Ellard Mini Standard V7 Instruction sheet

Page 1 of 8
PRODUCT INSTRUCTIONS
Mini Standard V7 3phase Controller Dallimore Rd, Wythenshawe,
Manchester. M23 9NX
T: +44 (0)161 945 4561
F: +44 (0)161 945 4566
Stock Code Description Doc No: PI-110
01003 Dalmatic Mini Standard V7 Controller Iss: 1
Controller
Specification
Supply voltage: 3ph - 400VAC ± 10% L1,L2,L3,PE (‘N’ not required)
50/60Hz,
Mains supply protection should be provided by
either 10A/phase MCB Type ’C’ or fuse equivalent
Maximum Load Max motor load by 3 x 400VAC: 4 kW
Temperature range -10…+50°C (operating)
Humidity: Up to 93% RH non-condensing.
Auxiliary Supply 24VDC ± 20% (non-regulated)
Max load: 250mA
(without additional plug-in options)
Safety edge input: Pneumatic air switch (N/C Contact)
Electric type - 8k2 termination ± 10%
Optical type (Fraba OSE or Dalmatic TSS/RSS)
Photo sensor input Photo-sensor, 24 VDC, Relay O/P N/C
Description
The Mini-Std controller has been designed as a controller which provides the
capabilities to operate an industrial door safely under electrical control by means of
a pushbutton station or key switch
Its intended use is to be connected to a suitable motor not exceeding the load for
the controller
The unit incorporates safety features to protect people or property from damage by
automatically reversing a closing door should they be activated
This together with the auto closing function and additional facilities for plug in Loop
Detectors and radio control make this unit very versatile
Connections are provided for Mains supply, Motor power, Travel Limits switches,
Push Buttons, Photocell and Safety Edge and 24VDC Auxiliary power (250mA max)

Page 2 of 8
The installation should only be carried out by a trained competent person and
in accordance with all local legislation. Please read the instructions in full
prior to installation
Board Layout

Page 3 of 8
Installation
1) Controller should be mounted in suitable enclosure for the environment and be:
a. Vertically mounted and free from vibration
b. Not exposed to and is free from all dust and debris
c. Fitted with appropriate cable glands to maintain IP rating of enclosure selected
d. Fitted with appropriate wall fixings used to secure the enclosure
2) Ensure that all power is OFF before connecting any wiring to the controller or motor referring
to the connection details in this manual,
3) Check ALL wiring connections are secure upon completion
Setting Travel Limits
1) Manually haul the door to mid position
2) Ensure ALL dipswitches are set to OFF
3) Re-apply mains supply power
4) Press the open button and observe the operating direction, the door should move in dead-
man operation in the opening direction
a. If not correct, turn the Main Supply Power OFF, rotate any two of the motor phases
U, V, W i.e. (U&V) (U&W) or (V&W)
b. Turn mains supply power ON and re-check for correct direction
5) Using pushbuttons move the door to its fully open position, then set the open travel limit cam
Repeat in the close direction setting the close travel limit cam
Fully open & close the door and check end of travel positions adjust travel limits if necessary

Page 4 of 8
Dipswitch Functions
Dipswitch
SW Description of function OFF ON
SW1 Operation – OPEN direction Dead-man OPEN Impulse OPEN
SW2 Operation – CLOSE direction Dead-man CLOSE Impulse CLOSE
SW3 External ‘Auto-Close’ operation (term X12) DISABLED ACTIVE
SW4 Go function (OPEN-STOP-CLOSE-STOP) DISABLED ACTIVE
SW5 Electric Safety Edge 8k2 enabled DISABLED ACTIVE
SW6 Optical Safety Edge enabled DISABLED ACTIVE
SW7 After-run/Safety Edge Mon. enabled DISABLED ACTIVE
SW8 Service Interval Counter DISABLED ACTIVE
Types of Operation
1) Dead man Open / Close - With all DIP Switches OFF the starter will operate in
dead-man condition, I.e. motor will stop when the control button is released
2) Impulse Open / Dead man Close – Move DIP Sw 1 to ON position, starter will
operate as one press to open / press and hold to close
3) Impulse Open / Close – Move DIP Sw 1 and 2 to ON position, starter will operate
as one press open / one press to close
In order to comply with current regulations, this condition must only be used in
conjunction with a monitored safety edge system
Auto-Close Timer
(This must be used in conjunction with a suitable monitored safety edge
system or photocell connected and have DIP Sw 1 and 2 turned on)
The Mini Basic LCCV.2 controller has an auto-close timer that can be set from 1 - 240 seconds;
its factory preset time is 15-seconds:
Adjustment of this time can only be changed using either the ‘ON BOARD’ or ‘MEMBRANE’
buttons it is not possible using an external prewired push button station
To select a different time:
1) Set DIP Sw 3 to ON
2) Press open button and run door to top limit
3) When at top limit position, press and hold both the open and close buttons together for 5
secs – the RED STOP LED will flash to show leaning mode
Wait for the desired time then press the CLOSE pushbutton once, the red STOP LED will turn
off , the time is now stored and the door will immediately close
Go Function
With Dip Sw 4 set to ‘ON’, the Mini Std V7 controller can be run using a single external non-latching
N/O pushbutton connected to the pushbutton ‘OPEN’ terminal
The OPEN pushbutton will now operate OPEN - STOP - CLOSE - STOP in a sequential mode
Safety Edges
The Mini Std V7 controller has been designed so can be used with and to monitor different types of
safety edge, these options include connections for resistive, pneumatic and optical safety edge’s
If a safety device is activated during the close cycle, the controller will immediately stop, briefly
pause then return to the fully open position. If the AUTO-CLOSE timer has been enabled the door
will close again on the expiry of the AUTO-CLOSE time or when the CLOSE button has been
pressed.

