GEA T.VIS A-15 User manual

Control and feedback systems
GEA T.VIS® A-15
Operating instruction (Translation from the original language)
430BAL010699EN_9

COPYRIGHT
These Operating Instructions are the English translation of the original operating
instructions in the sense of the EU Machinery Directive. This document is
protected by copyright. All rights reserved. The document may not, in whole or in
part, be copied, reproduced, translated or reduced to an electronic medium of
machine-readable form without the express permission of GEA Tuchenhagen
GmbH.
LEGAL NOTICE
Word marks
The designations T.VIS®, VARIVENT®, ECOVENT®, STERICOM®, VESTA® und
LEFF® are protected trademarks of GEA Tuchenhagen GmbH.
430BAL010699EN_9
2 11.01.2024

TABLE OF CONTENTS
1 General Information 7
1.1 Information on the Document 7
1.1.1 Binding Character of These Operating Instructions 7
1.1.2 Notes on the Illustrations 7
1.1.3 Symbols and Highlighting 7
1.2 Manufacturer address 8
1.3 Contact 8
1.4 EU Declaration of Conformity 9
1.5 Translated copy of the EU Declaration of Conformity 10
1.6 UK Declaration 11
1.7 Translated copy of the UK Declaration of Conformity according to the provisions on electromagnetic
compatibility from 2016 12
2 Safety 13
2.1 Intended use 13
2.1.1 Requirements for operation 13
2.1.2 Improper operating conditions 13
2.2 Operator’s Duty of Care 13
2.3 Subsequent changes 14
2.4 IP Protection classes 15
2.5 General safety instructions and dangers 15
2.5.1 Principles for safe operation 15
2.5.2 Environmental Protection 16
2.5.3 Electrical Equipment 16
2.6 Supplementary Regulations 16
2.7 Qualification of personnel 17
2.8 Safety equipment 18
2.8.1 Signs 18
2.9 Residual dangers 19
2.9.1 Electrostatically Endangered Components and Modules 19
2.10 Danger zones 19
3 Description 21
3.1 Functional description 21
3.1.1 Operation Principle 21
3.1.2 Control top without solenoid valves 21
3.1.3 Control Top with Solenoid Valves 21
3.1.4 Control Top with Cap Including Buttons 22
3.1.5 Control top with hood without buttons 23
3.1.6 Function of the Buttons 23
3.1.7 Safety Air Exhaust/Installation Position 24
4 Transport and storage 25
4.1 Storage conditions 25
4.2 Transport 25
4.2.1 Scope of supply 25
5 Technical data 26
5.1 Type plate 26
5.2 Technical data 29
5.3 Specifications for 24V DC version 31
5.4 IO-Link specifications 31
5.5 Specifications for AS-interface 36
5.6 DeviceNet specifications 38
5.7 Accessories 43
5.8 Tool 44
5.9 Lubricants 44
5.10 Equipment 44
6 Assembly and installation 46
6.1 Safety instructions 46
6.2 Establishing Hose Connections 46
6.3 Pneumatic connections 46
6.3.1 Control Top with 1 Solenoid Valve or Without Solenoid Valve 47
6.3.2 Control Top with 2 Solenoid Valves – for Lifting the Valve Disk 48
430BAL010699EN_9
11.01.2024 3

