HBM T10FH User manual

Mounting Instructions
English
T10FH

Hottinger Baldwin Messtechnik GmbH
Im Tiefen See 45
D-64239 Darmstadt
Tel. +49 6151 803-0
Fax +49 6151 803-9100
www.hbm.com
Mat.: 7-2002.2037
DVS: A2037-5.0 HBM: public
02.2016
EHottinger Baldwin Messtechnik GmbH.
Subject to modifications.
All product descriptions are for general information only.
They are not to be understood as a guarantee of quality or
durability.

T10FH A2037-5.0 HBM: public 3
English
1 Safety instructions 5........................................
2 Scope of supply 9..........................................
3 Application 10...............................................
4 Structure and mode of operation 11...........................
5 Mechanical installation 13....................................
5.1 Conditions on site 14..........................................
5.2 Mounting position 15..........................................
5.3 Mounting sequence 15........................................
5.4 Preparing for the rotor mounting 18.............................
5.5 Mounting the rotor 22..........................................
5.6 Installing the stator 25.........................................
5.7 Installing the clamp fixture 27...................................
5.8 Aligning the stator (speed measuring system) 29..................
6 Electrical connection 32......................................
6.1 General hints 32..............................................
6.2 Shielding design 33...........................................
6.3 Connector pin assignment Option 3, Code SU2 34................
6.4 Connector pin assignment Option 3, Code PNJ 37................
6.5 Supply voltage pin assignment (Option 3, Code SU2) 38...........
6.5.1 Supply voltage for self-contained operation 38....................
6.6 Supply voltage (Option 3, Code PNJ) 39.........................
7 TEDS transducer identification (Option 3, Code PNJ) 40........
7.1 Hierarchy of user rights 40.....................................
7.1.1 Standard rights (USR level) 40.................................
7.1.2 Calibration rights (CAL level) 40................................
7.1.3 Administrator rights (ID level) 41................................
7.2 Content of the TEDS memory as defined in IEEE 1451.4 41........

4A2037-5.0 HBM: public T10FH
8 Shunt signal (Option 3, Code SU2) 46.........................
8.1 Shunt signal 46...............................................
9 Settings (Option 3, Code SU2) 48.............................
9.1 Torque output signal 48........................................
9.2 Setting up the zero point 48....................................
9.3 Function testing 49............................................
9.3.1 Power transmission 49........................................
9.3.2 Checking the speed measuring system 50.......................
9.4 Speed measuring system 51...................................
9.5 Form of speed output signal 51.................................
9.6 Type of speed output signal 52.................................
10 Loading capacity 53.........................................
10.1 Measuring dynamic torque 53..................................
11 Maintenance 55..............................................
12 Specifications 56............................................
13 Dimensions Rotor T10FH rotating; option 2, code L 66.........
14 Dimensions Rotor T10FH non‐rotating; option 2, code N 68....
15 Mounting Dimensions 70.....................................
16 Supplementary technical information; option 2, code L 71......
16.1 Output signals 71.............................................
16.1.1 Output MD for torque (connector 1) 71...........................
16.1.2 Output N for rotation speed (connector 2) 72.....................
16.2 Circular run-out values 73......................................
17 Order number 74............................................
18 Accessories 75..............................................

Safety instructions
T10FH A2037-5.0 HBM: public 5
1 Safety instructions
Appropriate use
The T10FH Torque Flange may be used for
torque‐measurement and directly related control and
regulation tasks only. Any other use is not appropriate.
To ensure safe operation, the transducer may only be
used according to the specifications given in this manual.
When using the transducer, the legal and safety
regulations for the respective application must also be
observed. The same applies if accessories are used.
The transducer is not a safety device in accordance with
the regulations for appropriate use. For correct and safe
operation of these transducers it is essential to ensure
technically correct transportation, storage, installation
and fitting, and to operate all equipment with care.
This is a Class B EMC product. In a domestic
environment this product may cause radio interference in
which case the user may be required to take adequate
measures.
General dangers in the case of non-observance of
the safety instructions
The transducer comply with the state of the art and is
operationally reliable. If the transducer is used and
operated inappropriately by untrained personnel, residual
dangers may arise.
Anyone responsible for installing, operating, maintaining
or repairing these transducers must be sure to have read
and understood the operating manual and in particular
the notes on safety.

