gazex MDD-256/T User manual

MDD-256/T Control Unit User Manual Issue 1W21en ©gazex’2018 v1806 Page 1/ 22
Warsaw
Digital
Control
Unit
Issue 1W21en
M
MD
DD
D-
-2
25
56
6/
/
T
T
[ series W2 ]
BEFORE installation, fully read
the USER MANUAL.
Proceed with installation only after
gaining a full understanding of this
Manual.
For safety reasons during installation and use of the
device, it is advisable to follow the recommendations and
warnings included in this Manual and marked with the
depicted symbol.
The Manual should be stored for the Digital Gas Detection
Systems’ User perusal.
1.
Purpose
p. 2
2.
Technical specifications
3
3.
Description and assembly
4
4.
MDD installation within the system
5
5.
MDD configuration
8
6.
Digital Gas Detection System launch
15
6.8
PROBLEM ? Useful information
18
6.9
Installation and launch recommendations
19
7.
Maintenance/operation
22
8.
Storing the MDD
22
PRODUCER:
©gazex 2018. All rights reserved. No part of these pages, either text or image may be copied or distributed without GAZEX’s permission.
The gazex logo and name as well as dex, ASBIG, Aktywny System Bezpieczeństwa Instalacji Gazowej are registered trademarks of the GAZEX
company.
Work and live SAFER with us ! ©gazex
USER MANUAL

MDD-256/T Control Unit User Manual Issue 1W21en ©gazex’2018 v1806 Page 2/ 22
1. PURPOSE
The MDD-256/T Control Unit is designed for monitoring Digital Gas Detection System (DGDS)
consisting of DG/M, DD or DG.EN/M digital detectors and MDD..., MDP-1.A/TM digital modules
equipped with RS-485 digital communication port. Communication between the module and its
components takes place in the RS-485 industrial standard according to the MODBUS RTU protocol.
Supervision and control consists of cyclical polling of individual devices by the control module, and when
certain specified alarm parameters are exceeded, optical alarm signalling is activated, module outputs
are activated, and information is transmitted via digital network to another control/visualisation system. In
next parts of this Manual, the MDD-256/T control module will be referred to as the "MDD" module.
Features and functions performed by the MDD:
controls and manages the network of digital detectors and digital modules; controls the condition of
the wired connection with the detectors (provides full emergency detection);
galvanically isolated communication channel with RS-485 standard detectors (Modbus RTU);
enables remote configuration of detector parameters connected to the bus, i.e. changing alarm
thresholds, zeroing devices;
enables built-in procedures to facilitate remote configuration of detector networks, i.e. scanning the
existing network, addressing devices in a new and in the existing network, deleting device addresses
enables operation in four modes: "MEMORY MODE" - indicates that alarms have occurred after the
alarm has disappeared, "MAINTAINING MODE" - maintains active alarm states after the alarm source
has disappeared, "NO-MEMORY MODE" - automatically zeroes out the status of inputs and outputs
on the front panel after the alarm state has disappeared, "SERVICE MODE" - deactivates the module
outputs for 1 hour;
regardless of the above mentioned operation modes – it is possible switch on the following modes
directly with the front panel buttons: "SILENT MODE" - mutes the inner siren, "A2 LOCK MODE" -
deactivates the A2 voltage output for 15 minutes or until the next A2 Alarm occurs;
visually displays alarm and emergency states of individual detectors (LED display) and OUT1, OUT2,
OUT3, OUT4 control outputs, with simultaneous acoustic signalling (built-in siren);
allows changing the screen message display modes, i.e. collective alarms or cyclic display of the
individual detectors status;
stores in a non-volatile, internal memory 3000 recent events with an assigned time of occurrence and
a source of the event;
enables diverse configuration of outputs with assignment of a given output to a specific alarm or to a
selected zone;
enables very precise determination of on/off delay times of the outputs and their stability in time
thanks to microprocessor control;
voltage alarm outputs = 12V configurable, OUT5 and OUT6 control additional acoustic and optical
signalling devices;
OUT1, OUT2, OUT3 and OUT4 contact outputs are configurable (galvanically separated) and control
fans, motors, contactors, information boards, or connect with building’s/facility’s automation;
configurable fault contact output (galvanically separated) informs about the module's alarm status,
damage to the detectors’ connection line, or power failure;
the second isolated RS-485 communication channel (Modbus RTU) ensures cooperation with
external monitoring modules or with "intelligent building" control systems;
the casing is suitable for mounting on TS35 rail in standard electrical switchboards;
configuration of module settings by means of a keyboard on the front panel;
removable cable terminals on all outputs = improved start-up and servicing;
possibility to display and configure the module on a PC and to read the internal event log using the
"MDD256_View" software - available for download from www.gazex.pl or as a CDROM (see
MDD256_Visual set available from GAZEX).

MDD-256/T Control Unit User Manual Issue 1W21en ©gazex’2018 v1806 Page 3/ 22
CONNECTION DIAGRAM
MDD-1
DEX/P
MDD-1/T
24VDC
CONTROL OUTPUTS
DG/M
RS-485 bus
DG/F
MDD-256/T
DG.EN/M
DD
DEX/F
DG/P
MDD-L32/T
PU/T
230VAC
CONTROL OUTPUTS
RS485 (to BMS)
RS-485 bus
CB-4
MDD-R4/T
OUTPUTS
CB-4
PU/TB
CB-4
2. TECHNICAL SPECIFICATIONS
Model
MDD-256/T
Supply voltage
24V= (permissible range 15,0 ÷ 30V)
Power consumption
0,1A @24V= (without load on the 12V alarm outputs),
max 0,3A @24V (with max load on the 12V alarm outputs)
Operating temperature
-10°C to +40°C recommended,
-20°C to +45°C allowed periodically (<2h/24h)
Digital communication
PORT1 (network [DET.NET]): RS-485 standard, MODBUS RTU protocol,
parameters: 9600bps (11-bit frame, parity check: even, 1 stop bit)
galvanically isolated 1kV;
PORT2 (network [OUT.NET]): RS-485 standard, Modbus RTU protocol,
parameters: from 9600bps to 57600bps (11-bit frame, parity check: even or none, 1
or 2 stop bits) galvanically isolated 1kV;
Optical signalling of the
DET.NET network status
LED display - collective alarms of a detector network or the status of individual
detectors with indication of the measurement units: % of the range, %DGW, %v/v or
ppm
Optical signalling
of alarm states or operating conditions: 8 LEDs;
Fault signalling
yellow LED + messages on the LED sectional display
Acoustic signalling
inner piezoceramic siren:, max 65dB/30cm;
1Hz intermittent signal - A1 alarm signal
5Hz intermittent signal – A2 alarm signal
10Hz intermittent signal - A3 alarm signal
constant signal – FAULT signal;
(optional: no signalling – „SLEEP MODE” set with the keyboard)
Zeroing the module
using the button on the front panel or remotely via PORT2
Ev
ent memory
internal, non-volatile, 3000 recent alarm or fault states or configuration changes;
can be read from the „MDD256_View” PC software
Real-time clock
in-built, with battery support; setting date and time is possible via the
„MDD256_View” PC software
Voltage alarm output
OUT5, OUT6 – 12V=, sta bilised; total load = max 0,2A, to connect the SL-21,
SL-32, S-3x, LD-2 signalling devices
Control outputs
OUT1, OUT2, OUT3, OUT4 – relay, type NO and NC, load capacity: max 4A (with
resistive load) or max 2A (with inductive load - motors) or max 0,6A
(with purely inductive load – fluorescent lamps); max 250V~ or max 30V=
Output delays adjustment
activating outputs: 10 sec. by default, regulation: 3 ÷300 sec.;
deactivating outputs: 10 sec. by default, regulation 3 ÷900 sec.
Deactivating outputs
standard: automatic – alarm state deleted when the alarm source has disappeared
with same delay as in output deactivating (alarm memory is signalled on the
display),
optional:manual –
alarm state at the outputs maintained after the alarm source has
disappeared until it’s been manually deleted by the user (with the „OK./
Reset” key)
Module power supply control
green LED; also indicates the warm-up status of the MDD
Size, weight
106 x 90 x 65 mm, width x height x depth (width of 6 mod.); ca. 0,2kg
Casing
polystyrene, IP20; for installation in electrical switchboards on a 35 mm rail

MDD-256/T Control Unit User Manual Issue 1W21en ©gazex’2018 v1806 Page 4/ 22
3. DESCRIPTION AND ASSEMBLY
Digital communication port
Special functions control lamps
Keyboard
Terminal block of the power supply
Lights for output status
Terminal block of the relay outputs
Module or detector network status display Measurement units (for measuring detectors)
User’s description field
Pic.3.1 MDD-256/T front panel view (rail mounting position)
Pic. 3.1. View of terminal blocks - electrical connections
POWER 24VDC
01 02
OUT6 OUT5
24 23 22 21 20 19
com NO NC
OUT 1 OUT 2
MDD-256/T
%LE L
A+ B- GND
10 11 12
18 17 16
OUT 3
15 14 13
OUT 4
(PORT2)
com NO NC com NO NC com NO NC
+ M
CONTROL UNIT
ppm
%v/ v
OUT2
OUT3
OUT4
POWER
PORT1
DET.NET
OUT.NET
FAULT
OK
type
note
ACCUMULATORS 2x 7Ah or 2x 17Ah
PS-3/24
POWER SUPPLY
230V~
BACKUP POWER SUPPLY CONNECTION
+ -
N L
M
siren
light
SL
E
CONTROL RELAY OUTPUTS
ELECTRICAL SWITCHBOARD
optical-acoustic signalling device
35mm
RS-485
C3
FTP
PU/T
230V~
PORT2
OUT1
MENU
RESET
03 04 05 06
+ M + M
07 08 09
PORT1
A+ B- GND
+
or
RS-485
FTP (OUT.NET network)
DET.NET network
R
PE
OUT
F
R
ER3 E
24VDC
PE
+

