Concoa O2 Deficiency Alarm User manual

2
This page intentionally left blank.

3
Please Read Before Installation
The following will damage the Oxygen monitor.
1. The O2 monitor requires 24 VDC regulated power. Please Do Not connect
the monitor to any voltage that exceeds 24 Volts DC, or ANY AC Voltage.
2. Do not power the Oxygen monitor with the oxygen sensor unplugged from the
main PC board. Do Not Connect the O2 sensor to the PC board while the
monitor is powered. This Will Damage the O2 sensor.
3. The oxygen sensor cell is matched to the electronics. Never exchange the
electronics with an oxygen sensor from a different monitor.
4. When calibrating or challenging the O2 Ex monitors,
a. Do not expose the monitor to flow rates that exceed ½ liter per
minute, (500 cc per minute) flow.
b. When testing Sample Draw and Ex type monitors use an On
Demand regulator to expose the span gas to the monitor.
c. Expose the monitor to span gas blends that consist of Oxygen and
Nitrogen only. Do Not expose the monitor to any combustible
gas, i.e. Methane, Hydrogen, etc. Exposure to combustible span
gases can damage the oxygen zirconium sensor cell.
5. Do not expose the Oxygen monitor to silicone compounds. They can cause a
loss of sensitivity.
6. Do not expose the monitor to high flow air or install it directly in front of fans.
The high air flow can cool the oxygen sensor and cause an inaccurate
reading.
7. When using the O2 monitor, do not expose the oxygen sensor directly to a
water stream. In areas requiring wash downs, cover and protect the monitor
and power supply. Contact CONCOA for details on a waterproof enclosure.

4
Table of Contents
1: Introduction..................................................................................................................................2
1.1 Key Features ....................................................................................2
1.2 Component identification.................................................................3
2: Specifications...............................................................................................................................9
2.1 Performance Specifications .............................................................9
2.2 Gas Detection System......................................................................9
2.3 Signal Outputs..................................................................................9
2.4 Electrical Requirements...................................................................9
2.5 Physical Characteristics...................................................................9
2.6 System Default Factory Settings....................................................10
3: Installation .................................................................................................................................11
3.1 Site Requirements..........................................................................11
3.2 Mounting........................................................................................11
3.3 Wiring............................................................................................12
3.4 Initial Startup .................................................................................13
4: Normal Operation......................................................................................................................14
4.1 Signal Outputs................................................................................14
4.2 Instrument Faults ...........................................................................14
4.3 Routine Maintenance Schedule......................................................15
4.4 Loss of Power Indicator.................................................................15
4.5 Alarm Reset ...................................................................................15
5: O2Monitor Programming..........................................................................................................16
5.1 Joystick Operation .........................................................................16
5.2 Program Flowchart.........................................................................17
5.3 Entering the Password....................................................................21
5.4 Changing the User Password.........................................................22
5.5 Entering the Menus........................................................................25
5.5.1 Set 4-20mA Loop..................................................................25
5.5.2 Set Formats ...........................................................................27
5.5.3 Set Alarm Threshold Polarity ...............................................29
5.5.4 Set Latching..........................................................................31
5.5.5 Resetting a Latching Alarm ..................................................34
5.5.6 Set Alarm Delay....................................................................34
5.5.7 Set Zero Suppression ............................................................34
5.5.8 Set Alarm Thresholds ...........................................................35
5.5.9 Set Alarm Hysteresis.............................................................37
5.5.10 Set Sensor Adjust................................................................38
5.5.11 Main Operation Mode.........................................................39
6: Maintenance & Cell Verification...............................................................................................40
6.1 Sensor Verification ........................................................................40
6.2 Sensor Verification Procedure.......................................................41
7: Appendix....................................................................................................................................44
Rev 4.0 March 26, 2014

