IDEC FS1A-C11S User manual

FS9Z-B1218
FS1A-C11S
Safety Controller
SafetyOne
User’s manual


SAFETY PRECAUTIONS
Carefully read this user’s manual to ensure correct operation before starting installation, wiring,
operation, maintenance, and inspection of the SafetyOne.
In this user’s manual, safety precautions are categorized in order of importance Warning and
Caution, as follows:
Warning
Warning notices are used to emphasize that improper operation may cause severe personal
injury or death.
Caution
Caution notices are used where inattention might cause personal injury or damage to
equipment.
Warning
Do not disassemble, repair, or modify SafetyOne. This will cause impairment of the safe
operability of SafetyOne.
Turn off the power to SafetyOne before starting installation, removing, wiring, maintenance, or
inspection. This can cause electrical shocks or fire hazard.
Before operating SafetyOne, carefully read the instruction sheet and this manual, and ensure that
the environment conforms to the requirements of SafetyOne specifications. If SafetyOne is
operated in an environment that exceeds the specifications, it causes impairment of the safe
operation of SafetyOne.
The installation, wiring, configuration, and operation of SafetyOne must be performed only by
“Safety responsible persons”. Safety responsible persons are personal who have requisite
qualification authorizing them as being capable of safely carrying out each step including the
designing, installation, operation, maintenance, and disposal of SafetyOne. Persons without
technical expertise of safety products must not use SafetyOne.
SafetyOne must be subjected to regular proof test verification that each function of SafetyOne is
performing up to the required standard.
Installation of SafetyOne must be performed according to the instructions found in the instruction
sheet and this manual. Improper installation may cause the SafetyOne to fail.
Do not use the monitor outputs or solenoid/lamp outputs as a safety outputs. When there is a
failure in SafetyOne or peripheral devices, Impairment of the safe operation of the system is
possible.
The start switch has to be placed outside the danger zone and in a safe position from which there
is good visibility for checking that no person is within the danger zone.
Do not use the start input and the external device monitor input as a safety input. When there is a
failure in SafetyOne or peripheral devices, Impairment of the safe operability of the system is
possible.
Use the SafetyOne in compliance with laws and regulations of the country in which it is being
used.
Use safety inputs and safety outputs in circuit configurations conforming to the application
according to the usage, and the safety requirements.

Warning
Calculate respective safety distances, taking into consideration the response time of the
SafetyOne, safety devices to be connected to the SafetyOne, and each other device that forms a
part of the system configuration.
Applicable safety performance is dependent on each system configuration.
Use a power supply that meets following required specifications:
-Conforms to the power supply rating of SafetyOne.
-Complies with the SELV/ PELV circuit specified by EN 50178 or EN60950.
-Has the functionality or the functional equivalent of the control voltage and current of class 2
circuit, as defined in UL508 or UL1310.
-Is in compliance with safety laws and regulations relating to electrical safety, EMC, and like under
the laws and regulations of the country in which it is being used.
Ground the V- line (0V DC) for ground diagnosis.
In the case of a new configuration or modified installation, be sure to perform a check for each
input and output function.
Implement protective measures that personal, other than safety responsible persons operating
the SafetyOne, are unable to modify the configuration.
Separate SafetyOne from devices and wires which are not in accordance with class 2 circuit
requirements.

Warning
Do not connect devices having input and output specifications that do not satisfy the
requirements of the SafetyOne.
Refer to the following for information on the requirements of connected devices.
Connected Control Device
Requirements
Emergency stop switch
Device equipped with a direct opening action mechanism conforming to
IEC/EN60947-5-5 or indicated in IEC/EN60947-5-1
Interlock switch,
limit switch
Device equipped with a direct opening action mechanism indicated in
IEC/EN60947-5-1
Interlock switch with lock
Spring lock interlock switch with solenoid
Mode select switch
Device conforming to regulations of the country where used and required
categories (for example, switch conforming to IEC/EN60947-1)
Enabling switch
Device conforming to IEC/EN60947-5-8 (or IEC/EN60947-5-1)
Solid state output device
Device conforming to regulations of the country where used (for example,
safety light curtain conforming to IEC/EN61496-1)
PNP output (See Note 1)
Non-contact interlock switch
IDEC HS7A series, IDEC HS3A serise
Safety relay
Relay equipped with forced guide mechanism or conforming to EN50205
Contactor
(electromagnetic switch)
Contactor equipped with forced guide mechanism
Other control devices
Use start switches and other devices that conform to the regulations of the
country where used.
Muting sensor
Device conforming to IEC/EN60947-5-2 as shown below
-3 wire transmission (dark on) photoelectric switch which has a PNP open
collector output.
-3 wire (normal open) proximity switch which has a PNP open collector
output.
Muting lamp
Incandescent bulb indicator light conforming to IEC/EN60947-1 or
IEC/EN60947-5-1
Note 2: It is not possible to detect a disconnection of the muting lamp when
using an LED indicator light.
Input device for two-hand
control
Device witch the structure conforming to ISO13851, and consists of
momentary switches conforming to IEC/EN 60947-5-1 with NO/NC contacts.
Make sure that the end-user thoroughly understands the contents of this user’s manual.
Note 1. SafetyOne reads input data at regular intervals. Use a solid state output device that sends
output signals of the waveforms shown below. Otherwise the SafetyOne cannot process the input
signal correctly.
Applicable solid state
output device
Pulse output off cycle of 40ms or
more and an off time of 1ms or less.
Pulse output off time of 0.5ms or
less.
(Waveform of solid sate
output)
The device may not be usable even if the above specifications are satisfied. Be sure to
thoroughly confirm operations using the actual device.
Off cycle: 40ms or more
Off time:
1ms or less
Off time: 0.5ms or less

