Hurco TM6 Operating instructions

Lathe Programming Guide
I. Getting Started.
Steps to make sure your lathe is configured properly.
II. Two Axis Lathe Samples
Machines Covered
TM6, TM8, TM10, TM12, TM18
TMX8, TMX10
III. Live Tool Lathe Samples
Machines Covered
TMM8, TMM10
IV. Live Tool Y Axis Lathe Samples
Machines Covered
TMX8MY, TMX8MYS, TMX10MY, TMX10MYS
All live tool lathes that are an “i” series machine will use the same examples.
All examples are done programming in software version 09.02.68
Please read this document until a stop for your machine type is reached.
This document was designed to be used as a work book, do not jump ahead!
This document was developed by Hurco Applications in Indianapolis Indiana by Hurco USA.
THIS DOCUMENT IS STILL IN THE TESTING, THIS DOCUMENT MAY NOT BE EXACT OR COMPLETE AT THIS
TIME, PLEASE CALL HURCO APPLICATIONS FOR ADDITIONAL SUPPORT.

I. Getting Started
Make sure the software version on the machine is on this software or a
more current version than 09.02.68.
Check the first two digits to make sure it is larger than 09
Check the second set of digits to make sure it is larger than 02
Check the last set of digits to make sure it is larger than 68

The next step is to make sure the NC setting have been
properly set.
Press the AUX/Menu button on the control.
This button is located next to the Input button on the control. It will be one of the large
oval shaped buttons.
Press the utilities key on the touch screen.
Press the user preferences soft key
Press the NC Setting key
This control should display this screen.

Set all the settings as displayed above. The only setting
that may change is the ISNC G Code Mode. (see next page)
There are Two settings for G code interpertation.
The easiest way to think about these two modes is to imagine they are dialects, some of the
codes will mean different things, however all the functionallity exist in both modes, you may just need
to use a different code.
STOP!
Some codes are only available in certain modes. The mode of ISNC G-code will determine how
to program the machine.
Mode A is an older style of code and may not have all the functionality that Mode B will
contain. Mode A’s purpose is to add flexability. Mode A may allow programs from an older
control that is not a Hurco control to run on a hurco control will little to no modification.
Mode B is the Prefered way to program a Hurco Turning
Center!
ALL EXAMPLES WILL BE IN MODE B!

Most codes will retain the same functionallity.
These codes Containt the same functionality between modes, however may still require different
parameters.
G00, G01, G02, G03, G04, G06, G07, G08, G09, G10, G11, G17, G18, G19, G20, G21, G28, G40, G41, G42,
G53, G54-G59, G54.1, G61, G64, G65, G66, G67, G70, G71, G72, G73, G74, G75, G76, G80, G81, G82,
G83, G84, G85, G86, G87, G88, G89, G93, G96, G97.
This table will show the main differences
Mode A
Mode B
G50
Max RPM
G92
Max RPM
G98
Per Min Feed
G94
Per Min Feed
G99
Per Rev Feed
G95
Per Rev Feed
No Code
G98
Return to Initial Level
No Code
G99
Return to R point Level
G94
End Face Turning Cycle
G79
End Face Turning Cycle
G92
Thread Cutting Cycle
G78
Thread Cutting Cycle
No Code
X,Y,Z Coordinates Abs
G90
Absolute Programming
No Code
U,V,W Coordinates Inc
G91
Incremental
Programming
G90
Outer/Inner Cutting
Cycle
G77
Outer/Inner Cutting
Cycle
G32
Thread Cutting
G33
Thread Cutting
The table above can be used as a reference guide to change
codes to alter an existing program.