5
1: Introduction
The O2Deficiency Monitor is a compact gas monitoring system that’s ideal for the
continuous monitoring of inert gas storage areas, confined spaces, and other locations
where low oxygen levels may pose a hazard to personnel. Unlike electrochemical sensor
cells the O2zirconium cell provides stable oxygen readings even in areas where
temperature and humidity levels are changing. The CONCOA O2Deficiency Monitor is
suitable for either indoor or outdoor use. Factory calibrated against a NIST traceable
reference standard and Ce approved.
The heart of the monitoring system is a long lasting zirconium sensor, which responds to low
oxygen conditions within seconds and provides accurate measurements over a wide temperature
and humidity range. The zirconium O2sensor cell will operate continuously for 10 or more
years and requires an absolute minimum of maintenance. There are no zero or span calibration
pots to adjust and when compared to disposable type sensors, our long life zirconium O2sensor
can save up to hundreds of dollars in annual maintenance.
Ideal for continuously monitoring oxygen levels in confined spaces or areas where inert gases are
used, the O2Deficiency Monitor does not drift or loose sensitivity when the weather or
temperature changes. The electronics are housed in a Nema 3 housing.
Each system consists of a long life zirconium oxide sensor cell and three-wire transmitter. The
O2monitor may be used as a stand-alone gas detector, linked to optional CONCOA single and
multipoint controllers, or connected to your own centralized control and surveillance system.
This manual covers the installation, operation, and maintenance of the O2deficiency monitor.
1.1 Key Features
The O2monitor incorporates a number of user-friendly features designed to simplify installation,
operation, and maintenance.
1.1.1 Long Life Zirconium Oxide O2 Sensor
The system’s O2sensor cell has a life of well over 10 years of continuous operation. Unlike
concentration O2cells, CONCOA’s exclusive zirconium oxide sensor cell does not need an
oxygen reference gas for proper operation. The O2monitor can detect low oxygen levels in
confined spaces and process tools without the need of a reference gas.
1.1.2 Smart Electronics
The O2monitor incorporates a special electronic circuit that continuously monitors sensor
operation. With the addition of the alarm relay option, any cell degradation or complete failure
will immediately be detected. This smart circuitry alerts the user to sensor faults and other

6
electrical problems that may interrupt surveillance through the standard mA signal output signal
or through the optional fault relay option.
1.1.3 Calibration
The O2monitor incorporates a stable zirconium oxide sensor that rarely requires calibration.
Changing barometric pressure changes or changes in temperature and humidity do not affect the
zirconium oxide oxygen cell. The earth is a wonderful source of calibrated oxygen at 20.9%,
therefore under ambient conditions verification of the O2monitor to 20.9% oxygen is constantly
being performed. There are no zero or span pots to adjust. The O2monitor only requires periodic
testing with nitrogen to verify the cells response to low oxygen levels. See Section 6.2 for the
testing procedure to nitrogen.
1.2 Component Identification
1.2.1 Front View Exterior
1. Digital Display —3-digit backlit LCD digital display for showing the
oxygen levels in percent.
2. Joystick —Used for selecting and adjusting the built-in menus. The
O2monitor is available with optional dual level user selectable relays.
The joystick is also used to select alarm levels, relay settings and
resetting any latching visual and audio alarms.
3. Cable Port —This is the opening in the transmitter housing for
connecting the 4-20 mA output and 24 VDC power cable.
4. Sensor Protector—The O2sensor is heated and the sensor protector
shields the cell as well as provides airflow to the cell. It also has a ¼ “
diameter tube fitting to permit connecting a nitrogen cylinder for
testing the O2cell response. NOTE: The sensor protector will feel
HOT to the touch. This is normal.
5. Oxygen Sensor —A zirconium oxide sensor, which detects and
measures the level of oxygen. When exposed to oxygen, the sensor
6
8
1
8
6
4 & 5
8
2
7
9
3

