GEA T.VIS P-15 User manual

Control and feedback systems
GEA T.VIS® P-15
Operating instruction (Translation from the original language)
430BAL010747EN_3

COPYRIGHT
These Operating Instructions are the English translation of the original operating
instructions in the sense of the EU Machinery Directive. This document is
protected by copyright. All rights reserved. The document may not, in whole or in
part, be copied, reproduced, translated or reduced to an electronic medium of
machine-readable form without the express permission of GEA Tuchenhagen
GmbH.
LEGAL NOTICE
Word marks
The designations T.VIS®, VARIVENT®, ECOVENT®, STERICOM®, VESTA® und
LEFF® are protected trademarks of GEA Tuchenhagen GmbH.
We kindly request that you answer a few short questions about these instruction
manual. Use the following QR code or link to access the questionnaire:
https://www.ntgt.de/ra/s.aspx?s=367112X57707125X58087
430BAL010747EN_3
2 24.07.2020

TABLE OF CONTENTS
1 General Information 5
1.1 Information on the Document 5
1.1.1 Binding Character of These Operating Instructions 5
1.1.2 Notes on the Illustrations 5
1.1.3 Symbols and Highlighting 5
1.2 Manufacturer address 6
1.3 Contact 6
2 Safety 7
2.1 Intended use 7
2.1.1 Requirements for operation 7
2.1.2 Improper operating conditions 7
2.2 Operator’s Duty of Care 7
2.3 Subsequent changes 8
2.4 IP Protection Classes 8
2.5 General safety instructions and dangers 9
2.5.1 Principles for safe operation 9
2.5.2 Environmental Protection 10
2.5.3 Electrical Equipment 10
2.6 Supplementary Regulations 10
2.7 Qualification of personnel 11
2.8 Safety equipment 12
2.8.1 Signs 12
2.9 Residual dangers 13
2.9.1 Electrostatically Endangered Components and Modules 13
2.10 Danger zones 14
3 Description 15
3.1 Functional description 15
3.1.1 Operation Principle 15
3.1.2 Control Top with Cap Including Buttons 16
3.1.3 Control Top with Cap without Buttons 16
3.1.4 Function of the Buttons 17
3.1.5 Safety Air Exhaust/Installation Position 17
4 Transport and storage 18
4.1 Storage conditions 18
4.2 Transport 18
4.2.1 Scope of supply 18
5 Technical data 19
5.1 Type plate 19
5.2 Technical data 20
5.3 Specifications for 24V DC Version 22
5.4 Accessories 23
5.5 Tool 23
5.6 Lubricants 23
5.7 Equipment 24
6 Assembly and installation 25
6.1 Safety instructions 25
6.2 Establishing Hose Connections 25
6.3 Pneumatic connections 25
6.3.1 Control Top with Solenoid Valves 26
6.4 Electrical connections 27
6.4.1 Overview 27
6.4.2 Electrical 24 V DC Wiring 28
Connector M12 / 5-pin, A-coded (24) 28
Connector M12/5-pin, B-coded (50) 29
6.5 Visual Display 29
6.5.1 Illuminated dome 30
6.5.2 Colour Changeover 30
6.5.3 Connection Diagram for T.VIS Circuit Board (Bottom) 31
6.6 Mounting the Control Top to Different Valves 31
6.6.1 Mounting to VARIVENT Shut-Off and Divert Valves 32
430BAL010747EN_3
24.07.2020 3

6.6.2 Mounting to a Butterfly Valve T-smart 8000 32
6.6.3 Mounting to a Butterfly Valve T-smart 7 and a Mixproof Butterfly Valve T-smart 9 33
6.6.4 Mounting to ECOVENT Valves N_ECO and W_ECO 34
6.6.5 Mounting to VESTA Valve H_A/M 34
6.6.6 Mounting to VESTA Valve H_A 35
6.6.7 Fitting to an ASEPTOMAG Valve 36
6.6.8 Replacing Control Tops 37
7 Start-up 38
7.1 Safety precautions 38
7.2 Commissioning – Control Top with Solenoid Valves 38
7.3 Service Function 40
8 Operation and control 41
8.1 Safety instructions 41
8.2 Operating Overview 42
9 Cleaning 44
9.1 Cleaning 44
10 Maintenance 45
10.1 Safety precautions 45
10.2 Inspections 46
10.3 Removing the Control Top from the Valve 47
10.4 Dismantling the Control Top into its Components 47
10.4.1 Removing the Cap 47
10.4.2 Remove the circuit board 48
10.4.3 Install the circuit board 48
10.4.4 Removing the sensor module (9) 48
10.4.5 Removing the Solenoid Valves and the Control Plate 49
10.4.6 Removing the pneumatic block 50
10.4.7 Fitting the Pneumatic Block 50
10.4.8 Install valve plates 51
10.5 Maintenance 52
10.5.1 Replacing the Seals on the Base 52
10.5.2 Maintenance of Sound Absorber, Filter, Non-Return Valve and Exhaust Air Throttle 52
11 Alarms 54
11.1 Malfunctions and remedies 54
11.2 Carrying out a Reset – Back to Default Standard 56
12 Decommissioning 57
12.1 Safety instructions 57
12.2 Disposal 57
12.2.1 General notes 57
13 Spare parts list - control top type T.VIS P-15 58
14 Spare parts list - switch bar T.VIS P-15 60
15 Dimension sheet - control top type T.VIS P-15 62
16 Appendix 63
16.1 Lists 63
16.1.1 Abbreviations and terms 63
430BAL010747EN_3
4 24.07.2020

