Gemu 1435 ePos User manual

1435
e
Pos
1435
e
Pos
Intelligent Positioner
Status 01.06.16
From version 2.0.0.3
OPERATING INSTRUCTIONS
GB

2 / 48
1435
e
Pos
Quick commissioning of the GEMÜ 1435 ePos:
Prerequisites:
● Mounted to the valve
● Air supply, max. 6bar, connected
● 24 V DC supply voltage connected
● Set value signal need not be connected
● For correct commissioning proceed as described in the following flow chart:
The GEMÜ 1435 ePos
positioner is ready for
operation and reacts to
the externally specified
set value.
P = 45.4
D: NO INIT
Nach dem Einschalten
PRESS -> FOR 3s
C: CONFIG
länger als 3s drücken
1: SETPOINT
NO INIT
2: INIT ALL
PRESS -> FOR 3s
2: INIT ALL P = XX.X
2: INIT RUN 1
P = XX.X
2: INIT RUN 2
up -> down
2: INIT RUN 3
down -> up
2: INIT RUN 3
P = XX.X
2: INIT RUN 4
P = XX.X
2: INIT RUN 5
INIT OK
2: INIT ALL
1: SETPOINT
PRESS -> FOR 3s
C: CONFIG
X = 55.5
B: MANUAL. W = 55.5
.. .... X = 30.5
A: AUTO. W = 30.5
länger als 3s drücken
press for more than 3 seconds
press for more than 3 seconds
After switching on

3 / 48 1435
e
Pos
Contents
1 General safety information 4
1.1 General information 4
1.2 Explanation of symbols and signs 4
1.3 Safety notes 4
1.4 Correct use 5
1.5 Information on use in damp conditions 5
1.6 Mounting position 5
1.7 Tools required for installation and assembly 5
2 Manufacturer's information 5
2.1 Transport 5
2.2 Delivery and performance 5
2.3 Storage 5
2.4 Function 5
2.5 Fail safe function 5
3 Diagrammatic view of the inputs and outputs 6
4 Mechanical mounting 7
4.1 Mounting to linear actuators 7
4.1.1 Preparation of the actuator 7
4.1.2 Assembling the travel sensor 7
4.1.3 Mounting the positioner 7
4.2 Mounting to quarter turn actuators 7
4.2.1 Preparation of the actuator 7
4.3 Remote mounting 8
5 Pneumatic connections 8
5.1 Replacing the filter strainers 8
6 Electrical connections 8
6.1 Version with terminals (standard) 8
6.2 Version with connector (optional) 9
6.3 Checking the mounted assembly 9
7 Operation 9
7.1 Operating and display elements 9
7.2 Operator interfaces 9
7.2.1 System mode "CLASSIC" (simple basic functions) 9
7.2.2 System mode "ADVANCED"
(extended diagnostic facilities) 9
7.2.3 Changing the operator interfaces 10
7.3 Menu levels 10
7.3.1 Working level (AUTO and MANUAL) 10
7.3.2 Configuration level (CONFIG) 10
8 Commissioning 10
8.1 General information 10
8.2 Initial commissioning 10
8.2.1 Without factory setting
(when supplied without a valve) 10
8.2.2 With factory setting (positioner supplied mounted
to the valve) 12
9 System mode CLASSIC 13
9.1 Operating modes 13
9.1.1 Automatic operation (A:)AUTO) 13
9.1.2 Manual operation (B: MANUAL) 13
9.1.3 Configuration (C: CONFIG) 13
9.1.3.1 Parameter setting - new positioners
(from software V2.0.0.0) 13
9.1.3.2 Parameter setting - old positioners
(up to software V1.3.1.8) 13
9.2 Parameter table 14
9.3 Explanation of parameters 15
10 System mode ADVANCED 18
10.1 Menu level 18
10.1.1 Automatic operation (AUTO) 18
10.1.2 Select operating mode (Mode) 18
10.1.3 Manual operation (MANUAL) 18
10.1.4 Configuration (SETUP) 18
10.2 Configuration menu (SETUP) 19
10.2.1 Menu structure 1. Service 19
10.2.2 Menu structure 2. SetBasics 19
10.2.3 Menu structure 3. SetFunction 20
10.2.4 Menu structure 4. SetCalibration 20
10.2.5 Menu structure 5. Communication 20
10.2.6 Menu structure - Complete overview 21
10.3 Parameter table 22
11 Explanation of parameters 24
11.1 Service 24
11.1.1 Scanning the input and output signals 24
11.1.2 Activating or deactivating the user access 25
11.1.3 Reading out, deleting and deactivating error
messages 26
11.1.4 Display serial number, software version and enter
TAG no. 26
11.2 2 SetBasics 27
11.2.1 Definition of set value input 27
11.2.2 Reset 27
11.2.3 Initialisation 27
11.2.4 Making the display settings 29
11.3 3 SetFunction 29
11.3.1 Setting the positioner parameters 29
11.3.2 Setting the dead zone 30
11.3.3 Setting alarm output functions and switch points 31
11.3.4 Setting error output functions 31
11.3.5 Setting position feedback function and limiting
values 32
11.3.6 Storing parameter sets 32
11.4 4 SetCalibration 33
11.4.1 Setting direction of actual value display 33
12 Error messages 35
13 Table for changes to the factory settings 36
14 Disposal 37
15 Returns 37
16 Information 37
17 Technical data 38
18 Order data 39
19 Fail safe function 45
List of terms 46

4 / 48
1435
e
Pos
1 General safety information
Please read the following notes carefully and observe them.
1.1 General information
Important requirements to ensure the perfect function of this
GEMÜ 1435 ePos:
● Correct transport and storage
● Installation and commissioning by trained personnel
● Operation according to these operating instructions
● Recommended maintenance
The GEMÜ 1435 ePos must be used in accordance with
these directions. All information in these operating
instructions regarding operation, servicing and
maintenance must be observed and applied. If the
information is not observed, the operator's guarantee
rights and the manufacturer's legal liability cease. This
could also lead to the loss of any rights to compensation.
The manufacturer shall undertake no responsibility
for the GEMÜ 1435 ePos if these safety notes are not
observed.
Therefore, you must observe:
● the contents of these operating instructions
● the relevant safety regulations for the installation and
operation of electrical systems
● that this device must not be used in potentially explosive
areas.
The regulations, standards and guidelines named in these
operating instructions are only applicable in Germany. If
the GEMÜ 1435 ePos is used in other countries, the local
applicable regulations must be observed.When dealing with
harmonised European norms, standards and guidelines, these
apply within the Single European Market.The operator must
also adhere to national rules and guidelines, if applicable.
The descriptions and instructions in these operating
instructions refer to the standard version.
All rights including copyright and industrial property
rights are expressly reserved.
The safety information does not take into account:
7Unexpected incidents and events, which may occur during
installation, operation and servicing.
7Local safety regulations which must be adhered to by the
operator and by any additional installation personnel.
In cases of uncertainty:
7Consult the nearest GEMÜ sales office.
1.2 Explanation of symbols and signs
Important information is identified in these operating
instructions by the following symbols:
DANGER
This symbol indicates danger.There is danger to
life or health of persons and/or considerable
material damage can occur, if the instructions
given here are not followed.
Slight bodily injury and damage to property
can occur, if the safety information given in
connection with this symbol is not observed.
This symbol indicates notices which
give important information regarding your
GEMÜ 1435 ePos
1.3 Safety notes
DANGER
● Only qualified and trained personnel should
assemble, electrically connect and commission
the GEMÜ 1435 ePos. Use qualified personnel
for operation, servicing, inspection and
assembly.The areas of responsibility, the
monitoring of personnel and their competence
areas should be defined precisely by the
operator. Train personnel with insufficient
knowledge or, if necessary, have them trained
by the manufacturer / supplier on order of the
operator. Ensure that all members of personnel
understand the safety instructions.
● Ensure that the power supply equipment is
electrically safe.
● Ensure that the electrical values are correct.
If the safety information is disregarded then persons, the
environment and the GEMÜ 1435 ePos may be endangered.
Furthermore, failure to observe the safety information may lead
to a complete loss of claims rights.
Adhere to legal regulations.