7
outputs an electrical signal proportional to the actual concentration of
oxygen.
6. Mounting Feet —There are 4 feet used to mount the oxygen monitor
to a wall or other flat surface.
7. Transmitter Cover —A removable cover that protects the interior of
the transmitter.
8. Transmitter Cover Fasteners —There are 4 captive screws secure
the transmitter cover in place.
9. Electronics Fasteners —These captive screws secure the electronics
to the enclosure
1.2.2 Front View Exterior with Relay Option
10. Alarm Indicators —3 multi colored LED indicators for showing:
Alarm level 1 Orange LED
Alarm level 2 Red LED
Fault Alarm Yellow LED
6
2
9
6
3
1
9
10
Al 2
Al 1
Fault
4 & 5
4 & 5

8
1.2.3 Side View Exterior with Audio Alarm
11. Audio Horn —This optional built-in horn is a 90dB high pitched
audio sound that will activate when the oxygen levels go below the
selected alarm thresholds. The audio alarm is non-latching and will
automatically turn off when the oxygen levels go above the alarm
thresholds
NOTE: The audio alarm is an immediate alarm. Oxygen levels must recover above the
alarm thresholds before the horn turns off. There is no alarm delay function or
latching capability available.
1.2.4 Front view TX-1100-KF25 for vacuum chamber monitoring
11
3

9
Side view TX-1100-KF25 for vacuum chamber monitoring
12. KF-25 vacuum sensor assembly —Consists of the oxygen sensor
cell and KF25 vacuum fitting. The vacuum sensor assembly is designed to
mount directly into a mating KF-25 vacuum fitting.
WARNING:The Oxygen sensor cell must be handled with care. Never bounce or
drop the cell. Mating the cell into the KF-25 flange will support oxygen monitor
electronics and protect the cell
9

10
1.2.5 Front view TX-1100-DRAP for glove box mounting
Oxygen monitor for glove box Bottom View
Oxygen cell and KF-25 flange
Oxygen monitor with KF flange
attached directly to the monitor
NOTE: Cell is delicate. When
mounted in the corresponding
flange it is protected
Strain relief for power, analog
output and alarm relay wiring
Strain relief for
power and relay
outputs
Mounting Plate
NOTE: The
O-ring must be
installed to
insure an
airtight seal.
It rests inside
the O-ring
groove on the
bottom of the
mounting plate

11
1.2.6 Transmitter Interior
1. Power Analog Terminal Block —This terminal block is where the
24VDC power and 4-20 mA analog output connection is made.
2. Sensor Cell Connector —This connector is where the Oxygen sensor
cell is connected. NOTE: Never connect the oxygen sensor to this
connector while the monitor is powered. This will damage the
oxygen sensor
1. Power
Analog output
Terminal Block
Fuse
(Field
replaceable)
Common
Common
mA output
+ 24 VDC
+ 24 VDC
2. Sensor cell
connector

12
1.2.7 Alarm Relay Board
1.2.8 Enclosure Mounting Feet
Relay 2 Relay 1 Fault Relay Remote
NC C NO NC C NO NC C NO Reset
Horn Connector
Oxygen sensor
connector
Mounting Feet can
be oriented in any
direction
Feet can also be
removed for
mounting the O2
monitor flush with
a wall or other
surface
8

13
2: Specifications
NOTE: For our continual product improvement, all specifications are subject to change without
notice.
2.1 Performance Specifications
Sensor Type: Long Life Zirconium Oxide Sensor Cell 0-25%
Response Time: Within 1 second of any change in O2.
Repeatability: ± 1% of reading
Fault Indicators: Loss of VDC power (analog signal drops to 0 mA).
Sensor cell failure: Fault relay activated. (Must have Alarm relay option
for cell failure to operate)
Operating Temp: -40° to 134°F (-40° to +55°C); consult CONCOA for lower or higher
operating temperatures.
Humidity: 0 to 95% RH; consult CONCOA for sensors which can operate in 100%
condensing RH environments.
2.2 Gas Detection System
Type: Long Life Zirconium Oxide Sensor Cell, Range 0-25%
Sensor Life: 8 to 10+ years under normal conditions.
Transmitter: Microprocessor electronics with built-in 3-digit backlit LCD display
Joystick operated menus
2.3 Signal Outputs
Local Display: Digital display calibrated for Oxygen. The range is stated on the serial
number and can be accessed via the joystick on the front panel. In the
measurement mode pushing the joystick down will scroll the gas and
range on the display. Push the joystick down again to stop the scrolling
and display the gas again.
Standard Analog Output: DC 4-20 mA
Optional Relay Output: Dual level user selectable alarm relays and one fault relay
Rated, 2amps @ 30VDC; 2amps @ 240VAC
2.4 Electrical Requirements
Power: 24 VDC external power. A regulated 24VDC power supply is required.
Consumption: Approximately 250mA