1 General Information
1.1 Information on the Document
The present Operating Instructions are part of the user information for the
product. The Operating Instructions contain all the information you need to
transport, install, commission, operate and carry out maintenance for the product.
1.1.1 Binding Character of These Operating Instructions
These Operating Instructions contain the manufacturer's instructions to the
operator of the product and to all persons who work on or use the product
regarding the procedures to follow.
Carefully read these Operating Instructions before starting any work on or using
the product. Your personal safety and the safety of the product can only be
ensured if you act as described in the Operating Instructions.
Store the Operating Instructions in such a way that they are accessible to the
operator and the operating staff during the entire life cycle of the product. When
the location is changed or the product is sold make sure you also provide the
Operating Instructions.
1.1.2 Notes on the Illustrations
The illustrations in these Operating Instructions show the product in a simplified
form. The actual design of the product can differ from the illustration. For detailed
views and dimensions of the product please refer to the design documents.
1.1.3 Symbols and Highlighting
In these Operating Instructions, important information is highlighted by symbols
or special formatting. The following examples illustrate the most important types
of highlighting.
Danger
Warning: Fatal Injuries
Failure to observe the warning can result in serious damage to health, or
even death.
► The arrow identifies a precautionary measure you have to take to avoid
the hazard.
Warning: Explosions
Failure to observe the warning can result in severe explosions.
► The arrow identifies a precautionary measure you have to take to avoid
the hazard.
General Information
Information on the Document
430BAL010747EN_3
24.07.2020 5

Warning!
Warning: Serious Injuries
Failure to observe the warning can result in serious damage to health.
► The arrow identifies a precautionary measure you have to take to avoid
the hazard.
Caution!
Warning: Injuries
Failure to observe the warning can result in minor or moderate damage to
health.
► The arrow identifies a precautionary measure you have to take to avoid
the hazard.
Notice
Warning: Damage to Property
Failure to observe the warning can result in serious damage to the
component or in the vicinity of the component.
► The arrow identifies a precautionary measure you have to take to avoid
the hazard.
Carry out the following steps: = Start of a set of instructions.
1. First step in a sequence of operations.
2. Second step in a sequence of operations.
®Result of the previous operation.
®The operation is complete, the goal has been achieved.
Hint!
Further useful information.
1.2 Manufacturer address
GEA Tuchenhagen GmbH
Am Industriepark 2-10
21514 Büchen
1.3 Contact
Tel.:+49 4155 49-0
Fax:+49 4155 49-2035
www.gea.com
General Information
Manufacturer address
430BAL010747EN_3
6 24.07.2020

2 Safety
2.1 Intended use
The programmable positioner T.VIS P-15 (Tuchenhagen Valve Informations
System) kallows GEA Tuchenhagen and ASEPTOMAG single-seat valves to be
set to any position within the given stroke (5-70 mm), provided the pneumatic and
electrical connections are established correctly.
The positioner T.VIS P-15 consists of a base and a hood. It is completely
mounted on the actuator/adapter of the process valve provided for this purpose
using two clamps. The internal hose system directly connects the control air to
the process valve. For process valves which do not allow the air to be guided
internally, the control top has a connection option for supplying the air externally
via a hose.
The control top T.VIS P-15 may not be used in areas where ATEX approval is
required.
Hint!
The manufacturer will not accept any liability for damage resulting
from any use of the valve which is not in accordance with the
designated use of the valve. The risk is borne solely by the operating
company.
2.1.1 Requirements for operation
The prerequisite for reliable and safe operation of the component is proper
transportation and storage as well as professional installation and assembly.
Operating the unit within the limits of its designated use also involves adhering to
the operating, inspection and maintenance instructions.
2.1.2 Improper operating conditions
The operational safety of the component can not be guaranteed under improper
operating conditions. Therefore avoid improper operating conditions.
The operation of the component is not permitted if:
•Persons or objects are in the danger zone.
•Safety devices are not working or were removed.
•Malfunctions have been detected on the component.
•Damage to the component has been detected.
•Maintenance intervals have been exceeded.
2.2 Operator’s Duty of Care
The operating company of the component has a special responsibility for the
proper and safe handling of the component within their company. Only use the
component when it is in perfect operating condition in order to prevent danger to
persons and property.
Safety
Intended use
430BAL010747EN_3
24.07.2020 7

This operating manual contains information that you and your employees need
for safe operation over the life of the component. Be sure to read these Operating
Instructions carefully and ensure that the measures described here are observed.
The operator's duty of care includes planning the necessary safety measures and
monitoring that these measures are observed. The following principles apply:
•Only qualified personnel may work on the component.
•The operating company must authorize personnel to carry out the relevant
tasks.
•Order and cleanliness must be maintained at the work stations and in the
entire area surrounding the component.
•Personnel must wear suitable work clothing and personal protective
equipment. As the operating company must ensure that work clothing and
personal protective equipment are used.
•Inform personnel regarding any properties of the product which might pose a
health risk and the preventative measures to be taken.
•Have a qualified first-aid representative on call during the operation. This
person must be able to initiate any necessary first-aid measures in case of an
emergency.
•Clearly define procedures, competences and responsibilities for those
working in the area of the component. Everybody must know what to do in
case of an emergency. Instruct the staff in this respect at regular intervals.
•The signs on the component must always be complete and easy to read.
Check, clean and replace the signs as necessary at regular intervals.
•Observe the Technical Data specified and the limits of use!
Hint!
Carry out regular checks. This way you can ensure that these
measures are actually observed.
2.3 Subsequent changes
No technical modifications should ever be made to this component. Otherwise
you will have to undergo a new conformity process in accordance with the EC
Machinery Directive on your own.
In general, only original spare parts supplied by GEA Tuchenhagen GmbH
should be fitted. This ensures that the component is always operating properly
and efficiently.
2.4 IP Protection Classes
The control top T.VIS P-15 in its standard version fulfils the requirements of
protection class IP66 (DIN EN 60529). Models in protection classes IP67 or
IP69k (both DIN EN 60529) are also available.
Safety
Subsequent changes
430BAL010747EN_3
8 24.07.2020