5 / 48 1435
e
Pos
1.4 Correct use
7The GEMÜ 1435 ePos serves solely as a positioner and
must be used according to the data sheet.
7The GEMÜ 1435 ePos must not be used outdoors without
heating element.The version with heating element may only
be used outdoors in a rain-protected area.
7Any other use or use above and beyond this is not
permitted. GEMÜ shall not be liable for any consequential
damage which is solely at the user's risk.
7Please pay attention to the pertinent technical safety
regulations when planning both the use and operation of the
device. The designer, plant constructor or operator is always
responsible for positioning and mounting of the GEMÜ
1435 ePos.
1.5 Information on use in damp conditions
Under no circumstances whatsoever may the
GEMÜ 1435 ePos be cleaned with a high pressure
cleaning device because the protection class IP 65
is not sufficient for this.
The following information is intended to help when mounting
and operating the GEMÜ 1435 ePos in damp conditions:
● The GEMÜ 1435 ePos must be protected from direct impact
of rain water.
● Lay cables and and pipework so that condensate or rain
water that remains on the pipework / cables cannot enter
the cable glands of the M12 plugs of the GEMÜ 1435 ePos.
● Check that all cable glands of the M12 plug and the fittings
are mechanically secured.
● Check housing seal for correct position and damage each
time before closing.
● Close keypad cover properly immediately after use.
● Lock all covers (throttles, check valve) immediately after use.
1.6 Mounting position
The mounting position of the GEMÜ 1435 ePos is optional.
When mounted upside down it must be ensured that no liquids
or dirt can enter the outlet of the pressure relief valve.
1.7 Tools required for installation and assembly
The tools required for installation and assembly are not
included in the scope of delivery.
Open-end wrench SW10 and SW27
Allen key 3 mm and 4 mm
Electric screwdriver 3.5 mm
2 Manufacturer's information
2.1 Transport
lOnly transport the positioner by suitable means. Do not
drop. Handle carefully.
lDispose of packing material according to relevant local or
national disposal regulations / environmental protection
laws.
2.2 Delivery and performance
lCheck that all parts are present and check for any damage
immediately upon receipt.
lThe scope of delivery is apparent from the dispatch
documents and the design from the order number.
lThe performance of the positioner is checked at the factory.
● If the GEMÜ 1435 ePos positioner is ordered as a complete
unit with a valve, these parts and the accessories belonging
to them are supplied ready assembled and factory set. The
GEMÜ positioner is then ready for immediate operation.
2.3 Storage
lStore the positioner free from dust and moisture in its
original packaging.
lAvoid UV rays and direct sunlight.
lMaximum storage temperature: 60 °C.
2.4 Function
The GEMÜ 1435 ePos is an intelligent electro-pneumatic
positioner designed for mounting to pneumatic linear and
quarter turn actuators.
The positioner can be directly mounted to the actuator using
a suitable mounting kit.The mounting kit contains both the
mounting bracket / adapter and the appropriate travel sensor
with the relevant fastening screws.
Remote mounting is also possible, whereby the mounting
bracket / adapter is not needed.
The travel sensor measures the current position of the valve
and relays this position to the electronic control system of the
GEMÜ 1435 ePos which correlates the actual value of the
valve with the set value and adjusts the valve if necessary.
The information required can be called-up on the two-line
display of the GEMÜ 1435 ePos. Self-explanatory help texts
that explain the meaning of the parameters called-up are also
displayed.
The GEMÜ 1435 ePos is operated using four keys.
2.5 Fail safe function
The GEMÜ 1435 ePos has a fail safe function which ensures
that the outlets are vented during a pneumatic and electrical
power supply failure.
This fail safe function is not a substitute for specific plant safety
requirements.The GEMÜ 1435 ePos is not a safety control
system.

6 / 48
1435
e
Pos
3 Diagrammatic view of the inputs and outputs
Additional functions of the
positioner:
Automatic initialisation
Easy to understand help texts
for operating in system mode
"ADVANCED"
Stroke limiter and seal adjuster
Close tight function
Selectable or settable
characteristic curve
Safety position "fail safe"
Freely programmable alarm
outputs
Etc.
Operating parameters
Set value input for positioning
0-10 V
0-20 mA
4-20 mA
Actual value input for position
control using the travel sensor
Supply voltage
24 V DC
InputsSupply
Actual value output of
positioner
0-10 V
4-20 mA (optional)
Binary outputs
24 V DC
Outputs
Operation
Keypad

7 / 48 1435
e
Pos
4 Mechanical mounting
When operating with an actuator of control function
2 (opened by sping force), fit an external throttle
(order number 1435 DR6Z) into the air supply line
(connection P).
4.1 Mounting to linear actuators
4.1.1 Preparation of the actuator
1. The actuator must be in the zero position (actuator vented).
2. Should there be an optical position indicator in the actuator
(a red spindle), it must be removed.
3. Should there be a thread cover in the top of the actuator,
remove this too.
4.1.2 Assembling the travel sensor
DANGER
Pretensioned spring!
äDamage to the device.
● Slowly relax spring.
Attention: Damage to the spindle surface may lead
to failure of the travel sensor!
In the standard version the travel sensor consists of the travel
sensor, a compression spring and an operating bush (on larger
actuators a guide bush is also supplied which is fitted behind
the compression spring).
Travel sensor a
a
Spindle Spring
Operating bush
1. Pull out the spindle of the travel sensor up to the limit stop.
2. Push the spring over the spindle.
3. Fix the spindle at point a
(the spindle must not be damaged during this pro-
cess).
4. Screw the operating bush onto the spindle.
4.1.3 Mounting the positioner
1 Mounting bracket
2 Actuator
3 Travel sensor
4 Hexagon
5 M6 screws
6 M12 cable gland
7 M4 screws
7
2
4
3
5
61
1. For control function 1 (normally closed) place the mounting
bracket 1between the actuator head 2and travel sensor 3
and fix by turning the travel sensor at the hexagon 4.
2. For control function 2 (normally open) and control func-
tion 3 (double acting) place the mounting bracket 1
between the threaded adapter and travel sensor 3and also
place a sealing ring there. Fix by turning the travel sensor at
the hexagon 4.
3. Attach the positioner to the mounting bracket 1with 2 M6
screws 5.
4. Loosen screws 7on housing cover and swing the cover
open.
5. Feed cable from linear travel sensor into the M12 cable
gland 6of the positioner and connect to the terminal board
as shown in the wiring diagram (see chapter 6).
6. Then tighten the M12 gland.The cable must be held firmly
on all sides.
4.2 Mounting to quarter turn actuators
4.2.1 Preparation of the actuator
Actuator shaft (from above)
Rotary potentiometer shaft
Adapter
Rotary potentiometer connection
Butterfly disc: closed
Adapter marking
Pneumatic
connection
Potentiometer
shaft marking
Rotary potentiometer
Actuator
Butterfly
valve: open
Butterfly
valve: closed
3
1
6
2
4
1. The actuator must be in the zero position (actuator vented).
Double acting actuators should be moved to the valve
"CLOSED" position.
2. Remove the screw which retains the optical position indica-
tor.
3. Determine the turn direction of the actuator (seen from
above the turn direction of the actuator must be anticlock-
wise, when the actuator moves from the "CLOSED" to the
"OPEN" position).
4. Bolt rotary travel sensor 3to the actuator with mounting
bracket 1.
Observe correct fitting position of rotary travel
sensor to "double flats".
5. Mount positioner directly on the quarter turn actuator 2us-
ing a NAMUR adapter 4.

