FMX TD200 Series User manual

Customer is solely responsible for validating application, operation,
maintenance, and code compliance and other information and data
relating to the installation, operation, safety, and maintenance of all
components. There is no guarantee that this information is suitable for
your application, nor is there any manufacturer/supplier assumption of
responsibility for your product design, installation, testing, or operation.
Information herein is provided “as is” with no guarantee of any kind. Every
attempt has been made to ensure the accuracy and reliability of the
information provided in this document.
Check the label affixed to the side of the drive and make sure the
input and output power specifications match the available power
source and motor.
PRODUCT: E510-2P5-H-U MOTOR RATING: 0.5 HP
INPUT : AC 3PH 200-240V (+10%,-15%) 50/60Hz 4A
OUTPUT : AC 3PH 0-599 Hz 2.6A IP20/NEMA 1
ENCLOSURE : IP20
P/N BARCODE S/N BARCODE
TD200-20P5-3PH
1
2
4
5
4.8” / 12cm
2” / 5cm
4.8” / 12cm
2” / 5cm
Enclosure
Cooling Fan
Vent
Operating
Temperature:
-10°C - +50°C (14-122 °F)
If AC Drive is placed in an enclosure, provide
additional cooling and ventilation to maintain
ambient temperatures below
50°C
(
122 °F
)
AC Drive Label
Minimum Spacing Requirements
Adequate thermal management is key to extending the life of the AC
drive. Overheating and excessive dust/debris will shorten the life of
the drive significantly.
Identify Drive Specifications
Enclosure
Cooling Fan
2” / 5cm
Vent
1Verify receipt of proper drive model
2Verify Input Power
3Provide adequate circuit provision
• Ensure proper wire size
• Provide proper circuit protection
• Comply to all local codes and regulations
4Output Amperage
• Ensure output is adequate to meet the full load amps of the
motor or application
5Verify Environment
• Provide proper environmental protection
• Install drive in a clean and cool environment protected from
contaminants and debris
QUICK START
GUIDE
STEP 1
Mounting/Spacing Requirements
STEP 2
Applicable Models:
• 120V (1PH): 0.25 – 1HP
• 240V (1PH): 0.25 – 3HP
• 240V (3PH): 0.5 – 3HP
• 480V (3PH): 1 – 3HP
CAUTION
Installation and wiring must be performed by qualified personnel
Do NOT remove any protective covers or attempt any wiring while input
power is applied. Connect all power wiring and control wiring before
applying input power. Always turn OFF the power supply before
attempting AC Drive installation and terminal wiring.
Internal capacitors hold a charge after power supply has been removed.
After disconnecting power, wait at least 10 minutes before touching any
wiring, circuit boards, or components.
Check all wiring to ensure all connections are correct after installation of
AC Drive and any other devices. Failure to comply could result in serious
injury, death, fire, or damage to the AC Drive.
Do not use an improper voltage source. Failure to comply could result in
in serious injury, death, fire, or damage to the AC Drive. Verify the rated
voltage of the AC Drive matches the voltage of the incoming power
supply before applying power.
Do not connect a contactor or switch in series with the AC Drive and the
motor.
WARNING
This document is intended to provide a short guide on the installation
and setup of a FMX Tough Drive. Refer to the user manual for all safety
precautions and further details regarding installing, wiring, operating,
servicing, or inspecting the AC Drive.
NOTE
TD200-QS

Circuit protection must be installed before AC drive. See section 2.3
of the user manual for the appropriate circuit breaker for your drive.
AC Drive and motor-side ground. Improper grounding could result
in serious injury or death from contacting the motor case.
Grounding impedance: 240V class - less than 100Ω,
480V class - less than 10Ω
Do not connect any other terminal to ground.
Only the ground terminal with the symbol should be
connected to ground.
