Compac CNG Manual

Compac Industries Ltd.
52 Walls Road. Penrose. Auckland 1061, New Zealand.
PO Box 12 417 Penrose. Auckland 1642. New Zealand.
www.compacngv.com
Compac Industries Ltd.
52 Walls Road. Penrose. Auckland 1061, New Zealand.
PO Box 12 417 Penrose. Auckland 1642. New Zealand.
Tel: +64 9 579 2094 Fax: +64 9 579 0635 info@compacngv.com
www.compacngv.com
CNG Loading Post Installation and
Service Manual
Version 1.0.0

Conditions of Use
Compac Industries Ltd.
Page 2
www.compacngv.com
Conditions of Use
Read this manual completely before working on, or
making adjustments to, the Compac equipment
Compac Industries Limited accepts no liability for
personal injury or property damage resulting from
working on or adjusting the CNG equipment
incorrectly or without authorisation.
Along with any warnings, instructions, and
procedures in this manual, you should also observe
any other common sense procedures that are
generally applicable to equipment of this type.
Failure to comply with any warnings, instructions,
procedures, or any other common sense procedures
may result in injury, equipment damage, property
damage, or poor performance of the Compac
equipment
The major hazard involved with operating this
Compac CNG unit is electrical shock. This hazard
can be avoided if you adhere to the procedures in
this manual and exercise all due care.
Compac Industries Limited accepts no liability for
direct, indirect, incidental, special, or consequential
damages resulting from failure to follow any
warnings, instructions, and procedures in this
manual, or any other common sense procedures
generally applicable to equipment of this type. The
foregoing limitation extends to damages to person or
property caused by the Compac CNG unit, or
damages resulting from the inability to use the
Compac CNG equipment, including loss of profits,
loss of products, loss of power supply, the cost of
arranging an alternative power supply, and loss of
time, whether incurred by the user or their
employees, the installer, the commissioner, a
service technician, or any third party.
Compac Industries Limited reserves the right to
change the specifications of its products or the
information in this manual without necessarily
notifying its users.
Variations in installation and operating conditions
may affect the performance of Compac CNG
equipment. Compac Industries Limited has no
control over each installation's unique operating
environment. Hence, Compac Industries Limited
makes no representations or warranties concerning
the performance of the Compac CNG equipment
under the actual operating conditions prevailing at
the installation. A technical expert of your choosing
should validate all operating parameters for each
application.
Compac Industries Limited has made every effort
to explain all servicing procedures, warnings, and
safety precautions as clearly and completely as
possible. However, due to the range of operating
environments, it is not possible to anticipate every
issue that may arise. This manual is intended to
provide general guidance. For specific guidance
and technical support, contact your authorised
Compac supplier, using the contact details in the
Product Identification section.
Only parts supplied by or approved by Compac
may be used and no unauthorised modifications to
the hardware of software may be made. The use of
non-approved parts or modifications will void all
warranties and approvals. The use of non-
approved parts or modifications may also constitute
a safety hazard.
Information in this manual shall not be deemed a
warranty, representation, or guarantee. For
warranty provisions applicable to the Compac CNG
equipment, please refer to the warranty provided
by the supplier.
Unless otherwise noted, references to brand
names, product names, or trademarks constitute
the intellectual property of the owner thereof.
Subject to your right to use the Compac CNG
equipment, Compac does not convey any right,
title, or interest in its intellectual property, including
and without limitation, its patents, copyrights, and
know-how.
Every effort has been made to ensure the accuracy
of this document. However, it may contain technical
inaccuracies or typographical errors. Compac
Industries Limited assumes no responsibility for
and disclaims all liability of such inaccuracies,
errors, or omissions in this publication.

Page 3
Contents
Conditions of Use ............................................................................................................................................................. 2
Product Identification ....................................................................................................................................................... 5
Document Control Information ........................................................................................................................................ 6
Symbols and Units of Measure ........................................................................................................................................ 7
Safety ................................................................................................................................................................................. 8
Introduction .............................................................................................................................................................. 9
Mechanical Installation ................................................................................................................................................... 10
Preparing and Cleaning Pipework.......................................................................................................................... 11
Mounting the Loading post..................................................................................................................................... 12
Connecting the Pipework ....................................................................................................................................... 13
Electrical Installation ...................................................................................................................................................... 13
CNG Cable Requirements ..................................................................................................................................... 13
Connecting Mains Power ....................................................................................................................................... 14
Electrical Commissioning .............................................................................................................................................. 15
Mechanical Commissioning ........................................................................................................................................... 16
Set-up............................................................................................................................................................................... 17
Parameter switch ................................................................................................................................................... 17
K-Factor Switch...................................................................................................................................................... 17
C Configuration Code ............................................................................................................................................ 20
Reading the Loading Post Totals ........................................................................................................................... 21
CNG Loading ......................................................................................................................................................... 22
Servicing .......................................................................................................................................................................... 23
Degassing the Loading post................................................................................................................................... 23
Scheduled Servicing .............................................................................................................................................. 24
Solenoid Valve Seal Replacement......................................................................................................................... 27
Solenoid Coil Replacement.................................................................................................................................... 30
Compac Breakaway Seal Replacement................................................................................................................. 31
Three Way Refuelling Valve Seal Replacement .................................................................................................... 32
Refuelling Hose Replacement................................................................................................................................ 34
Power Supply Replacement................................................................................................................................... 35
C4000 Processor Board Replacement................................................................................................................... 36
Software Upgrade/Replacement ............................................................................................................................ 37
Meter Replacement................................................................................................................................................ 38
Unserviceable Parts List ........................................................................................................................................ 39
Loading post Calibration ................................................................................................................................................ 40
Meter Calibration.................................................................................................................................................... 40
Indicator LEDs ....................................................................................................................................................... 42
Power and Watchdog LEDs ................................................................................................................................... 42
Diagnostic and Output LEDs.................................................................................................................................. 43
Troubleshooting.............................................................................................................................................................. 44
Problems When Post is Idle ................................................................................................................................... 45
Problems Starting a Fill .......................................................................................................................................... 46

Conditions of Use
Compac Industries Ltd.
Page 4
www.compacngv.com
Problems Filling ..................................................................................................................................................... 47
Solenoid Problems................................................................................................................................................. 48
Appendix.......................................................................................................................................................................... 49
Approvals............................................................................................................................................................... 49
Specifications.................................................................................................................................................................. 50
Technical Specifications ........................................................................................................................................ 50
Component Specifications ..................................................................................................................................... 51
Hydraulic Layout –Loading Post ........................................................................................................................... 53
Spare parts ...................................................................................................................................................................... 55
Loading post Spare Parts....................................................................................................................................... 55
Fuses ..................................................................................................................................................................... 56
Error Codes ..................................................................................................................................................................... 57
End of Sale Indicators............................................................................................................................................ 59

