Geo Knight Digital Combo DC16 User manual

1
Version 3-14
Digital Combo
Multi-Purpose Press

2
Contents

3
Introduction
Default Operating Mode of Controller

4
Setup & Suggestions

5
Normal Operation
Normal Operating Mode
The normal operating mode of
the press will display the current
actual Temperature at the top of
the screen and the time setting
or elapsed time below the
temperature.
The right side the screen will
indicate the heating status by
stating HEATING, READY, both
of those words, or none at all,
depending on if it is cooling down or heating up to the set temperature.
READY is shown only if the current temperature is within 5 degrees of
the set point temperature.
The right side of the screen will also indicate the timing status by stating
OPEN, TIMING or DONE. The DONE indicator may remain on in
some cases until the press is opened back up.
If the pressure feature is enabled, the pressure bar graph will show the
last known pressure exerted when the press was closed.
Setting Temperature
From the normal operating mode,
simply press the TEMP key to set the
temperature.
The ashing 3-digit number is the
temperature setting (not the actual
current temp). Use the Arrow Keys to
set the desired temperature. Hold them
down to increase rapidly, press both
together to set it to 350°F.
Press TEMP again to lock in the setting.

6
Setting Time
From the normal operating mode, simply
use the Arrow Keys ONLY to set the
time. Do not touch the PRG key.
Hold down either the Up or Down arrow
key for more than 2 seconds and the time
will increase rapidly.
Press BOTH Arrow Keys and the time
will reset to 00 seconds.
Pre-Press Timer
There is a second timer available for
use, called the “Pre-Press Timer”.
This feature is useful if a multiple-step
process is performed.
For example: If a product must be
pre-pressed for 5 seconds before a
main pressing cycle of 20 seconds, the
Prepress timer can be set for 5 secs, and
the main timer for 20. When the operator closes the press, the 5-sec
time counts down. When the operator opens the press, the time setting
switches to 20 seconds.
The word PREPRESS will be displayed next to the pre-press time setting
when it is active. To set the pre-press time, simply use the Arrow Keys
to set the time. If PREPRESS is not displayed next to the time, quickly
close and then open the press to switch to the prepress time.
To turn ON the prepress timer feature, enter the User Options Menus
(see page 18) and go to the PPR setting and turn it ON. (see page 22)

7
The Digital Pressure Bar
Graph indicates a basic 0-9
scale of pressure exerted.
The pressure bar graph
resets when the press is
closed/locked while timing.
If the pressure adjustment has been changed, or a different thickness
item has been placed in the press, the pressure bar graph will not change
until the press is closed and locked and the timer is counting.
This bar graph is directly related to the amount of pressure, or resistance,
being felt and applied to the bottom table. If a thicker item is placed in
the press, and no adjustments are made to the pressure knob, then the
amount of pressure clamping down will be greater, and the bar graph
will show a higher number. Here are some bar graph guidelines:
A very light pressure slight clamping would be in the 0 to 3 range.
A good medium pressure for most applications would be 4 to 6.
Excessively high pressure for demanding items would be 7-9.
Pressure is set manually using the large black Pressure Adjustment
Knob. There is one important rule of thumb when setting pressure: The
press MUST LOCK IN PLACE when lowering and clamping the press.
Do not simply let the platen rest on the pad. A good solid two-handed
locking force is recommended when rst doing transfers to insure good
results. A “Ka-Thunk” click/clamp sound will result when locking the
press in place.
• To decrease the pressure, turn the
pressure knob to the left, counterclockwise.
The top head will rise away from the lower
table.
• To increase the pressure, turn the
pressure knob to the right, clockwise. The
top head will lower toward the pressing table.
Setting Pressure
Digital Pressure Bar Graph

8
Guidelines & Standard Settings

9
ERR Mode
During operation of the press, if there
is a loss of signal from the temperature
sensor wire, the ERR display will
appear.
This is a safety feature that will shut off
the relay so the press will not overheat
aimlessly without a temperature signal.
Once the temperature signal is restored (no longer broken, or plugged
back into the control) the press will resume the temperature display, and
start heating if necessary. If ERR persists, contact support.
Over-Temp Alarm
If the press heats beyond the set
temperature by 40 degrees or greater,
the OverTemp alarm will sound.
This is a safety feature that warns the
operator of a possible thermal run-away
of the press. This means the press relay
may be locked in a heating position
where it will never stop heating, to a
possibly harmful temperature level.
If the OverTemp alarm sounds, set the temperature to a higher value
than the current actual temp. Wait 30 seconds and then reset the press to
your desired temperature and Watch Carefully. Do not let the press rise
to extremely high temps.
If it continues to rise, turn off the press and let it cool off to room
temperature. Turn the power back on and immediately set the temperature
to a low setting like 200°F. Wait for the press to heat up. When the press
displays “READY”, monitor the temperature and see if it continues to
heat to a level that the OverTemp alarm activates again. If so, contact
the factory.

