DTM System EASY B232 User manual

AUTOMATIC SYSTEMS
GATE CONTROL UNIT
installation and manual
version 2.7 EASY B232
DTM System spółka z ograniczoną odpowiedzialnością spółka komandytowa
ul. Brzeska 7, 85-145 Bydgoszcz
tel./fax. (52) 340-15-83, 340-15-84
www.dtm.pl, [email protected]


1. Introduction
EASY B232 gate control unit is used to control drives of double leaf gates powered by alternating
voltage 230V, 50 Hz, max power 350W. With the cooperation of the Easy RX radio card of the capacity of
35 remote controls DTM433MHz series (secured transmission based on the Keeloq system), the driver
gains the radio control function.
The drive has a function of slowing down the move during the start and/or stopping and adjustment of
servomotor power. By adjusting the right mode of the driver we can complete automation system with
function of the automatic gate closure after time (time of auto closure is regulated from 1 up to 120
seconds), function of photo closure (automatic closure of the gate with time 5 seconds, started after the
infringement and repeated dismissal of photocells) EASY 232 has output of gate bolt control and
additional output with manual and radio steering, which can work under the bistable procedure
(connect/disconnect) or monostable (connect for 4 sec.), intended for connecting outside device.
Signal lamp power output 230 VAC / 50 Hz, enables connecting both lamp with the contact breaker built in,
as well as without (recommended). Additionally the driver is equipped with the signal lamp output LED 24
VDC/ 6W.
The operation of control unit depends on chosen work mode, see p. 5.4.
2. . Technical data
Basic parameters
- Power supply 230 AC V, 50 Hz
- Power consumption in non-active status 8VA
- Operational temperature (min./max.) -20°C /+55°C
- External dimensions (width. x depth x height) 180 x 95 x 241 mm or 120 x 80 x 166 mm
- Installation surface mounted
- Weight 1,1 kg
- IP 55
Outputs/Inputs
- Servomotor output (voltage / maximum power/in built condenser/quantity) 230VAC / 2 x 350W / none/ 2
- Signal lamp output transmitted max. 230VAC/6A and OC max. 24VDC/6W
- Periphery power output (photocells, bolt, etc.) 24V DC, 0,5A
- Photocells transmitter power supply output OC type (see function PHOTO-TEST)
- Gate bolt output 12V DC, engaged for 8 sec. on the start of opening
- Additional output relay (potential free) max. 1A/30V AC/DC operating in bistable
or monostable mode engaging time 4 sec (programmable
with DIP-SWITCH, p.5.2.1)
- Photocell inputs/ number NC type / 3
- Manual steering input OPEN A NO type
- Manual steering input OPEN B NO type
- Additional channel manual steering input OPEN C NO type
- Manual steering input STOP NC type
Steering part
- Regulation of opening and closing time and soft start/stop phases 1 sec. to 255 sec. (exact to 1 sec.) – learning function
- Power of servomotors regulation yes, separately for servomotor 1 and 2
- Regulation of second leaf delay with the help of potentiometers from 1 to 15 seconds
- 8 modes of servomotor work programmable with DIP-SWITCH, p.5.4
- Start with maximum strength programmable with DIP-SWITCH, p.5.2.1
- Auto-closing gate function yes, regulation with the help of potentiometer from 1 to 120s
- Photo-closing function yes, constant time after which the gate is closed 5 sec
- Pushing with increased power after closing, start with increased power programmable with DIP-SWITCH, p.5.2.1
- Initial work of signal lamp programmable with DIP-SWITCH, p.5.2.1
- Photo test (testing of photocells before the gate move) yes, p. 5.2.1
- Equipment user interface DIP-SWITCH to set control unit operation mode and switching
additional functions, LEARN button to conduct learning of
opening and closing time (slowdown), signal LED diodes
- Device configuration memory non-transistory
- Radio steering in option through connection for radio receiver available on
the board
1

Radio part – receiver EasyRX
- Radio module superheterodyne, ensuring high reliability, repeatability and
resistance to radio noise
-Transmission protection 64-bit dynamically changing Keeloq®
- Modulation type/ frequency ASK / 433,92 MHz
- Input aerial impedance 50 W
- Aerial internal, terminals for external aerial connection
- Outputs digital steering output
- Memory capacity 35 remote controls, every with individual number in memory
- Remote control configuration possibility to subscribe any of three functions (OPEN A, OPEN B, OPEN
C) to any remote control button
- Possibility to delete all memory yes
- Possibility to delete single remote control yes
- Possibility to subjoin remote control without the necessity
to access control unit button yes ( remote subjoin function of remote control)
- Remote subjoin function block yes
2

7
13
10
9
8
12
5
6
11
20
21
22
19
16
17
18
15
14
4
3
1
2
3
3. Installation
3.1. Important notice
Electrical and automation installations of the drive must be made by experienced and qualified
personnel according to all regulations in force. Device is designed to operate with dangerous 230V/50Hz
voltage, turn all power off while installing. EASY B232 control unit is classified as „ Gate and automatic
doors” category which indicates special safety measures. The installers task is safe installation of the
device which enables maximum reduction of risks connected with its operation. The person performing
the installation without compliance with all regulations is responsible for any presumptive damages
caused by the device.
3.2. Device description and installation method
EASY B232 control unit is main board and casing. Main board (Fig. 1) has built-in power supply
adaptor and execution circuit made on special relays and couplings to connect power of servomotor and
protecting, steering and signalling elements. Moreover, it is equipped with the microprocessor control unit
with the interface on LED diodes, DIP-SWITCHes, MICROSWITCH button and rotational
potentiometers. The casing of the control unit has IP 55 level of tightness. Impairments placed in the
lower part of the casing are for placing fixing bolts which mount the control unit to the surface. Impairments
in the side parts of the casing are to lead installation wires of the control unit. After making the hole it is
necessary to apply attached rubber gland of the diameter 25mm. The wires should be led to the device
through lower part of the casing. While making holes in the casing it is necessary to guarantee required
“IP” tightness. The presence of the supply voltage is being signalled with LED POWER diode lighting.
Fig. 1. Main board
1. fuse (4A/250V, T)
2. power supply connector 230V AC
3. connector for engine 1
4. connector for engine 2
5. signal lamp connector, 230V AC, max. 6A

