Carel uChiller UCHBP00000190 User manual

NO POWER
& SIGNAL
CABLES
TOGETHER
READ CAREFULLY IN THE TEXT!
µChiller
+0300053EN - ENG
Up to date version available on
www.carel.com
µChiller
Controller for Chiller / Heat Pump
USER MANUAL
ENG


3
ENG
µchiller +0300053EN rel. 2.2 - 14.12.2021
GENERAL WARNINGS
CAREL bases the development of its products on decades of experience
in HVAC/R, on continuous investments in technological innovations to
products, procedures and strict quality processes with in-circuit and fun-
ctional testing on 100% of its products, and on the most innovative pro-
duction technology available on the market. CAREL and its subsidiaries/
affiliates nonetheless cannot guarantee that all the aspects of the product
and the software included with the product respond to the requirements
of the final application, despite the product being developed according
to start- of- the- art techniques. The customer (manufacturer, developer
or installer of the final equipment) accepts all liability and risk relating to
the configuration of the product in order to reach the expected results
in relation to the specific final installation and/or equipment. CAREL may,
based on specific agreements, act as a consultant for the successful com-
missioning of the final unit/application, however in no case does it accept
liability for the correct operation of the final equipment/system. The CAREL
product is a state-of-the-art product, whose operation is specified in the
technical documentation supplied with the product or can be downloa-
ded, even prior to purchase, from the website www.carel.com. Each CAREL
product, in relation to its advanced level of technology, requires setup/
configuration/programming/commissioning to be able to operate in the
best possible way for the specific application. Failure to complete such
operations, which are required/indicated in the user manual, may cause
the final product to malfunction; CAREL accepts no liability in such cases.
Only qualified personnel may install or carry out technical service on the
product.
The customer must only use the product in the manner described in the
documentation relating to the product. In addition to observing any fur-
ther warnings described in this manual, the following warnings must be
heeded for all CAREL products:
• prevent the electronic circuits from getting wet. Rain, humidity and
all types of liquids or condensate contain corrosive minerals that may
damage the electronic circuits. In any case, the product should be used
or stored in environments that comply with the temperature and hu-
midity limits specified in the manual;
• do not install the device in particularly hot environments. Too high tem-
peratures may reduce the life of electronic devices, damage them and
deform or melt the plastic parts. In any case, the product should be used
or stored in environments that comply with the temperature and humi-
dity limits specified in the manual;
• do not attempt to open the device in any way other thandescribed in
the manual.
• do not drop, hit or shake the device, as the internal circuits and mecha-
nisms may be irreparably damaged.
• do not use corrosive chemicals, solvents or aggressive detergents to
clean the device.
• do not use the product for applications other than those specified in the
technical manual.
All of the above suggestions likewise apply to the controllers, serial cards,
programming keys or any other accessory in the CAREL product portfolio.
CAREL adopts a policy of continual development. Consequently, CAREL
reserves the right to make changes and improvements to any product
described in this document without prior warning. The technical speci-
fications shown in the manual may be changed without prior warning.
The liability of CAREL in relation to its products is specified in the CAREL
general contract conditions, available on the website www.carel.com and/
or by specific agreements with customers; specifically, to the extent whe-
re allowed by applicable legislation, in no case will CAREL, its employees
or subsidiaries/affiliates be liable for any lost earnings or sales, losses of
data and information, costs of replacement goods or services, damage to
things or people, downtime or any direct, indirect, incidental, actual, puni-
tive, exemplary, special or consequential damage of any kind whatsoever,
whether contractual, extra- contractual or due to negligence, or any other
liabilities deriving from the installation, use or impossibility to use the pro-
duct, even if CAREL or its subsidiaries/affiliates are warned of the possibility
of such damage.
DISPOSAL
Fig. 1 Fig. 2
INFORMATION FOR USERS ON THE CORRECT HANDLING OF WASTE
ELECTRICAL AND ELECTRONIC EQUIPMENT (WEEE)
The product is made up of metal parts and plastic parts. In reference to Eu-
ropean Union directive 2002/96/EC issued on 27 January 2003 and related
national legislation, please note that:
• WEEE cannot be disposed of as municipal waste and such waste must
be collected and disposed of separately;
• the public or private waste collection systems defined by local legisla-
tion must be used. In addition, the equipment can be returned to the
distributor at the end of its working life when buying new equipment;
• the equipment may contain hazardous substances: the improper use or
incorrect disposal of such may have negative effects on human health
and on the environment;
• the symbol (crossed- out wheeled bin) shown on the product or on the
packaging and on the instruction sheet indicates that the equipment
has been introduced onto the market after 13 August 2005 and that it
must be disposed of separately;
• in the event of illegal disposal of electrical and electronic waste, the pe-
nalties are specified by local waste disposal legislation.
Warranty on materials: 2 years (from production date, excluding consu-
mables).
Approval: the quality and safety of CAREL S.p.A. products are guaranteed
by the ISO 9001 certified design and production system.
IMPORTANT
NO POWER
&SIGNAL
CABLES
TOGETHER
READ CAREFULLYINTHE TEXT!
Separate as much as possible the probe and digital input cables from
cables to inductive loads and power cables, so as to avoid possible
electromagnetic disturbance. Never run power cables (including the
electrical panel cables) and signal cables in the same conduits.
Key to the symbols:
Important: to bring critical issues to the attention of those using the pro-
duct.
Note: to focus attention on important topics; in particular the practical ap-
plication of the various product functions.
Important: This product is to be integrated and/or incorporated into the
final apparatus or equipment. Verification of conformity to the laws and
technical standards in force in the country where the final apparatus or
equipment will be operated is the manufacturer’s responsibility. Before de-
livering the product, Carel has already completed the checks and tests
required by the relevant European directives and harmonised standards,
using a typical test setup, which however cannot be considered as repre-
senting all possible conditions of the final installation.
Warnings


