Cyndar Electronic Technology HL-1601 User manual

XD-Safety Contact Edge-202012
CYNDAR Safety Edge Sensor
Product manual

2
Directents
Directents
1. Safety edge Product profile......................................................................................................................3
2. Safety Touch Technology Selection Table....................................................................................... 4-6
Regular type.................................................................................................................................................. 4
Small size........................................................................................................................................................5
Special type................................................................................................................................................... 5
Type selection recommendations........................................................................................................... 6
3. security and edge contact configuration type and technical parameters.............................. 6-8
(1) Wire type......................................................................................................................................................6
(2) Wiring configuration.................................................................................................................................7
Controller configuration example 1........................................................................................................... 7
PLC configuration example 2...................................................................................................................... 7
(3) Safety contact edge technical parameters......................................................................................... 8
4. Installation instructions............................................................................................................................. 8
5. safety touch edge sensor wiring simple description................................................................10-12
6. Safety Relay Tner-A31 Technical Parameters............................................................................. 13-14
7. security Notes............................................................................................................................................ 14

3
1. Safety edge Product profile
Safe contact edges are flexible bending bands or circles. It can be fixed to dangerous edges of moving parts
such as tire molding, lift safety doors, machine workbench and electric doors. When the moving components
hits the operator or the moving components, these flexible safety edges are compressed and transmitted to
the power source has stopped this movement of these components. Safety edge contacts should work with
the controller to form a flexible and universal emergency stop system, where the robot operator and
installer must be able to easily conveniently stop the towing device. A complete safety contact edge includes
an aluminum guide to a safety contact and a built-in inductive signal band (contact band) ° special shape
(rubber side) protects the safety contact band from damage and allows an impact angle of more than 90 °.
The product has many specifications and sizes, and the customer can customize the length according to the
requirements after selecting the specifications. It is widely used in AGV trolleys, welding robots, packaging
machinery, automation equipment, automatic balancing vehicles, electric doors, etc.
Suitable for various applications, low trigger pressure, and a variety of specifications.
The length of the sensor is 200mm-6000mm.
It can be bent and is suitable for various mechanical protection occasions.
Protection grade IP65, suitable for use in various situations.
More than 3 million cycles of mechanical service life.
The jacket is made of EPDM rubber, resistant to various chemical corrosion, suitable for
Use in general conditions and civil occasions.
The maximum length of a control area (including link cables) should not be less than 100
square meters
Not suitable for fast-moving machines to protect against injuries
Safety edge sensor use case
Safety sensors installed on hazardous moving parts for contact detection are used in combination
with special controllers to meet PLe/ Safety Level 3.
(Suitable for occasions with internal safety relays that can directly prohibit the operation of
dangerous sources)
The simple and integrated structure integrates the sensor and the original cover. Resistance to
lateral forces. Can be used in multiple applications.Sensor length: 150mm〜6,100mm, Height:
27mm〜80mm
2. Selection table of safety edge technology
Regular type

4
2.Safety touch edge technology selection table
Regular type

5
Small size
Special type

6
Type selection recommendations
See the following table: The dimensions are reference values
Small AGV, garage access
control, industrial
applications
Application of various
electric doors, industrial
and civil fields
Application of AGV, electric
door and industrial fields
Application of AGV, electric
door and industrial fields
Application of AGV, electric
door and industrial fields
Large AGV anti-collision,
heavy industrial doors,
machinery and industrial
applications
Large AGV anti-collision,
heavy industrial doors,
machinery and industrial
applications
Large AGV anti-collision,
heavy industrial doors,
machinery and industrial
applications
3.Safety edge configuration type and technical parameters
Safety Touch Side Standard Product Length L=200mm-6100mm
Cable length of 450~500mm, is customizable
(1), Wire type
①. Standard type-single-sided straight lead
Outlet example diagram
A section of the safety edge is a non-action area (blind zone), the length S≈20~30mm
Induction zone S Outgoing
②Other customized
Bilateral direct
leads
Single-bottom
lead
Double-bottom
leads
Single-side
leads
Dual-side leads
There are 20~30mm non-sensing area (blind area) at both ends of both sides
No action area 20~30mm No action area 20~30mm

