GE SBC231A User manual

GEK-1
00637
B
INSTRUCTIONS
GE Multilin
215
Anderson
Avenue
Markham,
Ontario
L6E
1B3
Canada
http:I/www.GEindustrial.com/multilin
STATIC
BREAKER
BACK-UP
RELAY
TYPE
SBC
RELAY
SBC23IA

GEK-1
00637
Contents
Page
PRODUCT
DESCRIPTION
3
GENERAL
3
APPLICATION
3
CONFIGURATIONS
4
CALIBRATION
5
RANGES
5
HARDWARE
DESCRIPTION
6
CONSTRUCTION
6
RECEIVING, HANDLING
AND
STORAGE
6
INSTALLATION
PROCEDURE
6
Surge
Ground
6
ACCEPTANCE
TESTS
7
GENERAL
7
TEST
EQUIPMENT
7
DRAWINGS
7
EQUIPMENT
GROUNDING
7
GENERAL
RELAY
TESTS
7
Ti-PowerUp
7
T2-BFTTest
7
T3
-
Shutdown
Test
8
T4
-
Power
Supply
Alarm Test
8
T5
-
Target
Test
8
PERIODIC
TESTS
9
GENERAL
9
TEST
EQUIPMENT
9
DRAWINGS
9
EQUIPMENT GROUNDING
9
GENERAL
RELAY
TESTS
9
Ti
-
Power
Up
9
T2-BFf
Test
9
T3
-
Shutdown
Test
10
T4
-
Power
Supply
Alarm
Test
10
T5
-
Target
Test
10
SERVICING
11
SPARES
11
RENEWAL
PARTS
ii
SPECIFICATIONS
13
RATINGS
13
BURDENS
13
CONTACT
DATA
13
OVERCURRENT
UNITS
13
POWER
SUPPLY
ALARM
13
ACCURACY
13
CASE
14
DIMENSIONS
14
WEIGHT
14
Lists
of
Figures
and
Tables
14
(COVER
PHOTO:
8919539)
-2-

GEK-1
00637
PRODUCT DESCRIPTION
GENERAL
The
Type
SBC231
relay
is
a
three-phase
static
fault
instantaneous overcurrent
relay.
This
relay
provides
high-speed
operation
at
low
multiples
of
pickup,
minimum
transient
overreach
and
fast
dropout
times.
The
SBC231
relay
contains
the
following
basic
components
and
features.
1.
A
level
detector
with
two
independently adjustable
pickup
settings
for
phase
and ground
currents
with
a
reset
time
of
approximately
10
milliseconds.
2.
The
ability
to
configure
the
SBC
to
monitor
three
phase currents,
or
two
phase
currents
and
ground
current.
3.
Four
electrically
separate
(BFT) contact
output
circuits.
Two
of
these
circuits
have
an
electromechanical
series
target.
4.
One
electrically
separate
(BF’T)
output
circuit
with
selectable
normally
open
or
normally
closed
contact.
5.
One
output
circuit
that
can
be used
as
a
BFT
output
or
as
a
power
supply
alarm
output.
6.
A
regulated
power
supply
with
undervoltage
cutoff.
7.
Surge
suppression
on
all
AC and
DC
input
circuits.
The
power
supply
in
this
relay
is
so
designed
that
the
DC
voltage
must
exceed
60
percent
of
the
nominal
voltage
rating
for
the
relay
to
operate.
This
feature
prevents
false
trips
from
capacitance
discharge
or
from
the voltage
divider
effect
of the
ground
fault lamps on
the
DC
bus
in
the event
that
the
DC
input
terminal
of
the
SBC
is
accidentally
grounded.
APPLI
CATION
The
SBC23I
relay
is
intended
for
applications
requiring
an
instantaneous overcurrent detector
with
fast
pickup, fast
reset,
minimum
overreach,
and
Continuous
operation
in
the
picked
up
position.
The
three
input
current
circuits
to
the
SBC231
can
be
connected
to
the
three
phase
currents
(IA,
IB,
or
IC) in
a
three-phase
system,
or
to
two
phases
and
the
residual
current
(IA,
IB,
and
310).
Typical
applications
for
the
SBC231
relay
include
local
back-up
protection
for
circuit-breaker
failure,
underrated
interrupter
applications
on
circuit
breakers
or
circuit
switches,
or
fault-
detector
supervision
on
distance
schemes.
The
external,
connections
for
the
SBC231
are
shown
in
Figure
1.
These
instructions
do
not
purport
to
cover
all
details
or
variations
in
equipment
nor
provide
for
eveiy
possible
contingency
to
be
met
in
connection
with
installation,
operation
or
maintenance.
Should
further
information
he
desired
or
should
particular
problems
arise
which
are
not
covered
sufficiently
for
the
purchasers
purposes,
the
matter
should
be
referred
to
the
General
Electric Company.
To
the
extent
required the
products
described herein
meet
applicable
ANSi
IEEE
and
NEMA
standards;
but
no
such
assurance
is
given
with
respect
to
local
codes
and ordinances
because
they
vaty
greatly.
-3-

