Fastwel CPC505 User manual

CPC505
6U Compact PCI CPU Module
User Manual
Rev. 001
November 2022

Product Title: CPC505
Document name: CPC505 User Manual
Manual version: 001
Ref. doc. v.:
Copyright © 2022 Fastwel Co. Ltd. All rights reserved.
Revision Record
Rev. Index
Brief Description of Changes
Board Index
Date of Issue
001
Initial version
CPC505
November 2022
Contact Information
Fastwel Co. Ltd
Fastwel Corporation US
Address:
108 Profsoyuznaya st.,
Moscow 117437,
Russian Federation
6108 Avenida Encinas,
Suite B, Carlsbad,
CA92011, USA
Tel.:
+7 (495) 232-1681 Tel:
+1 (858) 488-3663
Fax:
+7 (495) 232-1654
E-mail:
Web:
http://www.fastwel.com/

CPC505
C P C 5 0 5 U s e r M a n u a l 3 © 2 0 2 2 F a s t w e l v . 0 0 1
Table of Contents
Table of Contents.....................................................................................................................................................3
List of Tables............................................................................................................................................................4
List of Figures ..........................................................................................................................................................5
Notation Conventions............................................................................................................................................... 7
General Safety Precautions..................................................................................................................................... 8
Unpacking, Inspection and Handling........................................................................................................................9
Three Year Warranty ............................................................................................................................................. 10
1Introduction............................................................................................................................................ 11
1.1 System overview......................................................................................................................................... 11
1.2 Module general description......................................................................................................................... 11
2Technical Specifications..........................................................................................................................12
2.1 Main technical characteristics..................................................................................................................... 12
2.2 Module versions.......................................................................................................................................... 15
2.3 Delivery checklist........................................................................................................................................ 15
2.4 Packaging information................................................................................................................................ 16
2.5 System expansion capabilities.................................................................................................................... 16
2.6 System information …...…………………………………………………………………………………………….16
2.7 Appearance and arrangement of elements……………………………………………………………………….17
3Functional description............................................................................................................................ 31
3.1 Features of operation of functional nodes………………………………………………………………………...19
3.2 Module interfaces……………………………………………………………………………………………………22
3.3 Timers………………………………………………………………………………………………………………...36
3.4 SPI/LEDs/GPIO controller………………………………………………………………………………………….38
3.5 Devices on the local SMBus………………………………………………………………………………………..40
3.6 Battery………………………………………………………………………………………………………………...40
3.7 SATA SSD……………………………………………………………………………………………………………40
4Installation.............................................................................................................................................. 41
4.1 Safety requirements.................................................................................................................................... 41
4.2 CPC505 installation procedure ………..…………………………………………………………………………...42
4.3 Board removal procedure ……………………………………………………………………………………...…...43
4.4 Installation of the CPC505 peripheral devices ………………………………………..……………………….…44
4.5 Replacing the battery …………………………………………………………………………………………..……44
4.6 Installation of M.2 SSD ……….………………………………………………………………………..……………45
5System Setup ......................................................................................................................................... 46
5.1 Resetting BIOS settings ….…………………………………………………………………………………...........46
5.2 Updating BIOS………………………………………………………………………………………………………..46
6AMI Aptio BIOS Setup.................................................................................................................... ……..47
6.1 Starting and updating the BIOS Setup program….………………………………………………………...........47
6.2 Main……………………………………………………………………………………………………………………49
7Troubleshooting..................................................................................................................................... 50
8 Power consumption …………………………………………………………………………………………………….…51
9 Exposure to external factors………………….......……………………………………………………………………...52
9.1 Temperature mode…………………………………………………………………………………………………..52
9.2 Operating conditions and MTBF……………………………………………………………………………………53
ANNEX A: RIO587 Rear I/O Module……………………………………………………………………………………………...54
A1: Introduction…………………………………………………………………………………………………………...54
A2: RIO587 versions……………………………………………………………………………………………………..54
A3: RIO587 delivery checklist…………………………………………………………………………………………...55
A4: RIO587 packaging information……………………………………………………………………………………..55
A5: Structure of I/O channels of RIO587……………………………………………………………………………….56
A6: Appearance and layout of RIO587 elements……………………………………………………………………..57
A7: Features of operation of RIO587 functional nodes………………………………………………………………63

