BrewBuilt X1 UNI PRO User manual

X1 UNI PRO
ASSEMBLY AND
INSTRUCTION GUIDE
CONTENTS:
PAGE 2–3..............Cleaning, Testing, What’s Included
PAGE 3 – 4...............................................................................Assembly
PAGE 5–8............................................................................How to Use
BREWBUILT.COM
WARNING
Read entire manual for important
safety information before using
your BrewBuilt X1 Uni Conical
Fermenter. Failure to follow warnings
could result in serious injury or death.

1. Neoprene Jacket
2. Pressure Pack
Additional Parts
Included:
ALWAY RELEASE PRESSURE from the fermenter
before removing any TC connection, tting,
accessory, or lid clamp connected to the Fermenter.
Read section below on how to release pressure
from Fermenter.
This guide will walk you through assembling
and using your new conical fermenter.
GETTING STARTED
2. CLEAN THE CONICAL
Before your first use, clean and rinse the conical
along with all the parts and fittings. This
will remove any leftover oil or dust from the
manufacturing process. We recommend using
PBW cleaner. Do not use bleach.
3. WATER TEST
After cleaning and rinsing, we also recommend
filling your conical with water and familiarizing
yourself with its operations prior to your first use.
Before you tighten down TC clamps, make sure the
gasket is seated properly into both flanges.
Once the gasket is in place, loosen the clamp so it
can be fitted around the flange ends.
You do not need to use any tools for leverage when
tightening TC clamps. Hand tightening is enough for
a secure, leak-proof connection.
WARNING!
READ AND UNDERSTAND
THIS FULL MANUAL
Before your first use, read through this full
manual, and make sure you understand the use &
warnings. Failure to follow these warnings could
result in serious injury or death.
1.
First Time Working
With TC Clamps?
ITEM DESCRIPTION QTY
A Pressure Lid 1
B 4" TC Clamp 1
C 4" TC Gasket 1
D 1.5" Blow Off Barb 1
E Silicone Blow Off Tube 1
F 1.5" TC Clamp 3
G 1.5" TC Gasket 3
H Conical Lid 1
I Lid Clamp 1
J Lid Gasket 1
K Conical Body 1
L 1.5" TC Thermowell 1
M 1.5" TC Sample Valve 1
N 2" TC Gasket 1
O 2" TC Clamp 1
P 2" Butterfly Valve 1
Q Flex Chamber 1
R 3/8" Leveling Foot 4
Parts List
PAGE 2 BREWBUILT.COM
1 2

BREWBUILT.COM PAGE 3
K
F
G
E
D
J
H
I
A
L
F
G
N
O
P
M
F
G
R
B
C
Q
ASSEMBLING FOR ALL X1 CONICALS
FEET
Thread each foot into the bottom of the legs on the Conical leaving about half an inch of thread visible. Adjust as needed.
BLOW OFF
Place 1.5" TC gasket into the open blow o port on the conical lid and fasten the Blowo U Barb with a 1.5" TC clamp, ensuring that the U
Barb is pointing downward o the side of the conical. Slide ½" Silicone tubing over the barbed side of the U Barb. It’s easiest to start with
one side and then work it around until barbs are fully covered.
THERMOWELL
Place 1.5" TC Gasket and Thermowell into the open port in front of the conical just below the etched BrewBuilt Logo and
fasten in place using 1.5" TC clamp.
SAMPLE VALVE
Place 1.5" TC Gasket and Sample Valve into the open port halfway down the conical base on the front of the unit and fasten in place using
1.5” TC clamp. Make sure the Sample Valve is closed by turning it clockwise until it stops.
BUTTERFLY VALVE
The Buttery Valve opens in one direction, so be sure to install it so the valve handle opens downward away from the conical bottom. Place
2" TC Gasket and Buttery Valve on the bottom port of the conical and fasten in place using 2" TC clamp.

`
LID CLAMP
WARNING: Improper assembly of the lid clamp can cause the X1 Lid to be released while under pressure, possibly resulting in injury or death.
•When installing the lid clamp, be careful to install it according to the pictures shown here. Incorrect assembly can be hazardous to both
equipment & user.
•Ensure that the lid is centered on top of the conical body during assembly. The two should be centered so that the clamp seals down evenly.
•Lid Clamp should be hand tightened fully so there is a 5/8" gap between the ends on the 27 and 42 gallon models and a 1/8" gap on the 7
and 14 gallon models. See assembly pictures below for proper setup.
LID GASKET
•Flip the lid upside down and install a section of the gasket, at
side seating into the lid groove rst. Lightly push the gasket in,
installing it in the groove as you go around the lid.
•Please Note, the gasket is larger than the groove to help ensure
a tight seal during fermentation. Continue pushing the gasket
against itself and into the lid until it is in the groove and equally
distributed without stretch points. Once you get the rst piece
of the gasket in the groove then you can use both hands to work
the gasket around the lid and into the groove with your thumbs.
GASKET
ORIENTATION
Flat Side Into Lid Groove
GASKET INSTALLATION
With Lid Upside Down, Push Flat End Of
Gasket Into Lid Groove
WARNING
WARNING: Improper assembly of the
lid clamp can cause the X1 Lid to be
released while under pressure, possibly
resulting in injury or death.
Correct Lid Clamp Assembly for 27 and 42 Gallon X1
Incorrect Lid Clamp Assembly: Backwards Arm
Incorrect Lid Clamp Assembly: Partial Engagement
Incorrect Lid Clamp Assembly: Rotated Arm
TOP VIEW
Top View
Top View
Top View
Side View
Side View
Side View
FULL
ENGAGEMENT FULL
ENGAGEMENT
FULL
ENGAGEMENT
FULL
ENGAGEMENT
CORRECT GAP
OF 1/8"
CORRECT
GAP
OF 1/8"
CORRECT
GAP
OF 5/8"
CORRECT GAP
OF 5/8"
CORRECT ARM
ROTATION
CORRECT ARM
ROTATION
CORRECT
ARM ROTATION
CORRECT
ARM ROTATION
INCORRECT
ARM ROTATION
BACKWARDS
ARM
PARTIAL
ENGAGEMENT
ARM
ROTATED
CORRECTLY BUT
NOT FULLY ENGAGED
IN SADDLE
Correct Lid Clamp Assembly for 7 and 14 Gallon X1
PAGE 4 BREWBUILT.COM

General Use
SANITIZE — Always sanitize your Conical before lling
it with wort. This includes opening your sample valve and
dump ports to ensure sanitizer makes contact with every
nook ‘n cranny. We recommend Star San or a similar sanitizer.
Never use a bleach solution as bleach will cause pitting and
corrosion on the surface of the stainless steel.
FILLING — Your conical can be lled by dumping wort
through the top, or pumped in via the sample valve.
WARNING: Do not overll your conical past the maximum
volumes listed below. Excess volume during fermentation can
cause fermentation material called Krausen to clog the blow o
and airlock causing over-pressurization of the conical to occur.
MAXIMUM FILL LEVELS :
•7 Gallon X1 – 5.5 gallons liquid
•14 Gallon X1 – 11 gallons liquid
•27 Gallon X1 – 21.5 gallons liquid
FERMENTATION — With the blow o barb and silicone
blow o hose connected, place the end of the silicone blow
o tubing into a bucket lled with water. We prefer the
silicone tubing as opposed to a rigid stainless blow o as
silicone tubing is much easier to remove and clean between
batches. Silicone also allows greater exibility with regards to
blow o location.