GEK-100637
Figure
2
shows
an
application
where
an
instantaneous
overcurrent
relay
may
he
used
to
prevent
attempted interruptions
of
fault
currents
above
breaker
rating.
For
some
system
conditions,
heavy
close-in line faults
such
as
Fl
might
exceed
the
interrupting
rating
of the
line
breaker
(3).
The
application
of
an
instantaneous
overcurrent
relay
set
near
the
line
brcaker
rating permits
operation
of
the
bus
tie
breaker
(BT)
to
relieve the
duty
on
the
line
breaker
for
these
critical
faults
before
operation
by
the
line
breaker. The
SBC231
is
particularly
well
suited
to
this
type
of
application
since
it
has
less
than
ten
percent transient
overreach
and
operating
times
of
approximately
one-half
cycle
(60
hertz
basis)
at
l.5X
pick
up.
(See
Figure
4.)
It
is
usually
possible
to
coordinate
this
high-set
overcurrent
protection
right
up
to
the
interruption
limits
of
the
line
breaker
without
introducing
any
delay
in
the
line
relaying
that
would affect
other
less
critical
faults such
as
at
F2.
Figure
3
shows
a
similar
application
for
protection
of
a
circuit
switcher
at
a
transformer
tap
on
a
transmission
line.
The
SBC231
overcurrent
relay
can
be
set
to
operate
just
below
the interrupting
capacity
of
the circuit switcher
to
avoid
possible
Interrupter
failure
for faults
at
the
high
side
of
the
transformer
at
Fl.
The
SBC
would
be
connected
to
block
the
operation
of
the
circuit switcher
until
the
fault
is
cleared
at
line
terminals
A
and
B.
Applications
of
the
SBC231
as
a
breaker-failure
relay
would
be
accomplished
on
a
per-breaker
basis.
On
this
basis
the
current
inputs
to
a
particular
SBC
relay
come
from
the
current
transformers
that measure
the
current
in
the
associated
breaker.
The
SBC
DC
supply
is
enabled
by
the
protective relays
associated
with
the
zone
of
protection,
and
the
output
of
the
SBC
is
connected
to
a
definite
timer,
such
as
a
Type
SAM
timing
relay.
The
timer
is
set
with
sufficient
delay
to
permit
interruption
of
the
associated
breaker
when
operated
by
the primary
relays.
(See
Figure
5.)
If
the
breaker
fails
to
interrupt
successfully
within
this
time,
the
timer
will
time
out
and
initiate
tripping
of
all
breakers
necessary
to
clear
the
fault.
A
detailed
discussion
of
breaker
failure
applications
for various
bus
configurations
is
included
in
GEK-100636.
The
SBC231
is
also
well
suited
to
applications
such
as
pilot
and
distance relay
line
protection
schemes
requiring
high-speed
overcurrent
detectors.
CONFIGURATIONS
Output
Studs
The
relay
is
delivered
with
a
Normally
Open Contact
at
Studs
15
and
16;
it can
be
changed
to
a
Normally
Closed
Contact
by
connecting
the
Fast-On
terminal
from
H15A
on
the
backplane
to
terminal
block
stud
15.
(See
Figure
7.)
The
SBC23I
is
delivered
with
aPower
Supply
Alarm contact
at
studs
7
and
8.
(See
Figure
7.)
This
Power
Supply
Alarm
contact
will
close
if
the
battery
voltage drops
below
19
VDC.
To
configure
the relay
to
have
an
Output
Contact
at
Studs
7
and
8,
move
relay
K4
from
position
K4B
to
position
K4A
on
the backplane.
Input
Currents
All
SBC231
models
are
delivered
in
the
configuration
that
accommodates
two
phase-current
inputs
and
one
ground
current
input.
However,
moving
connector
PM
on
the
backplane
to
cover
positions
3
through
8
will
enable
the
relay
to
monitor
three
phase
currents.
(See
Figures
7
and
When
connector
PL4
is
in
position
1
through
6,
and
the
external
connections
are
as
shown
in
Figure
1,
the
current
at
Studs
1,
2,
and
3,4
is
monitored
by
the phase-current
pickup
and
the
current at
studs
5
and
6
is
monitored
by
the
ground-current
pickup.
*
The
output
relays
on
the
SBC
have
a
pickup
time
of
6
-
lOms.
and
a
dropout
time
of
3
-
5
ms.
-4-

GEK-100637
When
connector
PL4
is
in
position
3
through
8,
and
the
external connections
are
as
shown
in
Figure
1A,
the
current
at
studs
1,2,
3,4,
and
5,6
is
monitored
by
the
phase-current
pickup
and
the
ground-current
pickup
is
disabled.
CALIBRATION
Level
Detector
All
SBC
relays
are
tested
using
automatic
test
equipment.
There
is
no
need
for
any
calibration
when
the
relay
is
received.
However,
if
the
analog
board
is
replaced,
the
user
does
have
the
ability
to
calibrate
the
level-detector
pickup.
This
is
done
by
first
configuring
the
relay
to
monitor
both
the
phase
and
ground
inputs
(see
CONFIGURATION).
Input
an
rms
value
of
current
equal
to
that
of
the
pickup
of
the
phase
or
ground
unit.
If
the
TB
ENERGIZED
LED
is
not
ON,
adjust
potentiometer
R25
(phase
unit) or R24
(ground
unit),
located
on
the
front
of
the
analog
board,
by
turning
the
screw
in
the
counter-clockwise
direction
until
the
TB
ENERGIZED
LED
is
ON
continuously.
If the
TB
ENERGIZED
LED
comes
ON
as
soon
as
the
current
is
applied,
turn
the
screw
in
the
clockwise
direction
until
the
TB
ENERGIZED
LED
goes
out,
then
turn
the
screw
in
the
counter-clockwise
direction
until
the
LED
is
ON
continuously.
Reset
Timer
The
reset
time
for the
SBC
is
a
permanent
value
built
into
the hardware
of
the
relay.
If
there
is
a
need
to
change
the
reset
time,
consult
the
factory
for details.
RANGES
SBC231
1
Amp
Version
5
Amp
Version
Phase
Current
O.2A
-
1.7A,
in
O.1A
steps
1.OA
-
8.5A,
in
O.5A
steps
Ground
Current
O.1A
-
O.85A,
in
O.05A
steps
O.5A
-
4.25A,
in
0.25
steps
-5-

GEK-100637
HARDWARE
DESCRIPTION
CONSTRUCTI
ON
I’he
components
of the
relay
are
mounted
on
a
cradle
assembly
that
can
easily
be
removed
from
the
relay
case,
refer
to
Figures
8
through
11.
The
cradle
is
locked
in
the
case
by
latches
at
the
top
and
bottom. The
electrical
connections
between
the
case
blocks
and
the
cradle
blocks
are
completed
through
removable
connection
plugs,
as
shown
in
Figure
12,
to
permit
testing
the
relay
in
its
case.
The
cover
is
attached
to
the
front
of
the
case
and includes
two
interlocking
arms
that
prevent
the
cover from
being
replaced
until
the
connection
plugs
have
been
inserted.
The
case
is
suitable
for
semi-flush
mounting
on
panels.
Hardware
is
available
for
all
panel
thicknesses
up
to
two
inches.
A
panel
thickness
of
1/8
inch
will
be
assumed
unless
otherwise
specified
on
the
order.
The
printed-circuit
hoards
are
mounted behind
the
nameplate
and
can
be accessed
by
removing
the
four
screws
securing the
nameplate.
The
boards
are
mounted
horizontally
in
guides.
Use
GE
part
nurnl)er
286A2847P1
card
puller
or
other
suitable
means
to
remove
the
circuit
boards.
If
you
do
not
have
a
card
puller, be
careful not
to
damage
or
bend
any
components
when
removing
the
boards.
RECEIVING,
HANDLING
AND
STORAGE
This
relay
contains
electronic
components that
could
be
damaged
by
electrostatic
discharge
currents
if
those
currents
flow
through
certain
terminals
of
the
components.
The
main
source
of
electrostatic
discharge currents
is
the
human
body,
and
the
conditions
of
low
humidity,
carpeted
floors
and
isolating
shoes
are
conducive
to
the
generation
of
electrostatic
discharge
currents.
Where
these conditions
exist,
care should
be exercised
when
removing
and
handling
the modules.
The
persons handling
the
module
should
make
sure
that
their
body
charge
has
been
discharged,
by
touching
some
surface
at
ground
potential,
before
touching
any
of the
components
on
the
modules.
These
relays,
when
not
included
as
part
of
a
control
panel,
will
be
shipped
in
cartons
designed
to
protect
them
against
damage.
Immediately upon
receipt
of
a
relay
examine
it
for
any
damage
sustained
in
transit.
If
damage
resulting
from handling
is
evident,
file
a
damage
claim
at
once
with
the
transportation
company
and
promptly
notify
the
nearest
General
Electric
Sales
Office.
If
the
relays
are not
to
be
installed immediately,
they
should
be
stored
in
their
original cartons,
in
a
place
that
is
free
from
moisture,
dust
and
metallic
chips.
INSTALLATION
PROCEDURE
The
relay should
be
installed
in
a
clean,
dry
location,
free
from
dust
and
excessive
vibration.
It
should
be
mounted
on
a
vertical surface.
The
outline
and
panel-drilling
dimensions are
shown
in
Figure
13.
Surge
Ground
The
case
stud
should
be
permanently connected
to
ground
by
a
conductor
not
less
than
AWG
No.
12
copper
wire
or
equivalent.
This
connection
is
made
to
ground
the
relay
case
and the
surge
suppression networks
in
the
relay.
The
surge-ground lead
should
be
as
short
as possibLe,
preferably
10
inches
or
less,
to
provide
maximum
protection
from surges.
Figure
10
shows
the
rear
view
of
an
M2
case,
illustrating the
position
of
the case-grounding
stud.
-6-