6.3.3 Control top with 2 solenoid valves – for lifting the double-disk, for the external air connection of an air/air
actuator or for the main stroke of an external process valve 49
6.3.4 Control top with 2 solenoid valves- for spreader lift of the double-disk 50
6.3.5 Control top with 3 solenoid valves for lifting the valve disk and double-disk 51
6.3.6 Control top with 3 pilot valves - to lift the double-disk and to spread lift the double-disk 53
6.3.7 Control top with 4 pilot valves for the lift of the valve disk and of the double-disk and for the spread lift of
the double-disk 54
6.4 Electrical connections 55
6.4.1 Overview 56
6.4.2 Electrical 24 V DC Wiring 57
Plug M12 / 5-pin (24.1) 57
Connector M12 / 8-pin (24.1) 58
Connector M12/12-pin / 9-strand 59
Cable gland (24) 60
6.4.3 Electrical 24 V DC Wiring 60
Plug M12 / 5-pin (24.1) 60
6.4.4 Electrical Wiring of AS-Interface 61
Plug M12 / 5-pin (24.1) 61
6.4.5 Electrical DeviceNet Wiring 61
Plug M12 / 5-pin (24.1) 62
External Proximity Switch (170) 62
6.5 Visual Display 63
6.5.1 Illuminated dome 63
6.5.2 Colour Changeover 64
6.5.3 Connection diagram for T.VIS circuit board (bottom) 65
6.6 Mounting the control top to different valves 67
6.6.1 Mounting to a VARIVENT Valve 67
6.6.2 Fitting to FLOWVENT Valve 68
6.6.3 Installation on VARIVENT mixproof valves with Lifting Actuator Type R, T_R, M/2.0, M_0(06), MT/T_R(08),
MX, MT, MT_DA 70
6.6.4 Mounting to a Butterfly Valve T-smart 8000 71
6.6.5 Mounting to a Butterfly Valve T-smart 7 and a Mixproof Butterfly Valve T-smart 9 72
6.6.6 Mounting to ECOVENT Valves N_ECO and W_ECO 73
6.6.7 Mounting to VESTA Valve H_A/M 74
6.6.8 Mounting to VESTA Valve H_A 75
6.6.9 Mounting to Valve N_/E or W_/E or STERICOM Valve 76
6.6.10 Mounting to a T-smart Single-Seat and Double-Seal Valve 77
6.6.11 Fitting to an ASEPTOMAG Valve 78
6.6.12 Replacing Control Tops 79
7 Start-up 80
7.1 Safety notes 80
7.2 Commissioning – Control Top without Solenoid Valves 80
7.3 Commissioning – Control Top with Solenoid Valves 81
7.4 Service Function 83
7.5 Adjust the initiator in the lantern - for unbalanced double-disks of the valves D, R, Y, B, T_R and MT 83
7.5.1 Adjust the initiator in the lantern - for double-disk of the tank bottom valves MT-DA (spreader lift) 86
7.6 Adjusting the Proximity Switch in the lantern of PMO Valve Type M/2.0 93
7.7 Test procedure for Tuchenhagen PMO valves type M / 2.0 95
7.7.1 Purpose 96
7.7.2 Process Overview 96
7.7.3 Hardware Description 96
7.7.4 Test Procedure 1 96
7.7.5 Test Procedure 2 97
8 Operation and control 99
8.1 Safety instructions 99
8.2 Settings in Programming Mode 99
8.3 Operating Overview 101
9 Cleaning 105
9.1 Cleaning 105
10 Maintenance 106
10.1 Safety instructions 106
10.2 Inspections 107
430BAL010699EN_9
4 11.01.2024

10.3 Maintenance intervals 108
10.4 Removing the Control Top from the Valve 108
10.5 Dismantling the Control Top into its Components 109
10.5.1 Variants of the Control Top 109
10.5.2 Removing the Cap 109
10.5.3 Removing the printed circuit board 109
10.5.4 Install the circuit board 110
10.5.5 Removing the sensor module (9) 110
10.5.6 Removing the logic element NOT (seal pack) 111
10.5.7 Fitting the Logic Element NOT (Sealing Package) 111
10.5.8 Removing the Solenoid Valves and the Valve Plate 112
10.5.9 Removing the pneumatic block 113
10.5.10 Fitting the Pneumatic Block 114
10.6 Install pneumatic connections 115
10.7 Maintenance 116
10.7.1 Replacing the Seals on the Base 116
10.7.2 Maintenance of Sound Absorber, Filter, Non-Return Valve and Exhaust Air Throttle 116
10.7.3 Mounting cap 117
11 Alarms 119
11.1 Malfunctions and remedies 119
11.2 Carrying out a Reset – Back to Default Standard 121
12 Decommissioning 122
12.1 Safety instructions 122
12.2 Disposal 122
12.2.1 General notes 122
13 Spare parts list - control top type T.VIS A-15 123
14 Spare parts list - switch bar T.VIS A-15 131
15 Dimension sheet - Control top type T.VIS A-15 133
16 Dimension sheet - switch bar LFT-R T.VIS A-15/M-20 for lifted valves R; T_R; L;
M_O(06); MT/T_R(08); M/2.0; MT; MT-DA; MX 134
17 Appendix 137
17.1 Lists 137
17.1.1 Abbreviations and terms 137
430BAL010699EN_9
11.01.2024 5

430BAL010699EN_9
6 11.01.2024

1 General Information
1.1 Information on the Document
The present Operating Instructions are part of the user information for the
product. The Operating Instructions contain all the information you need to
transport, install, commission, operate and carry out maintenance for the product.
1.1.1 Binding Character of These Operating Instructions
These Operating Instructions contain the manufacturer's instructions to the
operator of the product and to all persons who work on or use the product
regarding the procedures to follow.
Carefully read these Operating Instructions before starting any work on or using
the product. Your personal safety and the safety of the product can only be
ensured if you act as described in the Operating Instructions.
Store the Operating Instructions in such a way that they are accessible to the
operator and the operating staff during the entire life cycle of the product. When
the location is changed or the product is sold make sure you also provide the
Operating Instructions.
1.1.2 Notes on the Illustrations
The illustrations in these Operating Instructions show the product in a simplified
form. The actual design of the product can differ from the illustration. For detailed
views and dimensions of the product please refer to the design documents.
1.1.3 Symbols and Highlighting
In these Operating Instructions, important information is highlighted by symbols
or special formatting. The following examples illustrate the most important types
of highlighting.
Danger
Warning: Fatal Injuries
Failure to observe the warning can result in serious damage to health, or
even death.
► The arrow identifies a precautionary measure you have to take to avoid
the hazard.
Warning: Explosions
Failure to observe the warning can result in severe explosions.
► The arrow identifies a precautionary measure you have to take to avoid
the hazard.
General Information
Information on the Document
430BAL010699EN_9
11.01.2024 7