5
ENG
µchiller +0300053EN rel. 2.2 - 14.12.2021
Index
1. Introduction............................................................... 7
1.1 Main functions....................................................................................................7
1.2 Models ....................................................................................................................8
1.3 Accessories ...........................................................................................................8
2. Installation ............................................................... 12
2.1 Warnings ............................................................................................................. 12
2.2 Panel version..................................................................................................... 12
2.3 DIN rail version ................................................................................................ 13
2.4 Electrical installation .................................................................................... 13
2.5 Probe/digital input connection............................................................ 14
2.6 Connection to user terminals ................................................................ 15
2.7 Positioning inside the panel................................................................... 16
2.8 Electrical installation ................................................................................... 17
2.9 Connecting serial ports with two circuits ...................................... 17
2.10 Connection to Power+ (for BLDC) ...................................................... 18
2.11 Positioning of probes/ components ................................................. 19
2.12 Input/output configuration .................................................................... 19
2.13 Functional diagrams .................................................................................... 22
3. Initial conguration................................................ 36
3.1 APPLICA app..................................................................................................... 36
3.2 Configuration procedure.......................................................................... 36
3.3 Unit set-up parameter list......................................................................... 40
3.4 Applica Desktop ............................................................................................. 42
3.5 Configuration procedure with Applica Desktop - Legacy
Model............................................................................................................................... 43
4. User interface........................................................... 46
4.1 Introduction ...................................................................................................... 46
4.2 User terminal .................................................................................................... 46
4.3 Standard display ............................................................................................. 47
5. Functions .................................................................. 51
5.1 Temperature control.................................................................................... 51
5.2 User pumps ....................................................................................................... 53
5.3 Frost protection control............................................................................. 55
5.4 Compressor rotation.................................................................................... 58
5.5 Compressor management....................................................................... 60
5.6 BLDC compressor protectors................................................................. 62
5.7 BLDC comp. alarm prevention.............................................................. 63
5.8 Compressor alarms....................................................................................... 65
5.9 Power+ Speed drive..................................................................................... 65
5.10 Expansion valve driver................................................................................ 66
5.11 Control of the expansion valve............................................................. 66
5.12 Source pump.................................................................................................... 66
5.13 Source fans ....................................................................................................... 67
5.14 Free cooling....................................................................................................... 70
5.15 Types of free cooling ................................................................................... 70
5.16 Free cooling....................................................................................................... 73
5.17 Defrost.................................................................................................................. 74
5.18 4-way valve management........................................................................78
5.19 Manual device management................................................................. 78
5.20 Air/air unit management (Legacy model only) .......................... 79
5.21 Automatic heater management for water units (Legacy mo-
del only).......................................................................................................................... 80
5.22 Condensing unit management............................................................ 81
5.23 Automatic changeover (Legacy model only) .............................. 81
6. Parameter table....................................................... 83
6.1 System .................................................................................................................. 83
6.2 Compressor ....................................................................................................... 84
6.3 BLDC and Inverter ......................................................................................... 85
6.4 Valve....................................................................................................................... 86
6.5 Source................................................................................................................... 86
6.6 Input/output configuration .................................................................... 88
6.7 mCH2 parameters (Legacy models only) ....................................... 88
6.8 BMS port.............................................................................................................. 89
6.9 Password ............................................................................................................. 89
6.10 Dashboard values.......................................................................................... 89
6.11 Settings ................................................................................................................ 90
7. Supervisor table...................................................... 91
7.1 Coil Status........................................................................................................... 91
7.2 Input Status ....................................................................................................... 92
7.3 Holding Register............................................................................................. 93
7.4 Input Register................................................................................................... 97
8. Alarms and signals.................................................. 99
8.1 Types of alarms................................................................................................ 99
8.2 Alarm list........................................................................................................... 100
9. Technical specications .......................................102
9.1 Connector/cable table ............................................................................ 104
10. Release notes.........................................................104
Index


7
ENG
µchiller +0300053EN rel. 2.2 - 14.12.2021 Introduction
Chiller is the Carel solution for complete management of air/water and water/water chillers and heat pumps, and condensing
units. The solution also allows the field replacement of µchiller2 and µchiller2 SE with the new product (hereinafter called the
Legacy model). The maximum configuration manages 2 compressors per circuit (*), up to a maximum of 2 circuits (using an
expansion card for circuit 2). The distinctive element of Chiller is complete control of high- efficiency units through integrated
management of electronic expansion valves (ExV) and brushless BLDC compressors, thus ensuring greater compressor protec-
tion and reliability and a high-efficiency unit. The user terminal allows wireless connectivity with mobile devices and is built- in
on the panel mounted models, or sold separately on DIN rail mounted models. CAREL’s “APPLICA” app, available on Google Play
for the Android operating system, makes it easier to configure parameters and commission the unit in the field.
(*): 2 On/Off compressors or 1 BLDC compressor + 1 On/Off compressor.
1.1 Main functions
Ref. Description
Main features Up to two circuits and 2 + 2 compressors
Compressors in tandem configuration with possible BLDC compressor (*)
Air/water chiller or heat pump (A/W)
Water/water chiller or heat pump (W/W)
Cooling-only condensing unit
Reverse-cycle condensing unit
Air/air unit, cooling only (Legacy models only)
Air/air unit, reverse-cycle (Legacy models only)
1 evaporator per unit
Air-cooled condenser with separate/shared air circuit for A/W units
Water-cooled condenser with single circuit for W/W units
Hardware Panel mounted model: management of ON-OFF compressors
DIN rail mounted model: management of ON-OFF compressors
DIN rail mounted model, enhanced: management of ON-OFF compressors
DIN rail mounted model, high efficiency: management of BLDC compressors
User interface 7-segment, 2-row LED display, optional pGDx graphic display, communication via APPLICA
app (compatible with NFC and BTLE) for mobile devices
Temperature control PID at start-up
PID in operation
Set point compensation on outdoor temperature
Compressor rotation FIFO or timed
Compressor management Specific BLDC compressors (see list on KSA - Chiller section)
Generic scroll compressors
Oil management with BLDCOil recovery function (extended operation at part load)
Oil equalisation (tandem with BLDC compressor)
Circuit destabilisation Forced compressor rotation (extended operation at part load)
ExV driver Built-in valve driver on enhanced and high efficiency models
External driver management via FieldBus port (all versions)
Programming with time bands Unit ON-OFF or 2nd set point (1 time band per day)
"Noise reduction" function for condenser fans (1 time band per day)
User pumps 1/2 pumps (2 pumps only with 2 circuits)
Rotation by time or with pump overload alarm
Cyclical activation during standby
Water-cooled condenser 1 common pump for both circuits
Air-cooled condenser Independent fans on each circuit or common to both circuits
Fan modulation based on condensing temperature (On/Off fan control via CAREL CONVONOFF0 module)
Optimised start-up to quickly bring the compressor(s) to steady operation
Fan anti-block protection (harsh climate)
Defrost Simultaneous
Separate
Independent
Using only the fans
Defrost interval managed based on outside temperature ("sliding defrost")
Prevent Prevention of scroll compressor operating limits in relation to condensing and evaporation temperature
Evaporator frost prevention
Total management of the BLDC compressor envelope limits
Alarms Management of automatic and manual reset according to alarm severity (see the chapter on Alarms)
Alarm log (up to 20 events): alarm and reset date and time recorded
Connectivity/supervision RS485 serial port
Modbus RTU
Baud rate up to 115200 bit/s
Frame configurable by Parity (None, Even, Odd) and StopBits (1 or 2); Databits fixed at 8 bits.
Tab. 1.a
(*) the configuration envisaged requires the capacity of the ON/OFF compressor to be equal to 60% of the capacity of the BLDC compressor (at maxi-
mum speed).
1. INTRODUCTION