GEK-1
00637
ACCEPTANCE
TESTS
CAUTION
Power
Down
the
relay
by
removing
the
test
plugs
before
removing or
inserting
modules.
Failure
to
do
so
can
permanently
damage
the
relay.
GENERAL
This
section
is
a
guide
for
testing
the
relay.
It
is
not
necessary
that
the
tests
be
performed
for
incoming
inspection.
The
relay has
been tested
at
the
factory
with
automated
test
equipment.
TEST
EQUIPMENT
1.
Single
source
of
current
at
the
rated
frequency.
2.
AC
ammeter.
3.
Continuity
tester
or
Ohm meter.
4.
One
VDC
supply.
The
specific
requirements
of
the
equipment
are
given
in
the
text
of
this
section,
and
in
the
associated
circuit diagrams.
DRAWINGS
Figure
1,
located
in
the
PRODUCT
DESCRIPTION
section,
should be used
for
reference
during
testing.
EQUIPMENT
GROUNDING
All
equipment
used
in
testing the
SBC23I
relay
should
be
connected
to a
common grounding
point
to
provide
noise
immunity. This
includes
the
current
source,
as
well
as
the
SBC231
itself.
The
ground connection
on the
SBC231
is
terminal
#21
(case).
GENERAL
RELAY
TESTS
All
tests
are
performed
assuming
the
relay
is
configured
for
an
NO
Power
Supply
Alarm
contact
at
Studs
7
and
8
and
an
NO
contact
at
studs
15
and
16.
Ti
-
POWER
UP
I.
Connect
the relay
as
shown
in
Figure
14.
The
AC
input
is
not required
for
this
test;
only
the
DC
power
supply
voltage
is
required.
Apply
the
rated
DC.
2.
Only
the
Green,
ENERGIZED,
LED
should
be
on.
T2
-BFI’TEST
1.
Connect
the
relay
as
shown
in
Figure
15.
2.
Set
the
phase
and
ground
pickup
to
its
minimum
setting.
3.
Conduct
the
test
according
to
the
steps
in
Table
I.
-7-

GEK-100637
TABLE
I
Current
Current
Studs
Contacts Phase
or
Ground!
TB
Energized
95% of
phase
PU
1,2
open
off
95%
of
phase
PU
3,4
open
off
95%
of
ground
PU
5,6
open
off
105%
of
phase PU
1,2
closed
on
105%
of
phase
PU
3,4
closed
on
105%
of
ground
PU
5,6
closed
on
T3
-
SHUTDOWN
TEST
1.
Connect
the relay
as
shown
in
Figure
15.
2.
Conduct
the
test
accordin
to
the last
line
of
Table
I.
3.
While the
input
current
is
still
being
applied,
decrease
the
input
DC
to
60%
of
the
Rated
DC
voltage.
4.
The
only
relay
lights
that
should
remain
on
are
the
DC
Voltage
Low
light
and
the
Energized
light.
All
contacts
should
go
to
their
unenergized
state.
T4
-
POWER
SUPPLY
ALARM
TEST
1.
Connect
the
relay
as
shown
in
Figure
16.
2.
Conduct
the
test
according
to
the last
line
of
Table
I.
3.
While the
input
current
is
still
being applied,
lower
the
DC
voltage
to
19
VDC.
4.
All
output
contacts
should
go
to
their unenergized state
and
the Power
Supply
Alarm
contacts should
close.
T5
-
TARGET
TEST
1.
Connect
the relay
as
shown
in
Figure
17.
2.
Set
the
phase
pickup
to
1
A.
Input
2
A
into studs
1,2.
3.
Input
200
mA
through
contacts
11,12
and
see
that
the
I3FT1
target
has
tripped.
4.
Input
200
mA
through
contacts
13,14
and
see
that
the
BFT2
target
has
tripped.
-8-

GEK-1
00637
PERIODIC
TESTS
CAUTION
Power
Down
the
relay
by
removing
the
test
plugs
before
removing
or inserting
modules.
Failure
to
do
so
can
permanently
damage
the
relay.
GENERAL
This
section
is
a
guide for
testing the
relay.
It
is
not
necessary
that
the
tests
be
performed
for
incoming
inspection.
The
relay
has
been
tested
at
the factory
with
automated
test
equipment.
TEST
EQUIPMENT
1.
Single
source
of
current
at
the
rated
frequency.
2.
AC
ammeter.
3.
Continuity
tester
or
Ohm
meter.
4.
One
VDC
supply.
The
specific
requirements
of
the
eq4pment aregiven
in
the
text
of
this
section,
and
in
the
associated
circuit diagrams
in
the
ACCEPTANCE
TESTS
section.
DRAWINGS
The
External Connections
Diagram
(SBC231),
Figure
1
located
in
the PRODUCT
DESCRIPTION
section, should
be
used
for
reference
during
testing.
EQUIPMENT
GROUNDING
All
equipment
used
in
testing
the
SBC23I
relay
should be
connected
to a
common grounding
point
to
provide
noise
immunity.
This
includes
the
current
source,
as
well
as
the
SBC231 itself.
The
ground connection
on
the
SBC23
1
is
terminal
#10.
GENERAL
RELAY
TESTS
Ti
-
POWER
UP
1.
Move
the
rated
DC
voltage
switch
to
the
input
battery
voltage.
2.
Connect
the
relay
as
shown
in
Figure
14
The AC
input
is
not
required
for
this test;
only
the
DC
power-supply voltage
is
required.
Apply
the
DC.
3.
Only
the
Green,
ENERGIZED,
LED
should
be
on.
T2-BVI’TEST
1.
Connect
the
relay
as
shown
in
Figure
15.
2.
Apply
current
5
percent
below
the
pickup
value
to
each
of
the
three current
inputs.
3.
Notice
that
the
contacts
are open
and
no
lights
are
on.
4.
Increase
current
to
5
percent
above
the
pickup
value.
Notice
that
all
of
the
contacts
have
closed
and
the
Phase/Ground
and
TB
Energized
lights
are
on.
-9-

