Geotech ORS SITEPRO 2000 User manual

ORS SITEPRO™ 2000
Blower/Pump Control Panel
Installation and Operation Manual
Rev. 6 11/12/03 Part # 10367

1
Table of Contents
Chapter 1: ystem Description ................................................................................................................... p. 04
Function and Theory................................................................................................................................ p. 04
Chapter 2: ystem Installation.................................................................................................................... p. 11
Chapter 3: ystem Configuration................................................................................................................ p. 20
Chapter 4: ystem Operation ..................................................................................................................... p. 35
Chapter 5: ystem Maintenance................................................................................................................. p. 43
Chapter 6: Problem olving........................................................................................................................ p. 44
Chapter 7: ystem pecifications ............................................................................................................... p. 47
Appendix A: Panel Configuration heet...................................................................................................... p. 49
Appendix B: Glossary ................................................................................................................................. p. 50
Appendix C: Application Notes ................................................................................................................... p. 52
Warranty and Repair ................................................................................................................................... p. 54

2
DOCU ENTATION CONVENTIONS
This manual uses the following conventions to present information:
An exclamation point icon indicates a
WARNING
of a situation or
condition that could lead to personal injury or death. You should
not proceed until you read and thoroughly understand the
WARNING message.
A raised hand icon indicates
CAUTION
information that relates to
a situation or condition that could lead to equipment malfunction
or damage. You should not proceed until you read and
thoroughly understand the CAUTION message.
A note icon indicates
NOTE
information. Notes provide additional
or supplementary information about an activity or concept.
WARNING
CAUTION
NOTE

3
Quick Start Instructions
Read this section even if you don’t read anything else.
The large envelope shipped with your OR ITEPRO™2000 control panel contains Quick tart Installation and
Configuration Instructions. Familiarity with the information in this envelope is absolutely essential for safe and trouble free
operation of the OR ITEPRO™ 2000 control panel.
The OR ITEPRO™ Quick tart envelope contains the following instruction sheets:
• A Field Wiring Diagram that shows basic wiring of motors and probes.
• An Optional Feature Wiring Diagram that shows how to wire network connections, interlocks, analog sensors and
other specialized devices.
• A ite Configuration Guide that explains how to lay out your site and define network interlocks.
• A Panel Configuration Guide that explains how to configure individual panels after the OR ITEPRO™ network
has been laid out.
The information in this supplement is provided to complement the OR ITEPRO™ Installation & Operation Manual.
Although we highly recommend that all users read the entire Installation & Operation manual, we also recognize that
some experienced technicians may desire a quick start summary of essential information.
Please proceed as follows:
1. Refer to the ite Configuration Guide to determine the basic layout of your site.
2. Mount the OR ITEPRO™ panel(s) and carry out basic wiring according to the generic Field Wiring Diagram.
3. Carry out additional site-specific wiring according to the recommendations and examples provided in the Optional
Features Wiring Diagram.
4. Configure each panel according to the Panel Configuration Guide.
5. Document the configuration of each panel by filling out the Panel Configuration heet included in Appendix A of
the OR ITEPRO™ manual. Be certain that these sheets are available for reference before calling Geotech for
assistance.
Observe all Warning and Cautions included in the OR ITEPRO™ manual.

4
Chapter 1: System Description
Function and Theory
The OR ITEPRO™ 2000 Blower/Pump Control Panel (figure 1) is designed for simultaneous control of one blower (Air
tripper or oil Vapor Extraction) and one pump (influent water, transfer water or chemical feed). The controller is housed
within a weather-proof NE A 4 (IP66) enclosure and incorporates circuitry to receive intrinsically safe input from
sensors deployed in hazardous locations.
Figure 1
Each control panel can be operated by itself or can be linked to as many as 15 other similar panels in a user configurable
alarm communication network. Because each panel in the network has access to alarm inputs from all the other panels,
entire sites can be tied together and configured to respond appropriately to input received by any panel in the network.
The OR ITEPRO™ 2000 is fully instrumented and includes status displays that provide a visual representation of the
pump and blower operating conditions. The panel also incorporates a self-test feature that continuously monitors line
voltage, condition of the pump and blower control switches, panel temperature and probe integrity whenever the OR
ITEPRO™ 2000 is in operation. An additional self-test routine that runs at panel startup (or whenever Y TEM TE T
button is pressed), checks internal program and data memory, R -232 serial communications, the analog to digital (A/D)
converter, and the integrity of all panel indicators.
The standard OR ITEPRO™ 2000 Blower/Pump Controller is equipped with terminals that allow the panel to interface
with a standard OR density actuated level sensing probe, pressure switches as well as external interlock devices.
Additional inputs (including those for analog devices, and a totalizer), become available when the telemonitoring
option is installed. Form C dry contact outputs are also available for interfacing with additional external equipment
components, buzzers, indicators and security alarm systems.

5
Each standard OR ITEPRO™ 2000 Blower/Pump Control Panel is designed to run a single blower and a water pump.
Optional features include a telemonitoring package that incorporates remote monitoring and data logging as well as auto
dial-out on alarm to either PC or Fax machine. Panels are available for 6 HP blowers. Pumps and blowers larger than 2-
1/2 HP can be controlled by the OR ITEPRO™, but require the use of an external contactor.
To complement the optional remote monitoring and data logging features, Geotech offers a comprehensive software
package (OR ITEPRO™ Manager) to provide graphical representations of the OR ITEPRO™ 2000 panel as it
operates on site. Optional features of this software package allow the user to generate reports, graphs and active P&IDs
of remediation functions. OR ITEPRO™ Manager is available at no extra cost when the telemonitoring package is
purchased.
odes of Operation
User Interface odes
The OR ITEPRO™ 2000 can be operated in any of the three modes shown in figure 2 and described briefly on the
following pages.
Figure 2
anual Operation ode
The panel is equipped with controls and indicators that permit manual operation of the pump and blower. Controls include
pump and blower POWER switches that cut off all power to the motors, 3-position pump and blower CONTROL switches
and a CONTROL POWER switch to cut off power to the control circuitry. A Y TEM TE T button activates the panel’s
self-test feature. Refer to Chapter 4 for details of panel operation.
In OR itepro™ 2000 systems without the telemonitoring option, manual operation is the
only way the user can interface with the system.

