HPC CodeMax User manual

The CodeMax®
Computerized Code Key Machine
This manual and the internal software and data of the CodeMax®described in this manual
are copyrighted by:
HPC, Inc., Schiller Park, Illinois, U. S. A.
The internal software and data is a work fully protected by the United States
Copyright Laws.
Federal Law: This manual or the internal software of the CodeMax®may not be copied,
translated, photocopied, microfilmed, or reproduced in any manner to be machine readable
in any form (in whole or in part), without the express written consent of the
copyright holder.
HPC, Inc.
Schiller Park, Illinois
Copyright 2008
1
CodeMax®

2CodeMax®
X
Visit the CodeMax®web page at
www.hpcworld.com/km/codemax
to learn about your machine.
To watch the videos showing the
important features of the CodeMax®.
Watch Our
Other Videos
Look For...
Exploded
Views
To access the Exploded View and Parts
List to identify a spare part needed.
Look For...
1 2 3 4 5
Depth & Space
Data
To view or download the current list
of DSD numbers and the key cutting
details for each one.
Look For...
Manuals
and
Exploded Views
To view or download a PDF of the
CodeMax® Operation Manual.
Look For...
Features of the
CodeMax®
To learn the features of CodeMax®
Version 10 (Upgrades are available).
Look For...
Key Machine
Accessories
To see the accessories that are
available for your CodeMax®.
Look For...

3
Index
1. Introduction ..............................................................4
1.1 Product Packaging Checklist ..................................................5
1.2 Parts Designation...........................................................7
1.3 Preparation of the CodeMax®.................................................8
1.4 Basic Codemax Setup........................................................9
1.5 Emergency Button .........................................................10
2. Cutter Wheels ............................................................11
2.1 Cutter Wheel Descriptions ...................................................11
2.2 Changing Cutters ..........................................................12
2.3 Resharpening Cutters .......................................................14
3. Holding And Gauging Keys.................................................15
3.1 ViseJaws ................................................................15
3.2 Key Gauges ..............................................................19
3.3 Gauging Methods ..........................................................19
3.3.1 Standard Cylinder Key With Shoulder Gauge Using Jaw A ..................19
3.3.2 Standard Cylinder Key With Shoulder Gauge Using Jaw B . . . . . . . . . . . . . . . . . . 21
3.3.3 Red Full Short Tip Stop Gauging Using Jaw A ............................23
3.3.4 Red Middle Short Tip Stop Gauging Using Jaw A .........................24
3.3.5 Black Horseshoe Tip Stop Gauging Using Jaw B ..........................25
3.3.6 Medeco®–StandardCommercialJaw ..................................26
Using Jaw C (optional equipment)......................................26
3.3.7 Black Horseshoe Full End Tip Stop Gauging Using Jaw A or B ..............27
4. Key Cutting Methods......................................................29
4.1. Stand Alone Key Cutting....................................................30
4.1.1 ......................................................30
4.1.2 Medeco® Keys ......................................................32
4.1.3 After The Key Has Been Cut ..........................................35
4.1.4 Additional Notes
....................................................36
4.2 Computer Assisted Key Cutting ..............................................37
4.3 Micrometer Key Cutting . . . . . . . . . . . . . . . . . . . . . . . . . . . . . . . . . . . . . . . . . . . . . . . . . . . . 39
5. Recalibration Of The CodeMax®...........................................43
5.1 Electronic Calibration ......................................................43
5.1.1 Depth Instructions ...................................................44
5.1.2 Space Instructions ...................................................46
5.1.3 DSD Specific Instructions.............................................48
5.2 Manual Calibration ........................................................50
Space Calibration..........................................................50
5.2.1 Cutting Too Close To The Tip On Keys Gauged From The Tip ...............51
5.2.2 Cutting Too Far From The Tip On Keys Gauged From The Tip ...............53
5.2.3 Cutting Too Far From The Shoulder.....................................55
5.2.4 Cutting Too Close To The Shoulder .....................................57
5.3 Depth Adjustment .........................................................59
6. Updates .................................................................60
7. Troubleshooting ..........................................................61
8. Glossary ................................................................62
9. Exploded Views ..........................................................64
10. Preventive Maintenance, Lubrication, Repairs, and Guarantee ..................68
CodeMax®
Standard Keys

