Detcon DM-700 User guide

SAFETY MANUAL
SIL 2 Certified Model DM-700 Toxic Gas Sensor
Version 3.0
1 SAFETY CERTIFIED MODEL DM-700 TOXIC GAS DETECTOR
This manual addresses the specific requirements and recommendations applicable to the proper installation, operation, and
maintenance of all Safety-Certified (SIL-Certified) DM-700 sensors. For complete information regarding performance,
installation, operation, maintenance and specifications of the Model DM-700, refer to instruction manual Document
#3207.
2 SAFETY MESSAGES
Procedures and instructions in this section may require special precautions to ensure the safety of personnel performing
the operations. Information that raises potential safety issues is indicated by the word “Warning”. Always read and
understand these safety messages.
Warning:
The DM-700 Gas Detector is intended for use in hazardous environments that may include dangerous levels of toxic gas
vapors. This product must be properly installed, operated and maintained. Improper installation or use could result in
death or serious injury.
If applicable, do not remove the XP Junction box cover in explosive environments when device power is on and circuits
are live.
Detector must be properly installed, and XP junction box cover must be fully engaged to meet hazardous area explosion-
proof/non-incendive requirements.
3 DESIGN
The Model DM-700 is an electrochemical type toxic gas detector that is classified as a Type B smart device according to
IEC61508. The DM-700 sensor provides a 4-20 mA output that is proportional to toxic gas vapor concentrations in the
ranges of 0-1 ppm up to 0-10000 ppm. The DM-700 contains extensive self-diagnostics and is programmed to send the

current output to a specified failure state (0 mA) upon internal detection of a failure. A Modbus RS485 serial output is
available in addition to the analog signal output. The Safety Certification for the DM-700 Gas Detector only covers the
use of the standard analog 4-20 mA output.
Safety-Certification of the DM-700 includes:
The 4-20 mA output
The RS-485 Modbus signal output is not part of the SIL Certification.
Note: Proper analog signal loop resistance must be installed as documented in the instruction manual to enable proper
4-20 mA signal function. The end user must perform zero and span calibrations after any significant configuration
changes or repair events. These include: restore defaults, change of range, replacing plug-in electrochemical sensor, and
replacing ITM module.
4 VALID INPUT RANGE
DM-700 fault annunciation is provided on the 4-20mA signal output loop by signaling to 0mA current output level for at
least 5 seconds. The receiving device must be programmed to indicate an out-of-range condition when current levels reach
overcurrent (>21.5 mA) or undercurrent (<1.8 mA).
Note: The DM-700 analog signal output is not safety-rated during detector warm-up, configuration mode, calibration
mode, and during signal output loop testing. Alternative means should be used at the jobsite to ensure facility safety
during these activities.
5 DIAGNOSTIC RESPONSE TIME
The DM-700 will perform all critical diagnostic functions within 1 hour. This is the worst case diagnostic detection time.
6 CERTIFICATION
The DM-700 Safety-Certified version is certified by exida® to IEC 61508 for single input use in low and high demand,
SIL 2 Safety Instrumented Systems. The DM-700 sensor is SIL2 certified as an individual component, but it can be used
as part of a larger Safety Instrumented Systems as long as it is applied per the guidelines of this Safety Manual.
The DM-700 is SIL2 certified per IEC 61508-2010 with an HFT=0.
The DM-700 is a Proven-In-Use (PIU) device per IEC 61508-2010. The revision levels of the SIL 2 certified DM-700
sensor is noted as Main PCB Rev 1, Sensor Barrier PCB Rev 02, and Firmware V2.21M.
7 SAFETY – CERTIFIED PRODUCT IDENTIFICATION
The model number printed on the label will include the character “S” in the model number string, indicating exida®
approval for SIL 2 standard. Example: Model DM-700 S.