Product Identification
Compac Industries Ltd.
Page 5
www.compacngv.com
Product Identification
Manual Title
CNG Loading post Installation and Service Manual
Publication Date
05/05/2014
Models Covered
CNG Loading post
Application
Compressed Natural Gas
Power Supply
Air Supply Pressure
275 or 350 bar Max
220 - 240 VAC 50 Hz 2 Amp +/-
10%
5 to 10 bar ( Only required for units
with air actuated valves)
Related Manuals
Title
Publication Date
Validity
Compac Industries Limited reserves the right to revise or change
product specifications at any time. This publication describes the state of
the CNG Loading post at the time of publication and may not reflect the
product at all times in the past or in the future.
Manufacturer Contact
Details
The Compac CNG Loading post is designed and manufactured by:
Compac Industries Limited
52 Walls Road, Penrose, Auckland 1061, New Zealand
P.O. Box 12-417, Penrose, Auckland 1641, New Zealand
Phone: + 64 9 579 2094
Fax: + 64 9 579 0635
www.compacngv.com
Copyright ©2014 Compac Industries Limited, All Rights Reserved

Document Control Information
Compac Industries Ltd.
Page 6
www.compacngv.com
Document Control Information
Document Information and Revision History
Document Details
Compac Loading Post Installation and Service Manual
File Name and Location
Current Revision Author(s)
R Lacey
Authorised By:
Release Date:
Version
Date
Author(s)
Revision Notes
1.0.0
05/05/2014
R Lacey
New manual

Symbols and Units of Measure
Compac Industries Ltd.
Page 7
www.compacngv.com
Symbols and Units of Measure
Symbols
Symbols are used in this manual to highlight information that is critical
to the safety of people and equipment, and for the safe and correct
operation of the Compac equipment
An extreme hazard that may result in death or injury if
proper precautions are not taken.
A reminder of safety practices or unsafe practices that
could result in personal injury or damage to associated equipment.
A reminder of safety practices or unsafe practices that
could result in damage to associated equipment and/or voids the
warranty.
Important information essential to the installation and
operation of the Compac equipment
Units of Measure
The following units of measure are used in this manual:
Unit
Measure
Pressure
Bar (bar)
Temperature
Degrees Celsius (°C)
Volume
Litres (l)
Cubic Metres (m³)
Mass
Kilograms (kg)
Length
Metres (m)
Millimetres (mm)
Microns, Micrometres (m)
Inches (")
Torque
Newton Metres (Nm)
Voltage
Volts (V)
Current
Amps (A)
Frequency
Frequency (Hz)

Safety
Compac Industries Ltd.
Page 8
www.compacngv.com
Safety
You must adhere to the following safety precautions at all times when
working on the Compac equipment. Failure to observe these safety
precautions could result in damage to the loading post, injury, or death.
Make sure that you read and understand all safety precautions before
installing, servicing or operating the Compac equipment.
System Design
Ensure the system design does not allow the inlet pressure
to exceed its rating. The unit does not include any safety features to protect
against excessive inlet pressure. If necessary, suitable protective devices
should be fitted before the inlet.
Mechanical Safety
Observe the following electrical precautions:
Never tighten a fitting under pressure, even if a fitting or joint
is leaking. Always depressurise the line first
Never disassemble a fitting under pressure. Always
depressurise the line first
Be very careful when disassembling frozen pipework, as gas
pressure may be trapped and suddenly released. Always depressurise the
lines first.
Never reuse any O-ring seals that have been in a high
pressure gas atmosphere and then exposed to air. These o-rings swell and
cannot be reused. Always make sure you have a new seal kit available to
replace the seals before disassembly
Make sure that all internal surfaces are cleaned and that
sliding surfaces are lightly greased with O-ring lubricant before reassembly.
Dust and dirt entering components reduce the life span of the components
and can affect operation
Make sure the service area is thoroughly cleaned before
starting to service CNG components. Dust and dirt entering components
reduce the life span of the components and can affect operation
Electrical Safety
Observe the following electrical precautions:
Always turn off the power to the CNG unit before removing
the box lid. Never touch wiring or components inside the CNG Loading
post with the power on.
Never power up the CNG unit with the flameproof box lid
removed.
Always turn off the power to the unit before removing or
replacing software or memory IC's
Always take basic anti-static precautions when working on
the electronics, i.e., wearing a wristband with an earth strap.

Safety
Introduction
Compac Industries Ltd.
Page 9
www.compacngv.com
Introduction
The Compac CNC loading post is designed to provide safe and reliable
metered filling of CNG tanks from a supply tank.
Compac CNG loading posts are controlled by a C4000 board and use the
reliable Compac KG80 flow meter.
This manual contains the information required to operate and maintain your
loading post. Due to ongoing improvements and customised designs, there
may be software features that are not available on your particular unit.
The manual may refer to loading posts. Unless otherwise noted, this refers
to the loading post.
For clarity, this manual will refer to the "Dollars" display. If you do not use
dollars please substitute this for your local currency.

Mechanical Installation
Compac Industries Ltd.
Page 10
www.compacngv.com
Mechanical Installation
Overview
The stages of mechanical installation include:
Preparing and cleaning the pipework (see page 11).
Mounting the loading post.
Connecting the pipework (see page 13).
Special Precautions
Ensure the system design does not allow the loading post
inlet pressure to exceed its rating. The loading post does not include any
safety mechanisms to protect against excessive inlet pressure. If
necessary, suitable protective devices should be fitted prior to the loading
post inlet.
Take all possible steps to prevent water or dirt from entering
the system, both during installation and in the future. Water and dirt blocks
up the pipework, which can damage seals, and stop gas from flowing and
valves from operating.
At 200 bar of pressure, water freezes at 15°C in natural gas,
causing ice particle contamination.
Seals that have been damaged by moisture, methanol,
impurities, dirt slag etc, are not covered by warranty.
During installation, potential sources of water include:
Inlet gas.
Testing new inlet gas pipework with water, or allowing water to enter
the pipework before making the final connections.
Pumping the storage with air.
Allowing water to enter the high-pressure gas lines during installation.
If the inlet gas is likely to be saturated, install a gas drier into the
compressor inlet to ensure a dew point of –32°C at 250 bar of pressure.
Do not use methanol as an anti-freeze. If used in the wrong
concentrations, it causes freezing. It is also absorbs water, which can be
more damaging than the water that was originally present.
Pipework
Check the high points and low points of the
pipework distribution system to make sure
that:
Vents have been provided on all high
points.
Drains have been provided on all low
points.