Caution
SafetyOne is designed for installation within an enclosure. Do not install SafetyOne outside an
enclosure. Install SafetyOne in enclosure rated IP54 or higher.
Install SafetyOne in environments described in the catalog, instruction sheet, and user’s manual.
If SafetyOne is used in places where it is subjected to high temperature, high humidity,
condensation, corrosive gases, excessive vibrations, and excessive shocks then electrical shocks,
fire hazard, or malfunction may result.
Environment for using the SafetyOne is “Pollution degree 2”. Use SafetyOne in environments of
pollution degree 2 (according to IEC/EN60664-1).
Prevent SafetyOne from falling while moving or transporting otherwise damage or malfunction of
the SafetyOne may result.
Prevent metal fragments and pieces of wire from dropping inside the SafetyOne housing. Put a
cover on the SafetyOne during installation and wiring. Ingress of such fragments and chips may
cause fire hazard, damage or malfunction.
Install SafetyOne, so that there is adequate distance from the walls, heat generating bodies, and
peripherals, taking into consideration space requirements for maintenance and ventilation.
Install SafetyOne on 35mm DIN rails with BNL6 mounting clips (sold separately) on both sides of
SafetyOne.
Wire the connectors with conforming cables or ferrules.
Ground FE terminal to assure electromagnetic compatibility.
Use common 0V DC, if different power supplies are used for SafetyOne and other devices (ex.
safety light curtain).
Wire the inputs and outputs so that they are separated from power lines.
When overcurrent flows into output terminals, the protective function turns off the output. However,
when overcurrent status lasts long, internal protective elements will fuse. To protect the internal
elements, insert fuses of double the rated value to each terminal.
Use IEC60127 approved fuses on the power line of SafetyOne. (This is required for equipment
incorporating SafetyOne that is destined for Europe.)
When disposing of SafetyOne, handle it under the laws and regulations of the country in which it
is disposed.

BEFORE GETTING STARTED
Thank you for your purchase of the IDEC SafetyOne (Type Number FS1A-C11S).
This user’s manual describes the specifications, and the procedures for installing and operating
the SafetyOne.
Read this manual carefully before using the SafetyOne so that you have an adequate
understanding of its functions and performance.
About directives and standards
SafetyOne is approved for following directives and standards by TÜV SÜD.
1. EU directives
-Machinery Directive: Directive 2006/42/EC
2. EN standards / IEC standards / ISO standards
EN 61131-2, IEC 61508 Part1-4, EN ISO 13849-1, IEC/EN 62061, IEC 61326-3-1
SafetyOne is approved for following directives and standards by UL.
1. UL standards
- UL 508
2. CSA standards
- CSA C22.2 No.142
SafetyOne has not undergone the type examination in accordance with Article 44-2 of the
Japanese Industrial Safety and Law. SafetyOne, therefore, cannot be used in Japan as a
"Safety Device for Press or Shearing machine" as established in Article 42 of that law.
The reproduction, transfer, sale, assignment, or loan of any or a part of this manual is strictly
prohibited.
The contents of this manual are subject to change without notice.
Thorough measures have been taken in preparing the contents of this manual; however, in the
case you find an error or the like, please bring it to the attention of your IDEC sales
representative.
NOTE

CONTENTS
Chapter1 OVERVIEW .......................................................................................................................................................... 1-1
About the SafetyOne................................................................................................................................................. 1-1
Features of the SafetyOne........................................................................................................................................ 1-2
Chapter2 PRODUCT SPECIFICATIONS.............................................................................................................................. 2-1
Parts Description....................................................................................................................................................... 2-1
General specifications............................................................................................................................................... 2-2
Dimensions............................................................................................................................................................... 2-4
Applicable standards................................................................................................................................................. 2-5
Safety performance .................................................................................................................................................. 2-6
Safety input specifications ........................................................................................................................................ 2-8
Start input specifications........................................................................................................................................... 2-9
Safety output specifications.................................................................................................................................... 2-10
Monitor output specifications ...................................................................................................................................2-11
Solenoid/Lamp output specifications ...................................................................................................................... 2-12
Logic number.......................................................................................................................................................... 2-13
Indicators................................................................................................................................................................ 2-14
Specification of configuration switches ................................................................................................................... 2-16
Connector specifications......................................................................................................................................... 2-17
Chapter3 INSTALLATION AND WIRING.............................................................................................................................. 3-1
WARNIG and CAUTION........................................................................................................................................... 3-1
Installation method.................................................................................................................................................... 3-3
Wiring method........................................................................................................................................................... 3-6
Chapter4 BASIC OPERATIONS........................................................................................................................................... 4-1
Internal states........................................................................................................................................................... 4-1
Turning on the power................................................................................................................................................ 4-3
Using the protective cover ........................................................................................................................................ 4-3
Logic configuration.................................................................................................................................................... 4-4
Timer configuration................................................................................................................................................... 4-6
Canceling the Protection state.................................................................................................................................. 4-8
Canceling the Stop state........................................................................................................................................... 4-9
Chapter5 LOGIC................................................................................................................................................................... 5-1
Logic selection guide ................................................................................................................................................ 5-1
Safety performance on each wiring of inputs and outputs ........................................................................................ 5-3
Logic 101: The logic for various apparatus............................................................................................................... 5-8
Logic 11A: The logic for apparatus with openings................................................................................................... 5-19
Logic 11b: The logic for apparatus with NO/NC contact inputs ............................................................................... 5-31
Logic 11C: The logic for apparatus with openings................................................................................................... 5-43
Logic 11d: Muting function logic for apparatus with openings................................................................................. 5-55
Logic 102: Partial stop logic for apparatus with openings....................................................................................... 5-69