MAIN CIRCUIT POWER SUPPLY TERMINALS MUST BE
CORRECTLY WIRED
Single Phase Input: L1(L) and L3(N)
Three Phase Input: L1(L), L2, and L3(N)
MOTOR CONNECTION ONLY: T1, T2, T3
(input power connection here will destroy the AC Drive)
L1(L)
L2
L3(N)
AC Line
Reactor
Circuit
Protection
AC Input Voltage
Disconnect
3PH Input Models
1PH Input Models
Power Terminal Descriptions
Terminal Function
L1(L)
Power input
Single phase:L1(L)/L3(N)
L2
Three phase:L1/L2/L3
L3(N)
T1
AC Drive output, connect to U/V/W terminals of motorT2
T3
PExternally connected braking resistor, 480V models only
(Please see the braking resistors reference table in user manual)
BR
Ground terminal
Wiring the AC Drive
STEP 3
WARNING
Depending on the AC drive model, terminal labels and layouts may be
slightly different. Please see table below for details on terminal labels
and their functions.
NOTE
1: Only 480V 1-3HP units have a built-in braking
transistor. The braking resistor can be
connected directly between P and BR. All
others do not have external braking
capabilities.
2: Grounding impedance: 240V class - less than
100Ω, 480V class - less than 10Ω
Greater impedance indicates a poor ground.
NOTE
L1
L2
L3
T1
T2
T3
PBR
3Ø Induction motor
10V: Max. 20mA
AV I: Mul ti- Fun cti on An al og In pu t
ACI: Multi-Function Analog Input
S1
AO
AG ND
Analog Output
0 – 10 VD C
S2
S3
S4
S5
Multi-Functional Digital Inputs
(Default Settings)
Pr ese t S pe ed 2
Pr ese t S pe ed 1
FWD / STOP
REV / STO P
Braking Connection
COM (NPN)
AG ND: Ana log Signal Comm on
Multi-function
Relay Output
Con tact ra ti ng :
• 250VAC < 1.0A
• 30VDC < 1.0A
RA
RB
Reset
NO
Shielded wire
Control circuit
Main circuit
Note: 1
AC Line
Reactor
Circuit
Protection
AC Input Voltage
Motor
External Analog Inputs
0 – 10V o r
0 – 20mA
Potentiometer:
Disconnect
Note: 2
RS485 COM1
RJ45
1:RS485+
2:RS485-
7: 5V
8: GND
1
2
7
8
L
1
L
2
L
3
AC
Line
R
eac
t
or
C
ircuit
Pr
o
t
ec
ti
o
n
AC Input Voltage
Disconnect

Default Acceleration and Deceleration times are listed below.
Set (Acceleration Time 1) and (Deceleration Time 1) to
desired times.
Refer to the motor nameplate for FLA (Amps) when setting up the
drive. For this example we will use a 460V motor rated at 1.5 Full
Load Amps. Refer to the motor nameplate for FLA required at the
voltage in your application. An example nameplate is shown below:
1. Press MODE/PROG.
Display shows
+
2. Use navigation keys to
go to
3. Press and
hold LEFT/
ENTER then
use navigation
keys to enter
FLA of
4. Press and hold
LEFT/ENTER to save.
Display shows
+
5. Press
MODE/PROG
twice. Display
shows motor
frequency.
Commonly Used Parameters
I.D. Default Function Setting Range
00-02 0Main Run Command
Source Selection
0: Keypad
1: External Terminal (Control
Circuit)
2: Comm. Control (RS-485)
00-04 0Operation Modes for
External Terminals
0: Forward/Stop-Reverse/Stop
1: Run/Stop- Reverse/Forward
2: 3 Wire Control Mode Run/Stop
00-05 1Main Frequency
Command Source
0: UP/DOWN from Keypad
1: Potentiometer on Keypad
2: External AVI Analog Input
3: External ACI Analog Input
4: External Up/Down Frequency
5: Communication Setting Freq.
6: PID Output Frequency
00-12 60 Frequency Upper Limit 0.01–599.00 Hz
00-13 0Frequency Lower Limit 0.01–598.99 Hz
00-14 10.0 Acceleration Time 1 0.1–6000.0 s
00-15 10.0 Deceleration Time 1 0.1–6000.0 s
01-00 4Volts/Hz Patterns 1-7
02-01 –
Rated Current of Motor 1
(Amps)
Setting range is dependent on AC
drive model
07-09 0Stop Mode 0: Deceleration to Stop
1: Coast to Stop
I.D. Default Function Setting Range
00-14 10.0 Acceleration Time 1 0.1–6000.0 s
00-15 10.0 Deceleration Time 1 0.1–6000.0 s
Set Accel./Decel. Times (Optional)
STEP 6
Check Motor Direction
STEP 4
Set Motor FLA
STEP 5
Internal capacitors hold a charge after power supply has been removed.
