Econ ERIKS User manual

Installation & Operation Manual
Proven Quality since 1892
ECON ball valves Fig. 7422, 7442, 7522, 7542, 7622, 7642, 7722, 7742 www.eriks.com
Rev.4 Page 1
Content
1. ERIKS operating companies
2. Product description
3. Requirements for maintenance staff
4. Transport and storage
5. Function
6. Application
7. Installation
8. Maintenance
9. Service and repair
10. Troubleshooting
11. Removal
1. ERIKS operating companies
ECON ball valves are being delivered by several ERIKS operating companies on a worldwide
basis. In this manual these will be referred to as ‘ERIKS’, the individual terms of delivery of the
ERIKS operating company having executed the order are applicable.
2. Product description
The ECON ball valves are designed according the information in our latest catalogue or see our
website www.eriks.com and should be used in accordance with the applicable pressure-
temperature rating as stated on this website. Ball valves are provided with marking, according to
EN 19. The marking makes the identification of the valve easier and contains:
- size (inch)
- pressure rating class
- body material marking
- ECON logo
- heat numbers
3. Requirements for maintenance staff
The staff assigned to do assembly, operating and maintenance tasks should be qualified to carry
out such jobs and in any circumstance, ensure personal safety
4. Transport and storage
During transport and storage the valves should be protected against external forces, influence and
destruction of the painting layer as well. The purpose of the painting layer is to protect the valve
against rust, during transport and storage. The valves should be stored in an unpolluted space
and should also be protected against all atmospheric circumstances. There should be taken care
of the temperature and humidity in the room, in order to prevent condensate formation.
5. Function
ECON ball valves are designed to stop the flow of a medium. The valve is closed by turning the
lever clockwise; please don’t use tools to increase the torque on the lever.
6. Application
The ECON ball valves are used for industrial systems gasses and liquids. The valves are
designed for standard operating conditions. For the use of extreme conditions e.g. aggressive or
abrasive media, it is recommended to mention this at the ordering stage, to verify whether the
valve is suitable. The installation designer is responsible for the valve selection, suitable for the
working conditions. The valves are unsuitable, without written permission of an ERIKS company,
to apply for hazardous media as referred into Regulation (EC) No 1272/2008..

Installation & Operation Manual
Proven Quality since 1892
ECON ball valves Fig. 7422, 7442, 7522, 7542, 7622, 7642, 7722, 7742 www.eriks.com
Rev.4 Page 2
7. Installation
a. Remove the protective plastic cap on 2-threaded, BW and SW ends, and clean or flush the
valves.
b. Prior to mounting, flush and/or clean the pipeline to remove all accumulated extraneous
matters, which may damage the seats and ball surface and check if the valve has a preferred
flow direction and take this direction into account during installation.
c. Installation of threaded ends:
Use conventional sealant (e.g. Teflon) on the threads.
Apply a wrench only on the end cap of the valve for tightening. Applying a wrench on
the valve body or lever can seriously damage the valve.
d. Installation of BW and SW end valves
Tack-weld the valve on the pipe on four points on both caps, with the ball valve in
open position. Extended butt-weld end ball valves allow direct welding. For short butt-
weld or socket-weld end connections process the next steps.
Removed all body bolts except one and after losing the remaining one, the valve body
can be swung out. Secure seats from falling temporary with tape.
Finish welding both end caps on the pipe.
When cooled down, clean both end caps and body surface.
Remove temporary tape, swing the body back to the original position and replace the
bolts (if necessary). Put the valve in the open position. Tighten all nuts slightly. During
this operation it is very important to keep body and end caps perfectly parallel, thus,
preventing distortion of the end caps.
Tighten body bolts evenly. Make sure that maximum tightening torque is observed per
bolting torque data. See table B
e. Check proper operation of the valve.
f. The pipeline shall be free of tension after installation.
g. For any further information please contact the ERIKS company that has supplied the valves.
Contact information can be found on www.eriks.com
h. Make sure the pipeline will be flushed clean prior to operation.
i. The operation of the valve consist of turning the stem (by manual or automated means) ¼ turn
(900) clockwise to close, and ¼ turn counter-clockwise to open.
j. When the lever (if used) and/or stem flats or groove are in line with the pipeline, the valve is
open.
k. Besides operating by lever, Fig. 7422, 7442, 7522, 7542, 7622, 7642, 7722 and 7742 can also
be operated with an actuator, mounted on the ISO 5211 “Direct Mount” top-flange. (Please
see our catalogue to check top-flanges sizes)
l. Operating torque requirements will vary depending on the length of time between cycle, media
in the system line pressure and type of valve seat.
8. Maintenance
Long life and maintenance-free of valves can be maintained under normal working conditions and
in accordance with pressure/temperature and compatibility data chart.
Warning:
Before starting any service jobs, make sure that the medium supply to the pipeline is cut
off, pressure is decreased to ambient pressure, the pipeline is completely cleaned and
ventilated and the plant is cooled down.
Keep always personal safety precautions in mind and always use appropriate protection
e.g. clothing, masks, gloves etc.
Be alert that ball valves can trap pressurized fluid in ball cavity when closed position.
Be alert that the temperature still can be very high of low and can cause burns.