Mechanical Installation
Preparing and Cleaning Pipework
Compac Industries Ltd.
Page 11
www.compacngv.com
Preparing and Cleaning Pipework
This section provides a guide to current best practice in preparing the distribution
pipework that will be connected to the Compac Loading post.
For new stations, flush the gas feed lines thoroughly to remove all welding slag,
moisture, and impurities that may be present in the system.
Any steel, brass, or other impurities can damage the regulator and solenoid valve
seals.
The pipework installer is responsible for installing all pipework to
the post with care. Compac is not responsible for any pipework external to the
loading post.
Ensure that all pipework is completely clean. Any dirt trapped in the
pipework can damage the valve seals and surfaces.
Clean and Degrease the
Pipework
To clean and degrease the pipework:
To prepare pipework, purge the pipework with nitrogen at 200 bar vented to the
atmosphere to remove dirt, moisture, and water.
1. Mix together a 10% hydrochloric acid solution, to which you have added 25%
to 50% ammonia bi-fluoride and heat to a minimum of 65°C.
Wear adequate safety gear and take adequate precautions
when using chemicals. Clean up all spills in compliance with the local territory
authority laws and regulations.
2. Circulate the mixture through the pipework for four hours or more, depending
on the condition of the pipework.
3. Drain the acid solution from the pipework.
4. Blow out the pipework with compressed air.
5. Flush the pipework with clean water until the pH value is neutral.
Neutralise the Pipework
To neutralise the pipework:
1. Pass a 25% citric acid solution through the pipework once, or dry out the
pipework by blowing hot air through it.
Wear adequate safety gear and take adequate precautions
when using chemicals. Clean up all spills in compliance with the local territory
authority laws and regulations.
2. Fill the pipework with seal oil, then drain.
3. Blow out the pipework with compressed air.
4. Blast the pipes with nitrogen at 200 bar, letting the gas expand through the
pipes.
5. Once the pipework is cleaned, seal off the system to ensure no water, dirt or
other contaminates can re-enter the pipework.
Keep the pipework venting open to the atmosphere and feed in
the 200 bar of nitrogen to achieve maximum velocity.
Take care to keep pipe openings closed until the compressor is
started. This prevents rusting of the pipework, and stops dirt from entering.

Mounting the Loading post
Mechanical Installation
Compac Industries Ltd.
Page 12
www.compacngv.com
Mounting the Loading post
To mount the loading post:
1. Make sure that the post is located on a solid, horizontal foundation or plinth.
2. Seal the pipes to prevent dirt, moisture, or water from entering during the
mounting process.
3. Mark out the mounting points on the foundation, using the correct footprint
diagram for the model of loading post being installed.
4. Secure the loading post with 12 mm dynabolts and washers. 12 mm
dynabolts have the required strength to hold the unit but up to 16 mm
dynabolts can be used in the 19 mm footprint holes.

Electrical Installation
Connecting the Pipework
Compac Industries Ltd.
Page 13
www.compacngv.com
Connecting the Pipework
1. Make sure that your work area (including the vice, workbench, tool storage
area, and floor) is totally clean of particles or previous work. Cleanliness
and correct assembly practice can avoid most seal problems.
2. Make sure that the gas outlet pipes are properly supported before
connection.
Electrical Installation
CNG Cable Requirements
Cable requirements are as follows:
Cable Type
Requirement
Power
3 Core Steel Wire Armour Cable 2.5mm2,
220 - 240 Volts. 50 Hz, +/-10%
Core 1: 230 Volt Supply (Active).
Core 2: Neutral.
Core 3: Earth.
Power Consumption
25w Idle, 200W with all solenoids active.
Make sure that there is at least a two metre cable tail on both
the incoming underground 230 V cables to reach the C4000 flameproof box.

Connecting Mains Power
Electrical Installation
Compac Industries Ltd.
Page 14
www.compacngv.com
Connecting Mains Power
In sites where the electrical supply is unstable, it is
recommended that a power conditioner or UPS is installed.
To connect the loading post:
1. Wire the power to the C4000 Termination Board, as shown in the
diagram below. (Comms option is not available)
2. Connect the earth lead of the supply cable to the earth stud in the
flameproof junction box.
All cables must be terminated with approved flameproof
glands. The thread is 20 mm.
Typical wiring

Electrical Commissioning
Compac Industries Ltd.
Page 15
www.compacngv.com
Electrical Commissioning
This procedure outlines how to perform an electrical operational test
before carrying out full mechanical commissioning, making sure that the
loading post is functioning correctly. Check for any damage that may
have occurred in transit. Check all terminals, plugs, and chips to make
sure that they are securely in place.
Damage to electronics occurs most commonly from
vibration and jarring.
Before beginning this test, check that no gas pressure has been applied
to the loading post inlets. The factory set-up information should be
programmed into the loading post but all K-factor and Parameter switch
settings should be checked and confirmed before commissioning tests
are carried out.
To perform an electrical operational test:
1. Make sure that the inlet shut-off valves are closed (these are the
valves in the inlet lines at the base of the loading post, but they are
not part of the loading post).
2. Turn on the power supply to the loading post.
The displays and backlighting will illuminate, and the displays read
PA:uS:E, then count down for one minute.
The loading post is in a ready state once the countdown is finished
and the display shows 0.00.
3. With the loading post in a ready state, check that the C4000
Microprocessor Power LED (D1) is turned on
4. Press the Start button.
The display will show 888888 and the solenoids energise, initiating
a fill. Check that Diodes D8, D10 and D11 turn on, indicating a
signal is being sent to the triacs to open the solenoid valves.
The diagnostic LED (D18) flashes quickly when the start button is
pushed to initiate a fill.
5. Verify solenoid operation by listening for a click, or by using a
screwdriver tip or some other metallic tool to check for a magnetic
field present on the solenoid coils.
The solenoids will switch off after one minute. This is a default time-
out setting in the software for situations when there is no gas flow
registered.
6. Press the Stop button. The solenoids switch off and the fill ends.
When you release the Stop button, the loading post resets and
returns to a ready state.