1. Introduction
Thank you for purchasing this CodeMax®Machine; we appreciate your business.
The CodeMax® represents the latest development in the industry’s first computerized code
machine. Utilizing cutting edge technology, this version allows for electronic calibration,
DSD modification, and updates installed by your computer.
Please read this manual to become familiar with the features and operation of your
CodeMax®. This machine is updated every year with new information and features. Please
complete and return the enclosed warranty registration card to ensure you receive notice of
future updates.
We are confident your CodeMax®will provide years of service for you. If you have any
questions or comments about this machine (or any HPC products), please contact us.
Thank you,
HPC, Inc.
3999 N. 25th Avenue
Schiller Park, Illinois 60176
U.S.A.
Tel: 847.671.6280
Toll-free in U.S.A. and Canada: 800.323.3295
Fax: 847.671.6343
Email: [email protected]
www.hpcworld.com
4CodeMax®
CodeMax®

5
1.1 Product Packaging Checklist
HPC Cutter Wheel (installed) HPC Cutter Wheel HPC Cutter Wheel
(CW-14MC) (CW-1011) (CW-20FM)
HPC Cutter Wheel HPC Cutter Wheel
(CW-47MC) (CW-90MC)
Cutter Wrench Allen Wrench, 5/64" Cutter/Adjustment Wrench Red Tip Gauge
(WRENCH-3) (WRENCH-2) (WRENCH-1) (CM-1054MA)
Horseshoe Tip Gauge DSD List
(CM-1054R) CodeMax®Update &
Restore CD
(MAX-CD)
CodeMax®
CodeMax® Manual
(1200MAX-MAN)
Serial Cable
(CABLE-25S)

Your CodeMax® computerized code machine comes with the following additional items
(see the photos on the previous page):
Qty. Stock No. Description
1 CW-14MC HPC Cutter Wheel (Installed on Machine)
1 CW-1011 HPC Cutter Wheel
1 CW-20FM HPC Cutter Wheel
1 CW-47MC HPC Cutter Wheel
1 CW-90MC HPC Cutter Wheel
1 WRENCH-1 Cutter Shaft/Adjustment Wrench
1 WRENCH-3 Cutter Nut Wrench
1 WRENCH-2 Allen Wrench, 5/64-inch
1 CM-1054R Black Horseshoe Tip Gauge
1 CM-1054MA Red Tip Gauge
1 MAX-CD DSD List, CodeMax®Update and Restore CD
1 1200MAX-MAN CodeMax®Manual
1 — Warranty Registration Card
1 CABLE-25S Serial Cable
6CodeMax®CodeMax®

7
1.2 Parts Designation
X
120VAC Motor (CM-1080MA)
240VAC Motor (CM-1070)
Cutter Head (KM-1016)
Power Switch
120VAC (KM-1017)
240VAC (9160-SW)
Shoulder Gauge (CMB-FG)
Cutter Nut (CM-1039MA)
Cutter (Wide Selection
Available)
Wing Nut (EGN-1)
Keypad (MAX-4)
Eccentric Shaft
(CM-1041)
Tip Gauge (CM-1054MA)
Top Jaw (CM-1056MA)
Bottom Jaw
(CM-1055MA)
Emergency Stop Button
(MAX-50)
Pivot Arm (CM-1024X)
Automatic Angler
CodeMax®CodeMax®

1.3 Preparing To Use The CodeMax®Computerized Key Machine
Before using the CodeMax®key machine, read this manual in order to gain a thorough
understanding of all of its capabilities. You will receive peak performance and efficiency
from your machine by fully comprehending all of its functions.
Make sure that the power outlet that the CodeMax®will attach to is properly wired, i.e.,
grounded with correct hot and neutral leads. If the outlet is not wired properly or power
from the available outlet is not regular (i.e., you experience frequent power brownouts), the
CodeMax®may malfunction. While the CodeMax®contains an internal surge protector, it
is recommended that you also use an external surge/brownout protector when operating the
CodeMax®.
8CodeMax®
CodeMax®