4
6. additional relay output (NO)
7. gate bolt output 12VDC
8. LEARN button used while programming
9. DIP-SWITCH which is to set the operations mode and to control additional functions
10. LED diode signalling presence of power on the control unit board
11. first servomotor power regulation
12. second servomotor power regulation
13. radio receiver connector EasyRX
14. delay of the leaf regulation
15. closing time regulation
16. STOP button connector (NC)
17. manual steering buttons OPEN A, B and C connector
18. photocells outputs connector OP, CL and OP/CL
19. photocell transmitters power connector (necessary with photo test usage) – mass potential "-"
20. common accessories connector (mass potential)
21. accessories Power connector (+24V)
22. LED lamp connector (mass potential max. 6W)
3.3. Description of electric connections of EASY B232 control unit
Only qualified specialist, having suitable qualifications, can perform connecting to electrical grid 230
VAC. The delivered control unit is at once ready for the work, all required terminals are connected with
themselves, and every installed safety devices is stuck instead of the small wire bridge (jumper).
3.3.1. Network power terminals 230VAC, 50Hz (L, N, PE)
This connector is envisaged for connecting control unit power from electric grid 230VAC, 50 Hz. The
powering circuit to which the control unit will be connected, should be equipped with the switch cutting the inflow
of the electricity to the steering board. We add the phase cable to the L terminal, to the N terminal neutral cable,
and to the PE terminal protective cable (yellow-green).
3.3.2. Terminals for connecting the servomotors MOTOR1, MOTOR2 (PE, OPEN, COM, CLOSE)
Servomotor which opens as first (important when the leaves open “lap”) should be connected to
MOTOR 1 terminals. Second servomotor should be connected to MOTOR 2 terminals. Engine condensers, proper
for this type of servomotor, should be connected between OPEN and CLOSE terminals of the servomotors. The
servomotor opening wire should be connected to OPEN terminal, closing wire to CLOSE terminal, common wire
to COM terminal and servomotor protection wire to PE terminal.
3.3.3. Terminals for 230V (LAMP) signal lamp connection
Terminals are used to connect the lightning or the visual signalling of the current state of servomotor
work. We connect lamp leads 230 V, max. 6A directly to LAMP terminals in the control unit (fig. 2.). In case of the
lamp with the contact breaker built in, Blinking Lamp function should be turned off (see p. 5.2.1).
3.3.4. Terminals for 24V/6W signal lamp connection
Terminals are to connect LED lamp to 24V, maximum power 6W. We connect it to 24V/6W and +24V
terminals (fig. 2). In case of the lamp with the contact breaker built in, Blinking Lamp function should be turned off
(see p. 5.2.1).
3.3.5. Gate bolt connection terminals ( )
Control unit is equipped with output which can steer 12 VDC gate bolt. It is necessary to remember about
maximum load of accessories power supply output, all together 0,5A.
3.3.6. Additional output terminals (OUT C)
Control unit is equipped with the relay with NO type contacts led out with maximum load capacity of 30
VAC/DC 1A, enabling the steering with additional device, such as electric strike, additional control unit, lighting
(with applying additional relay of the appropriate load capacity) etc. The output is engaged with manual steering
OPEN C button or with the button of the remote control. Depending on the settings of the OUTC-BIST
microswitch (the channel works in bistable or monostable mode engaging time 4 s).

external
output
(NO)
max. 1A,
30V AC/DC
EASY B232
button
OPEN C (NO)
button
OPEN B (NO)
button
OPEN A (NO)
230V AC
50 Hz
M1
M2
230V AC
max. 6A
L
N
PE
button
STOP (NC)
POWER
24V DC
max. 6W
-
+
RX-OP TX-OP
12
24V
AC/DC
1 2 3 4 5
RX-CL TX-CL
12
24V
AC/DC
1 2 3 4 5
RX-
OP/CL
TX-
OP/CL
12
24V
AC/DC
NC NC NC
1 2 3 4 5
CCC
NO NO NO
24V
AC/DC
24V
AC/DC
24V
AC/DC
mass
+24V
TX -24V
relay
12VDC
Fig. 2. Elektric diagram.
5
CAUTION!
Switchboard settings unsuited to installation conditions can soon lead to its damage and loss of
warranty! After the completion of installation making stage and connecting the devices, the
switchboard should absolutely be programmed in order to adapt its operating parameters to the
current installation, in particular it is necessary:
- always to set the power of the servomotor
- always to programme opening and closing times
All the envisaged connections should scrupulously followed. In the uncertain situation it is
forbidden to try out, only to read relevant detailed technical cards of installed devices. Incorrect
making of connections can cause serious damage in the control unit and remaining devices.
D O N O T C O N N E C T A D D I T I O N A L P A R R A L E L E N G I N E S .
- unused photocells inputs should be connected to TX terminal
- unused STOP input should be bridged by wire (jumper)
- unused NO terminals should be left unconnected
motor left
230VAC
max. 350W
motor
right
230VAC
max. 350W
6W
24V
6W/24V

6
3.3.7. Accessories power supply terminals (+24VDC)
Control unit is equipped with accessories power supply outputs 24VDC max. load 0,5A. The outputs have
three equal screw terminals with mass potential (0V) and two equal terminals with the +24V potential.
3.3.8 Terminals for TX, PHOTO OP, PHOTO CL and PHOTO OP/CL photocells connection
If applied photocells are powered by 24V, with separate receiver and transmitter supply, then the
following connections are applicable: "+" of transmitter and receiver power supply to the output of accessories
supply +24 VDC, "- " transmitter power supply to the TX terminal (output OC type), and "-" of receiver power
supply to mass as standard. If photocells have a shared power supply for the transmitter and the receiver, then
their "- " of power supply to the TX output. Such a way of connecting, allows to use PHOTO-TEST function which
checks photocells operation before every move of the gate and blocks the move in case of detecting the
breakdown. PHOTO-TEST function improves the security level significantly. In order to engage PHOTO-TEST
function, see p. 5.2.1. PHOTO OP input is dedicated to the photocell installed parallel to the line of the gate
movement, it secures the zone of the stroke of the gate. PHOTO CL input is dedicated to the outside photocell
(outside premises) installed parallel to the edge of entrance, PHOTO OP/CL input is dedicated to the inside
photocell (on the area of premises), installed parallel to the edge of entrance. Unused sockets of photocells
should be connected with TX terminal (all sockets of photocells are connected with wire factory-made (bridged).
3.3.9. Manual steering INPUT STOP and OPEN (A, B, C) terminals
Momentary button (monostable) of NC type should be connected to INPUT STOP terminals. If the
button is not used, the terminals should be clenched with a wire. Momentary buttons of NO type can be
connected to OPEN A and OPEN B terminals. These momentary buttons will control the work of the control unit
according to the adjusted mode (see table of modes of the control unit). It is possible to connect the momentary
button of NO type to the OPEN C terminal. This button will activate additional channel output OUTC. All unused
inputs of NO type should be left not connected. Activating the button of the manual steering consists in its
momentary pressing. OPEN A, B and C inputs are functional equivalent of radio receiver channels (channel A, B
and C).
3.3.10. EasyRX radio receiver connector
This connector enables the control of servomotor with the help of DTM433MHz series remote controls
by the additional board of the radio receiver. The receiver communicates with the control unit through the local
data bus which makes it impossible to connect other radio receivers to the connector. The installation and the
programming are described in p. 6 of this manual.
4. Description of control unit operations
Control unit is immediately ready to work after switching on the power supply. After pressing any button
of the programmed remote control or releasing the controlling input, appropriate function of the control unit is
performed. In the operation mode, the current state is signalled with the help of the signal output and LED
diodes. In sleeping mode all red diodes should shine, and green ones remain turned off. Immediately after
switching on the power supply the first move is opening.
4.1 . Gate leaves synchronization
When one servomotor encounters an obstacle, which prevents its further movement it does not cause
the stop of the second one. In such case there is a possibility of gate leaves desynchronizing which can be
important when the closing order of the leaves is relevant. It is necessary to synchronize such gate again. It should
be performed as follows:
engage OPENING movement
wait for full opening of both gate leaves ( it May be necessary to engage CLOSING Direction and then OPENING).
5. Programming of EASY B232 control unit
EASY B232 control unit is programmed to needs of the given installation using the LEARN button with
the LEARN diode, DIP-SWITCH microswitches with the division into two sections FUNCTION and MODE and
three rotational potentiometers.
In order to conduct the process of the programming efficiently it is necessary to keep the following order :
- analyse tables with individual operational modes and choose appropriate with the help of DIP-SWITCH MODE
part
- turn on or turn off chosen functions off in FUNCTION section