IP classes provide information about the degree of protection an electrical device
housing provides against the ingress of solids (first digit) or humidity (second
digit). They attempt to reproduce common kinds of failure and assign so-called IP
codes to the protected systems. The letters IP stand for 'International Protection'
and are prefixed to the code numbers.
Position of the digit Explanation
1. digit* Protection against solids
6 Dust tight
2. digit* Protection against humidity
6 Protected against powerful water jets
7Protected against temporary
immersion
9k Protected against high pressure spray
downs
*For additional digits and more detailed descriptions please refer to the
pertinent standard.
Digits not to be mentioned can be replaced by the letter x (e. g. IPx6).
Concerning the ingress of humidity, IPx6 includes all lower IP classes. This is,
however, not the case for the higher protection class IPx7!
If cleaning agents are used that significantly reduce the surface tension and/or if
high-pressure cleaners are used, we recommend using IP69k rated equipment as
an option.
Hint!
The specified IP classes only apply if the connectors are connected
correctly, if the cable gland is properly sealed and if the control top is
fitted on the valve, see Chapter 6, Page 25.
2.5 General safety instructions and dangers
The component is safe to operate. It was built according to state-of-the-art
science and technology.
Nevertheless, dangers can arise from the component, if:
•the component is not used as intended
•the component is used improperly
•the component is operated under impermissible conditions
2.5.1 Principles for safe operation
Dangerous situations during operation can be avoided by safety-conscious and
proactive behaviour of the staff.
To ensure safe operation of the valve the following principles apply:
•The Operating Instructions must be kept ready to hand at the valve's place of
use. They must be complete and in clearly legible form.
Safety
General safety instructions and dangers
430BAL010747EN_3
24.07.2020 9

•Only use the valve for its intended use.
•The valve must be functional and in good working order. Check the condition
of the valve before starting work and at regular intervals.
•Wear tight-fitting work clothing for all work on the valve.
•Ensure that nobody can get hurt on the parts of the valve.
•Immediately report any faults or noticeable changes on the valve to the
person responsible.
•Never touch the pipes and the valve when these components are hot! Avoid
opening the valve unless the process plants have been emptied and
depressurised.
•Observe the accident prevention regulations and all local regulations.
2.5.2 Environmental Protection
Harm to the environment can be avoided by safety-conscious and proactive
behaviour of the staff.
For environmental protection the following principles apply:
•Substances harmful to the environment must not be discharged into the
ground or the sewage system.
•Always observe the pertinent regulations relating to waste avoidance,
disposal and utilization.
•Substances harmful to the environment must be collected and stored in
suitable containers. Clearly mark the containers.
•Dispose of lubricants as hazardous waste.
2.5.3 Electrical Equipment
For all work on electrical equipment, the following principles apply:
•Access to electrical equipment should only be allowed to qualified
electricians. Always keep unattended switch cabinets locked.
•Modifications of the control system can affect the safe and reliable operation.
Modifications are only permitted with the express permission of the
manufacturer.
•After completion of all work, check that the protective devices are fully
functional.
2.6 Supplementary Regulations
In addition to the instructions in this documentation the following also has to be
observed:
•pertinent accident prevention regulations,
•generally accepted safety rules,
•national regulations applicable in the country of use,
•work and safety instructions applicable in the facility,
Safety
Supplementary Regulations
430BAL010747EN_3
10 24.07.2020

•installation and operating regulations for use in potentially explosive areas.
2.7 Qualification of personnel
This section provides information on how the personnel working on the
component must be trained.
Operating and maintenance personnel must
•have the necessary qualification to carry out their tasks,
•be instructed with regard to possible dangers,
•know and observe the safety instructions given in the documentation.
Only allow qualified electricians to carry out work on the electrical equipment or
have a qualified electrician supervise the work.
Only allow specially trained personnel to carry out work on an explosion-
protected system. When working on explosion-protected equipment observe the
standards DIN EN 60079-14 for gases and DIN EN 50281-1-2 for dusts.
The following minimum qualifications are required:
•Training as a specialist for working independently on the component.
•Adequate instruction to work on the component under the supervision and
guidance of a trained specialist
Each employee must meet the following requirements to work on the component:
•Personal suitability for the respective task.
•Sufficient professional qualification for the respective task.
•Received instruction about the functionality of the component.
•Received instruction about operating sequences on the component.
•Familiar with the safety devices and their function.
•Familiar with these Operating Instructions, especially with the safety
instructions and the information which is relevant for the task on hand.
•Familiar with the basic regulations with regard to occupational health and
safety and accident prevention.
When working with the component, a distinction is made between the following
user groups:
Safety
Qualification of personnel
430BAL010747EN_3
24.07.2020 11

User groups
Staff Qualifications
Operating personnel Adequate instruction and sound knowledge in the following areas:
•Functionality of the component
•Operating sequences on the pump
•What to do in case of an emergency
•Lines of authority and responsibilities with respect to the task
Maintenance personnel Appropriate training and a sound knowledge of the structure and
functionality of the component.
Sound knowledge in the following areas:
•Mechanical equipment
•Electrical equipment
•Pneumatic system
Authorization with regard to safety engineering standards to carry
out the following tasks:
•Setting devices into operation
•Earthing of devices
•Marking of devices
The relevant certificates of qualification must be submitted before
work can be carried out on ATEX certified machines.
2.8 Safety equipment
2.8.1 Signs
Dangerous points on the control top are indicated by warning signs, prohibition
signs and mandatory signs.
The signs and notes on the control top must always be legible. Any illegible signs
must be replaced immediately.
Safety
Safety equipment
430BAL010747EN_3
12 24.07.2020

Signs on the control top
Sign Meaning
Fig.1
General hazard warning
Fig.2
Warning Crushing
2.9 Residual dangers
Dangerous situations can be avoided by safety-conscious and proactive
behaviour of the personnel and by wearing personal protective equipment.
Residual dangers on the control top and measures
Danger Cause Measure
Danger to life Inadvertent switch-on of the
control top
Effectively disconnect all components, effectively prevent switch-
on.
Electric power Observe the following safety rules:
1. Isolate from the power supply.
2. Take appropriate measures to prevent switch on.
3. Test absence of voltage.
4. Earthing and short-circuiting.
5. Cover or safeguard any adjacent live parts.
Damage to property Welding can cause damage to
the electronics or result in data
loss.
Do not carry out any welding work in the vicinity of the control top
or make sure electronics are properly protected.
2.9.1 Electrostatically Endangered Components and Modules
The control top contains electronic components that are sensitive to electrostatic
discharge (ESD). Contact with electrostatically-charged persons or objects can
endanger these components. In the worst case they are destroyed immediately
or fail after being put into operation.
To minimize or prevent the possibility of damage resulting from sudden
electrostatic discharge,
•observe the requirements of DIN EN 61340-5-1 and 5-2,
•be careful not to touch the electronic components,
•also take care not to touch electronic components when supply voltage is
present.
Use ESD-compliant packaging when returning electronic components. (Contact
GEA Tuchenhagen if you have any questions.)
Safety
Residual dangers
430BAL010747EN_3
24.07.2020 13

