HAWE Hydraulik D 7969 AC Operator's manual

Product documentation
04-2014-1.1
D 7969 AC
HAWE Hydraulik SE - Streitfeldstr. 25 • 81673 München
Max. operating pressure pmax: 350 bar
Max. nom. volume VO max: 2.8 dm
Diaphragm accumulator type AC
Symbol:

2 04-2014-1.1 - D 7969 AC www.hawe.de | 2014
©by HAWE Hydraulik SE.
Forwarding and copying as well as use and communication of the contents of this document are prohibited unless explicitly permitted.
Violations oblige to compensation for damages.
All rights reserved concerning patent or utility model registrations.

www.hawe.de | 2014 04-2014-1.1 - D 7969 AC 3
Contents
1 Overview diaphragm accumulator type AC.......................................................................................................... 4
2 Versions available, main data............................................................................................................................5
2.1 Available versions.............................................................................................................................................. 5
3 Parameters....................................................................................................................................................... 7
3.1 General............................................................................................................................................................. 7
4 Dimensions...................................................................................................................................................... 8
4.1 Diaphragm accumulator.......................................................................................................................................8
5 Installation, operation and maintenance information........................................................................................15
5.1 General notes...................................................................................................................................................15
5.1.1 Safety instructions............................................................................................................................................15
5.1.2 Legal provisions............................................................................................................................................... 15
5.1.3 Transport and storage....................................................................................................................................... 15
5.1.4 Operation and maintenance............................................................................................................................... 15
5.2 Designated use................................................................................................................................................ 16
5.3 Assembly information........................................................................................................................................17
5.3.1 Installation and commissioning..........................................................................................................................17
5.4 Operating instructions.......................................................................................................................................19
5.5 Maintenance information................................................................................................................................... 20
5.5.1 Replacing USIT ring (20)...................................................................................................................................20
5.5.2 Checking gas filling pressure..............................................................................................................................20
6 Other information...........................................................................................................................................21
6.1 Notes regarding the lay-out...............................................................................................................................21
6.2 Accessories, spare parts and separate components................................................................................................ 22
6.2.1 Testing device DFM...........................................................................................................................................22
6.2.2 Mounting brackets............................................................................................................................................ 22
6.2.3 Fittings........................................................................................................................................................... 23

4 04-2014-1.1 - D 7969 AC www.hawe.de | 2014
1Overview diaphragm accumulator type AC
The diaphragm accumulators with a capacity of up to 3.5 dm3are primarily used
as a source of pressure oil for supporting/increasing the pump delivery flow and
storing pressure energy, in order toachieve an accumulator charging circuit, for
example.
Various fittings enable the integration of a hydraulic system in different installation
positions and at different installation points.
All hydraulic accumulators listed here are subject to the Pressure Equipment
Directive 97/23/EC.
Features and benefits:
■Compact design
■Option of integration into the HAWE modular system
■Operating pressures up to 350 bar
Intended applications:
■Clamping systems
■Jigs
■Accumulator charging systems
These accumulators are used to:
■store pressure energy
■support the pump delivery
■improve system efficiency
■pulsation dampening in hydraulic systems
■compensation of pressure variations due to temperature changes
■compensate internal leakage (when apparent)
Figure 1: Diaphragm accumulator type AC

www.hawe.de | 2014 04-2014-1.1 - D 7969 AC 5
2Versions available, main data
2.1 Available versions
Symbol:
Examples:
AC 2001
AC 1002 /90
/140 /3A
/22
Connection thread (hydraulic side) Table 3 Connection thread
Gas filling pressure Table 2 Gas pre-load pressure p0(bar)
Basic version Table 1 Basic version
Table 1 Basic version
Basic type Nom. volume
V0(dm3)Max. perm. operating
pressure
pmax (bar)
Max. perm. pressure
ratio
p2/p0
Max. perm. pressure
dyn. difference
p2- p1
CE - stamping plus letter
of conformity
AC 0725 0.075 250 8/1 180 --
AC 202 0.16 250 6/1 210 --
AC 322 0.32 210 8/1 210 --
AC 603 0.6 330 4/1 150 --
AC 1002 1.0 210 8/1 140 --
AC 1414 1.4 140 8/1 140 o
AC 1035 1.0 350 4/1 150 o
AC 2001 2.0 100 6/1 65 o
AC 2002 2.0 250 6/1 140 o
AC 2825 2.8 250 6/1 140 o