7
- set the leaf delay time and/or auto closing time
- make adjustment of the strength of the towing power of
servomotors with potentiometers FORCE 1 i 2
- conduct the learning (in the simplified mode, p. 5.5 or in
extended mode p. 5.6)
- check the correctness of operation and if necessary repeat
the programming
5.1. LEARN button
LEARN button is used in learning procedure (p. 5.5
and 5.6) and to confirm changes in the settings of the
potentiometers (p. 5.3).
5.2. DIP-SWICH
DIP-SWICH (fig.3) allows turn on or turn off individual
functions easily and make changes in the operational mode of the control unit. The changes of settings are
immediate after switching and do not require additional confirmation
5.2.1 DIP-SWITCH FUNCTION section
We can perform the following settings in this group:
PHOTO-TEST turned on (ON) or turned off (OFF). Turning on causes photocells barrier testing right before the
beginning of the servomotor movement. This function protects against engaging the servomotor when the
photocell underwent the breakdown what could lead to dangerous situation. Testing the crash barrier is
conducted only right before initiating the move of the servomotor, never in sleeping mode. Turning on the
function of the phototest causes no disorders in the work of the control unit when the photocell is repeatedly
disturbed in sleeping mode (e.g. by animals or playing
children). Phototest won't be conducted in the event when
the move of the servomotor is a result of switching the
direction as a result of disturbing the photocell.
OVER-PUSHING start of the servomotor with the maximum
power turned on (ON) or turned off (OFF).
PRE-FLASHING preliminary, five-second signalling of the
lamp before the move of the gate turned on (ON) or turned off
(OFF).
BLINKING LAMP controlling with lamp without the contact
breaker built in (ON) or with lamp with its own contact breaker
(OFF). The lamp without the contact breaker allows to use the
additional signalling of the state of the gate by lamp flickering
with different time intervals.
OUTC-BIST allows for the work of the additional channel in
bistable mode (ON) or monostable 4 seconds (OFF).
5.2.2. DIP-SWITCH MODE section
It is used to set one of eight modes of the control unit
operation. Depending on the needs the most suitable mode
should be chosen after prior analysis of the settings MODE table (p. 5.4 ). In order to avoid possible irregularities in
action of controlling equipment adjust the mode when the state of control unit is “closed". After the change of
operational mode of the control unit it is good to turn off the power supply for few seconds which results in control
unit restart.
5.3. FORCE 1, FORCE 2, MOTOR DELAY and AUTO CLOSE control potentiometers
CAUTION!
After the change of the any set parameter with the help of the potentiometer LED LEARN diode will start
flickering announcing the need to approve changes with short pressing the LEARN button. Only after such
confirmation control unit changes the settings. During the change of the given parameter, a speed of
pulsing of LED LEARN diode changes what gives some idea of the value of the adjusted parameter.
Rysunek 3. DIP-SWITCH.
Fig. 4. Potencjometers.
OUTC

8
Control unit enables to regulate the power of servomotors. Regulation takes place separately for every
servomotor with the help of potentiometers ( respectively FORCE 1 fot the first servomotor and FORCE 2 for the
second servomotor)
If it is necessary to delay the movement of one of the leaves, MOTOR DELAY time is set
(0...15sek.).While OPENING the move of servomotor 2 is delayed and while CLOSING the move of servomotor 1 is
delayed. The delay of the movement is only when the leaf is in the final closing or opening position. The delay
while OPENING is max. 3 sec. even when higher parameter value is set with the help of MOTOR DELAY
potentiometer.
AUTO CLOSE potentiometer allows non-linear regulation of the automatic time of gate closing in the scope from
1 up to 120 seconds. The non-linearity of the regulation is the fact that initial changes of the potentiometer axis
angle give small increase in the autoclosing time, however after exceeding the half of the accessible angle of the
values rotation the delays increase much more quickly, all the way to the maximum value. The scale was drawn for
better understanding.
CAUTION!
Decreasing the operational power of the servomotor has positive influence on safety conditions, as well as
to the vitality of mechanical fittings.
5.4. Przełącznik DIP-SWITCH sekcja MODE - tryb (logika) pracy sterownika EASY B232
DIP-SWITCH MODE section - EASY B232 control unit operation mode (logic)
Below there are operation modes of EASY control unit. It is necessary to analyse the user needs and next
choose appropriate among available.
5.4.1. 1/A mode
Automatic mode, it has function of auto closing the gate after the set time -
maximum 120 seconds. Function of the wicket active, function of photo closing
disabled.
* If after removing an obstacle there are fewer than 5 seconds left to automatic closing then the time of automatic
closing is increased up to 5 seconds.
** When the last move was opening the wicket, it opens the gate.
OUTC
1/A mode
opens closing stopped open
OPEN_A rewers
OPEN_B rewers
INPUT STOP blocks OPEN A/B stop stop
PHOTO OP blocks OPEN A/B rewers blocks OPEN A/B blocks opening
PHOTO CL rewers
PHOTO OP/CL blocks OPEN A/B blocks OPEN A/B
closed
opens the gate
opens partially
and close after
and close after
auto-closing time
auto-closing time
closes the gate
Tab. 1. 1/A mode
closes the
gate/partially
(countdown autoc-
losing time)
closes the
gate/partially
(countdown autoc-
losing time)
auto shutdown
counting time
stopped until the
obstacle removed
auto shutdown
counting time
stopped until the
obstacle removed
closes the
gate/partially
blocks OPEN A/B
stop until unlock,
opens
stop until unlock,
opens
blocks closings
stop