Logic 12A: The logic for apparatus with a two-hand control device ........................................................................ 5-81
Logic 12b: The logic constructing an OR circuit for various apparatus ................................................................... 5-93
Logic 12C: The logic constructing an OR circuit for apparatus with openings ...................................................... 5-107
Logic 12d: Partial control logic for apparatus with openings ................................................................................. 5-120
Logic 103: Partial stop logic applicable for selection of active safety input devices.............................................. 5-132
Logic 13A: The logic applicable for selection of active safety input devices ......................................................... 5-144
Logic 13b: The logic constructing an OR circuit applicable for selection of active safety input devices................ 5-156
Logic 13C: Partial stop logic applicable for selection of active safety input devices ............................................. 5-170
Logic 13d: The logic applicable for selection of active safety input devices.......................................................... 5-184
Logic 104: Partial stop logic applicable for selection of active safety input devices.............................................. 5-198
Logic 14A: Partial stop logic applicable for selection of active safety input devices.............................................. 5-210
Logic 14b: Partial stop logic applicable for selection of active safety input devices.............................................. 5-222
Logic 14C: Partial stop logic applicable for selection of active safety input devices ............................................. 5-234
Logic 14d: Partial stop logic applicable for selection of active safety input devices for apparatus with openings . 5-246
Logic 105: Partial stop logic for apparatus with openings..................................................................................... 5-260
Logic 106: Partial stop logic for apparatus with openings..................................................................................... 5-272
Logic 107: Partial stop logic for various apparatus ............................................................................................... 5-284
Logic 108: Partial stop logic applicable for selection of active safety input devices in apparatus with openings... 5-296
Logic functions...................................................................................................................................................... 5-309
Chapter6 TROUBLE SHOOTING......................................................................................................................................... 6-1
Error descriptions and troubleshooting ..................................................................................................................... 6-1
APPENDIX ...............................................................................................................................................................................A-1
Minimum Distance ....................................................................................................................................................A-1
Maintenance and Inspection.....................................................................................................................................A-6
Type number.............................................................................................................................................................A-7
Accessories ..............................................................................................................................................................A-7
Options (sold separately)..........................................................................................................................................A-7


OVERVIEW
1-1
Chapter 1
Chapter1 OVERVIEW
This chapter provides an understanding of the SafetyOne. Make efficient use of
the SafetyOne by thoroughly familiarizing yourself with its functions.
About the SafetyOne
The FS1A series of SafetyOneTM controllers provides safeguarding measures for various factory
automation equipment and systems, including robots, production machinery, semiconductor
manufacturing apparatus, food packaging machinery, and printing machinery. You can easily
configure the safety circuits by using multiple safety inputs and outputs and selecting the circuit
(logic) built into the SafetyOne.

OVERVIEW
1-2
Features of the SafetyOne
You can configure safety circuits without the use of complicated external wiring or
special software, thereby greatly reducing the number of developmental man-hours
required for product certification and the training time of safety responsible persons.
You can use the DIP switches to select from 24 different types of logic circuits and set
the OFF-delay timer value to best match your application.
The SafetyOne has 16 DIP switches and an ENTER button, which can be used to set the
built-in types of logic and the delay timer values for the safety output is OFF.
You can choice logic circuit from integrated 24 types.
You can set the timer value to 0, 0.1, 0.5, 1, 2, 5, 15, or 30 seconds. You can set the stop
category to 0 or 1.
Conforms to the international safety standards IEC 61508 SIL 3 and EN ISO 13849-1 PL e
(Control category 4).
The SafetyOne can be used for functional safety standard IEC 61508 series and IEC 62061 SIL
1 to 3, which define the safety performance of machinery that uses microprocessors and
software, and for performance levels a to e of EN ISO 13849-1 and Control category B to 4 of
EN ISO 13849-1, which define safety performance of machinery control systems.
You can directly connect an emergency stop switch, interlock switch, light curtain, and
other various safety devices.
The SafetyOne provides dualchannel direct opening inputs such as an emergency stop switch or
interlock switch; dual channel NO/NC inputs such as a non-contact interlock switch; and dual
channel safety inputs such as a safety light curtain or safetylaser scanner. These inputs can be
enabled byselecting a certain type of logic, therebyenabling various safetydevices.
The SafetyOne comes with monitor outputs and solenoid/lamp outputs, which can be
used as control signals.
With monitor outputs, you can monitor the status of the SafetyOne, including safety inputs and
outputs and error information. When connected to a PLC, the SafetyOne can be used to control
all apparatus and the entire system. The SafetyOne is also provided with solenoid/lamp outputs,
which can be used to directly control spring lock safety switches with solenoids. In logic4,
muting lamps can be connected to solenoid/lamp outputs.
Obtain detailed diagnostic information with the LED displays.
The SafetyOne has two 7-segment LED displays for displaying internal information and 30 LED
lights for displaying status. You can use these to display input and output information and to
obtain detailed diagnostic information on the status of the SafetyOne.
Control multiple safety devices (12 safety inputs and 4 safety outputs) by a single unit.
The SafetyOne has 12 safety inputs and 4 safety outputs, and it can be configured for up to 6
dual channel inputs and 2 dual channel outputs (in case of use as a single channel output, up to
4 outputs)

PRODUCT SPECIFICATIONS
2-1
Chapter 2
Chapter2 PRODUCT SPECIFICATIONS
This chapter describes product specifications of the SafetyOne.
Parts Description
The protective cover is closed The protective cover is open
1. Protective cover: The cover protects unauthorized changing of configuration switches.
2. Input connector: Spring clamp connector for input devices. (Crimp connector can also be used.)
3. Output connector: Spring clamp connector for output devices and power supply.
(Crimp connector can also be used)
4. Logic LED: The 7-segment green LED indicates the number of logic pattern selected.
5. Error LED: The 7-segment red LED indicates an error in the SafetyOne and peripherals.
6. Timer LED: The eight Timer LEDs indicate the selected timer value.
7. Input/output status LED: The input LEDs indicate the state of inputs.
The output LEDs indicate the state of outputs.
SAFE-IN: Status of safe inputs, e.g. X0 … X15
START-IN: Status of start inputs, e.g. X16, 17
SAFE-OUT: Status of safe outputs, e.g. Y0 … Y3
SOLENOID-OUT: Status of solenoid outputs, e.g. Y17, 20
8. Logic switch: DIP switch for selecting the internal logic.
9. Timer switch: DIP switch for selecting the OFF-delay time for the safe output.
10. Enter button: button for activation of parameter changes.
11. Locking ring: ring for locking the protective cover