After disconnecting power, wait at least 10 minutes before touching any
wiring, circuit boards, or components.
Make sure it is safe to operate the AC Drive and motor before testing
motor direction.
WARNING
4. If motor does not turn in the desired direction: Remove power from
AC Drive and wait at least ten minutes for the capacitor charge to
drain completely. Swap T1 and T2 output leads at the AC Drive.
Repeat steps 1 and 2 to re-check the motor direction.
This test is to be performed solely
from the AC Drive keypad. Following
procedures assume all AC Drive
parameters are at default values and
all motor and input wiring
has been
completed correctly.
1. Apply input power to the AC Drive.
The display blinks, showing the
current output frequency setting.
(Set using the keypad potentiometer
by default)
2. Press the key. Motor will
operate at the speed set. Frequency
display on the keypad will be solid.
3. Press the key to stop the
motor.
PH FRAME
HP(kW) RPM
ENCL TYPE PF IP55
SF INS CL CODE HZ
NEMA NOM EFF 3/4 LOAD EFF DES
VOLTS AMPS
DUTY SFA MAX AMB
INVERTER DUTY MOTOR
356
1(0.75) 3470
TEFC 0.88
1.25 F K60
86.5 86.5 B
208-230/460 3.3-3.0/1.5
Cont 40C
Keypad Potentiometer
(Default Frequency Source)
Example Motor Nameplate
Example Procedure

• Set (Operation Modes for External Terminals) to
for “3-wire program initialization”.
• Set (Main Frequency Command Source) to for
External AVI Analog Signal input.
• See Diagram 3 for 3-wire control.
S1
S2
S3 Forward/Reverse
selection
COM
Run (N.O.Momentary)
Stop
(N.C. Momentary) Stop Command
Run Command
+10V: Max. 20mA
AV I: 0 -1 0VD C An al og In pu t
AG ND: Ana log Sign al Comm on
(N.O.Maintained)
FOR / REV
Potentiometer:
2kΩ – 10kΩ
S1
S2
COM
Forward
Reverse
Setting 00: 2-Wire FWD/REV External Control (default)
2-Wire External Control Operation
Setting 02: 3-wire Control, FWD/REV Selector, with
External Speed Pot.
REVERSE
FORWARD
STOP
RUN
REVFOR
SPEED
100
11001000
2-Wire External Control Operation
2. Press MODE/PROG.
Display shows
3. Use navigation keys to
go to
+
4. Press and
hold LEFT/
ENTER then
use nav. keys
to enter
”External
Terminal”
5. Press and hold
READ/ENTER
to save.
Display shows
8. Press MODE/PROG
until display shows
motor frequency.
Terminal S1 Terminal S2 Operation
Open Open Stop AC Drive
Closed Open Run Forward
Open Closed Run Reverse
Closed Closed Stop AC Drive, Display EF9 Alarm after
500ms
Terminal S1 Terminal S2 Operation
Open Open Stop AC Drive
Closed Open Run Forward
Closed Closed Run Reverse
3-Wire External Control Operation
Terminal S1 Terminal S2 Terminal S3 Operation
Open Open Open Stop AC Drive
Closed Open Closed Stop AC Drive
Open Closed Open Run Forward
Closed Closed Closed Run Reverse
6. Set to desired control mode below:
For default configuration (FWD/REV), go to Setting 00
For 2-wire RUN/STOP mode, go to Setting 01
For 3-wire control mode, go to Setting 02
Note: Terminal S1 must be closed for a minimum of
50ms to activate operation.
Set Main Command Source (Optional)
STEP 7
STOPRUN
REVFOR
S1
S2
COM
Run / Stop
Forward /
Reverse
Setting 01: 2-Wire RUN/STOP External Control
• Set (Operation Modes for External Terminals) to
• See Diagram 2 for 2-wire RUN/STOP control.
Return to AC Drive Status Display
• The default value of (Operation Modes for External
Terminals) is “2-Wire FWD/REV External Control”
• See Diagram 1 for 2-wire FWD/REV control.