6
Local Communication ode
When the OR ITEPRO™ 2000 is equipped with the telemonitoring option, the user can use a computer to
communicate with the panel either remotely over a telephone line (Remote Communication Mode) or locally via the
special cable to the RS-232 serial port (Local Communication Mode).
Two basic types of operations are possible using the Local Communication Mode:
1. et up and configure the data logging and remote monitoring features.
2. Download data from the data logger.
Procedures for using the Local Communication Mode are detailed in the manual that accompanies the OR ITEPRO™
Manager software package.
Remote Communication ode
The modem and associated hardware/software included with the telemonitoring option allows the user to communicate
with the OR ITEPRO™ 2000 panel from an off site computer.
Four basic types of operations are possible using the Remote Communication Mode:
1. et up and configure the data logging and remote monitoring features.
2. Download data from the data logger.
3. Access real time graphical representations of site conditions.
4. Auto dial-out on alarm.
The Remote Communication Mode can also be used to dial out to a fax machine.
Procedures for using the Remote Communication Mode are detailed in the manual that accompanies the OR
ITEPRO™ Manager software package.
Figure 3

7
How ORS SITEPRO™ works
The OR ITEPRO™ 2000 uses highly flexible microprocessor based electronics to provide a wide spectrum of
capabilities that range from basic motor control to complex and sophisticated multi-panel networking. This built in
versatility allow the OR ITEPRO™ 2000 to be configured on site to match the unique requirements of any remediation
application.
Basic otor Control
Figure 3, shows a simple water treatment system in which an OR ITEPRO™ 2000 Blower/Pump panel controls a
LOPRO™ Air tripper blower and a transfer pump. During normal operation, the blower runs continuously and the pump
cycles on and off in response to input from the sump level probe mounted in the Air tripper sump.
otor Control with Interlocks
In most applications, your OR ITEPRO™ 2000 will be integrated into a remediation system that includes additional
equipment components.
Figure 4
These components (holding tanks, hydrocarbon pumps, oil/water separators, carbon tanks, etc.) often must be interlocked
to the control panel to optimize system performance and to prevent permit excursions in the event of a component failure.
Figure 4, shows another simple water treatment system in which contaminated water first passes through an Air tripper
and then into a Carbon Tank. Again, the ON/OFF cycling of the transfer pump is controlled by the status of the sump
probe. In this application, however, a high pressure switch is wired to the control panel shuts off the transfer pump if the
carbon tank becomes clogged. Use of such external interlock devices (high level shut off switches, pressure switches,
etc.) is facilitated by a system of internal circuits built into every OR ITEPRO™ 2000 panel. These circuits provide four
separate alarm channels for attachment of interlock devices.
ulti-Panel Networks
When two or more OR ITEPRO™ 2000 panels are linked together in a network as shown in figure 5. The individual
panel microprocessors are able to communicate and share information through a system of circuits called the Interlock
Communication Bus, or ICB. Each panel in a network can be configured to send and/or receive alarm signals on any or
all of the four alarm channels. In this way, alarms received locally by one panel can be broadcast on the ICB and used to
shut off other panels in the network.
In figure 5, a feed pump and its control panel (Panel #2) have been added to the water treatment system diagrammed in
figure 4. Panel #2 receives input from its own level sensing probe and Panel #1 through the network cable shown in the

8
diagram. The network connection allows both pumps to be shut off by the carbon tank high pressure switch and also
enables the air stripper controls to shut off the feed pump in the event of a sump high level condition or a blower failure.
Figure 5
Network anagement
Whenever a multi-panel OR ITEPRO™ 2000 network is configured, one of the panels in the network must be
designated to carry out special Interlock Communication Bus management functions. This panel, called the Master,
controls the flow of information on the bus, assesses the interlock status of the other panels, called laves, and
communicates with the host computer if the telecommunication option is installed. ee figure 6 for a diagrammatic
representation of the relationship between Master and lave panels.
Figure 6