14
2.5 Physical Characteristics
Dimensions: 5.125 (W) x 3.15 (H) x 3.00 (D) inches; 130 x 80 x 76 mm (Max with
feet)
Weight: 1.1 pounds (0.5 kg)
Enclosure Type: General purpose; not intended for explosive atmospheres.
2.6 AirCheck O2 System Default Factory settings
The O2Deficiency Monitor, when supplied with the optional Relay module, is shipped with
factory defaults for the alarm relay settings. The following are the factory defaults:
Menu Function
Factory Default
Menu Defined
Set 4-20mA loop
The mA output is set at
the factory using a
calibrated Fluke meter.
Use this function to adjust the
Oxygen monitors 4mA, (Zero) and
20mA, (Span) to your PLC or
distributive control system.
Set Formats
LED and alarm relay
State **
Alarm 1 = Normal
Alarm 2 = Normal
Fault = Normal
Do you want the relays to
energize, (normal) or de-energize,
(fail safe) when the alarm
activates?
Set Alarm Threshold
Polarity
Alarm 1 = Inverted
Alarm 2 = Inverted
Audio = Inverted*
Do you want to alarm at a level
higher, (normal) or lower,
(inverted) than the alarm
threshold?
Set Latching
Alarm 1 = Non-latching
Alarm 2 = Non-latching
Audio = Non-latching
Do you want the alarm to
automatically reset? (non-latching)
or do you want to manually reset
the alarm? (latching)
Alarm Delay
Alarm = 5 seconds
How long do you want to wait
until the alarms activate?
Zero Suppression
000 = 0.00%
Refer to section 4.5.6
This function is Not Enabled on
the Oxygen monitor.
Set Alarm
Thresholds
Alarm 1 = 19.5 %
Alarm 2 = 18.0 %
Audio = 19.5%*
At what level do you want to
alarm?
Set Alarm Hysteresis
Alarm 1 = 0.0 %
Alarm 2 = 0.0 %
Audio = 0.0 %
For use when using the O2monitor
for control or valves and process.
See Section 5.4.8
Sensor Adjustment
No factory default
For use when dynamically gas
calibrating the Oxygen monitor to
a known span gas.
See Section 6.2
Manage Passwords
Factory default is 557
For use when changing the
password from factory default to a

15
new password of your choice.
NOTE:The built in relay settings may be changed by the user in the field. Refer
to Section 5.5.2
* NOTE: The Audio alarm feature is optional.
** NOTE: The LED indicators on the front panel are connected directly to the
alarm relays.

16
3: Installation
3.1 Site Requirements
The O2monitor enclosure should be mounted in an area free of vibration and electrical noise or
interference. If possible, avoid areas with high temperatures or condensing humidity.
WARNING: The O2monitor is not designed for installation in hazardous areas. Consult
CONCOA for information on enclosures for use in hazardous environments.
3.2 Mounting
3.2.1 Transmitter Enclosure
The O2monitor is designed primarily for wall mounting and should be installed at a height
convenient for operation, maintenance, and viewing of the instrument display. The following is
a drawing of the mounting dimensions.
3.2.2 O2 monitor
The transmitter and sensor should be installed in a location where gas leaks are likely to occur or
where released gases may accumulate. It should be mounted no closer than 12 inches above floor
level. Airflow within the monitored area, the characteristics of the gas (lighter or heavier than
air), and the position of workstations and personnel should all be considered in determining the
most suitable installation location.

