FISCHER ME50 R Series User manual

II 3G Ex nA IIC T4 Gc
-20 °C ≤ Ta ≤ +60°C
Operation manual
ME50 ... R
Programmable pressure transducer / pressure switch
for explosive areas
Gas explosion protection zone 2, gases and vapours
09005259 • BA_EN_ME50_ATEX • Rev. ST4-C • 03/22
*09005259*

| Masthead FISCHER Mess- und Regeltechnik GmbH
2/28 BA_EN_ME50_ATEX
Masthead
Manufacturer: FISCHER Mess- und Regeltechnik GmbH
Bielefelderstr. 37a
D-32107 Bad Salzuflen
Telephone: +49 5222 974 0
Telefax: +49 5222 7170
eMail: [email protected]
web: www.fischermesstechnik.de
Technical editorial team: Documentation representative: T. Malischewski
Technical editor: R. Kleemann
All rights, also those to the translation, reserved. No part of this document may
be reproduced or processed, duplicated or distributed using electronic systems
or any other form (print, photocopy, microfilm or another process) without the
written consent of the company FISCHER Mess- und Regeltechnik GmbH, Bad
Salzuflen.
Reproduction for internal use is expressly allowed.
Brand names and procedures are used for information purposes only and do
not take the respective patent situation into account. Great care was taken
when compiling the texts and illustrations; Nevertheless, errors cannot be ruled
out. The company FISCHER Mess- und Regeltechnik GmbH will not accept any
legal responsibility or liability for this.
Subject to technical amendments.
Version history
Rev. ST4-A 08/16 Version 1 (first edition)
Rev. ST4-B 09/17 Version 2 (corrections)
Rev. ST4-C 03/22 Version 3 (2L version not applicable)

FISCHER Mess- und Regeltechnik GmbH Table of Contents
BA_EN_ME50_ATEX iii/28
Table of Contents
1 Safety guidelines ............................................................................................................. 4
1.1 General................................................................................................................................... 4
1.2 Personnel Qualification........................................................................................................... 4
1.3 Risks due to Non-Observance of Safety Instructions............................................................. 4
1.4 Safety Instructions for the Operating Company and the Operator ......................................... 4
1.5 Unauthorised Modification...................................................................................................... 5
1.6 Inadmissible Modes of Operation........................................................................................... 5
1.7 Safe working practices for maintenance and installation work............................................... 5
1.8 Pictogram explanation............................................................................................................ 6
2 Product and functional description ............................................................................... 7
2.1 Delivery scope........................................................................................................................ 7
2.2 Performance characteristics................................................................................................... 7
2.3 Use as intended...................................................................................................................... 7
2.4 Function diagram.................................................................................................................... 8
2.5 Design and mode of operation ............................................................................................... 8
2.6 Product overview.................................................................................................................... 9
2.7 Type plate............................................................................................................................... 9
3 Installation and assembly ............................................................................................... 10
3.1 Generalities ............................................................................................................................ 10
3.2 Process connection ................................................................................................................ 10
3.3 Electrical connections............................................................................................................. 10
3.3.1 Ground connection..................................................................................................................... 11
4 Commissioning................................................................................................................ 13
4.1 General................................................................................................................................... 13
4.2 Control Elements .................................................................................................................... 13
4.3 Parameters ............................................................................................................................. 14
4.4 Parameter list ......................................................................................................................... 15
5 Technical Data ................................................................................................................. 19
5.1 Generalities ............................................................................................................................ 19
5.2 Input variables ........................................................................................................................ 19
5.3 Output parameters.................................................................................................................. 20
5.4 Measurement accuracy .......................................................................................................... 20
5.5 Auxiliary energy ..................................................................................................................... 20
5.6 Application conditions............................................................................................................. 21
5.7 Construction design................................................................................................................ 21
5.8 Parameters ............................................................................................................................. 22
6 Order Codes ..................................................................................................................... 23
6.1 Accessories ............................................................................................................................ 24
7 Attachments ..................................................................................................................... 25
7.1 EU Declaration of Conformity ................................................................................................. 25

1 | Safety guidelines FISCHER Mess- und Regeltechnik GmbH
4/28 BA_EN_ME50_ATEX
1 Safety guidelines
1.1 General
This operating manual contains basic instructions for the installation, operation
and maintenance of the device that must be followed without fail. It must be
read by the installer, the operator and the responsible specialist personnel be-
fore installing and commissioning the device.
This operating manual is an integral part of the product and therefore needs to
be kept close to the instrument in a place that is accessible at all times to the re-
sponsible personnel.
The following sections, in particular instructions about the assembly, commis-
sioning and maintenance, contain important information, non-observance of
which could pose a threat to humans, animals, the environment and property.
The instrument described in these operating instructions is designed and manu-
factured in line with the state of the art and good engineering practice.
1.2 Personnel Qualification
The instrument may only be installed and commissioned by specialized person-
nel familiar with the installation, commissioning and operation of this product.
Specialized personnel are persons who can assess the work they have been
assigned and recognize potential dangers by virtue of their specialized training,
their skills and experience and their knowledge of the pertinent standards.
For explosion-proof models the specialized personnel must have received spe-
cial training or instruction or be authorized to work with explosion-proof instru-
ments in explosion hazard areas.
1.3 Risks due to Non-Observance of Safety Instructions
Non-observance of these safety instructions, the intended use of the device or
the limit values given in the technical specifications can be hazardous or cause
harm to persons, the environment or the plant itself.
The supplier of the equipment will not be liable for damage claims if this should
happen.
1.4 Safety Instructions for the Operating Company and the
Operator
The safety instructions governing correct operation of theinstrument must be
observed. The operating company must make them available to the installation,
maintenance, inspection and operating personnel.
Dangers arising from electrical components, energy discharged by the medium,
escaping medium and incorrect installation of the device must be eliminated.
See the information in the applicable national and international regulations.
Please observe the information about certification and approvals in the Tech-
nical Data section.
The instrument must be decommissioned and secured against inadvertent re-
operationif a situation arises in which it must be assumed that safe operation is
no longer possible. Reasons for this assumption could be:

FISCHER Mess- und Regeltechnik GmbH Safety guidelines | 1
BA_EN_ME50_ATEX 5/28
• evident damage to the instrument
• failure of the electrical circuits
• longer storage outside the approved temperature range.
• considerable strain due to transport
Repairs may be carried out by the manufacturer only.
A professional single conformity inspection as per DIN EN 61010, section 1,
must be carried out before the instrument can be re-commissioned. This inspec-
tion must be performed at the manufacturer's location. Correct transport and
storage of the instrument are required.
1.5 Unauthorised Modification
Modifications of or other technical alterations to the instrument by the customer
are not permitted. This also applies to replacement parts. Only the manufacturer
is authorised to make any modifications or changes.
1.6 Inadmissible Modes of Operation
The operational safety of this instrument can only be guaranteed if it is used as
intended. The instrument model must be suitable for the medium used in the
system. The limit values given in the technical data may not be exceeded.
The manufacturer is not liable for damage resulting from improper or incorrect
use.
1.7 Safe working practices for maintenance and installation work
The safety instructions given in this operating manual, any nationally applicable
regulations on accident prevention and any of the operating company's internal
work, operating and safety guidelines must be observed.
The operating company is responsible for ensuring that all required mainten-
ance, inspection and installation work is carried out by qualified specialized per-
sonnel.

1 | Safety guidelines FISCHER Mess- und Regeltechnik GmbH
6/28 BA_EN_ME50_ATEX
1.8 Pictogram explanation
DANGER
Type and source of danger
This indicates a direct dangerous situation that could lead to death or serious
injury (highest danger level).
1. Avoid danger by observing the valid safety regulations.
WARNING
Type and source of danger
This indicates a potentially dangerous situation that could lead to death or ser-
ious injury (medium danger level).
1. Avoid danger by observing the valid safety regulations.
CAUTION
Type and source of danger
This indicates a potentially dangerous situation that could lead to slight or seri-
ous injury, damage or environmental pollution (low danger level).
1. Avoid danger by observing the valid safety regulations.
NOTICE
Note / advice
This indicates useful information of advice for efficient and smooth operation.

FISCHER Mess- und Regeltechnik GmbH Product and functional description | 2
BA_EN_ME50_ATEX 7/28
2 Product and functional description
2.1 Delivery scope
• Programmable pressure transducer / switch ME50
• User Manual
2.2 Performance characteristics
Important features
• Digital measured value display
• Highly precise
• Low hysteresis
• Can be configured
• Turn down 1:5
• Optional switch output
• Robust device model
• Large vibration resistance
Typical applications
• Pressure monitoring
• Content measurement
Application areas
• Procedural engineering
• Process technology
• Environmental technology
• Regenerative energies (biogas, etc.)
2.3 Use as intended
The ME50 is suitable for measuring relative pressure and under-pressure in
fluid or gas-like, neutral, non-aggressive media.
If there is dirty or aggressive media in the system, or if this is to be expected,
the device must be modified in terms of those parts that come into contact with
the media. The device is to be exclusively used for the applications agreed
between the manufacturer and the user.
Explosion hazard area classification
The pressure transducer is suitable as 'Electrical equipment for use in poten-
tially explosive areas', Zone 2 - (Gases and vapours).
Designation as per guideline 2014/34/EU (ATEX):
II 3G Ex nA IIC T4 Gc
-20 °C ≤ Ta ≤ +60°C

2 | Product and functional description FISCHER Mess- und Regeltechnik GmbH
8/28 BA_EN_ME50_ATEX
2.4 Function diagram
SP1
SP2
1.234
µC
þû ÿ
D
A
1
2 3
5678
Aout
4
Fig.1: Function diagram
1 Sensor 2 Signal converter
3 Switching outputs 4 Analogue output
5 Measured value display 6 Keyboard
7 Microcontroller 8 Pressure equalisation
2.5 Design and mode of operation
Depending on the measuring range, the ME50 is produced with a ceramic or a
piezo-resistive measuring cell. Two switch outputs are also possible in the ver-
sion with a 3-conductor connection.
Ceramic measuring cell
In the ceramic measuring cell, the pressure acts directly on the ceramic mem-
brane which in turn deforms. The membrane is constructed electrically like a
plate capacitor whose capacity change is proportional to the effective pressure.
The electronics that are controlled by a micro-controller implement this change
in capacitance into an standard electrical signal.
Piezo-resistive measuring cell
In the piezo-resistive measuring cell, the pressure is applied to a silicon mem-
brane into which the deformation-dependent resistances have been diffused.
The material resistance changes proportionally to the effective pressure. The
electronics that are controlled by a micro-controller implement this change in
resistance into an standard electrical signal.

FISCHER Mess- und Regeltechnik GmbH Product and functional description | 2
BA_EN_ME50_ATEX 9/28
2.6 Product overview
Accessories
Delivery scope
M12 plug
Pressure equalisation element
Casing lid
TC flange
TC seal
Process adapter G½
with TC flange
TC clamp
Fig.2: Product overview
2.7 Type plate
This type plate serves as an example of the information that is stated. The data
shown is purely fictive, but does correspond to the actual conditions. For more
information, please see the order code at the end of these instructions.
Marking
Technical data Serial number
Circuit diagram
Order Codes
ME5002J4BBMMD
4...20 mA
0...1 bar
1405250.02.001
II 3G
Ex nA IIC T4 Gc
-20 °C ≤ T ≤ 60°C
amb
ATEX code
Fig.3: Nameplate

