Bodine 3984 User guide

Isolated Interface Module
Part No. 074 00187.rev.C
www.Bodine-Electric.com
Instructions for Installation and Operation
Model 3984
SPECIFICATIONS
ACInputPower:..............................................115/230 VAC, 50/60 Hz
Motor Speed Signals
InputVoltageRange:.........................................-25to+25VDC;-250to+250VDC
InputCurrentRange:.........................................1to5mA;4to20mA;10to50mA
OutputSignalRange:.........................................0to+10VDC@10mA
Input/OutputLinearity:........................................±0.1%@10VDC(Typical)
ThermalDrift: ...............................................4mV/°C
MINpotentiometerrange:....................................OffsetVOUT±3VDC
MAXpotentiometerrange:....................................ScaleVOUT0to2times
Auxiliary Signals:.............................................MotorDirection
Motor Disable
Digital Tachometer

2www.bodine-electric.com
QUICK REFERENCE
IMPORTANT
Read this manual completely and carefully. Pay special attention to all
warnings, cautions, and safety rules. Failure to follow the instructions
could produce safety hazards which could injure personnel or damage
the module, control, motor, or other equipment. If you have any doubts
about how to connect this module refer to the detailed sections of this
manual and the specific control manual.
10K
TAK
511
ITAK
(Page 14)
ICOM
DIS
DIR
(Page 13)
Manual Direction Mode (DS1:4 = OFF)
Automatic Direction Mode (DS1:4 = ON)
DIR
DS1:4
Signal
Direction
SIGNALS
CONTROL
TB3 MOTOR
COM
VOUT
Signal
Speed
10K
V+ (+12 VDC) V+
(Page 14)
ISO- (-12 VDC)
ISO+ (+12 VDC)
(Page 13)
ISO+
4N35
COM
1.50K
100K
1K
243
200
200
ICOM
(Page 12)
IDIR
IDIS
ISO+
ISO-
MIN potentiometer: Oset VOUT signal up to ±3VDC
(Within 0 to 10 VDC limit of VOUT)
(Page 17)
MAX
MAX potentiometer: Scale VOUT 0-2 times VIN signal
(Up to max 10VDC limit of VOUT)
(Page 18)
ANALOG SPEED SIGNALS
VIN2
VIN1
VIN1
VIN1
VIN1
0 to ± 250 VDC
0 to ± 25 VDC
1 to 5 mA
4 to 20 mA
10 to 50 mA
(DS1:1,2,3 = OFF)
(DS1:1,2,3 = OFF)
(DS1:3 = ON; 1,2 = OFF)
(DS1:2 = ON; 1,3 = OFF)
(DS1:1 = ON; 2,3 = OFF)
TB2
ISOLATED
SIGNALS
25K
1.50K
COM
4N35
ISO+
CNY17-3
COM
0.1uF
Isolation and
Output
Amplier
Conversion
to Speed and
Direction
Signals
MIN
DS1:3
1-5
4-20
DS1:2
DS1:1
10-50
VIN1
100K
VIN2
+
-
+
-
Figure 1 – Quick Reference Diagram

www.bodine-electric.com 3
© 2009 Bodine Electric Company. All rights Reserved. All data subject to change without notice.
Printed in U.S.A.
TABLE OF CONTENTS
QUICKREFERENCE .....................................................2
GENERALINFORMATION ...............................................4
DESCRIPTIONANDFEATURES...........................................4
SPECIFICATIONS.......................................................5
IMPORTANTSAFETYPRECAUTIONS......................................6
APPLICATIONINFORMATION............................................8
TypicalControlSignalIsolation .......................................8
Bi-Directional Master Speed Control . . . . . . . . . . . . . . . . . . . . . . . . . . . . . . . . . .9
Master/SlaveSignalGenerator ......................................10
INSTALLATIONINSTRUCTIONS.........................................11
MountingtheModel3984Module ....................................11
ElectricalConnections ..............................................11
Controlling Speed With an Analog Input Voltage . . . . . . . . . . . . . . . . . . . . . . . .12
Controlling Speed With an Analog Input Current . . . . . . . . . . . . . . . . . . . . . . . .12
SpeedControlOutput ...............................................13
ControllingMotorDisable............................................13
Automatic Control of Motor Direction . . . . . . . . . . . . . . . . . . . . . . . . . . . . . . . . .13
Independent Control of Motor Direction . . . . . . . . . . . . . . . . . . . . . . . . . . . . . . .13
TachometerOutput .................................................14
InternalPowerSupply...............................................14
ACPowerConnections..............................................14
FuseInstallation....................................................15
OPERATINGINSTRUCTIONS............................................16
PreliminaryChecks .................................................16
Operation..........................................................16
InternalAdjustments/Calibration......................................17
MINSpeedPotentiometer...........................................17
MAXSpeedPotentiometer...........................................18
TROUBLESHOOTING...................................................19
WARRANTY...........................................................23
FIGURES
Figure1–QuickReferenceDiagram......................................2
Figure 2 – Typical Isolated Inputs for Bodine Controls . . . . . . . . . . . . . . . . . . . . . . .9
Figure 3 – Master Speed/Direction Control Configuration . . . . . . . . . . . . . . . . . . . .9
Figure4–Master/SlaveConfiguration ...................................10
Figure5–Model3984CircuitBoard......................................12
Figure6–ITAKOutput..................................................14
Figure7–ACPowerConnections .......................................15
MountingTemplate.........................................Centerfold

