparatus for Use in
Class I, II and III, Division 1
FM 3616:2011 Dust-Ignition proof Electrical Equipment,
General Requirements
CSA C22.2 No. 94.2-15 / UL50E Enclosures for Electrical Equipment,
Environmental Considerations
6
Section 2: General Safety Instructions

Installation, Operation and Maintenance Manual
September 2019
MAN720_IMVS2000v2_IOM Rev. 6
Storage
Section 3: Storage
Important
Not performing the following procedures will invalidate the product guarantee.
All the IMVS2000v2 leave the factory in perfect condition. When mounted on the
actuator they are guaranteed by the actuator test certificate; in other cases, they are
guaranteed by an individual certificate. In order to maintain these characteristics until
the IMVS2000v2 is installed on site, proper attention must be observed for preservation
during the storage period.
The standard plastic plugs used to protect the cable entries during the transport are not
weatherproof, they just prevent the entry of undesired objects during transport: during the
storage it is recommended to replace them with waterproof version.
In any case storage is recommended in a close ambient without excessive humidity.
IMVS2000v2 are weather-proof to IP66/68.
7
Section 3: Storage

September 2019
Installation, Operation and Maintenance Manual
MAN720_IMVS2000v2_IOM Rev. 6 MAN720_IMVS2000v2_IOM Rev. 6
Section 4: Device Description
Device Description
Section 4: Device Description
4.1 General Description
The IMVS2000v2 is designed to provide the Partial Stroke Test and SOV Test (in some
particular configurations). SOV test grant the solenoid valve integrity verification without
any actuator or valve movement, i.e.: perform the valve/actuator test and/or movement
able to verify and compare (diagnostic capability) signature values with ongoing test, in
particular, the continuously position verification (via encoder) and pressure verification in
actuator cylinder (these two functions are always active).
The functions above described are performed without any risk of process interruption.
A valve position sensor and sensors for external pressure are embedded on the
IMVS2000v2 unit: the analog output signals of the above sensors are monitored and
processed by logic control cards mounted within the device: through the above signals a
full control and diagnostic of every kind of valve actuator is available.
Typical applications, but not limited to, are the installation on all type of actuators, driven
pneumatically or hydraulically, for ON-OFF/ESD applications.
Different versions are available for:
• single or double acting actuators,
• actuators pneumatically or hydraulically operated,
• rotary or linear actuators,
• direct installation on actuator.
4.1.1 Main Features
In the following section the main features of the IMVS2000v2 are listed. For additional
details see Section 5.
POSITION SENSOR
The IMVS2000v2 is provided with an internal contactless position sensor. The position
(open or close) is directly takes on the shaft connected to the actuator.
PRESSURE SENSORS
The IMVS2000v2 can manage up to three internal pressure sensors for reading the actuator
(two sensors) and the pipeline (process) pressure.
CONFIGURATION-MANAGING INTERFACES
The IMVS2000v2 is provided with a powerful local operator interface, made of one 128x64
graphical OLED display and 3 push-buttons that allow entering the configuration data and
visualizing the values of variables or the status of the device.
Moreover, an RS232 and a Bluetooth serial communication ports are provided for the
connection with the “Biffi-Assistant” software tool (see [1] for details), to carry out
parameter configuration, or variables visualization or to download the recorded event data
for further analysis of pipeline behavior.
8

Installation, Operation and Maintenance Manual
September 2019
MAN720_IMVS2000v2_IOM Rev. 6
Section 4: Device Description
Device Description
POWER SUPPLY
The IMVS2000v2 accepts a wide range power supply:
• from 19.2 Vdc to 57.6 Vdc (24 Vdc -20% to 48 Vdc to +20%).
SOVs CIRCUITS
The IMVS2000v2 can manage two independent (isolated) circuits for controlling up to two
external Solenoid Valves (SOVs).
Each circuit has its own dedicated power supply (SIS) that through a relay is used to control the SOV.