GEK-100637
T3
-
SHUTDOWN
TEST
1.
Connect
the
relay
as
shown
in
Figure
15.
2.
Conduct
the test
according
to
item
4
of
the
BFT
TEST.
3.
While
the input
current
is
still
being
applied,
decrease
the
input DC
to
60%
of
the
Rated
DC
voltage.
4.
The
only
relay
lights
that
should
remain
on
are the
DC
Voltage
Low
light
and
the
Energized
light.
All
contacts
should
go to
their
unenergized
state.
T4
-
POWER
SUPPLY
ALARM
TEST
1.
Connect
the relay
as
shown
in
Figure
16.
2.
Conduct
the
test
according
to
item
4
of the
BFT
TEST.
3.
While
the input
current
is
being
applied,
lower
the
DC
voltage
to
19
VDC.
4.
All
output
contacts
should
go
to
their
unenergized
state
and
the
Power
Supply
Alarm
contacts
should
close.
T5
-
TARGET
TEST
1.
Connect
the
relay
as
shown
in
Figure
17.
2.
Input
current
5
percent
above the
Phase
pickup setting.
3.
Input
200
mA
through
contacts
11,12
and
see
that
the
BFTI
target
has
tripped.
4.
Input
200
mA
through
contacts
13,14
and
see
that
the
BFT2
target
has
tripped.
-10-

GEK-1
00637
SERVICING
CAUTION
Power
Down
the
relay
by
removing
the test
plugs
before removing
or
inserting
modules.
Failure
to
do
so
can
permanently
damage
the
relay.
SPARES
There
are
two
basic
approaches
that
may
be followed
in
servicing
the
SBC
relay.
One
approach
is
field
service,
where
an
attempt
is
made
to
replace
defective
components
at
the
relay
location.
Generally,
this
will
take
the
most
time and
require
the
highest
degree
of
skill
and
understanding.
it
can
also
he
expected
to
result
in
the
longest
system—outage
time.
The
preferred
approach
is
board
replacement,
where
a
determination
is
made
as
to
which
printed-circuit
board
has
failed,
and
that
hoard
is
replaced
with
a
spare
board.
The
system
can
then
be
quickly
returned
to
service.
Considerable
time
is
saved
and
there
is
much
less
pressure
to
make
a
decision
about
what
to
do with
the
defective
part.
This
approach
typically yields the
shortest
down time.
It
is
recommended
that
a
complete set
of
spare
printed-circuit boards
be
kept
at
the
main
maintenance
center.
For
those
who
wish to
repair
at the
component
level,
drawings
are available
from
the
factory.
When
requesting
drawings,
the
following
information
must
be
supplied
to
the
factory:
1.
Assembly
number
of
the
board.
This
is
found
on
the
component
side of
the
printed-circuit
board.
It
is
an
eight-digit
number
with a
letter
inserted
between
the
fourth
and
fifth
digit
and
suffixed
with
a
group
identification,
e.g.
0184B8921G2.
2.
Revision
number
of
the
board.
This
is
also
found
on
the
printed-circuit
board,
e.g.
REV.
1.
The
acceptance
tests
should
be
performed
after
a
printed-circuit
board
has
been
repaired
or
replaced.
Whenever
the
nameplate
is
removed
from
the
relay,
care
must
be
taken
when
replacing
it
so
that
it
does
not
interfere
with
the
mechanical
operation
of
any
switches
that
protrude
through
the
nameplate.
RENEWAL
PARTS
It
is
recommended
that
sufficient
quantities
of
renewal
parts
be
carried
in
stock
to
enable
the
prompt
replacement
of
any
that
are
broken
or
damaged.
When
ordering
renewal
parts,
address the
nearest
Sales
Office
of the
General
Electric
Company.
Specify
the
quantity
required,
the
name
of
the
part
wanted,
the
part
number
if
known,
and
the
complete
model
number
of
the
relay
for
which
the
part
is
required.
The table
below
lists
the
part
numbers
for the most common
replacement
parts.
It
is
recommended that
renewal
parts
only
be
obtained
from
the
General
Electric
Company.
Should
a
printed-circuit
card
become
inoperative,
it
is
recommended
that
the
card
be
replaced
with a
spare.
—11-

GEK-1
00637
RENEWAL
PARTS
MODEL NUMBER
FUNCTION
PART
NUMBER
SBC223AXXA
ANALOG
BOARD
0184B8921G002
SBC223BXXA
SBC223CXXA
SBC221AXXA
0184B8921G003
SBC223BXXA
SBC223DXXA
0184B8921G004
SBC23
1AXXA
SBC221BXXA
TIMER
BOARD
0184B8750G006
SBC223CXXA
SBC223DXXA
SBC23
1AXXA
SBC22
1AXXA
01
84B8750G007
SBC223AXXA
SI3C223BXXA
SBC2XXXXXA
POWER
SUPPLY
BOARD
0184B6385G003
SBC221AXXA
LOGIC BOARD
0188B9752G001
SBC22IBXXA
0188B9752G002
SBC223AXXA
0188B9752G003
SBC223BXXA
0188B9752G004
SBC223CXXA
0188B9752G005
SBC223DXXA
0188B9752G007
SBC23
IAXXA
0188B9752G006
SBC22IAOIA
BACKPLANE
BOARD
0215B8410G001
SBC22IAO2A
0215B84
10G003
SBC22IAO3A
SBC22IBO1A 0215B8410G002
SBC22IBO2A 0215B8410G004
SBC221BO3A
SBC223AO1A
0215B84110001
SBC223AO2A
0215B841
1G002
SBC223AO3A
SBC223BO1A
0215B8411G003
SBC223BO2A
0215B8411G004
SBC223BO3A
SBC223CO1A
0215B8411G003
SBC223CO2A
0215B8411G004
SBC223CO3A
SBC223DOIA 0215B8411G005
SBC23
1AO1A
0215B8412G001
SBC23
1AO2A
0215B8412G002
SBC23
I
AO3A
SBC2XXXXXA
EXThNDER
BOARD
0215B8031G001
CARD
PULLER
207A5404P001
UPPER
CRADLE
BLOCK
0184B8624G014
LOWER
CRADLE
BLOCK
0184B8624G013
UPPER
CASE
BLOCK
006418058G045
LOWER
CASE
BLOCK
0064180580129
-12-

