Eicom ENO-30 User manual


ENO-30 ENG, #04v2,2014
NOx Analyzer (ENO-30)
User’s Guide
Distributed by Eicom USA: 7098 Miratech Dr, Ste 100, San Diego, CA 92121, USA
Phone: (888) 680-7775 FAX: (858) 560-8040 Email: info@eicom-usa.com
Distributed by Eicom Europe: Hilton House Ardee Rd, Ground Floor, Rathimines Dublin 6, Ireland
Phone: +353 1 902 2700 FAX: +353 1 443 0784
Manufacturered by Eicom Corporation: 113 Kita Enmenden-cho, Shimotoba, Fushimi-ku Kyoto, Japan, 612-8497
Phone: +81-75-622-2112 FAX : +81-75-622-2114

Contents
1. INTRODUCTION ---------------------------------------------------------------------------------------------------------------------------1
1-1. About this user’s guide -----------------------------------------------------------------1
1-2. Important Safety Information ---------------------------------------------------------2
2. OVERVIEW ----------------------------------------------------------------------------------------------------------------------------------3
2-1. Principle of Measurement -------------------------------------------------------------3
2-2. Schematic of Parts and Functions --------------------------------------------------4
2-3. Tubing Flow Diagram-------------------------------------------------------------------6
2-4. Pump Seal Wash ------------------------------------------------------------------------7
2-5. Fittings and Tubing----------------------------------------------------------------------8
3. INSTALLATION--------------------------------------------------------------------------------------------------------------------------- 10
3-1. Location ----------------------------------------------------------------------------------10
3-2. Power Plug------------------------------------------------------------------------------ 10
3-3. Electrical connections (Detector Unit side panel)----------------------------- 11
3-4 Electrical Connections (Pump Unit Signal Terminal)--------------------------12
3-5. Manual injector Tubing Connections --------------------------------------------- 13
3-6. Connect Tubing to Autosampler (optional)--------------------------------------13
4. PUMP UNIT OPERATION-------------------------------------------------------------------------------------------------------------- 14
4-1. Pump overview-------------------------------------------------------------------------14
4-2. Power On --------------------------------------------------------------------------------15
4-3. Key Pad ----------------------------------------------------------------------------------16
4-4. Display Screen -------------------------------------------------------------------------18
4-5. Log Function---------------------------------------------------------------------------- 18
4-6. Adjusting the Settings ---------------------------------------------------------------- 19
4-7. Priming the Pump/ Purge Valve Operation -------------------------------------22
4-8. Pump error messages---------------------------------------------------------------- 23
5. DETECTOR/OVEN OPERATION ---------------------------------------------------------------------------------------------------- 24
5-1. Power Switch ---------------------------------------------------------------------------24
5-2. Setting Temperature ------------------------------------------------------------------24
5-3. Detector Readings--------------------------------------------------------------------- 24
5-4. Autozero Function --------------------------------------------------------------------- 24
6. ANALYSIS---------------------------------------------------------------------------------------------------------------------------------- 25
6-1. Accurate Analysis---------------------------------------------------------------------- 25
6-2. Water Quality ---------------------------------------------------------------------------25
6-3. Reagent Quality------------------------------------------------------------------------ 25
6-4. Carrier and Reactor Solutions Preparation ------------------------------------- 26
6-5. Standard Solution----------------------------------------------------------------------27
6-6. Waste-------------------------------------------------------------------------------------27
6-7. Prepare for Analysis-------------------------------------------------------------------27

