GEA HGX22e/85-4 S CO2 User manual

HGX22e/85-4 S CO2
HGX22e/105-4 S CO2
HGX22e/130-4 S CO2
HGX34e/145-4 S CO2
HGX34e/170-4 S CO2
HGX34e/210-4 S CO2
HGX34e/255-4 S CO2
Assembly instructions
96422-07.2018-Gb
Translation of the original instructions
GEA Bock HGX22e S CO2 /HGX34e S CO2

2
D
GB
F
E
96422-07.2018-DGbFEI
About these instructions
Read these instructions before assembly and before using the compressor. This will avoid misunder-
standings and prevent damage. Improper assembly and use of the compressor can result in serious
or fatal injury.
Observe the safety instructions contained in these instructions.
These instructions must be passed onto the end customer along with the unit in which the compres-
sor is installed.
GEA Bock GmbH
72636 Frickenhausen
GEA Bock GmbH
Benzstraße 7
72636 Frickenhausen
Germany
Phone +49 7022 9454 0
Fax +49 7022 9454 137
www.gea.com
Manufacturer
Contact

D
GB
F
E
3
96422-07.2018-DGbFEI
Contents Page
1 Safety 4
1.1 Identicationofsafetyinstructions
1.2 Qualicationsrequiredofpersonnel
1.3 General safety instructions
1.4 Intended use
2 Product description 6
2.1 Short description
2.2 Name plate
2.3 Type key
3 Areas of application 8
3.1 Refrigerants
3.2 Oil charge
3.3 Limits of application
4 Compressor assembly 9
4.1 Storage and transport
4.2 Setting up
4.3 Pipe connections
4.4 Pipes
4.5 Laying suction and pressure lines
4.6 Operating the shut-off valves
4.7 Operating mode of the lockable service connections
4.8 Suctionpipelter
5 Electrical connection 12
5.1 Information for contactor and motor contactor selection
5.2 Connection of the driving motor
5.3 Circuit diagram for direct start 230 V Δ/ 400 V Y
5.4 Electronic trigger unit INT69 G
5.5 Connection of the electronic trigger unit INT69 G
5.6 Functional test of the electronic trigger unit INT69 G
5.7 Oil sump heater (accessories)
6 Commissioning 18
6.1 Preparations for start-up
6.2 Pressure strength test
6.3 Leak test
6.4 Evacuation
6.5 Refrigerant charge
6.6 Start-up
6.7 Decompression valves
6.8 Avoiding slugging
6.9 Filter dryer
6.10 Connection of oil level regulator
7 Maintenance 22
7.1 Preparation
7.2 Work to be carried out
7.3 Spare parts recommendation
7.4 Accessories
7.5 Lubricants
7.6 Decommissioning
8 Technical data 24
9 Dimensions and connections 26
10 Declaration of installation 28
11 Service 29

4
D
GB
F
E
96422-07.2018-DGbFEI
1|Safety
1.1 Identicationofsafetyinstructions:
1.2 Qualicationsrequiredofpersonnel
WARNING Inadequatelyqualiedpersonnelposestheriskofaccidents,the
consequence being serious or fatal injury. Work on compressors
must therefore only be performed by personnel with the
qualicationslistedbelow:
• For example, a refrigeration technician, refrigeration mechatronics
engineer. As well as professions with comparable training, which
enable personnel to assemble, install, maintain and repair refrigeration
and air-conditioning systems. Personnel must be capable of assessing
the work to be carried out and recognising any potential dangers.
DANGER Indicatesadangeroussituationwhich,ifnotavoided,willcause
immediatefatalorseriousinjury
WARNING Indicatesadangeroussituationwhich,ifnotavoided,maycause
fatalorseriousinjury
CAUTION Indicatesadangeroussituationwhich,ifnotavoided,may
immediatelycausefairlysevereorminorinjury.
ATTENTION Indicatesasituationwhich,ifnotavoided,maycause
property damage
INFO Importantinformationortipsonsimplifyingwork

D
GB
F
E
5
96422-07.2018-DGbFEI
1|Safety
1.3 Safety instructions
WARNING Riskofaccidents.
Refrigerating compressors are pressurised machines and as such
call for heightened caution and care in handling.
The maximum permissible overpressure must not be exceeded,
even for testing purposes.
Riskofburns!
-Dependingontheoperatingconditions,surfacetemperaturesof
over 60°C on the discharge side or below 0°C on the suction side
can be reached.
- Avoid contact with refrigerant necessarily.
Contactwithrefrigerantcancausesevereburnsandskin
damage.
Danger of suffocation.
CO2 is a non-ammable, acidic, colorless and odorless gas and
heavier than air.
NeverreleasesignicantvolumesofCO2or the entire contents of
thesystemintoclosedrooms!
Safetyinstallationsare designed or adjustedinaccordancewith
EN 378-2 or appropriate safety standards.
These assembly instructions describe the standard version of the compressor named in the title
manufactured by GEA. GEA refrigerating compressors are intended for installation in a machine
(within the EU according to the EU Directives 2006/42/EC Machinery Directive, 2014/68/EU Pressure
EquipmentDirective).
Commissioning is permissible only if the compressor has been installed in accordance with these as-
sembly instructions and the entire system into which it is integrated has been inspected and approved
in accordance with legal regulations.
The compressor is intended for use with CO2in sub-critical systems in compliance with the limits of
application.
Onlytherefrigerantspeciedintheseinstructionsmaybeused.
Anyotheruseofthecompressorisprohibited!
1.4 Intended use
WARNING The compressor may not be used in potentially explosive
environments!

