Innovati Bipedinno User manual

Bipedinno
12-DOF Waist-high Robot
Instruction Manual
Version 1.18

i
Trademark
Innovati®, , and BASIC Commander®, are registered trademarks of Innovati Inc. InnoBASIC™and cmdBUS™
are trademarks of Innovati Inc.
Copyright ©2008-2009 by Innovati Inc. All rights reserved.
In view of unceasing improvement of products, this document and the product mentioned in this document are
subject to be changed by the company without notice. It is forbidden to reproduce and distribute any part or all of
the contents of the product without the written approval or authorization by the company.
Disclaimer
The user shall undertake all the risks in the applications where this product is used. The company shall not be liable
for any direct, indirect or consequential damages due to the use of the product including but not limited to the loss
of equipment, the loss of human safety and health and the loss of profit and reputation. The product of the company
shall not be used in life saving or any related instrument and equipment. Children under 14 shall not use this
product for any related experiment without being accompanied by adults.
Errata
We hope the users may regard this document as a lively and practical instruction manual. We have put tremendous
efforts in making this instruction manual complete and correct; however, there may be unavoidable missing parts or
errors. With a view to providing the user updated and complete information in the instruction manual, we keep
improving and supplement the contents of this instruction manual. If you find any error in this manual, please
contact us via the e-mail [email protected]. Any related update information will be disclosed on our
website. Please visit our website http://www.innovati.com.tw for more updated information.

ii
Precautions
This kit comprises 2 modules, BASIC Commander®and Servo Runner A, each with respective
instructions for use and functions. Please refer to these for optimal effects.
When installing BASIC Commander®to the Command Board, make sure the input voltage is within
the 6-12V range, otherwise the module may burn.
The input voltage to the Servo Runner A must correspond to the voltage rating of the servo. Servos
provided in this kit are rated 4.8-6V; over or under voltage may cause unpredictable results, even
burning of the motor. Make absolutely sure of the correct voltage before connecting the power
supply.
The kit provides a total of 12 servos. When operated simultaneously, they consume a large current;
make sure the power supply or battery connecting to Servo Runner A is capable of providing 8A of
current, so as to properly operate the kit. Insufficient current may cause unexpected results and
damage of the kit.
When using a battery power supply to the module, the voltage may lower after some while of
operation and cause abnormal actions of the kit. In such case, remove and fully charge the battery
before using again. If prolonged testing and operation is required, we suggest you use a power
supply unit to ensure uniform performance.
Prior to assembling the kit, install InnoBASIC™Workshop as per the content of the CD; also
make sure that the PC communicates with BASIC Commander®via a USB cable connection, so
that the entire assembly can be accomplished.

iii
Table of Contents
Part List........................................................................................................................................................1
Tools ..............................................................................................................................................................4
Assembly Procedure....................................................................................................................................5
Calibration Servos ....................................................................................................................................................5
Assemble the Leg Frames.......................................................................................................................................10
Connecting Top Board with Module......................................................................................................................16
Fine-Tuning Initial value of Servo............................................................................................................21
Structure fine-tuning...............................................................................................................................................21
Software fine-tuning...............................................................................................................................................21
Perform Demonstrative Motions..............................................................................................................27

1
Part List
Item Illustration Qt’y Specifications and instructions
Assembly Kit Parts
Main Board for
installing module
1
PC installation board for linking robot
electronic modules with its leg parts;
provides versatile layout of module or
power supply accessories.
Top Board for
installing module
1
PC board for installing electronic
module of the robot and connecting
with the main board; provides
versatile layout of modules.
Aluminum Foot
Bracket
2 For connecting with the Ankel Servo
Bracket.
Aluminum Servo
Bracket
12
For accommodating and fixing servo;
lock holes are provided for connecting
with another Servo Bracket or
U-shape Bracket.
Aluminum
U-shape Bracket,
27mm
4
Provides connection with the Servo
Bracket and movement space of the
Servo; it also provides connection
with two U-shape Brackets for
different applications.
Aluminum
U-shape Bracket,
22mm
8
Provides connection with the Servo
Bracket and movement space of the
Servo; it also provides connection
with two U-shape Brackets for
different applications.