8 CONSTRAINTS
The safety function of the Detcon Model DM-700 Toxic Gas Sensor is limited by the following constraints:
-Shall not be used in continuous mode applications
-Toxic gas is not constantly present (e.g. for long periods of more than 24 hours)
-The maximum load on the 4-20mA output of the DM-700 is 1KΩ with 24VDC input power and 500Ω with
12VDC input power

-Shall be zero and span calibrated every 180 days using a calibrated gas standard. After calibration, the sensor shall
be proof tested by applying the calibration gas and checking for the proper response of the 4-20mA output.
-After the DM-700 has been off power for more than 24 hours, it shall be allowed a 1 hour start-up period before
performing its safety function
-When the DM-700 detects a fault condition it will drive the output to 0mA for at least 5 seconds. Any PLC, DCS,
or other control system used to monitor the DM-700 shall indicate a fault when the output from the sensor drops
below 1.8mA for more than 4 seconds
-Any PLC, DCS, or other control system used to monitor the DM-700 shall indicate that the sensor is in calibration
mode when the output is greater than 1.8mA but less than 2.2 mA. When in calibration mode, the DM-700 cannot
perform its safety function.
-Any PLC, DCS, or other control system used to monitor the DM-700 shall indicate an over-range condition when
the output from the sensor is above 21.5mA. When the DM-700 is over-range, the actual gas concentration may
be higher than what is being reported by the 4-20mA output.
-The sensor shall not be installed in applications where it will be exposed to:
oTemperatures or humidity levels that exceed the specified limits
oSilicone vapors, routine long term exposure to any alcohols and solvents (especially from strong cleaning
agents), vapors from lead, and phosphates that might act as poisons that cause permanent damage.
-Shall be operated with an input power of 11VDC – 30VDC
-Shall be installed oriented vertically and mounted more than 1ft. above the ground
-Shall not be operated, stored, or transported outside the temperature range of -40ºC to 50ºC
-The DM-700 enclosure and connected cabling shall be properly grounded and shielded
-The Modbus interface shall not be connected when the DM-700 is used in SIL2 applications
-The magnetic switches on the DM-700 shall not be used while the DM-700 is performing its safety function
-The user shall validate the initial configuration and any subsequent configuration changes of the DM-700 before
using it for its safety function. This validation shall be accomplished by performing a proof test after all
configurations are complete.
-No online software tools are needed or are to be used when the DM-700 is performing its safety function.
9 INSTALLATION
NOTE: For complete information regarding performance, installation, operation, maintenance and specifications of
Model DM-700, refer to instruction manual Document #3207.
No specific or additional detector installation requirements exist above and beyond the standard installation practices
documented in the Model DM-700 Instruction Manual.
Environmental operating specifications are applicable as published in the general specifications section in the Model DM-
700 instruction manual.
The DM-700 operating power distribution system should be designed and installed so the terminal voltage does not drop
below 11 VDC when measured at any specific location. The maximum current limit must be less than 0.5 amperes. The
over-voltage protection on the power distribution system must be set for 30 VDC.
10 START-UP AND COMMISSIONING
The Safety Certified DM-700 gas detector can be commissioned by any qualified person with knowledge of gas detection
instruments and the configuration device being used. Refer to the Start-Up and Commissioning sections provided in the
DM-700 instruction manual.

Any configuration changes to the DM-700 require the use of the Detcon programming magnet. This programming magnet
is the only security measure used to prevent unauthorized changes to the DM-700 configuration.
11 OPERATION, MAINTENANCE, INSPECTION AND PROOF TESTING
All normal installation, start-up, and full field calibration recommendations as documented in the DM-700 instruction
manual are applicable to the Safety Certified DM-700 gas detector.
Safety – Certified DM-700 gas detectors require additional Proof Testing to be performed in all cases.
Personnel performing Proof Test procedures shall be competent to perform the task. All proof test results must be
recorded and analyzed. Any corrective actions taken must be documented in the event that an error is found in the safety
functionality. The proof tests must be performed at a frequency as shown in Table 1.