GEK-1
00637
SPECIFICATIONS
RATINGS
Rated
Frequency
50
or
60
Hertz
DC
Control
Voltage
36
-
280
VDC
Input
Circuit
Current
Ratings
Nominal
Current
=
1A
Nominal
Current
=
5A
Continuous
1A
5A
One
Second
100A
500A
Ambient
Temperature
Range
Operation
—20°
C
to
+65°
C
Storage
—40°C
to
+85°
C
Humidity
95%
without
condensation
Insulation
Test
Voltage
2kV
50/60
Hz,
one
minute
Impulse
Voltage
Withstand
5kV
peak,
1.2/50 milliseconds,
0.5
joules
Interference
Test
Withstand
SWC,
per
ANSI
C37.90.1;
IEC
255
BURDENS
Current
Circuits Ohms VA
@
5A
5A
Transactor
.029
ohm,
46.02°
at
60
Hz
.026
ohm,
40.9°
at
50
Hz
1A
Transactor
.597
ohm,
49.69°
at
60
Hz
.541
ohm,
44.98°
at
50
Hz
DC
Battery
(power
supply)
20
Watts
Max
CONTACT
DATA
Trip
Outputs
Continuous
Rating
3
Amps
Make
and
Carry
for
Tripping
Duty
30
Amps
(per
ANSI
C37.90)
Target
Operate
Level
Mm.)
150
mAmps
Max.)
30
Amps
for
I
sec.
Continuous)
5
Amps
OVERCURRENT
UNITS
Range
in
Amps
Resolution
in
Amps
I
Amp
Relay
5
Amp
Relay
1
Amp
Relay
5
Amp
Relay
Phase
.2
-
1.7
1
-
8.5
.1
.5
Ground
.1
-
.85
.5
-
4.25
.05
.25
POWER
SUPPLY
ALARM
<19
VDC
ACCURACY
IOC
5%
-13-

GEK-100637
CASE
M2
DIMENSIONS
See
Outline
and
Panel
Drilling
Dimensions, Figure
13
WEIGHT
Maximum
shipping weight
20
pounds(9.09
kilograms)
LIST
OF
FIGURES
and
TABLES
Figure
1
External Connections
and
Logic
Diagrams
SBC231
for
IA,IB,
&
310
Operation
15
Figure
1A
External
Connection
and
Logic
Diagram
of
SBC23I
for
IA,IB,
and
IC
Operation
16
Figure
2
Underrated
Line
Breaker
Application
17
Figure
3
Circuit
Switcher
Protective
Application
17
Figure
4
Relay
Operating
Time
18
Figure
5
Relay
Operating
Time
in
Breaker
Failure
Applications
19
Figure
6
Relay
Dropout
Time
20
Figure
7
Internal
Connections
Diagram
for
SBC231
21
Figure
8
SBC
with
Front
Cover
Removed
22
Figure
9
SBC
Front
View
Without
Nameplate
22
Figure
10
Rear
View of
Relay
Case and
Cradle
23
Figure
11
Typical
Removed
Module
24
Figure
12
Drawout
Case
Contact
Assembly
24
Figure
13
Outline
and
Panel
Drilling
Dimensions
25
Figure
14
Power
Up Test
Connections
26
Figure
15
BFT
Test Connections
26
Figure
16
Power
Supply
Alarm Test Connections
27
Figure
17
Target
Test
Connections
27
TABLE
I
8
-14-

B
C
NOTE:
SET
INTERNAL
JUMPER
PL4
TO
THE
1
THRU
6
POSITION.
—F
:I
PROTECTED
BREAKER
(+)
I
j
—
CD
01
-.
r)
-I
C,,
(-‘J
21
(CAsE)
TO
SURGE—
0
GROUND.
DIRECT
CONNECTION
TO
+DC
FOR
OVER
CUR
R
[NT
A
PLICATIO
N
K4
POSITION
OUTPUT
T
CONTACT
BFI
L__
911
13
15
r
T2 Ti
CO’a.ECTED
SB
T
0
T,
2
T
4
T
6
(FOR
BPEAKER
—
FAILURE
APPLICATICN)
(-)
POSITICN
B
POWER
SUPPLY
LAR
68
15
LEAD
CONNECTED
TO
iSA
0
m
ii’

c
J
i.
CD
C.
o
I.
A
B
NOTE:
SET
INTERNAL
JUMPER
PL4
TO
THE 3
THRU
8
POSITION.
C
G)
m
21
(CASE)
TO
SURGE
0
GROUND
(+)
DIRLOT
CONNECTION
To
+DC
FOR
OVEPOURRENT
APPLICATION
SF1
L__
(FOR
BREAKER
—
FAILURE
APPLICATION)
K4
POSPHON
OUrPUT
CONTACT
i
7
9
11
13
15
119
A
1
T2 Ti
J_TO
15B
I
LEAD
CONNECTED
T
2
T
4
116
K4
POSITION
B
POWER
SUPPLY
ALAR.A
68
15
LEAD
CONNECTED
TO
15
i6
(-)

GEK-1
00637
LOAD
NCR
TH
BUS
BUS
TIE
a
R
EAKE
R
SOUTH
BUS
—-I
CEDE
ND:
CIRCUIT
B
RE
A
K
ER
@
INSTANTANEOUS
OVERCURRENT
RELAY
Figure
2
(0285A6204-O)
Underrated
Line
Breaker
Application
LOC
K
F
1
LEG
E
ND
CIkCU1T6REAKER
Figure
3
lNSTANTANEOUSOVEPCUENTREL’
CI
ROUI
TSWI
T
C
1-4
ER
(0285A6205-O)
Circuit
Switcher
Protective
Application
-17-

GE
K-i
00637
SBC
—
Relay
Operating
Time
The
time
required
for
the
relay
to
close
contacts
of
output
relay.
Time
(ms)
-
I
10
11
12
13
Multiples
of
Pickup
Setting
Figure
4
(0286A5392)
Operating
Time
Graph
for
the
SBC
Relay
10
C.’
7_
I
I,•
Conditions:
1)
D.C.
Power
Supply Previously
Energized
2)
Current
Suddenly
Applied
3)_Includes_Time
to
Close
Contacts
7—
%%
—__
—
5—
4—
—-
3—
2—
-
- -
1—
--__
0
-—I
0
123456789
-I
-18-

GEK-1
00637
SBC
—
Relay
Operating
Time
for
the
SBC231
in
Breaker
Failure
Applications.
The
time
required
to
close
contacts
of
output
relay.
Time
(ms)
I
I
I
10
11
12
13
Multiples
of
Pickup
Setting
Figure
5
(0286A5394)
Breaker
Failure
Operating
Time
for
the
SBC231
Relay
20
1
1
1
I
1
1
1
1
1
9-
Conditions:
1)
D.C.
Power
Supply
Suddenly
Energized
0
2)
Steady
State
Current
Flowing
Previously
•
3)_Includes
Time
to
Close
Contacts
7—
6—
\
Maximum
Time
5
\
-——-Mrnmum_Time
s
3—
-
-
2—
-
—---
-___
—-
.—
1—
———
—-
10
II
I
I
I
I
012345
6789
II
-19-