II. Two Axis Lathe Programming Guide
Tools
1. OD turning tool
2. OD threading tool
3. ½ inch drill
4. ID turning tool
5. 1/8 cutoff/grooving tool
To start a Lathe Program begin with a safe startup line.
%
O1234(SAFE STARTUP LINE EXAMPLE)
G20 G40 G80 G90
G28 U0. W0. (SENDS TURRET HOME)
From This point call up a tool and set the max rpm and turn on the spindle.
T0101 (CALL TOOL ONE OFFSET ONE)
G92 S1000 (MAX RPM 1000RPM)
G97 M3 S500 (TURN THE SPINDLE ON AT 500 RPM)
Now we are ready to call up a work offset and command motion
G54
G0 G95 Z.25
From this point on we are able to begin programming features
From this point on most likely the next operation would be facing the part. We will leave
stock to take off later with a finish cycle.
Note: you must leave stock with a roughing cycle.
Tip: the position right before a canned cycle should be a safe position or
rapid position.

X2.25
G96 G1X2.1 F.004 (CONSTANT SURFACE SPEED)
G72 U.1 R.1 (U is depth of cut R is retract distance)
G72 P1 Q2 U0.005 W0.005 F.002 S1000 T0101
N1 G1 X2.0 Z0.
X-.04
N2 Z.05
G0 X2.25 Z.25 (RETURN TO SAFE POSITION)
Since the face is now roughed we can come back in with a finish pass
G70 P1 Q2 F.002 S1000
X2.25 Z.25 (RETURN TO SAFE POSITION)
In this example the profile was used from the roughing cycle.
Next step is to cut a profile. The profile for this example will be a basic step cylinder.

G71 U.1 R.1
G71 P3 Q4 U.005 W.002 F.005 S1000
N3 G1 Z.05 X.95
Z0.
X1.Z-.025
Z-.5
X1.2
X1.25 Z-.55
Z-1.
G2 X1.75 Z-1.25 R.25
G1 X1.95
X2. Z-1.3
N4X2.05
X2.25 Z.25 (RETURN TO SAFE POSITION)
Now the profile is roughed finishing can be done with one line of code.
G70 P3 Q4 F.002 S1000
X2.25 Z.25 (RETURN TO SAFE POSITION)
M5 (STOP SPINDLE)

The code above should display an image similar to this in the graphics screen.

Note: G73 can also be used to rough a profile, or to do multiple finish passes to
step down a profile.
Tool change
Before the turret is indexed to the next tool it should be at the home position.
G28 U0. W0.
Now the turret can index and setup the speed for the next tool and move to position.
T0202
G92 S1000
G97 M3 S500
G54
G0 G95 Z.25
X2.25
From this point an OD thread will be cut.

There are 3 cycles for threading in Mode B.
G33
Long Hand
G33 X___ Z___ P___(Start angle) F___
G76
Multiple Threading Cycle
G76 PXXXXXX Q___ R___
G76 X(U)___ Z(W)___ R___ Q___ F___
G78
Threading Cycle (box cycle)
G78 X___ Z___ R____(taper) F____
For this example G76 will be used
G76 P XX XX XX Q___ R___
The first two XX - number of finish passes 01-99
The second two XX –How many revs for a lead out 00-99
The final two XX –Angle of the tool tip (60 for 60 degree V)
Q- depth of cut
R –Finish Allowance
G76 X(u)___ Z(w)___ R___ P___ Q___ F___
X –Minor Diameter
Z –End position
R –Start radius minus end radius (taper)
P –Thread Height (major –minor)
Q –Depth for first pass
F –Thread lead

G76 P010060 Q.01 R.002
G76 X.875 Z-.25 R0 P.125 Q.015 F.076
X2.25 Z.25 (RETURN TO SAFE POSITION)
M5 (STOP SPINDLE)
At this point the part should resemble this in the graphics.
Now that the threading has finished the machine is ready to call
up another tool. The turret must be sent to the home position.
G28 U0. W0. (SENDS TURRET HOME)

