Cerlic O2X User manual

2002-11-18 MANE11/02 Ver 2.00
O2X
Dissolved Oxygen
Sensor

-2 -
TABLE OF CONTENTS
1. Introduction 3
2. A few words about this manual 3
3. Design 3
4. Measuring principle 3
5. Unpacking the sensor 4
Damages 4
Packaging 4
Content 4
Optional parts for O2X Dissolved Oxygen sensor: 4
6. Mounting the sensor 5
Cable Connections 5
Installation Tips 5
7. Removing the sensor 6
8. Changing or Installing a new electrode 6
Removing an old electrode: 6
Installing a new electrode: 7
Mounting the protection plate 7
9. Cleaning unit 8
Cleaning the Flushing Nozzle 8
Mounting plate for solenoid valves 9
10. Menu for O2X Transmitter 10
11. Calibration 12
Zero Calibration 12
Air calibrating a sensor 12
Air pressure conversion 13
12. Scaling 14
13. Technical description 15
Certificate of conformity 15
Optional parts for O2X Dissolved Oxygen Sensor: 15
14. Dimensions 16
Appendix 1, Assembly of handrail mounting kit 17
Appendix 2, Assembly of adjustable slide rail 18
Appendix 3, Support information 19
Appendix 4, Setup information 20

-3 -
1. Introduction
The O2X sensor is designed to continuously measure dissolved oxygen levels in liquids.
The O2X is effective in saving energy costs associated with aeration systems in an
activated sludge process. In addition, accurate measuring of dissolved oxygen allows
for better control of nitrification/denitrification.
2. A few words about this manual
This manual details installation procedures and operational features of the Cerlic O2X
sensor. Menu navigation and technical data for the BB2 control box can be found in the
BB2 service manual.
3. Design
The O2X sensor is manufactured with 316SS (SS2343) stainless steel. The electrode is
a Clark-type, field-replaceable cartridge with an FEP Teflon membrane. The active
components included in the electrode are treated to maximize their life span. The
electrode is equipped with a temperature sensor that provides compensation features for
added stability. The electrode housing is made of PVC. An O-ring on the electrode
prevents water from leaking into the O2X. A six-pin connector of the back of the
electrode connects to the O2X.
Built-in flushing nozzles allow for the most accurate readings with little maintenance.
The electronics is protected in the rugged casing, ensuring its reliability in very
demanding environments.
The sensor has a fixed, shielded 10 m (33’) cable used for signal transmission between
the sensor and the BB2 control box. The cable sheath is made of Hytrel and is highly
resistant to aggressive materials and fluids.
4. Measuring principle
The electrode is a Clark type electrode with a membrane in FEP. The Clark cell detects
the oxygen though its reduction at the Gold electrode. The sensor consists of a Gold
cathode and Silver anode. A membrane covers the two electrodes and blocks access of
most species to the electrodes. Only dissolved gases such as oxygen can traverse the
membrane, hence the reduction current responds to the oxygen concentration.
Active components included in the electrode are treated to maximize their life span.
Inside the electrode there is also a temperature sensor mounted in a way that minimizes
problems with temperature adjustments. This provides excellent compensation of the
electrode temperature instability. The electrode housing is made of PVC and is
equipped with an O-ring sealing against the mounting. There is a connector on the
electrode for the amplifier cable.