MDD-256/T Control Unit User Manual Issue 1W21en ©gazex’2018 v1806 Page 5/ 22
Table 3.1. Functions realised at MDD outputs (standard - factory version):
MODULE
STATUS
RELAY OUTPUTS
12V ALARM
OUTPUTS (*)
[OUT4]
FAULT
[OUT1]
A1
[OUT2]
A2
[OUT3]
A3
[OUT5] [OUT6]
A1 A2
Pair
COM-NO
Pair
COM-NC
Pair
COM-NO
Pair
COM-NC
Pair
COM-NO
Pair
COM-NC
Pair
COM-NO
Pair
COM NC
NORMAL CLOSE
OPEN
OPEN
CLOSE
OPEN
CLOSE
OPEN
CLOSE
no voltage
no voltage
A1
CLOSE
OPEN
CLOSE
OPEN
OPEN
CLOSE
OPEN
CLOSE
12V=
no voltage
A2
CLOSE
OPEN
CLOSE
OPEN
CLOSE
OPEN
OPEN
CLOSE
12V=
12V=
A3
CLOSE
OPEN
CLOSE
OPEN
CLOSE
OPEN
CLOSE
OPEN
12V=
12V=
FAULT
OPEN
CLOSE
OPEN
CLOSE
OPEN
CLOSE
OPEN
CLOSE
no voltage
no voltage
FAULT
(E.NET) OPEN CLOSE xxxxxxxx
(*) The outputs of the MDD module can be configured in various ways - the table shows factory settings
of the functions in the standard version. The way of assigning a specific alarm to a specific output, and
the allocation of outputs to zones can be defined by the user (see p.5.5.3.3).
x – means the last correct state from before the fault;
NORMAL state -all DET.NET devices in normal state, no alarms or faults, only green lights are on;
A1 – (ALARM A1) at least one of the DET.NET bus devices indicates exceeded A1 concentration
threshold, but not A2; inner siren pulsating tone is on;
red lights of the assigned outputs [OUT ...] are on;
A2 – (ALARM A2) at least one of the DET.NET bus devices indicates exceeded A2
concentration threshold, but not A3; inner siren pulsating tone is on;
red lights of the assigned outputs [OUT ...] are on;
A3 – (ALARM A3) at least one of the DET.NET bus devices indicates exceeded A3 concentration
threshold – measurement range; inner siren pulsating tone is on;
red lights of the assigned outputs [OUT ...] are on;
FAULT – MDD not powered or MDD internal circuits defective, all lights are off;
– at least one of the DET.NET bus devices reports a fault [F.dEt.], yellow fault light is on
[FAULT], red lights of the assigned outputs [OUT ...] are on;
FAULT (E.NET) – no communication with at least one DET.NET bus device, yellow fault light is on
[FAULT], the last correct state of the outputs from before the fault is kept, red lights of the assigned
outputs [OUT ...] are on;
4. MDD INSTALLATION WITHIN THE
SYSTEM
The MDD installation can be begun after a period of time suitable for the temperature compensation of
the MDD and the surrounding air. Especially in winter, at negative temperatures during transport or
storage, wait approx. 20 minutes before removing the MDD from the foil packaging to prevent water
condensation on the unit’s inner circuits!
4.1 Mount the module in the switchboard box, on the TS35 rail, outside an explosion-endangered
area, in a place free from strong electromagnetic interference, vibrations, strokes.
Caution! The setup can be carried out only when the power supply is off!!!
4.2 Connect the MDD module and the detectors and/or submodules to the common [DET.NET] bus.
4.2.1 To the [DET.NET] bus terminals, PORT1 - terminals "A+". [07], „B-” [08], „GND” 09], connect
the bus cable - shielded "twisted pair" of the FTP or STP type 4x2x0,5 cat.5e (recommended cables).
4.2.2 Prepare the bus cable as described in item 4.2.2.A, then insert the isolated wire ends into the
appropriate PORT1 terminals.
Caution: incorrect polarity of the cables may result in the inability to start the entire detector network.
Caution: in order to remove the FTP and STP conductor insulation (the cables are actually very
thin!), use only dedicated tools that will not “hurt” the conductors. Using a knife or other sharp tool
for this purpose may result in a local reduction of the cable conductor cross-section, which when bent

MDD-256/T Control Unit User Manual Issue 1W21en ©gazex’2018 v1806 Page 6/ 22
or pressed in, breaks the conductor and causes communication fail of the entire detector bus (which
is also optically difficult to locate quickly)!
4.2.2.A. Inserting the wire into the removable terminal designed for connecting FTP single wire
cables (on RS-485 buses):
(1). remove the wire insulation at the height of exactly 6 to 7 mm;
(2). push (insert) the insulated conductor end into the round terminal
hole with pliers as far as it will go; the terminals are closed in pairs
vertically.
A properly inserted cable cannot be removed from the terminal. The
cable can be removed by gently pressing the orange button with a
flat screwdriver (according to arrow [3] and removed according to
arrow [4]).
The terminal blocks can be removed from the module's connecting
pins without disconnecting the bus cables.
4.2.3 Connect the other devices (detectors and/or submodules) to the [DET.NET] bus, following the
suggested colour scheme when connecting the cables to the respective terminals. Connect the units
successively by making any wiring connections in the doubled bus terminals of the individual units.
Use one terminal to connect the current device to the end of the existing detector network, and the
other one to connect the next device.
Star-shaped connections should be avoided. This type of connection is allowed conditionally, if the
lengths of individual bus branches do not exceed approx. 15 m, and on condition that connection
boxes type CB-4 are used to connect branches to the main bus. The CB-4 boxes have multiple bus
connectors and can connect up to 4 bus branches.
Caution: No other connection of multiple bus lines by twisting the lines is permitted, as it is very
likely that the lines will break off when twisted or loosened in the future.
TABLE 4.2.2. Suggested use of the FTP / STP cables
(colour scheme used on labels of all RS-485 ports made by GAZEX)
WIRE COLOUR
FUNCTION
Blue
Power supply weight (*)
brown
Power supply weight (*)
green
Power supply weight (*)
white and blue
+ power supply (*)
white and brown
+ power supply (*)
white and green
+ power supply (*)
FTP/STP cable shielding
(grey on labels)
RS-485 – signalling mass (GND)
orange
RS-485 - signal B-
white and orange
RS-485 - signal A+
(*) – applies only to devices whose power supply and communication are provided
via a single FTP/STP cable
4.2.4 PORT1 of the MDD module is equipped with J1 connector "TERMINATION", which enables
switching on the R=120Ω resistor terminating the [DET.NET] bus in order to eliminate reflections
resulting from mismatch of bus impedance. It is recommended that the MDD module is always
placed on one end of the bus (with terminating resistor switched on = jumper J1 in the ON position -
factory position in the standard version). At the other end of the [DET.NET] bus (in the most distant
device, i.e. connected with the wire of the highest total length), switch on the second terminating
resistor of the bus using the appropriate jumper for this device.
Caution: Activating more terminating resistors increases the bus load and might lead to
damage to the MDD’s internal circuits which are responsible for data transmission. If only one
terminating resistor is activated (or if none is activated), reflective impulses can be generated
and digital communication between devices can be interrupted.
In order to disconnect the terminating resistor, switch the J1 jumper to the OFF position.
4.2.5 If shielded FTP/STP cables are used in installations with increased exposure to interference, it
is essential to connect the signal masses of the [DET.NET] bus with the cable shield ("GND" terminal
- [09] in the MDD) in all devices, and then connect one end of the shield (preferably from the MDD
side) to the PE shield rail of the power supply.