9
1.4 Basic CodeMax®Setup
Find a suitable location for the
CodeMax®machine. This should be
an area with good ventilation for the
cutter motor and easy access to the
front and top of the machine for use
and cleaning.
Plug the cord into the back of
the CodeMax®and then into the
appropriate electrical outlet. Turn
on the CodeMax®using the switch
located at the left rear of the
machine.
The display will read “Emergency
Stop Depressed”. Make sure there
is nothing interfering with the
pivot arm, cutter wheel, and motor.
Push the large, red emergency stop
button located at the front of the
CodeMax®until it pops out.
The CodeMax®will go through a brief test
routine to prepare itself for use. The CodeMax®
display will read “CodeMax Ready”, indicating
that the machine is in its main screen and ready
for use.
CodeMax Ready
HPCSoft Version 10.0
CodeMax®
CodeMax®

1.5 The Emergency Stop Button
The CodeMax®has an emergency stop button installed.
Pushing the emergency stop button at any time will immediately freeze the operation in
which the machine is engaged. For example, if you started the cutting process and realized
you had the wrong cutter or key blank, pushing the emergency stop button would instantly
turn off the cutter motor and stop the pivot arm from traveling.
To reset the CodeMax®, after the
machine freezes, push the emergency
stop button until it pops out, and
the machine will return to its Home
Position. Make the necessary
adjustments (e.g. put the shoulder
gauge down, or install the correct
cutter or key blank), and start the key
cutting process again.
*Note: When the emergency stop button is pushed, the CodeMax® will clear the bittings entered,
if the bittings were entered directly on the CodeMax®keypad.
If you have any questions, please call the HPC Service Dept. 1-800-323-3295.
10 CodeMax®
CodeMax®

11
2. Cutter Wheels
2.1 Cutter Wheel Descriptions
The model CodeMax®is supplied with five
standard cutter wheels. The CW-1011 cutter
is used for cabinet, padlock, and most vehicle
applications. The CW-14MC cutter is used for
cutting most standard cylinder keys. The CW-
90MC is similar to the CW-14MC but makes cuts with
a steeper slope for special applications. The CW-20FM cutter
is a 76 degree cutter used for Sargent applications.
The CW-47MC is an 87 degree cutter used for certain
automotive applications.
Flat steel cutters, the Medeco®cutter (CW-1012), the Emhart cutter (CW-1013), and the
Assa Cutter (CW-32MC) are all optional cutter wheels that are available for use with the
CodeMax®. Additionally, the Medeco®Commercial Jaw (MJ-1) is an optional jaw for
cutting the Medeco®Standard Commercial Keyway (Air). The KeyMark®Jaw is available
from Medeco®.
CodeMax®

12
2.2 Replacing Cutter Wheels
The following procedure is recommended when changing cutters:
IMPORTANT NOTE: Be sure the cutter is installed for a clockwise rotation, with the arrow
facing the outside, so it can be seen.
1) Turn the CodeMax®off.
2) Hold the cutter shaft with the
1/2 inch end of WRENCH-1.
3) Loosen the cutter shaft nut with
the 3/4 inch WRENCH-3 by turning
it clockwise (left hand thread). The
cutter shaft is threaded with reverse,
left-hand thread.
CodeMax®
CodeMax®

13
4) Remove the cutter. Slide the
replacement cutter onto the shaft.
IMPORTANT NOTE: Be sure the cutter is installed
for a clockwise rotation, with the arrow facing the outside, so it can be seen.
5) Hold the shaft with the 1/2 inch WRENCH-1.
6) Install the nut, turning counterclockwise
onto the cutter shaft with the
3/4 inch wrench.
Do not overtighten the nut!
CodeMax®
CodeMax®

2.3 Resharpening Cutter Wheels
One of the most important features of the CodeMax®is its capability to maintain correct
depth and spacing with virtually no setup time involved, including the changing of the
cutter wheels. This capability is dependent upon the use of cutters whose outside diameters
are carefully calibrated. We recommend using only HPC cutter wheels.
Eventually, cutters become worn and should be replaced. We do not recommend sharpening
cutters.The diameter of a resharpened
In order to maintain matched cutter diameters, all cutters for the CodeMax®
must be
resharpened at the same time to account for material lost during this process.
cutter is smaller and will therefore make cuts shallower
See Depth Adjustment Section (5.2) for further information.
14 CodeMax®
if no depth adjustment is made.