Diagram 1: 2-Wire FWD/REV External Control (default)
Diagram 2: 2-Wire RUN/STOP External Control
Diagram 3: 3-wire Control, FWD/REV Selector, with
External Speed Pot.
1. Set to
using the steps below.
7. Leave (S1 Multi-function Input) as and
(S2 Multi-function Input) as .
Example Procedure
This manual suits for next models
1
Other FMX DC Drive manuals
Popular DC Drive manuals by other brands

Masterflex
Masterflex L/S 07528-40 operating manual
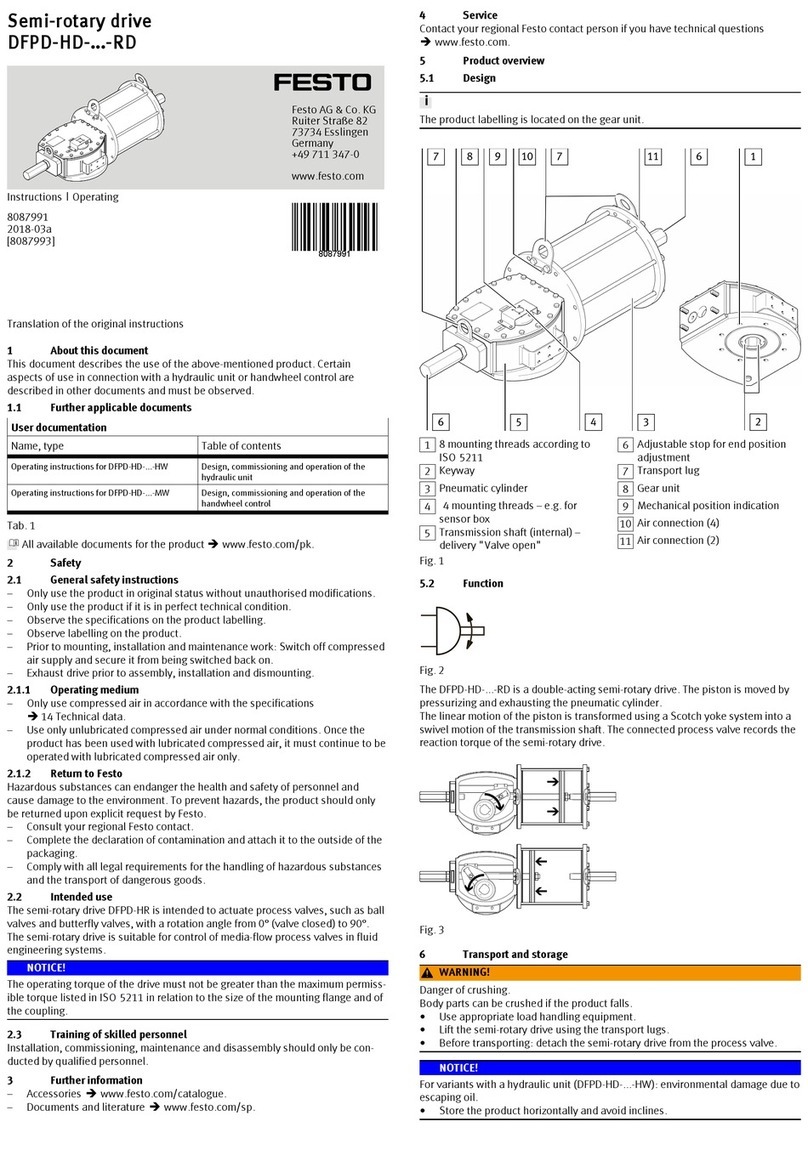
Festo
Festo DFPD-HD-RD Series Instructions and Operating