9
5.4.2. 2/S mode
This mode, similarly to 1/A, is automatic mode, it has function of auto closing the
gate after max. 120 seconds. Function of the wicket and photo closing active
* If after removing an obstacle there are fewer than 5 seconds left to automatic closing then the time of
automatic closing is increased up to 5 seconds.
** When the last move was opening the wicket, it opens the gate.
5.4.3. 3/E mode
Semi automatic mode with wicket function, without auto and photo closing.
.* When the last move was opening the wicket, it opens the gate.
OUTC
OUTC
stop until unlock,
opens
stop until unlock,
opens
Tab. 2. 2/S mode
2/S mode
OPEN_A rewers ** rewers
OPEN_B rewers rewers
INPUT STOP blocks OPEN A/B stop stop blocks OPEN A/B stop
PHOTO OP blocks OPEN A/B rewers blocks OPEN A/B
PHOTO CL rewers
PHOTO OP/CL blocks OPEN A/B blocks OPEN A/B
otwiera bramę i
zamyka po czasie
autozamykania***
otwiera furtkę i
zamyka po czasie
autozamykania
closes the gate countdown autoc-
losing time
countdown autoc-
losing time
closes the
gate/partially
blocks closings
blocks opening
blocks closings
opens closing stopped open
closed
5s after
unlock, closes*
5s after
unlock, closes*
blocks opening
opens closing stopped open
closed
Tab. 3. 3/E mode
3/E mode
OPEN_A stop * rewers
OPEN_B stop rewers
INPUT STOP blocks OPEN A/B stop stop blocks OPEN A/B blocks OPEN A/B
PHOTO OP blocks OPEN A/B rewers blocks OPEN A/B
PHOTO CL rewers blocks OPEN A/B
blocks OPEN A/Bblocks OPEN A/B
PHOTO OP/CL blocks OPEN A/B
closes the gate *
opens the gate
opens partially
closes
closes
closes the
gate/partially
blocks closings blocks closings
stop until unlock,
opens
stop until unlock,
opens

10
5.4.4. 4/EP mode
Semi automatic mode – step by step. OPEN A and OPEN B control respectively:
open-stop-close, in the event when the gate is opened: close-stop-open. Function of the
wicket active, function of auto and photo closing disabled.
* When the last move was opening the wicket, it opens the gate.
5.4.5. 5/B mode
Semi automatic mode. The easiest in operation, without wicket, auto and
photo closing functions.
OUTC
OUTC
blocks opening
Tab. 4. 4/EP mode
4/EP mode
OPEN_A stop * stop rewers *
OPEN_B stop stop rewers
opens closing stopped open
closed
INPUT STOP blocks OPEN A/B stop stop blocks OPEN A/B
PHOTO OP blocks OPEN A/B rewers blocks OPEN A/B
PHOTO CL rewers blocks OPEN A/B
blocks OPEN A/B
blocks OPEN A/B
blocks OPEN A/Bblocks OPEN A/B
PHOTO OP/CL blocks OPEN A/B
opens the gate
opens partially
closes
closes
blocks closings blocks closings
stop until unlock,
opens
stop until unlock,
opens
opens closing stopped open
closed
Tab. 5. 5/B mode
5/B mode
OPEN_A opens rewers opens
OPEN_B closes closes
INPUT STOP blocks OPEN A/B stop stop blocks OPEN A/B
blocks OPEN A/B
blocks OPEN A/B
blocks OPEN A/B
blocks OPEN A/B
PHOTO OP blocks OPEN A stop blocks OPEN A blocks OPEN A/B
PHOTO CL stop
PHOTO OP/CL blocks OPEN A stop stop
opens closing stopped open
closed

11
5.4.6. 6/C mode
Mode which requires the constant presence of the operator. The gate
movement lass as long as the button is pressed. Radio frequency disabled in this
mode.
5.4.7. 7/PA mode
Mode, in which the special stress is put for the better verification of the move
that undergoes through the gate. The resignation from reversing direction of the
servomotors operation and continuing the move after removing an obstacle shorten
the time when the gate is open. It reduces the chance of rushing (driving) to the area of
unauthorized people. Functions of auto closing, wicket and photo closing
active.
* If after removing an obstacle there are fewer than 5 seconds left to automatic closing then the time of
automatic closing is increased up to 5 seconds.
** When the last move was opening the wicket, it opens the gate.
OUTC
OUTC
opens closing stopped open
closed
Tab. 6. 6/C mode
6/C mode
OPEN_A opens stop opens
OPEN_B stop closes closes
INPUT STOP blocks OPEN A stop stop blocks OPEN A/B blocks OPEN B
PHOTO OP blocks OPEN A stop blocks OPEN A
PHOTO CL stop blocks OPEN A/B blocks OPEN A/B
PHOTO OP/CL blocks OPEN A stop stop blocks OPEN A/B blocks OPEN A/B
opens closing stopped open
closed
Tab. 7. 7/P mode
7/PA mode
OPEN_A stop ** rewers
OPEN_B stop rewers
INPUT STOP blocks OPEN A/B stop stop blocks OPEN A/B stop
PHOTO OP blocks OPEN A/B rewers blocks OPEN A/B
PHOTO CL blocks OPEN A/B
PHOTO OP/CL blocks OPEN A/B blocks OPEN A/B
opens the gate
and close after
auto-closing time
opens partially
and close after
auto-closing time
opens closing stopped open
closed
closes the gate
closes the gate/
partially(countdown
autoclosing time)
closes the gate/
partially (countdown
autoclosing time)
closes the
gate/partially
blocks closings
blocks openings
stop until unlock,
opens
stop until unlock,
opens
stop closings
until unlock
5s after
unlock, closes*
5s after
unlock, closes*