CPC505
C P C 5 0 5 U s e r M a n u a l 4 © 2 0 2 2 F a s t w e l v . 0 0 1
A8: RIO587 connectors………………………………………………………………………………………………….64
A9: Configuring and preparing the RIO587 module for operation………………………………………………….72
A10: RIO587 operating conditions and MTBF………………………………………………………………………….74
ANNEX B: MIC1901 mezzanine module…………………………….…………………………………………………………..75
B1: Introduction…………………………………………………………………………………………………………..75
B2: I/O Channel Structure of the MIC1901……………………………………………………………………………75
B3: Temperature range of the MIC1901………………………………………………………………………………75
B4: Appearance of the MIC1901 and layout of main elements……………………………………………………..76
B5: Information on MIC1901 packaging……………………………………………………………………………….79
B6: Delivery checklist of the MIC1901…………………………………………………………………………………79
B7: Specific performance features of the MIC1901 functional nodes……………………………………………...79
B8: Pinout charts of the MIC1901 connectors………………………………………………………………………..79
B9: Installation and preparation of the MIC1901 for operation……………………………………………………...80
B10: Operating Conditions of the MIC1901 and MTBF……………………………………………………………….83
ANNEX C: Terms and abbreviations ……………………………………………………………………………………….....84
ANNEX D: DISCLAIMER………………………………………………………………………………………………………….87
List of Tables
Table 2-1: Supply voltage of +5 V, +3.3 V from the CPCI bus..........................................................................14
Table 2-2: Maximum permissible consumption currents...................................................................................14
Table 2-3: Module versions ..............................................................................................................................15
Table 2-4: System information ……………………………………………………………..………………………….16
Table 3-1: Assignment of XMC XS4 (P15) connector pins ...……………………………………………………….22
Table 3-2: Assignment of XMC XS5 (P16) connector pins ……………………………………………………...….23
Table 3-3: Assignment of pins of the PMC XS2 (P1), XS3 (P3), XS6 (P2) and XS7 (P4) connectors ………...24
Table 3-4: Assignment of the M.2 XP5 connector pins ……………….…………………………………………….25
Table 3-5: Assignment of USB connectors pins on the front panel of the CPC505……..……………………….26
Table 3-6: Assignment of the Gigabit Ethernet connector pins …………………………………………………….27
Table 3-7: Assignment of the XS5 connector pins (DVI) of the CPC505 module …………………………….….28
Table 3-8: Assignment of the XS6 DisplayPort connector pins of the CPC505 module ………………………...29
Table 3-9: State of the SYS LED ………………………………...…………………………………………………....29
Table 3-10: Color code designations of connectors………….………………………………………………………..32
Table 3-11: Assignment of pins of the CompactPCI XS18 (J1) system connector …..……………………………32
Table 3-12: Assignment of the pins of XS16 (J2) system connector of 64-bit CompactPCI bus …..………….…33
Table 3-13: Assignment of XS11 (J3) connector pins of the CPC505…..…………………………………………..34
Table 3-14: Assignment of the XS8 (J4) connector pins of the CPC505……... ...………………………………....34
Table 3-15: Assignment of the XS1 (J5) connector pins of the CPC505……………………. ……………………..35
Table 3-16: Registers of SPI controller……………………………………. ……..……………………………………38
Table 3-17: Addresses of devices on SMBus ……………………………………………….…..………………….…40
Table 7-1: CPC505 fault causes and their troubleshooting ……………………………………………………..….50
Table 9-1: Processor frequency vs. temperature (for CPC505-01)……………………………………………...…52
Table 9-2: Environmental exposure when operating CPC505 ……………………………………………………..53
Table A-1: RIO587 versions ...………………………………..……………............................................................54
Table A-2: RIO587 temperature range (industrial and commercial version)………………………….…………..54
Table A-3: Weight of the RIO587-01 and RIO587-02 modules………………... ……..…………………………...55
Table A-4: Interfaces on rear panel of the RIO587-01 version…………...…………………..………………….…56
Table A-5: Additional interfaces on the rear panel of the RIO587-02 version ...………………………………….57
Table A-6: Additional interfaces at mezzanine connection …..………………. ...………………………………....59
Table A-7: Assignment of pins of the TH-4M connectors (XP3 and XP4) for feeding power to the CPC505....64
Table A-8: Assignment of pins of the PS/2 connector (XS4) for keyboard/mouse..……...………………………64
Table A-9: Assignment of the XP6 connector pins: COM1 port (RS232)………..…………..………………….…65
Table A-10: Assignment of pins of the XS11 connector: LPT port (IDC-26)….…………………………………….65
Table A-11: Assignment of pins of the XP10-XP12 connectors (COM2-COM4)………………………………...…66
Table A-12: Assignment of pins of the XP7 connector (COM5, RS485)………………………..…………………..66
Table A-13: Assignment of pins of the XP8 connector (COM6, RS485)…..………………………..……………....66
Table A-14: Assignment of the XP15 (SATA) connector pins ……..…………………………………….…………..67
Table A-15: Assignment of the ХS8 HDD …………………………….…………... ……..…………………………...67
Table A-16: Assignment of the CFast (XS5) card connector pins ….……..…………………..………………….…69
Table A-17: Assignment of the XP5 connector pins (GPIO and 3.3V power supply)………………………... ..….70
Table A-18: Assignment of the XP16 connector pins (LVDS) .…………………………………………..…………..71
Table A-19: Assignment of the XP19 connector pins (LCD panel backlight)………………………………….…....72
Table A-20: Power supply requirements for the RIO587…………………………………………..….….…………..73

CPC505
C P C 5 0 5 U s e r M a n u a l 5 © 2 0 2 2 F a s t w e l v . 0 0 1
Table A-21: Current consumption of the modules………………………………………………………………. .…...73
Table A-22: Exposure of external factors during operation of the RIO587……………………… …..………….…74
Table B-1: Interfaces on the front panel of the MIC1901 module ………………………………………………….75
Table B-2: Temperature range of the MIC1901 …………………………...…………………..………………….…75
Table B-3: MIC1901: Overall dimensions …………………………………………………………………………….78
Table B-4: Assignment of pins of the CFast (XS8) card connector …………………………... .………………....80
Table B-5: Assignment of pins of the Mic, LineIn, LineOut connectors (XS3)………….………………….. …....80
Table B-6: Power supply requirements of the MIC1901 …………………………………………………………....81
Table B-7: MIC1901 operating conditions ………………………………………………………...…………… .…...83
List of Figures
Figure 2-1: Block diagram………………………………………………………………………………………………...17
Figure 2-2: Overall dimensions and location of main components of the device….……………………………......18
Figure 3-1: XMC XS4 (P15) and XS5 (P16) connectors …..………………..…………………………….…………..22
Figure 3-2: The PMC XS2 (P1), XS3 (P3), XS6 (P2) and XS7 (P4) connectors. ……..…………………………...23
Figure 3-3: USB connectors on the front panel of CPC505……..…...……..…………………..………………….…26
Figure 3-4: Connector 2.5 Gigabit Ethernet…….…………………………………………………… .………………..27
Figure 3-5: DVI-I connector…………………………. ……………………………………………………………..…....27
Figure 3-6: DisplayPort connector …………………………………………………………………… .………………..28
Figure 3-7: LED indicators on the front panel ……...……………………………………………………………..…....29
Figure 3-8: CompactPCI connectors (J1–J5 in accordance with the CompactPCI specification.………………..31
Figure 6-1: Assignment of navigation keys………... ……………………………………………………………..…....47
Figure 6-2: Screen of the Main menu …………………...…………………………………………… .………………..49
Figure A-1: Block diagram of RIO587…………….. ……………………………………………………………..…......58
Figure A-2: RIO587-01 (4HP height)………………………………………………………….………..………………..60
Figure A-3: RIO587-02 (8HP height)………………………………………………………………………………….....61
Figure A-4: Designation of RIO587 key components on the top view ………………………………………...….....62
Figure A-5: RIO587-01 with the mounted SATADOM drive ………………………………….…… .………………..68
Figure A-6: RIO587-02 with the installed HDD 2.5"……………. ………….…………………………………..…......69
Figure B-1: Block diagram MIC1901……………………………….………………………………… .………………..76
Figure B-2: Designation of the MIC1901 main components in the bottom view………………… .………………..77
Figure B-3: Layout of the MIC1901 main components on the bottom view ………………………………………...77
Figure B-4: MIC1901: mounting and outside dimensions …………………………………………………...….….....78
Figure B-5: MIC1901: front panel with designation of connectors ………………………………….………………..78
Figure B-6: Schematic representation of the CPC505 with the MIC1901 installed…………………………….......81
Figure B-7: View of the CPC505 front panel with the MIC1901 module installed……………………………....…..82
Figure B-8: Designation of fixing positions on the MIC1901 (bottom view)…..……………………………….….....82
Figure B-9: Installation of holders to MIC1901……..…………………………………………..…… .………………..83
All information in this document is provided for reference only, with no warranty of its suitability for any specific purpose. This information has been thoroughly checked and
is believed to be entirely reliable and consistent with the product that it describes. However, Fastwel accepts no responsibility for inaccuracies, omissions or their
consequences, as well as liability arising from the use or application of any product or example described in this document.
Fastwel Co. Ltd. reserves the right to change, modify, and improve this document or the products described in it, at Fastwel's discretion without further notice. Software
described in this document is provided on an “as is” basis without warranty. Fastwel assumes no liability for consequential or incidental damages originated by the use of
this software.
This document contains information, which is property of Fastwel Co. Ltd. It is not allowed to reproduce it or transmit by any means, to translate the document or to convert
it to any electronic form in full or in parts without antecedent written approval of Fastwel Co. Ltd. or one of its officially authorized agents.
Fastwel and Fastwel logo are trademarks owned by Fastwel Co. Ltd., Moscow, Russian Federation. Ethernet is a registered trademark of Xerox Corporation. IEEE is a
registered trademark of the Institute of Electrical and Electronics Engineers Inc. Intel is a trademark of Intel Corporation. Microsoft is a trademark of the Microsoft
corporation. In addition, this document may include names, company logos and trademarks, which are registered trademarks and, therefore, are property of their
respective owners. Fastwel welcomes suggestions, remarks and proposals regarding the form and the content of this Manual.