10
The main feature that makes the Digital Combo so versatile is the
interchangeability of the heat platens. Because the heat platens are
modular in their method of connection, one platen can be unplugged
and another attached, in its place. These platens are “Hot Swappable”.
You do not need to wait for the platens to cool off to remove.
The following instructions apply to the 14x16, 12x14, cap, plate & mug
heat platen attachments. All of them disconnect and connect in the same
manner.
The heat platen can be safely disconnected with
the machine on. However, thermal gloves or
oven mitts must be used when handling hot heat
platens.
Using Attachments
Removing a Heat Platen

11
The heat platen can be safely connected with the machine on. However,
thermal gloves or oven mitts must be used when handling hot heat
platens.
Attaching a heat platen

12
There is a curved 1/2-moon cap
holddown device for stretching the
cap over the curved bottom table.
Simply pull the back strap of the
cap behind the pedestal and under
the 1/2-moon shaped bracket. This
will hold the cap in place for proper
printing.
Cap Hold-down Device (For Cap Attachment Only)
The table can be easily adjusted in a straight position if the heat platen
does not correctly line up with the pressing surface. The pedestal the
table rests on can slide front to back on the base of the machine. Loosen
the screw in the gibb plates that holds the pedestal in place in order to
adjust its position.
The pedestal can also be slightly rotated in order to align with the upper
platen. Loosen all (4) screws holding the gibb plates in place, position/
rotate the pedestal to the desired place, and retighten the gibb plates.
Aligning the Pedestal
The standard tables included with the DK7
or DK8 will accommodate most items.
However there are other sized bottom
tables that are instantly interchangeable.
For the DK7, there are 3 different curved
forms (the top heat platen stays the same).
The mid-sized and youth-sized forms
are not included with the press. The mid-
sized “EURO” form is especially useful
for solving wrinkling of caps in the middle
area for lower-prole tight-t caps.
Custom pedestals, bottom tables, and other
custom solutions are also available from the factory.
Optional Forms / Custom Pedestals

13
The full wrap mug attachment will operate exactly the same as the DK3
mug press. Here are some tips for using the mug attachment:
Only the modular connector needs to be conntected from the mug
attachment to the top control head of the press. The heat platen and
tables can be left on the main frame.
To start the timer, simply drop the handle
of the main frame after closing the handle
of the mug attachment.
Use an extra 1/8” green pad for pressing
narrow diameter cylinders like aluminum
water bottles and smaller undersized
mugs.
The cap attachment works the same as a
cap press. The only difference is that the
swing-away style Digital Combo press
allows complete access to the cap when
the heat platen is swung out, as opposed to
typical stand-alone clamshell cap presses.
Here are some tips for using the cap
attachment:
Make sure the cap holddown device is
attached to the bottom pedestal.
Make sure the proper bottom form is used.
If wrinkling/folding of the middle of the
cap occurs, this is a good indication that
the wrong form is being used.
Make sure the lower pedestal is adjusted and slid forward or backward
to line up with the heat platen above.
How to use the Cap Attachment
How to use the Mug Attachment

14
The plate attachment allows
the operator to press down
inside a dish or other indented
object. Here are some tips for
using the plate attachment:
Use the large T-Shirt at
bottom table.
Place the 3-sided aluminum
tray on top of the T-Shirt
table. This will protect the
main T-Shirt silicone pad
from being cut into by the
plate’s bottom edges.
Plate the black circular silicone pad on the tray. Center the pad so that
it is directly underneath the plate heater block attachment when swung
over. Make sure it lines up directly under the plate heat platen. Then
peel the backing off the circular black silicone pad and permanently
stick it to the tray.
The purpose of the black circular pad is to automatically center the plate
under the heat platen. It also provides cushioning when pressing plates.
Set the clamping pressure of the press so the black pad is compressed to
50% its height. Pressing heavier may risk breaking certain fragile style
plates.
Lay the 1/8” green circular pad on top of the transfer paper in the plate.
How to use the Plate Attachment
Pressing Ceramic Tile
To press ceramic tile, use the standard T-Shirt heat platen and bottom
table. Lay the 1/2” White Nomex Felt padding on top of the black
silicone pad. Then lay the transfer paper face-up, and the tile face-down
into the image. Press the tile from the back side, rmly. This wraps the
transfer paper nicely around the radius of the tile.