6
D
GB
F
E
96422-07.2018-DGbFEI
• HGX22e S CO2:Semi-hermetic two-cylinder reciprocating compressor with suction gas cooled
drive motor.
• HGX34e S CO2:Semi-hermetic four-cylinder reciprocating compressor with suction gas cooled
drive motor.
• Theowofrefrigerantsuckedinfromtheevaporatorisledovertheengineandprovidesfora
particularly intensive cooling. Thus the engine can be kept special during high load on a relatively
low temperature level.
• Oil pump independent of direction of rotation for reliable and safe oil supply
• One pressure relief valve each on the low and high pressure side, which vent into the
atmosphere when these inadmissibly high printing pressures are reached.
2|Product description
Name plate
2.1 Short description
Oil sight glass
Cylinder cover
Discharge shut-
off valve
Oil pump
Suction
shut-off valve
Drive section
Motor section
Dimension and connection values can be found in Chapter 9
Transport eyelet
Terminal box
Fig. 1 HGX22e S CO2
HGX34e S CO2
Fig. 2
Pressure relief valve
(ND)
Pressure relief
valve (HD)
Valve plate

D
GB
F
E
7
96422-07.2018-DGbFEI
1
2
3
4
513
12
7
11
6
10
8
9
40/55
AX34567A045
C85E
44,8/25,9A
Δ:178AY:103A
GEA Bock GmbH
72636 Frickenhausen, Germany
HGX34e/255-4 S CO2
22,3
26,8
IP66
2|Product description
1 Type designation
2 Machine number
3 maximum operating current
4 Starting current (rotor blocked)
5 ND (LP): max. permissible operating
pressure (g) Low pressure side
HD (HP):
max. permissible operating
pressur
e(g) High pressure side
50 Hz
60 Hz
6 Voltage,circuit,frequency
7 Nominal rotation speed
8 Displacement
9 Voltage,circuit,frequency
10 Nominal rotation speed
11 Displacement
12 Oiltypelledatthefactory
13 Terminal box protection type
}
}
Fig. 3
2.2 Name plate (example)
Observe the limits of
applicationdiagrams!
Electrical accessories can change
theIPprotectionclass!
/
HG 43 e 255- 4 CO2
XS
2.3 Typekey (example)
¹) HG - Hermetic Gas-Cooled (suction gas-cooled)
²) X - Ester oil charge
³) S - More powerful motor
CO2version
Motor variant ³)
Number of poles
Swept volume
e-series
Numbers of cylinders
Size
Oil charge ²)
Series ¹)

8
D
GB
F
E
96422-07.2018-DGbFEI
ATTENTION Property damage possible.
The oil level must be in the
visible part of the sight
glass; damage to the com-
pressor is possible if overfil-
ledorunderfilled!
-50 -45 -40 -35 -30 -25
-15
-20
-5
-10
5
0
t (°C)
C
-20
10
15
t (°C)
O
-15
?t = 10 K
Oh
R744
Fig. 5
Fig. 4Fig. 4
HGX22e S CO2
0,5 Ltr.
HGX34e S CO2
0,7 Ltr.
~
~
~
~
Max. permissible operating
pressure (LP/HP)1):40/55bar
Unlimited
application range
Evaporation temperature (°C)
Condensing temperature (°C)
Suction gas superheat (K)
Suction gas temperature (°C)
1) LP = Low pressure
HP = High pressure
3|Areas of application
max.
min.
oil level
ATTENTION Compressor operation is possible within the operating limits
showninthediagrams.Pleasenotethesignicanceoftheshaded
areas. Thresholds should not be selected as design or continuous
operation points.
- Permissible ambient temperature (-20°C) - (+60°C).
- Max. permissible discharge end temperature 160°C.
- Min. oil temperature ≥30°C.
- Min. pressure gas temperature ≥50°C.
-Max.permissibleswitchingfrequency8x/h.
- A minimum running time of 3 min. steady-state condition
(continuous operation) must be achieved.
Foroperationwithfrequencyconverter:
-Frequencyrange25-70Hz
- The maximum current and power consumption must not be
exceeded.Inthecaseofoperationabovethemainsfrequency,
the application limit can therefore be limited.
3.3 Limits of application
Thecompressorsarelledatthefactorywiththefollowingoiltype:
GEA C 85 E (only this oils may be used)
3.1 Refrigerants
• CO2: R744(RecommendationCO2quality4.5(<5ppmH2O))
3.2 Oil charge

D
GB
F
E
9
96422-07.2018-DGbFEI
Setuponanevensurfaceorframewithsufcientload-bearing
capacity. Only erect on a slant in consultation with the manufacturer.
Single compressor preferably on vibration damper.
Duplex and parallel circuits always rigid.
Provideadequateclearanceformaintenancework.
Ensureadequatecompressorventilation.
Do not use in a corrosive, dusty, damp atmosphere or a combustible
environment.
F
E
D
C
B
A
1
2
3
4
F
E
D
C
4
3
2
1
A
B
Tol.-Ang. DIN ISO 2768-mK
Ra Rz
Maß
Passung
Freigabe
Alternativbezug:
Baumustergeprüft
Teil inaktiv
Lieferantenzeichnung
-
-
K.-Auftrag:
PL:
Zeichnung ungültig
Entwicklungsstand
Teil keine Serie
120
400
±0.5
über 0.5
bis 6
Benzstraße 7 - 72636 Frickenhausen - Germany - www.bock.de
-
-
Unbemaßte Radien:
-
Diese Zeichnung ist unser Eigentum!
Sie darf ohne unsere Genehmigung weder nach-
gebildet, vervielfältigt, oder Dritten Personen zu-
gänglich gemacht werden. Der Nachbau nach
dieser Zeichnung, oder an Hand der nach dieser
Zeichnung hergestellten Gegenstände durch den
Abnehmer oder Dritte ist nicht gestattet.
Wir behalten uns alle Rechte, gemäß DIN ISO 16016
an dieser Zeichnung vor.
Bearb.
Datum
Änderungs-Nr.
Werkstoff:
Ausgangsteil, bzw. Rohteil:
--
Gepr.
Name
Datum
19.04.
Werkstückkanten
DIN ISO 13715
Ersatz für:
Ersetzt durch:
Erstellt
2010
Geprüft
-
Kurz
Zone
1/x
Oberflächenbehandlung / Härte:
-
Blatt:
Änderungsbeschreibung
400
Benennung:
±0.8
1000
30
6
-
±0.3
120
30
±0.2
Zeichn.-Nr. Teile-Nr.
Oberflächenangaben ISO 1302
x.xxxx-xxxxx.x
Zust.
Gußtoleranzen:
Gewicht: (kg)
±0.1
Maßstab:
1:1
Wasserwaage
für Indesign
Der Lieferant muß sicherstellen, dass die Ware in
einwandfreiem Zustand angeliefert wird (Korrosions-
schutz, Verpackung für sicheren Transport).
Rz 25
Rz 160
s
25
z
y
x
w
u
t
0,05
Rz 1,6
0,3
0,7
1,6
2
Rz 16
6,3
Rz 63
Rz 6,3
Rz 12,5
F:\user\kurz\3D Sachen\3D Teile\Zeichnungen\Wasserwaage
?
Use transport eyelet.
Do not lift manually!
Use lifting gear!
Storage at (-30°C) - (+70°C), maximum permissible relative humidity
10% -95 %, no condensation.
Do not store in a corrosive, dusty, vaporous atmosphere or in a com-
bustible environment.
Sun protection: If the compressor is set up outdoors, it has to be
protected from direct sunlight.
4.3 Pipe connections
ATTENTION Damage possible.
Superheating can damage the valve.
Remove the pipe supports therefore from the valve for soldering
and accordingly cool the valve body during and after soldering.
Only solder using inert gas to inhibit oxidation products (scale).
4|Compressor assembly
4.2 Setting up
INFO New compressors are factory-lled with inert gas. Leave this
service charge in the compressor for as long as possible and pre-
venttheingressofair.Checkthecompressorfortransportdamage
beforestartinganywork.
4.1 Storage and transportation
ATTENTION Attachments(e.g.pipeholders,additionalunits,fasteningparts,
etc.)directlytothecompressorarenotpermissible!