9
If the telecommunication option is installed in one of the panels in a network, that panel must be configured as the
Master. However, if no remote monitoring is required, any panel in the network can be the Master. Panels are
designated Masters or laves by setting dip switches inside each panel.
During network operation, the Master continuously polls the laves in a set sequence determined by the network
addresses the user chooses for the panels. When a lave is polled, it is temporarily given control of the Interlock
Communication Bus. The lave then broadcasts any current interlock alarms that are on alarm channels configured
to send. All other panels in the network ( laves and Master) will then respond to the alarms and shut down if they are
configured to receive on these same alarm channels.
tep by step procedures for configuring your OR ITEPRO™ 2000 Control Panel are provided in Chapter 3 of this
manual.
Additional Applications
The examples in this chapter have shown the OR ITEPRO™ 2000 Blower/Pump Control Panel being used to control
an air stripper blower and a transfer pump. Additional OR ITEPRO™ applications are listed on the following page:
Air Stripper w/Influent Feed Pump
When used to control an air stripper blower and an influent feed pump, the OR ITEPRO™ receives input from the air
stripper controls (sump probe & pressure switches) and a water pump level sensing probe. In this application, the normal
cycling of the feed pump is controlled by the level sensing probe. When the panel is properly configured, the pump can be
shut off by 1) a LOW-OVERRIDE signal from the level sensing probe, 2) a HI or LO PRE URE signal from the blower,
3) a HI UMP signal from the air stripper sump level probe or 4) an alarm generated by an external interlock device.
Air Stripper w/Chemical Feed Pump
When used to control an air stripper blower and a chemical feed pump, the OR ITEPRO™ receives input from the air
stripper controls (sump probe & pressure switches) and a level sensor mounted in the chemical vat. In this application,
operation of the chemical feed pump is controlled by the vat level sensor. The pump can be shut off by 1) a LOW-
OVERRIDE signal from the vat level sensor, 2) a HI or LO PRE URE signal from the blower, a HI UMP signal from the
air stripper sump level probe or 4) an alarm generated by an external interlock device.
SVE Blower w/ Knockout Drum
When used to control a soil vapor extraction ( VE) blower with a knockout drum, the OR ITEPRO™ receives input
from a knockout drum high level switch. In this application, the blower can be shut off by the high level switch or by any
external interlock device wired to one of the panel’s alarm channels.

10
Figure 7

11
Chapter 2: System Installation
1. Is the electrical service at the site properly sized for this panel and does it conform to NEC and local codes?
2. Are the electrical characteristics of your pump and blower compatible with those of the panel?
INSPECTION
Inspect all equipment upon arrival. Check the contents of the packing crate against the ystem pecification sheet at the
front of this manual. If any items are missing or damaged, make note of this on the shipping papers and immediately notify
Geotech Environmental Equipment, Inc. at 800-833-7958 OR (303) 320-4764.
PANEL INSTALLATION
ount Panel
1. Remove the panel from its packing crate and hold it against the intended mounting surface.
2. Refer to figure 2 and position the panel so that the access door will open at least 12-1/2” without obstruction.
3. If the mounting surface is wood, use wood screws to attach the panel mounting feet to the wall. If the surface is
metal, use the panel as a template and mark the locations of the mounting holes. Then drill and tap the holes and
use self-tapping screws to mount the panel.
WIRING
Install Chassis Ground
Before beginning panel hookup procedures, run a wire from the panel chassis ground lug to a good earth ground such as
the circuit breaker panel enclosure. The ground lug is located on the chassis behind the panel faceplate ( ee the OR
ITEPRO™ 2000 wiring diagram in figure 8).
The OR ITEPRO™ 2000 Blower/Pump Controller Panel must be deployed in a
non-hazardous location and all conduit runs from the well head to the panel must
conform to Article 501-5 of the National Electrical Code (NEC) 1993.
Before deploying the OR ITEPRO™ 2000 refer to the ystem Checklist at
the front of this manual and answer the following questions.
Do not use nails to attach the panel, as a misdirected hammer blow could
damage the enclosure.
All wiring must be carried out by a qualified electrician and be in accordance
with state and local codes. Proper grounding of the panel is necessary to
maintain the intrinsically safe rating of the OR ITEPRO™ 2000. ee the
following sections for panel grounding procedures.
Before installing wires, setting configuration dip switches or touching exposed
portions of the panel circuit board, safely discharge any static electricity from
your body by touching or otherwise grounding yourself to the panel chassis.

12
Figure 8
Install Intrinsically Safe Ground
Run a separate ground wire from the intrinsically safe ground lug to a good earth ground. The I. . grounding lug is
located next to TB1 on the back of the panel faceplate.
The intrinsically safe ground wire must be kept separate from the chassis
ground.

13
The OR ITEPRO™ panel enclosure is equipped with access ports to facilitate wiring. ee figure 2 (in Chapter 1) for
locations of access ports. The port on the side of the enclosure is for all intrinsically safe wiring. All other wiring,
including incoming power and pump connections must be routed through the access port in the bottom of the enclosure.
Wire Incoming Power
Run power wires through the port at the bottom of the enclosure and attach to the terminal block on the chassis behind
the faceplate (figure 8). Attach the power leads to terminals L1 and L2. In 115VAC systems, wire power leads to the
“HOT” and “NEUTRAL” terminals as shown in figure 8. Attach the ground wire to the grounding lug next to the terminal
block. Check tightness of terminal screws.
Wire Pump
Run the pump power wires through the port at the bottom of the enclosure and attach to the PUMP POWER OUT
terminals (figure 8). Attach the ground wire to the chassis grounding lug next to the terminal block. Check tightness of
terminal screws. For wiring instructions specific to your pump and blower, refer to the blueprint Field Wiring Diagram
provided with these items.
Wire Blower
Run the blower power wires through the port at the bottom of the enclosure and attach to the BLOWER POWER OUT
terminals (figure 8). Attach the ground wire to the chassis grounding lug next to the terminal block. Check tightness of
terminal screws. For wiring instructions specific to your pump and blower, refer to the blueprint sized Field Wiring Diagram
provided with these items.
Wire WTDP Probe
The OR ITEPRO™ 2000 Blower/Pump Control Panel is designed for use with either a standard density actuated
WTDP probe or an OR LO-PRO™ Air tripper sump level probe. When the OR ITEPRO™ is being used to control a
blower and an influent feed pump, the WTDP probe is wired to the panel as shown in figure 9. This probe uses three
separate switches (HI, LO, & LO-OVERRIDE) to monitor water level in the well. The HI and LO switches control the
normal ON/OFF cycling of the pump while the LO-OVERRIDE switch shuts off the pump in the event of a control system
failure.
Run the probe cable through the access port on the side of the enclosure and attach its leads to I terminal strips TB1 &
TB2 as shown in figure 9.
To maintain the NEMA 4 weatherproof characteristics of your panel after wiring
has been completed, seal all wiring access ports with weatherproofs conduit
hubs.
The OR ITEPRO™ 2000 circuit board shield (behind faceplate) is equipped
with a label that shows the locations of all terminals and configuration dip
switches. Refer to this label (and figure 8) throughout the panel wiring procedures
described in this chapter.
Do not run power wires within two inches of intrinsically safe (I ) wires or
terminals. Refer to figure 8 for location of I terminals (at top of panel), and
reference NEC Article 508 for relevant codes.
Refer to your pump manual and heed all relevant Warnings and Cautions.
Refer to your air stripper or VE manual and heed all relevant Warnings and
Cautions