12
5.4.8. 8/P mode
Semi automatic mode – step by step. OPEN A and OPEN B control respectively:
open-stop-close, when the gate is open: close-stop-open. Wicket and autoclosing
functions active, photo closing disabled.
* When the last move was opening the wicket, it opens the gate.
5.5. Learning in SIMPLIFIED mode
It is simple and fast form of setting the times of closing and opening in the control unit. The procedure
does not allow to set slowdown Turing start and stop.
In order to execute learning procedure correctly it is necessary to:
- make sure that connected photocells work correctly and peripheral switches of the servomotor are placed
correctly
- set the gate in the position of full closure (with the help of manual steering buttons or buttons of the
programmed remote control), if necessary disarrange servomotor and close the gate manually, next arrange
again.
- make sure that there is no obstacle in the way of photocells barriers, and on the way of the move of the gate,
- press and hold LEARN button up to the moment when LEARN diode goes on (we dismiss it within 2 seconds, if
we don't do it the control unit proceeds to the extended mode oflearning)
- press LEARN button again for a short time ( for conducting auto learning any OPEN A, OPEN B, OPEN C button
or button programmed on the remote control can be used instead of LEARN button
- leaves start the movement towards opening
- second pressing (of the earlier chosen button) – the leaves stop, LED LEARN diode goes off
5.6. Learning in EXTENDED mode
This procedure requires more involvement in the process the learning from the fitter, than in case of the
simplified mode. The fitter is able to set slowdown times at opening, slowdowns at closing, opening and closing
according to personal needs for every leaf separately.
In order to execute learning procedure correctly it is necessary to:
- make sure that connected photocells work correctly and internal peripheral switches of the servomotors (if
present) are set correctly
- set the gate in the position of full closure (with the help of manual steering buttons or buttons of the
OUTC
Tab. 8. 8/P mode
OPEN_A stop * stop
OPEN_B stop stop
INPUT STOP blocks OPEN A/B stop stop blocks OPEN A/B
PHOTO OP blocks OPEN A/B rewers blocks OPEN A/B
PHOTO CL
PHOTO OP/CL blocks OPEN A/B blocks OPEN A/B blocks OPEN A/B
blocks OPEN A/B blocks OPEN A/B
8/P mode
blocking OPEN A/B
opens the gate
and close after
auto-closing time
opens partially
and close after
auto-closing time
opens closing stopped open
closed
rewers *
closes the gate/
partially(countdown
autoclosing time)
closes the gate/
partially (countdown
autoclosing time)
rewers
blocks closings
blocks openings
stop until unlock,
opens
stop until unlock,
opens
rewers

13
programmed remote control), if necessary disarrange servomotor and close the gate manually, next arrange
again.
- make sure that there is no obstacle in the way of photocells barriers, and on the way of the move of the gate,
- press and hold LEARN button up to the moment when LEARN diode goes on (after about 3 seconds)
- press LEARN button shortly again (for learning you can use instead of LEARN button any OPEN A, OPEN B,
OPEN C button or remote control button programmed on the radio card) begins slowed movement of the first
leaf towards opening. From this moment only this chosen button will be used in the learning procedure.
- second pressing – leaf 1 increases speed to standard opening speed
- third pressing – leaf 1 is slowed down
- fourth pressing – leaf 1 stops
- fifth pressing – leaf 2 starts slowed move towards opening
- sixth pressing – leaf 2 increases speed to standard opening speed
- seventh pressing – leaf 2 is slowed down
- eighth pressing – leaf 2 stops
- ninth pressing – leaf 2 starts slowed move towards closing
- tenth pressing – leaf 2 increases speed to standard closing speed
- eleventh pressing – leaf 2 is slowed down
- twelfth pressing – leaf 2 stops
- thirteenth pressing – leaf 1 starts slowed move towards closing
- fourteenth pressing – leaf 1 increases speed to standard closing speed
- fifteenth pressing – leaf 1 is slowed down
- sixteenth pressing – leaf 1 stops and the procedure is finished, LEARN LED diode goes off.
In order to set the zero time of slowing down, it is necessary to press learning button again for less than 1
sec during slowed movement of control unit. Respectively to programme the delay phase it must last at least 1
sec.
CAUTION!
Disturbing photocells while learning, won't cause stopping of the servomotor! If needed, it is possible to
stop the move of the gate with manual steering STOP button. It will also interrupt learning operation and
restore all parameters the work of the control unit to the values as before initiating the learning function.
During the procedure photocells barriers should not be disturbed and it is necessary to provide free move of
the gate, without any obstacles on its way.

14
6. EasyRX dedicated radio receiver
CAUTION!
EasyRX radio card is intended exclusively for the cooperation with EASY B231- DTM6 control unit produced
by DTM System. It should not be used autonomously.
6.1. General information
This receiver expands functional possibilities of EASY control unit to remote steering with DTM 433MHz
series remote controls.
6.2. Receiver card installation
It is the best to start the installation of the receiver from connecting the aerial to it. Next, receiver in the
form of the card - board with the edge connector should be pressed into the socket with the RADIO description on
a control unit board on the right-hand side (4 pins), side where buttons are placed towards the connector.
6.3. Subscribing remote controls to the receiver
The receiver has three identically programmed channels A, B and C. They are functional equivalents of
OPEN A, OPEN B and OPEN C inputs in the control unit). In case of the second and third channel we act the same
as during the programming of the remote control in the first channel (using the button of the second and third
channel respectively). In order to programme any button of the remote control in the first channel it is necessary
to:
- press and hold first channel A button
- when first channel A button is pressed, press
chosen button of the remote control
- first channel A diode flickers which indicates
success of the operation
- release the button
6.4. Terminals for aerial connection
In the brand new receiver an inside
aerial 170 mm long is connected to the
terminal. To increase the range of the radio
remote control, it is necessary to connect
outside stubby aerial. To connect the coaxial
cable of the outside aerial to the terminal (centre vein of the cable) and to the terminal (cable screen). In order to
achieve the optimum radio reach it is important to remember about:
- negative influence of the receiver with energetic devices and metal objects in the aerial neighbourhood,
- negative influence of radio interference from other sources,
- negative influence of high-density housing, wet or reinforced concrete walls.
- shorten range with used remote control battery
- increasing range with increasing height of receiver aerial location
6.5. Remote subscribing of new remote control
The radio EasyRX card has a program enabling simple subscribing of the new remote control for the user
without the need for the access to buttons.
This function is only useful when you have a
remote control already subscribed in the
memory. To subscribe new remote control in
this way it is necessary to proceed according
to fig. 6.
CAUTION!
Possibility of adding remote control
without the access to the control unit
dramatically decreases the level of
security against third parties. Fig. 6. Remote subscribing of new remote control.
HOLD ANY OF „NEW”
REMOTE BUTTON
FOR 15s
HOLD ANY OF
ALREADY ASSIGNED
REMOTE BUTTON FOR
15s
MAX BREAK
PERIOD 3s
11 2
TIME
Fig. 5. Subscribing remote control OPEN A to the receiver.
11
2
CZAS
2
PUSH NEW
REMOTE
BUTTON
PRESS AND
HOLD
A BUTTON
+
TIME
REMOTES MUST BE IN RADIO RANGE