4www.bodine-electric.com
GENERAL INFORMATION
Thank you for selecting the Bodine Model 3984 Isolated Interface Module. It
will provide the same excellent performance and reliability that have been
a Bodine tradition since 1905. Bodine Electric Company takes price in the
quality of its products and in satisfying its customers. Every effort has been
made to provide you with a product free of defects in design, workmanship,
and materials. In order for us to maintain our tradition of quality, please report
any cases of unsatisfactory service or products to Bodine Electric Company
promptly.
About This Manual
This manual contains the basic information needed to install and operate the
Bodine Model 3984 Isolated Interface Module. It is organized in a systematic,
step-by-step fashion so that it may be installed in the shortest possible time. It
does not profess to cover all details or variations in equipment, nor to provide
for every possible contingency associated with installation, operation, or
maintenance. No warranty of fitness for purpose is expressed or implied.
Should further information be desired or should particular problems arise
which are not covered sufficiently for the user’s purpose, the matter should
be referred to the Bodine Electric Company.
The issuance of this manual does not confer to the recipient any license to
manufacture under any patents owned or controlled by the Bodine Electric
Company.
Safety Standards
Bodine products are designed and manufactured to comply to applicable
safety standards and in particular to those issued by ANSI (American
National Standards Institute), NEMA (National Electrical Manufacturers
Association), U.L. (Underwriters Laboratories, Inc.), and CSA (Canadian
Standards Association).
Bodine equipment “recognized by U.L., Inc.” are either labeled
with the UR or cURus marks. In addition, products that are CSA
certified are identified by the CSA mark. If you need specific
information regarding the third-party approval status of Bodine
products, contact the nearest Bodine representative, or the
home office.
DESCRIPTION AND FEATURES
Most Bodine motor controls have floating signal commons (i.e. the signal
common is not at ground potential). Input signals from transducers,
microprocessor controls, programmable logic controllers, and other

www.bodine-electric.com 5
electronic control devices may produce grounded signals or signals which
are at a different potential from those used in Bodine motor controls. The
Model 3984 Isolated Interface Module is designed to provide an interface
which optically isolates the motor control signals from external electronic
control signals, while still providing full use of Bodine control features.
The Model 3984 is a scalable voltage following device that accepts a wide
range of current and voltage analog speed input signals and delivers an
isolated output speed signal of 0 to +10 VDC @ 10mA. A built-in sensor circuit
monitors the polarity of the analog voltage speed input and changes the
motor’s direction of rotation when the signal goes from positive to negative.
Adjustable minimum and maximum potentiometers allow the output speed
signal to be scaled or offset in order to achieve a desired response based on
a given value of input signal.
Isolated motor disable and direction of rotation signals are also provided
as well as an isolated tachometer output which can be used to monitor the
speed of Bodine brushless DC motors. Isolated power supply connections are
provided on both the input and output sides of the Model 3984 for convenience.
The power supply delivers ±12 VDC @ 10mA at the +ISO/-ISO terminals and
+12VDC @ 10mA at the V + terminal.
The model 3984 can be used in a variety of configurations to control several
slave motor/control circuits from a single master. Configuration examples are
described in the Application Information Section of this manual.
SPECIFICATIONS
ACInputPower:....................115/230 VAC, 50/60 Hz
Motor Speed Signals
Input Voltage Range: . . . . . . . . . . . . . . .-25 to +25 VDC; -250 to +250 VDC
Input Current Range: . . . . . . . . . . . . . . .1 to 5 mA; 4 to 20mA; 10 to 50 mA
Output Signal Range:. . . . . . . . . . . . . . .0 to +10 VDC @ 10 mA
Input/Output Linearity:. . . . . . . . . . . . . .±0.1% @ 10 VDC (Typical)
Thermal Drift: . . . . . . . . . . . . . . . . . . . . .4mV/°C
MIN potentiometer range: . . . . . . . . . .Offset VOUT ±3 VDC*
MAX potentiometer range:. . . . . . . . . .Scale VOUT 0 to 2 times*
Auxiliary Signals:...................MotorDirection
Motor Disable
Digital Tachometer
Ambient Operating Temperature: . . . . .0° to 50°C
Dimensions: .......................in:4.75Lx2.75Wx1.55H
cm: 12.1L x 7.0W x 4.0H
*MIN and MAX adjustments are limited to within the 0-10 VDC limits of VOUT

6www.bodine-electric.com
IMPORTANT SAFETY PRECAUTIONS
The following safety precautions must be observed during all phases of
installation, operation, service, and repair of this module. Failure to comply
with these precautions or with specific warnings elsewhere in this manual
violates safety standards of design, manufacture and intended use of the
product. Bodine Electric Company assumes no liability for the customer’s
failure to comply with safety requirements and practices.
The use of electric motors and gearmotors, like that of all utilization of
concentrated power, is potentially hazardous. The degree of hazard can be
greatly reduced by proper design, selection, installation, and use, but all
hazards cannot be completely eliminated. The reduction of hazards is a joint
responsibility between the user, the manufacturer of the driven or driving
equipment and the manufacturer of the control or motor and interface circuitry.
The user should refer to Publication No. ANSI C5.1/NEMA MG 2, Safety
Standard for Construction and Guide for Selection, Installation and Use of
Electric Motors and Generators.
Available from:
National Electrical Manufacturers Association
www.nema.org
Warnings highlight procedures which present potential danger to people.
Cautions highlight possible danger to equipment. Both are used through-out
this manual and must always be followed.
WARNING
The chance of explosions, fires or electric shocks can be reduced
with thermal and over-current protection, proper grounding, enclosure
selection, and good maintenance. The following safety considerations
are not intended to be all-inclusive. Specific references throughout the
manual should also be consulted.
Inspection
Check the items you received against your purchase order. Carefully examine
the interface module for shipping damage. Report parts errors to Bodine.
Shipping damage claims should be made to the freight carrier.
Before installing this interface module, review the application to confirm
that the proper motor and control have been selected. This should be done
after reading the manual provided with the motor and all applicable safety
standards. If in doubt, contact your Bodine representative, or the home office