8
ENG
µchiller +0300053EN rel. 2.2 - 14.12.2021
Introduction
1.2 Models
P/NAssembly Connectivity Compresso
management: Notes Electronic expansion
valve management
UCHBP00000190 panel NFC On/Off Standard version bipolar: with EVD Evolution driver
UCHBP00000200 panel NFC, Bluetooth
(BLE)
On/Off Standard version bipolar: with EVD Evolution driver
UCHBD00001230 DIN rail - On/Off Standard version bipolar: with EVD Evolution driver
UCHBDE0001150 DIN rail - On/Off Enhanced version unipolar: built-in; bipolar with external
EVD Evolution driver
UCHBDH0001150 DIN rail - On/Off and BLDC - bipolar: with external EVD Evolution driver
UCHBE00001230:
2nd circuit expansion
DIN rail - On/Off and BLDC unipolar: built-in; bipolar with external
EVD Evolution driver
UCHBE00001150:
2nd circuit expansion
DIN rail - On/Off and BLDC - unipolar: built-in; bipolar:
with external EVD Evolution driver
UCHBP000X0190 panel NFC On/Off Legacy version bipolar: with EVD Evolution driver
UCHBP000X0200 NFC, Bluetooth NFC, Bluetooth On/Off Legacy version bipolar: with EVD Evolution driver
UCHBP000X0230 DIN rail - On/Off Legacy version bipolar: with EVD Evolution driver
Tab. 1.b
1.3 Accessories
1.3.1 Chiller user terminal
For DIN rail mounted models (built-in on the panel model). The user terminal includes the display and keypad, comprising four
buttons that, when pressed alone or combined with other buttons, access the operations available for the “User” and “Service”
profiles (see the paragraph on“Commissioning”). Connectivity - NFC or NFC + Bluetooth (BLE) based on the model - allows inter-
action with mobile devices and simplifies unit commissioning (after having installed the CAREL “Applica” APP for the Android
operating system, see chapters “Commissioning”and “User interface”). For assembly, see the technical leaflet +0500146IE.
Code Description
AX5000PD20A20 User terminal (NFC)
AX5000PD20A30 User terminal (NFC, Bluetooth BLE)
ACS00CB000020 Connection cable L=1.5 m
ACS00CB000010 Connection cable L=3 m
Fig. 1.a Tab. 1.c
1.3.2 pGDx Touch user terminal
The 4.3” pGDx graphic terminal is part of the touch screen family designed to make the user interface simple and intuitive. The
electronic technology used and the 65K colour display enable management of high quality images and advanced features to
ensure a high aesthetic standard. The touch screen display guarantees simple human-machine interaction, making it easier to
browse between the various screens. See the technical leaflet +050001895.
Code Description
PGR04****B*** pGDx, 1 x RS485 port, 1 x 24 Vdc power connector, 1 optional
keypad connector
PGR04****C*** pGDx, 1 x opto-isolated RS485 port, 1 x 24 Vdc power connector, 1
optional keypad connector, 1 Ethernet port
Fig. 1.b Tab. 1.d
1.3.3 EVD Evolution/EVD Evolution twin valve driver
The Enhanced and High Efficiency models have the driver built-into the controller, able to drive unipolar valves (up to Carel
model E3V, with a cooling capacity less than 90-100kW); all versions can be connected to the external EVD Evolution driver to
drive bipolar valves (with a higher cooling capacity).

9
ENG
µchiller +0300053EN rel. 2.2 - 14.12.2021 Introduction
Part number Description
EVD0000T20 EVD evolution twin universal (RS485/Modbus)
EVD0000T21 EVD evolution twin universal, (RS485/Modbus) multiple pack of 10 pcs.
EVD0000T50 EVD evolution twin Carel valve (RS485/Modbus)
EVD0000T51 EVD evolution twin Carel valve, (RS485/Modbus) multiple pack of 10 pcs.
Fig. 1.c Tab. 1.e
1.3.4 Temperature sensors
NTC sensors for measuring the temperatures in the user circuit, the outdoor air or source, and the refrigeration circuit. NTC**HT
sensors are recommended for discharge temperature measurement (with BLDC compressors in heat pump mode).
Fig. 1.d
Code Type Range
NTC060HF01 10 kΩ ±1% @25°C, IP67 -50 to 90°C strap-on
NTC060HP00 10 kΩ ±1% @25°C, IP67 -50 to 50 °C (105°C in air)
NTC060HT00 50 kΩ ±1% @25°C, IP67 -30 to 100°C RH95% in air (150°C in a dry environment)
Tab. 1.f
Notice: see manual +040010025 (ITA- ENG) /+040010026 (FRE- GER) for guidelines on installing the sensors on the unit.
1.3.5 Pressure sensors
These measure:
1. evaporation pressure in the circuit, used to control superheat, manage the evaporator frost protection function and the
operating limits;
2. condensing pressure in the circuit, to control the condensing stage and manage the operating limits.
See the technical leaflet +050000488.
Fig. 1.e
Code Type Application Range
SPKT0*13P* 0-5V LP R407C, R290 -1 to 9.3 bars
SPKT0*43P* 0-5V LP R410A, R32 0 to 17.3 bars
SPKT0*33P* 0-5V HP R407C, R290 0 to 34.5 bars
SPKT0*B6P* 0-5V HP R410A, R32 0 to 45 bars
SPKT0011C* 4-20mA LP R407C, R290 0 to 10 bars
SPKT0041C* 4-20mA LP R410A, R32 0 to 18.2 bars
SPKT0031C* 4-20mA HP R407C, R290 0 to 30 bars
SPKT00B1C* 4-20mA HP R410A, R32 0 to 44.8 bars
SPKC00*310 IP67 connection cable L=2 to 12 m
SPKC00*311 IP67 connection cable - 50 pcs L=0.65 to 1.3 m
Tab. 1.g

