Giltrap MultiPlus Series Application guide

MultiPlus–All Models
Part Number: 67418
Operation & Parts Manual
AUSTRALIA
GILTRAP AG EQUIPMENT PTY LTD
105-117 Boundary Road
Laverton North
Melbourne
Vic 3026
TEL: +61 3 936 96 548
FAX: +61 3 936 96 549
FREE: 1800 127 030 (AU ONLY)
SALES: [email protected]
PARTS: [email protected]
WEBSITE: www.giltrapag.com.au
NEW ZEALAND (HEAD OFFICE)
GILTRAP ENGINEERING LTD
7 Main North Road
PO Box 83
Otorohanga
TEL: +64 7 873 4199
FAX: +64 7 873 8131
FREE: 0800 804 458 (NZ ONLY)
GENERAL: [email protected]
PARTS: [email protected]
WEBSITE: www.giltrapag.co.nz

Page 2
Multiplus Operation & Parts Manual
Disclaimer
While every attempt has been made to ensure that information and diagrams in this
manual are correct, Giltrap Engineering Limited will not be responsible for any damage
or consequential loss arising out of misinterpretation or failure to follow recommended
procedures; nor will it be liable for any damage caused by or arising out of modification
or misuse of its product.
For parts or service enquiries, please use the applicable contacts on the previous page.
Printed February 2020
Copyright 2020 by Giltrap Engineering Ltd.
Printed in New Zealand
All rights reserved. Reproduction or use, without express permission, of editorial or
pictorial content, in any manner, is prohibited.

Page 3
Multiplus Operation & Parts Manual
Table of Contents
Introduction......................................................................................................................4
Warranty..........................................................................................................................5
Serial Number Identification.............................................................................................6
General Safety.................................................................................................................7
Pre-Service Guidelines & Settings.................................................................................10
Greasing & Lubrication..................................................................................................11
Operation.......................................................................................................................13
Scales Display & Power Supply.....................................................................................16
Hydraulic Requirements ................................................................................................17
Hydraulic Hose Layout...................................................................................................18
Parts Section .................................................................................................................24
Notes.............................................................................................................................52

Page 4
Multiplus Operation & Parts Manual
Introduction
Thank you for purchasing a Giltrap product. Giltrap Engineering Ltd has enjoyed a
long-standing success with their machinery. We would like you to enjoy the benefits of
owning a Giltrap too. By following the guidelines laid out in this book, you will ensure
trouble free, low maintenance operating for years.
Giltrap Engineering Ltd is a progressive company which continually strives to satisfy
your needs, so we welcome any feedback which you can provide to help us improve our
products and services and to ensure that they perform to your expectations. Any
constructive comments about this operator’s manual are also welcome.
Your machine has been designed to perform its task efficiently and with a minimum of
maintenance. This handbook provides safety guidelines, instructions, maintenance
requirements and parts listings. We recommend that you read the entire handbook,
before operating the machine as this will enable you to take full advantage of your new
machine’s considerable potential.
Manual Evaluation
We update our operating manuals regularly. Your suggestions for improvement help us
to create even more user friendly manuals. Send your suggestions by email to
Delivery and Warranty
Before you begin to use your machine, please check it to make sure there is no delivery
damage. If damage is evident, contact the dealer who supplied the machine so that
they can make the appropriate claims.
If you have any other queries, please contact your dealer or Giltrap Engineering Ltd
(0800 80 GILTRAP).
All Giltrap products are covered by a 24-month warranty on parts and labour, subject to
normal use.
Please fill in the details below for future reference.
Model:
Serial No:
Delivery Date:
Dealer:

Page 5
Multiplus Operation & Parts Manual
Warranty
The Goods specified in the Price List as designed and supplied by Giltrap Engineering
Ltd are warranted against faulty workmanship and defective materials for a period of 24
months from the date of purchase. In addition to the primary 24 month warranty for
Giltrap products, there is a further 12 month structural warranty for the goods, against
faulty workmanship and/or defective materials for structural items only. The structural
warranty does not apply to electronics or component parts.
Such warranty is subject to the following conditions:
1. This warranty covers the repair or replacement of parts or machinery sold by the
manufacturer and damaged as a result of the faulty workmanship or materials in such
parts or machinery. It does not extend to any other loss or damage including
consequential loss or damage or loss to other property or persons.
2. Without limiting the generality of paragraph 1 above, this warranty does not cover the
following:
(a) Travel expenses.
(b) Damaged caused by accident, misuse or abuse.
(c) Damage to any goods which have been altered or modified by someone other than
the manufacturer or its authorised agent.
(d) Damage or loss to the goods due to their unsuitability for any particular use or for
using with any particular tractor except where such use or tractor had been specifically
approved by the manufacturer.
(e) Damage or loss where the fitting and installation of the goods were not carried out
by the manufacturer or its authorised dealer.
3. Procedure for recovery under warranty.
No loss or damage will be covered by this warranty unless the loss or damage is
reported immediately to the dealer (who will contact the distributor who will advise
whether it is covered by the warranty and undertake the necessary action).
No warranty repair work is to be undertaken prior to an order number being obtained.
This warranty shall be interpreted according to the laws of New Zealand and the parties
agree to submit to the jurisdiction of the Courts of New Zealand.
Warranty Claims
If you wish to make a claim under warranty:
Immediately stop using the machine.
List details of the machine and damaged item including serial numbers and date
of purchase.
Consult with your Giltrap dealer (supplier) and have him forward your claim and
the damaged item to Giltrap Engineering Ltd.
No warranty to be undertaken unless an order number is obtained from the Seller
(Giltrap Engineering Ltd) prior to any work being done.

Page 6
Multiplus Operation & Parts Manual
Serial Number Identification
Before ordering any parts, check the serial number and the delivery
date of the machine and include this information with all orders.
If the Serial Number Plate is missing, the serial number will be
stamped on the front of the drawbar.
Serial number stamped
onto chassis here

Page 7
Multiplus Operation & Parts Manual
General Safety
For the safety of others and yourself, please read and follow the precautions in this
operator’s manual. Pay particular attention to the following safety aspects of operating
machinery.
Do not ride on or allow passengers on the machine.
Always use a recognised hitch pin with a safety
clip to hook trailed implements on behind the
tractor.
Always ensure when using a quick hitch that the
locking tab has come out and is in the locked
position before moving.
When pulling trailed implements or loads, be sure
to use a tractor of greater or equal weight than
the combined weight of the load and trailer.

Page 8
Multiplus Operation & Parts Manual
Carry a suitable fire extinguisher.
A fire can ignite under certain conditions, so please take the following precautions:
After running your machine for a short time, check for defective
bearings. A faulty bearing can become very hot, eventually
discolouring, requiring immediate replacement.
Do not allow combustible material to accumulate inside guards or
around rollers and other moving parts.
If your machine becomes blocked, stop immediately and remove
the obstruction.
Be careful when operating in hot or dry conditions or on extreme
fire risk days.
Never operate your machine without the safety
guards in place.
All chains should be properly
adjusted and replaced when
necessary.

Page 9
Multiplus Operation & Parts Manual
Release all hydraulic pressure from
implements before commencing service
work. Never look for suspected oil leaks
with your hands or body - use a piece of
cardboard instead.
Any fluid that penetrates the skin will
have to be removed immediately by a
medical expert. Seek specialist advice
on this type of injury.
Never attempt to unblock equipment while it is
still operating.
Always disengage power take-off, hydraulics and
shut down engine before removing materials,
checking or servicing.
Failure to follow these precautions is likely to
result in serious injury.
Wear proper protective clothing. Loose attire can easily
be snagged by rotating machinery resulting in serious
injury or death.