Safety instructions
6A2037-5.0 HBM: public T10FH
Residual dangers
The scope of performance and supply of these
transducers covers only part of the torque measurement
technology. In addition, those involved in planning,
constructing and operating the safety engineering
aspects of torque measurement technology must design,
produce and take responsibility for such measures in
order to minimize potential residual dangers. Prevailing
regulations must be complied with at all times. There
must be a clear reference to the residual dangers
connected with measurement technology.
In this manual, the following symbols are used to refer to
residual dangers:
Symbol Significance
WARNING This marking warns of a potentially dangerous
situation in which failure to comply with safety
requirements can result in death or serious physical
injury.
CAUTION This marking warns of a potentially dangerous
situation in which failure to comply with safety
requirements can result in slight or moderate physical
injury.
Notice This marking draws your attention to a situation in
which failure to comply with safety requirements can
lead to damage to property.
Emphasis
See….
Italics are used to emphasize and highlight text and
references to other chapters and external documents.
Symbols pointing out notes on use and waste
disposal as well as useful information:
CE mark
The CE mark enables the manufacturer to guarantee that
the product complies with the requirements of the rele

Safety instructions
T10FH A2037-5.0 HBM: public 7
vant EC directives (the declaration of conformity is avail
able at http://www.hbm.com/HBMdoc).
Statutory marking requirements for waste disposal
National and local regulations regarding the protection of
the environment and recycling of raw materials require
old equipment to be separated from regular domestic
waste for disposal.
For more detailed information on disposal, please contact
the local authorities or the dealer from whom you pur
chased the product.
Reconstruction and modifications
HBM's express consent is required for modifications
affecting the transducers' construction and safety. HBM
does not take responsibility for damage resulting from
unauthorized modifications.
Qualified personnel
The transducers may be used by qualified personnel
only; the technical data and the special safety regulations
must be observed in all cases. When using the transduc
ers, the legal and safety regulations for the respective
application must also be observed. The same applies if
accessories are used.
Qualified personnel means: personnel familiar with the
installation, fitting, start-up and operation of the product,
and trained according to their job.
Prevention of accidents
According to prevailing accident prevention regulations,
after fitting the T10FH torque flange a cover must be
fitted as follows:

Safety instructions
8A2037-5.0 HBM: public T10FH
SThe cover must not be able rotate.
SThe cover shall protect against crushing or cutting and
provide protection against parts that might come
loose.
SThe cover shall be installed at a safe distance from
moving parts or shall prevent anyone putting their
hand inside.
SThe cover shall even be fitted if the moving parts are
installed in areas to which persons do not usually
have access.
The above regulations may only be disregarded if
machine parts are already sufficiently protected owing to
the design of the machine or because other precautions
have been taken.
Guarantee
In the event of a claim, the guarantee can only be
considered if the torque flanges are returned in its
original packing.

Scope of supply
T10FH A2037-5.0 HBM: public 9
2 Scope of supply
STorque flange
SMounting Instructions
STest record
SOptional:
- Magnetic speed measuring system
- PTB calibration certificate in accordance with
DIN 51 309 or EA‐10/14: Class 0.5

Application
10 A2037-5.0 HBM: public T10FH
3 Application
The T10FH torque flange records static and dynamic
torque on fixed or rotating shafts and also return RS422
signals with direction of rotation information to determine
the speed.
The rotating version (frequency and voltage output) is
designed for:
Smarine engine test benches
Stransmissions
Spump test benches
The non-rotating version (mV/V output signal) is
designed for:
Scalibration tasks
Storque reference transducers
Storque transfer transducers
Designed to work without bearings and with contactless
digital signal transmission, the torque measuring system
is maintenance-free.
The torque flange is supplied for nominal (rated) torques
of 100 kN⋅m to 300 kN⋅m. Depending on the nominal
torque, maximum speeds of up to
3 000 min-1 are permissible.
The T10FH torque flange is reliably protected against
electromagnetic interference. It has been tested with
regard to EMC according to the relevant European stan
dards, and carries the CE mark.