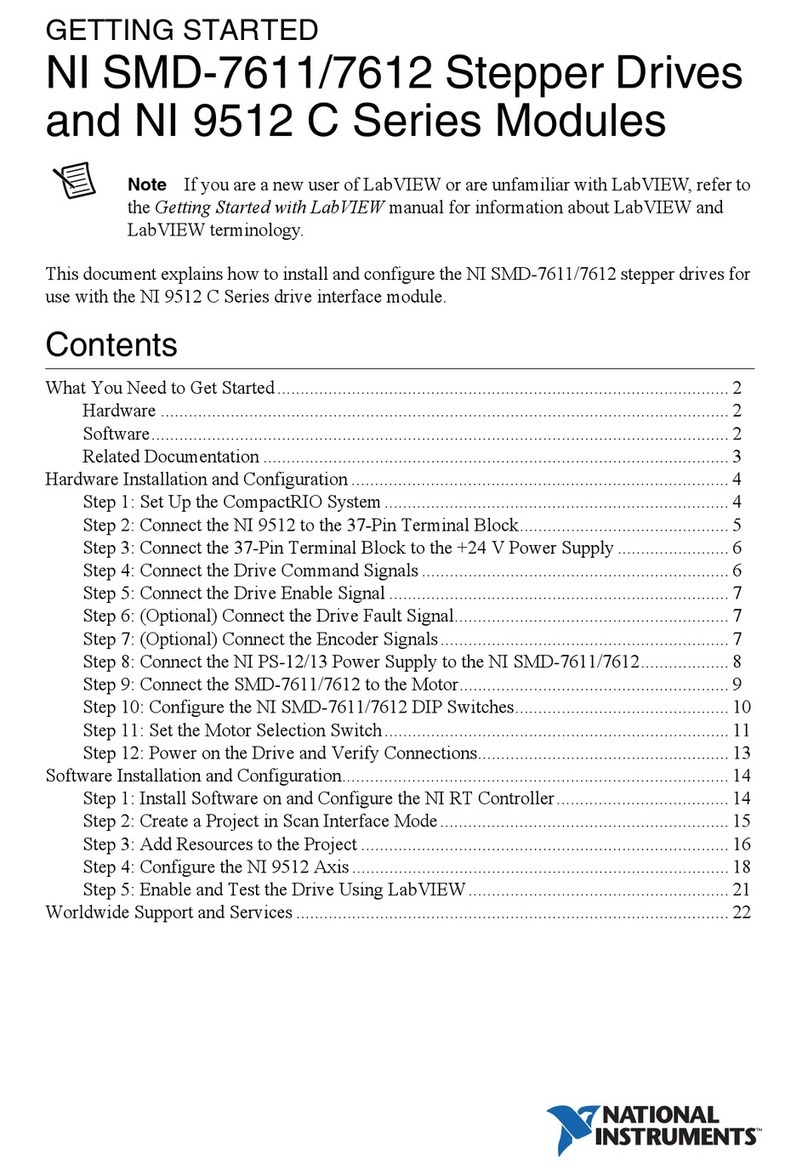
National Instruments
National Instruments 9512 C Series Getting started

LOVATO ELECTRIC
LOVATO ELECTRIC VLA1 series installation manual
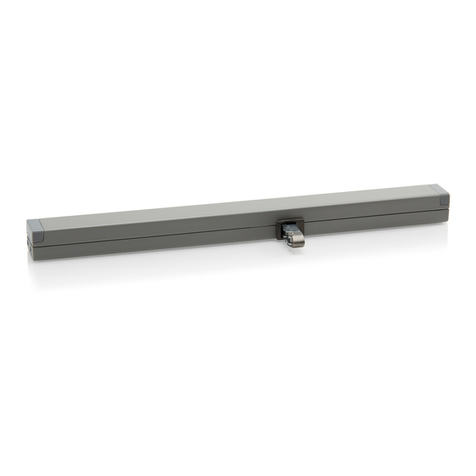
D+H
D+H CDC 200 -BSY+ Original instructions
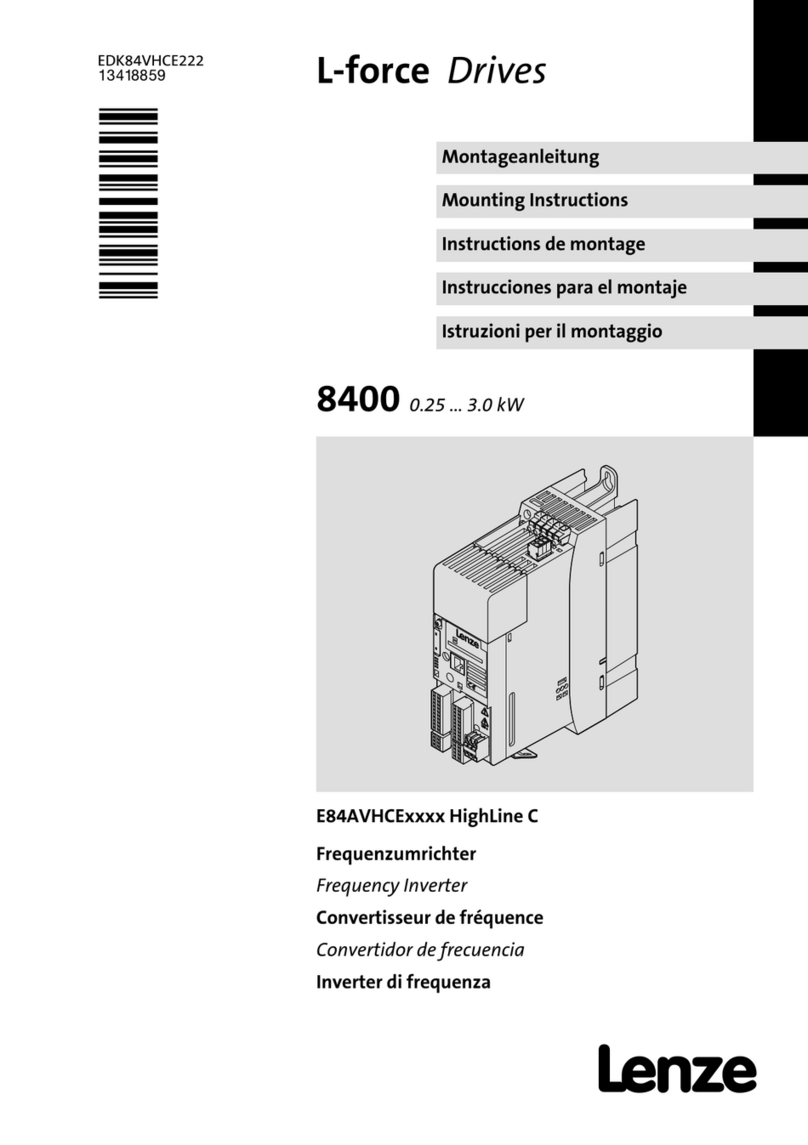