3 | Installation and assembly FISCHER Mess- und Regeltechnik GmbH
10/28 BA_EN_ME50_ATEX
3 Installation and assembly
3.1 Generalities
The unit is designed for vertical installation (process connection facing down)
and compared. No other installation positions are planned.
3.2 Process connection
• By authorized and qualified specialized personnel only.
• The pipes need to be depressurized when the instrument is being connec-
ted.
• Appropriate steps must be taken to protect the device from pressure surges.
• Check that the device is suitable for the medium being measured.
• Maximum pressures must be observed (cf. Tech. data)
The process connection of the ME50 is realised with a terminal clamp
(TriClamp) acc. to DIN 32676.
Fig.4: Tri Clamp connection
The pressure lines must be installed at an inclination so that when fluids are
measured no air pockets are created or when measuring gases, no water pock-
ets are created. If the required inclination is not reached, water or air filters must
be installed at suitable places.
The pressure lines must be kept as short as possible and installed without any
tight bends to avoid delays.
The pressure lines need to be vented for fluid measuring media.
If water is used as a measuring medium, the unit must be protected against
frost.
If the pressure sensing lines are already pressurised at the time of commission-
ing, zero-point control and adjustment cannot be performed. In such cases, the
device should be only connected to the mains without the pressure sensing
lines.
3.3 Electrical connections
WARNING
Operation in areas at risk of explosion
If operated in explosive areas, the electrical data of the unit and the valid local
regulations and guidelines for the installation and operation of electrical systems
in explosive areas must be observed. (e.g. DIN EN 60079)
The electrical connection may only be realised by authorised and qualified spe-
cialists that have undergone additional training or briefings or have a permit to
work on explosion-protected units in potentially explosive systems.
Risks emanating from electrical current of voltage should be prevented by
means of suitable action.
• When connecting the unit, the national and international electro-technical
regulations must be observed.
• Disconnect the system from the mains, before electrically connecting the
device.
• Do not connect the connector if strained.
• A CE-conform mains adapter with a slow 200 mA fuse only may be used in
the power supply circuit.

FISCHER Mess- und Regeltechnik GmbH Installation and assembly | 3
BA_EN_ME50_ATEX 11/28
The nominal supply voltage and the permissible range can be found in the tech-
nical data.
The admissible load / resistance is stated in the technical data.
3.3.1 Ground connection
Ground connection
Fig.5: Ground connection
The outer ground connection must always be connected to the protective poten-
tial equalisation or a similar local potential equalisation.
The ground terminal is suitable for connecting fine-wire conductors up to 4 mm2
or single-wire conductors up to 6 mm2.
3.3.2 3-conductor version
Pressure Transmitter Services
Output signal
Input signal
+Sig
+Ub
-Ub
-Sig
+Ub
-Ub
+
- -
+
Fig.6: 3L Circuitry
Without switch output
Fig.7: M12 connector 8-pin
PIN Signal name Cable colour
1Outlet +Sig white
2Services +Ubbrown
3--- n.c green
4--- n.c yellow
5--- n.c grey
6--- n.c pink
7Services -Ubblue
8Functional earth FE rot
ACoding A
Table1: Supply, and output signal
With switch output There are three options available for the semiconductor switch contacts K1 and
K2.
1. Potential-free
2. PNP-switching In this version, the connections K1(b) and K2(b) are connec-
ted with +Ub ex-works. The switch output is called PNP1 or PNP2.
3. NPN-switching In this version, the connections K1(b) and K2(b) are connec-
ted with -Ub ex-works. The switch output is called NPN1 or NPN2.
Please note that the type of switch contact can be programmed and can work
both as an NC or NO contact. For reasons of simplicity, they are shown as NC
contacts in this connection description.

3 | Installation and assembly FISCHER Mess- und Regeltechnik GmbH
12/28 BA_EN_ME50_ATEX
Fig.8: M12 connector 8-pin
Potential-free contacts
Pin Signal name Cable colour
1Output +Sig white
2Operating voltage +Ubbrown
3Switching output 1 K1 (a) green
4Switching output 1 K1 (b) yellow
5Switching output 2 K2 (b) grey
6Switching output 2 K2 (a) pink
7Operating voltage -Ubblue
8Functional earth FE red
ACoding A
Table2: Power supply, output signal and switching contacts
PNP-switching
Pin Signal name Cable colour
1Output +Sig white
2Operating voltage +Ubbrown
3Switching output 1 PNP1 green
4--- n.c. yellow
5Switching output 2 PNP2 grey
6--- n.c. pink
7Operating voltage -Ubblue
8Functional earth FE red
ACoding A
Table3: Power supply, output signal and PNP switching contacts
NPN-switching
Pin Signal name Cable colour
1Output +Sig white
2Operating voltage +Ubbrown
3Switching output 1 NPN1 green
4--- n.c. yellow
5Switching output 2 NPN2 grey
6--- n.c. pink
7Operating voltage -Ubblue
8Functional earth FE red
ACoding A
Table4: Power supply, output signal and NPN switching contacts

FISCHER Mess- und Regeltechnik GmbH Commissioning | 4
BA_EN_ME50_ATEX 13/28
4 Commissioning
4.1 General
All electrical supply, operating and measuring lines, and the pressure connec-
tions must have been correctly installed before commissioning. All supply lines
are arranged so that there are no mechanical forces acting on the device.
Check that the pressure connections do not leak before commissioning.
4.2 Control Elements
4.2.1 Advertisement
1
23
4
5
6
Fig.9: Measured value display
1 Keyboard 2 Measured Value Display
3 Unit 4 Switch points
5 Bar chart 6 Overflow
The 3½ digit LCD display represents the current pressure value in normal
mode. The unit is shown to the right of the measured value and is set ex-works.
The unit cannot be altered on site.
4.2.2 Keyboard
1
2
3
Fig.10: Keyboard
1 Arrow key down Menu: downwards Value: reduce
3 OK key Menu: open Value: save
5 Arrow key up Menu: upwards Value: increase
It is configured via a 3-key membrane keyboard. The keyboard can only be
reached after the housing lid has been removed. This can usually be unscrewed
manually. If this is not possible, please use a belt wrench to prevent damage

4 | Commissioning FISCHER Mess- und Regeltechnik GmbH
14/28 BA_EN_ME50_ATEX
4.3 Parameters
After it has been switched on, the unit carries out a display test and shows the
implemented firmware version for approx. 2s. Then the pressure transmitter
switches to the operating mode.
Press the OK key
û
to enter the configuration mode.
During configuration, the parameter name or the parameter value is shown in-
stead of the measured value. The unit continues to work during configuration
and shows pressure changes in the bar chart display. Changes can be followed
directly without changing the operating mode.
NOTICE
Time out
If no key is pressed for a longer period (approx. 1 minute), the units switches
automatically into work mode.
Set parameters Proceed as follows to set a parameter:
1. Press the enter OK key to switch to the configuration mode.
2. Use the arrow keys
ÿ
þ
to navigate through the parameter list until you
reach the required parameter.
3. Press the enter OK key to call up the parameter. The parameter value is
shown.
4. Use the arrow keys
ÿ
þ
to set the required parameter value.
5. Press the enter OK key to save the value. The parameter name is now
shown on the display.
6. Use the arrow keys
ÿ
þ
to navigate through the parameter list until you
reach the required parameter.
7. Press the enter OK key
û
to leave to the parameter menu. The pressure
transmitter switches to the operating mode.