Structure and mode of operation
T10FH A2037-5.0 HBM: public 11
4 Structure and mode of operation
The torque flange (Option 2, code N) consists of two sep
arate parts: the rotor and the stator.
The rotor comprises the measuring body and the signal
transmission elements.
Strain gages (SGs) are mounted on the measuring body.
The rotor electronics for transmitting the excitation volt
age and the measurement signal are located centrally in
the flange. The transmitter coils for the noncontact trans
mission of excitation voltage and measurement signal are
located on the measuring body. The signals are sent and
received by a separable antenna ring. The antenna ring
is mounted on a housing that includes the electronic sys
tem for voltage adaptation and signal conditioning.
Connectors for the torque signal, the voltage supply and
the speed signal (option) are located on the stator. The
antenna ring should be mounted more or less concentri
cally around the rotor (see chapter 5, page 13).
Speed measurement is effected by a magnetic field
dependent resistor and a ring gear attached to the rotor.

Structure and mode of operation
12 A2037-5.0 HBM: public T10FH
Housing
Speed sensor
(option)
Side A Side B
Stator
Antenna
segments
Transmitter coils
Rotor
Fig. 4.1 Mechanical construction, exploded view (rotating
version)

Mechanical installation
T10FH A2037-5.0 HBM: public 13
5 Mechanical installation
WARNING
Handle the torque flange carefully. The transducer might
suffer permanent damage from mechanical impact (e.g.
dropping), chemical effects (e.g. acids, solvents) or ther
mal effects (e.g. hot air, steam).
With alternating loads, you should cement the rotor con
nectionscrews into the mating thread with a screw lock
ing device (medium strength) to exclude prestressing
loss due to screw slackening.
An appropriate shaft flange enables the T10FH torque
flange to be mounted directly. It is also possible to
directly mount a joint shaft or relevant compensating ele
ments on the opposite flange (using an intermediate
flange when required). Under no circumstances must the
permissible limits specified for bending moments, lateral
and longitudinal forces be exceeded. Due to the torque
flange's high torsional stiffness, dynamic shaft train
changes are kept to a minimum.
CAUTION
Check the effect on speeds and natural torsional oscilla
tions critical to bending, to prevent the transducer being
overloaded by increases in resonance.

Mechanical installation
14 A2037-5.0 HBM: public T10FH
Notice
Even if the unit is installed correctly, the zero point
adjustment made at the factory can shift by
approx. ±150 Hz. If this value is exceeded, we advise
you to check the mounting conditions. If the residual zero
offset when the unit is removed is greater than ±50 Hz,
please send the transducer back to the Darmstadt fac
tory for testing.
For correct operation, do in any case observe the mount
ing dimensions (see chapter 15, page 70).
5.1 Conditions on site
The T10FH torque flange is protected to IP54 according
to EN 60529. Protect the transducer from coarse dirt,
dust, oil, solvents and moisture. During operation, the
prevailing safety regulations for the security of personnel
must be observed (see ”Safety instructions”, page 5).
There is wide ranging compensation for the effects of
temperature on the output and zero signals of the T10FH
torque flange (see “Specifications” on page 56). This
compensation is carried out at static temperatures. This
guarantees that the circumstances can be reproduced
and the properties of the transducer can be recon
structed at any time.
If there are no static temperature ratios, for example,
because of the temperature differences between flange A
and flange B, the values given in the specifications can
be exceeded. Then for accurate measurements, you
must ensure static temperature ratios by cooling or heat
ing, depending on the application. As an alternative,

Mechanical installation
T10FH A2037-5.0 HBM: public 15
check thermal decoupling, by means of heat radiating
elements such as multiple disc couplings.
5.2 Mounting position
The transducer can be mounted in any position. With
clockwise torque, the output frequency is 10...15 kHz
(Option 3, Code SU2). In conjunction with HBM ampli
fiers or when using the voltage output, a positive output
signal (0 V to +10 V) is present.
With counterclockwise torque, the output frequency is
5 kHz to 10 kHz.
In the case of the speed measuring system, an arrow is
attached to the head of the sensor to clearly define the
direction of rotation. When the transducer rotates in the
direction of the arrow, a positive speed signal is output.
With the non-rotating version, there is a positive output
signal in mV/V for clockwise torque.
5.3 Mounting sequence
As the diameter of the antenna ring is less than the
flange diameter of the rotor, the antenna ring must be
dismantled for mounting. If access to the rotor in its
installed state is difficult, we recommend mounting the
antenna ring beforehand.