10
D
GB
F
E
96422-07.2018-DGbFEI
4|Compressor assembly
Fig. 7
Rigid
fixed point As short as
possible
4.4 Pipes
Pipes and system components must be clean and dry inside and free of scale, swarf and layers of
rust and phosphate. Only use air-tight parts.
Lay pipes correctly. Suitable vibration compensators must be provided to prevent pipes being
cracked and broken by severe vibrations.
Ensure a proper oil return.
Keep pressure losses to an absolute minimum.
The pipe connections have graduated inside diameters so that pipes
with standart millimetre and inch dimensions can be used.
The connection diameters of the shut-off valves are rated for maximum
compressor output. Theactualrequiredpipecrosssectionmustbe
matched to the output. The same applies for non-return valves.
Fig. 6: graduated
internal diameter
4.5 Laying suction and pressure lines
Aruleofthumb:Alwayslaytherstpipesectionstartingfromtheshut-offvalve downwards and
parallel to the drive shaft.
INFO Proper layout of the suction and discharge lines directly after the
compressor is integral to the system’s smooth running and
vibration behaviour.
ATTENTION Property damage possible.
Improperlyinstalledpipescancausecracksandtears,theresult
being a loss of refrigerant.

D
GB
F
E
11
96422-07.2018-DGbFEI
Valve spindle seal
Release
Tighten
4|Compressor assembly
4.6 Operating the shut-off valves
Before opening or closing the shut-off valve, release the valve spindle seal by approx. ¼ of a turn
counter-clockwise.
After activating the shut-off valve, re-tighten the adjustable valve spindle seal clockwise.
Fig. 8 Fig. 9
Pipe connection
Pipe connection
4.7 Operatingmodeofthelockableserviceconnections
Fig. 10
Openingtheshut-offvalve:
Spindle: turn to the left (counter-clockwise) as far as it will go.
—> Shut-off valve completely opened / service connection closed.
Fig. 11
Opening the service connection
Spindle: Turn ½ - 1 turn to the right clockwise.
—> Service connection opened / shut-off valve opened.
Connection
blocked
Spindle
Spindle Connection
open
Compressor
Compressor
Service connection
closed
Service connection
opened
Afteractivatingthespindle,generallytthespindleprotectioncapagainandtightenwith14-16Nm.
This serves as a second sealing feature during operation.

12
D
GB
F
E
96422-07.2018-DGbFEI
5|Electrical connection
5 Electrical connection
INFO Connect the compressor motor in accordance with the circuit diagram
(see inside of terminal box).
Use suitable cable entry point of the correct protection type (see
name plate) for routing cables into the terminal box. Insert the strain
reliefs and prevent chafe marks on the cables.
Comparethevoltageandfrequencyvalueswiththedataforthe
mains power supply.
Only connect the motor if these values are the same.
DANGER Riskofelectricshock!Highvoltage!
Onlycarryoutworkwhentheelectricalsystemisdisconnected
fromthepowersupply!
5.1 Information for contactor and motor contactor selection
All protection equipment, switching and monitoring devices must comply with the local safety
regulationsandestablishedspecications(e.g.VDE)aswellasthemanufacturer’sspecications.
Motorprotectionswitchesarerequired! Motor contactors, feed lines, fuses and motor protection
switches must be rated according to the maximum operating current (see name plate). For motor
protection, use a current-independent, time-delayed overload protection device for monitoring all
three phases. Adjust the overload protection device so that it must be actuated within 2 hours at 1.2
times the maximum working current.
ATTENTION When attaching accessories with an electrical cable, a minimum
bending radius of 3 x the cable diameter must be maintained for
laying the cable.
For systems with long pipes and higher degree of contamination, a lter on the suction-side is
recommended.Thelterhastobebereneweddependingonthedegreeofcontamination(reduced
pressure loss).
4.8Suctionpipelter
4|Compressor assembly

D
GB
F
E
13
96422-07.2018-DGbFEI
Designation on the name plate Sticker on the terminal box
∆/Y
230 V ∆
Direct start Star-delta start
400VY
Direct start only
Elektrischer Anschluss
Electrical connection
Raccordement électrique ∆/ Y
96027-11.06-DGbF
∆
Niedere Spannung
Low voltage
Bas voltage
Y
Hohe Spannung
High voltage
Haut voltage
L3
L1 L2
L3
L1 L2
Elektrischer Anschluss
Electrical connection
Raccordement électrique ∆/ Y
96027-11.06-DGbF
∆
Niedere Spannung
Low voltage
Bas voltage
Y
Hohe Spannung
High voltage
Haut voltage
L3
L1 L2
L3
L1 L2
L1 L2 L3
L1 L2 L3
5.2 Connection of the driving motor
The compressor is designed with a motor for star-delta circuits.
Star-delta start-up is only possible on 230 V voltage supply. Example:
5|Electrical connection
INFO The connection examples shown refer to the standard version. In
thecaseofspecialvoltages,theinstructionsaffixedtotheterminal
box apply.

