EDI CMU-212 User manual

THIS MANUAL CONTAINS TECHNICAL INFORMATION FOR
THE CMU-212 AND CMUip-212 SERIES ITS CABINET MONITOR UNIT.
Firmware Version 2.5 (vXX25)
REVISION: JUNE 2019
pn 888-0212-001
CMU(ip)-212
ITS Cabinet Monitor Unit
Operations Manual
- NOTE -
EDI ECCOM SOFTWARE MUST BE UPDATED TO VERSION 4.2 OR HIGHER.
EDI MONITORKEY SOFTWARE MUST BE UPDATED TO VERSION 2.4 OR HIGHER.
EDI SOFTWARE IS AVAILABLE AT WWW.EDITRAFFIC.COM

THE CMU-212 SERIES CABINET MONITOR UNIT IS DESIGNED AND
MANUFACTURED IN THE USA BY EBERLE DESIGN INC.
PHOENIX, ARIZONA.
EDI IS CERTIFIED TO ISO 9001:2015 QUALITY SYSTEMS STANDARDS.
INFORMATION CONTAINED HEREIN IS PROPRIETARY TECHNICAL INFORMATION
OF EBERLE DESIGN INC. PUBLICATION, REPRODUCTION OR USE IN WHOLE OR
PART IS NOT PERMITTED EXCEPT UNDER TERMS AGREED UPON IN WRITING.
©COPYRIGHT 2019 EDI
U.S. Pat. No. 7,246,037
Canadian Patent No. 2,574,101
U.S. Pat. No. 9,460,620
U.S. Pat. No. 10,262,531
MAINTENANCE NOTE
THIS EBERLE DESIGN INC. CABINET MONITOR UNIT HAS BEEN
CAREFULLY INSPECTED AND TESTED TO ENSURE PROPER OPERATION.
IT IS RECOMMENDED THAT THE CABINET MONITOR UNIT BE TESTED AT
LEAST ANNUALLY TO ENSURE PROPER OPERATION AND COMPLIANCE
WITH FACTORY SPECIFICATIONS.

Table of Contents
Section 1 GENERAL ......................................................................................................... 1
1.1 Overview ................................................................................................................ 1
1.2 Channel Configuration............................................................................................ 1
1.3 Auxiliary Monitor Unit ............................................................................................. 1
1.4 CMU-212 Programming.......................................................................................... 2
1.5 Detailed CMU Status.............................................................................................. 2
1.5.1 ECcom Software Interface ............................................................................ 2
1.5.2 Auxiliary Display Unit .................................................................................... 2
1.6 Serial Bus #1.......................................................................................................... 3
1.6.1 Serial Bus #1 Message Types....................................................................... 3
1.7 Serial Bus #3.......................................................................................................... 3
1.7.1 Serial Bus #3 Message Types....................................................................... 3
1.8 Failed State Action (LFSA, LFSA-R, NFSA) ........................................................... 3
1.8.1 Exit From FSA............................................................................................... 4
Section 2 MONITOR FUNCTIONS .................................................................................... 5
2.1 Cabinet Power Supply Monitor ............................................................................... 5
2.2 Conflicting Channels Monitor.................................................................................. 5
2.3 Serial Bus Monitor.................................................................................................. 5
2.3.1 Serial Bus #1 Error........................................................................................ 5
2.3.2 Serial Bus #3 Error........................................................................................ 5
2.4 Type 62 FSA Message........................................................................................... 6
2.5 Lack of Signal Inputs Monitor ................................................................................. 6
2.6 Multiple Input Monitor ............................................................................................. 6
2.7 Yellow Clearance Monitor....................................................................................... 6
2.8 Yellow Plus Red Clearance Monitor ....................................................................... 7
2.9 Local Flash Status.................................................................................................. 7
2.9.1 Local Flash Status Recovery......................................................................... 7
2.10 Circuit Breaker Trip Status ................................................................................... 7
2.11 Flasher Unit Output Failed Alarm.......................................................................... 7
2.12 CMU Power Failure .............................................................................................. 7
2.12.1 AC+ RAW Level Sense ............................................................................... 8
2.12.2 Power Interrupt ........................................................................................... 8
2.12.3 Power Recovery.......................................................................................... 8
2.12.4 Power Up .................................................................................................... 8
2.12.5 Minimum Flash Interval ............................................................................... 8
2.13 Field Output Check............................................................................................... 8
2.13.1 Field Check Mode ....................................................................................... 8
2.13.2 Field Check Status ...................................................................................... 9
2.14 Diagnostic Error ................................................................................................... 9
2.14.1 Ram Memory Diagnostic............................................................................. 9
2.14.2 Nonvolatile Memory Diagnostic ................................................................... 9
2.14.3 Datakey Memory Diagnostic........................................................................ 9
2.14.4 Internal MPU Monitor .................................................................................10
2.15 Recurrent Pulse Detection...................................................................................10
2.15.1 Recurrent Pulse Detection Disable.............................................................10
2.16 Flashing Yellow Arrow (FYA) Protected-Permissive Monitoring ...........................11
2.16.1 FYA Configuration......................................................................................11
2.16.1.1 Protected Turn Channel ....................................................................11
2.16.1.2 Permissive Turn Channel..................................................................11
2.16.1.3 Opposing Through Channel ..............................................................11
2.16.2 Configuring the CMU-212 Fault Parameters For FYA.................................11

2.16.2.1 Conflict .............................................................................................12
2.16.2.2 Red Fail ............................................................................................12
2.16.2.3 Dual Indication ..................................................................................13
2.16.2.4 Minimum Yellow Clearance...............................................................13
2.16.2.5 Yellow Plus Red Clearance...............................................................13
2.16.3 Red and Yellow Input Enable .....................................................................13
2.16.4 Flash Rate Detection..................................................................................13
2.16.5 FYA Yellow Trap Conflict Detection............................................................14
Section 3 INPUT SIGNALS ..............................................................................................15
3.1 Field Signal Inputs.................................................................................................15
3.2 Load Switch Current..............................................................................................15
3.3 PDA Control Signal Inputs.....................................................................................15
3.3.1 Local Flash Status .......................................................................................15
3.3.2 Main Contactor (MC) Coil Status..................................................................15
3.3.3 Main Contactor (MC) Secondary Status .......................................................15
3.3.4 FTR Coil Drive Status ..................................................................................16
3.3.5 Circuit Breaker (CB) Trip Status ...................................................................16
3.3.6 Front / Rear Door Switch..............................................................................16
3.4 Monitor Interlock....................................................................................................16
3.5 External Test Reset input ......................................................................................16
3.6 Serial Bus #1 Address Inputs ................................................................................16
3.7 Serial Bus #1 Disable input ...................................................................................17
3.8 PDA Temperature .................................................................................................17
Section 4 FRONT PANEL DESCRIPTION .......................................................................18
4.1 Indicators ..............................................................................................................18
4.1.1 Power Indicator ............................................................................................18
4.1.2 24VDC FAIL Indicator ..................................................................................18
4.1.3 12VDC FAIL Indicator ..................................................................................18
4.1.4 CONFLICT Indicator ....................................................................................18
4.1.5 LACK OF SIGNAL Indicator .........................................................................18
4.1.6 MULTIPLE Indicator.....................................................................................18
4.1.7 CU / LOCAL FLASH Indicator ......................................................................18
4.1.8 CLEARANCE Indicator ................................................................................18
4.1.9 FIELD CHECK Indicator...............................................................................18
4.1.10 SB #1 ERROR Indicator.............................................................................19
4.1.11 SB #3 ERROR Indicator.............................................................................19
4.1.12 DIAGNOSTIC Indicator ..............................................................................19
4.1.13 SB #1 RX Indicator.....................................................................................19
4.1.14 SB #3 RX Indicator.....................................................................................19
4.2 Terminal Port.........................................................................................................19
4.3 Reset Button .........................................................................................................19
4.4 Datakey.................................................................................................................19
Section 5 SPECIFICATIONS............................................................................................20
5.1 Electrical ...............................................................................................................20
5.2 Timing ...................................................................................................................20
5.3 Mechanical............................................................................................................21
5.4 Environmental .......................................................................................................21
Section 6 CONNECTOR ASSIGNMENTS........................................................................22
6.1 Main DIN Connector..............................................................................................22
6.2 EIA-232 Connector................................................................................................22
6.3 CMUip-212 Ethernet LAN Port ..............................................................................23
6.3.1 Ethernet LAN Cable .....................................................................................23