DIGITAL INPUTS (Opto-isolated)
The IMVS2000v2 is provided with three opto-isolated Digital Inputs (DI) for controlling the
Solenoid Valves (SOVs) and for launching a PST test.
DIGITAL OUTPUTS (Solid State Relays)
The IMVS2000v2 is provided with six isolated (solid state relay) Digital Outputs (DO):
• OPEN
• CLOSE
• COMMON FAILURE ALARM
• PST IN PROGRESS
• PST PASSED
• PST FAILED
AUTO-DIAGNOSTIC
The IMVS2000v2 monitors the status of its internal sensors (pressure and position).
ADDITIONAL BUS CARDS
The IMVS2000v2 has the possibility to use one of the following optional Bus Card:
• HART Card (HART 7)
• MODBUS Card (MODBUS-RTU)
4.2 Identication of the Main Parts
In this section, only the main parts of the IMVS2000v2 are shown. Refer to the “PARTS LIST”
paragraph, for a full list of the IMVS2000v2 parts.
The IMVS2000v2 device is composed by three main parts:
a. a base cover with a glass window to display a mechanical visual indicator,
b. a local interface cover with three push-buttons and a glass window to
show the indication of an internal display,
c. a sensor manifold to allocate the pneumatic/hydraulic sensors with
relevant connections and cable entries for electrical wirings.
9

September 2019
Installation, Operation and Maintenance Manual
MAN720_IMVS2000v2_IOM Rev. 6 MAN720_IMVS2000v2_IOM Rev. 6
Section 4: Device Description
Device Description
Figure 1
a
b
c
The screws fixing the enclosure covers are made in Stainless Steel Class A4, grade 70,
with a minimum yield strength 450 N/mm².
The shaft, which transmits the movement from the valve to the internal position sensor,
is supported by a bush mounted on the sensors’ manifold and blocked on the external
diameter with LOCTITE 638 (or equivalent).
The various explosion-proof joint surfaces can be lubricated with Aeroshell Grease.
10

Installation, Operation and Maintenance Manual
September 2019
MAN720_IMVS2000v2_IOM Rev. 6
Section 4: Device Description
Device Description
Figure 2
Pos. Description
1 Position Sensor Assembly
2 Barrier Card
3 Display / Logic Cable
4 Pressure Sensor
5 Position Indicator
6 Base Power Card
7 Bus Card (OPT.)
8 Display Card
9 Logic Card
11

September 2019
Installation, Operation and Maintenance Manual
MAN720_IMVS2000v2_IOM Rev. 6 MAN720_IMVS2000v2_IOM Rev. 6
Section 4: Device Description
Device Description
4.3 Technical Specications
Table 1.
Device Power Supply (#)
Supply Voltage Range 19.2 Vdc - 57.6 Vdc (24 Vdc -20% - 48 Vdc +20%)
19.2 Vdc – 35 Vdc for CSA/CSAus device
Maximum Device Current Consumption 125 mA @ 24 Vdc (3 W)
62.5 mA @ 48 Vdc (3 W)
Galvanic Insulation from Logic Yes
SOVs Power Supply (SIS A – SIS B) (#)
Maximum allowed Voltage up to 57.6 Vdc
Maximum switching power (resistive load) up to 1 A
Galvanic Insulation from Logic Yes
Digital Inputs (#)
Maximum OFF signal 9 Vdc
Maximum ON signal 19.2 Vdc (24 -20%)
Maximum ON signal 57.6 Vdc (48 +20%)
35Vdc for CSA/CSAus device
Current Consumption min. 2.0 mA - max.11 mA
Galvanic Insulation from Logic YES
Galvanic Insulation from others DIs YES
Digital Outputs (SPST solid state dry contact) (#)
Maximum allowed Voltage up to 57.6 Vdc
up to 35 Vdc for CSA/CSAus device
Maximum allowed Current up to 0.5 A
Galvanic Insulation from Logic Yes
Galvanic Insulation from others DOs Yes
Pressure Sensors Range
Option 1 up to 10 barg (145 psig) (*)
Option 2 up to 100 barg (1450 psig)
Option 3 up to 200 barg (2900 psig)
Option 4 up to 400 barg (5800 psig) (**)
RS232 (Conguration Port)
Baud rate 115200 bps
Parity Bit Even
Stop Bit 1
Hardware flow control Off
Distance (cable length) Max. 10 meters
Bluetooth (Conguration Port)
Baud rate 115200
Parity Bit None
Stop Bit 1
Hardware flow control On
Distance Max. 10 meters
Various Characteristics
Operating Ambient Temperature from -40° C up to +75° C
Expected Lifetime 10 years
Weight 16,4 kg
12

Installation, Operation and Maintenance Manual
September 2019
MAN720_IMVS2000v2_IOM Rev. 6
Section 4: Device Description
Device Description
Stroking Time Limits (***)
Min. Actuator Stroking Time 2 sec.
