BUSCH R 5 series User manual

Get technical data,
instruction manuals,
service kits
Pump Control Instructions
R5
with FUJI Variable Frequency Drive
R5 RA/RC 1000-1600 B
0870239468/-_en / Original instructions / Modifications reserved 16/09/2021

Table of Contents
2 / 52 Pump Control Instructions R5 RA_RC 1000-1600 B with FUJI VFD_EN_en
Table of Contents
1 Safety .......................................................................................................................................4
2 Introduction..............................................................................................................................5
3 Parameter Kit Description.........................................................................................................6
3.1 Application....................................................................................................................... 6
3.2 Scope of Delivery ............................................................................................................. 6
4 Parameter Kit Installation .........................................................................................................6
4.1 PC-Software Installation................................................................................................... 6
4.2 USB Driver Installation...................................................................................................... 6
4.3 Computer Connection...................................................................................................... 7
5 Commissioning.........................................................................................................................8
5.1 Operate the Keypad......................................................................................................... 8
5.1.1 Keypad Overview.................................................................................................. 8
5.1.2 Navigation and Input............................................................................................. 8
5.1.3 Overview of VFD Modes....................................................................................... 9
5.1.4 Programming Mode ..............................................................................................11
5.1.5 Monitoring Mode.................................................................................................. 11
5.2 Run the Machine.............................................................................................................. 12
6 Custom Parametrisation ...........................................................................................................12
6.1 Machine Start / Stop ........................................................................................................ 13
6.1.1 Description ............................................................................................................ 13
6.1.2 Local or Remote Start / Stop ................................................................................. 13
6.2 Speed Control via Digital or Analog Inputs ....................................................................... 13
6.2.1 Description ............................................................................................................ 13
6.2.2 Set the Target Speed Value ................................................................................... 13
6.3 Pressure Control............................................................................................................... 14
6.3.1 Description ............................................................................................................ 14
6.3.2 Set the Target Pressure Value (SV) ........................................................................ 14
6.3.3 Change the Pressure Control Parameters............................................................... 15
6.4 Save Parameters............................................................................................................... 18
6.5 Reload Factory Settings .................................................................................................... 19
7 I/O Description.........................................................................................................................21
7.1 Overview I/O Connections .............................................................................................. 21
7.1.1 Analog Input Terminals .........................................................................................22
7.1.2 Digital Input Terminals .......................................................................................... 25
7.1.3 Analog Output Terminals ......................................................................................28
7.1.4 Transistor Output Terminals ..................................................................................29
7.1.5 Relay Output Terminals......................................................................................... 30
7.1.6 RS-485 Communications Port................................................................................ 31
7.2 Preventing Electromagnetic Interferences ......................................................................... 32
8 Troubleshooting .......................................................................................................................32
8.1 Alarm Mode..................................................................................................................... 32
8.2 LED Indicators .................................................................................................................. 33
8.3 Alarm Mode Display......................................................................................................... 33
8.4 Pump Safety Alarm “OH2”.............................................................................................. 34
8.5 Alarm Relay Output ......................................................................................................... 35
8.6 List of Errors ..................................................................................................................... 36
8.7 Releasing the Alarm and Switching to Running Mode ...................................................... 48
8.8 Displaying the Alarm History ............................................................................................ 49

Table of Contents
Pump Control Instructions R5 RA_RC 1000-1600 B with FUJI VFD_EN_en 3
8.9 Displaying the Status of the Inverter at the Time of Alarm................................................ 49
8.9.1 Confirm Alarm History........................................................................................... 49

1 | Safety
4 / 52 Pump Control Instructions R5 RA_RC 1000-1600 B with FUJI VFD_EN_en
1 Safety
These pump control instructions shall give further information concerning individual set-
ting or data analysis to experienced and trained users. Prior to handling the product, this
document should be read and understood. If anything needs to be clarified please con-
tact your Busch representative.
Read carefully before use and keep for future reference.
This document remains valid as long as the customer does not change anything on the
product.
The product is intended for industrial use. It shall be handled only by qualified personnel.
The product has been designed and manufactured according to state-of-the-art meth-
ods.
Nevertheless, residual risks may remain. This instruction manual highlights potential haz-
ards where appropriate. Safety notes and warning messages are tagged with one of the
keywords DANGER, WARNING, CAUTION and NOTICE as follows:
DANGER
... indicates an imminent dangerous situation that will result in death or serious injuries if
not prevented.
WARNING
... indicates a potentially dangerous situation that could result in death or serious injuries.
CAUTION
... indicates a potentially dangerous situation that could result in minor injuries.
NOTICE
... indicates a potentially dangerous situation that could result in damage to property.
NOTE
... indicates helpful tips and recommendations, as well as information for efficient and
trouble-free operation.