CMU-212 Cabinet Monitor Unit
Operations Manual
Eberle Design Inc. Page 1
Section 1
GENERAL
1.1 OVERVIEW
The model CMU-212 Cabinet Monitor Unit (CMU-212) is the principle part of the ITS Traffic
Control Cabinet Monitoring System. It is resident in the Power Distribution Assembly and
communicates with an Auxiliary Monitor Unit (AMU) located in each Output Assembly via
Serial Bus #3. The role of the CMU-212 is to query various cabinet conditions and, if the
application requires action, the CMU-212 will transfer control from the Advanced Traffic
Controller (ATC) to a flashing control mode. Applications include the detection of, and
response to, improper and conflicting signals and improper operating voltages in a cabinet
assembly caused by malfunctions of the (ATC), load switches, or miss wiring of the cabinet.
The communications between the ATC and the CMU-212 via Serial Bus #1 plays an
integral role in ensuring safe and proper operation of the cabinet equipment as well as
providing important diagnostic functions used for trouble shooting malfunctioning
equipment.
The Eberle Design CMU-212 meets with or exceeds all specifications outlined the
ASHTO/ITE/NEMA Intelligent Transportation System (ITS) Standard Specification for
Roadside Cabinets Version 01.02.17b document.
1.2 CHANNEL CONFIGURATION
The CMU-212 can be configured to monitor up to 28 physical load switch channels of three
inputs per channel. An additional four virtual channels can be programmed to provide a
total of 32 logical channels. Each channel is comprised of a Red / Don’t Walk input, a
Yellow input, and a Green / Walk input.
1.3 AUXILIARY MONITOR UNIT
The Auxiliary Monitor Unit (AMU-214) provides the CMU-212 with voltage and current
measurements from each installed Output Assembly. The AMU-214 has the capability to
measure and report field terminal voltages for fourteen channels of three inputs per channel
and load currents for fourteen channels. The AMU-214 is also compatible with a six
position Output Assembly. The AMU is configured by its output assembly address. This
address is set by a jumper plug located on the rear of the output assembly. For further
information concerning the AMU-214, see the Eberle Design AMU-214 Operations
Manual (pn 888-0214-001).
The AMU-214 address assignment specifies the physical arrangement of the Output
Assemblies. This defines the number of contiguous channels that the CMU-212 is
monitoring. An AMU-214 assigned as a 14 channel unit must be addressed as AMU #1
with AMU #2 reserved, or as AMU #3 with AMU #4 reserved. The following table shows the
ten possible cabinet configurations:

CMU-212 Cabinet Monitor Unit
Operations Manual
Eberle Design Inc. Page 2
AMU #1
AMU #2
AMU #3
AMU #4
Monitored Channels
14
reserved
none
None
1 thru 14
14
reserved
14
reserved
1 thru 28
14
reserved
6
None
1 thru 20
14
reserved
6
6
1 thru 26
6
none
none
None
1 thru 6
6
6
none
None
1 thru 12
6
6
6
None
1 thru 18
6
6
6
6
1 thru 24
6
none
14
reserved
1 thru 20
6
6
14
reserved
1 thru 26
The ATC must verify that all output assemblies being driven by a Serial Interface Unit
(SIU) are being monitored by an AMU-214 and that the AMU-214 is enabled by the
programming in the CMU-212. Failure to provide this check may result in
unmonitored load switch outputs. This could occur as a result of improper configuration
of the cabinet, improper address assignment for one or more AMU-214 units, improper
address assignment for one or more SIU units, or improper programming of the ATC.
1.4 CMU-212 PROGRAMMING
The CMU-212 is individually configured using a removable nonvolatile memory device
called a Datakeytm (Datakey is a registered trademark of Datakey Electronics, Inc.). The
Datakey replaces the mechanical jumper or diode based program card used in
conventional signal monitors and provides an electronic method of programming the CMU-
212. The Datakey contains a nonvolatile prom device that is read by the CMU-212. The
Datakey itself is programmed by a separate programming device using a Personal
Computer program such as the Eberle Design MonitorKey product. See the Eberle Design
MonitorKey Operations Manual (pn 888-1212-001) for further details.
The Datakey is interoperable with any CMU-212 meeting the requirements of the
ASHTO/ITE/NEMA Intelligent Transportation System (ITS) Standard Specification for
Roadside Cabinets Version 01.02.17b.
1.5 DETAILED CMU STATUS
1.5.1 ECCOM SOFTWARE INTERFACE
The front panel display of the CMU-212 provides limited operational status. Detailed status
is obtained through the front panel EIA-232 port (CMU-212) or optional Ethernet port
(CMUip-212) using Eberle Design ECcom Signal Monitor Communications software
running on a personal computer. The ECcom software provides access to real time monitor
data such as current field signal status, field terminal voltages, cabinet control voltages,
channel load current status, temperature, and fault status. Historical event logs and signal
sequence logs are also provided. See the EDI ECcom Operation Manual (pn 888-1000-
001) for further details. The ECcom Signal Monitor Communications software can be
obtained from the Eberle Design web site at www.EDItraffic.com.
1.5.2 AUXILIARY DISPLAY UNIT
The Eberle Design Auxiliary Display Unit (ADU) is a display module that provides an
enhanced user interface for the ITS Cabinet Monitor Unit (CMU-212) system. The Auxiliary
Display Unit is intended to mount into a 1U space of the 19 inch rack of an ITS Cabinet.
The ADU communicates with the CMU-212 via Serial Bus #3. See the ADU Operation
Manual (pn 888-0217-001) for details.