15
Loading a Preset
Programmable Presets
How Presets Work
There are 70 programmable presets in the controller. The operator can
store a Temperature, Time, Prepress Time, and Pressure setting in each
preset.
When a preset program is loaded by the operator, the Current Temperature
Setting, Time and Prepress Settings (if there is a Prepress setting in that
preset) are updated in the normal operating mode.
The pressure is NOT set for the operator mechanically. A brief display
of the pressure value in the preset is shown while updating the current
settings. This is simply a reference... a reminder of what pressure setting
the operator must adjust for that preset.
There are 2 main functions to using the presets. LOADING and EDITING
the preset. LOADING a preset simply means selecting a desired preset,
and returning to the normal operating mode where the current settings
are changed. EDITING a preset is when the operator actually changes
the preset’s settings.
To enter the presets, press the PRG
key.
SET will display on the screen.
Use the Arrow Keys to select a preset
from 00 to 70.
Press PRG to return to the normal
operating mode. The current active Temperature, Time & Prepress time
settings (if there is a prepress setting in that preset) are now updated
with the presets values.

16
Editing/Programming a Preset
To edit a preset and change it’s values to your
own desired settings, you simply use the TEMP
key while in the SET preset mode.
From the normal operating mode, press the PRG
key. SET displays on the screen. Use the Arrow
Keys to select the preset # you wish to edit.
Press the TEMP key. The temperature will ash.
Use the Arrow Keys to set the temperature for
that preset.
Press the TEMP key. The time will ash. Use
the Arrow Keys to set the time for that preset.
Press the TEMP key. The Prepress time will
ash. Use the Arrow Keys to set the Prepress
time. Set the Prepress time to 00 if only one timer
is to be used for that preset. Setting Prepress to
00 will disable the Prepress feature.
Press the TEMP key. The Pressure reference
value will ash. Use the Arrow Keys to set the
pressure for that preset. This will display 0 to 9
for presses congured for Bar Graph Pressure
readout, and will display 0:00 to 10:00 for
presses congured for a Height Gauge readout.
Press the TEMP key. The screen returns to the
preset #. Press PRG to return to the normal
operating mode, or use the Arrow Keys to select
a different preset and edit that as well.

17
A Walkthrough Tutorial for using Presets
Here is a tutorial of programming 2 different presets, and then an
example of using them in normal daily operations. Do this walkthrough
to practice using presets.
Part 1: Programming 2 different presets.
From the normal operating mode, press PRG. SET appears.
Use the arrow keys to select SET 01.
Press TEMP. Set the ashing temperature to 400 with the arrow keys.
Press TEMP. Set the ashing time to 45 with the arrow keys.
Press TEMP. Set the ashing Prepress time to 00 with the arrow keys.
Press TEMP. Set the ashing Pressure ref to 6 with the arrow keys.
Press TEMP. Use the arrow keys to select SET 02.
Press TEMP. Set the ashing temperature to 350 with the arrow keys.
Press TEMP. Set the ashing time to 12 with the arrow keys.
Press TEMP. Set the ashing Prepress time to 3 with the arrow keys.
Press TEMP. Set the ashing Pressure ref to 8 with the arrow keys.
Press TEMP. Press PRG to leave the preset mode.
Presets SET 01 and SET 02 have now been programmed.
Part 2: Loading the presets. Let’s say we are powering on the machine
and starting a job. The rst job will need to use preset 01, and later on
the next job will need preset 02.
From the normal operating mode, press PRG. SET appears.
Use the arrow keys to select SET 01 then Press PRG. Done!
The press is now set for 400°F and 45 seconds and will start to heat to
that temperature. When leaving the presets, the screen briey displayed
PRS 6 - indicating you must manually set the clamping pressure so the
bar graph shows 6 (or close to it) at the bottom of the screen.
Now let’s change to the next job. Press PRG. SET appears.
Use the arrow keys to select SET 02 then Press PRG. Done!
The press is now set for 350°F, 12 secs, 3 prepress, and you are reminded
to set the pressure heavier to 8 on the bar graph display (when closed).
That’s it! You can load a preset as often as needed: just press PRG, pick
the preset you want with the Arrow Keys, and press PRG again.

18
User Menus
Entering the user menus & options
There are many useful features beyond simply setting time & temperature,
and storing presets. All of these additional features are available to the
operator in the User Menus.
To access the user menus, simply press TEMP & PRG at the same
time from the normal operating mode and let go.
(Try to use two hands and press the keys at the exact same time. If one
key is pressed too early from the other, the temperature setting or preset
modes may be activated instead. Turn the press off and then on and try
again.)
Fahrenheit / Celsius
The current and set temperature can be
displayed in °F or °C. After entering the
user menus (see above), use the arrow
keys to select F or C. Press PRG to move
to the next menu item.
Timer Counter Units
The timer and Prepress timer can be set
for mins/secs (default) or hours/mins. If
special applications need a higher timer
range than 99 mins, 59 secs, this can be
changed. After entering the user menus
(see top of page), Press PRG until CNT
displays. Use the arrow keys to select
SEC or HR. Press PRG to move to the
next menu item.