www.bodine-electric.com 7
if there is no representative in your area. Although Bodine Electric Company
assists its customers in selecting motors and controls for specific applications,
determinationoffitnessforpurposeoruseissolelythecustomer’sresponsibility.
Grounding
Both electronic controls and motors must be securely mounted and adequately
grounded. Failure to ground properly may cause serious injury to personnel.
Fusing
The AC input to the isolated interface module should be fuse protected. The
fuse must conform to the value and rating listed on page 15.
Environment
Open circuit boards in ventilated enclosures may emit flame during failure.
Bodine does not offer an explosion-proof line of motion control accessories for
hazardous locations (e.g., environments of flammable or explosive gas, vapor,
or dust). Bodine recommends using only approved explosion-proof products
in hazardous locations. The National Electric Code (NEC) allows exceptions,
but NEC and NEMA safety standards should be studied thoroughly before
exercising this option.
Moisture increases the electrical shock hazard of electrical insulation.
Therefore, this module and other open-type or unsealed accessories or
controls not specifically designed for such use, should be protected from
contact with liquids or moisture.
Ventilated Products
Open, ventilated products are suitable for clean, dry locations where cooling
air is not restricted. Do not insert anything into a product’s ventilation
openings.
Servicing
Emergency field repairs must be made only by authorized Bodine service
representatives. Repairs made by persons not authorized by the Bodine
Electric Company will void the warranty. Field repairs must be limited to
replacing the entire printed circuit board assembly. Because of the danger
of introducing safety hazards, do not install substitute parts or perform any
unauthorized modifications to electronic PC boards or components. To ensure
continued compliance with the design specifications and safety standards,
the interface circuit module should be returned to Bodine Electric Company
or an Authorized Service Center for servicing.

8www.bodine-electric.com
This manual does not purport to cover all details or variations in equipment,
nor to provide for every possible contingency to be met in connection with
installation, operation, or maintenance – no warranty of fitness for purpose
is expressed or implied. Should further information be desired, or should
particular problems arise which are not covered sufficiently for the user’s
purpose, the matter should be referred to the Bodine Electric Company.
The issuance of this manual does not confer to the recipient any license to
manufacture under any patents owned or controlled by the Bodine Electric
Company.
APPLICATION INFORMATION
The Bodine Model 3984 Isolated Interface Module is a versatile device
which can be used with a single motor and control or combined with other
3984 modules, motors, and controls to satisfy a variety of motion control
applications. The following information is provided as reference material; it
does not include every possible configuration. If you have any doubts about
using the Model 3984 for a specific application, contact your local Bodine
representative or the home office.
WARNING
To avoid injury because of unsuspected mechanical motion, always
disconnect the power supply to the motor control before performing any
service procedures on the motor, control, interface circuitry or driven
equipment.
CAUTION
This section is not a substitute for installation and operating instructions.
Refer to those sections for details on mounting, wiring, and operation.
Typical Control Signal Isolation
In simple applications involving a single motor and control, the Model 3984
accepts signals from a variety of motion control sources and generates
isolated output signals which are compatible with Bodine motor control
inputs. Figure 2 illustrates typical inputs and outputs for a Model 3984 when it’s
used to isolate ABL-3910 or 3911 and UPM-3318C control inputs. Refer to the
Installation Instruction Section of this manual for specific wiring variations,
DIP switch settings, and other pertinent information.

www.bodine-electric.com 9
Bi-Directional Master Speed Control
The input side of the Model 3984 provides connections to an internal ± 12 VDC
power supply. If a 10 KQ potentiometer is connected across the power supply
and the wiper is connected to the VIN1 terminal of the Model 3984, as shown
in Figure 3, a voltage divider circuit is formed. When the wiper is in the center
position, zero volts is applied to VIN1, so the motor speed is zero RPM.
When the wiper is turned in one direction, a positive voltage is applied to VIN1
causing the motor to turn in a clockwise direction. When the potentiometer is
turned in the other direction, a negative voltage is applied to VIN1 causing the
motor to turn in the counterclockwise direction. The motor speed is always
directly proportional to the absolute value of the voltage applied to VIN1.
Figure 3 – Master Speed/Direction Control Configuration
Figure 2– Typical Isolated Inputs for Bodine Controls
Model 3984
ISO +
ISO -
ICOM
VIN1
VIN2
IDIR
IDIS
ITAK
TAK
DIS
DIR
VOUT
COM
TB2 TB3
S2
T-Out *
DISABLE
DIR
S1
V+
* T-out may be labeled T7 on some controls
ABL-3910/3911
Brushless DC Motor Control
Motor
V+
TB3
TB2
COM
VOUT
DIR
DIS
TAK
ITAK
IDIS
IDIR
VIN2
VIN1
ICOM
ISO -
Model 3984
S2
H1
S1
UPM-3318C
DC Motor Control
Analog IN
Analog IN
Motor
ISO +

