Delta Controls BACstat II Series User guide

Document Edition 3.1 Page 1 of 35
APPLICATION GUIDE
Delta Network Sensor Thermostat: BACstat II
DNS-24, DNT-T103, & DNT-T221
Document Edition 3.1
Product Description
The BACstat II is an intelligent 4-button room sensor/thermostat with a
custom 3-value, 96 segment LCD display that is used with Delta’s product
line of BACnet Application Controllers. It is capable of displaying a wide
range of digital or analog values, and is capable of communicating on Delta’s
proprietary LINKnet network or directly on a BACnet MS/TP network.
When connected to an Application Controller on a LINKnet network it
provides programmable remote sensor and expanded I/O capabilities to the
controller. When connected on an MS/TP network it functions as an
independent BACnet sensor device or a small local controller.
The DNS-24 model does not have additional I/O and built-in control strategies, while the DNT-T103 has 1
extra input, 3 binary outputs and a number of built-in application control strategies. The DNT-T221 has 2
extra inputs, 2 analog and 1 binary outputs and built-in application control strategies. As a result, the DNT-
T103 and DNT-T221 BACstats are capable of simple stand-alone control when directly connected on an
MS/TP network. When connected to a LINKnet network, the additional I/O may be MUXed or otherwise
controlled from the Application Controller it is connected to.
Contents
OTHER RELEVANT DOCUMENTS................................................................................. 2
IMPORTANT INFORMATION.......................................................................................... 2
SETUP &CONFIGURATION ............................................................................................ 3
NETWORK COMMUNICATIONS .......................................................................................... 3
DEVICE CONFIGURATION (KEYPAD) ................................................................................. 3
SERVICE TOOL MODE (KEYPAD) ...................................................................................... 6
INPUT CALIBRATION ......................................................................................................... 8
INPUT SCALE RANGES....................................................................................................... 8
SOFTWARE&PROGRAMMING..................................................................................... 9
OBJECTS............................................................................................................................ 9
PROGRAMMING ............................................................................................................... 10
CONTROL FUNCTIONS................................................................................................... 12
OVERVIEW ...................................................................................................................... 12
SOFTWARE LOOP CONTROLLER ...................................................................................... 13
SETPOINTS ...................................................................................................................... 16
CONTROL DIAGRAM........................................................................................................ 17
CONTROL APPLICATIONS (MUX,VAV, VVT, HPU, FCU, RAD,HUM) .......................... 18
OUTPUT FUNCTIONS &TYPES......................................................................................... 26
OWS FUNCTIONS ............................................................................................................. 30
APPENDIX (LCD Object Property Values & Programming Notes).............................. 32

Error! No text of specified style in document. DNS-24, DNT-T103, & DNT-T221 Application Guide
Page 2 of 35 Document Edition 3.1
Other Relevant Documents
•Associated BACstat II Installation Guide (DNS-24, DNT-T103, DNT-221, etc.)
•RS-485 Network Installation Guide (DOC818-11)
•ORCAview Operator Guide
•ORCAview Technical Reference Manual (particularly Appendix G)
•Release Notes for V3.21 Firmware, V3.22 Firmware, V3.30 Firmware, and BACstats
Important Information
This document has been updated to include features and capabilities of Release 3 firmware for BACstat II
products. And although BACstat firmware is independent from ORCAview, DCU, and Application
Controllers, certain BACstat capabilities require support in the other products. It is also important to note
that BACstats are not flash loadable in the field – an upgrade requires swapping out physical product.
1. V3.21FIRMWARE &SOFTWARE
Note the following issues when BACstats are used with ORCAview, DCU, and Application Controllers loaded
with V3.21 firmware/software.
MS/TP NETWORK CONNECTION
•A DCU is required (to which the MS/TP network is connected)
•Local BACstat display handling and control strategies may be enabled
•All data exchange must be done in GCL programming in the DCU
LINKNET NETWORK CONNECTION
•The BACstat must be connected to an Application Controller that supports LINKnet devices
•Local BACstat display handling and control strategies must both be disabled
•Additional I/O cannot be MUXed
•All functionality for the BACstat must be done in GCL programming in the Application Controller
(i.e., display handling, setpoint adjust, and strategies using the space temperature)
2. V3.22FIRMWARE &SOFTWARE OR HIGHER
Note the following issues when BACstats are used with ORCAview, DCU, and Application Controllers loaded
with V3.22 firmware/software.
MS/TP NETWORK CONNECTION
•A DCU is not necessarily required (as long as one System device exists on the MS/TP network)
•Local BACstat display handling and control strategies may be enabled
•Data exchange may be done in GCL programming in any DCU or Application Controller on the
MS/TP network
LINKNET NETWORK CONNECTION
•The BACstat must be connected to an Application Controller that supports LINKnet devices
•Local BACstat display handling may be enabled (so GCL programming in the Application
Controller for setpoint adjust and LCD display is not necessary)
•Local BACstat control strategies must be disabled, as this is more suitable on an MS/TP connection
•Additional I/O may be MUXed
•Additional BACstat strategies may be done in GCL programming in the Application Controller

Delta Controls
Document Edition 3.1 Page 3 of 35
Setup & Configuration
NETWORK COMMUNICATIONS
On an MS/TP network BACstats communicate at a default speed of 76,800 bps. Refer to the ORCAview
Technical Reference Manual for further detail on configuring the MS/TP network or changing baud
rates, etc.
On LINKnet BACstats communicate at 76,800 bps. Refer to the ORCAview Technical Reference
Manual for further detail on the NET1 object located in the MS/TP DAC device.
Also refer to the associated BACstat II Installation Guide for network installation details.
DEVICE CONFIGURATION (KEYPAD)
To use ORCAview OWS to configure BACstats refer to OWS Functions on page 30.
1. CONFIGURATION MENU USER ACCESS
Access to the Configuration Menu is protected by an access code or PIN. You must enter the valid PIN before
access is granted, which works as follows:
•First press the Up Arrow (σ), and then press the Down Arrow (τ) while still pressing the Up Arrow, and hold
them both down for at least 5 seconds.
•When the Pin text is displayed you are being prompted for the valid PIN or access code, a pre-configured
4-digit code, which you must enter before you can gain access to the Configuration Menu. The buttons on the
left side of the BACstat have a value of 0, while the buttons on the right side have a value of 1. Press the
proper button sequence to match the password.
•The default PIN is 1011. Note that the PIN access code, contained in AV31, can be changed through the
OWS when the BACstat is connected to an MS/TP network, but not over LINKnet or through the keypad.
•Once you have entered the valid 4-digit code you will gain access to the Configuration Menu, and CFg will be
displayed immediately to indicate you are now in Configuration mode. If you haven’t entered a valid code (or
if you do not press a button within about 10 seconds), the process will be aborted and you will be returned to
normal display mode.
•If at any time after you have gained access to the Configuration Menu you do not press a button for 2 minutes,
the BACstat will exit the Configuration Menu and return to normal display mode.
2. BUTTON &NAVIGATION FUNCTIONS
The Button functions are as follows within the Configuration Menu:
Button Description
Top Left •Represents a value of 0 when entering the PIN access code.
•PREVIOUS: Enter the current setting (and go backward in the menu).
Top Right •Represents a value of 1 when entering the PIN access code.
•NEXT: Enter the current setting (and go forward to the next item in the menu).
Bottom Left
(Down: τ)
•Represents a value of 0 when entering the PIN access code.
•Rotates downward through menu items and options.
•Decreases a numeric value with each button press.
Bottom Right
(Up: σ)
•Represents a value of 1 when entering the PIN access code.
•Rotates upward through menu items and options.
•Increases a numeric value with each button press.