Warning!
Warning: Serious Injuries
Failure to observe the warning can result in serious damage to health.
► The arrow identifies a precautionary measure you have to take to avoid
the hazard.
Caution!
Warning: Injuries
Failure to observe the warning can result in minor or moderate damage to
health.
► The arrow identifies a precautionary measure you have to take to avoid
the hazard.
Notice
Warning: Damage to Property
Failure to observe the warning can result in serious damage to the
component or in the vicinity of the component.
► The arrow identifies a precautionary measure you have to take to avoid
the hazard.
Carry out the following steps: = Start of a set of instructions.
1. First step in a sequence of operations.
2. Second step in a sequence of operations.
®Result of the previous operation.
®The operation is complete, the goal has been achieved.
Hint!
Further useful information.
1.2 Manufacturer address
GEA Tuchenhagen GmbH
Am Industriepark 2-10
21514 Büchen
1.3 Contact
Tel.:+49 4155 49-0
Fax:+49 4155 49-2035
www.gea.com
General Information
Manufacturer address
430BAL010699EN_9
8 11.01.2024

1.4 EU Declaration of Conformity
GEA INTERNAL
EU Declaration of Conformity
Manufacturer:
GEA Tuchenhagen GmbH
Am Industriepark 2-10
21514 Büchen, Germany
We hereby declare that the devices named below
Model:
Control Top T.VIS® A-15
Control top T.VIS® A-15/ Class I Division 2
Type:
24 VDC
AS-i
DeviceNet
IO-Link
due to their design and construction as well as in the versions sold by us, meet the basic safety and health requirements of
the following guideline:
Relevant EC directives:
2014/30/EU
2011/65/EU
EMC
RoHS
Applicable harmonized standards, in
particular:
Other applied standards
and technical specifications:
EN 61000-6-2: 2019
EN 61000-6-4: 2019
EN IEC 62026-1:2019
EN 62026-2:2013
IEC 61131-9:2013
DIN EN 61326-1 :2013-07
DIN EN 61131-2: 2008
CISPR11:2015
Remarks:
• The device type IO-Link meets the IO-Link test specification (Version 1.1.2 - 2014)
• Model T.VIS® A-15/ Class I Div. 2 not for type IO-Link!
• The above mentioned standards have been taken into account in accordance with
the respective scope of application
Person authorised for compilation and handover of technical
documentation:
GEA Tuchenhagen GmbH
CE Documentation Officer
Am Industriepark 2-10
21514 Büchen, Germany
Büchen, 08 November 2022
________________________________ ________________________________
Franz Bürmann pp. Stephan Dirks
Managing Director Director Hygienic Valves I & Control Top
General Information
EU Declaration of Conformity
430BAL010699EN_9
11.01.2024 9

1.5 Translated copy of the EU Declaration of Conformity
Manufacturer: GEA Tuchenhagen GmbH
Am Industriepark 2-10
21514 Buchen, Germany
We hereby declare that the devices named below
Model: Control top T.VIS® A-15
Control top T.VIS® A-15/Class I Division 2
Type: 24 VDC
AS-i
DeviceNet
IO-Link
due to their design and construction as well as in the versions sold by us, meet the basic safety and health requirements of the
following guideline:
Relevant EC directives: 2014/30/EU EMC
2011/65/EU RoHS
Applicable harmonized standards, in
particular:
EN 61000-6-2: 2019
EN 61000-6-4: 2011-09
DIN IEC 62026-2: 2013
IEC 61131-9: 2013
Other applied standards and
technical specifications:
DIN EN 61326-1: 2013-07
DIN EN 61131-2: 2008
CISPR11: 2015
Remarks: •The device type IO-Link complies with the IO-Link test specifications (version 1.1.2 - 2014)
•Model T.VIS® A-15/ Class I Div. 2 cannot be used with the type IO-Link!
•The standards stated have been taken into consideration according to the respective application area.
Person authorised for compilation and handover of technical
documentation:
GEA Tuchenhagen GmbH
CE Documentation Officer
Am Industriepark 2-10
21514 Büchen, Germany
Büchen, 08. November 2022
Franz Bürmann
Managing Director by order Stephan Dirks
Director Hygienic Valves I & Control Top
General Information
Translated copy of the EU Declaration of Conformity
430BAL010699EN_9
10 11.01.2024

