Econ ELSA50 User manual

Installation & Operation Manual
ECON actuator Fig. 7917EX, type ELSA50 – 260 www.eriks.com
Rev. 0 – April 10th, 2019
ECON SPRING RETURN ELECTRIC
ACTUATOR
Fig. 7917EX, type ELSA50 - 260
Installation and Operation Manual for actuator type: ELSA50, 130, 200 & 260

Installation & Operation Manual
ECON actuator Fig. 7917EX, type ELSA50 – 260 www.eriks.com
Rev. 0 – April 10th, 2019 1
Content
1. General Information ......................................................................................................................... 2
Safety Instructions ........................................................................................................................ 2
Installation Notices ....................................................................................................................... 2
1.2.1 General ............................................................................................................................. 2
1.2.2 Cable Glands .................................................................................................................... 4
Working Conditions ...................................................................................................................... 4
Standards ..................................................................................................................................... 4
Inspection, Storage, Transport ...................................................................................................... 5
1.5.1 Receiving / Inspection ....................................................................................................... 5
1.5.2 Storage ............................................................................................................................. 5
1.5.3 Transport .......................................................................................................................... 5
1.5.4 Lubrication ........................................................................................................................ 5
2. Product Overview ............................................................................................................................. 6
2.1 Features ....................................................................................................................................... 6
2.2 Actuator markings ........................................................................................................................ 7
3. Product Mechanical Data ................................................................................................................. 7
3.1 Parts Identification ........................................................................................................................ 7
3.2 Technical Information ................................................................................................................... 8
3.3 Mounting Base Details.................................................................................................................. 8
3.4 Actuator Selection ........................................................................................................................ 8
3.5 Sizing ........................................................................................................................................... 9
3.6 Duty Cycle – IEC .......................................................................................................................... 9
3.7 Flame path Joint ........................................................................................................................... 9
4. Mounting And Setup ....................................................................................................................... 11
4.1 Handwheel Installation ................................................................................................................ 11
4.2 Valve Mounting Instructions ......................................................................................................... 11
4.3 Wiring Instructions .......................................................................................................................13
4.4 Actuator Set-up ...........................................................................................................................13
4.4.1 Adjustment procedure for spring-return actuators in the fail-close position upon loss of
supply voltage. ..........................................................................................................................14
4.4.2 Adjustment procedure for spring-return actuator in the fail-open position upon loss of
supply voltage ...........................................................................................................................16
5. Modulating Control Board Adjustment ..........................................................................................18
5.1 Modulating Control Board Surface ...............................................................................................18
5.2 Programming ...............................................................................................................................19
5.3 Dip Switch Setting (SW1) ............................................................................................................19
5.4 P4 Terminal .................................................................................................................................22
5.5 Sensitivity Switch Setting (SW2) ..................................................................................................22
5.6 Settings for open and close .........................................................................................................22
5.7 Troubleshooting of modulating controller .....................................................................................24
6. Troubleshooting ..............................................................................................................................25
7. Actuator Options .............................................................................................................................27

Installation & Operation Manual
ECON actuator Fig. 7917EX, type ELSA50 – 260 www.eriks.com
Rev. 0 – April 10th, 2019 2
1. General Information
Failure to follow safety instructions may cause serious injury, equipment damage,
or voided warranty.
Safety Instructions
Installation, maintenance and repair works must be performed by trained personnel
and the safety and warning instruction contained in this manual must be followed.
The user should read and follow instructions contained in this operation manual
included with the product. Failure to do this may result in damages and void warranty.
ERIKS will not be liable for damages caused by operator negligence or misuse.
Local health and safety legislation shall be complied with.
In a few cases, the surface temperature may exceed 60°C (140°F). Please check
the surface temperature before operation, using an appropriate thermometer and
wearing protective gloves before operation.
Installation Notices
Operating by handwheel: Do not use any tools to increase force on the handwheel
for operating, as this can damage the actuator or valve.
1.2.1 General
The spring return actuator is shipped in spring return position (spring unloaded).
Standard actuators will be supplied with a clockwise spring return action for closing
the valve in case power outage occurs. However actuators can optionally be supplied
with a counter-clockwise spring return action for opening the valve.
DO NOT install in ambient temperatures that exceed 70°C (158 °F).
DO NOT, under any circumstances, remove the cover of the actuator while in a
hazardous location when the power is still live inside the actuator. This could cause
ignition of a hazardous atmosphere.
DO NOT, under any circumstances, use an explosion-proof electric actuator in a
hazardous location that does not meet the specification which the actuator was
designed for.
Mount, test, and calibrate actuators in a non-hazardous location.
When removing the actuator, care must be taken not to scratch, scar or deform the
flame path of the cover or base of the actuator. This will negate the protection rating
of the enclosure in a hazardous location.
The explosion proof electric actuator is shipped with mating surfaces of the cover