GEK-1
00637
Soc
—
Relay
Dropout
Time
The
time
required
for
the
output
relay
contacts
to
open.
Multiples of
Pickup
Setting
Figure
6
(0286A5395)
Dropout
(Trip
Output
Removal)
Operating
Time
for
the
SBC231
Relay
20
Time
(ms)
1
1
1
1
1
1
1
1
1
E
Conditions:
8—
—-
1)
Includes
Time
to
Open
Contacts
—
Current
Reduced
to
95%
of
PU
—
——
—
Current
Reduced
to
0%
of
PU
7.......
6—
—-
-___
5—
-
-
——
—
4—
—_-.-
.
———
—
—
3—
2—
—
1
—
•———
-______
10
I
P
I
I
P
I
II
0123456789
10
11
12 13
-20-
Table of contents
Other GE Relay manuals
Popular Relay manuals by other brands

Novatek-electro
Novatek-electro REV-201M user manual
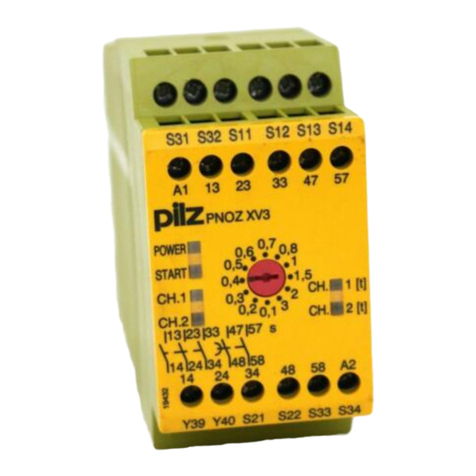
Pilz
Pilz PNOZ XV3 operating instructions

