IPR TK Series User manual

Assembly Instructions
Tool Changer TK-45
WZW_TK-45_V2.0 1
Tool Changer
ISO TK Series
TK-45
Version 2.0 last revision July 2019
Dear customer,
Thank you for the confidence that you have placed in our
company by purchasing an IPR tool changer.
Every tool changer is fully assembled in the plant and is subject
to an individual test. This includes examining their complete
proper functioning and safe working.
These instructions illustrate how the tool changer is set up and
operates. In addition, all the main details for assembly,
commissioning and maintenance are clearly arranged.
Please carefully read through the contents.
Do directly contact us if any of your questions are not answered
in these instructions. We are at the following address.
IPR – Intelligente Peripherien für Roboter GmbH
Jakob-Dieffenbacher-Str. 4/2
75031 Eppingen
Germany
Phone: +49 (0) 7262 9239-100
Fax: +49 (0) 7262 9239-400
E-Mail: service@iprworldwide.com
Internet: www.iprworldwide.com
© IPR – Intelligente Peripherien für Roboter GmbH 2019
Translation of Original Assembly Instructions
Table of contents
1.
General 2
1.1.
Information on these instructions 2
1.2.
Terms of the guarantee 2
2.
Safety 2
2.1.
Symbol explanations 2
2.2.
Intended use 2
2.3.
Inappropriate use 2
2.4.
General risks 2
2.5.
Owner obligations 2
2.6.
Requirements placed on the personnel 3
3.
Specifications 3
3.1.
General basic data 3
3.2.
Operating conditions 3
4.
Setup and function 3
4.1.
Overview 3
4.2.
Brief description 3
5.
Transport, packing, storage 3
5.1.
Transport 3
5.2.
Packing 4
5.3.
Storage 4
5.4.
Repairs 4
6.
Assembly and commissioning 4
6.1.
Assembly 4
6.2.
Commissioning 4
7.
Malfunctions 4
8.
Maintenance and repairs 4
8.1.
Cleaning and upkeep 4
8.2.
Maintenance 4
9.
Dismantling, decommissioning, disposal 4
9.1.
Dismantling 5
9.2.
Decommissioning 5
9.3.
Disposal 5
10.
Accessories 5

Assembly Instructions
Tool Changer TK-45
WZW_TK-45_V2.0 2
1.
0B
General
1.1.
10B
Information on these instructions
These instructions enable the tool changer to be safely and
effectively handled. These instructions form part of the machine
and should be kept close to it so that the personnel responsible
can easily access them.
The personnel involved must have carefully read through these
instructions and understood them before beginning any work.
Keeping to all the safety and handling pointers in these
instructions is the basis on which work is done safely.
Also applying are any local health & safety regulations and the
general safety conditions where the machine is used.
Illustrations in these instructions are there to assist in basic
understanding; they may deviate somewhat from the actual
design.
Also follow the generally valid, statutory and other binding
regulations of European and national legislation as well as the
accident prevention and environmental protection provisions in
force in your country.
1.2.
11B
Terms of the guarantee
The terms of the guarantee can be found in the manufacturer's
general terms & conditions of business. Please turn to our
Customer Service (for contact data see cover) if any matters are
not clear.
2.
1B
Safety
This section provides an overview on all the important safety
aspects for the protecting people and for reliable, no-trouble
operations. Further task-related safety instructions are included
in the sections on the individual service life phases.
2.1.
12B
Symbol explanations
Safety instructions are identified by symbols in these instructions.
The safety instructions are introduced by signalling words
expressing the degree of hazard involved.
CAUTION!
Points to a possible dangerous situation which - if
not avoided - may result in either minor or slight
injuries.
NOTE!
Points to a
T
possible
T
dangerous situation which - if
not avoided - may result in either material or
ecological damage.
This symbol brings useful tips and
recommendations to one's notice as well as
information on efficient, no-trouble operations.
2.2.
13B
Intended use
The TK tool changer system is solely for automatically and
pneumatically changing robot tools. It consists of a tool side and
a robot side. The tool side (T) is fitted at the tool and the robot
side (R) to the fixture flange of the robot.