Installation & Operation Manual
Proven Quality since 1892
ECON ball valves Fig. 7422, 7442, 7522, 7542, 7622, 7642, 7722, 7742 www.eriks.com
Rev.4 Page 3
a. Re-tighten Packing
For maximum stem packing life, the proper packing adjustment procedure must be followed:
Should a leakage occur at the stem packing, retighten the stem nut (8)
Take care that the stem nut (8) is not tighten too much. Normally the leakage can be
stopped by simply turning the stem nut (8) by 30° to 60° clockwise.
b. Replacement of seats and seals
1) Disassembly of parts can be done while the valve is installed in the pipeline:
Before disassembly, make sure the pressure is released, to discharge any hazardous
media from the valve inside body cavity and to cool down the ball valve.
Remove all body bolts and washers (15+16) except one and after losing the remaining
one, the valve body can be swung out, and place valve in close position.
To swing the body can only be done at the Non Fire-Safe executions!!
Remove body gasket (5), seat rings (4) and ball (3). Inspect the ball accurately on
scratches, if any, the ball should be replaced.
When the stem packing needs to be replaced. Remove parts of upper parts in following
order: Lever nut/screw (19+20), lever (18), nut-lock-cap (7), stem nut (8), Belleville
washers (9) and gland (10).
Push stem (6) down into body cavity and remove, then remove upper washer (11B),
stem packing (11A) and lower washer (11B) from the body (1).
Also the O-ring (12) can now be taken out from the stem.
Ball valve, standard –non fire-safe execution.

Installation & Operation Manual
Proven Quality since 1892
ECON ball valves Fig. 7422, 7442, 7522, 7542, 7622, 7642, 7722, 7742 www.eriks.com
Rev.4 Page 4
Ball valve, fire-safe execution.
2) Reassembly:
Clean and inspect all parts, reassembly by processes are reverse sequence of
disassembly.
Reassemble the ball valve by using new seat rings, body seal rings and stem packing
is strongly recommended.
Follow procedures 8b1 in reversed order. Swing the body back to original position. Put
the ball in open position. Tighten body bolts evenly per Torque Data Table B.
To swing the body can only be done at the Non Fire-Safe executions!!
Tighten the stem nut (8), using Table A stipulated torque figures.
Pressure test the valve, then cycle valve several times before resuming services