2
Servo
12
Servo provides for 180°rotation
moves capable of simulating
articulation behaviors; connections
with signal, power and ground are
required for the operation. Pay
attention to wire polarity. Avoid
having the servo sustained to a same
movement for a long period of time, to
prevent wearing the motor.
Dimensions (LxWxH):
40.6mmx20.0mmx42.8mm
Weight: 73 g, Speed: 0.33 sec/60°
Torque: 7.4 kg/cm
Screw A
48 ISOT 3 x 8 mm
Screw B 10 ISOP 3 x 6 mm
Screw C
20 ISOP 3 x 10 mm
Screw D 32 ISOP 2 x 5 mm
Screw E 40 TP1P 2 x 6 mm
Screw F 8 TP1P 2 x 8 mm
Screw G 4 ISOF 3 x 6 mm
Screw H 8 ISOF 2 x 5 mm
Nut A 90 3 x 5 mm
Nut B 32 2 x 4 mm
Washer A 72 3 x 0.4 x 8 mm
Washer B 12 3 x 1 x 6 mm
Bearing
12 3 x 4 x 8 x 9.5 mm

3
Hex post, copper
4 30 mm
Module Kits
BC1
1 Innovati®BASIC Commander®,
capable of storing programs and
controlling operations of modules
Servo Runner A
1 Innovati®Servo Runner A, for
controlling individual servos.
Command Board
1 Used for installing BC1, with spare
cmdBUS™allowing user to connect
with Innovati®modules.
Servo Power Line
1 Cable for connecting Servo Runner A
with Power Supply Unit.
Command Board
Power Line
1 Cable for connecting Command Board
with Servo Runner A’s Power Supply.
cmdBUS™
1 Signal cable for connecting Command
Board with Servo Runner A.
Servo Extension
Cable
4
Extends controlling signal cable of the
Servo, so that the user may perform
Servo control with a larger range or
longer distance.

4
USB cable
1
Links BC1 with PC, allowing
downloading of PC program to BC1,
or performing communication in
Debug Mode.
Cable Strap
12
Used for fixing wires, so that they do
not tangle or affect motions
unexpectedly during the operation of
the Servo.
i. Tools
Cross Screwdriver (2mm and 3 mm).
Long Nose Pliers
Screw Glue (selectively used between nut and Bracket joints, to prevent the nut from
loosening.)

5
ii. Assembly Procedures
Calibrating Servos
Before starting installation, verify if the servo horn is at the correct position; if not,
calibrate as follows:
Connect servo, Servo Runner A, Command Board, and power supply cable in
the sequence as illustrated below.
When the Command Board or Education Board shares the power supply with
Servo Runner A, please notice that the voltage of this kit should be 6V (please refer to
Notices). It is recommended to use a voltage regulator to ensure that the voltage is
within the safe range.
i. Connect the PC and BASIC Commander®with a USB cable.
ii. Make sure that the DIP switch on the Command Board is set at the 0 position
(power off state). If it is not at the 0 position, please poke it to the 0 position.
iii. Connect the power line of the servo to the power supply. (Please make sure that the
voltage and current from the power supply are within the ranges required by the
servo. After the power line is connected, the servo may make a transient motion due
to receiving a switch surge; this is normal. While connecting the power line, please
pay attention not to place your hands within the space where the servo may move to
avoid being clamped.)
Connect to power with Servo Power Line. Mind the
polarity. Connect “+” to the positive and “-” to the
negative of the power supply.
Connect to Command Board with Education Board Power
Line. Make sure to connect “+” to the positive and “-” to
the ne
g
ative of the
p
ower su
pp
l
y
.
Connect all servos with
Servo Runner, as shown in
the Fig. Pay attention to the
pin position while making
the connection.
Connect to Command Board with
cmbBus, and install BC1 to Command
Board. Make sure the Power Switch on
the Command Board is set to “0” (off).

6
iv. Start the InnoBASIC™Workshop
v. Click the “Tools” item in the menu bar on the top.
vi. Click the “Motion Editor” in the pull-down menu (If a warning window appears, it
means that the BASIC Commander®is not correctly connected. Please check if the
USB cable is connected or unplug and then plug it again to ensure a correct
connection. Exit the Motion Editor and then re-click this button.)
vii. If the connection is correct, the message “Downloading servo manager...” will be
displayed on the PC screen meaning that the program is being downloaded. Please
poke the DIPswitch on the Command Board to the 1 position and wait a moment.
viii. After the downloading is complete, a notification window will appear. Please make
sure that each servo has been connected correctly. After confirming all the
connections, please click “OK”. (If “Cancel” is clicked, the Motion Editor will be
closed. If there is any component is incorrectly connected at this moment, please
click “Cancel” to terminate the program.)
Click the application in the InnoBASIC™Workshop
folder to start the InnoBASIC™Workshop.
After clicking each item, a pull-down menu with
more function items will be displayed. Please click
the “Tools" item now.
Click “Motion Editor” to start the Motion Editor.
If this message appears, it means that the USB
cable is not connected correctly.
The message means that the program is being
downloaded. Please do not remove the
USB cable
.