Installation & Operation Manual
ECON actuator Fig. 7917EX, type ELSA50 – 260 www.eriks.com
Rev. 0 – April 10th, 2019 3
and base. When assembling them, pay attention to the mating number (QA code) in
order to assure the protection rating in a hazardous location.
Please read the operation manual and wiring diagram carefully before installation.
Verify that the supply voltage is in accordance with the data on the nameplate to
prevent short circuit or damage to the electrical/electronic parts caused by incorrect
power input.
Turn power off before wiring or maintenance.
There are grounding devices both inside and outside of the actuator. The ground
wires should be connected properly.
The metal plugs in the conduit entries are for transport only. For long term
protection appropriate flameproof cable glands and power cables must be fitted.
These must withstand a minimum temperature of 105°C (221°F). Please refer to
section 1.2.3
To avoid functional failure caused by a static load, do not touch any components on
the PCB with metal tools or bare hands.
Use proper cable glands in order to seal the conduit entries correctly. Don’t mount
the actuator with conduit entries in upright position in order to prevent water
ingress.
After manual operation, the actuator shall be returned to its unloaded position by
handwheel before electrical operation of the actuator.
The actuator should be installed in an upright or horizontal position. Do not mount
upside down or below the horizontal position.
Periodically inspect the actuator enclosure to prevent dust from accumulating.
Perform below inspections prior to installation. The actuator may not be used if any
of the below items is unqualified.
Check the actuator markings and certificate number in order to check if it
does comply with the intended application.
All parts of the housing must be assembled and fastened in the right
manner.
USE FASTENERS WITH YIELD STRESS ≥ 700MPa.
All the explosion-proof parts may not show cracks or functional defects.

Installation & Operation Manual
ECON actuator Fig. 7917EX, type ELSA50 – 260 www.eriks.com
Rev. 0 – April 10th, 2019 4
1.2.2 Cable Glands
Please select matching explosion-proof cable connectors/glands according
to the product specifications.
ATEX / IECEx
The actuator is delivered with two conduit entries plugged by metal plugs. Use cable
glands with ATEX / IECEx certification and in accordance with the technical standards
required by Ex db IIB Gb, Ex tb IIIC Db. The electrical supply cable must be suitable for
the applicable power rating and a minimal temperature of 105°C (221°F).
Working Conditions
ATEX / IECEx:
Atmospheric pressure:80 - 110 kPa.
Ambient temperature:- 30°C to + 70°C ( - 22°F to + 158°F ).
Relative humidity:Not more than 95% ( + 25°C / 77°F).
The actuator can operate normally within tolerated variation of ± 10% of rated
supply. voltage or ± 1% of rated frequency.
Standards
ATEX European Hazardous Area:
EN 60079-0:2018; EN 60079-1 2014/AC:2018-09; EN 60079-31:2014
Directive Group Ambient Temperature
II 2 GD Ex db IIB T4 Gb - 30°C to + 70°C ( - 22°F to + 158°F )
II 2 GD Ex tb IIIC T130°C Db - 30°C to + 70°C ( - 22°F to + 158°F )
IECEx International Hazardous Area:
IEC 60079-0:2017 Ed 7; IEC 60079-1:2014 Ed 7; IEC 60079-31:2013 Ed 2
Group Ambient Temperature
Ex db IIB T4 Gb - 30°C to + 70°C ( - 22°F to + 158°F )
Ex tb IIIC T130 °C Db - 30°C to + 70°C ( - 22°F to + 158°F )

Installation & Operation Manual
ECON actuator Fig. 7917EX, type ELSA50 – 260 www.eriks.com
Rev. 0 – April 10th, 2019 5
Inspection, Storage, Transport
1.5.1 Receiving / Inspection
Carefully inspect the package for any damages resulting from shipping and report
all damages to the freight carrier and supplier.
After unpacking the product, please keep the cartons and any packing materials in
case of product return or replacement. Verify that the items listed on the packing slip
or bill of lading are the same as what was ordered. If there is any discrepancy,
please contact your supplier.
Verify that the technical data on the nameplate is in accordance with your purchase
order.
1.5.2 Storage
The actuator should be stored in a dry area with a relative humidity of less than 90%
(20 ± 5°C) and at a temperature between - 20°C to + 40°C (- 4°F to + 104°F)
The product shall be stored with suitable protection from corrosive substances,
which could damage the metal and insulating parts.
The metal plugs for temporary protection should not be removed until the actuator is
ready to be cabled. Use suitable flameproof cable glands to ensure IP rated
protection when installing. Please refer to section 1.2.2.
1.5.3 Transport
Attach ropes or hooks for the purpose of lifting or hoisting only to the housing and
not to the handwheel.
Actuators packaged in cartons can stand up to land, sea, or air transportation.
Packaged actuators shall be safeguarded from violent impact and strong vibrations
and be protected from rain or snow.
1.5.4 Lubrication
The gear train has been sufficiently lubricated at the factory. No additional
lubrication is required.