Installation & Operation Manual
Proven Quality since 1892
ECON ball valves Fig. 7422, 7442, 7522, 7542, 7622, 7642, 7722, 7742 www.eriks.com
Rev.4 Page 5
Table A: Torque Figures for stem nut tighten
Size FB
Size RB
Stem nut size
Torque Nm
1/4”-1/2”
3/4”
7/16-20 UNF
10
3/4”
1”
7/16-20 UNF
10
1”
1.1/4”
9/16-18 UNF
10
1.1/4”
1.1/2”
9/16-18 UNF
10
1.1/2”
2”
3/4-16 UNF
20
2”
2.1/2”
3/4-16 UNF
20
2.1/2”
3”
7/8-14 UNF
30
3”
4”
7/8-14 UNF
30
4”
X
1.1/8-12 UNF
50
Table B: Torque Figures for flange bolt tighten
Size FB
Size RB
Body bolting
size
Torque Nm
Standard
Execution A2-70
Torque Nm Fire
Safe Execution
B8M Class 2 S10
1/4”-1/2”
3/4”
M6
5
7.5
3/4”
1”
M8
10
18
1”
1.1/4”
M8
12
18
1.1/4”
1.1/2”
M10
19
36
1.1/2”
2”
M10
25
36
2”
2.1/2”
M12
31
60
2.1/2”
3”
M14
53
X
3”
4”
M16
62
X
4”
x
M16
95
X
Above torques are only valid by using anti-seizing paste. This paste must be applied as well
on the bolt as on the nut surface which is in contact with the body.
The body bolts need to be greased with anti-seizing paste in order to prevent galling.
Fabricate, Bechem Berulub VPN 13 Spray

Installation & Operation Manual
Proven Quality since 1892
ECON ball valves Fig. 7422, 7442, 7522, 7542, 7622, 7642, 7722, 7742 www.eriks.com
Rev.4 Page 6
9. Service and repair
All service and repair jobs should be carried out by authorized staff, using suitable tools and user
shall use genuine valve parts.
- Welding repair and drilling of the valve is forbidden.
- It is forbidden to disassemble the valve when the valve is under pressure.
- Before you replace seats or seals you have to clean the working areas where you have to
put the seats or seals.
- After replacement of the ball valve it is necessary to check the valve operation and
tightness of all connections. Leakage test should be carried out.
- After installation, the valve should be checked and maintained periodically at least every 3
months, depending on the medium. A (partial) operation cycle of the valve is
recommended.
10. Troubleshooting
It is essential that the safety regulations are observed when identifying the fault.
Problem
Possible cause
Corrective measures
No flow
The ball valve is closed
Open the ball valve
Dust caps were not removed
Remove dust caps
Little flow
Valve not completely open
Open valve completely
Piping system clogged
Check piping system
Valve difficult to open
Stem packing too tight
Slacken stem nut
Wrong direction of rotation
Turn counter clockwise to open
Ball seat rings damaged by
foreign particles.
Replace the seat rings
Expanded medium behind the
ball
Cool down the ball valve
Leakage across the stem
Stem packing gland slack
Tighten stem nut, if necessary
replace the ball valve
Leakage across valve seat
Valve not properly closed
Pull lever tight without tools
Seat damaged by foreign
particles
Replace the seat rings
Medium contaminated
Clean valve and install dirt
screen
Operating failure
Packing too tight
Loosen stem nut
11. Removal
Dismantled and rejected valves cannot be disposed with household waste. The valves are made
of materials which can be re-used and should be delivered to designated recycling centers.
General warning:
General note for products which may be used for seawater:
Although our products can be used in seawater systems it should always be noted that, in case of
installation in a piping system made of materials which are frequently used because of their excellent
seawater resistance (e.g. Cunifer), large potential differences may occur possibly causing corrosion
which could permanently damage the proper functioning and integrity of our product.
A combination of different materials should always be mentioned prior to the purchase of our products
in order for us to give the best possible advise on a safe functioning.
Table of contents
Other Econ Control Unit manuals
Popular Control Unit manuals by other brands