14
D
GB
F
E
96422-07.2018-DGbFEI
Anschlußkasten Verdichter
BT1
INT69G
QA1
L1 L2 L3 N PE PE
FC1.1
FC2
SF1
BP1
P>
QA2
BP2
P
QA2
L1.1
L2.1
L3.1
L1.2
N
PE
BT3
1112 14
L N B1 B2
12
11
10
9
8
7
6
5
4
3
2
1
BT2
Θ
BT2
Θ
FC1.1
I> I>
I>
1
2
QA2
3
4
5
6
-EC1 3~
M
Θ
EB1
5.3 Circuit diagramm for direct start 230 V ∆/400VY
Fig. 12
BP2 High pressure safety controller
BP3 Safety chain (high/low pressure monitoring)
BT2 Thermal protection thermostat (PTC sensor)
BT3 Release switch (thermostat/pressostat)
EB1 Oil sump heater
EC1 Compressor motor
Compressor terminal box

D
GB
F
E
15
96422-07.2018-DGbFEI
Anschlußkasten Verdichter
BT1
INT69G
QA1
L1 L2 L3 N PE PE
FC1.1
FC2
SF1
BP1
P>
QA2
BP2
P
QA2
L1.1
L2.1
L3.1
L1.2
N
PE
BT3
1112 14
L N B1 B2
12
11
10
9
8
7
6
5
4
3
2
1
BT2
Θ
BT2
Θ
FC1.1
I> I>
I>
1
2
QA2
3
4
5
6
-EC1 3~
M
Θ
EB1
FC1.1 Motor protection switch
FC2 Control power circuit fuse
INT69 G Electronic trigger unit INT69 G
QA1 Main switch
QA2 Mains contactor
SF1 Control voltage switch

16
D
GB
F
E
96422-07.2018-DGbFEI
5.4 Electronic trigger unit INT69 G
5.5 Connection of the trigger unit INT69 G
The compressor motor is tted with cold conductor temperature sensors (PTC) connected to the
electronic trigger unit INT69 G in the terminal box. In case of excess temperature in the motor
winding, the INT69 G deactivates the motor contactor. Once cooled, it can be restarted only if the
electronic lock of the output relay (terminals B1+B2) is released by interrupting the supply voltage.
The hot gas side of the compressor can also be protected against overtemperature using thermal
protection thermostats (accessory).
The unit trips when an overload or inadmissible operating conditions occur. Find and remedy
the cause.
INFO Therelayswitchingoutputisexecutedas a oating changeover
contact.Thiselectricalcircuitoperatesaccordingtothequiescent
currentprinciple,i.e.the relay drops into a theidlepositionand
deactivatesthemotorcontactorevenincaseofasensorbreakor
open circuit.
INFO Connect the trigger unit INT69 G in accordance with the circuit dia-
gram. Protect the trigger unit with a delayed-action fuse (FC2) of
max.4A.Inordertoguaranteetheprotectionfunction,installthe
triggerunitastherstelementinthecontrolpowercircuit.
Οnderung
Klebeschilder
0
Datum Name
Datum
Bearb.
Gepr.
Norm
1
04.12.2009
Kelich
22.05.2015
Urspr.
2
Ers. f.
3
Ers. d.
4
Schaltplan
567
BOCK COMPRESSORS
8
=
+
9
Bl.
MP10 INt69 Bl.
MP10 INt69
INT69 G
Motor Protection MP10
Steuerstrom-
kreis
L
N
Steuerstrom-
kreis
L N
1112 14
B1 B2OG OG
+
-
BT1
Θ
X1 L1 L1 N N 43 43 11 12 14
L S M
X2123456
R1 R2
+
-
BT1
Θ
+
-
BT2
Θ
+
-
BT2
Θ
L
N
5|Electrical connection
Terminal box
Fig. 13
ATTENTION
Measure circuit BT1 and BT2
(PTC sensor) must not come
into contact with external
voltage.
This would destroy the trigger
unit INT69 G and PTC sensors.
Control circuit

D
GB
F
E
17
96422-07.2018-DGbFEI
5.7 Oil sump heater (accessories)
Inordertoavoiddamagetothecompressor,thecompressormustbeequippedwithanoilsumpheater.
Connexion:The oil sump heater must be connected via an auxiliary contact (or parallel wired auxiliary
contact) of the compressor contactor to a seperate electric circuit.
Electrical data: 110 - 240 V - 1 - 50/60 Hz, 50 - 120 W, PTC-heater adjusting.
ATTENTION Theoilsumpheatermustgenerallybeconnectedandoperated!
Relay position INT69 G
B2 12 14 11
Fig. 14
5.6 Function test of the trigger unit INT69 G
Before commissioning, after troubleshooting or making changes to the control power circuit, check
the functionality of the trigger unit. Perform this check using a continuity tester or gauge.
5|Electrical connection
Gauge state Relay position
1. Deactivated state 11-12
2. INT69 G switch-on 11-14
3. Remove PTC connector 11-12
4. Insert PTC connector 11-12
5. Reset after mains on 11-14

18
D
GB
F
E
96422-07.2018-DGbFEI
6|Commissioning
WARNING When the compressor is not running, depending on ambient
temperature and amount of refrigerant charge, it is possible
that the pressure may rise and exceed permitted levels for the
compressor.Adequateprecautions mustbetakentopreventthis
happening (e.g. using a cold storage medium, a receiver tank, a
secondaryrefrigerantsystem,orpressurereliefdevices).
6.1 Preparations for start-up
The compressor has undergone trials in the factory and all functions have been tested. There are
therefore no special running-in instructions.
Checkthecompressorfortransportdamage!
INFO Toprotectthecompressoragainstinadmissibleoperatingconditions,
high pressure and low pressure pressostats are mandatory on the
installation side.
6.3 Leaktest
Carry out the leak test on the refrigerating plant in accordance with EN 378-2 or a corresponding
safety standard, while always observing the maximum permissible overpressure for the compressor.
DANGER Riskofbursting!
The compressor must only be pressurised using nitrogen (N2).
Never pressurisewithoxygenorothergases!
The maximum permissible overpressure of the compressor must
not be exceeded at any time during the testing process (see name
platedata)! Do not mix any refrigerant with the nitrogen as this
could cause the ignition limit to shift into the critical range.
6.2 Pressure strength test
The compressor has been tested in the factory for pressure integrity. If however the entire system is
to be subjected to a pressure integrity test, this should be carried out in accordance with EN 378-2
or a corresponding safety standard without the inclusion of the compressor.