Mechanical Commissioning
Compac Industries Ltd.
Page 16
www.compacngv.com
Mechanical Commissioning
At the mechanical commissioning stage, the loading post should not be
pressurised.
If you find any leaks during commissioning, immediately close
all of the valves and de-gas the post (see page 23).
To perform a mechanical test:
1. Make sure that the outlet shut-off valves are closed. (These are the
valves in the lines at the base of the post, but they are not part of the
post.)
2. Check all post fittings, especially the outlet connections, to make sure
that they are tight.
Always de-gas the lines before tightening any fittings.
Never tighten fittings while they are under pressure.
3. Check that the outlet supply valve is closed and the nozzle valve is
closed.
4. Connect the nozzle to a tank containing CNG.
5. Turn on the post and wait for it to power up.
The loading post initially displays PA:uSE. When it is ready, 0.00 is
displayed.
6. Press the Start button.
If you are commissioning a dual hose loading post, press
the Start button on either side. This opens the loading post's solenoids.
The loading post automatically shuts off after approximately one minute
if no flow is detected.
7. Slowly open the inlet shut-off valves and listen for leaks. If you hear
leakage, shut off the inlets immediately. If the loading post shuts off
during this process, shut off the inlet valves, restart the loading post,
and continue.
8. Once the inlet valves are fully open, allow the loading post to time out
on the 1 minute no-flow timer and shut the solenoid valves, or manually
shut it down and close the solenoid valves by pressing the Stop button.
9. Press the Start button on the loading post.
10. Slowly open the outlet isolation valve on the side of the loading post
and listen for leaks. If you hear leakage, shut the valve immediately.
If the loading post shuts off during this process then shut the outlet
supply valve, restart the loading post, and continue.
11. Repeat steps 8 and 9 for the second hose on a dual hose loading post.
12. Once the outlet isolation valves are fully open, allow the loading post to
time out on the 1 minute no-flow timer and shut the solenoid valves, or
manually shut it down and close the solenoid valves by pressing the
Stop button.
The loading post and hose(s) are now fully pressurised.
13. Use soapy water to check all fittings (including the hose fittings) for
leaks.
Always de-gas the lines before tightening any fittings.
Never tighten fittings while they are under pressure.
14. Complete a few fills on a test cylinder, checking for leaks or unusual
operation.

Set-up
Parameter switch
Compac Industries Ltd.
Page 17
www.compacngv.com
Set-up
The parameter and K-Factor switches on the C4000 board are used to set
up and calibrate the post.
Parameter switch
The loading post is pre-programmed and the parameter switch would not
normally be used. Information on this switch can be found on the C4000
manual.
K-Factor Switch
The K-Factor switch is located on the C4000 indicator board. You can use
this switch to set the density factor (changing the units the display reads in)
and the meter calibration.
Figure 1: Parameter and K-Factor
switches.

K-Factor Switch
Set-up
Compac Industries Ltd.
Page 18
www.compacngv.com
Density Factor
The density factor (dSF)is used to set the format of the quantity that is
displayed. For kilograms, a density factor of 1.000 is used. For other
units of measure, different density factors are required.
To determine the correct density factor for the unit of measure you would
like to use on the read-out, consider the following:
The loading post read-out displays the measured quantity in
KG divided by the density factor.
When the required unit of measure is kg the density factor
should be set to 1. In this case the display will show the
measured quantity in kg
When another unit of measure is required, the density factor
should be set to the ratio between the required unit of measure
and kgs. In this case the display will show the measured
quantity (kg) / density factor (unit of measure/kg )
For example if you wish to show the display in pounds:
1 pound = 0.4535 Kg so the density factor is entered as 0.4535. If 1 Kg is
now dispensed the display will now read 1 / 0.4535 = 2.205 pounds.
Adjusting the Density factor
1. Make sure that the loading post is idle.
2. Open the access panel and remove the cover of the C4000
processor box.
3. Press the K-Factor switch once and release.
The display shows dSF X.XXXX, which is the current density factor
setting for the loading post that you are commissioning.
4. Enter the required Density Factor.
Each press of the K-Factor switch passes you over a digit
in a setting, making the digit blink. Holding the switch down for more than
a second changes whichever digit is currently displayed. If you want to
pass over a setting without changing any digits, keep pressing and
releasing the switch.
Meter K-Factor
The meter K-Factor (F)is a meter correction factor used to ensure the
displayed quantity is correct.
The K-Factor is set during the calibration phase Meter Calibration (see
page 40) and does not require adjusting during service.
To adjust the meter K-Factor
1. Make sure that the loading post is not in use.
2. Press and release the K-Factor switch until the required K-factor is
shown (F)
3. Enter the required K-Factor.
Each press of the K-Factor switch passes you over a
digit in a setting, making the digit blink. Holding the switch down for
more than a second changes whichever digit is currently displayed. If
you want to pass over a setting without changing any digits, keep
pressing and releasing the switch.

Set-up
K-Factor Switch
Compac Industries Ltd.
Page 19
www.compacngv.com
Minimum Flow Rate
The minimum flow rate (LFA) is the low flow cut-off at the end of the
fill.
These values are adjustable and can be set between 0.5 - 9.9 kg/min.
Do not set the minimum flow rate so that it is equal to or
above the maximum flow rate.
To adjust the Minimum Flow Rate
1. Make sure that the loading post is idle, with the nozzle in its holster.
2. Press and release the K-Factor switch until the required minimum
flow rate is displayed. ( LFA )
3. Enter the new minimum flow rate.
Each press of the K-Factor switch passes you over a
digit in a setting, making the digit blink. Holding the switch down for
more than a second changes whichever digit is currently displayed.
If you want to pass over a setting without changing any digits, keep
pressing and releasing the switch.
The Compac factory default setting is 1.0 kg/min.
4. Let the menu time out so that the value and quantity amounts are
displayed.
Maximum Flow Rate
The maximum flow rate (HFA) is the high flow cut-off for when the flow
through the post is too high.
These values are adjustable and can be set between 5 - 99 kg/min.
Do not set the maximum flow rate so that it is equal to or
below the minimum flow rate.
To adjust the Maximum Flow Rate
1. Make sure that the post is not in use.
2. Press and release the K-Factor switch until the required maximum flow
rate is displayed. (HFA )
3. Enter the new maximum flow rate.
Each press of the K-Factor switch passes you over a digit
in a setting, making the digit blink. Holding the switch down for more
than a second changes whichever digit is currently displayed. If you
want to pass over a setting without changing any digits, keep pressing
and releasing the switch.
The Compac factory default setting is 40 kg/min or 60
kg/min depending on application.
4. Let the menu time out so that the value and quantity amounts are
displayed.