8 / 48
1435
e
Pos
6. Loosen screws on housing cover and swing the cover open.
7. Feed cable from linear travel sensor into the M12 cable
gland 6of the positioner and connect to the terminal board
as shown in the wiring diagram (see chapter 6).
8. Then tighten the M12 gland.The cable must be held firmly
on all sides.
4.3 Remote mounting
1. The actuator must be in the zero position (actuator vented).
2. Mount travel sensor as described in chapter 4.1 or 4.2.
3. Feed travel sensor cable into the M12 cable gland of the
positioner and connect to the terminal board as shown in
the wiring diagram (see chapter 6).
4. Then tighten the M12 gland.The cable must be held firmly
on all sides.
5 Pneumatic connections
Filter strainers are installed in the pneumatic
connectors of the positioner to protect against
rough dirt particles.They can be ordered as
spare parts with order number 1435 SFI. Each
kit contains 3 filter strainers.These filter strainers
are meant as an additional protection and do not
replace the requirement to filter all site compressed
air.
1. Make the connection between pneumatic positioner out-
let A1 (single acting) or A1 and A2 (double acting) and the
pneumatic actuator control air inlet.
2. Connect the control air supply (additional air) to the air sup-
ply connection P* (max. 6 bar or 90 psi).
A2
A1
P
R
D1
RV
D2
Connection DIN ISO 1219-1 Description
P 1 Air supply connection G1/4
R 3 Venting connection G1/4 with silencer
D1 V1 Exhaust air throttle for A1
D2 V2 Exhaust air throttle for A2*
RV V3 Non-return valve
A1 2 Working connection for process valve
A2 4 Working connection for process valve*
* only double acting type (code 3)
5.1 Replacing the filter strainers
1. Switch off pneumatic control air supply.
2. Remove connection lines.
3. Carefully remove filter strainers from holes P, A1 and A2
(only double acting version).
4. Replace filter strainers (1435 SFI).
5. Re-connect connection lines.
6. Supply pneumatic control air.
6 Electrical connections
6.1 Version with terminals (standard)
1. Connect travel sensor (if not already done).
2. Connect analogue input 0/4-20 mA or 0-10 V to the
appropriate terminals for specification of set values.
3. Connect 24 V DC supply voltage cable and potential earth.
CAUTION
Damage to the spindle surface may lead to failure of the
travel sensor!
Important:
In order to compensate for differences of earthing
potential due to plant-specific installations, a
jumper can be placed between terminals "GND"
and "Iw-".
10 V X UW+ IW+ IW- UW- X+ X-
GND 24 V
or or or gr gr gr gr gr gr bl bl gn
gr gr gr gr
A1 A2
ERR
or orange
gn green
bl blue
gr grey
Legend
10 V green
Connection of external travel sensor
X brown
white
Iw+Set value input 0/4-20 mA
Iw-
Uw+Set value input 0-10 V
Uw-
X+ Actual value output 0-10 V
4-20 mA (optional) - internal supply
X-
GND Supply voltage 24 V DC
24 V
Potential earth
A1 Alarm1, 24 V DC
A2 Alarm2, 24 V DC
ERR Error message output
GND out

9 / 48 1435
e
Pos
6.2 Version with connector (optional)
X1
X2
X1
X2
X3
X3
45
12
3
45
12
3
45
12
3
Connection Pin Signal name
X1
A-coded
M12 plug
1Uv, 24 V DC
supply voltage
2Uo, error message output,
24 V DC
3Uv, GND
supply voltage
4 Uo, alarm output 1, 24 V DC
5 Uo, alarm output 2, 24 V DC
Connection Pin Signal name
X2
A-coded
M12 plug
1 Iw+, set value input 0/4-20 mA*
2 Iw-, set value input 0/4-20 mA*
3X+, actual value output
0-10 V / 4-20 mA
4X-, actual value output
0-10 V / 4-20 mA
5 n.c.
Connection Pin Signal name
X3
A-coded
M12 socket
1 Uv, actual value supply 10 V DC
2 Usig, actual value input 0-10 V DC
3 Uv, actual value supply GND
4 n.c.
5 n.c.
* for set value input Uw = 0 - 10 V on-site rewiring is required
Important:
For a set value input signal of 0-10 V DC the
positioner must be opened and the two wires of the
set value input must be reconnected from terminals
"Iw+" and "Iw-" to terminals "Uw+" and "Uw-".
or orange
gn green
bl blue
gr grey
10 V X UW+ IW+ IW- UW- X+ X-
GND 24 V
or or or gr gr gr gr gr gr bl bl gn
gr gr gr gr
A1 A2
ERR
6.3 Checking the mounted assembly
1. Connect positioner to power and air supply.
2. The following message is displayed:
The mounted actuator can be moved to the OPEN and
CLOSED positions using the +and ـkeys.
The displayed valve position must be between 2 %
and 98 %.
7 Operation
7.1 Operating and display elements
Back key
(yellow)
2-line display, 16-digit
Forwards key
(green)
Plus key
(red) +
Minus key
(black) ـ
7.2 Operator interfaces
The GEMÜ 1435 ePos offers a choice of two different operator
interfaces (System mode).These can be selected in the
"SYSTEMMODE" parameter.
7.2.1 System mode "CLASSIC" (simple basic functions)
When "CLASSIC" is selected all available parameters are in a
sequential chain.
7.2.2 System mode "ADVANCED"
(extended diagnostic facilities)
When "ADVANCED" is selected all available parameters are
divided into different categories and into different submenus. In
addition a large number of additional parameters are available,
providing additional information and adjustments to the GEMÜ
1435 ePos .