MDD-256/T Control Unit User Manual Issue 1W21en ©gazex’2018 v1806 Page 7/ 22
Caution: Do not connect the signal masses of the bus only in some of the devices, as this
may cause data transmission errors or complete bus failure. Connect the bus signal masses
of all devices or do not connect the mass terminals anywhere.
4.2.6 If it is necessary to use additional devices inside the [DET.NET] bus, e.g. fiber
optic converters, the choice of the device should be consulted with the GAZEX Technical Support
Department.
Caution: The use of an unverified device may cause data transmission errors (due to
incorrect matching of receiver impedance, long response time) or eventually damage the
internal systems of other bus devices (due to lack of galvanic isolation of the port).
4.2.7 A maximum of 247 devices can be connected in one [DET.NET] bus loop (applies to
devices with an RS-485 port manufactured by GAZEX). The transmission port is
isolated (1kV) from the MDD internal circuits and is protected against over-voltages.
The longest wired connection between the most remote devices on the bus must not
exceed 1200 m.
4.3 The MDD module can be connected via PORT2 to the external bus [OUT.NET] - to work with
external monitoring modules or with "intelligent building" control systems (BMS).
4.3.1 As in section 4.2, connect PORT2 - terminals "A+". [10], „B-” [11], „GND” [12], connect the bus
cable - shielded "twisted pair" type FTP or STP 4x2x0,5 cat.5e (recommended cables).
4.3.2 The same rules apply for connecting devices to the [OUT.NET] bus as for the [DET.NET] bus
(see p.4.2.2, 4.2.3, 4.2.5, 4.2.7).
4.3.3 PORT2 of the MDD module is equipped with J2 connector "TERMINATION", which enables
switching on an R=120Ω resistor terminating the bus in order to eliminate reflections resulting from
the mismatch in the wavelength impedance of the bus. If the MDD is connected at the end of the bus
[OUT.NET], switch jumper J2 to ON. If the MDD is placed in the middle of the bus, switch the
jumper to OFF.
Caution: Leaving more terminating resistors increases the bus load and might lead to
damage to the MDD’s internal circuits which are responsible for data transmission.
4.3.4 The length of the [OUT.NET] bus must not exceed 1200m at a speed of 9600bps or 200m at a
speed of 57600bps. The transmission port is isolated (1kV) from other MDD systems and is
protected against over-voltages.
Specification of the MDD communication protocol is in a separate document.
4.4 Connect to the 12V alarm outputs ([OUT5] and [OUT6] ) external cooperating devices, e.g.
automation controllers, signalling devices, etc. In case of placing the optical and acoustic signalling
devices in the same place, it is recommended to use an integrated acoustic-optical signalling device of
SL-32 or SL-21 type, which can be connected to the MDD using a three-wire cable (2x2x0,5 is
recommended).
4.4.1 Different phase voltage circuits or low voltage circuits can be connected to the contact outputs
[OUT1], [OUT2], [OUT3], [OUT4].
4.4.2 Inserting conductors into the removable terminal designed to connect solid and fine-stranded
conductors (connectors for contact, 12V alarm
and 24V power supply outputs):
(1). remove the wire insulation at the height of 8 mm;
[solid conductors]: (2) push (insert) the isolated
conductor end into the round terminal opening with
pliers as far as it will go;
[fine-stranded conductors]: (3) press the orange button
as depicted with the arrow, (2) push the isolated
conductor end into the round terminal opening as far as
it will go, then release the orange button.
A properly inserted cable cannot be removed from the
terminal. The cable can be removed by gently pressing
the orange button with a flat screwdriver (according to
arrow [3] and removed according to arrow [4]).

MDD-256/T Control Unit User Manual Issue 1W21en ©gazex’2018 v1806 Page 8/ 22
The terminal blocks can be removed from the module's connecting pins without disconnecting
the connected cables.
CAUTION: Removal may only be carried out with the power SWITCHED OFF - and in particular
when the voltage in the disconnected circuits may exceed the safe voltage!!!
Cable ends must be prepared in a way which prevents the connectors from having to be
wrapped round the module inside the box after they have been placed in the terminals. Solid
or fine-stranded conductors (with or without ferrulas) may be used.
The cables must be laid in such a way that they do not transmit mechanical forces to the
connection terminals.
4.5 Connect the 24V supply "E" lead from the PU.../T or the PS... power supply (with battery
connected); maintain proper polarity (the module is protected against reverse polarity).
The conductor cross-section of a cable depends directly on its total length and the number of MDD
modules and detectors powered from one PU/T or PS power supply. Choose the cross-section of wires
in such a way that the supply voltage on the last in a row connected to the detector is higher than the
minimum acceptable voltage level by at least 2V (in the conditions of maximum load, with the control
outputs switched on).
5. MDD CONFIGURATION
BEFORE SWITCHING ON the bus and MDD power supply, make sure that all connections
on the bus are made firmly and correctly in the correct sequence (any faulty connections will
prevent correct digital communication!!!!).
Confirm that there are no short circuits in the power supply cables (when using FTP/STP
cables with very thin conductors - possible short circuits in cables of long length do not
have to automatically switch off the overload protection of the power supplies!!!!) This can lead to
overheating and permanent damage to the cables!
It is also necessary to make sure that all wires of the single wire bus are connected - each unused wire
increases voltage drops on the cable - which significantly limits the length of the bus (system size).
CAUTION: all described procedures and LED display messages refer to the standard version of the module.
Custom version descriptions, changes and corrections can be found in any appended annexes to the user
manual.
5.1 Pre-configuration of the module according to individual customer needs can be done by means of a keypad
located on the front panel of the MDD.
CAUTION: press the keys gently in order not to damage the MDD internal circuits.
5.2 Turn on the MDD power supply (the module does not have a built-in power switch). After the power supply
is turned on, an acoustic test of the internal siren is performed as well as an optical test of all display
segments and signal lights. The following text appears on the segment display [ tESt ], and then information
about the module version (e.g. "W21") and the date of compilation of the installed software (in the format [
L.rmm], where "r" is the last digit of the year; "mm" - a month) - this information may be required when
contacting the GAZEX Technical Support Department. The individual lamps light up and go out one after
the other. During this time, the module settings are initialised.
5.3 After the testing phase, the module enters the normal operation mode - based on the configuration settings
in the internal data memory (the letter "n" appears in the middle of the display). The user can change the
configuration settings at any time, using the keyboard located on the front panel of the module. The special
functions that can be activated using the keyboard keys are described in section 6.5.
5.4 In order to make changes, press and hold [ ▲ ] key for 3 seconds]. Correct pressing of the key will be
confirmed by an intermittent acoustic signal, interruption of the warm-up mode and displaying on the LED
screen a request to enter the user password: [ P.000 ] (the factory password is: "P.001"). The password is
entered by means of the keys [ ▲ ] and [ ▼ ], and confirmed by means of the key [ OK ]. Incorrect
password causes exiting the menu and returning to the warm-up mode. In order to retry making changes to
the controller repeat the above mentioned operations.
Caution!!! The above password is the default one assigned to each MDD copy. In order to prevent
unauthorised access of outside persons to the controller settings, the password must be changed
individually (see section 5.4.5). The new password should be remembered and stored in a safe place.
Losing the password makes it impossible to make MDP configuration changes. Unlocking the
password is possible only by the manufacturer (paid service).

MDD-256/T Control Unit User Manual Issue 1W21en ©gazex’2018 v1806 Page 9/ 22
5.5 Entering the correct password will be confirmed by an intermittent acoustic signal. The controller enters the
setting mode. At this stage, all control and measurement procedures are suspended until the configuration
of the device is completed. The first item from the user menu is displayed on the LED screen. The below list
shows all available functions:
- [ d.nEt ]– DET.NET bus – configuration of the network of devices connected to the detector bus;
- [ d.dEt. ]– manual configuration of parameters of individual devices, i.e. DD, MDP-1.A/T, … ;
- [ d.out. ]– turning executive devices on/off, i.e. MDD-L32,… ;
- [ d.Scn. ]– automatic scanning, refreshing of device addresses in the existing network;
- [ d.Add. ]– adding new devices to the existing device network;
- [ d.dEL. ]– deleting the DET.NET network device parameters stored in the MDD memory, together
with zeroing out the addresses for all devices connected to the bus;
- [ o.nEt ] – OUT.NET bus - configuration of transmission parameters for an external bus;
- [ out. ] – module outputs – parameter settings;
- [ o._|-|_. ] – defining the on/off delay of the outputs;
- [ o.Fun. ] – defining the operating modes of the outputs;
- [ o.Zon. ] – assigning outputs to zones;
- [ SErv. ] – service functions;
- [ PASS. ]– password change;
- [ tESt ]– testing the module outputs;
- [ d.rSt. ]– setting the MDD zero mode, triggering detector bus zeroing;
- [ FAcT. ] – restoring factory settings;
- [ dISP. ] – special functions of the LED display;
- [ vAL. ] – defining the mode of displaying device parameters;
- [ LooP ] – switching the cyclic mode on/off;
- [ .... ]– automatic exit from the menu;
The LED screen displays only one function that is active at a time. In order to change the function to
another one, use the keys [ ▲ ] or [ ▼ ]. Confirm the selection of the function with the [ OK ] key.
To exit the menu, scroll through all available menu functions with [ ▼ ].
Pressing the [ OK ] key next to a specific function will enter the sub-menu. Moving in the sub-menu of the
respective function is similar to moving in the main menu - selection of the parameter by means of the [ ▲ ]
and [ ▼ ] keys, confirmation by means of the [ OK ] key.
The following sections provide a detailed description of the parameters of the individual MDD functions.
5.5.1 [ d.nEt. ] – Configuration of the DET.NET bus.
The first menu item groups all the functions required to configure the DET.NET bus, i.e. the detector
(module) network, correctly. From this level, the user defines the parameters of the devices, assigns network
addresses to the devices, refreshes the network content after changes, etc. The available functions are
described below.
5.5.1.1 [ d.dEt. ] - Detector parameters – parameter list:
This function is recommended when the DET.NET bus has already been configured, the devices are working
properly, and the parameters of the individual devices need only be manually changed. In this case, the user
knowing the addresses of the detectors to be reconfigured, selects specific slaves from the range [ d.001 ] ÷ [
d.224 ], and then changes the settings of the specific detector. It should be remembered that after choosing
the slave address, the MDD forces the user to correctly configure all parameters of a given detector (it is
necessary to go through the full configuration path and reconfirm all parameters of the detector).
Changes in the detector settings are made in real time, i.e. correct communication between the MDD and the
selected detector is required during parameter configuration.
If the MDD does not communicate with the detector, it signals this with a continuous acoustic signal and
blocks the possibility of changing the detector's parameters. In this case, the detector can only be switched
on/off and assigned to a specific zone.
If the MDD communicates correctly with the detector, this is indicated by an intermittent acoustic signal and
enables full configuration of the parameters of the selected detector. The new parameters are stored in the
MDD memory and in the detector memory.
The following are the configuration steps for a single detector. Always make changes by pressing the [ ▲ ]
and [ ▼ ] keys, confirm the settings by pressing the [ OK ] key. When confirming the selection of a given
option or group of options, the MDD sends a command to the detector. A correct change is indicated by an
intermittent acoustic signal (new settings are stored in the MDD memory and in the detector memory). Lack
of communication or failure to execute the command is signalled by a continuous signal (changes are not
made). Once all required settings have been confirmed, the detector automatically returns to the detector list.
a) Selecting the detector number from [ d.001 ] ÷ [ d.224 ].
Select a number that matches the slave address of the detector. Any changes will only apply to the
selected detector.