Introduction | 2
Pump Control Instructions R5 RA_RC 1000-1600 B with FUJI VFD_EN_en 5 / 52
2 Introduction
NOTE
Pump control instructions.
This document is delivered along with variable-frequency drive control device.
It only contains information about the variable-frequency drive parametrisation and con-
trol.
Please refer to the original instruction manual of the corresponding machine which con-
tent remains valid.

3 | Parameter Kit Description
6 / 52 Pump Control Instructions R5 RA_RC 1000-1600 B with FUJI VFD_EN_en
3 Parameter Kit Description
3.1 Application
The parameter kit allows a computer to be connected to the variable frequency drive.
The parameter kit is intended for:
– Parametrisation of the variable frequency drive
– Control (e.g. locking and releasing)
– Display of various process values
of the R5 RA/RC 1000-1600 B machines equipped with variable frequency drive.
This kit is optional, the variable frequency drive can also be configured using the front
panel keypad.
3.2 Scope of Delivery
Parameter kit - Kit number: 0987 241 383
Pos. Part Qty Part no.
1 Cable for PC 1 0987 241 385
2 USB Stick including PC-Software, USB driver and
Pump control instructions
1 0889 241 386
4 Parameter Kit Installation
4.1 PC-Software Installation
• Start the setup file of the PC-Software from the USB stick.
• Install the PC-Software on your computer.
• In case of trouble and for all information on the use and functionality of the PC-soft-
ware, please consult the "INR-SI47-2104b-E_FRENIC-Loader4_InstructionManual"
pdf documentation.
NOTE
MsgMgr USB Setup.exe
For a trouble-free installation, make sure you have executed and installed “MsgMgr
USB Setup.exe”.
4.2 USB Driver Installation
• Start the setup file of the USB driver from the USB stick.
• Install the USB driver on your computer.
• In case of trouble, please consult the "INR-SI47-2104b-E_FRENIC-Loader4_Instruc-
tionManual" pdf documentation.

Parameter Kit Installation | 4
Pump Control Instructions R5 RA_RC 1000-1600 B with FUJI VFD_EN_en 7 / 52
4.3 Computer Connection
NOTICE
Non-compatible variable frequency drive.
Risk of damage to the variable frequency drive!
• The remote control must only be operated with “FUJI AQUA” variable frequency
drive.
External Operation Measurement and Communication:
To connect a computer to the VFD:
• Remove the VFD front cover.
• Connect the computer to the USB port (mini B) via the cable included in the parame-
ter kit. The USB port (CN10*) is located on the upper right corner of the control print-
ed circuit board (control PCB).
• Open the inverter support software for Windows (FRENIC Loader). This allows to con-
figure function codes held in the inverter and manage data from the connected com-
puter.

5 | Commissioning
8 / 52 Pump Control Instructions R5 RA_RC 1000-1600 B with FUJI VFD_EN_en
5 Commissioning
5.1 Operate the Keypad
5.1.1 Keypad Overview
The keypad allows you to start and stop the machine, monitor the running status, specify
the function code data, and monitor I/O signal states, maintenance information, and
alarm information.
Position Description
1 Programming keys. They are used to perform various inverter operations.
2 Program key
3 RESET key
4 UP/DOWN/LEFT/RIGHT - arrow key
5 SET key
6 HELP key
7 STOP key
8 Run key (reverse)
9 Run key (forward)
10 LED indicators. They show the current running status of the inverter.
11 LCD monitor. It shows various information about the inverter according to
the operation modes.
5.1.2 Navigation and Input
Indication of LED Indicators:
LED Indicators Indications
STATUS
(Green)
Shows the inverter running state.
Flashing No run command input (Inverter stopped)
ON Run command input
WARNING
(Yellow)
Shows the light alarm state.
OFF No light alarm has occurred.
Flashing / ON A light alarm has occurred.