6 04-2014-1.1 - D 7969 AC www.hawe.de | 2014
Table 2 Gas pre-load pressure
Basic type Max. gas pre-load pressure
p0(bar)
AC 0725 130
AC 202 130
AC 322 130
AC 603 200
AC 1002 130
AC 1414 130
AC 1035 140
AC 2001 90
AC 2002 130
AC 2825 130
For information on the gas pre-load pressure p0see
also Chapter 6.1, "Notes regarding the lay-out"
For information on accessories, spare parts and
individual parts see also Chapter 6.2, "Accessories,
spare parts and separate components"
Table 3 Connection thread
Connection threadBasic type
Coding Description
AC 0725 /1A - G 1/4A (BSPP) *
AC 202 /3
/1A
/2A
/2AW
/3A
- G 1/2 (int. thread) (BSPP) *
- G 1/4A (BSPP)
- G 3/8A (BSPP)
- G 3/8A (BSPP)
- G 1/2A (BSPP)
AC 322 /3
/1A
/2A
/2AW
- G 1/2 (int. thread) (BSPP) *
- G 1/4A (BSPP)
- G 3/8A (BSPP)
- G 3/8A (BSPP)
AC 603 /3
/1A
/2A
/2AW
/3A
- G 1/2 (int. thread) (BSPP) *
- G 1/4A (BSPP)
- G 3/8A (BSPP)
- G 3/8A (BSPP)
- G 1/2A (BSPP)
AC 1002 /22
/2A
/2AW
/3A
- M22x1.5 (int. thread) *
- M33x1.5 (ext. thread) *
- G 3/8A (BSPP)
- G 3/8A (BSPP)
- G 1/2A (ext. thread) (BSPP) *
AC 1414 /22
/2A
/2AW
/3A
- M22x1.5 (int. thread) *
- M33x1.5 (ext. thread) *
- G 3/8A (BSPP)
- G 3/8A (BSPP)
- G 1/2A (BSPP)
AC 1035 /3
/1A
/2A
/2AW
/3A
- G 1/2 (int. thread) (BSPP) *
- M33x1.5 (ext. thread) *
- G 1/4A (BSPP)
- G 3/8A (BSPP)
- G 3/8A (BSPP)
- G 1/2A (BSPP)
AC 2001 /3A - G1/2A (BSPP) *
AC 2002 /4
/3A
- G 3/4 (int. thread) (BSPP) *
- G 1/2A (BSPP)
AC 2825 /3
/1A
/2A
/2AW
/3A
- G 1/2 (int. thread) (BSPP) *
- G 1/4A (BSPP)
- G 3/8A (BSPP)
- G 3/8A (BSPP)
- G 1/2A (BSPP)
* Basic version

www.hawe.de | 2014 04-2014-1.1 - D 7969 AC 7
3Parameters
3.1 General
Design Diaphragm type accumulator conforming Pressure Equipment Directive PED 97/23/EC
All types welded design
Surface protection Enameled (2k paint)
Installed position Preferable vertical position (with the fluid connection at the bottom), horizontal
Mounting Directly via pipe fittings.
Note
Ensure the pipe screw connections are correctly fitted. In the event of strong
vibrations, secure the accumulator to prevent it from coming loose.
Gas filling Only N2(nitrogen)!
Temperature }fluid: -10°C ... +80°C
}fluid: -40°C ... +80°C in type AC 322, AC 603, AC 1414, AC 2802
Hydraulic fluid Hydraulic oil: conforming to DIN 51 524 Part 1 to 3; ISO VG 10 to 68 conforming DIN 51 519
Viscosity range: min. approx. 10, max. approx. 300 mm2/s
Optimal operating range: approx. 10 to 35 mm2/s
Also suitable for biologically degradable pressure fluids type HEES (synthetic ester) at
operating temperatures up to approx. +70°C.
Diaphragm material NBR
ECO (compound) in type AC 0725, AC 202, AC 2825
Service life 1.2 x 109cycles
For all other operating conditions the service life in accordance with PD 5500 Annex C must
be observed (Pressure Equipment Directive)
Mass
Type AC 0725 = 0.75 kg
Type AC 202 = 1.0 kg
Type AC 322 = 1.3 kg
Type AC 603 = 3.0 kg
Type AC 1002 = 3.5 kg
Type AC 1414 = 6.0 kg
Type AC 1035 = 7.5 kg
Type AC 2001 = 4.0 kg
Type AC 2002 = 7.5 kg
Type AC 2825 = 8.6 kg