10 www.bodine-electric.com
Master/Slave Signal Generator
Several Model 3984 modules may be configured in a master/slave arrangement
as shown in Figure 4. The speed outputs of each slave module can be scaled
or offset to achieve different results for each slave motor. Each slave module
can control a different type of motor/control system.
The output of the master module can drive up to 10 slave modules. Each
slave module will follow the output of the master, but will vary proportionally
depending on the scaling or offset factor. For more information on adjusting
the speed control, refer to “Internal Adjustments/Calibration” in the Operating
Instruction Section of this manual.
Figure 4 – Master/Slave Configuration
potentiometers in
each slave 3984
can be used to scale
or oset each output
dierently. When the
master changes, all
of the slave outputs
will follow proportionally.
The MIN and MAX
Master
Slave 3
Slave 2
Slave 1
Motor 3
AC Line
DC Motor Control
Model WPM-2109C
S1
S2
COM
VOUT
AC Line
Module
3984
Model
VIN1
ICOM PM Motor
Motor 2
AC Line
Motor Control
Brushless DC
Model ABL-3911
S1
S2
COM
VOUT
AC Line
Module
3984
Model
VIN1
ICOM BLDC
ICOM
VIN1
Model
3984
Module
AC Line
VOUT
COM BLDC
ICOM
VIN1
Model
3984
Module
AC Line
VOUT
COM
S2
S1
Model ABL-3910
Brushless DC
Motor Control
AC Line
Motor 1

www.bodine-electric.com 11
INSTALLATION INSTRUCTIONS
Mounting the Model 3984 Interface Module
The mounting template (provided with this manual) can be used to position
and mark the location of mounting holes on the surface where the module is
to be located. The module may be mounted in any position provided there is
adequate air flow. It is equipped with four nylon spacers which provide ample
clearance between the mounting surface and the circuit board. The spacer
holes will accept No. 8 machine screws.
Electrical Connections
All connections to the Model 3984 are made at screw terminal blocks TB1, TB2,
and TB3. See Figure 5. Read the following instructions and all of the applicable
safety recommendations, before making any electrical connections.
WARNING
This module should only be installed by a qualified technician, electrician,
or electrical maintenance person familiar with its operation and associated
hazards. The National Electrical Code (NEC) local electrical and safety
codes, and when applicable, the Occupational Safety and Health Act
(OSHA) should be observed to reduce hazards to personnel and property.
The user must provide a proper enclosure. Circuitry is not at ground
potential. Do not perform work on or near the module while it is connected
to the AC line.
CAUTION
Exposed circuit boards should be protected from electrostatic discharge.
The interface module uses CMOS circuitry. Static discharge into the
circuit board must be avoided to prevent component damage.
WARNING
AC power should be the last connection made in order to prevent
accidental start-up. Disconnect the AC power before making any other
electrical connections.
CAUTION
Only copper wire with a minimum 60° C rated insulation is recommended
for all cable assemblies

12 www.bodine-electric.com
Controlling Speed With an Analog Input Voltage: Analog voltage speed
input signals are connected across the VIN1 or VIN2 and ICOM terminals,
on terminal black TB2, depending on the level of the voltage. In addition, DIP
Switch DS1 levers must be set properly. Refer to Chart 1.
Chart 1 – Voltage Speed Input Connections and DIP Switch Settings
Input
Voltage
Level
TB2
Terminal
Connection
DS1 DIP
Switch Levers
In ON Position*
DS1 DIP
Switch Levers
In OFF Position*
0 to ± 25 VDC
0 to ± 250 VDC
VIN1
VIN2
None
None
1, 2, 3
1, 2, 3
*DS1 lever 4 can be either ON or OFF depending on the direction control requirements
See Page 13 – Automatic Direction Mode.
Controlling Speed With an Analog Input Current: The Model 3984 will also
accept current speed inputs. Current speed control signals are applied
to VIN1 on TB2. For proper operation, DIP Switch DS1 levers must be set
correctly based on the level of the input current. Refer to Chart 2.
Chart 2 – Current Speed Input Connections and DIP Switch Settings
Input
Current
Level
TB2
Terminal
Connection
DS1 DIP
Switch Levers
In ON Position*
DS1 DIP
Switch Levers
In OFF Position*
1 to 5 mA
4 to 20 mA
10 to 50 mA
VIN1
VIN1
VIN1
3
2
1
1, 2
1, 3
2, 3
*DS1 lever 4 can be either ON or OFF depending on the direction control requirements.
See Page 13 – Automatic Direction Mode
Figure 5 – Model 3984 Circuit Board
MODEL 3984
115/230 VAC 50/60 HZ
ELECTRIC
BODINE
ISOLATED INTERFACE MODULE
CHICAGO IL 60618 USA
COMPANY
TB3
MOTOR
V+
CONTROL
COM
DIR
VOUT
DIS
TAK
ITAK
IDIS
IDIR
VIN2
ICOM
ISO-
ISO+
TB2
TB1
SIGNALS
ISOLATED
VIN1
TB1
10-50
4-20
1-5
DIR
MAX MIN
DS1
ON
1234
AC INPUT TERMINALS
1234