6-8. Start up ----------------------------------------------------------------------------------- 28
7. SAMPLE INJECTION ------------------------------------------------------------------------------------------------------------------- 29
7-1. Manual Injector Operation-----------------------------------------------------------29
7-2. Sample Amount ------------------------------------------------------------------------30
7-3. Autosampler Operation (optional) -------------------------------------------------30
8. SHUTDOWN AFTER ANALYSIS----------------------------------------------------------------------------------------------------- 31
8-1. Short Shutdown, less than 2 weeks ----------------------------------------------31
8-2. Complete Shutdown, over 2 weeks----------------------------------------------- 31
9. RESTART ---------------------------------------------------------------------------------------------------------------------------------- 32
9-1 After complete shutdown procedure----------------------------------------------- 32
9-2. After short shutdown procedure----------------------------------------------------32
10. PRECOLUMN --------------------------------------------------------------------------------------------------------------------------- 34
10-1. Determining the Precolumn Condition------------------------------------------34
10-2. How to Repack the Precolumn---------------------------------------------------35
10-3. Filter Exchange-----------------------------------------------------------------------37
11. SEPARATION COLUMN (NO-PAK) ----------------------------------------------------------------------------------------------- 38
11-1. NO-PAK--------------------------------------------------------------------------------- 38
11-2. Identification of Separation Quality----------------------------------------------38
11-3. Washing the Separation Column-------------------------------------------------38
12. REDUCTION COLUMN (NO-RED) ------------------------------------------------------------------------------------------------ 39
12-1. Structure and Maintenance--------------------------------------------------------39
12-2. Timing to Exchange -----------------------------------------------------------------39
12-3. Damage --------------------------------------------------------------------------------39
13. TROUBLESHOOTING ---------------------------------------------------------------------------------------------------------------- 40
13-1. Pump Problems ----------------------------------------------------------------------40
13-2. Checking the Flow Rate------------------------------------------------------------ 40
13-4. Removing Air Bubbles --------------------------------------------------------------40
13-4. High Carrier Pump pressure ------------------------------------------------------41
13-5. Unstable Baseline-------------------------------------------------------------------- 41
13-6. Peak Shape --------------------------------------------------------------------------- 41
14. MAINTENANCE------------------------------------------------------------------------------------------------------------------------- 42
14-1. Pump Head Parts--------------------------------------------------------------------42
14-2. Changing the Piston Seal and Piston------------------------------------------- 43
15. APPENDICES --------------------------------------------------------------------------------------------------------------------------- 47
15-1. Autosampler and Data Processor (EPC-700) Connection ----------------47
15-2. Specifications ------------------------------------------------------------------------- 48
15-3. Sample Preparation -----------------------------------------------------------------49


1 | P a g e
1. Introduction
Thank you for purchasing the Eicom NOx Analyzer (ENO-30). Please read this user’s guide
before use.
The ENO-30 is an HPLC-based system designed to perform high sensitivity analysis of Nitrite
and Nitrate in biological samples. The lower half of the system is the pump unit. It has two
independent pumps and a two channel online degasser. The pump has s self-learning pulse
damping flow control which ensures stable liquid delivery, and is made of inert, non-metallic
parts for better salt and acid resistance.
The upper unit uses forced air and a Peltier device to maintain the columns, reaction loop, and
detector cell at the correct temperature for the analysis. The detector signal is taken from the
side terminals into a data process (EPC-700) and digitized for analysis in a PC with the Envision
software.
1-1. About this user’s guide
Latest-breaking information may be supplied separately.
We reserve the right to change the content of this document with or without notice.
No part of this guide may be reproduced by any means without the prior written permission
of Eicom. All rights reserved.
The ENO-30 requires a thorough understanding of this document for proper operation.
Please contact Eicom directly if you have any unanswered questions after reading this
document.