www.hawe.de | 2014 04-2014-1.1 - D 7969 AC 15
5Installation, operation and maintenance information
5.1 General notes
These accumulators are acc. to the Pressure Equipment Directive PED 97/23/EC.
According to section 3 of above regulation accumulators with the following specifications
■volume > 1 liter and p· V > 50 bar · liter (sect. 1.1 a, fluids of group 2)
■p · V > 10.000 bar · liter (sect. 1.1 b, fluids of group 2)
require a Declaration of Conformity as well as the CE mark.
5.1.1 Safety instructions
DIN EN ISO 4413:2010 provides further information on the technical design of accumulator systems. In a nutshell, there must be a
facility to release the accumulator pressure on the fluid side when servicing is carried out (drain valve and pressure gauge for monitor-
ing purposes). The accumulator must have its own safety valve (valve with TÜV unit approval). This must limit any momentary overpres-
sure to 10% of the highest permissible pressure. In addition, a warning stating “Caution – pressure to be released from accumulator
before removal” must be affixed.
5.1.2 Legal provisions
Hydrostatic accumulators are classified as pressure vessels under the European Pressure Equipment Directive 97/23/EC. The applicable
stipulations for commissioning and operation apply to the installation location for hydrostatic accumulators. The operator holds sole
responsibility for compliance with the existing stipulations. The supplied documents must be kept in a safe place, they will be needed
for recurring inspections.
5.1.3 Transport and storage
Caution
Danger of injury and material damage due to incorrect transportation!
■Comply with the relevant regulations on transportation and safety.
Note
Accumulators must be stored in a cool, dry place and protected from direct sunlight.
Dirt must be prevented from entering the accumulator.
If the accumulator is stored over a longer period, it is advisable to restrict the gas pre-load pressure to approx. 10 bar to
prevent deformation of the sealing element or separator.
5.1.4 Operation and maintenance
Only operate the accumulator within the permissible values. The accumulator must only be installed, maintained and repaired by
authorised and appropriately trained personnel; these tasks are governed by national regulations. In Germany, the Betriebssicher-
heitsverordnung (BetrSichV) industrial health and safety regulations apply.
The gas pre-filling must be checked regularly.

16 04-2014-1.1 - D 7969 AC www.hawe.de | 2014
Note
The complete hydraulic system has to be discharged prior to any kind of repair. A respective plate (HAWE order No. 7788 022
(4708 4258-00)) has to be applied at an easily visible spot on or near-by the accumulator.
No modification (welding, soldering, nor mechanical) must be carried out on the accumulator.
Genuine spare parts have to be used when necessary!
5.2 Designated use
This fluid-power product has been designed, manufactured and tested using standards and regulations generally applicable in the
European Union and left the plant in a safe and fault-free condition.
To maintain this condition and ensure safe operation, operators must observe the information and warnings in this documentation.
This fluid-power product must be installed and integrated in a hydraulic system by a qualified specialist who is familiar with and adheres
to general engineering principles and relevant applicable regulations and standards.
In addition, application-specific features of the system or installation location must be taken into account if relevant.
This product may only be used within oil-hydraulic systems.
The product must be operated within the specified technical parameters. This documentation contains the technical parameters for
various product versions.
Note
Non-compliance will void any warranty claims made against HAWE Hydraulik.