Error! No text of specified style in document. DNS-24, DNT-T103, & DNT-T221 Application Guide
Page 4 of 35 Document Edition 3.1
Use the NEXT and PREVIOUS buttons to navigate through the menu options. Once you have navigated to the
desired item you wish to display or change, use the arrow buttons to make any necessary changes. Once the
changes are made or you wish to move on, press NEXT or PREVIOUS.
3. CONFIGURATION MENU OPTIONS
The Configuration Menu is a list of items which you can navigate through and make changes to as you need for
setup purposes. The Configuration Menu items are as follows:
Menu Item Description
CFg Displayed momentarily to indicate you have successfully entered the Configuration
Menu.
[Application] The Control Application (AV12). You may choose from any of the following
applications:
•None This disables all control strategies and allows the outputs and control
icons to be controlled remotely from another device.
•VAV This enables the VAV control strategy and allows you to configure the
outputs for your VAV application.
•VVT This enables the VVT control strategy and allows you to configure the
outputs for your VVT application.
•HPU This enables the HPU control strategy and allows you to configure the
outputs for your Heat Pump Unit application.
•FCU This enables the FCU control strategy and allows you to configure the
outputs for your Fan Coil Unit application.
•Unt This is no longer an option. Configure control for a Unit Heater using
the FCU application.
•rAd This enables the Radiation control strategy and allows you to configure
the outputs for your Radiant Heating application.
•HuM This enables the Humidity control strategy and allows you to configure
the outputs for your Humidity application.
OP1 Output 1 Configuration. This includes the output function and type (what it will
control and how) and other setup parameters as required (such as delays or limits).
OP2 Output 2 Configuration. This includes the output function and type (what it will
control and how) and other setup parameters as required (such as delays or limits).
OP3 Output 3 Configuration. This includes the output function and type (what it will
control and how) and other setup parameters as required (such as delays or limits).
[More] Additional parameters to set, which are dependent on the Application and Output
Configuration, may include:
•Run Actuator Runtime in seconds (AV24)
•AFF Air Flow Factor for VAV only (AV25)
•Min Minimum Air Flow for VAV and Damper Minimum for VVT (AV26)
•MAM Maximum Air Flow for VAV and Damper Maximum for VVT (AV27)
DEG The Temperature Units Setting (degrees C or F).
[Settings] Additional control settings, which are particularly useful when an Application is
selected for local control, typically include:
•Set Day Setpoint (AV6) •HI Max. Day Setpoint (AV8)
•DIF Day Differential (AV9) •Pb CO Proportional Band (AV19)
•LO Min. Day Setpoint (AV7) •rr CO Reset Rate (AV20)

Delta Controls
Document Edition 3.1 Page 5 of 35
Menu Item Description
DSP The LCD Display Code Setting (AV15), a 4-digit value (ABCD) configures local
display and button handling as follows:
A Line 1 (Top Left – i.e., Outside Value): 1 to 4
1- Disabled
2- Value from AV5 (i.e., remote value such as OAT)
3- Value from AI2 (i.e., external sensor)
4- Value from AI3 (i.e., Humidity)
B Line 2 (Center – i.e., Inside Value): 1 to 4
1- Disabled
2- Temperature from AI1
3- Humidity from AI3
4- Alternates between Temperature (AI1) & Humidity (AI3)
C Line 3 (Bottom – i.e., Setpoint Value): 1 to 5
1- Disabled
2- No Setpoint until an arrow button is pressed (adjustable)
3- Setpoint is always displayed (adjustable)
4- No Setpoint until an arrow button is pressed (not adjustable)
5- Setpoint is always displayed (not adjustable)
D House & Day/Night Mode Icons: 1 to 9
HOUSE OUTLINE ON/OFF TEXT MAN SUN/MOON
1 No No No No
2 No Flash No No
3 No Yes No No
4 No No No Yes
5 Yes No No No
6 Yes Yes No No
7 Yes Yes Yes No
8 Yes No Yes No
9 Yes No No Yes
NOTE: When connected to LINKnet with V3.21 firmware/software the Display
Code should be set to 1111. When connected to MS/TP, or LINKnet with V3.22
firmware/software or higher, the Display Code may be set to any valid value –
making it unnecessary to write GCL programs for display and button handling.
Note that whenever an application is selected, a matching default Display Code is
also set automatically (typically 1237), but this can be set to something else if so
desired.
Ser The Service Tool Mode access setting (AV32) has the following options:
0 Disables all access to Service Tool Mode
1 Provides limited access for VAV, or full access for other applications
2 Provides full access with advanced Air Balancer functions for VAV
Lnt The LINKnet Communications Setting (ONor OFF), to match the connection
method. When turned ONthe network communications is set to LINKnet, and when
OFF the communications is set to MS/TP.
DNA The DNA Setting (ONor OFF), for inheriting a derived address from higher-up
devices on an MS/TP network, or not, and is not an option when LINKnet is ON.

Error! No text of specified style in document. DNS-24, DNT-T103, & DNT-T221 Application Guide
Page 6 of 35 Document Edition 3.1
Menu Item Description
Add The device Address (1 to 99), which is used internally as the MAC Address. As the
BACstat can only be a Subnet device on MS/TP, this address is always mapped in as
the Subnet value. On LINKnet, this address is the physical address for the device
(limited to 1 to 12) and the other address settings are irrelevant. Note: On MS/TP
the complete BACnet address is in the form of “OEM_Area_System_Subnet”
SYS The System number (0 to 99), which can only be set manually when on MS/TP and
DNA is turned OFF – and is inherited when DNA is ON.
ArE The Area number (0 to 99), which can only be set manually when on MS/TP and
DNA is turned OFF – and is inherited when DNA is ON.
OEM The OEM number (0 to 3), which can only be set manually when on MS/TP and
DNA is turned OFF – and is inherited when DNA is ON.
BAU The Network Speed (9.6 KB, 19.2 KB, 38.4 KB, or 76.8 KB). The default for both
LINKnet and MS/TP is 76.8 KB. While the baud rate for MS/TP devices may need
to be adjusted to suit, the speed for LINKnet networks should remain at 76.8 KB.
End To exit the Configuration Menu (Yes or No). If you do not press a button within 1
minute the device will automatically exit and return to its normal display mode.
NOTE:AI2 (and AI3 for the DNT-T221) are not configured through the Configuration Menu.
These objects must be configured through the OWS (i.e., for Scale/Units) – except when AI2 is
used for VAV airflow. Refer to OWS Functions on page 30 for more information.
SERVICE TOOL MODE (KEYPAD)
Note that a new BACstat II Quick Reference Card for Service Tool Mode (product number REF-817) now
exists for quick and easy reference for navigating and using the various Service Tool features. Although
shipped with the product, additional copies can be ordered as necessary.
1. SERVICE TOOL MODE USER ACCESS &NAVIGATION
Access to Service Tool Mode and its associated menu options is not protected by an access code or PIN.
However, user access must be enabled (via AV32 or the setting located in the Configuration Menu) and the valid
key sequence must be entered.
•To enter Service Tool mode, first press the Down Arrow (τ), and then the Up Arrow (σ), and hold them both
down for at least 5 seconds (which is the opposite sequence to the Configuration menu). There is no PIN or
password.
•Once you have entered the valid user key sequence you will gain access to Service Tool Mode, and SEr will
be displayed immediately along with a main menu of several options.
•You may now use the up and down arrow buttons to navigate through the main menu options, and the NEXT
or PREVIOUS buttons to penetrate deeper into their associated options.
•Once you have navigated to the desired item you wish to display or change, use the arrow buttons to make
any necessary changes. Once the changes are made or you wish to move on, press NEXT or PREVIOUS.
•If at any time you do not press a button for 30 minutes, the BACstat will exit Service Tool Mode and return to
normal display mode. Any outputs commanded manually will remain in manual, and a VAV box
commanded to various Air Balancer modes (Minimum, Maximum, Close, Open, Zero Calibration) will also
remain as commanded. A subsequent user command (CtL) is required to put the BACstat and associated
outputs back under control (or Auto).
2. SERVICE TOOL MENU OPTIONS
Service Tool Mode contains two menus: the Main menu and an Air Balancer menu (which is only available when
the application is configured for VAV).

Delta Controls
Document Edition 3.1 Page 7 of 35
Service Tool Main Menu Options
Menu Item Description
SEr Displayed on line 2 of the LCD (center screen) to indicate you are at the Main menu
of the Service Tool Mode.
[Option] Service Tool Mode has these following main menu options, which you rotate
through using the arrow keys. Press the NEXT or PREVIOUS buttons to select the
option and penetrate deeper.
•CAL To calibrate Inputs AI1 to AI3 as compared to an external measuring
device. Navigate past the inputs you don’t wish or need to calibrate.
•MAn To manually command AV1 to AV3 (0-100% for tri-state or PWM, and
OFF or ONfor binary outputs), associated with OP1 to OP3 respectively.
This allows for end-to-end commissioning of output devices. Navigate
past the outputs you don’t wish or need to command. [When outputs are
defined as tri-state in the Configuration menu, modifications can only be
made to the primary output – the other output cannot be modified.]
•bAL To enter Air Balancing mode, which is only an option when VAV is
selected as the Application in the Configuration Menu.
•End To exit Service Tool mode (Yes or No). At any time within the Service
Tool menus, if you do not press a button within 30 minutes the device
will automatically revert to its normal temperature display mode (but
retains manually commanded outputs and stays in any forced VAV box
mode: MIN, MAX, CLOSED, OPEN).
Air Balancer Menu Options
Menu Item Description
BA Displayed on line 1 of the LCD (top left) to indicate you are in the Air Balancer
Mode.
[Option] Air Balancer Mode has these following menu options, which you rotate through
using the arrow keys. Press the NEXT or PREVIOUS buttons to penetrate deeper.
•AF Displays the current Air Flow, and penetrating deeper allows you to
view the internal Air Flow Setpoint and the Air Flow Factor (with
possible adjustment).
•MIn Displays the current Minimum Air Flow setting, and penetrating deeper
allows you to adjust the value and force the box to the minimum value.
•MAM Displays the current Maximum Air Flow setting, and penetrating deeper
allows you to adjust the value, force the box to the maximum value, and
calibrate the display value to match a measured value.
•CLO Penetrating deeper allows you to force the box fully closed and auto-
calibrate for zero flow.
•Opn Penetrating deeper allows you to force the box fully open.
•CtL Penetrating deeper puts the box back under control (releasing the box
from forced modes: MIN, MAX, CLOSED, OPEN, or ZERO Calibrate).
•End To exit Service Tool mode (Yes or No). At any time within the Service
Tool menus, if you do not press a button within 30 minutes the device
will automatically revert to its normal temperature display mode (but
retains manually commanded outputs and stays in any forced VAV box
mode: MIN, MAX, CLOSED, OPEN, or ZERO Calibrate).