2.10 Danger zones
Please observe the following notes:
•In the event of malfunctions, shut down the control top (disconnect from the
power and air supply) and secure it against being used.
•Before starting any service, maintenance or repair work, disconnect the
control top from the power supply and secure it against inadvertently being
switched back on again.
•Only allow a qualified electrician to carry out any work on the electrical power
supply.
•Check the electrical equipment of the control top at regular intervals.
Immediately remedy loose connections and molten cables.
•If work on live parts cannot be avoided, call in a second person, who can
operate the main switch in case of an emergency.
Safety
Danger zones
430BAL010747EN_3
14 24.07.2020

3 Description
3.1 Functional description
3.1.1 Operation Principle
The positioner T.VIS A-15 works with an integrated microprocessor, which
contains the software for the operation, visualization and intelligent position
detection. The valve stroke is detected by a contactless position measuring
system integrated in the positioner, and the information is supplied to the
microprocessor.
During automatic initialization and end position programming, the positioner
learns the stroke of the valve used completely autonomously. This procedure can
be activated either by operating the button in/under the cap or by an external
control signal (programming input).
After completion of the programming procedure, the positioner T.VIS P-15 is in
operating mode.
Here, when the customer feeds an analogue signal (4-20 mA), the positioner can
receive a nominal value default which is processed in the microprocessor and
which by means of appropriate pilot valve activations leads to the desired stroke
of the process valve.
The position regulated in this way is made available for further external treatment
by the positioner as an analogue signal (4-20 mA). Additionally, the position
feedback signals for START/END and an error signal can be made available to
the user as a 24 V DC switching output. The status of the process valve is locally
displayed to be visible from a distance by coloured LEDs under the dome light.
In manual mode, the main actuator can be controlled using the buttons in the cap
in order to move the process valve to its end positions or by operating the
solenoid valves manually. To do this, use a screwdriver to turn the screw (S) from
0 to 1, see graphic.
Fig.3
To assemble or disassemble the valve insert, the main actuator can be controlled
in service mode using the buttons in the cap in order to relieve the spring tension,
which depends on the valve type.
Description
Functional description
430BAL010747EN_3
24.07.2020 15

3.1.2 Control Top with Cap Including Buttons
Fig.4: Control top with cap including buttons (standard variant in IP66)
According to protection class IP66 (EN 60529) the control top T.VIS P-15 is
suitable for use in this design and if the electrical and pneumatic connections are
installed correctly.
The control top is operated with the cap closed using the plus/minus buttons.
Operation see Section 8.2, Page 42.
3.1.3 Control Top with Cap without Buttons
Fig.5: Control Top with Cap without Buttons
Fig.6: Circuit board (A)
According to protection class IP67 and/or 69k (EN 60529) the control top T.VIS
P-15 is suitable for use in this design and if the electrical and pneumatic
connections are installed correctly.
Description
Functional description
430BAL010747EN_3
16 24.07.2020

To operate the control top, take off the cap and press the plus/minus buttons
directly on the circuit board (A).
Observe the general instructions regarding ESD protection.
Operation see Section 8.2, Page 42.
3.1.4 Function of the Buttons
Automatic end position programming and manual mode are generally activated
using the buttons in or under the cap. For safety reasons, the buttons are only
enabled within a specific time window after activation of the operating voltage.
During this time window, functions can be started. The buttons are automatically
locked again after the allowed time has expired.
In manual mode the stroke of the actuator can be changed locally in 5 % steps in
the direction of the START or END position using the buttons in or under the cap.
The buttons in the cap can also be used to make customer-specific parameter
settings for the positioner.
3.1.5 Safety Air Exhaust/Installation Position
To provide protection against excess pressure which can build up in the inside of
the control top, a vent plug E2 is fitted in the base. In operating mode, the
exhaust air from the lifting actuators is discharged via this vent plug. In the
unlikely event of a damaged solenoid valve or in case of sealing problems,
pressure relief is ensured.
Fig.7: Control top (standard variant in IP66)
This vent plug is a safety device that must be handled as such. Do not cover the
vent plug. When fitting the control top note that the installation position of the vent
plug E2 must never be pointing vertically upwards.
Description
430BAL010747EN_3
24.07.2020 17

4 Transport and storage
4.1 Storage conditions
You must first dry and preserve the control top to prevent damage if the control
top is exposed to temperatures ≤ 0°C during transport or storage.
Hint!
We recommend that the valve should be stored at a temperature of ≥ 5
°C for a period of 24 hours prior to any handling (disassembling the
housings / activation of actuators) so that any ice crystals formed by
condensation water can melt.
4.2 Transport
For transport, the following principles apply:
•Only use suitable lifting gear and slings for transporting the package units/
control tops.
•Observe the pictograms on the package.
•Control tops must be protected from animal and vegetable fats.
•The synthetic materials of the control tops are susceptible to breaking. Take
care when transporting the control top. Do not grip sensitive parts of the unit
to lift or push the unit or to support yourself.
4.2.1 Scope of supply
After taking delivery of the component, check if
•the details on the type plate correspond to the data in the order and delivery
documents,
•the equipment is complete and all components are in good order.
Transport and storage
Storage conditions
430BAL010747EN_3
18 24.07.2020

5 Technical data
5.1 Type plate
The type plate is used to uniquely identify the control top.
Fig.8
Code/Type T P 1 5 N 4 P A J
Item in the order code 14 15 16 17 18 19
Explanation of the items in the order code
Item in the order code Designation Explanation
14 Feedback location
T P 1 5 Control Top T.VIS P-15
15 Control top type
N 2 solenoid valves
16 Feedback
4 T.VIS P-15 (with analog
module)
5 T.VIS P-15 (with analog
module + 2 digital
feedback signals / 1 error
output)
17 Type of interface/mode
P 24 V DC programmable
18 Solenoid valve
A 24 V DC 0.85/ 1.6 W
19 Screw connection (cable/air) for air hose Ø 6/4
mm
Technical data
Type plate
430BAL010747EN_3
24.07.2020 19