C Configuration Code
Set-up
Compac Industries Ltd.
Page 20
www.compacngv.com
C Configuration Code
The C configuration code (C) changes the operation of the loading post. It
is the last setting accessed through the K-Factor switch. The configuration
code has been factory set and should not be changed. If the memory gets
wiped and you need to re-enter it, the configuration is written on the yellow
label on the C4000 processor board cover.
To adjust the C Configuration Code
1. Make sure that the post in not in use.
2. Press and release the K-Factor switch until C is displayed.
3. Enter the new C configuration see diagram below.
Each press of the K-Factor switch passes you over a digit
in a setting, making the digit blink. Holding the switch down for more than
a second changes whichever digit is currently displayed. If you want to
pass over a setting without changing any digits, keep pressing and
releasing the switch.
4. Let the menu time out so that the value and quantity amounts are
displayed.
Other manuals for CNG
2
Table of contents
Other Compac Dispenser manuals
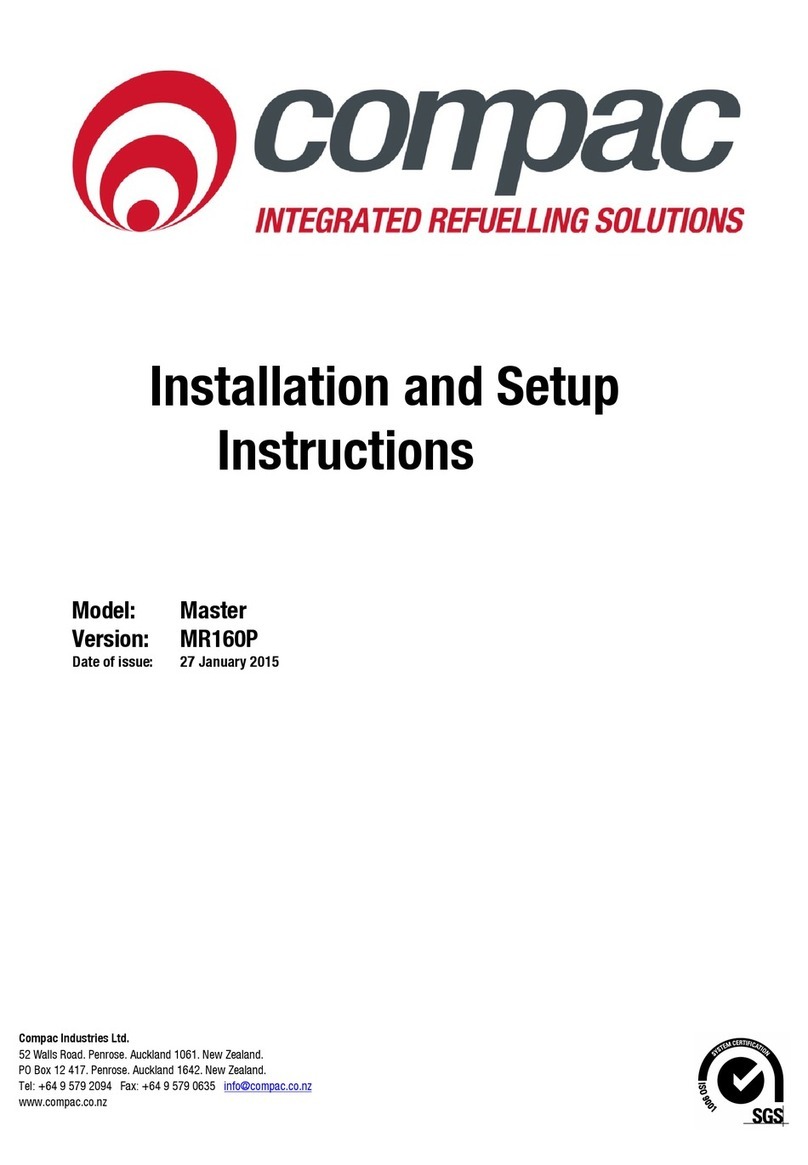
Compac
Compac Master Manual
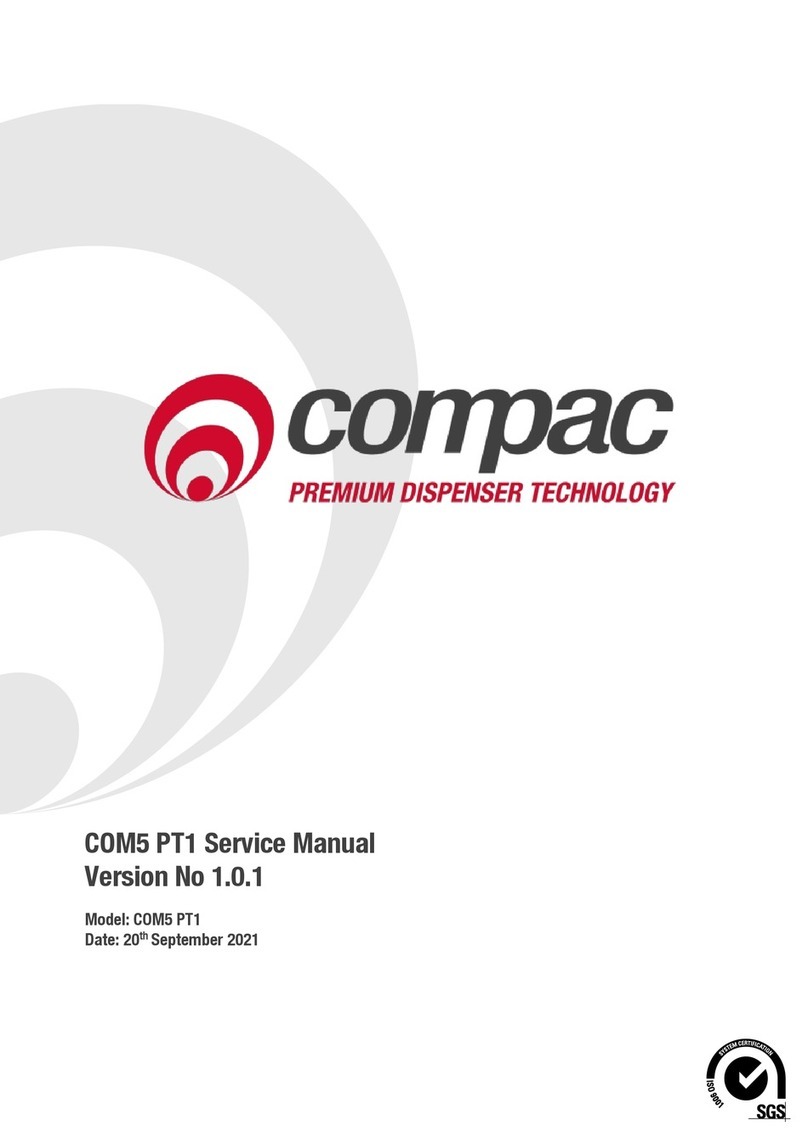
Compac
Compac COM5 PT1 User manual
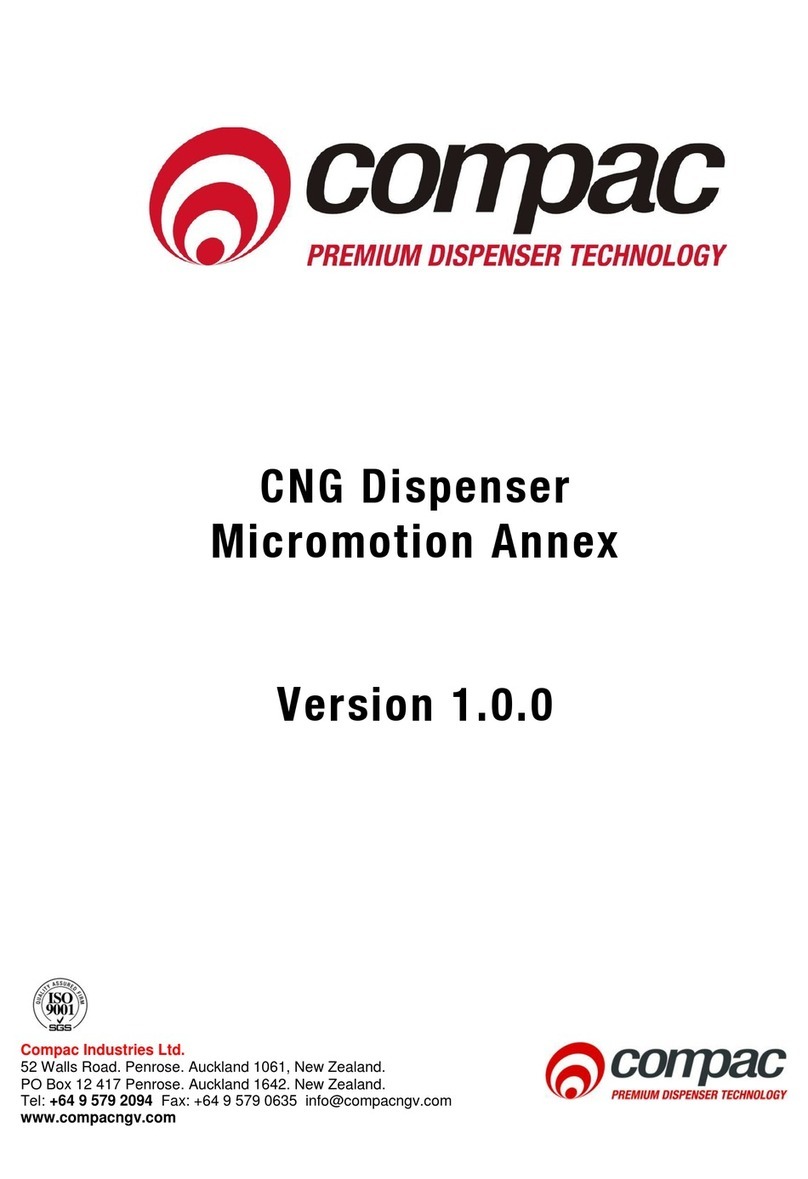
Compac
Compac Micromotion CNG50 User manual