Tool changers are not ready-to-use machines as envisaged
under the EU Machinery Directive. Tool changers are solely for
attaching to machinery and equipment.
Do also follow their documentation.
NOTE!
You must use this tool changer exclusively in
accordance with the operating conditions and
performance specifications established in theses
instructions.
2.3.
14B
Inappropriate use
Any other use or one going beyond that described in the
"Intended Use" chapter is deemed to be inappropriate and will
void all warranty or guarantee claims.
It is the owner - and not the manufacturer - who accepts liability
for damage resulting from this.
NOTE!
The tool changer must not be used in any
explosive environment.
2.4.
15B
General risks
The tool changer was state-of-the-art manufactured at the time of
delivery. Even so, dangers could still proceed from it if the safety
information listed here in these instructions is not followed.
The personnel involved must have carefully read through
these instructions and understood them before beginning
any work.
The instructions must always be available for all users
where the tool changer is deployed.
These instructions are also to accompany the tool changer
if it is handed over to third parties.
Do not delve into moving components or handle them
during on-going operations.
Never open protective covers under ongoing operations.
Only authorized specialist personnel - outside the danger
zone - are allowed to carry out any work such as assembly,
commissioning, operating, dismantling and maintenance.
Before any work is begun on the tool changer, the energy
supply needs to be disconnected and the line system
relieved of pressure. Secure the system against being
unintentionally reactivated for the duration of the work.
Ensure during commissioning that all pneumatic
connections are either allocated or firmly closed.
2.5.
16B
Owner obligations
Together with the safety instructions in these instructions, the
valid safety, accident prevention and environmental protection
regulations in force where the tool changer is used must be
adhered to.
As part of his obligation to exercise due car, the owner is to
ensure that:
The tool changer is used as intended
During the entire period of use of the tool changer a check
is to be made on whether his operating instructions comply
with the ongoing status of the standards & codes and, if
necessary, he is to adapt them.
The responsibilities for installation, operation, fault
rectification, maintenance and cleaning are clearly settled
and laid down.
All those dealing with the tool changer have both read these
instructions and understood them. In addition, he has to
regularly train the personnel involved and inform them as to
hazards/risks.

Assembly Instructions
Tool Changer TK-45
WZW_TK-45_V2.0 3
1
2
3
7
5
8
9
6
4
10
2.6.
17B
Requirements placed on the personnel
The variety of tasks described in these instructions place differing
requirements on the qualifications of those performing these
tasks.
Only appropriate specialist personnel or a duly instructed person
under the supervision of specialist personnel are allowed to carry
out any work such as assembly, commissioning, operating,
dismantling and maintenance.
In view of his technical training, knowledge, experience and
knowledge of the relevant standards and regulations, the
specialist is in a position to perform the work he has been
entrusted with and - on his own - to recognize/avoid any hazards.
3.
2B
Specifications
(Please refer to the ongoing catalogue or the internet for
specifications of the individual tool changers.)
3.1.
18B
General basic data
Min. operating pressure: 4,5 bar
Max. operating pressure: 8 bar
Temperature range: 5 °C to 80 °C (higher if requested)
Drive: Pneumatic with fail-safe spring
Material: Casing of high-strength aluminium hardcoat-
ed/Operating parts hardened tool-steel
Tolerance particulars
Thread: +/− 0.1 mm
Alignment pin drill hole: +/− 0.02 mm
3.2.
19B
Operating conditions
The working environment is not to contain any dirt, dust, spray or
vapours. The machine is to be used at temperatures between
10 °C and 40 °C.
The maximum (non-condensing) relative air humidity is to be
between 10% and 70%.
4.
3B
Setup and function
4.1.
20B
Overview
1
Cover
8
Tool Side
2 Robot Side 9 Centering Bushing
3
Ball Bushing
10
Locking Bushing
4
Piston
5
Fail
-
Safe Spring
6 Taper Pin
7
Ball
4.2.