WARNING: Never remove the blow o tube during a
fermentation.CappingthefermenterbeforeALLCO2production
has nished can cause dangerous over-pressurization. Always
use the optional BrewBuilt Pressure Fermentation Kit if you
intend to capture ANY CO2from fermentation.
If you wish to add pellet hops, whole hops, oak, or any other
loose material to the fermentation we recommend using a
mesh bag. Boil the mesh bag before use to ensure its sanitized.
WARNING: Do not place pellet hops, whole hops, oak chips,
or other items directly into the fermenter. Loose material can
clog the blow o and airlock causing over-pressurization of
the conical to occur. Use a mesh bag to contain these types of
materials.
DUMPING YEAST AND TRUB — One of the biggest ben-
ets of a Conical Fermenter is the ability to dump yeast & trub
from the bottom port. This couldn’t be easier with the 2" TC
USING YOUR X1 PRO CONICAL
IMPORTANT SAFETY INFORMATION! Please read this entire instruction manual for important safety information prior to
the use of your BrewBuilt X1 Uni Conical Fermenter. Failure to follow these warnings could result in serious injury or death.
WARNING: Follow all chemical labeling & cautions when cleaning and sanitizing Fermenter, always use approved cleaning agents.
WARNING: Do not pick up Fermenter when full.
WARNING: Do not overll your conical past the maximum volumes listed below. Excess volume during fermentation can cause fermentation
material called Krausen to clog the blow o and airlock causing dangerous over-pressurization of the conical to occur. Over-pressurization can result
in injury or death.
WARNING: If using the optional Flex Chamber, always keep the bottom buttery valve open to allow CO2to escape while the Flex Chamber is
installed. Close valve only before removing.
WARNING: Do not place pellet hops, whole hops, oak chips, or other items directly into the fermenter. Loose material can clog the blow o and
airlock causing dangerous over-pressurization of the conical to occur. Use a mesh bag to contain these types of materials.
WARNING: Only pressurize your Fermenter when using the optional BrewBuilt Pressure Pack accessory kit.
WARNING: If pressurizing, never exceed 15 PSI.
WARNING: Do not alter or change the Pressure Relief Valve (PRV) built into the lid.
WARNING: Always use an approved CO2regulator, with a functional low pressure gauge, to apply pressure to your BrewBuilt Fermenter.
WARNING: Incorrect assembly of the lid clamp can cause the X1 Lid to be released while under pressure.
WARNING: If your Fermenter is under pressure, release all pressure before removing the lid clamp, tri-clamp (TC) ttings, or accessories. Failure
to release pressure from the X1 could result in a tting or lid being released while still under pressure, possibly resulting in injury or death.
WARNING: Only ferment under pressure when using the optional BrewBuilt Pressure Fermentation Kit.
WARNING: Never close o/cap your X1 during fermentation at any time unless you are using the optional BrewBuilt Pressure Fermentation Kit.
GENERAL WARNINGS:
PRESSURE WARNINGS:
Failure to follow these instructions & warnings can cause a lid/clamp failure, possibly resulting in injury or death.
RELEASING PRESSURE WARNINGS:
PRESSURE FERMENTATION WARNINGS:
Failure to follow these instructions & warnings can cause dangerous over-pressurization resulting in a lid/clamp failure, possibly resulting in injury
or death.
BREWBUILT.COM PAGE 5

valve with a 2" TC clamp.
TIP: If you are connecting the Flex Chamber to a full X1 conical, it’s
important to understand some basic displacement concepts. The
empty Flex Chamber is lled with gas (oxygen) that will be sent
up through your beer. If this happens post fermentation it could
negatively impact the beer’s avor. See below to learn how to use
your Flex Chamber side ports to ush with CO2.
COLLECTING AND DUMPING TRUB
WITH FLEX CHAMBER
The ability to remove trub and hop sediment is one of the key
advantages of a conical fermenter. With the buttery valve
open and the Flex Chamber attached, trub separates directly
into the Flex Chamber, which can then be easily removed.
Follow the process outlined below.
1. If you are using the conical with the Pressure Pack lid, make
sure the entire conical system has been depressurized and
that the bottom buttery valve is in the open position. For
instructions on releasing pressure see the section below
titled ‘Releasing Pressure’.
2. When you are sure the system has been depressurized,
close the buttery valve at the bottom of the conical.
3. Place a bowl, pan, or small bucket below the Flex Chamber
to collect drips and un-clamp the Flex Chamber from the
buttery valve.
FLUSHING THE FLEX CHAMBER WITH CO2
An optional step is to ush your Flex Chamber with CO2
prior to attaching it. This will help eliminate oxygen from the
Flex Chamber. You can easily do this by attaching a ball lock
adapter (Part# KG500) to one of the threaded side ports.
Here’s how to eectively ush the Flex Chamber with CO2.
1. Soak or spray the Flex Chamber and all parts — caps,
gaskets, clamps, etc. — with sanitizer prior to assembling
and attaching it to your conical dump port.
2. Attach the Flex Chamber to the bottom of the buttery
valve, keeping the buttery valve closed. Remove one
black side cap and install the KG500 ball lock adapter.
Slightly loosen the other black cap on the opposite side of
the Flex Chamber so that CO2can escape while ushing.
3. Set the regulator on your CO2tank to its lowest possible
setting i.e. 1–2 psi and connect your Ball Lock Gas QD to
the KG500 ball lock adapter.
4. Allow gas to ow out of the Flex Chamber for a few
seconds to ensure all the oxygen has been ushed. Tighten
the black cap. You can replace the KG500 with the black
cap or leave it in place for fermentation.
Pressure Package
WARNING: Only pressurize your Fermenter when using the
optional BrewBuilt Pressure Pack accessory kit.
WARNING: If pressurizing, never exceed 15 PSI.
WARNING: Do not alter or change the Pressure Relief Valve
(PRV) built into the lid.
WARNING: Always use an approved CO2regulator, with a
functional low pressure gauge, to apply pressure to your BrewBuilt
Fermenter.
Buttery Valve on the bottom of your conical. Another add-
ed advantage is being able to harvest your yeast for use on
future batches. Regardless of whether you’re dumping trub,
hops, or yeast, you will want to guide that slurry into a drain
or receiving vessel like a bucket or jar. Be sure to spray the
Buttery Valve down with sanitizer prior to dumping. Also
keep in mind that you will need to open one of the ports on
the top of the conical to allow air to replace the liquid that
is owing out the bottom. Another option is the included
BrewBuilt Flex Chamber that connects to the bottom of the
conical and allows you to collect and dump yeast and trub.
Learn more about using the Flex Chamber on the following
page.
TRANSFERRING FINISHED BEER — Racking your beer
with the sample port is as easy as hooking up some sanitized
tubing and opening the valve. Remember that you will need
to either open one of the ports on the top of the conical to
allow air to replace the liquid that is owing out, or hook up
CO2to the blow o port to replace the headspace and limit
oxygen exposure. Using CO2also eliminates the need for the
liquid to be gravity fed into the keg or other receiving vessel.
Either way, we recommend pushing your nished beer into
a sanitized keg via the bev-out body connect port. This will
keep splashing to a minimum as beer will ow down the
beverage dip tube and gently ll the keg from the bottom
up. Lastly, pull up the PRV ring on the keg and set it in the
open position to allow air (or CO2if you pre-purged the keg)
to escape as your fresh beer ows in.