Installation & Operation Manual
ECON actuator Fig. 7917EX, type ELSA50 – 260 www.eriks.com
Rev. 0 – April 10th, 2019 6
2. Product Overview
ECON Fig. 7917EX ELSA series explosion-proof spring return fail-safe actuators are
designed and manufactured as flame-proof and combustible dust-proof products.
ECON ELSA series spring return fail-safe electric actuators offer torque ranges from 50 Nm
up to 260 Nm (445 in-lb to 2300 in-lb) and are designed for fail-safe positioning of quarter-
turn valves or dampers upon loss of supply voltage, which include On/Off control, floating
control and modulating control. A rack and pinion spring mechanism is used to position the
controlled device to either fully OPEN or fully CLOSED position without any external power
source. For On/Off types, a mechanical BUFFER is used at the end of the spring stroke to
reduce the “water hammer” effects in pipes. A clutch-less manual override is provided for
manual positioning of the controlled device. Actuators without a manual override can be
ordered as an option.
ATEX / IECEx Explosion-proof instructions
II 2 G Ex db IIB T4 Gb
II 2 D Ex tb IIIC T130°C Db
Fig. 7917EX ELSA series Explosion-Proof Spring Return Fail-safe Electric
Valve Actuator (referred as "actuator"). It is a control device for valves and can
be used in the places, where is classified as Zone 1 or Zone 2, contained Group
II A and Group II B gases, Zone 21 or Zone 22, contained the combustible dust
atmosphere or the mixture circumstance with the explosive gas atmospheres
and the combustible dust atmospheres. Temperature group T1 - T4.
Certificate Numbers:
Sira 19 ATEX 1176 X
IECEx SIR19.0043X
2.1 Features
IP68 enclosure (7m/72 hours).
Controls: On/Off, floating (optional), modulating (optional).
Clutch-less manual override.
ISO 5211 mounting flange.
Domed visual position indicator.
Built-in motor thermal protection

Installation & Operation Manual
ECON actuator Fig. 7917EX, type ELSA50 – 260 www.eriks.com
Rev. 0 – April 10th, 2019 7
2.2 Actuator markings
ECON logo (trade mark)
Model number
Running time
Torque (output)
Fail-safe direction
Enclosure rating
Motor power
Supply voltage
Rated current
Serial Number
Date of manufacture
ATEX and IECEx markings
ATEX and IECEx certificate No.
Please make sure the explosion-proof specification
for the product is in consistence with nameplate and
instruction.
3. Product Mechanical Data
3.1 Parts Identification
Actuator top cover
Top cover bolts
Warning text
Handwheel
Type plate
Manual override gear box
Conduit entries
Visual position indicator
Spring unit cover
Actuator without manual override
Actuator with manual override

Installation & Operation Manual
ECON actuator Fig. 7917EX, type ELSA50 – 260 www.eriks.com
Rev. 0 – April 10th, 2019 8
3.2 Technical Information
Model
Torque Motor Power
Weight
Nm In-lb Watt
Without manual
override
With manual
o
verride
kg lb kg lb
ELSA50 50 445 50 28 62 38 84
ELSA130
130 1,150 130 59 130 76 168
ELSA200
200 1,770 130 97 214 137 302
ELSA260
260 2,300 130 97 214 137 302
3.3 Mounting Base Details
3.4 Actuator Selection
Model
Mounting
Flange Shaft (A) Depth of Shaft
(B)
ISO 5211 mm inch mm inch
ELSA50 F07 17 0.669 30 1.181
ELSA130
F10 22 0.866 41 1.614
ELSA200
F12 27 1.063 45 1.772
ELSA260
F12 27 1.063 45 1.772
Fig. 7917EX ELSA- - - - -
❶ Type
ELSA50
ELSA130
ELSA200
ELSA260
❷ Voltage
24: 24VAC
D24:24VDC
110:110VAC 1PH
120:120VAC 1PH
220:220VAC 1PH/3PH
240:240VAC 1PH/3PH
380:380VAC 3PH
440:440V AC 3PH
❹
Control Mode
T:On/Off.
F:Floating.
M:Modulating.
❸
Direction of Rotation
CW:
Fail Clockwise Spring
Return.
CCW:
Fail Counter-Clockwise
Spring Return.
❺
Manual Override
Y:With Manual
Override.
N:Without Manual
Override.