FISCHER Mess- und Regeltechnik GmbH Commissioning | 4
BA_EN_ME50_ATEX 15/28
4.4 Parameter list
esc
ma
Reception
me
dp
sp1a
sp1e
sp1f
sp1d
sp2a
sp2e
sp2f
sp2d
0ff
span
np
1 g1
1 g2
1 er
tast
rst
esc
Outlet
Outlet
Fig.11: Parameter list
The following describes all parameters in the shown list. Please note that some
parameters are not available depending on the unit version. For instance, the
parameters for the switch points are hidden, if the unit does not have any switch
points.
Parameter Escape
esc
This parameter is the input and output of the parameter list. It is stated at the
start and also at the end of the list.
• If the OK button
û
is pressed in work mode, the unit switches to the config-
uration mode. The
ESc
parameter appears on the display.
• To leave the configuration mode, use the arrow keys
þ
ÿ
to set the
ESc
parameter and press the OK button
û
. The unit switches into work mode.
Parameter measuring range
MA ... ML
The measuring range within the basic measuring range can be spread (see type
plate) using the parameters measuring range start
Employee
and measuring range
end
ML
. The spread (Turn down) is maximum 1:5.
Turn down = Settable measuring span
Basic measuring range
The characteristic curve can also be inverted with these parameters.
•
Employee
<
ML
: rising characteristic curve
•
ML
<
Employee
: falling characteristic curve
Please note that the minimum settable measuring span cannot be undercut.
Both parameters can be set over the entire basic measuring range. The output
signal is automatically scaled to the set measuring range.
Parameter switch points
If the unit has a switch output, the following parameters appear in the list:
Switch point 1:
sp1a sp1e sp1f sp1d
Switch point 2:
sp2a sp2e sp2f sp2d
As the parameters for both switch points function in the same way, the paramet-
ers for switch point 1 (SP1) are explained below.

4 | Commissioning FISCHER Mess- und Regeltechnik GmbH
16/28 BA_EN_ME50_ATEX
(i) Parameter activation and deactivation point
SP1A SP1E
These parameters are used to define the activation and deactivation point. Both
parameters can be set individually over the entire basic measuring range.
•
sp1E
>
sp1a
If the measured value exceeds the activation point
sp1E
, the contact
switches. It is only switched off again, if the measured value undercuts the
activation point
sp1a
. (Hysteresis function).
•
sp1E
>
sp1a
If the measured value exceeds the activation point
sp1E
, the contact
switches. If the measured value undercuts an equally large deactivation
point
sp1a
, the contact drops.
•
sp1E
<
sp1a
The contact switches if the measured value lies within the range between
the activation point
sp1E
and the deactivation point
sp1a
. If the measured
value lies outside this area, the contact drops.
As switched contact is shown in the display as
SP1
or
SP2
.
(ii) Parameter function
sp1f
The type of contact is defined with this parameter.
sp1f
= 0
The contact works as an open contact (NO).
sp1f
= 1
The contact works as an make contact (NC).
CAUTION
Power failure
Please note that the contact is always open if no current flows, regardless of the
programmed contact type.
(iii) Parameter damping
sp1d
This parameter allows the reaction of the switch output to be delayed by 0° ...
°200 s. This delay applies equally for switching on and off.
Parameter offset correction
0ff
This parameter is used to correct an offset, if the measured value at the zero-
point deviates from zero. The display shows the current measured value that
you can change by up to ±10% of the basic measuring range.
Parameter span correction
span
This parameter is used to correct an offset of the span, if the measured value at
the end or the measuring range deviates from the end value. The display shows
the current measured value that you can change by up to ±10% of the basic
measuring range.

FISCHER Mess- und Regeltechnik GmbH Commissioning | 4
BA_EN_ME50_ATEX 17/28
Parameter zero-point window
np
In many cases, unsteady readings are not a problem during normal operating
mode, but this is not true for the idle state, i.e. if a measured value of zero is ex-
pected. The zero-point window parameter is designed for precisely this case.
Its value defines a range of measurement values around zero, for which the
measuring value is set to zero. The display only stops showing zero when the
measurement leaves the set window. When reaching double the value, the
measured value and the reading match again. This avoids jumps in the display.
-nP-2nP nP 2nP
Advertisement
Measured value
Zero-point window
0
Parameter lower current limit
i g1
This parameter defines the lower current limit of the output signal in a value
range of 3.5…22.5 mA. The limit is activated with the value 0.
Parameter upper current limit
i g2
This parameter defines the upper current limit of the output signal in a value
range of 3.5…22.5 mA. The limit is activated with the value 0.
Parameter error signal
i Er
This parameter defines the output signal in a value range of 3.5…22.5 mA that
should be issued when there is an internal error in the device.

4 | Commissioning FISCHER Mess- und Regeltechnik GmbH
18/28 BA_EN_ME50_ATEX
Parameter key lock
tast
The key lock can be activated with this parameter. If no button is pressed within
the given time, the keyboard is locked. Unlock the keyboard by interrupting the
power supply.
•
tast
= 0
The key lock is deactivated
•
tast
= 1 … 100 s
The key lock is activated after the end of a given time.
Parameter reset
rst
If the parameter is set to the value 1, all parameters are reset to the default set-
tings.
NOTICE
User settings
If the system is reset to the default settings, all user settings are deleted per-
manently.