The Flex Chamber
WARNING: Always keep the bottom buttery valve open when
the ex chamber is installed so that CO2from fermentation can
properly vent.
The Flex Chamber is designed specically for
use with a BrewBuilt X1 conical Fermenter.
It attaches directly to the 2" buttery dump
valve and can be used for removing trub,
harvesting yeast, and many other tasks.
Always keep the buttery valve open
when the Flex Chamber is installed. When
you are ready to remove the Flex Chamber,
depressurize the system with the buttery
valve open. This allows any pressure to also
leave the Flex Chamber. Aer relieving all pressure
in the system you can close the buttery valve and safely
remove the Flex Chamber.
PREPARING YOUR FLEX CHAMBER FOR
USE EACH TIME
1. Soak or spray the Flex Chamber and all parts — caps,
gaskets, clamps, etc. — with sanitizer prior to assembling
and attaching it to your conical dump port.
2. Assemble your Flex Chamber by attaching the lid and
threading the caps onto the threaded ports on each side.
3. Spray sanitizer into the closed buttery valve on your
conical dump port as well as the top of the Flex Chamber
and its TC gasket. Fasten the Flex Chamber to the buttery
PAGE 6 BREWBUILT.COM

WARNING: Before removing any tri-clamp, tting or lid clamp
connected to the conical, release pressure from conical following
the instructions in this section. Failure to release pressure from your
X1 Uni could result in a tting or lid being released under pressure
which could cause bodily harm or death.
WARNING: Before applying pressure make sure the Pressure
Relief Valve (PRV) is properly installed in the lid.
WARNING: Always conrm your Lid PRV is clean and working
properly before applying CO2pressure.
The Pressure Pack, specically designed to work
with BrewBuilt X1 Conical Unitanks, unlocks many
possibilities. Apply low pressure before cooling
to eliminate sucking oxygen back in. Use it to
grab a sample or transfer nished beer to a
keg in a true oxygen-free environment.
The Clear Float allows sampling or
transferring of the clearest possible
beer from the top down! In this guide.
Please read and follow the additional
instructions that come with your Pressure
Pack Kit.
Whenever your X1 conical is under
pressure be aware that you will need
to relieve pressure before removing
the lid clamp or any tting that is
attached to your X1 fermenter. If you
are using a Flex Chamber collection
vessel, make sure the bottom buttery
valve is always in the open position
when in use and when relieving pressure
from the conical.
INSTALLATION
Assemble the Pressure Pack lid per the diagram. DO NOT
USE TEFLON TAPE to assemble threaded body connects
as they seal with the included o-rings. When attaching the
Pressure Pack lid to your X1 conical, be sure your TC gasket is
properly seated and then tighten down the TC clamp. Follow
instructions that come with your Pressure Pack lid.
TIP: A welded a hook on the bottom of the Pressure Pack Lid can be
used to hang drawstring bags for avoring additions.
APPLYING PRESSURE
First Test — First take a moment and read the warnings above.
For safety we always recommend the rst pressure test be
made while the conical is lled with water. Aer the conical
is completely lled with water, replace the u-shaped blowo
with an included tri-clamp end cap. Before connecting CO2
pressure be sure you have a working, accurate regulator with
a low pressure gauge. We recommend setting your regulator
to 1–2 psi to start with, and always less than 15 psi. Connect
your gas-in ball lock QD on your CO2dra system to the gas-in
body connect located on the Pressure Pack. The gas-in body
connect has a notch on the side, while the beverage-out
body connect does not. With 1–2 psi applied to the conical,
practice releasing pressure by unthreading the PRV cap. Read
the section on releasing pressure slowly as instructed in the
section ‘Releasing Pressure’ below.
TIP: When applying pressure some brewers choose to cap the blowo
port with an optional tri-clamp pressure relief valve with a gauge.
TRANSFERRING AND SAMPLING – The bev-out tting
is equipped with a unique oating dip tube that will pull
beer from the top rather than the middle or bottom of the
conical. We recommend using a ball lock jumper, a section of
beer line with a beverage-out QD at both sides, to transfer
beer from your X1 to the bottom of your keg. When applying
pressure for sampling or transferring start with a low pressure
and increase only as needed. Keep in mind that your X1 Uni
and Pressure Pack lid is rated at 15 psi and the PRV will start
releasing pressure around this point. Never apply more than
15 PSI to your X1.
TIP: Filling your keg from the bottom up will keep splashing to a
minimum as beer will ow down the beverage dip tube and gently
ll the keg from the bottom up. Lastly, pull up the PRV ring on the
keg and set it in the open position to allow air (or CO2if you pre
purged the keg) to escape as your fresh beer ows in.
RELEASING PRESSURE
WARNING: Before removing the lid clamp, tri-clamp tting, or
any accessory it is required to rst release any pressure from
your BrewBuilt Fermenter.
Releasing pressure from your X1 can be achieved by loosening
the cap on the Pressure Relief Valve (PRV) that is built into
the lid. Slowly loosen the cap counterclockwise until you hear
the release of any CO2exiting the PRV. When the release has
stopped, continue to slowly unthread the cap. At any point
while loosening the cap if you hear additional CO2being
released, stop and wait. When no additional CO2is being
released slowly remove the cap completely to ensure that all
pressure has been removed from the fermenter. Only then is
it safe to begin removing ttings or the lid clamp.
TRANSFERRING CLEAR BEER TO KEG
UNDER PRESSURE
Push your nished beer into a keg using CO2so it never
becomes exposed to oxygen—it’s simple and fast using the
Pressure Pack. Thanks to the Clear Float stainless steel oating
pick up, you’ll be transferring the clearest beer from the top
down.
Once your beer is ready to be packaged into a keg, follow
these instructions. NOTE: you will need a Corny Keg Ball
Lock Jumper Line (beverage tubing with bev-out ball lock
connectors at both ends).
1. Fill your keg with sanitizer solution. Push the sanitizer out
using CO2. Open the keg pressure relief valve to let CO2
exit the keg during lling.
2. Attach your CO2tank to the gas-in post on your Pressure
Pack lid and set it to around 10–12 psi.
3. Attach the Corny Keg Ball Lock Jumper Line to the bev-out
post on your Pressure Pack lid.
4. Once you hook up the bev-out to the keg, beer will
start owing from the pressurized X1 Unitank into the
unpressurized keg.
5. Once your beer has transferred, unhook the bev-out and
gas-in connectors. Pressurize your keg.
BREWBUILT.COM PAGE 7

6. Be sure to release any pressure from inside your X1 before opening it for cleaning.
FERMENTING UNDER PRESSURE
WARNING: Follow all special warnings and instructions that come with the optional BrewBuilt Pressure Fermentation Kit. DO
NOT pressure ferment without using the optional Pressure Fermentation Kit.
If you wish to ferment under pressure, or capture CO2at the end of fermentation, you must use the optional BrewBuilt
Pressure Fermentation Hardware Kit. The optional hardware kit comes with a commercial-grade pressure relief that connects
to the 1.5" TC port on the lid. It also comes with an adjustable spunding valve. The spunding valve allows you to set a safe
pressure to ferment. With the Pressure Fermentation Kit installed, there are three safety relief valves: the standard pressure
relief valve welded into the lid, the commercial 1.5" TC relief valve, and the PRV on the Spunding Valve. The Fermentation kit
includes a no-foam krausen reducer, CellarScience®Foam-Axe to reduce the chance that krausen could enter any of the PRVs.