19
Recorded Pressings Odometer
There is an “odometer” that records
pressing cycles done. This can be cleared
and reset to 0 at any time when needed.
The gure scrolls and it’s beginning and
end are separated by a “-” sign.
After entering the user menus (see
top of page 19), Press PRG until REC
displays. Use the arrow keys to reset the
counter to 0. Press PRG to move to the
next menu item.
Pressings Countdown Odometer
There is a second type of “odometer”
that counts down the number of pressing
cycles from a set amount.
After entering the user menus (see
top of page 19), Press PRG until CTD
displays. Use the arrow keys to set it
ON or OFF.
When this feature is ON - the normal
countdown timer display is replaced by this odometer instead. The
arrow keys no longer adjust the countdown timer, but instead are used
to set the countdown odometer. When OFF, the timers are visible.
The timer & prepress timer (if ON) still operate. However they are not
visible. Instead, at the end of every main timing cycle (but not prepress),
the odometer decreases by 1. This way, the opreator can keep track of
how many pressings are left to do, without checking the REC menu.
This feature is useful when a specic amount of pressings must be
performed, and the operator must be aware of how many pressings are
remaining. Simply use the arrow keys to adjust this value in the normal
operating mode (just like they are normally used to change the time).
This value will automatically decrease at the end of each timing cycle.
Press PRG to move to the next menu item.

20
Pressure Maximum
To reset and redene “9” for the pressure
bar graph, use this calibration menu. Do
NOT adjust this setting unless you
are sure adjustments are necessary.
Adjust the pressure of the machine
so there is extremely heavy pressure
when clamping and locking the press.
Press either Arrow Key. The press now
considers this pressure as “9” on the
Pressure Bar Graph Display.
Press PRG to move to the next menu item.
Pressure Minimum
To reset and redene “0” for the pressure
bar graph, use this calibration menu. Do
NOT adjust this setting unless you
are sure adjustments are necessary.
Adjust the pressure of the machine so
there is barely any locking pressure
when clamping and locking the press.
Press either Arrow Key. The press now
considers this pressure as “0” on the
Pressure Bar Graph Display.
Press PRG to move to the next menu item.
Table of contents
Other Geo Knight Power Tools manuals
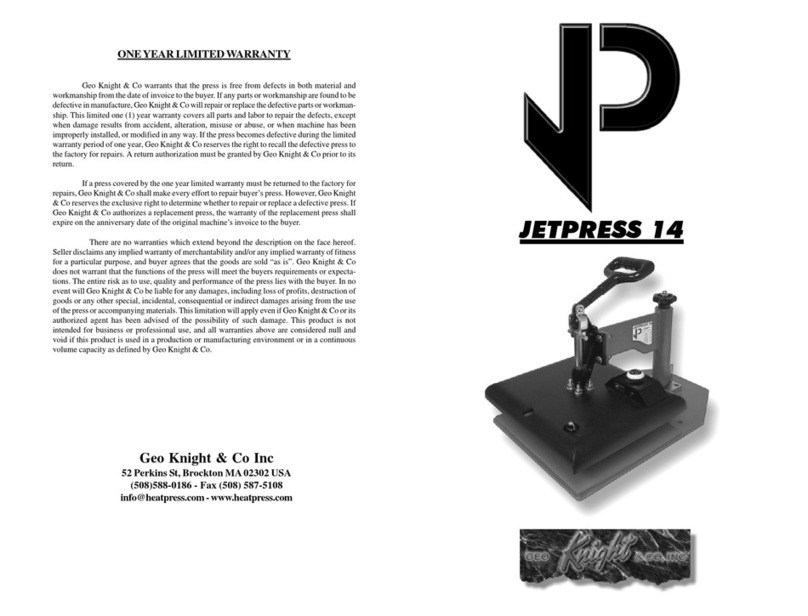
Geo Knight
Geo Knight JetPress 14 User manual
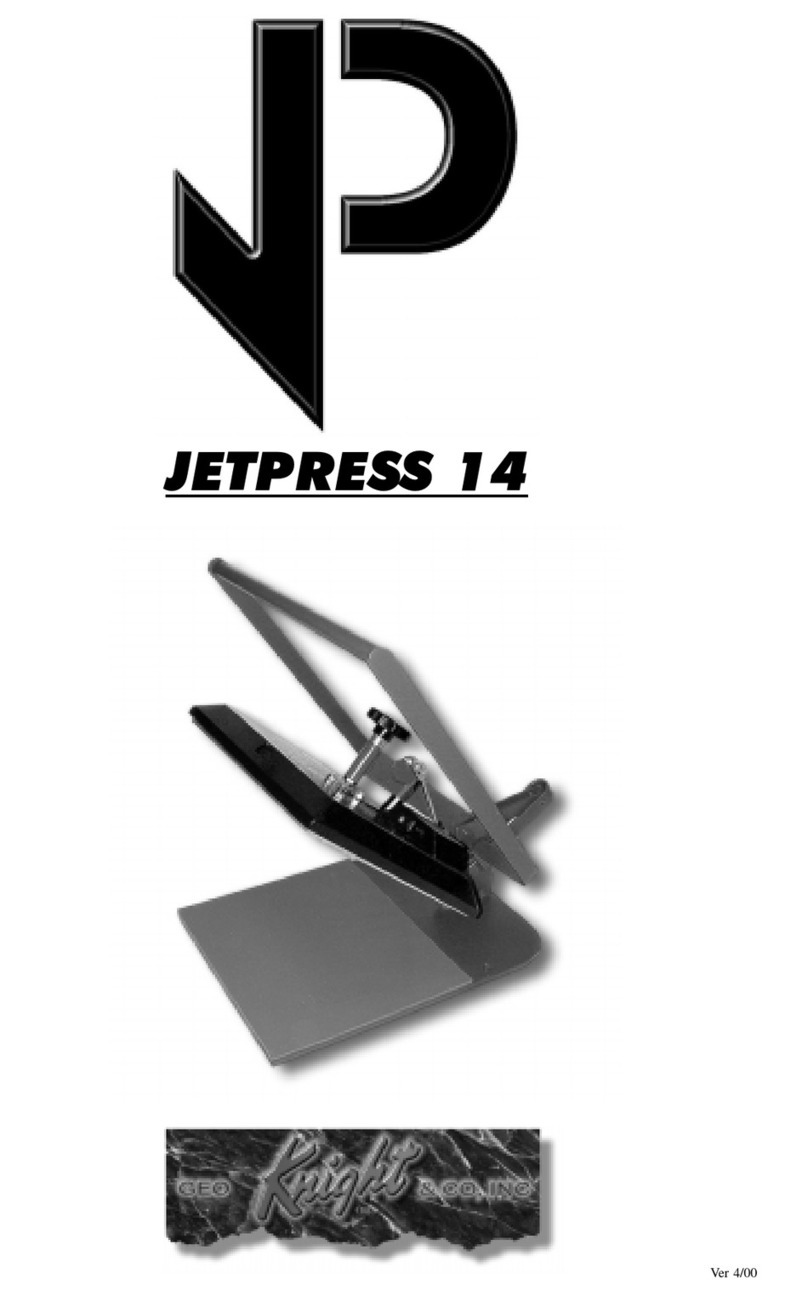
Geo Knight
Geo Knight JETPRESS 14 User manual