FISCHER Mess- und Regeltechnik GmbH Technical Data | 5
BA_EN_ME50_ATEX 19/28
5 Technical Data
5.1 Generalities
Reference conditions (acc. to IEC 61298-1)
Temperature error +15 … +25 °C
Relative humidity 45 … 75 %
Air pressure 86 … 106 kPa 860 … 1060 mbar
Installation position User-defined
5.2 Input variables
Ceramic measuring cell Measuring range Smallest
measuring span
Over-pressure
safety
[mbar] [mbar] [bar]
-20 … +20 10 4
-40 ... +40 20
-100 … +100 40
0 … 60 12 4
0 … 100 20
0 … 200 40
Piezo-resistive measuring
cell
Measuring range Smallest
measuring span
Over-pressure
safety
[mbar] [mbar] [bar]
0 … 400 80 1
0 … 600 120 3
[bar] [bar] [bar]
0 … 1 0.2 3
0 … 1.6 0.32 7.5
0 … 2.5 0.5 7.5
0 … 4 0.8 15
0 … 6 1.2 15
0 … 10 2 30
0 … 16 3.2 90
-0.6 … 0 0.12 3.0
-1 … 0 0.2 3.0
-1 … +0.6 0.32 3.0
-1 … +1.5 0.5 7.5
-1 … +3 0.8 15
-1 … +5 1.2 15
-1 … +9 2.0 30
-1 … +15 3.2 90
The measuring cell can be set within the pre-defined measuring range, which is
also stated on the type plate, using the parameters
Employee
and
ML
. The smallest
settable measuring span is listed for every measuring range and is a minimum
of 1:5 in relation to the basic measuring range.