Max. Actutor Stroking Time 300 sec.
Max. Ratio between Op. and Cl. times 10 (****)
Modbus Rtu (optional card) (*****)
Transmission Technology RS485
Baud rate (configurable) 600,1200,2400,4800,9600,19200,38400 bps
Parity Bit (configurable) Even, Odd, None
Stop Bit (according to Parity Bit) 1, 2
Galvanic Insulation from Logic Yes
4-20 mA Analog Output + HART (optional card) (******)
Feedback Signal Pressure or Position
Output Current Range 4-20 mA
Maximum Load (cable+resistor) 300 ohm
External Power Supply Voltage 21.6 - 26.4Vdc – max 21 mA
Galvanic Insulation from Logic Yes
Notes:
(*) Consult Factory for availability.
(**) Consult Factory for applications over 345 barg.
(***) Contact Biffi for the availability of applications that do not respect these ranges.
(****) Ratio greater than 5 affects the accuracy of the PST.
(particularly for pneumatic application)
(*****) See [3] for details.
(******) See [2] for details.
(#) For CSA/CSAus devices must be supplied from a limited energy source.
(voltage available is to be limited to 35 Vdc)
13

September 2019
Installation, Operation and Maintenance Manual
MAN720_IMVS2000v2_IOM Rev. 6 MAN720_IMVS2000v2_IOM Rev. 6
Section 4: Device Description
Device Description
4.4 Overall Dimensions
Figure 3
4.5 Options
See Section 14 for the available options.
14

Installation, Operation and Maintenance Manual
September 2019
MAN720_IMVS2000v2_IOM Rev. 6
Section 5: Working Principle
Working Principle
Section 5: Working Principle and
Detailed Description
5.1 Working Principle
The IMVS2000v2 is a PST device designed to diagnose an actuator/valve system. It directly manages the
SOVs of the control panel (up to two). It offers the possibility to check all the parts of the system: Valve,
Actuator and SOVs (Solenoid Valves).
The IMVS2000v2 can automatically find the mechanical stoppers through the “Calibration” command
(see Section 5.1.1 for details).
The IMVS2000v2 can perform both Partial Stroke (PST) and to the Full Stroke (FST) in opening and
closing and also a SOV Test (in some particular configurations).
For every FST and PST the IMVS2000v2 stores the following data:
• Time (seconds)
• Pressure 1 (bar or psi) – pressure sensor S1 (*)
• Pressure 2 (bar or psi) – pressure sensor S2 (**)
• Process pressure (bar or psi) – pressure sensor S3 (***)
• Position (%)
• Pr. 1 – Pr. 2| - absolute value of the difference between Pressure 1 and Pressure 2 (**)
It is possible to set tolerances on time, pressure and position of both FST and PST. During the
commissioning procedure (see 10.7) the IMVS2000v2 stores:
• the “ideal” opening FST and closing FST (Baseline Signature)
• the “ideal” PST (Baseline PST)
The further FSTs (Maintenance Signature, Opening FST or Closing FST) are compared with the
Baseline Signature and further PSTs (Manual PST). It is possible to set tolerances on time, pressure
and position of both FST and PST and if the measured values compared to the Baseline ones, overtake
these settings the IMVS2000v2 generates dedicated alarms (see Sections 5.2.7 and 8 for details).
