Cattron CANplus CP1000 User manual

CANplusTM CP1000
Installation Manual
9M01-1000-A401-EN

CANplusTM CP1000
Installation Manual
2
9M01-1000-A401-EN
Revision B
Revision History
VERSION
DATE
NOTES
A
12/2019
B
12/2020
Document rebranded and contact information updated
Any information furnished by Cattron™ and its agents is believed to be accurate and reliable. All specifications are subject to change without notice.
Responsibility for the use and application
of Cattron products rests with the end user since Cattron and its agents cannot be aware of all potential uses.
Cattron makes no warranties as to non-infringement nor as to the fitness, merchantability, or sustainability of any Cattron products for any specific
or general uses. Cattron Holdings, Inc., or any of its affiliates or agents shall not be liable for incidental
or consequential damages of any kind. All
Cattron products are sold pursuant to the Terms and Conditions of Sale, a copy of which will be furnished upon request. When used as a tradename
herein,
Cattron means Cattron Holdings, Inc. or one or more subsidiaries of Cattron Holdings, Inc. Cattron™, corresponding logos, and other marks
are
trademarks or registered trademarks of Cattron Holdings, Inc. Other marks may be the property of third parties. Nothing herein provides a license
under any Cattron or any third party intellectual property right.

CANplusTM CP1000
Installation Manual
3
9M01-1000-A401-EN
Revision B
Contents
1 Introduction...........................................................................................................................................................4
2 Mechanical Mounting ...........................................................................................................................................5
2.1 AluFlex™ Panels ......................................................................................................................................5
2.1.1 Mounting Templates ....................................................................................................................5
3 Connector Pinouts................................................................................................................................................8
3.1 D21 to Engine Pinout................................................................................................................................8
3.2 D31 IO Pinout ...........................................................................................................................................9
4 Typical Wiring.................................................................................................................................................... 10
4.1 Power and Ground................................................................................................................................. 10
4.2 ECU Power Out ..................................................................................................................................... 10
4.3 Starter Power Out .................................................................................................................................. 10
4.4 Resistive Senders.................................................................................................................................. 10
4.5 CAN Bus Termination ............................................................................................................................ 10
5 Testing............................................................................................................................................................... 11
6 Certifications ..................................................................................................................................................... 12
6.1 FCC Part 15 Certification....................................................................................................................... 12
6.2 Industry Canada Certification ................................................................................................................ 13
7 Technical Support ............................................................................................................................................. 14

CANplusTM CP1000
Installation Manual
4
9M01-1000-A401-EN
Revision B
1 Introduction
This manual provides general installation information for the CANplusTM CP1000. This manual’s target audience
is professional installers for Engine Distributors and OEMs of engine-driven machines. The engine manufacturer
specific application information should be followed for any detailed or specific requirements. Cattron sales and
technical support are available at www.cattron.com/contact to discuss specialized requirements or custom
applications.

CANplusTM CP1000
Installation Manual
5
9M01-1000-A401-EN
Revision B
2 Mechanical Mounting
The CP1000 control panel is adaptable to a wide variety of applications. The included engine harness connector
facilitates quick installation.
The following is a list of installation guidelines:
1. The panel mount shall be
a. Easily accessible by the operator.
b. Placed away from moving equipment.
c. Stable during equipment operation and transportation.
2. The vibration isolation mounts shall
a. Be properly installed.
b. Have normal movement.
c. Be located so the panel does not hit any adjacent structure during operation.
2.1 AluFlex™ Panels
AluFlex panel enclosures are constructed from extruded aluminum and powder-coated for durability. The
faceplate is aluminum or powder-coated galvanized steel and the backplate is powder-coated galvanized steel.
The enclosure is splash proof and includes condensation drain holes in the bottom.
AluFlex panel isolation mounts are preinstalled to a heavy-duty mounting bracket with mounting holes to
accommodate various installations. Isolator mounts should not be twisted when installed, as doing so will lead to
premature failure.
2.1.1 Mounting Templates
The following two figures show the one-to-one hole template for the CP1000 mounting bracket.