-4 -
5. Unpacking the sensor
The unit has been tested and approved before delivery from the supplier. Please check
to confirm that no visible damages occurred during shipment.
Damages
If damages occurred during shipment, immediately contact UPS or other truck line as
well as your Cerlic representative. The shipment can be returned only after contact has
been made with Cerlic.
Packaging
The original packaging is designed to protect the equipment and should be used for
storage or if the goods must be returned.
Content
Please check that the content corresponds to your order and packing list.
Every shipment should include:
•O2X sensor P/N: 11305473, including 33 ft. (10 m) cable and 33 ft. (10m)
flushing hose.
You will also need an electrode (below) to get the sensor working:
Optional parts for O2X Dissolved Oxygen sensor:
•Electrode cartridge. P/N 11805160
•Stainless steel Mounting bracket X, including rod holder P/N 11205539
•Telescopic rod, 4 m, including transmitter holder P/N 20205501
•Adjustable slide rail sensor holder P/N 11205600
•Solenoid valve for flushing P/N 11705516
•Aluminum handrail mounting plate predrilled for BB2
and solenoid valves w/ u-bolts, outside US version P/N 10605533
•Aluminum handrail mounting plate predrilled for BB2
or solenoid valves w/ u-bolts, US version P/N 31204049
•33 ft. (10m) extension cable with plug-in connectors. P/N 20805510
•Y-Splitter for two sensors to one BB2 control box P/N 21505534

-5 -
6. Mounting the sensor
The O2X is mounted on a telescopic fibreglass rod and placed in a mounting bracket
that fastens to a handrail, please refer to the Appendix 1 for further details. As an
alternative way of mounting the sensor, an adjustable slide rail holder is available,
please refer to the Appendix 2 for further details.
For best measurement, the rod shall be mounted in an angle, 5 –30 degrees from
vertical.
Cable Connections
Connect the sensor to the BB2 control box using the attached connector on the end of
the sensor cable. In the event that two sensors are to be connected to the same BB2
control box, use the Y-splitter (P/N 21505534).
NOTE! Never try to turn the connector housing to fasten or remove the connector, only
the fluted ring at the top of the connector shall be turned.
Installation Tips
•Adjust the rod so that the sensor is at least 12” below the liquid surface or the
lowest water level in decant applications (SBRs) to prevent the sensor from
coming out of the liquid.
•In an aeration tank, ensure that the sensor is not directly above a diffuser head.
To obtain the most representative dissolved oxygen level, the sensor should be
installed on the backside of the rolling diffuser effect.
•In an aeration basin, flushing may not be required if the tank is well agitated. To
verify the need for flushing, remove the sensor from the liquid after it has been
in the liquid for several days. If the sensor is coated with solids, flushing with
water or compressed air is recommended.
NOTE! The transmitter is delivered with the
electrode uninstalled. A yellow plastic cap
protects the electrode connection plug and the
flushing nozzle in the transmitter. The plastic
cap must be removed and the electrode must be
installed and calibrated before the transmitter
is submerged into water (refer to Section 7).
Retain the yellow cap as it may be used as
protection later. Do not press on the top of the
cap if the electrode is installed.

-6 -
7. Removing the sensor
The sensor is removed in the following steps:
•Disconnect the sensor cable from the BB2 and the flushing hose from solenoid.
•Open the clamp, and pull the rod out of the mounting bracket
•Make sure all water inside the rod is drained.
•Clean the sensor and rod with a brush or clean cloth. Do not use a wire brush!
•Open the black sensor adapter.
•Flush the inside of the rod with clean water.
•Mount the protective cap (or a small plastic bag) on the sensor cable connector.
•Pull the cable and flushing hose out of the rod.
•Blow compressed air through the flushing hose to get rid of the water in the hose
and the sensor.
8. Changing or Installing a new electrode
The electrode can usually be both assembled and disassembled without tools. Do not
ever clamp onto the sensor housing or part of the cable when installing or removing the
flushing head.
Removing an old electrode:
•Make sure automatic flushing is disabled.
•If using the protection plate, you must remove it before changing the electrode.
•Remove the flushing head by rotating it.
•Unplug the electrode.
•Remove the electrode from the flushing head by pressing firmly on the backside
near the cable connector.
•Ensure that the O-ring that seals the flushing head is fixed in its proper position
in the sensor body.
•Screw the flushing head back onto the sensor, do not screw it tight.
•If a new electrode is not to be mounted, the yellow plastic cap shall be mounted
to protect the electrode connection plug and the flushing nozzle in the
transmitter.