Explanation of the items in the order code
Item in the order code Designation Explanation
J 5-pin connector M12/5-
wire/M20x1.5
Acoded / for feedback
code 5: additional 5-pin
connector M12/M16; B-
coded
for air hose Ø 6,35/4,31 mm
P 5-pin connector M12/5-
wire/M20x1.5
Acoded / for feedback
code 5: additional 5-pin
connector M12/M16; B-
coded
Options /22 5-pin M12 junction box
for screw connection
J, P (Material No.
508-963)
8-pin M12 junction box
for screw connection
H, I (Material No.
508-061)
/67 Protection class IP 67
(immersion)
/69k Protection class IP 69K
(high-pressure spray
down cleaning)
/A For ASEPTOMAG valves
Example: TP15I4PAJ/A
/UC Certification UL/CSA
For indoor use
5.2 Technical data
Refer to the following tables for the key technical data of the control top:
Technical data: Temperatures and compressed air supply
Designation Description
Ambient temperature -20 to +55 °C
Control air acc. to ISO 8573-1
Technical data
Technical data
430BAL010747EN_3
20 24.07.2020
Table of contents
Other GEA Control System manuals
Popular Control System manuals by other brands
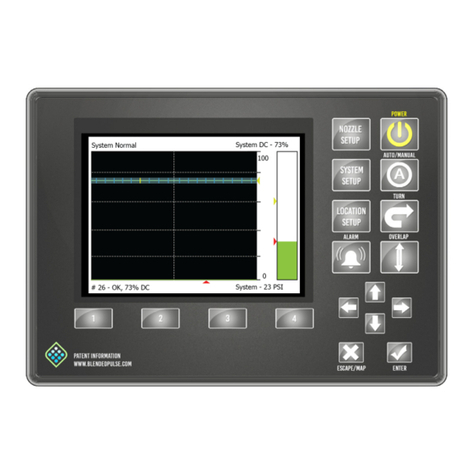
CapstanAG
CapstanAG PinPoint II Quick Reference Information

Teleco
Teleco TVNRG868E04 Installer instruction manual
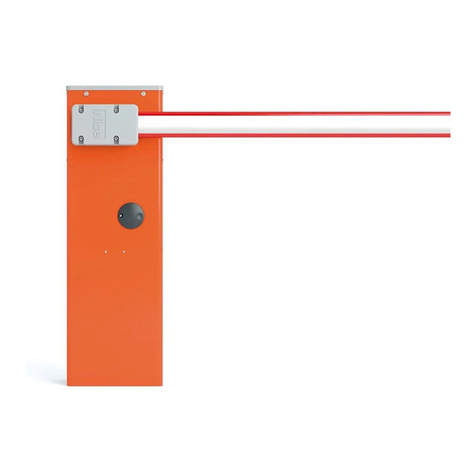
Nice
Nice WIDE S Instructions and warnings for installation and use