Commissioning | 5
Pump Control Instructions R5 RA_RC 1000-1600 B with FUJI VFD_EN_en 9 / 52
LED Indicators Indications
ALARM
(Red)
Shows the alarm state (heavy alarm).
OFF No heavy alarm has occurred.
Flashing A heavy alarm has occurred.
Overview of Keypad Functions:
Keys Functions
PRG
(Program)
The PRG key switches the operation modes between Running
mode/Alarm mode and Programming mode.
RESET
The RESET key works as follows according to the operation
modes.
In Running mode: This key cancels the screen transition.
In Programming
mode:
This key resets the alarm states and switch-
es to Programming mode.
In Alarm mode: This key discards the settings being config-
ured and cancels the screen transition.
UP/DOWN
The UP/DOWN keys work as follows according to the operation
modes.
In Running mode: These keys switch to the digital reference
frequency and PID command modification
screen (when commands from the keypad
are enabled).
In Programming
mode:
These keys display multiple alarms and
alarm history.
In Alarm mode: These keys select menu items, change data,
and scroll the screen.
LEFT/RIGHT These keys move the cursor to the digit of data to be modified,
shift the setting item and switch the screen.
SET
The SET key works as follows according to the operation modes.
In Running mode: Pressing this key switches to the selection
screen of the LCD monitor content.
In Programming
mode:
Pressing this key switches to the alarm de-
tailed information screen.
In Alarm mode: Pressing this key established the selected
items and data being changed.
HELP
Pressing this key calls up the HELP screen according to the current
display state. Holding it down for 2 seconds toggles between the
remote and local modes.
FWD
(Forward)
Pressing this key starts running the motor in the forward rotation
(when a run command from the keypad is enabled).
REV
(Reverse)
Pressing this key starts running the motor in the reverse rotation
(when a run command from the keypad is enabled).
STOP Pressing this key stops the motor (when a run command from the
keypad is enabled or the STOP key priority is selected).
5.1.3 Overview of VFD Modes
•Running mode: After powered ON, the inverter automatically enters this mode. This
mode allows to specify the frequency set point in speed control mode, the pressure set
point in pressure control mode and start/stop the machine with the FWD / REV /
STOP keys. It is also possible to monitor the running status in real time.

5 | Commissioning
10 / 52 Pump Control Instructions R5 RA_RC 1000-1600 B with FUJI VFD_EN_en
•Programming mode: This mode allows to configure function code data and check a
variety of information relating to the inverter status and maintenance.
•Alarm mode: If an alarm condition arises, the inverter automatically enters Alarm
mode. In this mode, you can view the corresponding alarm code (indicating the cause
of the alarm condition) and its related information on the LCD monitor.
The figure below shows the status transition of the inverter between these three opera-
tion modes. If the inverter is turned ON, it automatically enters Running mode, making it
possible to start or stop the motor.

Commissioning | 5
Pump Control Instructions R5 RA_RC 1000-1600 B with FUJI VFD_EN_en 11 / 52
5.1.4 Programming Mode
Programming mode allows the setting and confirmation of function codes, and monitor-
ing of maintenance-related and input/output (I/O) terminal information, as well as other
functions. A menu format is used to enable simple function selection. The menu transi-
tion for programming mode is described as follows:
•Setting up function codes
PRG > 2 (Function Code) > 1 (Date Set)
This section explains how to set function code data.
The example below shows how to change a F (fundamental) parameter.
RESET key = Return to previous screen
PRG key = Return to running mode
• 1: Press the PRG key while the running mode screen is displayed.
• 2: Use the UP/DOWN keys to select [2. Function Code] and confirm with the SET
key.
• 3: Use the UP/DOWN keys to select [1. Data Set] and confirm with the SET key.
• 4: Use the UP/DOWN keys to select the function code you wish to set (in this
case, F: Fundamental).
5.1.5 Monitoring Mode
In Running mode, the following items listed below can be monitored. Immediately after
the inverter is turned on. Press the SET key to enter Monitoring mode and switch be-
tween monitor items.
Monitor names Sub monitor Unit Meaning of displayed value Function
code
Output frequen-
cy 1 (before slip
compensation)
Fout1 Hz Frequency actually being output 1
Output current Iout A Current output from the inverter
in RMS
13
Output voltage Vout V Voltage output from the invert-
er in RMS
14
Calculated
torque
TRQ % Motor output torque in %
(Calculated value)
18
Input power PWR kW Input power to the inverter 19
Load factor LOF % Load factor of the motor in %
as the rated output being at
100%
25