7
(2)Wiring configuration
Determine the wiring configuration according to the number of safety contact edges (sensors) connected in
series. (Up to 5 safety contact edges can be connected in series)
Configure Number
Outline drawing
Output Type
Wiring configuration
1
2-wire cable
NO
One-end outgoing line 2-line cable (2-
line system)
2
2-Line cable, 2-Line cable
NO
Two-line outgoing line cable at both
ends (4-line system)
3
2-wire cable
Terminalresistance
NO
One end outgoing line 2 line cable (2
line system) and end resistance at the
other end (8.2KΩ 0.25W)
Controller configuration example 1
Use a safe touch edge Use N safe touch edges
2-wire cable 2-wire cable connection
Safe touch Safe touch Safe touch Safe touch
Controller Controller
2-wire cable 2-wire cable connection
Safe touch Safe touch Safe touch Safe touch Terminating resistor
Controller Controller
PLC configuration example 2
Secure edge and PLC connection mode
Normally open wiring:
①Line No. is connected to the power supply or the negative pole of PLC
②Line No. is connected to PLC emergency stop input signal interface
Normally closed wiring:
③Line No. is connected to the power supply or the negative pole of PLC. (Connect with the COM interface of the relay)
④Line No. is connected to the PLC emergency stop output signal interface (connected to the NO interface of the relay
⑤⑥Line No. is connected to the input terminal of the relay signal (regardless of the positive and negative poles)
Safe touch
Safe touch
Safe touch
Normally
open wiring
PLC
①
②
Safe touch
Normally
closed wiring
PLC
③
④
Safe touch
Relay:
⑤
⑥

8
(3), Safety Touch Parparameters
Specification
Model Number
Trigger
force value
Trigger
Distance:
Bend
Radius:
Color /
Material
Underwit
hstand
voltage
Withsta
nd
current
Blind area
Scope
Standard
wiring harness
Ambient
temperatur
e
Signal
mode
HL-1601
≤ 30N
3-5mm
≥ 120mm
Black
color
Rubber:
Rubber
EPDM
≤ 24V
≤ 1A
Current
current
Range is
generall
y in
(1mA ≤ I
≤
100mA)
Single side
20-30mm
Length:
50 cm
Customizable
Line diameter:
3.5mm
Copper-core
Cross-
section:
0. 25mm2
-20 ° to
80 °
Normally
open
(The
controller
can be
used as a
normally
closed
type)
HL-1603
≤ 30N
3-5mm
≥ 100mm
HL-1605
≤ 30N
3-5mm
≥ 120imn
HL-1606
≤ 30N
3-5mm
HL-1607
≤ 30N
3-5mm
≥ 80mm
HL-1608
≤ 30N
3-5mm
≥ 70mm
HL-1609
≤ 30N
3-5mm
≥ 100mm
HL-1610
≤ 30N
3-5mm
≥ 100mm
HL-1611
≤ 30N
5-8mm
≥ 350mm
HL-1612
≤ 30N
5-8mm
≥ 350mm
HL-1614
≤ 30N
3-5mm
≥ 120mm
HL-1615
≤ 30N
3-5mm
≥ 120inm
HL-1616
≤ 30N
3-5mm
HL-1617
≤ 30N
5-8m m
≥ 350mm
HL-1619
≤ 30N
3-5mm
≥ 120mm
HL-1620
≤ 30N
3-5mm
≥ 100nim
Other parameters
Nano
conductive
adhesive
Place of Origin: Japan Brand: Shin-Etsu
Durable life
100N load pressure 10000 times, the change is
less than 20%; no cracking/deformation/abnormal
noise/expansion
Insulating
elastomer
Material Brand: China Plastic
Insulated pin
Material: Teflon Function: High and low
temperature resistance
Shock proof
500N (7*12mm^2) no
break/deformation/abnormal noise/expansion
after one impact
Seal on both
sides
Material: PTFE
Wire
strength
≥60N
preservative
Resistant to slight acids and alkalis
Adhesive
strength
≥60N/mm
Protection
level
IP65
Note: Please contact customer service for other specifications

9
4.Installation instructions
Safety contacts must be installed by the designated person
1. For facilitate installation of edge installation. The mounting
base must be secured to a flat surface. If the safety contact edge
needs to be installed with a certain arc. The radius of the current
curvature shall not be less than a fixed minimum.
2.The mounting base must be fixed with countersunk screws or
rivets. The diameter is 4mm. The nail holes are 4.5mm. They must
be evenly distributed over the entire length of the mounting base.
The hole spacing must not exceed 300mm: the counterbore part
must be processed according to the screw size.
When using a special base, drill a pilot hole in the slot to ensure
that the head of the countersunk screw can pass through (about
8mm).
3.Do not use flat-head or round-head screws. Otherwise, the
connecting wires in the mounting base may be damaged.
4.In order for the connecting wire to pass through the base, an
8mm hole must be drilled in the appropriate position. Carefully
remove the burrs on both sides.
5. The receiving wire and the end of the cable with terminating
resistor must be placed in the mounting base
6.To make the safety edge easier to install, soapy water should be
sprayed on the mounting base and the safety edge. After the
soapy water evaporates, the safety edge can be firmly fixed on
the aluminum base. In order to avoid sliding after the safety
touch edge, do not use long-lasting lubricants such as talcum
powder and oil.
7.For the safety contact edge with C-shaped base, one side must
be buckled into the installation base. Then press into the entire C-
shaped base. Pushing and pulling the safety contact edge in the
installation base will cause the safety contact edge to damage the
floor. Avoid it anyway.
C-type base
8. For the safety contact edge with T-shaped base, it should be
inserted from the side along the groove of the mounting base.
T-type base
To use other fastening methods. Must be agreed with the
manufacturer in advance.