Taylor Made Environmental
Taylor Made Environmental Cruisair SMX II Installation & operation
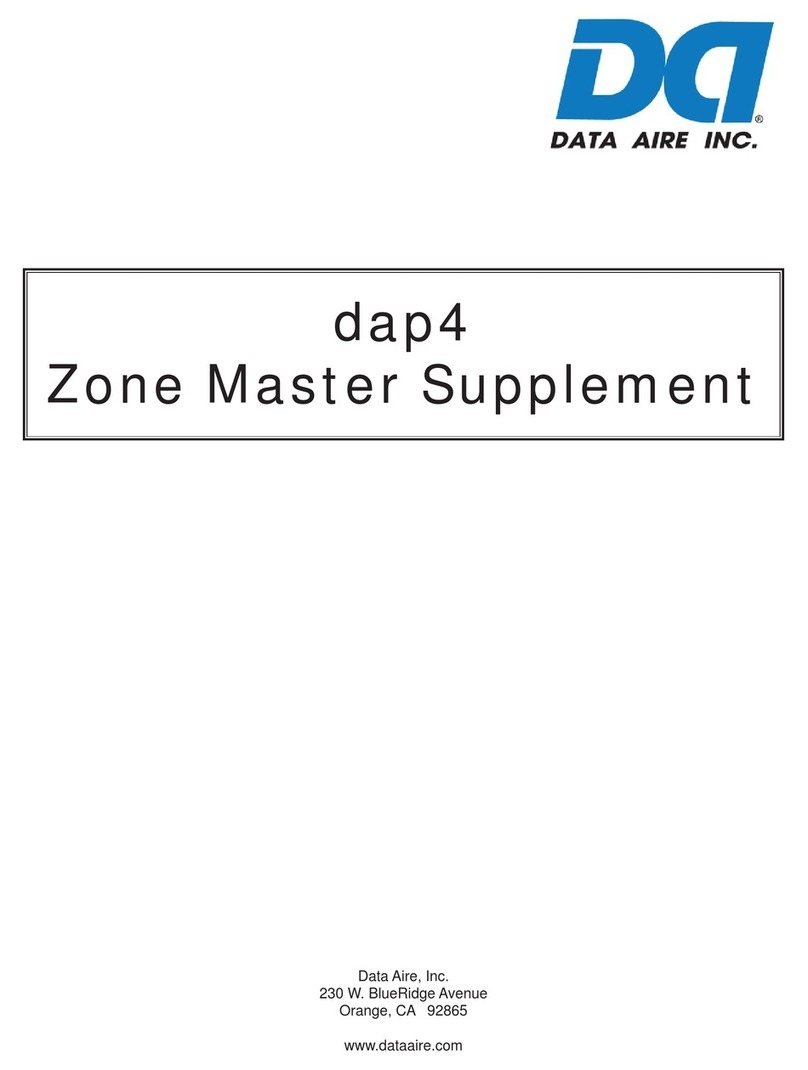
Data Aire
Data Aire dap4 touch Supplement manual
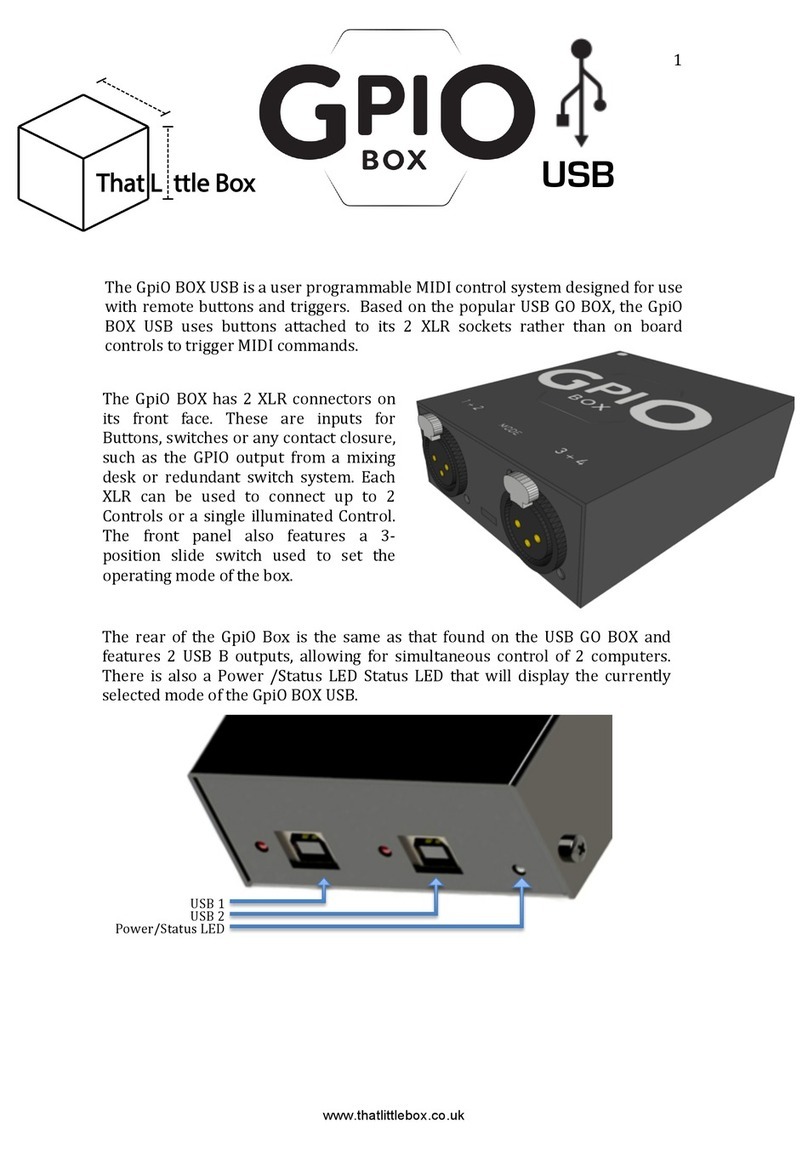
That Little Box
That Little Box GpiO BOX USB manual