Table 1: Frequency for Performing Proof Tests
DM
-
700 Proof Test Name
Commissioning
Frequency per year
Visual Field Inspection Proof Test
Yes
2
Gas Response
Proof
Test
Yes
2
Output Response
Proof
Test
Yes
1
Warning: Failure to perform the specified testing and inspection may lower or void the SIL rating for the product or
system.
12 VISUAL FIELD INSPECTION PROOF TEST
Tools Required: Programming magnet
Visual inspection of all Safety-Certified DM-700 Gas Detectors shall be conducted semi-annually to confirm that no
external blockage of gas/vapor path into the sensing chamber exists, ex. debris, trash, snow, mud, external equipment, etc.
Corrective action shall include removal of such impediments should they exist. All gas detectors must be inspected to
ensure that they are capable of providing expected performance and protection. The Model DM-700 provides a scrolling
LED display that indicates fault messages when operational parameters are abnormal. A momentary magnetic swipe
across either programming magnet will visually indicate any scrolling Fault Messages should any be present.
Completion of Visual Field Inspection Proof test will be recorded and documented in the SIS logbook.
13 GAS RESPONSE PROOF TEST
Tools Required:
50% of FS Range Span Calibration Gas Cylinder containing target gas in balance Air or N2
(concentration should be at least between 10% and 90% of FS Range)
Calibration Kit provided by Detcon
This proof test, commonly referred to as a “gas bump test”, requires application of high accuracy compressed calibration
gas to the detector while in NORMAL operational mode and inspecting the 4-20 mA signal output level to ensure that the
signal output is accurately indicative of the applied test gas concentration.

Warning: Any external alarm equipment, systems or signaling devices that could be automatically initiated by
performing this test must be disabled or bypassed before performing this test!
When test gas is flowing into the detector, inspection of proper analog signal level output can be made by reading the
analog signal output displayed on the control device. The criteria used for inspection pass is a stabilized response signal
within +/- 20% of the applied gas level. If response test is not within acceptable limits, then a Full Calibration procedure
must be performed and the Gas Response Proof Test re-performed.
13.1 FULL CALIBRATION
Tools Required:
Zero Gas Cylinder – Zero Air or N2 (may use local ambient air if it’s confirmed to be free of the target
gas or any gases with cross-interference)
Span Calibration Gas Cylinder - 50% of FS Range Span Calibration Gas Cylinder containing target gas in
balance Air or N2 (concentration should be at least between 10% and 90% of FS Range)
Calibration Kit provided by Detcon
Programming magnet
Full Calibration shall be conducted when required. The procedure for performing the Full Calibration is
in the Calibration section of the DM-700 instruction manual. In all cases the model DM-700 gas detector
should be allowed to warm up for 5 minutes before conducting a Full Calibration.
Warning: The 4-20mA output from the DM-700 will drop to 2mA during the Full Calibration
Successful completion of the Gas Response Proof Test must be recorded and documented in the SIS
logbook. If the Full Calibration is performed, it should also be documented in the SIS logbook.
14 OUTPUT RESPONSE PROOF TEST
Tools Required:
Span Calibration Gas Cylinder - 50% of FS Range Span Calibration Gas Cylinder containing target gas in
balance Air or N2 (concentration should be at least between 10% and 90% of FS Range)
Calibration Kit provided by Detcon
The Output Proof Test is performed as follows:
1. Inhibit alarm response at the control device.
2. Apply test gas (50% of FS Range) to the detector. Verify correct 4-20mA output signal at the control device.
3. Re-activate alarm response at the control device.
15 FAULT/FAILURE ACTION PLAN
In the event that a Full Calibration does not result in acceptable Gas Response Proof test, then the standard Maintenance,
Troubleshooting, and Device Repair and Return Procedures are listed in the DM-700 instruction manual must be
followed. Any failure to successfully complete the Gas Response Proof Test must be recorded and documented in the SIS
logbook.