1.6 UK Declaration
1/1
GEA CONFIDENTIAL
UK- Declaration of Conformity by Electromagnetic Compatibility Regulations 2016
Manufacturer:
GEA Tuchenhagen GmbH
Am Industriepark 2-10
21514 Büchen, Germany
Hereby, we declare that the machine designated in the following
Model:
Control top T.VIS® A-15
Control top T.VIS® A-15 / Class I Division 2
Type:
24 VDC
AS-i
DeviceNet
IO-Link
by virtue of its design and construction and in the versions placed on the market by us, complies with the essential health
and safety requirements of the following directive:
Relevant UK legislation:
Electromagnetic Compatibility Regulations 2016
Regulations: restriction of hazardous substances (RoHS)
Applicable harmonized standards, in
particular:
Other applied standards
and technical specifications:
EN IEC 61000-6-2: 2019
EN IEC 61000-6-4: 2019
EN IEC 62026-1: 2019
EN IEC 62026-2: 2013
EN IEC 61131-9:2013
DIN EN 61326-1:2013
DIN EN 61161-2: 2008
CISPR11:2015
Remarks:
• The device type IO-Link meets the IO-Link test specification (Version 1.1.2 – 2014)
• Model T.VIS® A-15/ Class I Div. 2 not for type IO-Link!
• The above-mentioned standards have been taken into account in accordance with the
respective scope of application
Person authorised for compilation and handover of technical
documentation:
GEA Tuchenhagen GmbH
Documentation Officer
Am Industriepark 2-10
21514 Büchen, Germany
Büchen, 08 November 2022
________________________________ ________________________________
Franz Bürmann pp. Stephan Dirks
Managing Director Director Hygienic Valves I & Control Top
General Information
UK Declaration
430BAL010699EN_9
11.01.2024 11

1.7 Translated copy of the UK Declaration of Conformity according to the provisions on
electromagnetic compatibility from 2016
Manufacturer: GEA Tuchenhagen GmbH
Am Industriepark 2-10
21514 Büchen, Germany
We hereby declare that the devices named below
Model: Control top T.VIS® A-15
Control top T.VIS® A-15 / Class I Division 2
Type: 24 VDC
AS-i
DeviceNet
IO-Link
due to its design and construction as well as in the versions sold by us, meet the basic safety and health requirements of the following
guideline:
Relevant UK directives: Regulations on electromagnetic compatibility 2016
Regulations: Restriction of hazardous substances (RoHS)
Applicable harmonized standards, in particular: EN IEC 61000-6-2: 2019
EN IEC 61000-6-4: 2011-09
DIN IEC 62026-1:2019
DIN IEC 62026-2:2013
DIN IEC 61131-9:2013
Other applied standards and technical specifications: EN IEC 61326-1: 2013
EN IEC 61161-2: 2008
CISPR11:2015
Remarks: •The IO-Link device type meets the IO-Link test specification (version 1.1.2 – 2014)
•Model T.VIS® A-15/ class I div. 2 not for type IO-Link!
•The standards stated have been taken into consideration according to the respective application area.
Person authorised for compilation and handover of technical
documentation:
GEA Tuchenhagen GmbH
CE Documentation Officer
Am Industriepark 2-10
21514 Büchen, Germany
Büchen, 08. November 2022
Franz Bürmann
Managing Director by order Stephan Dirks
Director Hygienic Valves I & Control Top
General Information
Translated copy of the UK Declaration of Conformity according to the provisions on electromagnetic compatibility from
2016
430BAL010699EN_9
12 11.01.2024

2 Safety
2.1 Intended use
With the automatic control top T.VIS A-15 all Tuchenhagen and ASEPTOMAG
process valves with VARIVENT adaptation can be connected pneumatically and
electrically. Using the device for any other purpose is considered contrary to its
designated use.
The control top T.VIS A-15 is available as
•position indicator without solenoid valve
•with solenoid valve as control top
The control top T.VIS A-15 is completely installed on the dedicated actuator/
adapter of the process valve by means of a clamp connection. Due to the internal
air guiding system, the control air can pass directly from the control top into the
actuator on suitable process valves. For process valves which do not allow the air
to be guided internally, the control top has a connection option for supplying the
air externally via a hose.
The control top T.VIS A-15 may not be used in areas where ATEX approval is
required.
Hint!
The manufacturer will not accept any liability for damage resulting
from any use of the valve which is not in accordance with the
designated use of the valve. The risk is borne solely by the operating
company.
2.1.1 Requirements for operation
The prerequisite for reliable and safe operation of the component is proper
transportation and storage as well as professional installation and assembly.
Operating the unit within the limits of its designated use also involves adhering to
the operating, inspection and maintenance instructions.
2.1.2 Improper operating conditions
The operational safety of the component can not be guaranteed under improper
operating conditions. Therefore avoid improper operating conditions.
The operation of the component is not permitted if:
•Persons or objects are in the danger zone.
•Safety devices are not working or were removed.
•Malfunctions have been detected on the component.
•Damage to the component has been detected.
•Maintenance intervals have been exceeded.
2.2 Operator’s Duty of Care
Safety
Intended use
430BAL010699EN_9
11.01.2024 13