-7 -
Wrench
Electrode
Flushing head
Installing a newelectrode:
•Untighten the flushing head about one turn (if not already lose) to let the air out
when the electrode is pushed in place.
•Plug the electrode cable into the connector on the electrode.
•Install the new electrode into the flushing head. Do not touch the membrane of
the electrode when mounting.
•Tighten the flushing head and mount the protection plate, if needed. See below
for instructions on mounting the protection plate.
•A new air-calibration must be performed whenever the electrode is changed.
Mounting the protection plate
Bend the plate slightly and press it down between the flushing nozzles. Ensure that the
plate fits into the notches on the flushing nozzles. Correct the plate when it is mounted.
Do not ever remove a flushing nozzle in order to mount the protection plate. The
nozzles are fastened with a special locking jam.

-8 -
9. Cleaning unit
The transmitter is equipped with built-in flushing nozzles. The nozzles are used to
direct the cleaning medium, compressed air or water, via a flushing hose that is
connected to the top of the transmitter. The air or liquid is controlled with a solenoid
valve that is wired into the BB2 control box.
Flushing must be activated in the “Settings” menu in the BB2 control box:
•Select the O2X transmitter in the Main Menu by using the or buttons.
•Press ENTER for approximately five seconds to enter the Transmitter Menu.
•Use the arrows to select “Settings” and press ENTER.
•Use the arrows to select “Cleaning” and press ENTER.
•In the “Cleaning” submenu, adjust the “Cleaner” setting to “flush” and specify
the cleaning interval in minutes and the flush time in seconds.
•Specify the relay to be used according to the wiring inside the control box. For
example, if the solenoid is wired to relay #1, select “#1” for flushing.
•“Next time” displays the next time flush will be activated, pushing ENTER will
set it to current time and those start cleaning..
Cleaning the Flushing Nozzle
If the flushing nozzle becomes plugged, removing the flushing head to backflush the
nozzles with clean water can clean it. Before removing the flushing head, close the
valve for the flush water source. Place a ½” hose over the flush nozzle and carefully
open the water valve. The pressure should clear the line of solids. If backflushing does
not work initially, try cleaning the three flushing nozzles with a needle. Try
backflushing the nozzles again as described above until clean water comes out.
Flushing tube
Flushing
water
Sensor cable
Note!
•Pay attention to the requirements for protection against backflow, according to
the EN 1717 standard for drinking water devices. If possible, use plant reuse
water or effluent water for cleaning.
•Never flush if the electrode is not installed.
•
When the electrode is not installed, the yellow plastic cap should be kept on the

-9 -
Mounting plate for solenoid valves
To provide an easy mounting of solenoid valves for the built-in flushing nozzles Cerlic
offers a predrilled Aluminum handrail mounting plate. The Mounting plate is fixed to
the rail using two u-bolts.
Please see technical specifications for details and ordering information on Solenoid
Valves and Mounting Plate.
Mounting plate for one or two solenoids
(outside US version).