Error! No text of specified style in document. DNS-24, DNT-T103, & DNT-T221 Application Guide
Page 8 of 35 Document Edition 3.1
INPUT CALIBRATION
MS/TP CONNECTION
The inputs are typically calibrated in their associated local AI objects. These same calibration fields
are also mapped to variables (AV16 to 18) to provide access to other vendors in a multi-vendor
installation, which can be also used to calibrate the inputs. Besides this, the inputs may also be
calibrated right at the BACstat using the Service Tool Menu.
LINKNET CONNECTION
With local handling of the LCD display and buttons disabled (AV15 = 1111), the BACstat sends
A/D values to its associated AI objects in the Application Controller, where calibration and filtering
is applied. Calibrate the AI objects in the Application Controller. Do not calibrate the BACstats
locally (via Service Tool Menu) or use the AV objects (mapped to AV16 to 18).
With local handling of the LCD display and buttons enabled (AV15 > 1111), the BACstat sends
actual values to its associated AI objects in the Application Controller – all calibration and filtering
is done in the BACstat. Calibrate the BACstats locally (via Service Tool Menu) or use the AV
objects (mapped to AV16 to 18). Do not calibrate the AI objects in the Application Controller.
INPUT SCALE RANGES
Local Input Scale Ranges are selected by setting the units, from the following available options.
Input Valid Units Scale Description Application Notes
1 C / F Standard 10K Thermistor (in ºC or ºF) Only available options for AI1.
2 C / F Standard 10K Thermistor (in ºC or ºF) Available whenever the VAV
application is not enabled.
% 0-5 or 0-10v input signal (depending on
jumper) converted to a 0-100% value
Available whenever the VAV
application is not enabled.
CFM / LPS Air Flow (in CFM or LPS) using a 0-1”
DP Sensor (Kavlico or Setra)
Fixed whenever the VAV
application is enabled.
3 C / F Standard 10K Thermistor (in ºC or ºF) Available whenever the HUM
application is not enabled.
% 0-5 or 0-10v input signal (depending on
jumper) converted to a 0-100% value
Available whenever the HUM
application is not enabled.
%RH Built-in Custom Humidity Sensor
(optional)
Fixed whenever the HUM
application is enabled.
Unless inputs are multiplexed, many of the input units and associated scale ranges are automatically
set when a built-in application is selected. Also refer to page 31 for configuring AI2 and AI3.
MS/TP CONNECTION
Only those units and associated scale ranges resident locally in the BACstat may be used.
LINKNET CONNECTION
With local handling of the LCD display and buttons disabled (AV15 = 1111), the AI objects in the
Application Controller may be configured for any valid units and scale ranges that are available up
in the Application Controller.
With local handling of the LCD display and buttons enabled (AV15 > 1111), only those units and
associated scale ranges resident locally in the BACstat may be used.

Delta Controls
Document Edition 3.1 Page 9 of 35
Software & Programming
OBJECTS
The following is a list of predefined or “fixed” objects that reside in the BACstat II products, which you
cannot create or delete. When connected to an MS/TP network, these objects are readily accessible over
the network. When connected to a LINKnet network, many of these objects are mapped into matching AI
or AV objects residing in the Application Controller above.
Object Name Description Default Value
DEV1 BACstat * Device Object N/A
AI1 Temperature Input 1 (10K Thermistor Value) N/A
AI2 Input 2 * Input 2 (Available Input) N/A
AI3 Humidity Input 3 (Humidity on DNT-T103) N/A
Input 3 Input 3 (Extra Input on DNT-T221) N/A
AV1 Output 1 * Output 1 (0 – 100%, Name Changes) N/A
AV2 Output 2 * Output 2 (0 – 100%, Name Changes) N/A
AV3 Output 3 * Output 3 (0 – 100%, Name Changes) N/A
AV4 KeyPress KeyPress Value N/A
AV5 External * External Object Value (i.e., OAT) N/A
AV6 Day Setpoint Room Setpoint ºC = 21; ºF = 71; % = 30
AV7 Day Minimum Minimum Adjustable Day Setpoint ºC = 18; ºF = 65; % = 20
AV8 Day Maximum Maximum Adjustable Day Setpoint ºC = 25; ºF = 77; % = 55
AV9 Day Differential Room Setpoint Differential ºC = ±0.5; ºF = ±1, % = ±2.5
AV10 Night Heat Setpoint Night Setpoint for Heating (or Humidity) ºC = 16; ºF = 60; % = 30
AV11 Night Cool Setpoint Night Setpoint for Cooling ºC = 30; ºF = 86; % = 30
AV12 Application Control Application (Name Changes) None
AV13 Alg Mode Algorithm Mode 0 (OFF or Night)
AV14 Controller Status Status of Internal Control Loop N/A
AV15 Display Code Local Display & Button Handling As per Control Application
AV16 AI1 Calibration Input 1 Calibration (Temperature) 0.0
AV17 AI2 Calibration Input 2 Calibration (MUXed IP) 0.0
AV18 AI3 Calibration Input 3 Calibration (Humidity) 0.0
AV19 Proportional Band Control Loop Tuning Parameter ºC = 1; ºF = 2; % = 10
AV20 Reset Rate Control Loop Tuning Parameter 1.0
AV21 Output 1 Config Output 1 Configuration Variable As per Application Setup
AV22 Output 2 Config Output 2 Configuration Variable As per Application Setup
AV23 Output 3 Config Output 3 Configuration Variable As per Application Setup
AV24 Setup 1 Setup Variable 1 (Name Changes) As required
AV25 Setup 2 Setup Variable 2 (Name Changes) As required
AV26 Setup 3 Setup Variable 3 (Name Changes) As required
AV27 Setup 4 Setup Variable 4 (Name Changes) As required
AV28 Setup 5 Setup Variable 5 (Name Changes) As required
AV29 Setup 6 Setup Variable 6 (Name Changes) As required
AV30 Baud Rate Network Baud Rate 76,800 bps
AV31 PIN PIN (4-Bit Configuration Access Code) 1011
AV32 Service Tool Mode Service Tool Access Disable/Enable (0-2) 1 (or 2 when AV12 = VAV)
AV33 Box Mode Heating & Cooling Modes for VAV/VVT 0 (Cooling)
* Names are user settable (to a maximum of 8 characters), and only on outputs when they are controlled remotely (i.e., MUXed).
These are the typical objects that may be commanded on-the-fly by a user or from GCL, and would also include the Outputs
(AV1-3) when they are MUXed. Never command the Configuration Variables (AV12, AV21-13) on-the-fly. Refer to page 34.

Error! No text of specified style in document. DNS-24, DNT-T103, & DNT-T221 Application Guide
Page 10 of 35 Document Edition 3.1
NOTE:The DNS-24 model does not have any extra inputs, any outputs, and does not support
control applications, so it only contains a subset of these objects (highlighted in bold).
The DNT-T103 and DNT-T221 models support the full compliment.
PROGRAMMING
MS/TP CONNECTION
Objects
All of the existing predefined BACstat II objects are readily accessible over the MS/TP network.
Control Applications
BACstats with I/O may be configured to run one of seven possible built-in control applications.
Another option disables local control altogether.
GCL Programming
BACstats are not programmable devices – GCL does not reside in a BACstat. Rather, when
connected to an MS/TP network you configure a BACstat for local operation and write GCL located
elsewhere as necessary to do additional functions. In this way you configure the BACstat for local
operation (both display & button handling and local control) and then write any necessary GCL in
another controller for additional strategies.
For example: Through the Configuration Menu, you typically configure the BACstat II display and
buttons to functional locally, so GCL programs are not necessary for handling the display value or
adjusting setpoint (i.e., AV15 = 1237). With a BACstat that has additional I/O, you may also select
a suitable control application for local control. Then, using GCL programming located in another
controller (i.e., DCU or other System Device) you make mode and setpoint changes based on Time-
of-Day or other conditions.
WITH V3.21 FIRMWARE: All GCL programming for mode changes, data exchange, and other
strategies must be written in the DCU.
WITH V3.22 FIRMWARE OR HIGHER: A DCU is no longer necessary and since data exchange is
supported across MS/TP-based products, no specific GCL is required for this. GCL programming
for mode changes, or other strategies may be written in any appropriate controller on the network.
Refer to Appendix G in the V3.22 ORCAview Technical Reference Manual for further programming
information, and the Programming Notes on page 34.
LINKNET CONNECTION
Device Limitations
Note that there are inherent limitations to the total number of devices per LINKnet network, as well
as the number of devices that have outputs. Refer to Appendix G in the V3.22 ORCAview
Technical Reference Manual for further information.
Objects
Only the BACstat information that is represented by objects resident in the Application Controller is
readily accessible over the network. The objects resident within each BACstat are not directly
accessible to other devices in the system. To gain access to BACstat objects, you create objects in
the Application Controller that correspond to the objects located in its respective BACstats.