www.bodine-electric.com 13
Connect the disable input across ICOM and IDIS on terminal block TB2.
Connect the DIS output to the disable input on the motor control.
Automatic Control of Motor Direction: The Model 3984 has a built-in circuit
which can be used to set motor direction based on the polarity of the voltage
signal applied to VINI or VIN2 on Terminal block TB2. This automatic circuit
is enabled by switching DIP Switch DS1, lever 4 ON. When used with Bodine
ABL-3910/3911 controls as shown in Figure 2, the motor will rotate in a CW
direction when VIN>0; it will rotate in a CCW direction when VIN<0.
NOTE: If a voltage divider potentiometer is connected across ISO+ and ISO- to create
a master speed/direction control, DS1: 4 must be ON. See Figure 3
The DIR output at the TB3 terminal block should be connected to the DIR input
on Bodine motor controls (if applicable).
Independent Control of Motor Direction: The automatic direction mode can
be disabled by switching DIP switch DS1, lever 4 OFF. When disabled, a
separate switched input may be connected across IDIR and ICOM to control
motor direction of rotation. The switched input can be a manual switch, relay
contact, or digital signal from any open collector type device capable of
sinking a current of 10 mA minimum and withstanding 12VDC.
The DIR output at the TB3 terminal block should be connected to the DIR input
on Bodine motor controls (if applicable).
WARNING
Never rely on logic circuitry as a means of disabling the motor or control.
To prevent unsuspected mechanical motion and potential injury, the AC
power should always be disconnected from the control power supply
whenever logic circuits or the driven equipment are serviced.
Speed Control Output: The Model 3984 Module provides a scalable speed
control output signal between 0 and +10 VDC. The output signal is delivered
across VOUT and COM on terminal block TB3. On Bodine motor controls, the
VOUT signal should be connected to S2. The COM signal should be connected
to S1 (Control Signal Common). Refer to “Internal Adjustment/Calibrations” in
adjustment procedures.
Controlling Motor Disable: An isolated motor disable input IDIS is provided at
terminal block TB2. A switch closure or activation by an open collector device
capable of sinking 10 mA minimum will generate a disable signal at DIS on
terminal block TB3.

14 www.bodine-electric.com
Tachometer Output: When used with the Bodine ABL-3910/3911 Brushless
DC Motor Controls, the Model 3984 module provides digital tachometer
output at the ITAK terminal for monitoring motor speed. The output pulse
levels correspond to one motor revolution. The ITAK output provides an
unterminated open collector output. A pull-up resistor or another logic device
is required for assistance in interfacing the ITAK output.
Internal Auxiliary Power Supply: The Model 3984 Isolated Interface Module
has an internal ±12 VDC, 10 mA power supply which may be used for external
components if needed. It is accessible via the ISO+, ISO-, and ICOM terminals
on terminal block TB2.
AC Power Connections
AC Power should always be the last connection made during installation
and the first item disconnected before servicing. The Model 3984 may be
connected to either a 115 VAC, 50/60 Hz or a 230 VAC, 50/60 Hz source.
For 120 VAC:
Connect a jumper from terminals 1 to 2 and from 3 to 4. Refer to Figure 7. Then
connect 120 VAC source to terminals 1 and 4 of terminal block TB1.
For 240 VAC:
Connect a jumper from terminal 2 to 3, then connect 240 VAC source to
terminals 1 and 4. Refer to Figure 7.
Figure 6 – ITAK Output
pull-up resistor
User supplied
User Equipment
User Input
I less than or
equal to 2mA
equal to 55V
V less than or
(+)
User Logic Supply
ICOM
ITAK
Model 3984
collector output
Unterminated open
Model 3984
Logic

www.bodine-electric.com 15
Fuse Installation: It is recommended that the Model 3984 be protected with
an external fuse. The amperage rating of the fuse depends on the AC line
voltage used to power the module as shown in Chart 3. In a multi-control
system, each module should have a separate fuse. (SEE CAUTION BELOW.)
Chart 3 – Recommended AC Fuse Value
Line Input Fuse Value Fuse Type Manufacturer P/N
115 VAC .062 Amp Slow Blow Littlefuse 313.062
230 VAC .032 Amp Slow Blow Littlefuse 313.031
CAUTION
In installations where one side of the AC supply is at ground potential, only
the hot side will require a fuse. If both sides of the AC line are at a potential
with respect to ground, each line will require a separate fuse.
Figure 7 – AC Power Connections
TB1
4
3
2
1
115 VAC
50/60 HZ
230 VAC
50/60 HZ
1234
AS SHOWN
TERMINALS 1 TO 2 AND 3 TO
4
USE JUMPERS TO CONNECT
TB1
AS SHOWN
TERMINALS 1 TO 2 AND 3 TO 4
USE JUMPERS TO CONNECT

16 www.bodine-electric.com
OPERATING INSTRUCTIONS
WARNING
Explosions, fires, or electric shock hazards can be reduced through
thermal and over-current protection, good maintenance, proper grounding,
and enclosure selection. Review safety considerations outlined in the
important Safety Precautions and Installation Instruction Sections.
Preliminary Checks
1. Before applying signals to the Model 3984, check all fuses, connections,
and adjustments as outlined in this manual and in the motor control manual.
2. Proper consideration should be given to all rotating members. Before
starting, be sure keys, pulleys, etc. are securely fastened. Proper guards
should be provided to prevent hazards to personnel while the equipment
is rotating.
3. Mechanical considerations such as proper mounting and alignment of
products, and safe loads on shafts and gears should be reviewed. Do not
depend upon gear friction to hold loads.
4. The motor or gearmotor should be securely mounted (because of possible
reaction torque). Test the motor/gearmotor unloaded to be certain that
proper connections have been made.
5. If the motor/gearmotor does not start promptly and run smoothly, or if
the control does not react to input signals, disconnect the AC power
immediately. Double check all wiring, and refer to “Troubleshooting” in this
manual and the motor control manual.
6. If the problem persists, contact your Bodine representative or a Bodine
Authorized Service Center and describe the problem in detail. Include
all the motor/gearmotor nameplate data and control information. Do not
disassemble or attempt to service any products unless authorized by
Bodine. Removing screws voids the Warranty.
Operation
1. Disconnect the AC power to the Model 3984 and the motor control and
double check all control connections as outlined in the motor control
manual.
2. Set external speed potentiometers to ZERO or null positions. If a Disable
switch is used, close the switch.
3. Connect the AC power to the Model 3984 module and the motor control.
4. Set the manual Direction switch, if provided, for the proper direction of
rotation.
5. Open the Disable switch if used.
6. Turn the speed potentiometer until the motor rotates. Then adjust the
potentiometer to achieve the desired speed.