21B
Brief description
The locking mechanism of the tool changing system is realized
over balls. The balls are pressed over a bevel in a receptacle.
With air pressure loss the balls are held in the receptacle by a
spring integrated in the cylinder, whereby an automatic locking is
ensured with decrease of pressure. Contacts fitted with springs
are used for the signal transmission. Thanks to the springs a
bend of the contacts can be avoided. The individual contact pins
can be exchanged individually by a patch cord. Thereby a high
life span and transmission reliability are ensured.
Principle illustration: (1) System decoupled; (2) System coupled; (3)
System locked
Power and moment transmission is by means of two generously
proportioned pins that also function as an antitwist protector.
After the system is locked, the TK 45 tool changer system can
transfer 8 pneumatic lines and electrical signals from the robot
side to the tool side.
Tool changer of the TK-series provide a number of benefits:
For fast and problem-free changing from tools and grippers
at robots or gantries up to a payload of 1000kg.
Transmissionof electrical signals by spring fitted contact
pins
Coupling and uncoupling of pneumatic and hydraulic lines.
Specific splash-proof execution (optional)
IP 65 sealed electrical signal transmission (optional)
Tool changer with internal routing (optional)
Stainless steel tool changer (optional)
5.
4B
Transport, packing, storage
5.1.
22B
Transport
Immediately check on the delivery when received as to
completeness and any transportation damage.
Proceed as follows if there are signs of external damage:
Do not accept the delivery or only under reservation.
Note down the extent of damage on the transportation
documents or on the forwarder's delivery note.
Initiate the complaint procedure.
Object to any shortcoming as soon as it is
discovered. Claims for damages can only be filed
within the valid time spans as set aside for
complaints.
Transportation temperature −20 °C to 65 °C.
Protect against external impact (jolt, blow, vibration)

Assembly Instructions
Tool Changer TK-45
WZW_TK-45_V2.0 4
5.2.
23B
Packing
The packing is to be such as to protect the components up to the
assembly stage from transportation damage, corrosion and other
kinds of damage. Thus, the packing is to be left intact and only
removed just before actual assembly.
Only recyclable materials are used for the packing.
Dispose of packaging materials in accordance with the
respectively valid statutory regulations and local requirements.
5.3.
24B
Storage
Store packs under the following conditions:
Do not store outdoors.
Store at a dry and dust-free location.
Do not expose to corrosive media.
Protect from direct sunlight.
Avoid mechanical shocks.
Temperature for storage: 15 °C to 35 °C
Relative air humidity: max. 60%.
In cases of storage exceeding 3 months, regularly check on
the general condition of all the parts and packing. If need
be, either recondition the conservation protection or renew
it.
There may also be information on the packs
themselves extending beyond the requirements set
out here. They are to be correspondingly kept to.
6.
5B
Assembly and commissioning
CAUTION!
Before assembling the tool changer, the energy
supply needs to be disconnected and the line
system relieved of pressure.
Make a note of the safety instructions and general
hazards listed on Page 2.
6.1.
25B
Assembly
The assembly drill holes and pneumatic connections can be
taken from our ongoing catalogue or the internet.
The tool changer is only to be fastened at the threads provided
for the purpose. If needed, manufacture an appropriate adapter
flange or acquire it from the manufacturer.
Tighten the assembly bolts with thread locking adhesive (e.g.
Loctite 4052) or with Schnorr/Nord lock washers, as appropriate.
Provide compressed air at 4,5-8 bar, install pneumatic
connections at the housing; close off any connections not
needed.
Connect electrical signal lines on the robot and tool sides. To this
end, use either sub-D plug connections or IP65 type plug con-
nections depending on version.
6.2.
26B
Commissioning
There is no extra switch-on/off procedure for the system. The
system is ready-for-operations following installation at the ro-
bot/tool and when the compressed air is supplied. Alternatively,
the system is shut down when the robot is immobilized and the
supply of compressed air interrupted.
In the case of a drop in air pressure, the system is automatically
locked. Only when the system is supplied with compressed air
can the tool be disconnected.
7.