Lenze
Lenze L-force 8400 Series Mounting instructions
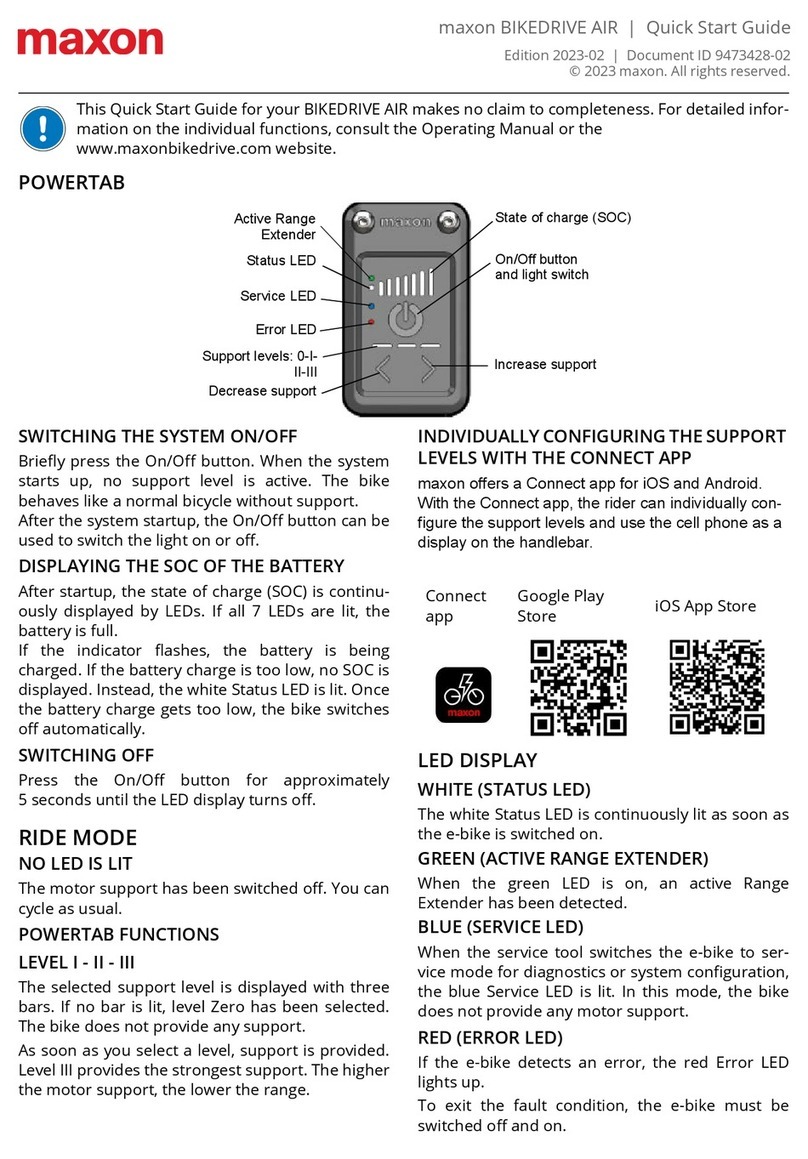
Maxon
Maxon BIKEDRIVE quick start guide

Pro-dig
Pro-dig T9K5 Operating Instruction, Maintenance Instruction
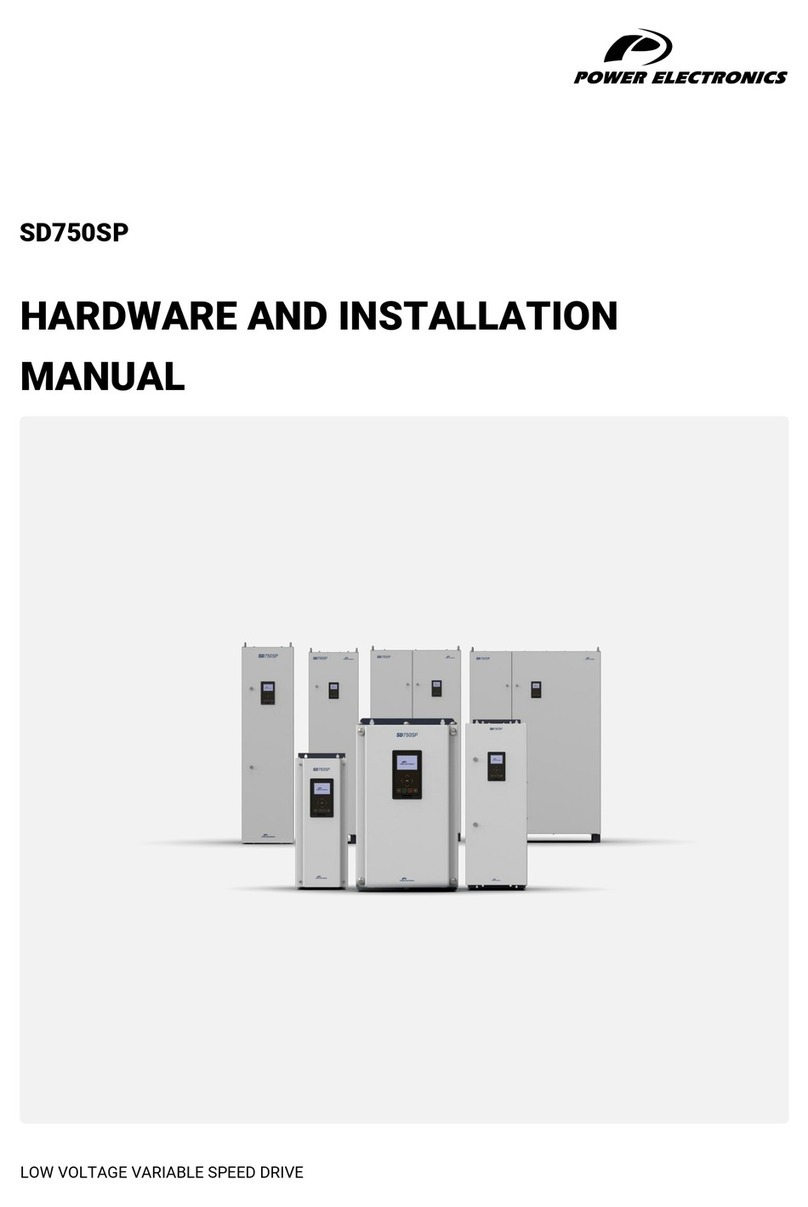
Power Electronics