Kessel
Kessel Staufix SWA Installation and operating manual
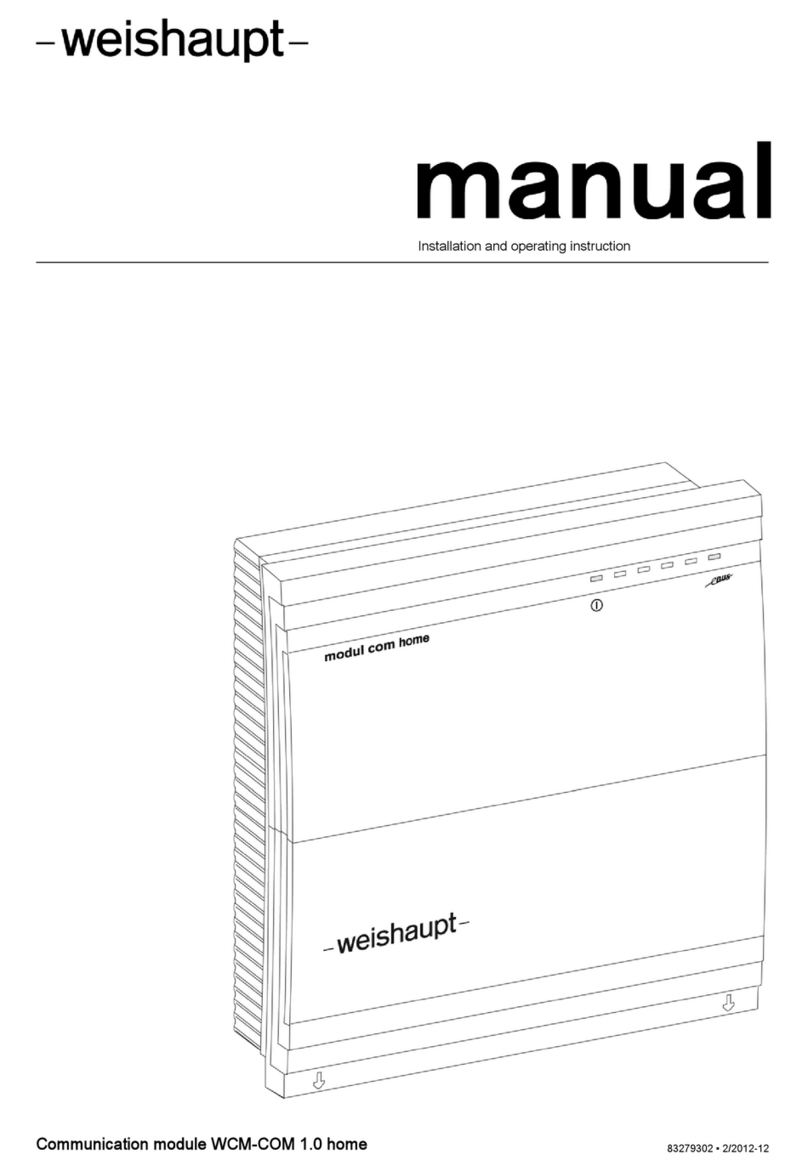
Weishaupt
Weishaupt WCM-COM 1.0 home Installation and operating instruction

Belden
Belden GRASS VALLEY MDX-3901 Guide to installation and operation
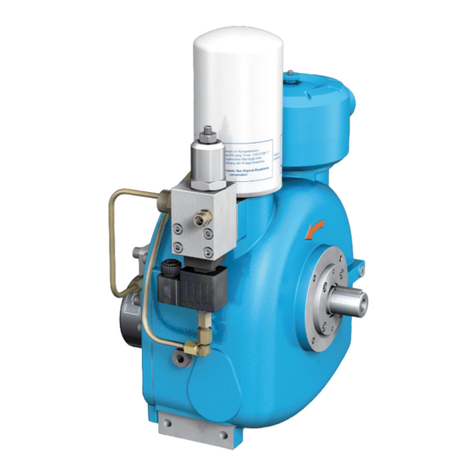
ROTORCOMP
ROTORCOMP NK 31 Installation and operating manual

Graco
Graco CleanShot instructions
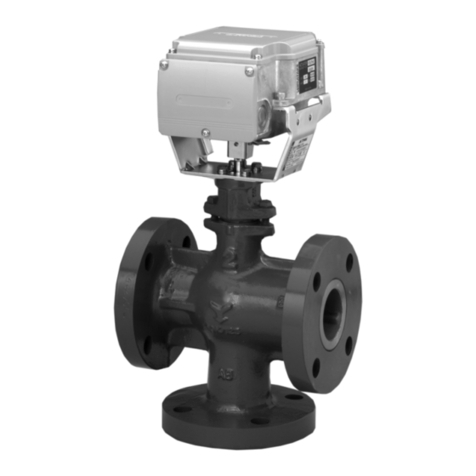
Azbil
Azbil ACTIVAL VY54X0F Series Specifications & instructions