D
GB
F
E
19
96422-07.2018-DGbFEI
6|Commissioning
First evacuate the system and then include the compressor in the evacuation process.
Relieve the compressor pressure.
Open the suction and pressure line shut-off valves.
Turn on the oil sump heater.
Evacuate the suction and discharge pressure sides using the vacuum pump.
At the end of the evacuation process, the vacuum should be < 1.5 mbar when the pump is switched off.
Repeatthisprocessasoftenasisrequired.
Make sure that the suction and pressure line shut-off valves are open.
6.5 Refrigerant charge
Fillingtheliquidrefrigerant:Itisrecommendedthatthesystemrstbelled
at standstill with gas on the high-pressure side up to a system pressure of at
least5.2bar(ifitislledbelow5.2barwithliquid,thereisariskofdryice
formation).Furtherllingaccordingtosystem.
To eliminate the possibility of dry ice formation when the system is operating
(duringand after thellingprocess),the shut-off point ofthe low-pressure
switch should be set to a value of at least 5.2 bar.
•Arefrigerantsupplement,whichmaybecomenecessaryafterstart-up,canbe
topped up in vapour form on the suction side.
ATTENTION Avoid overfilling the machine with refrigerant!
Donotchargeliquidrefrigerantintothesuction-sideonthe
compressor.
Do not mix additives with the oil and refrigerant.
CAUTION Wear personal protective clothing such as goggles and protective
gloves!
WARNING Never exceed the max. permissible pressures while charging.
Precautionsmustbetakenintime.
INFO Depending upon design of the CO2refrigerantllingbottle(with/
without tubing) CO2canbelledinliquidafterweightorgase-
ously.
Use only high-dried CO2quality(see chapter 3.1)!
6.4 Evacuation
ATTENTION Do not start the compressor if it is under vacuum. Do not apply
any voltage - even for test purposes (must only be operated with
refrigerant).
Under vacuum, the spark-over and creepage current distances of the
terminal board connection bolts shorten; this can result in winding and
terminal board damage.

20
D
GB
F
E
96422-07.2018-DGbFEI
CO2 streaming
out
Fig. 15
6|Commissioning
Check that the safety and protection devices (pressure switch, motor protection, electrical contact
protection measures, etc.) are functioning properly.
Switch on the compressor and let it run for at least 10 minutes.
Themachineshouldreachastateofequilibrium.
Check the oil level: The oil level must be visible in the sight glass.
After a compressor is replaced, the oil level must be checked again. If the level is too high, oil
mustbedrainedoff(dangerofoilliquidshocks;reducedcapacityoftherefrigeratingsystem).
WARNING Ensure that both shut-off valves are open before starting the
compressor!
ATTENTION Iflargerquantitiesofoilhavetobetoppedup,thereisariskofoil
impacteffects.Ifthisisthecase,checktheoilreturn!
6.6 Start-up
6.7 Decompression valves
ATTENTION Thecompressoristtedwithtwodecompressionvalves.Onevalve
each on the suction and discharge side. If excessive pressures are
reached,thevalvesopenandpreventfurtherpressureincrease.
Thereby CO2isblownofftotheambient!
Intheeventthatapressurereliefvalveactivatesrepeatedly,check
valve and replace if necessary as during blow-off extreme condi-
tionscan occure,whichmayresult in apermanentleak.Always
checksystemforrefrigerantlossafteractivationofpressurerelief
valve!
The decompression valves do not replace any pressure switches
and the additional safety valves in the system. Pressure switches
mustalwaysbeinstalledinthesystemanddesignedoradjustedin
accordance with EN 378-2 or appropriate safety standards.
FailuretoobservecanresultinriskofinjuryfromCO2streaming
outofthetwodecompressionvalves!
This manual suits for next models
6
Table of contents
Other GEA Compressor manuals