7
ix. Please pay attention not to place your hands within the space where the servos may
move into to avoid being clamped. Please check the checkbox for activating the
servos on the left side to move all the servos to their central points. Please note that
the number next to it should be 1500. If it is not 1500, please click the number
directly, enter the number 1500 and then click “Enter”.
Check if the disks of all servos are at correct position; in case of any deviation,
remove the central screw and pull off the disk, adjust it to the correct angle and
re-lock.
While making the assembly, before fixing the disk, make sure the disk is
maintained at the correct angle. In case the disk is moved, follow this procedure
to adjust it, to prevent from any unexpected movement or damage of the parts.
The message appears for notifying the download is complete. Please
make sure that each component has been connected correctly.
There are 4 sets of 3 holes
on the disk of the servo.
Verify if the central hole is
on the top of the disk in a
right angle, as shown in the
figure.
If the hole is in an incorrect position,
loosen this screw and pull up the disk;
adjust the disk to the correct position
and refit the disk and replace the
screw.

8
Installing the bearing (For reference only. Please do not
assemble it first.)
Fixing the servo (For reference only. Please do not assemble it
first.)
Bearing fixed on
U-shape Bracket
Nut A Washer B Screw C
While connecting the Servo Bracket and
the U-shape Bracket, the bearing should
be used for the joints with the same fixing
methods. Pass the Screw C from outside
towards the inside through the bearing
mounted on the U-shape Bracket, then the
Washer B and the Servo Bracket. Finally,
fix it with the Nut A at the inner side of
the Servo Bracket.
Servo is fixed on the Servo Plate with Screw A passing through
Washer A and the square hole on the motor, tightened with Nut
A from the lower side of Servo Plate.
After fixing servo, fix U-shape Bracket to secervo horn with
Screw E. Make sure the disk is not disturbed.
Washer A Screw A
Screw A
U-shape Bracket
Servo Plate

9
A. Assemble the leg frames
i. Assemble the Right Leg Frame
Part F: Fix the Foot Bracket to the 27mm U-shape Bracket with Screw
G and Nut A. Make sure the screw points upwards.
Part E: Align two Servo Brackets as shown;
fix them with Screw D and Nut B.
Part D: Place two 22mm U-shape Brackets
back to back as shown, fix them with Screw B
and Nut A.Add bearings to each U-shape
Bracket on the same side.
Part C: Place 22mm U-shape Bracket
together with Servo Bracket as shown, fix
them with Screw D and Nut B.
Part B: Place 27mm U-shape Bracket
together with Servo Bracket as shown, fix
them with Screw D and Nut B.
Part A: Align two Servo Brackets and fix
them with Screw D and Nut B.

10
Using Part D as the
connect its lower s
Part E with a beari
its upper side to Par
with another bearin
that a Servo Brack
the bottom and a 22
U-shape Bracket at
top, as shown.
center,
ide to
ng, then
t C
g, so
et is at
mm
the
Connect Part B above with
with a
wo
re
ch
m
n the
Part C and fix them
bearing; now that t
U-shape Brackets a
perpendicular to ea
other, with the 27m
U-shape Bracket o
top.
Connect Part A on top of
Part B and fix them with a
bearing. The upper-most
part is Servo Bracket of
Part A. Note the positions
of fixing holes on both Part
A and Part B.
Finally fix the lowest Se
Leg Frame is complete. C
structure in the illustratio
rvo Plate to Part F with a bearing and the Right
heck if the Right Leg Frame conforms to the
n.

11
ii. Assemble Left Leg Frame
Part A: Align two Server Plates
as shown; fix them with Screw
D and Nut B.
Part B: Place the 27mm
U-shape Bracket together with
Servo Plate as shown; fix them
with Screw D and Nut B.
Part C: Place the 22mm
U-shape Bracket together with
Servo Plate as shown; fix them
with Screw D and Nut B.
Part D: Place two 22mm
U-shape Brackets back to back
as shown and fix them with
Screw B and Nut A. Place
bearings on the U-shape
Brackets on the same side.
Part E: Align two Servo Plates
as shown; fix them with Screw D
and Nut B.
Part F: Fix the Foot Bracket with 27mm U-shape Bracket with Screw G and
Nut A. Make sure the screw points upwards.