CMU-212 Cabinet Monitor Unit
Operations Manual
Eberle Design Inc. Page 3
1.6 SERIAL BUS #1
Serial Bus #1 provides a communication path between the CMU-212 to the ATC. The
communications between the ATC and the CMU-212 plays an integral role in ensuring safe
and proper operation of the cabinet equipment as well as providing important diagnostic
functions used for trouble shooting malfunctioning equipment. Standardized
communications can be broken into three categories; real time and latched fault status,
configuration verification, and malfunction detection and diagnosis.
Messages are defined that allow the ATC and the CMU-212 to perform redundant checks
on each other. The ATC has access to all CMU-212 information including field signal input
status, permissive programming, and fault status. This gives the ATC the capability to
provide a backup monitoring function and make enhanced event logging, remote
intersection monitoring, and remote diagnostics feasible. Similarly, the CMU-212 receives
information from the ATC that corresponds to the output commands to the load switches.
This data allows the CMU-212 to better respond to and diagnose fault situations.
1.6.1 SERIAL BUS #1 MESSAGE TYPES
The CMU-212 is compatible with the following message types:
Type 60 Module Identification Command / Type 188 Module Identification Response
Type 61 Load Switch Drivers Command / Type 189 CMU Status Response
Type 62 Set FSA Command / Type 190 FSA Response
Type 65 Get CMU Configuration Command / Type 193 CMU Configuration Response
Type 66 Time and Date Broadcast Command
Type 67 Load Switch Drivers Command / Type 195 CMU Short Status Response
1.7 SERIAL BUS #3
Serial Bus #3 is used to transfer data from a maximum of four AMU-214 units to the CMU-
212. The CMU-212 will poll each enabled AMU-214 for its voltage and load current data
every 20 milliseconds. The CMU-212 then maps the retrieved data to the proper logical
channel and evaluates the state of the field signals for fault conditions. The CMU-212 is
compatible with AMU-214 units configured for 6-channel operation or 14-channel operation.
1.7.1 SERIAL BUS #3 MESSAGE TYPES
The CMU-212 is compatible with the following message types:
Type 1 AMU 6 Status Command / Type 129 AMU 6 Status Response
Type 2 AMU 14 Status Command / Type 130 AMU 14 Status Response
Type 128 Negative Acknowledge Response
1.8 FAILED STATE ACTION (LFSA, LFSA-R, NFSA)
When triggered by the detection of a fault condition that exists longer than the minimum
defined period, the CMU-212 will enter the Failed State Action (fault) mode causing the
OUTPUT relay to de-energize and the contacts on the OUTPUT NO pins to open. The
cabinet assembly should be wired such that the opening of the OUTPUT NO relay contacts

CMU-212 Cabinet Monitor Unit
Operations Manual
Eberle Design Inc. Page 4
will cause an automatic switching of the field signal outputs from normal operation to
flashing operation.
Only Unit Reset from the Reset Button or EXTERNAL RESET TEST input will reset the
CMU-212 from a LATCHED FAILED STATE ACTION (LFSA). Only a Unit Reset from the
Reset Button or EXTERNAL RESET TEST input or a CMU-212 Power Fail will reset a
LATCHED RESETTABLE FAILED STATE ACTION (LFSA-R).
A NONLATCHED FAILED STATE ACTION (NFSA) will be reset if the fault conditions
causing the NFSA have been removed. An NFSA will last for the programmed Minimum
Flash time at a minimum.
Only one LFSA, LFSA-R or NFSA fault state will be set at any time.
1.8.1 EXIT FROM FSA
Prior to the CMU-212 transferring the OUTPUT NO contacts from the FSA state to the No
Fault state, a transition period of 500 milliseconds will occur. During the transition period
the OUTPUT NO contacts will be in the FSA state and the CMU-212 will set the Start-Up
Flash Call bit in the Type 189 Frame to 1.At all other times the Start-Up Flash Call bit of
the Type 189 Frame will be set to 0. This provides an early indication to the ATC that exit
from the FSA state is occurring and the start-up phases should be set.

CMU-212 Cabinet Monitor Unit
Operations Manual
Eberle Design Inc. Page 5
Section 2
MONITOR FUNCTIONS
2.1 CABINET POWER SUPPLY MONITOR
The CMU-212 will sense the Cabinet +24VDC and +12VDC power supply sources. The
CMU-212 will also sense the Cabinet +24VDC state in each Output Assembly as reported
by each AMU. Voltages equal to or greater than +22 Vdc and +11 Vdc respectively will not
cause a LFSA. Voltages at or less than +18 Vdc and +9 Vdc for 500ms or longer will cause
a LFSA. If the sensed voltage is less than +22 Vdc or +11 VDC for 200 ms or less, the
CMU-212 will not cause a LFSA. All other timing or voltage conditions may or may not
cause LFSA. A +24VDC failure or +12VDC failure during the programmed Minimum Flash
time or during a CMU-212 Power Failure will not cause a LFSA. The CMU-212 will report
the value of the +24 VDC and +12 VDC power supply sources in the Type 189 response
frame.
There is programming in the Datakey to disable +12 VDC power supply monitoring.
2.2 CONFLICTING CHANNELS MONITOR
For purpose of conflict determination, an active signal on either of the Green/Walk or
Yellow inputs associated with any of the 32 channels will be considered as that channel
being active. The Datakey will contain the permissive channel pair programming.
When any conflicting channels are detected as concurrently active for less than 200
milliseconds the CMU-212 will not cause a LFSA. When any conflicting channels are
detected as concurrently active for 500 milliseconds or more, the CMU-212 will cause a
LFSA. When any conflicting channels are detected as concurrently active for more than
200 milliseconds but less than 500 milliseconds, the CMU-212 may or may not cause a
LFSA.
2.3 SERIAL BUS MONITOR
The CMU-212 communicates with both Serial Bus (SB) #1 and #3. In SB #1 the CMU-212
is a Secondary device, polled by the ATC Primary device. On SB #1, the CMU-212 will
respond to the Serial Bus #1 Address defined by the ADDRESS 0 and ADDRESS 1 pins.
On SB #3 the CMU-212 is the Primary device, polling each AMU-214 Secondary device.
2.3.1 SERIAL BUS #1 ERROR
The CMU-212 will cause a FSA when a Type 61 or Type 67 Frame has not been received
from the ATC for greater than 1000 milliseconds. The first and second failures in a 24-hour
period will be a NFSA. The third failure in a 24-hour period will be a LFSA-R. If a CMU-212
Power Fail resets the LFSA-R, the SB #1 failure count will be reset to two, such that the
next SB #1 timeout results in a LFSA-R.
A SB #1 timeout failure during the programmed Minimum Flash time or during a CMU-212
Power Failure will not cause a FSA. The SB #1 Timeout function will be disabled if the SB
#1 DISABLE input is at a True (Low) state
2.3.2 SERIAL BUS #3 ERROR
The CMU-212 will cause a FSA when a Type 129 or Type 130 Frame has not been
received from each AMU for greater than 300 milliseconds. The first and second failures in
a 24-hour period will be a NFSA. The third failure in a 24-hour period will be a LFSA-R. If a
CMU-212 Power Fail resets the LFSA-R, the SB #3 timeout count will be reset to two, such
that the next SB #3 timeout results in a LFSA-R.
A SB #3 timeout failure during the programmed Minimum Flash time or during a CMU-212
Power Failure will not cause a FSA.