The next step is going to be drilling.
The drill must be positioned
T0303
G92 S1000
G97 M3 S700
G54
G0 G95 Z.25
X0.
There are several drilling cycles
G81 X___ Z___ F___ S___ (standard drill cycle)
G82 X___ Z___ P___ F___ S___ (dwell drill cycle)
G83 X___ Z___ P___ Q___ F___ S___ (peck drill cycle)
G83.1 X___ Z___ P___ Q___ F___ S___ (chip breaker)
X - X position
Z - Depth
F - Feed
S - Speed (RPM)
P - Dwell at the bottom of the hole
Q - Peck depth
G83 X0. Z-1.5 P1. Q.1 F.005 S700
G80 (CANCELS CANNED CYCLE)
M5 (STOP SPINDLE)
The drill needs to be sent home.
G28 U0. W0. (SENDS TURRET HOME)

There is also Rigid tapping available. This is not in the
sample code, however here is the information for the canned
cycle.
Here is an example line of code for rigid tapping
M29
G84 X0. Z-.5 P1. Q.25 F.07692 S250
Q is Peck depth.
The next process is boring.
This follows the same principles as OD turning and facing.
T0404
G92 S1000
G97 M3 S500
G54
G0 G95 Z.25
X.5
G96
G71 P5 Q6 U.005 W.002 F.005 S1000
N5 G1 X.85 Z.05
Z0.
X.75 Z-.05
Z-1.
N6 X.5
G0 Z.25 X.5
G70 P5 Q6 F.002 S1000
G0 Z.25 X.5

M5 (STOP SPINDLE)
Once those operations are completed the tool should be sent
home for a tool change.
G28 U0. W0. (SENDS TURRET HOME)
Now the grooving tool should be called up in the program, and
we can position to a safe position
T0505
G92 S1000
G97 M3 S500
G54
G0 G95 Z-.3
X2.25

There is no canned cycle for grooving; everything must be
programmed point to point.
X1.1 Z-.3
G96
G1 X.865 F.005
G0 X1.1
Z-.25
G1 X1. F.002
Z-.275
G3 X.95 Z-.3 R.025
G1 X.865
G0 X1.1
Z-.35
G1 X1. F.002
Z-.325
G2 X.95 Z-.3 R.025
G1 X.865
G0 X2.25
M5 (STOP SPINDLE) (DO NOT USE THIS LINE IF THE MACHINE IS A 2 AXIS LATHE. A SPINDLE STOP
IS ONLY NEEDED IF ANOTHER TOOL WERE TO BE CALLED.)
If the machine has live tool capabilities please skip cutoff block
Live tool operations will be programmed before cutoff.

Cutoff
Omit the 4 lines below (green) for two axis example; these 4 lines are only for reference for live
tool examples.
T0505
G92 S1000
G97 M3 S500
G54
Z-1.75
X2.1
G1 X1.85 F.003
G0 X2.1
Z-1.65
G1 X2.
Z-1.7
X1.9 Z-1.75
X-.04
X2.25
M5 (STOP SPINDLE)
G28 U0. W0.

Two axis sample program
%
O1234(TWO AXIS SAMPLE)
G20 G40 G80 G90
G28 U0. W0. (SENDS TURRET HOME)
T0101 (CALL TOOL ONE OFFSET ONE)
G92 S1000 (MAX RPM 1000RPM)
G97 M3 S500 (TURN THE SPINDLE ON AT 500 RPM)
G54
G0 G95 Z.25
X2.25
G96 G1X2.1 F.004
G72 U.1 R.1 (U IS DEPTH OF CUT R IS RETRACT DISTANCE)
G72 P1 Q2 U0.005 W0.005 F.002 S1000 T0101
N1 G1 X2.0 Z0.
X-.04
N2 Z.05
G0 X2.25 Z.25 (RETURN TO SAFE POSITION)
G70 P1 Q2 F.002 S1000
X2.25 Z.25 (RETURN TO SAFE POSITION)
G71 U.1 R.1
G71 P3 Q4 U.005 W.002 F.005 S1000
N3 G1 Z.05 X.95
Z0.
X1.Z-.025
Z-.5
X1.2
X1.25 Z-.55
Z-1.
G2 X1.75 Z-1.25 R.25
G1 X1.95
X2. Z-1.3
N4X2.05
X2.25 Z.25 (RETURN TO SAFE POSITION)
G70 P3 Q4 F.002 S1000
X2.25 Z.25 (RETURN TO SAFE POSITION)
M5 (STOP SPINDLE)
G28 U0. W0. (SENDS TURRET HOME)
T0202
G92 S1000
G97 M3 S500
G54
G0 G95 Z.25

