Flow Controller Systems FCS PDS II User manual

FCS PDS II
Product Manual
!"#$%&'()*+)%,-./%0'*1.%2$$/%3456'1%7+..)/%7,%"8#"9%%%%%%%%%%%%
"!#:#;<:88#"%=%>'(1*6?@A(:'(B6.1%%%%%%%%%%%
!"#$%#&'(#"")(*+*'),*-%#,
!"#$%#&'(#"")(*+*'),*-%#,

Important information:
Please read the instructionsbefore operating the product.
Warning:
Tubing may crack due to wear. This results in the overflow of
fluid from tubing. People and instruments may be injured. You
must check tubing often and change tubing as needed.
Please connect power directly to a wall socket. Avoid using an
extension cord.
If power line or plug have wear or other damage, please unplug
it by holding the plug, not the line.
If the following situation occurs, please turn off the power
and unplug the unit, holding the plug, not the line.
1. Fluid splashes on the pump.
2. You think the pump needsto maintain or amend.
Your power socket must have a ground wire, and have reliable
grounding.

Catalog
PDS II Product Introduction..............................................................- 1 -
PDS II Appearance............................................................................- 2 -
PDS II Controller Interface fracture...................................................- 4 -
Filling Volume Reference Parameter (Media is Water) .................- 14 -
PDS II Technical Specifications.........................................................- 15 -
Product Size Chart:.......................................................................- 16 -
Main Functions and Features of PDS II...........................................- 17 -
External Control Interface Instruction of the Control Unit:.........- 18 -
Maintenance:...................................................................................- 19 -
Warranty and After Sales Service:...................................................- 20 -

-1 -
PDS II Product Introduction
PDS II(Programmable Dispensing
System)Series includes one controller and many
independent filling units. Each filling unit has two working
modes: Independent working mode and logic working mode.
In independent working mode, each filling unit can be
used as one independent peristaltic pump to achieve the
transferring or dispensing of liquid. The filling units work
independently. The tubing size and pump models of
each filling unit can be the same or different.
In logic working mode, many filling units are
operated according to the preset logical relation.The
tubing size and pump models of each filling unit can be the
same or different.
PDSII with 7‟‟ TFT color display touch
interface, intelligent calibration function,and online
micro-adjusting function offers various external controls
for your needs, supportsRS232 and RS485 (two
interfaces), standard MODBUS protocol, and accomplishes
external control in different industry conditions. Suitable
for transferring liquid with no pollution and high accuracy.
The accuracy can be 0.5%-1%.
PDS II

-2 -
PDS II Appearance
A B C
Composition:
A——Pump Heads
B——Filling Unit
C——Controller
Product Composition
PDSII consists of one controller and many independent
filling units, adding or deleting filling units as needed. You can
also set the validity of each filling unit as needed.
Below is a diagram of cascading many filling units:
①② ⑧
PDS II

-3 -
Cascading instruction:
1 - All the filling units (independently) can connect to the
controller. The controller has a separate interface for each
filling unit.
2 - Each controller can control 8 filling units max.
A
BC
Back side of filling unit
Interface Specification:A——Power switch
B——Power socket
C——Interface connecting the controller(G)
Interface Specification of controller
D
E
F
G
Back side of controller
D——Power switch
E——Power socket
F——External input interface
G——Interface connecting the filling unit(C)
PDS II

-4 -
PDS II Controller Interface Hierarchy
系统
主界面
单元
参数设置
有效
单元
常用
模式
全速
界面
时间
日期
选择要查
看的单元
流量校
正
步骤查看
步骤参数
查看
独立运
行常用
模式
逻辑运
行常用
模式
外控设置
界面
Main
Interface
Unit
parameter
Settings Effective
unit Common
mode Interface at
full speed External
control
interface
Review
unit See the
steps Date and
Time
Check the
parameter
s
Commonly
used logic
operation
mode
Run
independentl
y commonly
used mode
The flow
calibration
PDS II controller operation interface introduction
1 - Boot interface:After power on, the system will display
the welcome interface.
2 - Main Interface:
The diagram of main interface:
A - Speed display:The interface will loop display the speed of the
PDS II