Compac
Compac Laser AdBlue LA 30S Manual
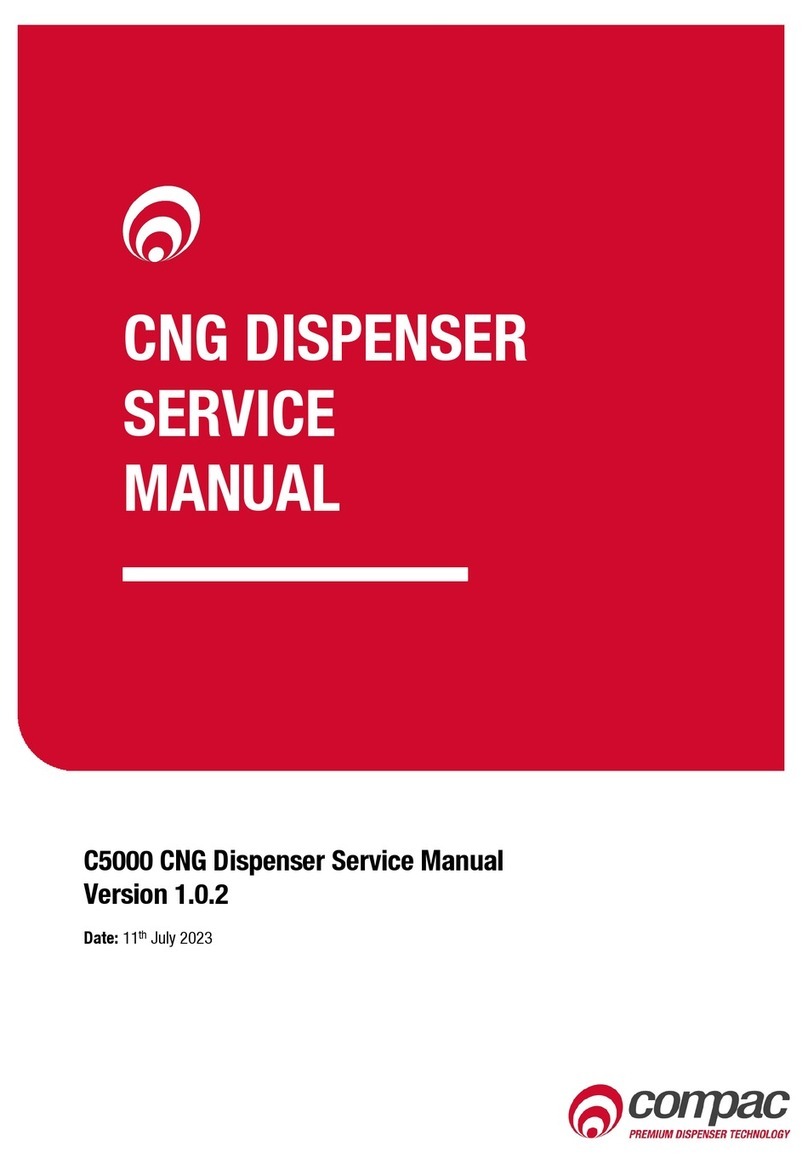
Compac
Compac C5000 User manual
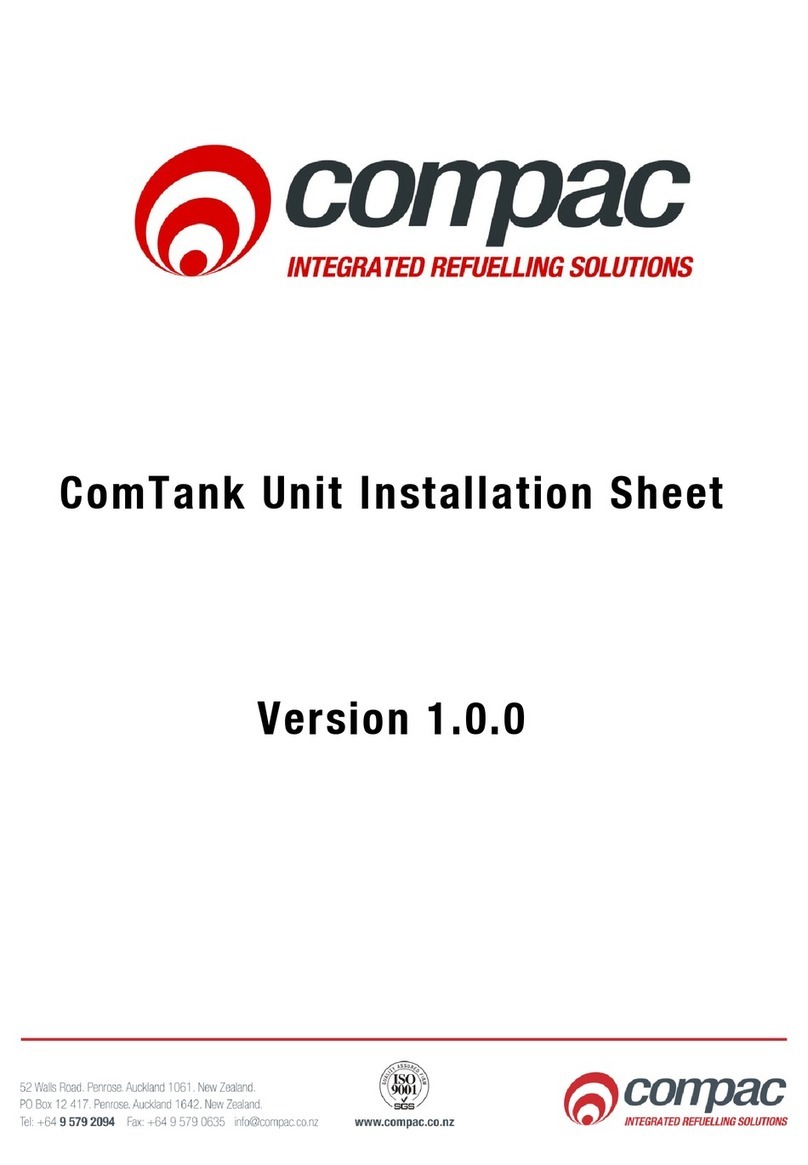
Compac