X2.25
G76 P010060 Q.01 R.002
G76 X.875 Z-.25 R0 P.125 Q.015 F.076
X2.25 Z.25 (RETURN TO SAFE POSITION)
G28 U0. W0. (SENDS TURRET HOME)
M5 (STOP SPINDLE)
T0303
G92 S1000
G97 M3 S700
G54
G0 G95 Z.25
X0.
G83 X0. Z-1.5 P1. Q.1 F.005 S700
G80 (CANCELS CANNED CYCLE)
G28 U0. W0. (SENDS TURRET HOME)
M5 (STOP SPINDLE)
T0404
G92 S1000
G97 M3 S500
G54
G0 G95 Z.25
X.5
G96
G71 P5 Q6 U.005 W.002 F.005 S1000
N5 G1 X.85 Z.05
Z0.
X.75 Z-.05
Z-1.
N6 X.5
G0 Z.25 X.5
G70 P5 Q6 F.002 S1000
G0 Z.25 X.5
G28 U0. W0. (SENDS TURRET HOME)
M5 (STOP SPINDLE)
T0505
G92 S1000
G97 M3 S500
G54
G0 G95 Z-.3
X2.25
X1.1 Z-.3
G96
G1 X.865 F.005
G0 X1.1

Z-.25
G1 X1. F.002
Z-.275
G3 X.95 Z-.3 R.025
G1 X.865
G0 X1.1
Z-.35
G1 X1. F.002
Z-.325
G2 X.95 Z-.3 R.025
G1 X.865
G0 X2.25
Z-1.75
X2.1
G1 X1.85 F.003
G0 X2.1
Z-1.65
G1 X2.
Z-1.7
X1.9 Z-1.75
X-.04
G0X2.25
M5 (STOP SPINDLE)
G28 U0. W0. (SENDS TURRET HOME)
M30
Other manuals for TM6
1
This manual suits for next models
12
Other Hurco Lathe manuals
Popular Lathe manuals by other brands
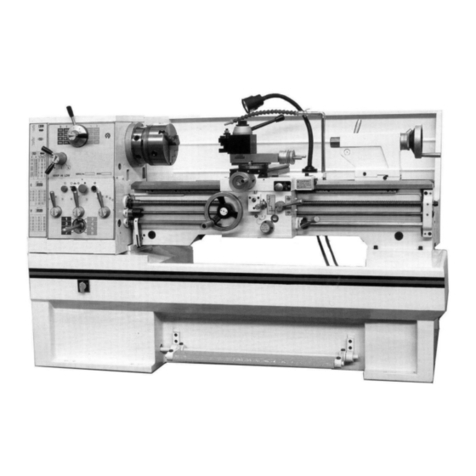
YANGZHOU SUPER MACHINE TOOL