6 | Custom Parametrisation
12 / 52 Pump Control Instructions R5 RA_RC 1000-1600 B with FUJI VFD_EN_en
Monitor names Sub monitor Unit Meaning of displayed value Function
code
Motor output MPW kW Motor output in kW 26
Input watt-hour Wh – Input watt-hour (kWh) / 100 35
PID control 1
command
SV1 – PID control 1 command and its
feedback converted into physi-
cal quantities of the object to be
controlled.
53
PID control 1
feedback
PV1 – 54
5.2 Run the Machine
The machine is configured to run in speed control mode at maximum rotational speed,
and to be remotely started/stopped with a digital signal (factory setting):
Machine type Motor frequency
R5 RA/RC 1000 B 60 Hz
R5 RA/RC 1600 B 60 Hz
• Refer to the Installation and Retrofit instructions of the corresponding machine for the
complete commissioning procedure and for the electrical connection of the machine.
• Maximum permissible number of starts by using the digital signal: unlimited
As soon as the machine is operated under normal operating conditions:
• Measure the mains current or read it via PC-Software or controller.
For setting of the speed target, operation of the machine in pressure control mode or
start/stop of the machine locally via the built-in keypad, refer to chapter Custom Para-
metrisation [►12].
NOTICE
Frequent starts and stops by connecting and disconnecting from the power supply.
Risk of damage to the machine!
Starting the machine by connecting and disconnecting the power supply is permitted
max. 2x per minute. Between disconnecting and connecting at least 10 seconds must
have been passed. If the process requires more frequent starts/stops of the machine:
• Use the digital start signal.
6 Custom Parametrisation
DANGER
Maintenance work without disconnecting the variable-frequency drive.
Risk of electrical shock.
• Disconnect and isolate the variable-frequency drive before attempting any work on it.
High voltages are present at the terminals and within the variable-frequency drive for
up to 10 minutes after disconnection of the electrical supply.
• Always ensure by using a suitable multimeter that no voltage is present on any drive
power terminals prior to commencing any work.

Custom Parametrisation | 6
Pump Control Instructions R5 RA_RC 1000-1600 B with FUJI VFD_EN_en 13 / 52
DANGER
Live wires. Carry out any work on the variable-frequency drive and motor.
Risk of electrical shock!
• Electrical installation work must only be executed by qualified personnel.
NOTICE
Change factory settings.
Risk of damage to the machine!
If wrong or not allowed parameters have been set, Busch disclaims any liability for dam-
age to the machine.
• Change only the allowed parameters described in the chapter Parameter Description.
6.1 Machine Start / Stop
6.1.1 Description
It is possible to start / stop the machine remotely using a digital input or locally from the
keypad.
6.1.2 Local or Remote Start / Stop
The function code F02 selects the source that specifies the Start / Stop method, as de-
scribed in the table below:
Data for F02 Description
1 External signal (Digital input
terminal commands)
Enable terminal command FWD to run and
stop the machine.
2 Keypad (Forward rotation) Enable FWD / STOP keys to run and stop
the machine.
6.2 Speed Control via Digital or Analog Inputs
6.2.1 Description
In speed control mode, the machine runs at a fixed speed.
NOTE
In speed control mode
To display the actual speed value in Hz in the main screen:
• Go to monitoring mode.
• Select parameter 1.Fout (Sync), see Monitoring Mode [►11].
6.2.2 Set the Target Speed Value
The following function codes specify 4 frequencies to apply when switching frequencies
by turning Digital input commands ON or OFF selectively, as listed below.

6 | Custom Parametrisation
14 / 52 Pump Control Instructions R5 RA_RC 1000-1600 B with FUJI VFD_EN_en
Selected Frequency Command Speed DI 2
Digital Input X4
Speed DI 1
Digital Input X3
Analog Input 0 0
C05 0 1
C06 1 0
C07 1 1
C05/06/07 Frequency modes
C05 = XX Hz / C06 = YY Hz / C07 = ZZ Hz
XX = Set the frequency, it can not be lower than minimum speed or higher than maxi-
mum speed.
NOTE
For all information about the operating speed range of the machine, refer to the Installa-
tion and Retrofit instructions of the respective pump.
6.3 Pressure Control
6.3.1 Description
In pressure control mode, the target pressure value (SV*) and actual pressure value
(PV**) are compared and the system then regulates to reach the pressure target.
*SV = Set Value / **PV = Process Value
NOTE
In pressure control mode
To display the actual pressure value in mbar in the main screen:
• Go to monitoring mode.
• Select parameter 54.PV1 PID Control 1 feedback [mbar], see Monitoring Mode
[►11].
6.3.2 Set the Target Pressure Value (SV)
• In running mode, press the UP/DOWN key to display the PID process command. The
PID process command corresponds to the target Pressure Value for the machine in
mbar. The lowest digit and its decimal point blink on the LCD monitor.
• To change the PID process command, press the UP/DOWN key again. The new set-
ting can be saved into the inverter's internal memory.