14
Figure 9
Before wiring an older OR probe to the OR ITEPRO™ panel, it will be necessary to cut the connector from the probe
cable. After wiring the probe to the panel as shown in figure 9 (above), attach a jumper wire from terminal #5 on TB2 (red
wire) to any of the +5VDC I. . terminals on TB1.
Wire Sump Probe & Pressure Switches
When the OR ITEPRO™ is being used to control an air stripper blower and a transfer pump, the ON/OFF cycling of the
pump is controlled by a sump level probe mounted in the air stripper sump. The probe also has a HI-OVERRIDE sensor
that can shut off an optional feed pump if the water level in the air stripper sump rises too high and threatens to flood the
blower.
If your OR ITEPRO™ 2000 Blower/Pump Control Panel is being used with an OR LO-PRO™ II Air tripper, the sump
probe and the pressure switches are pre-wired into a junction box as shown in figure 10. Wire from the junction box to
TB1 and TB2 inside the OR ITEPRO™ panel as shown in figure 10.
Conductivity actuated probes can be used only with the addition of a relay. Call
Geotech for further information.

15
Figure 10
Wire Interlocks
The OR ITEPRO™ 2000 has four intrinsically safe and four non-intrinsically safe interlock inputs available for
attachment of external interlock devices to the panel alarm channels. Geotech suggests that a maximum of two
interlocks be wired to a channel, when two interlocks are wired to the same channel, both must be wired either Normally
Open, or Normally Closed. If both switches are wired normally closed, however, both switches must open for the panel
to respond with an alarm on that Interlock channel.
To shut off an optional feed pump in the event of a High ump Level or High/Low
Pressure condition, the inputs for each of these functions must be jumpered to an
alarm channel as explained in Appendix D: Application Notes.
Never wire both a Normally Open and a Normally closed interlock device to the same
channel. Doing so could cause the panel to either lock in alarm or be unable to read an
alarm.

16
Figure 11
As your interlocks are installed, keep track of which ones are wired Normally Open and which are Normally Closed.
This information will be required for completion of the system configuration procedures described in Chapter 3.
Wire Network Connections
To wire two or more OR ITEPRO™ panels together into a network, use a high quality shielded twisted pair cable and
wire as shown in figure 12 (below). Wire the conductors from terminals 10 & 11 of TB4 on one panel to the same
terminals on the next. On all but the last panel in the network, connect the shield to the terminal 12 on TB4. Do not splice
shield segments together.
Figure 12
Wire each interlock device to the OR ITEPRO™ panel as follows:
1. Run the intrinsically safe interlock wires through the access port on the side of the
OR ITEPRO™ enclosure. Run non-intrinsically safe interlock wires through the
port at the bottom of the enclosure. Use 20-25 AWG wire in all cases.
2. For intrinsically safe interlocks, attach one wire to terminal 1, 2, 3 or 4 of TB2 and
the other to one of the +5VDC intrinsically safe terminals on TB1. For non-intrinsically
safe interlocks, attach one wire to terminal 1, 2, 3 or 4 of TB3 and the other to one of
the COMMON terminals on TB3.
Refer to figure 11 (below) for an example of interlock wiring.
In this example, Normally Closed pressure switch is wired to intrinsically safe terminal
strips TB1 and TB2. Because the switch is wired to terminal 4 on TB2, an alarm will be
generated on Channel 4 when the switch opens. The second wire from the switch could
be attached to any of the +5VDC intrinsically safe terminals on TB1.

17
Always wire number to number (color to color) when establishing network connections between panels. The maximum
network wire run cannot exceed 3000’ (1000M).
After the network wiring connections have been made, the start and termination of the network must be designated by
installing jumpers on the first and last panel in the network. Each OR ITEPRO™ 2000 panel is equipped with a 2-pin
jumper located next to TB4 (see figure 12). On the first and last panel in the network, lift the jumper cap from the pins
and reinstall it so that both pins fit into the cap.
Wire Dry Contact Outputs
The OR ITEPRO™ 2000 features Normally Open and Normally Closed 100 mA dry contact outputs that can be
used to trigger a wide variety of external devices including relays, visual indicators, buzzers, and security system alarms.
Two sets of Form C dry contact outputs are provided on TB6. The example in figure 13 shows a security system alarm
panel wired in a Normally Closed configuration to TB6 of the OR ITEPRO™ 2000. The Form C outputs are shown
schematically (dashed box).
Figure 13
Wire Analog Inputs
Analog input devices (pressure transducers, thermocouples, etc.) can be interfaced with the telemonitor equipped OR
ITEPRO™ 2000 if they are wired into the analog input connections on TB3 (see figure 9). Figure 14 shows how a
pressure transducer might be wired to the OR ITEPRO™. Note that the transducers power supply must be provided by
the customer or purchased from Geotech.
Wire Totalizer
Terminals 8&9 on TB4 are available for wiring a totalizer to an OR ITEPRO™ panel that is equipped with the
telemonitoring option. Totalizers must supply a 0 to 5-24VDC pulse to the control panel. The pulse should be generated
by a solid state device (i.e. an open collector output). The pulse should be 1 msec wide minimum. The maximum rate of
pulses accepted by the panel is 120 pulses/gallon at 20 gpm this corresponds to 40Hz.