CMU-212 Cabinet Monitor Unit
Operations Manual
Eberle Design Inc. Page 6
2.4 TYPE 62 FSA MESSAGE
If the “N” bit is set in a Type 62 message, the CMU-212 will react by causing a NFSA. The
NFSA will remain until the receipt of a Message 62 with the “N” bit cleared or until the
CMU-212 is reset by a Unit Reset or CMU-212 Power Fail. The NFSA will last for the
programmed Minimum Flash time at a minimum.
If the “L” bit is set in a Type 62 message, the CMU-212 will react by causing a LFSA.
2.5 LACK OF SIGNAL INPUTS MONITOR
The CMU-212 will detect the absence of a required signal voltage on all the inputs of a
channel OR the absence of any required channel load current. For voltage purposes a
required signal on the Green OR Yellow OR Red inputs associated with a channel will be
considered as that channel being Voltage Active. For load current purposes a total channel
load current above the programmed threshold for a channel will be considered as that
channel being Current Active. When a channel is not Voltage Active OR Current Active for
less than 700 milliseconds, the CMU-212 will not cause a LFSA. When a channel is not
Voltage Active OR Current Active for greater than 1000 milliseconds, the CMU-212 will
cause a LFSA. When a channel is not Voltage Active OR Current Active for more than 700
milliseconds but less than 1000 milliseconds, the CMU-212 may or may not cause a LFSA.
The Current Sense Unit (CSU) monitor function is hardwired to the maximum of 28 physical
channels, thus Virtual Channels do not have CSU monitoring capability. The CSU monitor
function must be disabled for any physical channel that has an input remapped to a Virtual
Channel.
Lack of Signal Input monitoring will be disabled for all channels when the MC COIL
STATUS input is not active. There is programming in the Datakey to disable Lack of Signal
Input monitoring on a per channel basis.
Lack of Signal Input monitoring will also be disabled for any channel which has the DARK
CHANNEL MAP bit set to "1" in the Datakey programming for the DARK CHANNEL MAP
addressed by the DARK CHANNEL MAP SELECT bits in a Type 61 message.
2.6 MULTIPLE INPUT MONITOR
The CMU-212 will detect the presence of an active signal on two or more inputs of a
channel. When the presence of an active signal on two or more inputs of a channel is
detected for less than 200 milliseconds, the CMU-212 will not cause a LFSA. When the
presence of an active signal on two or more inputs to a channel is detected for 450
milliseconds or more, the CMU-212 will cause a LFSA. When the presence of an active
signal on two or more inputs to a channel is detected for more than 200 milliseconds but
less than 450 milliseconds, the CMU-212 may or may not cause a LFSA.
Multiple Input monitoring may anticipate and prevent a possible conflicting signal display in
the intersection in the event that a proceed signal on the current phase hangs up and is
constantly detected as active. An open or no load condition (i.e., burned-out bulb) may be
also detected as an active signal depending on the output impedance characteristics of the
load switch (i.e. load switch leakage current), and may cause a Multiple Input Fault.
Multiple Input monitoring will be disabled when the MC COIL STATUS input is not active.
There is programming in the Datakey to disable Multiple Indication monitoring on a color
combination basis (G+Y, Y+R, G+R) for each channel.
2.7 YELLOW CLEARANCE MONITOR
The CMU-212 will verify that the Yellow Change interval is at least 2.7 +/-0.1 seconds. The
Yellow Change interval consists of the duration of time in which the Yellow field signal input
is active in a sequence from Green to Yellow to Red. When the minimum Yellow Change

CMU-212 Cabinet Monitor Unit
Operations Manual
Eberle Design Inc. Page 7
interval is not satisfied, the CMU-212 will cause a LFSA. The CMU-212 will report a
Skipped Yellow Clearance when the Yellow Change interval is less than 100 milliseconds.
The CMU-212 will report a Short Yellow Clearance when the Yellow Change interval is less
than 2.7 +/- 0.1 seconds and greater than 100 milliseconds.
Minimum Yellow Change interval monitoring will be disabled when the MC COIL STATUS
input is not active. There is programming in the Datakey to disable Minimum Yellow
Change interval monitoring on a per channel basis.
2.8 YELLOW PLUS RED CLEARANCE MONITOR
The CMU-212 will verify that the Yellow Change plus Red Clearance interval between the
end of an active Green/Walk signal and the beginning of the next conflicting Green/Walk
signal is at least 2.7 +/-0.1 seconds. When the minimum Yellow Change plus Red
Clearance interval is not satisfied, the CMU-212 will cause a LFSA.
Minimum Yellow Change plus Red Clearance monitoring will be disabled when the MC
COIL STATUS input is not active. There is programming in the Datakey to disable Minimum
Yellow Change plus Red Clearance interval monitoring on a per channel basis.
2.9 LOCAL FLASH STATUS
The CMU-212 will monitor the LF STATUS input. This input is used to indicate to the CMU-
212 that the cabinet should be placed into NFSA as a result of the AUTO/FLASH switch
being transferred to the FLASH postion. When this signal is sensed as not active for
greater than 500 milliseconds the CMU-212 will cause a NFSA. When this signal is sensed
as not active for less than 200 milliseconds the CMU-212 will not cause a NFSA.
2.9.1 LOCAL FLASH STATUS RECOVERY
Recovery from Local Flash Status NFSA will occur when this signal is sensed as active for
greater than 500 milliseconds. When this signal is sensed as active for less than 200
milliseconds the CMU-212 will not cause recovery from Local Flash Status NFSA.
2.10 CIRCUIT BREAKER TRIP STATUS
The CMU-212 will monitor the CB TRIP STATUS input. When one or more circuit breakers
have tripped this input will go to the not-active state. When this signal is sensed as not
active for greater than 500 milliseconds the CMU-212 will cause a LFSA. When this signal
is sensed as not active for less than 200 milliseconds the CMU-212 will not cause a LFSA.
2.11 FLASHER UNIT OUTPUT FAILED ALARM
The CMU-212 will monitor the FLASHER 1-1, FLASHER 1-2, FLASHER 2-1, FLASHER 2-
2 voltage states reported by each AMU-214. The AMU-214 reports the flasher state at the
output assembly. Thus a failed state may indicate a malfunction of the connector system or
flash voltage bus or flasher unit.
When a transition from the inactive state to the active state or a transition from the active
state to the inactive state is absent for greater than 2500 milliseconds, the CMU-212 will set
a status bit in the Type 189 frame. This alarm condition will not cause a FSA. It should
cause the appropriate response in the ATC. This status is non-latching such that once a
status bit has been set, the sensing of five valid transitions of the input will clear the status
bit.
2.12 CMU POWER FAILURE
The CMU-212 will monitor the AC+ RAW input and the NRESET and POWERDOWN
cabinet control inputs to determine a CMU Power Failure response. The POWERDOWN
signal in the False (low) state indicates loss of AC+ RAW in the ATC. A CMU Power Failure