17
3.3 Wiring
The O2monitor requires a single, 3-wire shielded cable for analog output and 24
VDC power input. A three-wire shielded cable; 3-conductor, 18 AWG stranded
General Cable E2203S.30.860, or equivalent is recommended for the connection.
The maximum permissible cable length is 0.62 miles (1 km). The analog out and
VDC power in connections are made on the terminal block inside the transmitter
housing.
These connections are made as follows:
Pin #
Connection
Description
-
Common (Signal Ground)
0V
-
Common (Signal Ground)
0V
MA
Signal Out
DC 4-20mA Output
+
Power
DC + 24V Input
+
Power
DC + 24V Input
NOTE: CONCOA has added additional contacts for +24VDC power and Common to
accommodate additional wiring for remote horns and strobes
- Common
- Common
mA 4-20mA signal output
to PLC
+ 24VDC Power
+ 24VDC Power
Identification Legend

18
33.4 Initial Startup
Once installation of the gas detector has been completed, it is ready for startup. The following
procedures should be performed before putting the instrument into operation:
1. Check the integrity of all wiring.
2. Apply 24 VDC power.
The instrument should now be powered up. Upon power up, the O2monitor LCD displays the
CONCOA logo and then starts a 4-minute, (240 second) count down as the current to the
zirconium oxide O2sensor stabilizes. The monitor will output a 4 mA signal during the entire
warm-up period. After the countdown, the oxygen sensor will continue to reach its operating
temperature for approximately 30 minutes and the reading displayed will slowly increase to
ambient. Do not make any adjustments to the reading until after the monitor has been
powered for at least an hour.
NOTE: When the O2monitor is supplied with an Audio Horn, it will activate
momentarily at the completion of the warm up.
NOTE: The O2monitor’s reading may be adjusted to the ambient oxygen level.
See section 6.1 for instructions on adjusting.
Oxygen
239 WARM

19
4: Normal Operation
The O2monitor is a single point monitor designed for the continuous detection and measurement
of ambient oxygen concentration levels.
4.1 Signal Outputs
The O2monitor outputs a continuous 4-20 mA analog signal proportional to the measured
concentration of oxygen. 4 mA represents 0% O2and 20 mA represents 25% O2which is the full
range. In the event of a system fault, a specific factory defined code will be displayed on the
local digital display. This code will indicate the exact nature of the system fault.
4.2 Instrument Faults
The O2monitor incorporates a number of self-checking features to ensure
reliable operation. In the event that a fault condition is detected, the analog
output signal is altered as follows:
Condition
Analog Signal
**Supply Voltage Out of
Range Fault code 16
Analog output drops to 2 mA
Transmitter cable cut
Analog output drops to 0 mA
O2 Cell complete failure
Fault Code 128
Analog output drops to 2 mA (0 mA on request)
Fault Relay activates
(Available with Relay Option Only)
O2 System Warm Up
Analog output drops to 2 mA
Fault Relay activates and turns off when system is
in the Oxygen operation mode
(Available with Relay Option Only)
O2 Cell voltage fault
Fault Code 64
Analog output drops to 2 mA (0 mA on request)
Fault Relay activates
(Available with Relay Option Only)
EEPROM Fault 08
Analog output drops to 2mA (0 mA on request)
NOTE:All system faults are displayed on the front panel. Each fault
has it’own specific code to identify the specific problem. Please
contact PureAire whenever a fault is displayed.
** When using your own power supply please insure that the voltage
is regulated to 24VDC +/- 0.5 volts. If the voltage is too low or high
you will activate a “Supply Voltage Out of Range fault and disable
the monitor.

