check-all Valve EPIC User manual

CHEC
K
-ALL VALVE MFG. CO.
1800FullerRd.WestDesMoines,IA50265
PH:(515)224‐2301Fax:(515)224‐2326
ISO9001CERTIFIED
EPIC™
INSTALLATION & OPERATION Manual
WARNING:READALLOFTHESEINSTRUCTIONSBEFOREPROCEEDING.ONLYEXPERIENCEDPERSONNELSHOULDBEALLOWEDTOINSTALLORHANDLETHEENCLOSEDVALVE(S).ANYDAMAGE
RESULTINGFROMMISHANDLINGORIMPROPERINSTALLATIONISNOTCOVEREDBYTHEMANUFACTURER’SWARRANTY.FORWARRANTYDETAILS,REFERTOTHELATESTREVISIONOF
CHECK‐ALLVALVE®MANUFACTURINGCOMPANYMANUFACTURER’STERMSANDCONDITIONS(Form#160).SEEwww.checkall.comORREQUESTACOPYFROMTHEFACTORY.Form#106B
The EPIC™is an in-line spring loaded poppet-type
check valve that is designed to be simple, rugged, and
efficient in any flow orientation. It is streamlined so
that media flows through the valve over smooth
contoured surfaces with a minimum change in
direction. This minimizes the pressure drop across
the valve. The patent pending EPIC™features a
complete drop in Replaceable Insert that is
engineered for silent operation. The valve closes
quickly and smoothly to minimize fluid hammer.
The following instructions are meant as a guideline
only. They do not cover every situation and rely on
the common sense and expertise of the person
installing the valve. See also checkall.com/EPIC for
an Assembly/Disassembly video. In no way is
Check-All®liable for any damage to the valve, the
system, or for personal injury resulting from use of
these guidelines.
INSTALLATION
Prior to installation remove any end caps and inspect
the valve(s) for any damage, internal debris or loose
parts that may have occurred during shipment.
Orient the valve so the FLOW ARROW is pointing
in the direction of desired flow (Fig. 1). From the
closed position the POPPET moves away from the
SEAT in the direction of flow (Fig. 2).
Connect the valve inlet and outlet to the system.
Care should be taken to prevent disassembling
the valve body. After the valve has been installed
verify that it is properly supported to prevent
additional loading on the valve body.
To avoid personal injury, take appropriate
precautionary measures if the system contains
hazardous materials. Discharge, depressurize, and
drain the surrounding system prior to removing the
valve from service. If the media within the system is
colder or hotter than room temperature allow the
valve to return to room temperature before removing
from the system.
While holding the valve ends disconnect it from the
system. Care should be taken to prevent
disassembling the valve body.
Clean the valve to remove any thread sealant, tape,
debris and/or hazardous materials prior to
preforming maintenance, inspection and/or re-
installation.
Table 1
EPIC™Kits
Valve Part Number Replaceable Insert
Kit Part Number
EPIC-0125, all styles
EPIC-0250, all styles
EPIC-0375MP
EPIC-0375FT
EPIC-0375DF
EPIC-RKD
EPIC-0375FP
EPIC-0500MP
EPIC-0500DF
EPIC-0500FT
EPIC-RKF
EPIC-0500FP
EPIC-0750MP
EPIC-0750DF
EPIC-0750FT
EPIC-RKH
EPIC-0750FP
EPIC-1000MP
EPIC-1000DF
EPIC-1000FT
EPIC-RKI
EPIC-1000FP
EPIC-1250MP EPIC-RKJ
Scan here
for Online
Ordering
Insert kits come with
a replaceable insert,
insert o-ring, and
body o-ring
Fig. 2: Vertical Flow Up Orientation
(Example Only)
INLETENDOUTLET END
Fig. 1: Horizontal Orientation
(Example Only)
FLOWARRO
W
REMOVAL

CHEC
K
-ALL VALVE MFG. CO.