PRODUCT SPECIFICATIONS
2-2
General specifications
Operating conditions
Operating temperature
(Surrounding air
temperature)
-10 to +55 ºC (no freezing)
Relative operating humidity
10 to 95% (non-condensing)
Storage temperature
-40 to +70 ºC (no freezing)
Relative storage humidity
10 to 95% (non-condensing)
Pollution degree
2 (IEC/EN 60664-1)
Degree of protection
IP20 (IEC/EN 60529)
Corrosion immunity
Atmosphere be free from corrosive gas
Altitude
Operation: 0 to 2,000m (0 to 6,565 feet)
Transportation: 0 to 3,000m (0 to 9,840 feet)
Vibration resistance
Vibration (IEC/EN 60068-2-6):
5 to 8.4 Hz amplitude 3.5 mm,
8.4 to 150 Hz acceleration 9.8 m/s2(1G),
2 hours per each of XYZ axes
Bump (IEC/EN 60068-2-29):
Acceleration 98 m/s2(10G), 16ms duration, 1000 times per
each of XYZ axes
Shock resistance
147 m/s2(15G), 11 ms duration, 3 times per each of XYZ axes
(IEC/EN 60068-2-27)
Connector durability
50 times maximum
Operation strength of
configuration switches
100 operations maximum (per 1 switch)
Operation strength of
enter button
1000 operations maximum
Enclosure material
modified-Poly Phenylene Ether (m-PPE)
Weight
Approximately 330g
Life time
10 years (at 40 ºC of operating temperature)
Over voltage category
II
Electrical conditions
Rated voltage
24V DC
Allowable voltage range
20.4V DC to 28.8V DC
Maximum power
consumption
48W (at 24V DC, all inputs and outputs are ON,
includes output loads)
Allowable momentary
power interruption
10ms minimum (at rated voltage DC)
Reaction time
ON to OFF: 40 ms maximum Note1
: 100ms maximum Note2
OFF to ON: 100 ms maximum Note3
Start-up timeNote4
6s maximum
Dielectric strength
Between live part and FE terminal: 500VAC, 1 minute
Between enclosure and FE terminal: 500VAC, 1 minute
Insulation resistance
Between live part and FE terminal: 10MΩ minimum
(at 500V DC megger)
Between enclosure and FE terminal: 10MΩ minimum
(at 500V DC megger)
Noise immunity
(Noise simulator)
DC power terminals: ±1.0 kV, 50 ns to 1 µs
I/O terminals: ±2.0 kV, 50 ns to 1 µs (with coupling adapter)

PRODUCT SPECIFICATIONS
2-3
Chapter 2
Inrush current
25A maximum
Affect of improper power
supply connection
Reverse polarity: No operation, no damage
Improper voltage: Permanent damage may occur
Note1. Time to shut OFF safety outputs after safety inputs are turned OFF or input monitor error
is detected (in case of OFF-delay timer is 0s). If the timer value except 0s, add the
selected OFF-delay time to this reaction time.
Note2. Time to shut OFF safety outputs after error (except input monitor error) is detected, or
configuration change is detected. This reaction time does not depend on OFF-delay
timer value.
Note3. Time to turn ON safety outputs after safety inputs are turned ON (in case of auto start).
In case of manual start, it means time turn ON safety outputs after start input is turned
ON. In case of control start, it means time to turn ON safety outputs after start input
transits from ON to OFF.
Note4. Time to change to Run state after power ON.

PRODUCT SPECIFICATIONS
2-4
Dimensions
Detail of locking ring
Locking ring

PRODUCT SPECIFICATIONS
2-5
Chapter 2
Applicable standards
Standard
Title
IEC 61508 Part1-7
: 2010
Functional safety of electrical/electronic/programmable electronic
safety-related systems
EN ISO 13849-1
: 2015
Safety of machinery -- Safety-related parts of control systems -- Part 1:
General principles for design
IEC 62061
: 2005/A2: 2015
EN 62061
: 2005/A2: 2015
Safety of machinery - Functional safety of safety-related electrical,
electronic and programmable electronic control systems
IEC 61496-1
: 2012
EN 61496-1
: 2013
Safety of machinery - Electro-sensitive protective equipment - Part 1:
General requirements and tests
EN 61131-2
: 2007
Programmable controllers Part 2: Equipment requirements and tests
IEC/EN 61000-6-2
: 2005
Electromagnetic compatibility (EMC) –Part 6-2: Generic standards –
Immunity for industrial environments
IEC 61000-6-4
: 2006/A1:2010
EN 61000-6-4
: 2007/A1:2011
Electromagnetic compatibility (EMC) –Part 6-4: Generic emission
standards –Residential, commercial, and light industry
IEC/EN 61326-3-1
: 2017
Electrical equipment for measurement, control and laboratory use -
EMC requirements - Part 3-1: Immunity requirements for safety-related
systems and for equipment intended to perform safety-related functions
(functional safety) - General industrial applications
ISO13851
: 2002
Safety of machinery -- Two-hand control devices -- Functional aspects
and design principles
UL 508
Industrial control equipment
CSA C22.2 No.142
Process control equipment