www.hawe.de | 2014 04-2014-1.1 - D 7969 AC 17
5.3 Assembly information
The hydraulic system must be integrated in the equipment with standard connection components that comply with market require-
ments (screw fittings, hoses, pipes, etc.). The hydraulic system must be shut down as a precautionary measure prior to dismounting; this
applies in particular to systems with hydrostatic accumulators.
5.3.1 Installation and commissioning
Installation
Warning
Risk of injury due to stored pressure escaping in an uncontrolled manner!
■Prior to all maintenance work, relieve the pressure in the hydraulic system.
1. Fit the accumulator to the bracket supplied for this purpose, if possible route the gas connection for the system upwards.
2. Fit the required shut-off, drain and safety valves between the accumulator and the hydraulic system. The easiest way to do this is
probably using a 'safety block' that contains all the above components.
Initial filling
Danger
Risk to life due to diaphragm accumulators potentially exploding if they are not filled correctly!
■Fill diaphragm accumulators exclusively with N2(nitrogen).
■Only use suitable filling and testing devices to fill.
Ensure that the accumulator is suitable for the operating conditions with regard to max. operating pressure, filling pressure and
temperature range.
Filling with gas: M16x2 mm gas valve with protective cover

18 04-2014-1.1 - D 7969 AC www.hawe.de | 2014
Filling device for diaphragm accumulators type DFM
The pressure of the gas filling of diaphragm accumulators can be checked and altered with the filling device DFM. It is suited for accumula-
tors with thread M28x1.5 and a filling socket screw M8x10. The filling device comes in a box 210x230x80 mm which also contains a pressure
gauge As diaphragm accumulators are pressure vessels where the European pressure Vessel Directive applies (for exceptions see there), it has
to be made sure that the safety especially against excessive pressure is guaranteed. Usually the accumulators are filled from nitrogen bottles
(pressure 200 or 300 bar). It is therefore mandatory to use a pressure reducing valve to make sure that the permissible
■Permissible operating gauge pressure of the diaphragm accumulator
■Permissible gas filling pressure of the diaphragm accumulator
■Permissible display range of the related pressure gauge
are not exceeded. Therefore these accumulators must not be filled via adaptors directly from the nitrogen bottle! Testing and filling have to be
performed only by trained staff utilizing a pressure reducing valve, pressure gauge and hoses with fittings G 1/4 and G 1/2 DIN 560 (BSPP).
Note
For order numbers for the filling and testing device, see Chapter 6, "Other information"

www.hawe.de | 2014 04-2014-1.1 - D 7969 AC 19
Filling instructions
Danger
Risk to life due to diaphragm accumulators potentially exploding if they are not filled correctly!
■Fill diaphragm accumulators exclusively with N2(nitrogen).
■Only use suitable filling and testing devices to fill.
Gas filling: Gas filling valve M28x1.5 mm with protective cover
1. Check that the diaphragm accumulator (1) is completely depressurized on the hydraulic side. Undo and remove the protective cap (2) from
the filling port (3) (M28x1.5). Carefully slacken the gas filling screw by a 1/4-turn via an Allan head ( (4) / 6 mm)
2. Close the drain screw (5) at the filling device 6 to its stop.
3. Mount the filling device (6) incl. hose (7) onto the gas port (3) of the diaphragm accumulator (take care that O-ring (8) is apparent and
properly positioned in the groove). Connect hose fitting (13) to the outlet port of the pressure reducing valve (15) (bottle valve (16) and
shut-off valve (17) have to be still closed)
4. Open the bottle valve (16) and slowly turn the knob (18) until the desired pressure is visible on the pressure gauge (19). Open shut-off
valve (17).
5. Twist the toggle (11) until the Allan key (10) engages in the socket head of the filling screw (4). Turn it slowly counter clockwise until
pressure balance is audible. Leave shut-off (17) open i.e. let the nitrogen flow, until pressure gauge (12) shows the desired pressure. Close
shut-off valve (17) and bottle valve (16) – wait until the diaphragm accumulator, cooled down by the filling process, has achieved ambient
temperature again. Repeat filling procedure when the gas pressure in the accumulator has dropped.
As soon as the desired gas filling pressure is achieved:
6. Make sure that the Allan key (10) is still engaged and rotate toggle (11) clockwise until the filling screw (4) is shut. Open drain screw (5)
that the trapped gas can escape from the filling device.
7. Remove filling device 6 from the diaphragm accumulator (1). Tighten the filling screw (4) with 20+5 Nm and reinstall the protective cap (2)
on gas port 3 (M28x1.5)
5.4 Operating instructions
Filtering and purity of the hydraulic fluid
Soiling in the fine range, e.g. abraded material and dust, or in the macro range, e.g. chips, rubber particles from hoses and seals, can
cause significant malfunctions in a hydraulic system. It is also to be noted that new hydraulic fluid “from the drum” does not necessari-
ly meet the highest purity requirements.
For trouble-free operation pay attention to the purity of the hydraulic fluid (see also purity class in Chapter 3, "Parameters").

