CNC LGW-CNC-13T User manual

CNC aluminum profile bending
machine
LGW-CNC-13T
Instruction manual

PREFACE
Thank you for using our production equipment, before you use the
equipment, please spare some time to read the manual, so that your
device is in the best running state, but also make your device to obtain
the best economic benefit.
We sincerely hope that you in the process of using the equipment,
the problems found and good suggestions timely feedback to us, so that
we can better work in the future cooperation.
Thank you!

一、Main application and applicable scope:
Use:Bending machine is used for irregular aluminum profile、rectangular iron
pipe bending,it is the decoration company,aluminum doors and windows company
bending arc of the machine.
二、The machine features:
1. The surface after bending is not deformed, without scratches or wrinkles, and the
straight edges and arcs at both ends of the product can achieve uniform transition
2. Profile can be bent and formed at one time, and the efficiency is particularly high;
3. 100 bending formula can be saved (different profiles, radians and various
parameters that have been saved), and can be used at any time;
4. colorful touch screen operation, imported industrial computer automation control,
clear interface, easy and simple operation;
5. High circuit stability, great applicability to the working environment, and has
automatic detection and diagnosis functions.
6, the profile curved arc mould is simple and practical, users can process it by
themselves.
三、 Equipment configuration
1, Control system: Japanese “Panasonic” controller
2, AC servo system: ESTUN servo driver and servo motor
3, Operation screen: Taiwan weinview Touch Screen
4. Electrical components: Schneider, France
5,Speed reducer: China production
6, the transmission device: China production
7, mechanical parts: China production
8,The mould: our company processing (customer could make themselves)
四、 The technical parameters
Model: LGW-CNC-13T
Input power: 4.0KW

Voltage: 380V 50Hz 3 phase
Min. radius of bending:100mm (relate to profile)
Max. processing profile size:120mm*150mm
Spindle diameter:50mm
Y axis Hydraulic thrust:13T, max. 20 tons
Max torque of X axis:2500N.M
Rotation speed of shaft:1-15r/min
Y axis push rod repeat positioning accuracy: ≤0.01mm
Total weight:900kg
Overall dimension:1500mm*1200mm*1400mm
五、Equipment installation
1, environmental requirements:
The machine should be installed in a dry clean, non corrosive gas, temperature 15 ~
35 degrees indoor hard cement ground.
2,The machine level adjustment:
By adjusting the bolt to adjust the bottom of the machine will be transferred to the
horizontal position of the machine. Specific requirements are: three the pressure
plate plane error is less than 1mm, the machine after adjusting the lock nut.
3, the machine is connected with the earth:
The machine must be based on the requirements of the electrical wiring diagram and
the connecting line is connected to earth, soft copper wire, its cross-sectional area
greater than 2.5 square mm, grounding resistance less than 4 ohm.
4, the machine power supply:
The machine input voltage: 380V 50HZ, connecting line for the soft copper wire, its
cross-sectional area greater than 2.5 square mm (three-phase four wire).
六、 Use and operation
1,The machine is connected to the power
Confirm the machine properly connected, open the power switch, the machine
electricity,operation screen appear as follows "the initial interface":

2, To enter the main interface
Press "ENGLISH" button in the initial screen, then press "INTO" key, the screen to
enter the password input interface, as shown in:
In the "password" interface, click the password input box, enter the password
"85761765", "the main interface of system":

In the main interface screen, click on each key, the operation panel is converted into
a corresponding interface.
3, Manual operation
In the "Main interface", click "Manual operation" button, the system appears the
following the manual operation interface:
In the "Manual" interface,
Click on the "Return" button, the system returns to the main interface
Click on the "←" or "→" arrow, can make the workpiece move to the left or right

Click on the "speed setting" , set the speed roller spindle rotation;
Click on the "up" or "down" arrow, the intermediate shaft move backward and
forward;
Click on the "home" button, can make the intermediate roll back to zero position;
Enter the data of”move to” and press the "ok" key to move the middle wheel to the
absolute position
Enter the data of”move” and press "OK" to move the middle wheel to the relative
position.
The icon “backward limit”,“forward limit”and “origin”of this interface are the
input signals of the Y-axis limit switch. Only when the limit switch is inductive, the icon
display color will change.
4, The system parameters
In the main interface, click on the "Paramater" button, the screen to enter the
"Parameter setting" interface, as shown in the following figure:
In the "Parameter setting" interface,click on the "Ruturn" button, the system returns to
the main interface
Each parameter interpretation:
Y speed setting:

"Manual" means that the speed of hydraulic cylinder to move the manual operation
"Start" said hydraulic cylinder move start speed
"forward speed" indicates the maximum speed of the cylinder when the cylinder is
positioned forward
"forward creeping" means the speed of the cylinder after it has decelerated before
moving to the target position
"Backward speed" indicates the maximum speed of the cylinder when the cylinder is
positioned backwards
"Backward creeping" means the speed of the cylinder after it decelerates before
moving to the target position
“reference point” means the speed of the oil cylinder's return after automatic
processing is completed;
Action in advance:
“Forward deceleration ”indicates the displacement of the cylinder after
deceleration during the forward positioning of the cylinder during automatic
processing;
"Backward deceleration" indicates the displacement of the cylinder after decelerating
when the cylinder is positioned backward during automatic processing
"Forward precision" indicates the number of pulses sent by the deceleration system
of the cylinder during the forward positioning of the cylinder during automatic
processing;
"Backward precision" means the number of pulses sent by the deceleration system of
the cylinder when the cylinder is positioned backward during automatic processing;
The others:
Auxiliary wheel diameter: The roller that moves with the curved profile, the accuracy
of its diameter determines the dimensional accuracy of the profile position;
Zero time delay: the time for the spindle to rotate after the automatic processing is
completed and the setback position is reversed;
Fixed wheel spacing D0: the distance between the left and right shafts;
X zero distance: the distance from the photoelectric sensor switch to the left axis;

Forward soft limit: the amount of displacement from the Y axis to the forefront;
Retreat distance: After the automatic processing is completed, the distance that the
moving wheel shaft retracts from the starting position;
Retreat sync length: After the automatic processing is completed, the Y-axis moves
backward from the end position to the starting position, and the corresponding
distance the workpiece moves in the discharge direction.
5, The auxiliary calculator
In the main interface, click on the " auxiliary " button, the screen to enter the "
Auxiliary calculator " interface, as shown in the following figure:
"Calculate" is for easy radius calculation in actual use, the parameters of arc is
encountered, through calculation, provide the basis for practical use;
Methods: the known length of chord "S",and arc height "H"
Calculate the radius parameter "R" and the arc length parameter "L"
6, Rebound calculator
"Rebound calculator" function is to correct the error by circular arc profile of the
rebound coefficient modification,
because the profiles of different sizes, the hardness of the material is different, so the
rebound coefficient profiles are also different, in the actual production process, the

rebound coefficient profiles for increase of bending radius increases,
it is a linear relationship between the irregular.
The coefficient of restitution of the input is a empirical data, in the processing of the
first workpiece, processing of the arc can not achieve the desired size, this needs to
be calculated by the "Rebound calculator" features a new rebound coefficient, so that
the processing of arc is more close to the demand.
In the main interface, click on the " Compensation " button, the screen to enter the
"Rebound calculator " interface, as shown in the following figure:
The methods used are as follows:
A、Fixed wheel radius RA: the minimum radius of the fixed shaft mold
B、Fixed wheel spacing: 350mm or other data
C、The target radius:The radius of the circular arc needed
D、The measurement radius :the measurement data of the radius measuring
instrument
Enter the radius: Through the "Auxiliary calculation" to calculate the radius
E、Old parameter K0: rebound coefficient data In profile formula
The input is completed, click the "calculate" button, the system will automatically

calculate the new parameter K1, in profile formula interface, the parameter of K1 to
replace the old K0 parameters, click on the "conserve" button, and then enter to
automatic processing.
7, Signal monitoring
In the main interface, click on the " diagnosis " button, the screen to enter the "
Diagnostic interface " interface, as shown in the following figure:
Through the "Diagnostic interface" interface can detect the input signal source
(button, stop button, the grating ruler, rotary encoder) is normal, the output signal
(solenoid valve, relay) is normal
8, C shape processing
select C formula corresponding to the automatic operation,in the main interface, click
on the " C shape formula" button, the screen to enter the " C formula " interface, as
shown in the following figure:

In the "C shape editor "interface, press the" + "or" - "button, can obtain the
corresponding formula, C shape processing can store 100 profile formula, in each
profile formula, enter the profile name, arc radius, arc length, fixed wheel radius RA,
rolling start position, rebound coefficient,etc. various parameters, press "save
formula" key, the formula automatically save, press "back" key, return to the main
interface, click on the "process" button, the screen switches to "C shape processing"
at the interface, which can automatically process. can also be in the "C shape
formula" interface press "Ent process" button to enter C shape automatic processing
interface.