CMU-212 Cabinet Monitor Unit
Operations Manual
Eberle Design Inc. Page 8
will be recognized when both the POWERDOWN and NRESET signals are False (low) for
greater than 100 ms or the AC+ RAW voltage is less than 82 +/- 2 Vrms.
The 24VDC Monitor function (section 2.1) will be disabled while the POWERDOWN signal
is in the False state. The 24VDC FAIL indicator will flash at a 2Hz rate (section 4.1.2).
2.12.1 AC+ RAW LEVEL SENSE
The CMU-212 will monitor the AC+ RAW input and AC+ RAW inputs reported by each
AMU-214. When any AC+ RAW voltage is less than the AC Line Dropout voltage (section
5.1) for greater than AC Line Level Sense timing (section 5.2) the CMU-212 will cause a
NFSA. Once NFSA has been set, the POWERDOWN and NRESET signals will not be
monitored until all AC+ RAW voltages have exceeded the AC Line Restore voltage (section
5.1).
2.12.2 POWER INTERRUPT
The CMU-212 will disable monitoring of the +12VDC and +24VDC power supply inputs
when either the POWERDOWN or NRESET input is False (low). When the POWERDOWN
and NRESET signals are both False (low) the CMU-212 will cause a NFSA.
2.12.3 POWER RECOVERY
When the POWERDOWN input is True (high) and the NRESET signal goes from False
(low) to True (high) the CMU-212 will begin timing the programmed Minimum Flash
Interval. During the Minimum Flash Interval the CMU-212 will be in NFSA.
2.12.4 POWER UP
Following initial application of AC+ RAW voltage the CMU-212 will maintain a NFSA until
the POWERDOWN input is True (high) and the NRESET signal goes from False (low) to
True (high). The CMU-212 will then begin timing the programmed Minimum Flash Interval.
During the Minimum Flash Interval the CMU will be in NFSA.
2.12.5 MINIMUM FLASH INTERVAL
During the Minimum Flash Interval the CMU-212 will be in NFSA. The Minimum Flash
Interval will be programmed in the Datakey between the limits of 6 seconds to 16 seconds
with an incremental adjustment of 1 second. The CMU-212 will not set a FSA during the
Minimum Flash Interval.
2.13 FIELD OUTPUT CHECK
The Field Output Check is a continuous verification that the field signal output states set by
the ATC are properly driven to the signal loads and correctly sensed by the AMU-214 and
CMU-212. It is an enhanced function made possible by the Serial Bus #1 communications
between the ATC and CMU-212. The CMU-212 will receive a Type 61 message from the
ATC that contains an image of the controller output commands to the load switches. When
a fault condition triggers the CMU-212, the Type 61 message information received while
the fault condition was being timed will be used by the CMU-212 to determine whether the
sensed field signal input status corresponded to the ATC output commands. This
diagnostic information may then be used to isolate whether the fault condition was caused
by an ATC malfunction or a failure in the load switch and/or field wiring.
The Field Output Check function is enabled for each channel input individually and provides
two modes of operation, Field Check Mode and Field Check Status.
2.13.1 FIELD CHECK MODE
The CMU-212 will compare the active states of the field signals with the states reported by
the ATC in the Type 61 frame. When a mismatch is detected for less than 700 milliseconds

CMU-212 Cabinet Monitor Unit
Operations Manual
Eberle Design Inc. Page 9
the CMU-212 will not cause a LFSA. When a mismatch is detected for 1000 milliseconds
or more, the CMU-212 will cause a LFSA. When a mismatch is detected for more than 700
milliseconds but less than 1000 milliseconds, the CMU-212 may or may not cause a LFSA.
The Field Check Mode is typically caused by a miss-wired or improperly configured cabinet.
When the Field Check Mode is detected the FIELD CHECK front panel indicator will be
illuminated solid.
Field Output Check monitoring will be disabled when the MC COIL STATUS input is not
active. There is programming in the Datakey to disable Field Output Check monitoring on a
channel input basis.
2.13.2 FIELD CHECK STATUS
The CMU-212 will compare the active states of the field signals with the states reported by
the CU in the Type 61 frame. When a mismatch is detected while a Conflict, Lack of Signal,
or Multiple fault is timing, Field Check Status will be reported with the fault to indicate the
faulty channel(s) and color(s).
If a Conflict, Lack of Signal, or Multiple fault has triggered the CMU-212 to the fault mode
and the CMU-212 indicates that there is no Field Check Status, the ATC or ATC
programming is the most likely cause. The lack of Field Check Status indicates the ATC
drove the signals to an improper state. If a Conflict, Lack of Signal, or Multiple fault has
triggered the CMU-212 to the fault mode and the CMU-212 indicates that there is Field
Check Status, then cause of the malfunction can be isolated to the SIU, load switch, field
wiring, or signal load.
When Field Check Status is detected the FIELD CHECK front panel indicator will be flash
at a 2Hz rate.
Field Output Check monitoring will be disabled when the MC COIL STATUS input is not
active. There is programming in the Datakey to disable Field Output Check monitoring on a
channel input basis.
2.14 DIAGNOSTIC ERROR
The CMU-212 is provided with a resident series of self-check diagnostic capabilities. When
a Diagnostic fault is detected, a LFSA-R will be set and the DIAGNOSTIC indicator
illuminated. Should a Diagnostic error occur, other fault indicators that may be concurrently
displayed with the DIAGNOSTIC indicator may not be valid due to the nature of these
hardware and/or firmware failures.
2.14.1 RAM MEMORY DIAGNOSTIC
This test will verify that all RAM elements are operating correctly at power-up or following a
Unit Reset.
2.14.2 NONVOLATILE MEMORY DIAGNOSTIC
This test will verify that the nonvolatile flash ROM and event log eeprom contain the proper
data. The routine will perform a check on each ROM device and make a comparison with a
check value. This test is performed at power-up and at a minimum rate of 1024 bytes per
second during operation
2.14.3 DATAKEY MEMORY DIAGNOSTIC
This test will verify whether the non-volatile Datakey contains valid data. The routine will
perform a check on each nonvolatile memory element at power-up and whenever read and
make a comparison with a 16 bit Frame Check Sequence (FCS) procedure defined in
clause 4.6.2 of ISO/IEC 3309. Invalid data may result from corrupted Datakey contents, an

CMU-212 Cabinet Monitor Unit
Operations Manual
Eberle Design Inc. Page 10
invalid FCS calculation, invalid parameter values, or a Datakey Protocol Version
incompatibility.
The Datakey not present will cause a LFSA and illuminate the DIAGNOSTIC indicator if the
DOOR SWITCH FRONT input is sensed as not active (door closed). The DIAGNOSTIC
indicator will flash at a rate of 2Hz if the Datakey is not present when the DOOR SWITCH
FRONT input is sensed as active (door open).
2.14.4 INTERNAL MPU MONITOR
The CMU-212 will monitor the operation of its microprocessor with an independent circuit.
At a minimum, the monitoring circuit will receive logic state transitions at least once every
50 milliseconds from the microprocessor. When the logic state transition is not received for
500 milliseconds the monitor circuit will force a LFSA-R and illuminate the DIAGNOSTIC
indicator.
2.15 RECURRENT PULSE DETECTION
This error detection function supplements the normal Conflict, Multiple, and Lack of Signal
monitoring algorithms for sensing faults that are intermittent or pulsing in nature. The RMS
signal detection algorithm is designed to filter out short term transients commonly found on
the electrical service and provide noise immunity against false signal detections. The
Recurrent Pulse detection function is designed to respond to fault conditions that are
intermittent in nature and do not meet the continuous timing requirements of the normal
detection algorithms, yet may still produce improper signal displays. These input conditions
are differentiated by their longer time constant and fault response times.
The figure below shows a simple example of a recurrent Conflict fault. Channel 2 Green is
detected active due to a malfunction of the load switch that caused the output to “flicker” On
for 100 ms approximately every 200 ms. Because normal Conflict detection requires a
continuous fault of at least 350 ms duration, this event could go undetected. The Recurrent
Pulse detection algorithm will combine these pulses into one event and trigger a Conflict
fault once the longer recurrent timing threshold is exceeded.
When triggered by a recurrent fault condition, the Signal Monitor will enter the fault mode,
transfer the Output relay contacts to the Fault position, and illuminate the appropriate
CONFLICT, MULTIPLE, or LACK OF SIGNAL indicator. The unit will remain in the fault
mode until reset by the Reset button or the External Reset input. Fault response times will
vary depending on the pulse width and frequency of the recurrent inputs, but will range
from 1000 ms minimum to 10.4 seconds maximum. Recurrent Pulse detection can be
disabled with the SEL1 option jumper, see Section 2.15.1.
2.15.1 RECURRENT PULSE DETECTION DISABLE
The Recurrent Pulse Detection function can be disabled by soldering a 0-ohm jumper into
position SEL1 on the CMU-212 printed circuit board. When the jumper is inserted,
Recurrent Pulse Detection is disabled. When the jumper is removed, Recurrent Pulse
Detection is enabled.