CANplusTM CP1000
Installation Manual
6
9M01-1000-A401-EN
Revision B

CANplusTM CP1000
Installation Manual
7
9M01-1000-A401-EN
Revision B

CANplusTM CP1000
Installation Manual
8
9M01-1000-A401-EN
Revision B
3 Connector Pinouts
There are two connectors on the CP1000, as described in the following subsections.
3.1 D21 to Engine Pinout
This connector contains the typical connections required for electronically or mechanically governed engines.
The following is the pinout:
Pin Signal Comment Pin Signal Comment
A Pre-Heat 1 A @
System Voltage M Aux IN 2 Active Low
B B+ N Temp SW Active Low,
Normally Open
C Sender Return P Oil PSI Sender System Voltage
0 – 750 Ω
D Starter 10 A @
System Voltage R --- ---
E GND S Pulse2 Tach System Voltage
F CAN Shield T Oil PSI SW Active Low,
Normally Closed
G ECU/Solenoid 10 A @
System Voltage U CAN Low
H Temp Sender System Voltage
0 – 750 Ω V CAN High
J Ignition 1 A @
System Voltage W Aux IN 1 Active Low
K Pulse Tach System Voltage X Fuel Level
Sender
System Voltage
0 – 750 Ω
L --- --- --- --- ---

CANplusTM CP1000
Installation Manual
9
9M01-1000-A401-EN
Revision B
3.2 D31 IO Pinout
This connector contains the CP1000’s expanded IO.
The following is the pinout:
Pin Signal Comment Pin Signal Comment
1 Switched In 1 Active Low 17 Switched Out 5 1 A @
System Voltage
2 Switched In 2 Active Low 18 Transducer
Power 1
1 A @
System Voltage
3 Switched In 3 Active Low 19 Transducer
Power 2
1 A @
System Voltage
4 Switched In 4 Active Low 20 Pulse In 1
5 Switched In 5 Active Low 21 Pulse Gnd
6 Switched In 6 Active Low 22 Pulse In 2
7 Isolated Power
In 1a 20 A 23 E-Stop Input Normally
Grounded
8 Isolated Power
In 1b 24 4-20 mA In
9 Isolated Power
Out 1a 20 A 25 4-20 mA In
10 Isolated Power
Out 1b 26 4-20 mA In
11 Isolated Power
Out 2 10 A 27 4-20 mA In
12 Isolated Power
In 2 10 A 28 4-20 mA In
13 MODBus (+) 29 4-20 mA In
14 MODBus (-) 30 Float 1 Active Low
15 Switched Out 3 1 A @
System Voltage 31 Float 2 Active Low
16 Switched Out 4 1 A @
System Voltage

CANplusTM CP1000
Installation Manual
10
9M01-1000-A401-EN
Revision B
4 Typical Wiring
The following subsections describe the typical engine interface wiring.
4.1 Power and Ground
The panel’s Power and Ground must connect directly to the battery posts and must not share power and ground
wiring with any other devices, especially any high current loads. The Power line should have overcurrent
protection in the form of current-limiting devices, fuses, circuit breakers or fusible links to protect the harness
wiring in the event of fault conditions.
4.2 ECU Power Out
The CP1000 can directly power the engine ECU.
4.3 Starter Power Out
The Starter Power Out is intended to power the starter relay, which is required. When power is removed from the
relay coil, the collapsing magnetic field generates a negative voltage surge. Negative voltage surges can damage
components. The CP1000 has protection against these negative surges. However, it is still required to have a
protection/suppression diode as close to the relay as possible. Cattron recommends the use of relays that have
this protection/suppression diode built in. The protection/suppression diode must have sufficient voltage ratings to
survive and sufficiently suppress these negative voltage surges. Cattron recommends a 1N4001 diode. Cattron
sells a spike-suppressing diode kit (Part Number 630-4007-77).
4.4 Resistive Senders
The Resistive Sender connections send system voltage out to the sender to obtain the current value. It is required
that the sender return connection be connected to a ground point (the engine chassis, for example), as close to
the sender as possible in order to get an accurate measurement. If more than one sender is used, each sender
should have a sender return connected to a ground point near that particular sender. All sender returns should
then be connected together near the panel and the combined returns connected to the panel’s sender return
input.
4.5 CAN Bus Termination
CAN bus requires two 120 Ω termination resistors each at the extreme ends of the wiring harness. Typically, the
engine ECU provides the termination resistor on its end (see the engine documentation to verify). The CP1000
has a termination resistor that can be turned off and on as needed. The CP1000’s default configuration has this
termination resistor turned on.