Page 10
Multiplus Operation & Parts Manual
Wheel Nut Recommended Torque Settings
M18 200 ft/lbs or 270Nm
M20 280 ft/lbs or 380Nm
Axle Mounting Bolt Recommended Torque Settings
M16 180 ft/lbs or 245Nm
M20 355 ft/lbs or 480Nm
Recommended Tyre Pressures
11.5/80-15.3 60psi 4.1 bar
400/60-15.5 65psi 4.5 bar
15.0/70-18 62psi 4.25 bar
385/65-22.5 (15RX22.5) 79psi 5.5 bar
500/45-22.5 52psi 3.6 bar
500/60-22.5 40psi 2.8 bar
Pre-Service Guidelines & Settings
Prior to delivering your machine, your dealer should have completed a pre-delivery
check.
It is beneficial to check the following points before using the machine for the first time.
CHECK FLOOR CHAIN TENSION. A simple check is to stand in the bin and exert a
strong pull at the centre of the floor. There should be approximately 75mm (3”) of
vertical movement in this area.
CHECK ELEVATOR CHAIN TENSION. With elevator fully raised, exert a pull at the
mid-point of the outside elevator face. If necessary, adjust for approximately 35mm (1-
1/2”) of movement from rest outwards.
CHECK ALL WHEEL NUTS ARE SUFFICIENTLY TIGHT.
CHECK ALL TYRE PRESSURES ARE CORRECT.
CHECK ALL AXLE MOUNTING BOLTS AND NUTS ARE SUFFICIENTLY
TIGHT.
THERE ARE SEVERAL GREASE POINTS on all Giltrap feeders. Check the
yellow label on the side of your machine to see how many grease points there
are. You should fully grease everything before running it for the first time. See
page 11-13 for greasing and lubrication details.

Page 11
Multiplus Operation & Parts Manual
Greasing & Lubrication Schedule
Elevator Shaft Bearings –Grease monthly
Cross Conveyor Shaft Bearings –Grease monthly
Elevator Ram Pivots –Grease monthly
Floor Driveshaft Deadeyes –Grease every 10 loads
Floor Idler Sprockets –Grease every 10 loads
Axle Bushes –Grease every second day
Wheel Hubs –Grease every 3 months
Rear Gate Latch –Grease every 3 months
Rear Gate Pins –Grease monthly
Tow Eye –Grease monthly
Jack Stand –Grease monthly
Greasing & Lubrication
Shaft Deadeye Remote
Greasing Bank
MULTIPLUS 13 X3
MULTIPLUS 16, 18 X5
Ram Pivot
X4
Swivel Tow
Eye
Jack
Elevator & X-Conveyor
Shaft Bearings
X8

Page 12
Multiplus Operation & Parts Manual
Tailgate Pivot
X4
Tailgate
Latch
Rear Idle Sprocket
MULTIPLUS 13 X2
MULTIPLUS 16, 18
X4
Wheel Hub
X4
Axle Bushes
X4

Page 13
Multiplus Operation & Parts Manual
Oil & Grease
Grease Grade Recommended
NLGI 2 oil based
Cross Conveyor Gearbox
Type: Berma RT120-40
Oil: GL-5 80w-90
Main Floor Drive Gearbox
Type: Berma RT200-40
Oil: GL-5 80w-90

Page 14
Multiplus Operation & Parts Manual
Operation
Loading the Feeder
Load the feeder from the rear to the front. When difficult material has to be handled, e.g.
long, wet silage, load the material in sections.
Feeding Out
Best feeding out conditions occur when the feeder is freshly loaded. If left loaded
overnight, the material can settle into a hard mass that becomes difficult to feed out.
The practice of leaving a load in the machine for hours before feeding out will also
accelerate the deterioration of the machine because of the acidic nature of the material.
Standard Control
Standard machines will require three hydraulic remotes - one for each of the main
functions. The main floor conveyor, the cross conveyor / elevator, and the elevator
position.
When pressure is supplied to the standard valve block (HCV1918A-1), the elevator will
run continuously and the cross conveyor will move as required to keep the feed against
the elevator. The relief on the valve block can be adjusted via the knob on the left of the
machine. Winding the adjuster clockwise increases relief pressure which will increase
the feed rate.
The main floor is manual and requires the operator to control the movement of feed
from the bin onto the cross conveyor. If required, the main floor can be reversed.
The elevator position can be adjusted to feed into troughs or over/under fences.
The standard side gate on the left of the machine can be unlatched and can be used to
feed out.
Diverter Valve Control Option
Machines fitted with a diverter valve will require two hydraulic remotes. One will supply
the diverter valve and the other will control the standard valve block. The diverter valve
can be switched via the in-cab control to supply the elevator ram circuit or the main floor
conveyor motor. The other remote will control the cross conveyor and elevator
(HCV1918A-1) as per standard spec above.
The diverter valve is controlled by a coil which is powered on or off to give the two
selectable positions. When the coil is switched off, the valve is in position 1 which
diverts flow to the main floor motor. When the control is switched on the coil moves the
valve into position 2, diverting flow to the elevator ram circuit.
It is recommended that the diverter valve switch be connected to an ignition switched
power supply so that if the controller is left set to the position where the coil is switched
on and the tractor is turned off, the battery is not drained.