15
6.6. Blocking of remote subscribing of remote control
It is a function which prevents all remote controls, both already subscribed as well as the one subscribed
in the future, from participating in the process of remote subscribing of new remote control.
In order to protect the device against unauthorized attempts to subscribe additional remote control (particularly
essential in areas with protected access of users), it is recommended to block the function of remote subscribing
of remote controls. In order to block this function, we press A and B buttons of the radio receiver simultaneously
and next we release one of them (it does not matter which as long as the second remains pressed all the way to
the end of the procedure). After about 4 sec. A diode turns on (it means that currently the blocking of remote
subscription is turned off), we hold the button all the time. After 4 consecutive seconds B diode turns on (it means
that the function of remote subscription will be blocked). When we release the button kept, the card will
remember settings and remote subscribing of remote controls will be blocked. The procedure of unblocking is
the same, but we release the button when OPEN A diode turns on.
In the factory settings (after formatting), the blocking of remote subscribing of remote controls is turned off.
Fig. 7. Lock / unlock.
2
RELEASE
BUTTON
A OR B
PRESS AND
HOLD
A AND B
BUTTON
1
AFTER 4s
BLINKING
LED A AND B
13
BEZ
BLOKADY
BLOKADA
UNLOCKED
LOCKED
RELEASE
NEXT BUTTON,
A OR B
TURN
LED B
LOCKED
TURN
LED A
UN-
LOCKED
44a
4b
1
23
4
a)
b)
1
23
4
Fig. 8. Remote: a) NEO, b) VICTORY

16
6.7. Deleting of the remote control from memory
Deleting single remote control from the receiver memory is as follows:
- press and hold A and B buttons,
- press the button of remote control which is to be deleted.
CAUTION!
Holding the buttons on the card for too long (more than 10 seconds) may lead to format of the memory
and as a result to the removal of ALL remote controls.
6.8. Deleting of all remote controls from card memory
We delete all remote control from the receiver
memory when we press and hold for more that 15
seconds A and B buttons.
CAUTION!
Format process of the memory card causes irreversible removal of all remote controls and turning off the
block of remote subscribing of remote controls.
6.9. Board of radio receiver EasyRX
1. channel A signal diode
2. A channel button
3. channel B signal diode
4. B channel button
5. connector of the card
6. channel C signal diode
7. C channel button
8. aerial connector
7. Acceptance tests
8
2
1
4
3
7
6
5
Fig. 11. EasyRX board.
TIME
Fig. 10. Formatting card.
TIME
Rysunek 9. Deleting remote.
1
1
2
CZAS
+
PUSH DELETING
REMOTE
BUTTON
PRESS AND
HOLD
A BUTTON
PRESS AND
HOLD MIN 15s
A AND B BUTTONS

17
7.1. General remarks
After installing control unit and all cooperating devices, especially safety devices, final trials should be
performed to check the entire automation. These trials should be executed by the competent staff, being aware
of existing dangers! Final trials are the most important phase at the realization of automation. Individual
components, as the engine, photocells, and the like, can require the peculiar control and because of this,
executing checking procedures, included in the manual of given components are recommended.
- if the servomotor contains peripheral switches breaking the power-driven circuit, it is necessary to make sure
that at this stage they won't disconnect the servomotor in the unexpected moment.
- in case of the resignation from the installation of manual steering buttons, it is necessary to remember about
bridging the terminals. The lack of the bridge will make any move of the servomotor impossible.
- in case of the resignation from the photocell installation, the input (PHOTO OP, PHOTO CL or PHOTO OP/CL)
should be bridged with TX terminal.
- in case of the resignation from the protecting EDGE installation, it is necessary to connect input with the mass
terminal "-"
7.2. Final trials schedule the following stages
7.2.1. Movement direction control
Check whether at steering of OPENING function, automation physically moves towards opening. If the
movement is towards closing or any movement is missing it is necessary to disconnect control unit power supply
and exchange the connections of servomotor wires to OPEN and CLOSE terminals. Check again.
7.2.2. Control unit programming
It is necessary to set all required control unit operation parameters such as times of closing and opening
of the control unit, possible phases of slowing down and towing force of servomotor.
7.2.3. Security check
If photocells are installed, it is necessary to cause manual disturbance of the OP photocell, on the
controller board a PHOTO diode should go out 1. Act the same for the CL photocell and OP/CL if are installed. In
sleeping mode when optical crash barriers aren't disturbed, signalling PHOTO diodes 1, 2 and 3 should shine. If it
isn't so, it means error in photocells operation (incorrect connecting, not synchronizing the transmitter with the
receiver or the failure of the photocell).
7.2.4. Control of servomotor move steering functions
Check OPEN A, OPEN B and STOP functions using remote control button or manual button. After
consecutive impulses from the button the sequence of servomotors move should take place according to the
chosen operational mode.
7.2.5. Setting the power
The desirable strength of the towing power of the servomotor should be adjusted, with the help of the
potentiometer of the strength of servomotors adjustment. Proper setting of the power of the servomotors
operation, has a key importance for safety conditions, as well as the vitality of mechanical fittings. Usually
servomotors operation with power rating is not necessary, it should be adjusted individually to installation
conditions (taking into consideration the weight of gate leaves, tensions occurring after the closing or opening of
the gate leaves, existing resistance or exposing to strong wind, etc.) Special attention should be paid to stresses
arising after closing or opening the leaves, as well as predict consequences of the accidental lock of the obstacle
between the leaves of the gate. It should be remembered, that the less the value of the parameter, the less
powers will work on the possible obstacle appearing in the way of the gate. Adjusting the power of operational
servomotors, one must realize the resistance of the gate leaves, as well as their instability in time (influence of
weather conditions, wearing out etc. ) so the operational power cannot be too small, it must provide solid leaf
movement in the whole scope of the gate operation.