Geo Knight
Geo Knight DC16AP User manual
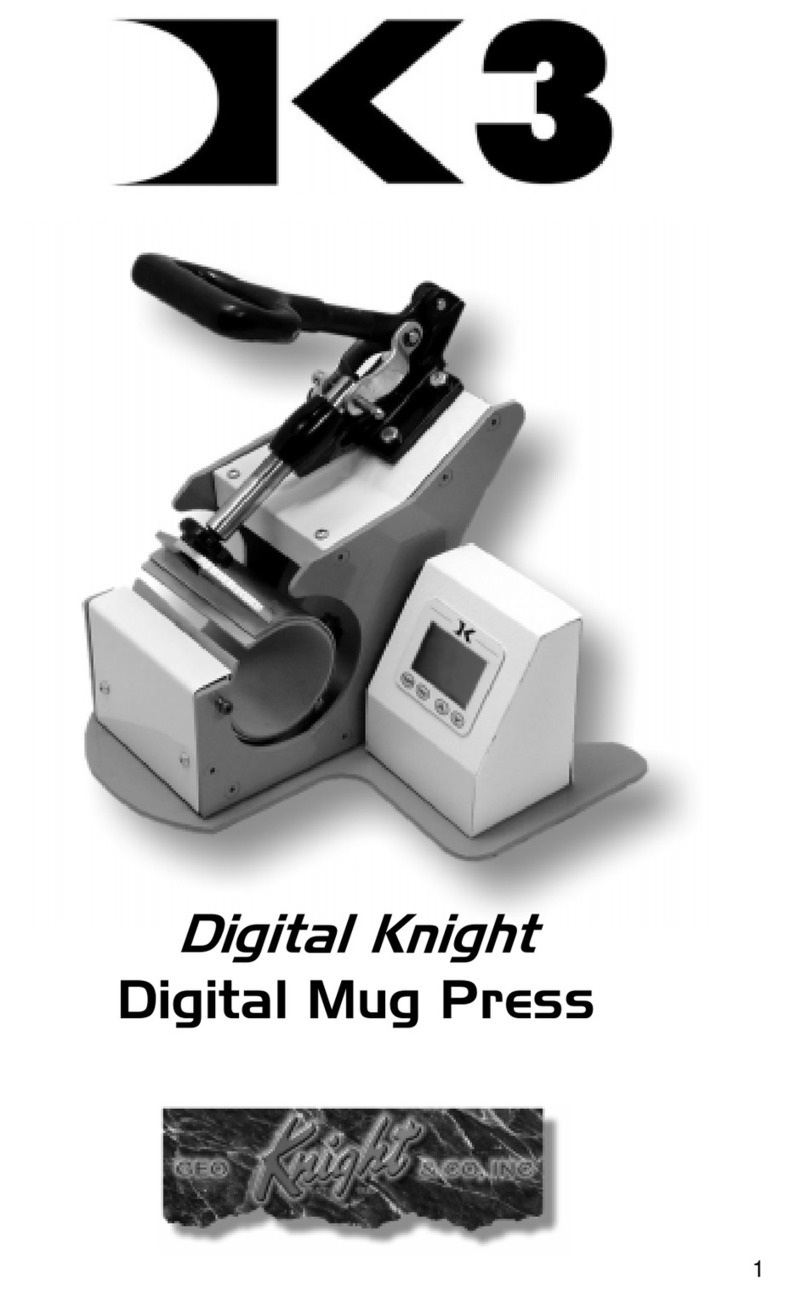
Geo Knight
Geo Knight Digital Knight DK3 User manual
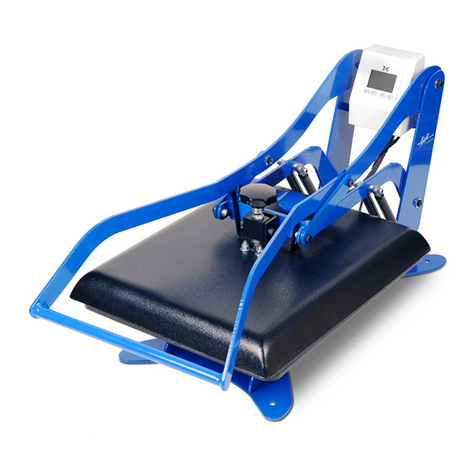
Geo Knight
Geo Knight Digital Knight DK20 User manual