Delta Controls
Document Edition 3.1 Page 11 of 35
Object Name Description Creation
LCDx01 LinkLCD# Object for BACstat LCD & Button Presses Automatic
AIx01, 02, 03 [User Specified] Matching object for the Input Value Manually
AVx01, 02, etc. [User Specified] Matching object for the corresponding AV Manually
where “x” refers to the device address (1 to 12) multiplied by 100.
An LCD object is automatically created for each BACstat connected to the LINKnet network.
However, the associated AI objects representing the room temperature in each BACstat must be
created manually, and must follow a predefined numbering scheme. The object instance number is
the LINKnet device address (1 to 12) multiplied by 100, plus 1. For example, you would create
AI501 in the Application Controller to represent the 10K Thermistor value on a BACstat with a
LINKnet device address of 5.
With V3.22 loaded in the Application Controller, AV objects may be created in a similar fashion to
the AI objects, which map to corresponding AV objects in the BACstat. You can then use these in
GCL programming as well. With V3.21, mapped AV objects are not supported.
Control Applications
BACstats with I/O should have their built-in control applications disabled. If you wish to have
BACstats running a local control strategy, then it should be connected to an MS/TP network instead.
GCL Programming
All GCL programming for BACstats on a LINKnet network is written in the Application Controller
that the BACstats are connected to, using the mapped objects resident in the Application Controller.
The LCD object is used for display and button handling. The mapped AI objects are used for
reading values. And with at least V3.22 firmware on the Application Controller, the mapped AV
objects are used for outputs, setpoints, and various other settings.
WITH V3.21 FIRMWARE: When connected to LINKnet, local display and button handling should be
disabled (i.e., AV15 = 1111), which is the default when you set the LINKnet Communications
Setting to ON. This way, the LCD and buttons are fully accessible from the Application Controller
for custom programming. Then, with GCL and the LCD and AI objects resident up in the
Application Controller, you program the BACstat to operate as you want (similar to how ISTATs
were programmed) – all BACstat functionality is written in GCL located in the Application
Controller. Note that none of the AV objects are accessible with V3.21 firmware.
WITH V3.22 FIRMWARE OR HIGHER: You may disable local display and button handling (i.e.,
AV15 = 1111) and program everything in GCL in the Application Controller as previously
described for V3.21 firmware. Or, by setting the Display Code to something other than 1111, the
display and buttons may be configured to function locally and GCL commands from the Application
Controller for display and button handling (via the LCD object) are ignored. This may be the
preferred method as no GCL needs to be written to handle setpoint adjust and the display of values
on the LCD. In addition to this, BACstats with outputs may be controlled as MUXed outputs
through corresponding AV objects (AV1-3). And the setpoints and other settings are also accessible
through their corresponding AV objects.
Refer to Appendix G in the V3.22 ORCAview Technical Reference Manual for further programming
information, and the Programming Notes on page 34.

Error! No text of specified style in document. DNS-24, DNT-T103, & DNT-T221 Application Guide
Page 12 of 35 Document Edition 3.1
Control Functions
OVERVIEW
1. CONTROL APPLICATIONS (DNT-T103AND DNT-T221ONLY)
When connected to an MS/TP network, the DNT-T103 BACstat may configured to operate according to one of 8
possible application control strategies, and displayed in the Application variable (AV12).
Application Description AV12
None (MUX) Provides remote control of the outputs from another device. 0
VAV Provides control of a simple VAV box and optional fan. 1
VVT Provides control of a simple VVT box and optional fan. 2
HPU Provides control of a Heat Pump Unit with a reversing valve and a fan. 3
FCU Provides control of a Fan Coil Unit with heating/cooling and a fan. 4
Unit Heater No longer supported. Use FCU instead.
Radiation/Reheat Provides control of single or multi-stage heating with no fan. 5
Humidity Provides control of a Humidifier and assumes a model of the BACstat
with a humidity sensor.
6
Refer to the Application section of this guide for further detail on each of these control strategies, starting on page
18.
2. ALGORITHM MODE
The application control strategy operates in one of various basic modes, as determined by the Algorithm Mode
variable (AV13).
Algorithm Mode Description AV13
Unoccupied (Night) Uses Night Setpoints 0
Occupied (Day) Uses Day Setpoints 1
Minimum VAV Only: Forces the box to its minimum position 10
Maximum VAV Only: Forces the box to its maximum position 11
Closed VAV Only: Forces the box to its fully closed position 12
Open VAV Only: Forces the box to its fully open position 13
Zero Calibration VAV Only: Forces calibration of the bias so the air flow reads
zero at current conditions. This assumes that the Air Handler has
been shut down and that there is no air flow at the box.
14
Heating Lockout All heating control and associated icons are completely disabled
(as though no heating stages even exist)
20
Cooling Lockout All cooling control and associated icons are completely disabled
(as though no cooling stages even exist)
21
Heating/Cooling Lockout Both heating and cooling control and their icons are disabled 22
Unless the fourth digit of the Display Code (AV15) is set to 1 or 5, or Fan Control is configured as Manual, the
top two buttons on the BACstat – OFF (O) and ON(I) – will switch between Night and Day modes. Changing to
the other modes for VAV is keypad accessible in Air Balancer mode within the Service Tool menus. The Alg.
Mode (AV13) is also fully accessible from another device over the network (via GCL or ORCAview OWS or 3rd
Party devices), to command it to any mode as required (including the lockouts).

Delta Controls
Document Edition 3.1 Page 13 of 35
Lockout Modes
Heating and cooling lockout modes are operational for all Control Applications.
Basically, once a BACstat has been configured for various stages of heating and cooling, either the heating and/or
cooling may be disabled on-the-fly as necessary for various control strategies simply by commanding the Alg.
Mode (AV13). In all other regards, control continues to function the same as it would when in Occupied mode.
Communications Reset Enable
The Algorithm Mode variable also has a property represented by a checkbox in the object dialog called Comm
Reset Enable. This can be enabled or disabled, depending on the requirements of the installation.
Disabled Enabled (the default as of Release 3 Firmware)
•The BACstat does not try a reset on the loss
of communications
•Should the device reset, the mode reverts to
whatever it was just prior to the reset (i.e., last
value as stored in non-volatile memory)
•The BACstat will reset once on the loss of
communications to try to re-establish
communications
•Should the device reset, the mode is set to
DAY
3. BOX MODE (DNT-T103AND DNT-T221ONLY)
When the application control strategy is configured for either VAV or VVT, the Box Mode (variable AV33) can
be set to either cooling (default) or heating. When set to cooling, the air supply is treated as the first stage of
cooling. When set to heating, the cooling controller is inverted and the air supply is treated as the first stage of
heating.
Box Mode Description AV33
Cooling Duct Supply Air to the box provides cooling (default) 0
Heating Duct Supply Air to the box provides heating 1
Note that this variable cannot be commanded or changed from the BACstat. As this function is completely
dependent on the air supplied to the boxes from another source, this variable would normally be commanded over
the network (i.e., typically via GCL) whenever the air system changes between heating and cooling.
NOTE:In Release 3, VAV and VVT applications can no longer be configured with more than 1 stage of cooling.
In earlier releases of firmware, do not configure a BACstat with more than 1 stage of cooling, as
additional stages of cooling don’t work properly when Box Mode is ever set to heating.
SOFTWARE LOOP CONTROLLER (DNT-T103 and DNT-T221 Only)
1. GENERAL
The operation of the BACstat II is centered around a software controller. The controller uses the following
parameters in its operation.
Parameter Object Default Value Notes
Room Temperature AI1 N/A Input 1 **
Temperature Setpoint* OCCUPIED: Uses Day Setpoint (AV6)
UNOCCUPIED: Uses Night Heat Setpoint
(AV10) if the Input is below the Day Setpoint
(AV6); and uses the Night Cool Setpoint
(AV11) if the Input is above the Day Setpoint
(AV6); otherwise it is in a null zone.
Proportional Band AV19 4.0 ºF / 2.0 ºC Degrees F or C as configured for AI1
Reset Rate AV20 1.0 Resets per hour
Day Differential AV9 1.0 ºF / 0.5 ºC Degrees F or C as configured for AI1
* Humidity Setpoint if operating as a Humidity controller ** Input 3 (AI3) if operating as a Humidity controller