10 / 48
1435
e
Pos
7.2.3 Changing the operator interfaces
In order to switch the operator interface from [CLASSIC] to
[ADVANCED] proceed as follows:
1. Select parameter "50: SYSTEMMODE".
2. Switch from [CLASSIC] to[ADVANCED] and do not exit the
parameter.
3. Switch off supply voltage.
4. Switch on supply voltage.
In order to switch the operator interface from [ADVANCED] to
[CLASSIC] proceed as follows:
1. Select parameter "SYSTEMMODE" in the SetBasics menu.
2. Switch from [ADVANCED] to [CLASSIC] and confirm with
"OK". Do not exit the parameter.
3. Switch off supply voltage.
4. Switch on supply voltage.
7.3 Menu levels
The GEMÜ 1435 ePos uses two menu levels.These are the
working level (AUTO and MANUAL) and the configuration level
(CONFIG).
7.3.1 Working level (AUTO and MANUAL)
The GEMÜ 1435 ePos is automatically at this level after the
supply voltage is switched on.
A:AUTO
The positioner is triggered by an external set value signal when
using the AUTO operating mode.
B: MANUAL
When MANUAL is selected the valve can be moved manually
using the +and ـkeys.
7.3.2 Configuration level (CONFIG)
Various parameters can be set at this level in order to realise
optimal adaptation to the application conditions.
8 Commissioning
● The GEMÜ 1435 ePos must not be used
outdoors without heating element.The version
with heating element may only be used outdoors
in a rain-protected area.
● The GEMÜ 1435 ePos must be protected from
direct impact of rain water.
If the GEMÜ 1435 ePos is delivered fully mounted
to a valve ex works, it is already preset at the
factory (at a control pressure of 5.5 - 6 bar without
operating pressure) and is therefore ready for
operation. A reinitialisation (see chapter 8.2)
is recommended if the plant is operated with a
different control pressure or if the mechanical
end positions have been changed (e.g. seal
replacement on the valve or actuator replacement).
1. Turn on the pneumatic air control supply (observe maxi-
mum control pressure for the positioner and the valve!)
2. Switch on supply voltage 24 V DC.
3. Specify an analogue set value 0/4-20 mA or 0-10 V.
8.1 General information
Before adjustments are made to the settings and
parameters of the GEMÜ 1435 ePos, the two
screws on the keypad cover must be undone.The
cover can be turned away by slightly pulling it out.
All parameter settings and the initialisation are
retained even in the event of voltage cutoff.
Use the and keys to reach the various operating levels
and parameters.To enter the configuration menu "C: CONFIG"
the key must be kept pressed for more than 3 seconds.
Parameters can be changed by pressing the +key and then
selecting the parameter using the key.
The value can then be changed using the +and the ـkeys.
Then the cursor must be moved to the right-hand bracket using
the key and the set value confirmed using the +key.
8.2 Initial commissioning
8.2.1 Without factory setting
(when supplied without a valve)
After assembly and all electrical and pneumatic connections,
the positioner must be initialised.
Before being initialised the positioner is in the "D: NO INIT"
operating mode.This operating state can also be reset to the
factory default setting by selecting "DEFAULT" in the menu
"3: DEFAULT STATE".
The mounted actuator can be moved to the
OPEN and CLOSED positions using the +and
ـkeys.
Pressing +and additionally ـmoves the
actuator quickly to OPEN.
Pressing ـand additionally +moves the
actuator quickly to CLOSED.
The displayed valve position must be between
0 % and 100 %.

11 / 48 1435
e
Pos
Starting automatic initialisation
P = 45.4
D: NO INIT
Nach dem Einschalten
PRESS -> FOR 3s
C: CONFIG
länger als 3s drücken
1: SETPOINT
NO INIT
2: INIT ALL
PRESS -> FOR 3s
2: INIT ALL P = XX.X
2: INIT RUN 1
P = XX.X
2: INIT RUN 2
up -> down
2: INIT RUN 3
down -> up
2: INIT RUN 3
P = XX.X
2: INIT RUN 4
P = XX.X
2: INIT RUN 5
INIT OK
2: INIT ALL
1: SETPOINT
PRESS -> FOR 3s
C: CONFIG
X = 55.5
B: MANUAL. W = 55.5
.. .... X = 30.5
A: AUTO. W = 30.5
länger als 3s drücken
The GEMÜ 1435 ePos
positioner is ready for
operation and reacts to
the externally specified
set value.
press for more than 3 seconds
press for more than 3 seconds
After switching on
Display Error cause Error elimination
PRESS <-
ERROR RUN 1
Actuator's direction cannot be established.
Cause:
a) No compressed air supply
b) Compressed air supply too low
c) Travel sensor wrongly connected
d) Valve stroke < 3mm
● Press key
a) Check compressed air supply (max.6 bar)
b) Check compressed air supply (max.6 bar)
c) Check connection assignment
d) Check valve stroke
PRESS <-
ERROR RUN 2.1
Zero point adjustment cannot be carried
out. Cause:
a) Incorrect travel sensor / mounting kit
b) Adjust quarter turn travel sensor
● Press key
Adjust valve manually, display value P must
be > 2.0 in CLOSED position.
a) Check order no.
b) Turn quarter turn travel sensor (only on
quarter turn actuators) until value P > 2.0
PRESS <-
ERROR RUN 2.2
Zero point adjustment cannot be carried
out. Cause:
a) Incorrect travel sensor / mounting kit
b) Adjust quarter turn travel sensor
● Press key
Adjust valve manually, display value P must
be < 98.0 in CLOSED position.
a) Check order no.
b) Turn quarter turn travel sensor (only on
quarter turn actuators) until value P < 98.0
PRESS <-
ERROR RUN 2.2
PRESS <-
Stroke Error
Actuator does not move. Cause:
a) No compressed air supply
b) Compressed air supply too low
c) Mechanical parts are defect
● Press key
a) Check compressed air supply (max.6 bar)
b) Check compressed air supply (max.6 bar)
c) Check mechanical parts
PRESS ->
up -> down X.X
ADJUST NOZZLES (S)
THEN PRESS <-
up -> down
2: INIT RUN 3
Travel time (OPEN – CLOSED) of valve less
than 1 second
A2
A1
P
R
D1
RV
D2
● Press key
● Adjust throttle D1 (on double acting
actuators throttles D1 and D2)
-+
● Press key
● Repeat if necessary until travel time > 1
second
PRESS ->
down -> up X.X
ADJUST NOZZLES (S)
THEN PRESS <-
down -> up
2: INIT RUN 3
Travel time (CLOSED – OPEN) of valve less
than 1 second
A2
A1
P
R
D1
RV
D2
● Press key
● Adjust throttle D1 (on double acting
actuators throttles D1 and D2)
-+
● Press key
● Repeat if necessary until travel time > 1
second

12 / 48
1435
e
Pos
Display Error cause Error elimination
Old positioners (up to software
V1.3.1.8)
Leakage RUN 4
PRESS <-
Leakage in the system ● Press key
● Remove leakage
● Restart automatic initialisation
New positioners (from software
V2.0.0.0)
PRESS ->
LEAKAGE
REMOVE LEAKAGE
THEN PRESS <-
REPEAT CONTINUE
<- OK ESC
P = XX.X
2: INIT RUN 5
Leakage in the system ● Press key
● Remove leakage
● Press key
● Press key for another test
● Press +key to skip the leakage test
ATTENTION! Skipping the leakage test
may lead to bad control characteristics and
increased wear.
8.2.2 With factory setting (positioner supplied mounted to the valve)
PRESS -> FOR 3s
C: CONFIG
X = 55.5
B: MANUAL W = 55.5
X = 30.5
A: AUTO W = 30.5
X = 55.5
B: MANUAL [W = 55.5]
"A: AUTO" appears in the display.The positioner is ready for operation.
To adjust the valve manually, press the key 1x. "B: MANUAL" appears.
Pressing the +key opens a bracket at the set value. The digit to be changed in the value must be selected using the key and
set using the +or ـkeys. Then the cursor must be moved to the right-hand bracket using the nd the set value confirmed
using the +key.
The positioner must be initialised again after
replacing the valve or exchanging the valve seals.
Proceed as described in chapter 8.2.1.