18
Figure 14
Connect odem
If your OR ITEPRO™ 2000 is equipped with the telemonitoring option, plug your phone jack into the receptacle of the
panel modem. Refer to figure 9 for location of modem connections.
Wire Current Sensors
To provide current sensing for 3-phase blowers or pumps, install the current sensors included with the control panel. Each
sensor must be installed around one leg of the blower or pump motor power wiring as shown in figure 15. Then run the
sensor leads into the OR ITEPRO™ control panel and wire to the terminal block provided. ecure the current sensor
with a nylon tie wrap.
In lightning prone areas, have your electrician install a phone line lightning arrestor.
Contact your telephone company for further information.
A sensor for single phase pumps is already mounted inside the control panel (if
the motor is less than 2-1/2 HP @ 230VAC or 1 HP @ 115VAC). When wiring the
pump to the panel, run one leg of the pump power wiring through the current
sensor as shown in the Field Wiring Diagram.

19
Figure 15
Wire Thermal Overloads
Additional thermal overload protection for your blower can be obtained by wiring from the Normally Closed thermal
overload contacts of your blower external motor starter to the OR ITEPRO™ panel. Wire to input terminals 5 and 7 on
TB3 after removing the existing jumper.
Set Blower Time Delay
As delivered from the factory, the panel is wired to shut down the blower 3 minutes after a High or Low Pressure condition
is detected. The time delay can be reduced to 7 seconds by installing a jumper between terminals TB4-5 and TB4-7.
When a blower thermal overload is sensed (blower thermal overload contacts
open), the blower will shut down and the THERMAL OVERLOAD indicator on
the panel will be illuminated.
Table of contents
Popular Control Panel manuals by other brands

Edwards
Edwards 2010-2-PAK-900 Registration Guide
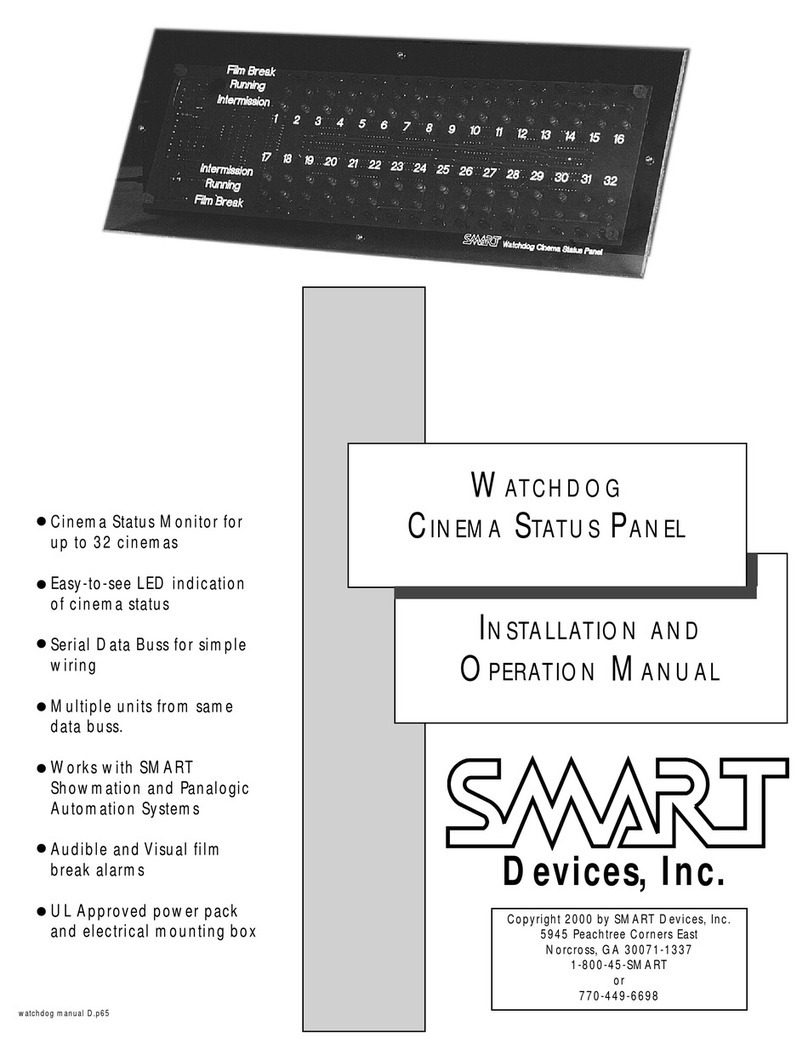
SMART
SMART Watchdog Installation and operation manual
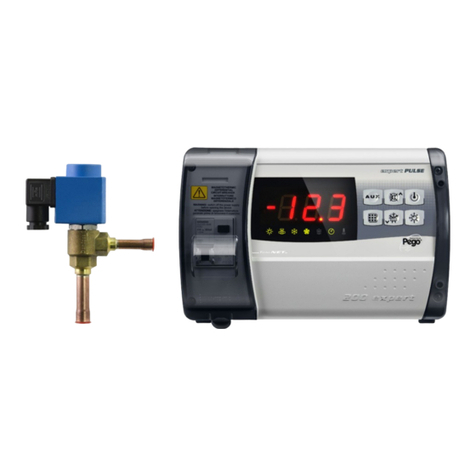
Pego
Pego ECP200 Expert d7.5 Use and maintenance manual
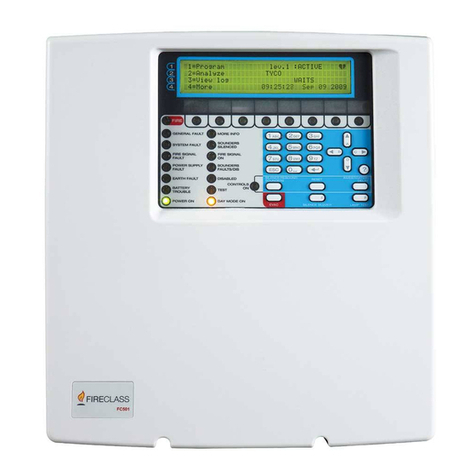
FireClass
FireClass FC501-L user manual