Error! No text of specified style in document. DNS-24, DNT-T103, & DNT-T221 Application Guide
Page 14 of 35 Document Edition 3.1
2. CONTROLLER OPERATION
Heating
Setpoint
-100%
Cooling
Heating
Day Setpoint
Cooling
Setpoint
Day
Differential
Deadband
Proportional BandProportional Band
Controller
Output
(Cooling)
0%
100%
Controller
Output
(Heating)
0%
Temperature
NORMAL CONTROLLER ACTION
Deadband is a span of 0.2 around setpoint (heating or cooling) over which neither heating nor cooling takes place.
Here are a few rules and restrictions to how the internal Loop Controller functions:
•Heating and Cooling will not be ONat the same time
•If the Input temperature is less than (Day Setpoint – (Day Differential – ½ Deadband)) then the controller is
in HEATING
•If the Input temperature is greater than (Day Setpoint + (Day Differential + ½ Deadband)) then the controller
is in COOLING
•If the Input temperature is between these two extents for Heating and Cooling, then the controller is in A null
zone
For all control applications (except when Box Mode is heating in VAV or VVT) the Controller Status (AV14)
will modulate from -100 to 100% and sequence any necessary output stages. A value of 0 to 100% represents
heating output from the controller, while a value of 0 to -100% represents cooling output from the controller.
Heating
Setpoint
Flow
Damper
Auxilary
Heating
Day Setpoint
Cooling
Setpoint
Day
Differential
Deadband
Proportional BandProportional Band
100%
Controller
Output
0%
Temperature
200%
WITH BOX MODE = HEATING

Delta Controls
Document Edition 3.1 Page 15 of 35
For VAV or VVT applications, when the Box Mode is changed to heating, cooling is inverted and used for
controlling the flow damper as the first stage of heating, and the null zone is placed on the far right. Moving from
right to left, away from setpoint, the Controller Status (AV14) will modulate from 0 to 200% and sequence all the
necessary heating stages. The flow damper modulates open over the first 0 to 100% and in so doing provides the
first stage of heating. Any additional stages of heating modulate open over 100 to 200%. Therefore, only when
the Box Mode is in heating does the Controller Status (AV14) modulate to a value greater than 100%, where
200% indicates all heating is fully open.
For heating lockout (in all applications), the heating output from the controller is forced to 0%, and the heating
icon is disabled on the LCD. Similarly, for cooling lockout, the cooling output from the controller is forced to
0%, and the cooling icon is disabled on the LCD. As a result, the Controller Status (AV14) will be limited
accordingly.
3. CONTROLLER STAGING
Each controller can be split up into as many as three stages. The number of stages is automatically determined by
the output configuration associated with the selected application control strategy. The controller stages are
cascaded.
Cooling
Controller
C1 C2 C3
0%
100%
0%
100%
4. RESET ACTION (RESET RATE IN REPEATS PER HOUR)
If the Reset Rate is non-zero, reset action is enabled. As long as there is a difference (or error) between the input
value (i.e., space temperature) and setpoint value, reset action will increment or decrement the Controller Status
value (AV14) over time - in proportion to the value of the reset rate and the magnitude of the error - in an attempt
to remove the error. In this way, the Controller Status value is continually fluctuating in order to reach setpoint.
Also note that the amount of reset does not decrease internally as the input value approaches setpoint, but the reset
value is frozen while in deadband. The only time reset action has no affect on the controller output is when the
input is equal to the setpoint (no error). For this reason, be cautious about applying too much reset action,
otherwise you may cause unnecessary movement on actuators. By setting Reset Rate to 0, you disable reset
action altogether.

Error! No text of specified style in document. DNS-24, DNT-T103, & DNT-T221 Application Guide
Page 16 of 35 Document Edition 3.1
SETPOINTS
The BACstat II uses a series of setpoints for various purposes, most of which interact with one another.
For a complete list of these setpoints and other objects and their defaults, refer to the Object table on page
9. It is important to note that when you change the units setting between ºC and ºF all of these setpoints
will revert back to their matching default values – the BACstat does not do a conversion on-the-fly. What
follows hereafter is a working description for each of these setpoints. If the particular setpoint is settable
in the Configuration Menu it is indicated with its LCD text.
Day Setpoint (AV6) – SEt
This is the setpoint used when in DAY mode. With the Display Code (AV15) set to an appropriate value
the setpoint can be adjusted up or down by pressing the buttons. Whether or not this setpoint is displayed
or is adjustable on the LCD, it is used internally for control. The units for the setpoint are ºC or ºF (as per
AI1) unless the second digit of the Display Code (AV15) is set to 3 (for Humidity), in which case the units
become %RH. The value for Day Setpoint can also be set in the Configuration Menu, or by commanding
the variable (via GCL or ORCAview OWS or 3rd Party devices).
Day Minimum Setpoint (AV7) – LO
This is the minimum value a user can adjust the Day Setpoint to. If an attempt is made to adjust the Day
Setpoint lower, it will not change. If a lower value is commanded from the OWS or another device, it will
not accept the change. The value for Day Minimum Setpoint can be set in the Configuration Menu, or by
commanding the variable (via GCL or ORCAview OWS or 3rd Party devices).
Day Maximum Setpoint (AV8) – HI
This is the maximum value a user can adjust the Day Setpoint to. If an attempt is made to adjust the Day
Setpoint higher it will not change. If a higher value is commanded from the OWS or another device, it
will not accept the change. The value for Day Maximum Setpoint can be set in the Configuration Menu,
or by commanding the variable (via GCL or ORCAview OWS or 3rd Party devices).
Day Differential (AV9) – DIF
This is the differential setting between the Day Setpoint and the internal Heating Setpoint (which is used
for heating control), and between the Day Setpoint and the internal Cooling Setpoint (which is used for
cooling control). The one value is used for both, one on each side of the Day Setpoint. Refer to the
diagram on page 14. The purpose of this setting is to separate heating from cooling so as to prevent
overlap, and to create a reasonable null zone, within which no modulating control takes place – preventing
unnecessary actuator wear when the measured value is close to or on setpoint. The value for Day
Differential can be set in the Configuration Menu, or by commanding the variable (via GCL or
ORCAview OWS or 3rd Party devices).
Day Heating Setpoint (Internal)
This is the setpoint used internally for heating control (which is the Day Setpoint - Day Differential). This
value is not directly adjustable. It can only be adjusted by setting either the Day Setpoint or the Day
Differential.
Day Cooling Setpoint (Internal)
This is the setpoint used internally for cooling control (which is the Day Setpoint + Day Differential).
This value is not directly adjustable. It can only be adjusted by setting either the Day Setpoint or the Day
Differential.

Delta Controls
Document Edition 3.1 Page 17 of 35
Night Heating Setpoint (AV10)
This is the setpoint used when in NIGHT mode and night setback heating is required. If the current
temperature is below the current Day Setpoint when in NIGHT mode, this value will be displayed on the
BACstat LCD (depending on how setpoint display has been defined by the Display Code). Please note
that this value is not adjustable either by a user or through the keypad in any Configuration or Service
menu. It can only be changed by commanding the variable (via GCL or ORCAview OWS or 3rd Party
devices). Pressing the up or down arrow will cycle to show the Night Cooling Setpoint.
Night Cooling Setpoint (AV11)
This is the setpoint used when in NIGHT mode and night setback cooling is required. If the current
temperature is above the current Day Setpoint when in NIGHT mode, this value will be displayed on the
BACstat LCD (depending on how setpoint display has been defined by the Display Code). Please note
that this value is not adjustable either by a user or through the keypad in any Configuration or Service
menu. It can only be changed by commanding the variable (via GCL or ORCAview OWS or 3rd Party
devices). Pressing the up or down arrow will cycle to show the Night Heating Setpoint.
CONTROL DIAGRAM (DNT-T103 and DNT-T221 Only)
The following diagram helps to provide an illustration of the relationship between the internal software
loop controller and various objects, including outputs.
Controller &
Sequencing
Input (AI1)
Setpoint (AV6)
Binary (Dir or Rev)
PWM (Dir or Rev)
Analog (Dir or Rev)
Analog VAV Flow Damper
Tri-State Actuator
Tri-State VAV Flow Damper
Heating Stage 1 (H1)
Heating Stage 2 (H2)
Heating Stage 3 (H3)
Cooling Stage 1 (C1)
Cooling Stage 2 (C2)
Cooling Stage 3 (C3)
Constant Fan Operation (C)
Intermittent Fan Operation (I)
Manual Fan Operation (M)
Output 1
Output 2
Binary (Dir or Rev)
PWM (Dir or Rev)
Time Proportioned (D or R)
Analog (Dir or Rev)
Tri-State Actuator
Tri-State VAV Flow Damper
Output 3
Binary (Dir or Rev)
PWM (Dir or Rev)
Time Proportioned (D or R)
Cooling
Heating
Fan
Algorithm Mode
(AV13)
BACstat Buttons
(or remote
command via
GCL or OWS)
∗
∗ ∗
∗ ∗
∗
∗
∗
∗ ∗
∗
∗
∗
Notes:
1.
∗
indicates the output type is only applicable for the DNT-T103.
2.
∗ ∗
indicates the output type is only applicable for the DNT-T221.
3. An analog output type for outputs 1 & 2 on a DNT-T221 when HPU has been
selected provides a 0 or 10v signal - it is not a 0 to 10v signal nor a dry contact.
4. The output functions and types that are available are dependent on the control
application selected and what was selected for the previous output.
5. This is not a comprehensive diagram and does not include all output functions.
Refer to Output Functions and Types later in this document.
Binary Fan (On/Off)
∗
∗