13 / 48 1435
e
Pos
9 System mode CLASSIC
9.1 Operating modes
9.1.1 Automatic operation (A:)AUTO)
Automatic operation is the normal operating mode. The initialised positioner responds to set value changes and adjusts the valve
accordingly.The +and ـkeys have no function in this operating mode.
The current position (x) is shown as a percentage in the display and also as a bar chart.
The lower line shows the current operating mode and at the right is the current set value (w) in percent.
By pressing the key the operating mode "B: MANUAL" is reached.
9.1.2 Manual operation (B: MANUAL)
With manual mode the valve can be adjusted manually. Pressing the +key opens a bracket at the set value. The digit to be
changed in the value must be selected using the key and set using the +or ـkeys. Then the cursor must be moved to the
right-hand bracket using the nd the set value confirmed using the +key.The valve is then moved into the set position.
By pressing the key the operating mode "C: CONFIG" is reached.
9.1.3 Configuration (C: CONFIG)
Various parameter values of the positioner can be changed in the configuration menu.To reach the configuration menu the
parameter "C: CONFIG" must be selected in the working level and then the key must be kept pressed for more than 3 seconds.
The parameter value appears in the top line, the name and number of the parameter appear in the bottom line. Operation is as
shown in the picture below.
9.1.3.1 Parameter setting - new positioners (from software V2.0.0.0)
PRESS -> FOR 3s
C: CONFIG
4...20 mA
1: SETPOINT
NO INIT
2: INIT ALL
länger als 3s drücken
[ 4...20 mA]
<- OK ESC
[ 4...20 mA]
<- -> + -
[ 0...10 V]
<- -> + -
[ 0...10 V]
<- OK ESC
0...10 V
1: SETPOINT
DEFAULT
3: DEFAULT STATE
PRESS -> FOR 3s
2: INIT ALL
PRESS -> FOR 3s
3: DEFAULT STATE
...
press for more than 3 seconds
9.1.3.2 Parameter setting - old positioners (up to software V1.3.1.8)
0..10V
1: SETPOINT
0..20mA
1: SETPOINT
4..20mA
1: SETPOINT
PRESS -> FOR 3s
2: INIT ALL
NO INIT
2: INIT ALL
PRESS -> FOR 3s
3: DEFAULT
DEFAULT
3: DEFAULT STATE
FALL
11: X-DIRECTION
RISE
11: X-DIRECTION
Press -> For 3s
C: CONFIG

14 / 48
1435
e
Pos
9.2 Parameter table
Display Function Value range Unit Factory setting
1:SETPOINT Type of set value
0..10V
0..20mA
4..20mA
V
mA
mA
4..20mA
2:INIT ALL Starting automatic initialisation NO INIT
Init OK – NO INIT
3:DEFAULT STATE Return to factory setting NO DEFAULT
DEFAULT – DEFAULT
11:X-DIRECTION Direction of X display and actual value
output
RISE
FALL RISE
12:ALARM FUNCT Determines the function of the alarm
outputs (ALARM1 und ALARM 2)
OFF
min/max
min/min
max/max
OFF
13:LEVEL ALARM1 Switch point of alarm 1 0.0...100.0 10.0
14:LEVEL ALARM2 Switch point of alarm 2 0.0...100.0 90.0
15:ERROR FUNCTN Determines the function of the error
message output (ERROR)
ERROR
ERROR+INACTIVE
RANGE
ERROR + RANGE
ERR+RANGE+INAC
ERROR
+ RANGE
16:ERROR TIME Valve travel time monitoring
(Error message output)
auto
0...100 S auto
17:ERROR LEVEL Maximum system deviation
(Error message output)
auto
0.0...100.0 % auto
18:RANGE FUNCTN Range monitoring of set value input
< 4 mA
> 20 mA
<4mA or >20mA
mA <4mA or
>20mA
21:MIN POSITION Limits the CLOSED position of the valve
min. position 0.0...100 % 0.0
22:MAX POSITION Limits the OPEN position of the valve max.
position 0.0...100 % 100.0
23:CLOSETIGHT Determines the function of the close tight
function
no
min
max
min & max
no
24:SETP DIRECTN Direction of set value NORMAL
INVERSE NORMAL
25:SETP RAMP Ramp function - set value auto
0...400 S 0
26:SPLIT START Split range (set value range) start 0.0 ... 90 % 0.0
27:SPLIT END Split range (set value range) end 10 ... 100 % 100
28:SETP FUNCTN Defines the function of the control
characteristic
Linear
1:25
1:50
free
Linear
30:FREE 0 %
31:FREE 10 %
32:FREE 20 %
33:FREE 30 %
34:FREE 40 %
35:FREE 50 %
36:FREE 60 %
37:FREE 70 %
38:FREE 80 %
39:FREE 90 %
40:FREE 100 %
Definition of the programmable
characteristic curve
11 calibration points
0...100 %
2
3
4.4
6.5
9.6
14.1
20.9
30.9
45.7
67.6
100
42:DEADBAND Size of dead band auto
0.0...10.0 % 1.0
43:PROP GAIN Proportional amplification (PD controller) Kp = 0.1...100.0 1.0
44:DERIV TIME Differential time consant (PD controller) Tv = 0.00s...10.00s S 0.1
45:FIELDBUS SETP.ANALOG
FIELDBUS SETP.ANALOG
46:RELEASE VXX Software release V X.X.X.X
50:SYSTEMMODE Defines the type of operator interface CLASSIC
ADVANCED CLASSIC

15 / 48 1435
e
Pos
9.3 Explanation of parameters
1: SETPOINT
Range of analogue set value input (Voltage: 0-10 V or power:
0/4-20 mA)
2: INIT ALL
Initialisation
Automatic initialisation is started by using +or ـand
pressing the key (> 3 sec).The progress of the initialisation
is shown with "run 1" to "run 5" in the display.
During the initialisation process the positioner optimises its
control parameters for controlling the valve concerned.
3: DEFAULT STATE
Default setting
Return to factory setting and resetting initialisation. The
positioner is set to "DEFAULT" by using +or ـand pressing
the key (> 3 sec).
After "Default" the positioner must be initialised
again. All actuation parameters established so far
are deleted.
11: X-Direction
Correcting variable direction
Here the display direction (rising or falling) and the position
feedback can be adjusted.
Pressuriza-
tion state
outlet A1
X-Direction Displayed
value
Allocated
actual
position x
vented
pressurized
rise 0 %
100 %
0 %
100 %
vented
pressurized
FALL 100 %
0 %
100 %
0 %
12: ALARM FUNCTN
Activates or deactivates the alarm function
The reaction of the alarms (limiting contacts) relates to the
POSITION measurement (mechanical distance).
x = current actual value
min/max:
Position State
output A1
State
output A2
x < Level Alarm1 < Level Alarm2 24V 0V
Level Alarm1 < x < Level Alarm2 0V 0V
Level Alarm1 < Level Alarm2 < x 0V 24V
min/min:
Position State
output A1
State
output A2
x < Level Alarm1 < Level Alarm2 24V 24V
Level Alarm1 < x < Level Alarm2 0V 24V
Level Alarm1 < Level Alarm2 < x 0V 0V
max/max:
Position State
output A1
State
output A2
x < Level Alarm1 < Level Alarm2 0V 0V
Level Alarm1 < x < Level Alarm2 24V 0V
Level Alarm1 < Level Alarm2 < x 24V 24V
13: LEVEL ALARM 1
Switch point for Alarm 1. When the switch point has been
reached, digital output A1 (24V DC output) is switched.
14: LEVEL ALARM 2
Switch point for Alarm 2. When the switch point has been
reached, digital output A2 (24V DC output) is switched.
15: ERROR FUNCTN
Function of error message output (24V DC output)
Setting ERROR
TIME
ERROR
LEVEL
RANGE
FUNCTN
C:CONFIG
ERROR X X
ERROR+
INACTIVE X X X
RANGE X
ERROR+
RANGE X X X
ERR+RANGE+
INAC X X X X
16: ERROR TIME
Monitoring time for setting the error messages (10 x travel
time).The set value (s) serves as a specified value for the time
within which the positioner must have reached the idle state.
The associated trigger threshold is specified with parameter
17. When the set time has been exceeded the error message
output ERR is set at 24 V DC.
17: ERROR LEVEL
Trigger threshold of error message
Here a value (%) can be set for the permissible size of system
deviation for triggering the error message.
If parameters 16 and 17 are both set to "Auto" the error
message is set if the slow-travel zone has not been reached
within a set time.This time is 10x (parameter value AUTO) the
initialisation travel time.
18: RANGE FUNCTN
Range monitoring of the set value signal
Here it is possible to set whether the RANGE error signal is
triggered when it falls below 4mA (cable break monitoring) or
exceeds 20 mA (short circuit monitoring).
21: MIN POSITION
Limits the CLOSED position of the valve
This function is equivalent to a mechanical seal adjuster.
22: MAX POSITION
Limits the OPEN position of the valve
This function is equivalent to a mechanical stroke limiter.
The mechanical regulating distance (from limit stop
to limit stop) is limited to the set values with the
parameters MIN POSITION and MAX POSITION.
That way the actuator's mechanical positioning
range range can be limited.

