Globaljig Quick Pull Service manual



3
INDICE
1. GENERAL CHARACTERISTICS....................................................................4
1.1. Identification data.................................................................................4
2. INTENDED USE ...............................................................................................5
2.1. Technical characteristics table..........................................................5
2.2. Quick Pull Hydraulic Power Lift encumbrance dimensions....6
2.3. Quick Pull Hydraulic Power orientation.........................................7
3. PACKAGING .....................................................................................................8
4. HANDLING........................................................................................................8
5. POSITIONING AND INSTALLATION........................................................9
5.1. Identifying the working position....................................................10
5.2. Fastening the hydraulic lift’s base to the floor.........................11
6. SYSTEM CONNECTIONS.............................................................................12
6.1. Airdraulic connection..........................................................................13
6.2. Electrical connection...........................................................................14
7. QUICK PULL ELECTRO-HYDRAULIC CONTROL UNIT (400v) .......15
8. SAFETY ZONE ................................................................................................17
9. RAISING AND LOWERING THE HYDRAULIC POWER LIFT............18
10. TROUBLESHOOTING...................................................................................19
11. WARNINGS AND PRECAUTIONS TO BE TAKEN.................................20
12. SAFETY DEVICES..........................................................................................21
13. INSPECTION AND MAINTENANCE.........................................................22
14. WARRANTY ....................................................................................................22
15. DECOMMISSIONING AND DISPOSAL...................................................22
16. MACHINE LOG...............................................................................................23
17. ANNEXES.........................................................................................................25

4
1. GENERAL CHARACTERISTICS
The Quick Pull is a hydraulic power lift with a scissor-like structure which has
been designed and built to guarantee load bearing stability during both
raising and lowering operations.
The raising and lowering movements are carried out by a pair of single-
action hydraulic jacks which are controlled by an electro-hydraulic control
system. The hydraulic lift has reduced encumbrance dimensions and allows
for the work operations to be performed at a suitable height.
This manual is
supplied together with the machine, is to be considered an integral part of
the machine itself and must always remain with the machine, even in the
case of sale to a third party: The manual must be preserved in a safe place
in proximity to the hydraulic lift’s place of installation and use.
The manufacturer reserves the right to make any changes to the lift
described in this manual without prior notice, save for the observance of any
eventual prior agreements with the purchaser.
1.1. Identification data
Manufacturer: GLOBALJIG INTERNATIONAL s.r.l.
Via Aurelia Ovest Km 383
54100 Massa – Italy
Model: QUICK PULL
Type: Hydraulic power lift for motor vehicles – max capacity 2500 Kg
Machine data label:

5
2. INTENDED USE
The Quick Pull is intended for AUTO-REPAIR activities. It is not designed,
nor is it suitable, for lifting people. The hydraulic power lift must be used
inside the workplace and be protected from the weather (rain, humidity,
wind, etc.). The temperature of the workplace in which the lift will be
installed must never be less than 10 ° C nor above 40 ° C. The weight of the
structure and the maximum capacity limit are provided in this manual.
The Quick Pull has not been designed in such a way so that people may
perform operations of any kind beneath the lift’s structure or beneath its
support devices. Failure to take account the intended machine uses
described herein could lead to serious operator risks. The responsibility for
any such risks shall be borne by the operators themselves. The user is
required to use the lift in accordance with its intended use, with all of the
manufacturer's specifications, as well as in compliance with the current
workplace safety and accident prevention standards.
Important: The manufacturer shall bear no responsibility for any
damages caused to persons or property resulting from improper use,
carelessness or uses other than those for which the hydraulic power
lift is expressly intended.
2.1. Technical characteristics table
MEASUREMENT UNIT OF MEASURE QUICK
PULL
Maximum capacity Kg-lb 2500 - 5513
Minimum platform height from the ground mm-inch 100-3.94
Maximum platform height from the ground mm-inch 1340 - 52.76
Platform length mm-inch 2622 - 103
Platform width mm-inch 783 – 30,8
Hydraulic power lift base length mm-inch 1705- 67.13
Hydraulic power lift base width mm-inch 730 – 28,73
Hydraulic circuit operating pressure bar-lb/inch2300 - 4213
Compressed air supply circuit pressure bar-lb/inch28-110
Ascent time sec 40
Descent time sec 80
Electric motor power Kw/hp 2.2/1.6
Electrical power supply voltage Volt 230/380/400
Electrical power supply frequency Hertz 50/60
Auxiliary command circuit voltage Volt 24
Hydraulic power lift mass (weight) without accessories Kg/lb 865/548,4
Acoustic pressure level at the operator’s station: LpA Db(A) 54.5
Average acoustic pressure level considered: LpAm Db(A) 56.7
Acoustic power level: LwA Db(A) 73.6
Control unit oil quantity Litres/Gall 5/1.15

6
2.2. Quick Pull Hydraulic Power Lift encumbrance dimensions

7
2.3. “QUICK PULL” Hydraulic Power orientation
The frontal portion of the hydraulic power lift (as indicated in the diagram) is
the “side with the “hydraulic lifting jacks” and the control unit connections
outputs.
In order to obtain maximum stability upon the platform, always orient the
heaviest portion of the load at the front of the hydraulic power lift..
HYDRAULIC JACKS
FRONT SIDE

8
3. PACKAGING
The specific components which make up the Quick Pull hydraulic power lift
are packaged as follows:
Component Packaging type
a) Hydraulic power lift wooden pallet Kg 650
b) Control unit wooden crate Kg 50
c) Various accessories cardboard box Kg 350
When opening of the packages is recommended to check that the declared
parts correspond to the actual contents of the packages and that the
merchandise has not suffered damage during transport. Since the purchaser
is responsible for the merchandise during transit, save for different
agreements stipulated upon purchase, these inspections should be
performed in the presence of the courier. The manufacturer shall not answer
to any claims for damages suffered during transport, loading, unloading
and/or improper unpacking.
4. HANDLING
Handling of the consignment must be performed in compliance with the
current safety regulations by personnel who has experience with mechanical
load handling. Said personnel must be equipped with suitable protective
clothing. The manual handling of the package containing the hydraulic power
lift itself is expressly forbidden. The hydraulic power is packaged separately
from its electro-hydraulic control unit and its accessories. The relative
connections to these components must be performed during installation.
Important: Loading and unloading operations must be performed using a
forklift truck or other lifting devices of suitable capacity, with reference being
made to the package weights listed in the technical characteristics table. The
hydraulic power lift must be handled with a forklift truck or a bridge crane of
suitable capacity when moving it from the means of transport to its place of
installation.