2 | P a g e
1-2. Important Safety Information
We insist that users observe the following procedures in order to prevent accidents:
1) Be sure to read and understand this manual completely prior to operating the ENO-30.
2) Follow all warnings listed herein very closely.
3) Do not alter the ENO-30.
4) Never attempt to repair or dismantle the ENO-30 on your own.
This device has been produced for experts who have knowledge of chemical
analysis and handling research reagents. Failure to follow instructions may
not only lead to poor quality data, but could result in a safety hazard such as
fire, electric shock, injury or other damage. DO NOT OPERATE the ENO-30
until reading and understanding this instruction manual completely.
WARNING
Before you operate the ENO-30 using harmful chemical reagents,
be sure to understand its handling methods, physical and chemical
characteristics and MSDS (material safety data sheets). Mishandling
harmful chemical reagents might result in death or serious injury to the user.
To avoid health hazards, wear proper protective gloves, goggles and mask,
and be sure there is adequate ventilation. Never allow leakage from any
connection points of the tubing.
WARNING
Flammable chemical reagents must be kept away from sources of
ignition and may give off flammable vapors if left uncovered.
WARNING

3 | P a g e
2. Overview
2-1. Principle of Measurement
The ENO-30 is a high sensitivity instrument for measuring nitrite and nitrate ion level in
biological fluids. This is achieved by combining a colorimetric diazo coupling method (Griess)
with the advantages of HPLC.
After the sample is injected it is filtered by the guard column. Then the separation column
interacts with the ions in such a way that they flow though the column at different rates. Nitrite
exits the column first, and then some minutes later, the Nitrate leaves the column. The NO2-and
NO3-next flow into the reduction column made is cadmium and copper.
Inside the reduction column, the NO3-is reduced to NO2-through a reaction with the cadmium
and reduced copper. The NO2- that exited first will not react. So now there are two Nitrite peaks,
the first is from the Nitrite in the sample and the second is from the Nitrate in the sample. Both
are mixed with a Reactor solution supplied by a second pump at a 3-way joint, and then flow
into a reaction loop. This gives time for the reaction come to the right temperature and complete
formation of a light absorbing diazo compound that can measured at the detector.
In the detector cell, 540 nm (green) light passes through the sample, and the absorption is
proportional to the amount of diazo compound, and thus to the amount of Nitrite or Nitrate.
The response of the detector is transformed to a voltage which it generates at the CPU terminal.
The time/voltage change is traced by a data processor such as the optional Eicom EPC-700. By
comparing peak area or height shown on a chromatogram with a standard one, the exact
concentration Nitrite and Nitrate can be calculated.

4 | P a g e
2-2. Schematic of Parts and Functions
1. Pump control panel
Set the flow rate of each pump and the upper pressure limit. Then start and stop the pump.
2. Degasser
This degasser removes dissolved air from the Carrier and Reactor solutions before they enter
the pumps. It does not work for large bubbles in the inlet tubing. The degasser prevents bubbles
from forming in the pumps, which will cause them to stop. The internal volume of each degasser
channel is 300 µL.
3. Carrier Pump
It supplies carrier solution to the separation column and reduction column.
4. Reactor Pump

5 | P a g e
It supplies the reactor solution to the reaction coil.
5. Reactor Backpressure Coil
It maintains high enough pressure that the reactor pump can work efficiently.
6. Manual Injector (and/or Autosampler)
Manual injection of up to 50 µL of sample using a blunt ended Hamilton syringe can be made
here.
7. Mixer
Mixes the column effluent with the Reactor solution before entering the reaction coil.
8. Reaction Coil
Gives time for the reaction to be heated and go to completion. It also helps to reduce mixing
noise.
9. Detector Cell
Detects absorbance at 540 nm.
10. Separation Column
Separates the Nitrite and the Nitrate from other biological compounds.
11. Reduction Column
Reduces the Nitrate to Nitrite so that it can react with the Greiss reagent.

6 | P a g e
2-3. Tubing Flow Diagram
Please use this diagram as a guide in make all the proper tubing connections.
Important points:
The column effluent (Carrier) and the Reactor solution should enter the 3-way joint on
opposite sides of the straight part of the joint to improve mixing.
Be careful to never let the Reactor solution enter the separation column. It may be
severely damaged.
Also turn the Reactor pump off 1 minute before the Carrier pump in order to wash all the
Reactor solution out of the tubing because it can stain if left in place. This will lead to
higher background.