16 / 48
1435
e
Pos
0
80
60
40
20
100
100
80
60
40
20
Physical
stroke
x [%]
Unlimited stroke
Limited stroke
Set value w [%]
Max
Pos
Min
Pos
If parameter 23: CLOSETIGHT is activated the
actuator is vented at a set value of < 0.5 %, even if
there is a set MIN POSITION of, for example, 10 %.
With a set value > 1.5 % the actuator is moved
back to 10 %.
With a set value > 99.5% the actuator is opened
completely, even if the MAX POSITION is set to,
for example, 90 %.With a set value < 98.5 % the
actuator is moved back to 90 %.
23: CloseTight
'Close tight' variables
With this function the valve can be moved into the seat using
the maximum possible actuating force (spring force).The
close tight function can be activated for one end or both end
positions. CLOSE TIGHT becomes effective when the set
value falls below 0.5 % or exceeds 99.5 %.
The switch back hysteresis is 1 %.
0
98,5
1,5
0,5
99,5
100
100
80
60
40
20
Hub x [%]
Sollwert w [%]
Stroke x [%]
Set value w [%]
24: SETP DIRECTN
Set value direction
Setting the set value direction serves to reverse the direction
of the set value. It is mainly required for split-range operation
and for single acting actuators with the fail safe "OPEN" setting
(control function 2).
Stroke x [%]
Set value w [%]
Control function 2
Control function 2
Control function 1
NORMAL NORMAL
INVERSE
OPEN
CLOSED
25: SETP RAMP
Set value ramp
The set value ramp is effective during automatic operation and
limits the speed of change of the effective set value. When
switching over from manual to automatic operation the effective
set value is matched to the set value on the unit via the set
value ramp.
In the position SETP RAMP = auto the slower of the two travel
times which have been established during initialisation is used
for the set value ramp.
26: SPLIT START
Set value split range start
27: SPLIT END
Set value split range end
Parameters 26 and 27 in conjunction with parameter 24 serve
to limit the effective set value range. In this way split range
tasks with the curves
rising / falling
falling / rising
falling / falling
rising / rising
are resolved.
Stroke x
Set value
w
Set value range
Positioner 1 Positioner 2
Set value range
The difference between SPLIT START and SPLIT
END values must be > 10 %.
28: SETP FUNCTN
Set value function
With this function non-linear valve characteristics can be
linearised and with linear valve characteristics any flow
characteristics can be reproduced.
Four valve characteristics are stored in the unit:
equal-percentage 1 : 25
(in CLOSED position valve remains 4 % open)
equal-percentage 1 : 50
(in CLOSED position valve remains 2 % open)
linear
free
When free is selected at 30: a characteristic with 11 calibration
points can be entered.
30: FREE 0 %
.
.
.
40: FREE 100 %
At gaps of 10 % a flow characteristic value can be allocated to
the set value calibration point concerned.These points make a
traverse with 10 straight lines, which then provides a pattern of
the valve characteristic.
Entering the set value calibration points is only
possible at 28: SETP FUNCTN = free.

17 / 48 1435
e
Pos
42: DeadBand
Positioner's dead band
The dead band shows the maximum permissible system deviation between actual value and set value.
During initialisation, on DEADBAND = Auto the dead band is matched to the requirements of the control circuit. In the other
discrete settings the fixed value for the dead band is used.
The height of the system deviation should always correspond to the requirements of the valve and the control circuit.
It is recommended that you do not set a value of < 1.0% since this could (especially for actuators with discontinuous
movement profiles) cause oscillating control characteristics.This could put a great deal of stress on the internal pilot
valves and cause them to reach the end of their service life more quickly.
Basically: the smaller the fixed value, the higher the wear and the shorter the service life.Therefore, the value should
be set only as accurate as needed.
43: PROP GAIN
Proportional amplification
Adjusting the proportional amplification Kp
Kp = 0.1...100.0
The height of the amplification should always correspond to the requirements of the valve and the control circuit.The optimum set-
ting is determined during automatic initialization but must be moved out of adjustment later if necessary.
The behaviour of the positioner is influenced as follows:
PROP GAIN
Set value larger than determined value Set value smaller than determined value
The positioner controls faster (but tends to oscillate). The positioner controls slower.
The set value is achieved in larger steps by increasing the
correcting variable.
The set value is achieved in smaller steps by decreasing the
correcting variable.
Control is less accurate. Control is more accurate.
44: DERIV TIME
Derivative action time
Adjusting the derivative action time Tv (time by which a specific correcting variable is reached earlier because of the D component
than with a pure P-positioner)
Tv = 0.00 s...10.00 s
46: RELEASE VXX
Status of the current software version V X.X.X.X
50: SYSTEMMODE
Selection of operator interface
CLASSIC
menu configuration as described in chapter 7.2 System mode
ADVANCED
menu configuration as described in chapter 7.2 System mode
In order to switch the operator interface from [CLASSIC] to [ADVANCED] proceed as follows:
1. Select parameter "50: SYSTEMMODE".
2. Switch from [CLASSIC] to[ADVANCED] and do not exit the parameter.
3. Switch off supply voltage.
4. Switch on supply voltage.
In order to switch the operator interface from [ADVANCED] to [CLASSIC] proceed as follows:
1. Select parameter "SYSTEMMODE" in the SetBasics menu.
2. Switch from [ADVANCED] to [CLASSIC] and confirm with "OK". Do not exit the parameter.
3. Switch off supply voltage.
4. Switch on supply voltage.
Lineare u. gleichprozentige Kennlinien
2,0 3,0 4,4 6,5
9,6
14,1
20,9
30,9
45,7
67,6
100,0
4,0 5,5 7,6 10,5
14,5
20,0
27,6
38,1
52,5
72,5
100,0
0
10
20
30
40
50
60
70
80
90
100
0,0
20,0
40,0
60,0
80,0
100,0
120,0
0 20 40 60 80 100 120
Sollwert w [%]
Hub x [%]
1:50
1:25
linear
Stroke x [%] Linear and Equal-Percentage characteristic control curves
Linear
Set value w [%]