9
5. POSITIONING AND INSTALLATION
The Quick Pull is a fixed hydraulic power lift that must be permanently
installed in a pre-established well-lit location, which is sheltered from the
atmospheric elements and free of flammable gases or vapours. The
hydraulic power lift must be installed at floor level and fixed with the
supplied anchoring screws.
The cement flooring, upon which the hydraulic power lift will rest, must be
level and integral and must possess suitable load-bearing characteristics.
The reinforced concrete must have a load bearing capacity of at least 300
kg/cm2, a concrete class of no less than 300 rbk and a cast depth of no less
than 200mm. All of the tubes and electrical cables for connecting the
hydraulic power lift’s base to the mobile control unit must be:
positioned in such a way so as to not be damaged during positioning.
covered by the metallic Omega protection which can be supplied upon
request
Note. The hydraulic power lift must be fastened to the ground with the
appropriate supplied “anchoring screws”.
ATTENTION
Failure to comply with this mandatory requirement could lead to
risks of load tipping with potentially serious consequences for
people and objects.
In cases where, during the installation of the hydraulic power lift,
the supplied cables result as not being of sufficient length, the
electrical connections must be redone without splicing the cables.
The hydraulic power lift’s intake air pressure must not be less than 8
bar.
The control unit must be positioned at least 3,000 mm from the edge of the
hydraulic power lift.
The operator is likewise required to only use the button panel at a safe
distance from the hydraulic power lift (at least 3,000 mm), and always from
the front of the structure, in order to avoid the risks associated with
potential lateral load capsizing.
The raising and lowering of the hydraulic power lift must always be
monitored by the operator. The operator must immediately arrest the
manoeuvre in the improbable event of load shifting.
Attention: No obstacles must be located behind the operator which could
impede the operator from distancing himself/herself from the machine in the
event of immediate danger.

10
5.1. Identifying the working position
In order to work in complete safety, it is necessary that the operator be
positioned at a distance of 3.00 m from the edge of the machine, without
interfering with any other equipment, so as to be able to directly monitor the
lifting and/or lowering operations without being impeded from quickly
distancing himself/herself. For this reason, a rectangular area of at least
8.00 m by 6.90 m must be available within the garage.
The flooring must be perfectly level and horizontal, and its concrete must
possess, as a minimum, the characteristics described in the previous section.
If the floor’s surface should be rough, irregular and/or not level, suitable
spacers must be placed beneath the base of the lift in order to ensure that
its support and anchoring points are level.
Failure to observe this requirement could compromise the
opening/closing functionality of the arms and could result in
structural loads which were not taken into consideration during the
hydraulic power lift’s design and testing which could, in turn, lead to
the deformation of the equipment.

11
5.2. Fastening the hydraulic lift’s base to the floor
Once the position of the hydraulic power lift within the garage has been
determined, perform the following operations before fastening it to the floor:
1. Centre the lift with respect to its established location;
2. Trace a yellow, rectangular perimeter line on the surrounding floor,
with a width of no less than 10 cm, parallel to the external edges of
the platform. The distance between the external edge of the yellow
line and the external edge of the pit must not be less than 20 cm on
every side of the pit;
3. Identify a rectilinear path for conducting the hydraulic power lift’s
tubing to the electro-hydraulic control unit.
After having performed the above operations, follow the procedure below to
fasten the hydraulic power lift to the floor:
1. Raise the platform to its
maximum height.
2. Use a percussion drill to
create φ20 holes
(A41884+KR20 anchor
lodgings) with a depth of
6 cm, using the holes
found on the base as a
reference template (see
the following image).
3. Clean the drilled holes
carefully.
4. Place the anchors in the
holes.
5. Use a heavy hammer to
drive the anchor into the
hole without damaging
the threading.
6. Tighten the nuts of the
anchors well to fasten the hydraulic power lift to the ground. See the
installation sequence diagram.
7.
INSTALLATION SEQUENCE DIAGRAM
Detail “A”
6 positions

12
6. SYSTEM CONNECTIONS
The connection between the control unit and the base of the
hydraulic power lift is made up of a sheathing which contains:
1 flexible oil-pressure tube (lift movements).
1 compressed air tube for controlling the opening of the arms;
ATTENTION
In order to avoid functional damage, REPLACE the air-tight
"transport" cap with the "working" cap (aerated) after having
positioned the control unit and before using the lift. The working cap
is found within a nylon bag inside the mobile control unit
COMPRESSED-
AIR SUPPLY
SAFETY
RELEASE
OIL PRESSURE
SUPPLY
LIFT BASE
CONTROL
UNIT

13
6.1. Airdraulic connection
After having removed the relative cap, connect the flexible oil pressure tube
by coupling the double key connectors. Tighten the connectors appropriately
(do not tighten excessively) and check that there is no leakage or drawing
after a brief period of function.
Connect the compressed air tubes using the quick connectors.
Connect the control unit’s air intake tube to the mains system.
IMPORTANT
A dehumidifier with a lubricator must be installed upstream from the
control unit on the compressed air distribution system.
The lack of this device could result in damage to the pneumatic solenoid
valve and thereby compromise the arm opening/closing functionalities.
Make sure that all of the connections have been performed properly.
Even a single incorrect connection or lack of contact will inhibit the
equipment’s proper function.
After having checked the control unit’s oil level (see the amount
recommended by the manufacturer in the Technical Characteristics Table),
raise and lower the lift 2 or 3 times in order to allow the air bubbles to be
purged from the hydraulic circuit.
It is absolutely forbidden for the user to tamper with the pressure
relief valve, which has been calibrated by the Manufacturer.