-10 -
10. Menu for O2X Transmitter
Use or to select the sensor in the main display. The menu for the selected sensor
is accessed by pressing ENTER for five seconds. If the selected sensor is not active (the
text No transmitteris shown) a warning is displayed that asks you to make another
choice in order to show the sensor menu.
Settings
I-Time Integration time or dampening -can be set up to 999 seconds
Decimals 1 or 2 for display and menu
Alarm Relay ”-” ”#1”, ”#2”, or ”#1 and #2”. Check that the relay is not being
used for cleaning
Analog ”None”, ”Channel 1”, ”Channel 2”, or ”Both”. Pick which analog
output contacts are to be used with sensor. If “Both” is chosen,
channel 1 will give the dissolved oxygen according to the
sensors selected scale, channel 2 will give the temperature
scaled 0-100 degrees C. The temperature is to be seen as
additional information, not a primary measurement.
Cleaning Press ENTER to go to Cleaning program
Cleaner ”None”, ”Flush”, or ”Brush”. Do not select “Brush” since this
does not exist for O2X sensor
Interval min 0-999 minutes, time between cleaning cycles
Length sec 0-999 seconds, duration of flushing cycle
Freeze sec 0-999 seconds, time the output signal shall be frozen after
flushing
Relay ”-”, ”#1”, or ”#2”. Select relay to operate solenoid for flush cycle.
These are the same relays used for “Alarm relay” above
Next time The next scheduled cleaning time. Pushing “Enter” on this line
will set the time to current time and start a cleaning cycle. This
could be used to test the “Flush” cycle.
Calibrate
Airpres.mBar Specify within 10 mBar
Calibrate ”No”, ”Zero”, or ”Air”. Select what calibration to do.
Temp (info) Shows actual temperature in the electrode
Test (info) Shows actual dissolved oxygen level
Setvalue Calculated with air pressure and transmitter temp; shall be the
same as “test” immediately after the calibration

-11 -
Scale
Max 0-99.9 mg/l, measured value equal to 20 mA output signal.
Min 0-99.9 mg/l, measured value equal to 4 mA output signal.
Hi Alarm 0-99.9 mg/l, the value zero inactivates the alarm
Low Alarm 0-99.9 mg/l, the value zero inactivates the alarm
System
Type Type of sensor, read only
Serial Serial number of the sensor, read only
SoftW Software version of the sensor, read only
Temp Sensor temperature, read only
Info Press “ENTER” to go to “info” read only menu. This menuis for
Cerlic internal use, it may change without notice
MS0 SA value for zero sample
MS1 SA value for air sample
Cons 1 Calculated concentration at last air calibration
Ch1 Raw value for dissolved oxygen measurement
Ch2 Raw value for channel temperature measurement
Con mg/l, This is what is displayed on main screen
Samp/s Number of samples per second
Service Not accessible for users.

-12 -
11. Calibration
It is important that the instrument has been turned on for about 30 minutes prior to
calibration so that the sensor and electronics can stabilize.
Zero Calibration
The sensor is zero calibrated at the factory, and does not often need to be zero calibrated.
We do however recommend to do a new zero calibration when replacing the electrode
since half the job is then already done. Remove the electrode before performing a zero
calibration. Refer to “Section 8 –Changing or installing a New Electrode”.
Zero calibrating a sensor:
•Select the O2X transmitter in the Main Menu by using the or buttons.
•Press ENTER for approximately five seconds to enter the Transmitter Menu.
•Use the arrows to select the “Calibration” sub menu, and press ENTER.
•Use the arrows to select “Calibrate”. Press ENTER.
•Use the arrows to select “Zero” (three choices can be done, Air/No/Zero). Press
ENTER.
•Wait for the zero calibration to finish (usually takes about ten seconds). The
system will return to the previous menu.
Install the electrode before performing an air calibration. Refer to “Section 8 –
Changing or installing a New Electrode”. Continue with “Air calibrating a sensor”
Air calibrating a sensor
The most important thing to keep in mind while performing an air calibration is that it is
necessary to create a constant environment. The electrode cartridge must be dry with no
water drops on the membrane. Fill a bucket halfway with water. Suspend the sensor
~1-1.5 ft above the water surface to create a humid environment and cover the bucket
with a towel. If rain and/or strong winds are present, the calibration procedure could be
disturbed. In this case shield the equipment so that it is protected from the rain or wind.
An open plastic bag over the transmitter may slow the calibration time down, but is
otherwise a good way to help constant conditions.
•Select the O2X transmitter in the Main Menu by using the or buttons.
•Press ENTER for approximately five seconds to enter the Transmitter Menu.
•Use the arrows to select the “Calibration” sub menu, and press ENTER.
•Use the arrows to select “Calibrate”. Press ENTER.
•Enter the current air pressure in mBar. It is sufficient to specify the pressure
within 10 mBar (se table below for conversion from inHg to mBar).
•Use the arrows to select “Air” (three choices can be made, Air/No/Zero). Press
ENTER.
•Wait for the transmitter to be calibrated. A successful calibration will take
anywhere between 5 and 15 minutes for the sensor to stabilize. After calibration,