Custom Parametrisation | 6
Pump Control Instructions R5 RA_RC 1000-1600 B with FUJI VFD_EN_en 15 / 52
NOTE
The target pressure value will be saved either automatically by turning the main power
OFF or only by pressing the SET key.
6.3.3 Change the Pressure Control Parameters
This menu gives access to the parameters of the pressure regulation (used to control the
machine in pressure control mode):
• P = Proportional gain
• I = Integral time
• D = Differential time
The modification of the PID parameters is possible, in order to adjust the reactivity / sta-
bility of the machine and fine tune the pressure control to each application and each pro-
cess requirement.
P Proportional gain
J110 specifies the gain for the PID processor.
– Data setting range: 0.000 to 30.000 (times)
P (Proportional) action
An operation in which the MV (manipulated value: output frequency) is proportional to
the deviation is called P action, which outputs the MV in proportion to deviation. How-
ever, the P action alone cannot eliminate deviation. Gain is data that determines the sys-
tem response level against the deviation in P action. An increase in gain speeds up re-
sponse, but an excessive gain may oscillate the inverter output. A decrease in gain delays
response, but it stabilizes the inverter output.
I Integral time
J111 specifies the integral time for the PID processor.
– Data setting range: 0.0 to 3600.0 (s)
0.0 means that the integral component is ineffective.
I (Integral) action
An operation in which the change rate of the MV (manipulated value: output frequency)
is proportional to the integral value of deviation is called I action, which outputs the MV
that integrates the deviation. Therefore, I action is effective in bringing the feedback
amount close to the commanded value. For the system whose deviation rapidly changes,
however, this action cannot make it react quickly.
The effectiveness of I action is expressed by integral time as parameter, that is J04 data.
The longer the integral time, the slower the response. The reaction to the external distur-
bance also becomes slow. The shorter the integral time, the faster the response. Setting
too short integral time, however, makes the inverter output tend to oscillate against the
external disturbance.

6 | Custom Parametrisation
16 / 52 Pump Control Instructions R5 RA_RC 1000-1600 B with FUJI VFD_EN_en
D Differential time
J112 specifies the differential time for the PID processor.
– Data setting range: 0.00 to 600.00 (s)
0.00 means that the differential component is ineffective.
D (Differential) action
An operation in which the MV (manipulated value: output frequency) is proportional to
the differential value of the deviation is called D action, which outputs the MV that dif-
ferentiates the deviation. D action makes the inverter quickly react to a rapid change of
deviation.
The effectiveness of D action is expressed by differential time as parameter, that is J05
data. Setting a long differential time will quickly suppress oscillation caused by P action
when a deviation occurs. Too long differential time makes the inverter output oscillation
more. Setting short differential time weakens the suppression effect when the deviation
occurs.
The combined uses of P, I, and D
The combined uses of P, I, and D actions are described below.
•(1) PI control
PI control, which is a combination of P and I actions, is generally used to minimize the
remaining deviation caused by P action. PI control always acts to minimize the deviation
even if a commanded value changes or external disturbance steadily occurs. However,
the longer the integral time, the slower the system response to quick-changed control. P
action can be used alone for loads with very large part of integral components.
•(2) PD control
Under PD control, the moment that a deviation occurs, the control rapidly generates
greater MV (manipulated value) than that generated by D action alone, to suppress the
deviation increase. When the deviation becomes small, the behavior of P action becomes
small. A load including the integral component in the controlled system may oscillate due
to the action of the integral component if P action alone is applied. In such a case, use
PD control to reduce the oscillation caused by P action, for keeping the system stable.
That is, PD control is applied to a system that does not contain any damping actions in
its process.