Installation & Operation Manual
ECON actuator Fig. 7917EX, type ELSA50 – 260 www.eriks.com
Rev. 0 – April 10th, 2019 9
3.5 Sizing
For safety reasons, do not remove or inspect the SPRING STRUCTURE. Proper
tools must be used or serious injury will occur
The actuator shall be sized to ensure that its torque output meets the operating torque of the
valve and its ability to overcome the required duty cycle of the application (A safety factor of
minimal 30% on top of the required valve torque is recommended).
If the maximum torque of a valve is 80 Nm 80 x 1.3 = 104 Nm
104 Nm < 130 Nm (ELSA130) OK!
104 Nm > 50 Nm (ELSA50) NOT OK!
3.6 Duty Cycle – IEC
The duty cycle is the relationship between the running time and resting time. It is
calculated as below:
Duty Cycle = x 100 %
Rest Time (s) =
If the motor running time is 10 s, the spring return time is 5 s and the duty
cycle is 50%, the rest (off) time shall be calculated as below:
Running time: [ 10 s × ( 1 - 50 % ) ] / 50 % = 10, rest time is 10 s
Reset time:[ 5 s. × ( 1 - 50 % ) ] / 50 % = 5, rest time is 5 s
One cycle is equal to: open-rest-close-rest
A rest time is required after spring return action because the gear train
and motor are driven during spring release.
3.7 Flame path Joint
The following conditions apply to both certificate numbers SIRA 19 ATEX 1176 X and
IECEx SIR 19.0043X: The flame paths in this equipment are different to the standard
dimensions given in EN/IEC 60079-1. If specific flame path dimensions are required
then the manufacturer (OEM) must be contacted.
Running Time (s) x ( 1 - Duty Cycle)
Duty Cycle
Running Time (s) + Rest Time (s)
Running Time (s)

Installation & Operation Manual
ECON actuator Fig. 7917EX, type ELSA50 – 260 www.eriks.com
Rev. 0 – April 10th, 2019 10
During cover removal and conduit entry removal, ensure that surfaces are
free from scratches or scrapes.
Actuator installation and maintenance must be performed by trained
personnel.
Cover Removal
Please gently remove the cover, but first remove the conduit entry metal plugs to
relieve the pressure inside the actuator and in order to avoid a vacuum by lifting the
cover. It will ease the top cover removal. DO NOT attempt to remove the top cover
with a screwdriver as it will damage the closing surfaces.
Cover Installation
Please ensure that the O-ring seal is in good condition prior to cover
installation. Slowly re-install the cover while being careful not to pinch the
O-ring seal.
The explosion-proof enclosures are marked with a QA-code on both of the
connection flanges. Please verify that QA-code inside the cover is identical
to the one on the connection flanges-during installation. Covers of these
actuators are not interchangeable!
Please follow below table to tighten the top cover screws:
Model Screw Allen Key Torque
mm Nm
ELSA50 M10 8 43
ELSA130 M14 12 120
ELSA200 to ELSA260 M16 14 185
Main Housing
F
lame
path
J
oint
Conduit Entries
Flamepath Joint
Explosion-proof
Metal Plug
O-ring
Top Cover
Flamepath Joint
Top Cover Screw

Installation & Operation Manual
ECON actuator Fig. 7917EX, type ELSA50 – 260 www.eriks.com
Rev. 0 – April 10th, 2019 11
4. Mounting And Setup
4.1 Handwheel Installation
a. Slide the fixing screw through the washers and handwheel and secure them to the
override shaft as shown in the figure below.
Turn off power when installing the handwheel.
b. Assembly completed as shown in the figure below.
4.2 Valve Mounting Instructions

Installation & Operation Manual
ECON actuator Fig. 7917EX, type ELSA50 – 260 www.eriks.com
Rev. 0 – April 10th, 2019 12
a. The spring return actuator is shipped in spring return position (spring unloaded).
Standard actuators will be supplied with a clockwise spring return action for closing the
valve in case power outage occurs. However actuators can optionally be supplied with
a counter-clockwise spring return action for opening the valve.
b. Make sure the valve is in the correct FAIL POSIITION before mounting the actuator to
it. Refer to illustration above.
c. Remove all of the valve manual operation parts, such as the mechanical open/close
stoppers in order to prevent interference with the electric operation.
Do not remove the packing gland or other parts necessary for safe operation
of the valve.
d. Check again if the valve and actuator are in the same position (fully-open or fully-
closed).
e. Once mounted together, either directly or with a mounting kit, ensure that they are
properly secured together by fastening all fasteners by using corrects tools.
f. Remove the conduit entry plug to relieve the pressure inside the actuator for the ease
of the top cover removal and gently remove the cover.
The power supply must be switched off before removing the cover.
g. A label with the wiring diagram is inside the cover of the actuator.
h. Supply power to the actuator.
Care must be taken at all times as there are live circuits present which may
cause an electrical shock.
i. Re-calibration may be required for the end positions, refer to section 4.4 for further
instructions.
j. Assemble the cover and secure the cover bolts firmly after setting.
Refer to 3.7 for installation and check if the flame path joint between the cover
and base is clean and without obstacles.
Please ensure that the O-ring seal is in good condition prior to cover
installation.
The explosion proof enclosures are marked with a QA-code on both of the
connection flanges. Please verify that QA-code inside the cover is identical to
the one on the connection flanges-during installation. Covers of these
actuators are not interchangeable!