Compac ComTank Assembly instructions
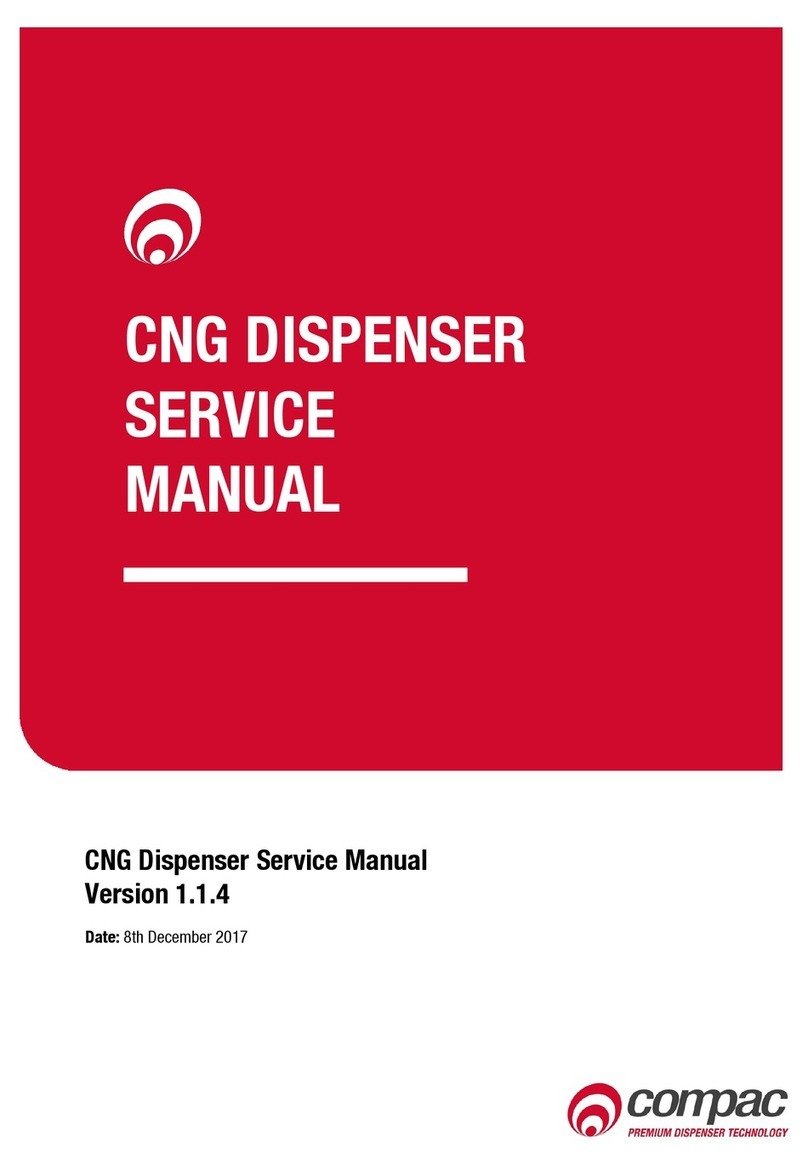
Compac
Compac CNG User manual
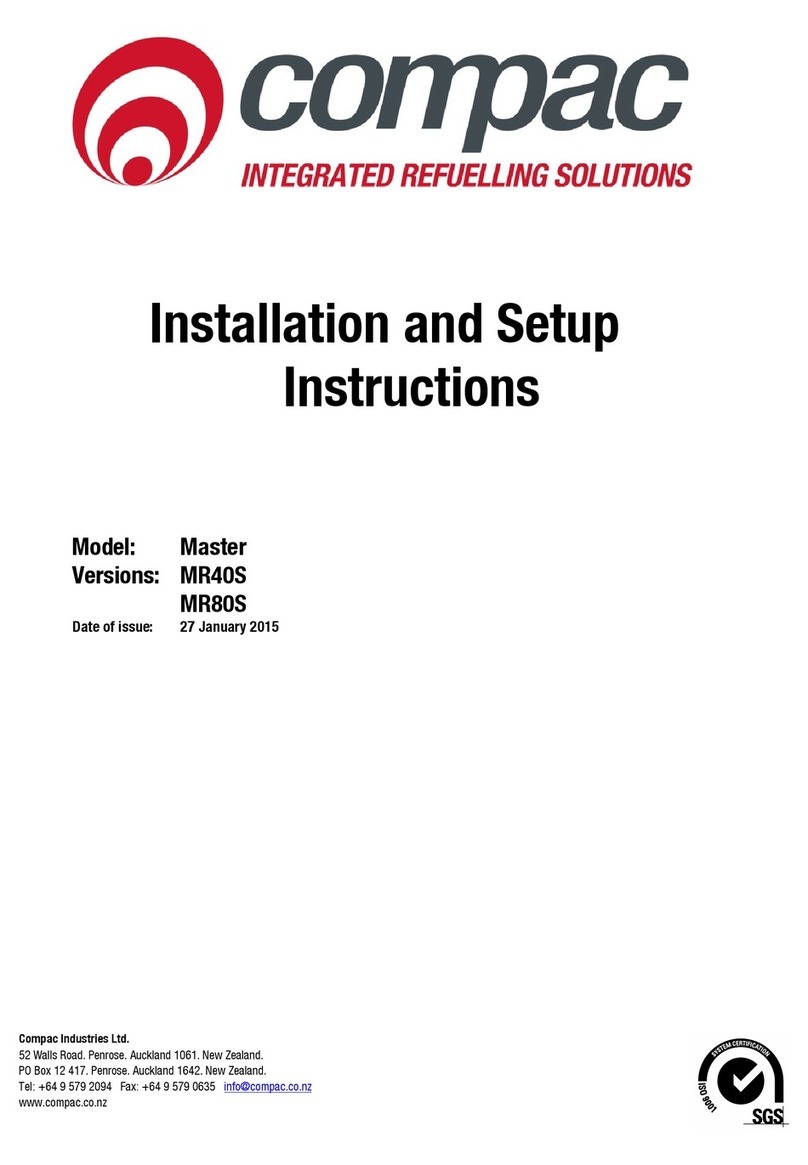
Compac