1800FullerRd.WestDesMoines,IA50265
PH:(515)224‐2301Fax:(515)224‐2326
ISO9001CERTIFIED
EPIC™
INSTALLATION & OPERATION Manual
WARNING:READALLOFTHESEINSTRUCTIONSBEFOREPROCEEDING.ONLYEXPERIENCEDPERSONNELSHOULDBEALLOWEDTOINSTALLORHANDLETHEENCLOSEDVALVE(S).ANYDAMAGE
RESULTINGFROMMISHANDLINGORIMPROPERINSTALLATIONISNOTCOVEREDBYTHEMANUFACTURER’SWARRANTY.FORWARRANTYDETAILS,REFERTOTHELATESTREVISIONOF
CHECK‐ALLVALVE®MANUFACTURINGCOMPANYMANUFACTURER’STERMSANDCONDITIONS(Form#160).SEEwww.checkall.comORREQUESTACOPYFROMTHEFACTORY.Form#106B
DISASSEMBLY
Orient the valve to the VERTICAL FLOW UP
position (Fig. 2). Hold the Inlet End and unthread
the OUTLET from the INLET and set aside (Fig. 3).
Remove the REPLACEABLE INSERT from the
INLET (Fig 3). Clean to remove any debris that may
be present. Inspect the SEAT (Fig. 2) for debris,
dings, scratches and/or tears. Replace as needed
(See Table 1 for Insert Kits).
Remove the INSERT O-RING from the INSERT
GROOVE (Fig. 3) and replace.
Remove the BODY O-RING from the BODY
GROOVE (Fig 3) and replace.
Clean the INLET and OUTLET to remove any
thread sealant, tape, debris and/or hazardous
materials that may be present.
ASSEMBLY
Orient the INLET to the VERTICAL FLOW UP
position. Insert the BODY O-RING into the BODY
GROOVE (Fig 3). Verify that the o-ring is positioned
correctly in the groove and is free from debris, dings,
scratches and/or tears.
Place the INSERT O-RING into the INSERT
GROOVE (Fig 3). Verify that the o-ring is
positioned correctly in the groove and is free from
debris, dings, scratches and/or tears.
Place the REPLACEABLE INSERT onto the
INLET face so that the YOKE goes inside of the
INLET and the POPPET is exposed (Fig 2 &3).
Note: The Replaceable Insert will self-center within
the INLET and OUTLET when assembled.
CAUTION: The Replaceable Insert can be
installed backwards which will prevent flow
and/or result in damage to the valve. VERIFY
THAT THE REPLACEABLE INSERT IS
INSTALLED CORRECTLY BEFORE
PROCEEDING.
Hold the INLET stationary in the VERTICAL
FLOW UP position. Tighten the two body
components to the appropriate torque for your
individual application requirements. (Fig 3). Note:
Thread lubricant may be required to prevent thread galling.
WARNING: DO NOT CHANGE THE VALVE
ORIENTATION UNTIL THE VALVE HAS
BEEN COMPLETELY ASSEMBLED.
CAUTION: Improper seating of components will
result in failure of the valve and/or diminish the
life of the Replaceable Insert and/or o-rings.