See Sections 5.1.2, 5.1.6, 5.1.8, and 5.1.9 for details about Signature, FST and PST.
The IMVS2000v2 offers the possibility to monitor:
• Actuator Pressure
• Actuator Position
• Pipeline Pressure (Pressure Sensor S3)
• PST cycles number
• FST cycles number
• Sensors Status (pressure and position)
Dedicated alarms are provided (see Sections 5.2.7 and Section 8 for details).
(*): if the pressure sensor 1 is enabled.
(**): if the pressure sensor 2 is present and enabled.
(***): if the process pressure sensor is present and enabled.
15

September 2019
Installation, Operation and Maintenance Manual
MAN720_IMVS2000v2_IOM Rev. 6 MAN720_IMVS2000v2_IOM Rev. 6
Section 5: Working Principle
Working Principle
5.1.1 Calibration
The Calibration is a mandatory operation for using the IMVS2000v2. It must be performed as first
step of the Commissioning Procedure (see Section 10.7 for details). To performe the Calibration, the
IMVS2000v2 must be correctly connected and configured and it must be able to control the valve/
actuator system.
The Calibration is an operation that allows the IMVS2000v2 to find the mechanical stoppers.
The Calibration operation consists of: two Opening FST and two Closing FST and it is “automatically
managed by the IMVS2000v2.
During the execution of the Calibration the Digital Inputs status is not considered. The status of the
Calibration is stored in a dedicated parameter. The Calibration command can be inhibited
(see Section 6 for details). A new Calibration cancels all the stored signatures, FSTs and PSTs data.
The Calibration can be launched by the following interfaces:
• Local Operator Interface
• Biffi Assistant (Bluetooth and RS232)
• Bus Interface
For using the IMVS2000v2 at its own best, it is suggested to perform the Calibration in the
following conditions:
• Pressures and position stable
• Valve in its “normal” working position (ex. Open position for a “fail to close” actuator)
5.1.2 Signature
There are two different types of signature:
• Baseline Signature
• Maintenance Signature
To performe the Baseline Signature and the Maintenance Signature, the IMVS2000v2 must be
correctly connected and configured and it must be able to control the valve/actuator system.
The Baseline Signature can be performed only if a Calibration is already successfully executed. The
Maintenance Signature can be performed only if a Baseline Signature is already successfully executed.
A new Baseline Signature cancels all the stored Maintenance Signatures, FSTs and PSTs data.
The Baseline Signature and the Maintenance Signature consist of one Opening FST and one Closing
FST and they are “automatically” managed by the IMVS2000v2; at the end of the operation the valve/
actuator system comes back to the starting position.
During the execution of the Baseline Signature or of the Maintenance Signature the Digital Inputs
status is not considered.
The Baseline Signature is a mandatory operation for using the IMVS2000v2. It must be performed as
second step of the Commissioning Procedure (see 10.7 for details).
It allows the IMVS2000V2 to record the reference times and pressures of the Opening FST and of the
Closing FST.
The Maintenance Signature allows the IMVS2000V2 to record the times and pressures of the Opening FST
and of the Closing FST; these values are compared to the ones of the Baseline Signature and if they overtake
the set tolerances, dedicated alarm are generated (see Sections 5.2.7 , 8, 5.1.6 and 5.1.8 for details).