CPC505
C P C 5 0 5 U s e r M a n u a l 6 © 2 0 2 2 F a s t w e l v . 0 0 1
Ownership rights
This document contains information that is the property of Fastwel Group. It may not be copied or
transmitted by any known means, nor may it be stored in information storage and retrieval systems
without the prior written consent of Fastwel Group or one of its authorized agents. The information
contained in this document, to the best of our knowledge, is free from any errors, however, Fastwel
Group accepts no responsibility for any inaccuracies and their consequences, as well as liability
arising from the use or application of any diagram, product or example given in this document.
Fastwel Group reserves the right to change and improve both this document and the product
presented inside of it at its discretion without any further notice.
Safety requirements
This Fastwel Group’s product is developed and tested for the purpose of ensuring compliance to
the electric safety requirements. Its design provides long-term trouble-free operation. The service
life of the product can be significantly reduced due to the improper handling during unpacking and
installation. Therefore, in the interests of your safety and in order to ensure proper operation of the
product, you should follow the recommendations below.

CPC505
C P C 5 0 5 U s e r M a n u a l 7 © 2 0 2 2 F a s t w e l v . 0 0 1
Notation Conventions
Warning, ESD Sensitive Device!
This symbol draws your attention to the information related to electro static
sensitivity of your product and its components. To keep product safety and
operability it is necessary to handle it with care and follow the ESD safety
directions.
Warning! Hot surface!
This sign and inscription warns of the dangers associated with touching hot
surfaces of the product.
Caution: Electric Shock!
This symbol warns about danger of electrical shock (> 60 V) when touching
products or their parts. Failure to observe the indicated precautions and
directions may expose your life to danger and may lead to damages to your
product.
Warning!
Information marked by this symbol is essential for human and equipment
safety. Read this information attentively, be watchful.
Note
This symbol and title marks important information to be read attentively for
your own benefit.

CPC505
C P C 5 0 5 U s e r M a n u a l 8 © 2 0 2 2 F a s t w e l v . 0 0 1
General Safety Precautions
This product was developed for fault-free operation. Its design provides conformance to all related
safety requirements. However, the life of this product can be seriously shortened by improper
handling and incorrect operation. That is why it is necessary to follow general safety and
operational instructions below.
Warning!
All operations on this device must be carried out by sufficiently
skilled personnel only.
Caution: Electric Shock!
Before installing this product into a system and before installing
other devices on it, always ensure that your mains power is switched
off.
Always disconnect external power supply cables during all handling
and maintenance operations with this module to avoid serious
danger of electrical shock. This also applies to the other power
supply cables.

CPC505
C P C 5 0 5 U s e r M a n u a l 9 © 2 0 2 2 F a s t w e l v . 0 0 1
Unpacking, Inspection and Handling
Please read the manual carefully before unpacking the module or mounting the device into your
system. Keep in mind the following:
ESD Sensitive Device!
Electronic modules and their components are sensitive to static
electricity. Even a non-perceptible by human being static discharge
can be sufficient to destroy or degrade a component's operation!
Therefore, all handling operations and inspections of this product
must be performed with due care, in order to keep product integrity
and operability:
Do not leave the product without its protective packaging when it is not in use.
If possible, always work with the products in a workplace that is protected against static
electricity. If this is not possible, the user should remove static discharge from the user before
touching the product with their hands or tool, which is best performed by touching the metal part
of the of the system housing.
It is especially important to take precautions when replacing expansion boards expansion
boards, jumpers, etc. If the product has batteries to power the memory or real-time clock, do not
place the board on conductive surfaces, such as antistatic mats or sponges. They may cause a
short circuit and result in damage to the board. short-circuit and cause damage to the battery
and the board's conductive circuits.
General rules for using the device
■The product must not be altered or modified in any way in order to maintain the warranty. Any
unauthorized modifications and improvements other than those given in this manual or received
from DOLOMANT Technical Support as a set of instructions for their execution will void the
warranty.
■This device must only be installed and connected to systems that meet all necessary technical
and climatic requirements. This also applies to the operating temperature range of the specific
version of the board. The temperature limitations of the batteries installed on the board must also
be taken into account.
■Follow the instructions in this manual only when carrying out all necessary installation and setup
operations.
■Retain the original packaging for storing the product in the future or for transportation in case of
warranty. In case it is necessary to transport or store the board, pack it in the same way as it was
packed when you received it.
■This device must only be installed and connected to systems that meet all necessary technical
and climatic requirements. This also applies to the operating temperature range of the specific
version of the board. The temperature limitations of the batteries installed on the board must also
be taken into account.

CPC505
C P C 5 0 5 U s e r M a n u a l 10 © 2 0 2 2 F a s t w e l v . 0 0 1
Three Year Warranty
Fastwel Co. Ltd. (Fastwel), warrants that its standard hardware products will be free from defects
in materials and workmanship under normal use and service for the currently established warranty
period. Fastwel’s only responsibility under this warranty is, at its option, to replace or repair any
defective component part of such products free of charge.
Fastwel neither assumes nor authorizes any other liability in connection with the sale, installation
or use of its products. Fastwel shall have no liability for direct or consequential damages of any
kind arising out of sale, delay in delivery, installation, or use of its products.
If a product should fail through Fastwel's fault during the warranty period, it will be repaired free of
charge. For out of warranty repairs, the customer will be invoiced for repair charges at current
standard labor and materials rates.
Warranty period for Fastwel products is 36 months since the date of purchase.
For custom-made products, the warranty period is 60 months from the date of sale (unless
otherwise specified in the supply agreement).
The warranty set forth above does not extend to and shall not apply to:
1. Products, including software, which have been repaired or altered by other than
Fastwel personnel, unless Buyer has properly altered or repaired the products in
accordance with procedures previously approved in writing by Fastwel.
2. Products, which have been subject to power supply reversal, misuse, neglect,
accident, or improper installation.
Returning a product for repair
1. Apply to Fastwel company or to any of the Fastwel's official representatives for the
Product Return Authorization.
2. Attach a failure inspection report with a product to be returned in the form, accepted by
customer, with a description of the failure circumstances and symptoms.
3. Carefully package the product in the antistatic bag, in which the product had been
supplied. Failure to package in antistatic material will VOID all warranties. Then
package the product in a safe container for shipping.
4. The customer pays for shipping the product to Fastwel or to an official Fastwel
representative or dealer.