www.bodine-electric.com 17
7. If the motor does not operate, check all connections and fuses. If a fuse is
blown and the motor is not locked (stalled) or overloaded, do not replace
the fuse. The control may be damaged. Refer to “Troubleshooting” in this
manual and the motor control manual. If the motor is overloaded, reduce
the load and replace blown fuses with new ones of the proper rating. (See
page 15).
Internal Adjustments/Calibration
The Model 3984 is factory adjusted to provide a VOUT signal of 0 to 10 VDC
for a 0 to ±10 VDC signal applied to VIN. The polarity of the output voltage is
always positive regardless of the input.
If other input signal ranges are required, the Model 3984 can be calibrated
using the following procedures for adjusting the MIN and MAX potentiometers.
WARNING
Use a non-metallic or insulated adjustment tool (such as a television
alignment tool) for internal adjustments. Circuit components are not at
ground potential and accidental short circuiting and shock hazard may
occur with conducting tools. Adjustment should be made only by qualified
service personnel.
MIN Speed Trim Potentiometer: The MIN trim potentiometer is used to adjust
the minimum speed of the motor to correspond to a specific input voltage
or current signal. For example, by adjusting the MIN potentiometer CW it is
possible for the motor to run at a minimum speed in the absence of an input
signal. This is useful in applications where the motor must keep running.
To adjust the MIN trip potentiometer:
1. Apply the desired voltage or current signal across terminals VIN1 or VIN2
and ICOM on terminal block TB2.
2. Adjust the MIN potentiometer until the motor RPM reaches the desired
level.
CAUTION
Adjusting the MIN potentiometer will affect the MAX potentiometer
setting and the MAX potentiometer will have to be readjusted.

18 www.bodine-electric.com
MAX Speed Trim Potentiometer: The MAX trim potentiometer is used to adjust
the maximum speed of the motor to correspond to a specific input voltage.
For example, adjusting the MAX potentiometer CW will allow an input voltage
less than ±10 VDC to generate a maximum +10 VDC output to run the motor at
rated speed.
Conversely, it may be adjusted CCW so that input signals greater than ±10
VDC can be used to operate the motor at its full rated speed.
To adjust the MAX trim potentiometer:
1. Apply the desired voltage or current signal across terminals VIN1 or VIN2
and ICOM on terminal block TB2.
2. Adjust the MAX potentiometer until the motor RPM reaches the desired
level.

www.bodine-electric.com 19
TROUBLESHOOTING
WARNING
Disconnect the AC power to the Model 3984 before troubleshooting.
The charts on the following pages provide assistance in troubleshooting
common problems which occur during normal installation and operation. If
the problem persists, contact your source of purchase or a Bodine Authorized
Service Center and describe the problem in detail. Do not disassemble
the product unless authorized by Bodine Electric Company. Performing
unauthorized repairs will void the warranty.
SYMPTOM PROBABLE CAUSE CORRECTIVE ACTION
MODULE BLOWS
FUSE
Incorrect AC power wiring
Damaged module
Components
Check connections, look for
shorts and repair as required.
Contact Bodine or Service
Center for assistance.
MOTOR WILL
NOT START
Open AC power fuse
Wrong input settings
Input signal too low
Disable switch closed
Replace fuse. Refer to page 15
for proper value
Check DS1 settings, page 12
Increase input signal or scale.
VOUT using MAX trim
Potentiometer, page 18
Open Disable switch
MOTOR WILL
NOT COME UP
TO SPEED
MAX trim pot set
too low
Input signal too low
Motor overloaded
Adjust MAX trip pot, page 18.
Increase input signal or scale.
VOUT using MAX trim
Potentiometer, page 18
Re-examine the load
parameters.
MOTOR SPEED
IS UNSTABLE OR
PULSATES
Input signal too low Increase input signal or scale
VOUT using MAX trim
potentiometer, page 18.