The Baseline Signature and the Maintenance Signature can be launched by the following interfaces:
• Local Operator Interface
• Biffi Assistant (Bluetooth and RS232)
• Bus Interface
16
Table of contents
Other BIFFI Control Unit manuals
Popular Control Unit manuals by other brands
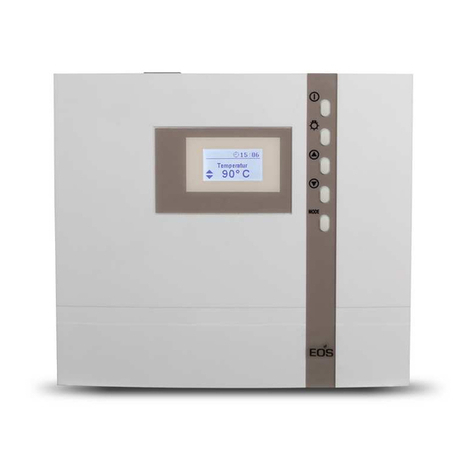
EOS
EOS ECON D1 Installation and operating instruction
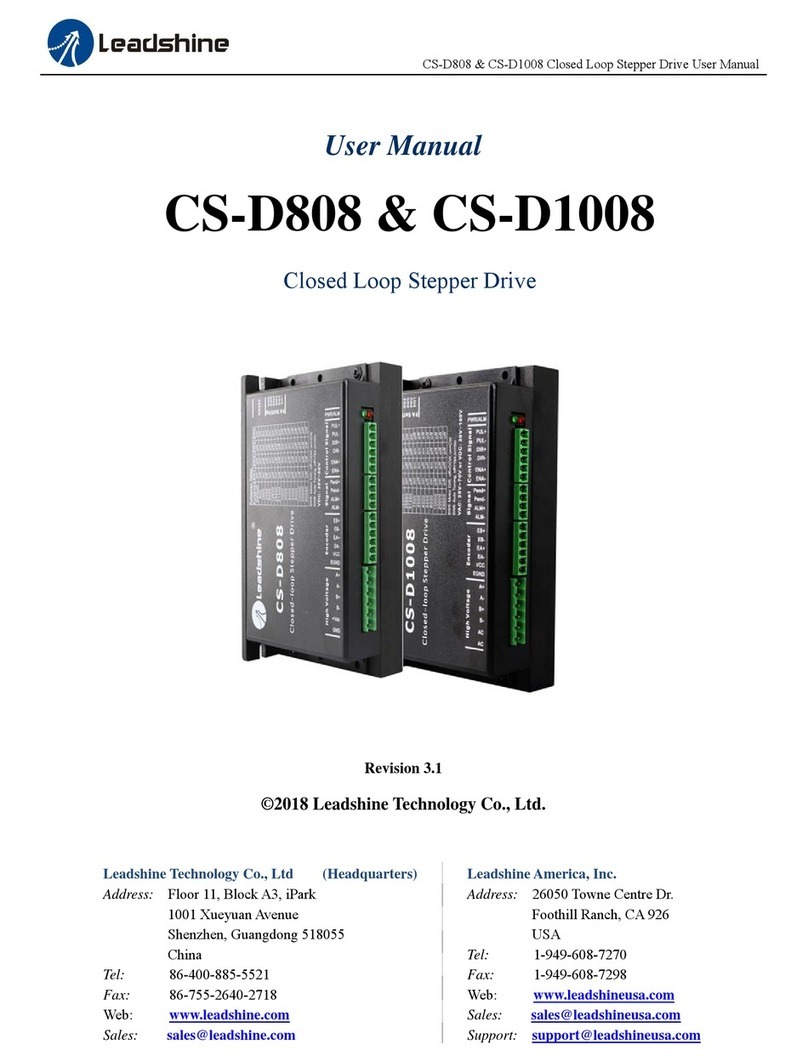
Leadshine Technology Co.