GEA
GEA Bock FK50 Series User manual
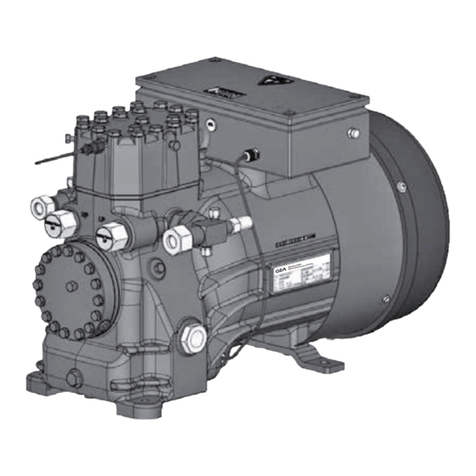
GEA
GEA HAX2 CO2 T User manual
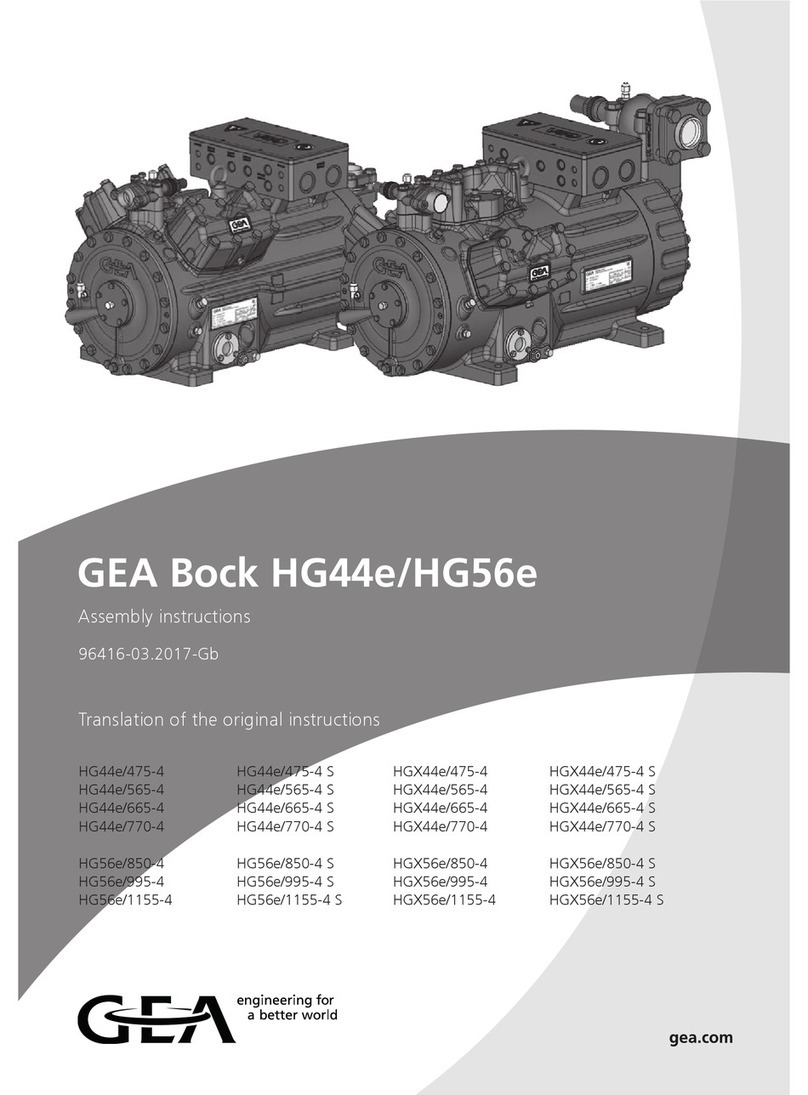
GEA
GEA HG44e/475-4 S User manual
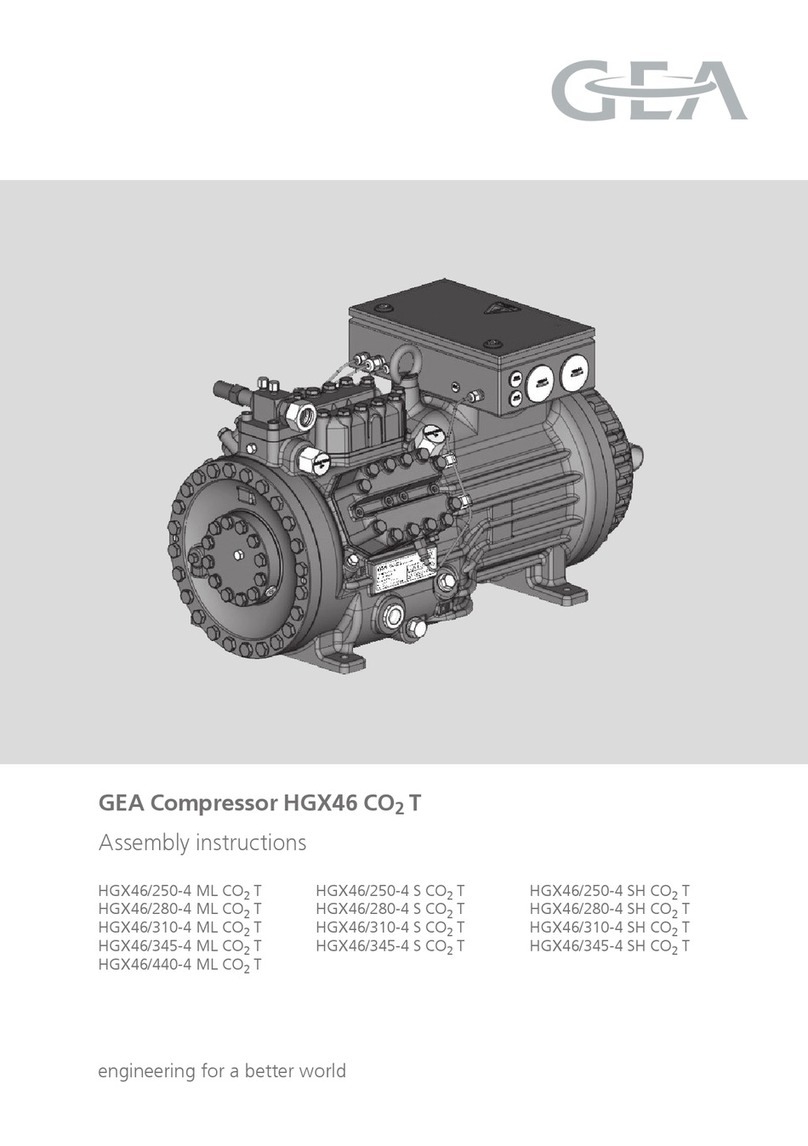
GEA
GEA HGX46/250-4 S CO2T User manual
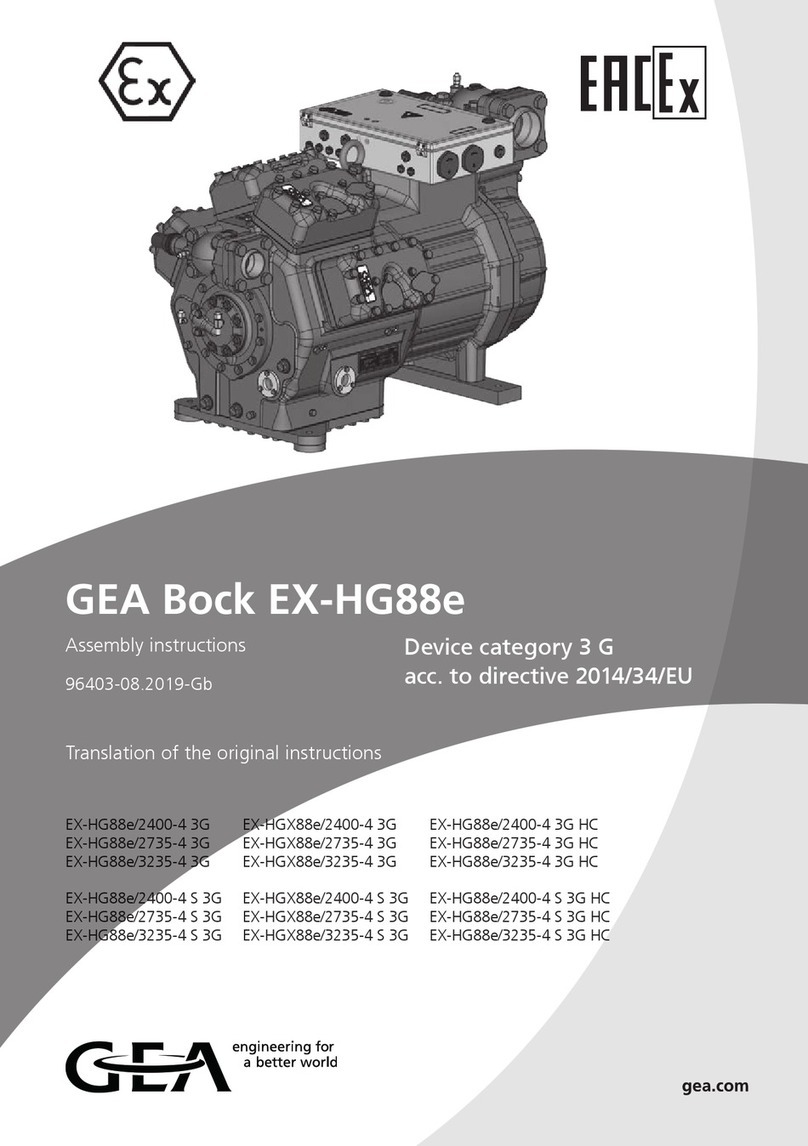
GEA
GEA Bock EX-HG88e Series User manual
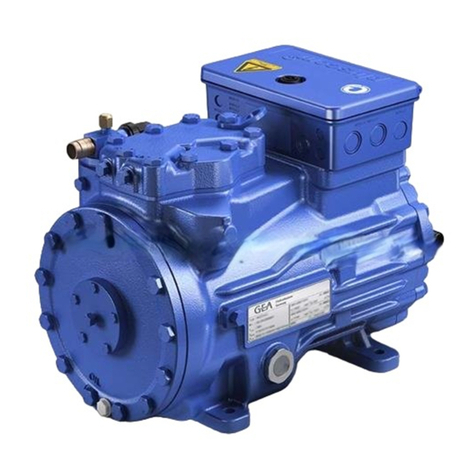
GEA
GEA HG22e Series User manual
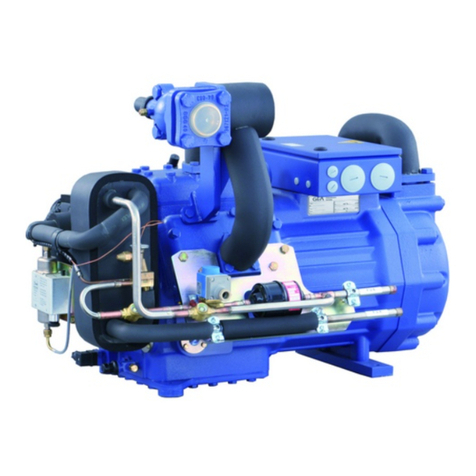
GEA
GEA HGZ7 Series User manual