YANGZHOU SUPER MACHINE TOOL CD6240 Instruction manual and parts list
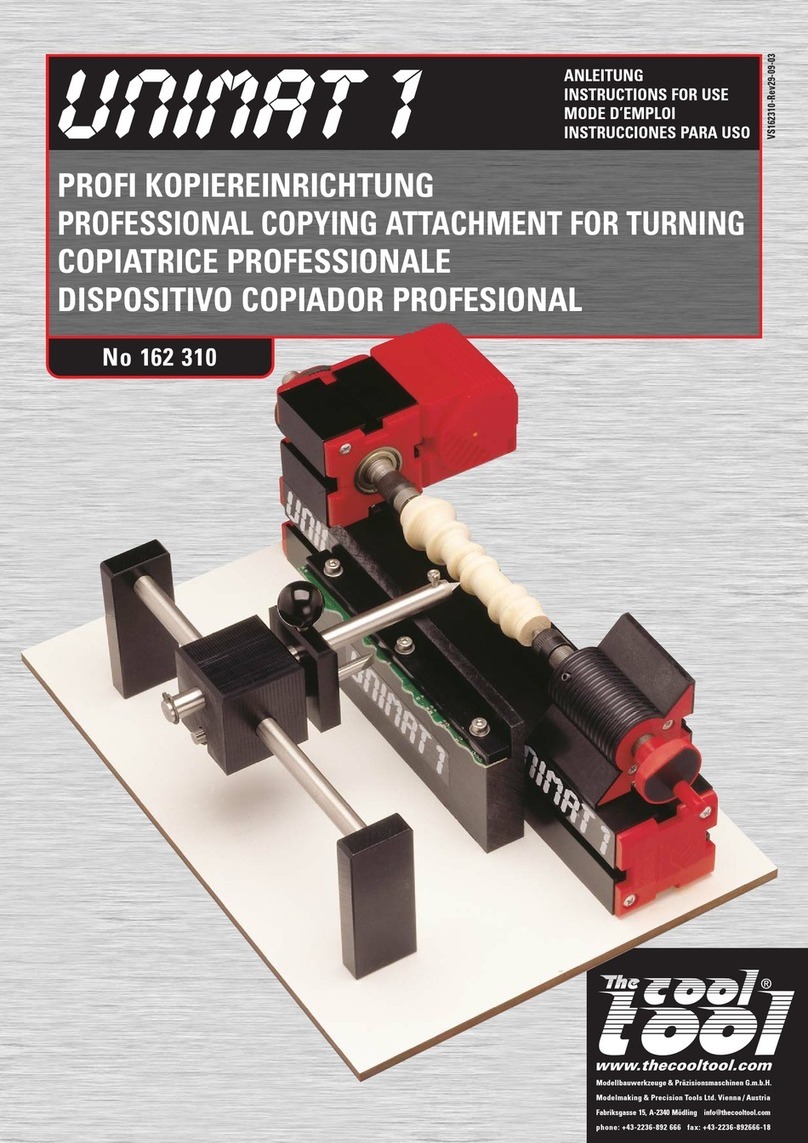
Cool Tool
Cool Tool UNIMAT 1 Instructions for use
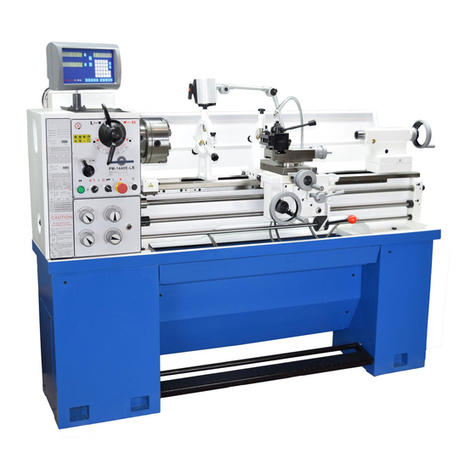
Precision matthews
Precision matthews PM-1440E-LB Faq
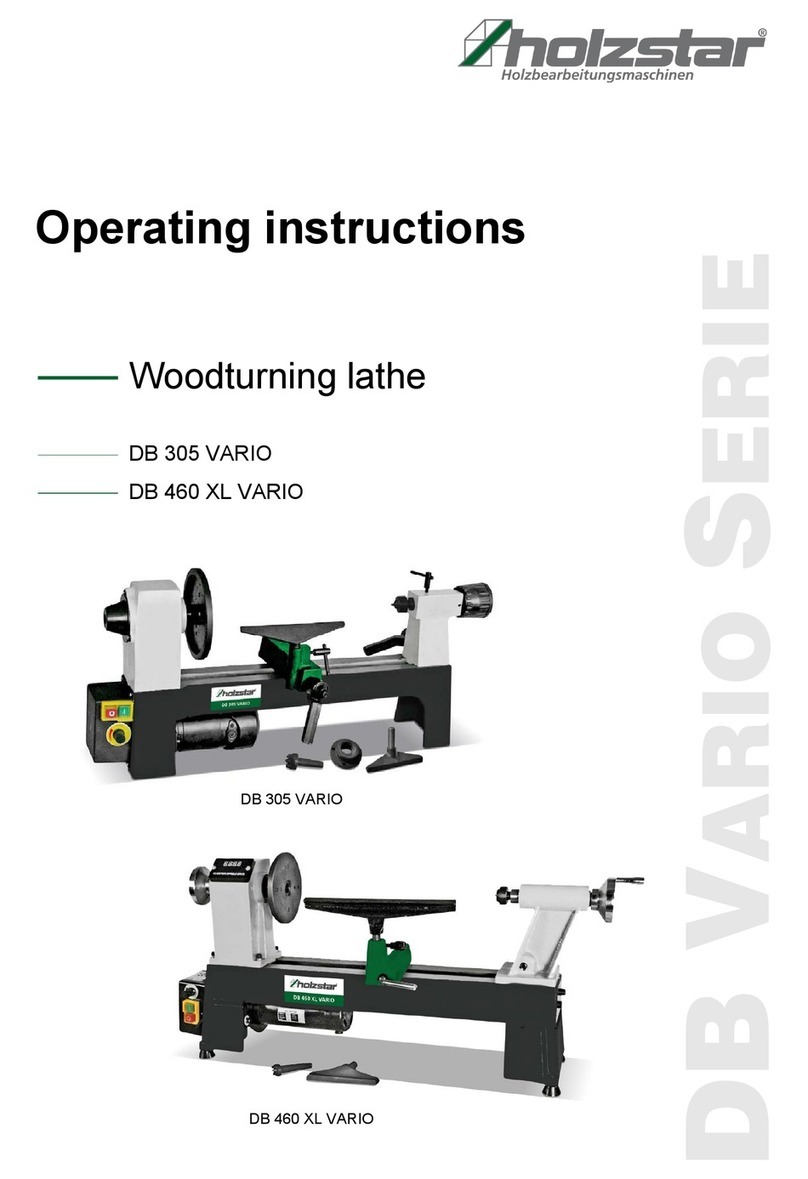
Holzstar
Holzstar DB 305 VARIO operating instructions
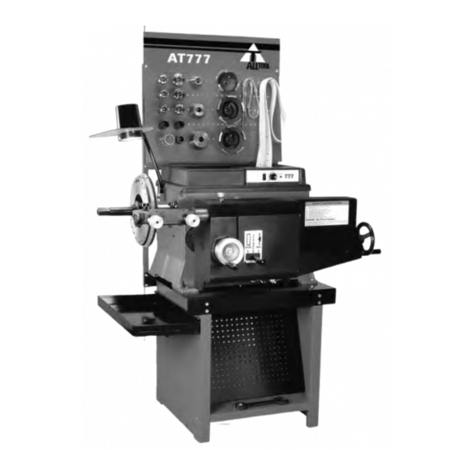
AllTool
AllTool MicroFinisher 777 Operating manual & parts list
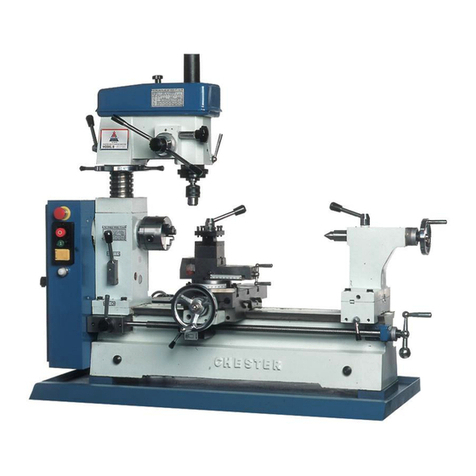
CHESTER U.K.
CHESTER U.K. B-Super 3-in-1 instruction manual