Custom Parametrisation | 6
Pump Control Instructions R5 RA_RC 1000-1600 B with FUJI VFD_EN_en 17 / 52
•(3) PID control
PID control is implemented by combining P action with the deviation suppression of I ac-
tion and the oscillation suppression of D action. PID control features minimal control de-
viation, high precision and high stability. In particular, PID control is effective to a system
that has a long response time to the occurrence of deviation.
Follow the procedure below to set data to PID control function codes.
It is highly recommended that you adjust the PID control value while monitoring the sys-
tem response waveform with an oscilloscope or equivalent. Repeat the following proce-
dure to determine the optimal solution for each system.
• Increase the data of function codes J110 (PID control P (Gain)) within the range
where the feedback signal does not oscillate.
• Decrease the data of function codes J111 (PID control I (Integral time)) within the
range where the feedback signal does not oscillate.
• Increase the data of J112 (PID control D (Differential time)) within the range where
the feedback signal does not oscillate.
Refining the system response waveforms is shown below.
1) Suppressing overshoot
Increase the data of function codes J111 (Integral time) and decrease that of J112 (Dif-
ferential time)
2) Quick stabilizing (moderate overshoot allowable)
Decrease the data of J110 (Gain) and increase that of J112 (Differential time)
3) Suppressing oscillation whose period is longer than the integral time specified by func-
tion codes J111
Increase the data of function codes J111 (Integral time)

6 | Custom Parametrisation
18 / 52 Pump Control Instructions R5 RA_RC 1000-1600 B with FUJI VFD_EN_en
6.4 Save Parameters
NOTE
As soon as a parameter is modified in the VFD interface, the new setting is automatically
saved and it is not possible to cancel the modification to go back to the previous setting.
Before making any change, backup the current parameters via PC-Software.
• Make sure that the machine is stopped.
• Connect the variable-frequency drive to the computer with the provided cable.
• Start the PC-Software previously installed, see PC-Software Installation.
• Select “Functions” (see figure below).
• Check communication
Position Description
1Functions
2Main menu. You can select all loader functions.
3Toolbar. You can select the primary loader functions.
4Status bar. The text that describes the selected function appears in this area.
It also displays the status of connection with the inverter in the lower right
box.
• Press “Read from the inverter” status into the status bar.

Custom Parametrisation | 6
Pump Control Instructions R5 RA_RC 1000-1600 B with FUJI VFD_EN_en 19 / 52
• Go to “File”, then click “Save As”.
• Save the file “.fnl” in your database in order to reload the initial or specific parameters
for future purposes.
6.5 Reload Factory Settings
• Make sure that the machine is not running.
• Connect the variable-frequency drive to the computer with the provided cable.
• Start the PC-Software previously installed, see PC-Software Installation.
• Select “Open” to load the file “.FNL” or “.FNC” from your parameter list.
• Click on “Write”.

