Econ 7343FS User manual

Installation & Operation Manual
ECON ball valves Fig. 7343, 7383 www.eriks.com
Rev. 2
Content
1. ERIKS operating companies
2. Product description
3. Requirements for maintenance staff
4. Transport and storage
5. Function
6. Application
7. Installation
8. Maintenance
9. Service and repair
10. Troubleshooting
11. Removal
1. ERIKS operating companies
ECON wafer type ball valves are being delivered by several ERIKS operating companies on a
worldwide basis. In this manual these will be referred to as ‘ERIKS’, the individual terms of
delivery of the ERIKS operating company having executed the order are applicable.
2. Product description
The ECON wafer type ball valves are designed according to EN 1983 and should be used in
accordance with EN 1092 pressure-temperature rating and the information in our latest catalogue
or on our website www.eriks.com Ball valves are marked according to EN 19. The marking makes
the identification of the valve easier and contains:
- size (DN in mm or Inch)
- pressure class
- body and bonnet material marking
- ECON logo
- heat numbers
- tag plate
3. Requirements for maintenance staff
The staff assigned to assembly, operating and maintenance tasks should be qualified to carry out
such jobs and in any circumstance, ensure personal safety
4. Transport and storage
Transport and storage should always be carried out with the ball complete closed and the valves
should be protected against external forces, influence and destruction of the painting layer as well.
The purpose of the painting layer is to protect the valve against rust, during transport and storage.
The valves should be stored in an unpolluted space and should also be protected against all
atmospheric circumstances. There should be taken care of the temperature and humidity in the
room, in order to prevent condensate formation.
5. Function
ECON ball valves are designed to stop the flow of a medium. The valve is closed by turning the
lever clockwise; please don’t use tools to increase the torque on the lever. It is recommended to
use the ball valve in a complete open or closed position. An intermediate position must be avoided
as much as possible, to protect the seats.
6. Application
The ECON ball valves are used in industrial applications with clean gasses and liquids. The valves
are designed for standard operating conditions. For the use in extreme conditions e.g. highly
corrosive media, it is recommended to mention this at the ordering stage, to verify whether the
valve is suitable. The installation designer is responsible for the valve selection, suitable for the
working conditions. The valves are unsuitable, without written permission of an ERIKS company,
to apply for hazardous media as referred into Regulation (EC) No 1272/2008.

Installation & Operation Manual
ECON ball valves Fig. 7343, 7383 www.eriks.com
Rev. 2
7. Installation
During the installation of the wafer type ball valves, the following rules should be observed:
- make sure before an installation that the ball valves were not damaged during the
transport or storage.
- make sure that applied ball valves are suitable for working conditions, medium used in the
plant and the right system connections, according to pressure and temperature limits as
per the tag plate.
- to take off dust caps if the valves are provided with them.
- the interior of the ball valve and pipeline must be free from foreign particles.
- the valve should be assembled in the pipeline in open position, for a correct functioning,
the valve must be stress free mounted in the pipeline, supports must be arranged to
prevent any additional stress, caused by the weight of the valve or the pipeline.
- the valve may be fitted in any position and direction in the pipeline.
- mount the pipeline in such a way that harmful forces, excessive vibrations, bending and
tensional forces are avoided.
- for easy operating, the clear distance around the lever shall be not less than 100 MM.
- tighten the flange bolt crosswise using the stipulated torque, see Table A
- before plant startup, especially after repairs carried out, flush the pipeline, with fully
opened ball.
Warning:
When the valve is used at the very end of the pipelines, the end cap of the valve must be facing
and connecting towards the pipeline. Be extremely careful that it should never be facing on the
opposite direction (away from the pipeline). Please refers to the below picture for the correct valve
direction when the valve is installed under such circumstances.
8. Maintenance
Before starting any service jobs, make sure that the medium supply to the pipeline is stopped,
pressure is decreased to ambient pressure, the pipeline is completely cleaned and ventilated and
the plant is cooled down. Always keep safety instructions in mind and take all personal safety
precautions.
During maintenance, the following rules should be observed:
- keep always personal safety precautions in mind and always use appropriate protection
e.g. clothing, masks, gloves etc.
- be alert that the temperature still can be very high or low and can cause burns.
- be alert that a closed ball can contain medium under pressure and a opened ball can
contain some medium in the cavity-space behind the ball.
- check the ball valve on all possible leakages.
- dust, grease and medium residual, must be frequently cleaned of the valve body and all
moving parts, such as stem, to guarantee all operating functions.
- if required replace the stem seal, for safety reasons we recommend that the stem seal can
only can be replaced when the valve is depressurized, drained and ventilated.
Please see for the needed torque information Table A.
- to ensure a safe operation we recommend to check the ball valves at an interval of three
months.
Re-tighten packing.
- should a leakage occur at the gland packing, retighten the stem (gland) nut (13).
- take care that the stem nut (13) are not tighten too much. Normally the leakage can be
stopped by simple turning the stem nut (13) by 30°-60°