18
8. Warranty.
DTM System provides operational and ready to use devices. The producer gives 24 months warranty
from the selling date to the end customer. This time is counted according to the producer warranty labels or serial
numbers placed on every product. Producer obliges himself to repair the device for free if during the warranty
period there are problems which come because of his fault. Broken device should be supplied on customer's
expense to the place of purchase and enclose clear and brief description of the breakage. The cost of
mount/dismount is covered by the user. The warranty does not cover: batteries in the remote controls, faults
caused by improper usage, user self repairs and adaptations, lightning strikes, voltages or short circuits in the
electrical grid. Appropriate legal acts regulate details of the warranty.
Table of contents
Other DTM System Control Unit manuals
Popular Control Unit manuals by other brands
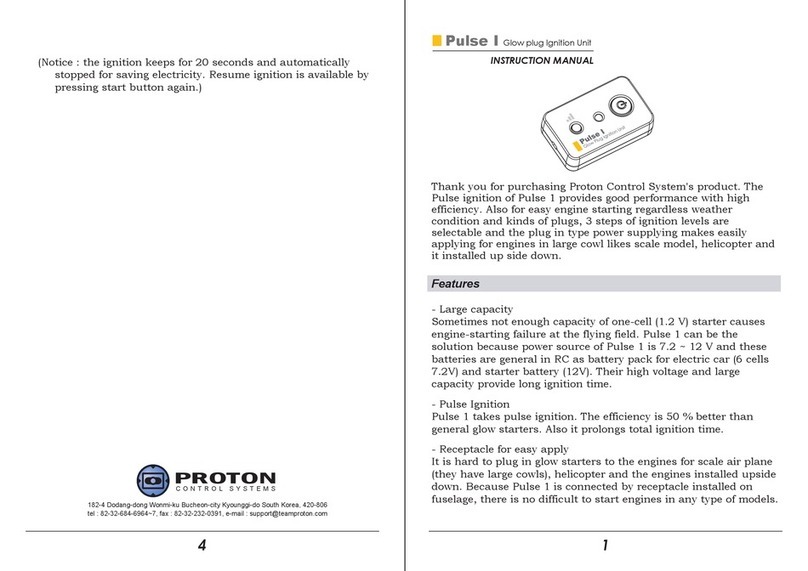
Proton
Proton Pulse I instruction manual