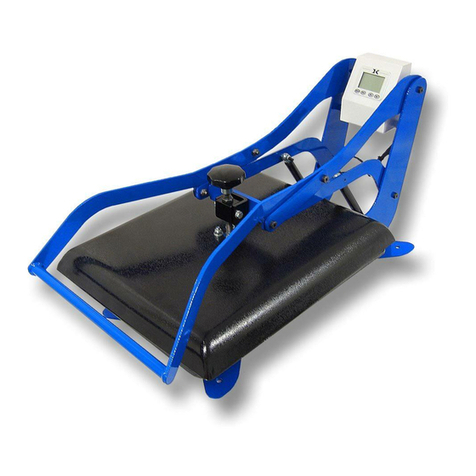
Geo Knight
Geo Knight Digital DK20 16x20 User manual
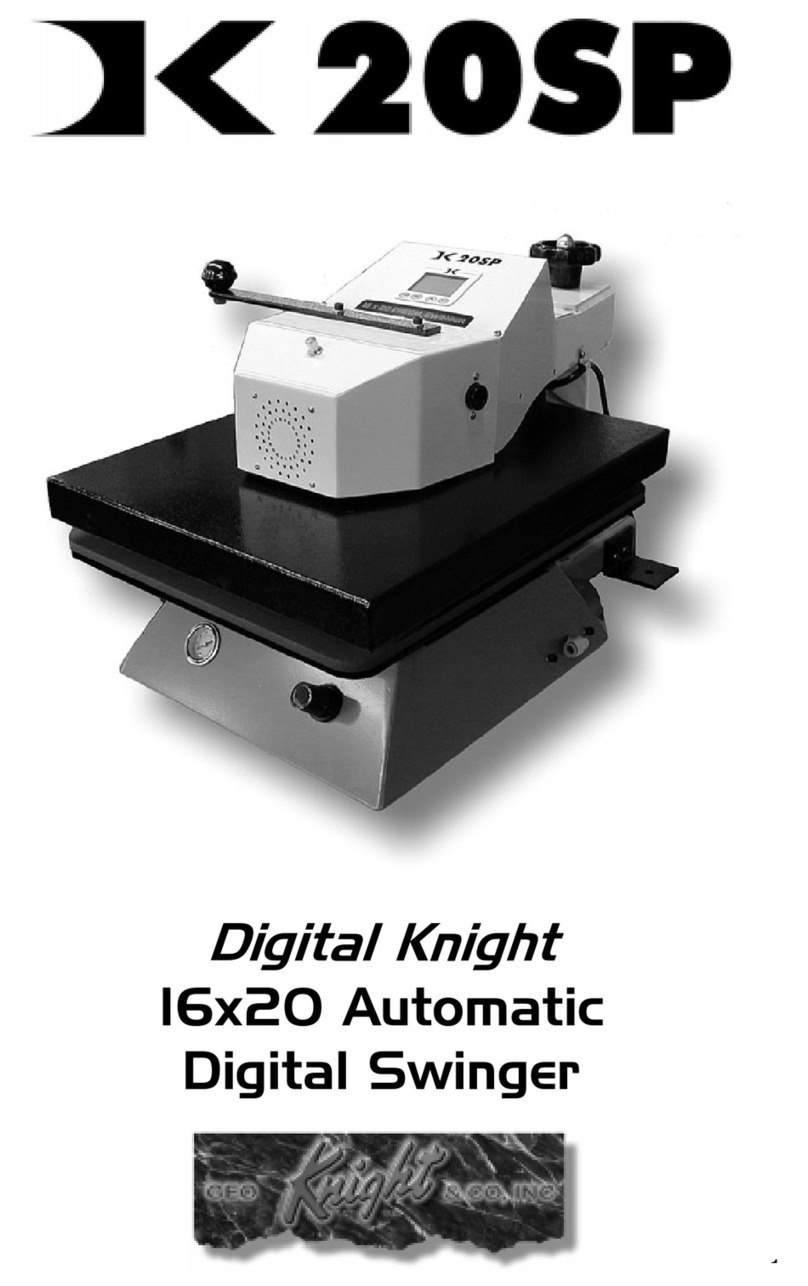
Geo Knight
Geo Knight Digital Knight DK20SP User manual
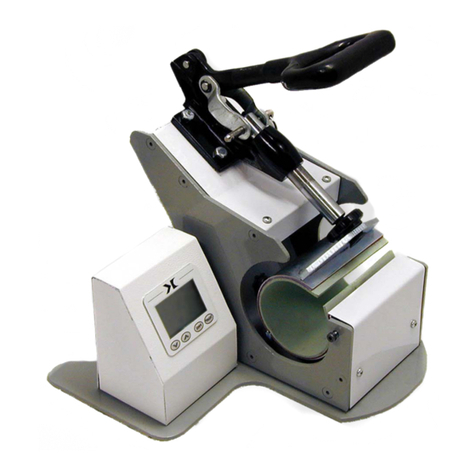