20 www.bodine-electric.com
SYMPTOM PROBABLE CAUSE CORRECTIVE ACTION
MOTOR WILL NOT
STOP WITH SPEED
POT ADJUSTED
AT ZERO OR WITH
NO INPUT SIGNAL*
MIN potentiometer out of
adjustment
Wrong DIP switch
settings
Defective input circuitry
Adjust MIN potentiometer,
Page 17.
Check DIP switch settings,
page 12.
Check VIN1, VIN2, and ICOM
for presence of input signal.
NO SPEED
ADJUSTMENT
Defective input circuitry Check VIN1, VIN2, and
ICOM for presence of
input signal.
MOTOR TURNS
IN WRONG
DIRECTION
Polarity of input signal
reversed
Check polarity of voltage
at VIN1 or VIN2. See page
13, Automatic Control of
Motor Direction.
MOTOR DOES
NOT CHANGE
DIRECTION
WHEN POLARITY
OF VIN CHANGES
DIP switch DS1, lever 4
is in the OFF position
Turn DS1:4 to ON position
*Note: The disable input should be activated or the disable switch closed when the motor is
expected to remain stopped.
Table of contents
Other Bodine Control Unit manuals
Popular Control Unit manuals by other brands
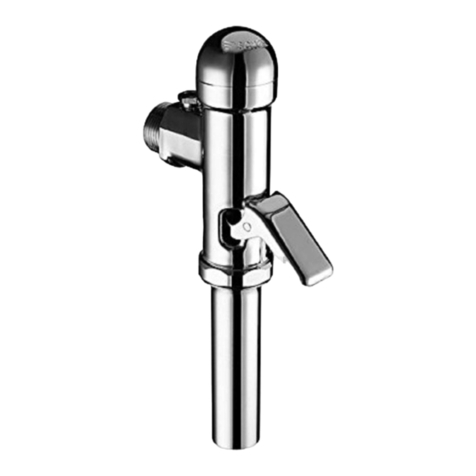
Schell
Schell Schellomat 02 204 06 99 Assembly and service instructions
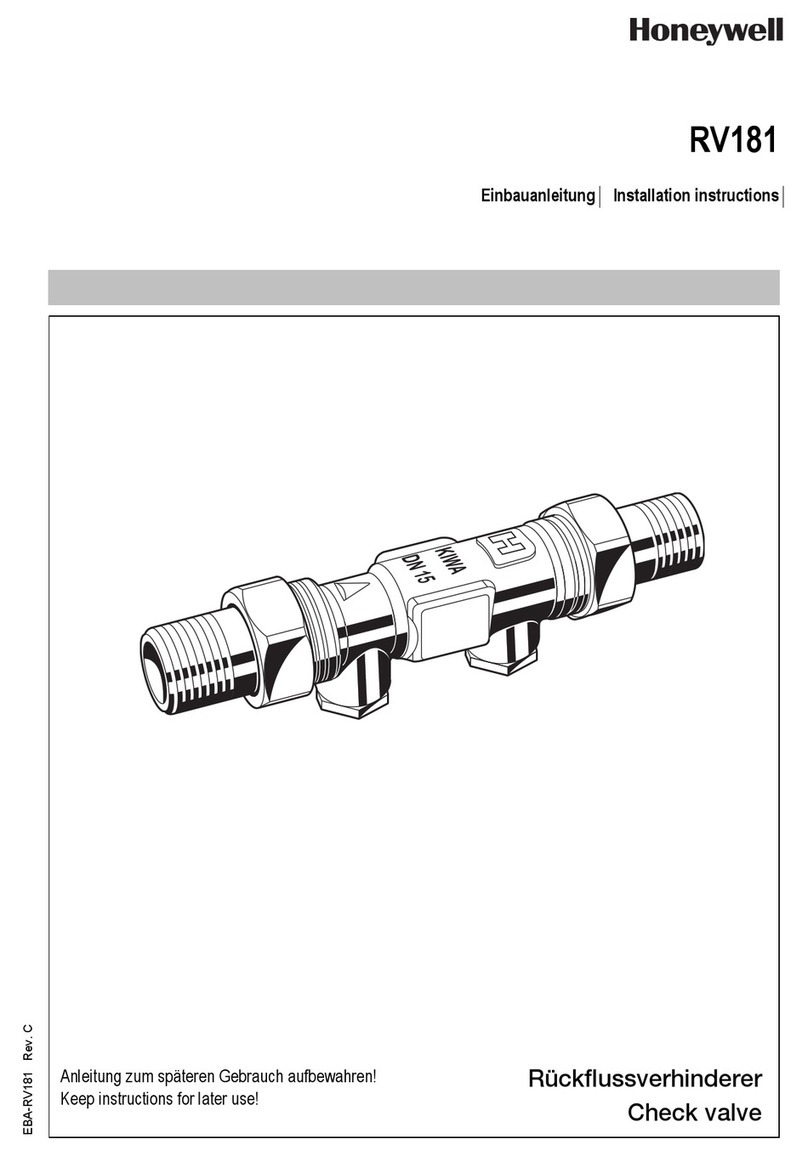
Honeywell
Honeywell RV181 installation instructions
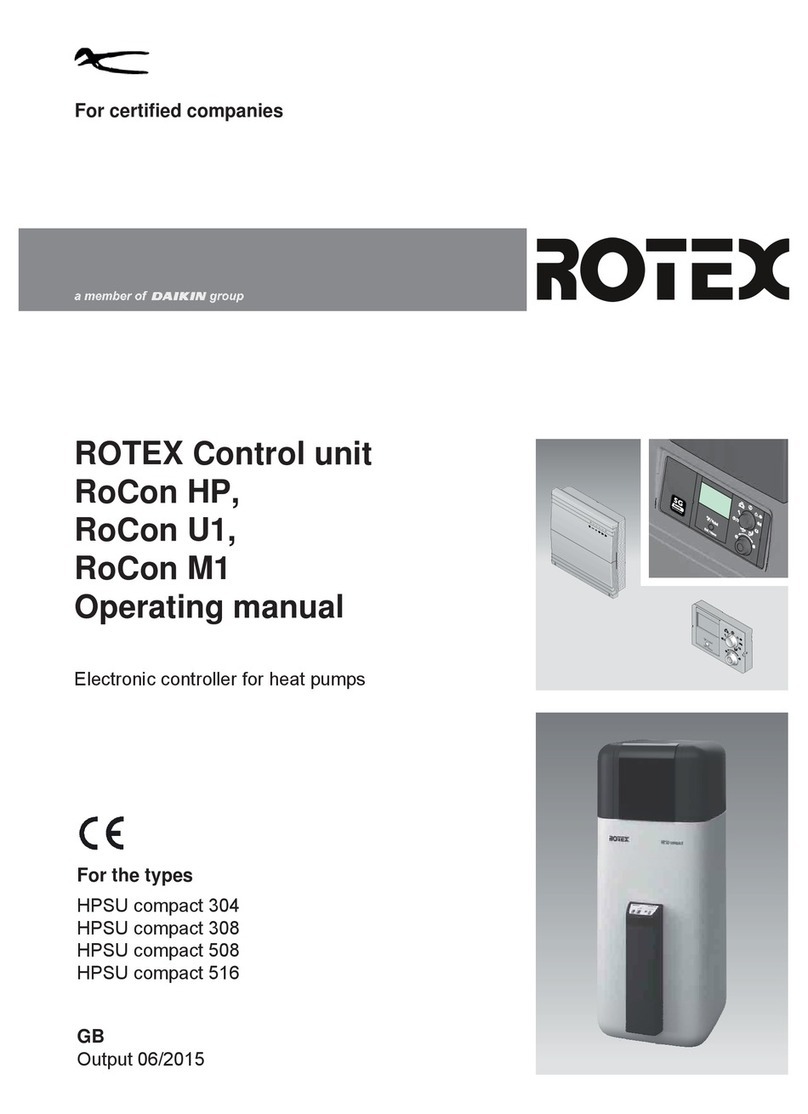
Rotex
Rotex RoCon U1 operating manual