20
4.3 Routine Maintenance Schedule
Continuous gas detection systems depended upon to measure and detect hazardous gas leaks in
the workplace requires periodic maintenance to ensure proper operation. The frequency with
which this routine maintenance is required depends on the environment. The following table is
intended to serve as a general guideline for routine maintenance. The conditions in your
particular application, as well as your organization’s maintenance policies, will ultimately
determine the best routine maintenance schedule for your equipment. Routine Visual Checks
Items to check
Check for power and proper operation
Condition / status when
operating properly
Unit should be outputting a 17.4 mA signal when
the oxygen level is at 20.9%. The LCD digital
display should also indicate 20.9% 02 when the
oxygen is at ambient levels.
4.3.2 Recommended Routine Maintenance Schedule
Routine Visual Checks Every 6 - 12 months
Sensor Verification with nitrogen Every 6 - 12 months**
** The ambient oxygen level is 20.9%; therefore, under ambient conditions verification of the O2
monitor to 20.9% oxygen is constantly being performed. The O2monitor only requires periodic
testing with nitrogen to verify the cells response to low oxygen levels. See Section 5.5.10 for
how to make minor adjustments.
4.4 Loss of Power Indicator
In the event the O2monitor loses 24VDC power, the 4-20 mA analog output signal drops to
0mA. The LCD display will also display a blank screen.
4.5 Alarm Reset
It the O2monitor is supplied with the optional alarm relays, whenever the monitors alarms are
activated, the built-in alarm relays, panel mounted LED’s and optional audio horn will also
activate. When the relay settings are non-latching, the alarm relays, LED’s and horn will
automatically reset. If the relay settings are latching, then a manual reset of the alarms are
required. Resetting the alarms can be performed through use of the joystick or through the use of
the remote reset function.
Joystick –You must enter the password to enter the reset function. After the password is entered
and accepted, push the joystick in; (enter) to reset the alarms.
Remote Reset –See section1.2.7. The alarm relay board has a two-pin connector for wiring to a
remote switch. When connected to a switch, this remote reset will bypass the joystick and a
password will not be needed to reset the alarms.
NOTE:The oxygen levels must recover above the alarm thresholds before the horn can be
reset from the remote reset switch or joystick.
Table of contents
Other Concoa Measuring Instrument manuals
Popular Measuring Instrument manuals by other brands

MKS
MKS Spectra-Physics Tsunami Pre-installation guide
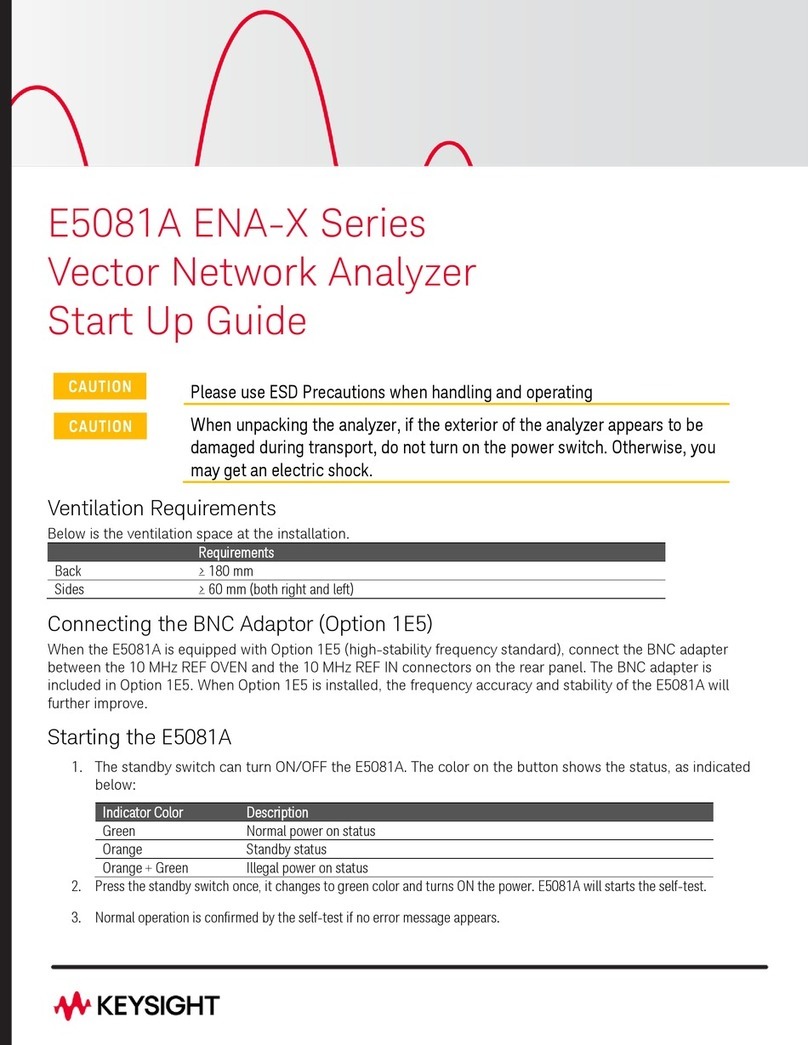
Keysight
Keysight E5081A ENA-X Series Startup guide