14
6.2. Electrical connection
Check the operating voltage and frequency of the hydraulic power lift’s
electro-hydraulic control unit. This information is provided on the label
located on the control unit’s protective guard.
The electrical distribution panel which powers the hydraulic power lift’s
control unit must contain a three fuse valves and a circuit breaker.
The connection between the electrical distribution panel and the control unit
must be performed using the supplied cable.
If the control unit’s electrical power cable is too short, it must be completely
replaced with a longer cable, with technical and safety characteristics
identical to those of the original.
IT IS FORBIDDEN TO SPLICE THE POWER CABLE
DANGER !!!
It is forbidden to connect the hydraulic power lift’s electrical system
directly to the garage’s system outlets: Distribution system
malfunctions could result in irreparable damage to the control unit
and serious operator injury.
Before connecting the control unit’s power cable to the electrical distribution
panel, make sure that the switch is in its “O” (off) position

15
7. QUICK PULL ELECTRO-HYDRAULIC CONTROL UNIT (400v)
1
2
3
4
5
6
RIF. CODE DESCRIPTION
1 GK6
AIR SOLENOID VALVE
2 GK7
OIL SOLENOID VALVE
3 GK8 1.85KW MOTOR
4 GK9
CONTROL UNIT
RIF. CODE DESCRIPTION
5 GK1
LIGHT BULB SOCKET
6 GK2
16°
SWITCH

16
7
8
9
RIF. CODE
DESCRIPTION
7 GK3
CONTACTOR
8 GK4
TRANSFORMER
9 GK5
CIRCUIT

17
8. SAFETY ZONE
Before using the equipment, make sure that the perimeter of the work area
has been delineated according to that which is described in section 5.1, in
such a way so that a safe distance from other equipment and/or surrounding
walls has been maintained.
Never stand within the working area while the hydraulic power lift is
manoeuvring. Only manoeuvre the lift under visual supervision and with
utmost care.
Always make sure that the work area is free of any type of work equipment
or other obstacles.
The operator must always have an escape route available behind him/her.
As already highlighted under point 5.1, the hydraulic power lift’s operating
area (Safety Zone) must conform to the following characteristics:
1. It must be at least 6.90 m long and 8.00 m wide;
2. the hydraulic power lift must be located at the centre of this zone;
3. The control unit (and consequently the operator when manoeuvring
the hydraulic power lift by means of the button panel), bust be located
at least 3.00 m from the lift’s structure (or rather, from outside of the
Safety Zone).
During raising and lowering operations, the Safety Zone must absolutely be
free of personnel, animals and any eventual objects.
Work must always be performed at a suitable height (MAX 1.300 mm) and
must never be performed beneath the vehicle or beneath the lift’s structure.

18
9. RAISING AND LOWERING THE HYDRAULIC POWER LIFT
After connecting the unit to
its electrical power and
compressed air supplies, turn
the switch on the mobile
control unit and engage the
emergency button on the
button panel.
After opening the load
support by means of their
relative command, the lifting
pads are to be positioned and
their thickness chosen
according to the requirements
(vehicle bottom). Press the
raise button again to raise the
load to the desired height.
The hydraulic power lift has a mechanical safety spear device which is
always on, while a total closure valve positioned directly upon the lifting
jacks will impede the lift from lowering at all times due to any eventual (and
improbable) air-pressure supply tube ruptures.
In order to lower the load, if the hydraulic power lift is in safe conditions,
raise the platform a few inches to release the safety catch then press the
lower button until the platform has descended completely.
The lower button is equipped double action: The first opens the discharge
valve, while the second sends air to the safety catch device in order to
disengage it.
This functionality allows for the hydraulic power lift to be placed in safe
conditions once the desired height has been reached; in fact, by lightly
pressing the lower button, the discharge valve opens and the lift descends
until the safety catch device engages within the its lodgings on the base,
thereby impeding further descent.
ATTENTION: When working upon the vehicle, the hydraulic power lift must
be placed in safe conditions by following the procedure described above.
Before and during all manoeuvres, always act in an attentive manner, while
checking the stability of the load.
After the descent has been completed, or rather, when the vehicle is resting
upon the floor on its wheels and the lift pads are no longer in contact with
the vehicle, release the lower button, remove the lifting pads and close the
arms.
Emergency button
LOWER button
Safety deactivation button

19
ATTENTION
At the end of the working day, or during breaks, always place the
lift’s platform in its resting position (completely on the floor). Loads
must never be left in a raised position in the absence of the
operator.
10. TROUBLESHOOTING
MALFUNCTION POSSIBLE CAUSE PROBABLE RESOLUTION
Loss of electrical
power.
Check the electrical
distribution panel and
adjust the main switch if
necessary.
Check the position of the
mushroom-head emergency
button on the console. If
necessary, disengage it and
press the reset button.
Turn off the main switch on
the electrical panel and
open the control unit’s
panel to check the status of
the fuses.
Replace them if necessary.
Motor breakdown. Replace the electric motor.
Pump breakdown. Replace the pump.
The lift does not
function.
Electrical connections. Check the efficiency of the
connections.
Insufficient oil in the
control unit’s tank. Check the tank’s oil level
and add oil if necessary.
When using the raise
command, the lift does
not rise or else
struggles to rise both
empty and loaded. Pump highly worn. Replace the pump.
Insufficient hydraulic
power lift capacity.
Oil pressure circuit
operating pressure
insufficient.
Use a pressure gauge to
check the operating
pressure and replace the
pump if necessary.