-5 -
effective units every 5 seconds.
B - Dynamic display:Display the working state of each unit in
real time, dynamically display the monitoring result. It also has
an alarm function. If a bottle appears red (alarm signal), the
responding unit‟s bottle is absent. Please check the production
line.In the stop condition, you can click the bottle to
enter the parameter setting interface.
a - When the unit is on dispensing mode, you can click the bottle
to enter the parameter check interface, and fine-tune the flow
rate online.
b - When the unit is in transferring mode, you can click the bottle to
enter the parameter setting interface.In this condition,you
can only change the flow rate, speed,and direction.Other
parameters can‟t be modified.
c - If the unit is not the effective unit, it will highlight errors when
clicking the bottle.
C - Choose Looping units:Click to choose the unit displaying
in the “D” area.
D - Parameter display:This area will loop display the system settings
of the effective units every 5 seconds. Click the lock sign in
the upper right corner to lock the current unit and stop loop
display.
E - Date/Time display:Displays the Date/Time in real-time.
Click to set the parameters.
F - Settingsbutton: Click this button to enter the
settingsinterface.You can select the effective unit, common
mode, and the external control settings.
G - Full speed button:Click this button to enter the full speed
interface.
H - Start/stop selection area:This area can stop or start the
working unit.
3 - Settingsinterface
PDS II

-6 -
Common mode settings: Click this button to enter the
common mode interface.
Effective unit: Click this button to enter the effective unit
selection interface.
External control setting interface:Click this button to enter the
communication setup interface.
4 - Loop unit selecting interface
Select the unit
Please choose to view the unit
1234
678
5
ESC
In the main interface, you can click the “FCS” logo to enter
the loop unit selecting interface. After selecting the units, the
speed will display in “A“ area and system parameters in “D”
area will change to display the selected unit’s speed and
parameters.
PDS II

-7 -
5 - Effective unit interface.
The effective unit interface diagram is below:
Click the “effective unit” button in the main interface to
enter the effective unit selection interface. You can set the
validity of the unit here. When finished, you can click the
“OK” button to go back to main interface. If aunit is in
operation, the current working unit can‟t be modified.
Please note: Selecting effective unit is the first step to
set parameters.You can only operate on the effective units.
6 - Independent operating parameters settingsinterface
The diagram of the Independent operating parameters settings
are below:
PDS II

-8 -
When the unit stopsworking, click the bottle which selects it as
the independent effective unit to enter the parameter
settingsinterface of the corresponding unit.
A - Unit number display:This area displaysthe current
parameter settings' unit number.
B - System parameter settings:This area is for setting the
system parameters of this unit. It includes the pump model, tube
type, back suction angle,and direction. If the pump head or
tube is changed, then it will recalculate the parameters
and the calibration data will resume to the default setting.
C - Transferring working mode Parameter settings:This area
is for setting the transferring parameters. Click the “ ” sign to
select this mode and set the start delay, flow rate,and speed
of this unit under transferring working mode.
D - Dispensing working mode Parameter settings:This area is
for setting the dispensing parameters of the unit. Click the “ ”
sign to select this mode and set the parameters of this unit
under dispensing working mode.
E - Correction button:Click this button to enter flow rate
calibration interface.You can calibrate the flow rate
of the independent operating unit.
7 - Independent working mode flow rate calibration
interface.
Diagram of Independent operation flow rate calibration
interface as follows:
PDS II