MDD-256/T Control Unit User Manual Issue 1W21en ©gazex’2018 v1806 Page 10 / 22
b) Switching detector operation on/off:
- [ d.YES ] – operation of the detector is on - in normal mode the module cyclically checks the status of
the detector with the previously specified address;
- [ d.no ] – operation of the detector off (default setting) - the module bypasses the detector in normal
operation mode, communication with the detector is off.
c) Assigning detector to zones:
- [ d.Zo.A ] – detector assigned to both ZONE1 and ZONE2 (default setting),
- [ d.Zo.1 ] – detector assigned only to ZONE1,
- [ d.Zo.2 ] – detector assigned only to ZONE2.
Assigning the detector to a selected zone determines the activation of selected MDD outputs in the event
of an alarm or fault condition in the detector.
If there is no correct communication with the detector, return to point a).
d) Detector type and measurement unit:
- [ d.-P ] – measuring detector,
- [d.-F ]– threshold detector.
The type of measurement unit is indicated by a horizontal line on the MDD screen. The information about
the type of detector and measurement unit is read out automatically, it is not possible to change it.
e) Switch the detector on/off:
- [ d.On ] – sensor power supply in the detector switched on,
- [ d.OFF ] – (default setting) sensor power supply in the detector switched off.
When the sensor is switched off, the measuring functions of the sensor are blocked in the detector until
the sensor is switched on again. The detector then reports no alarm or fault conditions. Switching off the
sensor is justified in case of servicing, i.e. in case of replacement of the sensor in the detector, or in case
of sensor damage.
f)A3 measuring range (for the measuring detector only):
The value is non-editable and reads automatically from the detector.
g) Alarm type (for measuring detector only):
- [ d.A12 ] – momentary value alarms,
- [ d.t.Av. ] – alarms averaged over time;
Non-editable values read automatically from the detector.
The [ d.A12 ] option means the activation of alarms if the momentary value of the detector signal exceeds the set
thresholds A1 and A2. The [ d.t.Av ] option assigns a time average to the alert thresholds. The A1
threshold corresponds to the TWA - Time Weighted Average of harmful substances in the work
environment (in Poland - in accordance with Regulation of the Minister of Family, Labour and Social Policy
dated June 7th 2017, Journal of Law of 2017 pos. 1348 + changes), the A2 threshold corresponds to the
STEL- Short-Term Exposure Limit to harmful substances in the work environment (in accordance with
Regulation as above).The A3 threshold corresponding to the measuring range is always activated if the
instantaneous value of the detector signal exceeds the A3 value (time averaging is deactivated).
h) Direction of alarms (for the measuring detector only):
- [ d._|‾‾ ] – excess (default setting),
- [ d.‾‾|_ ]– shortage.
Non-editable values read automatically from the detector.
Excess option [ d._|‾‾ ] means activation of the alarm thresholds if the detector signal exceeds the value
of the set alarm concentration thresholds A1 and A2, where A1 <= A2.
Defect option [ d.‾‾|_ ] means activation of the thresholds after the detector signal drops below the set
alarm thresholds A1 and A2, where A1 >= A2.
i) Determination of the A2 threshold value ( for measuring detector only).
Adjustable value in the range from 5 ÷ 100% of the A3 measuring range ( default setting is A2 = 30%).
j) Determination of the A1 threshold value (measuring detector only).
Adjustable value in the range from 5 ÷ 100% of the A3 measuring range (default setting is A1 = 10%).
5.5.1.2 [ d.out. ] - Settings of the executive devices:
Here, the user can configure the parameters of the executive devices, e.g. MDD-L32/T or MDD-R4/T
modules, on a common DET.NET bus. These modules are controlled by the MDD-256/T (reserved network
addresses above [A.224]). The MDD refreshes the register of executive devices each time it queries the
entire detector network.
Each executive module can only be linked to a selected group of 32 detectors (see Table 5.5.1.2).
This way the user can divide the detector network into up to 7 groups of up to 32 detectors and control the
facility automation locally using the contact and voltage alarm outputs of the executive modules.

MDD-256/T Control Unit User Manual Issue 1W21en ©gazex’2018 v1806 Page 11 / 22
TABLE 5.5.1.2
Identity number
of the executive device
in the MDD menu
Detector address
range [A. …]
(groups)
[d.o.0.1]
[d.o.1.1]
[d.o.2.1]
1 – 32
[d.o.0.2]
[d.o.1.2]
[d.o.2.2]
33 – 64
[d.o.0.3]
[d.o.1.3]
[d.o.2.3]
65 – 96
[d.o.0.4]
[d.o.1.4]
[d.o.2.4]
97 – 128
[d.o.0.5]
[d.o.1.5]
[d.o.2.5]
129 – 160
[d.o.0.6]
[d.o.1.6]
[d.o.2.6]
161 –192
[d.o.0.7]
[d.o.1.7]
[d.o.2.7]
193 – 224
The configuration of the executive modules is two-stage and does not require proper communication with the
selected module.
The first step is to choose from the list of [ d.o.0.1] ÷ [ d.o.2.7 ] the correct device number. Then activate or
deactivate the device by choosing:
-[ d.YES ] – device activated;
-[ d.no ] – device deactivated (default setting);
The next step is to define the operation mode of the executive device outputs (similar to the MDD) by
choosing one of the following:
- [ Zo.31 ]– three alarm levels A1, A2, A3 and FAULT – no division into zones (default),
- [ Zo.22 ]– two alarm levels A1 and A2, no FAULT – in two zones: ZONE1 and ZONE2,
- [ Zo.12 ]– one alarm level A1 and FAULT – in two zones: ZONE1 and ZONE2,
- [ Zo.11 ]– one alarm level A1 and FAULT – no division into zones;
Detailed description of the zones is in section 5.5.3.3.
5.5.1.3 [ d.Scn. ] – Scanning, refreshing the existing detector network.
This function enables a simple and quick scanning of all slave addresses of the detector network within the
range of [ A.001 ] ÷[ A.224 ] and on this basis the recreation of the detector network. This procedure is
particularly recommended when installing a new MDD module in an existing, operational detector network.
The prerequisite for scanning is correct connection of all sensors with unique slave addresses to the
DET.NET bus and correct communication.
The scanning of the detector networks that have set addresses goes as follows:
1) The MDD sends a query to the [ A.001 ] slave and awaits a response.
2) If there is a detector with address [ A.001 ], it can answer your query. The MDD receives a response from
slave A.001, stores the slave settings and registers them in the detector network.
3) If there is no detector with an address [ A.001 ], the MDD will skip it in the DET.NET detector network
after the required response time.
4) The steps listed in points 1÷3 are repeated until all available detector network addresses have been
scanned.
5.5.1.4 [ d.Add. ] - Addressing detectors on the bus - allows you to create a new detector network and add
detectors to an existing network.
This feature allows you to quickly and easily set up a detector network and assign the required slave
addresses to each detector. The prerequisite for the addressing procedure is that all detectors are correctly
connected to the DET.NET bus.
When this option is selected, the module starts the addressing procedure for the detectors by sending a
command to start addressing all detectors connected to the bus. The detectors go into the "addressing
mode". The MDD displays the initial slave address [ A.001 ] from which addressing will start. The initial
address can be changed by the user using the keys [ ▲ ] and [ ▼ ], the selection can be confirmed by
pressing the [ OK ] key.
The addressing procedure for the detectors that don’t have set addresses goes as follows:
5) The MDD gives temporary slave address, e.g. A.001 to all detectors.
6) The MDD sends a query to the A.001 detector and awaits a response.
7) The user confirms that the A.001 address is assigned to a chosen detector by pressing the correct key
(depending on the device type). After confirmation, the chosen detector assigns the A.001 address to
itself permanently, it sends a response to the MDD and exits the registration procedure.
8) The MDD receives a response from the A.001 slave, saves the slave settings and registers it in the
detector network.
9) The MDD confirms registering the detector by polling the detector.
10) The MDD automatically changes the slave address to the next one (A.002) and temporarily assigns it to
the remaining detectors.
11) The steps listed in points 2÷6 are repeated.