10
ENG
µchiller +0300053EN rel. 2.2 - 14.12.2021
Introduction
1.3.6 Unipolar valve (P/NE2V**FSAC*)
Used with a compatible stator from the E2VSTA03**series. Unipolar electronic expan-
sion valve, managed directly by the controller, which guarantees precise refrigerant
flow even at low flow- rates. See the technical leaflet +050001680.
Fig. 1.f
1.3.7 Ultracap module (EVD0000UC0)
The Ultracap module EVD0000UC0 is an optional external backup module for the
EVD Evolution driver that ensures the valves are closed in the event of a power fail-
ure. The module guarantees temporary power supply to one EVD Evolution driver
(single or twin) only in the event of a power failure, for enough time to immediately
close the connected electronic valves (one or two). It therefore also avoids the need
to install a solenoid valve in the refrigeration circuit, or a backup coil kit.
Fig. 1.g
1.3.8 Ultracap module for unipolar valve (EVD000HAC0)
The Ultracap module EVD000HAC0 is an optional device used with the µChiller mod-
els equipped with an integrated unipolar electronic valve driver. This external backup
module closes the valve in the event of a power failure.
Part number Description
EVD000HAC0 Ultracap module for HVAC ACU APPLICATIONS
ACS00CB002370 Ultracap module cable for unipolar valve 0.3 m
Fig. 1.h
1.3.9 Couldgate for tERA connection
CloudGate is CAREL’s new family of IoT gateways to enable monitoring and tERA plat-
form services for HVAC/R systems with up to 10 units.
Compact, standard installation inside an electrical panel and a local LED interface
with immediate indication of communication status make Cloudgate easy to install
in the field, without the need for experts in connectivity devices.
Fig. 1.i

11
ENG
µchiller +0300053EN rel. 2.2 - 14.12.2021 Introduction
1.3.10 Connector kit
Part number Description
UCHCONP000 uChiller panel MOLEX/free connector kit
UCHCONP010 uChiller panel MOLEX/free connector and 100 cm cable kit
UCHCONP030 uChiller panel Molex/free connector and 300 cm cable kit
UCHCOND000 uChiller DIN MOLEX/free connector kit
UCHCOND010 uChiller DIN MOLEX/free connector and 100 cm cable kit
UCHCONPMC0 Adapter kit for MCH2
Fig. 1.j
1.3.11 Cables for LED displays (DINmodels only)
Part number Description
ACS00CB000010 Display cable AX JST/JST 3 M
ACS00CB000020 Display cable AX JST/JST 1.5 m
ACS00CB000012 Display cable AX JST/JST 3 m, multiple pack (10 pcs)
ACS00CB000022 Display cable AX JST/JST 1.5 m, multiple pack (10 pcs)
Fig. 1.k
1.3.12 USB/RS485 converter (CVSTDUMOR0)
Electronic device used to interface an RS485 network to a personal computer via the
USB port. See the technical leaflet +050000590.
Fig. 1.l

12
ENG
µchiller +0300053EN rel. 2.2 - 14.12.2021
Installation
2. INSTALLATION
2.1 Warnings
Important: avoid installing the controller in environments with the following characteristics:
• temperature and humidity that do not comply with the ambient operating conditions (see “Technical specifications”);
• strong vibrations or knocks;
• exposure to water sprays or condensate;
• exposure to aggressive and polluting atmospheres (e.g.: sulphur and ammonia gases, saline mist, smoke) which may cause
corrosion and/or oxidation;
• strong magnetic and/or radio frequency interference (thus avoid installation near transmitting
• antennae);
• exposure to direct sunlight and the elements in general;
• wide and rapid fluctuations in ambient temperature;
• exposure to dust (formation of corrosive patina with possible oxidation and reduction of insulation).
2.2 Panel version
2.2.1 Dimensions - mm (in)
300053_002_R01
78,5
36,5
46,6
88,6
Drilling template
71x29 mm
74,7
84,9
Fig. 2.a
2.2.2 Assembly
Important: before carrying out any maintenance, disconnect the controller from the power supply by moving the main
system switch to“off”.
300053_003_R01
1 2 3
Fig. 2.b
1. Place the controller in the opening, pressing lightly on the side anchoring tabs.
2. Then press on the front until fully inserted (the side tabs will bend, and the catches will attach the controller to the panel).
Important: IP65 front protection is guaranteed only if the following conditions are met:
• maximum deviation of the rectangular opening from flat surface: ≤ 0.5 mm;
• thickness of the electrical panel sheet metal: 0.8-2 mm;
• maximum roughness of the surface where the gasket is applied: ≤ 120 m.
Notice: the thickness of the sheet metal (or material) used to make the electrical panel must be adequate to ensure safe
and stable mounting of the product.

13
ENG
µchiller +0300053EN rel. 2.2 - 14.12.2021 Installation
2.2.3 Removal
300053_004_R01
2
1
1
Open the electrical panel from the rear and press the anchor-
ing tabs and then the controller to remove it.
1. Gently press the side anchoring tabs on the controller;
2. Exert slight pressure on the controller until it is removed.
Important: the operation does not require the use of
a screwdriver or other tools.
Fig. 2.c
2.3 DINrail version
2.3.1 Dimensions - mm(in)
66,2 (2.6)
11.09 (4.36)
13.83 (5.4)
70.4 (2.8)
300053_005_R01
Apply slight pressure to
the controller resting on
the DIN rail until the rear
tab clicks into place.
Fig. 2.d
2.3.2 Removal
Use a screwdriver as a lever in the hole to lift and release the tab. The tab is held in the locked position by return springs.
2.4 Electrical installation
Important: before carrying out any maintenance, disconnect the controller from the power supply by moving the main
system switch to“off”.
2.4.1 Description of the terminals
Panel model
J1
J7
G0 G
J6
C
C
NO1
NO2
NO3
NO4
NO5
J2
J3
J4 BMSJ5 FBus
S1 S3 5V
S2Y2
Y1ID1
ID2
ID3ID5
ID4S4
S6 +V
VL S5
Fig. 2.e