Connecting the Control Panel
WARNING: Do not use if there is any damage to the wiring.
WARNING: Always use a GFCI to power your control panel.
The BrewBuilt Control Panel has an included InkBird heating and
cooling controller and a 500 watt 12V DC power supply. It has
a tab welded to the top four screws and can be hung on a wall
or one of our optional stainless controller stands (CONP735 &
CONP736). On the bottom of the box there are 4 sockets. One
socket is for the power cord and it contains the power switch and
a fuse. There is a 3-pin connector for the heating element and two
2-pin connectors for the cooling. Depending on what system you
have you may only need one cooling connector.
The power connectors are sealed with a water-tight cap. It is best to leave the caps in place when not in use. The connectors
are polarity sensitive and will only go in one way. Once aligned correctly they push in and rotate clockwise 1/4 turn to lock.
DO NOT spray or immerse the control panel. To clean wipe with a damp cloth when unplugged.
COOLING
ON
POWER UP
SET DOWN
HEATING
ON
FACTORY SETTINGS:
• tS = Set Point = 68
• CF = Celsius/Fahrenheit = F
• CA = Calibration Oset = 0
• Pt = Compressor Delay = 0
• dS = Dierential = 1
To change the settings hold the S button down till tS is showing (about 5 seconds). Using the up and down arrows nd the
setting you wish to check or change and press S. Set the new value with the up and down buttons and press S when nished.