10
5.Simple description of safety touch edge sensor wiring
Apply vertical pressure to the safety contact edge to make the
conductors of the internal induction belt contact each other,
which causes the resistance and current to change, which is
further analyzed by the control device. If the installation is
correct, as long as the internal induction belt is not damaged,
the safety edge cover can function normally even if it is damaged.
This product is normally open.
There are two core wires (black and red in two colors), black and red are a set of normally open
switches, which will be turned on under the action of external force (people step on it), thereby
transmitting signals to the controller or relay to achieve control of the machine .
1. This product is a pressure touch switch, which needs to be used with a controller or
relay.
2. The product is not suitable for use in water. If it is used in this environment, please
communicate with the supplier in advance.
Precautions:
1. This product must not directly contact the power source, and requires the auxiliary
use of a relay or a controller.
2. The maximum voltage is DC24V
Attached wiring diagram:
Two-wire non-resistance edge circuit diagram:
Circuit diagram with second wire:

11
Safety contact edge standard safety controller model: Tner-A31
A1: is connected to + 24V ± 10% (20V~26V)
A2: to 0V
Automatic reset: Diial switch to A
Manual reset: Diial switch to M
(No resistance contact edge) Tner-A31 safety relay connection method:
Touch edge 1: Red and black lines: connect T1 and R1,
Touching edge 2: Red wire and black wire: connect to T2 and R2 in no particular order. If there
is no touch edge 2, it can be left unconnected.
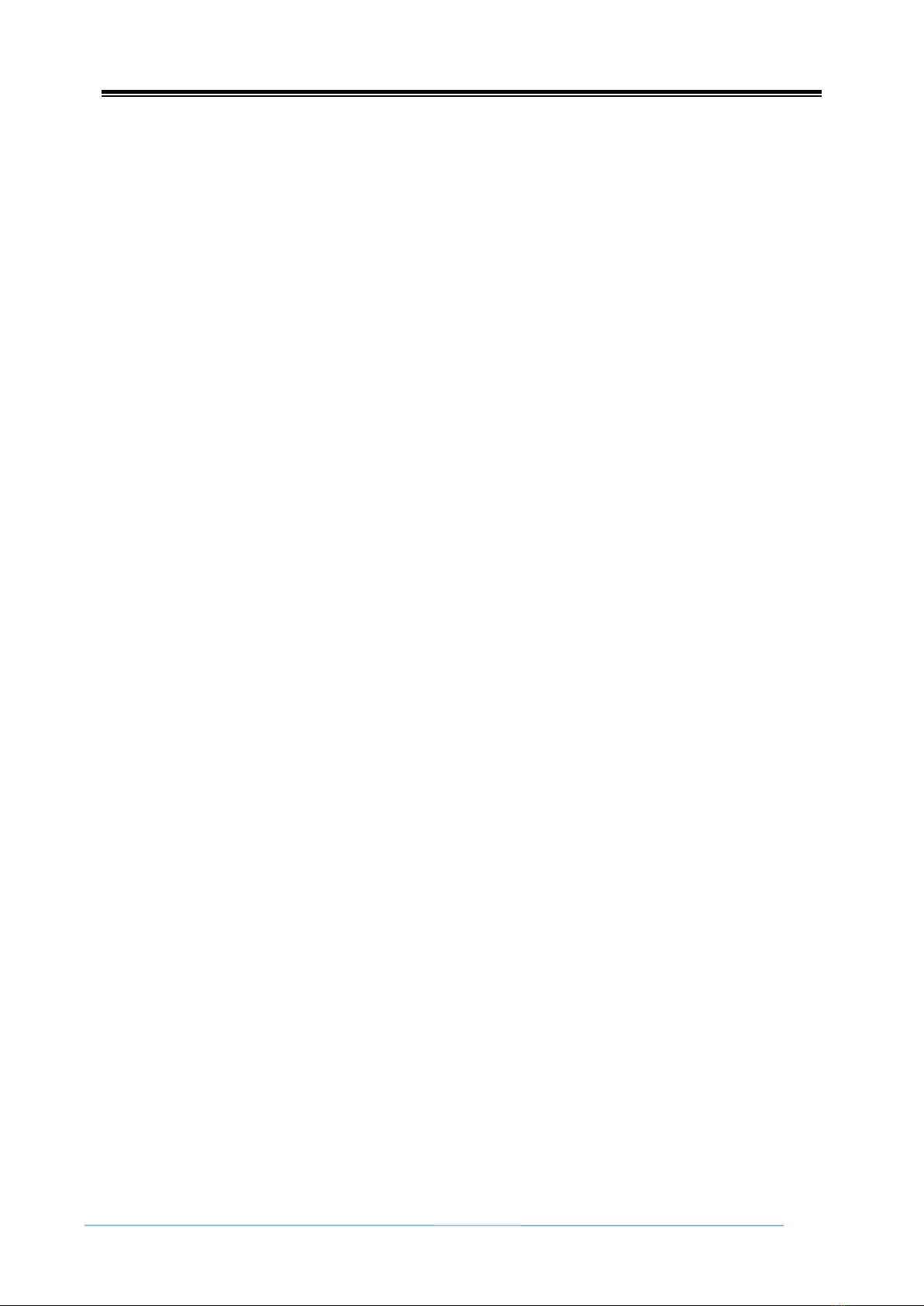
12
(Touch edge with resistance) Tner A31 safety relay connection method:
Touch edge 1: Red and black lines: connect T1 and R1,
Touch edge 2:: red line and black line: connect T2 and R2,. If not touch edge 2, connect a
5.6k resistance.