MDD-256/T Control Unit User Manual Issue 1W21en ©gazex’2018 v1806 Page 12 / 22
If the user assigns addresses to all detectors connected to the DET.NET network, they confirm the end of
the addressing process by pressing the [ OK ] key. The module completes the addressing procedure, saves
the settings of the new detector network in a non-volatile memory and displays the number of stored
detectors on the screen. The new settings remain active until you make new changes.
The addressing procedure for detectors with set addresses (adding a new, additional device or
replacing a faulty device with a new one) is as follows:
1) The MDD polls further detectors from the existing network (the detectors exit the registration procedure
after a response has been sent);
2) After polling the existing network, the MDD stops at the first available address, sends a query to the
detector and awaits a response.
3) The user confirms assigning the displayed address to the added detector by pressing the correct key
(depending on the device/detector type). After confirmation the chosen detector assigns the given
address to itself permanently, it sends a response to the MDD and exits the registration procedure.
4) The MDD receives a response from the new detector and saves it by registering it in the DET.NET
Network.
5) The steps in points 2 ÷ 4 are repeated for the rest of the new devices.
If the user assigns addresses to all detectors connected to the DET.NET network, they confirm the end of
the addressing process by pressing the [ OK ] key. The module completes the addressing procedure, saves
the settings of the new detector network in a non-volatile memory and displays the number of stored
detectors on the screen. The new settings remain active until you make new changes.
CAUTION: If the user of an extensive Digital Gas Detection System envisages the use of multiple
devices/controllers/executive devices - i.e. envisages more than two zones (subsystems) requiring
independent control (max. 7 groups of up to 32 detectors, each group divided into 1 or 2 zones) -
they should consider such a division into address groups when assigning addresses to
individual detectors as per Table 5.5.1.2.
5.5.1.5 [ d.dEL. ] - Deleting the slave addresses of the detectors connected to the DET.NET bus.
This function allows you to delete all slave addresses assigned to the detectors. It is especially
recommended before addressing an unknown detector network, or when some detectors may have the
same slave addresses. In order to confirm deleting, select option [ d.YES ] with the [ ▲ ] key and confirm
with the [ OK. ] key.
CAUTION!!! Deleting will reset the addresses of all devices connected to the DET.NET bus. After deletion,
all detectors remain inactive and require the re-addressing procedure described in section 5.5.1.4 to be
carried out correctly. In addition, the MDD will reset the stored detector network configuration, excluding the
DET.NET bus operation.
5.5.2 [ o.nEt. ] – OUT.NET bus parameter settings.
The parameters of the external bus communication designed for the MDD communication with higher-level
external devices or visualisation systems must be configured here.
Settings include parameters listed below:
- slave address assigned to the MDD: [A.001 ] (default setting) ÷ [ A.247 ];
- data transmission speed: 9600bps, 19200bps, 38400bps or 57600bps (default setting);
- parity check: even (default setting) or none;
5.5.3 [ out. ] - Output settings.
This item groups a set of functions used to configure the required functionality of the outputs. The properties
of the individual functions are described in detail below.
The MDD has four relay outputs marked OUT1, OUT2, OUT3, OUT4 and two voltage outputs marked OUT5,
OUT6.
5.5.3.1 [ o._|¯|_ ] – Defining the on/off delay of the outputs.
In order to set time parameters:
a) choose the correct output number from the range [ out.1 ] ÷ [out.6 ],
b) specify the on delay of the outputs, i.e. the time (default = 10 sec.) from the moment the MDD registers a
given alarm state coming from at least one of the detectors connected to the bus, to the time the MDD
activates the relevant output;
the delay can be set within the range: [ ┌┘003 ] ÷ [ ┌┘300 ] seconds.
c) specify the off delay of the outputs, i.e. the time (default = 10 sec.) from the moment the given alarm
state coming from at least one of the detectors connected to the bus disappears, to the time the relevant
output is activated;
the delay can be set within the range: [└┐003 ] ÷ [└┐900 ] seconds.

MDD-256/T Control Unit User Manual Issue 1W21en ©gazex’2018 v1806 Page 13 / 22
5.5.3.2 [ o.Fun. ] – Defining the operating modes of the outputs.
From the menu level the following operating modes of the module are available:
- [ F.h12 ] – normal mode with ALARM MEMORY (default setting),
- [ F.A12 ] – ALARM MAINTAINING mode,
- [ F. n ] – auto-zeroing mode, NO ALARM MEMORY,
- [ F.Ser ] – SERVICE mode with timed, 1-hour blockade of the module outputs.
The operating mode determines the specific control functionality of the MDD outputs. Depending
on the set mode, the MDD leaves information on the front panel about alarm conditions that have
ended (alarm memory), or clears messages (no alarm memory). Additionally, MDD outputs can be
activated for the duration of the alarm or until the user manually deletes them (alarm maintaining
mode). Details are provided in the table below.
Operation
mode
Active alarm Finished alarm
Optical
visualisation
of the output
status
Inner acoustic
signal
Alarm
output
status
Optical
visualisation of
the output
status
Inner
acoustic
signal
Alarm output
status
[ F.h12 ] Continuous
Pulsating
cycle depends on
alarm level
Active Pulsating Pulsating
1s/4s Inactive
[ F.A12 ] Continuous
Pulsating
cycle depends on
alarm level
Active Continuous
Pulsating
cycle depends
on alarm level
Active
[ F. n ] Continuous
Pulsating
cycle depends on
alarm level
Active None None Inactive
[ F.Ser ] Continuous
Pulsating
cycle depends on
alarm level
Inactive Pulsating Pulsating
1s/4s Inactive
Normal mode with ALARM MEMORY – activates alarm and fault signalling both during the event and after it
has ceased. The pulsating signalling after an alarm has disappeared is maintained until the user consciously
resets the MDD to zero. Alarm outputs are activated only for the duration of the alarm, while maintaining the
delays of switching on and off the outputs. This mode can be activated indefinitely.
ALARM MAINTAINING mode – causes the alarm outputs to be activated both for the duration of the alarm
and for this state to be maintained after the end of the event which caused the alarm. The output will be
disabled ONLY after external user intervention (MDD zeroing with "OK" button). This mode can be activated
indefinitely.
NO MEMORY mode – automatically resets the MDD after an alarm has been triggered, no user intervention
is required. There is no message on the front panel about an alarm that has ended. The acoustic signals are
also switched off. This mode can be activated indefinitely. Recommended especially for mechanical
ventilation control systems.
SERVICE mode – enables the MDD outputs to be disabled for 60 minutes. Recommended for maintenance
of gas detection system. In this mode, the MDD measurement activities are retained, i.e. the MDD controls
the status of the connected detectors, displays alarm and fault information on the front panel, but does not
activate the outputs. The mode can be switched off at any time before the end of the full time period from the
user menu or by temporarily turning off the power supply to the module. When the service mode is activated,
the POWER light flashes.
5.5.3.3 [ o.Fun. ] – Assigning the MDD outputs to zones.
From the menu level the following options are available on the MDD outputs (see Table 5.5.3.3):
- [ Zo.31 ] – three alarm levels A1, A2, A3 and FAULT – no division into zones (default),
- [ Zo.22 ] – two alarm levels A1 i A2, no FAULT – in two zones,
- [ Zo.12 ] – one alarm level A1 and FAULT – in two zones,
-[ Zo.11 ]– one alarm level A1 and FAULT – no division into zones;
Mode [ Zo.31 ] is recommended when the MDD operates a network made up of MDP-1.A/T or MDD-1
measuring modules, in which every detector has three alarm thresholds assigned to it. It should also be used
for a two-way detector network when using the Fault output is required.
Mode [ Zo.22 ] is recommended for two-way detector networks if it’s necessary to divide the detectors to two
zones, but a fault relay output is not required (Fault status is available via PORT2 after polling by the control
module).
Modes [ Zo.12 ]and [ Zo.11 ] are recommended in one-way detector networks, e.g. the DD detector type.

MDD-256/T Control Unit User Manual Issue 1W21en ©gazex’2018 v1806 Page 14 / 22
TABLE 5.5.3.3 – assigning zones and alarms to the MDD outputs.
Zone
mode
Relay output
OUT 1
Relay output
OUT 2
Relay output
OUT3
Relay output
OUT4
Voltage output
OUT5
Voltage output
OUT6
[Zo.31] ALARM A1 ALARM A2 ALARM A3 FAULT ALARM A1 ALARM A2
[Zo.22]
ALARM A1
Zone 1
ALARM A2
Zone 1
ALARM A1
Zone 2
ALARM A2
Zone 2
ALARM A1
Zone 1+2
ALARM A2 Zone
1+2
[Zo.12]
ALARM A1
Zone 1
FAULT
Zone 1
ALARM A1
Zone 2
FAULT
Zone 2
ALARM A1
Zone 1
ALARM A1
Zone 2
[Zo.11] ALARM A1 ALARM A1 ALARM A1 FAULT ALARM A1 ALARM A1
5.5.4 [ SErv. ] – Service functions, special functions.
This item groups a set of service and special functions used when servicing the MDD. The available options
are described below.
5.5.4.1 [ PASS. ] – Password change.
-[ P.001 ] – default user password (default setting);
-[ P.000 ] ÷ [ P.999 ]– password regulation range.
Caution!!! In order to prevent unauthorised access of outside persons to the controller settings, the
password must be changed individually. The new password should be remembered and stored in a
safe place. Losing the password makes it impossible to make MDP configuration changes.
Unlocking the password is possible only by the manufacturer (paid service).
5.5.4.2 [ test ] – MDD output test.
Module output test - allows all outputs to be checked for correct activation without the need for detectors
connected to the bus to generate alarms.
Outputs are switched on sequentially for duration = 10 sec. The currently enabled outputs are signaled on
the front panel by an appropriate LED light. After testing all outputs, the MDD automatically returns to the
user menu. The outputs are switched on in the following order ("+" indicates the active output):
Duration
[s]
Relay
output
OUT 1
Relay
output
OUT 2
Relay
output
OUT3
Relay
output
OUT4
Voltage
output
OUT5
Voltage
output
OUT6
0 – 10
+
10 – 20
+
20 – 30
+
30 – 40
+
40 – 50
+
50 – 60
+
5.5.4.3 [ d.rSt. ] – Setting the zeroing of the device network connected to the DET.NET bus.
From the zeroing settings two options are available:
[ r.SEt. ] – determines how to reset the MDD and the detector network when the user presses the [ OK ] key
on the MDD front panel. With the [ r.On ] setting selected - each time the MDD is reset with the
button, all devices in the detector network are automatically reset to zero. When [ r.OFF ] is
selected, only the MDD is reset, while the status of the devices in the detector network remains
unchanged.
[ r.run ] – enables the reset command to be triggered from the menu for the entire detector network
(independent of the "RESET" button on the front panel).
5.5.4.4 [ FACt. ] – Restoring MDD default settings.
This option restores the standard MDD configuration settings (specified in sections 5.5.1 to 5.5.5.) by
cleaning the previously made changes. This option is particularly recommended in situations where not
knowing the previous settings may unexpectedly trigger MDD control procedures unsuitable for the desired
configuration.
5.5.5 [ diSP. ] – Switching special LED display functions on/off.
From the display settings level two options are available:
[ vAL. ] – setting it to [ v.YES ] additionally causes displaying the current detector status while browsing
slave addresses is triggered (see section 6.3). Setting it to [v.no ] disables displaying detector
status.
[ LooP ] – setting it to [ L.YES ] loops the slave address browsing procedure. When the entire detector
network is displayed, the MDD automatically restarts the display from the beginning. The
display can be interrupted by pressing the [▼] key for approx. 2 seconds.