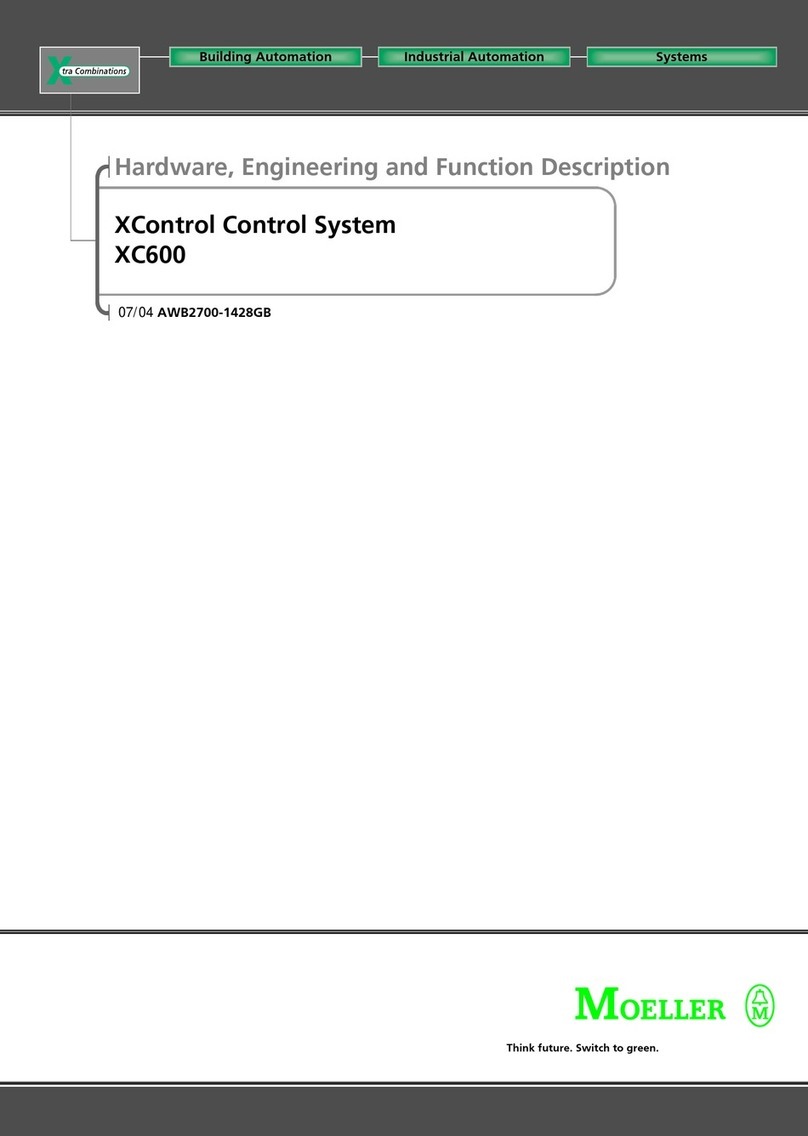
Moeller
Moeller XControl XC600 Hardware, Engineering and Function Description
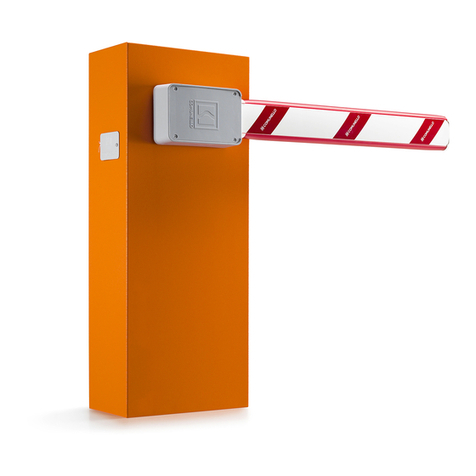
Comunello
Comunello BORDER 400 Installation and user manual
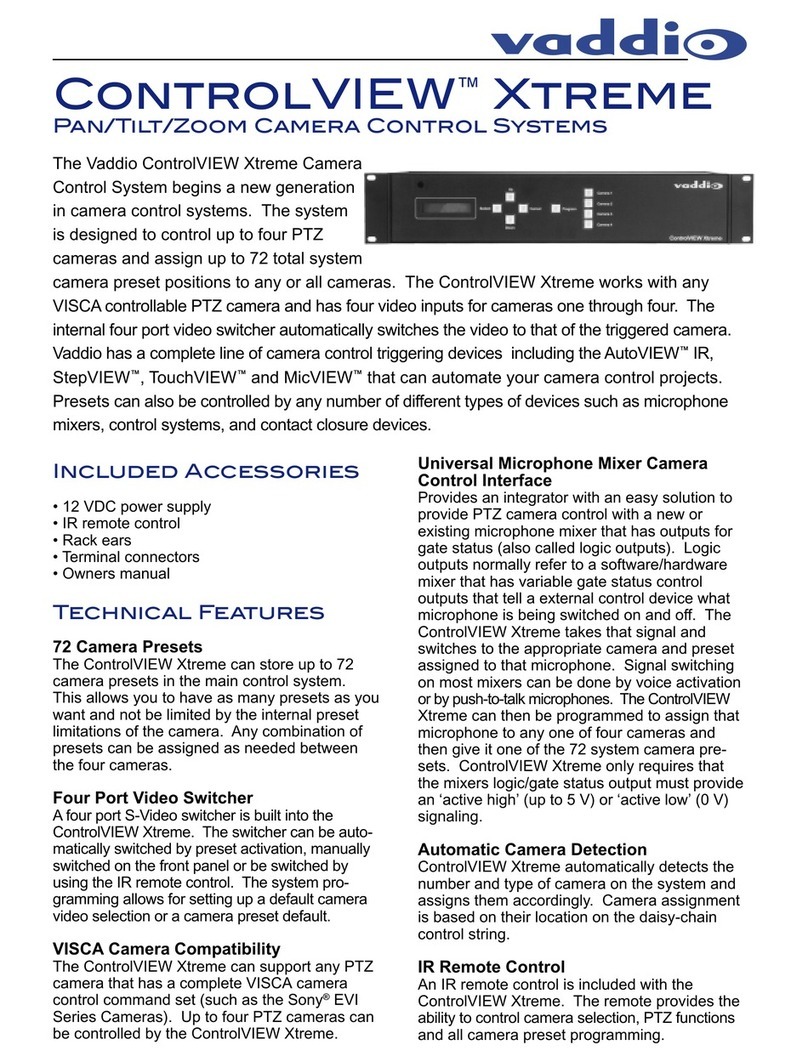
VADDIO
VADDIO ControlVIEW Xtreme manual