CANplusTM CP1000
Installation Manual
11
9M01-1000-A401-EN
Revision B
5 Testing
WARNING
DURING THE FOLLOWING PROCEDURE, CORRECT ANY PROBLEMS BEFORE PROCEEDING
TO THE NEXT STEP. CONTINUED TESTING MAY DAMAGE THE PANEL, HARNESS OR ENGINE.
Use the following testing procedure:
1. Turning the keyswitch ON initiates self-test; check all connections and battery polarity on failure.
2. Test to verify overcurrent protection; identify and correct any wiring fault on failure.
3. Verify fuel run/stop solenoid or ECM energizes.
4. Fuel solenoid should be powered for 10 to 30 seconds when the key is turned on.
a. The ECM should send CAN bus data as soon as the self-test completes.
b. Verify engine cranks when the key is turned to start; check all connections on failure.
5. If the engine does not start, check the fuel lines and bleed if necessary.
6. Verify gauges and indicators with the engine running.
a. See the CP1000 User Manual for details.
7. Test all safety shutdowns.
a. See the CP1000 User Manual for details.
8. Run the engine for an extended time to identify any temperature or connection problems.
!

CANplusTM CP1000
Installation Manual
12
9M01-1000-A401-EN
Revision B
6 Certifications
6.1 FCC Part 15 Certification
This device complies with Part 15 of the FCC Rules. Operation is subject to the following two conditions:
(1) this device may not cause harmful interference, and (2) this device must accept any interference received,
including interference that may cause undesired operation.
WARNING
CHANGES OR MODIFICATIONS NOT EXPRESSLY APPROVED BY THE PARTY RESPONSIBLE
FOR COMPLIANCE COULD VOID THE USER’S AUTHORITY TO OPERATE THE EQUIPMENT.
Note: This equipment has been tested and found to comply with the limits for a Class B digital device,
pursuant to Part 15 of the FCC Rules. These limits are designed to provide reasonable protection
against harmful interference in a residential installation. This equipment generates, uses and can
radiate radio frequency energy and, if not installed and used in accordance with the instructions, may
cause harmful interference to radio communications. However, there is no guarantee that interference
will not occur in a particular installation. If this equipment does cause harmful interference to radio or
television reception, which can be determined by turning the equipment off and on, the user is
encouraged to try to correct the interference by one or more of the following measures:
—Reorient or relocate the receiving antenna.
—Increase the separation between the equipment and receiver.
—Connect the equipment into an outlet on a circuit different from that to which the receiver is
connected.
—Consult the dealer or an experienced radio/TV technician for help.
This equipment uses the following Antennas and may not be used with other antenna types or with antennas of
higher gain:
Mfg.: Pegasus Wireless Products
Type: Dipole
Gain: 3 dBi
This equipment complies with FCC RF Exposure requirements and should be installed and operated with a
minimum distance of 20 cm between the radiator and any part of the human body.
!

CANplusTM CP1000
Installation Manual
13
9M01-1000-A401-EN
Revision B
6.2 Industry Canada Certification
Note: These statements are required to be listed in both English and French Languages.
This device complies with Industry Canada licence-exempt RSS standard(s). Operation is subject to the following
two conditions: (1) this device may not cause interference, and (2) this device must accept any interference,
including interference that may cause undesired operation of the device.
Le présent appareil est conforme aux CNR d'Industrie Canada applicables aux appareils radio exempts de
licence. L'exploitation est autorisée aux deux conditions suivantes : (1) l'appareil ne doit pas produire de
brouillage, et (2) l'utilisateur de l'appareil doit accepter tout brouillage radioélectrique subi, même si le brouillage
est susceptible d'en compromettre le fonctionnement.
Under Industry Canada regulations, this radio transmitter may only operate using an antenna of a type and
maximum (or lesser) gain approved for the transmitter by Industry Canada. To reduce potential radio interference
to other users, the antenna type and its gain should be so chosen that the equivalent isotropically radiated power
(e.i.r.p.) is not more than that necessary for successful communication.
Conformément à la réglementation d'Industrie Canada, le présent émetteur radio peut fonctionner avec une
antenne d'un type et d'un gain maximal (ou inférieur) approuvé pour l'émetteur par Industrie Canada. Dans le but
de réduire les risques de brouillage radioélectrique à l'intention des autres utilisateurs, il faut choisir le type
d'antenne et son gain de sorte que la puissance isotrope rayonnée équivalente (p.i.r.e.) ne dépasse pas l'intensité
nécessaire à l'établissement d'une communication satisfaisante.
This equipment complies with the ICES RF radiation exposure limits set forth for an uncontrolled environment.
This equipment should be installed and operated with a minimum distance of 20 cm between the radiator and any
part of the human body.
Cet équipement est conforme aux limites d'exposition aux radiations ICES définies pour un environnement non
contrôlé . Cet équipement doit être installé et utilisé à une distance minimale de 20 cm entre le radiateur et une
partie de votre corps.