-9 -
unit7
Step 03
Volume
7.0000 mL
Rum time
60.00 S
Test Vol
0.0000 mL
start
CAL
Reset
Ass
Dec
ESC
Fine adjust
+0.0000 uL
In the independent operation parameter settingsinterface, click
the calibration button to enter the calibration interface. In
dispensing mode, first click the “dispensing groups” drop-down
list, then choose the dispensing groups for calibrating unit (to
ensure the filling accuracy, you need to calibrate separately for
each group), target volume,and working time are data set before
and they are not modified. In the transferring working mode, the
target volume is the calculation result of current flow rate and
working time.It is not modified. The default working time is
60s.You can click it to modify.
Calibration process before working:
A - Enter the calibration interface. In dispensing mode,you
can‟t change the running time.In transferring mode, you can
set the running time.
B - Click the start button to start the test. The display will
countdown dispensing time. It will stop automatically and
the numerical keyboard will appear. Input the actual dispensing
volume. After input,it will ask whether to continue the
test (suggest 3 times). If you choose „YES,‟ it will test again. If
you choose „NO,‟ you'll go back to the calibration interface.
C - After several tests, actual dispensing volume display area
PDS II

- 10 -
displays the average volume. Click „Calibration‟ button.
Display calibration successful.
D - Test again to check whether the dispensing volume
meetsrequirements.If higher accuracy is needed,you can use the
adjust function.Click the „Add‟ or „Dec‟ button to micro-adjust
the dispensing volume to meet high accuracy dispensing.
E - Clicking the „Cancel‟ button cancels the tests. Actual filling
volume returnsto 0.
8 - Logic working mode checking interface
Logic working mode checking interface table:
In the running state of the allocation mode, click on the
running bottle at the main interface to enter this interface. In
this interface, you can view the unit's system parameter
settingsand detailed allocation parameters. Clicking on
the micro increase or micro decrease buttons, you can adjust
the currently running allocation group of this unit. Click on
the exit button takes you back to the main interface.
9 - Full speed interface
Full speed interface shown below
PDS II

- 11 -
RUN Back
Please select the vaild unit and itd direction
Unit1
Unit5 Unit6
√
Unit7 Unit8
√√
Unit3Unit2
√Unit4
Click on the full speed button in the main interface takes you
to the full speed interface. After selecting the direction and
number of the unit, click the full speed button.The selected
unit runs at full speed in the selected direction. Clicking the
select all button selects all units.If the running unit is in
transmission mode, then you can choose the unit,but you cannot
change the direction.Ifin allocation mode or logic mode, the
unit is effective, then the unit can't be set to full speed.
10 - Common mode interface:
Independent operation common mode interface:
Free Relative
Mode 1
unit Pump
head
Tubing
size
Suck-
back mode Flow
1YZ1515X 13# 360.00 7.00ml/min
Dispens
2YZ1515X 16# 0.00 90.00ml/min
Transfer
3 --
4
Calling Delete Clear Return
5
Save mode Parameter
--
--
--
--
--
--
--
--
--
--
--
6
VOL ml Run time
--
--
--
-- --
45 30.00 S
--
--
--
--
--
--
-- -- -- -- -- -- --
PDS II

- 12 -
Click the common mode button in the main interface to enter
Call button: Click this button to call the common mode.The
operating parameters of the corresponding unit after the call will
be changed to the parameters of the commonly used mode.
Delete button: Select acommon mode.Click the delete
button. This will pop up a dialog box asking whether to
delete the dialog box.Click 'yes' to delete this model.
Empty button: Clicking this button will pop up adialog box
asking "all empty?" Click "yes" for empty all mode.
Cancel button: Click this button to return to the system
settings interface.
Add and subtract page button: If you have more than
one common mode, click on this button to view the
previous page or the next page of the commonly used mode.
Save mode button (the common mode interface of
independent operation): Click this button to save the
current parameters of all the independent operating units as a
common model.It is convenient for the users to save the
settingsof the parameters (can save up to 5 groups).
Detailed parameters button (the common mode interface of
independent operation): After you select a certain unit of
the filling mode in the following table, click this button to see
the detailed parameters of the filling unit.
11 - External control settingsinterface
External control setting interface:
PDS II