Velleman
Velleman Whadda WPM457 manual
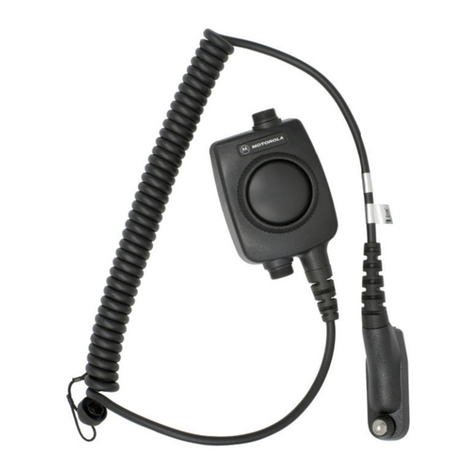
Motorola solutions
Motorola solutions PMLN6827 manual
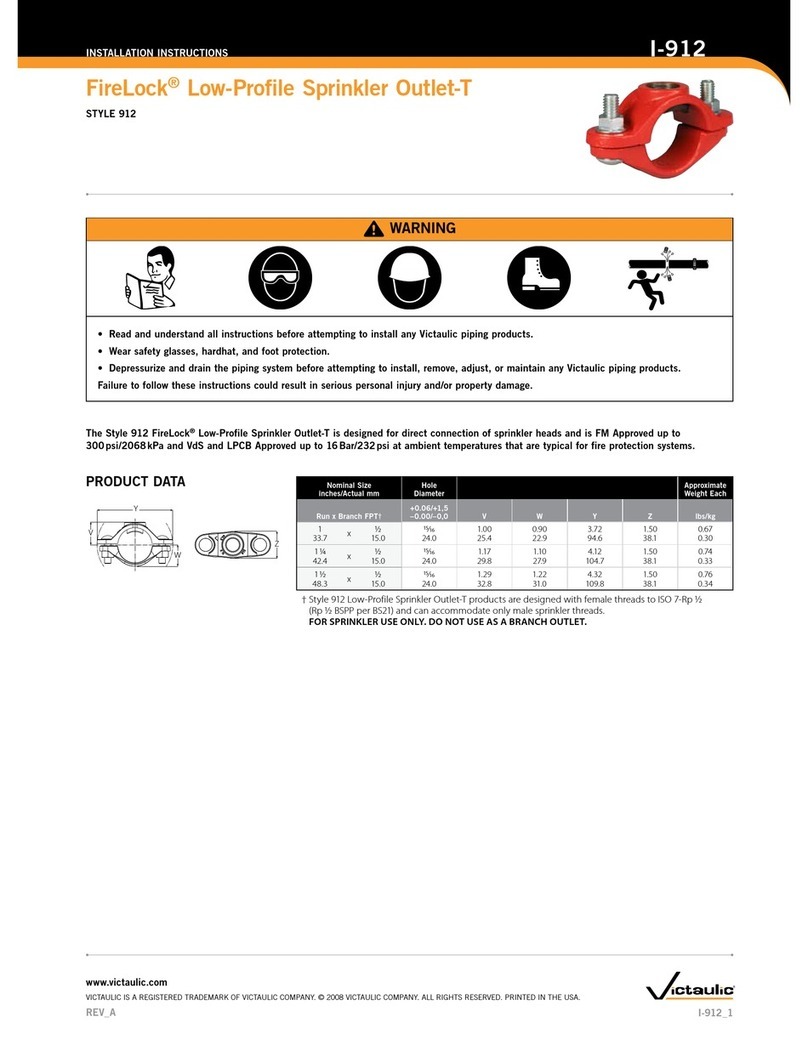
Victaulic
Victaulic FireLock 912 Installation instructions manual