14
ENG
µchiller +0300053EN rel. 2.2 - 14.12.2021
Installation
DIN rail model
Basic Enhanced/ High Eciency
J1
J7
G0 G
J6
C
C
NO1
NO2
NO3
NO4
NO5
J2
J3
J4 BMSJ5 FBus
S1 S3 5V
S2Y2
Y1ID1
ID2
ID3ID5
ID4S4
S6 +V
VL S5
J11
C NO6
J9
J8
S7ID6
J1
J7
G0 G
J6
C
C
NO1
NO2
NO3
NO4
NO5
J2
J3
J4 BMSJ5 FBus
S1 S3 5V
S2Y2
Y1ID1
ID2
ID3ID5
ID4S4
S6 +V
VL S5
J11
C NO6
J10
J9
J14 J8
S7ID6
Fig. 2.f
Ref. Description Ref. Description
J1 G Power supply J5 - Fieldbus serial port (RS485): Rx/Tx -
G0 Power supply: reference + Fieldbus serial port (RS485): Rx/Tx +
J2 5V Ratiometric probe power supply O Fieldbus serial port (RS485): GND
S3 Analogue input 3 J6 C Common for relays 1, 2, 3, 4
S1 Analogue input 1 NO1 Digital output (relay) 1
Y1 Analogue output 1 NO2 Digital output (relay) 2
ID1 Digital input 1 NO3 Digital output (relay) 3
O GND: reference for probes, digital inputs and ana-
logue outputs
NO4 Digital output (relay) 4
S5 Analogue input 5 J7 C Common for relay 5
S2 Analogue input 2 NO5 Digital output (relay) 5
Y2 Analogue output 2 J8 - Unit terminal connector (AX5* or PGR04*)
ID2 Digital input 2 J9 S7 Analogue input 7
J3 ID3 Digital input 3 ID6 Digital input 6
ID5 Digital input 5 O Input reference
+V Power supply to 4-20 mA active probes O Input reference
S6 Analogue input 6 J10* G Ultracap module power supply (future use)
VL Not used G0
ID4 Digital input 4 Vbat Emergency power supply from Ultracap module (future use)
O GND: reference for analogue and digital inputs J11 - (not used)
S4 Analogue input 4 C Common for relay 6
J4 - BMS serial port (RS485): Rx/Tx- NO6 Digital output (relay) 6
+ BMS serial port (RS485): Rx/Tx+ J14* Carel ExV unipolar valve connector
O BMS serial port (RS485): GND Tab. 2.a
(*) for DIN Enhanced / High Efficiency models only
2.5 Probe/digital input connection
NTC probes 0-5 V ratiometric pressure probes
300053_008_R01
J2
S1
S2Y2
Y1ID1
ID2
NTCNTC
NTC
S5
S3 5V
300053_011_R01
J3 J2
ID3ID5
ID4S4
S6
VL
S1 S3
S2Y2
Y1ID1
ID2 S5
+V
5V
Fig. 2.g Fig. 2.h

15
ENG
µchiller +0300053EN rel. 2.2 - 14.12.2021 Installation
0-10 Vdc probes 4-20 mA probes/digital inputs
J3
0...10Vdc
S4
S6 +
V
VL
300053_009_R01
300053_011_R01
J3 J2
ID3ID5
ID4S4
S6
VL
S1 S3
S2Y2
Y1ID1
ID2 S5
+V 5V
Fig. 2.i Fig. 2.j
Controller terminals Pressure probe with current signal Controller terminals Pressure probe with current signal
11
+V Power supply brown 5V Power supply black
S1 Signal white O Power reference green
S1 Signal white
Tab. 2.b Tab. 2.c
Notice: O = GND
Notice: if an ExV valve is connected, an NTC temperature sensor must also be connected to read the gas suction temperature:
this sensor must be connected to one of the available inputs provided. For the position of the sensor on the suction pipe, see
the installation guide +040010025““Sonde e sensori - Guida alla scelta e all’installazione ottimale / Probes and sensors - Selection
and optimal installation guide”, available at carel.com under product => sensor => quick guide.
2.6 Connection to user terminals
2.6.1 Panel model
J4
PGDx
1
Fig. 2.k
2.6.2 DINrail model
PGDx
J8
J4
3
User terminal
J8
J4
2
PGDx
User terminal
J8
J4
4
Fig. 2.l

16
ENG
µchiller +0300053EN rel. 2.2 - 14.12.2021
Installation
Connection to connector J4
+–
230 Vac
24 Vdc
PSU PGTA00TRX0
PGDx
shield
Tx/Rx-
Tx/Rx+
GND
J4 BMS
J1
J7
G0 G
J6
C
C
NO1
NO2
NO3
NO4
NO5
J4 BMSJ5 FBus
S1 S3 5V
S2Y2
Y1ID1
ID2
ID3ID5
ID4S4
S6 +V
VL S5
Fig. 2.m
Connection to connector J8
+–
230 Vac
24 Vdc
PSU PGTA00TRX0
PGDx
J1
J7
G0 G
J6
C
C
NO1
NO2
NO3
NO4
NO5
J2
J3
J4 BMSJ5 FBus
S1 S3 5V
S2Y2
Y1ID1
ID2
ID3ID5
ID4S4
S6 +V
VL S5
J11
C NO6
J9
J8
S7ID6
J8
Tx/Rx-
Tx/Rx+
GND
Power
Supply
shield
Tx/Rx-
Tx/Rx+
GND
Fig. 2.n
Notice: (1) and (4) with PGDx connected to port J4 (BMS): the parameters must be set as shown in the following table.
Communication parameters
User Display Code Description Value
S x Hd00 BMS: serial address 1
S x Hd01 BMS: baud rate
3=9600; 4=19200; 5=38400; 6=57600; 7=115200
6
S x Hd02 BMS: settings
0=8-NONE-1; 1=8-NONE-2; 2=8-EVEN-1; 3=8-EVEN-2; 4=8-ODD-1; 5=8-ODD-2
0
Tab. 2.d
2.7 Positioning inside the panel
The position of the controller in the electrical cabinet must be chosen so as to guarantee correct physical separation from the
power components (solenoids, contactors, actuators, inverters, ...) and the connected cables. Proximity to such devices/cables
may create random malfunctions that are not immediately evident. The structure of the panel must allow the correct flow of
cooling air.

17
ENG
µchiller +0300053EN rel. 2.2 - 14.12.2021 Installation
2.8 Electrical installation
Important: When laying the wiring,“physically” separate the power part from the control part. The proximity of these two
sets of wires will, in most cases, cause problems of induced disturbance or, over time, malfunctions or damage to the compo-
nents. The ideal solution is to house these two circuits in two separate cabinets. Sometimes this is not possible, and therefore the
power part and the control part must be installed in two separate areas inside the same panel.
For the control signals, it is recommended to use shielded cables with twisted wires. If the control cables have to cross over the
power cables, the intersections must be as near as possible to 90 degrees, always avoiding running the control cables parallel
to the power cables.
Pay attention to the following warnings:
• use cable ends suitable for the corresponding terminals. Loosen each screw and insert the cable ends, then tighten the
screws. When the operation is completed, slightly tug the cables to check they are sufficiently tight;
• separate as much as possible the probe signal, digital input and serial line cables from the cables carrying inductive loads
and power cables to avoid possible electromagnetic disturbance. Never run power cables (including the electrical cables) and
probe signal cables in the same conduits. Do not install the probe cables in the immediate vicinity of power devices (contac-
tors, circuit breakers or similar);
• reduce the path of the probe cables as much as possible, and avoid spiral paths that enclose power devices;
• avoid touching or nearly touching the electronic components fitted on the boards to avoid electrostatic discharges (ex-
tremely damaging) from the operator to the components;
• do not secure the cables to the terminals by pressing the screwdriver with excessive force, to avoid damaging the controller:
maximum tightening torque 0.22-0.25 N•m;
• for applications subject to considerable vibrations (1.5 mm pk- pk 10/55 Hz), secure the cables connected to the controller
around 3 cm from the connectors using clamps;
• all the extra low voltage connections (analogue and digital inputs, analogue outputs, serial bus connections, power supplies)
must have reinforced or double insulation from the mains network.
2.9 Connecting serial ports with two circuits
For serial connections (FBus and BMS ports), the cables used must be suitable for the RS485 standard (shielded twisted pair,
see the specifications in the following table). The earth connection of the shield must be made using the shortest connection
possible on the metal plate at the bottom of the electrical panel.
Master device Serial port Lmax (m) Wire/wire capaci-
tance (pF/m)
Resistance on rst and
last device
Max no. of slave
devices on bus
Data rate
(bit/s)
Chiller FBus 10 <90 120 Ω 16 19200
PC (supervision) BMS 500 <90 120 Ω 16 115200
Notice: 120 Ω 1/4W terminating resistors on the first and last devices in the network must be used when the length exceeds
100 m.
For two-circuit units, the power supply connections must be in phase between the two controllers (G0 on the master controller
and G0 on the slave controller connected to the same power supply wire); the serial connection between the two controllers (J5
FBus on the master and J4 BMS on the slave) must be made as shown in the figure (+ with + and - with -).
G0 G
C
C
NO1
NO2
NO3
NO4
NO5
J2
J3
S1 S3 5V
S2Y2
Y1ID1
ID2
ID3ID5
ID4S4
S6 +V
VL S5
J4 BMS
J5 FBus
J4 BMS
J3 J2
J5 FBus
S1 S3 5V
S2Y2
Y1ID1
ID2
ID3ID5
ID4S4
S6 +V
VL S5
J1
J7
G0 G
J6
C
C
NO1
NO2
NO3
NO4
NO5
J8J10 J14
J9
S7
ID6
J11
C
NO6
Master
Slave
shield
EVD evolution
twin
shield
L
N
Fig. 2.o