Installation & Operation Manual
ECON ball valves Fig. 7343, 7383 www.eriks.com
Rev. 2
Replacement of seats and seals
Disassembly
- place the valve in half-open position and flush the line to remove any hazardous material
from the valve body.
- place the valve in close position, remove both counter flange bolts & nuts and lift valve
from line.
- remove handle nut (16), handle (17) or actuator set, stop-lock-cap (14), stem nut (13),
Belleville washer (12), gland (11), bush (10), stem packing (9).
- remove cap (2), separated from body (1), remove body gasket (20).
- make sure that the ball is in closed position, thus the ball (3) can be taken out easily form
the body, then take out the body ball seat.
- push the stem (5) down into the body cavity and remove, then remove stem O-ring (8),
packing (9) form the body.
Reassembly
- reassembly process is reverse sequence of disassembly.
- clean and inspect all parts, full replacement of all soft parts (seats and seals) are strongly
recommended.
- tighten the cap (2) crosswise using the stipulated torque value. See Table A
- tighten the stem nut (13) using the stipulated torque value. See Table A
- cycle the valve slowly with gentle back and forth motion to build gradually to full quarter
turn.

Installation & Operation Manual
ECON ball valves Fig. 7343, 7383 www.eriks.com
Rev. 2
Table A: Torque values for body inserts, body bolts and stem nuts.
For the DIN and ASME ball valves.
Fig. 7343 & 7383
Threaded body insert
Stem nut
PN10/PN16
PN25/PN40
Thread
Torque (Nm)
Size
Torque (Nm)
DN15
M48*1.5
110~125
7/16-20UNF
9~12
DN20
M52*1.5
130~145
7/16-20UNF
9~12
DN25
M60*1.5
155~180
9/16-18UNF
12~16
DN32
M70*1.5
240~270
9/16-18UNF
12~16
DN40
M80*1.5
305~335
3/4-16UNF
17~22
DN50
M95*2
450~480
3/4-16UNF
17~22
DN65
M115*2
650~685
7/8-14UNF
25~32
DN80
M132*2
730~765
7/8-14UNF
25~32
PN10/PN16
PN25/PN40
Body bolts
Stem nut
Size
Torque (Nm)
Size
Torque (Nm)
A2-70
8.8
DN100
M12
50
67
1-1/8-12UNF
42~50
DN100
M16
127
170
DN125
M14
80
107
1-3/8-12UNF
65~75
DN150
DN125
M16
127
170
DN150
M20
248
331
Fig. 7343 & 7383
Threaded body insert
Stem nut
CL 150
CL 300
Thread
Torque (Nm)
Size
Torque (Nm)
1/2
M42*1.5
110~125
3/8-24UNF
9~12
3/4
M52*1.5
130~145
3/8-24UNF
9~12
1
M60*1.5
155~180
9/16-18UNF
12~16
1.1/4
M70*1.5
240~270
9/16-18UNF
12~16
1.1/2
M80*1.5
305~335
5/8-18UNF
17~22
2
M95*2
450~480
5/8-18UNF
17~22
2.1/2
M115*2
650~685
7/8-14UNF
25~32
3
M132*2
730~765
7/8-14UNF
25~32
CL 150
CL 300
Body bolts
Stem nut
Size
Torque (Nm)
Size
Torque (Nm)
A193
B8
A2-
70
4
-
9/16-
12UNC
84
84
1-1/8-12UNF
42~50