CPC505
C P C 5 0 5 U s e r M a n u a l 11 © 2 0 2 2 F a s t w e l v . 0 0 1
1 Introduction
1.1 System overview
The CompactPCI processor module (CPCI) presented in this User Manual supports the PCI
architecture. This gives you the ability to work with a wide range of equipment. For information on
the CompactPCI standard, please refer to the PCI and CompactPCI Standards Specifications. For
more information on these standards and how to use them, please visit the PCI Industrial
Computer Manufacturers Group (PICMG) website at: http://www.picmg.org/.
1.2 Module General Description
The CPC505 processor module is designed to provide customers with a highly integrated x86
platform solution in 6U CompactPCI format for use in real-time, production control, high-speed data
acquisition and processing applications. The module is based on 9th generation Intel Xeon and
Core processors with an integrated graphics engine.
The CPC505 uses the CM246 chipset, which has the latest set of interfaces, including PCI Express
3.0, SATA 3.0, USB 3.1, etc. The graphics engine integrated into the processor provides the
module with great opportunities when working via DisplayPort, DVI-I, LVDS video interfaces.
Up to 32 GB of DDR4 RAM with ECC can be installed on the module.
The CPC505 supports one 64-bit 66 MHz CompactPCI interface. The board interacts with the bus
CompactPCI through integrated bridge PCI-E <-> PCI.
One of the CPC505 features is support for the PICMG CompactPCI Packet Switching Backplane
Specification version 2.16. Installed in a backplane that supports packet switching mode, the
CPC505 can communicate via the two Gigabit Ethernet ports attached to it with other peripheral
devices or with a main system card that also supports this mode.
Due to the stability of CPC505, the device can be used in all industrial applications. The
components on which the CPC505 is based are carefully selected for their use in embedded
systems and long-term availability on the market, making it an ideal device on which to build
systems with a long lifecycle.
The CPC505 is compatible with operating systems such as Windows 10 and Debian 10.

CPC505
C P C 5 0 5 U s e r M a n u a l 12 © 2 0 2 2 F a s t w e l v . 0 0 1
2 Technical Specifications
2.1 Main technical characteristics
Intel Xeon E-2276ML 2.0GHZ 25W processor (Coffee Lake-H Refresh):
6 x cores Intel x64, 12 x threads;
3 x graphics engines;
12 MB cache;
Intel Core i3-9100HL 1.6GHZ 25W processor (Coffee Lake-H Refresh):
4 x cores Intel x64, 4 x threads;
3 x graphics engines;
6 MB cache;
RAM:
DDR4-2666 SDRAM 32 GB, with ECC support;
Memory bus width 64 bit;
Video output:
DVI-I interface (1920x1200@60Hz), routed to the front panel;
DisplayPort interface (4096x2304@60Hz), routed to the front panel;
DisplayPort interface (4096x2304@60Hz), routed to RIO;
LVDS interface (1920x1200@60Hz), routed to RIO;
Simultaneous operation of three interfaces is possible.
PCI bus:
Routed to the CompactPCI J1/J2 connectors;
64 bit /66 MHz;
Implemented on the PCIe->PCI-X PI7C9X130 bridge;
HotSwap support;
Operation in the peripheral slot (Non-transparent Bridge mode);
LPC bus:
Routed to the P16 XMC connector;
Routed to RIO;
PCIe bus:
PCIe Gen3 (up to 8GT/s), routed to the P15 XMC connector with support of the
devices up to x8;
PCIe Gen2 (up to 5GT/s), routed to the CPCI J3/P3 connector, with support of
the devices up to x4;
XMC is compatible with the ANSI/VITA 42.3 specification;
SMBus:
Compatibility with the 2.0 specification;

CPC505
C P C 5 0 5 U s e r M a n u a l 13 © 2 0 2 2 F a s t w e l v . 0 0 1
Rate up to 100 Kb/sec;
Flash BIOS:
2x128 Mb SPI-Flash;
Modifiable in the system.
FRAM:
Capacity 32 KB;
Implemented on SPI bus;
Integrated SATA SSD:
Capacity 32 GB;
Interface SATA III 6 Gb/sec;
Support of the drives of M.2 2280 standard (PCIe x4 Gen3);
SATA interface:
One interface is routed to the P16 XMC connector;
One interface is used for the connection of integrated SSD;
Two interfaces are routed to RIO;
SPI interface:
FRAM support;
Frequency up to 25 MHz;
4 x LAN 10/100/1000 Mb ports on PCIe x4 Gen2:
Two channels are routed to RIO connector;
Two channels are routed to the P16 XMC connector;
Support of the PICMG 2.16 standard;
Intel® Ethernet Controller I350 is used;
2 x LAN 10/100/1000/2500 Mb ports on i225 controllers:
Support of rates up to 2.5 Gb/sec. on 5еcat. cable;
USB ports:
Support of USB 2.0 (480 Mb/sec), USB 3.0 (5 Gb/sec), USB 3.1 (10 Gb/sec);
Connection of up to 4 x devices via front panel connectors (USB 3.0);
2 x interfaces USB 3.1 are routed to the P16 XMC connector;
6 x USB 2.0 interfaces are routed to RIO;
Real Time Clock:
Powered from the lithium battery CR2032 (3V);
Audio support:
HD Audio interface is routed to the P16 XMC and RIO connectors;
COM port:
The COM0 port is routed to the connector on the board, and a D-SUB plug can
be installed in the XMC mezzanine front panel cutout if necessary. In this case
using the XMC mezzanine is not possible;
Watchdog Timer:
Internal, with program control possibility;
Hardware monitor:

CPC505
C P C 5 0 5 U s e r M a n u a l 14 © 2 0 2 2 F a s t w e l v . 0 0 1
Implemented via the PECI/SMBUS interfaces;
Monitoring of three supply voltages;
Monitoring of CPU temperature;
Monitoring of PCB temperature;
Support of XMC/PMC expansion boards:
Support of one PMC/XMC module;
PCI-X 64bit/133MHz bus is routed to the P1-P4 PMC connector (ANSI/VITA 39,
PCI-X on PMC);
PMC I/O P4 is routed to RIO (PICMG 2.0);
PCIe x8 Gen3 bus is routed to the P15 XMC connector (ANSI/VITA 42.3, XMC
PCI Express Protocol Standard);
Additional interfaces (1xSATA, 2xUSB, LPC, HD Audio, 2xEthernet) are routed to
the P16 XMC connector;
Indication:
Board startup diagnostics LED/ Hot-Swap LED;
SATA drives access LED;
Two software-controlled LEDs (user LEDs);
Software compatibility:
Linux Debian 10;
Astra Linux Special Edition, “Smolensk” release v1.5, v1.6;
Microsoft Windows 10 IoT Enterprise 64bit;
Power supply:
The +5 V, +3.3 V supply voltages from the CPCI bus and their maximum
permissible current consumption are shown in Table 2-1, Table 2-2;
Table 2-1 –Supply voltage of +5 V, +3.3 V from the CPCI bus
Voltage (V)
Minimum (V)
Maximum (V)
+5
4.75
5.25
+3.3
3.15
3.46
Table 2-2 –Maximum permissible consumption currents
Voltage, V
Minimum
voltage, V
Maximum
voltage, V
Maximum
consumption
current, A
+5
4.75
5.25
7
+3.3
3.1
3.5
3
Note:
Table 2-2 shows the maximum values of current consumption of the module when
loaded with synthetic tests.
Operating temperature:
Industrial version: from -40°C to +85°C;
Resistance to cyclic wet heat where there is a conformal coating:

CPC505
C P C 5 0 5 U s e r M a n u a l 15 © 2 0 2 2 F a s t w e l v . 0 0 1
At air temperature + (55±2) °C, relative humidity (93±3)%.;
Resistance to single shock/vibration:
30g/2g;
Module overall dimensions, range, mm:
266±0.5 × 212.5±1.5 × 20.8±0.2;
Weight, no more than:
0.700 kg;
2.2 Module versions
The module versions are specified in the Table 2-3.
Table 2-3 –Module versions
Description of the supplied configurations:
CPC505-01 –CPC505 CPU - Module, Intel Xeon E-2276ML 2.0 GHz, 6 x cores, 32 GB DDR4
SDRAM, from -40 °C to +85 °C;
CPC505-02 –CPC505 CPU - Module, Intel Core i3-9100HL 1.6 GHz, 4 x Cores, 16 GB DDR4
SDRAM, from - 40 °C to +85 °C;
Note:
The modules with conformal coating option have a “\СOATED” caption added to the
name when ordered.
2.3 Delivery checklist
The delivery checklist includes:
1 Module;
2 Installation kit IMES.467941.056 containing:
1) IMES.711141.007 rack - 1 pcs;
2) Screw DIN7985 M2х4-A2 - 1 pcs;
3) Screw DIN7985 M2х6-A2 - 1 pcs;
3 Packaging.
Item
number
Version
Processor
Memory
Temperature
range
1
CPC505-01
Intel Xeon E-2276ML 2.0 GHz 6C/12T 25W
32GB 2666 DDR4
-40…+85 °C
2
CPC505-02
Intel Core i3-9100HL 1.6 GHz 4C/4T 25W
16GB 2666 DDR4
-40…+85 °C

CPC505
C P C 5 0 5 U s e r M a n u a l 16 © 2 0 2 2 F a s t w e l v . 0 0 1
2.4 Packaging information
The CPC505 module is supplied in in a box 350х260х70 mm in size. The packed weight of the
device is max. 1.050kg.
Note
Retain the anti-static packaging and consumer packaging of the module in its original condition
until the end of the warranty period.
2.5 System expansion capabilities
The number of interfaces routed from the CPC505 module can be increased by
▪ installing the XMC/PMC expansion module;
▪ connecting the RIO587 module.
2.5.1 PMC/XMC modules
The PMC/XMC interface of the CPC505 board supports XMC/PMC expansion modules, which
makes it possible to easily and flexibly adapt CPC505 to the requirements of different applications
(see subparagraph 3.2.1 PMC/XMC Interface). One possible expansion module is the MIC1901
(please, see Annex B).
2.5.2 Rear I/O expansion module RIO587
The RIO587 module expands functionality and I/O capabilities of the CPC505 when installed at the
rear of the system chassis. See Annex A for a description of the RIO587 module.
2.6 System information
Table 2-4 –System information
Characteristics
Note
Operating in a system slot as a
system master board (System
Master)
The CPC505 module is designed to be used as a system master. As such, it
can communicate with up to 7 peripheral boards via a 64-bit 33/66 MHz bus. At
the same time, the CPC505 can also operate in a peripheral slot, in which case
the CPC505 is connected to the PCI bus via a “non-transparent” bridge.
Operating in a peripheral
system slot
When installed in the peripheral slot of the system, the CPC505 module is
connected to the PCI bus through the “non-transparent” bridge. The CPC505 is
powered by the backplane and can operate with a Rear I/O board as well as in
packet switching mode (if that mode is supported by the system) with support
for up to two Gigabit Ethernet channels.

CPC505
C P C 5 0 5 U s e r M a n u a l 17 © 2 0 2 2 F a s t w e l v . 0 0 1
Operating systems
CPC505 is compatible with the following operating systems:
Linux Debian 10;
Windows 10.
2.7 Appearance and arrangement of elements
2.7.1 Block diagram
Block diagram is shown in Figure 2-1.
Figure 2-1 –Block diagram

CPC505
C P C 5 0 5 U s e r M a n u a l 18 © 2 0 2 2 F a s t w e l v . 0 0 1
2.7.2 Overall dimensions and arrangement of main components
Figure 2-2 –Overall dimensions and location of main components of the device

CPC505
C P C 5 0 5 U s e r M a n u a l 19 © 2 0 2 2 F a s t w e l v . 0 0 1
3 Functional description
3.1 Features of operation of functional nodes
CPU Intel Xeon E-2276ML / Intel Core i3-9100HL
64-bit Intel microprocessor, manufactured in accordance with the 14 nm process technology, with
TDP of 25 W. Includes up to 6 improved 9th generation Intel Xeon / Core i3 cores, dual-channel 64-
bit DDR4 SDRAM memory controller (up to 32 GB, 2666) with ECC support, advanced graphics
subsystem with 2D/3D acceleration GT2, input/output subsystem PCI-Ex16 Gen3. State-of-the-art
DDI high-speed graphics interfaces.
The processor is made in BGA1440 socket with a size of 42x28 mm.
PCH Intel CM246
Highly integrated interface controller that includes standard peripherals of IBM PC AT platform and
modern high-speed interfaces PCI-E Gen3, SATA 6Gps, USB 2.0/3.1. Implemented in the BGA874
enclosure.
DDR4 SDRAM
The board can be equipped with (soldered) 36 x DDR4 2666 SDRAM chips with a total capacity of
up to 32 GB. Operating mode is dual-channel with ECC support.
BIOS
2 x 128 Mb SPI-Flash microchips are used to store the main (working) copy of the BIOS.
RTC, CMOS
The real time clock is built into the PCH CM246. The clock functionality is ensured by a CR2032
lithium battery that is mounted on the board when the power supply is switched off. BIOS settings
are stored in non-volatile FRAM.
SPI FRAM
Non-volatile 32 KB memory (Ramtron, FM25L256, SPI) needed to store user data (used as a
substitute for the standard non-volatile RAM). The manufacturer guarantees 100 trillion read/write
cycles, which as a part of this application corresponds to ~340 years of operation (in case of
continuous cyclic read/write procedure).
BGA SSD
The board has a 32GB SATA III 6 Gbps SSD in a 16 x 20 mm Jedec MO-276 TFBGA enclosure.
Ethernet