When all settings are correct press the power button to return to normal operation.
NOTE: Changing from Celsius to Fahrenheit resets the other settings.
To set the Calibration oset, place the temperature sensor in a glass of ice water and stir till the reading is stable. Subtract 32
from the reading and change the sign. If it reads 34, subtract 32 to get 2, change the sign, and set the oset to -2. This allows
for changes in the resistance of the probe and connections.
Setting Your Temperatures
The controller in your control panel comes programmed
with a default setting of 68F, the most common
fermentation temperature for ales. To change the
temperature setting, follow these directions:
POWER
SWITCH
FUSE
POWER
CORD HEATER COOLING
PAGE 8 BREWBUILT.COM
Table of contents
Other BrewBuilt Brewing System manuals
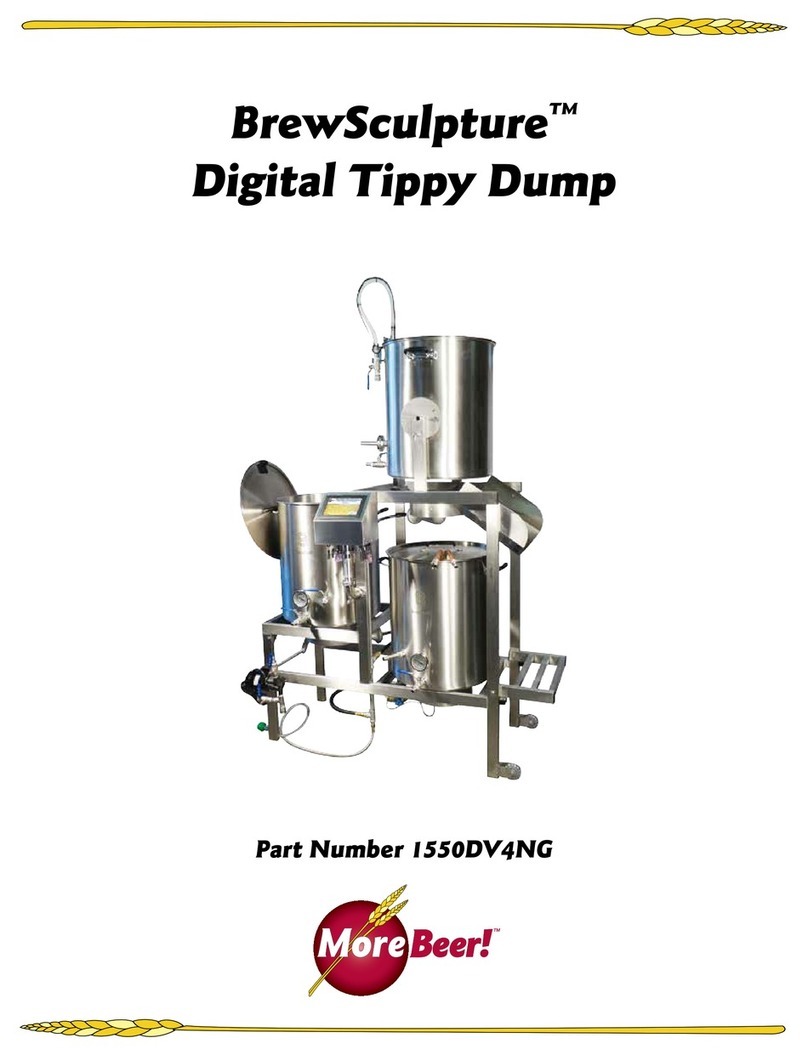
BrewBuilt
BrewBuilt BrewSculpture User manual
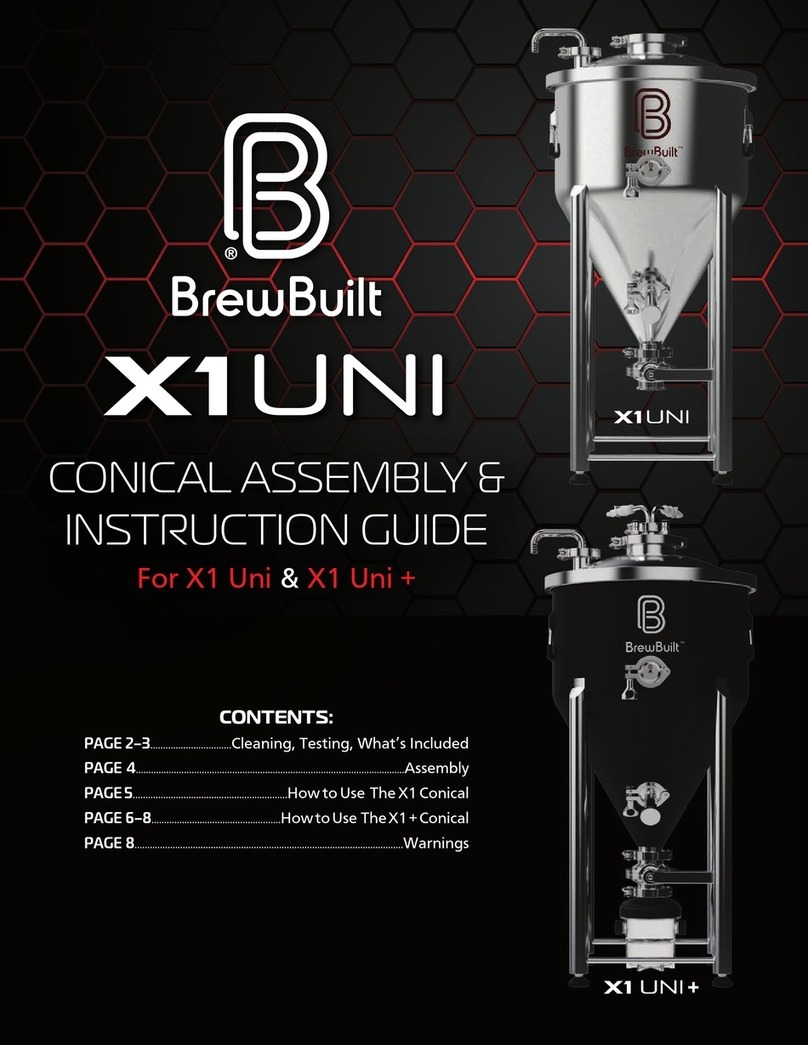
BrewBuilt
BrewBuilt X1 Uni User manual
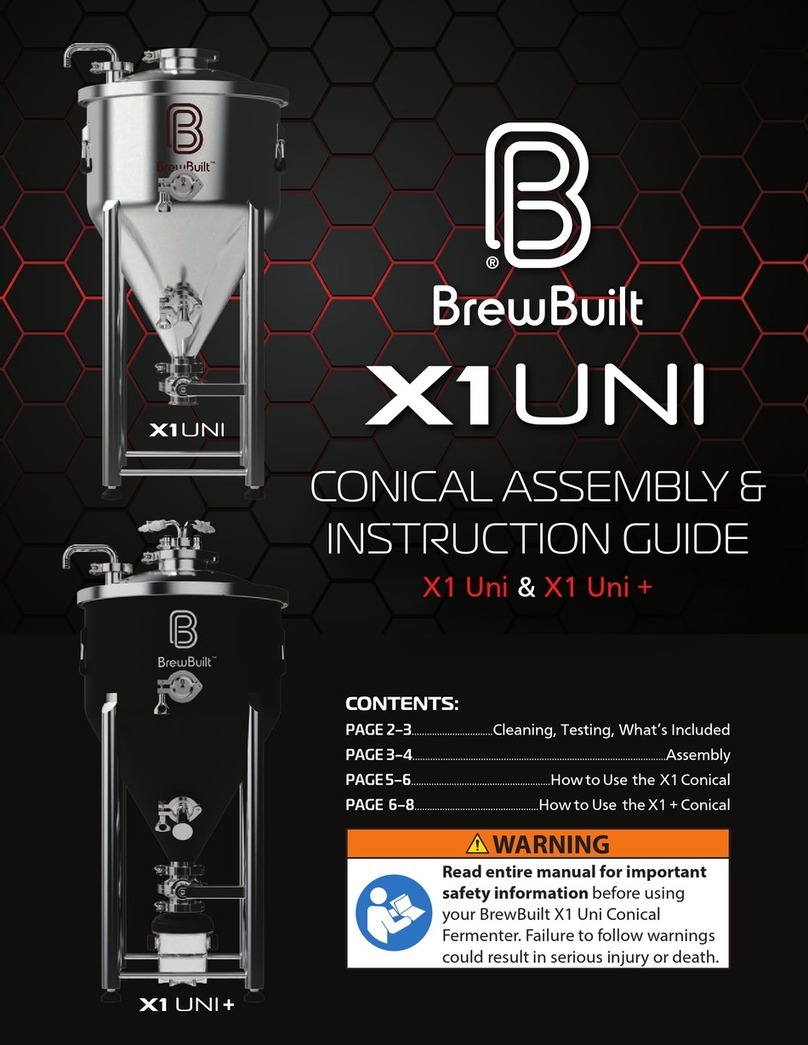
BrewBuilt
BrewBuilt X1 UNI User manual
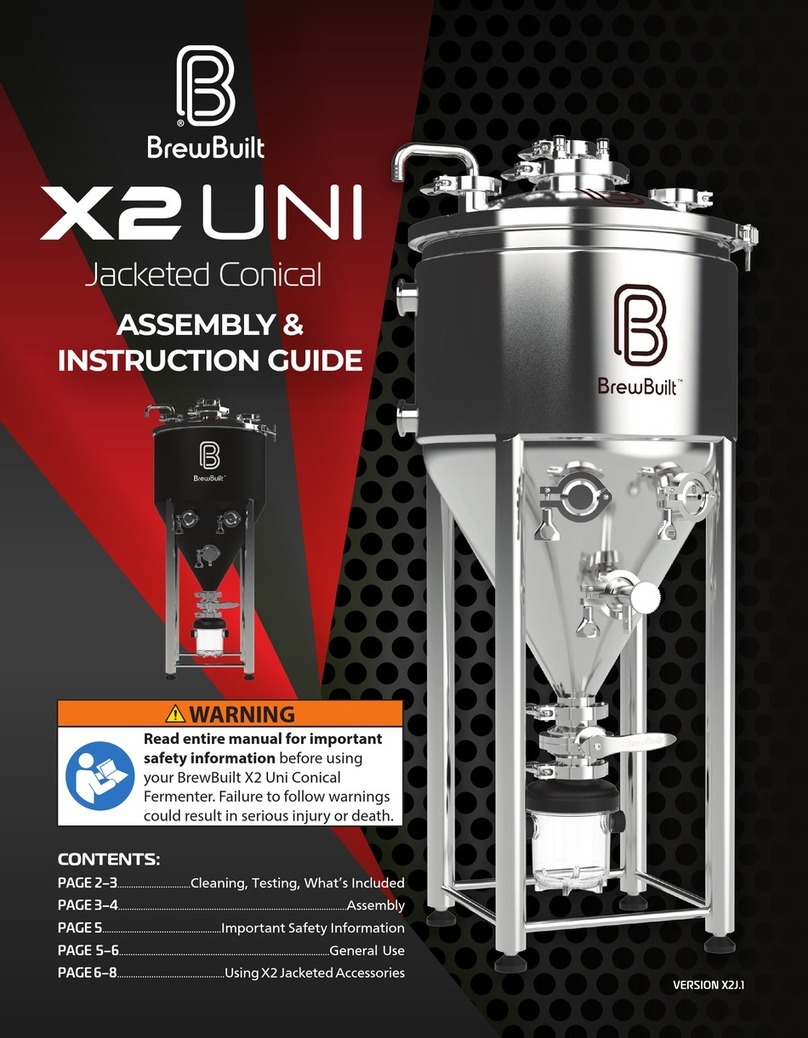
BrewBuilt
BrewBuilt X2 UNI User manual
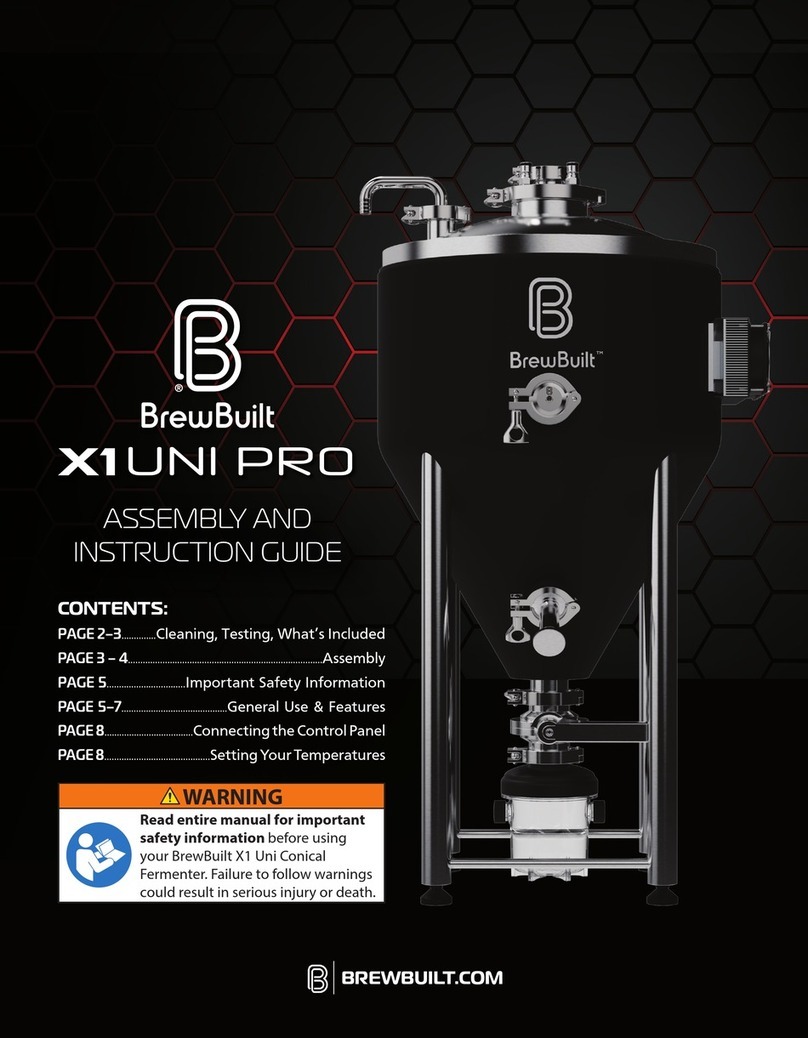
BrewBuilt
BrewBuilt X1 UNI PRO User manual
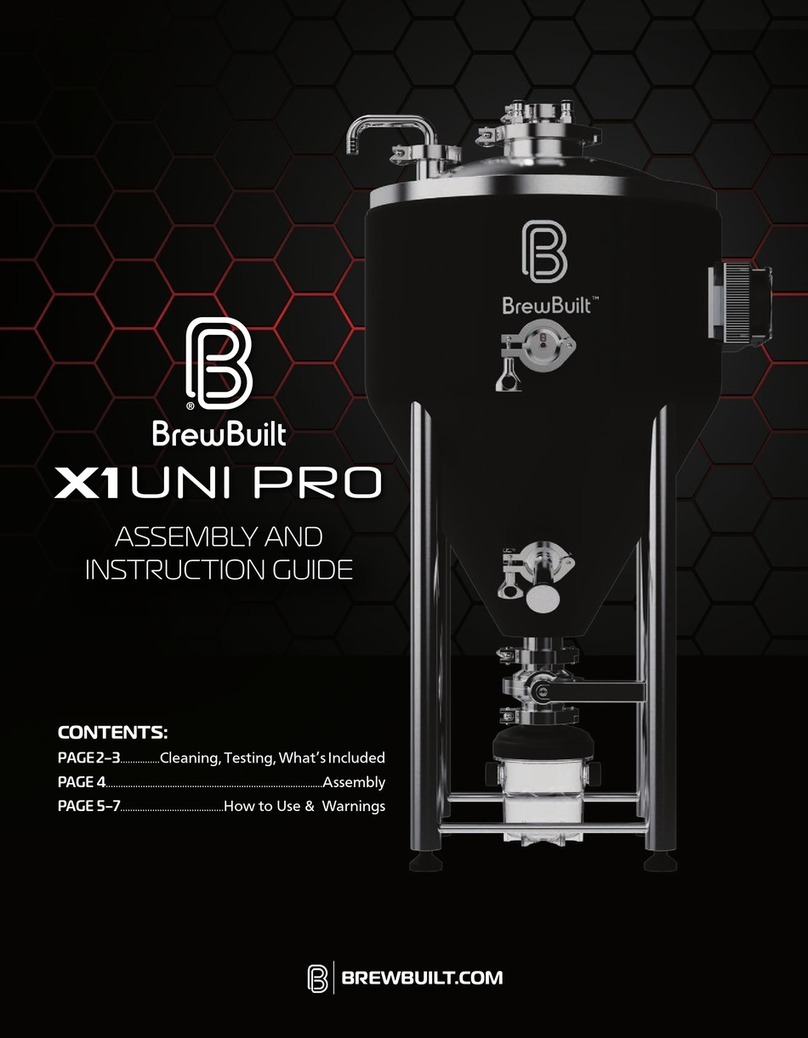
BrewBuilt
BrewBuilt X1 Uni Pro User manual
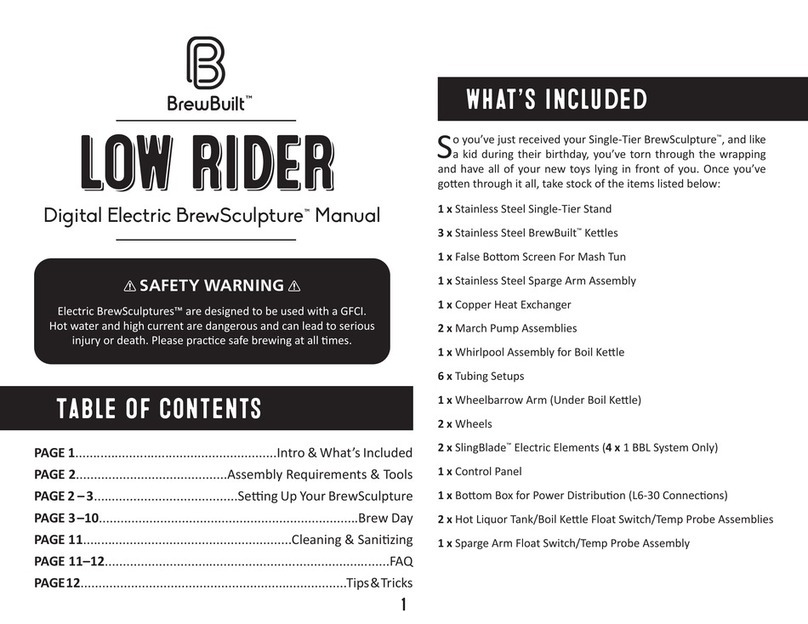
BrewBuilt