12
Connect Part A on top of Part B
and fix them with a bearing.
The upper-most part is Servo
Plate of Part A. Note the
positions of fixing holes on
both Part A and Part B.
Using Part D as the
center, connect its
lower side to Part E
with a bearing, then its
upper side to Part C
with another bearing,
so that a Servo Plate is
at the bottom and a
22mm U-pate at the top
as shown.
Connect Part B above
Part C and fix them with
a bearing; now that two
U-shape Brackets are
perpendicular to each
other, with the 27mm
U-shape Bracket on the
top.
Finally fix the lowest Servo Plate to Part F with a bearing and the
Left Leg Frame is complete. Check if the Left Leg Frame conforms
to the structure in the illustration.

13
Confirmation of the Right Leg Frame
Confirmation of the Left Leg Frame

14
iii. Connecting the Left and Right Legs
Place two 22mm U-shape Brackets back to back as shown. Then,
fix them with Screw B and NutA and add bearings to each
U-shape Bracket on the same side.
Connect the bearing to the Servo Bracket on
top of leg frames.
Right Leg Frame
Left Leg Frame

15
B. Connecting Top Board with Module
i. Assemble Top Board with Command Board
Insert Screw C into 4 holes of Command Board and fix them with
Nut Afrom below as illustrated.
Pass 4 screws through Top Board. Add a NutA on each of the protruding
screws under the Top Board; after turning them up with hand, secure them with
long nose pliers.

16
ii. Assemble Main Board with Servo Runner A
Insert Screw C into 4 holes of Servo RunnerA and fix
them with Nut A, in the direction as illustrated.
Pass the 4 screws through Top Board.Add a Nut A on each of
the protruding screws under the Top Board; after turning them
up with hand, secure them with pointed pliers.
Table of contents
Other Innovati Robotics manuals
Popular Robotics manuals by other brands
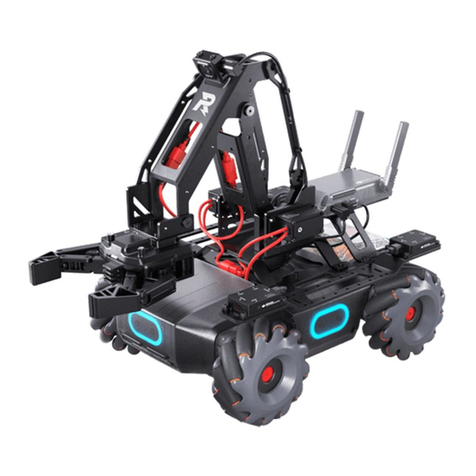
dji
dji RoboMaster EP Disclaimer and safety guidelines