CANplusTM CP1000
Installation Manual
9M01-1000-A401-EN
Revision B
Due to continuous product improvement, the information provided in this document is subject to change without notice.
Cattron Support
For remote and communication control systems support, parts and repair, or technical support, visit us online at:
www.cattron.com/
contact
Cattron North America Inc., 655 N River Rd NW, Suite A,
Warren, OH 44483
Other manuals for CANplus CP1000
2
Table of contents
Other Cattron Remote Control manuals
Popular Remote Control manuals by other brands
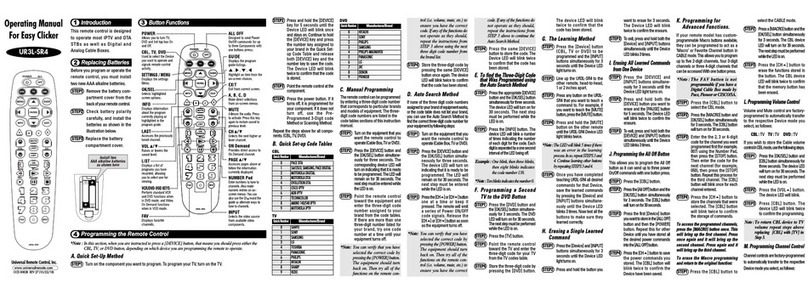
Universal Remote Control
Universal Remote Control Easy Clicker UR3L-SR4 operating manual
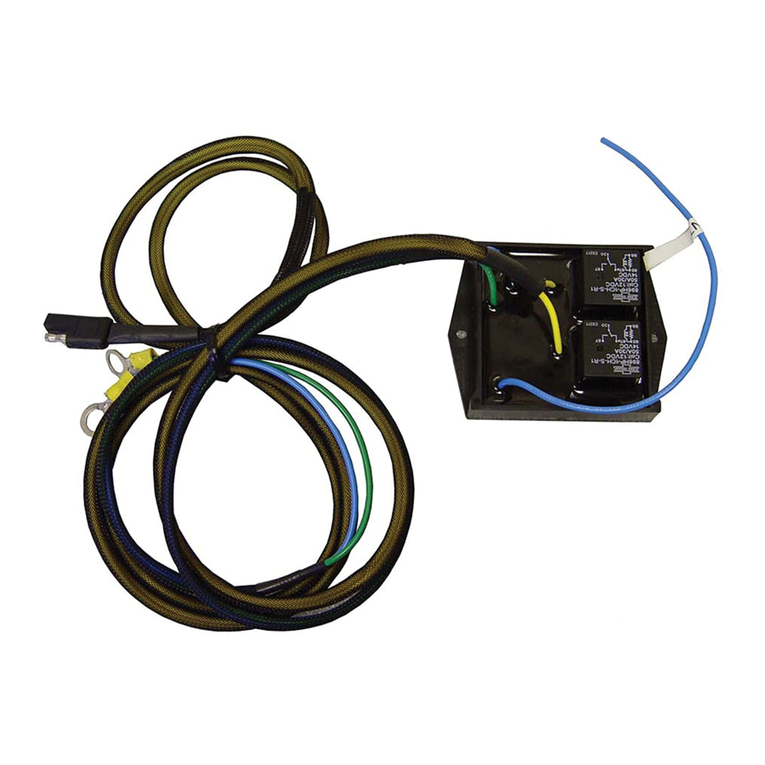
CMP
CMP Panther 55-0105 Installation and operating instructions
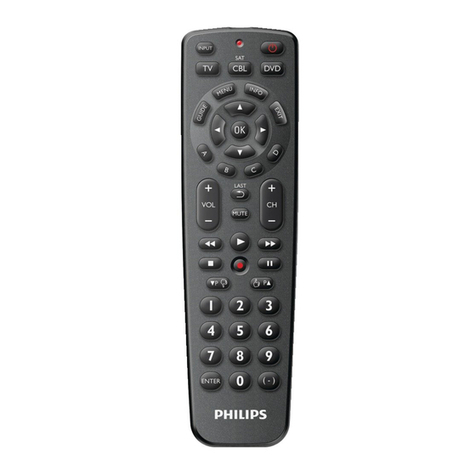
Philips
Philips SRP1103/27 quick start guide
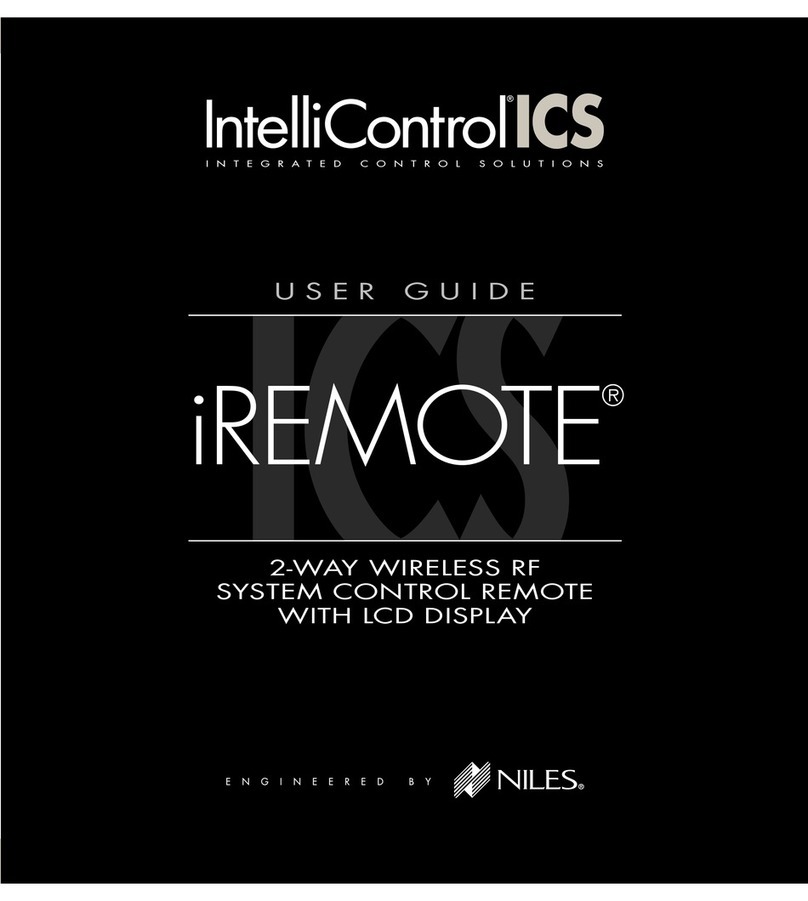
ICS
ICS iREMOTE user guide
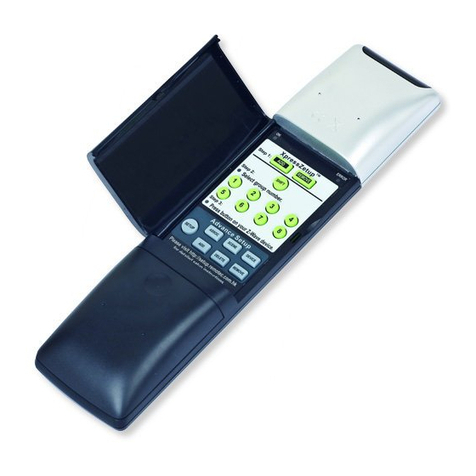
Z-Wave
Z-Wave Z-URC XpressZetup Quick setup guide
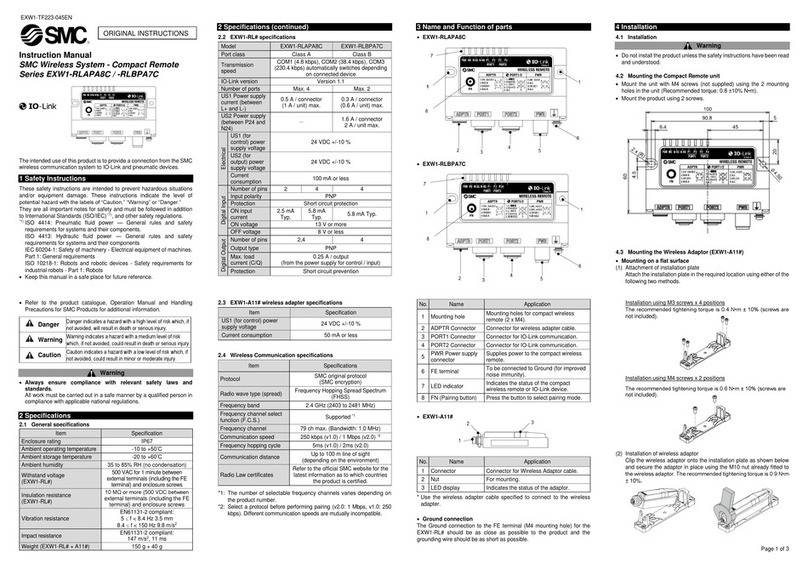
SMC Networks
SMC Networks EXW1-RLAPA8C Series instruction manual