MDD-256/T Control Unit User Manual Issue 1W21en ©gazex’2018 v1806 Page 15 / 22
6. DIGITAL GAS DETECTION SYSTEM LAUNCH
All devices for the Digital Gas Detection System equipped with RS-485 communication ports are supplied by
GAZEX with communication switched off as a default setting (set to "zero" address). In this state, the devices will
not respond to the control module's queries until the control module has assigned an individual address to them.
This is a safe setting because it ensures that there are no two (or more) devices with the same address in the
same network, which would result in communication errors.
If a new device network is being created and it is not certain that all devices have a "zero" address, the device
addresses must be reset before addressing can begin. This can be done manually on each device (according to
the operating instructions of the respective device) or automatically from the MDD menu, option [d.dEL.], section
5.5.1.5.
Caution! Please note that starting the address zeroing procedure in the existing network will erase
all addresses of the devices and you will need to repeat the addressing procedure for the entire
network.
If access to detectors or modules connected to the digital bus is difficult at the installation site, it is
recommended to address these devices before installing them on site. This can be done by connecting the devices
individually to the MDD and assigning consecutive addresses to them. Remember to label your device with an
address label and a description of the physical location of the installation. In the network of devices installed in this
way, it is enough to run the option of scanning the network from the MDD menu, option [d.Scn.], section 5.5.1.3.
and check whether the number of found devices and their addresses are consistent with the actual state.
Caution! Please note that starting the network scan procedure will remove from the list of devices
supported by the MDD those that will not respond to the query. Therefore, before starting the [
d.Scn ] function scan, make sure that all devices in the network are powered on and connected
to the bus. Scanning only changes the MDD settings and does not erase, does not set slave
addresses in devices connected to the bus.
The addressing procedure, option [ d.Add. ], section 5.5.1.4, can be started when you are sure that the devices
you configure have zeroed addresses, or to add new devices to an existing, properly functioning network. The
required startup steps are described below.
6.1 Switch on the MDD power supply and the power supply for all devices connected to the DET.NET bus. Wait
until the MDD module completes the initialisation procedure for the startup parameters (last settings loaded,
display and light test) and displays the "n.OFF" symbol on the LED screen, which means that the DET.NET bus
communication is disabled (no MDD-configured detector network).
6.2 Configure the new detector and/or sub-module network connected to the DET.NET bus as follows:
a) Ensure that the electrical connections of the detector network and the MDD module are correct.
b) Ensure that all components of the detection system are properly powered.
c) Enter the MDD menu (see sections 5.4 and 5.5).
d) From the main menu choose the option [ d.nEt ] (see section 5.5.1), confirm with the [OK] key.
e) Activate addressing of the detector network, option [ d.Add. ] (see section 5.5.1.4), confirm with [OK].
All devices connected to the DET.NET bus should signal entering the addressing mode. If this is not the
case, finish the addressing procedure by pressing the [OK] key twice, locating and repairing the fault
(description of typical digital bus faults and methods of solving them are described in section 6.9). After the
repair, restart the addressing procedure by repeating steps from e).
If there is an existing detector network, the MDD will automatically skip all busy addresses in the network
(the devices of the existing network will exit the registration procedure) and stop at the first, smallest free
address.
f) Specify the starting address for addressing the devices (default: [ A.001 ]) and confirm by pressing [OK].
From the moment of confirmation, the MDD waits for a response from the device with the indicated
address, signalling this status with the "rotating" symbol "c" on the segment display.
g) Go to the first device and confirm the new address by following the instructions in the manual for the
selected device. The addressed device signals that the new address is stored and exits the reporting
procedure starting with normal operation. (The exact algorithm of the addressing procedure implemented in
the MDD is described in section 5.5.1.4).
h) Wait a few seconds for the MDD to signal with an intermittent beep that the address is being confirmed and
to display the next address value on the LED screen.
Caution! If addressing is confirmed simultaneously on the next device before the MDD changes address to
the next, the same address is assigned on the two devices, resulting in communication errors!!!
i) If the user does not want to keep the addressing order, they can change the address to any value before
confirming the next device with the use of [ ▲ ] and [ ▼ ] keys. Confirm your selection with [OK]. If the
selected address is already occupied, the MDD will automatically increment it to the next free address.
j) After confirming the addresses of all devices, complete the reporting procedure by pressing [OK]. The
MDD indicates the end of the procedure by displaying the number of addressed devices. If this number is
not consistent with the actual number of devices on your network, you may have omitted some devices
when confirming addresses. In this case, you must redial the addressing procedure. Wait until the MDD
scrolls through the stored addresses and then the DET.NET bus configuration. The detailed description of
the procedure is described in section 6.7.

MDD-256/T Control Unit User Manual Issue 1W21en ©gazex’2018 v1806 Page 16 / 22
6.3 Configure the other MDD parameters as required (see section 5 for details). Exit the menu.
6.4 After exiting the configuration settings (or omitting the configuration stage by the user), the MDD switches to
the normal operation mode, where it cyclically polls the configured network of detectors connected to PORT 1.
Correct communication is signalled by the flashing green PORT1 light marked [DET.NET]. On the front panel
are signaled in real time: collective status of detector network, states of outputs, correctness of power supply
and RS-485 communication as well as possible activation of special MDD functions. The signalling method is
described below.
a) The LED segment display is assigned to indicate the current status of the detector network connected to the
MDD. The alarm or fault states displayed are collective states of the entire detector network that are triggered
by one or more detectors. The symbols are explained below:
-alarm states:
[ n.OFF ]– communication is off (no active detectors);
[ n ] – normal state of the detector network;
[A1 ] – active alarm of level 1 being exceeded;
[ A2 ] – active alarm of level 2 being exceeded;
[A3 ] – active alarm of level 3 being exceeded;
[ h1 ] – there was (historical) an alarm of level 1 being exceeded;
[ h2 ] – there was an alarm of level 2 being exceeded;
[ Er.03 ] – short-circuit or overload of the MDD voltage outputs;
[ Er.04 ] – external power supply fault;
-fault states or special information of devices in the DET.NET detector network:
[E.nEt ]– no communication with a device in the DET.NET network,
[ F.dEt ] – fault reported by a device in the DET.NET network;
[ d.OFF ] – inactive device (with its sensor off);
[ d.SEt ] – device in setting mode;
[ hEAt. ] – device in warm-up mode;
b) Red lights [ OUT1 ] ÷ [ OUT4 ] indicate the status of the alarm outputs:
-continuous light - alarm output active;
-pulsating light – in the cycle (0,5s/0,5s) – SERVICE mode on (all outputs temporarily locked);
-pulsating light – in the cycle (1sec. on / 3sec. off) – inactive alarm output (historical memory of the active
output);
-off – inactive alarm output;
b) Green [ DET.NET ] light indicates detector bus communication status:
-pulsating light in time intervals according to the polling frequency (ca.3÷30 sec.; depends on the number
of detectors in the network) – correct communication;
-off – MDD communication off, no active detectors/devices in the DET.NET network;
-continuous light – the module sends queries to the bus but receives no response; this state may mean
no power supply to the detectors, a faulty detector bus, no terminating resistors or a high level of
interference in the bus;
c) Green [ POWER ] light indicates MDD power supply status:
-continuous light – power supply parameters normal;
-pulsating fades – for 1 sec. in a 4 sec. cycle – correct power supply, SILENT MODE on (no inner siren);
-pulsating light – in the cycle (0,5s/0,5s) – correct power supply, SERVICE mode on (all outputs
temporarily locked);
-pulsatingly faded light (3 fades, 0,5s each, within 4 sec) – correct power supply, A2 LOCK MODE on
(temporary blockade of the A2 voltage output);
-off – no power supply to the module;
f) Yellow light [ FAULT ] – fault present in the system:
-continuous light – active fault state (including lack of power supply) coming from a detector/device
connected to the bus, damaged digital bus, or MDD module fault;
-off – no fault;
g) Inner acoustic siren signals alarm and fault states in the MDD:
-continuous sound – any fault;
-sound pulsating in the cycle (0,1s on / 0,1s off) – active alarm A3;
-sound pulsating in the cycle (0,2s/0,2s) – active alarm A2;
-sound pulsating in the cycle (0,5s/0,5s) – active alarm A1;
-sound pulsating in the cycle (1s/4s) – alarm or fault state has ended (historical memory);
-no sound – normal state;
6.5 The MDD module is controlled with a keypad located on the front panel. During normal operation (not in the
menu mode), additional functions are permanently assigned to the keypad keys. Pressing and holding the key
for a certain time causes respectively:
•key [ ▲ ] (≥1 sec. but < 3 sec.) – Activating the procedure displaying the detector bus slave address
configuration; the LED segment screen displays in turn the number of active detectors in the network and
the subsequent slave addresses of the detectors. If the detector status display is enabled, the current
device status is displayed when each slave address is displayed. When all addresses have been
displayed, the MDD returns to normal operation.