Scan here for Express Line homepage
Fig. 3: Expande
d
Assembl
y
Popular Control Unit manuals by other brands

Zodiac
Zodiac Ei2 Expert Instructions for installation and use
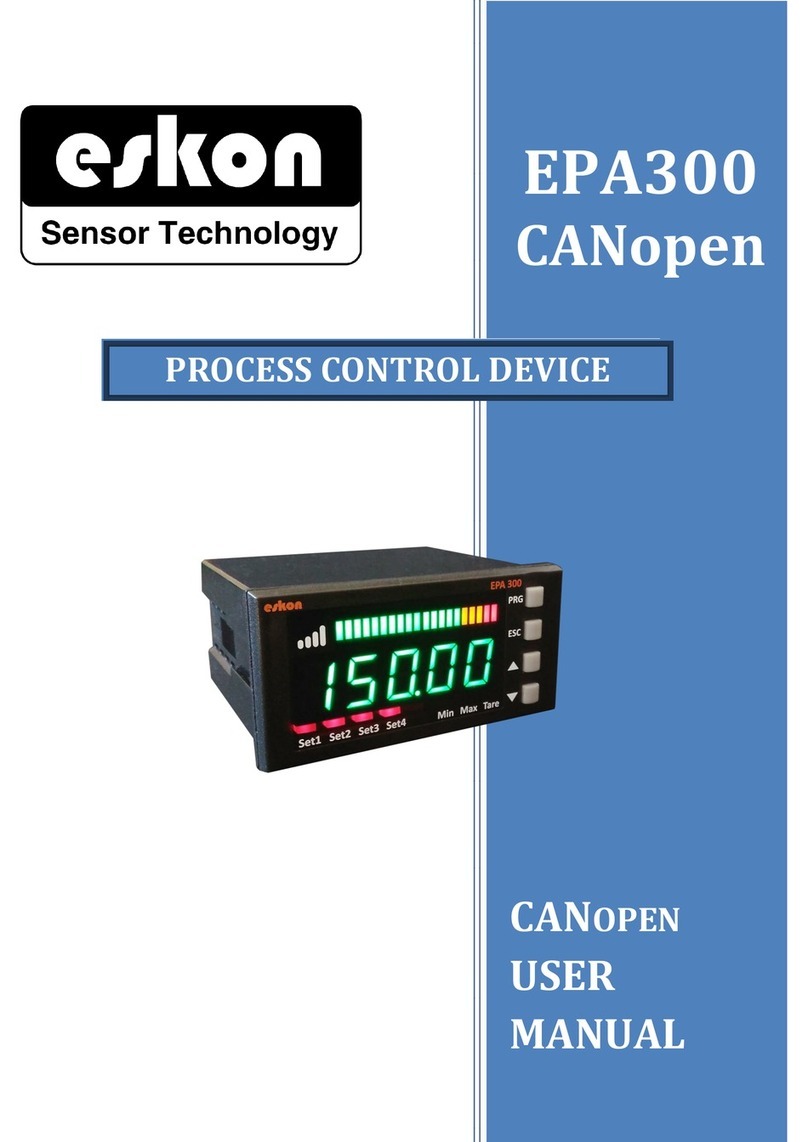
Eskon
Eskon EPA300 user manual

Zurn Wilkins