CPC505
C P C 5 0 5 U s e r M a n u a l 20 © 2 0 2 2 F a s t w e l v . 0 0 1
The module has 6 x integrated Gigabit Ethernet interfaces. 2 of them are routed to the P16 XMC
connector, another 2 are routed to the backplane (PICMG 2.16). The XMC has an MDI link. The
interfaces are implemented on a high-speed i350 server controller. Two of the interfaces are on the
front panel and are based on the new Intel i225 adapter that supports transfer rates up to 2.5 Gb/s
over the widely used cables of the 5e category.
USB 2.0
The device has 6 x USB 2.0 channels, routed to RIO.
USB 3.0
The board has 4 x USB 3.0 channels, routed to the type A USB of the front panel.
USB 3.1
The board has 2 x USB 3.1 channels routed to the XMC.
SATA
3 x interfaces for connecting the drives: 1 x interface is routed to the P16 XMC connector, 2 x
interfaces are routed to the RIO connector.
M.2 2280
The module supports M.2 2280 removable drives (PCI Express x4 Gen3 interface).
DVI-I
Designed to connect analog VGA (1920x1200@60Hz) or digital DVI (1920x1200@60Hz) displays.
LVDS
Supports panels up to 1920x1200@60Hz.
DisplayPort
These interfaces are designed to connect digital displays up to 4096x2304@60Hz. One interface is
on the front panel and another one is on the RIO.
PCI Express
The PCIe Gen3 bus is routed to the P15 XMC connector in ANSI/VITA 42.3 standard. The
interface allows you to connect XMC expansion modules with a set of x1, x2, x4, x8 links.
The PCIe x4 bus is on the CPCI J3/P3 connector.