7 | P a g e
2-4. Pump Seal Wash
Sy ringe
Check
Valve
Check
Valve
Tubing
Stop
The ENO-30 has a pump seal wash function, which greatly expands the pump seal lifetime, and
prevents damage to the inside of the pump. Small amount of salt containing liquid can leak
passed the seal. If it is allowed to crystallize, the salt crystals will scratch the piston and seal,
causing premature wear and eventually leakage.
Please purge the washing tube with 2-3 mL of purified water before and after running the
pump.
The inlet end of this tube should be set at the bottom of a bottle containing super pure water.
The outlet can be routed back to the same bottle or directly to waste. Be sure to change this
water frequently to prevent bacterial growth and the buildup of salts and acids.
To begin the flow of water through the wash ports at the back of the pump heads, you must
prime the fluid path with the syringe.
1. Close the tubing roller clamp and aspirate with the syringe.
2. Open the tubing stop and gently dispense the water. Do not force the water too aggressively
as that can cause issues inside the pump. If the water doesn’t flow easily, the tubing may be
clogged or damaged. Check tubing and replace. Leave the syringe in place.
3. Now you can start the pumps. You should see drops of water flowing from the outlet as the
pumps run.

8 | P a g e
2-5. Fittings and Tubing
There are two main types of fittings used to connect tubing on the ENO-30.
Easy Fit The Easy Fit connector is for column joints and other high pressure
locations. Before tightening the nut, push the tubing end all the way
through the Easy Fit connector until it stops inside the connection, and
hold it in place while you screw down the nut. The tubing can
sometimes be pulled back and not actually be connected. If the tube is
not attached properly, the peak shape will be influenced. Be careful not
to overtighten because this can cause the tubing to be crushed and
the fluid passage blocked.
Flat Seal Some connections use a flat seal type of nut and
ferrule (white triangle in the figure). Please check
the direction of the ferrule, the wide side should
be flush with the end of the tubing before
inserting into the connection.
Tubing
Material
Dimension
Product Name
Use
PEEK
0.125 mm x 1/16”
PT-12F (red stripe)
Reactor back pressure
PEEK
0.250 mm x 1/16”
PT-25F (blue stripe)
Carrier
PEEK
0.500 mm x 1/16”
PT-50F (orange stripe)
After pumps
PEEK
0.750 mm x 1/16”
PT-75F (green stripe)
Before pumps
PTFE
1 x 3 mm
TFE-1030
Inlet tubing
PTFE
2 x 3 mm
TFE-2030
After degasser
ETFE
0.3 mm x 1/16”
TZ-30
Reaction coil and waste
ETFE
0.8 mm x 1/16”
TZ-80
Seal wash
Silicon
1 x 3 mm
SIL-1030
Seal wash

9 | P a g e
Tubing and Nut Uses
Tubing Section
Tubing Type
Connector
Inlet Tubing
Degasser
1 mm x 3 mm
PTFE
Connector (Translucent) &
Ferrule(White)
for 1/8” Flat Seal
3 Way Connector
under Pump Head
2 mm x 3 mm
PFA
Connector (Black) &
Ferrule (Yellow)
for 1/8” Flat Seal
Inlet Check Valve
0.75 mm PEEK
(Green stripe)
Fitting 1/16 inch
Outlet Check Valve
Purge Valve
0.50 mm PEEK
(Orange stripe)
Hexagon-fitting
1/16 inch (Large)
Pump head
Washing Ports
Seal Washing Tube
0.8 mm x 1/16”
ETFE
Hexagon-fitting
1/16 inch (Small)
**Caution: When using the hexagonal fittings, please fasten by a hand at first
and then rotate no more than about 45˚ with a wrench.
Tubing (installation)
Generally, Eicom or its distributor will install the ENO-30 and connect all tubes. In the event that
you have to reconnect the tubing yourself, please refer to the following points.
Connect the outlet tube of the Reactor pumps to the three way joint through a hole in the
right side of the Detector unit.
Connect the outlet tube of the Carrier pumps to the manual injector port “2” (remove the
stop fit at the port and connect by Easy fit connector).
When the Autosampler is installed, the tubing that would normally go to the column inlet
should, instead, go to the valve in the autosampler, and then tubing from the Autosampler
valve should come back to the column inlet. For further details, refer to the autosampler
manual.