Page 15
Multiplus Operation & Parts Manual
Joystick Control Option
Machines fitted with joystick control will require one hydraulic remote. This supplys a
valve block which is controlled by the in-cab joystick and switch. The joystick controls
the cross conveyor feed (Joystick left and right) and the main floor feed (Joystick up and
down). The feed rate can still be adjusted as standard, using the adjustment knob on
the left side of the machine. The momentary switch controls the elevator position.
The joystick control valve block is controlled by 6 coils. The coil plugs on the valve
block, numbered 1-6, are connected as show below:
COIL 6
COIL 5
COIL 4
COIL 3
COIL 2
COIL 1
HOSE A1
HOSE B1
HOSE A2
HOSE B2
HOSE A3
HOSE B3
Elevator Up
Elevator
Down
Main Floor
Forward
Main Floor
Reverse
CC Right
CC Left

Page 16
Multiplus Operation & Parts Manual
Scales Display & Power Supply
The remote display is designed to be mounted in the tractor cab and be easily
accessible to the driver. It contains a radio frequency (RF) communication device to
communicate with the scale system.
It will require shielding from the weather elements of sun and rain etc.
The remote display requires 12-24 volts DC to operate. It will typically only draw 0.2A.
The power supply must originate from the tractor battery as part of the installation loom
(supplied with the machine).
The scales system is powered from the tractor while operating. When disconnected
from the tractor, it draws power from its own sealed lead acid battery.
The tractor requires an installation loom (supplied) which provides a switched and fused
positive and negative supply from the tractor battery to the rear 7-pin socket. The tractor
battery is the best power supply point as it provides the most stable and “quiet” power
source. Do not use any other power source.
Tractor Plug
There are three CPC connectors on the Control module.
If a connector is not used, place the terminal cap over it.
RF positive supply
from wiring loom
(BROWN)
RF negative supply
from wiring loom
(BLUE)
Terminal cap
Wagon plug:
RF positive supply
(BLACK) wire to be in
pin 2
RF negative supply
(BLUE) wire to be
combined with (WHITE)
wire into pin 3

Page 17
Multiplus Operation & Parts Manual
Hydraulic Requirements
For optimal machine performance the tractor used should be checked to provide an oil
flow rate of between 30 and 45 litres per minute at full working pressure –Usually
between 2500psi (170 Bar) and 2800psi (190 Bar). If these conditions are not satisfied,
the feeder will perform poorly or not at all.
Technical Notes:
Machines that develop or operate with a jerking or shuddering action can be
rectified by fitting a non-standard inline valve (SCCB 154Z P8) with relevant
fittings between the port marked “ELEV PRES: and the elevator motor. This
preloads the hydraulic circuit and smooths the operation.
Quick Valve Orifice Diagnosis
If orifice (5) is blocked then the cross conveyor
will not drive load onto elevator when loaded.
If orifice (6) is blocked then the floor will not slow
down when the DPBB (3) is adjusted out and
floor will likely overload and stall the elevator.