VERIS INDUSTRIES, INC.
VERIS INDUSTRIES, INC. V222 installation guide

LOVATO ELECTRIC
LOVATO ELECTRIC PMV 50-N manual
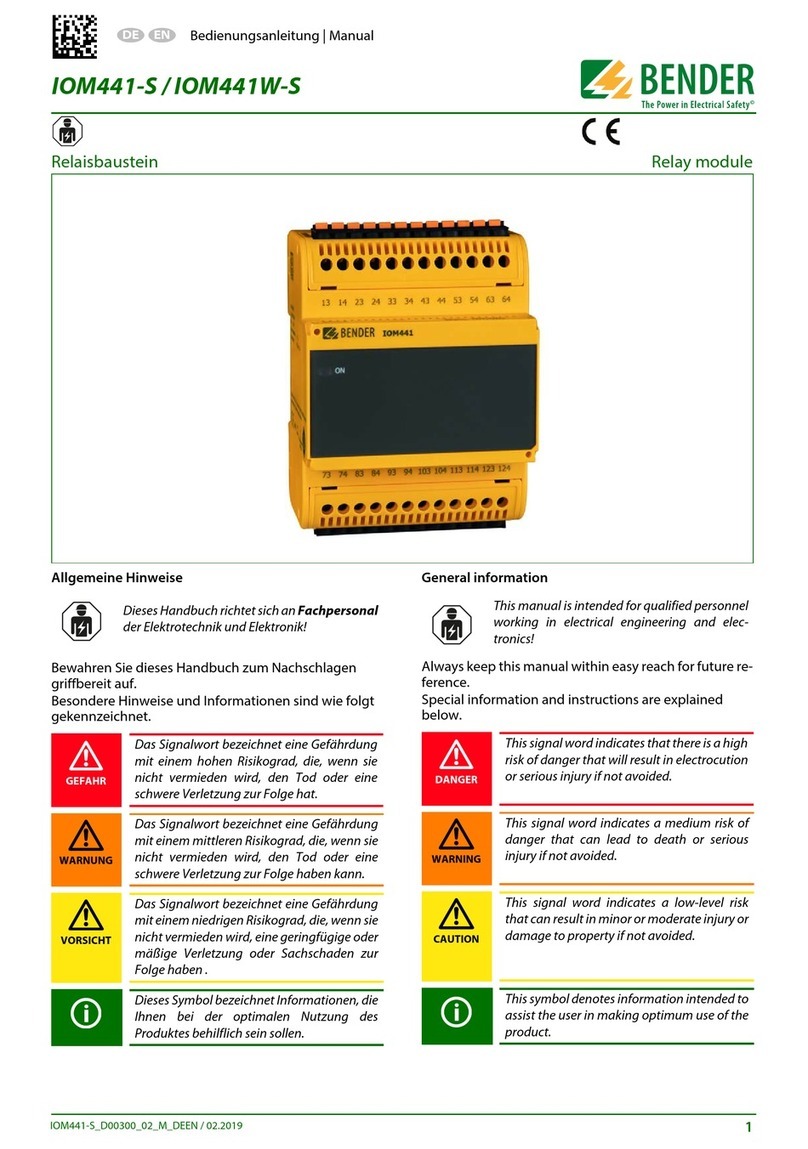
Bender
Bender IOM441-S manual
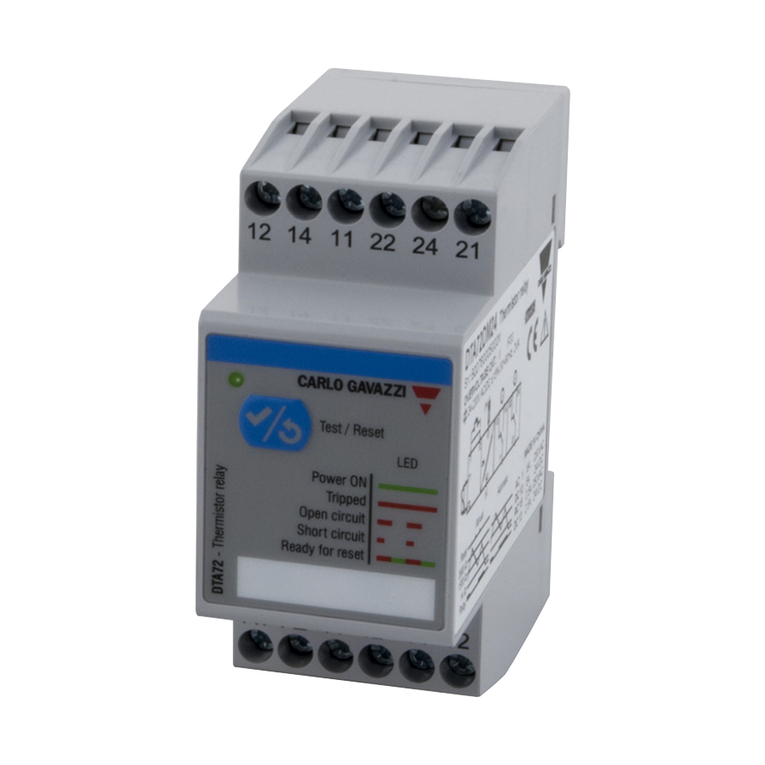
CARLO GAVAZZI
CARLO GAVAZZI DTA71CM24 Technical data, installation and operation
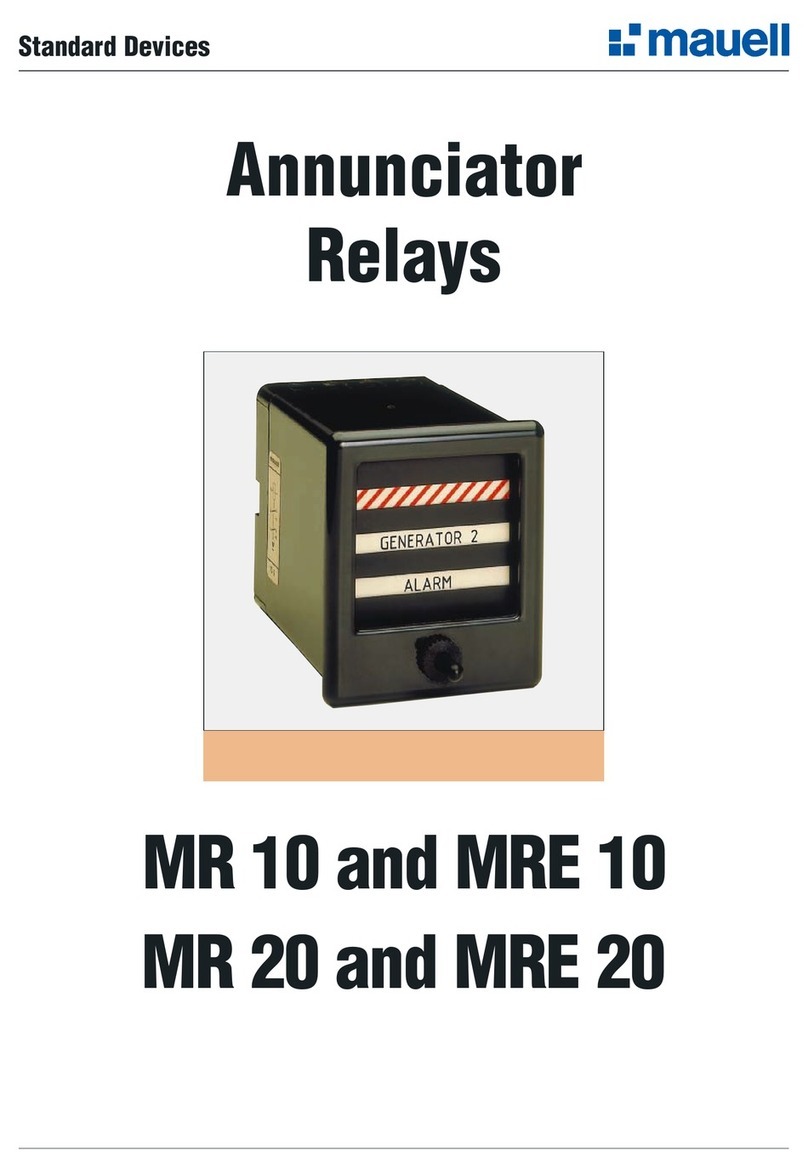
Mauell
Mauell MR 10 manual
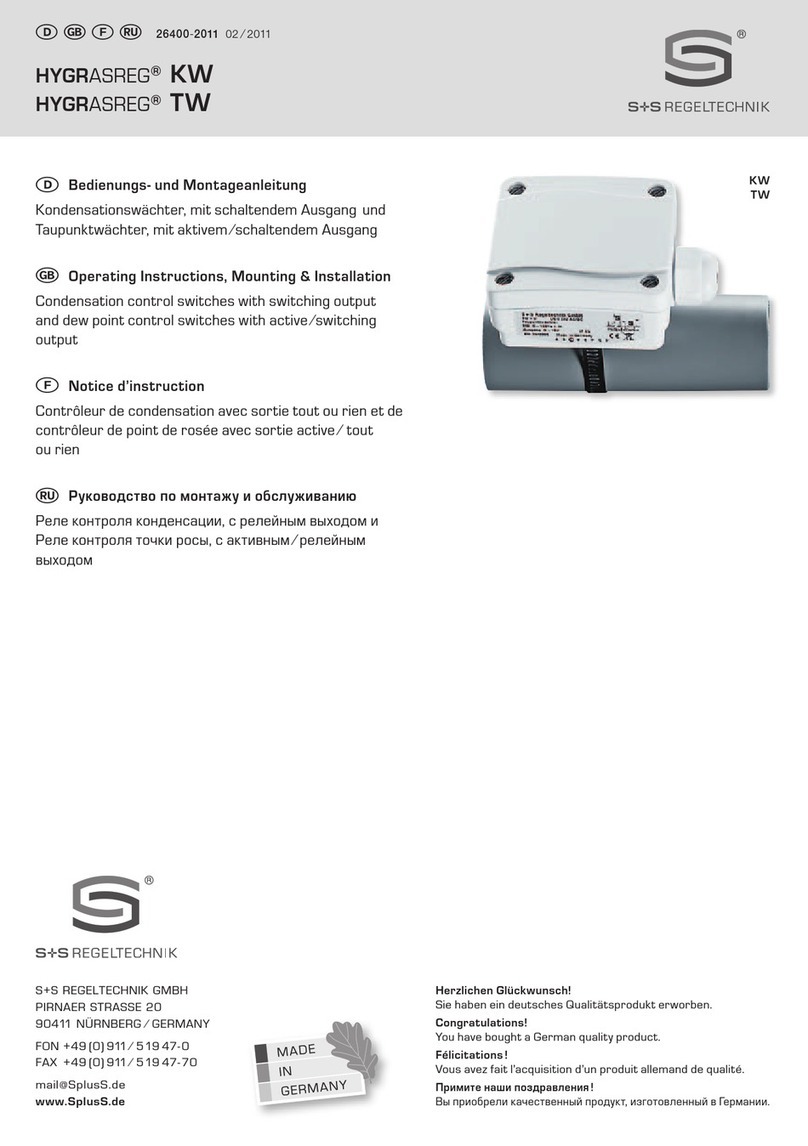
S+S Regeltechnik
S+S Regeltechnik HYGRASREG KW Operating Instructions, Mounting & Installation