Mechanical installation
16 A2037-5.0 HBM: public T10FH
CAUTION
When installing the rotor, make sure that you do not
damage the stator. It is essential in this case to comply
with the notes on assembling the antenna segments (see
chapter 5.5 “Mounting the rotor”, page 22).
2. Install stator mounting
3. Remove one antenna segment 4. Install antenna segment around shaft
train
Customer mounting
1. Install rotor

Mechanical installation
T10FH A2037-5.0 HBM: public 17
5. Align stator and finish installation
Support supplied by
customer
Clamp fixture
6. Install clamp fixture

Mechanical installation
18 A2037-5.0 HBM: public T10FH
5.4 Preparing for the rotor mounting
CAUTION
The rotor is heavy (as much as 148 kg, depending on the
measuring range)! Use a crane or other suitable lifting
equipment to lift it out of its packaging and install it.
When working with the crane, be sure to meet relevant
safety requirements and wear safety boots.
1. Remove the top layer of foam packaging.
Fig. 5.1 T10FH packaging
2. Fasten two equal-length ropes of sufficient bearing
strength to the eyebolts (each of the two ropes must
be able to bear the full weight of the rotor) and hoist
the rotor out of its packaging with the crane
(see Fig. 5.2).

Mechanical installation
T10FH A2037-5.0 HBM: public 19
Fig. 5.2 Hoist the rotor out of its packaging
3. Place the rotor onto a clean and stable base.
4. Remove one of the eyebolts.
5. Carefully lift the rotor until it hangs freely.
6. Carefully tilt the rotor by lowering it over the flange
edge until it rests horizontally on both outer flange
surfaces (see Fig. 5.3).