20
11. WARNINGS AND PRECAUTIONS TO BE TAKEN
The Quick Pull must be used by personnel over the age of 18 years who has
been duly trained and authorized with respect to that which is provided this
manual.
The instruction, use and maintenance manual must be read carefully
before the installation and use of the lift and must be properly applied in all
of its parts.
It is forbidden to use the machine for lifting people.
Before performing raising and lowering manoeuvres, always make sure
that the joints and the structure are free of tools, rags and objects of
any kind. In the event of accidental blockage during descent, immediately
stop the manoeuvre by releasing the button, raise the lift, remove the
obstacle and resume the descent manoeuvre.
In the case of power cables (for lighting, hand tools, etc.) present within the
lift’s manoeuvring area, always make sure that these do not pass over
or rest upon the structure in order to prevent them from being cut and
thereby conducting electrical current throughout the machine’s metallic
structure. This check must always be performed before the lift is activated.
Always check the load visually, especially during lifting, making sure that
it does incline or shift in an improper or abnormal fashion. In such cases,
lower the lift to ground level and position the vehicle properly.
Clean the vehicle support surfaces well regularly, as dirt build-up could
result in the load sliding.
Make sure that the air pressure input to the pneumatic circuit is
calibrated between 8 and 10 bar.
Ensure that the electrical system is equipped with an automatic
circuit breaker before connecting the cable to the electrical panel.
Bring the load to ground level at the end of the working day. Do not
leave the lift fully loaded.
The hydraulic power lift’s maximum capacity is 2,500 kg.
The operator is required to wear Personal Protection Devices and to
take all the necessary measures and precautions to ensure his/her own
safety.
WARNING
The safety devices must not be tampered with. These must always
be in optimal condition.
Table of contents
Other Globaljig Lifting System manuals
Popular Lifting System manuals by other brands
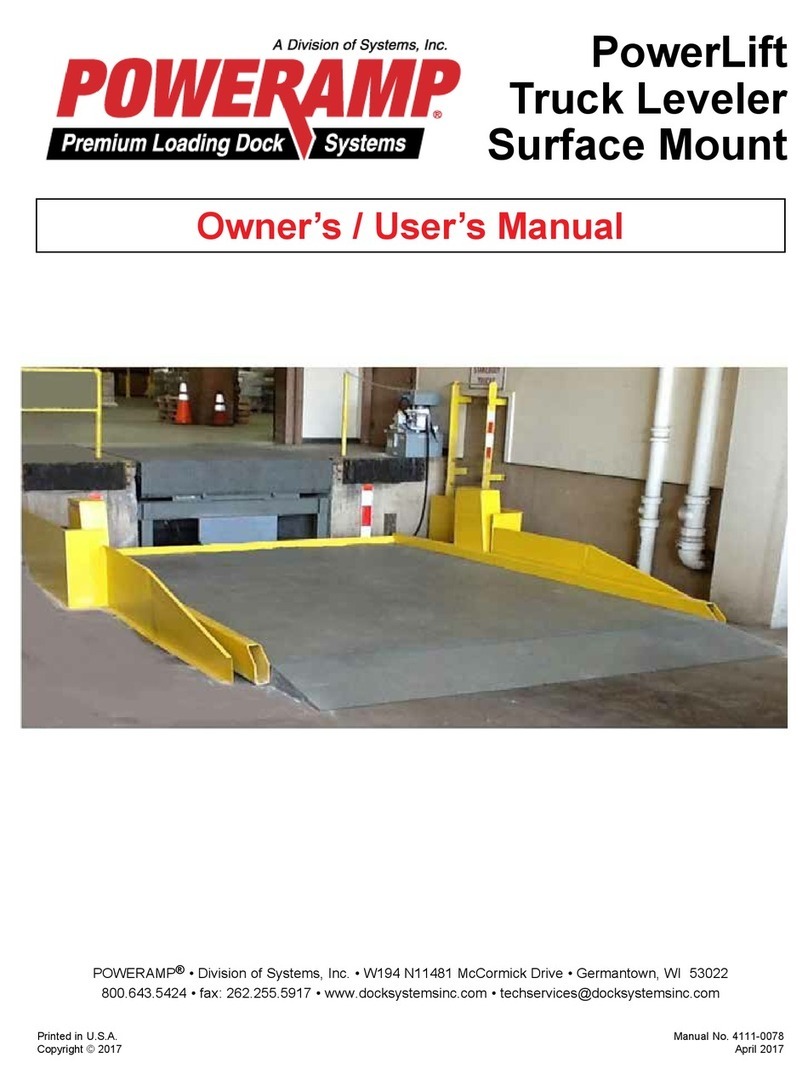
Poweramp
Poweramp PowerLift Owner & user manual
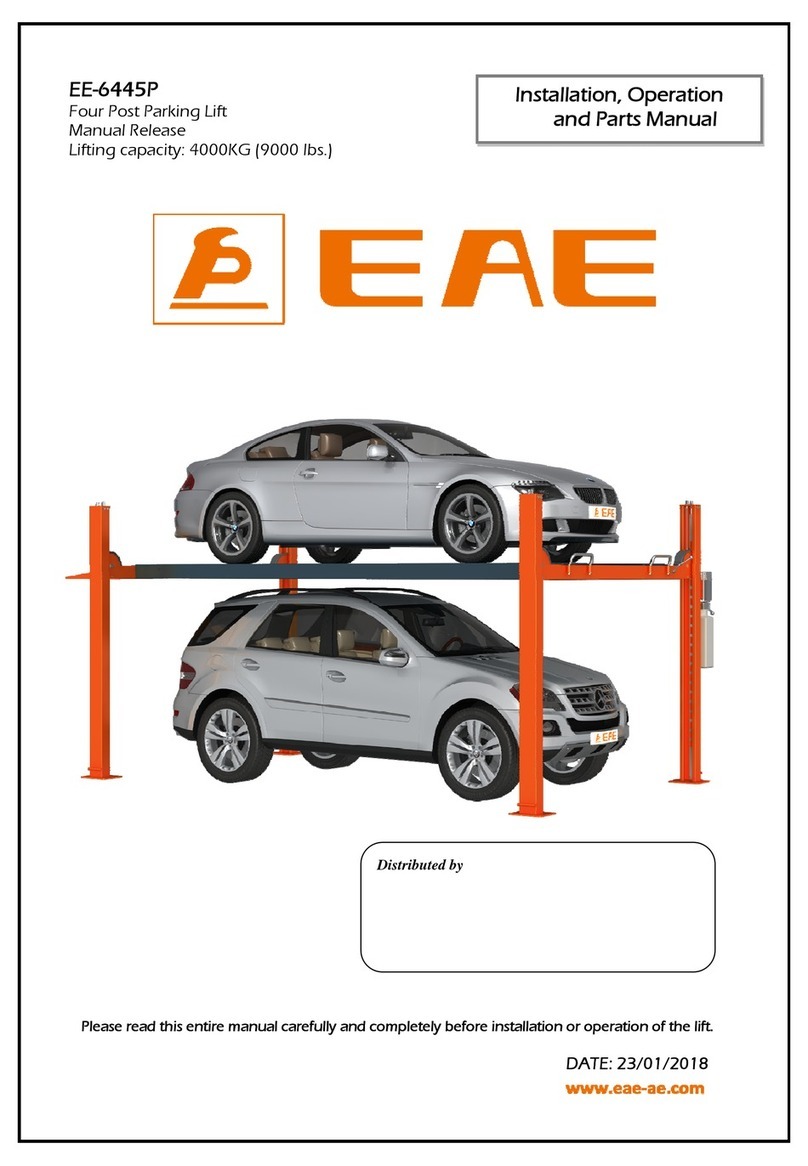
EAE
EAE EE-6445P Installation, operation, and parts manual
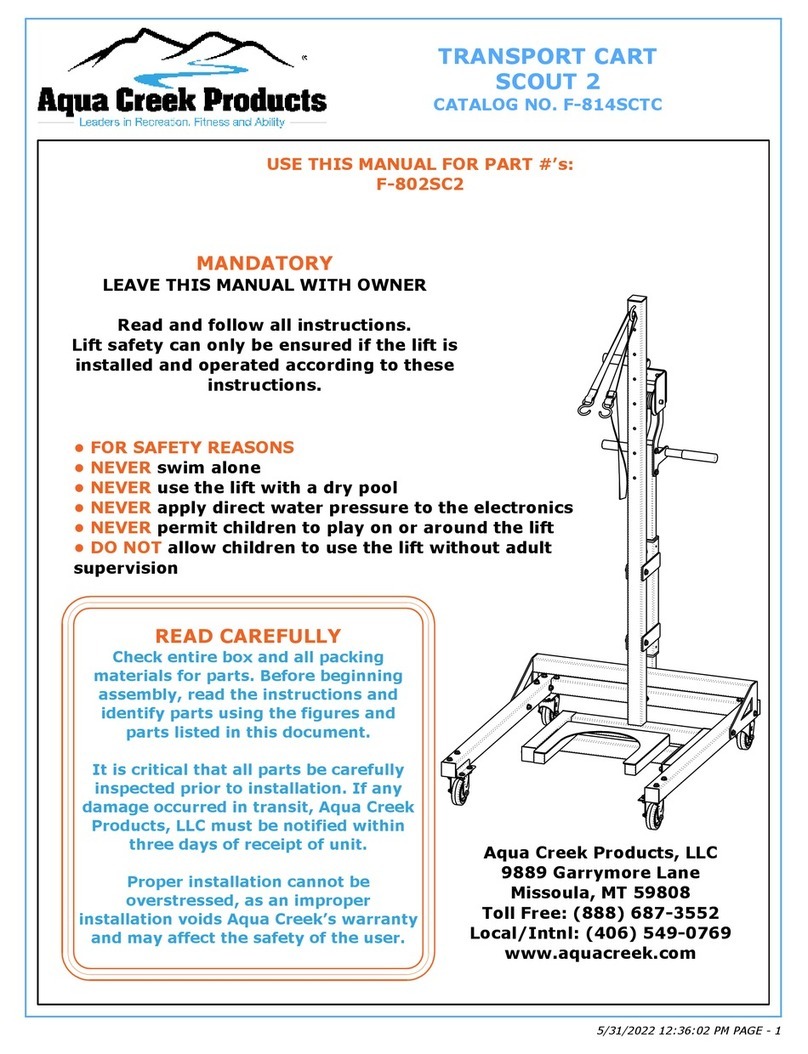
Aqua Creek Products
Aqua Creek Products F-802SC2 quick start guide
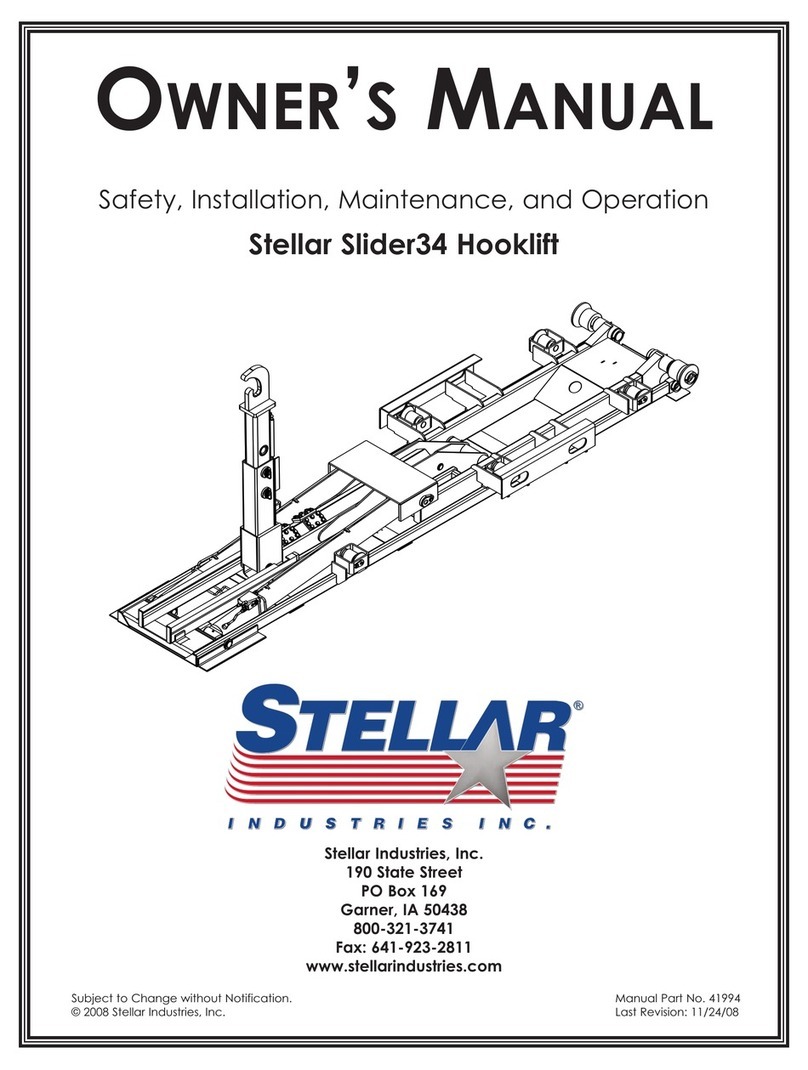
stellar labs
stellar labs Slider34 owner's manual
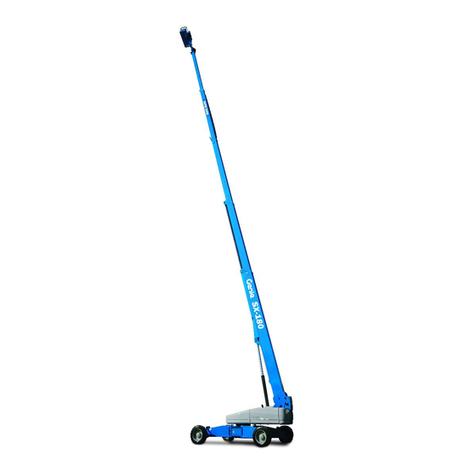
Genie
Genie SX-180 Service and repair manual