PRODUCT SPECIFICATIONS
2-6
Safety performance
In the case of using safety outputs as dual channel outputs, SafetyOne can be used in a system
for control category B to 4 and performance level a to e in accordance with EN ISO13849-1.
In the case of using safety outputs as single channel outputs, SafetyOne can be used in a
system for control category B to 3 and performance level a to d in accordance with EN
ISO13849-1.
Average probability of failure on demand (PFD) and Probability of a dangerous failure
per hour (PFH)
・In the case of using safety outputs as dual channel outputs
The following table describes PFD and PFH in the case of dual channel outputs. They are
needed for calculation of safety integrity level (SIL) which is applied to a system with SafetyOne.
In this case SafetyOne can be used in a system for SIL 1 to 3 in accordance with IEC61508.
Proof test interval lNote
Average Probability of Failure
on Demand (PFD)
Probability of a dangerous Failure per
Hour (PFH)
6 months
< 2.1 x 10-5
< 7.1 x 10-9
1 year
< 3.6 x 10-5
2 years
< 6.7 x 10-5
5 years
< 1.6 x 10-4 (SIL2)
10 years
< 3.2 x 10-4 (SIL2)
In this case SafetyOne can be used in a system for SIL 1 to 3 in accordance with IEC/EN62061.
Proof test interval Note
Probability of a dangerous Failure per Hour (PFH)
10 years
< 1.4 x 10-8
・In the case of using safety outputs as single channel outputs
The following table describes PFD and PFH in the case of single channel outputs. They are
needed for calculation of safety integrity level (SIL) which is applied to a system with SafetyOne.
In this case SafetyOne can be used in a system for SIL 1 to 2 in accordance with IEC61508.
Proof test interval Note
Average Probability of Failure
on Demand (PFD)
Probability of a dangerous Failure per
Hour (PFH)
6 months
< 4.1 x 10-5
< 1.6 x 10-8
1 year
< 7.5 x 10-5
2 years
< 1.5 x 10-4
5 years
< 3.6 x 10-4
10 years
< 7.0 x 10-4
In this case SafetyOne can be used in a system for SIL 1 to 2 in accordance with IEC/EN62061.
Proof test interval Note
Probability of a dangerous Failure per Hour (PFH)
10 years
< 2.0 x 10-8
Note. Refer to Maintenance and Inspection in “APPENDIX” for proof test procedure.

PRODUCT SPECIFICATIONS
2-7
Chapter 2
Mean Time To dangerous Failure (MTTFd) and diagnostic coverage (DC)
・In the case of using safety outputs as dual channel outputs
The following table describes MTTFdand DC in the case of dual channel outputs. They are
needed for the calculation of Performance Level (PL) which is applied to a system with
SafetyOne. In this case SafetyOne can be used in a system for PL a to e in accordance with EN
ISO13849-1.
Mean time to dangerous failure (MTTFd)
Diagnostic Coverage (DC)
100 years
High
・In the case of using safety outputs as single channel outputs
The following table describes MTTFdand DC in the case of single channel outputs. They are
needed for the calculation of Performance Level (PL) which is applied to a system with
SafetyOne. In this case SafetyOne can be used in a system for PL a to d in accordance with EN
ISO13849-1.
Mean time to dangerous failure (MTTFd)
Diagnostic Coverage (DC)
100 years
Medium