Electronic Devices Limited
Electronic Devices Limited ED591 instruction manual
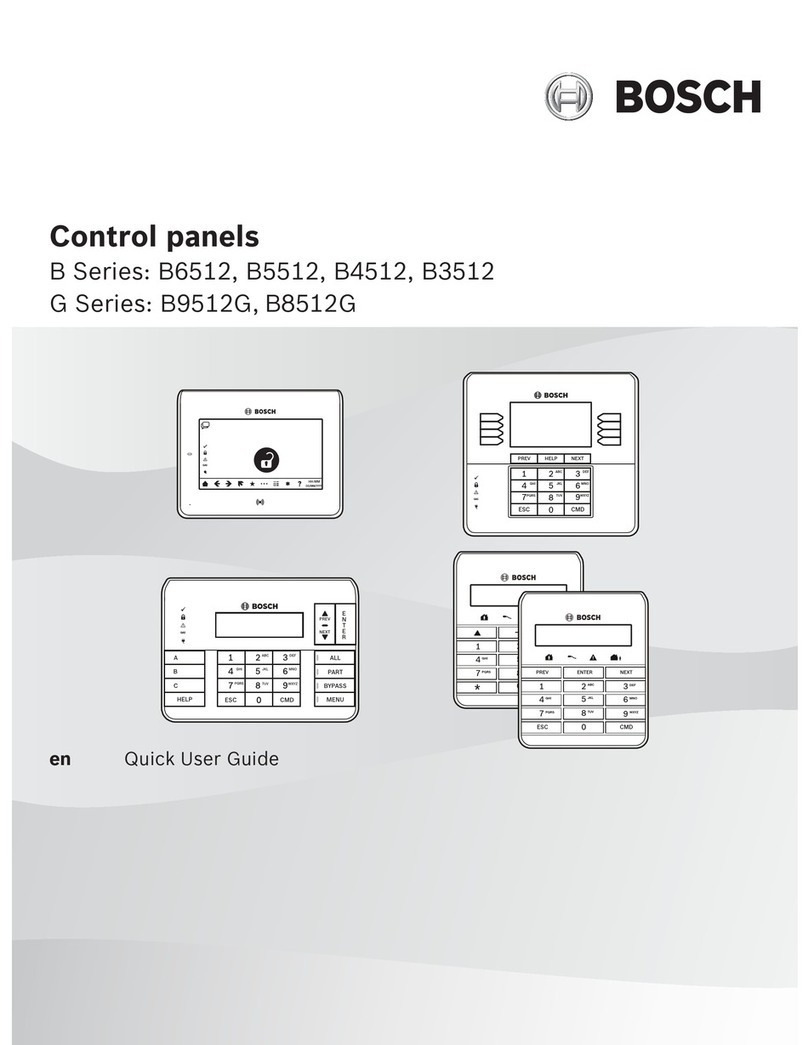
Bosch
Bosch B6512 Quick user guide
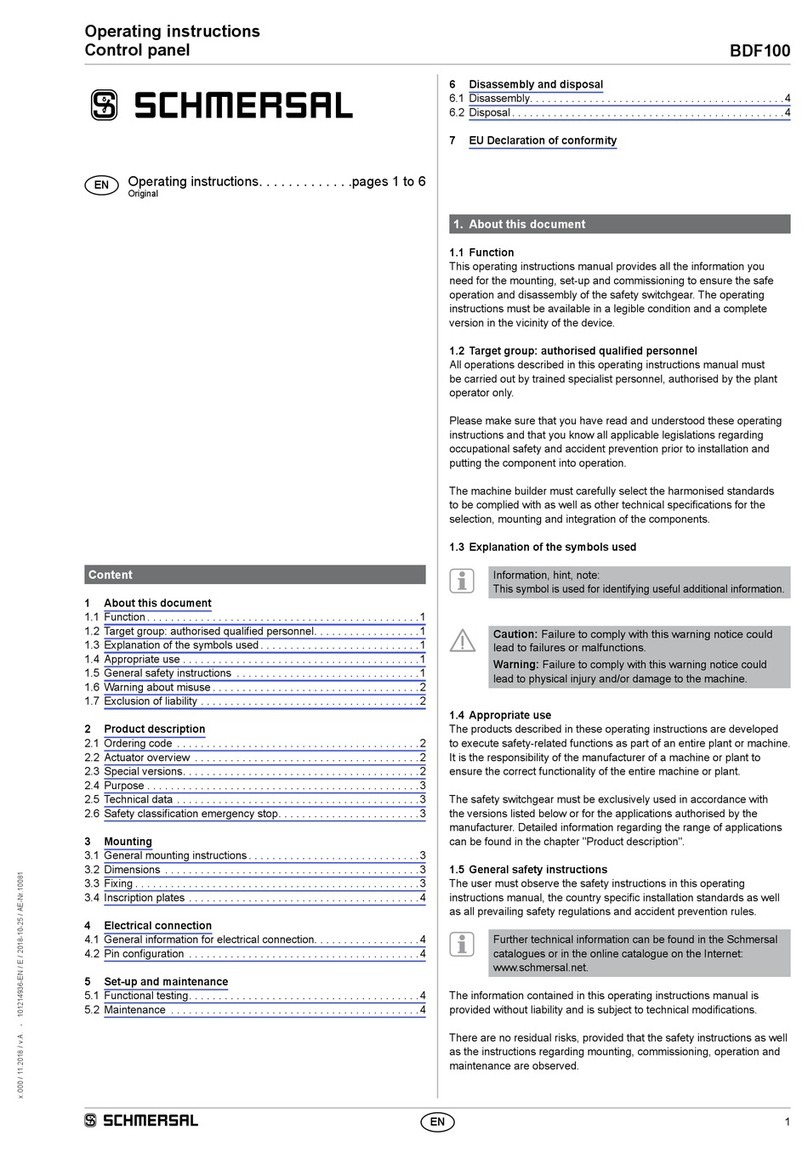
schmersal
schmersal BDF100 operating instructions