Leadshine Technology Co. CS-D1008 user manual

YASKAWA
YASKAWA IM 053PN manual
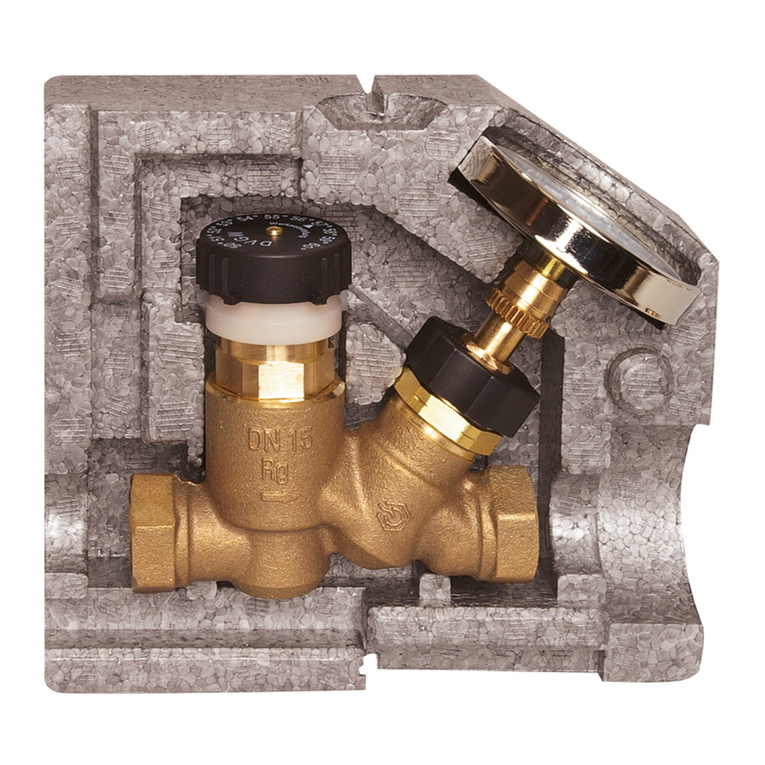
flamco
flamco NexusValve TW DN15 manual
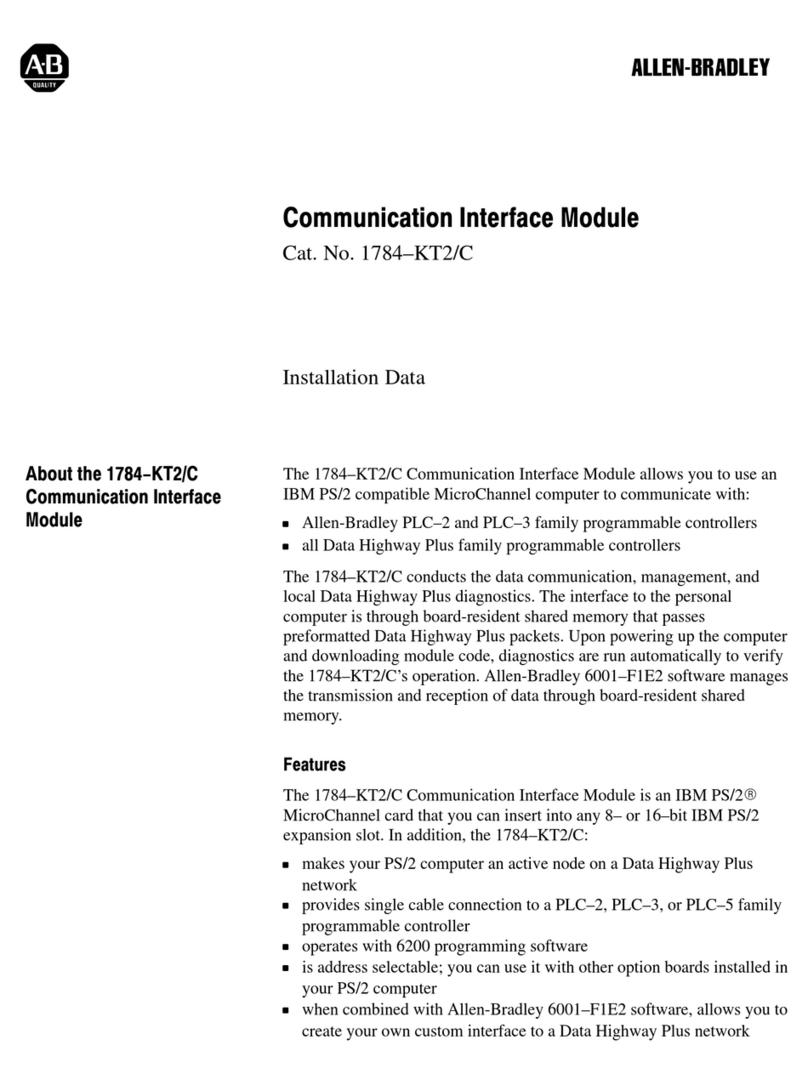
Allen-Bradley
Allen-Bradley 1784-KT2/C Installation data

Honeywell