Page 18
Multiplus Operation & Parts Manual
Hydraulic Hose Layout
Standard
HCV1918A-1
HCV331K

Page 19
Multiplus Operation & Parts Manual
Option 2 –Diverter Valve
HCV1918A-1
HCV331K

Page 20
Multiplus Operation & Parts Manual
Option 3 –Joystick Control
HCV1918A-1
HCV331K
Table of contents
Other Giltrap Farm Equipment manuals
Popular Farm Equipment manuals by other brands
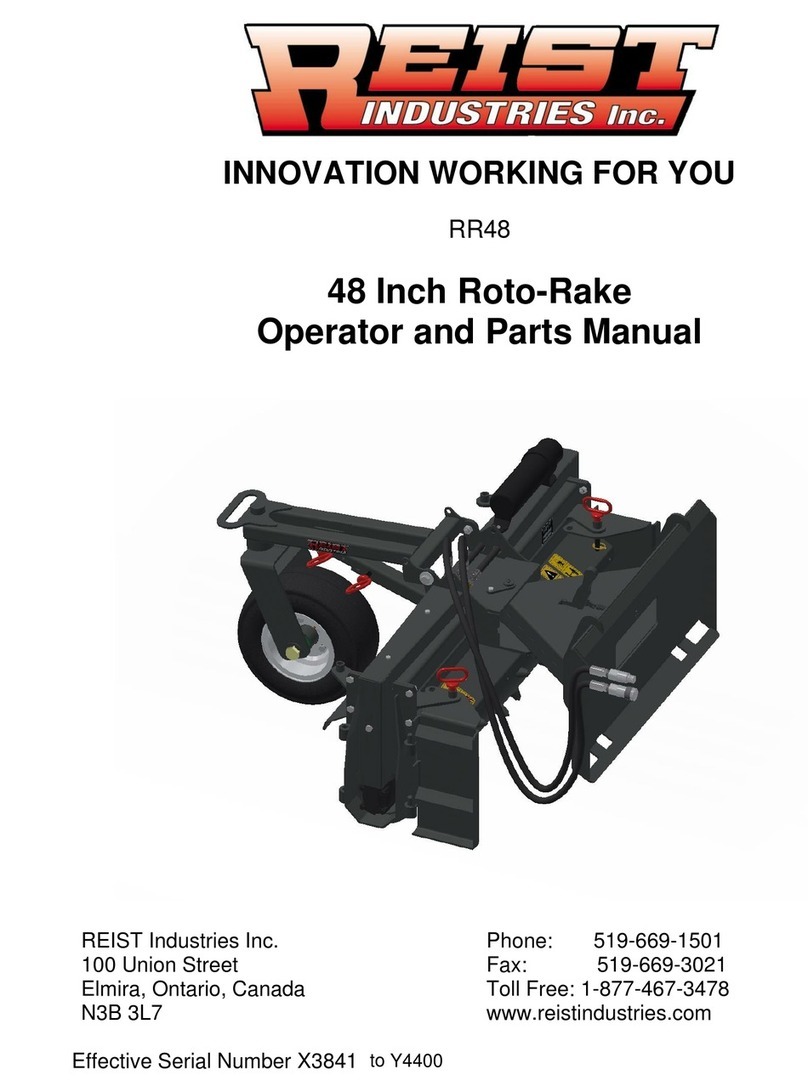
REIST INDUSTRIES
REIST INDUSTRIES RR48 Operator and parts manual