Mitsubishi Electric
Mitsubishi Electric MELFA FR CR800 Series user manual
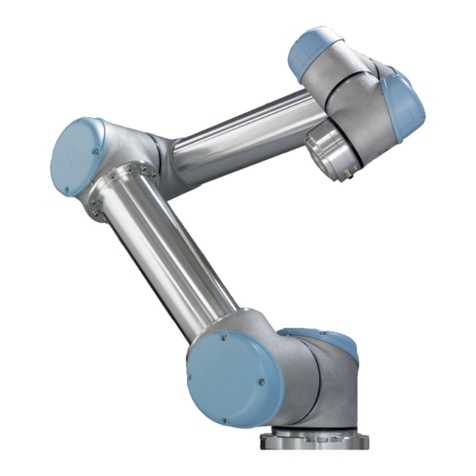
Universal Robots
Universal Robots UR-6-85-5-A user manual
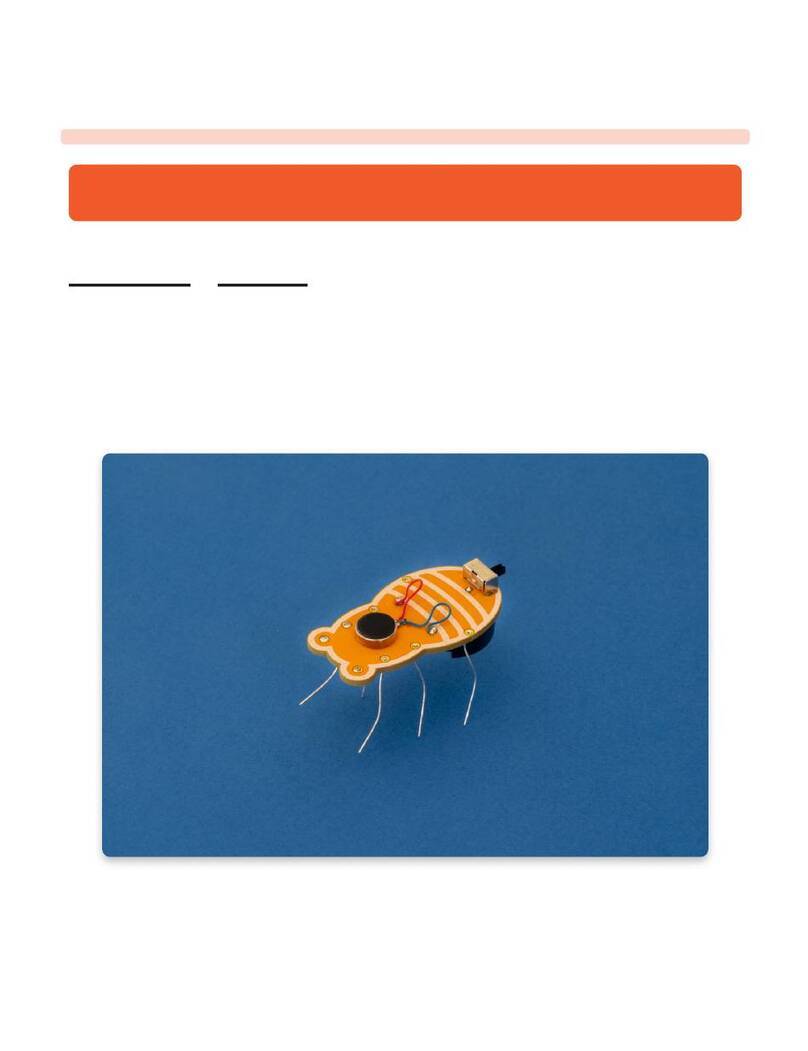