16 PRODUCT REPAIR
The DM-700 is partially field-repairable. Follow the DM-700 instruction manual for proper guidance in executing the
allowable field repair/replacement actions. No firmware changes are permitted or authorized. All failures detected by the
transmitter diagnostics or by the Proof Test must be reported.
17 OPERATING, ENVIRONMENTAL, AND PERFORMANCE SPECIFICATIONS
The Safety-Certified DM-700 product versions fully comply with, and must be operated in accordance with the
functional, environmental, and performance specifications provided in the DM-700 instruction manual. A 24 hour mean
time to repair should be assumed for safety availability calculations. All DM-700 diagnostics have a maximum 1 hour test
interval.
18 SPARE PARTS
Refer to “Spare Parts” in the DM-700 instruction manual. Safety Certification is based on having a sufficient number of
spares to achieve a 24 hour mean time to repair.
19 CERTIFICATION AND FAILURE RATE DATA
All Safety-Certified DM-700 models are certified compliant to:
IEC61508:2010
SIL 2 Certified
PFDavg @ 1 year is 1.5% of the SIL2 range.
Safe Failure Fraction (SFF): 91.1%
Safety Accuracy: +/-20% FS Range
Safety Response Time: T80 < 60 seconds
Product Life: 10 years (Intelligent Transmitter Module)
3 years+ (Electrochemical Cell, depending on gas type)
20 CERTIFICATIONS
cCSAus, ATEX, CE Marking (Refer to the Model DM-700 Instruction Manual for details).
FMEDA Report available.
For complete information regarding performance, installation, operation, maintenance and specifications of Model DM-
700, refer to the instruction manual Document #3207.
21 REVISION LOG