20 04-2014-1.1 - D 7969 AC www.hawe.de | 2014
5.5 Maintenance information
This product is largely maintenance-free.
Conduct a visual inspection to check the hydraulic connections for damage at regular intervals, but at least once per year. If external
leaks are found, shut down and repair the system.
Check the device surfaces for dust deposits at regular intervals (but at least once per year) and clean the device if required.
5.5.1 Replacing USIT ring (20)
If there is a suspicion of damage or a leak is found, the USIT ring (20) must be replaced; for this purpose the gas filling pressure must
be fully relieved (mostly after a very long period of use and/or if there are large pressure differences in flow of filling gas). To relieve
the pressure undertake the first (3) steps for the gas pressure filling check and then open the drain screw (5) until the pressure gauge
(12) indicates the value zero. After unscrewing the filling device (6) the gas filling screw (4) can be fully unscrewed and the USIT ring
(20) replaced with a new ring. During this process attention is to be paid to a clean and undamaged sealing surface. After screwing
back in the gas filling screw (4) the filling process as per Chapter 5.3, "Assembly information" for a gas filling pressure change from
zero to the required value can be started.
5.5.2 Checking gas filling pressure
1. Check that the diaphragm accumulator (1) is completely depressurized on the hydraulic side. Undo and remove the protective cap (2)
from the filling port (3) (M28x1.5). Carefully slacken the gas filling screw by a 1/4-turn via an Allan head ((4) / 6 mm)
2. Close the drain screw (5) at the filling device (6) to its stop.
3. Mount the filling device (6) without hose (7) onto the gas port (3) of the diaphragm accumulator (take care that O-ring (8) is