C shape automatic processing steps: In "C shape processing" interface, press
the "PUMP" button, hydraulic station start,loosen the nut, the workpiece is placed
into the machine, press "AUTO start" button, the middle roller moves to the rolling
start point, then tighten the nut(no need very tight, suitable is ok), Again press to the
"AUTO start" button, the machine automatically start bending processing. Repeat the
above process, can be produced in large quantities. once finished, press the "pump"
button, the oil pump motor to stop, this time can turn off the power switch.
In "C shape processing" interface, you can set the find the reference speed and
bending speed.(1~15r/min)
9.U-shaped processing
In the "Main Interface", press the "U-shaped formula" key, and the system enters the
"U-shaped formula" interface:
In the "U-shaped recipe" interface, press the "+" or "-" key to call the corresponding
recipe. U-shaped processing can store 100 profile formula. In each formula, enter the
profile name, arc radius, Wheel radius, starting cylinder position, and other
parameters. Press the "save formula" key, and the formula is automatically stored in
the "U-shaped processing" interface. Press the "back" key to return to the "Main
Interface" screen, and then press the "process" key , The screen changes to the

"U-shaped processing" interface, and it can be processed automatically.
U shape automatic processing steps: In "U shape processing" interface, press the
"PUMP" button, hydraulic station start,loosen the nut, the workpiece is placed into
the machine, press "AUTO start" button, the middle roller moves to the rolling start
point, then tighten the nut(no need very tight, suitable is ok), Again press to the
"AUTO start" button, the machine automatically start bending processing. Repeat the

above process, can be produced in large quantities. once finished, press the "pump"
button, the oil pump motor to stop, this time can turn off the power switch.
In "U shape processing" interface, you can set the find the reference speed and
bending speed.
10、3R shape processing
In the "Main Interface", press the "3R shape formula" key, and the system enters the
"3R shaped formula" interface:
In the "3R shaped recipe" interface, press the "+" or "-" key to call the corresponding
recipe. 3R shaped processing can store 100 profile formula. In each formula, enter
the profile name, arc radius, Wheel radius, starting cylinder position, and other
parameters. Press the "save formula" key, and the formula is automatically stored in
the "3R shaped processing" interface. Press the "back" key to return to the "Main
Interface" screen, and then press the "process" key , The screen changes to the "3R
shaped processing" interface, and it can be processed automatically.
3R shape automatic processing steps: In "3R shape processing" interface, press the
"PUMP" button, hydraulic station start,loosen the nut, the workpiece is placed into
the machine, press "AUTO start" button, the middle roller moves to the rolling start
point, then tighten the nut(no need very tight, suitable is ok), Again press to the