3. Holding And Gauging Keys
The CodeMax® comes from the factory calibrated and ready to cut keys to manufacturers’
specifications. The necessity for special gauges and adapters has been held to a minimum.
Basically, one upper Vise Jaw, which is removable and reversible, covers the greatest range
of key cutting. This upper Vise Jaw (CM-1056MA) is marked “A” on one side and “B” on
the other. When the A side is in use, the letter “A” faces up, in sight of the operator. The
B side is in position when the “B” is seen. Manufacturers’ data and information about the
corresponding jaws can be found on the DSD-CD.
3.1 Vise Jaws
Jaws A & B – Standard Jaws (CM-1056MA) Installed
Fig. 1A. Properly seated key in jaw A. Fig. 1B. Properly seated key in jaw B.
Vise jaw A is used for all standard keys with the deepest cut no less than .142 inches (see
Fig. 1A). Jaw B is used for small keys that use cuts of such great depth that a lip on the jaw
is provided to hold the key closer to the cutter. See Fig. 1B.
Some keys (Best™for example) will tip
when using Jaw A. If there is a problem
holding the key in Jaw A, use Jaw B
by placing the lip of Jaw B on the edge
of the blank. The blank must still be
positioned at the back of the bottom jaw.
See Fig. 2.
Fig. 2.
15
CodeMax®
CodeMax®

Jaw C – Medeco®Jaw (MJ-1) Optional Equipment Required For Cutting Medeco®
Keys (Not Required For Biaxial Keys)
Fig. 3A. Fig. 3B. Properly seated key in jaw C.
An optional cutter (CW-1012) and Jaw C (MJ-1) are required to cut commercial level
Medeco®keys. Both parts are readily available from your HPC distributor. Biaxial keys
only require the CW-1012 cutter, not MJ-1.
The optional Jaw C is a specially milled CodeMax®jaw. It is required for holding the
standard Medeco®keys (see Fig. 3A). Vise Jaw C is milled to fit and firmly nest into
the Medeco®commercial key grooves. The proper and firm grip provided by Jaw C is
necessary due to the extremely deep cuts used on Medeco®keys. Instructions for using
Medeco’s KeyMark®Jaw are available from Medeco®.
Gauge the key from the shoulder, making sure the key grooving and special jaw milling are
nested together (see Fig. 3B).
16
Shoulder Gauge
CodeMax®
CodeMax®

3.2 Key Gauges
Fig. 4 Fig. 5 Fig. 6 Fig. 7
Fig. 8 Fig. 9 Fig. 10
Keys with shoulders are gauged by placing them squarely into the vise assembly and
swinging the key Shoulder Gauge (CMB-FG) upward. The key is moved laterally, as
required, until the key’s shoulder just touches the left hand surface of the gauge (see Fig. 4).
Note: Be sure to tighten the wing nut and swing the Shoulder Gauge back down before starting
the cutting process.
Keys without shoulders are properly gauged by using the Red Tip Gauge (CM-1054MA) or
the black Horseshoe Tip Gauge (CM-1054R). The bottoms of these tip gauges have several
grooves, allowing them to be held in different positions by a spring loaded ball bearing.
These tip gauges are pulled back to the first position where they are held within the base of
the lower jaw (Figs. 5 & 6) safely out of the path of the cutting wheel.
See Figs. 7, 8, 9, & 10 for tip gauge references.
17
Position 2
Horseshoe Tip
Gauge
Top View of
Horseshoe
Tip Gauge in
Position 1
Horseshoe Tip
Gauge
Top View of
Red Tip Gauge
in Position 2
Position 1
Red Tip
Gauge
Shoulder
Gauge
CodeMax®
CodeMax®
Red Tip
Gauge
Position 2