Installation & Operation Manual
ECON ball valves Fig. 7343, 7383 www.eriks.com
Rev. 2
9. Service and repair
All service and repair jobs should be carried out by authorized staff, using suitable tools and use
original spare parts (packing, gasket, etc.) of the same valve size.
- welding repair and drilling on the valve is forbidden.
- it is forbidden to disassemble the valve and replace seats or seals when the valve is under
pressure.
- before new seats or seals are placed, the areas where they are placed, must be cleaned.
- after replacement of seats or seals it is necessary to check the valve operation and
tightness of all connections. Tightness test should be carried out.
- after installation, we recommend to check the ball valve at an interval of three months.
10. Troubleshooting
It is essential that the safety regulations are observed when identifying the fault.
Problem
Possible cause
Corrective measures
No flow
The ball valve is closed
Open the ball valve
Dust caps were not removed
Remove dust caps
Little flow
Valve not completely open
Open valve completely
Piping system clogged
Check piping system
Valve difficult to open
Stuffing box seal too tight
Slacken nut
Wrong direction of rotation
Turn counter clockwise to open
Ball seat damaged by foreign
particles.
Replace the ball seats
Leakage across the stem
Stuffing box gland slack
Tighten stuffing box gland, if
necessary renew stuffing box
packing
Leakage across valve seat
Valve not properly closed
Pull lever tight without tools
Seat damaged by foreign
particles
Replace the ball seats
Medium contaminated
Clean valve and install dirt
screen
Operating failure
Packing too tight
Loosen gland nut
11. Removal
All dismantled and rejected valves cannot be disposed with household waste. The valves are
made of materials which can be re-used and should be delivered to designated recycling centers.
.
This manual suits for next models
1
Table of contents
Other Econ Control Unit manuals
Popular Control Unit manuals by other brands
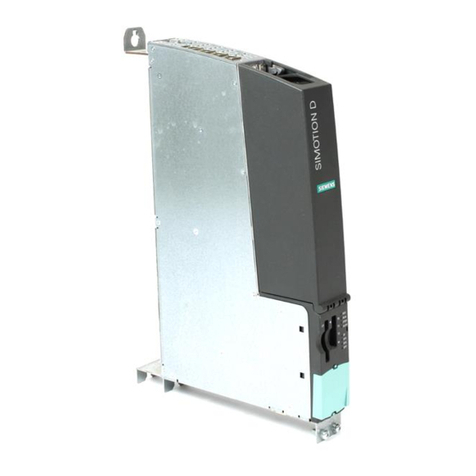
Siemens
Siemens SIMOTION D4 Series manual
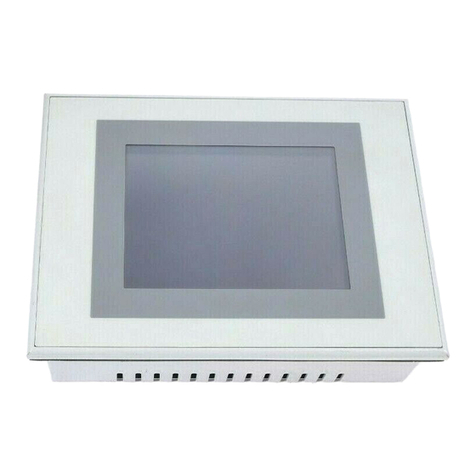
Lenze
Lenze EPM-H505 operating instructions
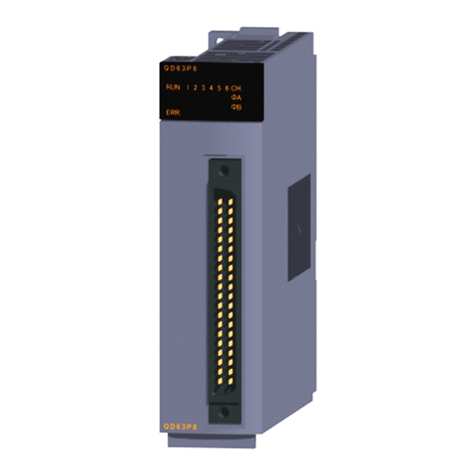
Mitsubishi Electric
Mitsubishi Electric MELSEC Q Series user manual
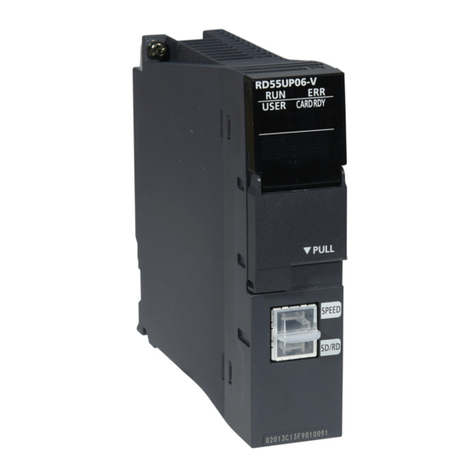
Mitsubishi Electric
Mitsubishi Electric MELSEC iQ-R C Programming manual
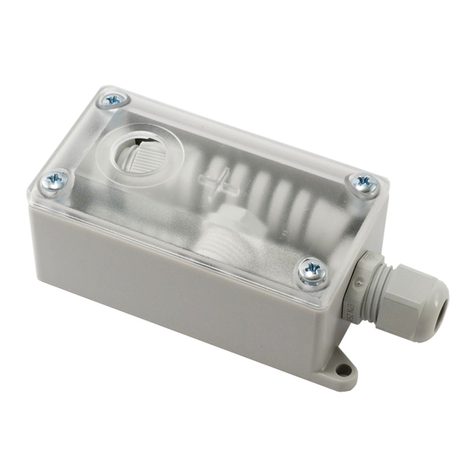
VITECTOR FRABA
VITECTOR FRABA OSE-C 1001 Copy of original manual
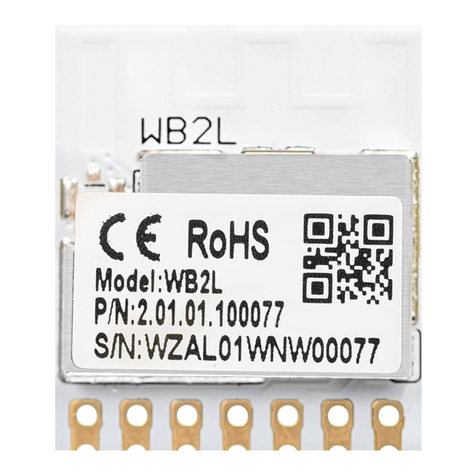
TUYA
TUYA WB2L datasheet