"AUTO start" button, the machine automatically start bending processing. Repeat the
above process, can be produced in large quantities. once finished, press the "pump"
button, the oil pump motor to stop, this time can turn off the power switch.
In "3R shape processing" interface, you can set the find the reference speed and
bending speed.
七.Maintenance
In order to keep the arc bending machine working continuously, reliably reduce the
damage of the parts, and extend the service life, the maintenance system of the arc
bending machine must be implemented.
1. Daily maintenance: once every shift.
1.1 Check the tightening bolts and nuts everywhere.
1.2 Check the connection of various agencies. If there is any abnormality, it should be
cleared. Lubricates horizontal slide rails and retractable universal joints.
1.3 Check the electrical system: After turning on the power, check the rotation
direction and operation of the motor.
1.4 Keep the arc bender tidy and clean the dirt inside the arc bender frequently.
1.5 The hydraulic oil (46 # wear-resistant) in the hydraulic station is replaced every
six months.
2, technical maintenance: check the mould to ensure that the mould is intact without
damage.
Other CNC Cutter manuals
Popular Cutter manuals by other brands
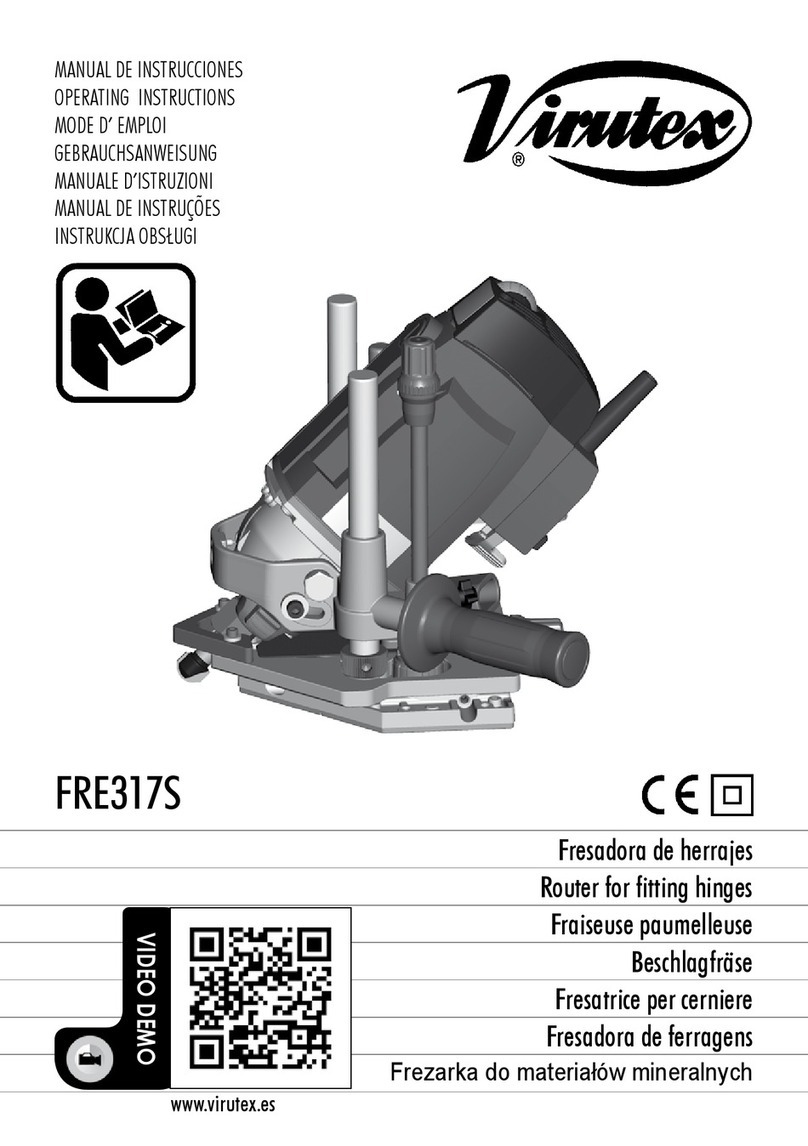
Virutex
Virutex FRE317S operating instructions
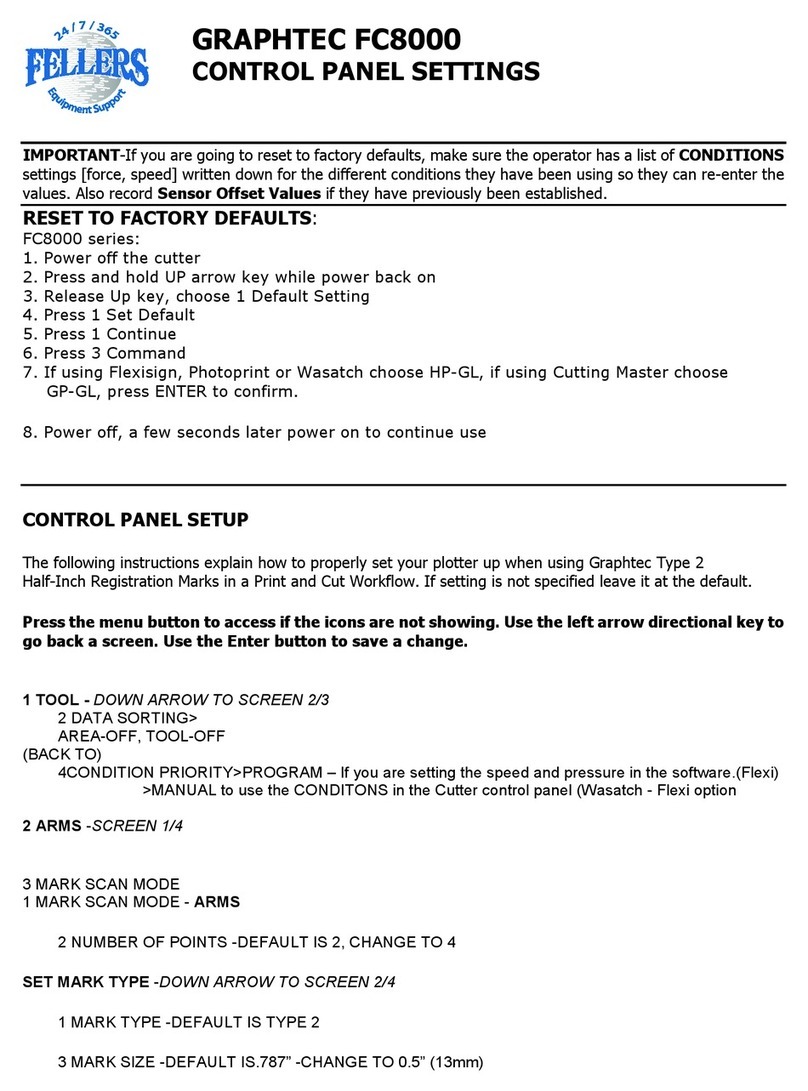
GRAPHTEC
GRAPHTEC FC8000 Series quick start guide
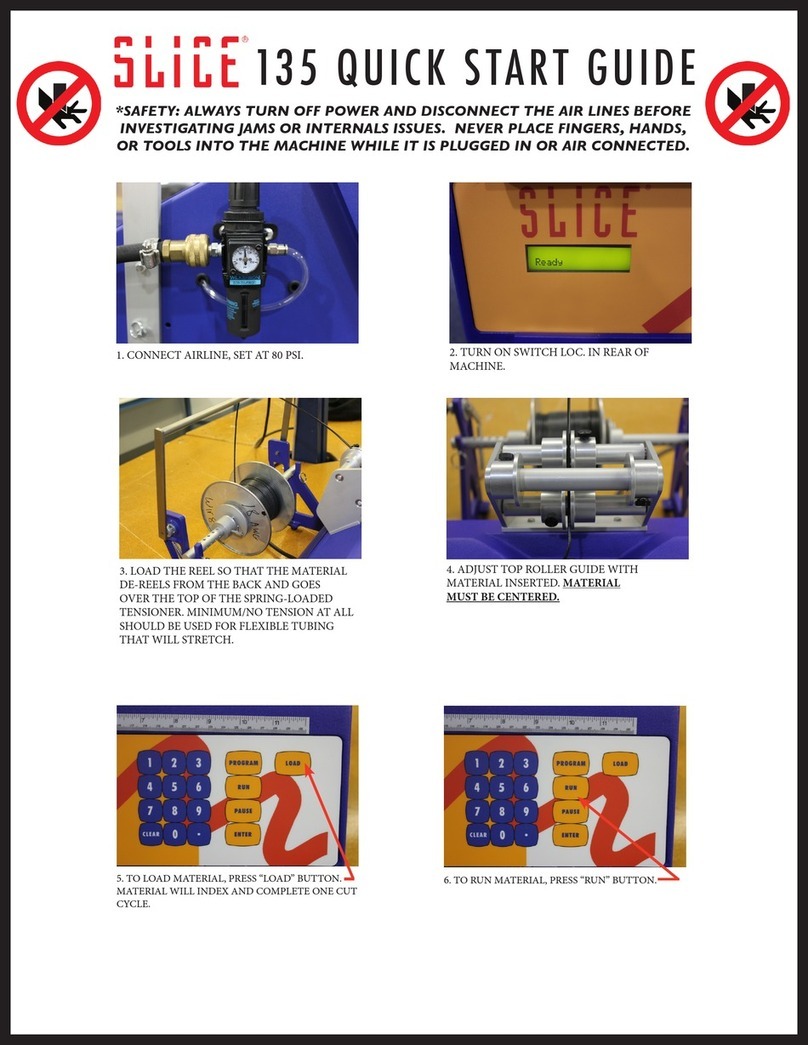
AMTI Products
AMTI Products SLICE 135 quick start guide