Page 5 of 8
Pneumatic Safety edge (not to used on a new installation)
This type of safety edge is not monitored and can become problematic and fail to work
should any air-leaks occur, therefore is not compliantfor new installations and should be
restricted to existing / older installations
1) Ensure the pneumatic safety edge has been fitted correctly and has no air leakage
2) Connect the N/C switch contact to (X4) 17~18
3) Set DIP Sw 7 to ON
4) Set OPEN limit switch as normal and set the CLOSE limit switch to a maximum 50mm
from the fully open position
Electric Safety Edge (8K2 resistive type)
This type of safety edge is monitored by the Mini-Std,It senses any changes to the
resistance value (8k2) flowing through the safety edge
1) Ensure the resistive edge has been correctly assembled and that the resistance value
measurers 8k2
2) Connect each wire from the safety edge to (X4) 15~16
3) Set DIP Sw 5 to ON
4) Set DIP Sw 7 to ON
5) Set OPEN limit switch as normal and set the CLOSE limit switch to a maximum 50mm from
the fully open position
Optical Safety Edge
This type of safety edge is also monitored by the Mini-Std, It consists of a light barrier
transmitter and receiver fitted intoeach end of the safety edge and senses any interruption
to the beam flowing through the safety edge
Only use FRABA compatible optical safety edge
1) Ensure the connections are correct BROWN (+12v) GREEN (signal) WHITE (0v) and they
correspond with the board connections (X4) 19~20~21
2) Set DIP Sw 6 to ON
3) Set DIP Sw 7 to ON
4) Set OPEN limit switch as normal and set the CLOSE limit switch to a maximum 50mm from
the fully open position
Note:
If any safety device is activated during the close cycle, the controller will immediately stop, briefly
pause, and return to the fully open position. If the AUTO-CLOSE timer has been enabled the door
will close again on the expiry of the AUTO-CLOSE time or when the CLOSE button has been
pressed.
After run/Safety Edge Monitoring
. Setting S1 Dipswitch 7 to ON will enable the After-run function.
This uses the Close limit (set 50mm from the floor) as a safety edge override limit.
When the Closed limit is activated the operator electronically overruns this limit (max. of 0.3
seconds) until a signal from the safety edge is received.
If no safety edge signal is received the AMBER Safety Fail LED will flash and the controller
will revert to dead-man until the fault is cleared
Pressing the OWR (override) and CLOSE pushbuttons simultaneously will override the fault
condition.