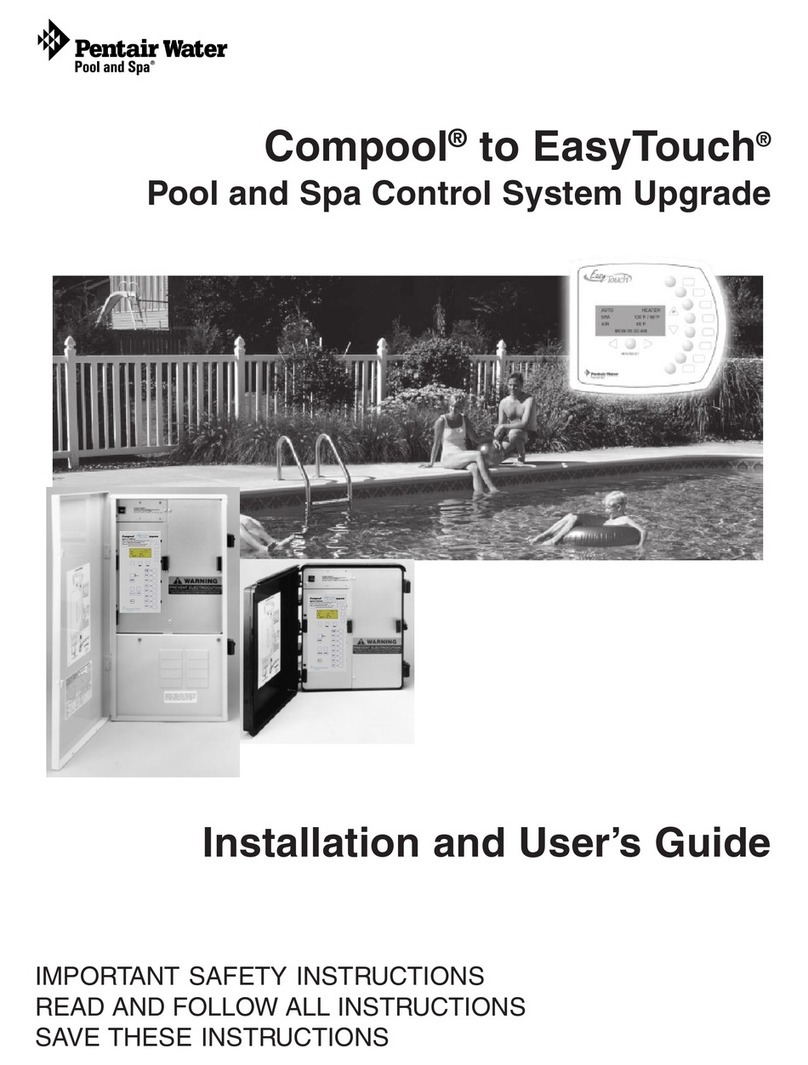
Pentair Pool Products
Pentair Pool Products Compool Installation and user guide
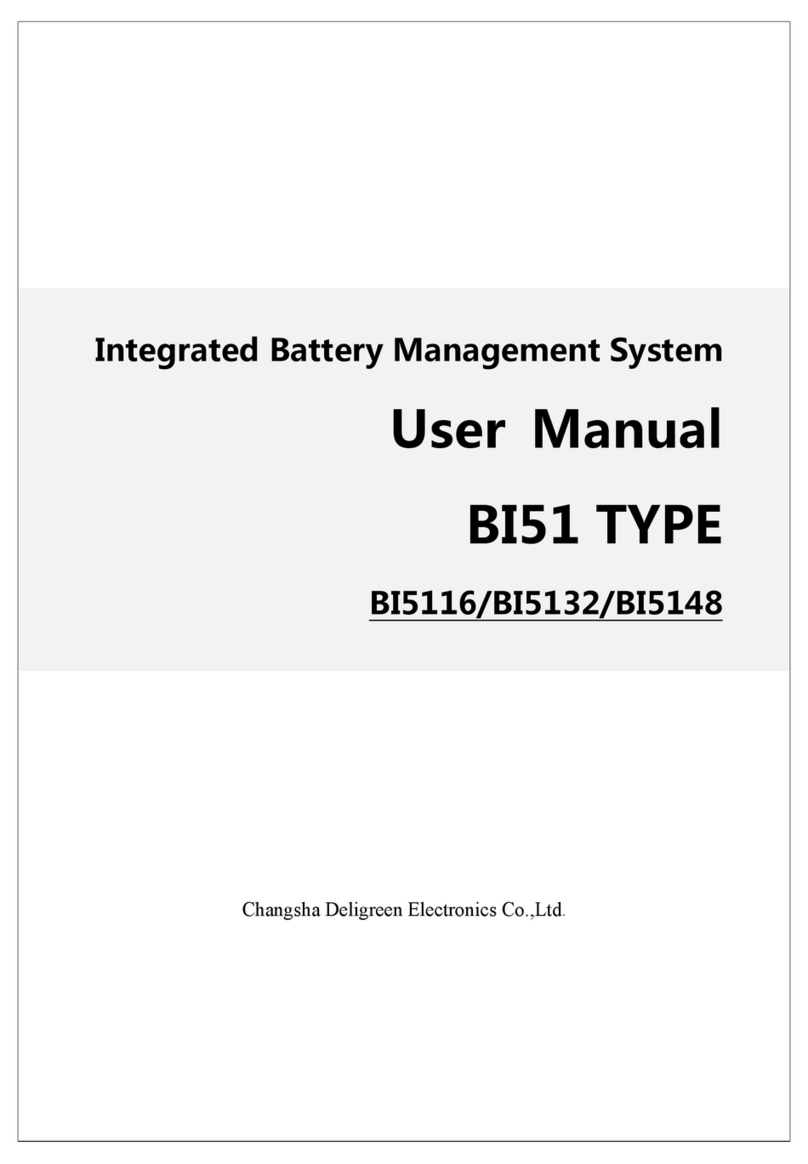
Deligreen
Deligreen BI51 user manual
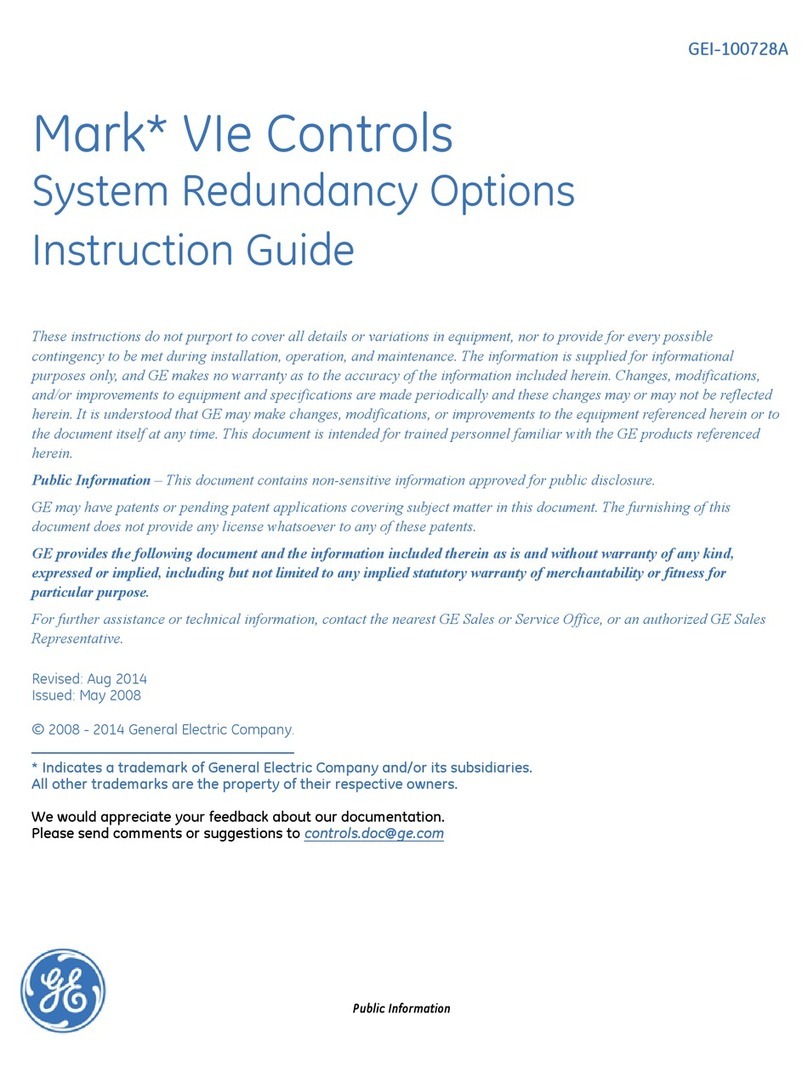
GE
GE Mark VIe Instruction guide