GEA
GEA InTouch HAX12P/60-4 User manual
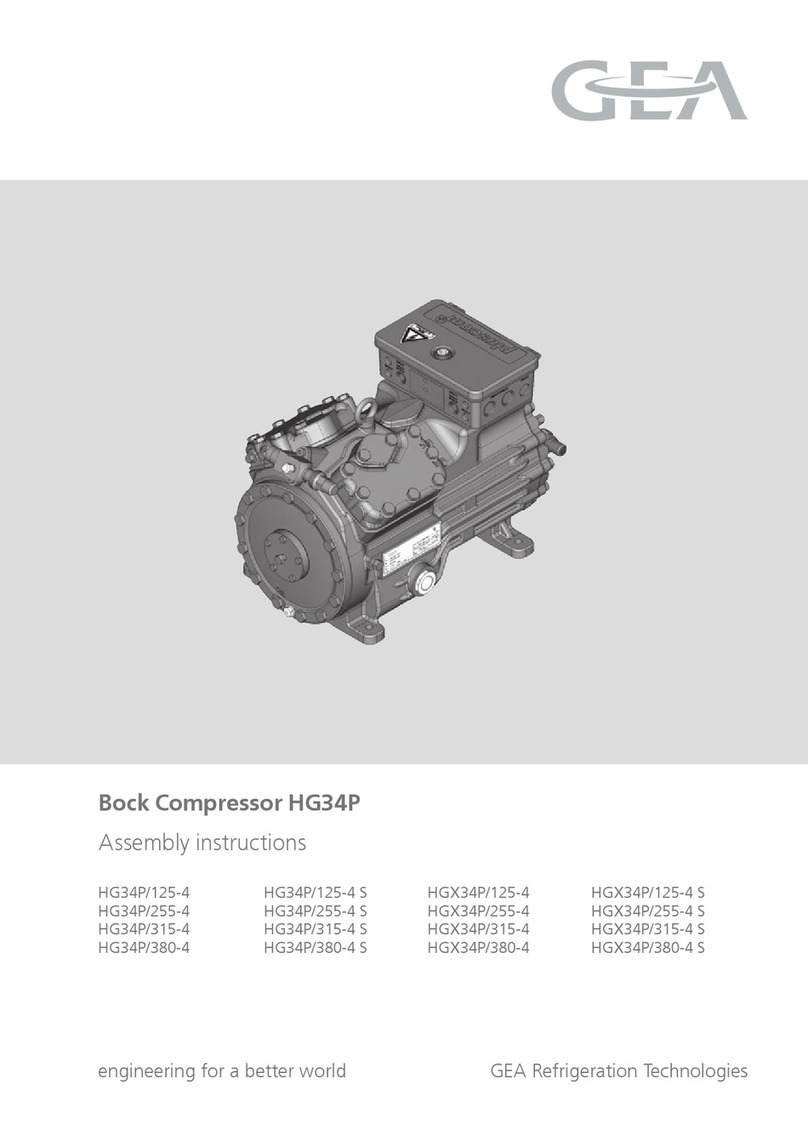
GEA
GEA HG34P Series User manual
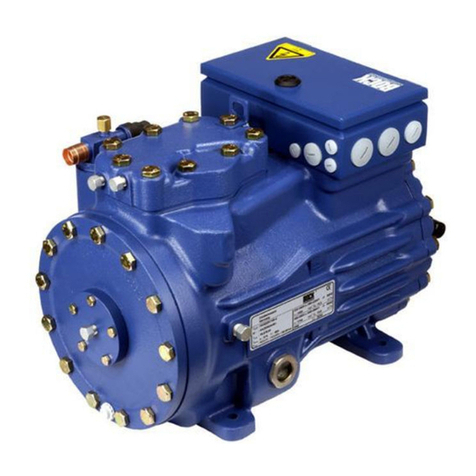
GEA
GEA HG Series User manual
Popular Compressor manuals by other brands
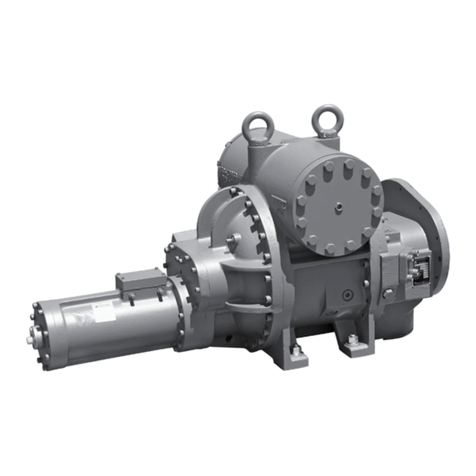
Frick
Frick SGC 1913 Installation
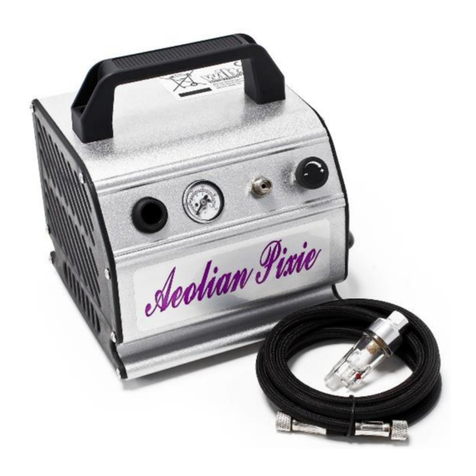
WilTec
WilTec AS-176 instruction manual