Installation & Operation Manual
ECON actuator Fig. 7917EX, type ELSA50 – 260 www.eriks.com
Rev. 0 – April 10th, 2019 13
4.3 Wiring Instructions
Turn off the power before making the electrical connection!
There are grounding devices both inside and outside of the actuator (green screws).
The grounding wires should be connected properly.
Both conduit entries are plugged with metal plugs according to the specification as
mentioned below.
ELSA50 to ELSA260: 1/2” NPT, 3/4” NPT, M20 x 1.5 or M25 x 1.5.
Use correct glands with threaded ends that match the inside threads of the
actuator in order to prevent dame to these threads.
Verify the supply power is in accordance with the data on the nameplate to prevent
a short circuit and an electrical shock.
Do not apply power to the actuator before wiring, otherwise it can cause an
electrical shock or damage the components of the actuator.
After wiring, please tighten the conduit entries with suitable cable glands and cover
properly. Unused conduit entries have to be sealed with metal plugs to reach the
explosion-proof function. Please refer to section 1.2.2.
4.4 Actuator Set-up
If the actuator is equipped with a manual override, rotate the handwheel to return
the actuator to its fully unloaded spring position before the power is supplied.
Securely tighten the conduit fittings to ensure the enclosure protection rating.
The spring return actuator provides fail-safe positioning and the end stop position of the
spring return action is determined by either a buffer or mechanical stop (On/Off by the buffer,
floating or modulating limited by mechanical stop). When the actuator is motorized, the end
position is determined by limit switches.
The actuator has been set and calibrated at the factory. Most products will not require
recalibration of these settings. However these are general settings. After the valve and
actuator are bolted together, apply power to drive the actuator to its fully-open (spring
compressed for a spring to close actuator). Then remove power to let the rack and pinion
spring mechanism drive back to its fully-closed position. If the OPEN or CLOSE stop point
are not aligned with the valve or damper position correctly, the end positions must be
adjusted. Please follow steps below:

Installation & Operation Manual
ECON actuator Fig. 7917EX, type ELSA50 – 260 www.eriks.com
Rev. 0 – April 10th, 2019 14
For modulating unit, ensure to loosen the sector gear of potentiometer first before
adjusting the following settings.
4.4.1 Adjustment procedure for spring-return actuators in the fail-close position
upon loss of supply voltage.
Adjust FULLY-CLOSED (spring released) stop point. Follow the steps below:
a. Turn the power off and loosen the end stop protection cover using a 5mm hex key.
b. Loosen the hex locknut of the End Stop using a 17mm hex wrench. Hold the locknut and
turn the End Stop using a 10mm hex wrench to adjust the end position
c. Turn the buffer or End Stop in order to adjust the fully-closed stop point.
ELSA50 : One turn = 2.3 degrees
ELSA130 to ELSA260 : One turn = 1.4 degrees
d. Once completed, tighten the hex nut, replace the cover and tighten the bolts.
If the buffer or End Stop is adjusted, TC2 must be reset in accordance with
the buffer or the End Stop
e. Loosen the M3 cap bolt of the cam TC2 with a 2.5mm hex key.
f. Rotate the cam TC2 counter-clockwise until a light click is heard and then slowly rotate
the cam TC2 clockwise until a light click is heard.
g. Tighten the cap bolt of cam TC2.
Spring released 0°
Clockwise (CW)
Counter
-
clockwise (CCW)
Spring compressed 90°
Desired Position
Original Position
End stop
Hex Nut
End
stop
Protection
Cover
O
-
ring

Installation & Operation Manual
ECON actuator Fig. 7917EX, type ELSA50 – 260 www.eriks.com
Rev. 0 – April 10th, 2019 15
Adjust FULLY-OPEN (spring compressed) stop point. Follow the steps below:
a. Apply power to drive the actuator to its fully-open (spring compressed) position. If the
open stop point is not aligned with the valve or damper properly, then it must be adjusted.
b. Turn the power off and let the spring unit drive the actuator back to its fully-closed (spring
released) position.
c. If it is required to adjust, loosen the cap screw of cam TC1 with a 2.5m hex key.
To increase the opening angle, turn the cam clockwise.
To decrease the opening angle, turn the cam counter-clockwise.
【ELSA50】 【ELSA130 up to ELSA260】
d. After adjusting the cam, apply power to drive the actuator to the fully-open position.
e. Verify that it is in the correct fully-open position.
If it is in correct position, turn the power supply off and lock the cap bolt of cam TC1
If it is not in the correct position, repeat step C until the correct position is reached.
f. If auxiliary switches will be used for feedback, cams TC3 and TC4 need to be calibrated.
Adjust cam TC3 so it trips just before cam TC1 does.
Adjust cam TC4 so it trips just before cam TC2 does.
增加角度
Decrease
the
opening angle
Increase
the
opening
angle
Decrease
the
opening angle
In
crease
the
opening
angle
ELSA50 ELSA130, ELSA200 and ELSA260