6 | Custom Parametrisation
20 / 52 Pump Control Instructions R5 RA_RC 1000-1600 B with FUJI VFD_EN_en
• In the next window (“Select function code data write operation”), select “All function
code data” and click “OK”.
Other manuals for R 5 series
18
Table of contents
Other BUSCH Controllers manuals
Popular Controllers manuals by other brands
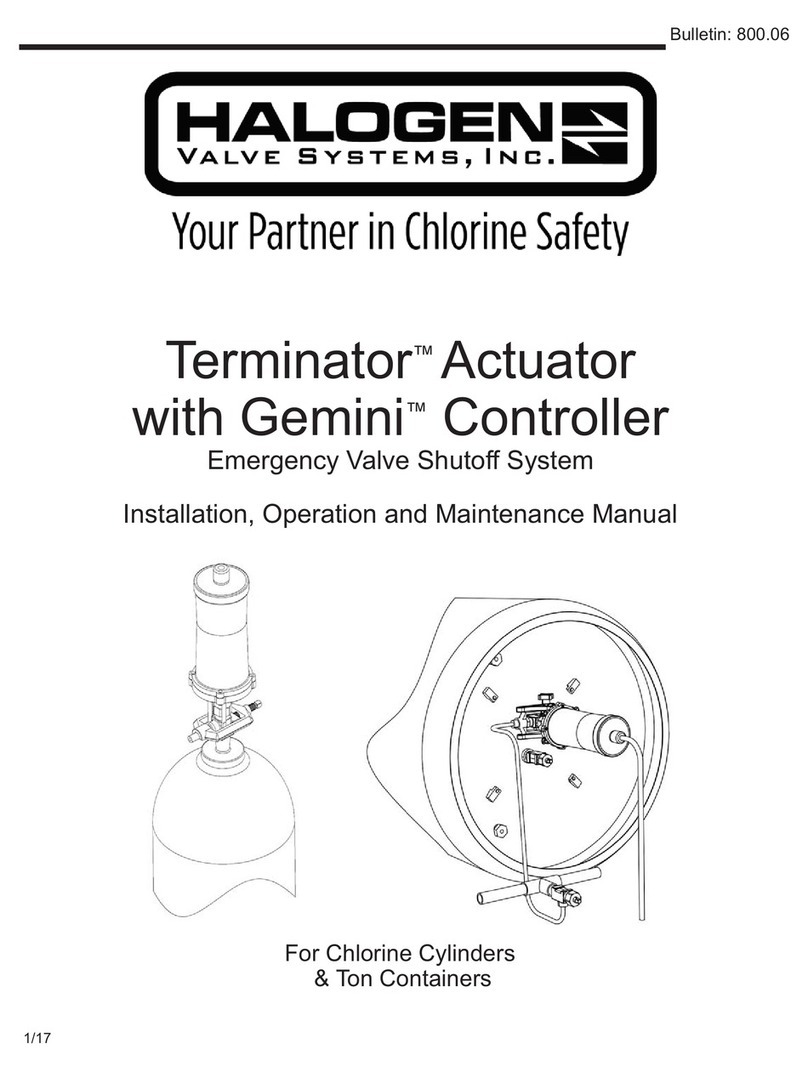
HALOGEN VALVE SYSTEMS
HALOGEN VALVE SYSTEMS Terminator Installation, operation and maintenance manual