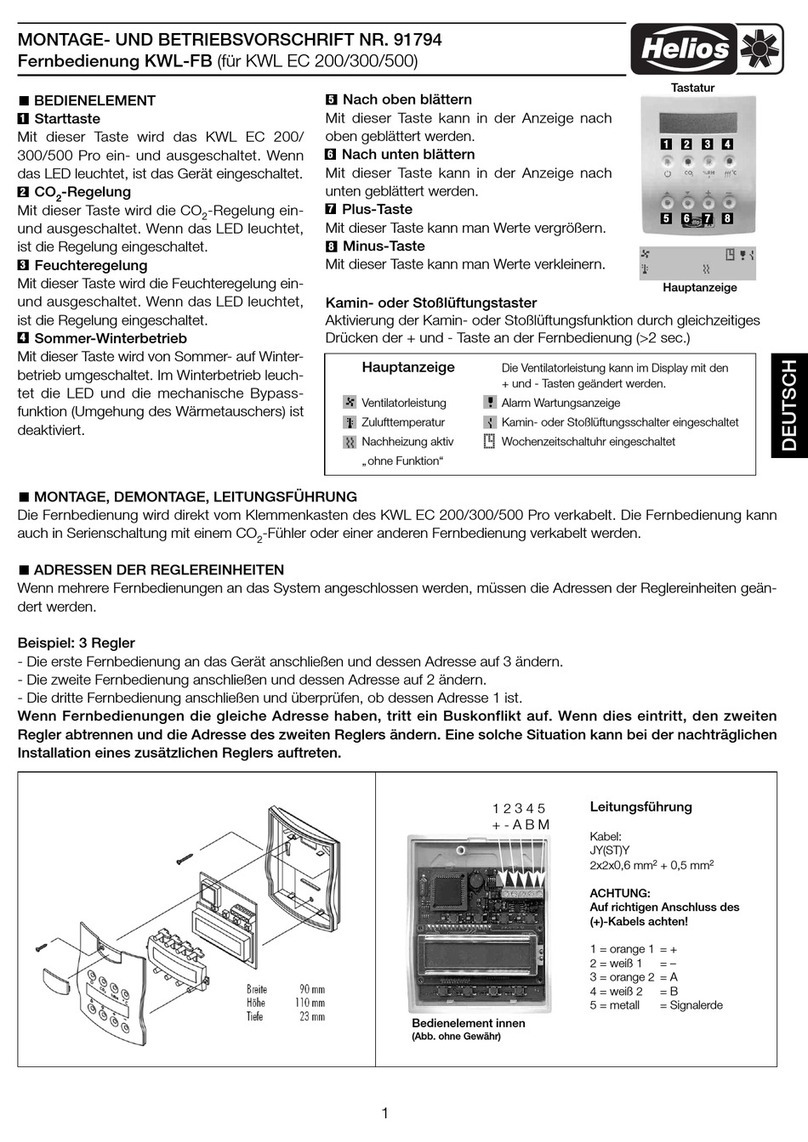
Helios
Helios KWL-FB Installation and operating instructions
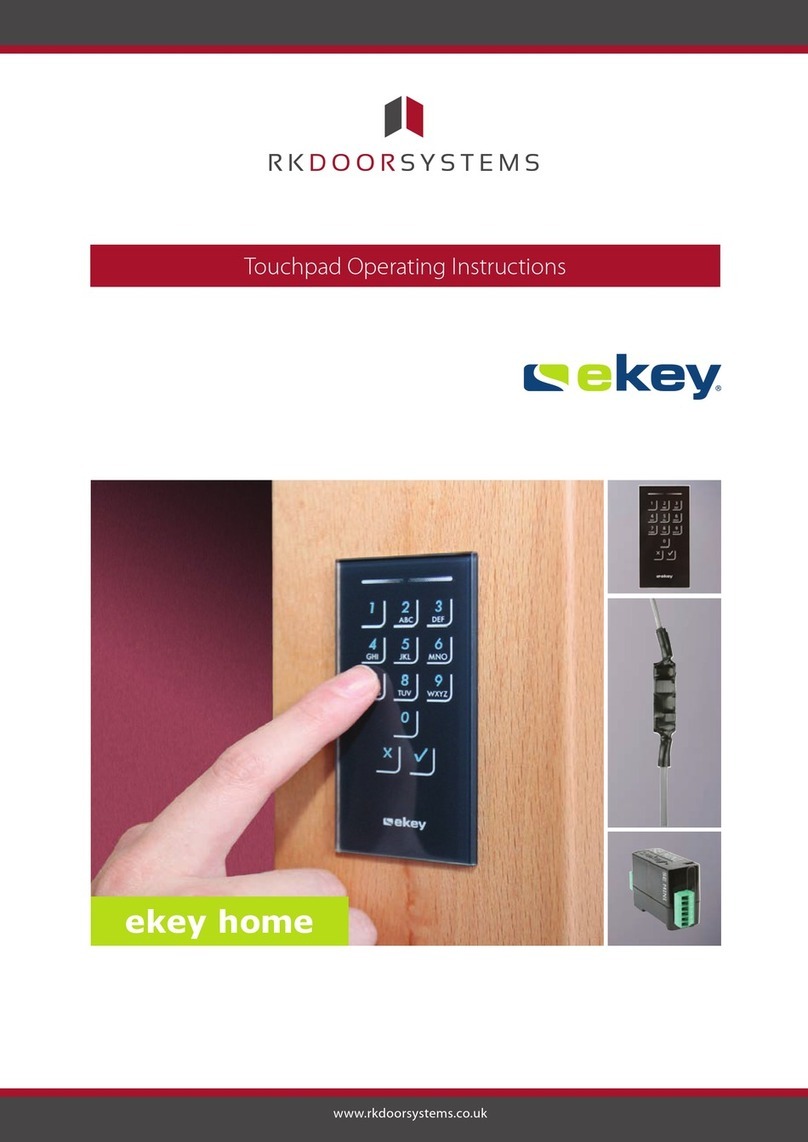
eKey
eKey home FS OM operating instructions
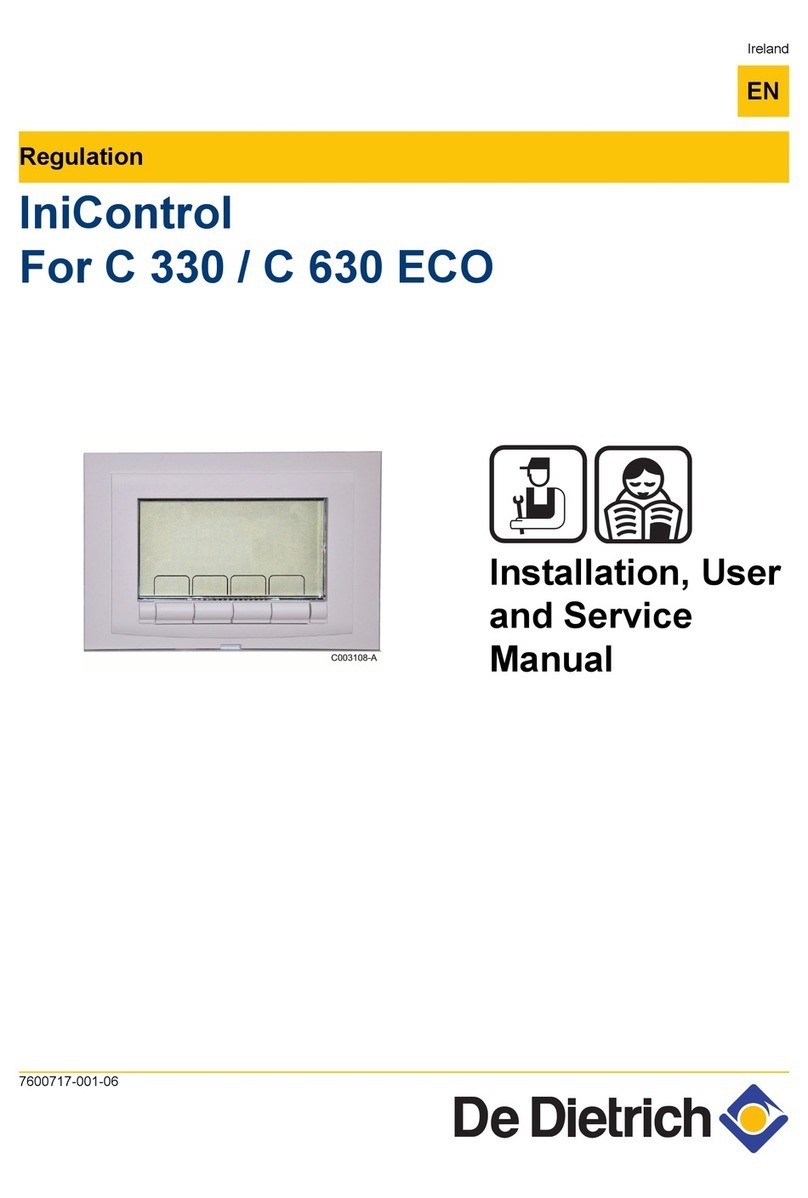
DeDietrich
DeDietrich IniControl Installation, user and service manual

Visonic
Visonic PowerMaster-33 G2 Installer's guide
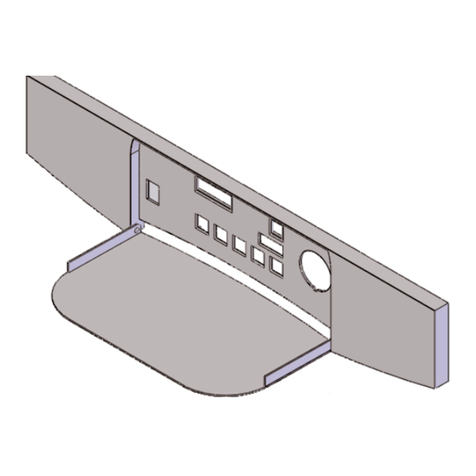
TriangleTube
TriangleTube PSCS01 Replacement