CMU-212 Cabinet Monitor Unit
Operations Manual
Eberle Design Inc. Page 11
2.16 FLASHING YELLOW ARROW (FYA) PROTECTED-PERMISSIVE MONITORING
The CMU-212 is designed to monitor an intersection with up to six approaches using the
four section Flashing Yellow Arrow (FYA) movement outlined by the NCHRP Research
Project 3-54 on Protected/Permissive signal displays with Flashing Yellow Arrows, and
complies with all requirements of NEMA Standard TS-2 Amendment 4-2012 Flashing
Yellow Arrow.
For monitoring purposes an FYA approach is logically defined as a four input “logical
channel” consisting of the solid Red Arrow, solid Yellow Arrow, flashing Yellow Arrow
(permissive), and solid Green Arrow (protected). A Flashing Yellow Arrow approach is
typically monitored using two load switches and two physical channels of the CMU-212.
2.16.1 FYA CONFIGURATION
The following three clauses define the nomenclature used in this Section 2.16.1, as
described in NEMA Standard TS-2 Amendment 4-2012 Flashing Yellow Arrow.
2.16.1.1 PROTECTED TURN CHANNEL
The Protected Turn Channel of the FYA channel pair is composed of the solid
Green arrow (Ga) indication of the FYA Signal Output Group.
2.16.1.2 PERMISSIVE TURN CHANNEL
The Permissive Turn Channel of the FYA channel pair is composed of the solid Red
arrow (Ra), solid Yellow arrow (Ya), and the flashing Yellow arrow (fYa) indications
of the FYA Signal Output Group. The flashing Yellow arrow (fYa) indication will be
displayed as the Green input of the Permissive Turn Channel.
2.16.1.3 OPPOSING THROUGH CHANNEL
An Opposing Through channel is also associated with the FYA channel pair. The Opposing
Through channel is the channel that conflicts with the FYA Protected Turn Channel and is
permissive with the Permissive Turn Channel (flashing Yellow arrow).
2.16.2 CONFIGURING THE CMU-212 FAULT PARAMETERS FOR FYA
The CMU-212 built-in Setup Wizard in the MonitorKey software will automatically configure
the fault configuration parameters for Red Fail, Dual Indication, Field Check, and Minimum
Y+R Clearance. The Flashing Yellow Arrow configuration settings should be applied
before running the MonitorKey Setup Wizard. The MonitorKey form for setting the FYA
parameters is shown below:

CMU-212 Cabinet Monitor Unit
Operations Manual
Eberle Design Inc. Page 12
For an FYA channel pair the fault configuration parameters are to be applied to the
Primary channel with three inputs, Ra-Ya-fYa. The fault configuration parameters
programmed for the Sparse channel of the FYA pair with only one input, Ga, only affects
the sparse channel and not the Primary channel, and should be used only when the RY
INPUT Enable option is Enabled for that channel.
2.16.2.1 CONFLICT
The CMU-212 will verify that no conflicting channels to the solid Yellow arrow channel
(clearance) are active as determined by the Program Card compatibility programming of
the solid Yellow arrow channel of the pair except during the following sequences:
2.16.2.1.1 PROTECTED YELLOW CHANGE INTERVAL CONFLICT
During the Yellow change interval of the Protected Turn channel (Green arrow), the CMU-
212 will verify that no conflicting channels to the solid Yellow arrow channel (clearance) are
active as determined by the Permissive compatibility programming of the Protected Turn
channel (Green arrow) of the pair.
2.16.2.1.2 PERMISSIVE YELLOW CHANGE INTERVAL CONFLICT
During the Yellow change interval of the Permissive Turn channel (flashing Yellow arrow),
the CMU-212 will verify that no conflicting channels to the solid Yellow arrow channel
(clearance) are active as determined by the Permissive compatibility programming of the
Permissive Turn channel (flashing Yellow arrow).
2.16.2.2 RED FAIL
A Red Fail fault will occur if the solid Red Arrow AND solid Yellow Arrow AND flashing
Yellow Arrow AND solid Green Arrow all remain inactive for the Red Fail fault response
time. The fault status will be displayed for both channels of the FYA channel pair.
If the Red Fail function is enabled and the RY Input option is Enabled for the sparse
channel (Ga), then a Red Fail fault will occur if the Red AND Yellow AND Green all remain
inactive on the sparse channel for the Red Fail fault response time. The fault status will be
displayed for the sparse channel of the FYA pair.

CMU-212 Cabinet Monitor Unit
Operations Manual
Eberle Design Inc. Page 13
2.16.2.3 DUAL INDICATION
A Dual Indication fault will occur if any two or more of the solid Red Arrow, solid Yellow
Arrow, flashing Yellow Arrow, or solid Green Arrow signal combinations are active
simultaneously for the Dual Indication fault response time. The fault status will be displayed
for both channels of the FYA pair when the sparse channel input (Ga) is active.
If the RG, RY, or GY Dual Indication function is enabled and the RY Input option is enabled
for the sparse channel (Ga), then a Dual Indication fault will occur if any two or more of the
Red, Yellow, or Green inputs are active simultaneously on the sparse channel for the Dual
Indication fault response time. The fault status will be displayed for the sparse channel of
the FYA pair.
2.16.2.4 MINIMUM YELLOW CLEARANCE
A Yellow Clearance fault will be detected if the channel pair sequences from the protected
Green Arrow to the solid Red Arrow without a minimum clearance time on the solid Yellow
Arrow. The fault status will be displayed for the solid Yellow Arrow channel.
A Yellow Clearance fault will be detected if the channel pair sequences from the permissive
flashing Yellow Arrow to the solid Red Arrow without a minimum clearance time on the solid
Yellow Arrow. The fault status will be displayed for the solid Yellow Arrow channel.
If the Minimum Yellow Clearance function is enabled and the RY Input option is enabled for
the sparse channel (Ga), a Yellow Clearance fault will be detected if the sparse channel
sequences from the Green input to the solid Red input without a minimum clearance time
on the Yellow input. The fault status will be displayed for the sparse channel (Ga).
2.16.2.5 YELLOW PLUS RED CLEARANCE
The Minimum Yellow Plus Red Clearance function is not designed to operate with Flashing
Yellow Arrows. This function must be Disabled for the FYA channels that provide the
Permissive flashing Yellow arrow. This allows the CU to sequence from the Permissive Left
turn channel directly to the Protected Left Turn channel without a solid Yellow arrow
clearance interval.
2.16.3 RED AND YELLOW INPUT ENABLE
The Red and Yellow outputs of the sparse channel of an FYA channel pair are typically not
loaded with a signal head and thus left floating. In these cases the Red and Yellow inputs
for the sparse FYA channels can be forced to the Off state in the CMU-212 by default. This
simplifies the cabinet wiring such that the use of dummy cabinet loads or modifications to
the Output harness are not necessary.
If the Red and Yellow outputs of the sparse channel of an FYA channel pair are driving
signal loads (such as a hard wired right turn overlap) then they must be monitored by the
CMU-212 at all times. The RY INPUT option should then be enabled for that channel. The
fault configuration parameters programmed for this Sparse channel of the FYA pair only
affects the Sparse channel and not the Primary channel, and should be enabled only when
the RY INPUT option is Enabled for that channel.
2.16.4 FLASH RATE DETECTION
When the FLASHRATE FAULT option is enabled, the CMU-212 will monitor a flashing
yellow arrow output for a lack of flashing operation. If any of the enabled flashing yellow
arrow signals remain active for more than the FYA Flash Rate Fault time (Section 5.2), the
CMU-212 will enter the fault mode, transfer the OUTPUT relay contacts to the Fault
position, and display the FYA FLASH-RATE FAIL status screen. The CMU-212 will remain
in the fault mode until the unit is reset by the RESET button.