MDD-256/T Control Unit User Manual Issue 1W21en ©gazex’2018 v1806 Page 17 / 22
•key [ ▼ ] ((≥1 sec. but < 3 sec.) – activating the procedure displaying current faults and alarms with
assigning slave addresses to detectors that have reported given state; the LED segment screen displays
the type of faults or alarms, followed by the slave addresses of the detectors. When all active events have
been displayed, the module returns to normal operation.
•key [ OK ] ( ≥ 3 sec.) – zeroing the module, i.e. restoring initial settings of the MDD registers just as when
the power supply has just been switched on. Zeroing deletes the signalling devices’ memory of alarms or
faults that have ended.
•key [ ▲ ] ( ≥ 3 sec.) – entering the user menu. Holding down this key at any time during module
operation interrupts MDD control and measurement processes and enables the user to make required
changes to the module settings.
•key [ ▼ ] ( ≥ 3 sec.) – switching the internal siren on and off. Switching off the siren (activating the "silent
mode") is indicated by an intermittent acoustic signal and a pulsating green POWER light. This option is
especially recommended when the controller is installed inside switch boxes and only functions as a
ventilation controller, without the need to generate acoustic signals. Silent mode allows you to mute the
internal siren for an indefinite period of time (also after a power break).
•keys [ ▼ ] and [ OK ] ( ≥ 3 sec.) – if the keys are pressed simultaneously with the A2 alarm active, the
OUT6 voltage output is switched off for 15 minutes or until the next new A2 alarm is activated.
6.6 After correct installation and heating of the detectors in clean air, no acoustic or optical signals shall be
generated and an 'n' symbol indicating the normal status of the detector network shall be displayed on the
LED screen. If the "n.OFF" symbol is displayed on the screen, there are no active detectors in the network.
If other symbols are visible on the LED screen, yellow or red lights are on, and an acoustic signal is heard, the
detectors are incorrectly installed or the MDD configuration is faulty. Check the bus connections and the MDD
settings.
6.7 The final stage of the System performance check is the generation of all alarm states for all connected
detectors, and the performance check of external devices.
PREREQUISITES FOR THE SYSTEM CHECK:
-the MDD module is in a normal mode marked with the [n ] symbol, the green [POWER] light is on;
-active devices connected to the DET.NET network do not generate alarm or fault signals.
6.7.1 Generate alarm conditions successively for each detector installed on the DET.NET network with a test
gas of known concentration, according to the instructions in the detector's manual. After the gas has
been fed to the sensor, the LED display of the MDD module shall show [ A1 ], [ A2 ] or [ A3 ]. Pressing
the [ ▼ ] key for ca. 2 seconds displays the address of the detector that generated the alarm. The
display of the alarm status and the correspondence of the address are sufficient proof of correct
interaction between the detector and the module.
If the detector's alarm signals last for at least the time corresponding to the delay in activating the
outputs, an alarm signal shall be generated at the corresponding alarm outputs, the red lights [ OUT1
], [ OUT2 ] or [ OUT3 ] shall be lit, and the acoustic signal shall be activated. The outputs will be
activated according to the set zoning modes.
6.7.2 After the test gas has been removed, the gas concentration in the detector decreases, resulting in a
change of the detector status on the LED display to [ A2 ] or [ A1 ] and a message [ h3 ], [ h2 ] or [ h1 ]
(depending on the generated alarm number) being shown. The control outputs return to their normal
state (red LEDs go out), while the acoustic signal changes to intermittent in a 1s/4s cycle. The alarm
information remains on the LED display until the user deletes it manually and consciously.
6.7.3 The test procedure 6.5.1 shall be completed by an output test (outputs in normal mode and not in
'service' mode) conducted by the software from the user menu level described in point 5.5.4.2.
Results of the control or the launch should be entered into Periodic Control Protocol
If the test result is positive, the Digital Gas Detection System may be considered as
operational.

MDD-256/T Control Unit User Manual Issue 1W21en ©gazex’2018 v1806 Page 18 / 22
6.8. PROBLEM ?
Before you call the system Producer, check and compare the effect you observed with the below table
6.8 TABLE for exceptional states of the MDD module after switching on the power:
EFFECT
WHY
WHAT TO DO
All lights off
No power supply to the MDD
or reverse polarisation
Turn off the power supply
Just the FAULT light
on
MDD fault
Contact GAZEX service
[ E.nEt ] on MDD
display
No communication between
MDD and detector(s) in
DET.NET bus
Due to the problem’s complexity the exact procedure is
described in section 6.9. The detailed way of installing the
DET.NET bus connections is in section 4.2. of this manual
[ Er.04 ] on MDD
display
Power supply below allowed
value
Check and correct power supply parameters of the MDD
During A2 or A1 state,
[ Er.03 ] shows on
MDD display
Short-circuit or overload
(I>200mA) of the
outputsOUT5 and OUT6
Disconnect and check the devices/signalling devices
connected to the OUT5 and OUT6 outputs; after
disconnecting the devices, the message should disappear
No indication of alarms
in the detector
Deactivated detector
operation with this address,
detector service mode
activated
Check if the detector address is on the list of supported
devices (press the [ ▲ ] key for approx. 2 sec.); check the
detector settings
MDD signals the alarm
from a detector on the
LCD screen, does not
activate the outputs
MDD service mode on, or
long output activation delay
time
Check the MDD parameter settings
MDD does not activate
the outputs with the
detector A2 alarm on
Other zone mode on MDD
outputs enabled, e.g.
assigning outputs to A1
alarm only
Check the current settings of the zones on the outputs,
change the settings as needed
After the power supply
is switched on, the
segment display shows
alarm messages of the
devices for a few/a few
dozen seconds, then
the alarms disappear
If the detectors are stored for
a long time or if the ambient
temperature is low, the
warm-up period was too
short for the intended 1
minute (for low-calibration
detectors)
Wait a few minutes after powering up the system. After
completing the alarms, press the [OK] button for at least 3
seconds and clear the MDD
display (restore the module to its
normal state); correct the settings for the warm-up time of the
DET.NET bus devices
If you notice effects other then the above mentioned contact an Authorised Service or the Producer.

MDD-256/T Control Unit User Manual Issue 1W21en ©gazex’2018 v1806 Page 19 / 22
6.9. INSTALLATION AND LAUNCH RECOMMENDATIONS
The MDD user and the INSTALLER must be aware of the special way
in which the RS-485 bus was designed to digitally communicate with
detectors.
This means that installation and maintenance must be done with
THE HIGHEST CARE!!
Systems based on digital communication between the detectors and the MDD allow the transfer of an unlimited
amount of data between devices, increasing their functionality, but require great care when wiring. The most
common problems related to the lack of digital communication between MDD and devices in the DET.NET bus, or
between MDD and the control system in the OUT.NET bus, are caused by errors in the installation of the bus
cabling, the use of incorrect cabling, poor bus topology, or the use of untested additional devices in the network.
The following describes the recommended installation steps for connecting the bus cabling to the individual devices
and the startup recommendations, which describe the typical procedures in the case of reporting by the MDD a
lack of communication with a selected device, a group of devices or the entire bus (on the MDD screen the
message "E.nEt" appears).
6.9.1 Preparation.
-Before wiring, the installer should familiarise themselves with the basic parameters of the RS-485 interface and
observe the guidelines described in sections 4.2 and 4.3 of this manual when designing the topology of the
digital bus.
-Please refer to the operating instructions of the equipment to be installed. In case of installing devices to which
power supply and communication are to be provided by a common "twisted pair", it is necessary to use
terminal boxes type CB-4 in places where local power supply for a selected group of devices is to be provided.
CB-4 boxes are equipped with connectors (adequately internally connected) to connect power wires (maximum
cross-section 2.5mm2) supplied from a local 24V= power supply, and bus connectors designed for connecting
a twisted pair (device bus).
-The digital bus cable (twisted pair) should be distributed in series, starting from the MDD installation point
(control module), then successively through the installation points of the individual devices, terminal boxes, up
to the most remote device. Leave an excess of about 20-30cm of cable in the installation area for easier
connection of the device.
-It is essential to avoid distributing the digital bus cables in parallel and in close proximity to other cables of the
object, which may cause increased emission of interference (control of automation of the object, motors,
inverters). The optimal solution to eliminate many problems during system startup and operation is to use
shielded STP/FTP cables.
-All wiring connections must be made when the power supply is switched off..
6.9.2 MDD installation procedures.
-Connecting the twisted pair of the digital bus should be started with the first bus device, i.e. the MDD (control
module).
-Prepare and press the cable ends (according to section 4.2.2.A) to the terminals of the PORT1 of the bus:
"A+". - [07], „B-” [08] and 'GND' – [09], while maintaining the required conductor colour scheme (according to
section 4.2).
-Unused twisted pair wires must be protected against short circuiting, as it is possible to supply 24V for other
bus devices over these wires.
-If the digital bus cable runs through areas with expected electromagnetic interference, you must also connect
the shield of the cable ("GND") to the PE terminal of the electrical system at only one point, preferably at the
MDD module.
-Check that the wires are correctly connected to the terminals. Check that the colours of the conductors
connected to the respective terminals are in accordance with Table 4.2.2.
-Set jumper J1 at PORT1 to ON, thus activating the R=120Ω terminating resistor between the signals "A+" [07]
and "B-" [08] (default setting).
-After the MDD installation is complete, go to the next device in the bus.
6.9.3 Installation procedures for remaining devices.
-At the place of installation of the next bus device, cut the twisted pair cable and (according to section 4.2.2.A)
prepare the ends of the cable coming from the connected devices (from the control module).
-Use an ohmmeter to check the resistance values between the individual wires of the twisted pair cable
according to Table 6.9. The measurement should be carried out on a "hanging" wire (connecting the wire to the
terminals connected to the current device before measuring, will cause the wires to short-circuit in this device
and will make it impossible to check the correctness of earlier connections). It is essential to pay attention to
the polarity of the cables.
-If the measured resistance values are different, it means that the wires of the cable are wrongly connected to
the previous device, or that the last section of the cable is damaged. In this case, return to the previous device,
check again and correct the connections of the cables coming out to the last device, or check the wiring status
between the devices.