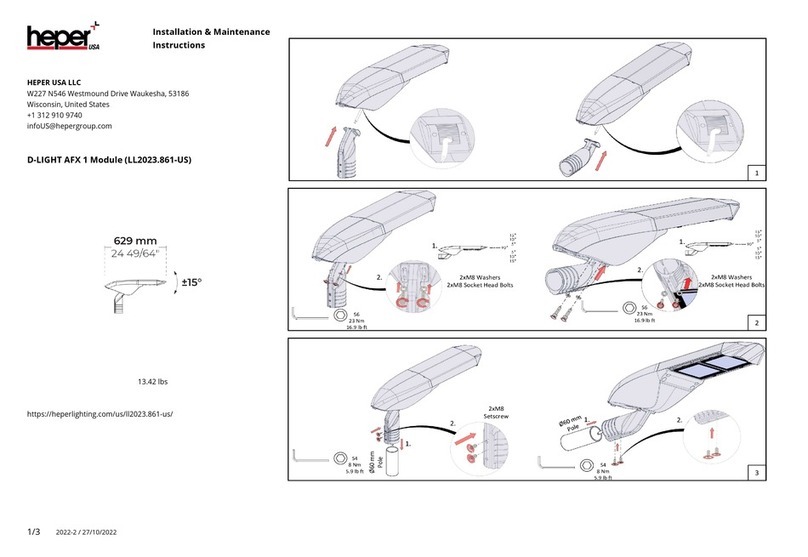
HEPER
HEPER D-LIGHT AFX 1 Installation & maintenance instructions
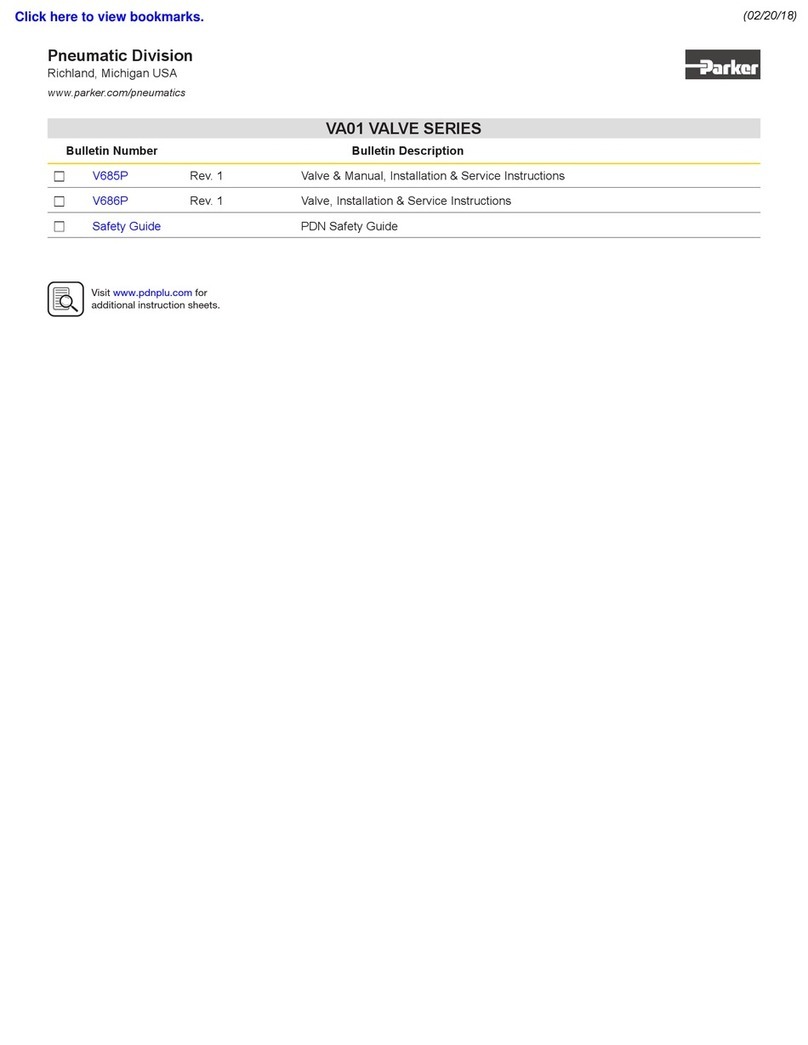
Parker
Parker VA01 Series manual
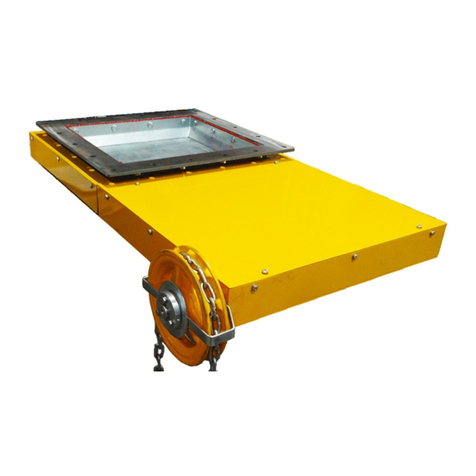
Anval
Anval SG Series Installation & maintenance manual
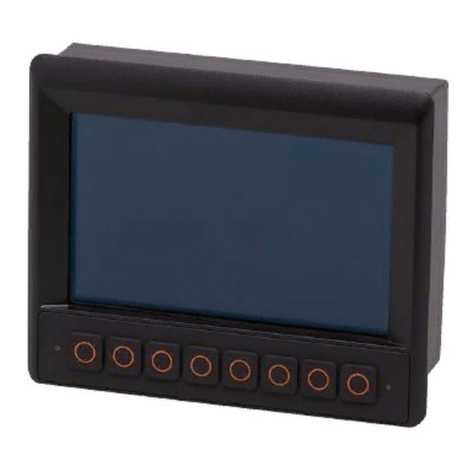
IFM Electronic
IFM Electronic Ecomat100 CR1083 PDM360 NG installation instructions
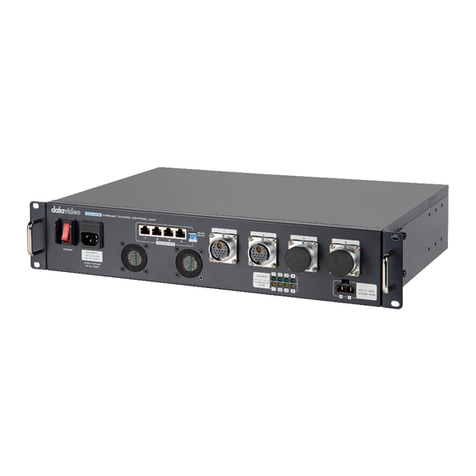
Data Video
Data Video CCU-200 instruction manual
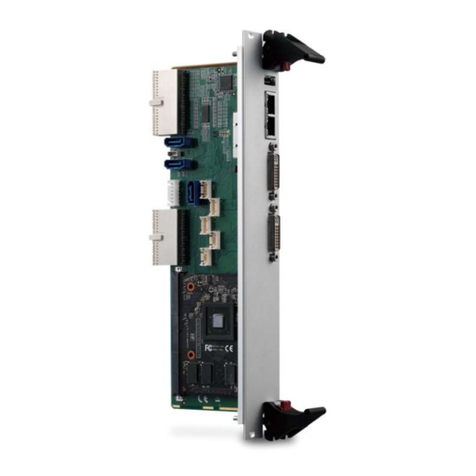
ADLINK Technology
ADLINK Technology cPCI-R6500 Series user manual
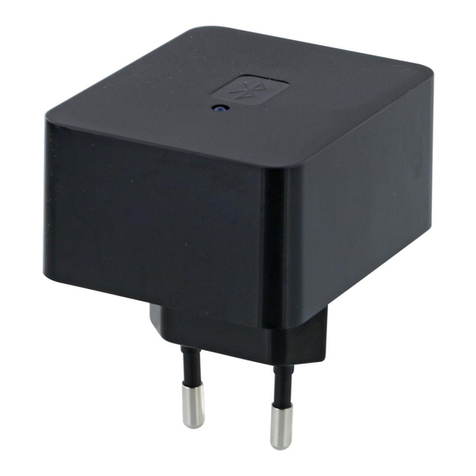
Halemeier
Halemeier AppMitter installation instructions
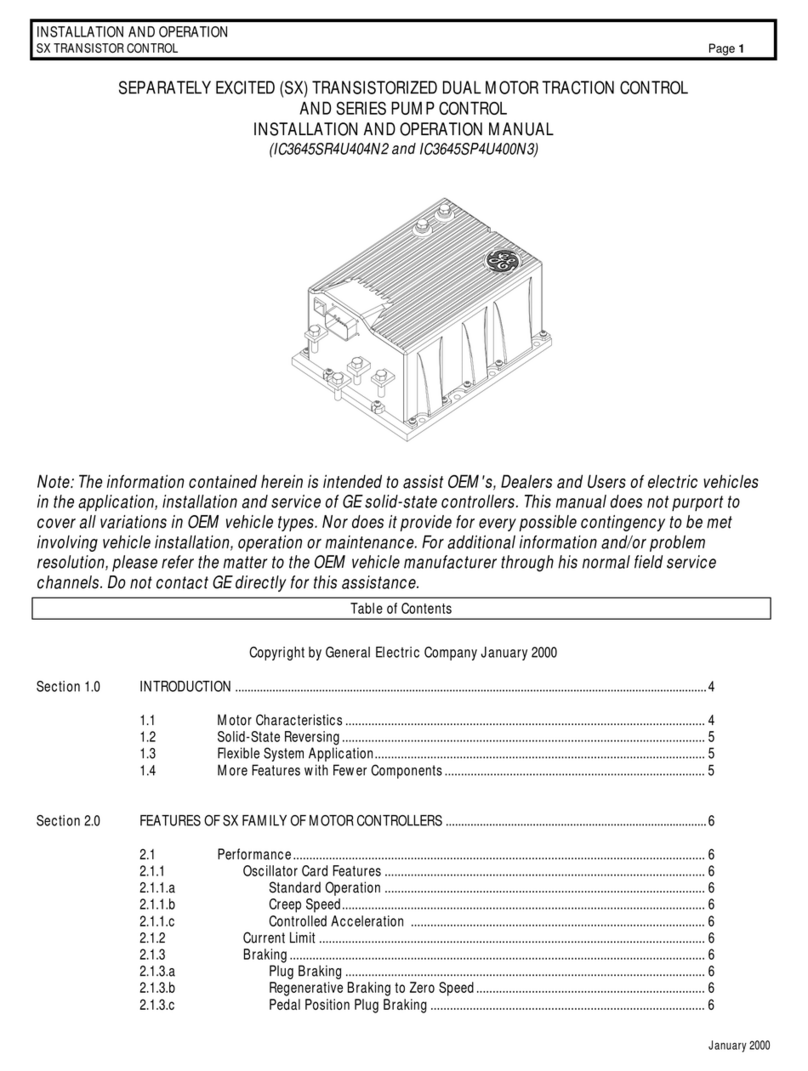
GE
GE SX TRANSISTOR CONTROL IC3645SR4U404N2 Installation and operation manual
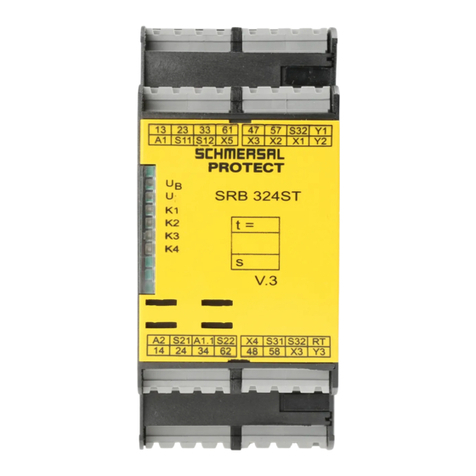
schmersal
schmersal SRB 324ST V.3 operating instructions

WAGO
WAGO 2789-9080 product manual
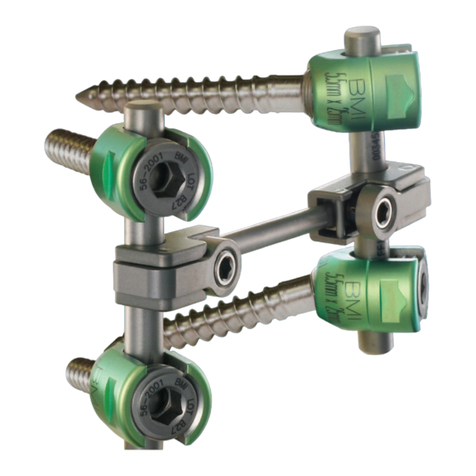
Orthofix
Orthofix SFS manual