CMU-212 Cabinet Monitor Unit
Operations Manual
Eberle Design Inc. Page 14
2.16.5 FYA YELLOW TRAP CONFLICT DETECTION
When the FYA TRAP DETECT option is enabled, the CMU-212 will monitor each FYA
permissive turn channel for the FYA Yellow Trap condition. The FYA Yellow Trap conflict
condition occurs when the Permissive Turn channel (flashing yellow arrow) sequences to
the solid yellow arrow clearance while the Opposing Through channel is still showing a
green ball.
When the FYA Yellow Trap Conflict condition is detected, the CMU-212 will enter the fault
mode, transfer the OUTPUT relay contacts to the Fault position, and display the
“CONFtrap” fault status screen. The CMU-212 will remain in the fault mode until the unit is
reset by the RESET button.

CMU-212 Cabinet Monitor Unit
Operations Manual
Eberle Design Inc. Page 15
Section 3
INPUT SIGNALS
3.1 FIELD SIGNAL INPUTS
A Green or Yellow signal input will be sensed active when it exceeds 25 Vrms and will not
be sensed active when it is less than 15 Vrms. A Green or Yellow signal between 15 and
25 Vrms may or may not be sensed active. There is programming in the Datakey to disable
the Yellow input for each physical channel.
A Red signal input will be sensed active when it exceeds 70 Vrms and will not be sensed
active when it is less than 50 Vrms. A Red signal between 50 and 70 Vrms may or may not
be sensed active.
3.2 LOAD SWITCH CURRENT
Load current is sensed by the AMU-214 based on total load current to all colors of a
channel. Total load current is an indication that a signal load is present. Lack of adequate
load current indicates no active load (i.e. burned out lamps) or an open field wire condition.
Load current monitoring is used by the Lack of Signal monitoring function (see 2.5) to
detect the loss of signal load while the load switch is in the On state.
A channel will be sensed active when the load current exceeds 105% of the Channel
Current Sense Threshold programmed for that channel in the Datakey. A channel will not
be sensed active when the load current is less than 95% of the Channel Current Sense
Threshold programmed for that channel in the Datakey. A load current value between 95%
and 105% of the Channel Current Sense Threshold may or may not be sensed active. This
provides a hysterisis value of +/- 5% of the Channel Current Sense Threshold.
The Channel Current Sense Threshold should be programmed for each monitored channel
based on the minimum signal load under all worst case conditions.
3.3 PDA CONTROL SIGNAL INPUTS
3.3.1 LOCAL FLASH STATUS
The cabinet should be wired such that operation of the cabinet in AUTO mode will place
AC+ on the LF STATUS pin. Operation of the cabinet in FLASH mode should be open
circuit on this input. This input will be considered active when the input voltage exceeds 89
Vrms. This input will not be considered active when the input voltage is less than 70 Vrms.
Signals between 89 Vrms and 70 Vrms may or may not be considered active. The CMU-
212 will report the state of this input in the Type 189 frame. See section 2.9.
3.3.2 MAIN CONTACTOR (MC) COIL STATUS
The cabinet should be wired such that the MC COIL STATUS input is connected to the
AC+ RAW side of the main contactor signal bus relay coil. An active signal on this input
indicates the Signal Bus should be powering the load switches. This input will be
considered active when the input voltage exceeds 89 Vrms. This input will not be
considered active when the input voltage is less than 70 Vrms. Signals between 89 Vrms
and 70 Vrms may or may not be considered active. The CMU-212 will report the state of
this input in the Type 189 frame.
3.3.3 MAIN CONTACTOR (MC) SECONDARY STATUS
The cabinet should be wired such that the MC SECONDARY STATUS input will be
connected to the output side of the main contactor signal bus relay. An active signal on this
input indicates the Signal Bus is powering the load switches. This input will be considered
active when the input voltage exceeds 89 Vrms. This input will not be considered active
when the input voltage is less than 70 Vrms. Signals between 89 Vrms and 70 Vrms may or

CMU-212 Cabinet Monitor Unit
Operations Manual
Eberle Design Inc. Page 16
may not be considered active. The CMU-212 will report the state of this input in the Type
189 frame.
3.3.4 FTR COIL DRIVE STATUS
The cabinet should be wired such that the FTR COIL DRIVE STATUS input is connected to
the FTR COIL DRIVE signal in the AC SIGNAL POWER BUS. An active signal on this input
indicates the flash transfer relays are energized and the field signals are driven from the
load switch outputs. This input will be considered active when the input voltage exceeds 89
Vrms. This input will not be considered active when the input voltage is less than 70 Vrms.
Signals between 89 Vrms and 70 Vrms may or may not be considered active. The CMU-
212 will report the state of this input in the Type 189 frame.
3.3.5 CIRCUIT BREAKER (CB) TRIP STATUS
The cabinet should be wired such that the CB TRIP STATUS input will be connected to the
Auxiliary Switch output of the circuit breaker unit. The active state of this input indicates that
the circuit breaker unit is not in the tripped state. This input will be considered active when
the input voltage exceeds 89 Vrms. This input will not be considered active when the input
voltage is less than 70 Vrms. Signals between 89 Vrms and 70 Vrms may or may not be
considered active. The CMU-212 will report the state of this input in the Type 189 frame.
3.3.6 FRONT / REAR DOOR SWITCH
The cabinet should be wired such that AC+ is applied to the DOOR SWITCH FRONT or
DOOR SWITCH REAR inputs when the respective door is Open. These inputs will be
considered active (door open) when the input voltage exceeds 89 Vrms. These inputs will
not be considered active (door closed) when the input voltage is less than 70 Vrms. Signals
between 89 Vrms and 70 Vrms may or may not be considered active. The CMU-212 will
report the state of these inputs in the Type 189 frame.
The Datakey not present will cause a LFSA if the DOOR SWITCH FRONT input is sensed
as not active (door closed). See section 2.14.3.
3.4 MONITOR INTERLOCK
The MONITOR INTERLOCK input is connected to VDC GROUND within the CMU-212.
The cabinet should be wired such that the lack of VDC GROUND on this pin forces the
cabinet to the flash mode. This prevents a cabinet from operating without a CMU-212
installed.
3.5 EXTERNAL TEST RESET INPUT
The EXTERNAL TEST RESET input is used to reset the CMU-212 from the FSA condition.
When the EXTERNAL TEST RESET input is connected to VDC GROUND (True) all front
panel indicators will be illuminated for 100 msec and the OUTPUT relay energized.
Continuously activating the input will not affect CMU-212 operation.
The EXTERNAL TEST RESET input is intended for use in testing the CMU-212 and should
not be connected in the cabinet.
3.6 SERIAL BUS #1 ADDRESS INPUTS
The Address Select input pins ADDRESS 0 and ADDRESS 1 define the Serial Bus #1
address of the CMU. The pins are left open for a logical False, and are connected to VDC
GROUND for a logical True.
ADDRESS 1
ADDRESS 0
SB #1 ADDRESS
This manual suits for next models
1
Table of contents
Other EDI Measuring Instrument manuals
Popular Measuring Instrument manuals by other brands
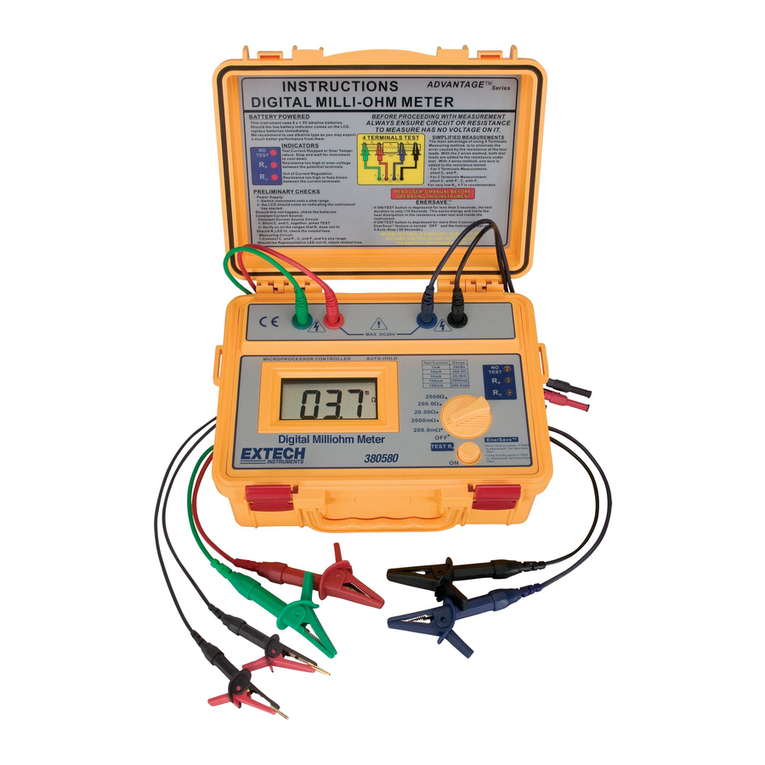
Extech Instruments
Extech Instruments 380580 user guide
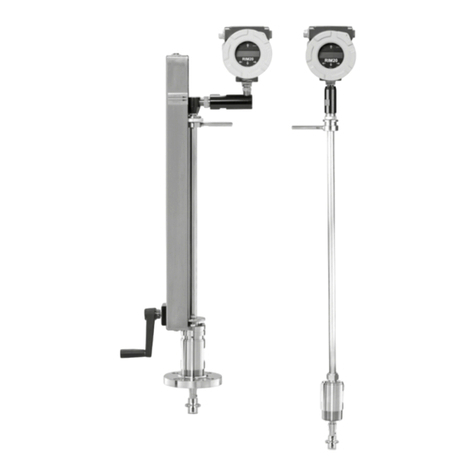
Spirax Sarco
Spirax Sarco RIM20 Installation and maintenance instructions