13
6.Safety Relay Tner-A31 Technical Parameters
Power supply
Power supply supply
24V DC
Voltage tolerance
+10%/-20%
Power consumption
2.9W
Output
Relay safety output
3NO + 1NC
Transistor signal output
<500mA 24VDC
Relay contact capacity
AC-1
6A/250VAC/1500VA
AC-15
4A/240VAC
DC-1
6A/24VDC/150W
DC-13
4A/24VDC
Maximum switching
capacity
12A(assigned on all security output contacts)
Contact resistance
<100m Ω
Minimum load
10mA/5V
Contact Material
AgSnO2 + 0.2 µmAu
General parameters
Output fuse (external)
5A gL/gG
Release the Response Time
<30m s(, from input to output),
Check resistance of input
tail
(Touch the edges / carpet)
1kΩ ~10kΩ
Electrical life
80,000 times
Pollution level
2
Operating temperature
-25℃~85℃
Working humidity
35% -85% (unfrozen or condensed)
Impact-withstand voltage
2.5kV
Protection level
Case IP30, terminal IP20, recommended for cabinet or housing IP54
Storage temperature
-40℃~105℃
Housing material
Flame-retardant PA66
Installation mode
Standard 35mmDIN guide rail / spring buckle
Dimensions
114.5mm×100.5mm×22.5mm
Weight:
172g
Connection parameters
Range of cross-section
available for rigid
conductors
0.5~2.5mm ²
Range of cross-sections
available for flexible
conductors
0.5~2.5mm ²
Minimum conductor cross-
section
AWG 24
Maximum conductor cross-
section
AWG 12
Stritrip length
8mm
Minimum tightening torque
0.5 Nm
Maximum tightening
torque
0.6 Nm
Standard Application
Coniant
EN 60947-1:2007/A2:2014 // EN 60947-5-1:2004/A1:2009
EN ISO 13849-1:2015 // EN 62061:2005 + A2:2015

14
7.Safety contact precautions
1)
Storage and use environment requirements Do not save or use this product in a long-term direct sunlight
environment.
Do not save and use it outside of the ambient temperature-35 ℃to + 80 ℃.
Do not save and use it outside of air pressure 86 " 106KPa.
Do not preserve and use them in the environment containing strong corrosive or combustible gases;
2) Installation precautions
Do not lift or move the safety contact by pulling the cable.
Use a special bracket to install a safety touch edge.
Do not fold or punch on the edge of the safety contact.
Do not install the safety edge on the surface raised area, but on a flat, smooth surface.
3)Use precautions
Be sure to use the safety contacts in this marking voltage range or with the safety relays matched in this
description.
Do not apply a load for long times, or it may cause damage to the safety touch edge.
Do not dip safety edges in water or for frequent splashing.
Please strictly follow the chemical resistance of the product.
Safety characteristics
PL Performance Level L
EN ISO 13849-1:2015
PLe
Category Category
EN ISO 13849-1:2015
Cat.4
SIL CL
EN 62061:2005 + A2:2015
SIL CL 3
PFHd[1 / h]
EN 62061:2005 + A2:2015
2.10E-09
This manual suits for next models
15
Table of contents