Campbell Hausfeld
Campbell Hausfeld IN281600AV operating instructions
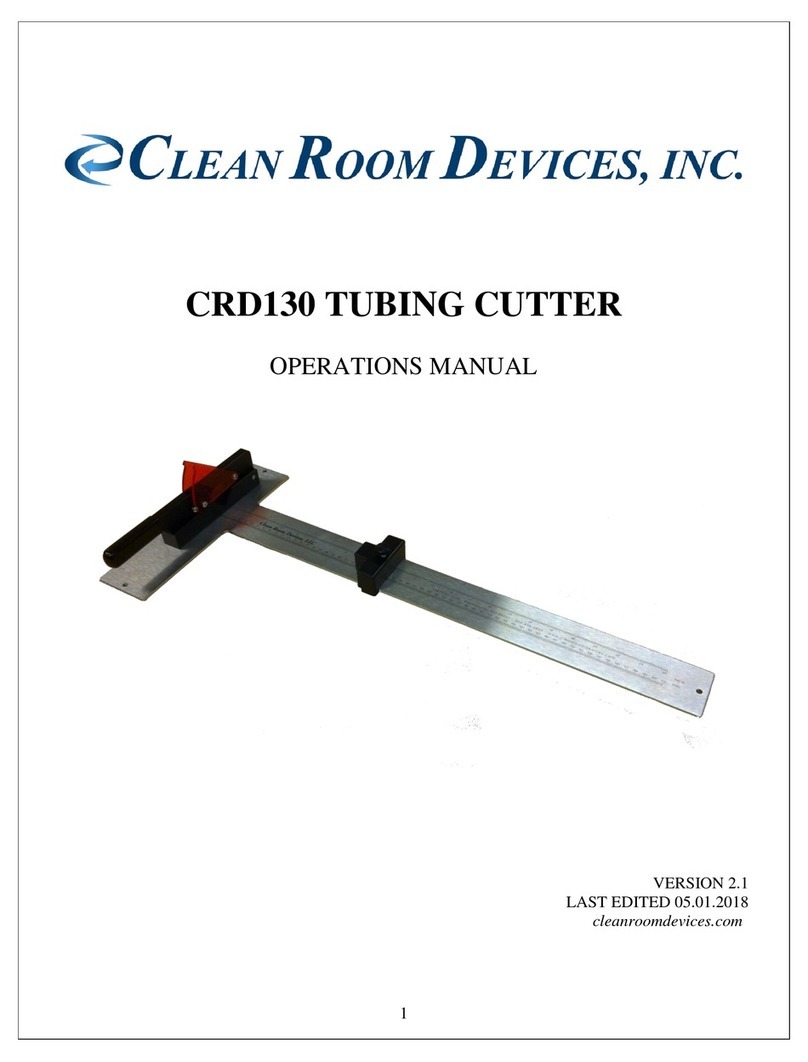
CLEAN ROOM DEVICES
CLEAN ROOM DEVICES CRD130 Operation manual
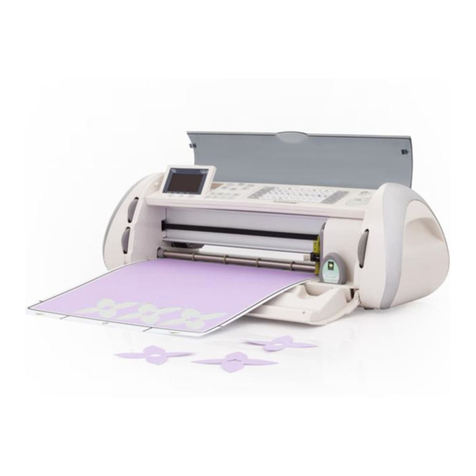
Cricut
Cricut expression user manual