Circuitmess
Circuitmess MR. BEE The Wacky Robot Build guide
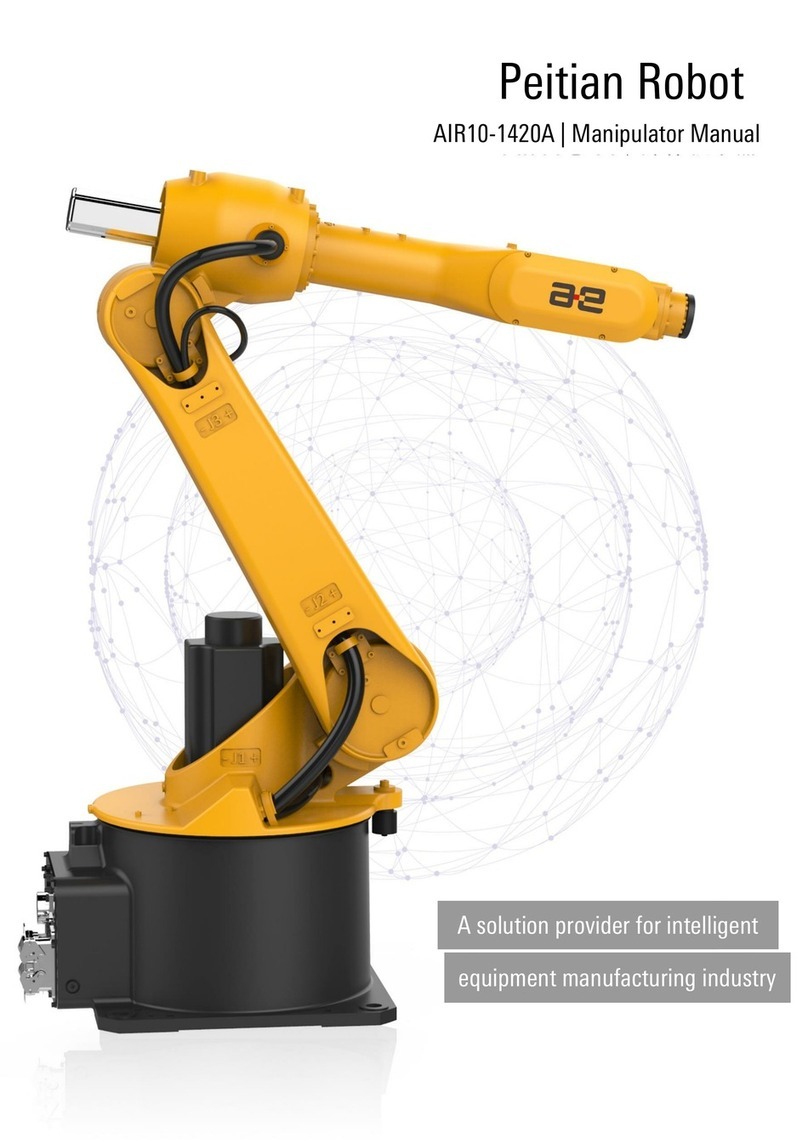
PEITIAN ROBOTICS
PEITIAN ROBOTICS AIR10-1420A MANIPULATOR MANUAL