Fig. 11. Fig. 12. 5 Pin Ford.
In the third position, the Red Tip Gauge is sent forward into the third groove and this is
the proper setting for old, 5-pin Ford keys (see Figs. 11 & 12). To clamp and gauge double
sided Ford type keys, the offset of the key is set against the face of the jaw. Slide the key to
the right until the tip butts against the tip gauge and tighten the wing nut. The blank is held
off the key rest by this method, thereby eliminating the need for any special blocks (see
Figs. 11 & 12).
Red (Plastic) Tip Gauge (CM-1054MA) (Black) Horseshoe Tip Gauge (CM-1054R)
Position 1: Out of the way Position 1: Best – Right Leg
Position 2: Best Position 2: Ford – Right Leg
Position 3: Ford Position 3: Best – Left Leg (same as 2 red)
Position 4: Ford – Left Leg (same as 3 red)
Note: Red Tip Gauge should be pulled back to position 1 or removed when
cutting shoulder gauged keys.
Remove Black Horseshoe Tip Gauge completely when gauging or cutting shoulder gauged
keys or when gauging from positions 3 and 4 prior to cutting.
Positions 1 and 2 of Horseshoe Tip Gauge are designed to bring the tips of key blanks even
with the right side of the jaw. If the right leg is bent inward (so the tip gauge doesn’t enter
the jaw) or bent outward (so key blanks gauge beyond the right side of the jaw) the right leg
should be gently tapped back into alignment.
18
Position 1
Position 2
Position 3
Position 3
Position 2
Position 1
Position 4
Right Leg
Left Leg
Red Tip Gauge
Red Tip
Gauge
Wing Nut
CodeMax®
CodeMax®
Position 3

3.3 Gauging Methods
3.3.1 Standard Cylinder Key With Shoulder Gauging Using Jaw A (Example:
Schlage, DSD #60)
1) Place the key blank in Jaw A. Raise the Shoulder
Gauge to its upright position. Position the key blank
with the shoulder of the key lightly touching the left
hand edge of Shoulder Gauge (avoid undue pressure
– see Note below).
Note: The spacing of the key cuts can be significantly affected
by any damage incurred to the Shoulder Gauge. Handle the
Shoulder Gauge with care! Damage to the Shoulder Gauge
most often occurs when the gauge comes in contact with the
cutter, or when undue pressure is used when gauging against
the key’s shoulder. Make sure to gently position the key blank
against the Shoulder Gauge to avoid damage.
2) Make sure the Tip Gauge
(if installed) is out of
the way. The Red Tip
Gauge is pulled to the rear
and safely in the detent
position (Position 1)
before continuing, and the
Horseshoe Tip Gauge is
removed.
19
Red Tip
Gauge
Position 1
CodeMax®
CodeMax®
Shoulder Gauge
Table of contents
Other HPC Cutter manuals
Popular Cutter manuals by other brands