BrewBuilt BrewSculpture LOW RIDER User manual
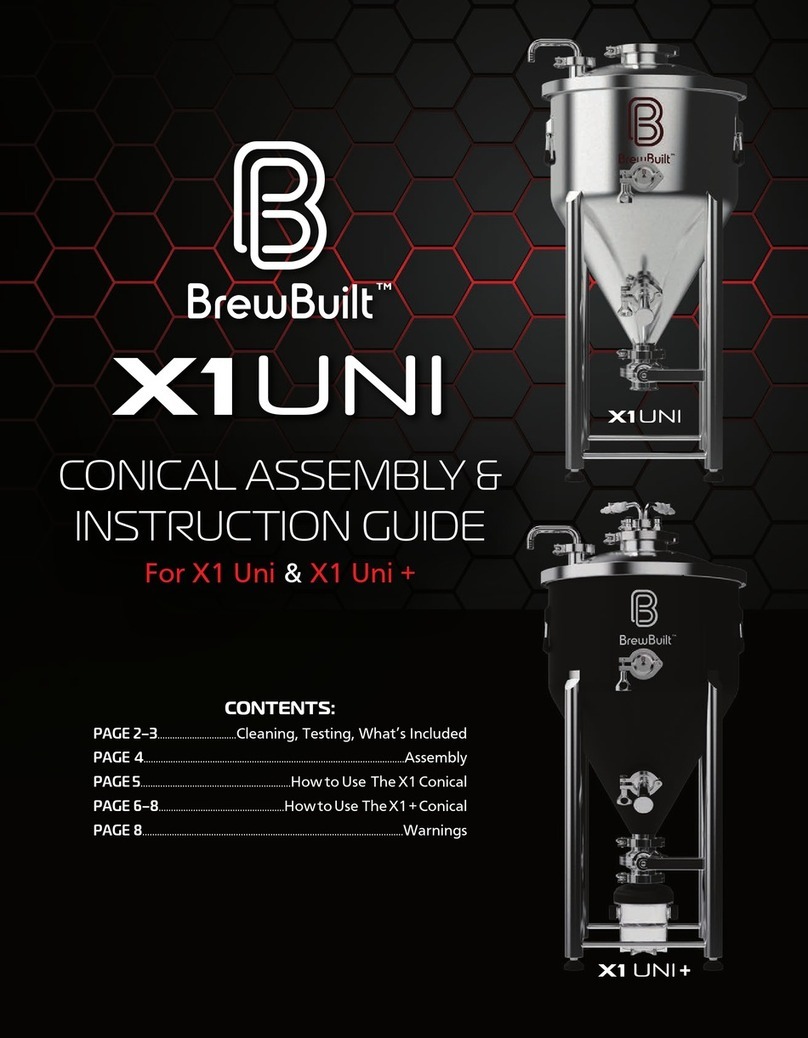
BrewBuilt
BrewBuilt X1 UNI User manual
Popular Brewing System manuals by other brands
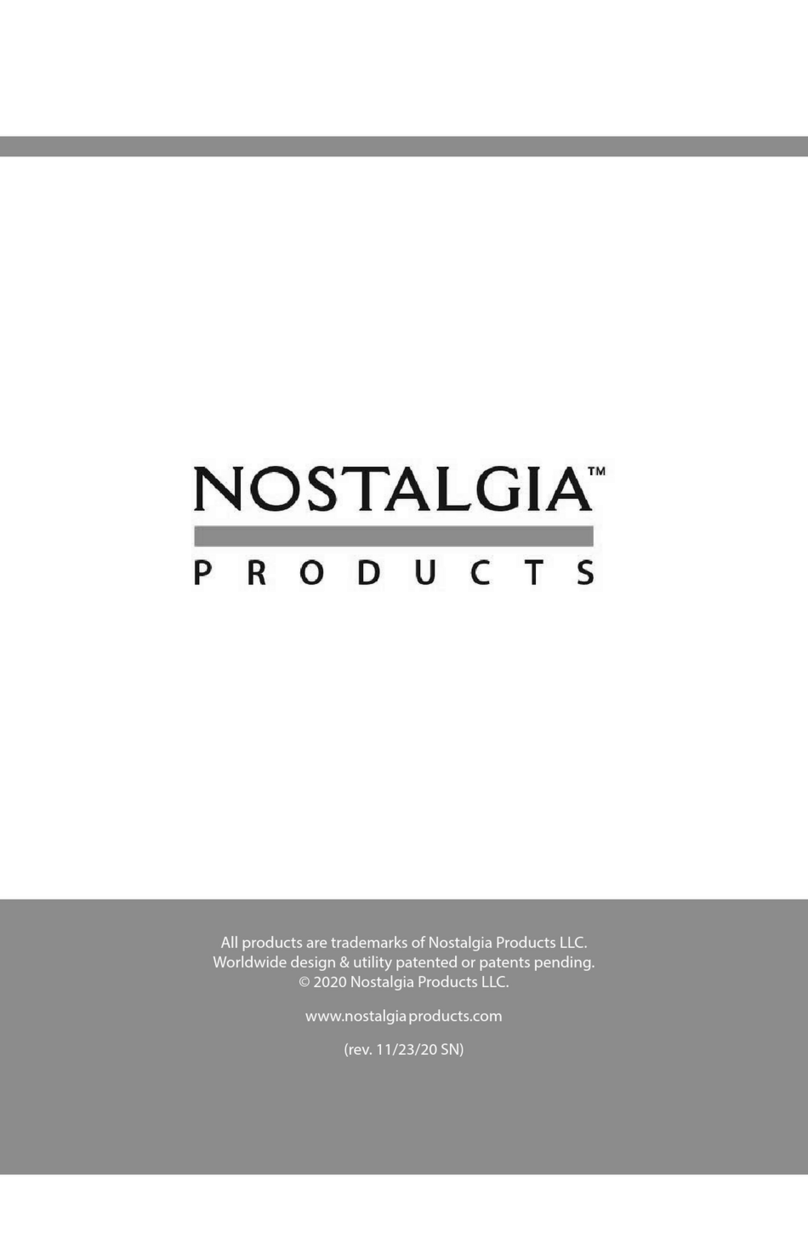
Nostalgia Electrics
Nostalgia Electrics CLITPLS3AQ instruction manual
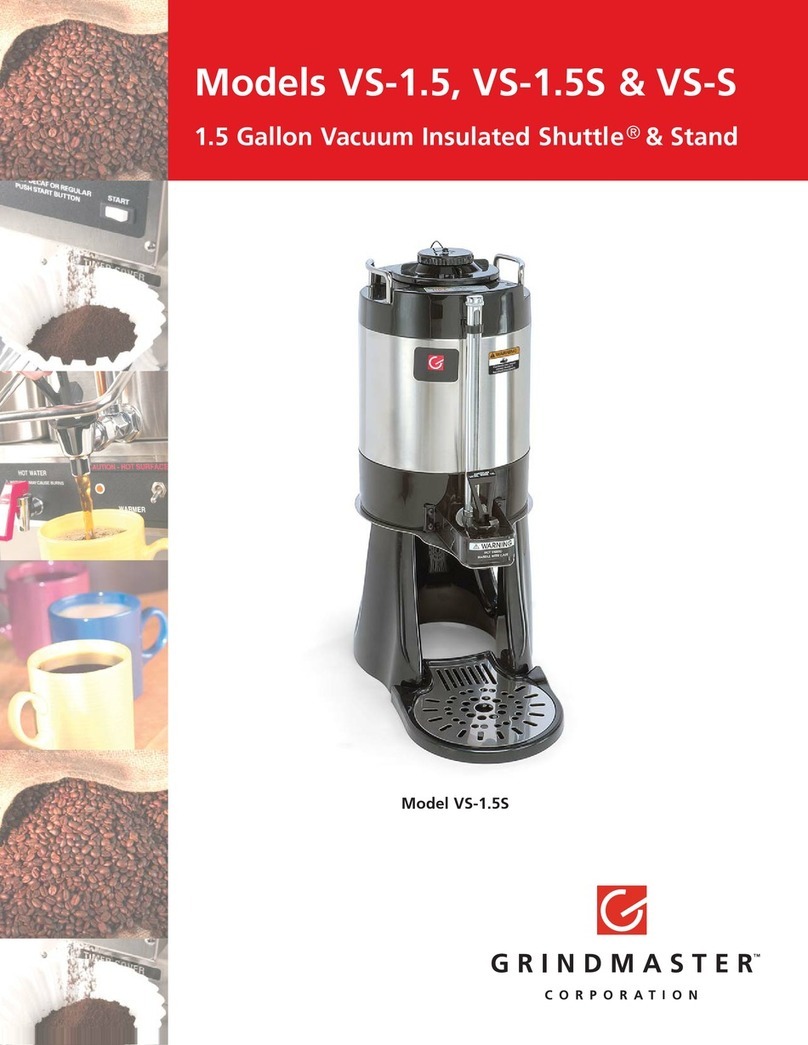
Grindmaster
Grindmaster VS-1.5 Specification sheet
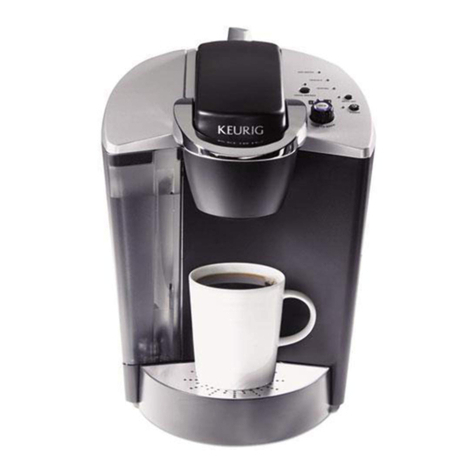
Keurig
Keurig K-CUP K140 Operator's manual

Keurig
Keurig Custom quick start guide
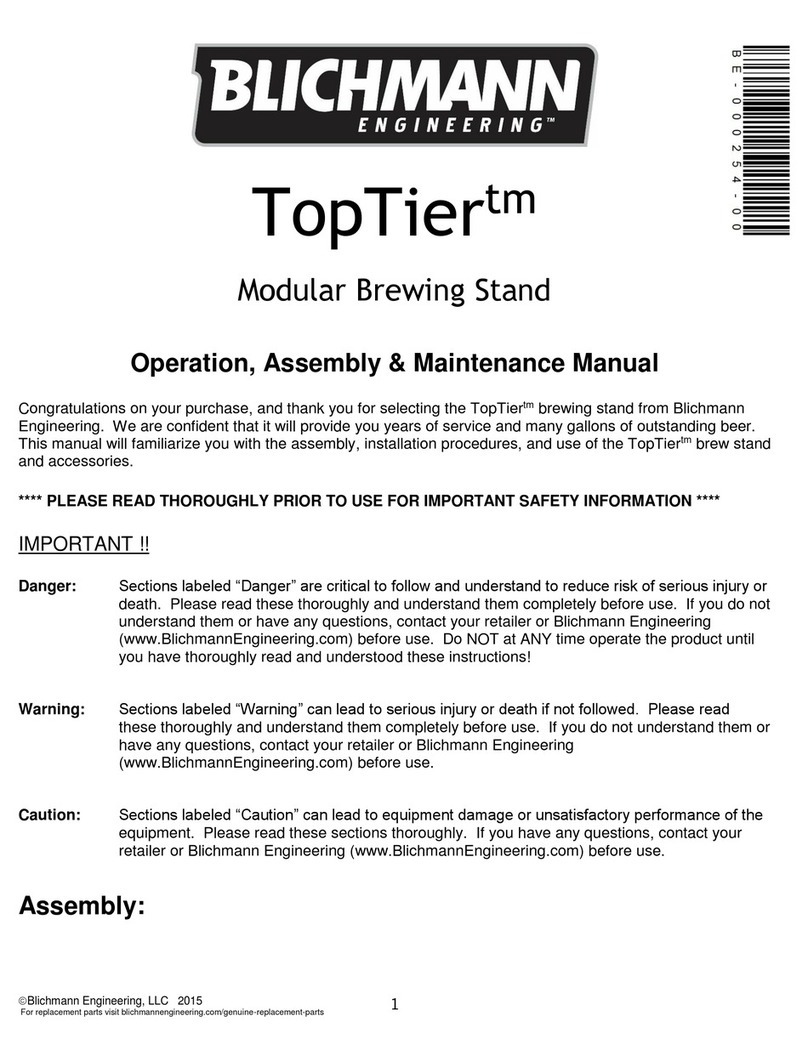
Blichmann
Blichmann TopTier Maintenance manual
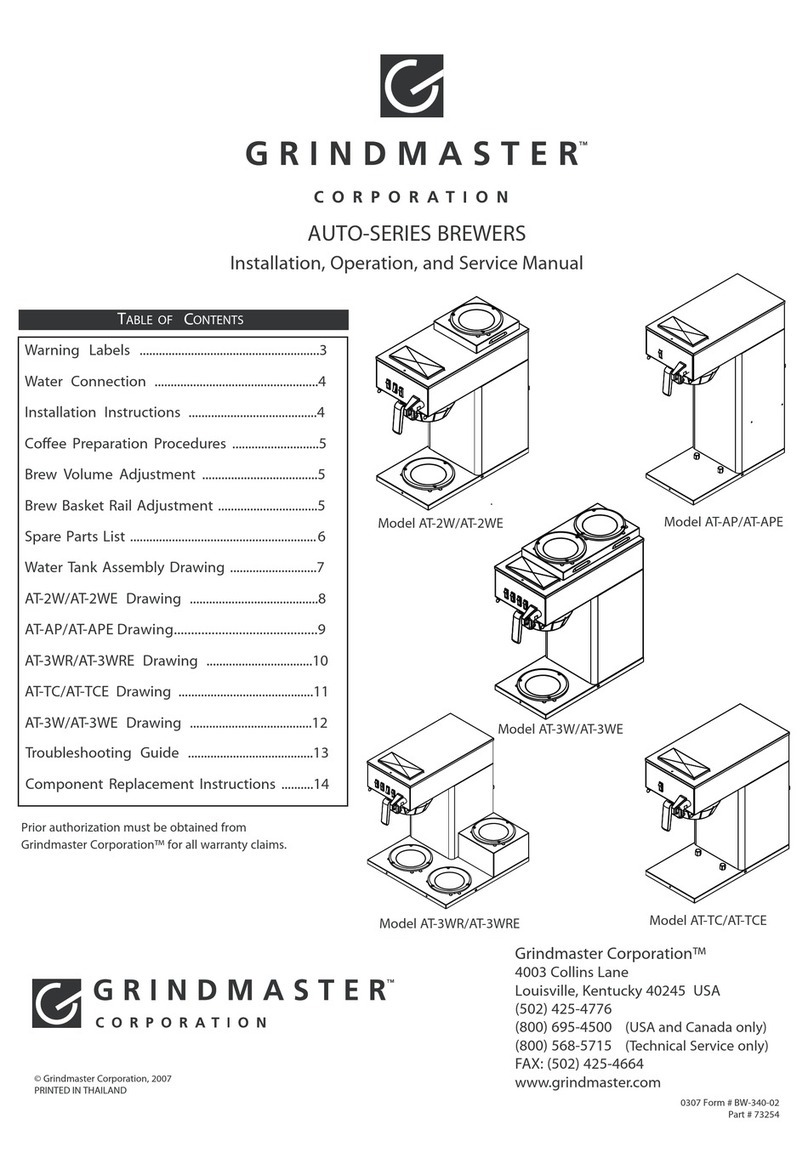
Grindmaster
Grindmaster AUTO Series Installation, operation and service manual