Table of contents
Other Fastwel Computer Hardware manuals
Popular Computer Hardware manuals by other brands
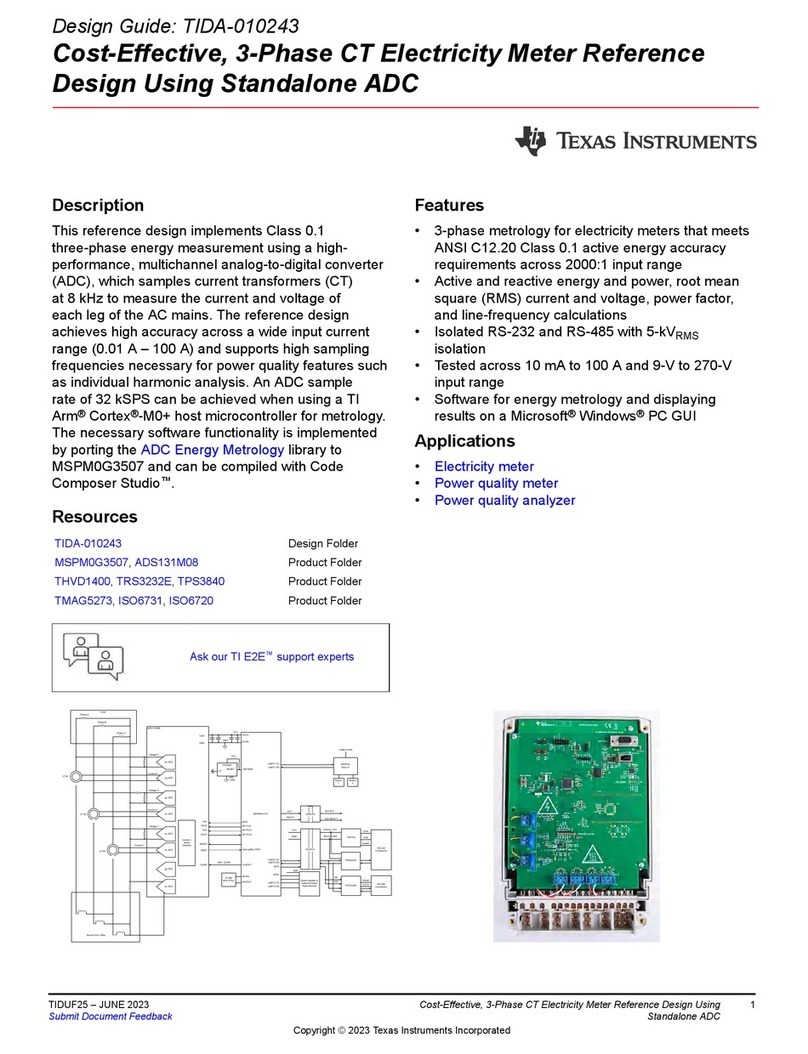
Texas Instruments
Texas Instruments TIDA-010243 Design guide
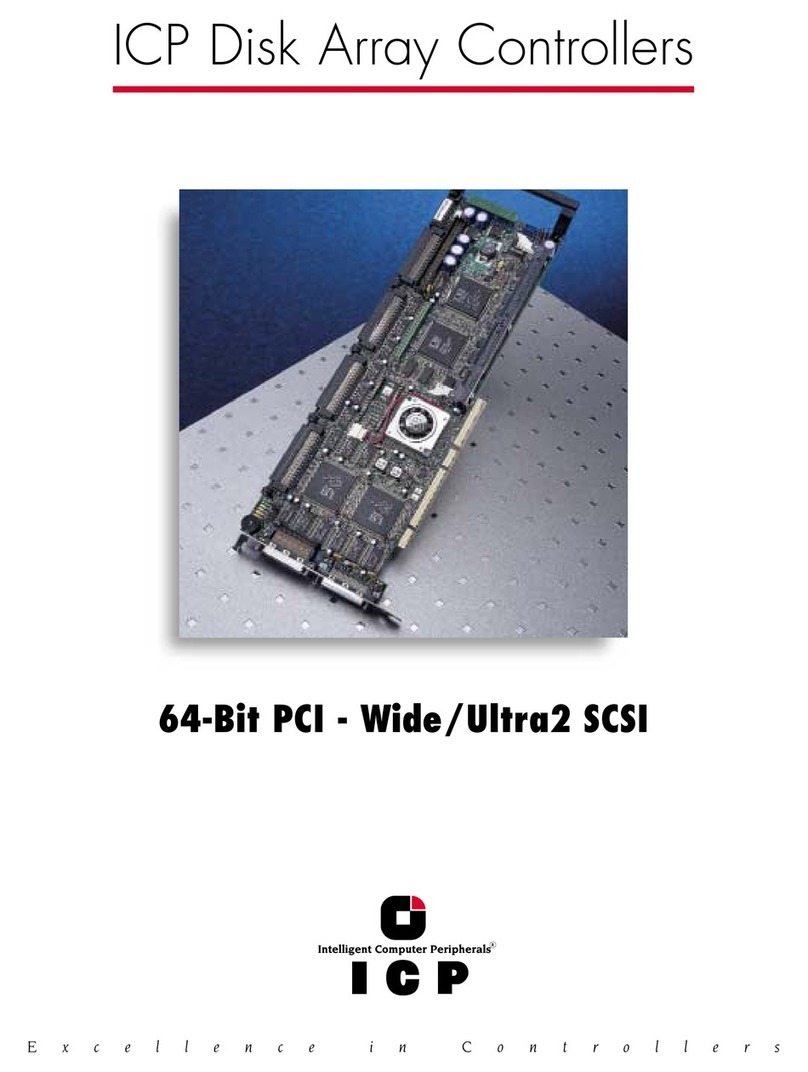
ICP vortex Corporation
ICP vortex Corporation 64-Bit PCI - Wide/Ultra2 SCSI specification
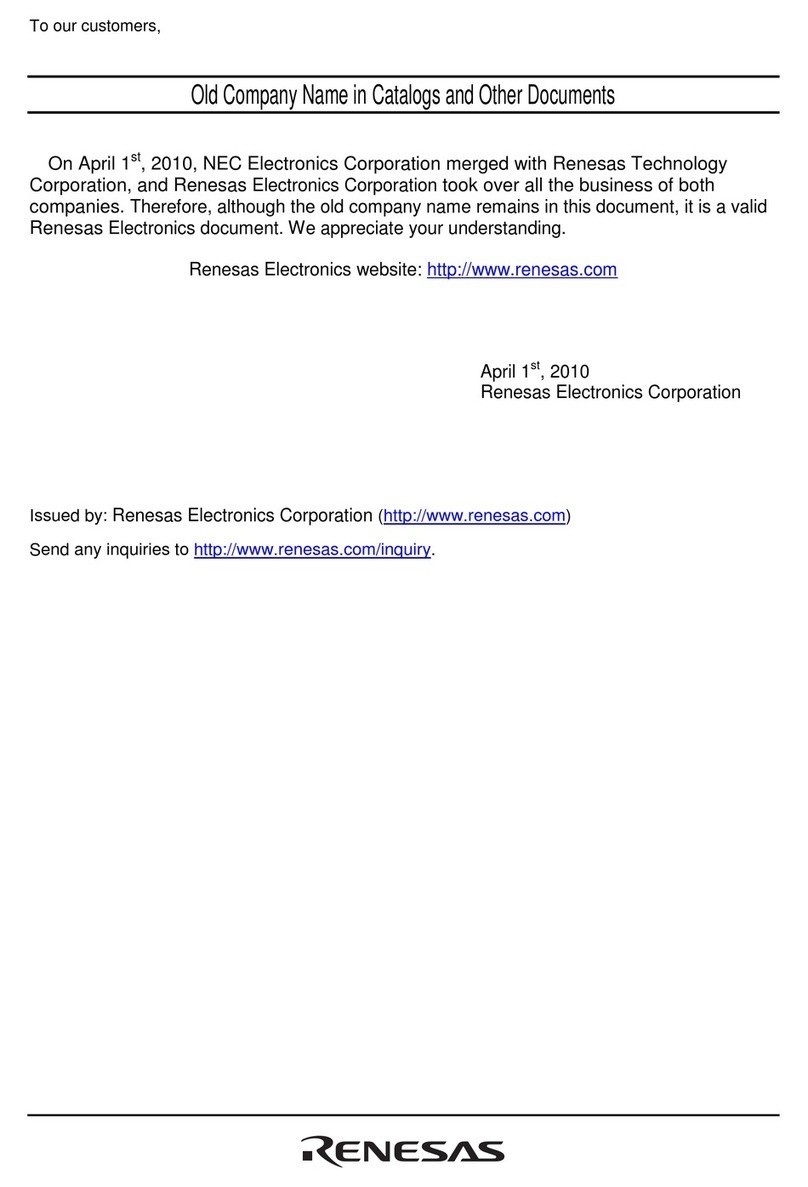
Renesas
Renesas Converter Board R0E5212BACFG00 user manual
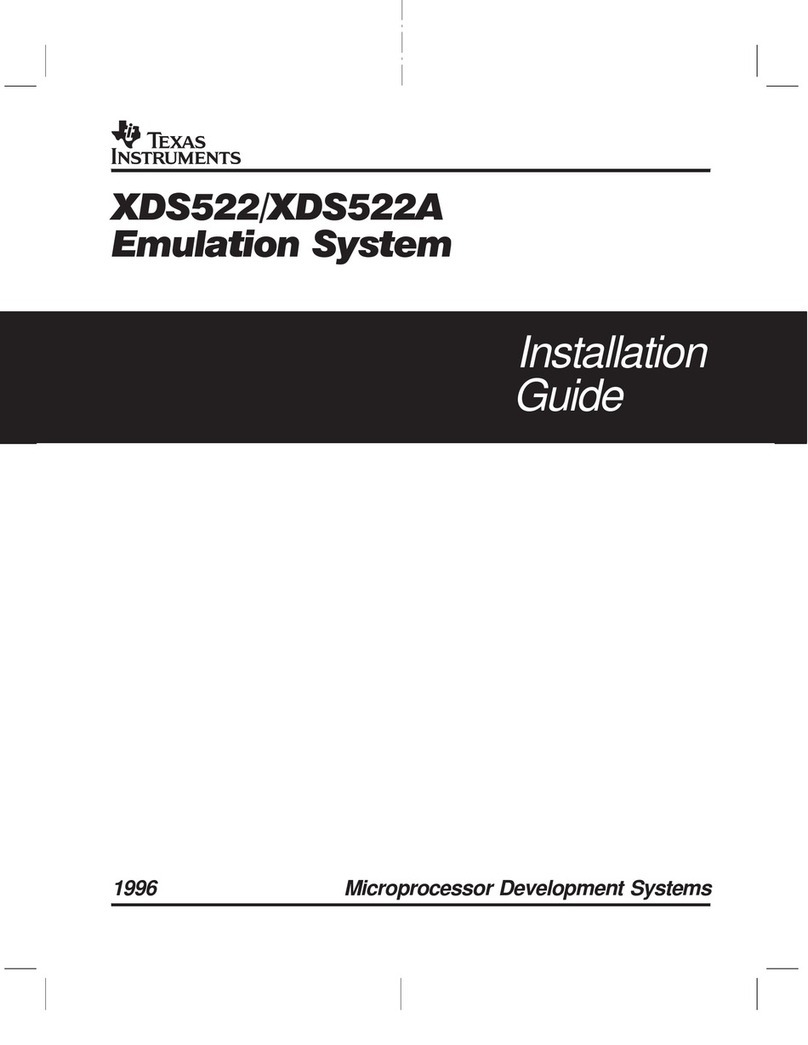
Texas Instruments
Texas Instruments XDS522 installation guide
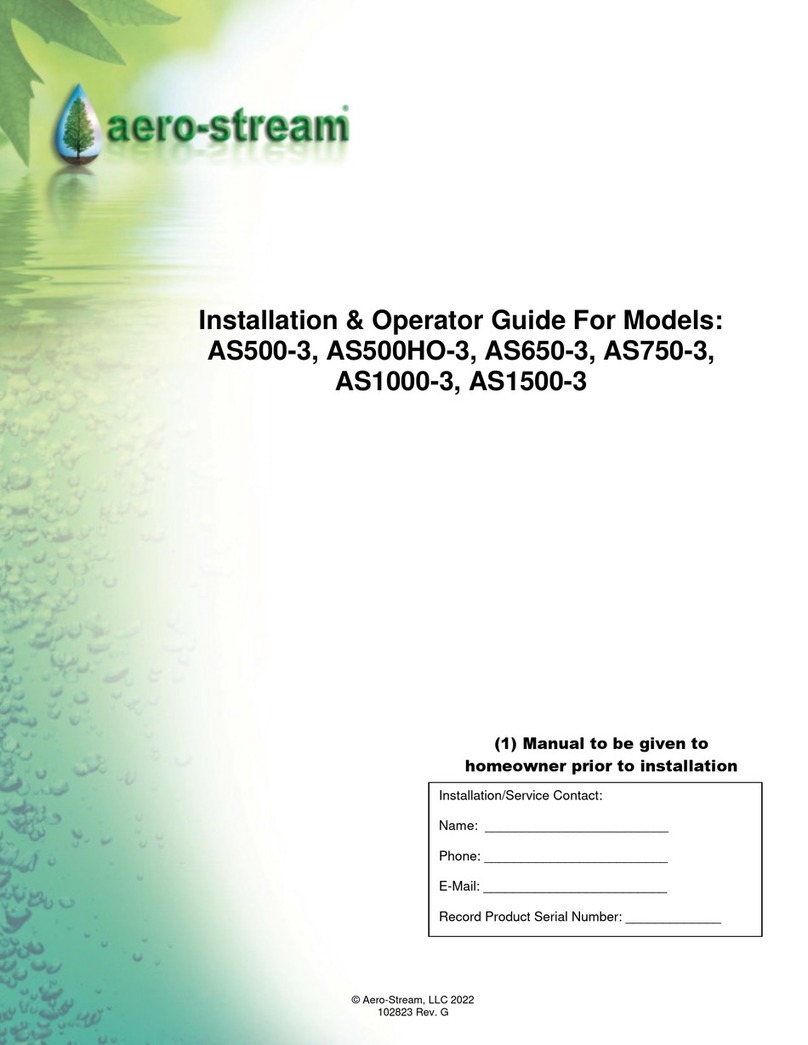
aero-stream
aero-stream AS500-3 manual
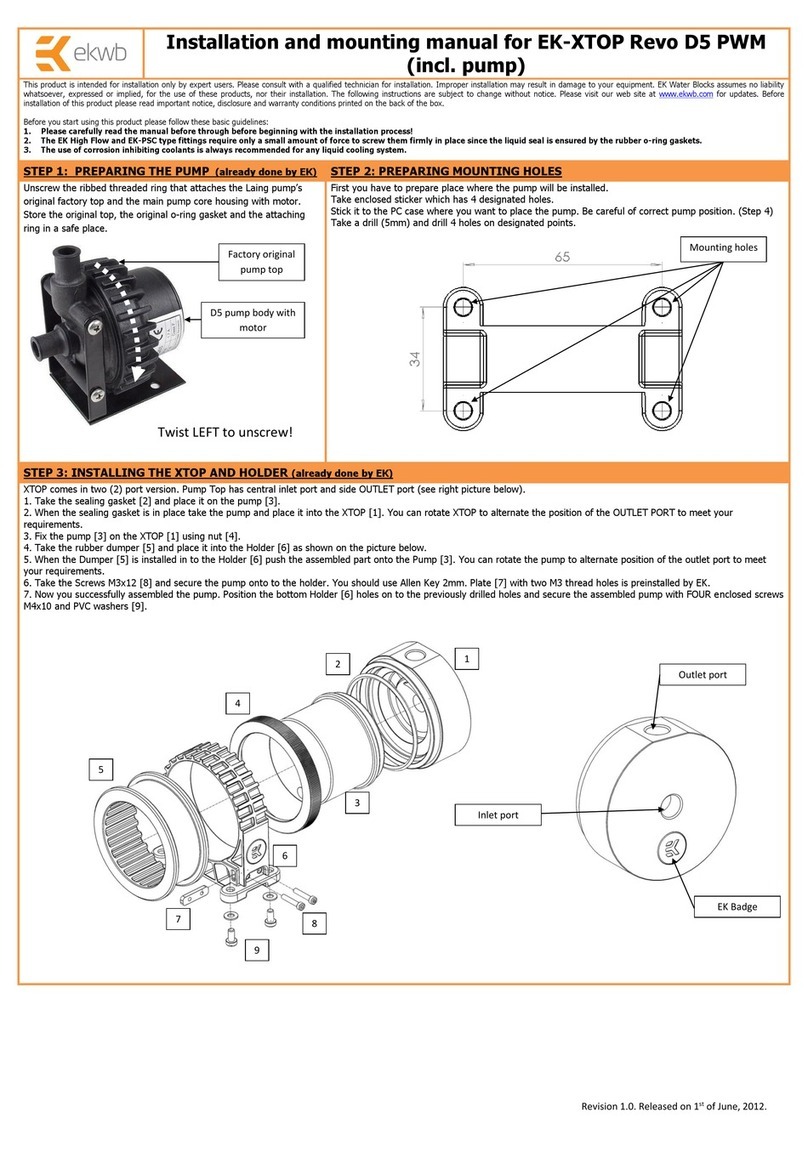
ekwb
ekwb EK-XTOP Revo D5 PWM INSTALLATION AND MOUNTING MANUAL