10 | P a g e
3. Installation
The information in this section is given as a reference only. Everything should have been set up
by your Eicom Representative during the installation/training. However, if you need to move the
instrument or disconnect tubing or electrical connections, this section will be helpful.
3-1. Location
The ENO-30 is designed for use in laboratories for life science.
Do not expose to direct sunlight.
Install only on a sturdy, horizontal surface.
Leave space more than 4 inches of space around instrument.
Make sure nothing is liable to fall onto the ENO-30.
Do not leave anything on top of the ENO-30.
Do not place in a location that is prone to vibration.
This product should be operated only in room where there is a minimum of temperature
fluctuations. Maintain the temperature between 15-30 °C during use.
Do not expose the directly to drafts, including heating and air conditioning vents.
Keep away intense heat sources and other equipment that may produce strong magnetic
fields or electrical noise.
Do not use or store organic solvents or chemicals that emit caustic gases nearby. Always
maintain adequate ventilation.
The ENO-30 should be operated in a dust-free environment. Remove any dust from
around the ENO-30 frequently.
Do not block the ventilation slits on side of the ENO-30. Excessive heat from
the machine may accumulation inside the product and cause damage.
Maintain sufficient space around the ENO-30 to ensure adequate ventilation.
3-2. Power Plug
Power supply conditions of ENO-30 are as follow. Please make sure to use the included triple
core cable with grounding wire as power supply.
Power supply Voltage: AC 100V~240V Single Phase (±10V)
Frequency: 50 or 60 Hz
Power Supply: 2 x 200 W supplies
Connection: Cable with Grounding Wire (Triple Core)
Caution

11 | P a g e
3-3. Electrical connections (Detector Unit side panel)
The ENO-30 is set up when delivered by Eicom or its distributor. If for some reason, you set up
the electrical connectors of the ENO-30 by yourself, please use the diagram below as a guide.
CPU (analog output)
The absorbance is converted to voltage at a ratio of the 1 ABS (absorbance) = 1 V.
This port is usually connected to the Detector 1 signal input of a data processor such as Eicom
EPC-700.
AUTO ZERO/ SIG. IN
An external device such as an autosampler or manual sample injector should be connected to
this port so that the output signal is reset to zero for each injection. The input trigger from the
external device is also sent to the SIG. OUT terminals.
SIG. OUT
This terminal will output a signal when “AUTOZERO/ SIG. IN” is triggered. Connect this position
to Input 1 of the data processor. This will start the data collection as each injection is made.

12 | P a g e
3-4 Electrical Connections (Pump Unit Signal Terminal)
If you have an autosampler installed this communication signal terminal may be of use to you.
Otherwise, you don’t need to connect anything here. See below on how the <ERROR OUT> signal can
be used.
ERROR OUT Contact closures will output here if a pump stops because of an
error. If you connect to the input channels of the autosampler
here and have the input command set to “Freeze”, the
autosampler will stop making injections when the pump stops.
This way you avoid losing precious samples.
RUN/STOP IN A contact closure signal of more than 10 msec at the <run/stop
in> commands will cause the pump to start or stop. This is one
way to have the system shutdown automatically after completing
analysis.
PRESSURE OUT If you want to monitor pressure for some reason, this terminal
outputs a voltage of up to 100 mV (100 MPa) to communicate
the pressure in the system.