Norco
Norco 72674 Setup, operating, maintenance instructions
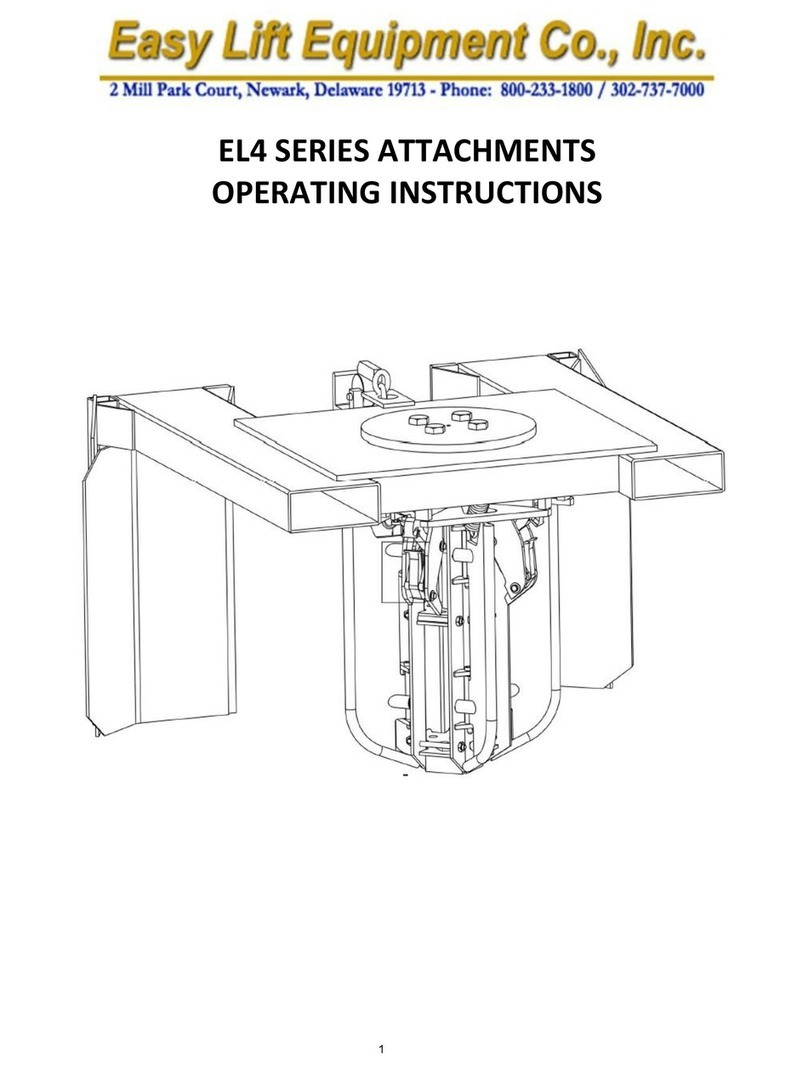
Easy Lift Equipment
Easy Lift Equipment EAGLE-GRIP EL4 Series operating instructions