apparent and properly positioned in the groove).
Note
The check valve (9) installed at the hose side will only work when no hose is connected.
4. Twist the toggle (11) until the Allan key (10) engages in the socket head of the filling screw (4). Turn it slowly counter clockwise
until pressure audible enters the filling device. (Note: The gas filling screw (4) can‘t be completely screwed out while the filling
device (6) is mounted. It can be screwed out only as far until a slot apparent on the side can act as passage. The passing gas
generates a hissing noise also acting as a warning when the gas filling screw gets opened unintended) The gas filling pressure
apparent (conditions: ambient temperature) will be shown at the pressure gauge (12). Close shut-off valve (17) and bottle valve (16)
– wait until the diaphragm accumulator, cooled down by the filling process, has achieved ambient temperature again. Repeat filling
procedure in case the gas pressure in the accumulator has dropped.
As soon as the desired gas filling pressure is achieved:
5. Make sure that the Allan key (10) is still engaged and rotate toggle (11) clockwise until the filling screw (4) is shut. Open drain
screw (5) that the trapped gas can escape from the filling device.
6. Remove filling device (6) from the diaphragm accumulator (1). Tighten the filling screw (4) with 20+5 Nm and reinstall the
protective cap (2) on gas port 3 (M28x1.5)
Note
Whenever the gas filling pressure is checked a slight amount will escape via the filling device. This can be prevented if the
gas filling pressure is checked via the hydraulic side.
Table of contents
Other HAWE Hydraulik Power Pack manuals
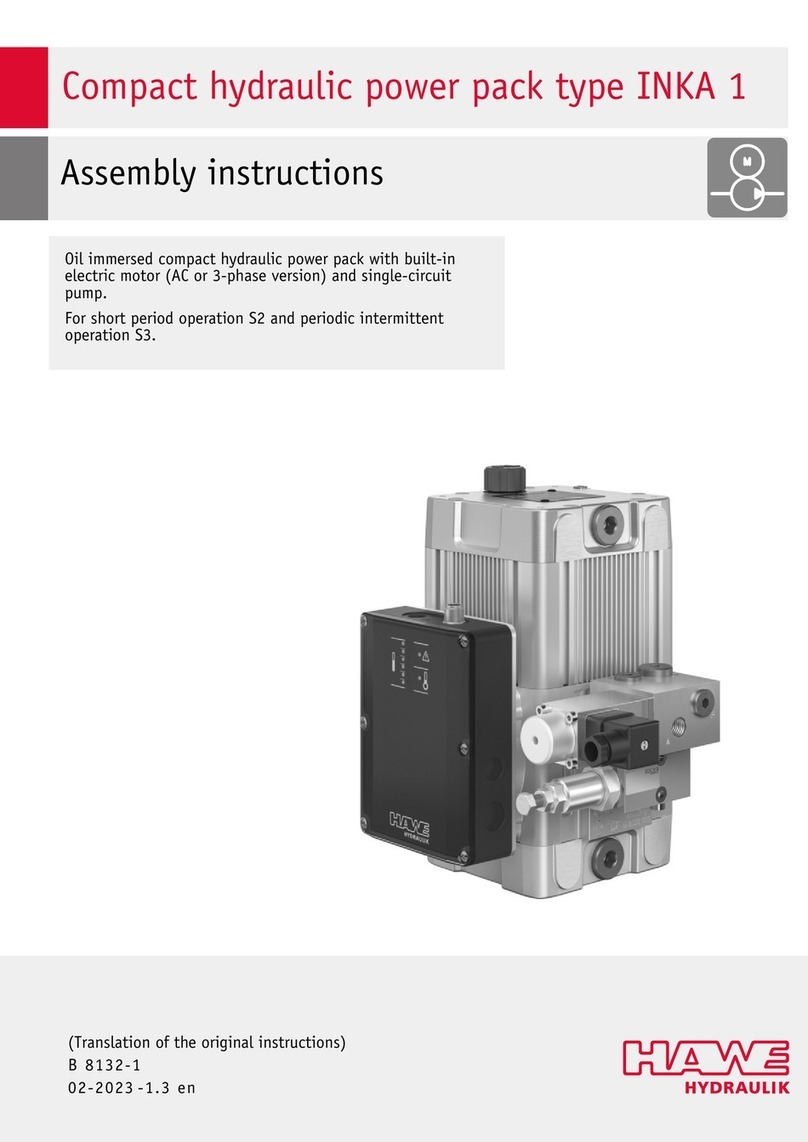
HAWE Hydraulik
HAWE Hydraulik INKA 1 User manual
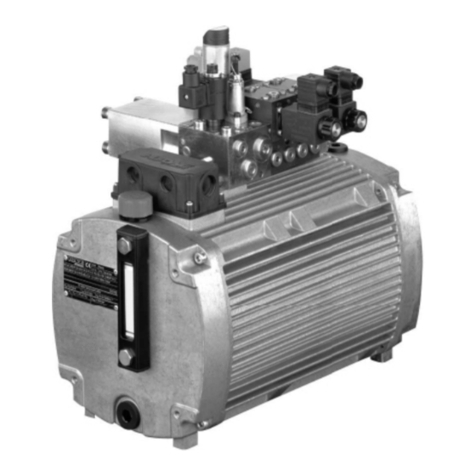
HAWE Hydraulik
HAWE Hydraulik KA2 User manual