Installation & Operation Manual
ECON actuator Fig. 7917EX, type ELSA50 – 260 www.eriks.com
Rev. 0 – April 10th, 2019 16
4.4.2 Adjustment procedure for spring-return actuator in the fail-open position upon
loss of supply voltage
Adjust FULLY-OPEN (spring released) stop point. Follow the steps below:
a. Turn the power off and loosen the end stop protection cover using a 5mm hex key.
b. Loosen the hex locknut of the End Stop using a 17mm hex wrench. Hold the locknut
and turn the End Stop using a 10mm hex wrench to adjust the end position.
c. Turn the buffer or End Stop to adjust the fully-open stop point.
ELSA50: One turn = 2.3 degrees
ELSA130 to ELSA260: One turn = 1.4 degrees
d. Once completed, tighten the hex nut, replace cover and tighten the bolts.
If the buffer or End Stop is adjusted, TC2 must be reset in accordance with the
buffer or the End Stop
e. Loosen the M3 cap screw of cam TC2 with a 2.5mm hex key.
f. Rotate the cam TC2 counter-clockwise until a light click is heard, and then slowly
rotate the cam TC2 clockwise until a light click is heard.
g. Tighten the cap bolt of cam TC2.
Adjust FULLY-CLOSED (spring compressed) stop point. Follow the steps below:
a. Apply power to drive the actuator to its fully-closed (spring compressed) position. If the
Spring released 90°
Clockwise (CW)
Counter
-
clockwise (CCW)
Spring compressed 0°
Desired Position
Original Position
ELSA50 ELSA130, ELSA200 and ELSA260

Installation & Operation Manual
ECON actuator Fig. 7917EX, type ELSA50 – 260 www.eriks.com
Rev. 0 – April 10th, 2019 17
close stop point is not aligned with the valve or damper properly, then it must be
adjusted.
b. Turn the power off and let the spring unit drive the actuator back to its fully-open
(spring released) position.
c. If it is required to adjust, loosen the cap bolt of cam TC1 with a 2.5m hex key.
To increase the opening angle, turn the cam clockwise.
To decrease the opening angle, turn the cam counter-clockwise.
【ELSA50】 ELSA130 up to ELSA260】
d. After adjusting the cam, apply power to drive the actuator to the fully-closed position.
e. Verify that it is in the correct fully-closed position.
If it is in correct position, turn the power supply off and lock the cap bolt of cam
TC1.
If it is not in the correct position, repeat step C until the correct position is reached.
f. If auxiliary switches will be used for feedback, cams TC3 and TC4 need to be
calibrated.
Adjust cam TC3 so it trips just before cam TC1 does
Adjust cam TC4 so it trips just before cam TC2 does.
For modulating actuators, after completing the calibration, turn the actuator to the
fully-closed position and follow the procedure below:
a. Loosen M5 set screw.
b. Rotate the sector gear clockwise
to the position shown in the
figure below.
Ensure that the round gear and
sector gear are engaged
properly.
c. Tighten M5 set screw.
增加角度
Decrease
the
opening angle
Incr
ease
the
opening
angle
Decrease
the
opening angle
Increase
the
opening
angle
S
ector
Round
Shaft
M5 Set
End Position
of Sector Gear

Installation & Operation Manual
ECON actuator Fig. 7917EX, type ELSA50 – 260 www.eriks.com
Rev. 0 – April 10th, 2019 18
5. Modulating Control Board Adjustment
5.1 Modulating Control Board Surface
The layout is based on 115 / 230V voltage.
TC2 is utilized for sensing fully-closed stop point. Once the spring mechanism has been
released when power outage, the actuator will not drive under power again until it has reached
its fail stop position and TC2 trips.
TC1 ”OPEN ”
Clockwise: increase opening degree.
Counter-clockwise: decrease opening degree.
Note:
LS2 shall trip while TC2 reaches the end stop point.
TC3 & TC4 are optional, refer to section 4.4.1 and 4.4.2 for calibration.
6
7
8
9
10
11
12
5
4
3
2
1
P4 Terminal
Dip Switch
es
LD1
-
LD9