Zurn Wilkins ZW204 Installation, Troubleshooting, Maintenance Instructions
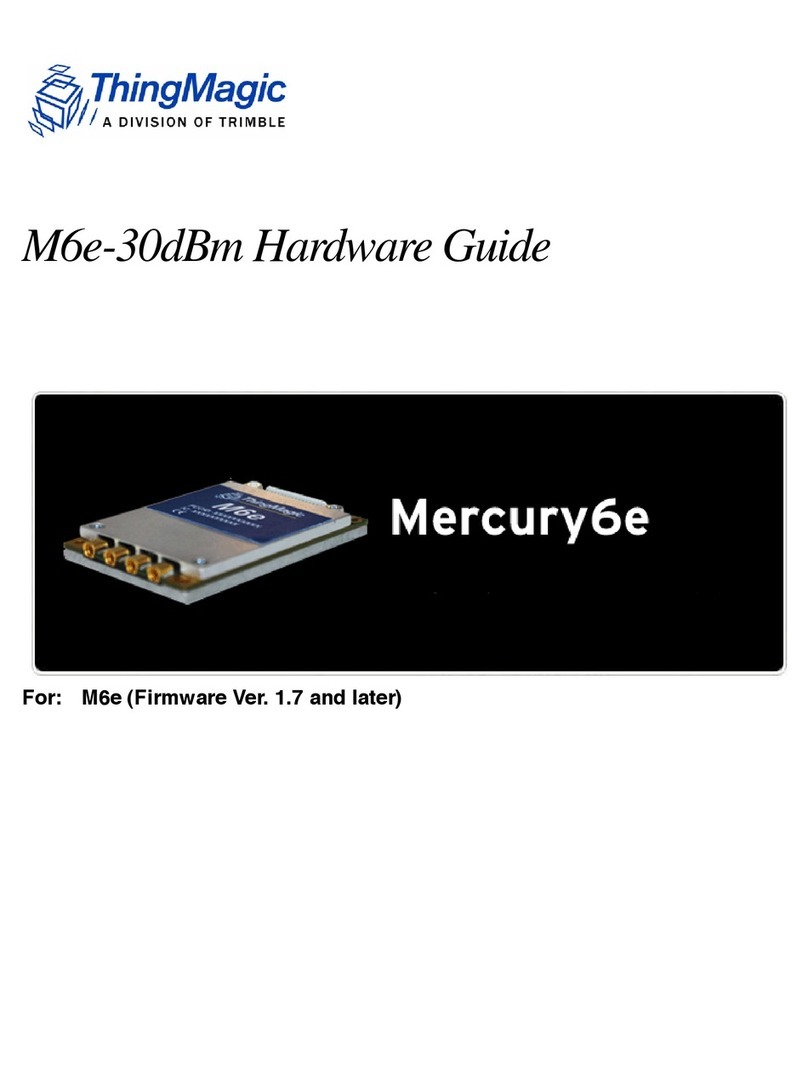
ThingMagic
ThingMagic Mercury6e M6e-30dBm Hardware guide
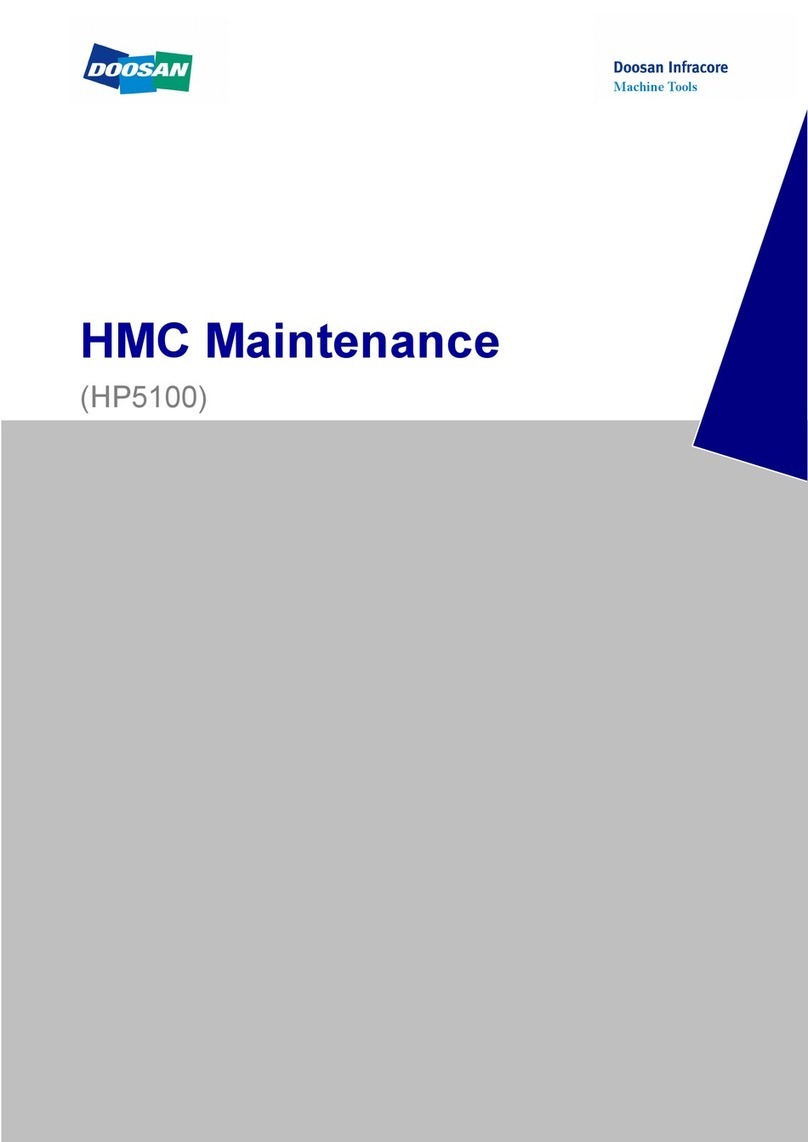
Doosan
Doosan HP5100 maintenance

NI
NI SCXI-1333 installation instructions