MULTISPAN
MULTISPAN MC-1003 operating manual

Ambient
Ambient ACC 501 user manual
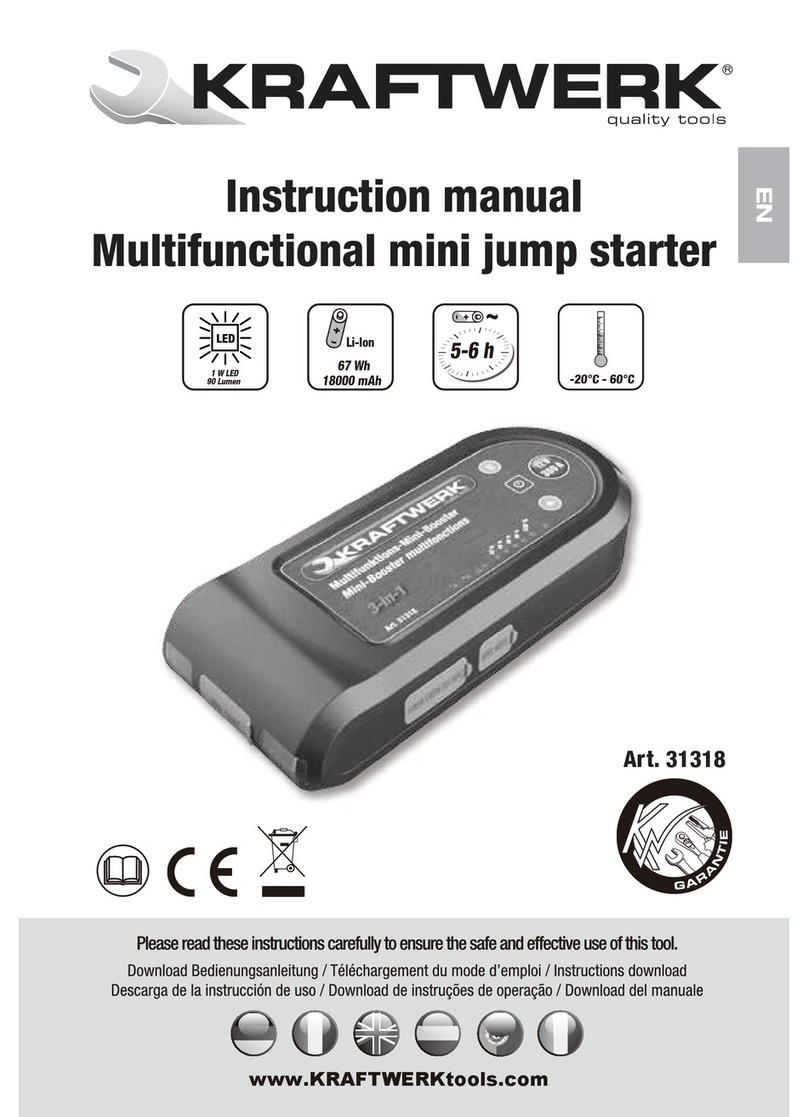
KRAFTWERK
KRAFTWERK 31318 instruction manual
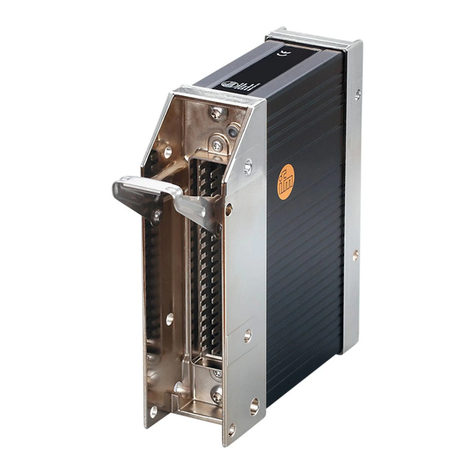
IFM Electronic
IFM Electronic SmartController CR2530 installation instructions
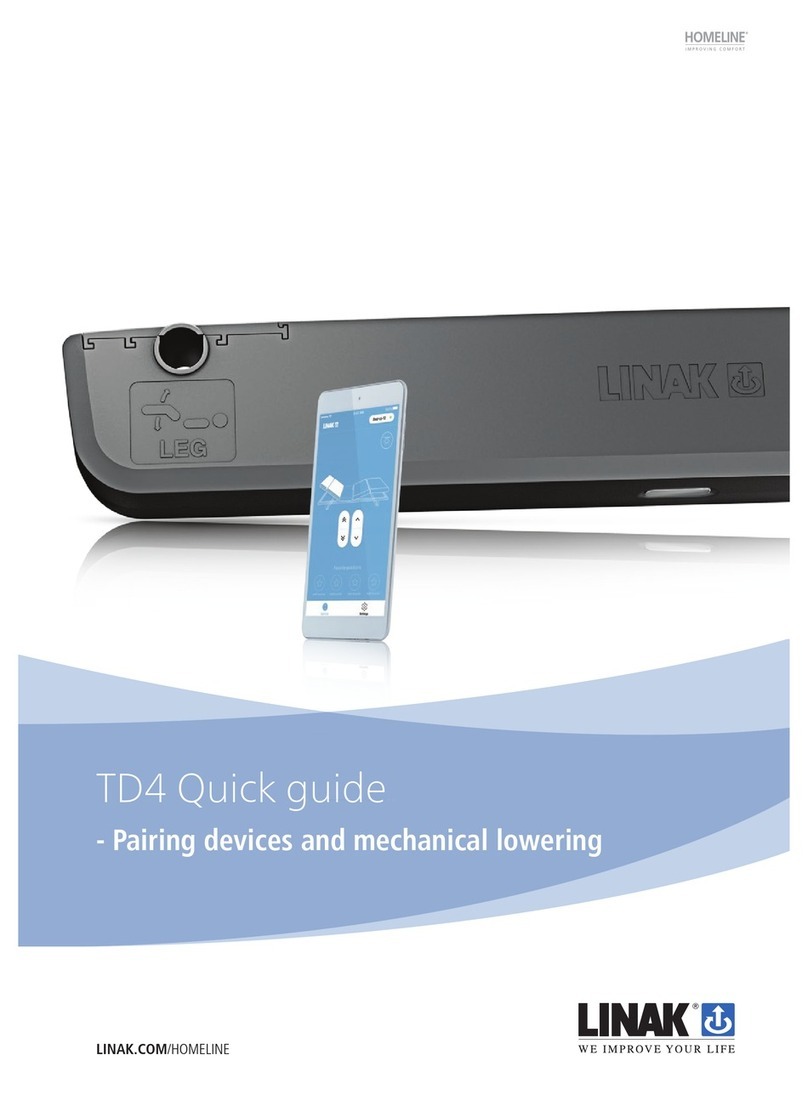
Linak
Linak TD4 quick guide