Geo Knight
Geo Knight Digital Knight DK3 User manual
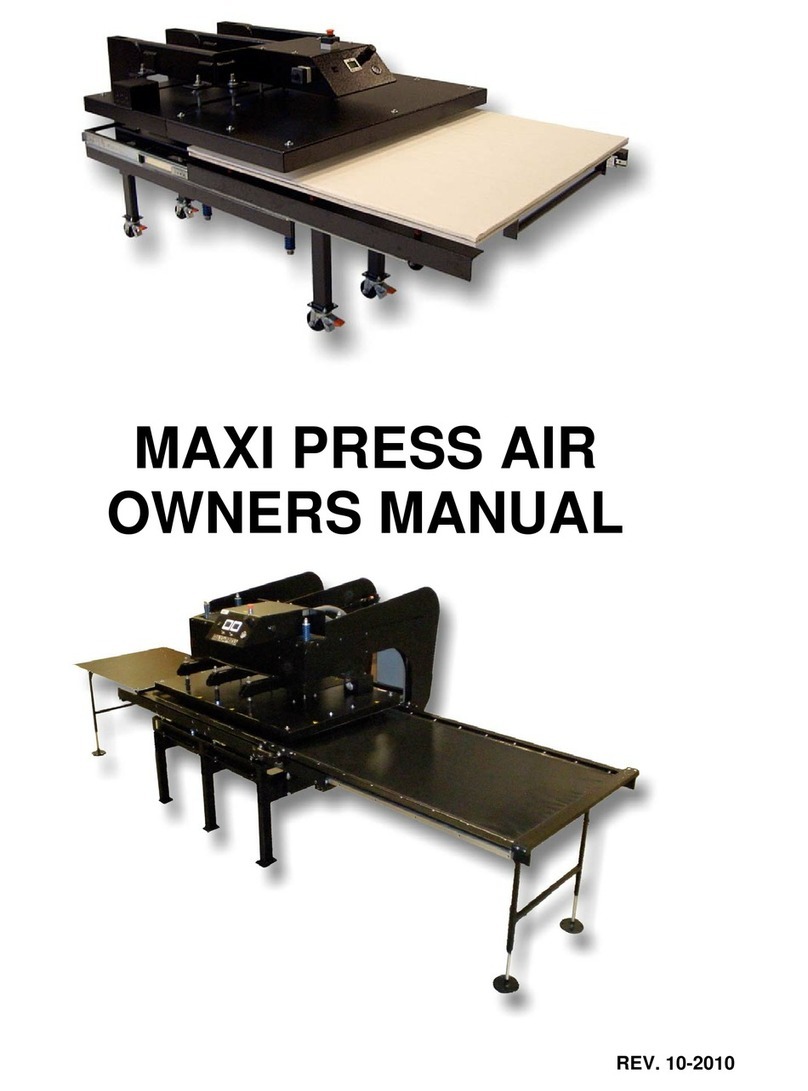
Geo Knight
Geo Knight Maxi Press Air User manual
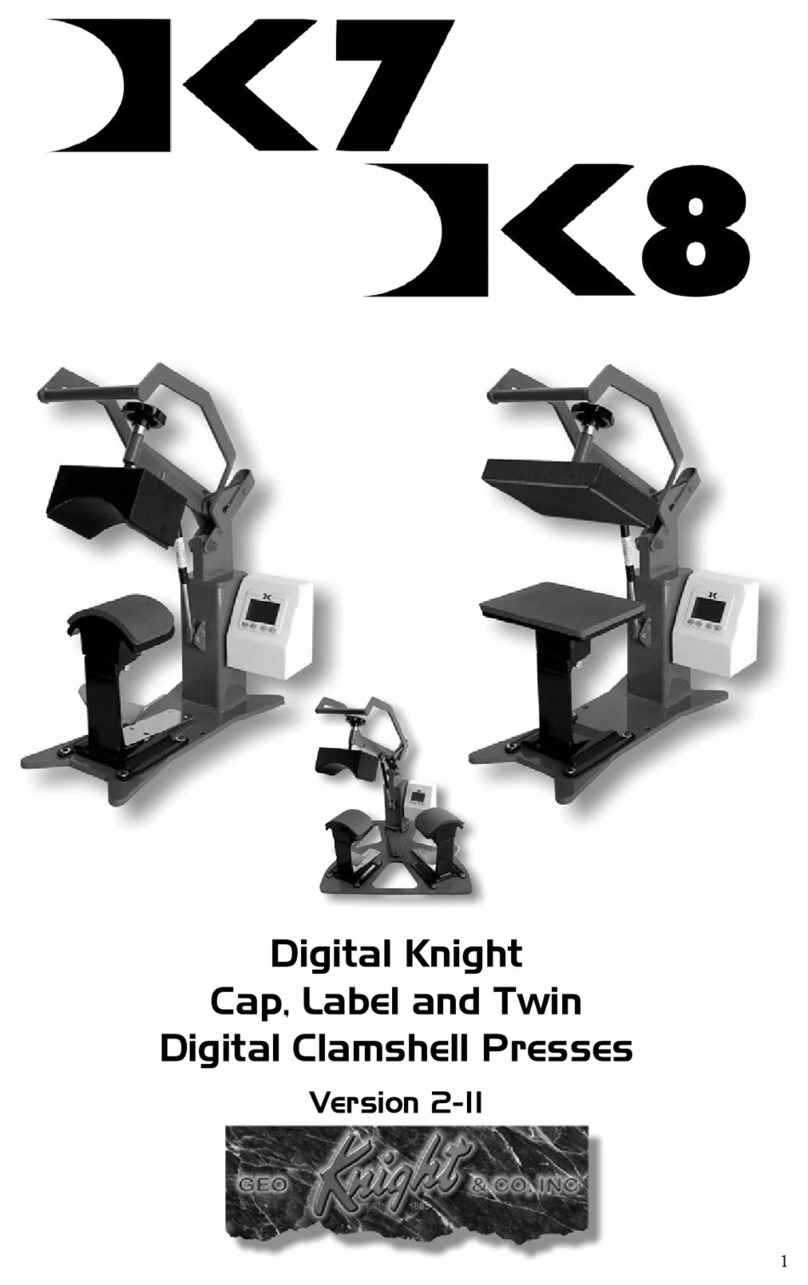
Geo Knight
Geo Knight DK7 User manual