Installation & Operation Manual
ECON actuator Fig. 7917EX, type ELSA50 – 260 www.eriks.com
Rev. 0 – April 10th, 2019 19
5.2 Programming
Σ
Controller Motor Driver
Feedback
Signal
Motor
Gear Box
-
e
+
Input Signal
Output
Signal
5.3 Dip Switch Setting (SW1)
The Dip Switch SW1 is a combination of 8 switches and equally divided in two rows. It is
utilized to select the input signal type as well as the output and fail
positioning type,when the signal input fails. The sliders can be
placed at either ON (upper) or OFF (lower) state position. Factory
settings are switches 1, 4, 8 at ON state and switches 2, 3, 5, 6, 7
at OFF state.
Please follow the steps below if an adjustment of these settings are required. Please
restart the actuator after adjusting.
1
2
3
4
5
6
7
8
Factory Setting
ON OFF OFF
ON OFF OFF OFF
ON
4
-
20 mA input
ON
OFF
1
-
5V input
OFF
OFF
2
-
10V input
OFF
ON
4
-
20 mA output
OFF
ON
OFF
2
-
10V output
ON
OFF
ON
Input 20 mA / 5V / 10V to operate valve to fully
-
open position
OFF
Input 20 mA / 5V / 10V to operate valve to fully
-
closed position
ON
When signal
input failed, driving valve to fully