Honeywell GSMVLP5 Installation and setup guide
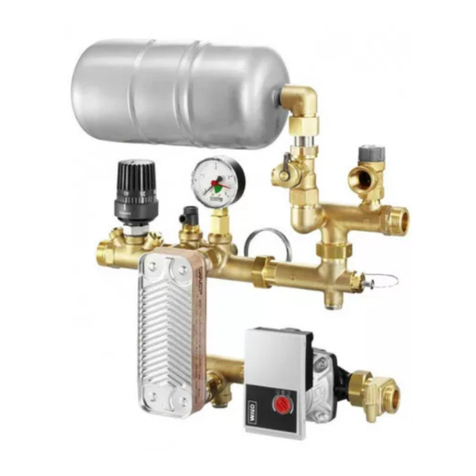
oventrop
oventrop Regufloor HX Installation and operating instructions for the specialised installer
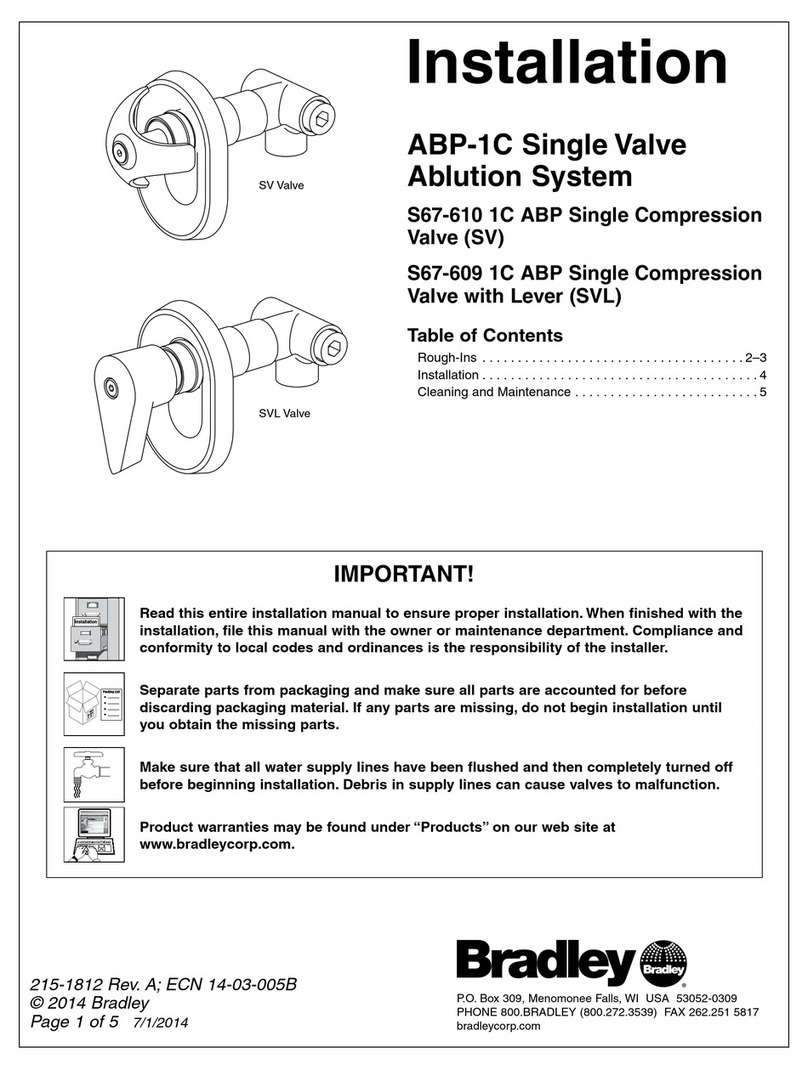
Bradley
Bradley S67-610 Installation

Panasonic