HAWE Hydraulik
HAWE Hydraulik HR 050 User manual
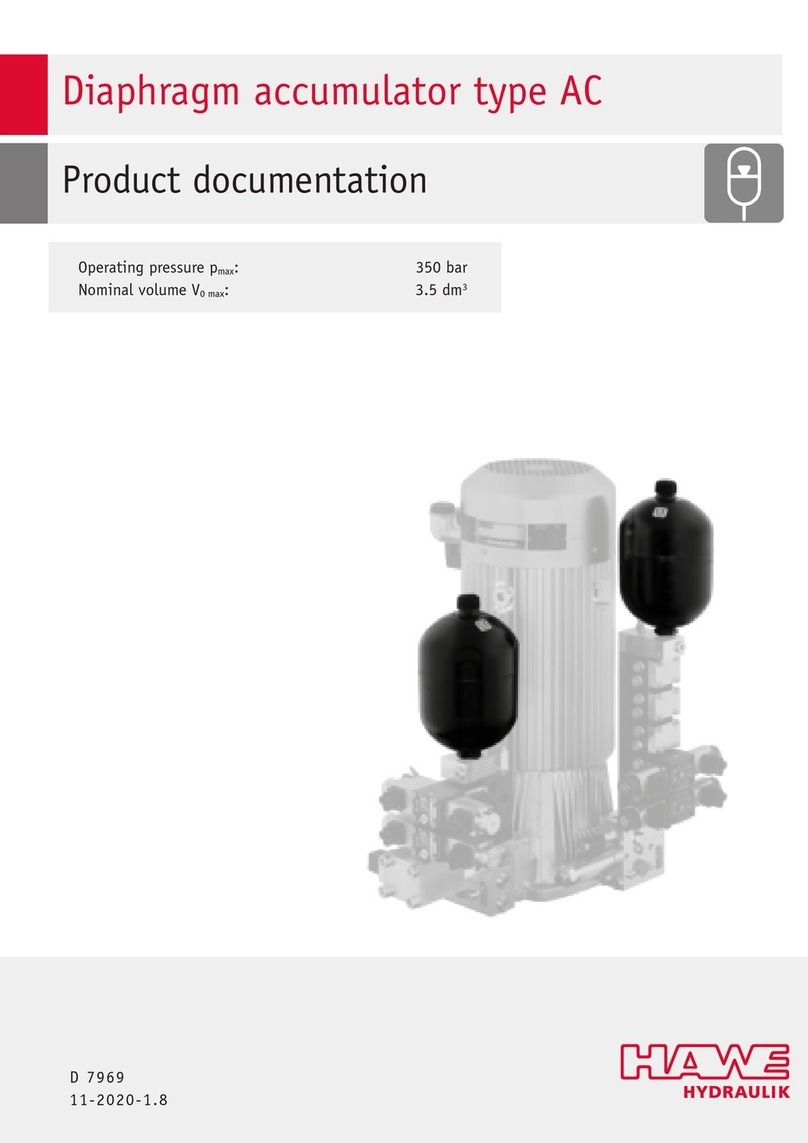
HAWE Hydraulik
HAWE Hydraulik AC Series Operator's manual