18
ENG
µchiller +0300053EN rel. 2.2 - 14.12.2021
Installation
2.10 Connection to Power+ (for BLDC)
For the serial connection between the controller and the Power+ speed drive, see the specific manual. Also see the following
diagrams.
J4 BMS
J3 J2
J5 FBus
S1 S3 5V
S2Y2
Y1ID1
ID2
ID3ID5
ID4S4
S6 +V
VL S5
J1
J7
G0 G
J6
C
C
NO1
NO2
NO3
NO4
NO5
J8J10 J14
J9
S7
ID6
J11
C
NO6
L
N
power+
speed drive
shield
EVD
evolution
shield
Fig. 2.p
L
N
power+
speed drive
shield
EVD
evolution twin
shield
power+
speed drive
shield shield
Master Slave
12
J4 BMS
J3 J2
J5 FBus
S1 S3 5V
S2Y2
Y1ID1
ID2
ID3ID5
ID4S4
S6 +V
VL S5
J1
J7
G0 G
J6
C
C
NO1
NO2
NO3
NO4
NO5
J8J10 J14
J9
S7
ID6
J11
C
NO6
J4 BMS
J3 J2
J5 FBus
S1 S3 5V
S2Y2
Y1ID1
ID2
ID3ID5
ID4S4
S6 +V
VL S5
J1
J7
G0 G
J6
C
C
NO1
NO2
NO3
NO4
NO5
J8J10 J14
J9
S7
ID6
J11
C
NO6
Fig. 2.q
Notice: if connecting Power+ (for BLDC) and EVD evolution, the connection parameters are not configurable, and must be
set as shown in the table.
Device Address Network settings Baudrate
Power+ speed drive 1 1 8 - NONE - 2 19200
Power+ speed drive 2 1 8 - NONE - 2 19200
EVD evolution 198 8 - NONE -2 19200
Tab. 2.e

19
ENG
µchiller +0300053EN rel. 2.2 - 14.12.2021 Installation
2.11 Positioning of probes/ components
Water-cooled unit Air-cooled unit
E
L
F
SL
CP
PS
PU
T
T3
C
P3
P1
P2
T
2
T
1
U
S
T4
F1
T5
VV1
PU
300053_XYZ_R02
E
L
F
SL
CP
T
T3
C
P3
P1
P2
T2
T1
U
T4
F1
T5
VV1
Fig. 2.r Fig. 2.s
Ref. Description Ref. Description
S Source PU User pump
U User PS Source pump
E Evaporator P2 Evaporation pressure probe
F Filter-drier T1 Discharge temperature
L Liquid receiver T2 Suction temperature
CP Compressor P3 High pressure switch
C Condenser T3 Outside air temperature
SL Liquid sightglass F1 User pump flow switch
P1 Condensing pressure probe T4 Water delivery temperature (to) user
V Solenoid valve T5 Water return temperature (from) user
V1 Thermostatic expansion valve T6 Water delivery temperature (to) source
Tab. 2.f
2.12 Input/output conguration
Information on how to configure the µChiller Legacy inputs and outputs to replace mCH2 and mCH2 SE is shown below.
Panel mounting model DIN rail model (Basic)
J1
J7
G0 G
J6
C
C
NO1
NO2
NO3
NO4
NO5
J2
J3
J4 BMSJ5 FBus
S1 S3 5V
S2Y2
Y1ID1
ID2
ID3ID5
ID4S4
S6 +V
VL S5
J1
J7
G0 G
J6
C
C
NO1
NO2
NO3
NO4
NO5
J2
J3
J4 BMSJ5 FBus
S1 S3 5V
S2Y2
Y1ID1
ID2
ID3ID5
ID4S4
S6 +V
VL S5
J11
C NO6
J9
J8
S7
ID6
Fig. 2.t Fig. 2.u