Error! No text of specified style in document. DNS-24, DNT-T103, & DNT-T221 Application Guide
Page 18 of 35 Document Edition 3.1
CONTROL APPLICATIONS (DNT-T103 and DNT-T221 Only)
1. NONE (or MUX) – [Application (AV12) = 0]
Function: No local control strategy, allowing the outputs (via AV1 to AV3) to be directly controlled from a
remote device.
•Triac outputs may be configured as Binary (which are not delayed; their values are transferred immediately
upon being received), PWM, and Tri-state (on Outputs 1 & 2).
•Analog outputs may be configured for 0-10v actuators (DNT-T221 only).
•Outputs configured as Pulse Width Modulation require that their “Low” and “High” variables are
appropriately configured for the particular type of device the outputs are connected to. Default values of 59
and 293 are suitable for Belimo PWM actuators (representing 0.59 and 2.93 seconds respectively).
•Outputs 1 and 2 configured as a Tri-State pair require that the “Tri-State Runtime” (AV24) be configured for
the associated Tri-State actuator. The default of 120 seconds is suitable for certain Honeywell actuators.
NOTE:BACstats (particularly with I/O) that are connected to a BACnet MS/TP network are
designed to operate as stand-alone devices using a local control application. For custom
applications and MUXing purposes, connect the BACstat to a LINKnet network.
2. VAV – [Application (AV12) = 1]
Function: Control of a simple VAV box with air flow measured with a Kavlico sensor (DFT740-A) or Setra
sensor on Input 2 (0 to 1” range), a Tri-State damper on Outputs 1 and 2 (for DNT-T103) or an analog damper on
Output 1 (for DNT-T221), and various options on the remaining outputs (some no longer available in Release 3).
DNT-T103 I/O (Outputs 1 to 3 are Triacs)
Input AI1 Input AI2 Input AI3 Remote AV5 Output 1 Output 2 Output 3
Room Temp. Air Flow
(0 to 1”)
N/A Optional OAT Tri-State Flow
Damper (Open)
Tri-State Flow
Damper (Close)
Heating 1
Room Temp. Air Flow
(0 to 1”)
N/A Optional OAT Tri-State Flow
Damper (Open)
Tri-State Flow
Damper (Close)
Cooling 2
(not in R3)
Room Temp. Air Flow
(0 to 1”)
N/A Optional OAT Tri-State Flow
Damper (Open)
Tri-State Flow
Damper (Close)
Fan
Room Temp. Air Flow
(0 to 1”)
N/A Optional OAT Tri-State Flow
Damper (Open)
Tri-State Flow
Damper (Close)
None
(MUX)
DNT-T221 I/O (Outputs 1 & 2 are Analog, and Output 3 is a Triac)
Input AI1 Input AI2 Input AI3 Remote AV5 Output 1 Output 2 Output 3
Room Temp. Air Flow
(0 to 1”)
N/A Optional OAT Analog Flow
Damper
Heating 1 Heating 2
Room Temp. Air Flow
(0 to 1”)
N/A Optional OAT Analog Flow
Damper
Heating 1 Cooling 2
(not in R3)
Room Temp. Air Flow
(0 to 1”)
N/A Optional OAT Analog Flow
Damper
Heating 1 Fan
Room Temp. Air Flow
(0 to 1”)
N/A Optional OAT Analog Flow
Damper
Heating 1 None
(MUX)
Room Temp. Air Flow
(0 to 1”)
N/A Optional OAT Analog Flow
Damper
Cooling 2
(not in R3)
Heating 1
Room Temp. Air Flow
(0 to 1”)
N/A Optional OAT Analog Flow
Damper
Cooling 2
(not in R3)
Fan
Room Temp. Air Flow
(0 to 1”)
N/A Optional OAT Analog Flow
Damper
Cooling 2
(not in R3)
None
(MUX)
Room Temp. Air Flow
(0 to 1”)
N/A Optional OAT Analog Flow
Damper
None
(MUX)
None
(MUX)

Delta Controls
Document Edition 3.1 Page 19 of 35
NOTES:For fan-powered boxes, series fans should always be configured for continuous
operation – never intermittent or the fan could run backwards on startup. When a
parallel fan is used in a heating application it should be configured as the 1st stage of
heating (and wired to the appropriate output accordingly), rather than as a fan output.
Setup Parameters
Setup Variable Function Notes
AV24 Tri-state Flow Damper Runtime Default of 120 seconds
AV25 Air Flow Factor Converts Duct size and Air flow
velocity to CFM or Liters/Second
AV26 Air Flow Minimum Minimum Air Flow Setpoint
AV27 Air Flow Maximum Maximum Air Flow Setpoint
AV28 PWM minimum value or Binary On Delay
(or Binary Off Delay for a Fan)
Depends on OP3 configuration
AV29 PWM maximum value or Time
Proportioned Heating Controller Limit
Depends on OP3 configuration
Sequence of Operation
The air flow setpoint is generated from the Cooling Minimum setpoint, Cooling Maximum Setpoint and the Cool
1 value as shown below.
Air flow Setpoint
Max
Cooling flow
Min
Cooling flow
Controller Output (Cooling 1)
0
Max Flow
0% 100%
The Air Flow input is compared to the current Airflow setpoint by the flow control loop. On the DNT-T103, the
Tri-State damper outputs 1 and 2 are used to control the damper to adjust the flow to match the current airflow
setpoint. The rate of the damper from closed to open is adjusted using AV24 – Damper Run Time. The default
value is 120 seconds. On the DNT-T221, the analog damper output 1 is used to control air flow, but also requires
that an appropriate runtime be set for the actuator (via Setup variable AV24).
In Unoccupied Deadband mode the Airflow Setpoint is set to zero.
Output 3 may be selected as a fan for fan-powered boxes. Alternatively, the output may be selected to be Heating
1 or supplementary Cooling 2, which may be of type Binary or PWM or Timed Proportional.
Note that variable AV25 (Air Flow Factor) represents a value that includes duct size and any other constants or
conversion factors so Input 2 reads air flow (in CFM or L/S), and requires that:
•a 0 to 1” H2O (0 to 248.8 Pa) sensor is connected to Input 2 (AI2); and
•the air flow units of either CFM or L/S is selected
AFF = box K factor * Area in in2/ 144 [which is then divided by 2.1188 to get L/S, if desired]
Also refer to page 13 for information on Box Mode and Controller Operation.
NOTE:So as to prevent a series fan
from starting backwards, the damper
stays shut in all night modes – it does
not modulate. If heating is required
during the night, a radiant panel can
be used to meet the Night Heating
Setpoint (AV10). Since the damper
will not modulate for night cooling
(AV11), if night cooling is required
write a GCL program in an
associated DSC controller on the
network to put the box/BACstat into
Occupancy mode and bring on the air
system until the setpoint is achieved.