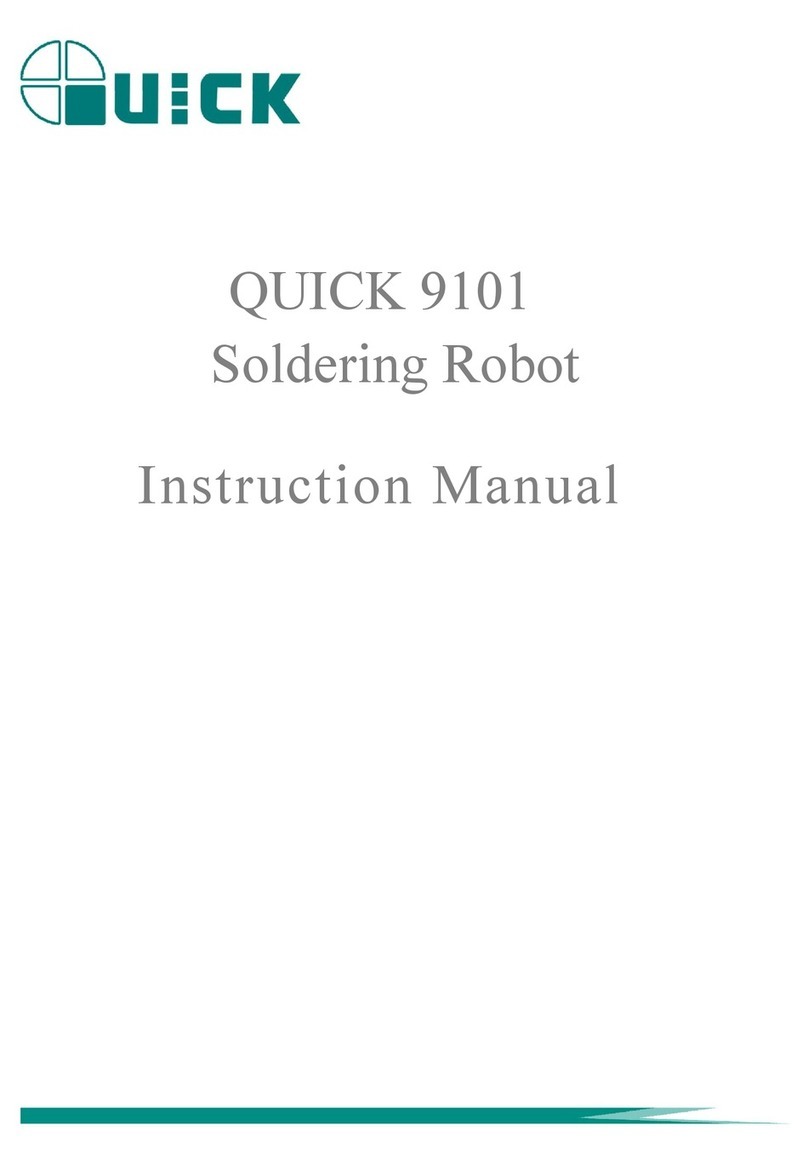
Quick
Quick 9101 instruction manual
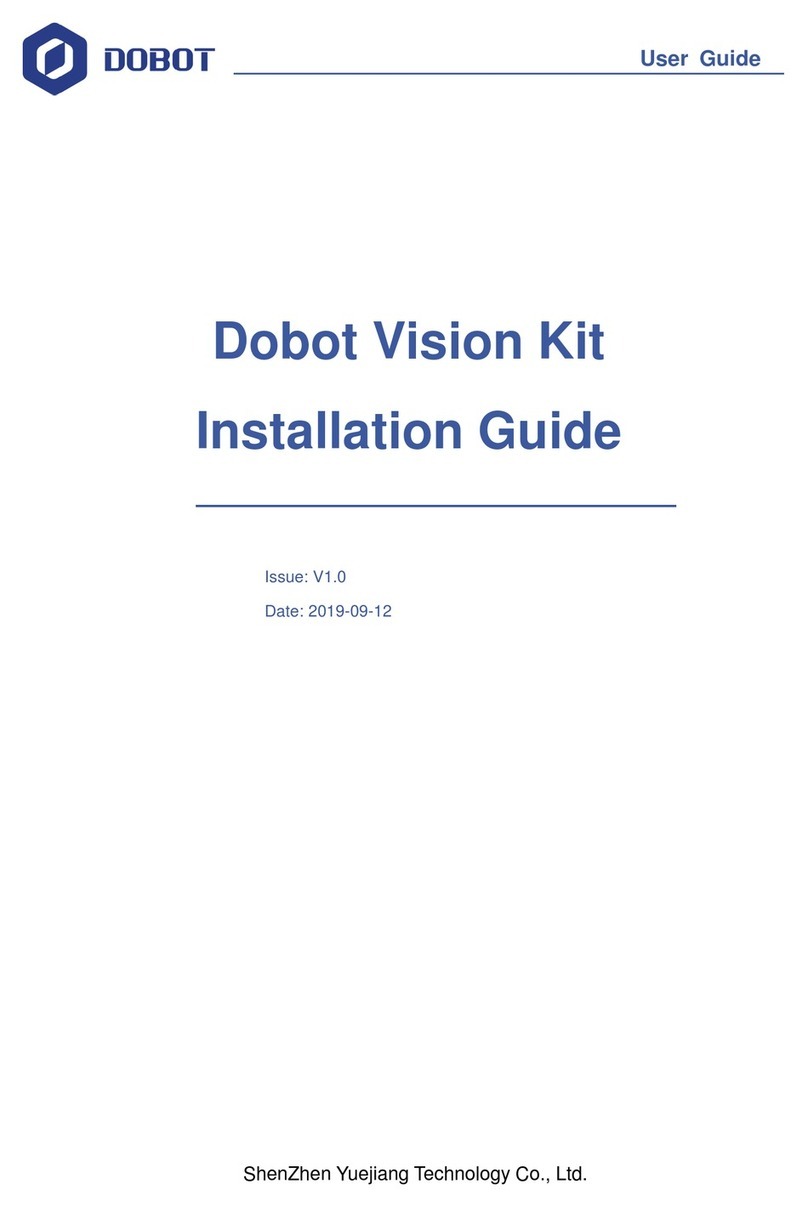
ShenZhen Yuejiang Technology
ShenZhen Yuejiang Technology Dobot Vision Kit installation guide