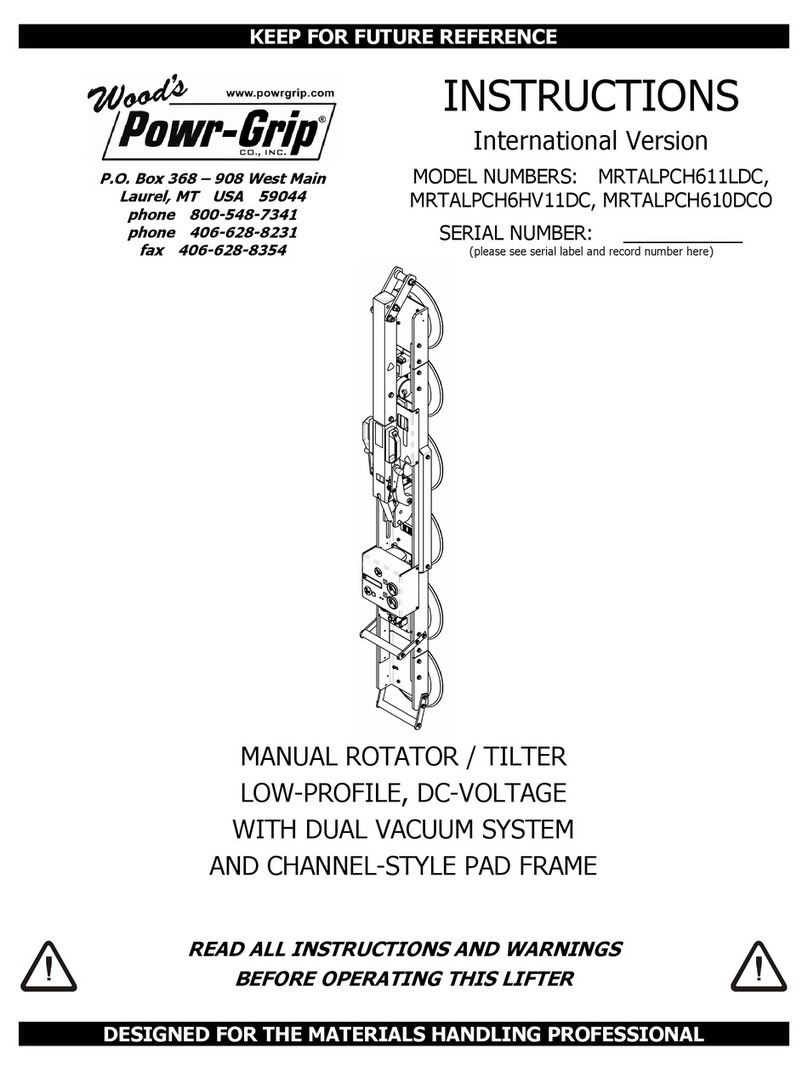
Wood’s
Wood’s Powr-Grip MRTALPCH611LDC instructions
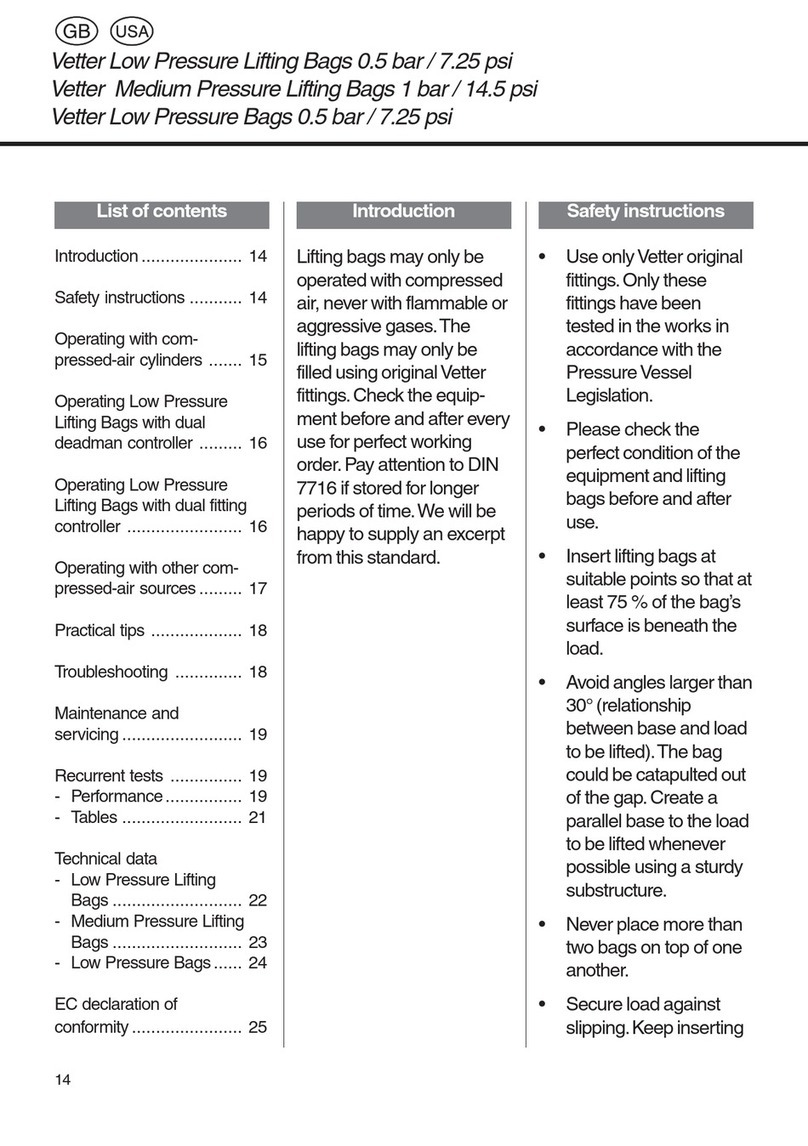
Vetter
Vetter VSL 12 manual
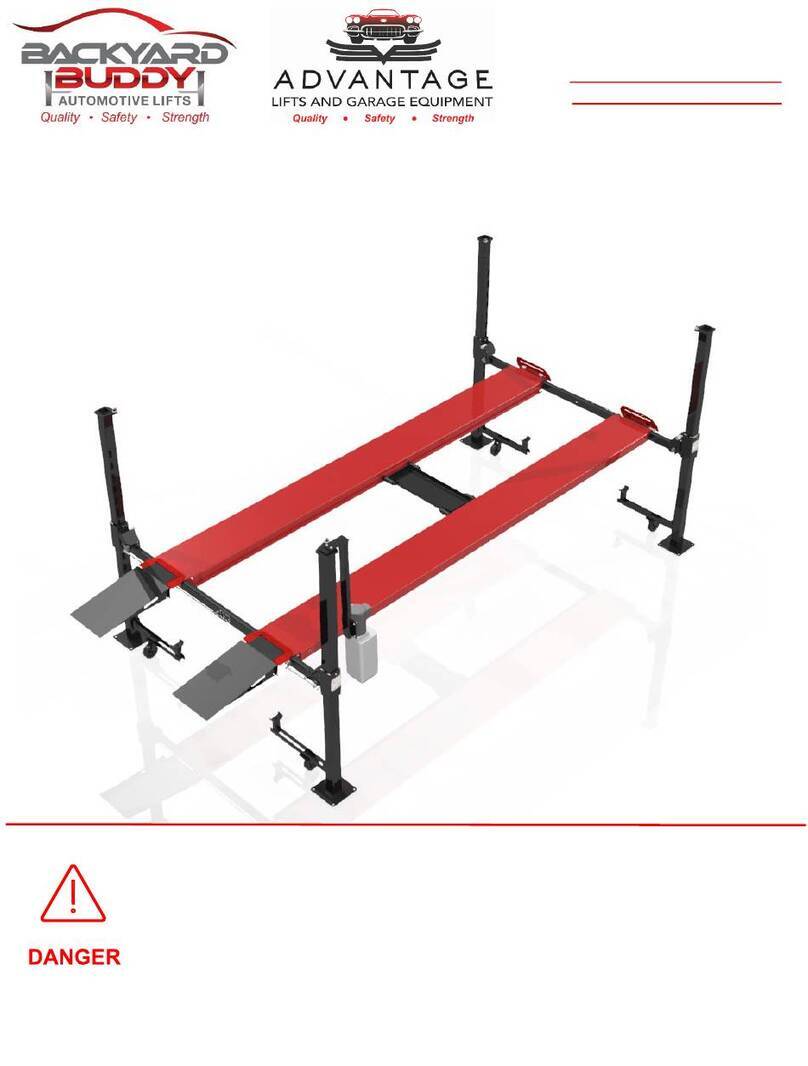