Error! No text of specified style in document. DNS-24, DNT-T103, & DNT-T221 Application Guide
Page 20 of 35 Document Edition 3.1
3. VVT – [Application (AV12) = 2]
Function: Control of a simple VVT box with a Tri-State damper on Outputs 1 and 2 (for DNT-T103) or an
analog damper on Output 1 (for DNT-T221), and various options on the remaining outputs (of which some
options are no longer available in Release 3 firmware).
DNT-T103 I/O (Outputs 1 to 3 are Triacs)
Input AI1 Input AI2 Input AI3 Remote AV5 Output 1 Output 2 Output 3
Room Temp. N/A Optional OAT Tri-State
Damper - Cool
(Open)
Tri-State
Damper - Cool
(Close)
Heating 1
Room Temp. N/A Optional OAT Tri-State
Damper - Cool
(Open)
Tri-State
Damper - Cool
(Close)
Cooling 2
(not in R3)
Room Temp. N/A Optional OAT Tri-State
Damper - Cool
(Open)
Tri-State
Damper - Cool
(Close)
Fan
Room Temp. N/A Optional OAT Tri-State
Damper - Cool
(Open)
Tri-State
Damper - Cool
(Close)
None
(MUX)
DNT-T221 I/O (Outputs 1 & 2 are Analog, and Output 3 is a Triac)
Input AI1 Input AI2 Input AI3 Remote AV5 Output 1 Output 2 Output 3
Room Temp. N/A Optional OAT Analog Damper
(Cooling 1)
Heating 1 Heating 2
Room Temp. N/A Optional OAT Analog Damper
(Cooling 1)
Heating 1 Cooling 2
(not in R3)
Room Temp. N/A Optional OAT Analog Damper
(Cooling 1)
Heating 1 Fan
Room Temp. N/A Optional OAT Analog Damper
(Cooling 1)
Heating 1 None
(MUX)
Room Temp. N/A Optional OAT Analog Damper
(Cooling 1)
Cooling 2
(not in R3) ☺
Room Temp. N/A Optional OAT Analog Damper
(Cooling 1)
Cooling 2
(not in R3)
Fan
Room Temp. N/A Optional OAT Analog Damper
(Cooling 1)
Cooling 2
(not in R3)
None
(MUX)
Room Temp. N/A Optional OAT Analog Damper
(Cooling 1)
None
(MUX)
None
(MUX)
NOTE:For fan-powered boxes series fans should always be configured for continuous
operation – never intermittent or the fan could run backwards on startup. And, in order for
a parallel fan to be properly sequenced it should generally be configured as the 1st stage of
heating (and wired to OP1), rather than as a fan.
Setup Parameters
Setup Variable Function Notes
AV24 Damper Runtime (Tri-state or Analog) Default of 120 seconds
AV25 N/A
AV26 Damper Minimum Damper Minimum Position
AV27 Damper Maximum Damper Maximum Position
AV28 PWM minimum value or Binary On Delay
(or Binary Off Delay for a Fan)
Depends on OP3 configuration
AV29 PWM maximum value or Time Proportioned
Heating Controller Limit
Depends on OP3 configuration
This manual suits for next models
3
Table of contents
Other Delta Controls Thermostat manuals

Delta Controls
Delta Controls DNT-T103 User manual
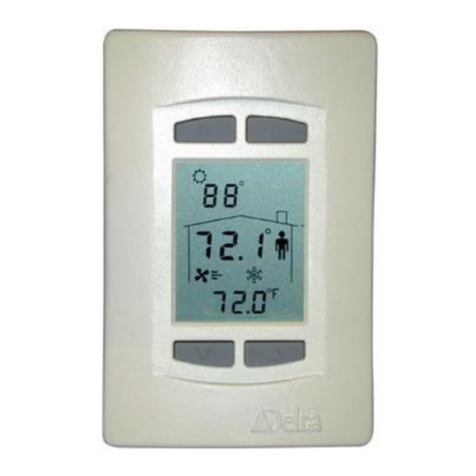
Delta Controls
Delta Controls BACstat II User manual
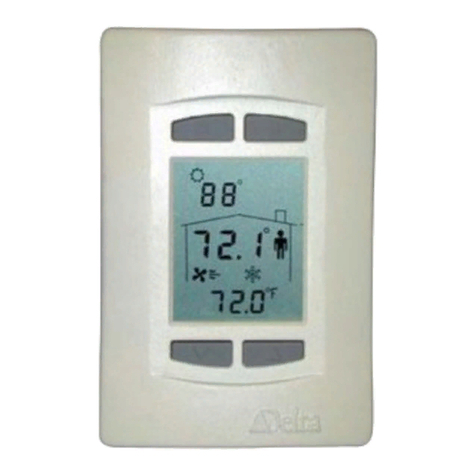
Delta Controls
Delta Controls BACstat III DNT-T221-FCU User guide
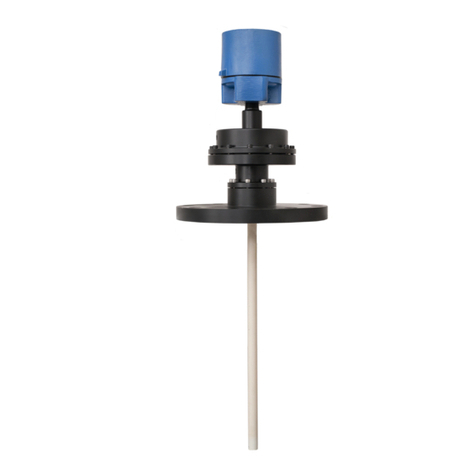
Delta Controls
Delta Controls HTP User manual
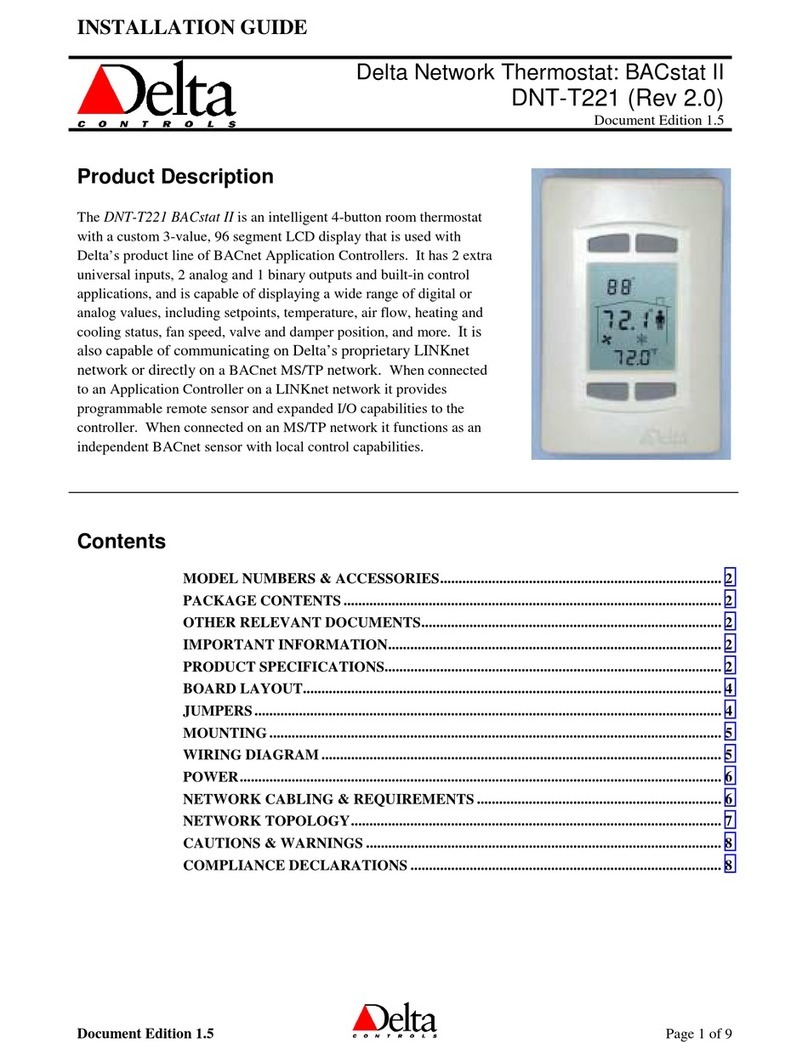
Delta Controls
Delta Controls DNT-T221 User manual
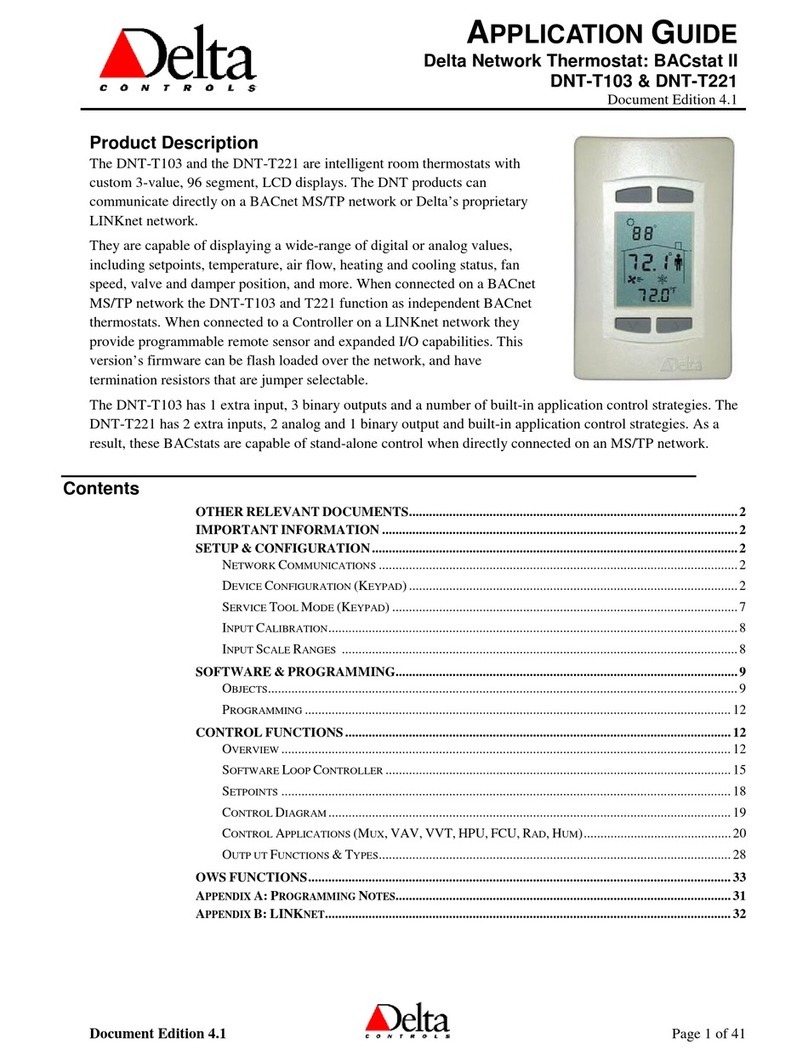
Delta Controls
Delta Controls DNT-T103 User guide
Popular Thermostat manuals by other brands
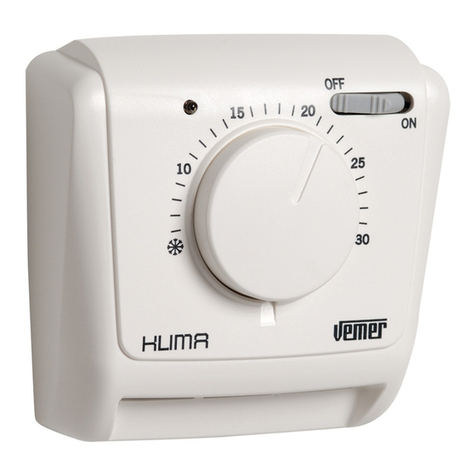
Vemer
Vemer KLIMA Series user manual
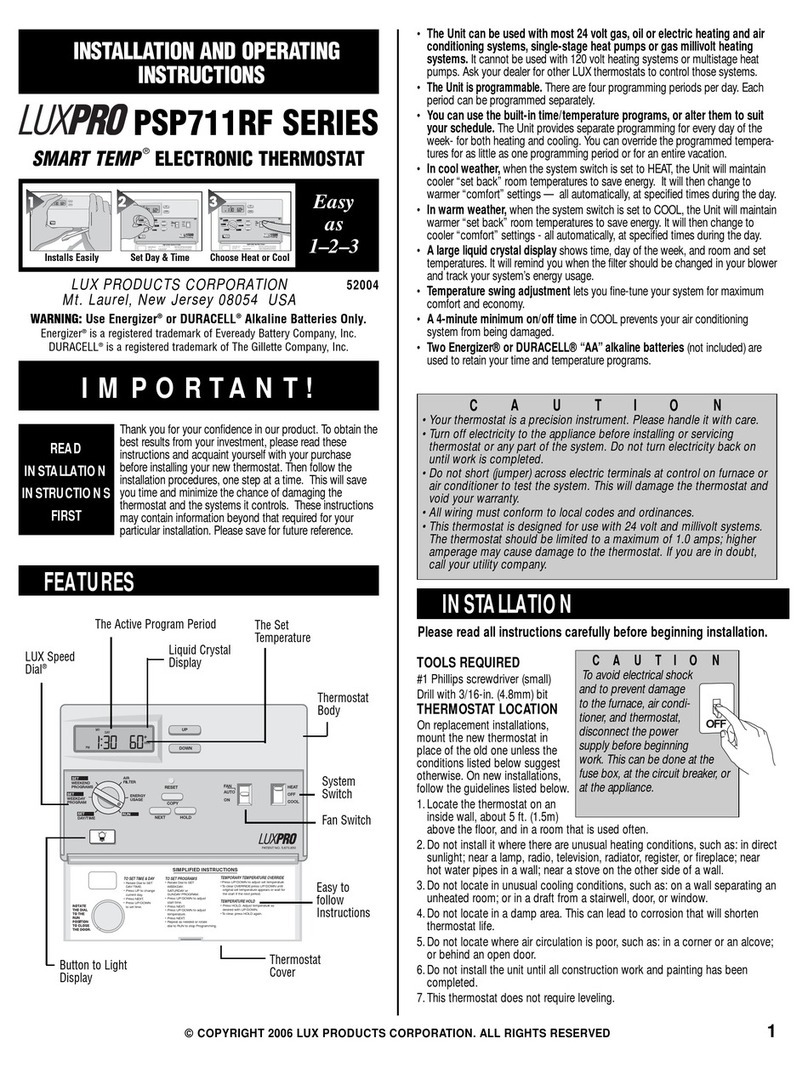
Lux Products
Lux Products PSP711RF Series Installation and operating instructions
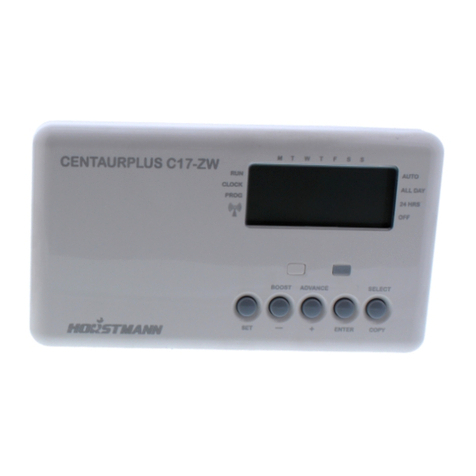
Horstmann
Horstmann CentaurPlus C17-ZW User operating instructions