Cricut
Cricut Mini Getting started

B+BTec
B+BTec Diamond3 RAPTOR Translation of the original operating instructions
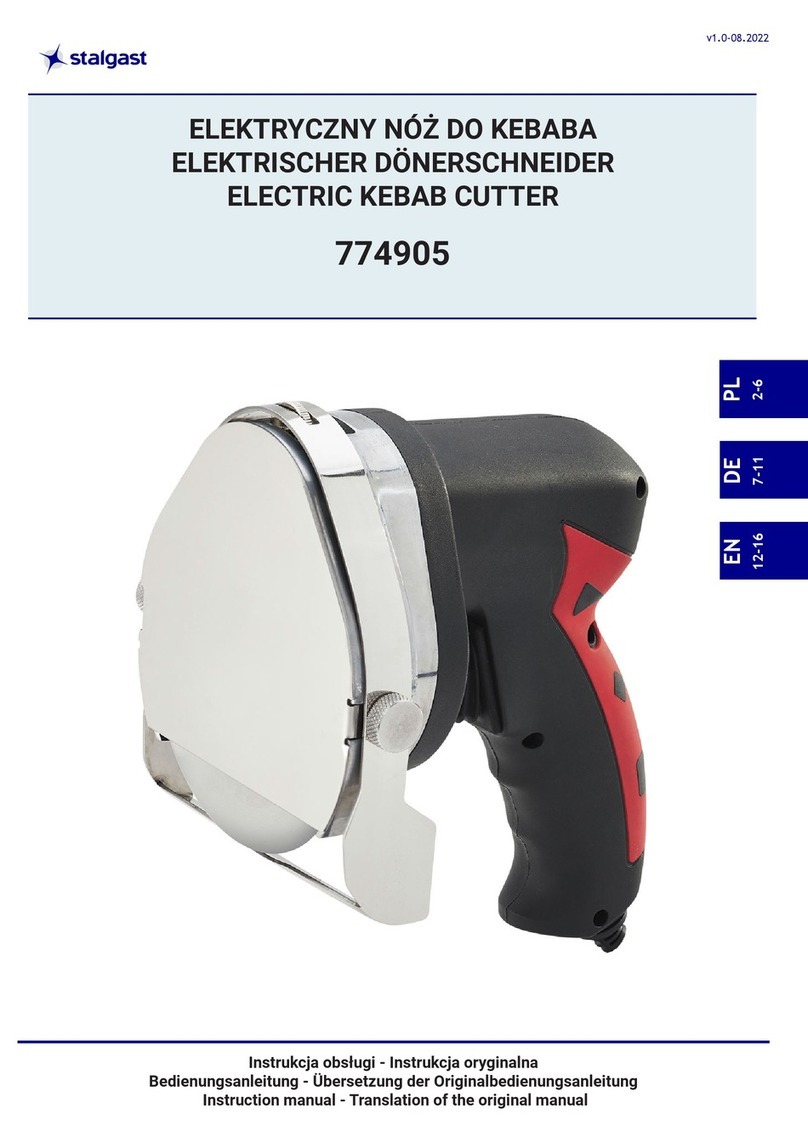
Stalgast
Stalgast 774905 instruction manual
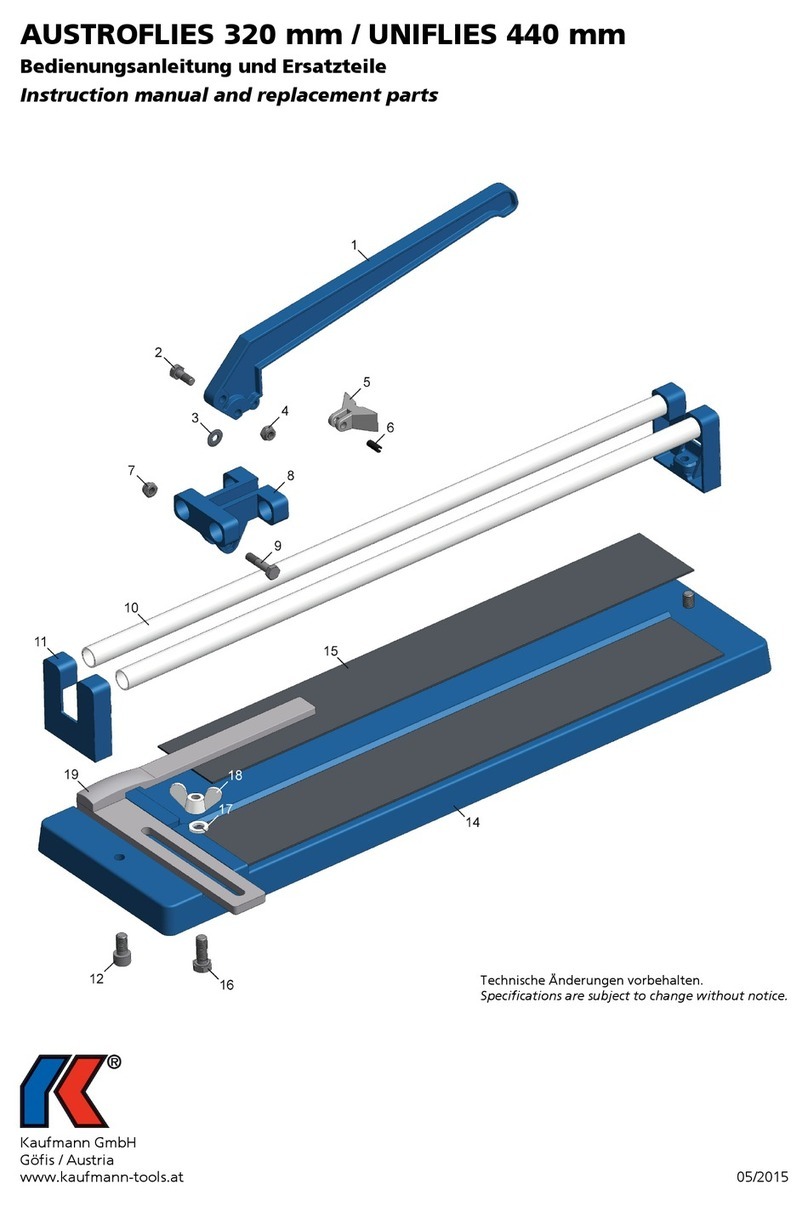
Kaufmann
Kaufmann AUSTROFLIES 320 Instruction Manual and Replacement Parts