-13 -
compare the current dissolved oxygen value with setvalue (see below for
description). The unit returns to the menu when the calibration is finished.
Air pressure conversion
It is important to enter the correct air pressure before doing an air calibration. Air
pressure is measured in mBar (which is exactly the same as the SI-unit hPa).
Below is a formula and a table to convert from inHG to mBar (and thus to hPa).
InHg mBar / hPa
29.2 990
29.3 993
29.4 997
29.5 1000
29.6 1003
29.7 1007
29.8 1010
29.9 1014
30.0 1017
30.1 1020
30.2 1024
30.3 1027
30.4 1030
The following appear in the Calibration menu as read-only:
•Temp (info): Displays the current temperature of the sensor.
•
Test (info): Displays the current measured dissolved oxygen value.
Immediately after calibration and before the sensor is placed in the
liquid, this
value should closely resemble the setvalue. A reading outside of an acceptable
range may indicate that the electrode needs to be replaced.
•Setvalue: Ideal value calculated using temperature and air pressure.
5
.
29
1000
∗
=inHg
mBar

-14 -
12. Scaling
The “SCALE” menu (see the BB2 manual) allows the user to set the high and low
boundaries for a 4-20mA output signal. In addition, this menu allows the user to set
high and low alarms values that can be used to notify when the level has reached critical
points.
MAX sets the 20 mA point output
MIN sets the 4 mA point output (may be a negative value for special
applications)
H-ALARM sets the High Alarm set point, the value zero inactivates the alarm
L-ALARM sets the Low Alarm set point, the value zero inactivates the alarm

-15 -
13. Technical description
O2X P/N 11305473
Material 316SS (SIS2343)
Dimensions See section 13.
Weight 4.6 lbs. (2,1 kg)
Process connection Submerged
Max Depth 33 ft. (10 m)
Max temperature 140°F (60°C)
Measuring principle Clark cell
Cable, connection 5-pin M12-plug
Cable, length 33 ft. (10 m)
Cable, material Hytrel
Flushing, Pressure 60-90 psi (4-6 bar)
Flushing hose, length 33 ft. (10 m)
Flushing hose, material PVC
Enclosure IP68 NEMA 4X
Certificate of conformity
The Sensor has been developed and manufactured in accordance with the following
standards:
SS-EN50 082-2 (immunity), SS-EN50 081-2 (emission), SS-EN61 010-1 (safety)
89/336/EEC, 92/31/EEC, 93/36/EEC, 73/23/EEC
Optional parts for O2X Dissolved Oxygen Sensor:
•Electrode cartridge. P/N: 11805160
•Mounting bracket X, including rod holder P/N 11205539
•Telescopic rod, 4 m, including transmitter holder P/N 20205501
•Adjustable slide rail sensor holder P/N 11205600
•Solenoid valve for flushing P/N 11705516
•Aluminum handrail mounting plate predrilled for BB2
or solenoid valves w/ u-bolts, outside US version P/N 10605533
•Aluminum handrail mounting plate predrilled for BB2
or solenoid valves w/ u-bolts, US version P/N 31204049
•33 ft. (10m) extension cable with plug-in connectors. P/N 20805510
•Y-Splitter for two sensors to one BB2 control box P/N 21505534