20
ENG
µchiller +0300053EN rel. 2.2 - 14.12.2021
Installation
2.12.1 Analogue inputs
The analogue inputs on µChiller Legacy are divided into four groups, according to the type of sensor connected. The groups and
the list of parameters used to configure the different analogue inputs are shown below:
Group Sensor Master cong. parameter Slave cong. parameter
GRP1 S1 HC31 HC41
S2 HC32 HC42
S3 HC00 HC43
GRP2 S4 HC34 HC44
S5 HC35 HC45
GRP3 S6 HC03 HC05
GRP1* S7* HC04* HC47
Tab. 2.g
(*) available only on DIN version
The meanings assigned to the analogue inputs according to the various groups for the Master controller (circuit 1) are as follows:
Value GRP1 GRP2 GRP3
0Source water delivery temp. Source water delivery temp. Source water delivery temp.
1Outside temperature Outside temperature Outside temperature
2Discharge temperature circuit 1 Discharge temperature circuit 1 Remote set point
3Condensing temperature circ. 1 Condensing temperature circ. 1 Discharge temperature circuit 1
4Suction temperature circ. 1 Suction temperature circ. 1 Condensing temperature circ. 1
5Evaporation temperature circ. 1 Evaporation temperature circ. 1 Suction temperature circ. 1
6System water return temperature Condensing pressure circ. 1 Evaporation temperature circ. 1
7System water delivery temp. Evaporation pressure circ. 1 Condensing pressure circ. 1
8System water return temperature Evaporation pressure circ. 1
9System water delivery temp. System water return temperature
10 System water delivery temp.
11 System water delivery temp.
Tab. 2.h
The meanings assigned to the analogue inputs according to the various groups for the Slave controller (circuit 2) are as follows:
Value GRP1 GRP2 GRP3
0Not used Not used Not used
1Source water delivery temp. Source water delivery temp. Source water delivery temp.
2Outside temperature Outside temperature Outside temperature
3Discharge temperature circuit 2 Discharge temperature circuit 2 Remote set point
4 Condensing temperature circ. 2 Condensing temperature circ. 2 Discharge temperature circuit 2
5 Suction temperature circ. 2 Suction temperature circ. 2 Condensing temperature circ. 2
6 Evaporation temperature circ. 2 Evaporation temperature circ. 2 Suction temperature circ. 2
7 Common delivery water temperature Condensing pressure circ. 2 Evaporation temperature circ. 2
8Evap. water delivery temp. 2 Evaporation pressure circ. 2 Condensing pressure circ. 2
9Common water delivery temperature Evaporation pressure circ. 2
10 Evap. water delivery temp. 2 Common water delivery temperature
11 Evaporator 2 water outlet temperature
Tab. 2.i
2.12.2 Digital inputs
Below is the list of parameters used to configure the digital inputs:
Digital input Master conguration parameter Slave conguration parameter
ID1 HC14 HC16
ID2 HC15 HC17
ID3 High pressure switch circ. 1 High pressure switch circ. 2
ID4 HC06 HC09
ID5 HC07 HC10
ID6* HC08* HC11
Tab. 2.j
(*) available only on DIN version
This manual suits for next models
10
Table of contents
Other Carel Controllers manuals

Carel
Carel MCHRTF Series User manual

Carel
Carel IRMPX00000 User manual
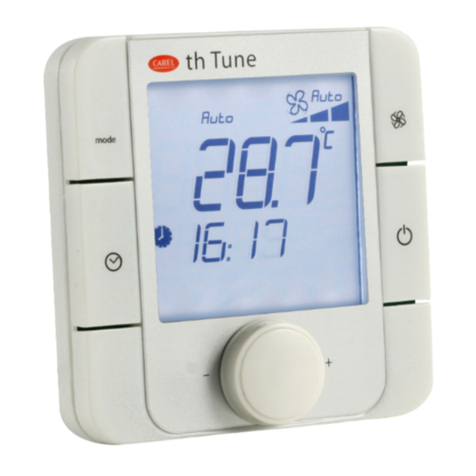
Carel
Carel AT th Tune Series User manual
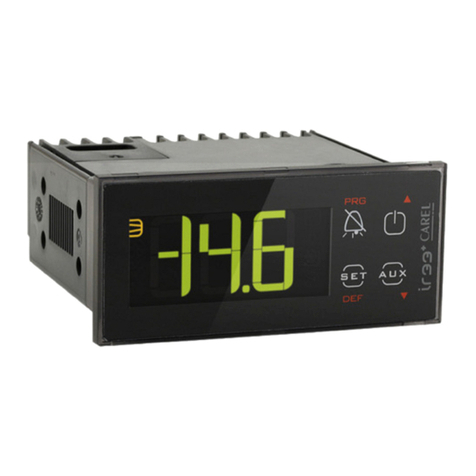
Carel
Carel ir33+ User manual
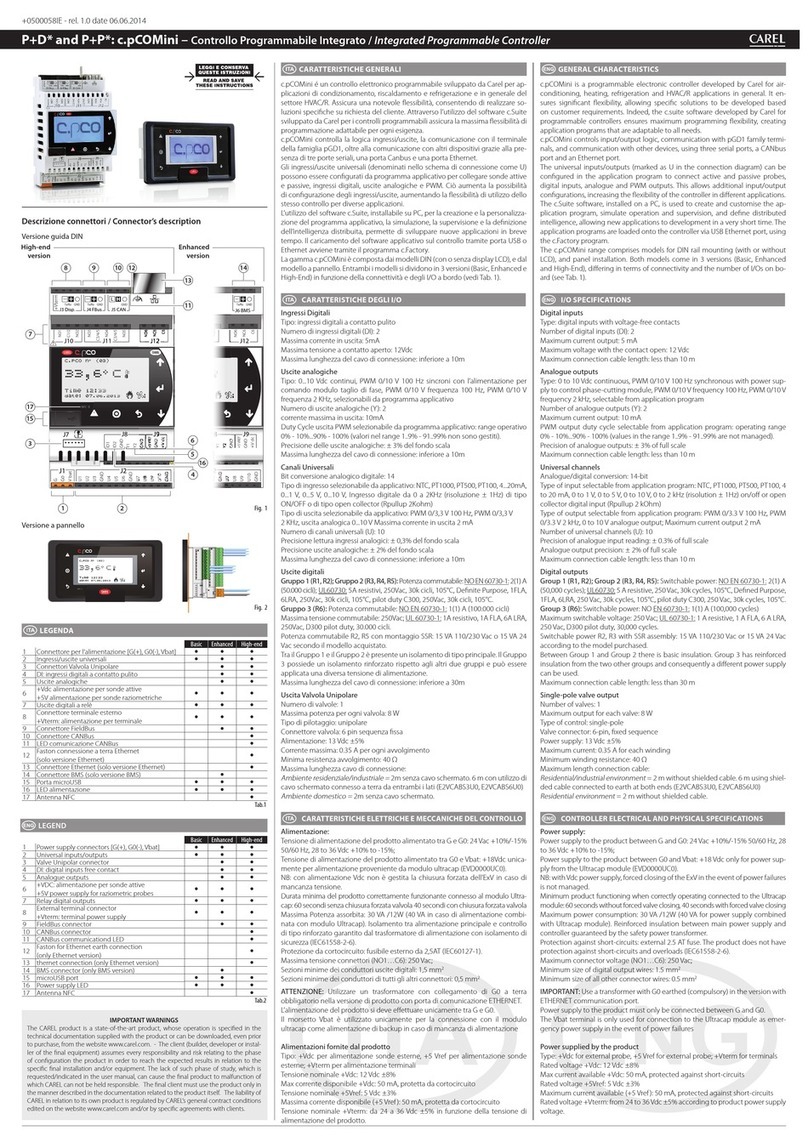
Carel
Carel c.pCOMini User manual