5 | Technical Data FISCHER Mess- und Regeltechnik GmbH
20/28 BA_EN_ME50_ATEX
5.3 Output parameters
The ME50 versions differ in the number and type of outputs available (see order
code):
Analog output 0/4 … 20 mA
Load RL ≤ ((Ub – 10 V) * 50 Ω) + 300 Ω
Current limitation approx. 26 mA
Switching output
0 ... 2 Photo MOS relay not short-circuit proof, thermally protected
Contact Umax Imax RON
potential-free (AC/DC) 30 V 200 mA < 1 Ω
PNP/NPN switching (DC) Ub200 mA < 1 Ω
5.4 Measurement accuracy
Accuracy ± 0.2% of measuring range (FS)*)
Temperature drift ± 0.01% FS/K
Zero point
Measuring range
Temperature error band over the com-
pensated temperature range
Compensated measuring range -10 °C … +70 °C
Long-term stability < ±0.1 % FS/year
*) Includes non-linearity, hysteresis, non-repeatability, zero and full scale devi-
ation. Calibrated in vertical mounting position with process connection down-
wards.
5.5 Auxiliary energy
WARNING
Supply circuit
A CE-conform mains adapter with a slow 200 mA fuse only may be used in the
power supply circuit.
Rated voltage 24V DC
Perm. operating voltage 12 … 30 V DC
Power consumption < 1 W
Table of contents
Other FISCHER Switch manuals
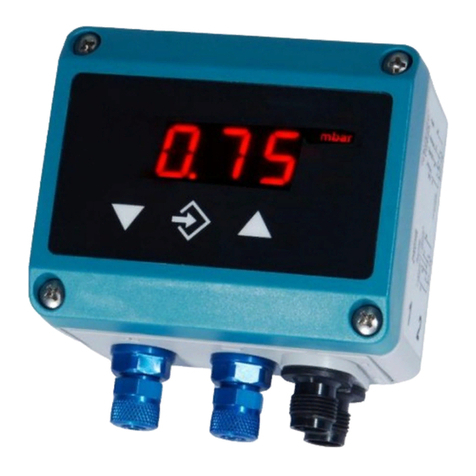
FISCHER
FISCHER DE45 series Instruction Manual
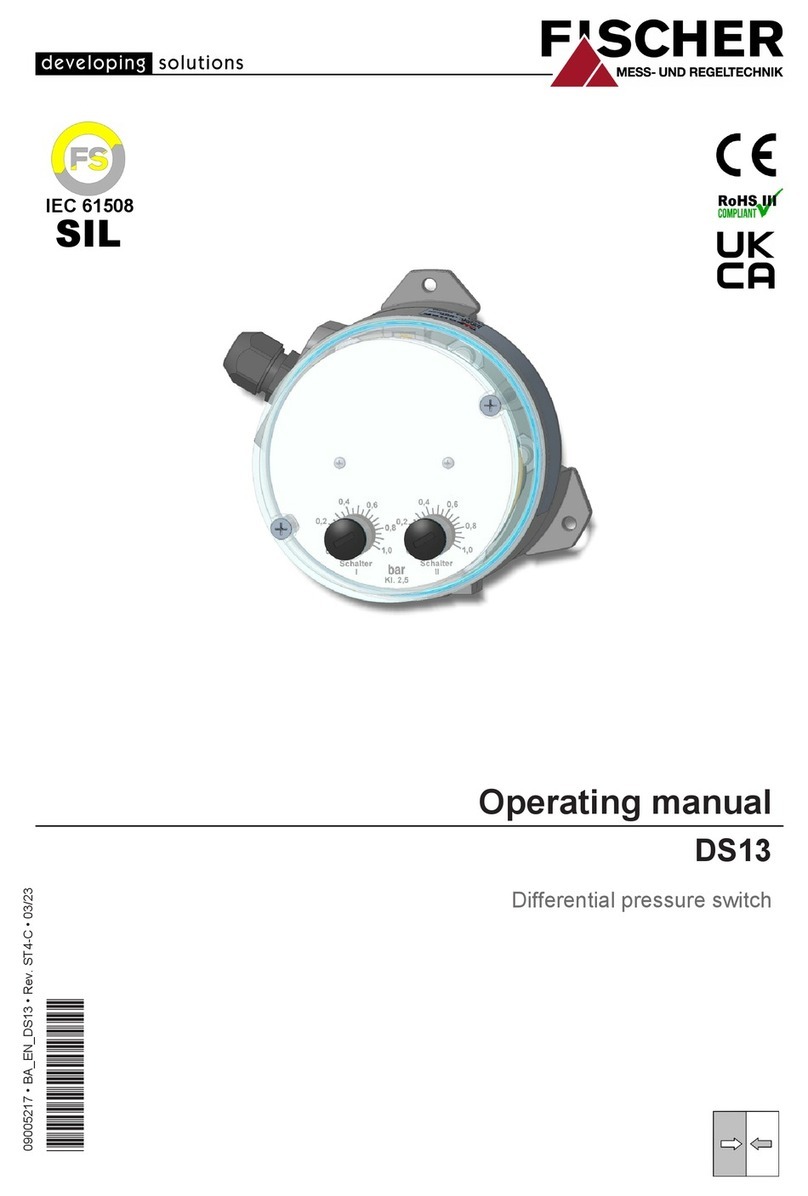
FISCHER
FISCHER DS13 User manual
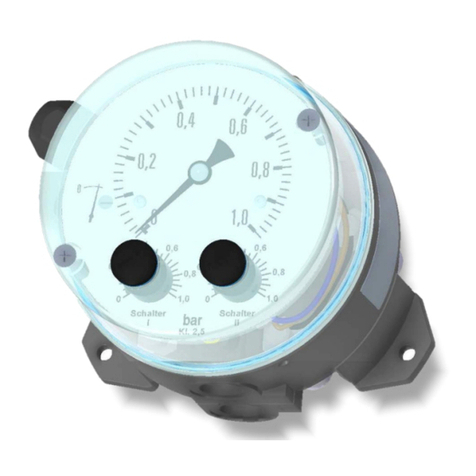
FISCHER
FISCHER DS 11 User manual
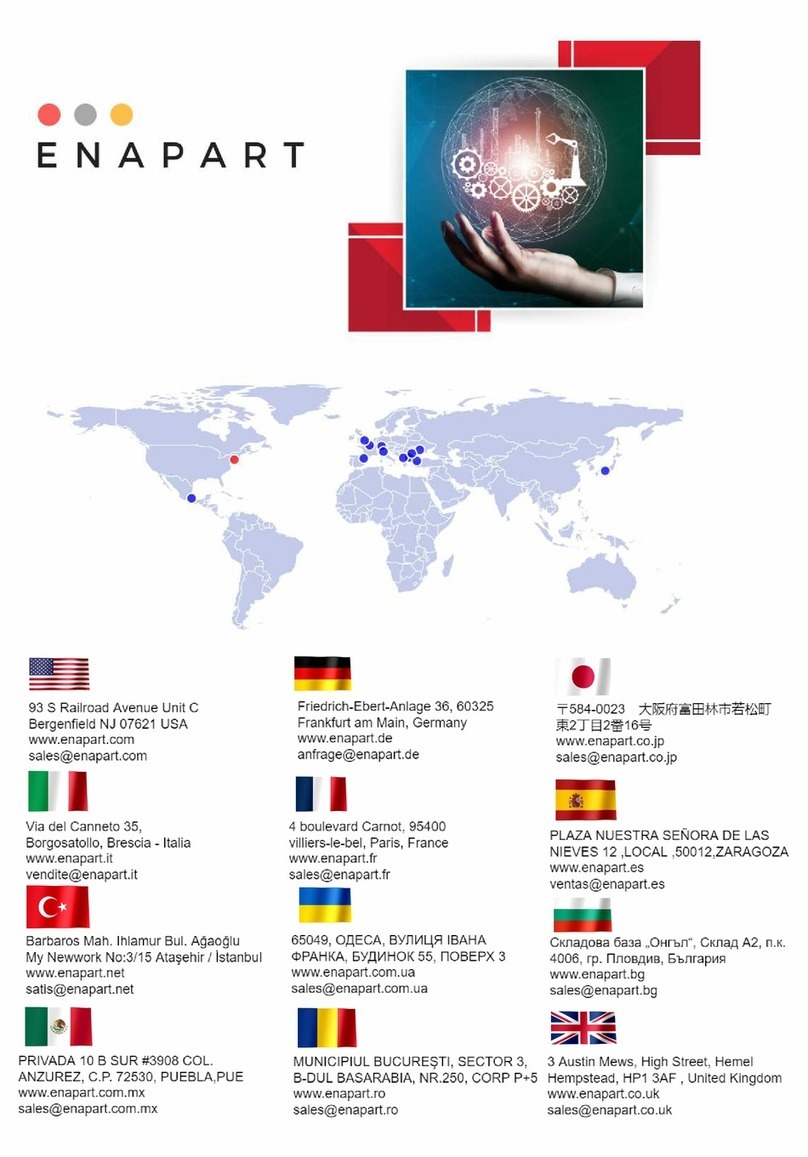
FISCHER
FISCHER DS 11 User manual
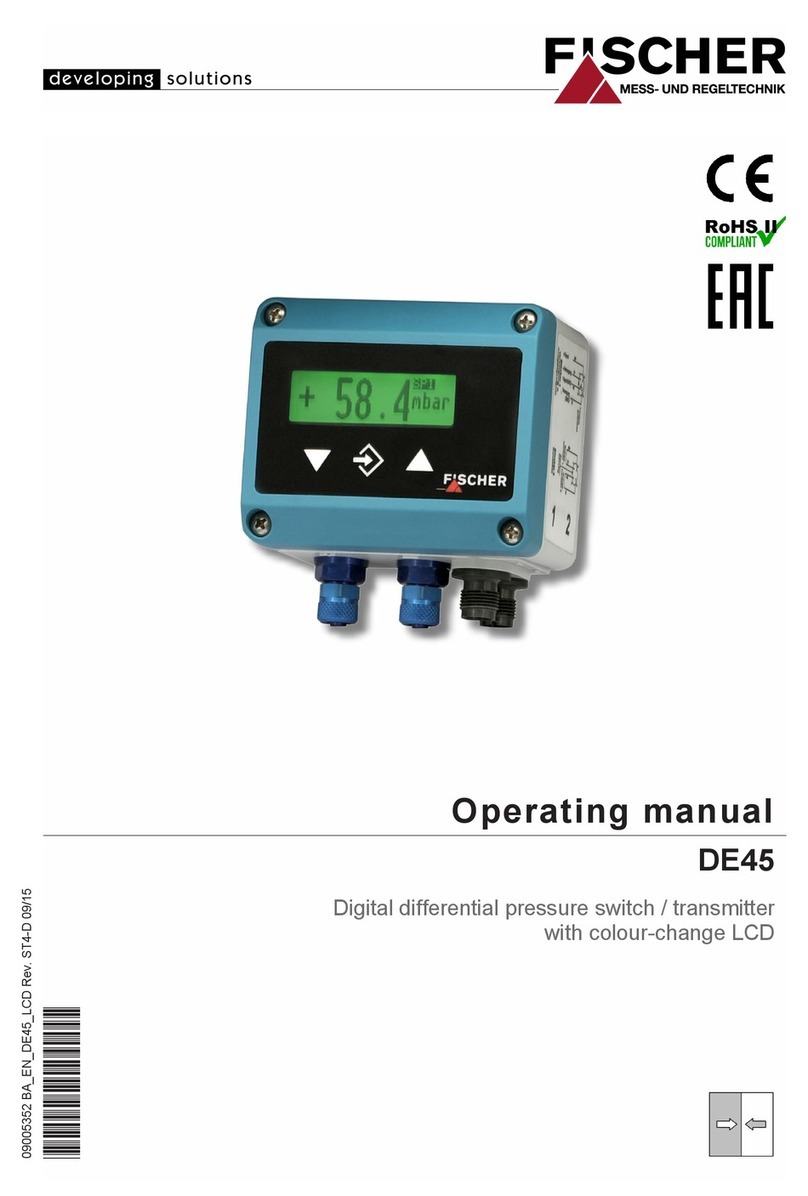
FISCHER
FISCHER DE45 series User manual