-16 -
14. Dimensions

-17 -
Appendix 1, Assembly of handrail mounting kit
•Disassemble the bracket guide and place
around the telescopic rod.
•Use the SS screws on bracket to tighten the
bracket to the rod.
•Mount the Flexible Mounting Bracket on existing handrail or on
separate holder. The bent lip on the mounting plate shall be on top
and faced toward the liquid or tank. Adjust the Mounting Bracket to
the correct angle and tighten the nuts. The bracket shall be fixed to
the rail, and must not be able to rotate around it.
•Insert the PVC bracket guide with the telescopic rod
into the mounting bracket. Make sure that the bracket
guide tracks are properly seated in the bracket.
•Fasten the safety-locking clamp.
•Check that the bracket is safely fixed to the rail for the
spring to work the way it is intended.
Example of a holder
to be used for the
mounting bracket
when no handrail is
•Pull the cable and hose through the sensor holder and rod.
•Connect the telescoping fiberglass rod to the sensor with the two piece black PVC adapter.
•The adapter halves should be tightened until snug, which will leave about 1/16" gap.
NOTE!The gap is required so the water can drain from the rod.
•Adjust the length of the telescopic sensor rod as necessary by twisting the nuts while holding the
rod.
NOTE! Do not extend the rod sections beyond the black lines. This could lead to rod damage.

-18 -
Appendix 2, Assembly of adjustable slide rail

-19 -
Appendix 3, Support information
Before calling Cerlic support, please collect the information in this form and have it at
hand.
Company _____________________________________________________
Name _____________________________________________________
Phone _____________________________________________________
E-mail _____________________________________________________
Sensor Type _____________________________________________________
Position / Tag
_____________________________________________________
First go to the BB2 menu, it is accessed by pressing and ENTER at the same time for
five seconds. Select “System” and press ENTER, then select “Status” and press ENTER
again.
Version _____________________________________________________
Serial _____________________________________________________
Box temp _____________________________________________________
Boxheat _____________________________________________________
Leave the BB2 menu by pressing and ENTER at the same time. Use or to
select the sensor in the main display. Go to the sensor menu, it is accessed by pressing
ENTER for five seconds. Select “System” and press ENTER.
Type _____________________________________________________
Serial _____________________________________________________
SoftW _____________________________________________________
Temp _____________________________________________________
Select “Info”, then press “ENTER” to go to the “info” menu.
MS0 _____________________________________________________
MS1 _____________________________________________________
Cons 1 _____________________________________________________
Ch1 _____________________________________________________
Ch2 _____________________________________________________
Con _____________________________________________________
Samp/s _____________________________________________________
Leave the BB2 menu by pressing and ENTER at the same time.