Philio
Philio PAN05-1A user manual
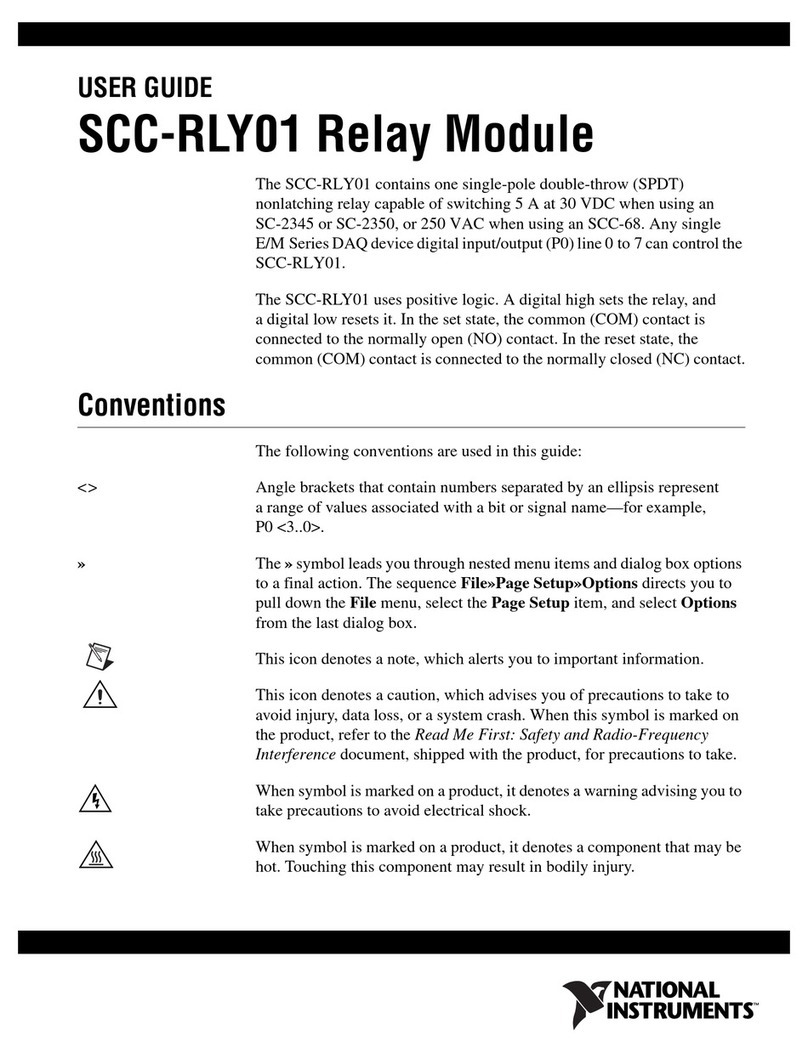
National Instruments
National Instruments Relay Module SCC-RLY01 user guide
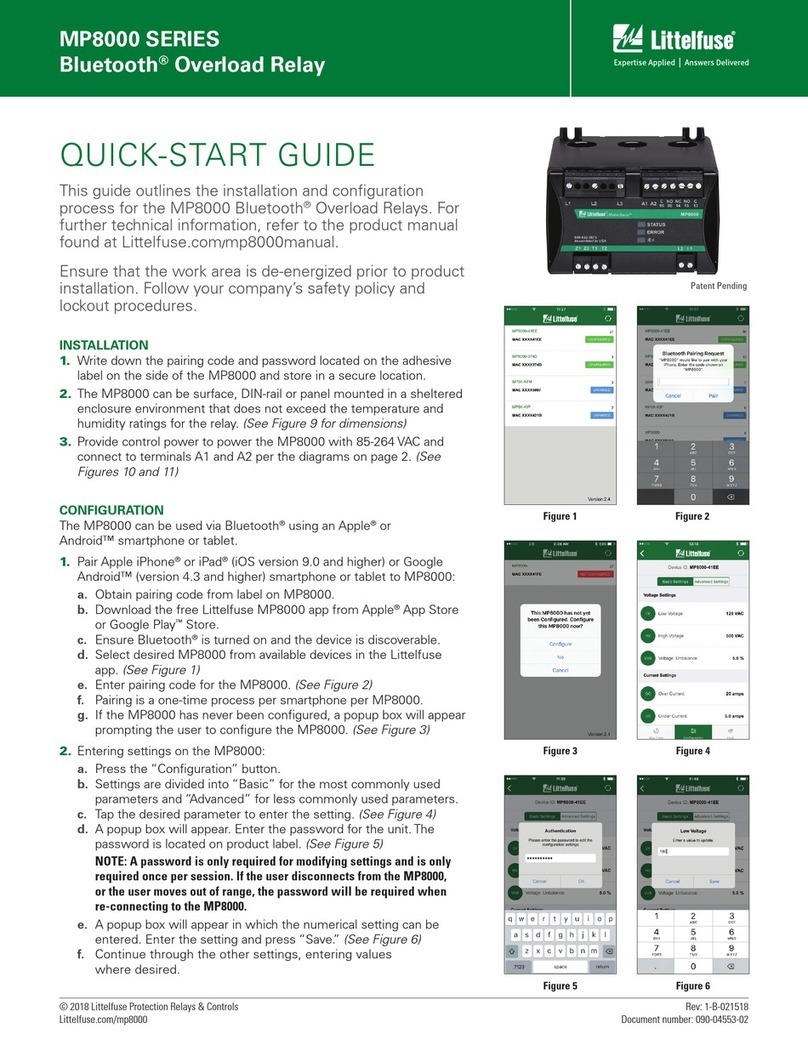
Littelfuse
Littelfuse MP8000 Series quick start guide
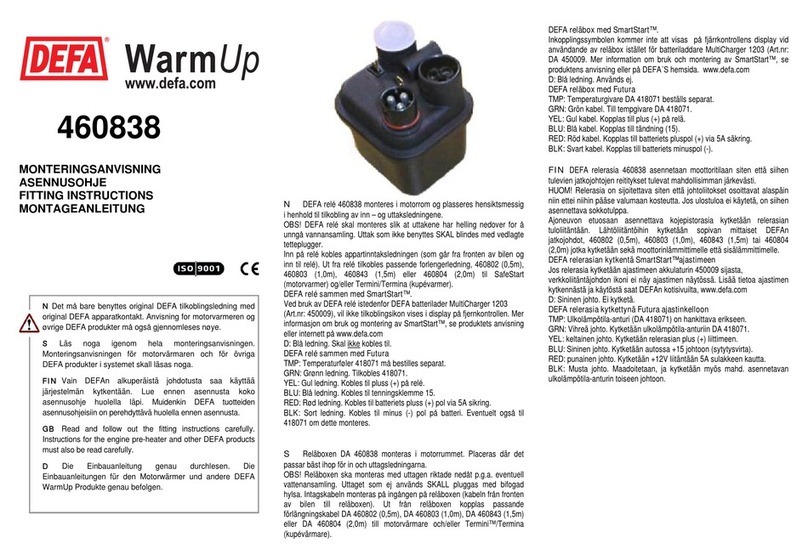
DEFA
DEFA 460838 Fitting instructions