Page 6 of 8
Service Counter
The Mini Std V7 has a settable service interval counter that can be set via the S1
Dipswitches, each dipswitch equates to a set number.
S1 Dipswitch
D/Sw Count D/Sw Count
1 1,000 5 30,000
2 5,000 6 40,000
3 10,000 7 50,000
4 20,000 8 Not used
Setting the Service Interval Counter:
1) Note and record all S1 Dipswitch settings
2) Set ALL S1 Dipswitches to OFF
3) Set S1 Dipswitch 8 to ON
4) Set only one other S1 Dipswitch to ON
5) Press simultaneously the OWR, CLOSE and OPEN pushbuttons for 3-seconds
6) The Service LED will illuminate for 3-seconds to confirm
7) Return ALL S1 Dipswitches to their original settings and test the door for correct operation
Resetting the Service Interval Counter
1) Press simultaneously the OWR, CLOSE and OPEN pushbuttons for 3-seconds
2) The Service LED will illuminate for 3-seconds to confirm
Disabling the Service Interval Counter
1) Note and record all S1 Dipswitch settings
2) Set ALL S1 Dipswitches to ON
3) Press simultaneously the OWR, CLOSE and OPEN pushbuttons for 3-seconds
4) The Service LED will illuminate for 10-seconds to confirm
5) Return ALL S1 Dipswitches to their original settings and test the door for correct operation
LED Status Indicators
LED Description Colour Status Description of status
D5 POWER Green ON 24VDC supply is ON
D8 SAFETY FAIL Amber Flashing S1 D/SW 6 is ON (but no signal from the
safety edge)
Amber ON Open circuit safety device(s) / incorrectly
set S1 D/SW 5
D10 STOP RED ON Open circuit Stop circuit / incorrectly set
limit switches
RED Flashing Auto-Close Timer learning mode
D12 SPEED/RUNT. Red ON Run Time of door has expired
Red Flashing Service Indicator - Door requires servicing
D14 CLOSE limit switch Amber ON Open circuit limit switch - Close
D15 OPEN limit switch Amber ON Open circuit limit switch - Open
D16 OPEN pushbutton Amber ON OPEN pushbutton is ON
D17 CLOSE pushbutton Amber ON CLOSE pushbutton is ON

Page 7 of 8
EC DECLARATION
OF INCORPORATION
PRODUCT: 3-phase motor controller
MODEL NUMBER: Mini Standard V7
DECLARATION:
The product to which this Declaration of Incorporation relates to must only be put
into service in a completed machine or system that complies with the requirements
of the machinery Directive 2006/42/EC.
The controller meets the following EC Directives:
EMC Directive 2004/108/EC
Low Voltage Directive 2006/95/EC
Harmonised standards:
EN60493-1
EN61000-6-2
EN61000-6-3
EN12453:2001
EN12445
DECLARATION MADE BY: David Butler
Technical Manager
ON BEHALF OF: Ellard Ltd
Roundthorn Industrial Estate
Wythenshawe
Manchester. M23 9NX
Tel: +44(0)61 945 4561
Fax: +44(0)61 945 4566
WWW:ellard.co.uk
Email: sales@ellard.co.uk

Page 8 of 8
Table of contents
Other Ellard Controllers manuals
Popular Controllers manuals by other brands
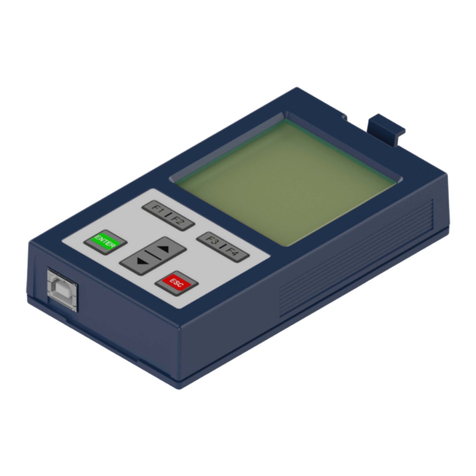
KEBCO
KEBCO COMBIVERT F6 Instructions for use