Revision Date Changes made Approval
1.0
7/26
/13
Initial Release
RJM
2.0
8/2/13
Changed startup time to 1 hour in Section 8. Changed proof test
accuracy to ±20% in Section 13.
RJM
3.0
8/8/13
Add product life for electrochemical cell
RJM
Other manuals for DM-700
1
Table of contents
Other Detcon Gas Detector manuals
Popular Gas Detector manuals by other brands

CAMPERGUARD
CAMPERGUARD KL-QG05 quick start guide

SENKO
SENKO SP-MGTP user manual

DALEMANS
DALEMANS D-TEX3F+ instruction manual
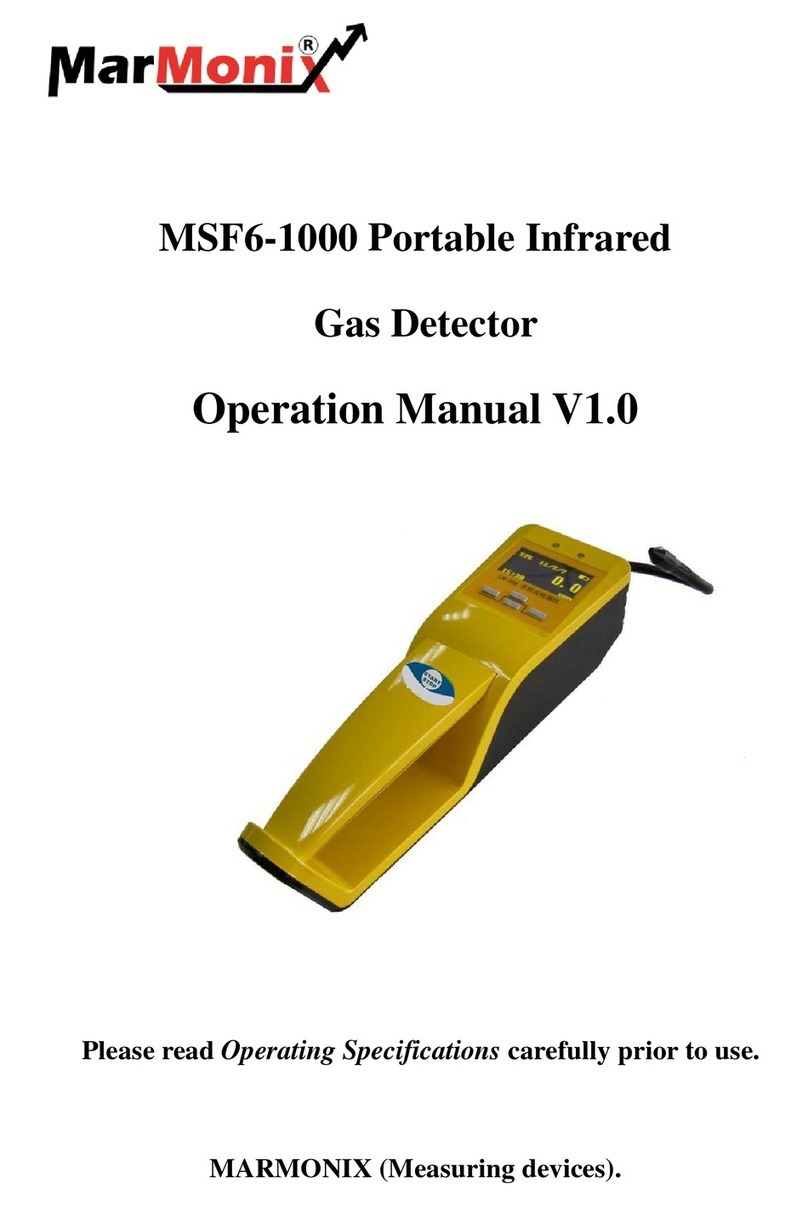
MarMonix
MarMonix MSF6-1000 Operation manual
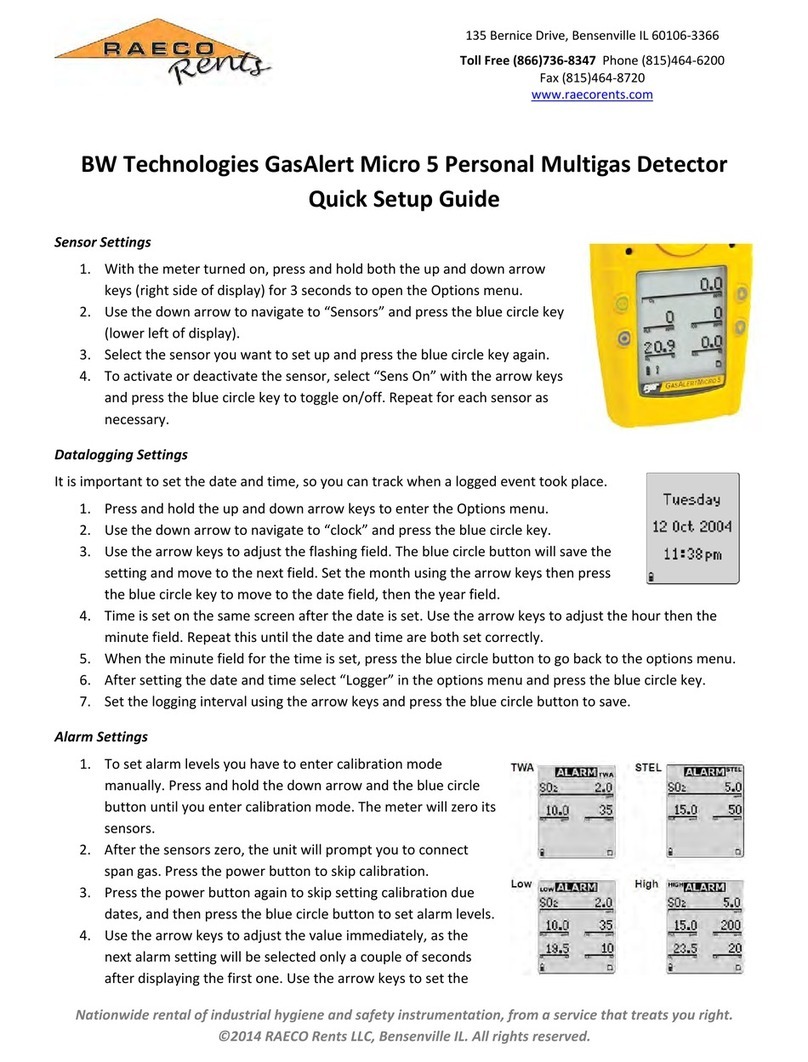
BW Technologies
BW Technologies GasAlert Micro 5 Quick setup guide
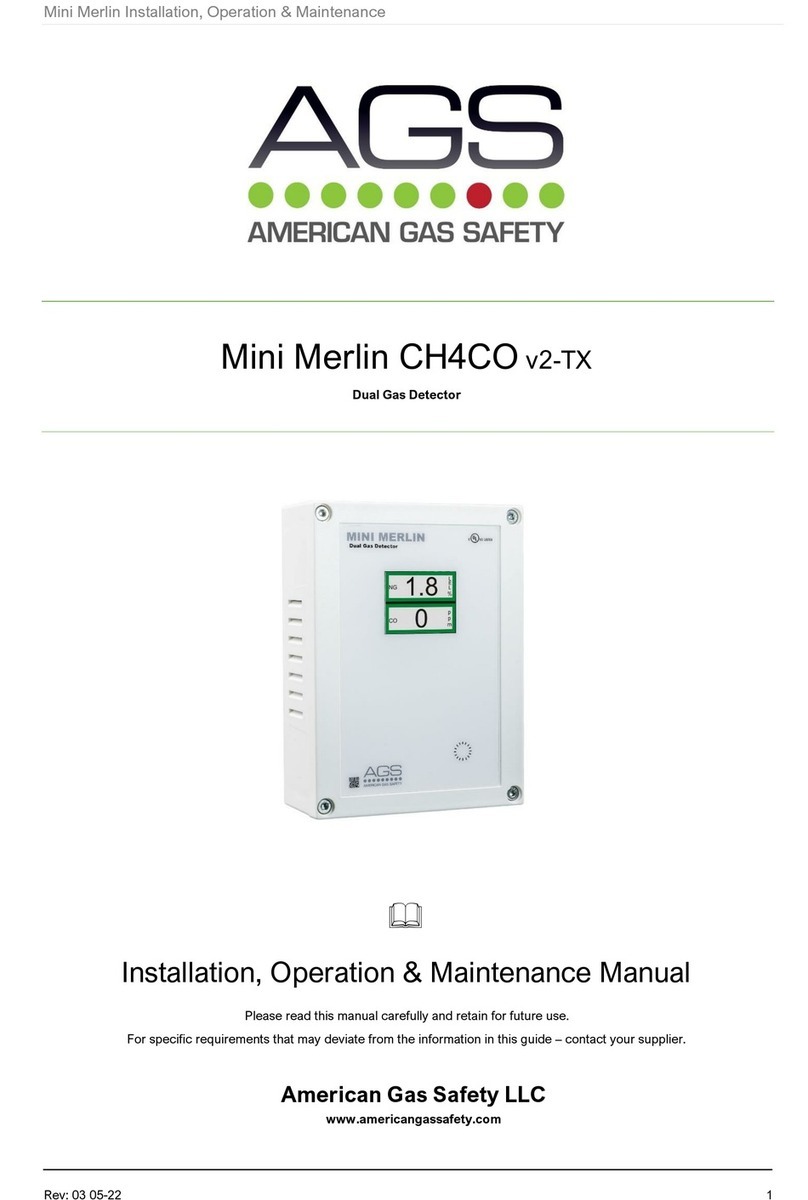
AGS
AGS Mini Merlin CH4CO v2-TX Installation, operation & maintenance manual