MDD-256/T Control Unit User Manual Issue 1W21en ©gazex’2018 v1806 Page 20 / 22
-If the resistance values are correct, press the wires into the appropriate terminals of the current device
(according to the user's manual), keeping the required conductor colour scheme. For legibility of connections, it
should be assumed that the wires coming to the device from the MDD side are connected to the lower
openings of the port terminals.
-Prepare the conductor ends of the bus cable towards the next unit. Push it into the upper holes of the port
terminals using the same rules as for the incoming cables.
-Repeat the installation steps described in section 6.9.3 for each device until the last one.
-Connect a terminating resistor R=120Ω on the last device between the "A+" terminals (orange) and 'B-' (white
and orange). The resistance value measured between these terminals when the resistor is connected at the
end of the bus should be about R=60Ω.
Table 6.9
MEASURED
RESISTANCE
BETWEEN TWISTED
PAIR WIRES
FUNCTION (COLOUR)
RS-485 - „A+”
(white and
orange)
RS-485 - „B-”
(orange)
RS-485 – power
supply weight
(FTP screen)
+ power supply
(white and green)
+ power supply
(white and brown)
+ power supply
(white and blue)
power supply
weight (green)
power supply
weight (brown)
power supply
weight (blue)
FUNCTION (COLOUR)
Power supply weight
(blue)
open open R (1)
Power supply weight
(brown)
open open R (1)
Power supply weight
(green)
open open
+ power supply
(white and blue)
open R (1)
+ power supply
(white and brown)
open R (1)
+ power suppply
(white and green)
open
RS-485 - weight
(ekran FTP)
open
RS-485 - „B-”
(orange)
60÷300
[Ω] (2)
RS-485 - „A+”
(white and orange)
Additional information:
(1) In the case of a short
-circuit between the power wires, the readout value of R will correspond to the
resistance resulting from the length of the wires between the measurement point and the nearest point of the
short-circuit (the resistance of the wires of the twisted pair is about 200 Ω / km of the cable loop).
(2) In case of measurement between "A+" and "B
-" lines, the value of the read resistance depends on the
number of connected terminating resistors and the length of signal cables:
-no resistors: open,
-one resistor: R = ca. 120 + line resistance [Ω],
-two resistors: R = ca. (120 / 2) + line resistance [Ω],
-three and more (not allowed!): R = ca. (120 / n ) + line resistance [Ω], where n – number of resistors
6.9.4 Checking the correct power supply for the devices.
After completion of installation of devices described in sections 6.9.2 and 6.9.3, power supply to the system should
be switched on and optical signalling of devices connected to the common bus should be checked (according to
dedicated manuals). If the observed signalling (or lack of it) indicates an incorrect voltage supply for the selected
devices, the cause should be found and the fault corrected. Table 6.9.4 describes typical problems with powering
the device bus.
Table of contents
Other gazex Control Unit manuals
Popular Control Unit manuals by other brands

Caltta
Caltta ZXIMCU PT01 P200 Operation manual

Comunello
Comunello CU 230V HP Installation and user manual
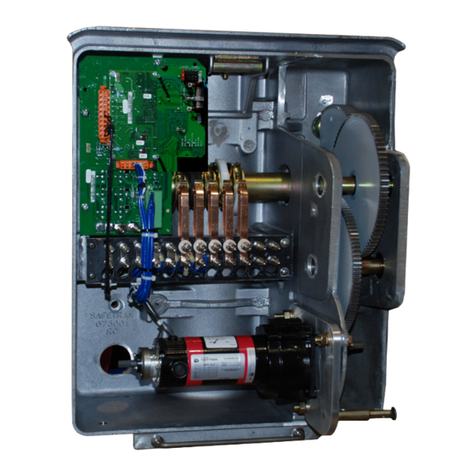
Siemens
Siemens S-60 quick start guide
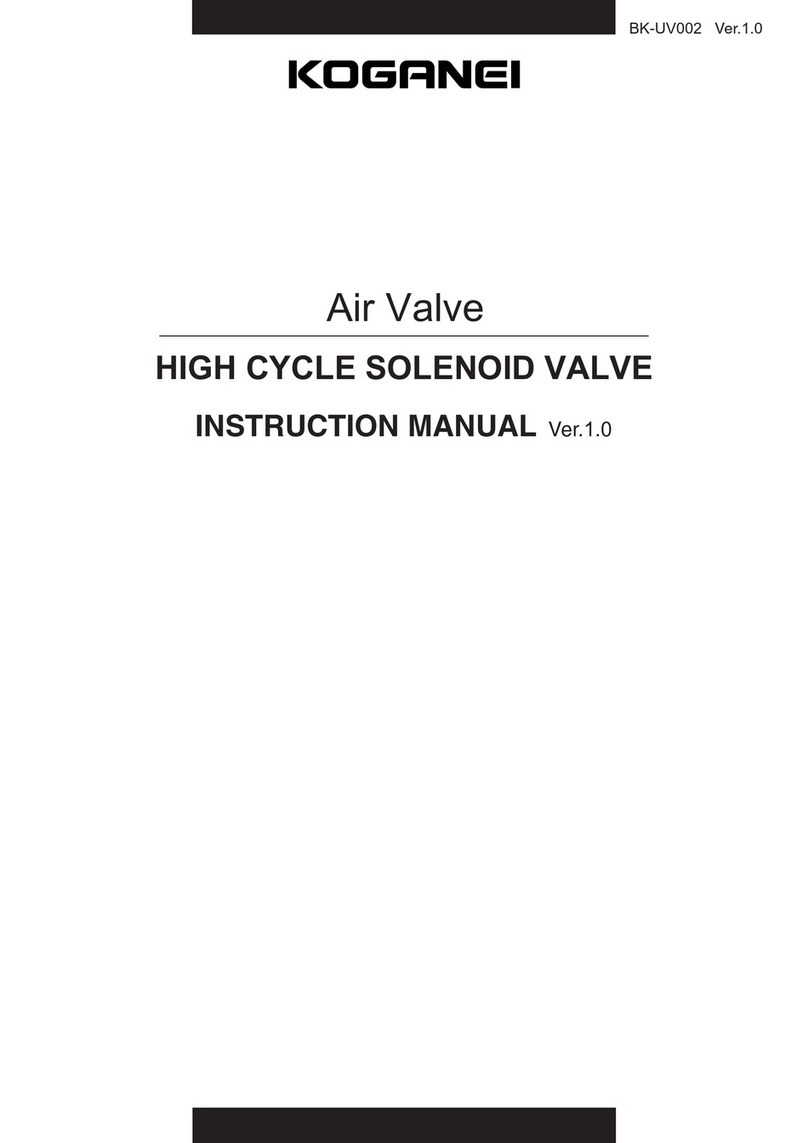
KOGANEI CORPORATION
KOGANEI CORPORATION HV160E1-2 instruction manual
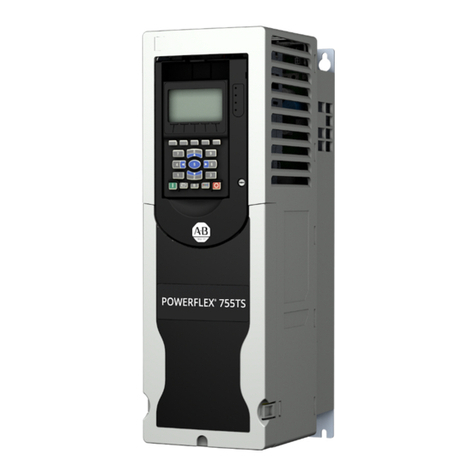
Allen-Bradley
Allen-Bradley PowerFlex 755 user manual

ThaiEasyElec
ThaiEasyElec MP3 user manual