Power Electronics SD750SP Hardware and installation manual
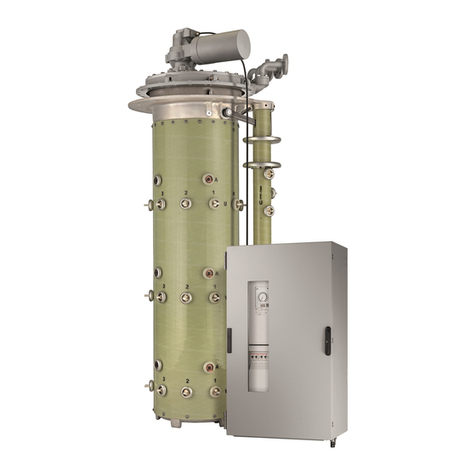
MR
MR ETOS TD operating instructions
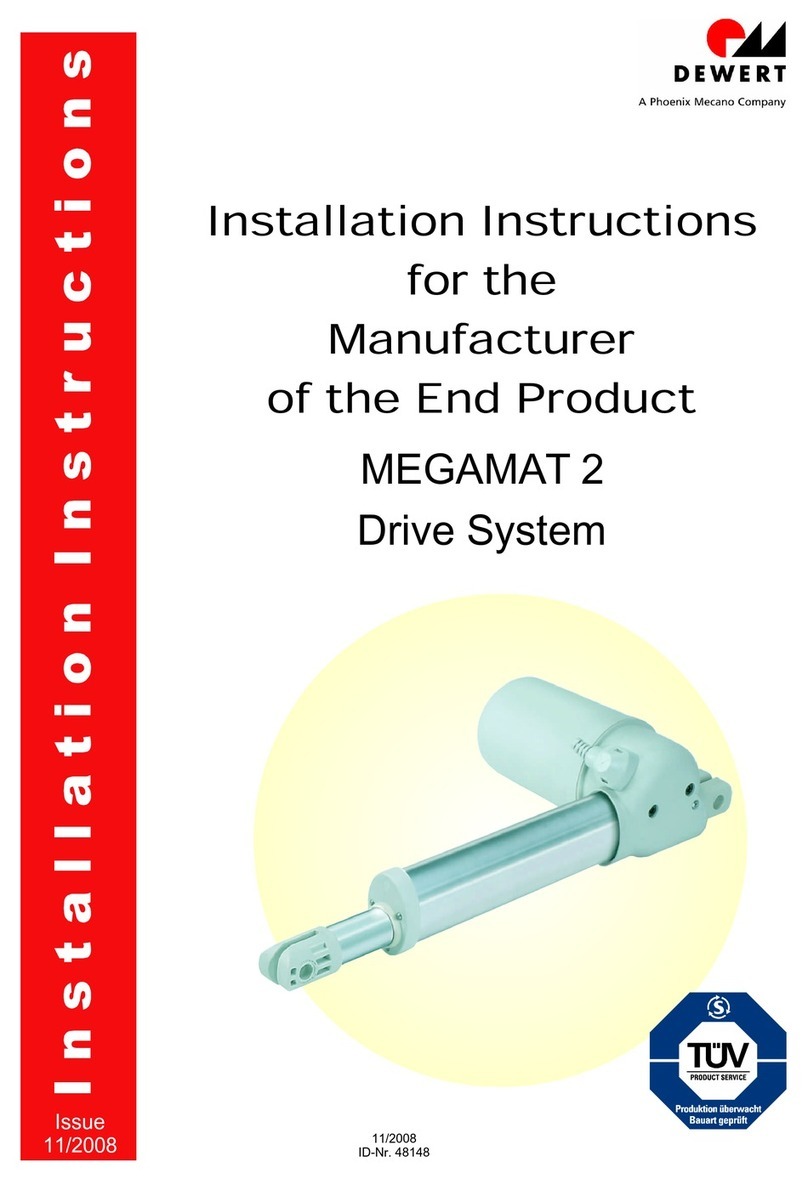
Phoenix Mecano
Phoenix Mecano DEWERT MEGAMAT 2 installation instructions

ABB
ABB ACS580MV Hardware manual