Mr Beam
Mr Beam Dreamcut II user manual

DeWalt
DeWalt Impact Connect DWAPVCIR instruction manual
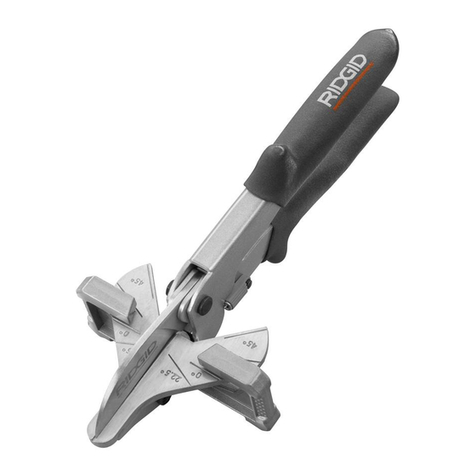
RIDGID
RIDGID FT6012 quick start guide
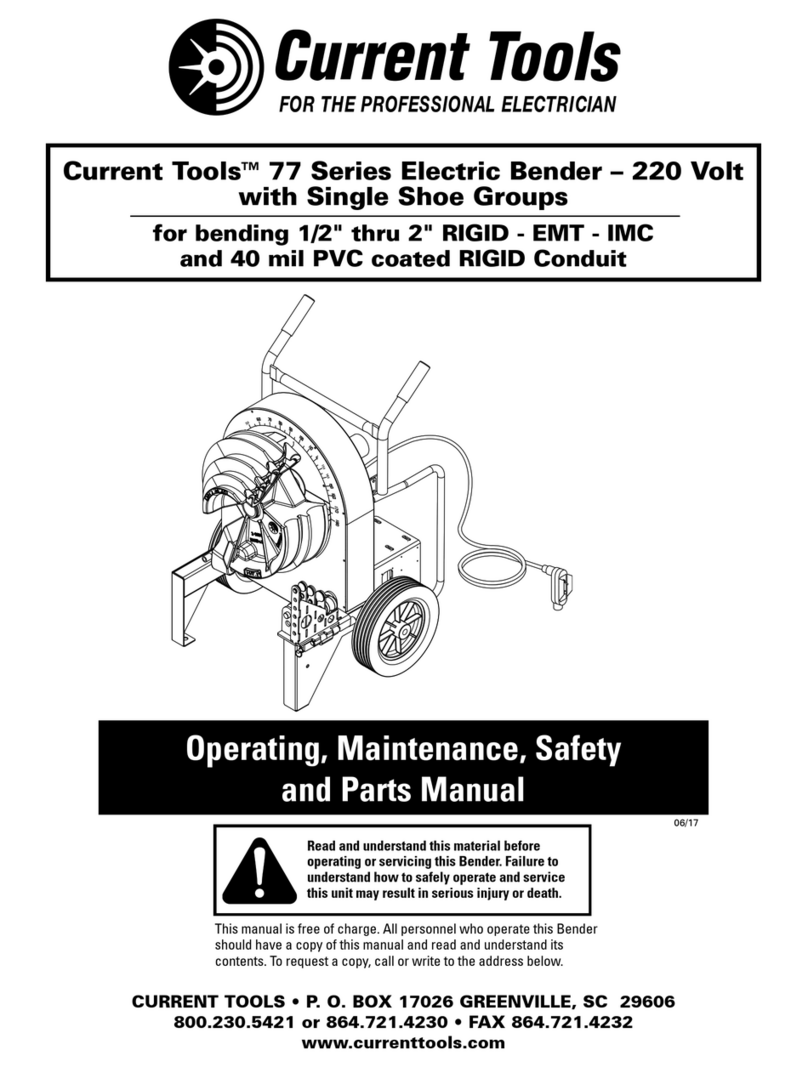
Current Tools
Current Tools RotaBoom 77-22 Operating, Maintenance, Safety and Parts Manual