Mechanical installation
20 A2037-5.0 HBM: public T10FH
CAUTION
Crush hazard. Keep your hands and feet a safe distance
away from the rotor.
Fig. 5.3 Tilt rotor
7. Secure the rotor with wedges to stop it rolling away.
8. Screw the second eyebolt back into the tapped holes
in the outer flange surface.
9. Fasten the rotor to the hook of the crane with two
equal-length ropes. The rotor is now prepared for hori
zontal installation (see Fig. 5.4).
Other manuals for T10FH
1
Table of contents
Other HBM Measuring Instrument manuals
Popular Measuring Instrument manuals by other brands
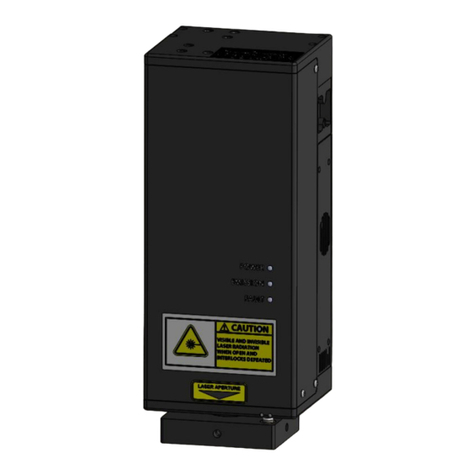
Quantum Composers
Quantum Composers miniSystem Series operating manual
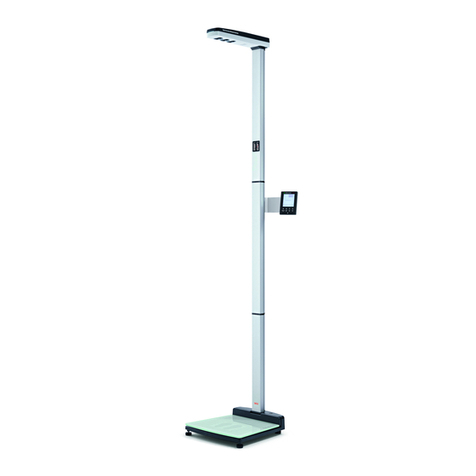
Seca
Seca 287 Instruction manual and guarantee
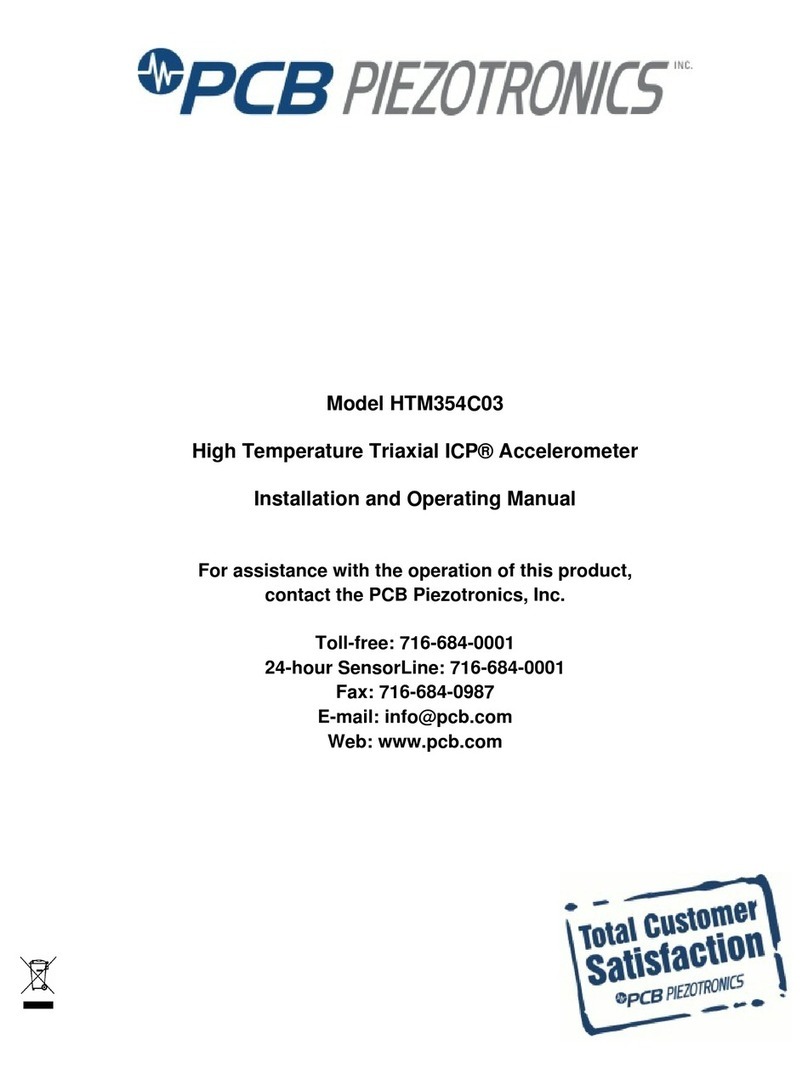
PCB Piezotronics
PCB Piezotronics ICP HTM354C03 Installation and operating manual
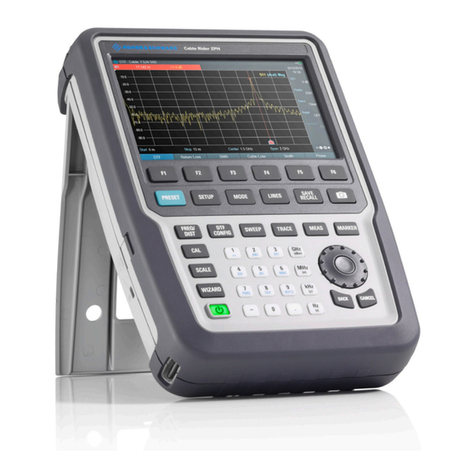
ROHDE & GRAHL
ROHDE & GRAHL R&S ZPH Series manual
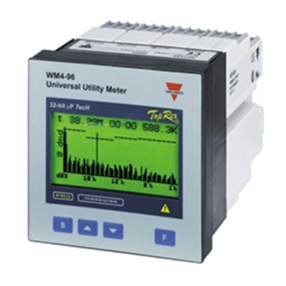
CARLO GAVAZZI
CARLO GAVAZZI WM4-96 - PROGRAMMING manual
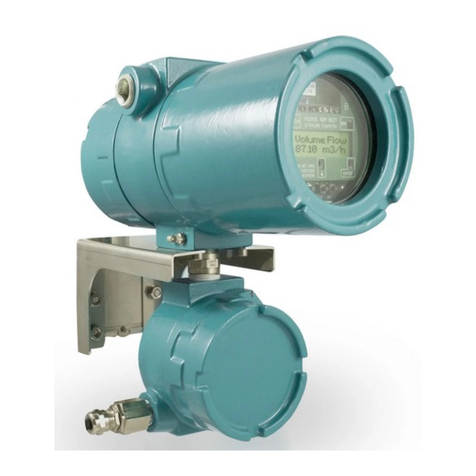
Flexim
Flexim FLUXUS G800 user manual