CAMPAGNOLA
CAMPAGNOLA SPEEDY Use and maintenance manual

Krone
Krone BiG X 600-3 Original operating instructions
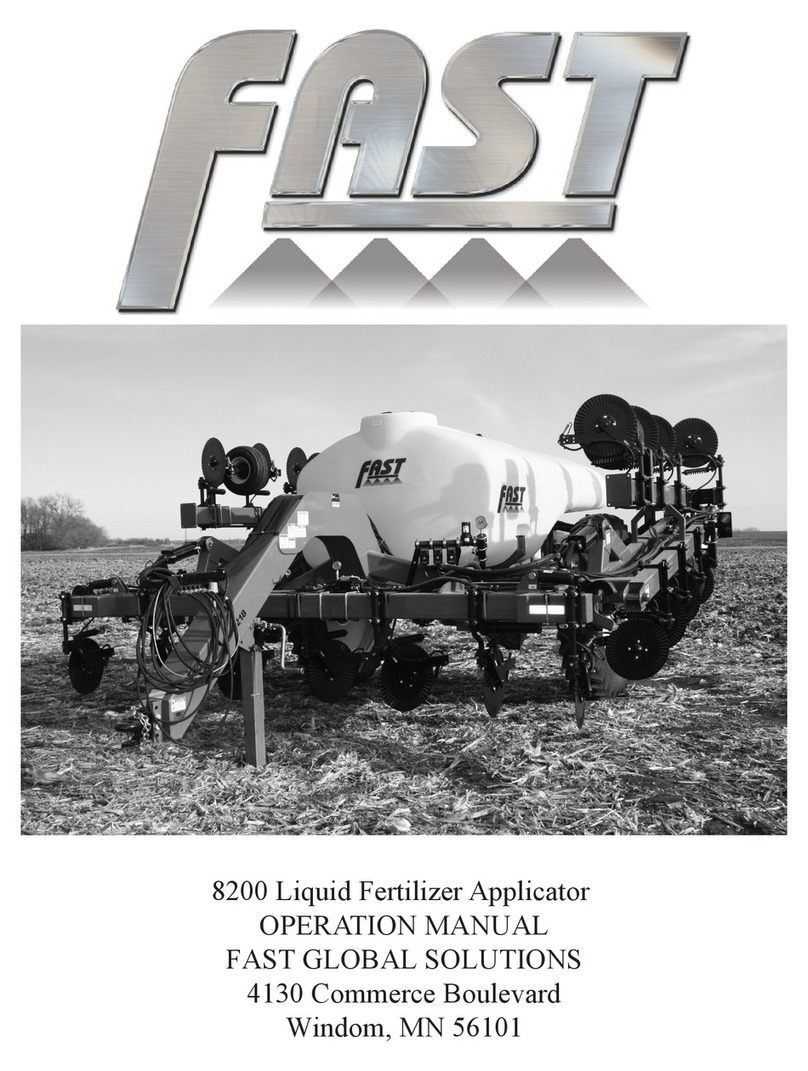
Fast
Fast 8200 Operation manual

Chapman Machinery
Chapman Machinery TF Series Original instructions
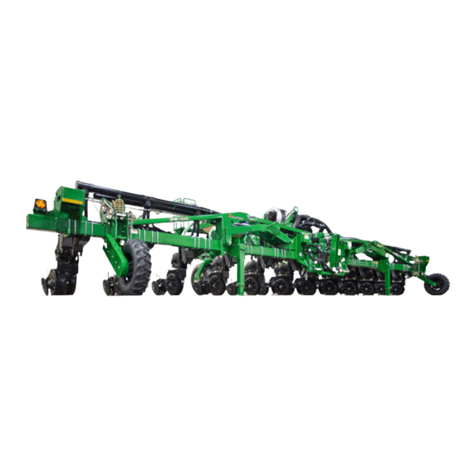
GREAT PLAINS
GREAT PLAINS Yield-Pro 3PYP Operator's manual
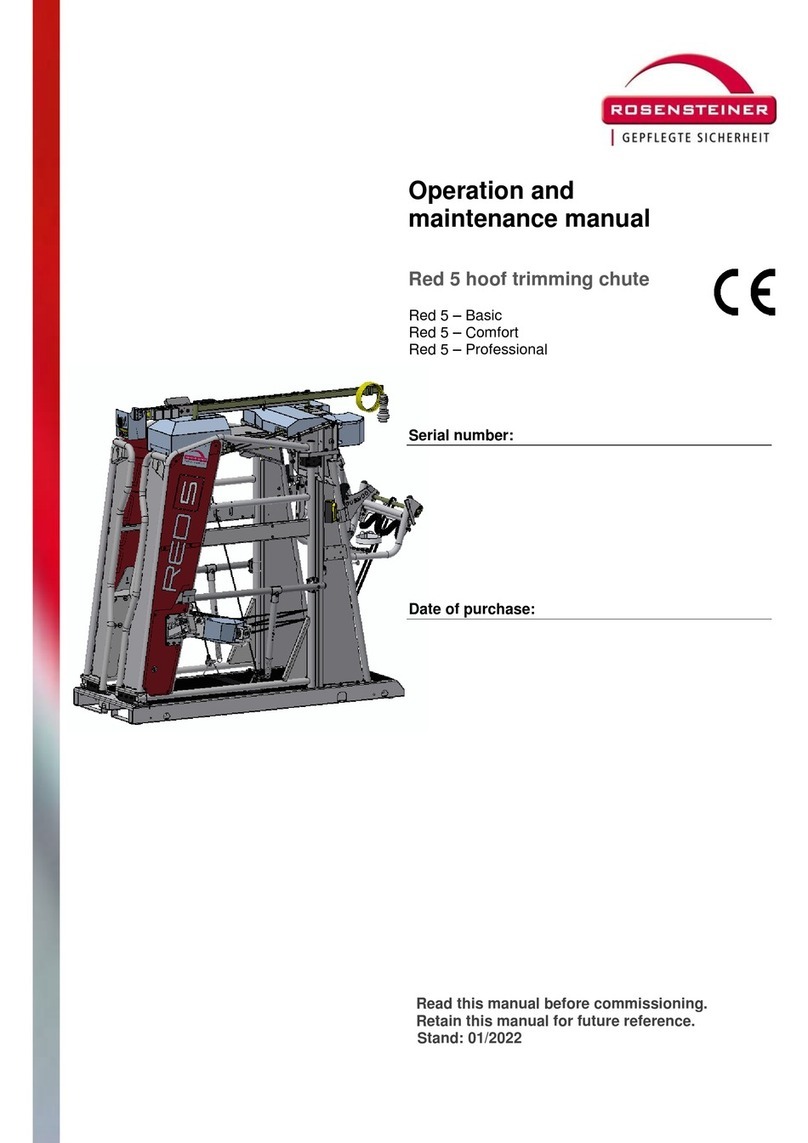
Rosensteiner
Rosensteiner Red 5 Operation and maintenance manual