HAWE Hydraulik
HAWE Hydraulik A 100 User manual
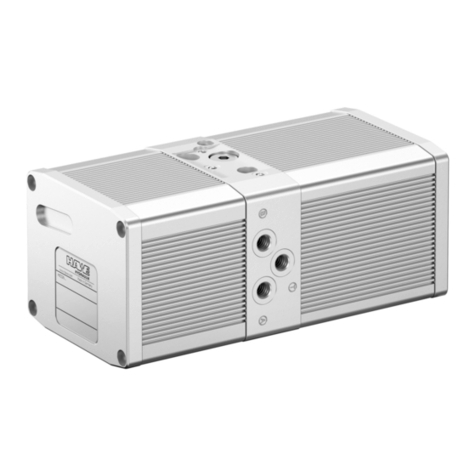
HAWE Hydraulik
HAWE Hydraulik HICON User manual
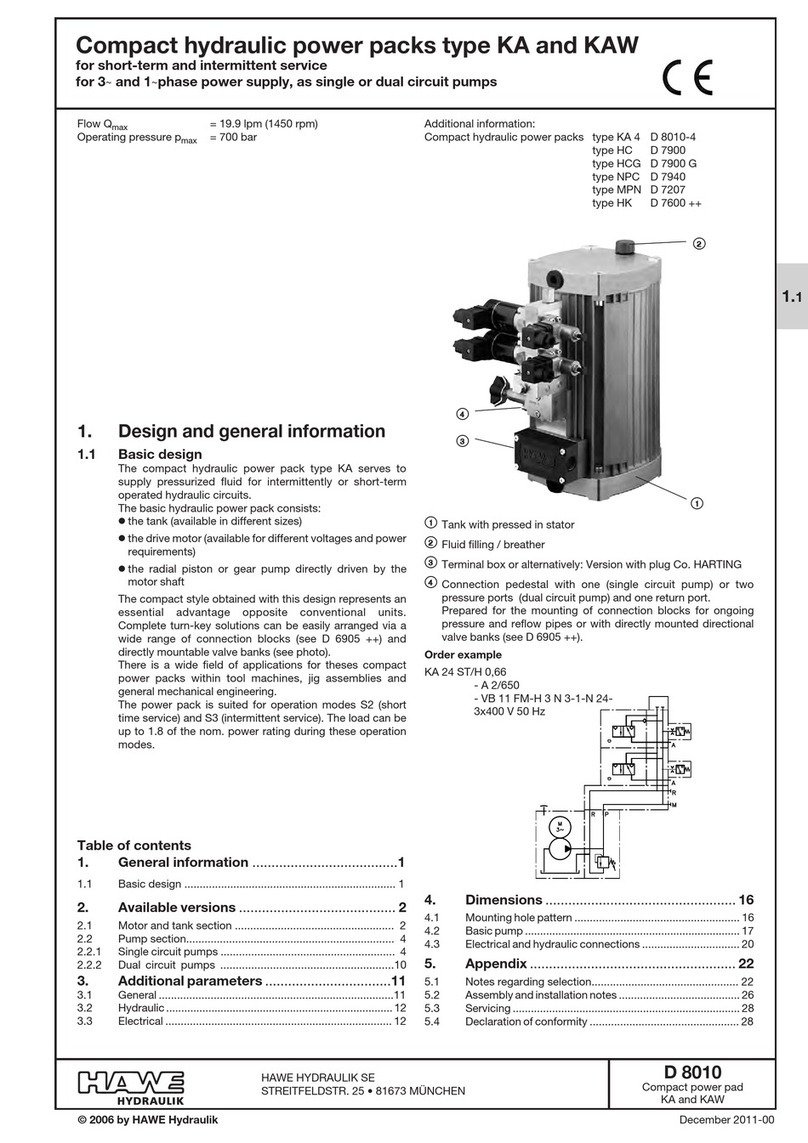
HAWE Hydraulik
HAWE Hydraulik KA User manual
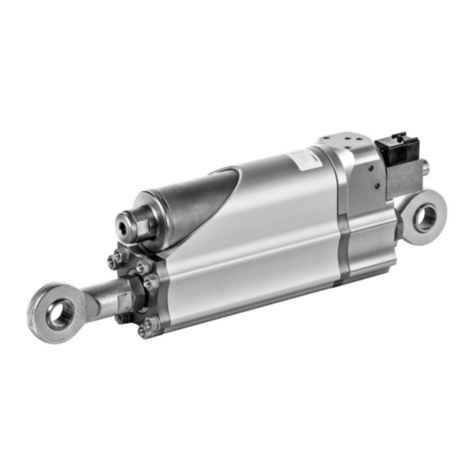
HAWE Hydraulik
HAWE Hydraulik HLU LE-X User manual