FISCHER
FISCHER DS 11 User manual

FISCHER
FISCHER DS31 User manual

FISCHER
FISCHER DS34 User manual

FISCHER
FISCHER DS31 User manual
Popular Switch manuals by other brands
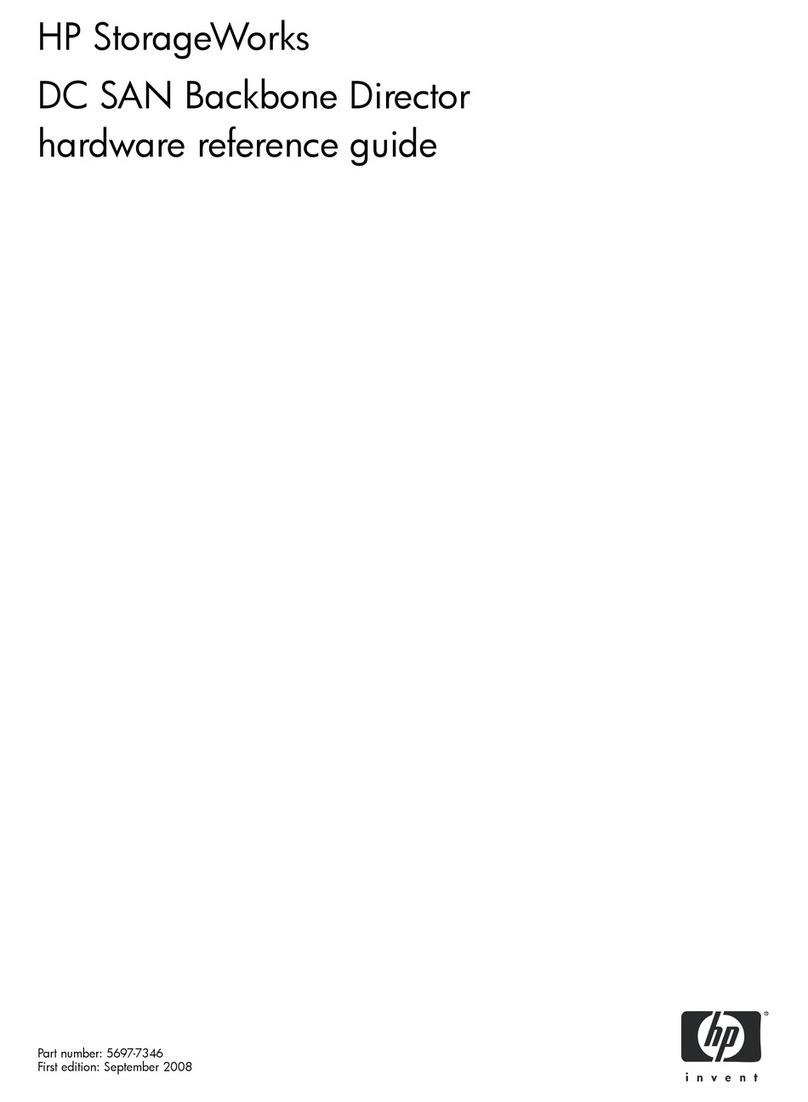
HP
HP A7990A - StorageWorks SAN Director 4/16 Blade... Hardware reference guide
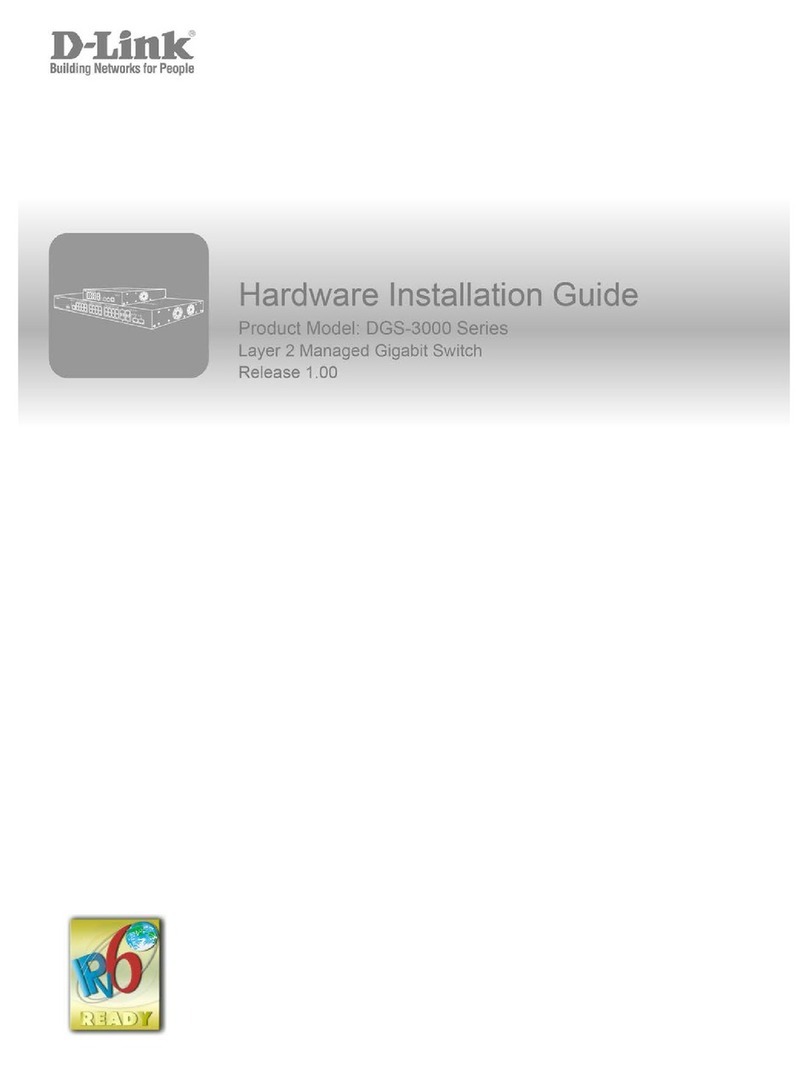
D-Link
D-Link DGS-3000 series Hardware installation guide
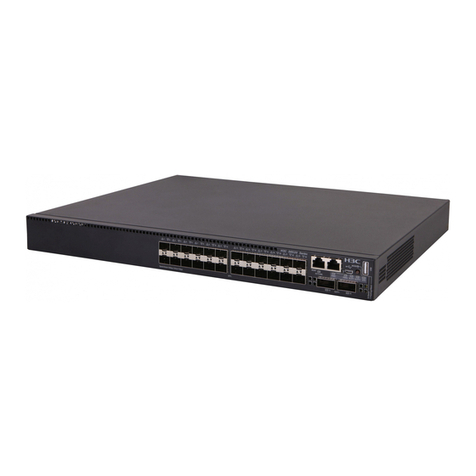
H3C
H3C S6520X-EI Series manual