OSOYOO
OSOYOO Omni-wheel manual
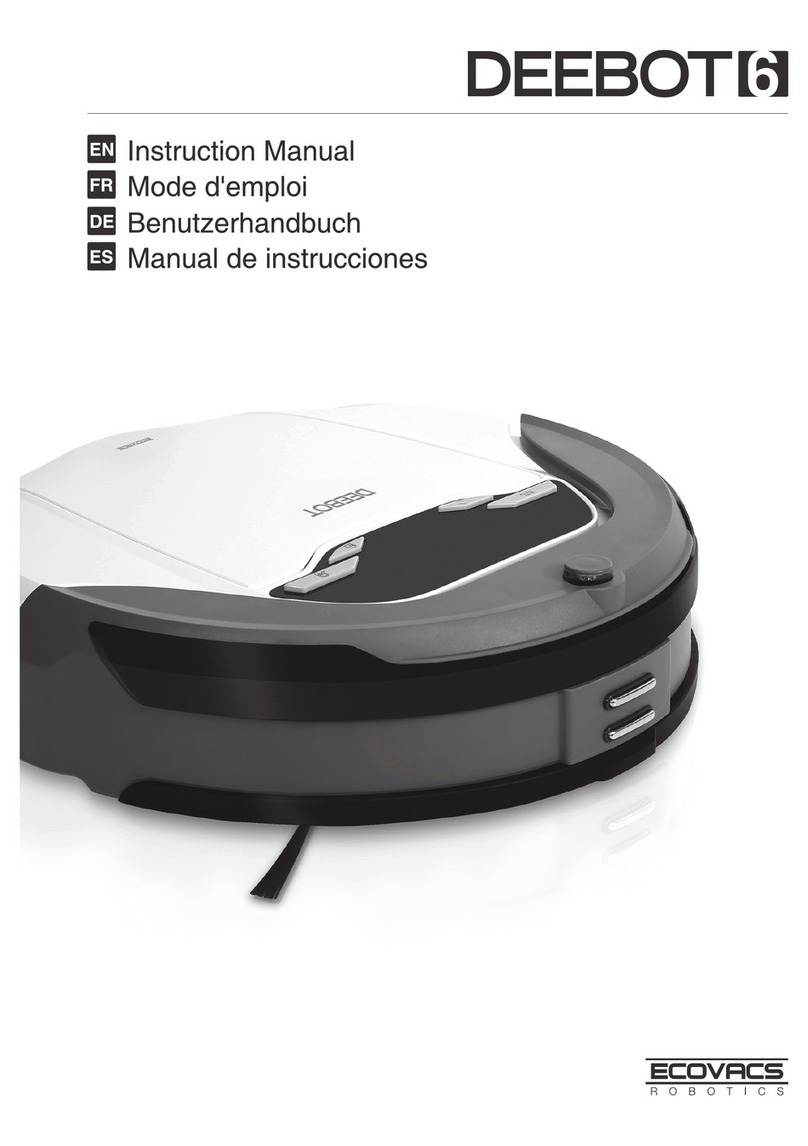
ECOVACS
ECOVACS Deebot 6 instruction manual
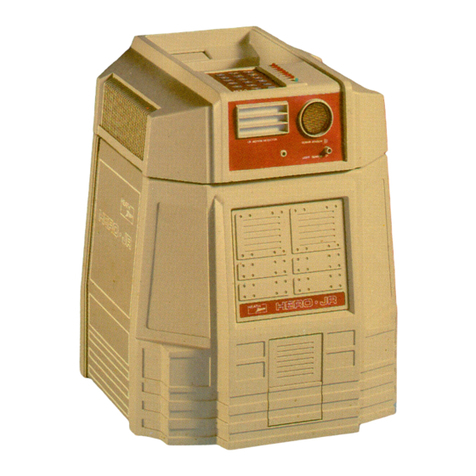
Heath Zenith
Heath Zenith Hero Jr RT-1 owner's guide
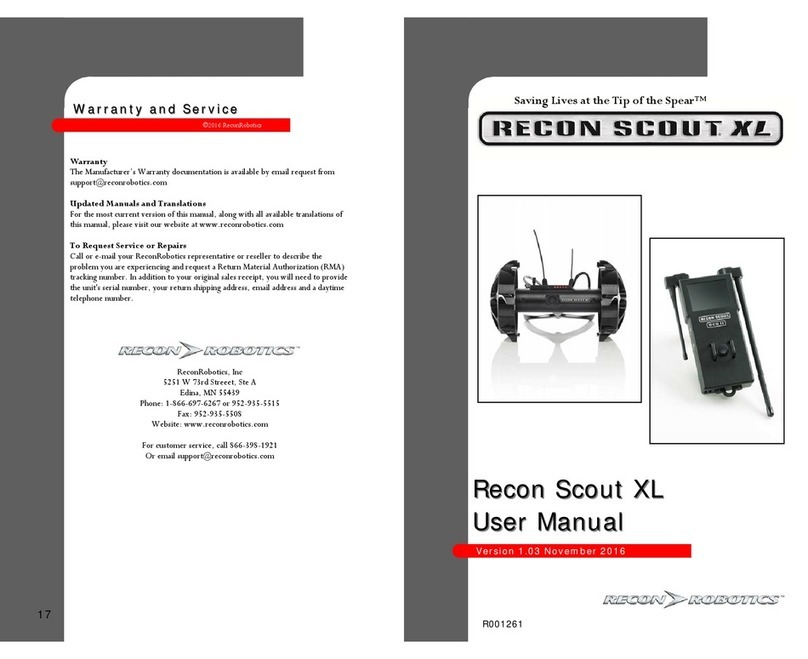
ReconRobotics
ReconRobotics Scout XL user manual

Pro's Kit
Pro's Kit GYROSCOPE kit Assembly & instruction manual