6B
Malfunctions
Tool changer does not lock/unlock
Check on supply of air, replace any non-tight lines, if
necessary
Air pressure too low, raise the air pressure
Examine tool changer seals and renew, if necessary
Tool changer does not dock
Foreign matter/contamination present; clean the tool
changer
Ball resetting ring jams or is faulty; grease or possibly renew
8.
7B
Maintenance and repairs
NOTE!
Make a note of the safety instructions and general
hazards listed on Page 2.
8.1.
27B
Cleaning and upkeep
NOTE!
Corrosive cleaning agents could damage the tool
changer seals and result in them ageing more
rapidly.
Make a note of the following when cleaning and tending to the
tool changers:
Use protective caps and the like to firmly close all the
openings
Check that all connections are tight
Use a metal cleaner
Remove any coarse dirt and keep the coupling surfaces
clean.
8.2.
28B
Maintenance
No particular maintenance is necessary under normal operations
given that the Tool changer is used as originally intended.
To retain tool changer functions, we recommend carrying out the
following maintenance steps at least 2x a year:
Clean tool changer
Check screws and connectors, if necessary retighten them
Check tool changer functions, if necessary repair it
Inspect tool changer for outer damage, defects and wear, if
necessary repair it
Check O-ring seal at the sealing surface if necessary
remove it
8.3.
29B
Repairs
The manufacturer provides you with a comprehensive tool
changer repair service.
Repairs are only to be carried out by authorized specialist
personnel.
CAUTION!
Risk of injury from tensioned compression
springs
There is a strongly tensioned compression spring
in the piston chamber on the robot side. This
stored spring tension could result in serious injuries
arising when dismantling.
- Be careful when opening and taking apart

Assembly Instructions
Tool Changer TK-45
WZW_TK-45_V2.0 5
The following corrective maintenance can be carried out at the
owner’s:
Replacing the seals of the coupling surfaces
Replacing the locking piston/seals on the robot side
Replacing the ball bushing on the robot side
Replacing the tapered pins on the robot side
Proceed as follows:
Locking piston
1. Undo fastening screws (1)
2.
T
Caution!
T
Cover (2) under spring tension - when unscrewing
the final two screws, press the cover on the robot flange
downwards to prevent injuries due to the housing cover
popping up
3. Remove the compression spring (3) and locking piston (5).
Remove the 4 hardened steel balls (8) from the locking pis-
ton
4. You can now replace the piston seals
Ball Bushing
5. Carry out Items 1 -4
6. Lay the main body (9) on the mounting surface
7. Now use a rubber hammer to lightly tap the ball bushing (7)
inwards towards the piston chamber
8. Refit in reverse order
9. Check tool changer as to function
Tighten all screw connectors with a DIN-based
tightening torque and lock to medium strength with
a thread locking adhesive (e.g. Ergo 4052).
Spare parts and a full set of seals can be obtained through the
manufacturer.
1
Flat head screw
7
Ball
Bushing
2 Cover 8 Balls
3
Compression spring
9
Housing
4
P
iston seal
10
O
-
rings
5
Locking piston
11
Taper Pin
6 O-ring
9.
8B
Dismantling, decommissioning, dis-
posal
CAUTION!
Before dismantling the tool changer, the energy
supply needs to be disconnected and the line
system relieved of pressure.
Make a note of the safety instructions and general
hazards listed on Page 2.
9.1.
30B
Dismantling
At the end of their useful lives, the tool changer must be
dismantled and disposed of in an environmentally compatible
manner.
Properly clean sub-assemblies and components and
disassemble them with consideration given to the prevailing local
health & safety and environmental protection provisions.
9.2.
31B
Decommissioning
You carry out decommissioning in the reverse order to
commissioning.
Any tool changer malfunctioning needs to be corrected
before decommissioning
Tool changer needs to be cleaned
Non-plugged connection openings need to be firmly closed
9.3.
32B
Disposal
Pass on disassembled parts for recycling if no arrangements
have been made for returning them or disposal:
Turn metals into scrap.