Integra
Integra Xmart STA-16A user manual
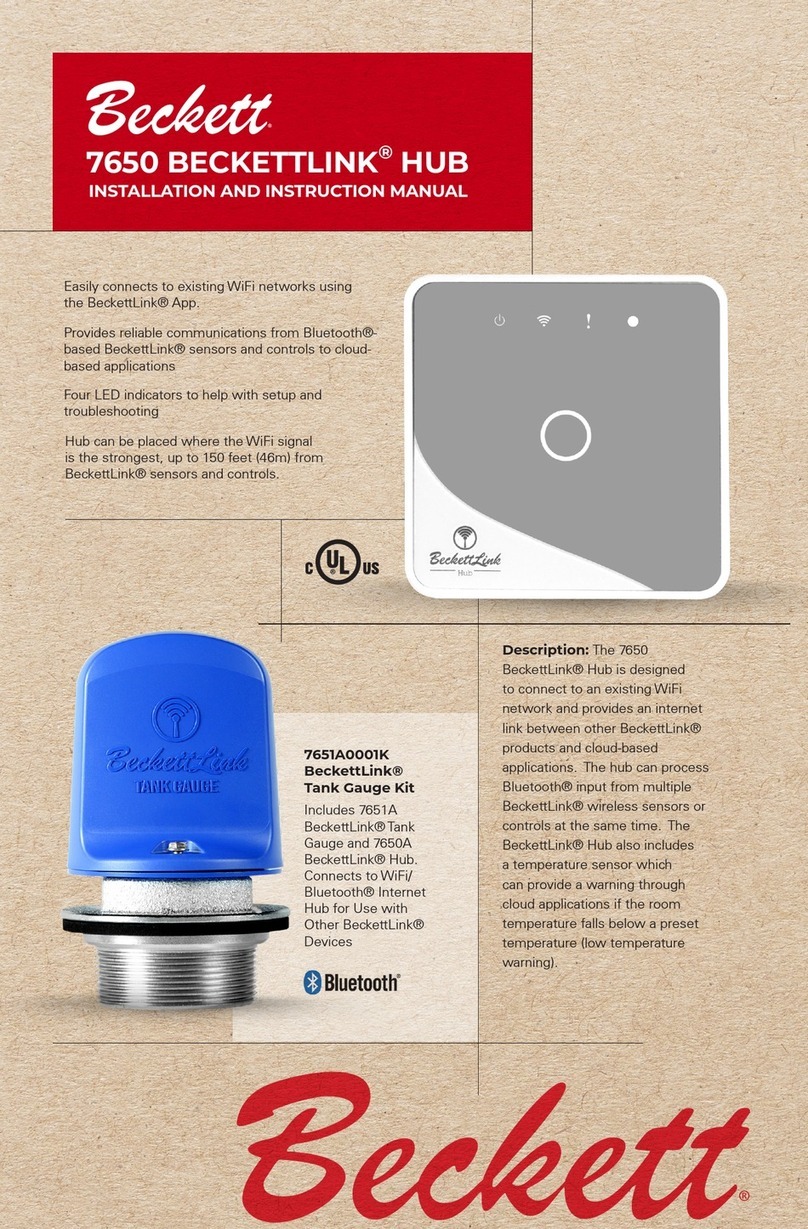
Beckett
Beckett Beckettlink Hub 7650 Installation and instruction manual
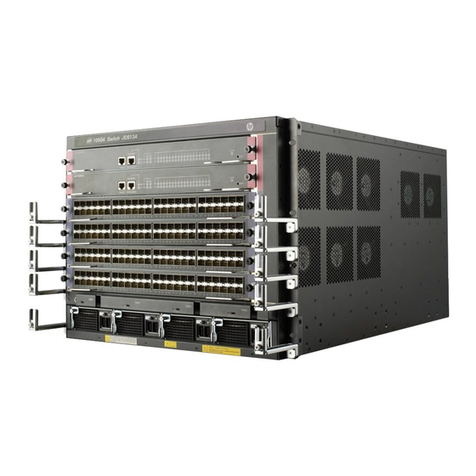
HP
HP 10504 installation guide