Scheppach
Scheppach HC550TC-230V Translation of original instruction manual
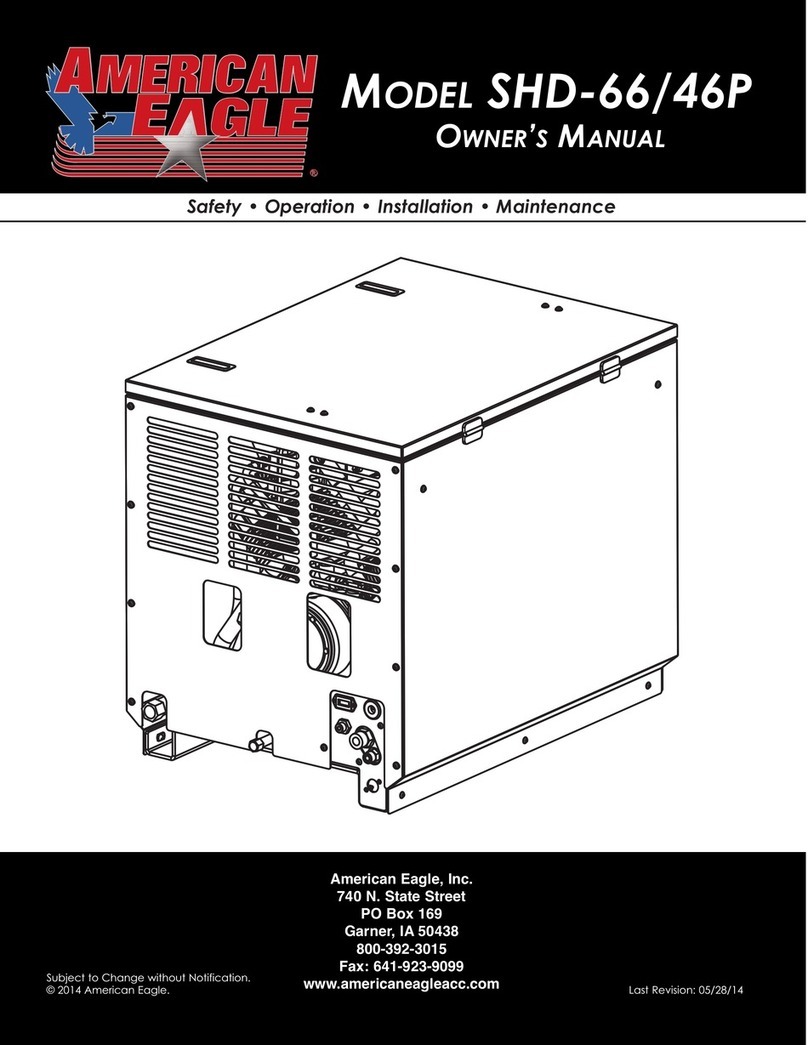
American Eagle
American Eagle SHD-66 owner's manual

Ingersoll-Rand
Ingersoll-Rand HP375WJD Operating, Maintenance & Parts Manual

Secoh
Secoh EL-60 Periodic Maintenance Procedure