PRODUCT SPECIFICATIONS
2-8
Safety input specifications
Drive terminal specifications (T0, T1, T2, T3, T4, T5, T6, T7, T10, T11, T12, T13, T14, T15)
Rated drive voltage
Power supply voltage
Minimum drive voltage
Power supply voltage –2.0V
Number of drive terminals
14
Maximum drive current
20mA per port (at 28.8V DC) Note1
Receive terminal specifications (X0, X1, X2, X3, X4, X5, X6, X7, X10, X11, X12, X13, X14, X15)
Rated input voltage
24V DC
Input ON voltage
15.0V DC to 28.8V DC
Input OFF voltage
Open or 0V DC to 5.0V DC
Number of receive terminals
14
Rated input current
10mA per port (at rated voltage)
Type of input
Sink type input (for PNP output), Type 1 (EN 61131-2)
Wiring specifications
Cable lengthNote2
100m maximum (total wiring length per 1 input)
Allowable wiring resistance
300Ω maximum
Note1. The drive port generates check pulses in order to diagnose input devices and internal
circuits. (Wiring and the diagnostic function are different depending on the logic
selected. See “Chapter 5 LOGIC” for details. But the basic function is same.)
Note2. For cables longer than 30m between SafetyOne and connected devices, or wiring drive
terminals and receive terminals separately, use grounded shielded cables to assure
electromagnetic compatibility.
Note3. In the common connection of several interlock switches, applicable safety performance
depends on result of risk assessment for whole of the safety configuration. Refer to
ISO14119 for analysis the connection.
Safety input equivalent circuit Safety input operating range
Xn
I n t e r n a l C i r c u i t
2.2kΩ
V-
Voltage(V)
Current
(mA)
28.8
24
15
5
1
6
10
12
ON area
Transition area
OFF area