The operating company of the component has a special responsibility for the
proper and safe handling of the component within their company. Only use the
component when it is in perfect operating condition in order to prevent danger to
persons and property.
This operating manual contains information that you and your employees need
for safe operation over the life of the component. Be sure to read these Operating
Instructions carefully and ensure that the measures described here are observed.
The operator's duty of care includes planning the necessary safety measures and
monitoring that these measures are observed. The following principles apply:
•Only qualified personnel may work on the component.
•The operating company must authorize personnel to carry out the relevant
tasks.
•Order and cleanliness must be maintained at the work stations and in the
entire area surrounding the component.
•Personnel must wear suitable work clothing and personal protective
equipment. As the operating company must ensure that work clothing and
personal protective equipment are used.
•Inform personnel regarding any properties of the product which might pose a
health risk and the preventative measures to be taken.
•Have a qualified first-aid representative on call during the operation. This
person must be able to initiate any necessary first-aid measures in case of an
emergency.
•Clearly define procedures, competences and responsibilities for those
working in the area of the component. Everybody must know what to do in
case of an emergency. Instruct the staff in this respect at regular intervals.
•The signs on the component must always be complete and easy to read.
Check, clean and replace the signs as necessary at regular intervals.
•Observe the Technical Data specified and the limits of use!
Hint!
Carry out regular checks. This way you can ensure that these
measures are actually observed.
2.3 Subsequent changes
No technical modifications should ever be made to this component. Otherwise
you will have to undergo a new conformity process in accordance with the EC
Machinery Directive on your own.
In general, only original spare parts supplied by GEA Tuchenhagen GmbH
should be fitted. This ensures that the component is always operating properly
and efficiently.
Safety
Subsequent changes
430BAL010699EN_9
14 11.01.2024

2.4 IP Protection classes
The control top T.VIS A-15 in its standard version fulfils the requirements of
protection class IP66, IP67 and IP69 (DIN EN 60529) and protection class IP6k9k
(ISO 20653).
IP classes provide information about the degree of protection an electrical device
housing provides against the ingress of solids (first digit) or humidity (second
digit). So-called IP codes are assigned to the protected systems. Its digits
represent common possible errors the system is protected from. The code always
starts with the letter IP for “international protection”.
First digit * Meaning
ISO 20653 DIN EN 60529 Protection against contact Protection against solids
6k 6 Complete contact protection Complete protection against dust
ingression (dustproof)
Second digit * Meaning
ISO 20653 DIN EN 60529 Protection against humidity
5 5 Protected against water jet (nozzle) from any angle
6 6 Protected against powerful water jets
6k Protected against powerful water jets under increased pressure
7 7 Protected against temporary immersion
9 Protected against high pressure spray downs
9k Protected against high pressure spray downs
* For additional digits and more detailed descriptions please refer to the pertinent standard.
Digits not to be mentioned can be replaced by the letter x (e. g. IPx6).
Concerning the ingress of humidity, IPx6 includes all lower IP classes. This is,
however, not the case for the higher protection class IPx7!
Hint!
The specified IP classes only apply if the connectors are connected
correctly, if the cable gland is properly sealed and if the control top is
fitted on the valve, see Chapter 6, Page 46.
2.5 General safety instructions and dangers
The component is safe to operate. It was built according to state-of-the-art
science and technology.
Nevertheless, dangers can arise from the component, if:
•the component is not used as intended
•the component is used improperly
•the component is operated under impermissible conditions
2.5.1 Principles for safe operation
Dangerous situations during operation can be avoided by safety-conscious and
proactive behaviour of the staff.
To ensure safe operation of the valve the following principles apply:
Safety
IP Protection classes
430BAL010699EN_9
11.01.2024 15

•The Operating Instructions must be kept ready to hand at the valve's place of
use. They must be complete and in clearly legible form.
•Only use the valve for its intended use.
•The valve must be functional and in good working order. Check the condition
of the valve before starting work and at regular intervals.
•Wear tight-fitting work clothing for all work on the valve.
•Ensure that nobody can get hurt on the parts of the valve.
•Immediately report any faults or noticeable changes on the valve to the
person responsible.
•Never touch the pipes and the valve when these components are hot! Avoid
opening the valve unless the process plants have been emptied and
depressurised.
•Observe the accident prevention regulations and all local regulations.
2.5.2 Environmental Protection
Harm to the environment can be avoided by safety-conscious and proactive
behaviour of the staff.
For environmental protection the following principles apply:
•Substances harmful to the environment must not be discharged into the
ground or the sewage system.
•Always observe the pertinent regulations relating to waste avoidance,
disposal and utilization.
•Substances harmful to the environment must be collected and stored in
suitable containers. Clearly mark the containers.
•Dispose of lubricants as hazardous waste.
2.5.3 Electrical Equipment
For all work on electrical equipment, the following principles apply:
•Access to electrical equipment should only be allowed to qualified
electricians. Always keep unattended switch cabinets locked.
•Modifications of the control system can affect the safe and reliable operation.
Modifications are only permitted with the express permission of the
manufacturer.
•After completion of all work, check that the protective devices are fully
functional.
2.6 Supplementary Regulations
In addition to the instructions in this documentation the following also has to be
observed:
•pertinent accident prevention regulations,
•generally accepted safety rules,
Safety
Supplementary Regulations
430BAL010699EN_9
16 11.01.2024