Panasonic PAN9026 Product specification
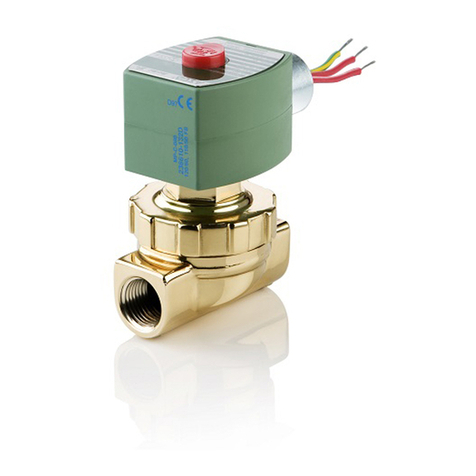
Asco
Asco 8210 series Installation and maintenance instructions
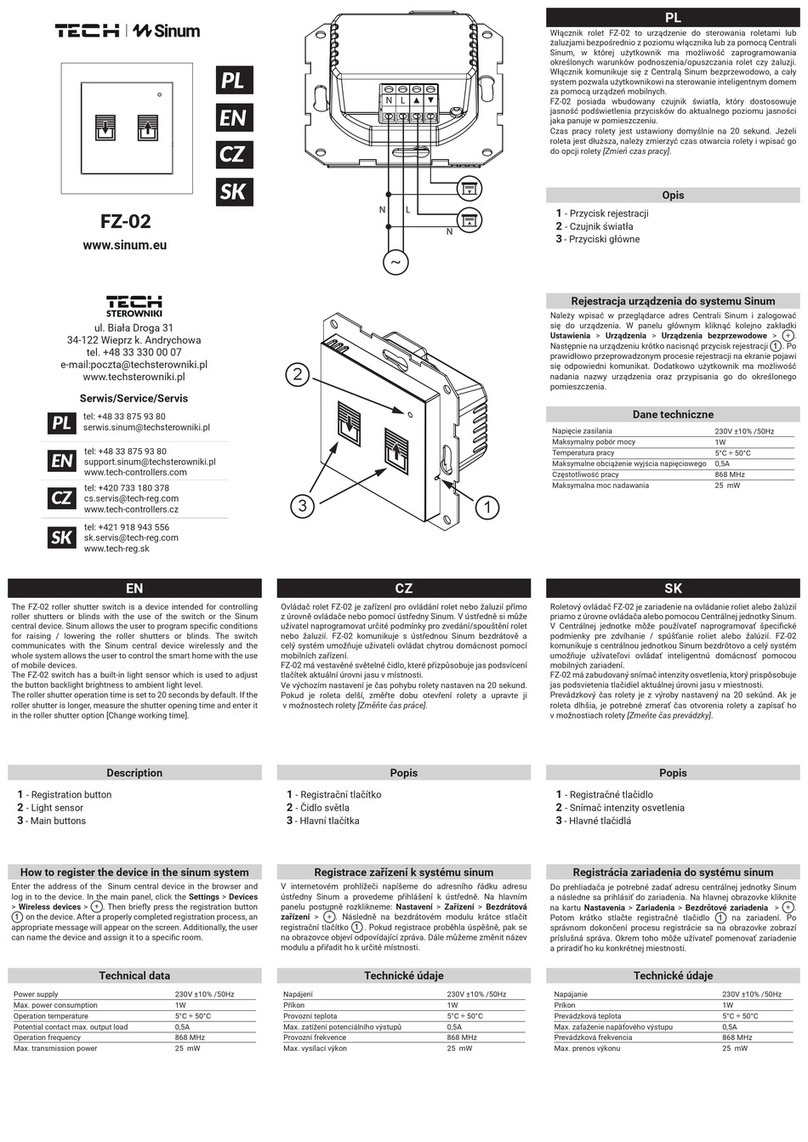
TECH
TECH Sinum FZ-02 quick start guide

VIPA
VIPA System 300S IM 353-1DP01 manual