-
open (when S6 sets at “ ON”).
OFF
ON
When signal input failed, driving valve to fully
-
closed (when S6 sets at “ ON”).
ON
OFF
When signal input failed, driving valve to fully
-
closed (when S6 sets at “ OFF”).
OFF
ON
When signal input failed, driving valve to fully
-
open (when S6 sets at “ OFF”).
ON
OFF
When signal input failed, valve stays at the last position.
ON
ON
This manual suits for next models
3
Table of contents
Other Econ Controllers manuals
Popular Controllers manuals by other brands
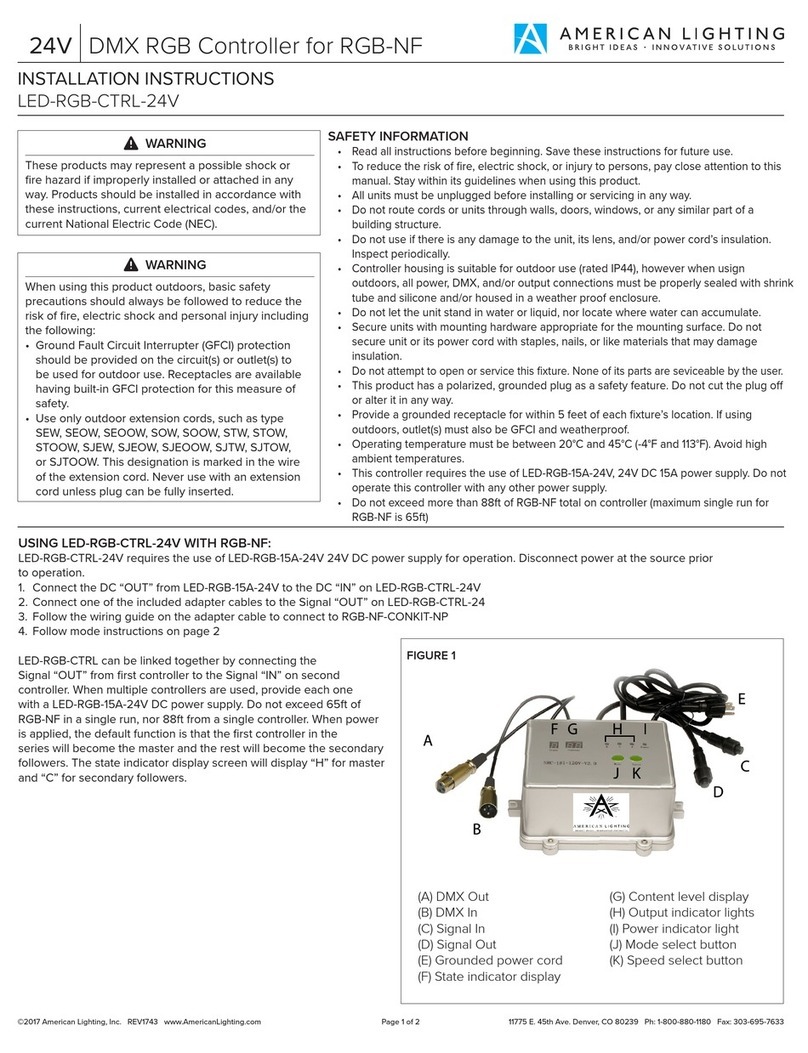
American Lighting
American Lighting LED-RGB-CTRL-24V installation instructions
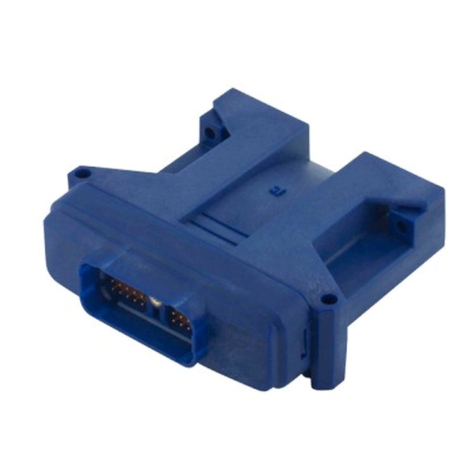
Danfoss
Danfoss PLUS+1 SC0XX-1 Series technical information
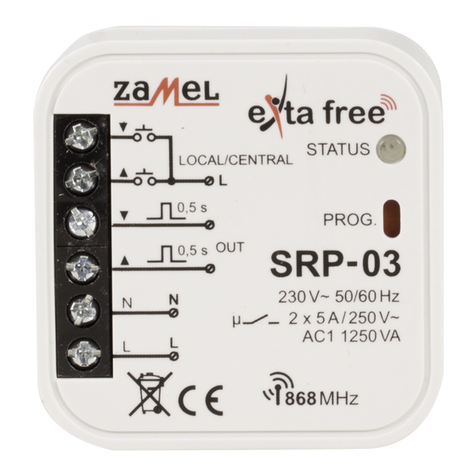
Zamel
Zamel SRP-03 Manual instruction
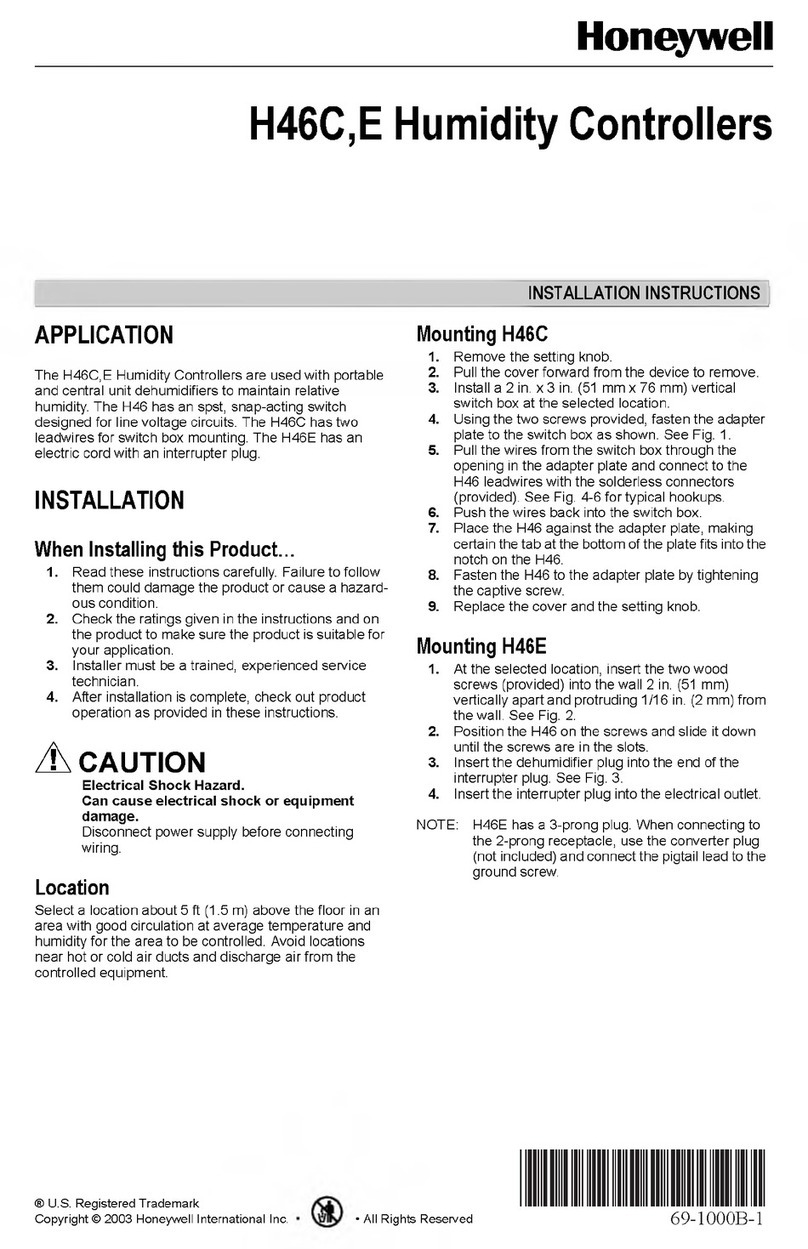
Honeywell
Honeywell H46E installation instructions
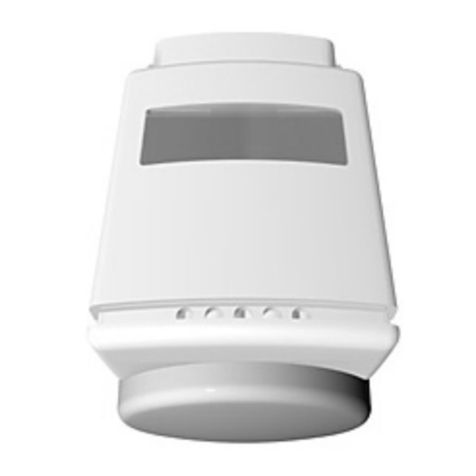
Honeywell
Honeywell HR 80 installation guide
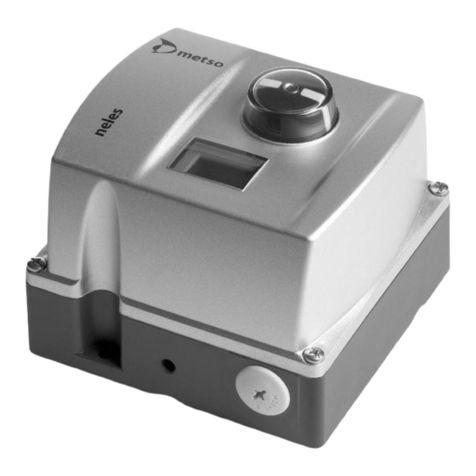
Metso
Metso neles ND9000H Installation, maintenance and operation instructions