Compac Master MR40S Manual
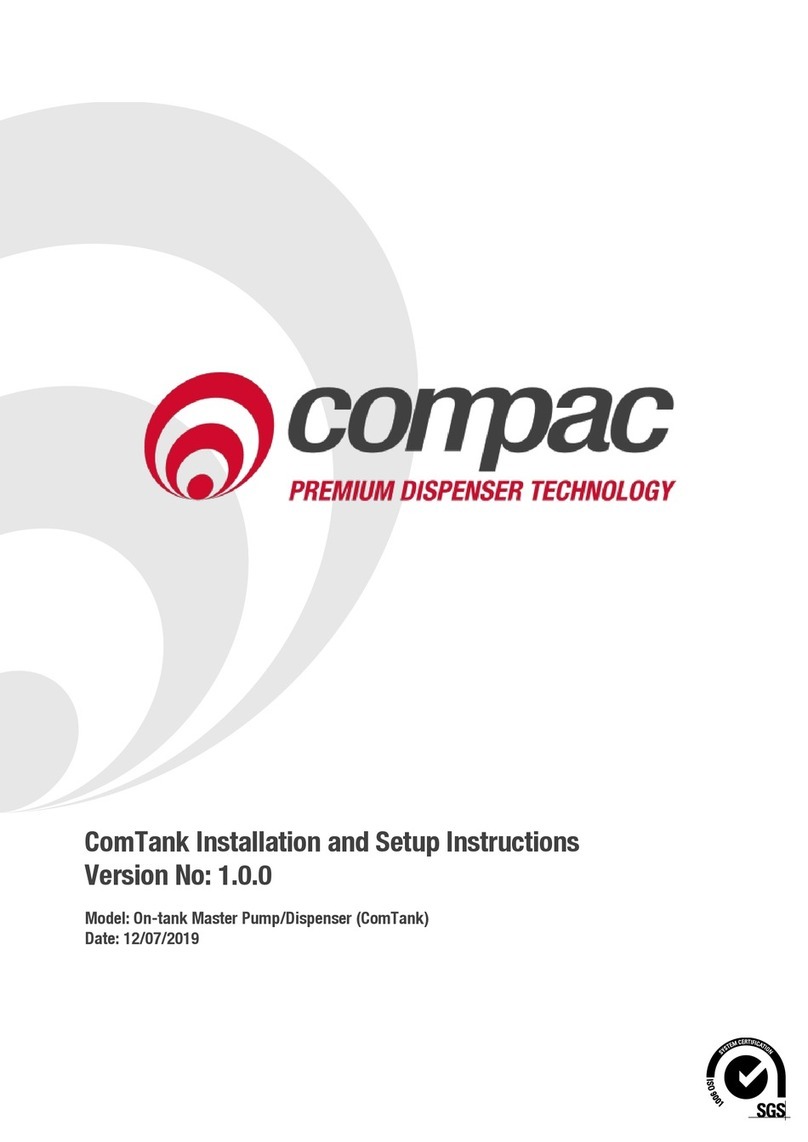
Compac
Compac ComTank Master MR Manual
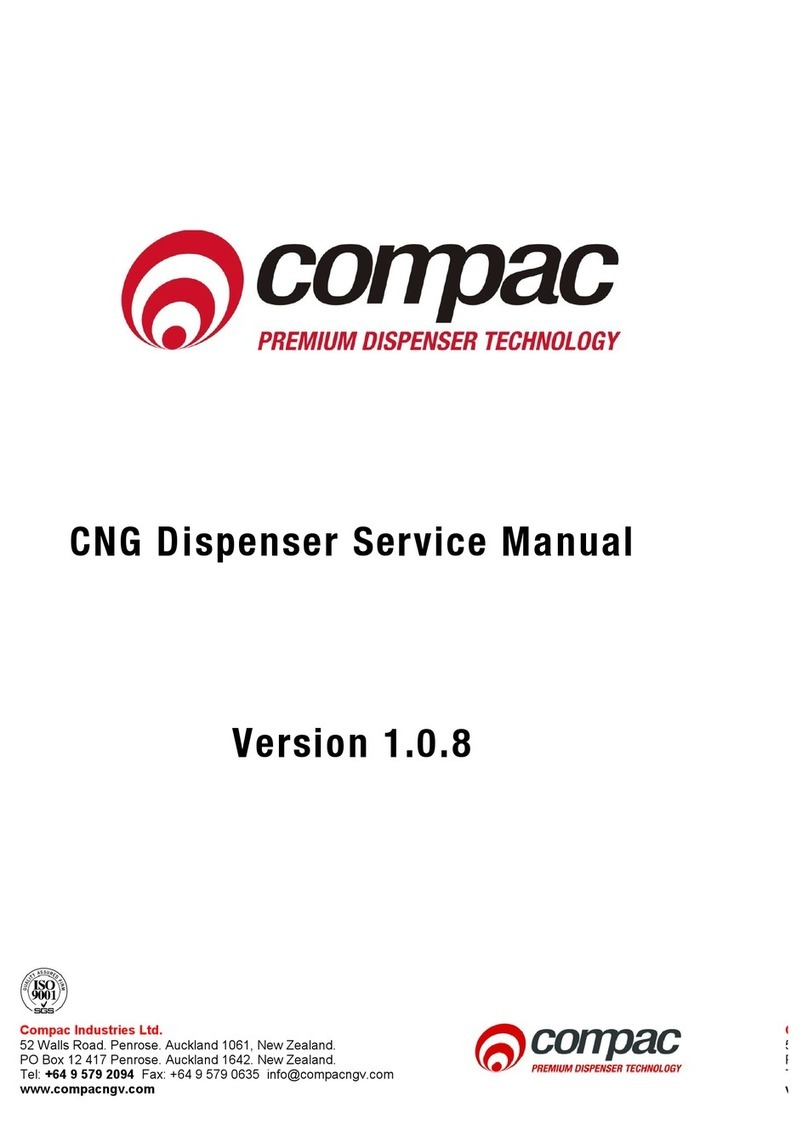
Compac
Compac CNG User manual