aivituvin
aivituvin XZ7002 instruction manual

Landoll
Landoll Brilllion Till'N Seed BPSB-8 Operator's manual
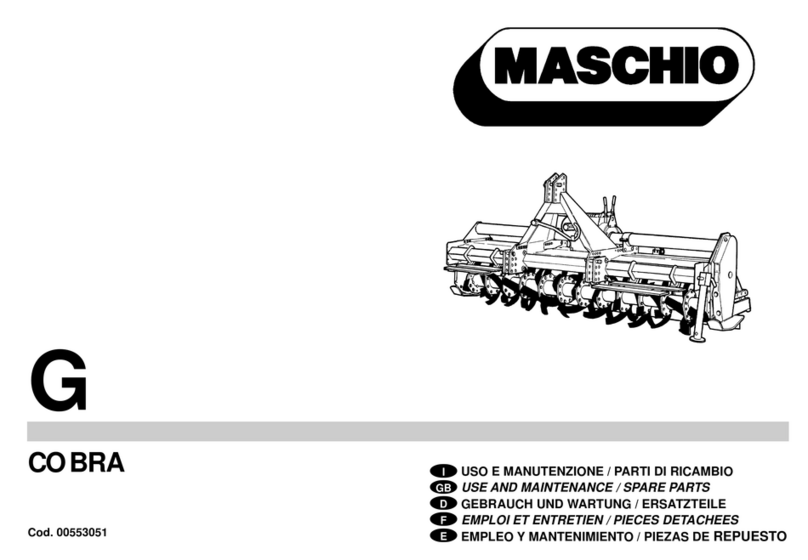
Maschio
Maschio COBRA 00553051 Use and maintenance / spare parts

Janschitz
Janschitz Milky FJ 32 Operating instruction
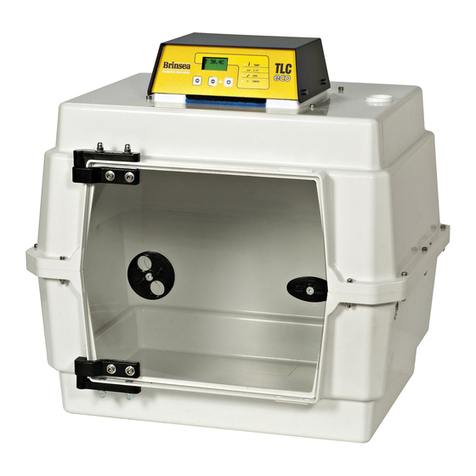
Brinsea
Brinsea TLC-40 User instructions