-20 -
Appendix 4, Setup information
This sheet can be used to document the setup of a sensor.
Sensor Type _____________________________________________________
Position / Tag _____________________________________________________
In the System sub menu of the sensor menu the following information can be collected.
Serial _____________________________________________________
SoftW _____________________________________________________
In the Settings sub menu of the sensor menu the following parameters can be set.
I-time _____________________________________________________
No of decimals _____________________________________________________
Alarm Relay _____________________________________________________
Analog _____________________________________________________
Cleaner _____________________________________________________
Cleaning interval _____________________________________________________
Cleaning length _____________________________________________________
Cleaning freeze _____________________________________________________
Cleaning relay _____________________________________________________
In the Scale sub menu of the sensor menu the following parameters can be set.
Max _____________________________________________________
Min _____________________________________________________
High alarm _____________________________________________________
Low alarm _____________________________________________________
Leave the BB2 menu by pressing and ENTER at the same time.
This manual suits for next models
1
Table of contents
Other Cerlic Measuring Instrument manuals
Popular Measuring Instrument manuals by other brands
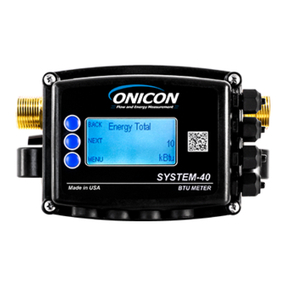
Onicon
Onicon SYSTEM-40 Installation and operation guide
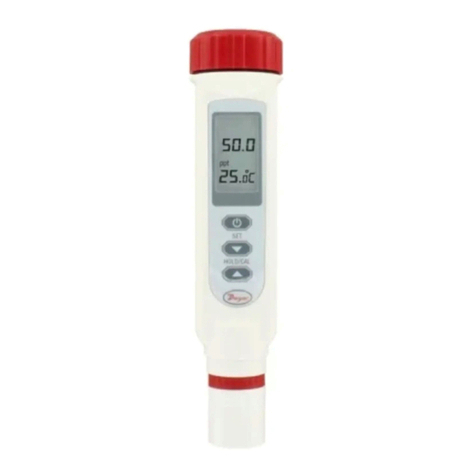
Dwyer Instruments
Dwyer Instruments WSM-10 Installation and operating instructions
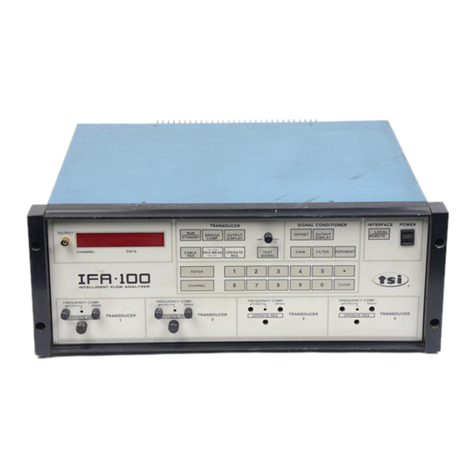
TSI Incorporated
TSI Incorporated IFA 100 manual
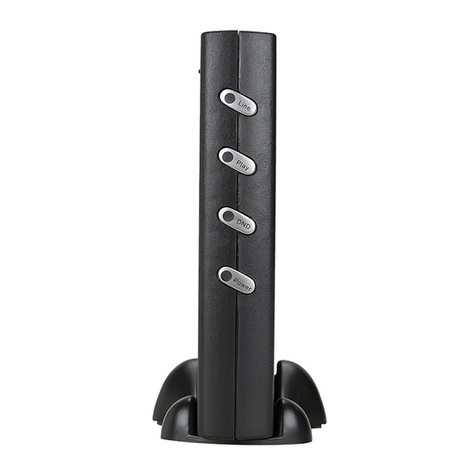
ARTECH
ARTECH Fonkorder1 manual
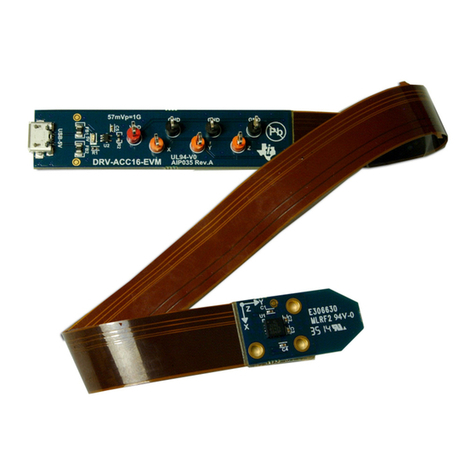
Texas Instruments
Texas Instruments DRV-ACC16-EVM user guide
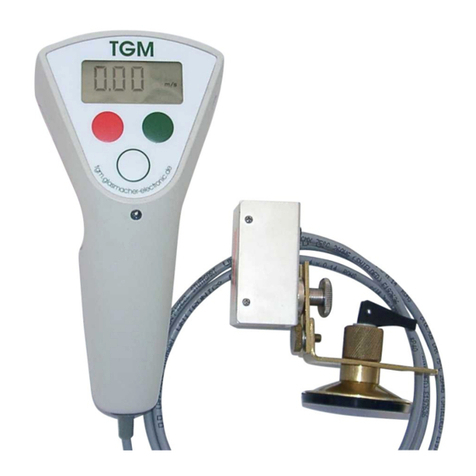
glasmacher electronic
glasmacher electronic TGM 5 Instruction guide