Loepfe
Loepfe MillMaster TOP installation manual

Polimaster
Polimaster PM1605 Software guide
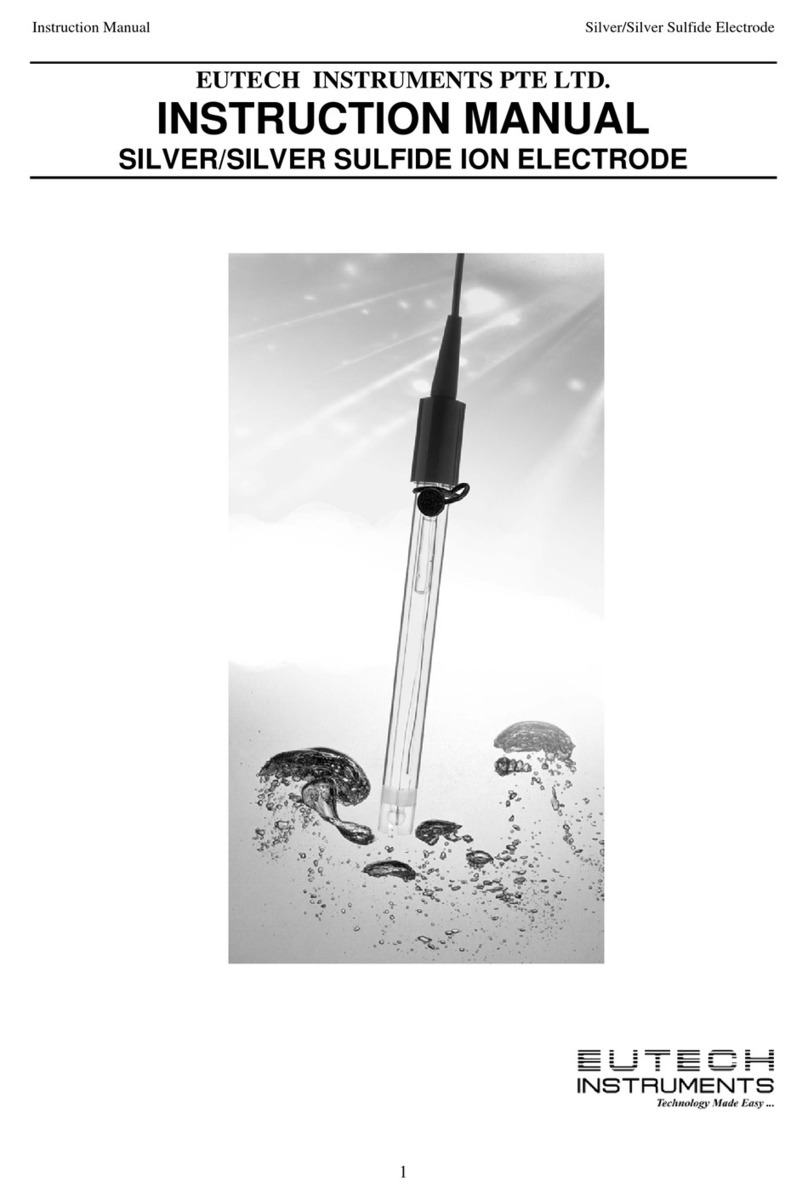
EUTECH INSTRUMENTS