Toshiba
Toshiba Density (Consistency) Meter LQ500 Installation
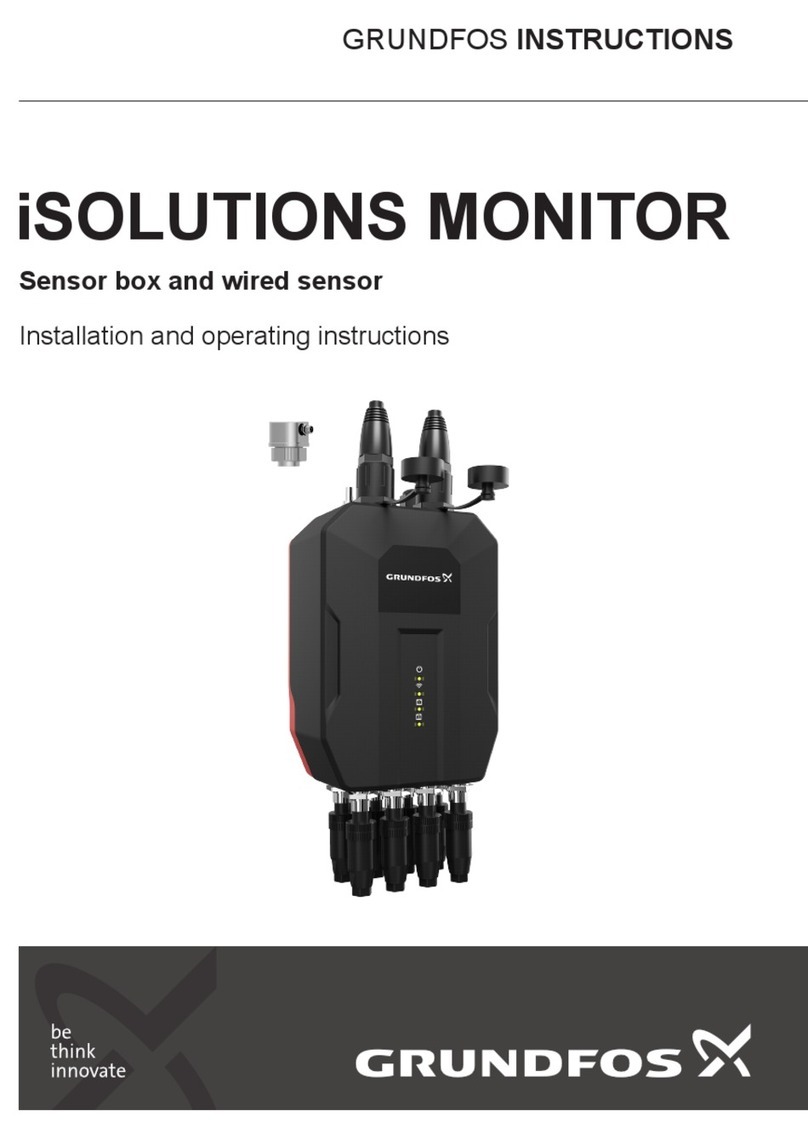
Grundfos
Grundfos iSolutions Monitor Installation and operating instructions
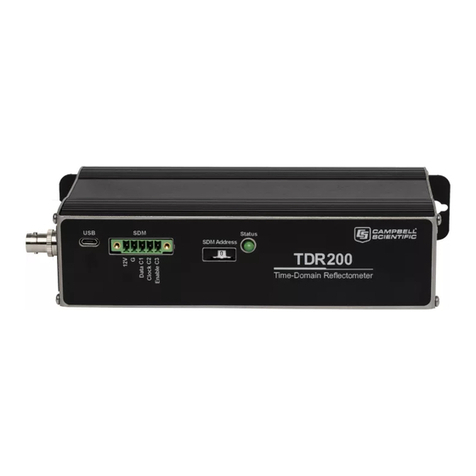
Campbell
Campbell TDR200 product manual
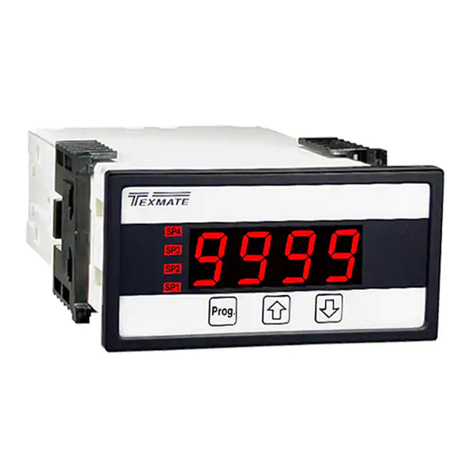
Texmate
Texmate DL-40PSF-PROCESS quick start guide