•national regulations applicable in the country of use,
•work and safety instructions applicable in the facility,
•installation and operating regulations for use in potentially explosive areas.
2.7 Qualification of personnel
This section provides information on how the personnel working on the
component must be trained.
Operating and maintenance personnel must
•have the necessary qualification to carry out their tasks,
•be instructed with regard to possible dangers,
•know and observe the safety instructions given in the documentation.
Only allow qualified electricians to carry out work on the electrical equipment or
have a qualified electrician supervise the work.
Only allow specially trained personnel to carry out work on an explosion-
protected system. When working on explosion-protected equipment observe the
standards DIN EN 60079-14 for gases and DIN EN 50281-1-2 for dusts.
The following minimum qualifications are required:
•Training as a specialist for working independently on the component.
•Adequate instruction to work on the component under the supervision and
guidance of a trained specialist
Each employee must meet the following requirements to work on the component:
•Personal suitability for the respective task.
•Sufficient professional qualification for the respective task.
•Received instruction about the functionality of the component.
•Received instruction about operating sequences on the component.
•Familiar with the safety devices and their function.
•Familiar with these Operating Instructions, especially with the safety
instructions and the information which is relevant for the task on hand.
•Familiar with the basic regulations with regard to occupational health and
safety and accident prevention.
When working with the component, a distinction is made between the following
user groups:
Safety
Qualification of personnel
430BAL010699EN_9
11.01.2024 17

User groups
Staff Qualifications
Operating personnel Adequate instruction and sound knowledge in the following areas:
•Functionality of the component
•Operating sequences on the pump
•What to do in case of an emergency
•Lines of authority and responsibilities with respect to the task
Maintenance personnel Appropriate training and a sound knowledge of the structure and
functionality of the component.
Sound knowledge in the following areas:
•Mechanical equipment
•Electrical equipment
•Pneumatic system
Authorization with regard to safety engineering standards to carry
out the following tasks:
•Setting devices into operation
•Earthing of devices
•Marking of devices
The relevant certificates of qualification must be submitted before
work can be carried out on ATEX certified machines.
2.8 Safety equipment
2.8.1 Signs
Dangerous points on the control top are indicated by warning signs, prohibition
signs and mandatory signs.
The signs and notes on the control top must always be legible. Any illegible signs
must be replaced immediately.
Safety
Safety equipment
430BAL010699EN_9
18 11.01.2024

Signs on the control top
Sign Meaning
Fig.1
General hazard warning
Fig.2
Warning Crushing
2.9 Residual dangers
Dangerous situations can be avoided by safety-conscious and proactive
behaviour of the personnel and by wearing personal protective equipment.
Residual dangers on the control top and measures
Danger Cause Measure
Danger to life Inadvertent switch-on of the control top Effectively disconnect all components, effectively prevent
switch-on.
Electric power Observe the following safety rules:
1. Isolate from the power supply.
2. Take appropriate measures to prevent switch on.
3. Test absence of voltage.
4. Earthing and short-circuiting.
5. Cover or safeguard any adjacent live parts.
Damage to property Welding can cause damage to the electronics
or result in data loss.
Do not carry out any welding work in the vicinity of the control
top or make sure electronics are properly protected.
Voltage peaks The permitted voltage ranges of the respective connection
types can be found in chapters 5.3 to 5.6 and must not be
exceeded.
2.9.1 Electrostatically Endangered Components and Modules
The control top contains electronic components that are sensitive to electrostatic
discharge (ESD). Contact with electrostatically-charged persons or objects can
endanger these components. In the worst case they are destroyed immediately
or fail after being put into operation.
To minimize or prevent the possibility of damage resulting from sudden
electrostatic discharge,
•observe the requirements of DIN EN 61340-5-1 and 5-2 and
•take care not to touch the electronic components!
2.10 Danger zones
Please observe the following notes:
Safety
Residual dangers
430BAL010699EN_9
11.01.2024 19