Hand in plastic elements for recycling.
Sort the rest of the components by material properties and
dispose of accordingly.
10.
9B
Accessories
(Please refer to the ongoing catalogue or the internet for
individual tool changer accessories.)
OPTION:
Specifici splash-proof execution
IP65 sealed electrical signal transmission
Tool changer with internal routing
Stainless Steel tool changer for pharmaceutical, medical
and food industry
3
7
6
5
9
1
8
4
2
10
11
This manual suits for next models
1
Table of contents
Other IPR Tools manuals
Popular Tools manuals by other brands
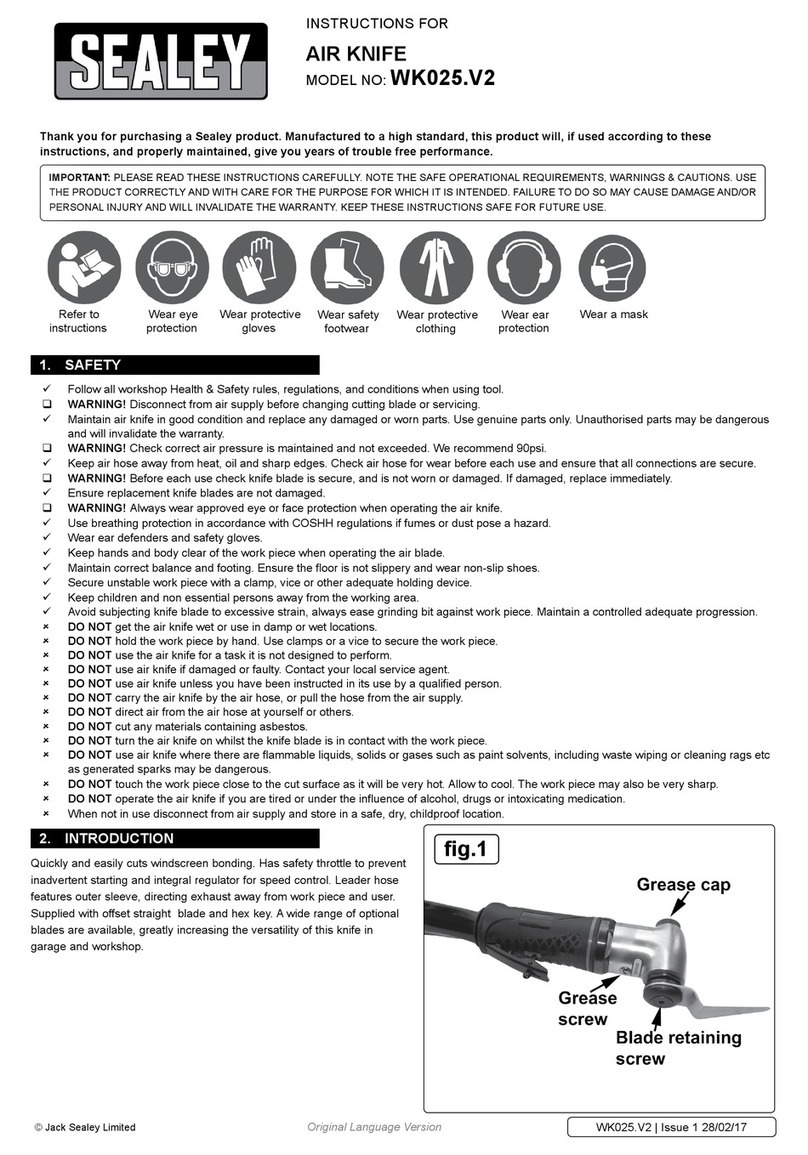
Sealey
Sealey WK025.V2 instructions
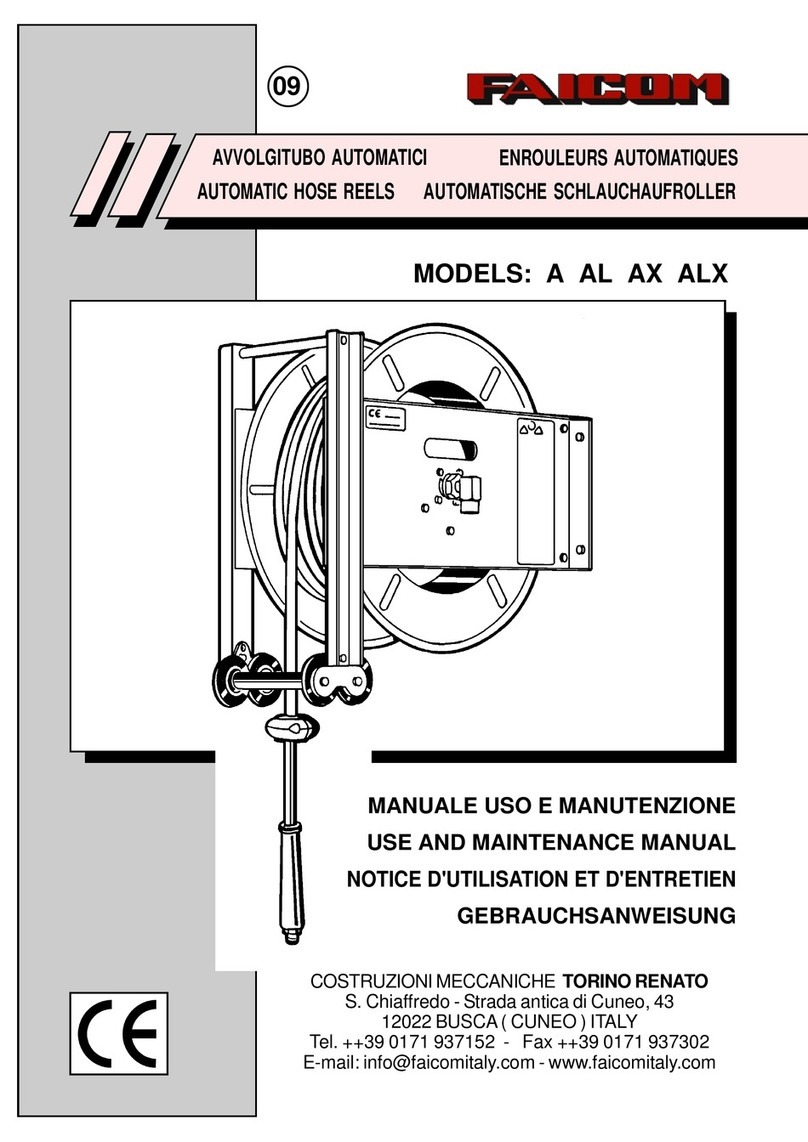
Faicom
Faicom A Series Use and maintenance manual
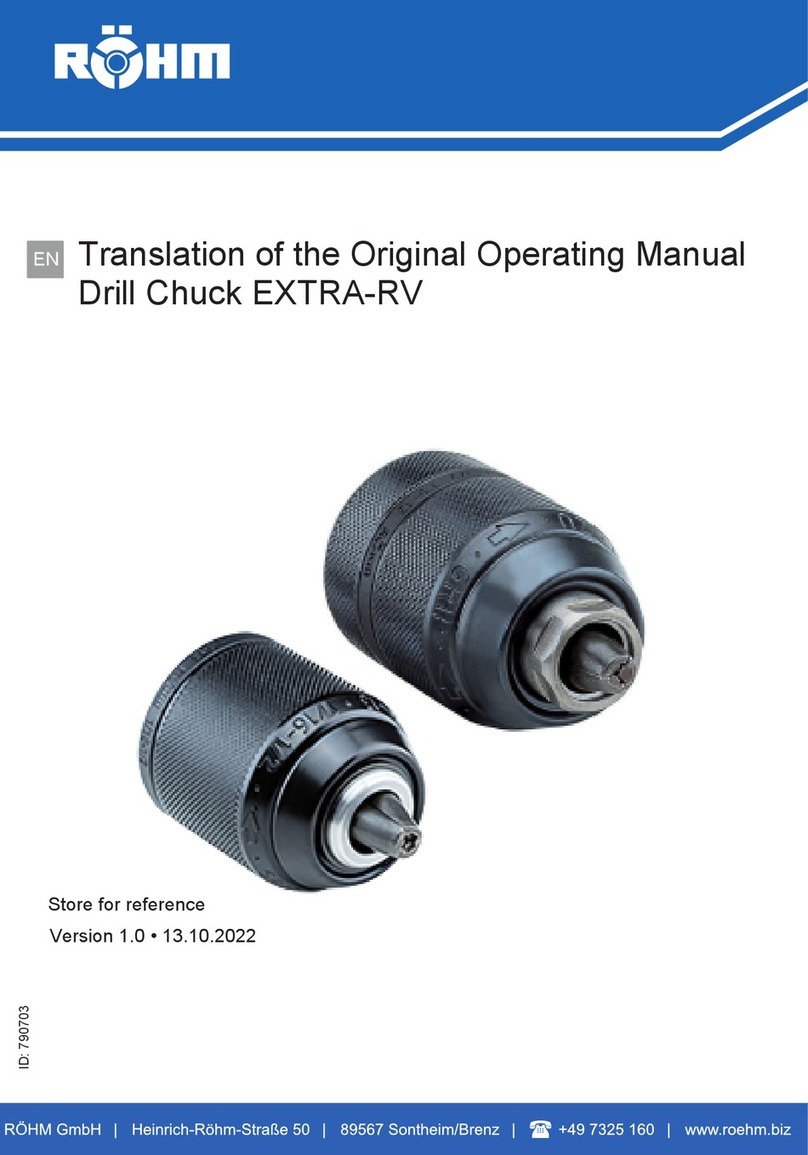
Rohm
Rohm EXTRA-RV Translation of the original operating manual