- 13 -
Set baud rate
9600
RS232/RS485
RS232
Stave NO.
01
Lack on/off
ON OFF
Return
COM ON/OFF
ON OFF
Click the external control set button in the main interface to
enter the external control set interface. The interface can set the
relevant parameters of communication and the start/stop of the
stop filling due to lack of bottle.
This product supports Modbus communication protocol -
RTU mode. First,select the communication baud rate
and the communication interface (RS232 or RS485).Click on
the local host button of the machine.Input the peristaltic
pump address number (1-32) for selecting a communication
enable to on.Now the pump can communicate with the PC,
receiving a PC control signal.
Note: After the setting is completed, the peristalsis pump can only
receive the communication signal control at the main
interface. Other settings interface communication control is invalid.
This product supports stop filling due to lack of bottle function.
Select the function button for ON. At this point, the pump can
receive the signal of the "stop filling:lack of bottle,"and when the
signal is received, the pump stops running and alarms immediately.
12 - Start/stop operation area
Independent operation area: Click on the right side of the plus,
PDS II

- 14 -
minus button in order to select the unit that you wish to
operate."ALL" is the operation for all independent
operation of the effective unit.
13 - Set date time interface
Set date and time interface:
Back
12-hour
24-hour
Set Date
Set Time
2012-3-15
8:45:35 AM
Friday
This interface can be set to the current date and time and
display in the upper right corner of the main interface.
Click set date button. This popsup the digital keyboard.Set the
year range for 1970-2099.After setting, click OK to enter the
month, then set the day.Click the set time button. This pops up
the digital keyboard.Set the hours, minutes, and seconds.
Filling Volume Reference Parameter (Media is water)
Controller
Pump
head
Tubing
size
Filling
volume
(ml)
Filling
time
(s)
Filling
accuracy
(±%)
PDS
YZ1515x
YZ2515x
13#
0.1
0.5
±5μl
13#
0.3
0.7
1.5
13#
0.5
1
0.8
PDS II

- 15 -
13#
1
2
0.5
14#
2
1
1
14#
3
1.5
0.8
19#
5
1.2
1
16#
7
1
0.5
25#/15
#
10
1
1
25#/15
#
15
1
0.8
25#/15
#
20
1.2
0.5
17#/24
#
30
1.2
0.8
17#/24
#
50
2
0.5
18#
80
2.5
0.5
18#
100
3
0.5
DZ25-3L
35#
150
4
0.5
36#
200
4
0.5
PDS II Technical Specifications
Dispensing volume
0.1-9999ml
Prime speed
600rpm
Dispensing time range
0.1-9999s
External control
Switch signal
Pause time range
0.5-9999s
Speed resolution
0.1rpm
PDS II

- 16 -
Volume resolution
0.01ml
Temperature
0-40℃
Time resolution
0.01s
Relative Wet
<80%
Dispensing numbers
1-9999,0means
unlimited
Controller Dimension
(L*W*H)
240*185*85
mm
Speed range
0.1-600rpm
Controller weight
2.5Kg
Back suction angle
0-360°
IP rate
IP31
Product size chart:
Filling unit size chart: Unit (mm)
PDS II

- 17 -
Main functions and features of PDS II
All models of pump heads can be installed on the PDS
pump.The same controller can control a variety of different
models of pump head at the same time.
Precise angle control technology to achieve high precision
filling
Each filling unit not only can transfer liquid but also can
dispense liquid
Color display w/touch screen, user-friendly interface,
dynamic display filling status.Display system settings for
8 cells on the same screen.
Intelligent calibration function: Automatic calibration of
filling volume before production to ensure the filling accuracy
Online micro adjusting function:Helps you adjust the
liquid volume to a certain filling unit in order to prevent
filling error caused by fatigue and the elasticity of the
hose
Multiple filling units can be extended on a controller to
maximize the cost savings.
Each unit is independently controlled and can be set with
different filling parameters, start/stop independently,or at
the same time.
Real-time monitoring, dynamic display monitoring results,
and alarm function ensures safe production.
Effective unit settingscan be opened or closed at any one or
several filling units.This can be set to a logical operation or
independent operation mode so as to meet different needs.
Back suction angle setting avoidsliquid drop off when the
PDS II
Table of contents
Popular Laboratory Equipment manuals by other brands