18 / 48
1435
e
Pos
10 System mode ADVANCED
If the parameter "SYSTEMMODE" is set to "ADVANCED" the menu configuration is different, as are a certain number of new
parameters.
To activate the system mode "ADVANCED" the parameter "SYSTEMMODE“ must be changed to "ADVANCED" and
then the supply voltage interrupted for more than 3 seconds.
10.1 Menu level
10.1.1 Automatic operation (AUTO)
Automatic operation is the normal operating mode.The initialised positioner responds to set value changes and adjusts the valve
accordingly.The +-or ـkeys have no function in this operating mode.
The current position (x) is shown in the top right of the display and in the middle is the applied set value signal (w) as a percentage.
In the bottom line a help text is shown describing the currently selected parameter.
The SETUP menu is reached by pressing the key.
By pressing the key again the "Mode" parameter is reached.
A: W 50.0 : X 50.0 SETUP MODE Auto
10.1.2 Select operating mode (Mode)
In this parameter the "AUTO" or "MANUAL operating mode is selected.
For this, pressing the +key takes it to changing the set value, this is displayed with two brackets. Then use the key to place the
cursor under the value to be changed which is then changed with the +or ـkey.Then the cursor is placed under the last bracket
with the key. The message "OK" now appears in the bottom line of the display. This is now confirmed with the +
key.
Mode [ Manual]
<- OK ESC
Mode Manual
Mode [ Manual]
<- -> + -
Mode [ Auto]
<- ->+ -
Mode [ Auto ]
<- OK ESC
Mode Auto
A: W 50.0 : X 50.0 SETUP
10.1.3 Manual operation (MANUAL)
With manual mode the valve can be adjusted manually. The required set value is set using the +or ـkey.
The SETUP menu is reached by pressing the key.
10.1.4 Configuration (SETUP)
Various parameter values of the positioner can be changed in the configuration menu.To reach the configuration menu the
parameter "SETUP" must be selected in the working level and then the +key must be pressed.

19 / 48 1435
e
Pos
10.2 Configuration menu (SETUP)
Service
1
SetBasics
2
SetFunction
3
SetCalibration
4
Return
6
SETUP
A: w XX.X: x XX.X
Mode Auto
Communication
5
The configuration menu consists of five submenus with the following functions:
1. Service This menu is used to read out all information/diagnostics regarding the positioner, the connected signals
and errors that occur.
2. SetBasics SetBasics is used to set the basic settings for the GEMÜ 1435 ePos such as the initialisation, selection of
input signals and resetting to factory settings.
3. SetFunction The special positioner functions are activated or deactivated here and the control parameters set.
4. SetCalibration SetCalibration is used to set the directions of action, characteristic curves, stroke limiter and seal adjuster.
5. Communication Without function
10.2.1 Menu structure 1. Service
Diagnosis
1.3
Logout
Service
1
hrs. XXXXX:XX:XX
I w: XX.X mA
I / O Status
1.1
S/N 743984/ 1
Seriennummer
Gemü specific
1.4
Return
W. Pos X
XX.X % XX.X% Relais K1 : K2 : Err
Return
1.5
Return
Return
Valve. 1 : 2 : 3 : 4
Code: 0
Active Level: 3
(0...10000)
Logout?
OK
NewCode:1 0
0...10000
NewCode:2 0
0...10000
Warnings ON
ON...OFF
Errors ON ....
ON...OFF
Clear Error List
OK
NewCode:3 0
0...10000
1.2
V: 1.1.1.1
min - Pot - max
0,0 % 100 % Pot Abs XX.X % Pos Ctrl Out.
I
Error List
Return
TAG2
TAG1
U w: XX.X V
10.2.2 Menu structure 2. SetBasics
Init All
Return
Init All
Auto . Man ESC
Setpoint: 4-20 mA
0-20 mA
4-20 mA
0-10 V
Default: Default
Default
No Default
CalPointQty 9
1...19
D. Refresh 0.5 s
0.1...1.0 s
DLightTime 5min
1...60min
SetBasics
2
Helptext. ON
ON...OFF
HelpLanguage D
D
GB
Systemmode
CLASIC
ADVANCED
DLight On Key
On Key
On