EUTECH INSTRUMENTS SILVERSULFIDE EPOXY instruction manual
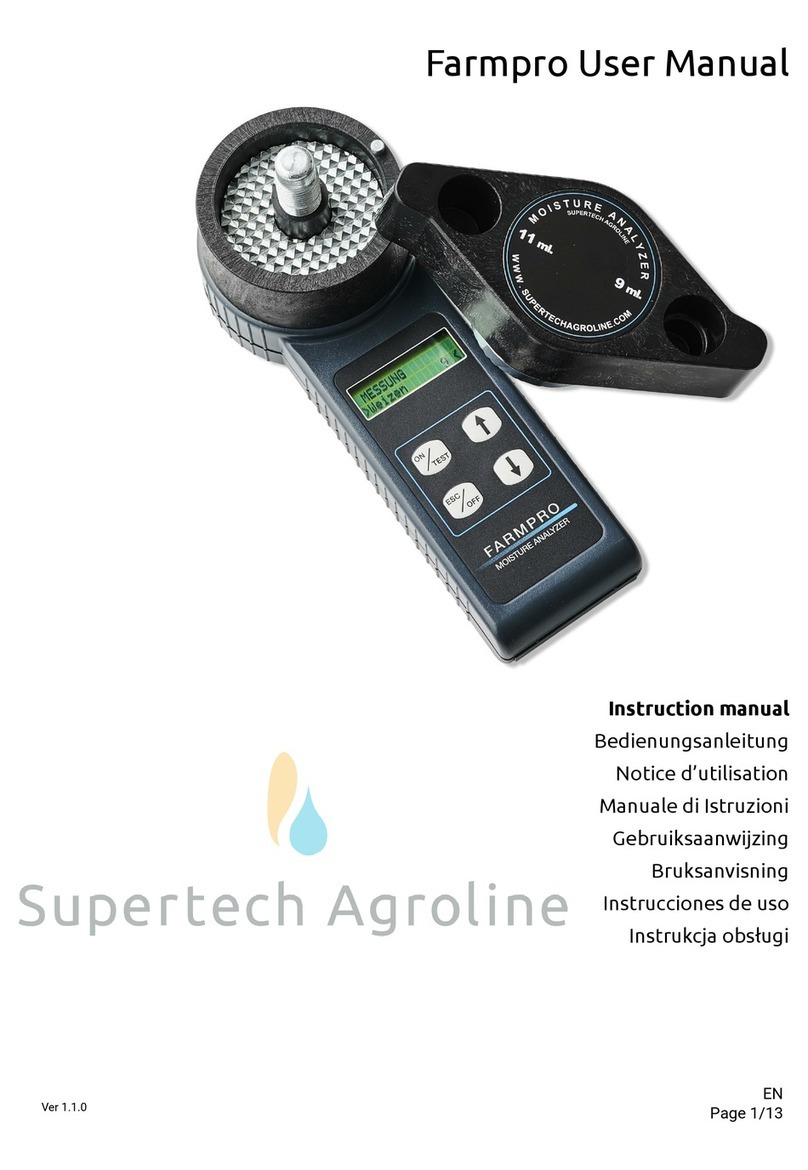
Supertech agroline
Supertech agroline Farmpro user manual