Advantage
Advantage Backyard Buddy Installation and operation manual
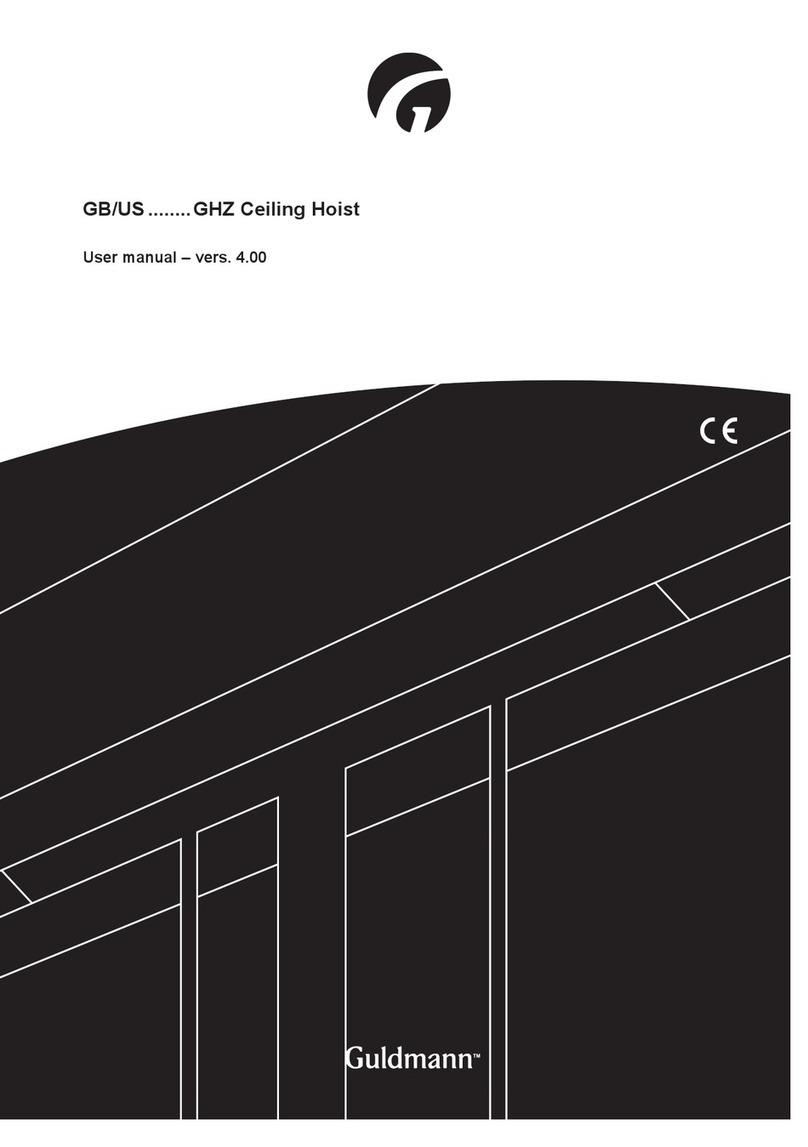
Guldmann
Guldmann GHZ Series user manual

Winncare
Winncare Luna Twin quick start guide