20 / 48
1435
e
Pos
10.2.3 Menu structure 3. SetFunction
Level Alarm2 90.0 %
0.0...100.0 %
Level Alarm1 10.0 %
0.0...100.0 %
PosCtrl
SetFunction
3
Position Output
Return
Return
Return
Prop Gain 1.0
0.1...100.0
CpyParaSet OFF
P1<=W
P1=>P2
P1<=P2
P1=>P3
P1<=P3
P1=>P4
P1<=P4
Deriv Time 0.1 s
0.01...1 s
Dead Band Auto
0.0...10.0 %
Min Pos 0.0 %
0.0...100.0 %
Max Pos 100.0 %
0.0...100.0 %
Close Tight no
no
min
max
min & max
Alarm Fn OFF
OFF
min/max
min/min
max/max
Error Level... Auto
0.0...100.0 %
Error Time Auto
0.0...100.0 s
Error Functn Error
Error+Inactive
Range
Error+Range
Err+Range+Inac
Range Functn <4mA or >20mA
< 4mA
> 20mA
<4mA or > 20mA
Alarm Output
Return
Error Output
Out max 100.0 %
0.0...100.0 %
Out min 0.0 %
0.0...100.0 %
Analog Out 0-10V
0-20mA *
4-20mA *
Return
10.2.4 Menu structure 4. SetCalibration
W 0% 2.0 %
0.0...100.0 %
SetCalibration
4
Return
X-DIR: RISE
RISE...FALL
SetpDir: NORMAL
NORMAL
INVERS
W 10% 3.0 %
0.0...100.0 %
W 40% 9.6 %
0.0...100.0 %
W 90% 67.7 %.
0.0...100.0 %
W 20% 4.4 %
0.0...100.0 %
W 70% 30.9 %...
0.0...100.0 %
W 50% 14.1 %
0.0...100.0 %
W 100% 100.0 % ...
0.0...100.0 %
W 30% 6.5 %
0.0...100.0 %
W 80% 45.7 %...
0.0...100.0 %
W 60% 20.9 %...
0.0...100.0 %
Setp Fn: linear
linear
1:25
1:50
free
Setp Ramp: 0s
0...400 s
Split Start: 0.0 %
0.0...100 %
Split End: 100.0 %
0.0...100 %
Return
Setp Fn
10.2.5 Menu structure 5. Communication
Communication
5
Return
Fieldbus SETP.ANALOG
SETP.ANALOG
SETP.BUS
Other manuals for 1435 ePos
1
Table of contents
Other Gemu Controllers manuals
Popular Controllers manuals by other brands
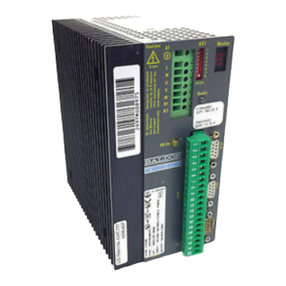
Baldor
Baldor DBSC105-AAA-1 Installation and operating manual
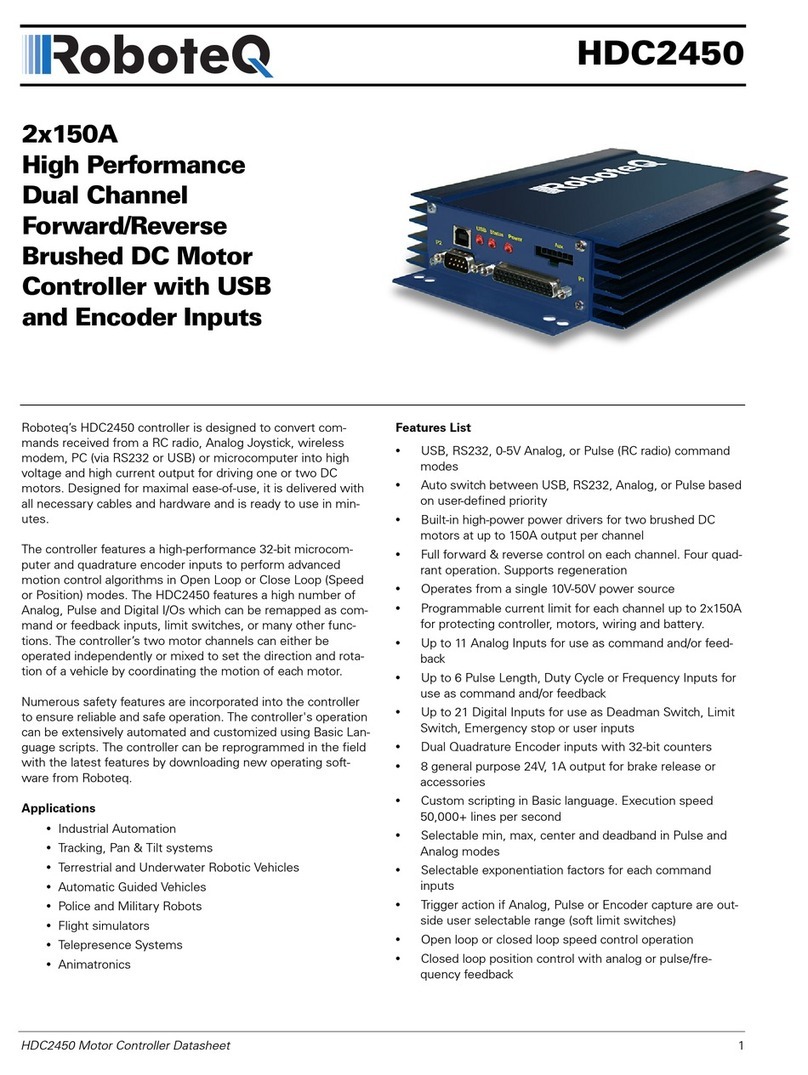
RoboteQ
RoboteQ HDC2450 datasheet
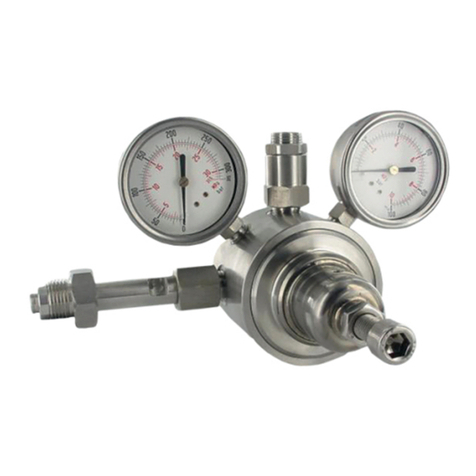
AirCom
AirCom RH3000 operating manual
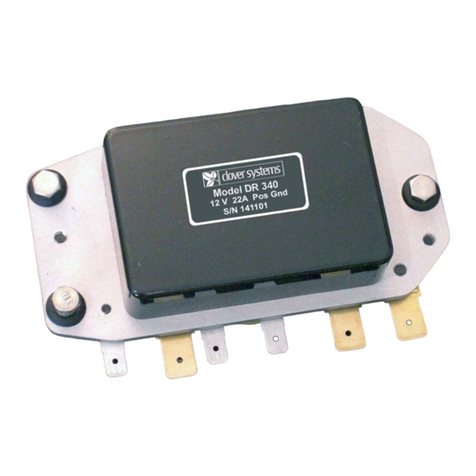
Clover Systems
Clover Systems DR340 instruction manual
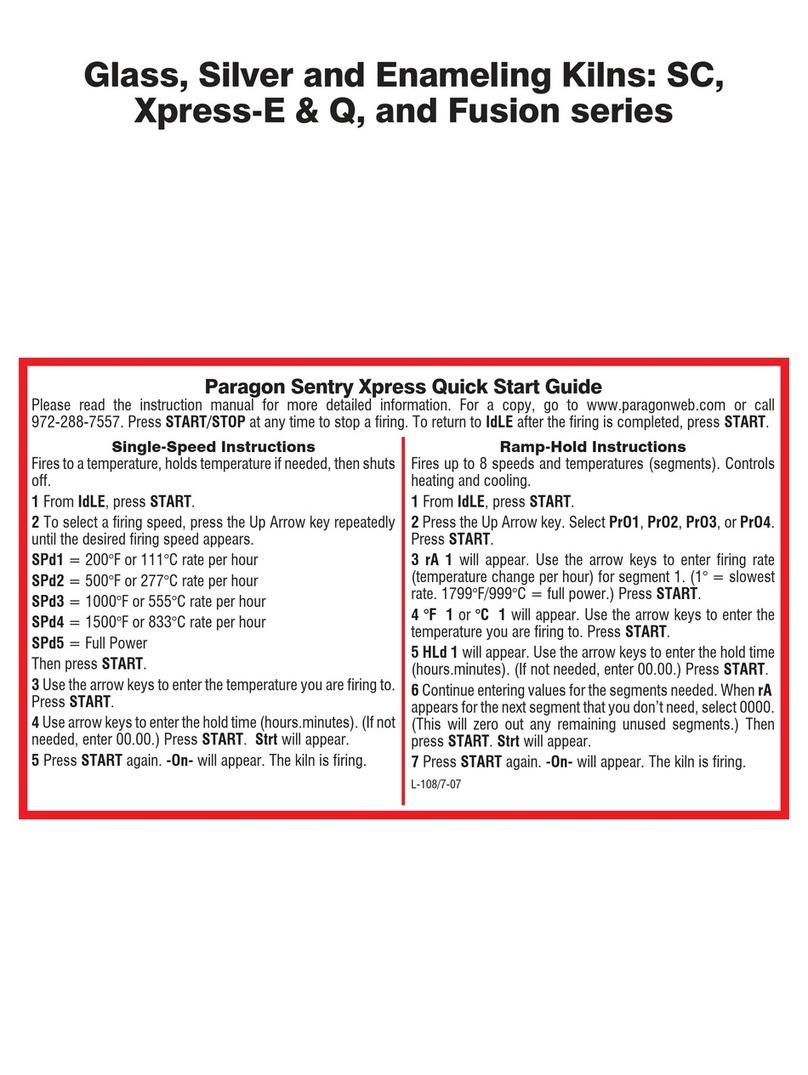
Paragon
Paragon Sentry Xpress SC Series quick start guide
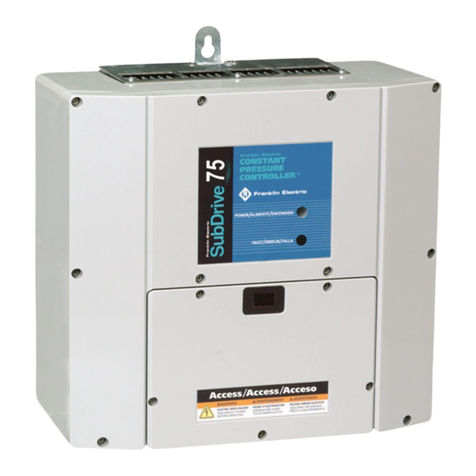
Franklin Electric
Franklin Electric SubDrive75 installation manual