Carel
Carel uC2 User manual
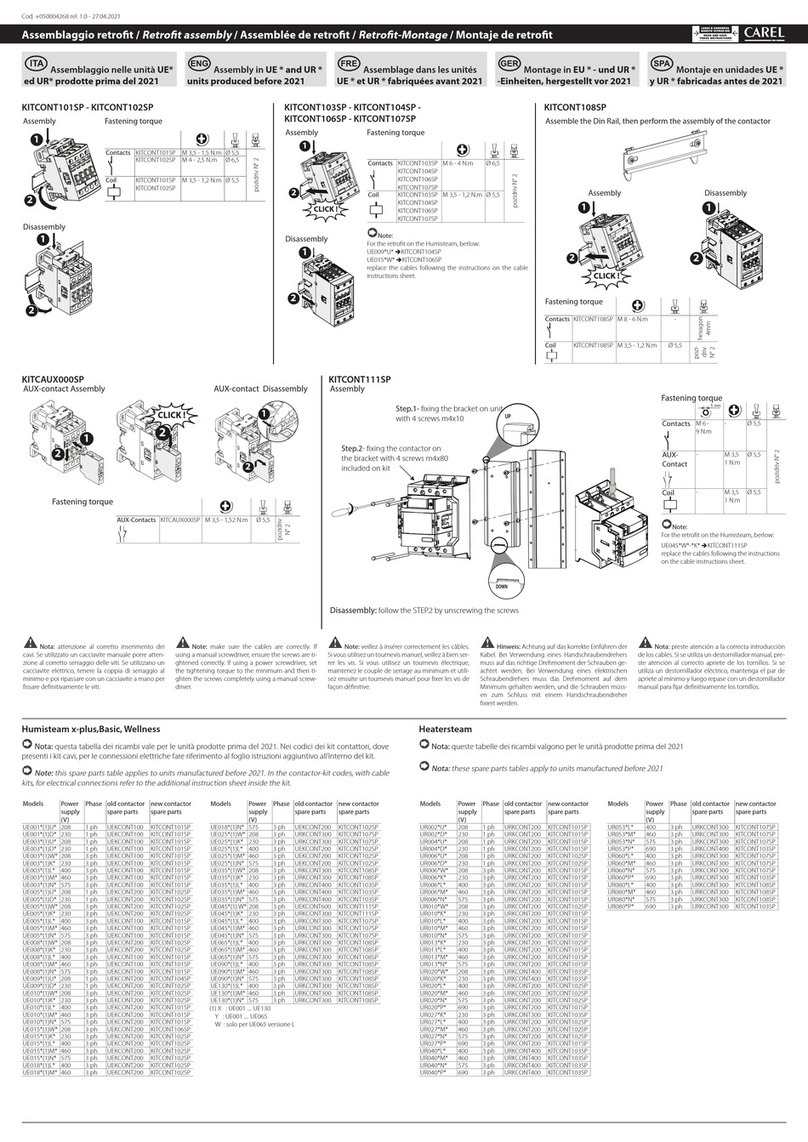
Carel
Carel KITCONT101SP User manual
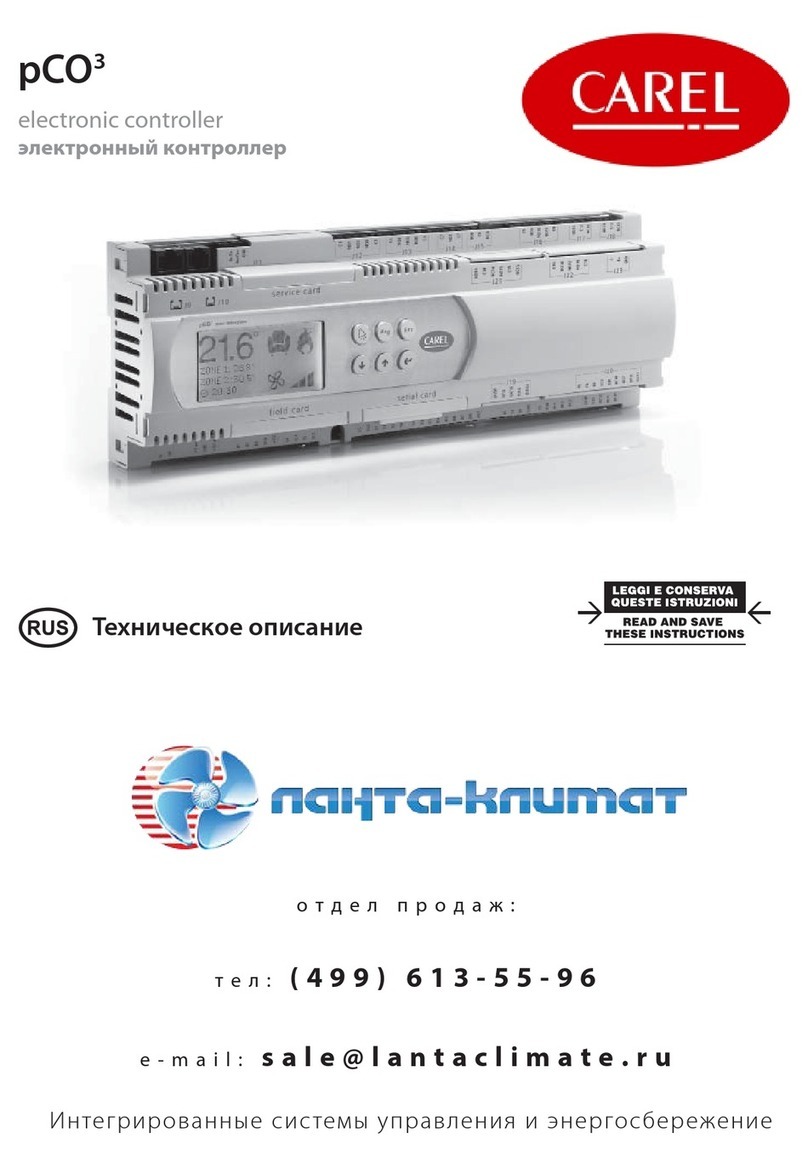
Carel
Carel pCO3 series Manual
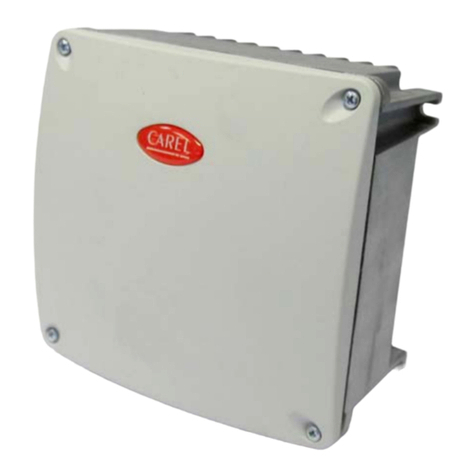
Carel
Carel FCP/1 User manual

Carel
Carel mastercella Manual