Zimmer
Zimmer ZK1000 Series Installation and operating instructions
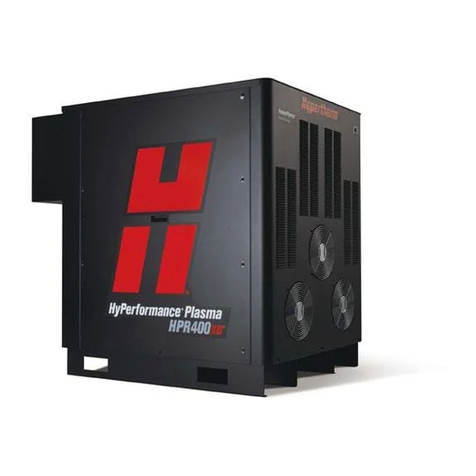
Hypertherm
Hypertherm HyPerformance HPR400XD instruction manual
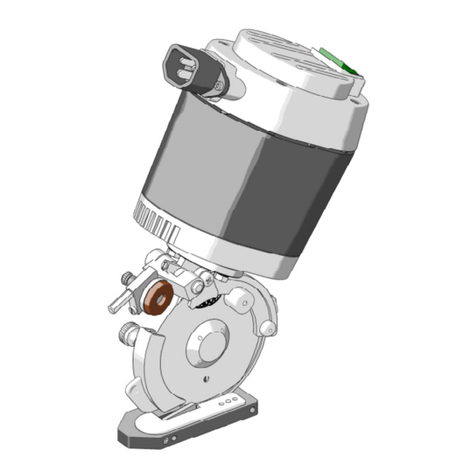
RASOR
RASOR D 86PS user manual
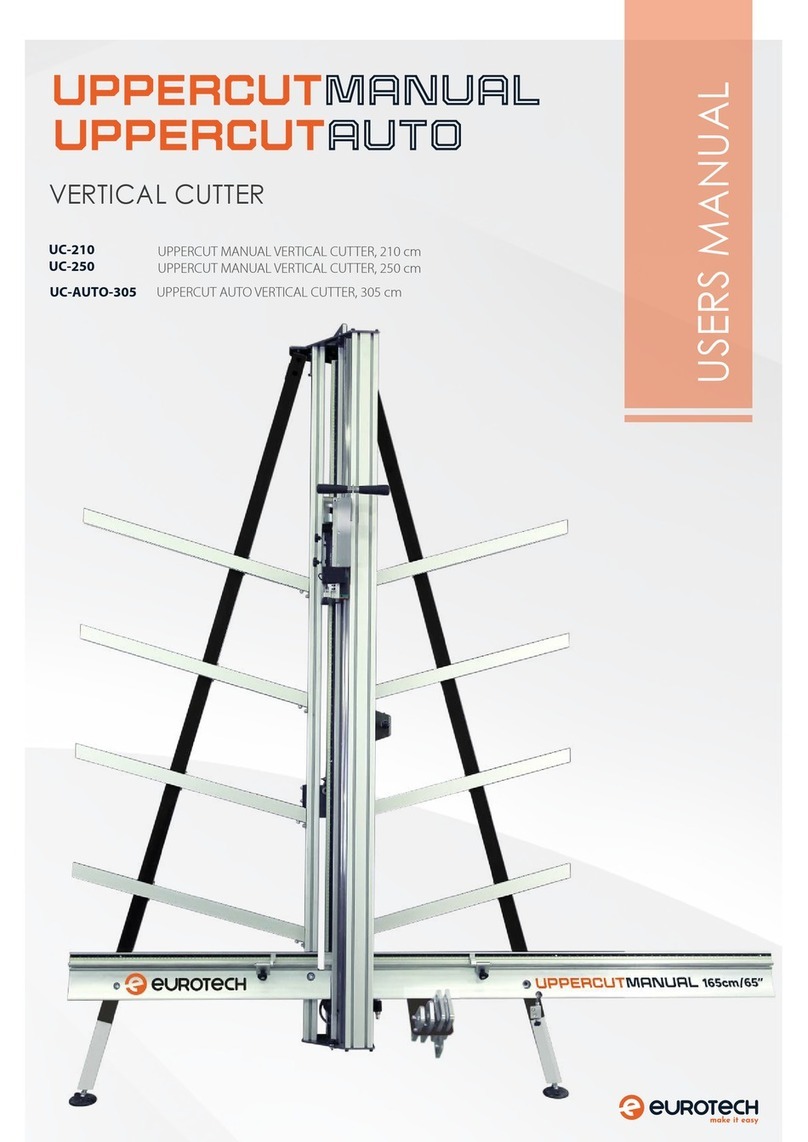
Eurotech
Eurotech UPPERCUTMANUAL user manual