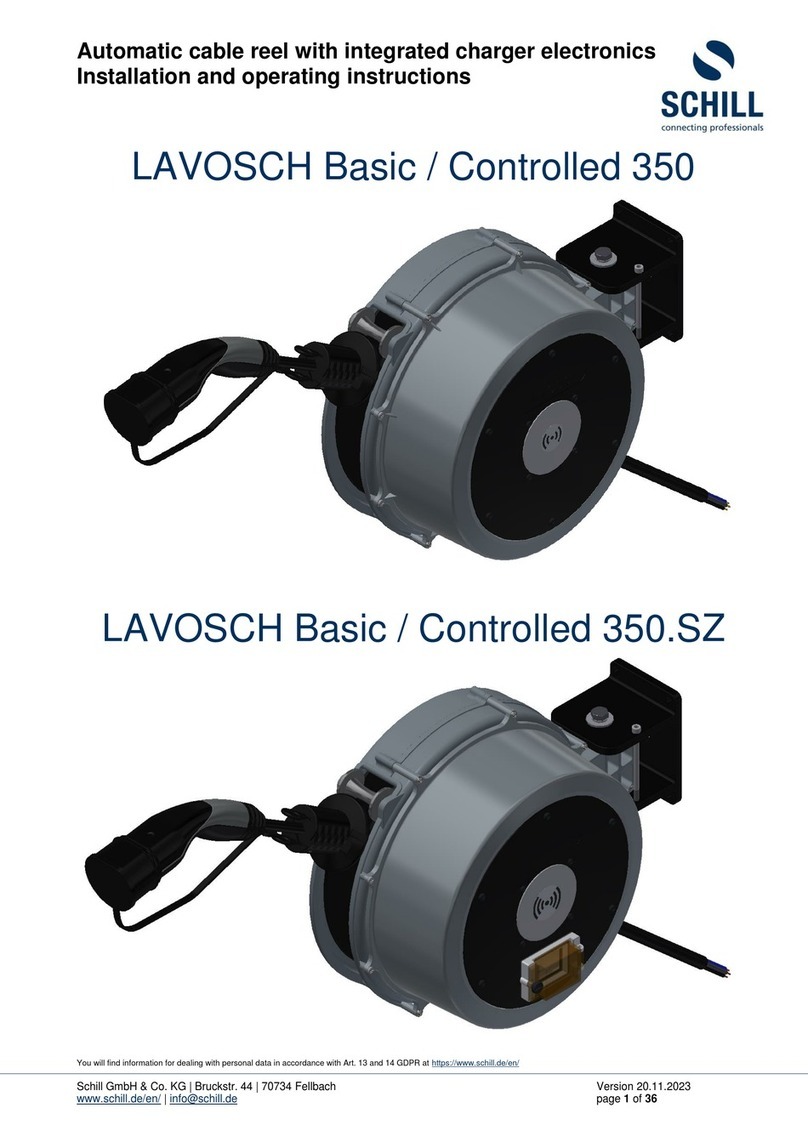
Schill
Schill LAVOSCH Basic / Controlled 350 Installation and operating instructions
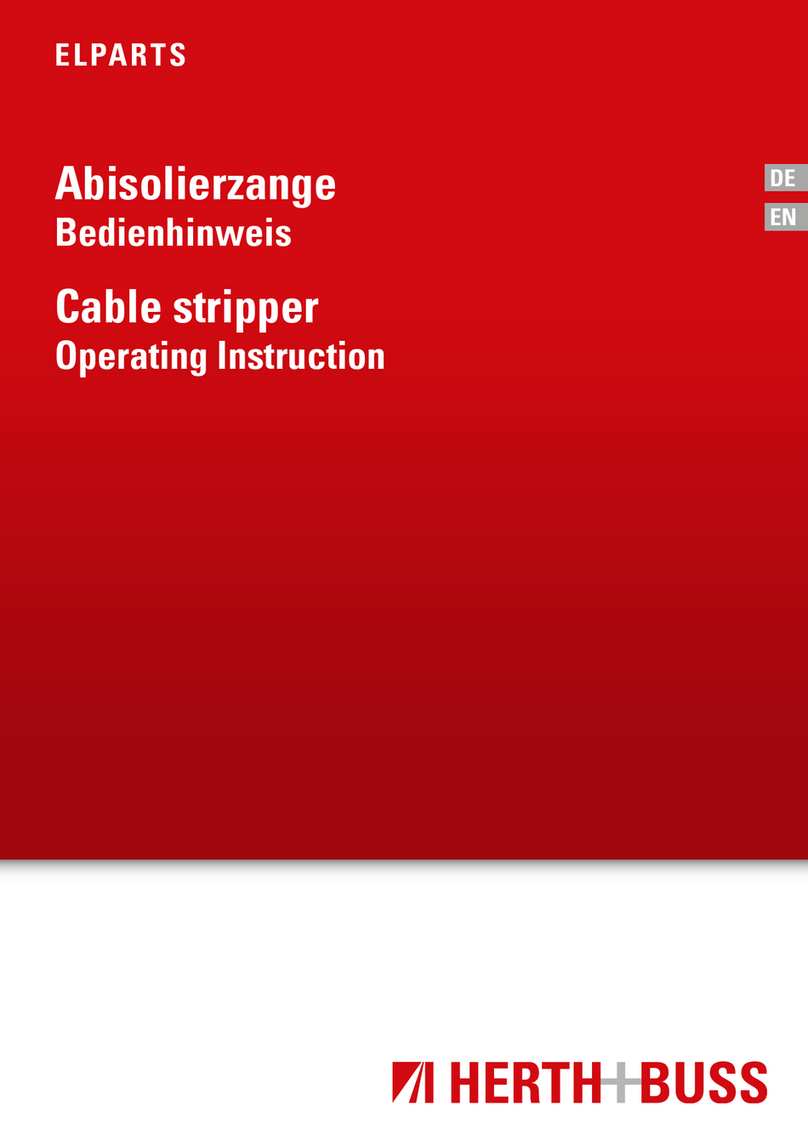
Herth+Buss
Herth+Buss 95942299 Operating instruction

HYDROSCAND
HYDROSCAND HoseReel 7 manual