COMINOX
COMINOX Sterilclave 6 B Speedy Use and maintenance manual

MELAG
MELAG Euroklav 23 S+ Technical manual
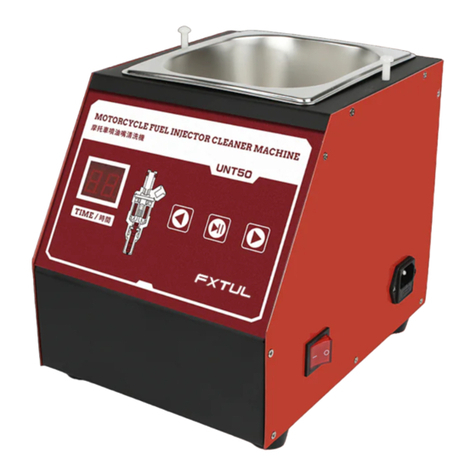
FXTUL
FXTUL UNT50 user manual
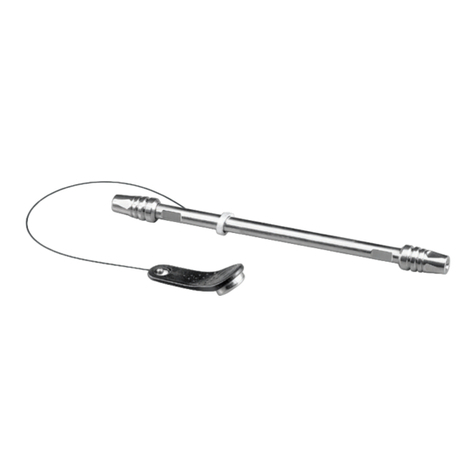
Waters
Waters Anionic Polar Pesticide Column Care and use manual
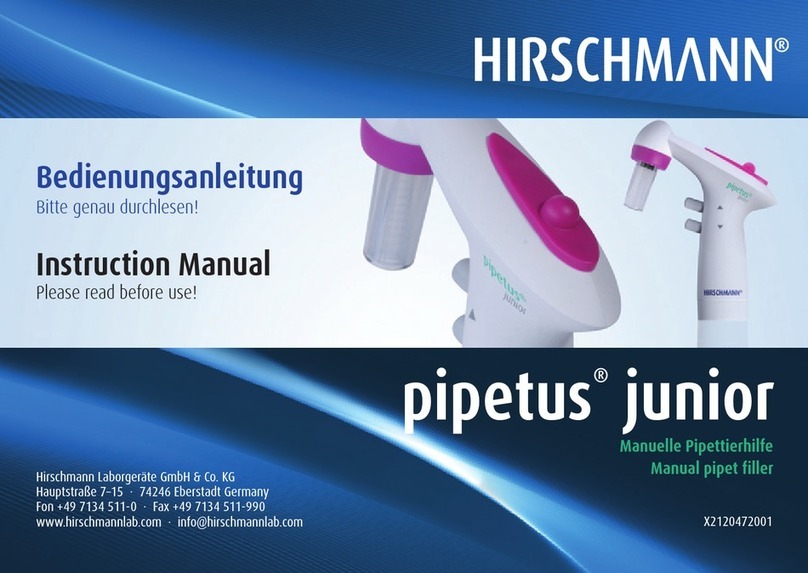
Hirschmann
Hirschmann Pipetus Junior instruction manual
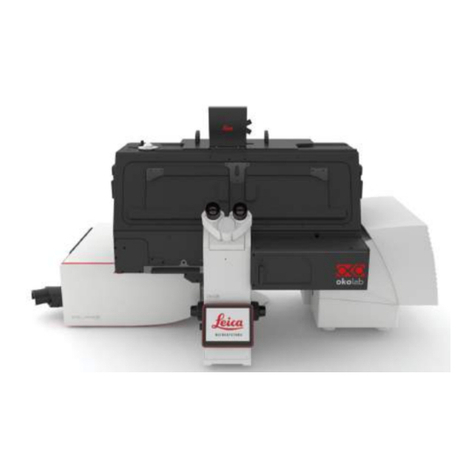
Okolab
Okolab H201-ENCLOSURE-DMi8-LASERSAFE-158 Assembly manual