13 | P a g e
3-5. Manual injector Tubing Connections
At the back of the manual injector:
Port #1 and #4 has the sample loop
Port #2 receives the tubing from the Carrier pump
Port #3 goes to the precolumn/separation column, or if installed, to an
autosampler. (tubing from the autosampler will come back and connect to
the columns)
Ports #5 and #6 are drain ports (check the crystals don’t form on the outlet
as that can prevent proper manual injection volumes)
3-6. Connect Tubing to Autosampler (optional)
On the valve inside and towards the top of the AS-700 autosampler:
Port # 2 and #5 has the sample loop
Port #1 receives the tubing from the port #2 of the manual injector, or if you
prefer, directly from the Carrier pump
Port #6 connects to the columns
Port #3 connects to the syringe via the buffering tube
Port #4 is where the sample needle connects

14 | P a g e
4. Pump Unit Operation
4-1. Pump overview
The ENO-20 has the very precise liquid delivery pump with double pistons. The reciprocal action of the 2
pistons provides for continuous pulseless flow of the mobile phase.
Outlet Check Valve
At the top each side of the pump head (2 per pump), there is an outlet check valve. This valve
prevents solution from flowing back into the pump. This is a very sensitive; be very careful to not
over-tightened when using a wrench. The internal parts can be crushed and the part will need to
be replaced
Inlet Check Valve
At the bottom of each side of the pump head, (2 per pump), there is an inlet check valve. This
valve also prevents solution from flowing from the pump back to the reservoir. This is very
sensitive; be very careful to not over-tightened when using a wrench. The internal parts can be
crushed and the part will need to be replaced
How it Works
As each piston movers forward the outlet check valve opens and the fluid is sent to the columns
at high pressure. Then as the piston starts to move back, the outlet check valve with close and
the inlet check valve will open so that the piston space can will with fluid. The cycle is completed
as the piston begins forward again; at which time, the inlet check valve closes and the outlet
valve opens.
Check Valve (Outlet)
Pump Head
Front
Mobile Phase
(Inlet)
Check Valve (Inlet)
Piston Seal
Back up Ring
O-Ring
Seal Washing Liquid Space
Pump Head Guide
Piston
Washing Seal
Rod
Guide Ring