Radio Thermostat
Radio Thermostat CT101 install guide

Honeywell Home
Honeywell Home VisionPRO 8000 Smart Product data
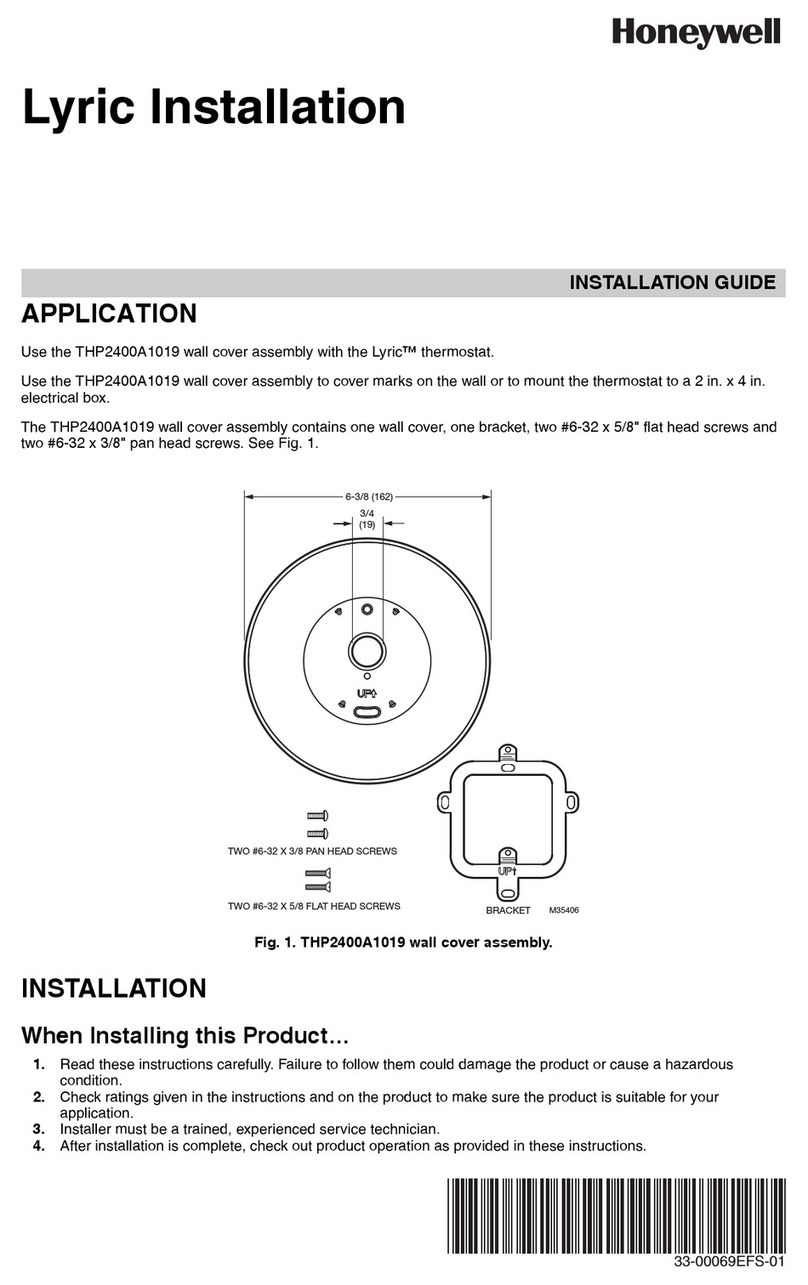
Honeywell
Honeywell Lyric installation guide