•In the event of malfunctions, shut down the control top (disconnect from the
power and air supply) and secure it against being used.
•Before starting any service, maintenance or repair work, disconnect the
control top from the power supply and secure it against inadvertently being
switched back on again.
•Only allow a qualified electrician to carry out any work on the electrical power
supply.
•Check the electrical equipment of the control top at regular intervals.
Immediately remedy loose connections and molten cables.
•If work on live parts cannot be avoided, call in a second person, who can
operate the main switch in case of an emergency.
Safety
430BAL010699EN_9
20 11.01.2024
Other manuals for T.VIS A-15
1
Table of contents
Other GEA Control System manuals
Popular Control System manuals by other brands
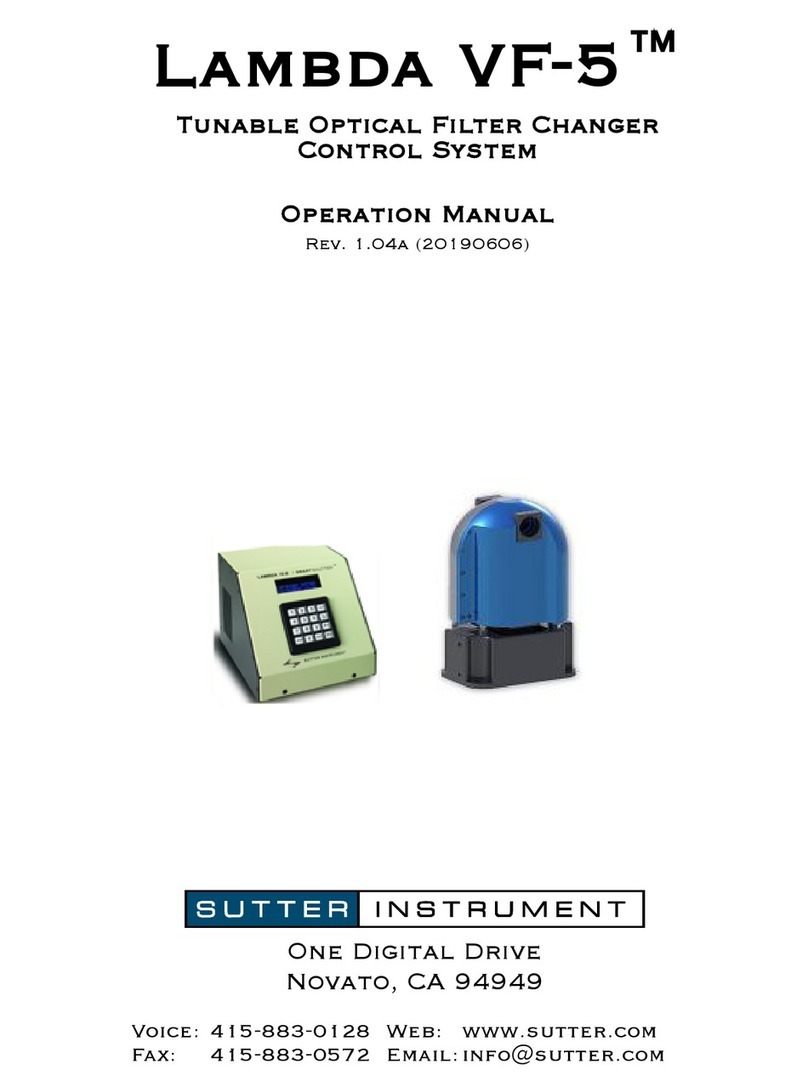
Sutter
Sutter Lambda VF-5 Operation manual
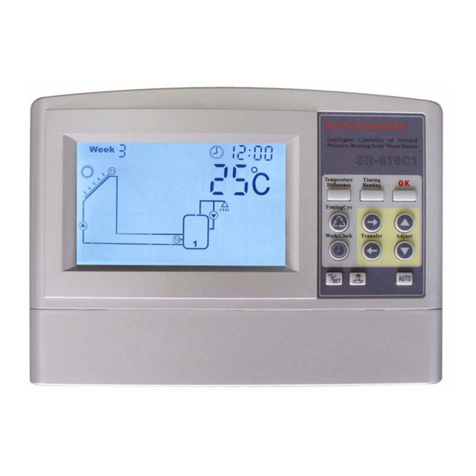
Shuangri Electric
Shuangri Electric SR618C1 Installation and operating manual