15 | P a g e
4-2. Power On
Turn on the main power switch on the left side of main body. The display will light up after the power
is turned on. A start screen will appear before entering the operation screen. The degasser vacuum
pump will immediately start and continue to run on and off throughout operation to maintain a vacuum.
Start Screen
*The EP-700 stores the parameters from the last time the pump was used and loads those
upon startup.
Status Indicator
The EP-700 indicator communicates the functional state of the instrument by color, on/off, or blinking.
Indicator
Subject
Lighting Pattern
DEGASS
Vacuum pump
degasser is
running
Turn off
Normal
Red Blinks
Abnormal *
PUMP A
PUMP B
Machine motion
of PUMP A and
PUMP B
Turn off
Operation Off
Green Light
Operation On
Green Blinks
Pump Off timer is in
operation
*DEGASS When the indicator blinks red, there is a problem inside the
degasser. Please contact Eicom or one of its distributors immediately.
Indicator Lights
Table of contents
Other Eicom Measuring Instrument manuals
Popular Measuring Instrument manuals by other brands
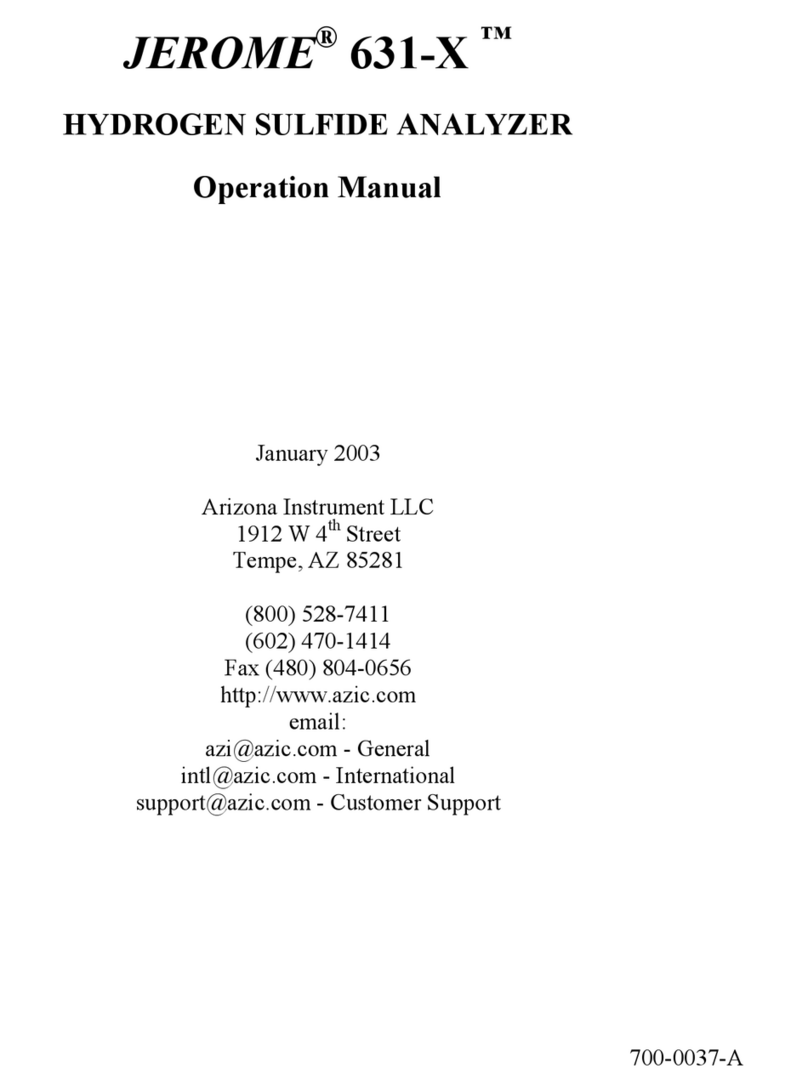
Arizona
Arizona Hydrogen Sulfide Analyzer Jerome 631-X Operation manual
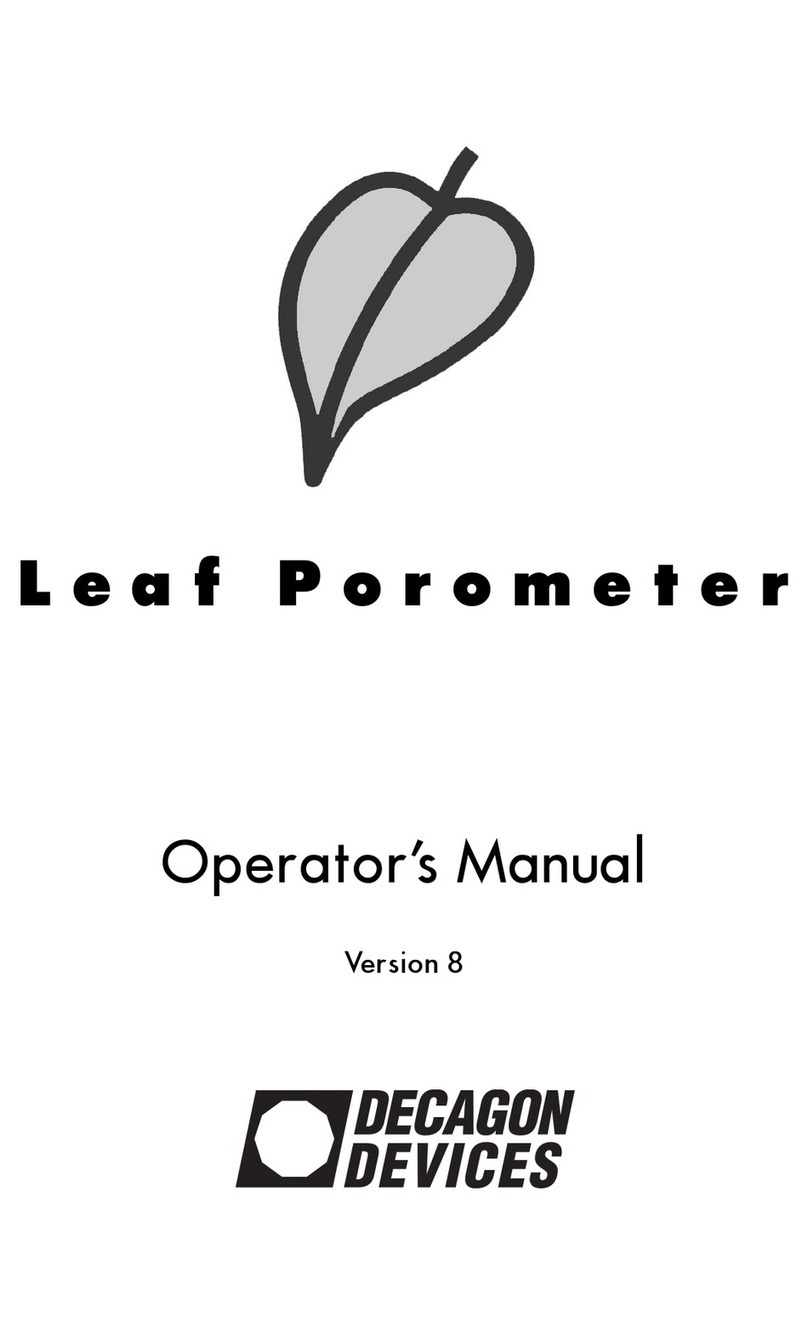
Decagon Devices
Decagon Devices SC-1 Operator's manual
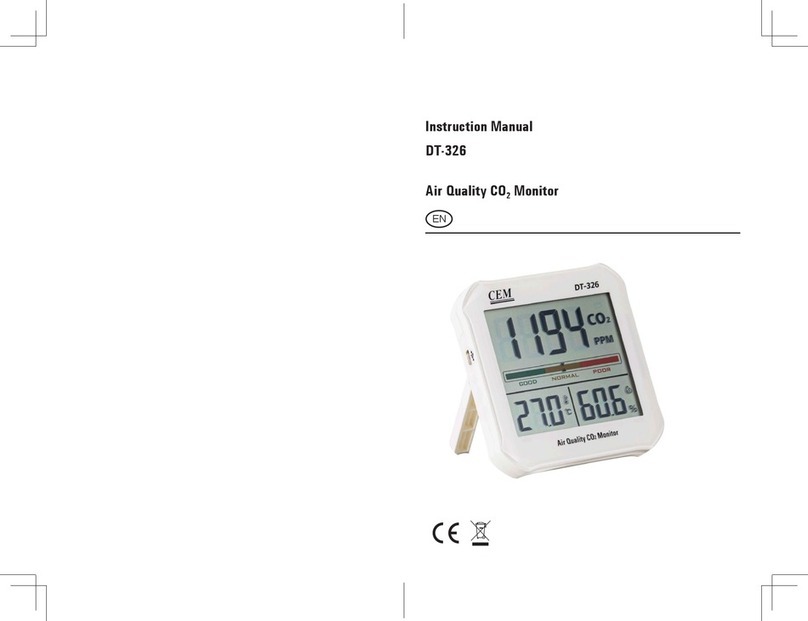
CEM
CEM DT-326 instruction manual

Aquametro Oil & Marine
Aquametro Oil & Marine CONTOIL VZF II DN 15 Spare Parts - Repair - Maintenance

Extech Instruments
Extech Instruments RH25 user guide

Reer
Reer LAD3 Installation, use and maintenance