Table of contents
Other IDEC Controllers manuals
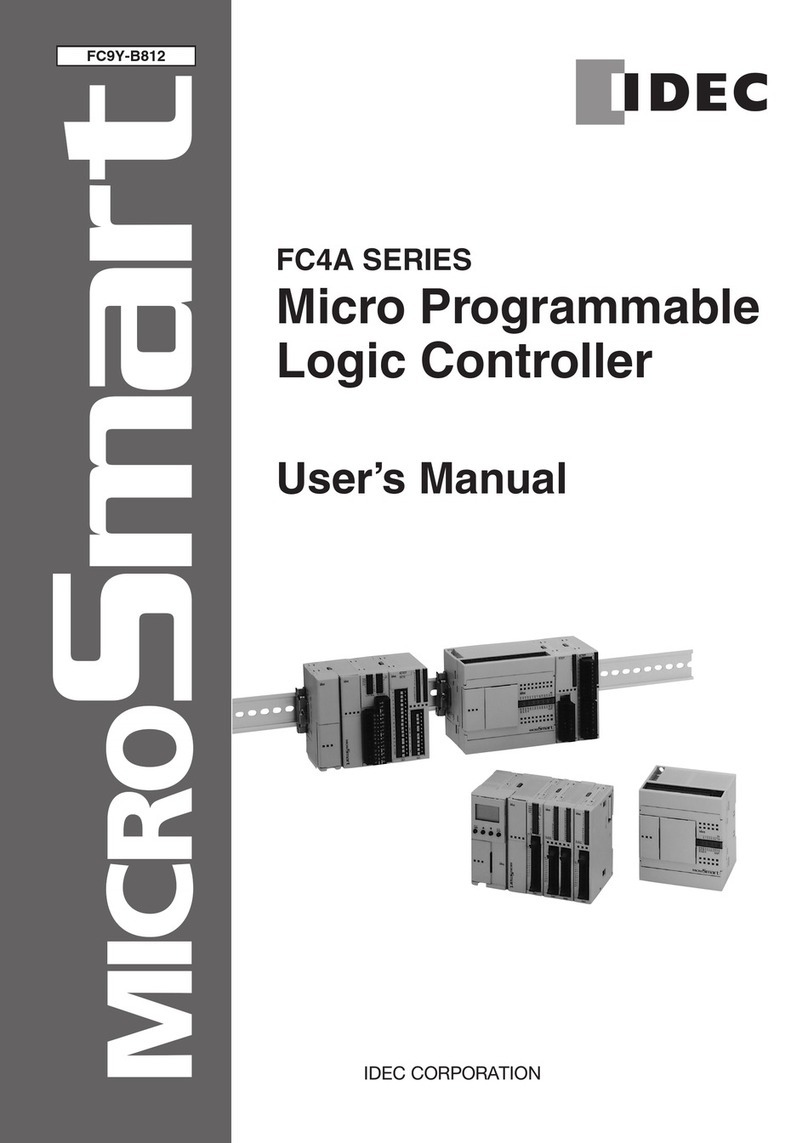
IDEC
IDEC FC4A-C10R2 User manual
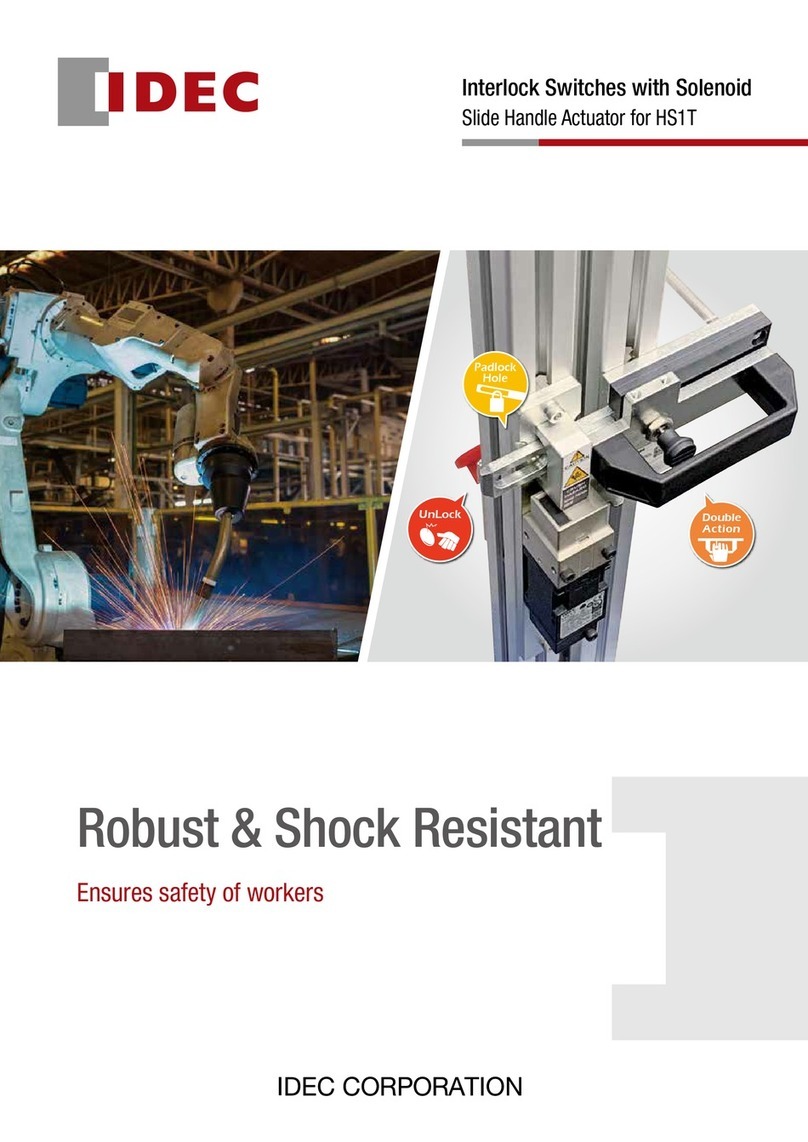
IDEC
IDEC HS9Z-FL54 User manual
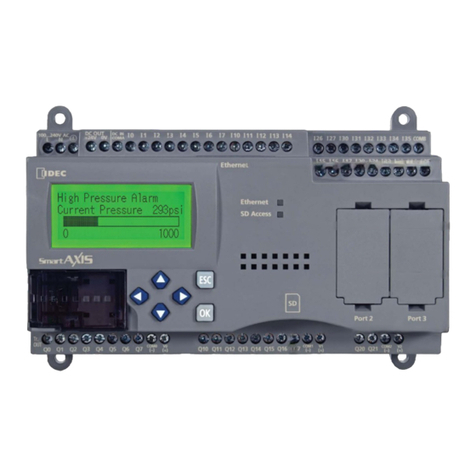
IDEC
IDEC SmartAXIS Touch FT1A Series User manual
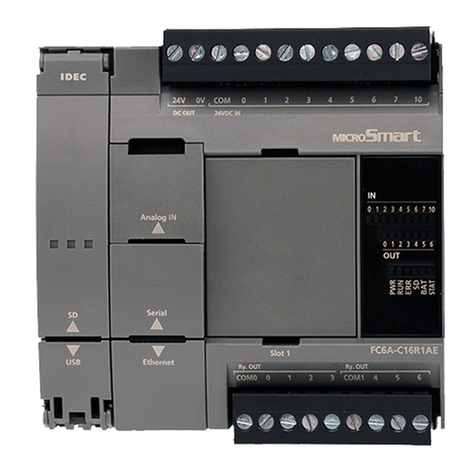
IDEC
IDEC MICROSmart FC6A Series Owner's manual
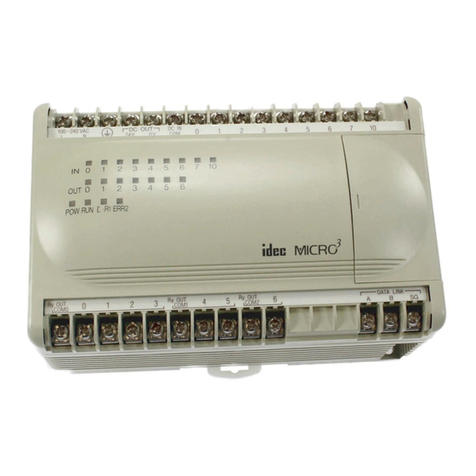
IDEC
IDEC MICRO3 User manual
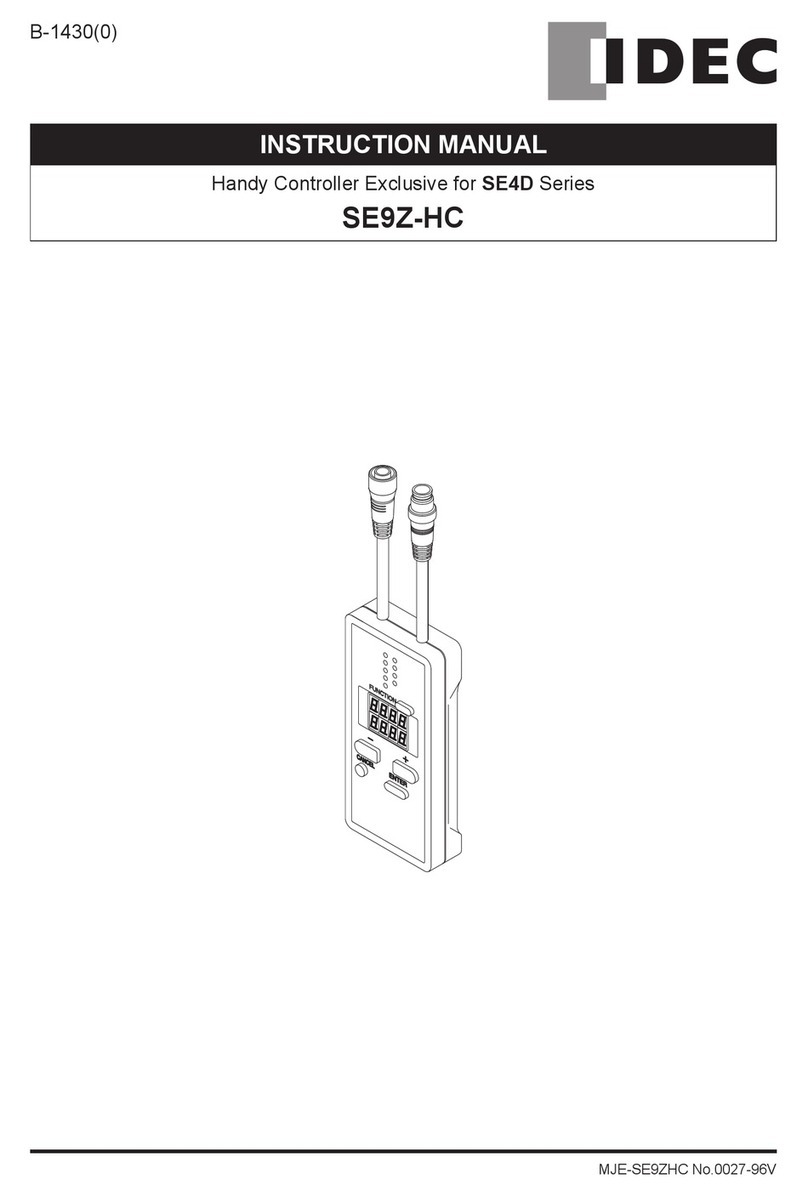
IDEC
IDEC SE9Z-HC User manual
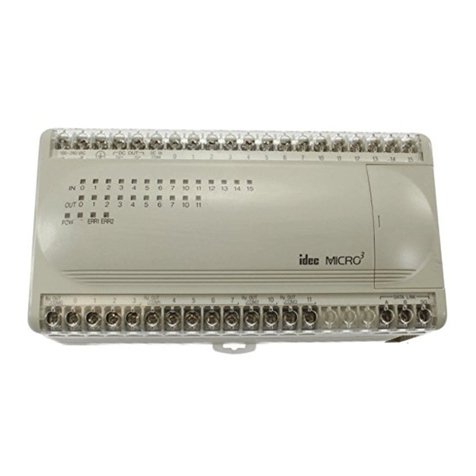
IDEC
IDEC MICRO3C User manual
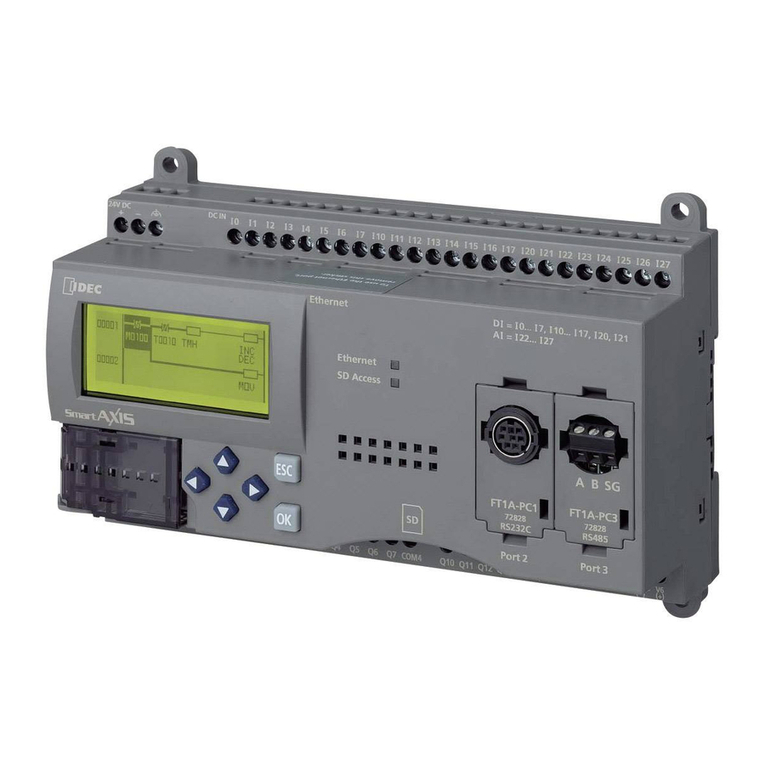
IDEC
IDEC SmartAXIS Touch FT1A Series User manual
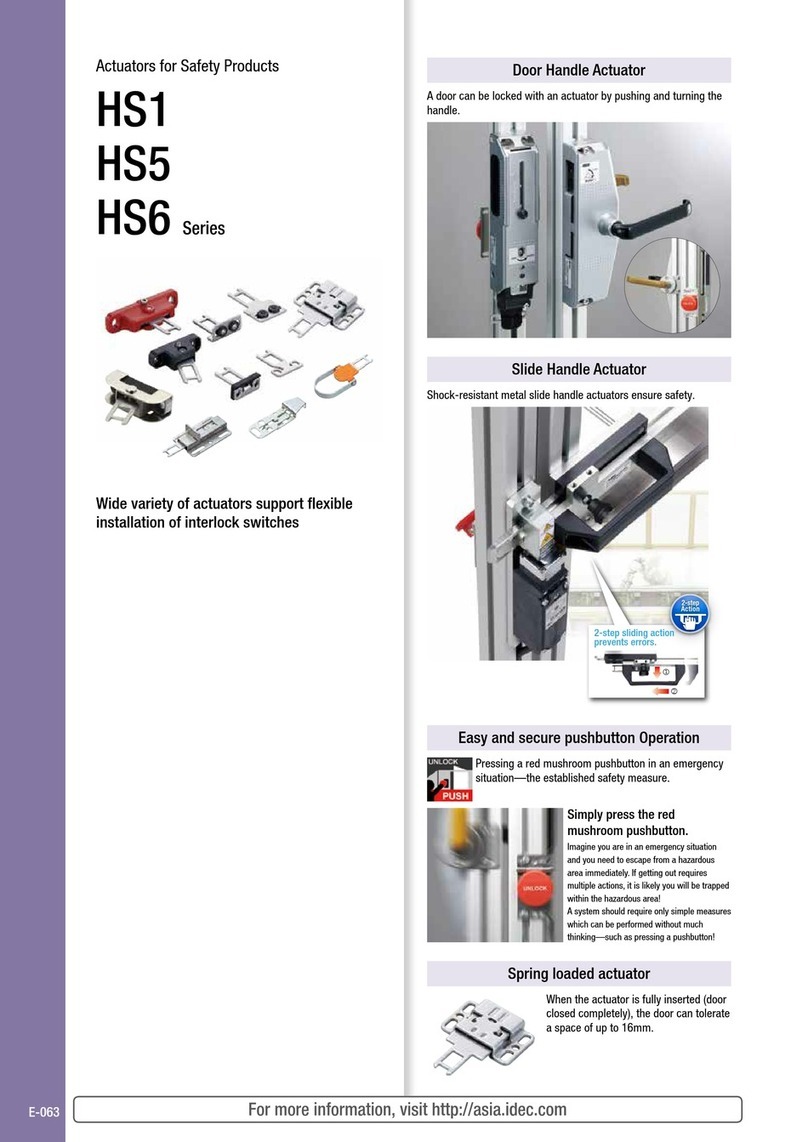
IDEC
IDEC HS1 Series User manual
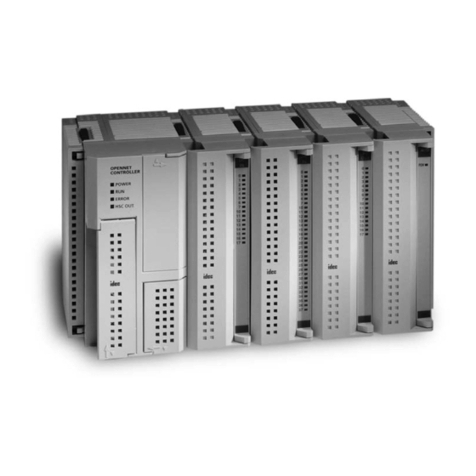
IDEC
IDEC OpenNet series User manual