Dryer Master
Dryer Master DM510 Commissioning Guide
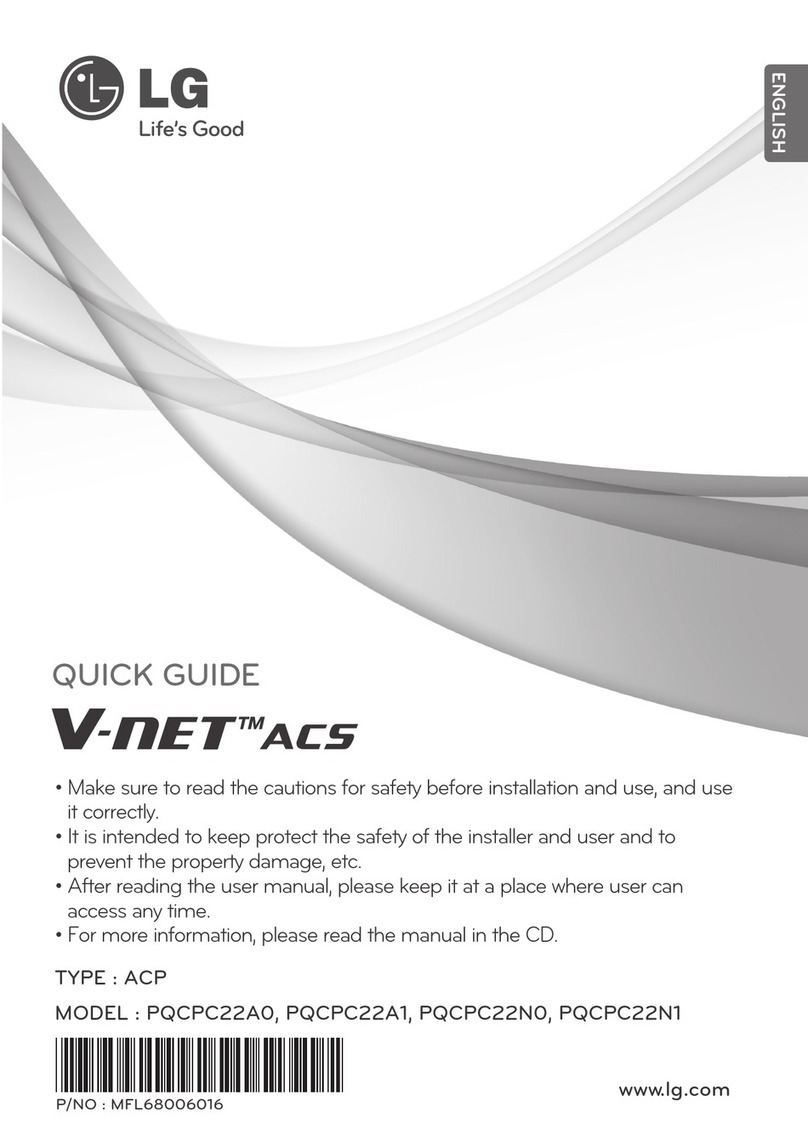
LG
LG V-NET PQCPC22A0 quick guide
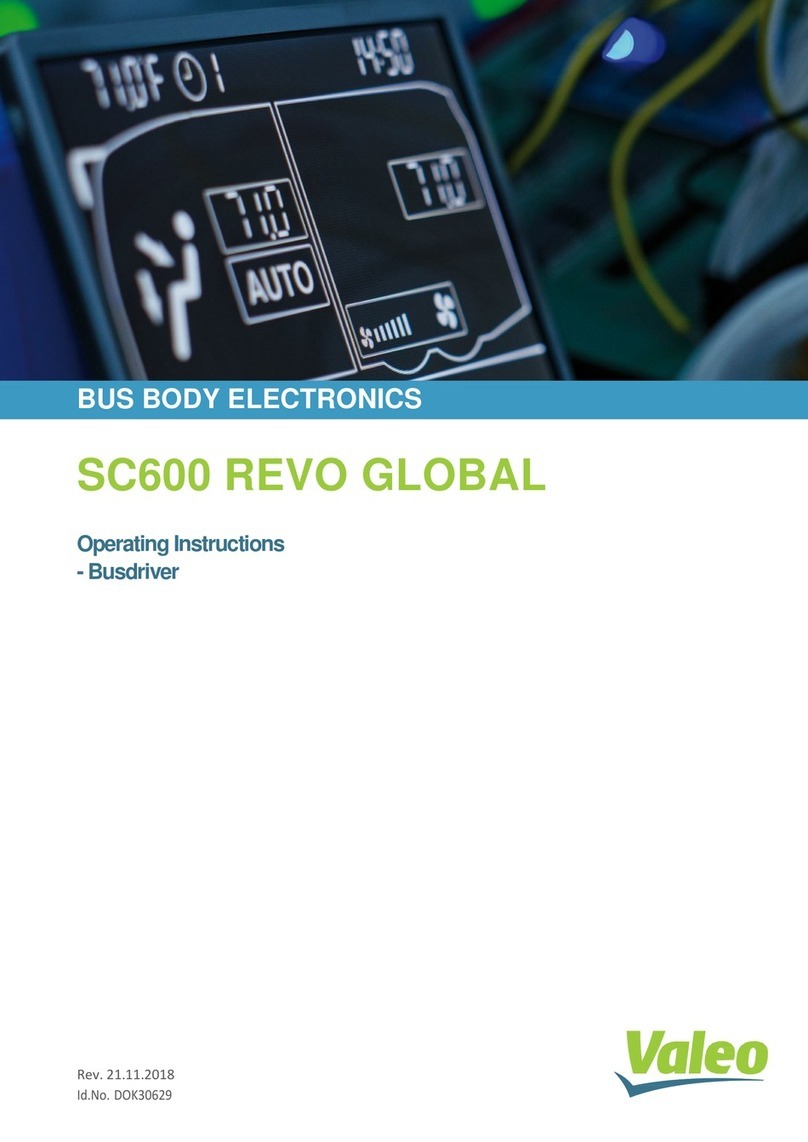
Valeo
Valeo SC600 Revo Global operating instructions

Extron electronics
Extron electronics TouchLink TLC Pro 526M Series user guide