Timeguard
Timeguard MLB3000 Installation & operating instructions

MB QUART
MB QUART GMR-LED Operator's guide
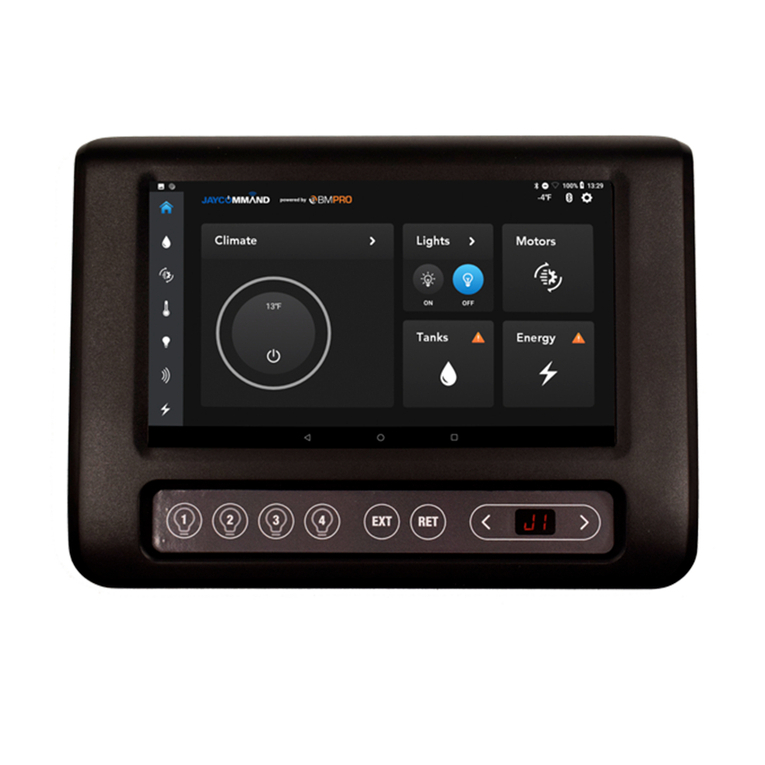
BM PRO
BM PRO JAYCOMMAND owner's manual
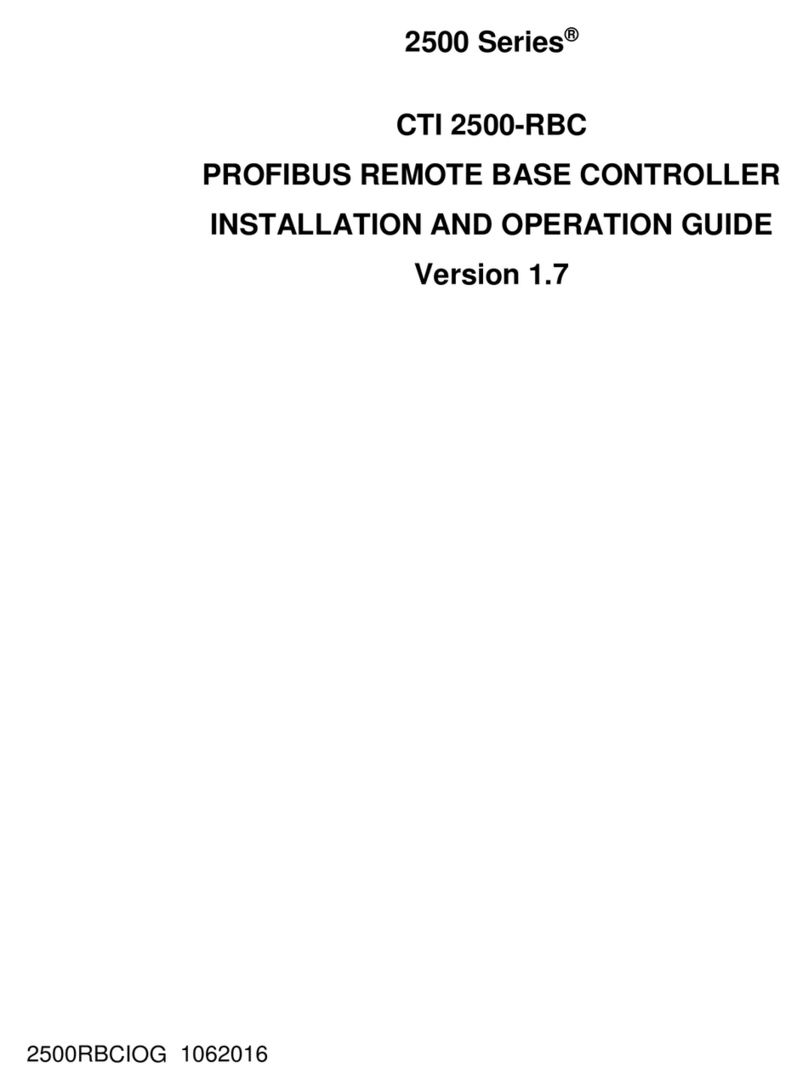
Control Technologies
Control Technologies 2500 Series Installation and operation guide
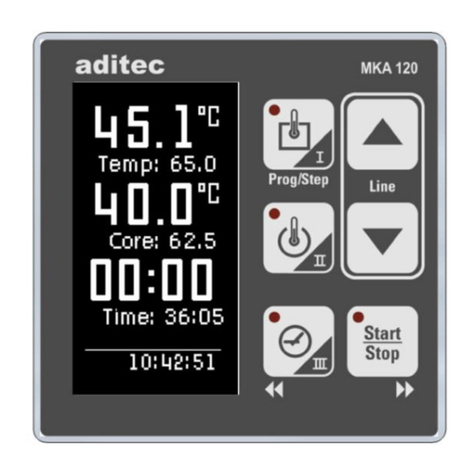
aditec
aditec MKA 120 user manual